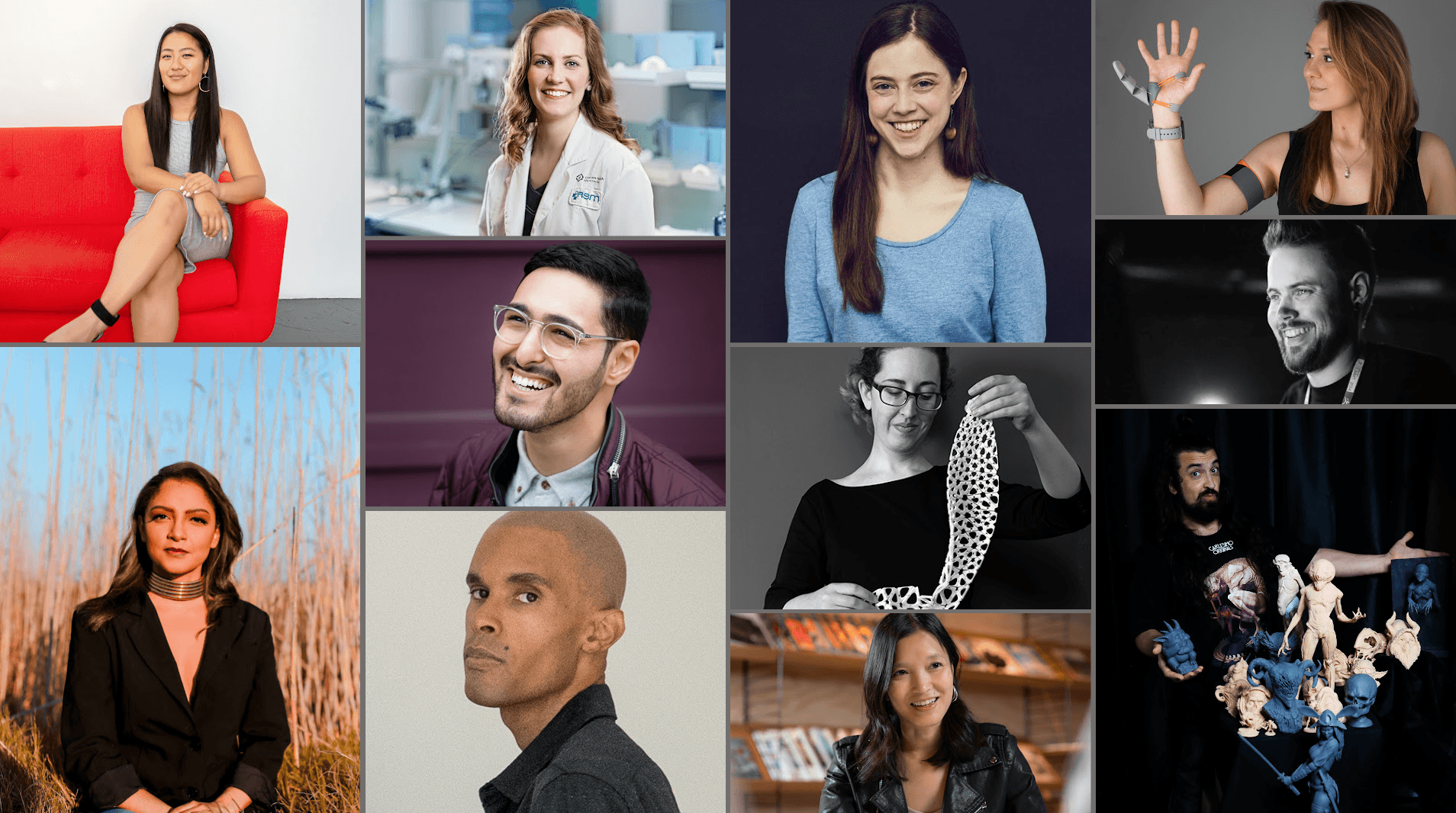
Formlabs Ambassadors Inspire!
Meet our community of over 50 3D printing leaders from 13 countries, using Formlabs products to solve challenging problems.
The same tools, dozens of perspectives
From users who rely on a single printer for everyday prototyping, to those leveraging print farms to manufacture at scale, our ambassadors all have one thing in common: they are redefining the way things are made.
Formlabs Ambassadors share their experiences and expertise with the 3D printing community by leading webinars, writing blog posts, posting their work on social media, and advising on white papers.
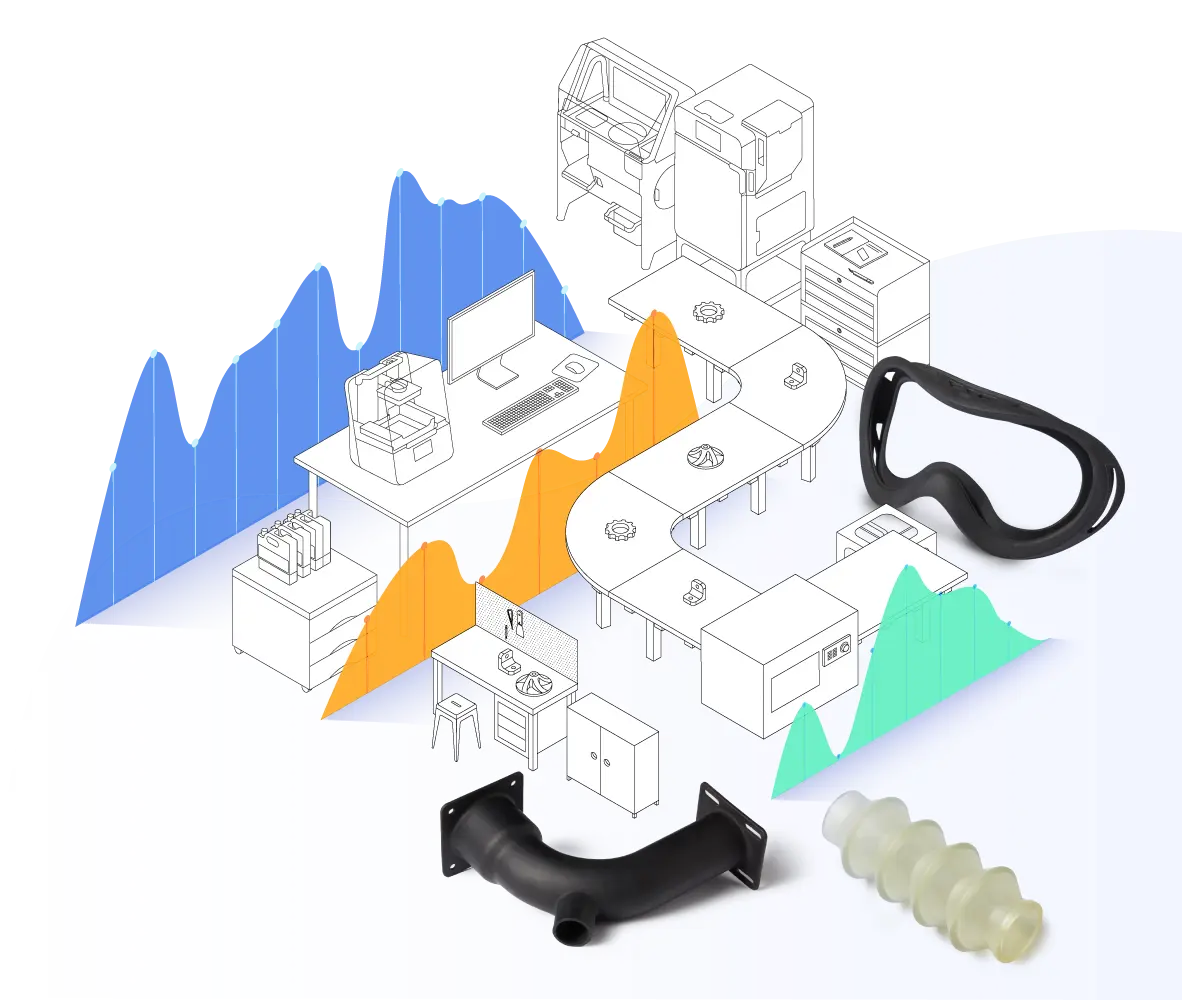
The 2022 3D Printing Applications Report
Filled with key insights on what is driving current and future investment in additive manufacturing, our report is based on survey data from 400 global businesses, and includes testimonials from Ambassadors Kat Ermant, Christina Perla, and Will Hilgenberg.
