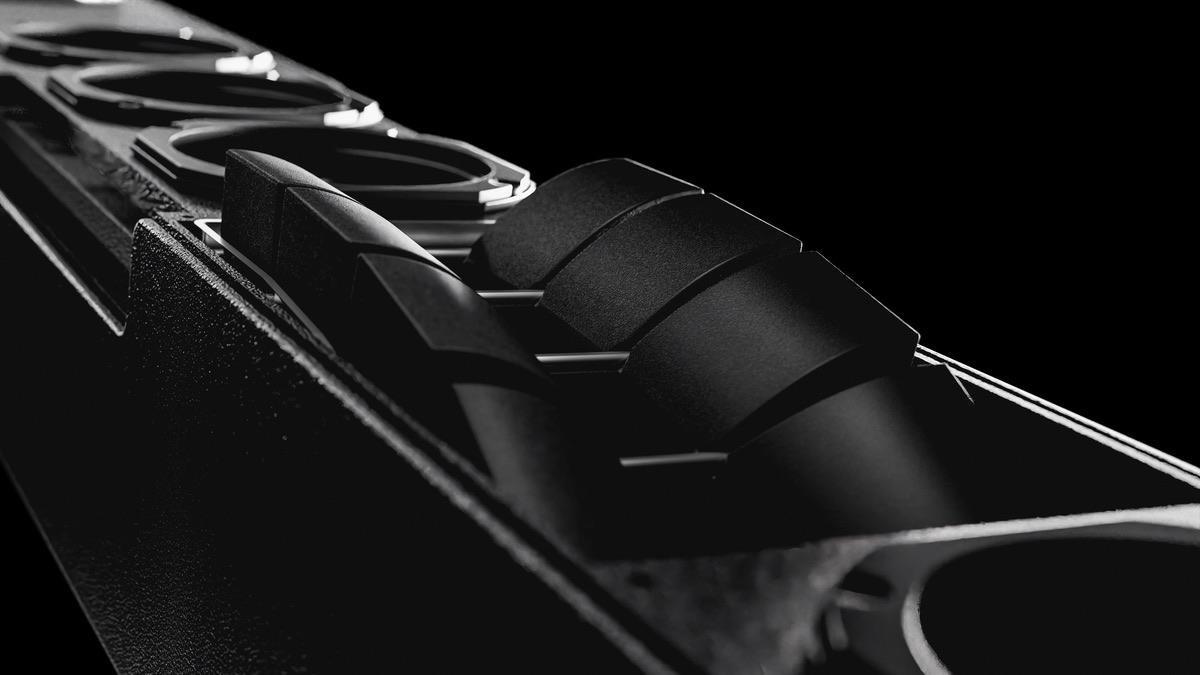
絶え間ない技術の進歩、モダンなデザイン、そして用途の幅広さ。Kling & Freitagの音響増幅システムシステムが他社製品と一線を画す理由は、この点にあります。
過去20 年にわたり、Kling & Freitagは据え置き型および仮設型の音響システム開発にアディティブマニュファクチャリングを活用してきました。元々はラピッドプロトタイピングを目的として導入したものですが、最近では革新的な大音量スピーカーシステム、PIA Mの量産にも上手く活用できることがわかり、アディティブマニュファクチャリングの導入に踏み切りました。
Kling & FreitagのデザインエンジニアであるAndré Figula氏との対談では、アディティブマニュファクチャリングを数年にわたって活用してきた経験、3Dプリントがエンジニアリングにもたらすメリット、そしてKling & Freitagが目指す今後のイノベーションの展望についてお話を伺いました。
30年超の業務用音響増幅システムと大音量スピーカーシステムの開発経験
