Ceramic 3D Printing Made Accessible: Introducing Alumina 4N Resin for Technical Ceramic Parts
Formlabs is proud to announce Alumina 4N Resin — the first accessible, affordable, high-performance technical ceramic 3D printing material for stereolithography (SLA) 3D printers.
For the first time, users can now leverage the workflow flexibility and design freedom of 3D printing with a 99.99% purity alumina material, opening the doors to intuitive and cost-effective ceramic 3D printed part manufacturing.
“By offering a low-cost production set-up, Formlabs opens up a new chapter for the additive manufacturing of ceramics. The printer’s ease of use, combined with intuitive software solutions and a large build volume - especially given the printer's small footprint - make the Formlabs ecosystem a perfect choice for organizations looking to directly print ceramic parts.”
Dr. Malte Hartmann, Development Engineer at Bosch Advanced Ceramics, Grow Platform GmbH. Bosch Advanced Ceramics is a recognized development partner for client-specific ceramic assemblies, integrated products, ceramic components, and small and large production runs of every complexity.
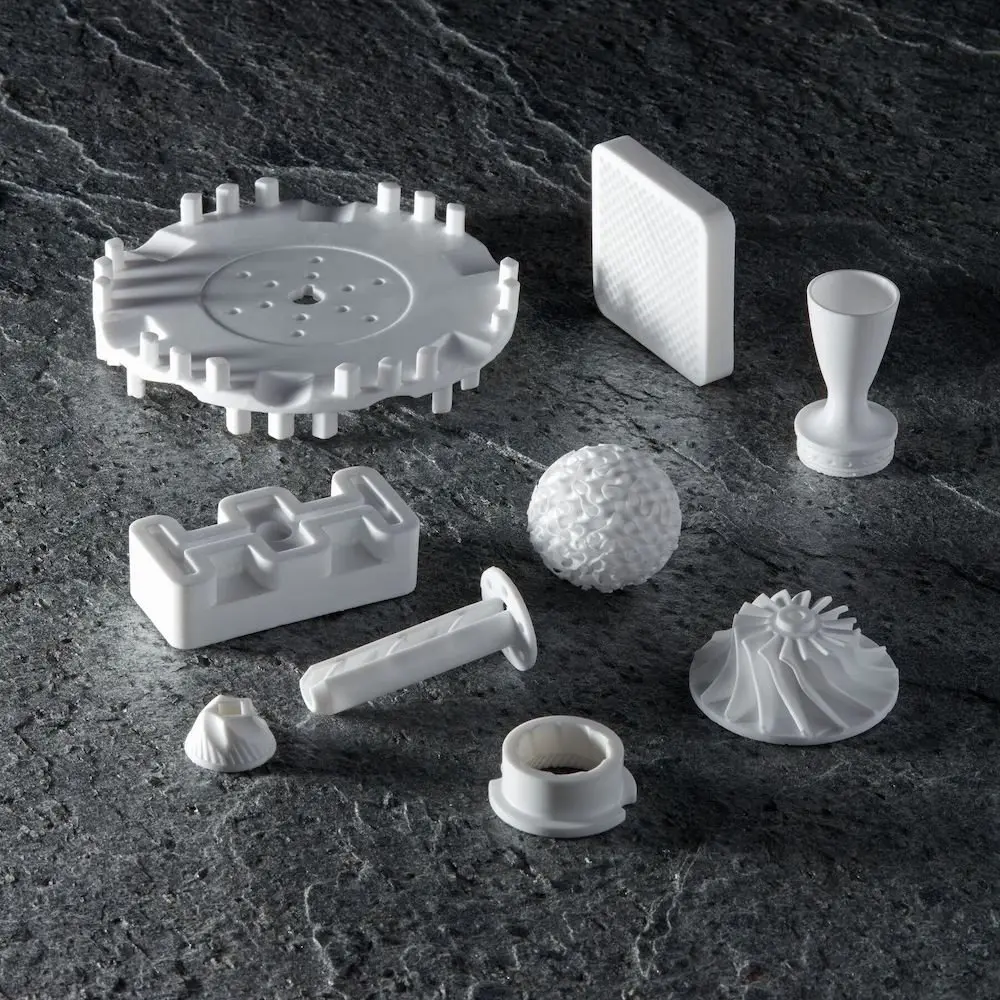
How Formlabs Unlocks the Future of Ceramic Engineering
Watch the webinar to learn how manufacturing ceramic components with 3D printing is possible with reduced production costs and lead times and increased design freedom.