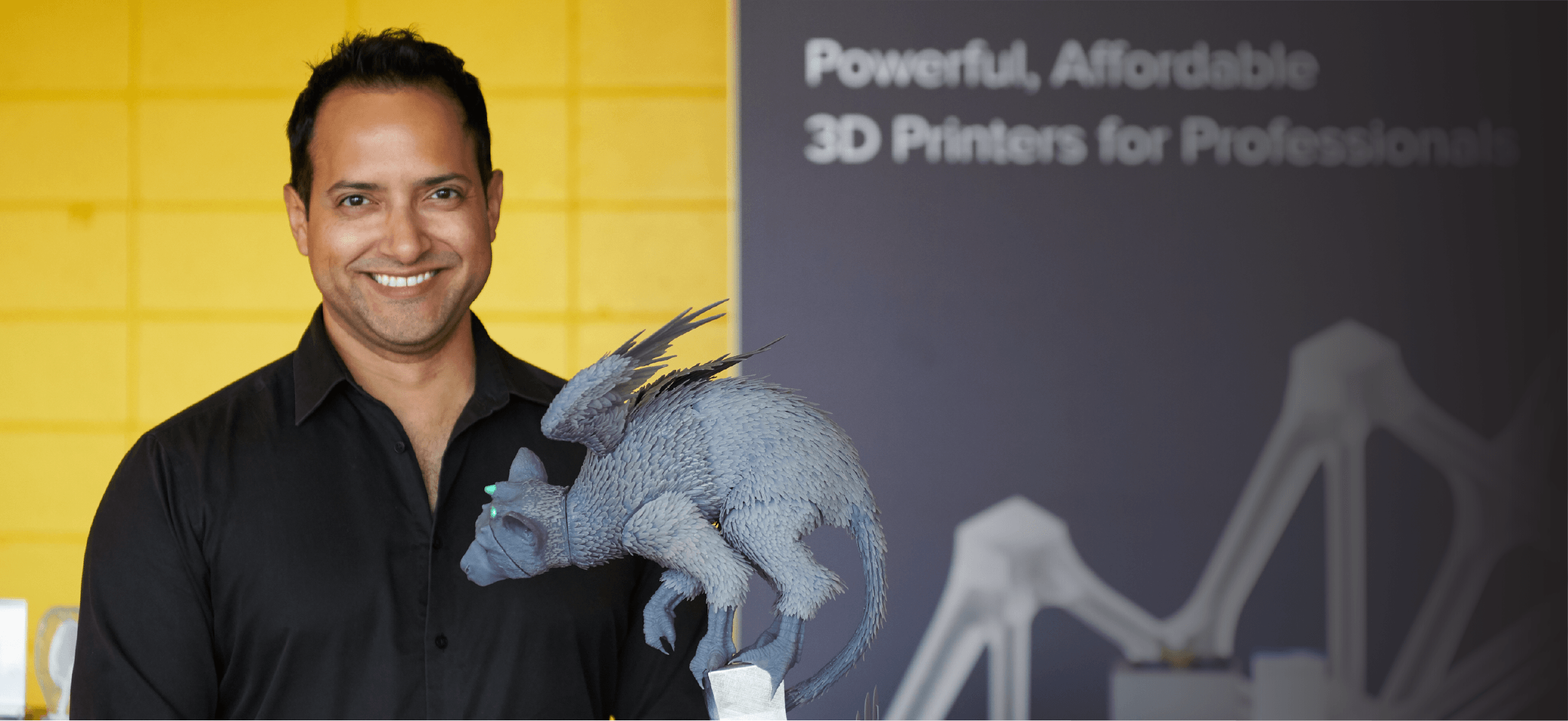
Daniel De Leon of Lion Arts showcased his intricate model of Trico from The Last Guardian at Formlabs User Summit 2019.
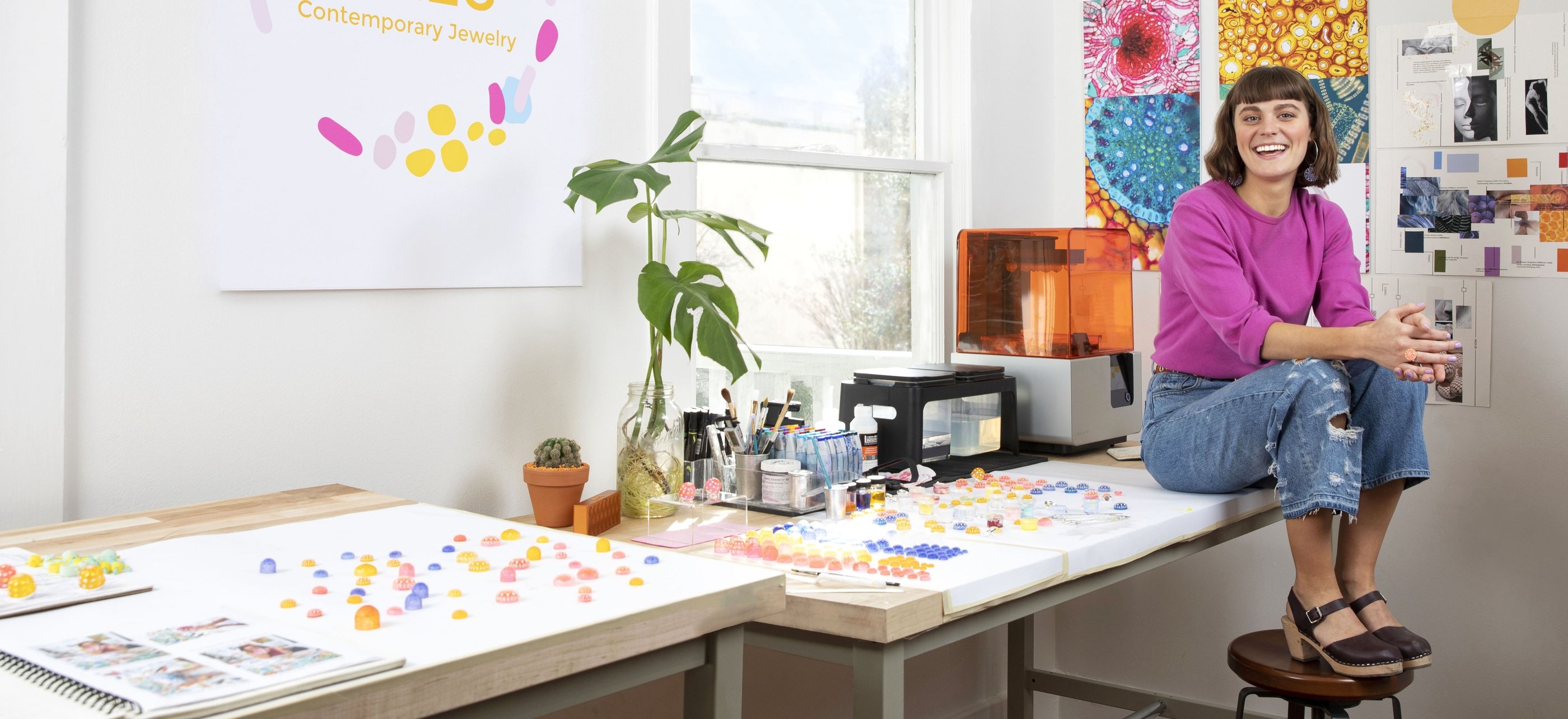
Jocelyn DeSisto at work in her NYC studio where she runs environmentally sustainable jewelry brand Lot28 Design.