最高級のサウンドと多彩な業務用音響システム – これがKling & Freitagの強みです。
1991年の創立以来、Kling & Freitagは、世界中で数多くの映画館やスタジアム、コンサートホールに革新的な音響システムを提供してきており、フェスや展示会、野外イベントなど短期的な用途にも、サービスとして大音量スピーカーを提供してきました。
2018年、Kling & Freitagは、多数の大規模プロジェクトの1つを完了。それは、ドイツ、ハンブルクにあるエルプフィルハーモニーのコンサートホールに、アコースティックサウンドの音響増幅システムを設置することでした。
エルプフィルハーモニーのコンサートホール天井には、Kling & Freitagが提供するVIDA L大音量スピーカーが設置されており、ホール全体を贅沢な音響で包み込みます。
音響面での性能はもちろんのこと、Kling & Freitagのシステムは見た目も非常に美しいものです。滑らかで、それぞれのパーツが目立たない大音量スピーカーは、特に建築家とプロジェクトを進める企業から、非常に高い評判を得ています。
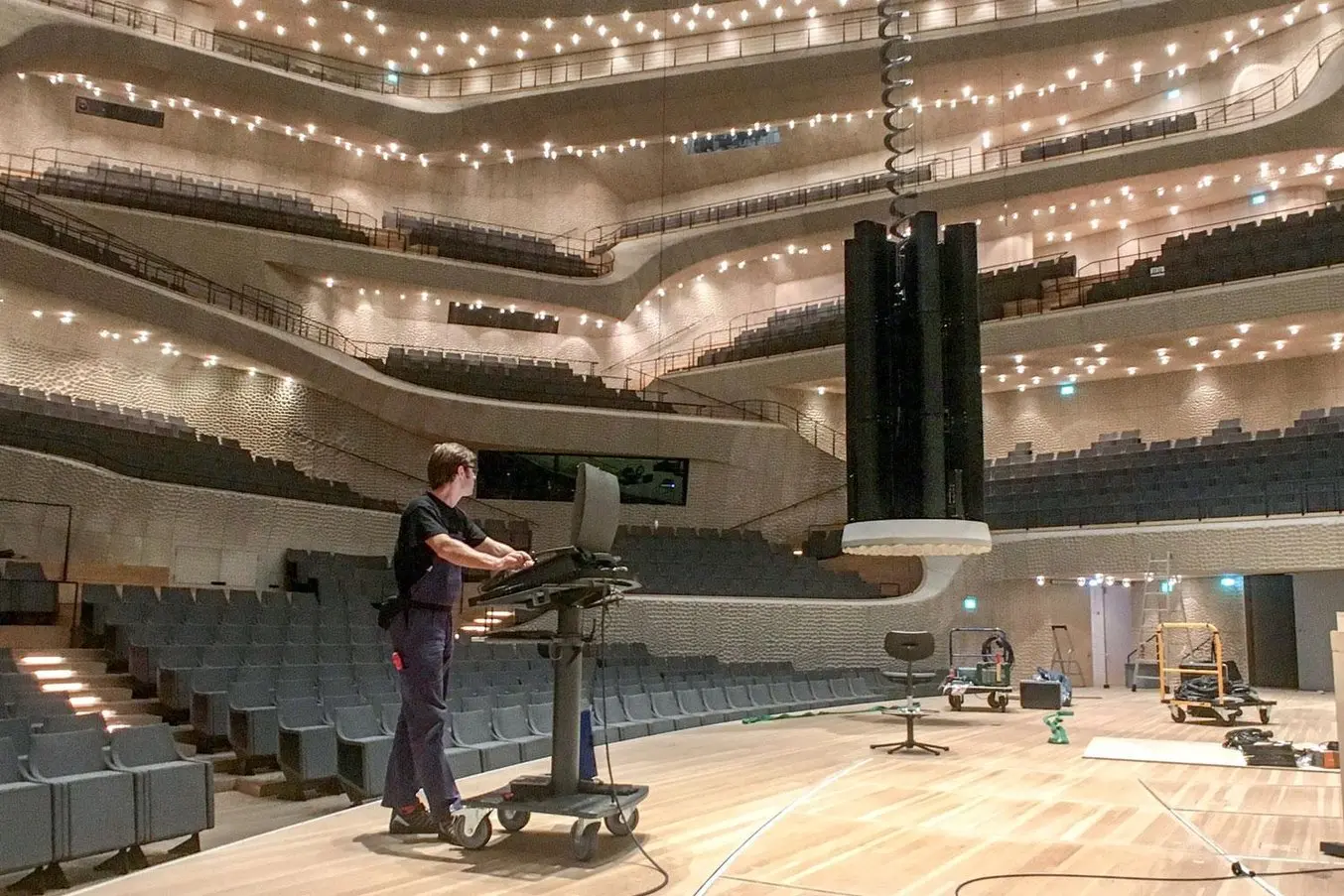