A New Era of Accessible Technical Ceramics
Formlabs SLA printers bring ease of use, reliability, and affordability to high-performance 3D printing. With each newly released material, those qualities extend to new applications and industries, empowering our users to continue innovating and pushing the boundaries of what’s possible.
Alumina 4N Resin is the first high-performance technical ceramic that is within reach for anyone looking for an affordable and intuitive workflow, or who is currently using Form 3 Series desktop printers and wants to expand their applications.
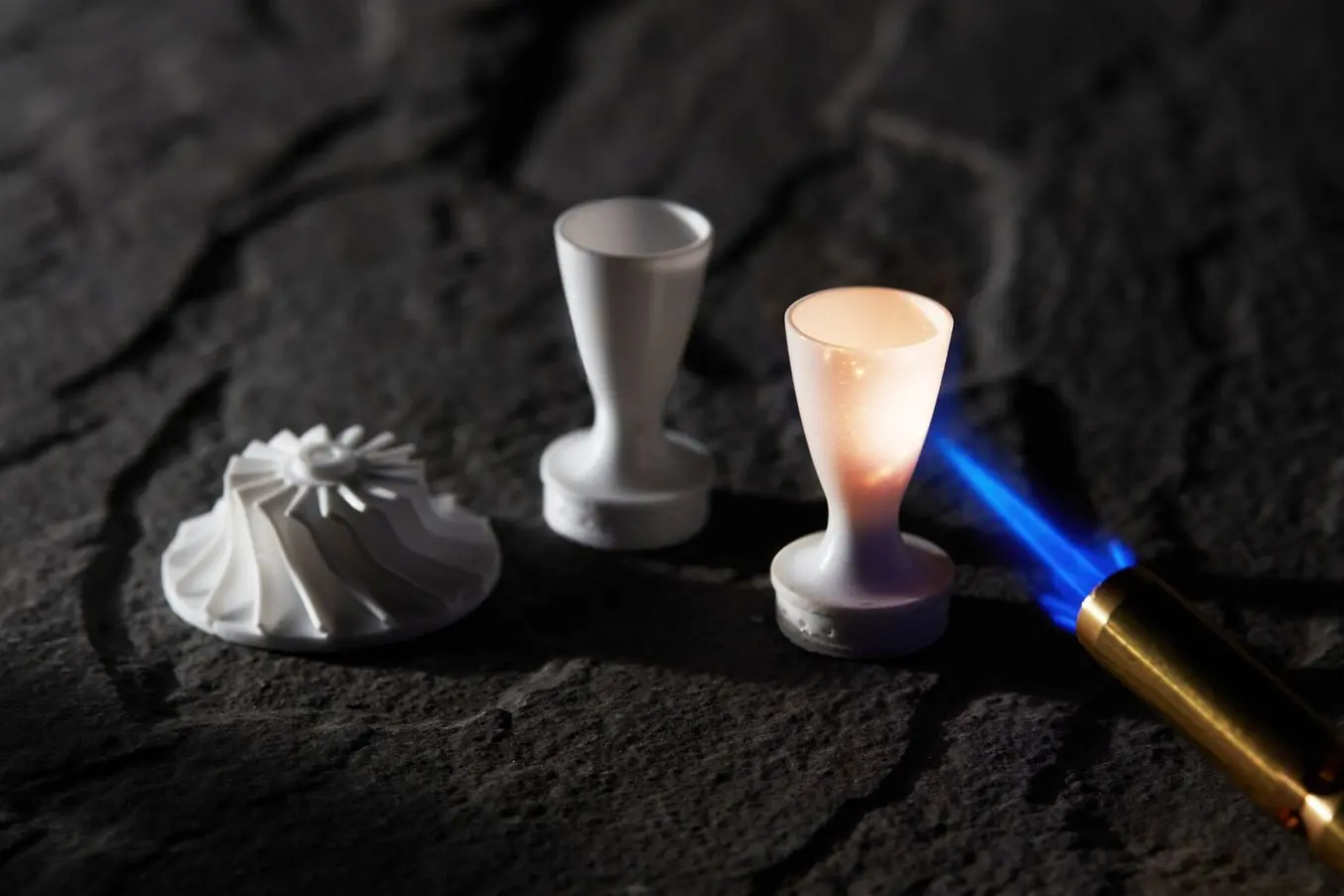
Alumina 4N Resin offers extremely high thermal resistance unprecedented in 3D printing.