Follow #formlabsambassador on Instagram
Why Become a Formlabs Ambassador?
As a Formlabs Ambassador, you'll receive unique and exclusive benefits.
Be the first
Gain first access to new Formlabs materials
Get Featured
See your work at in-person and virtual events
Earn more
Earn free materials of your choice
Get recognition
Generate awareness for your business across Formlabs' vast global online reach
Ambassador Directory
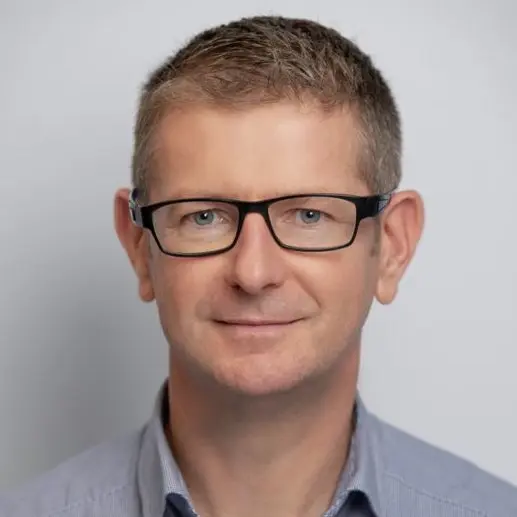
Christophe Lambrecq
Managing Director, TechShop Ateliers Leroy Merlin
Paris, FranceChristophe Lambrecq worked in the mold and tool industry for 20 years as a sales technician in the field of Electrical Discharge Machining. For the past 4 years, he has been managing the biggest Makerspace in France, Techshop Ateliers Leroy Merlin, a 600 square meter facility in the center of Paris dedicated to training and helping professionals, students, entrepreneurs with project analysis, prototyping, and manufacturing through classes, workshops and personalized help.
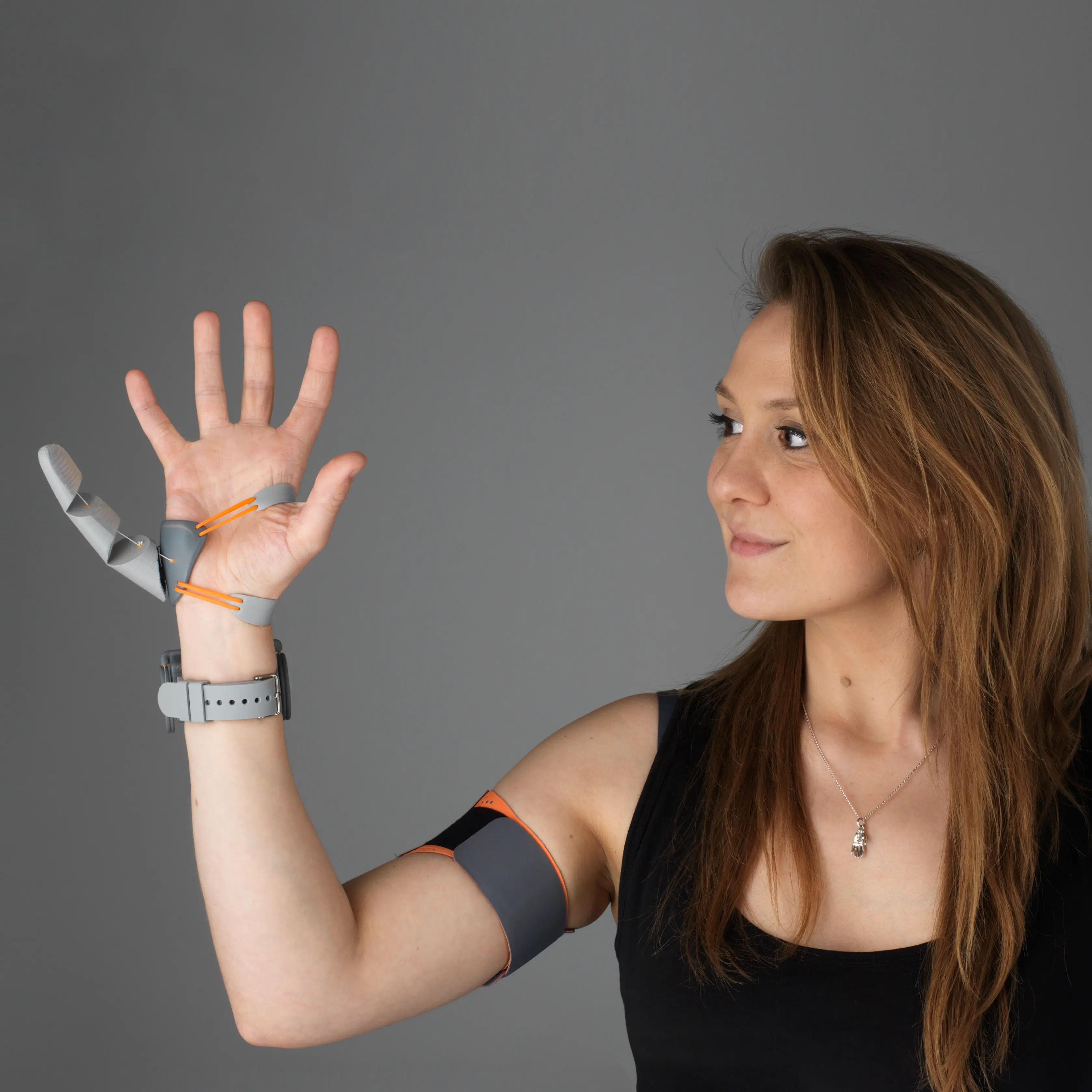
Dani Clode
Lead Designer, The Third Thumb
London, UKDani Clode is a multi-disciplinary collaborative prosthetics designer investigating the perception and future architecture of our bodies. 3D printing provides the innovative materials and complex geometry options to work with unique body shapes. Her main project “The Third Thumb” is currently being developed for neuroscience research in collaboration with The Plasticity Lab at University College London. The main focus of the study is to explore the brain’s ability to adapt to augmentation.