エルプフィルハーモニー管弦楽団の大ホール天井から吊り下げられたKling & FreitagのVIDA Lラウドスピーカーは、ホール全体に豪華な音響体験を提供する。
音響面での性能はもちろんのこと、Kling & Freitagのシステムは見た目も非常に美しいものです。滑らかで、それぞれのパーツが目立たない大音量スピーカーは、特に建築家とプロジェクトを進める企業から、非常に高い評判を得ています。
外注からSLS 3Dプリントでの内製へ
Kling & Freitagは、長年3Dプリントを活用してきました。Figula氏が最初にアディティブマニュファクチャリングに興味を持ったのは、2000年代初期まで遡ります。当時、Figula氏とそのチームは、いわゆる高周波ホーンと呼ばれるものを手作業で、何週間もかけて製作していました。顧客からの要望である高い精度と、それによって実現する高品質なサウンドに応える必要があったためです。
しかし、当時はまだSLS 3Dプリンタは非常に高額で、数千万円を超える価格帯の投資が必要でした。そのため、請負でアディティブマニュファクチャリングでの製作を行う事業者に外注する形で機能確認用の試作品を製作していました。この方法であれば、試作品を直接スピーカーに実装して検証することができた上、外注する手間を考慮しても尚、数週間分の作業負荷が削減できたのです。