Why Choose Ceramic 3D Printing?
Reduce Production Costs and Lead Times
Traditional methods of fabricating ceramic parts include expensive slip casting, pressing, or injection molding processes. These workflows are typically outsourced to specialist contractors and require specialized equipment and expertise. Engineers and manufacturers that only need a few ceramic parts are locked into a price and process that only becomes cost-effective at high volumes.
As 3D printing has done for so many other materials and applications, it also provides answers to these challenges; Formlabs SLA printers make manufacturing extremely cost-effective.
Ceramic Manufacturing Method | Time to First Part | Cost for Single Part |
---|---|---|
3D Printing With Formlabs Alumina 4N Resin | 8 - 15 days | $50 - $500 |
3D Printing With Other Ceramic 3D Printers | 8 - 15 days | $300 - $2,500 |
Slip Casting | 3 days - 6 months | $50 - $20,000 |
Pressing | 2 - 12 months | $30,000 - $500,000 |
Injection Molding | 3 - 15 months | $50,000 - $1,500,000 |
Increase Design Freedom
Additionally, these traditional manufacturing processes pose severe design constraints — the casting and molding workflows inhibit design freedom and make it difficult to produce overhangs, internal channels, lattice structures, and more.
The design flexibility of 3D printing opens up new opportunities for innovation in industries that require high heat and chemical resistance, like aerospace and automotive. In these applications, air or fluid flow can be improved by even the smallest design change, but for ceramic parts, these changes are often limited by the design constraints of traditional methods. 3D printing makes it possible to produce technical ceramic parts that can be used in extreme environments in order to find the best design and realize these complex features that would be impossible to mold or cast.
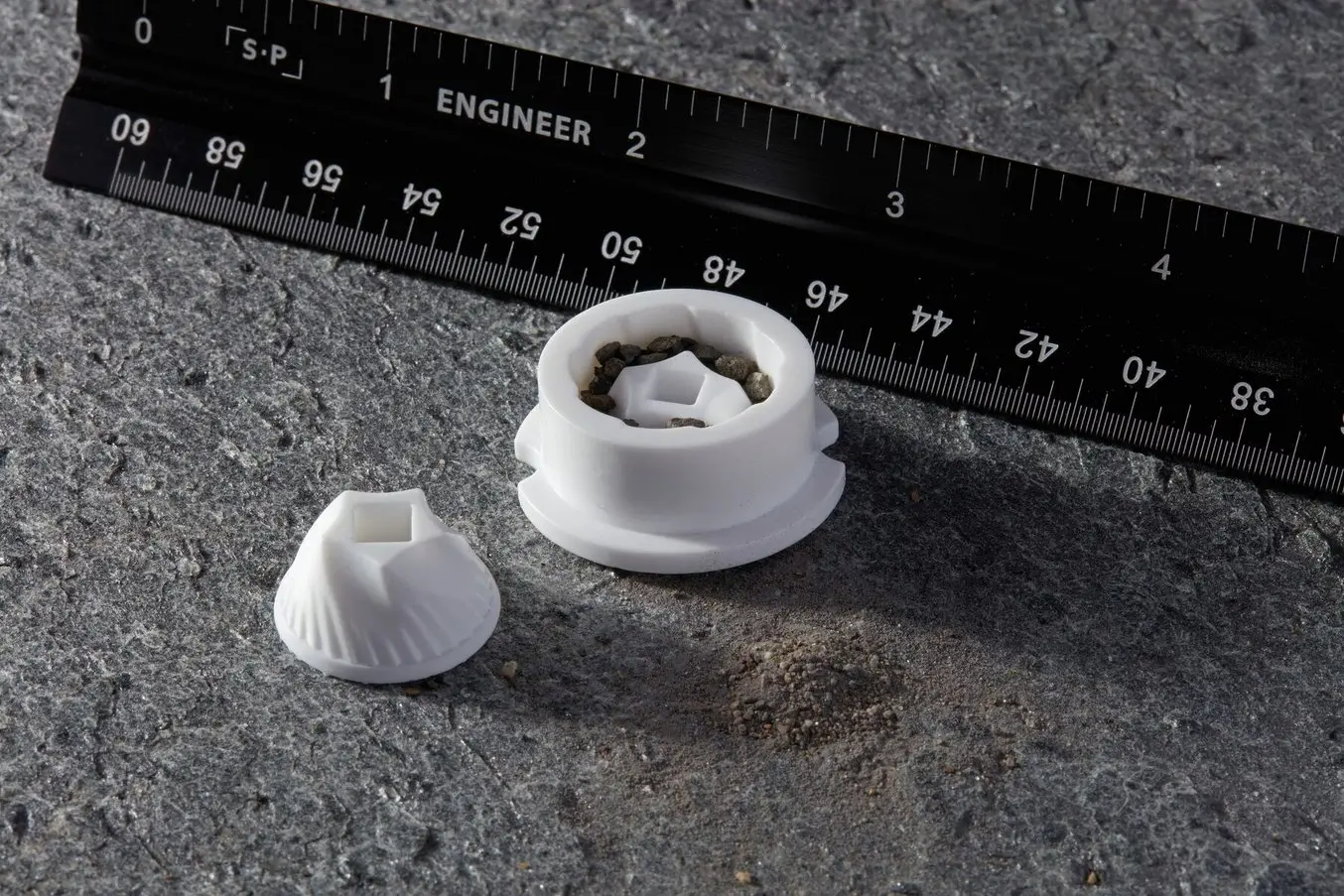
A grinding disk and burr 3D printed in Alumina 4N Resin.