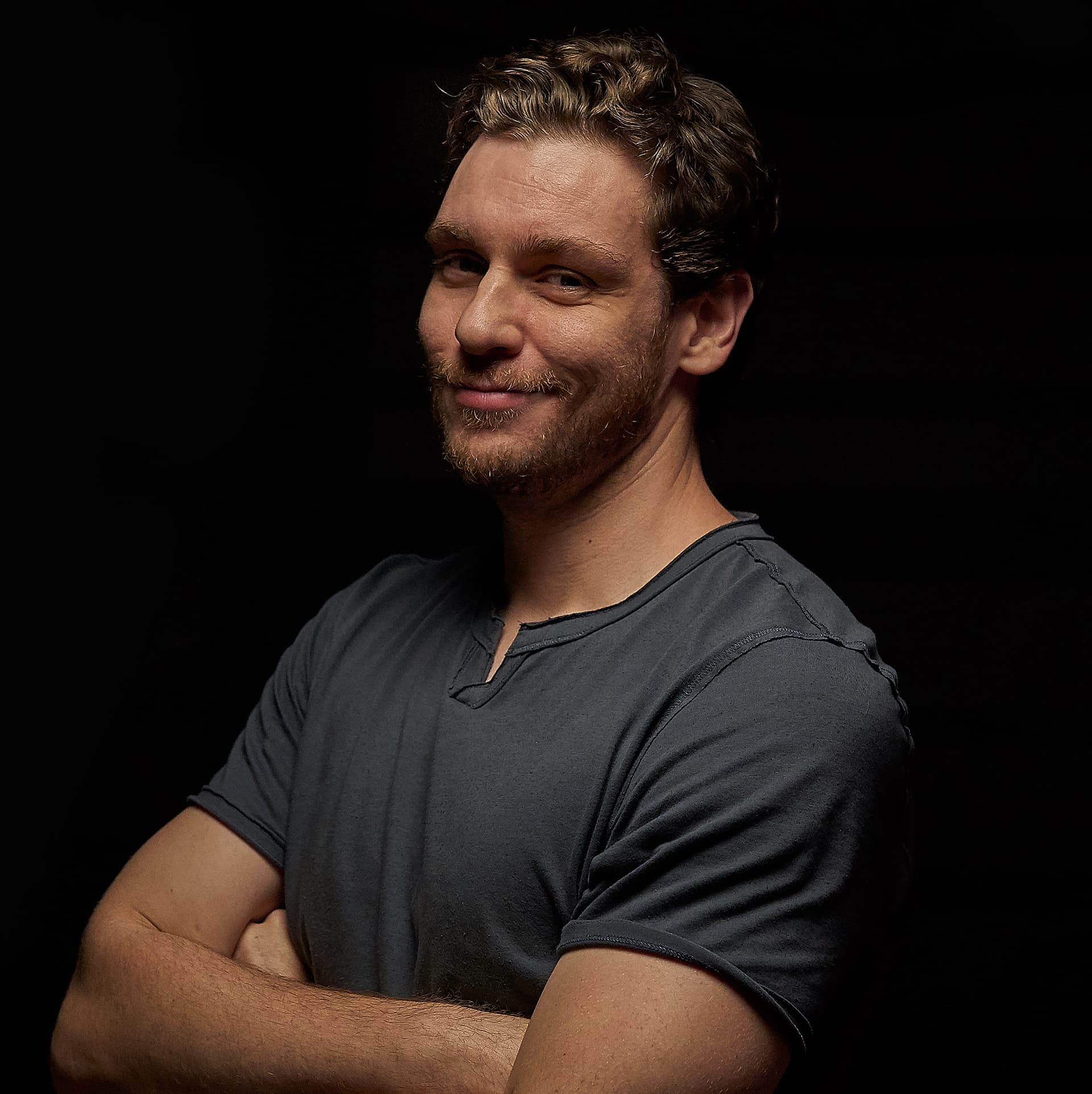
Daniel Bel
Digital Sculptor and Art Director, Sideshow Collectibles
Buenos Aires, ArgentinaI was born in 1984 in Buenos Aires, Argentina. I'm a CG Artist and Digital Sculptor and I have been working in different areas of the field for more than fifteen years. My first job connected with the 3d world was in engineering as a Mechanical Designer. Later on, I moved to Architectural Visualization as a Technical Director. This was followed by Video Games, where I worked as Lead Animator. Then I entered the Advertising and Motion Graphics business as a CG artist and Art Director. And for the last 5 years, I´ve been working as a digital sculptor for some of the best collectible companies in the world, like Sideshow Collectibles. There, I perform the role of Senior Sculptor, giving life to many DC and Marvel characters, from the comics to the statue collectible world.

Daniel De Leon
Founder, Lion arts
Los Angeles, CADaniel is a passionate multi-disciplinary artist, designer, and upcoming filmmaker with a unique background in fine arts, digital design, and clinical emergency medicine. Daniel specializes in digital sculpting and 3D printing for visual effects in film and video games. He’s worked with top-tier brands including Amazon Studios, Netflix, Jurassic World, HBO’s WestWorld, and often asked to sculpt detailed anatomy. The Form 2 has extended Daniel’s reach from the digital world to the physical, working with clients on physical prototypes, functional props, collectable models, or beautifully detailed statues for private collections.