その後、SLS方式3Dプリンタをおよそ10分の1程度にまで低価格化したプリンタ、Fuse 1が市場に登場したことで、Kling & Freitagのような中小規模のブランドもアディティブマニュファクチャリングを導入できるようになりました。
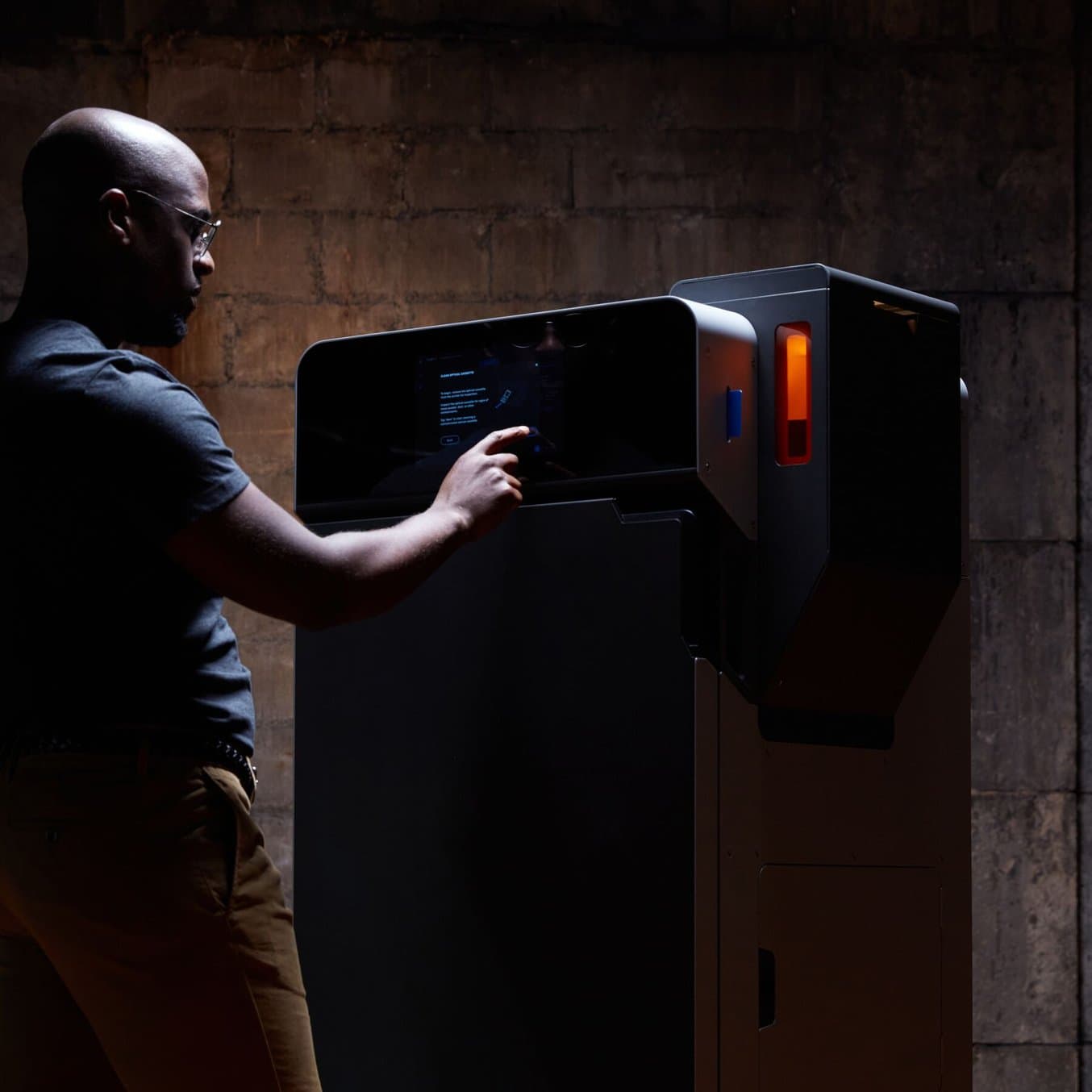
外注か内製か: SLS方式3Dプリントが適するケースとは?
本技術資料では、主にコストと投資対効果の観点から、SLS 3Dプリンタを社内に導入することによるベネフィットを外注時と比較して評価します。
Fuse 1で新たなウェーブガイドを量産
これまでにない革新的なコラムスピーカー「PIA M」は、Kling & Freitagからリリースされた最新のプロダクトです。本製品独自の機能として、ツイーターホーンまたはウェーブガイドと呼ばれる部品があります。可動式の4つのホーンアレイからなり、特定の設置環境において高品質なサウンドを実現するものです。