Impressions From Our Beta Testers
Several Alumina 4N Resin users remarked on the material’s success within ceramic additive manufacturing:
Air Force Research Laboratory
The Air Force Research Laboratory's Materials and Manufacturing Directorate develops materials, processes, and advanced manufacturing technologies for structural, electronic, and optical components of aircraft, spacecraft, missiles, rockets, and ground-based systems. Air Force product centers, logistic centers, and operating commands rely on the directorate's expertise in materials, nondestructive inspection, systems support, and advanced manufacturing methods to solve systems, expeditionary deployment, and operational challenges.
“The Alumina 4N Resin and Form 3 was used to rapidly prototype parts for turbine engines and materials research, making parts that are extremely difficult, if not impossible, to make using traditional ceramic manufacturing. The combination allowed us to iterate quickly and affordably on designs without having to wait for expensive tooling to be made. Additionally, we used the resin and printer to manufacture custom fixtures for our ovens. One such fixture holds a ceramic matrix composite specimen in a specific manner in the furnace during sintering. Another use was making crucibles to a specific dimension to hold powder and parts during thermal debind and sintering. Alumina 4N Resin is remarkably easy to work with and plugs into our workflow seamlessly. It fits a need in the market, with a low barrier of entry that allows us to rapidly iterate on designs and produce parts at a comparably low cost.”
Benjamin Lam, Materials Research Engineer at the Air Force Research Laboratory
Atlas Elektronik UK
Atlas Elektronik UK LTD is a naval/marine electronics and systems business based in the United Kingdom. Their expertise in the fields of hydroacoustics, sensor engineering, and information technology has made them the preferred supplier to numerous navies and civilian customers worldwide.