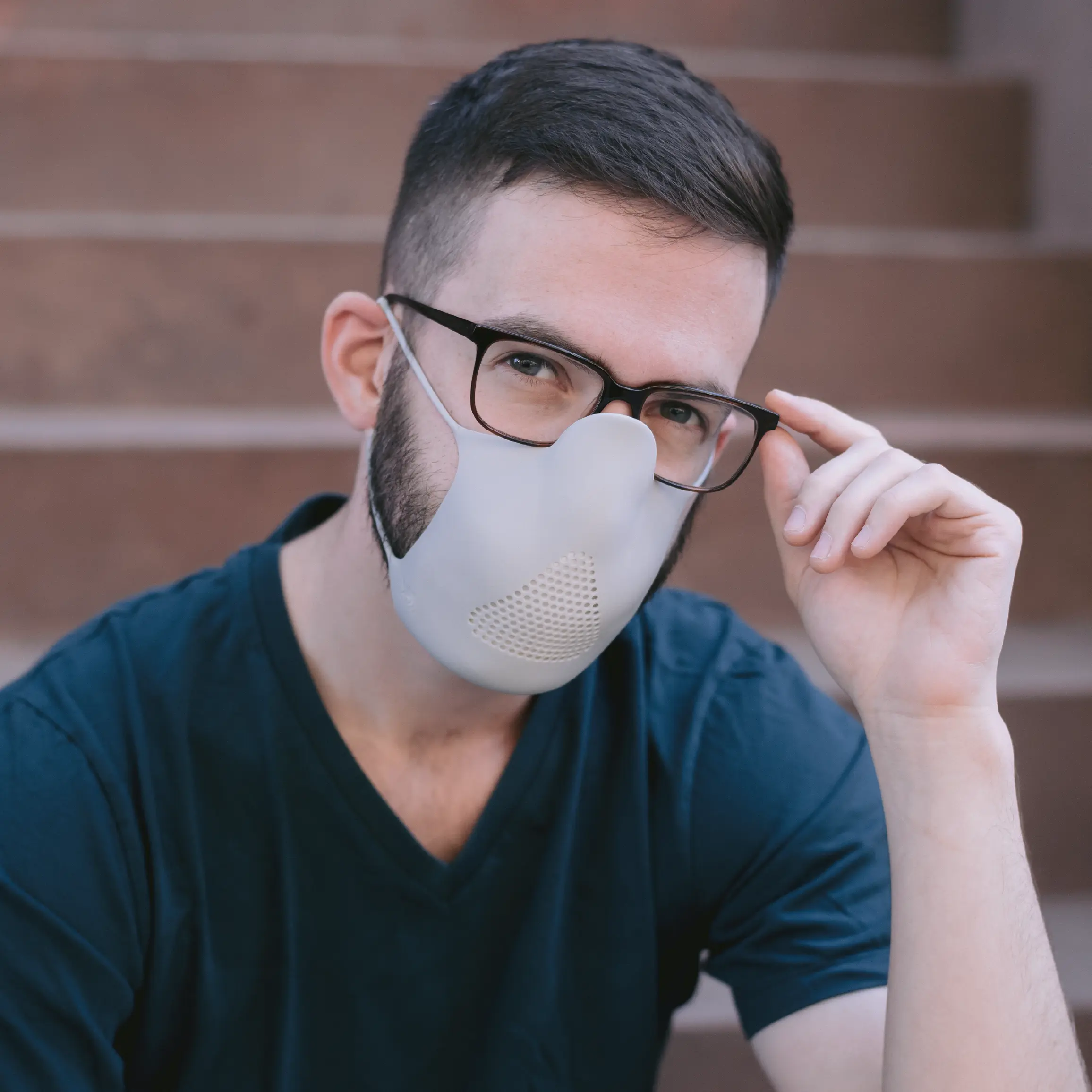
David Michael Reichmann
Owner, Rawrycat
New York, NYWedding photographer turned inventor. While developing pet products, pivoted to masks in response to the ongoing global crisis. Used the Form 3 to rapidly prototype and develop the Rawrycat Mask and bring it to market. Using 3D printing to continue to develop future products.
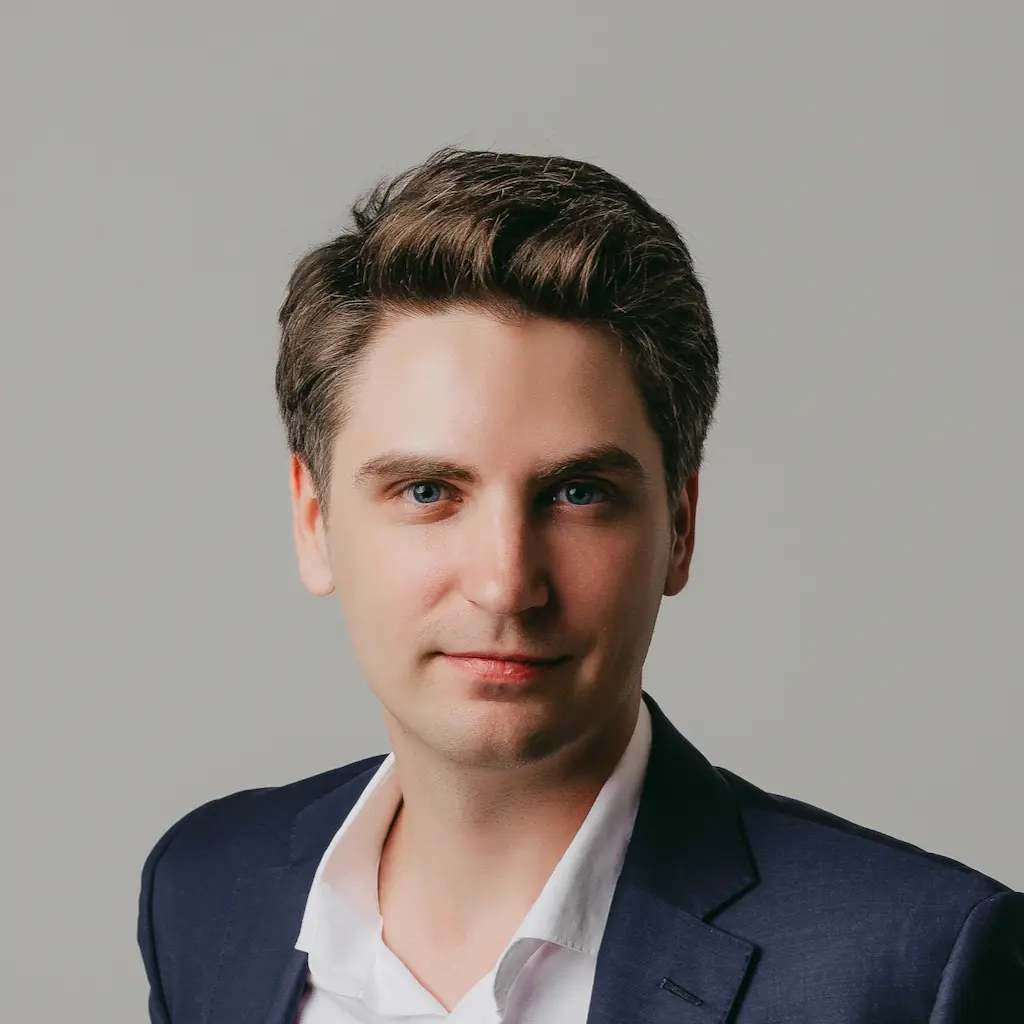
Dmitry Vasilev
Co-Founder & Development Director, Karfidov Lab LLC
Moscow, RussiaDmitry Vasilev is a co-founder and CBDO of "Karfidov Lab" LLC and "Komarik" LLC. He graduated NUST MISiS in Moscow and then received master's degree in a joint program of the Skolkovo Institute of Science and Technology and MIT. In 2014 Dmitry worked at the laboratory of advanced manufacturing technologies at the USC (University of South Carolina). His research was done under guidance of Professor Zafer Gurdal and Professor Psakhie S.G. in the field of FDM-like manufacturing process to produce composite parts with anisotropic properties. Dmitry along with his partner Alexey are among the first donors of the Skolkovo Institute of Science and Technology.
Since 2014, co-owner of the engineering company Karfidov Lab. After 7 years the company has become the market leader in industrial design and high-tech design of innovative devices and products with a turnover of more than 2 mln USD. He co-founded several spin-off companies, attracted VC round to a medical equipment project.