刻々と変化する会場や観客数に応じて、一貫した高品質な音響を実現するのはモバイルユースの音響システムでは至難の業です。そこでPIA Mでは、その洗練された技術によってアコースティックを常に微調整でき、製品の設置環境がどんなものであっても観客席全体に一貫した広がりの豊かなサウンドを届けられるようになっています。
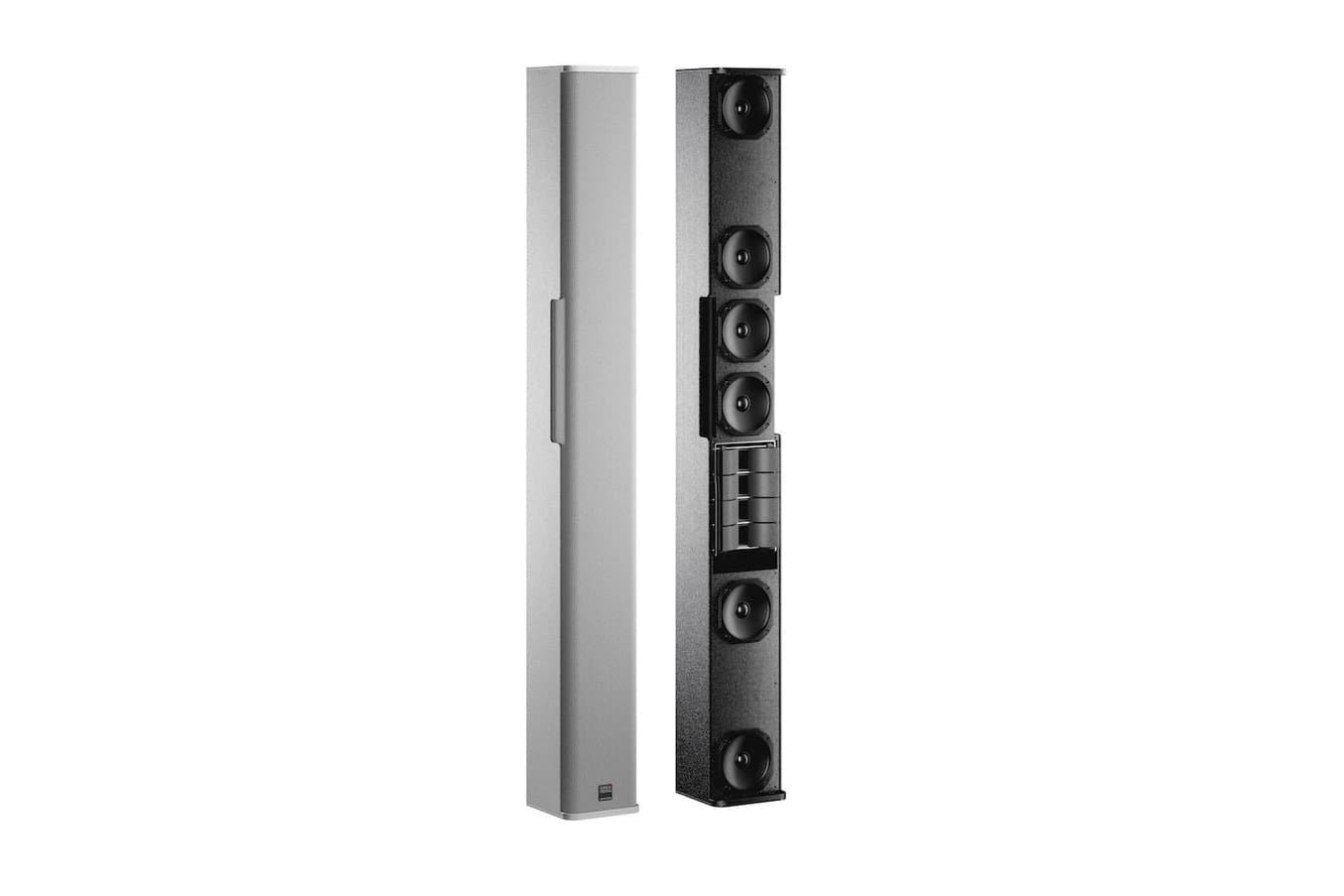
4枚の可動式ホーンアレイで音の広がりを調整可能に。
形状が複雑な可動式ホーンアレイを射出成形で量産しようとした場合、技術的な難易度とコストが格段に高くなってしまいます。
「不可能ということではなかったのですが、射出成形で量産するとしたら、FormlabsのSLSを購入するのと同じくらいのコストがかかってと思います。だから自社にプリンタを導入して、ウェーブガイドの開発とその後の量産を3Dプリントで行うことを決めたのです。」
André Figula氏 Kling & Freitag デザインエンジニア
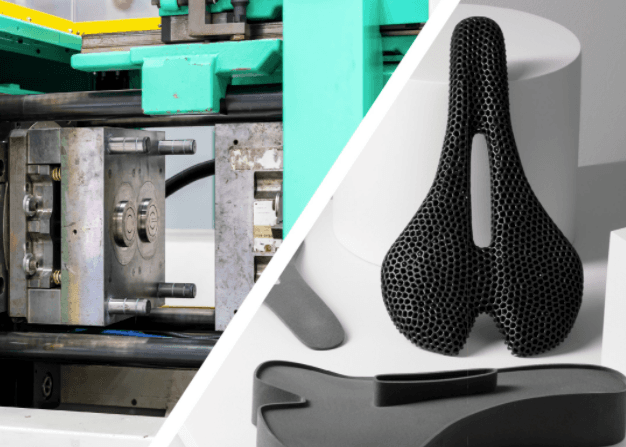
SLS 3Dプリント vs 射出成形:金型レスに切り替えるべき時は?