“This new ceramic material from Formlabs helps us convert existing parts over to additive manufacturing. The heat sink pictured is a ‘simple shape’, but it can carry a long lead time of up to 3 weeks which we are able to reduce to just a few days. Also, the work for another application gave us complete design freedom to assist our R&D section giving optimal solutions to more complex problems with wear resistance and its electrical properties.”
Kieran Smith, Production Technician, Atlas Elektronik UK LTD
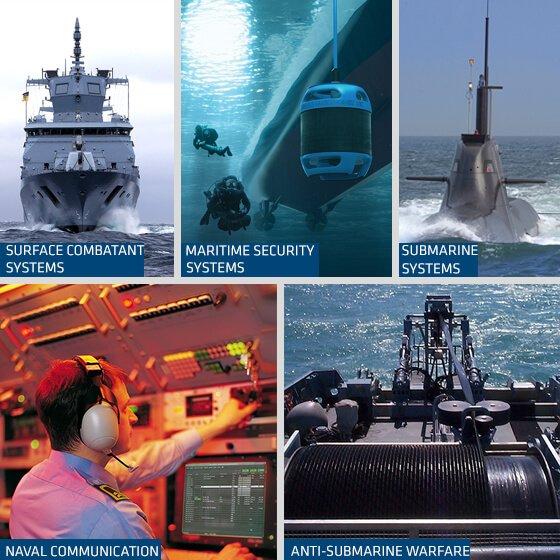
How Atlas Elektronik 3D Prints Technical Ceramic Parts with Formlabs
Learn how Formlabs and Atlas Elektronik use Alumina 4N Resin alongside traditional firing techniques to produce highly technical ceramic parts.
Applications for 3D Printed Ceramic Parts
Technical ceramics are commonly used in any industry that requires extreme heat, chemical, or electrical resistance, such as:
- high voltage applications
- thermal protective parts
- foundry tools for metal casting
- customized casting tools and kiln furniture
- functional engineering prototypes that require high temperature, chemical, or electrical resistance
Mechanical Properties | Sintered (Metric) | Method |
---|---|---|
High Temperature Flex Strength (1270°C) | 250 MPa | ASTM C-1211 |
Purity [%] | 99.99% | - |
Relative Density | 98.60% | ASTM C-373 |
CTE (Coefficient of Thermal Expansion) | 5 ppm/K | ASTM E-228 |
Maximum Working Temperature | 1500°C | - |
Young’s Modulus | 380 GPa | ASTM C-1259 |
As a high temperature insulative material, ceramic is ideal for electrical testing and for parts like isolators, connector housings and covers, terminal blocks, spark plug insulators, electrical mounting, and insulating housings or tubes. For engineering firms and manufacturers, access to a technical ceramic that can be customized, tested, and deployed cost-efficiently in low volumes can make that switch easier and more efficient.
Using Alumina 4N Resin for manufacturing aids in traditional foundry and casting processes is another opportunity for increased efficiency and cost-savings. Despite the range of shapes, sizes, and forms traditionally manufactured objects can take, the ovens, kilns, and other equipment remains the same. With Alumina 4N Resin, custom designed jigs, fixtures, kiln furniture, hooks, hangers, and more can be easily designed and printed to fit more parts into an oven, optimize the space and time, and improve the consistency of the firing results.
For engineering research, a technical ceramic workflow that doesn’t require extensive grant funding and red tape can pave the path to innovations in energy efficiency, aerospace, transportation, chemical handling, and more. Being able to produce ceramic parts such as equipment or tools faster and more affordably will give engineers a head start on developing products and processes that can change the way these industries currently operate.