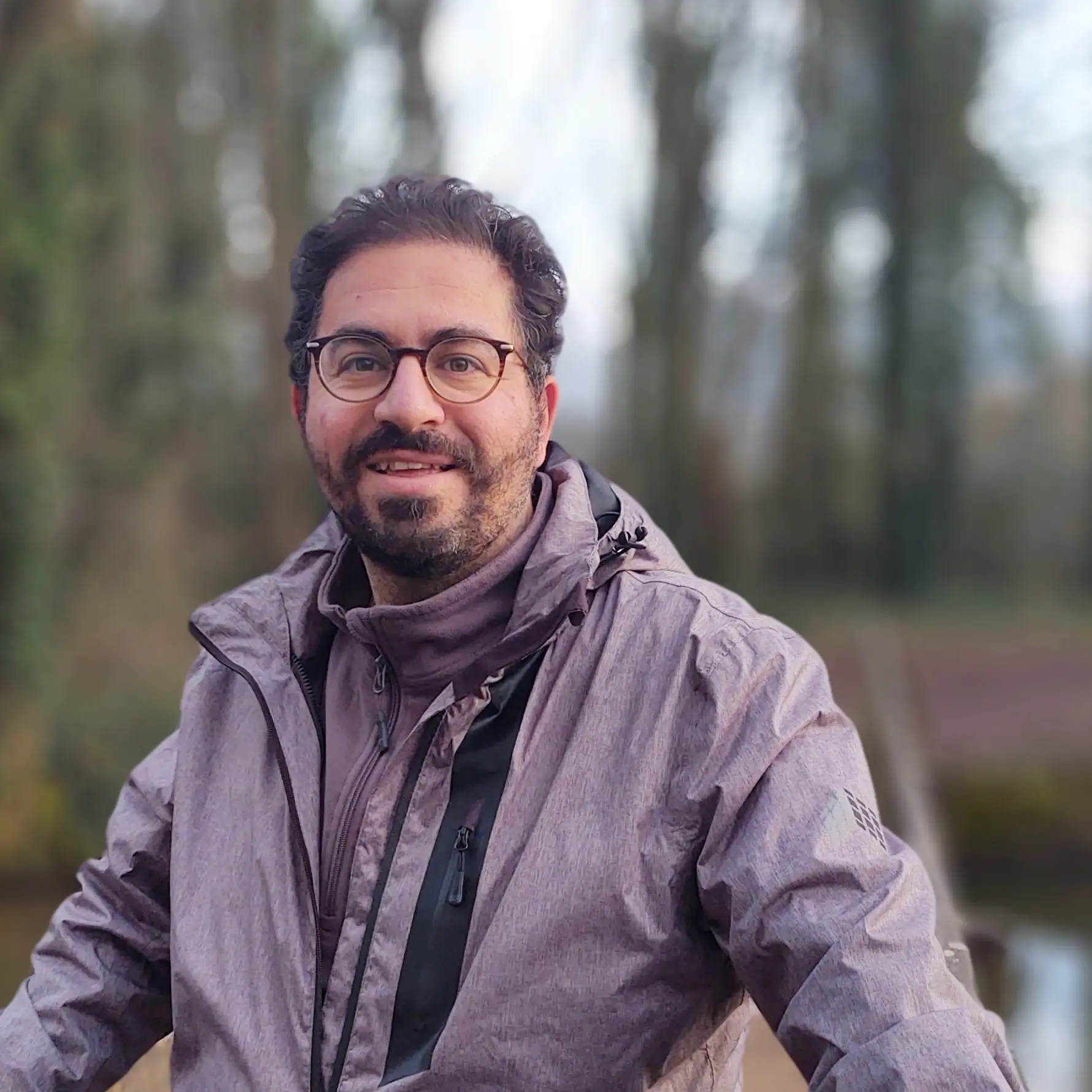
Evros Loukaides
Assistant Professor, University of Bath
Bath, UKEvros works at the interface of solid mechanics and production engineering. He is particularly interested in shape-shifting structures, mechanical metamaterials and waste-free manufacturing processes. 3D printing, despite its relatively recent introduction has strong synergies with all of the above and is often used in his lab to construct demonstrators and components for testing rigs.
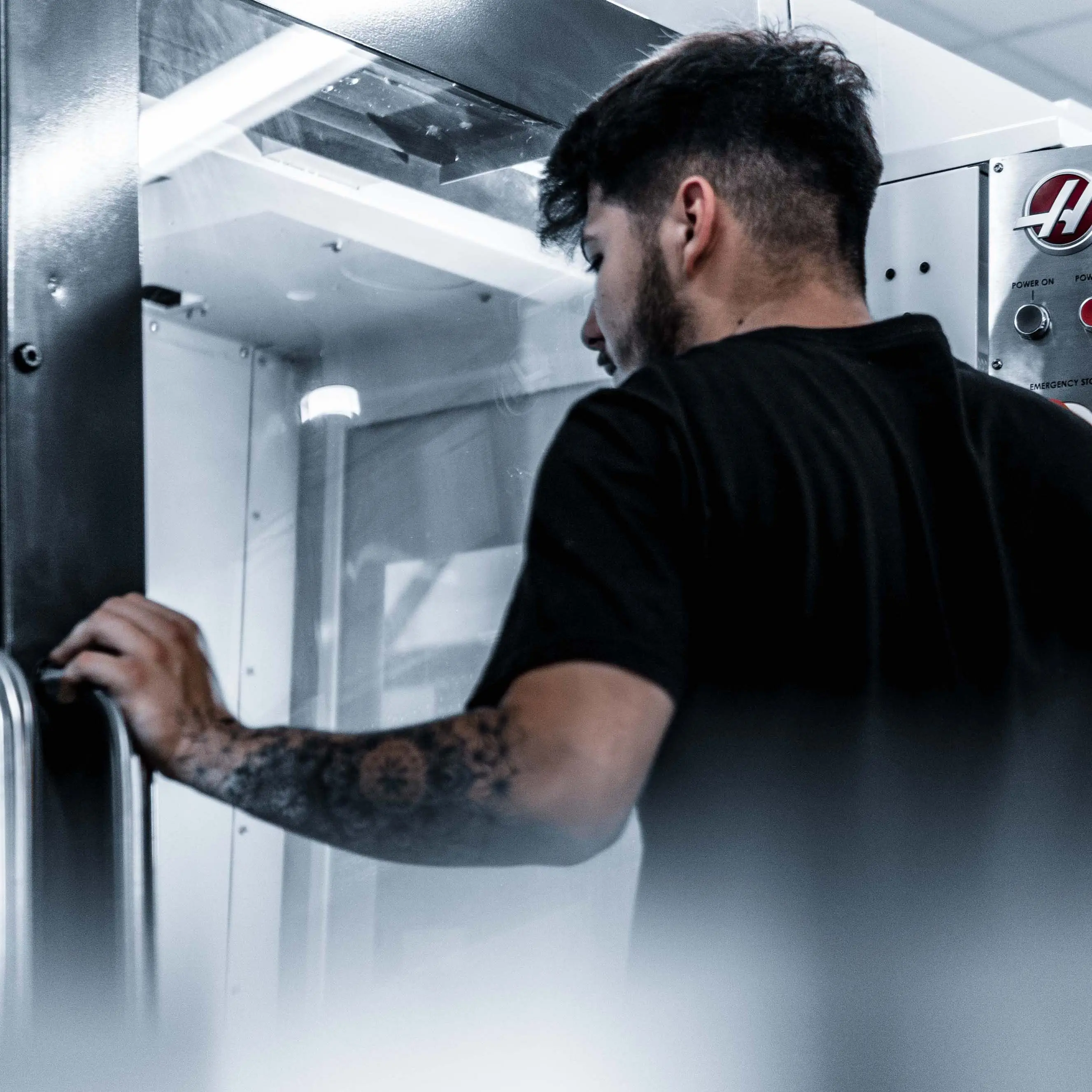
Fabien Almodovar
CEO, ACED
Aubagne, FranceFabien Almodovar , je suis le responsable de l'agence ACED. Agence de design hybride créée en 2017 Ma premier expérience avec l'impression 3D était à l'age de 16 ans par la conception d'un surf électrique en carbone dans mon garage. De la conception 3D à la fabrication composite j'ai réalisé une partie des pièces en frittage de poudre pa12 et SLA. Étant étudiant l'objectif était de diminuer le cout de fabrication avec des pièces fonctionnelles ne nécessitant pas d'outillage de fabrication 3 ans plus tard à la suite de ma licence spécialisation des matériaux composites j'ai intégré un post de responsable de projet chez un fabricant de pièces moto. A mes 21 ans j'ouvre l'agence ACED spécialisée dans la conception, prototypage et mise en production de produits innovants.