本技術資料では、実際のユースケースにおけるコストダイナミクスを分析し、SLS 3Dプリントと射出成形、またはその両方を使用する際のガイドラインを解説します。

PreForm softwareにてSLS 3DプリンタFuse 1のビルドチャンバーに最大限までパッキングした造形品。
Figula氏らはウェーブガイドの量産を始めて以来、業務用オーディオの業界から多くの問合せを受けるようになりました。
また、Fuse 1を活用するたびにそのシナジーを実感しているようです。例えば、試作品を製作する際にビルドチャンバーのスペースに余白があれば他の部品もそこでプリントして開発作業に利用することで、多くの時間とコストを削減できています。
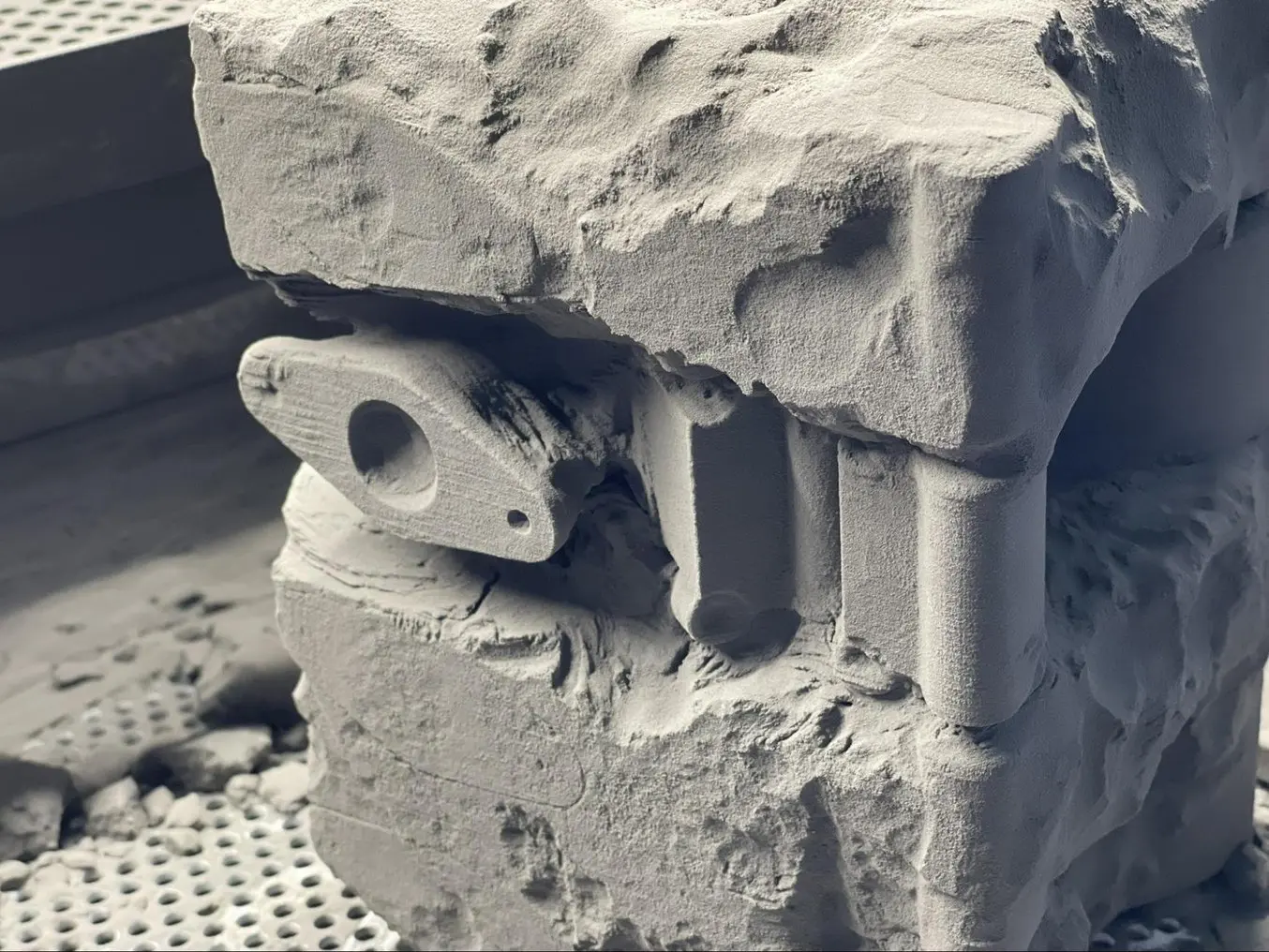
Fuseシリーズによるプリント品はFuse Siftの半密閉式陰圧ブースで後処理(粉末の除去)を行う。
アディティブマニュファクチャリングがもたらすデザインの自由
Kling & Freitagは、SLS 3Dプリンタによる内製を始めたことで、他のメリットにも気が付きました。新製品開発におけるデザインの自由度です。