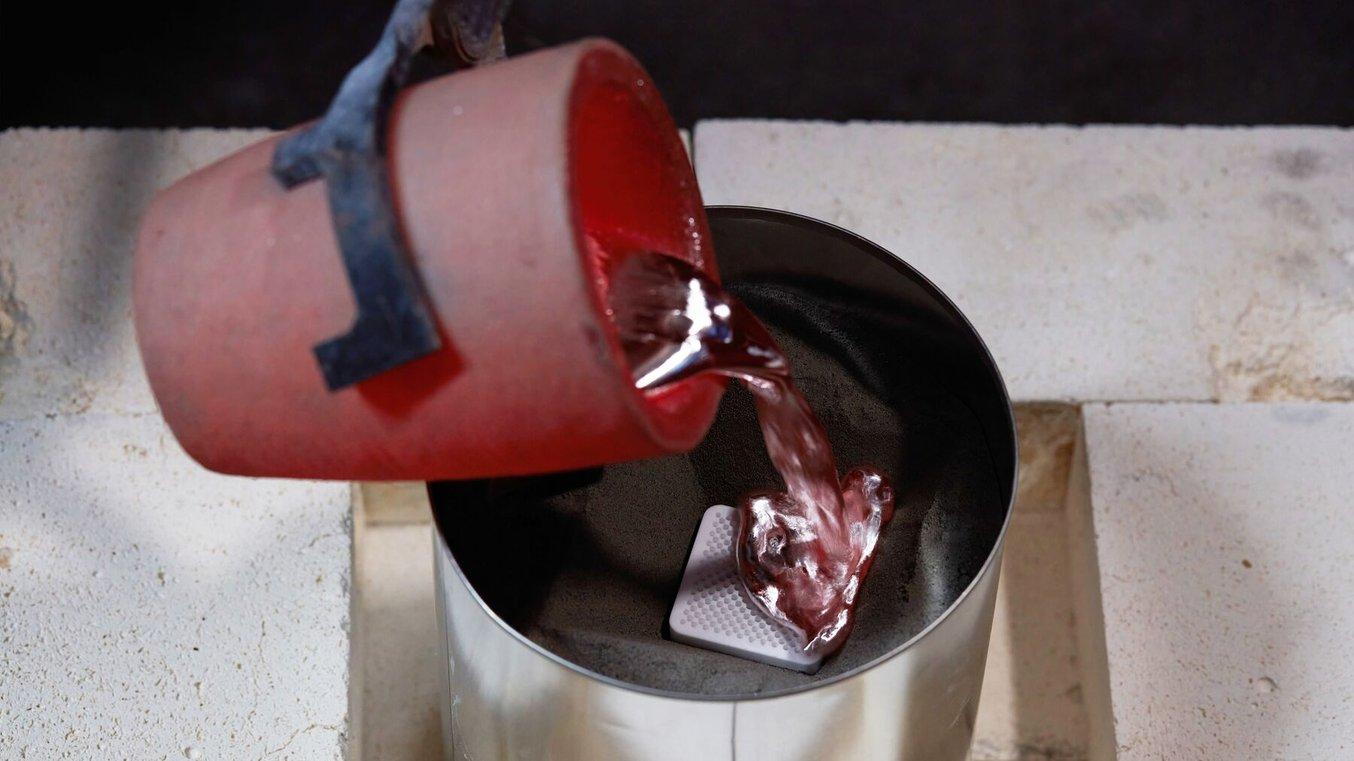
Metal pouring through a sieve printed in Alumina 4N Resin.
How to 3D Print Ceramic Parts with Alumina 4N Resin
The intuitive workflow of the Formlabs SLA printers combined with Alumina 4N Resin creates an entirely new means for producing high performance ceramic parts, previously only possible through expensive contractors or 10x more expensive (dedicated) ceramic 3D printers with complex workflows.
-
3D Print: Alumina 4N Resin prints on Form 3/B/+ printers at 50 microns layers. Due to the high green strength, it requires a thin part removal tool, such as a razor blade, in order to remove it from the Stainless Steel Build Platform.
-
Wash: After the parts are removed from the platform, use the required Ceramic Wash Solution to clean the parts, including for wet sanding supports. The solvent can be used in the Finish Kit buckets or Form Wash.
-
Debind and Sinter: Remove excess solvent with compressed air before drying the parts completely in an oven. Move the parts to the debinding oven and sinter them in the oven for the final step in the process. In order to achieve optimal material properties, follow the firing schedule instructions exactly, found here.