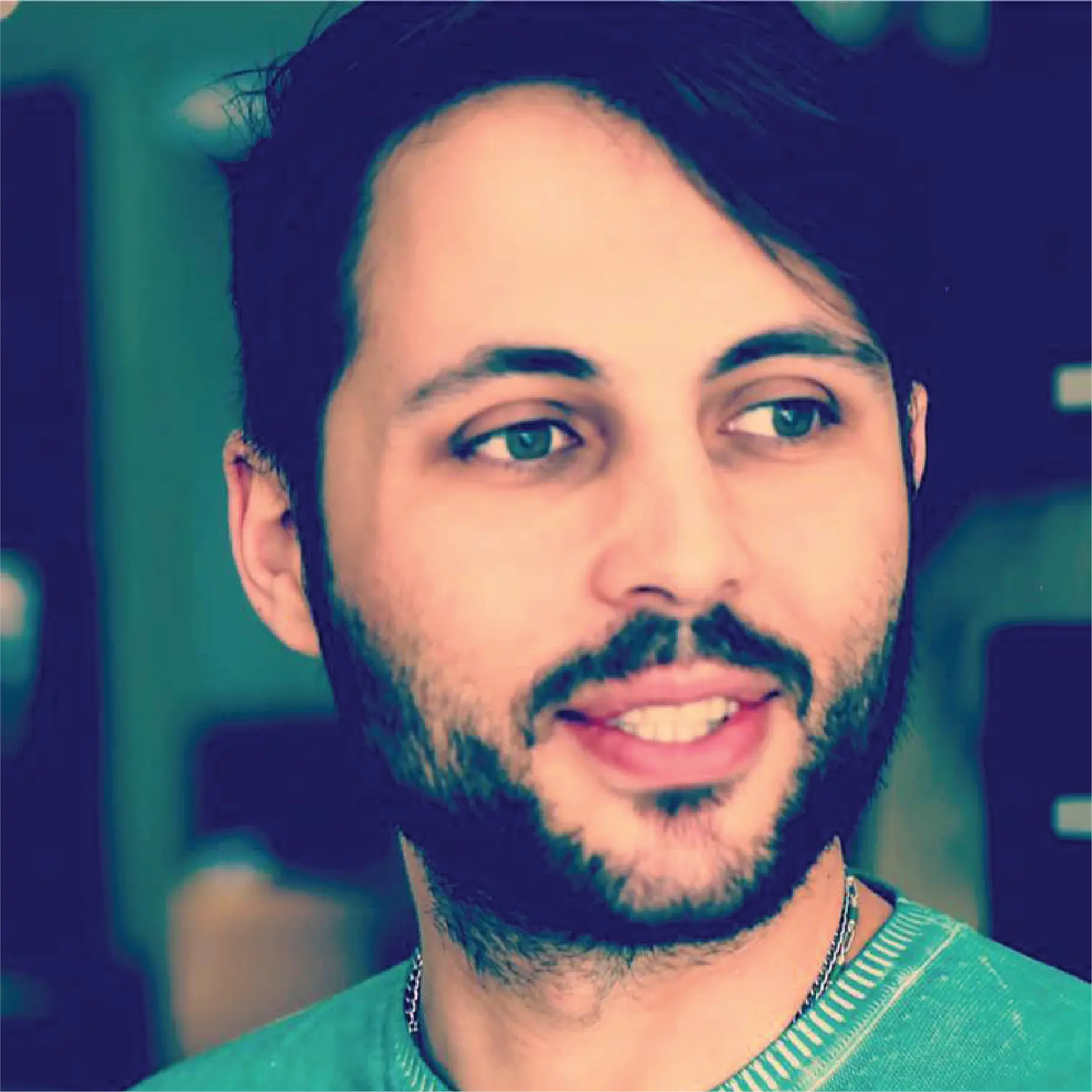
Ferdinando Petrella Deci
Co-Founder, idea3Di
Rome, ItalyFerdinando Petrella Deci is a promising Designer, with over six years of experience in the fields of Industrial Design, Marketing and Communication, Social Media, Graphic and Web Designer.He works as a consultant for leading companies, providing services and training related to digital manufacturing, Social Media, Graphic and Web Designer. He began his career in 2014 by founding idea3Di and starting a collaboration with the 3Ditaly company, leader in Italy in the field of 3D design and printing.
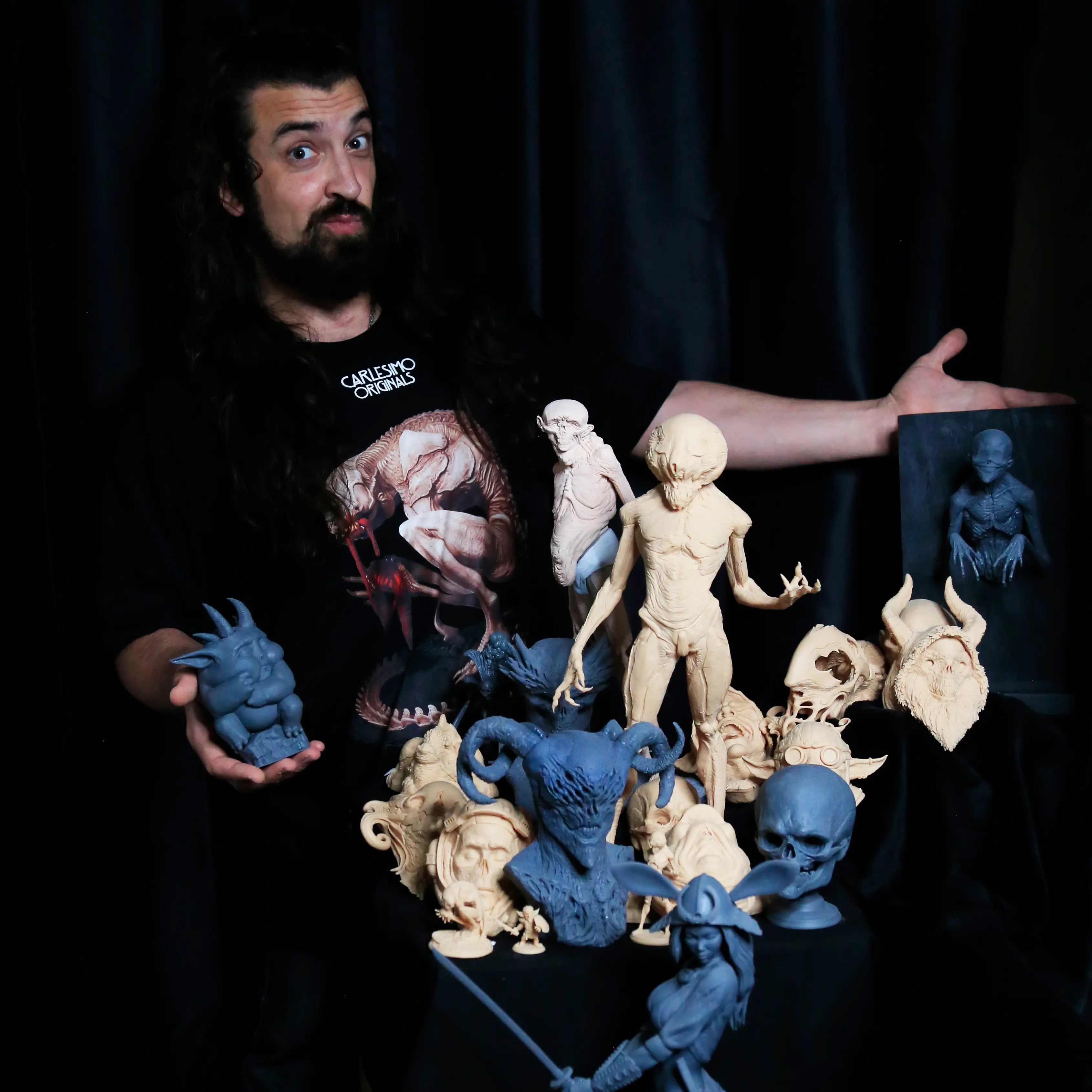
Franco Carlesimo
Digital Artist
Barcelona, SpainI been a digital artist for over 15 years, focus mostly in character modeling. I came across 3D printing from a tutorial I saw from Jeff Feligno, and from that moment on I was hooked. Now I work mostly for collectibles and all I do ends up 3D printed. I just could´t be working doing what I love without this technology.