「例えば、新製品を開発する際には試作と検証後のデザイン調整で、その形状をかなり柔軟に調整することができます。射出成形ではそんなことはできないので、製品の完成形は違ったものになっていたでしょう。」
André Figula氏 Kling & Freitag デザインエンジニア
ウェーブガイドの繊細な形状、そしてデザイン上にある無数のアンダーカットは、射出成形では実現できないものでした。
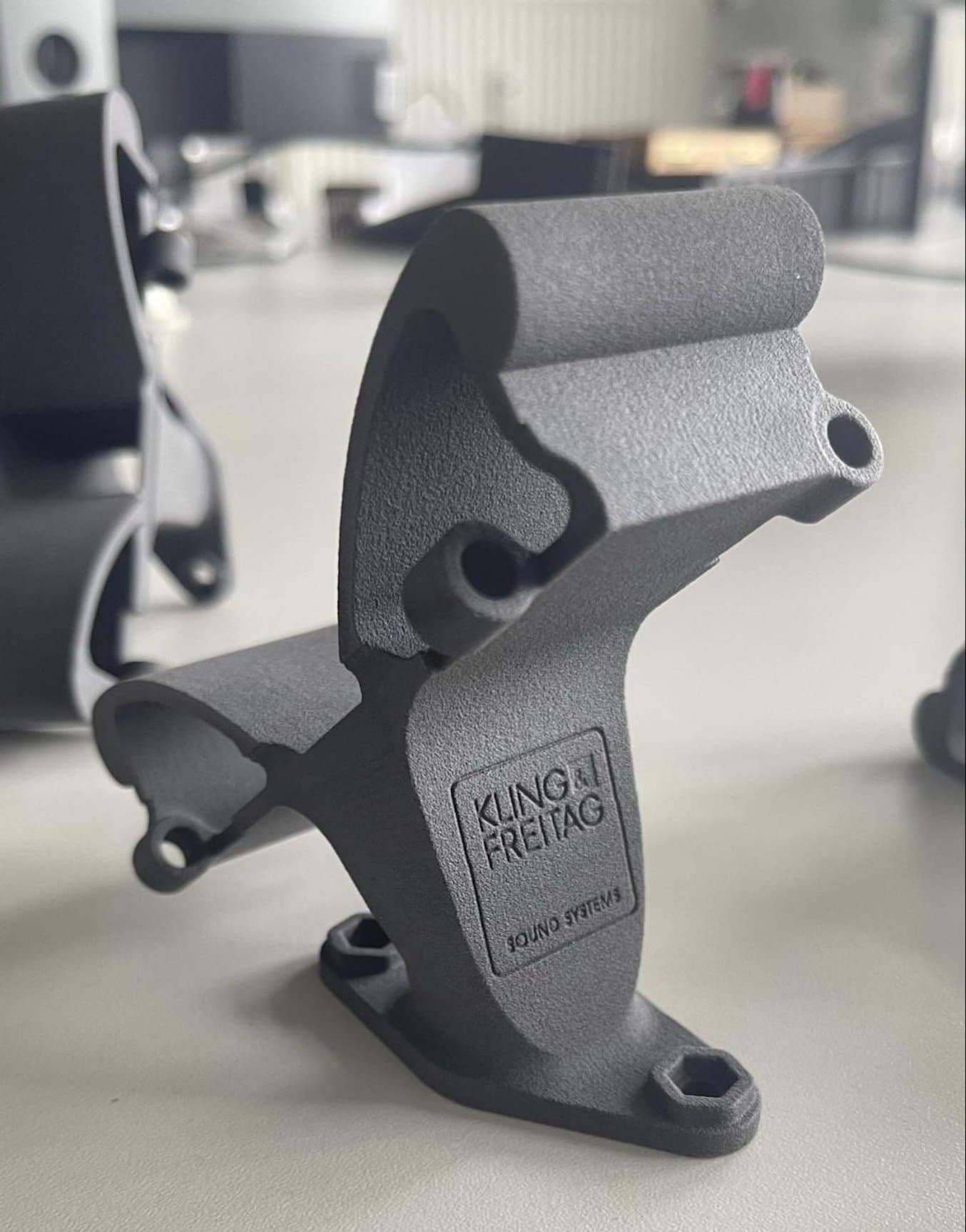
Nylon 12パウダーで造形した4つの可動式ホーンアレイのひとつ。
「大音量スピーカーPIA Mのウェーブガイドは、Fuse 1なしでは実現できなかったと思います。」
André Figula氏 Kling & Freitag デザインエンジニア
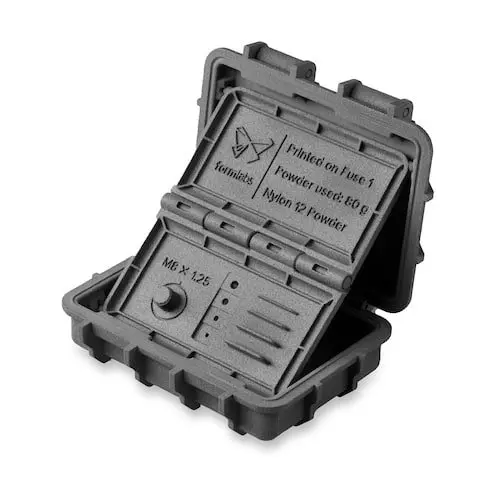
次のステージへ:Fuse 1で特許取得を目指せるイノベーションを
現在、Kling & Freitagでは3Dプリンタが絶え間なく稼働しています。主な用途は大音量スピーカーシステムPIA Mのウェーブガイドの量産ですが、新製品の開発にも使用されています。
「3Dプリントによって、新製品の開発プロセス全体が以前よりも早く、柔軟かつ高いコスト効率で行えるようになりました。」
André Figula氏 Kling & Freitag デザインエンジニア
その新機軸の1つはSLS 3DプリンタFuse 1で開発から量産まですべて一貫して行われ、特許出願まであとわずかというところまで来ています。
「外部委託で製造していた頃は、イテレーションを行うごとに新しい試作品の完成までに8週間も待つ必要がありました。それが今では、新しいバージョンのデザインが出来上がるたびにFuse 1にアップロードするだけで、あっという間に機能確認用の試作品が出来上がるんです」と、Figula氏は教えてくれます。
Fuse 1でラピッドプロトタイピングや量産を行う方法の詳細は、Formlabsのスペシャリストにお問合せいただき、無償サンプルパーツをお申し込みください。