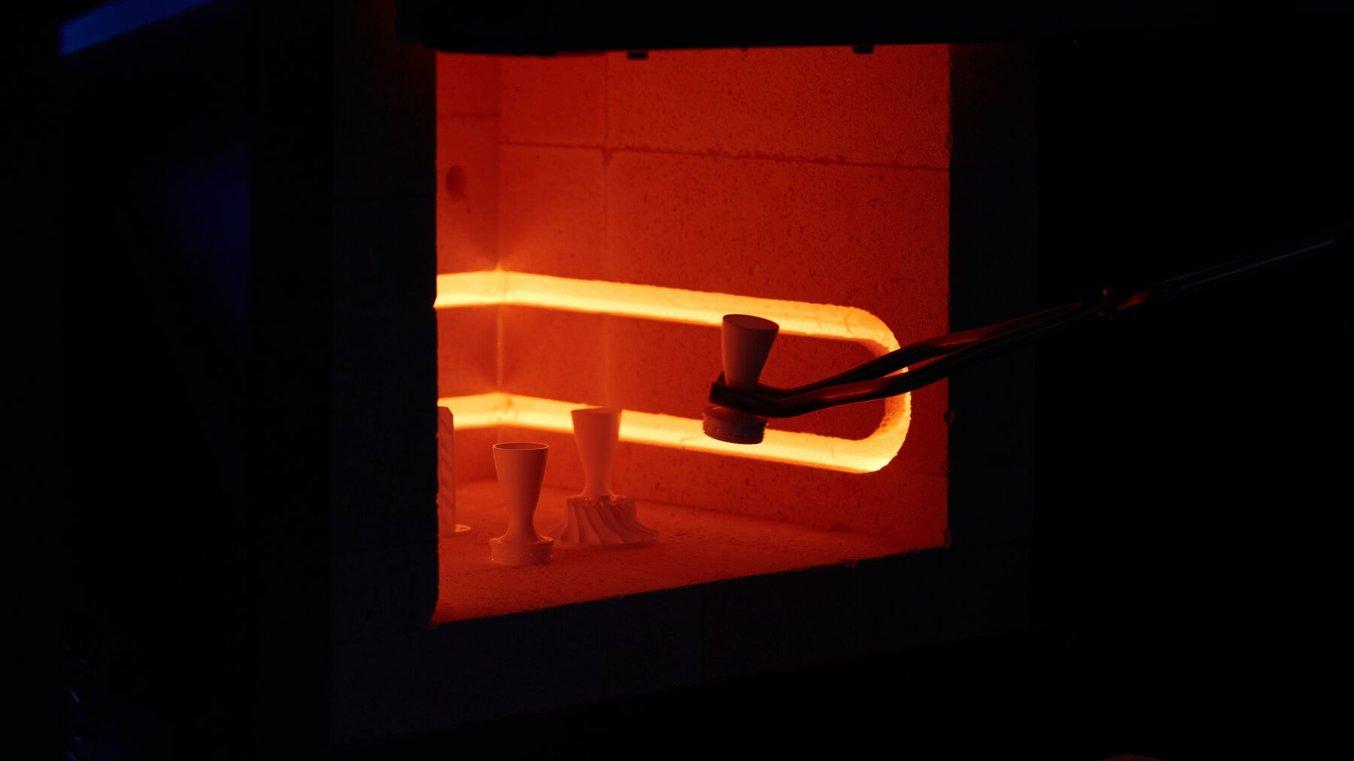
Parts printed in Alumina 4N Resin need to be sintered in a hot kiln.
The Bridge to the Future of Ceramic Engineering
Ceramic parts and products have been used for millennia, but little has changed. Modern industries that rely on ceramics for high heat, electrical, and chemical tolerance are held back by the limitations of slip casting, pressing, or molding. Though some ceramic 3D printers have shown what’s possible, these workflows have been out of reach for many due to their high cost and complexity.
Through the same efficiency, ease of use, and affordability that Formlabs has brought to so many other workflows, Alumina 4N Resin changes what it means to manufacture technical ceramic parts. This new, high-purity, technical ceramic 3D printing material can merge the best of 3D printing with the best of high performance materials, and expand possibilities in every industry.
To learn more about Alumina 4N Resin, or to discuss your application with a specialist, contact our team today.