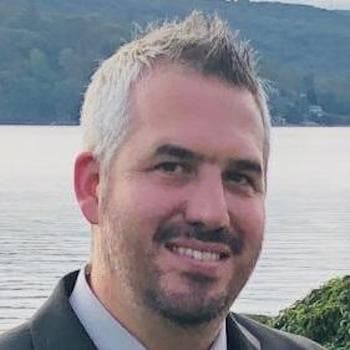
Greg Gagnon
Biomedical Engineer, Baystate Health
Springfield, MAGreg Gagnon is a Clinical Engineering and 3D Printing Specialist at Baystate Health. One of his daily responsibilities is 3D printing anatomy for patient education and pre-surgical planning. He uses these models to communicate with staff on novel surgical approaches which reduce OR times for staff and patients, improve accuracy, and increase patient confidence. Beyond replicating anatomy, Greg also helps to design and create custom surgical tools and guides for intraoperative use with members of Baystate’s surgical team. Depending on the project, Greg chooses from among Formlabs’ large library of resins and the Form 2 is his go-to printer.
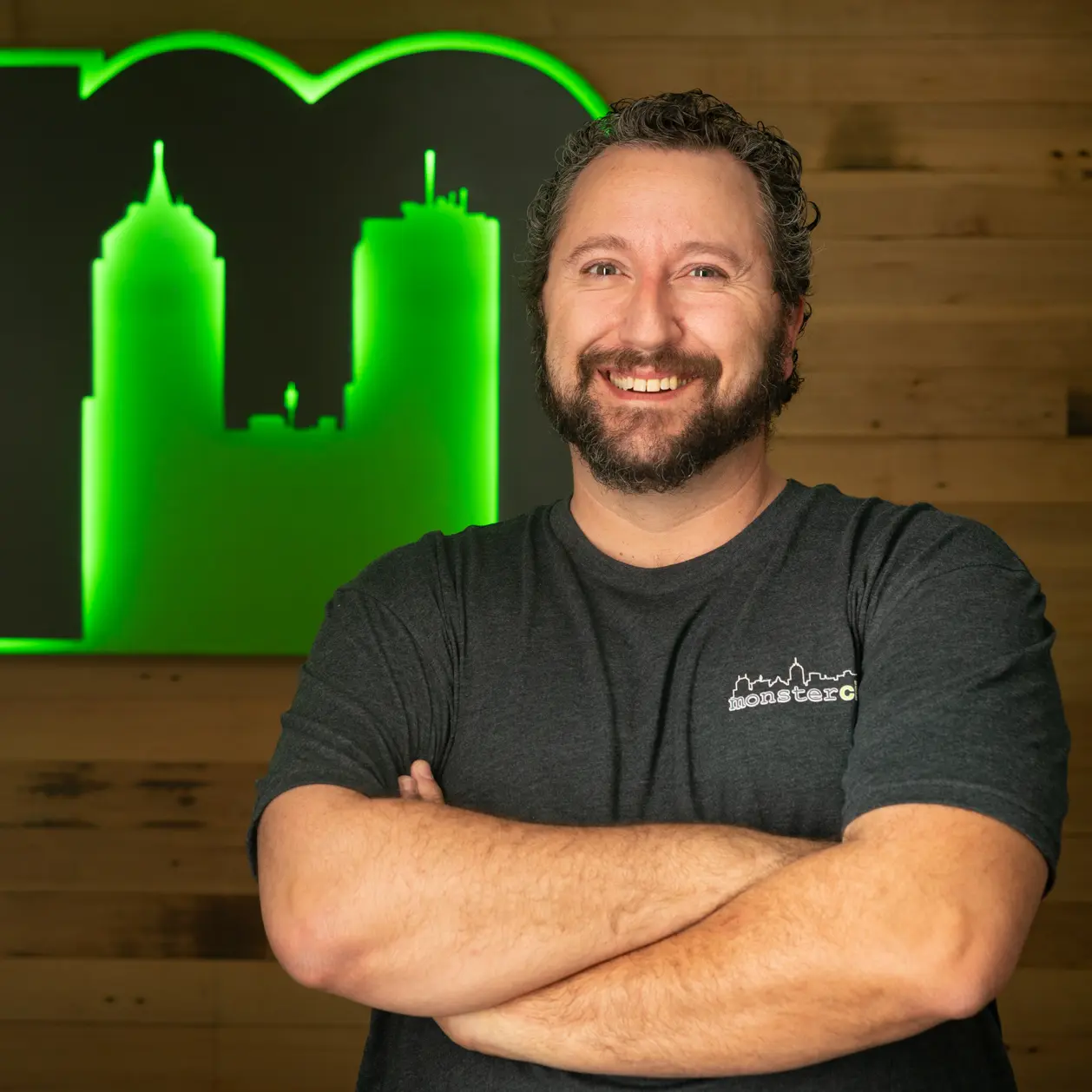
James Powell
Founder, Monster City Studios
Fresno, CAIf creativity could be bottled and sold, James would make a fortune. He has oodles of the stuff. As a child prodigy, James began building models, but they weren’t any ordinary models like most of us have built – from a kit – passing out from the smell of glue. Having done projects for companies such as Disney, Paramount Pictures, the Cartoon Network, Sony and others, as well as projects for notable celebrities and high profile clients, James has been able to apply years of industry experience to helping Monster City develop memorable, award-winning creations. We’re still searching for ways to bottle all that creativity.