Fly, Fix, Fly: Solving Tactical Dehydration for Fighter Pilots With SLS 3D Printing
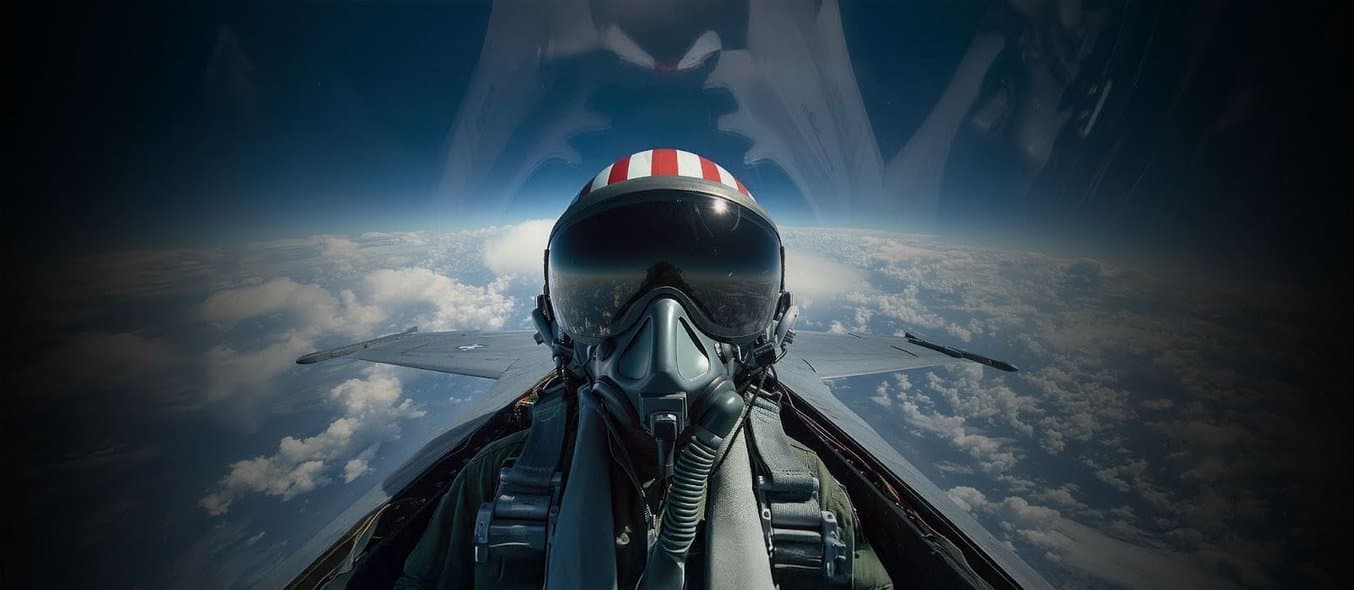
Tactical dehydration in fighter pilots goes beyond discomfort — it can be the critical factor between maintaining consciousness during high G-force maneuvers or blacking out, risking mission failure and potentially fatal consequences. But for many fighter pilots, especially females, the difficulty and inconvenience of relieving themselves during a flight deters them from hydrating at all. “We have lost pilots and aircraft multiple times to G lock,” says Jennifer West, PhD(c), Medical Advisor for Airion and former Air Force Captain.
AFWERX, the innovation arm of the Air Force and Air Force Research Laboratory, issued a challenge in 2021 for innovators across the country to devise a solution for tactical dehydration and bladder relief in female fighter pilots. AIRION, a Los Angeles-based start-up answered the challenge, along with very familiar, established names in the defense contracting industry. One year later, after bids had been submitted and initial prototypes built, it was the innovative start-up that won the award over the multi-billion dollar competition.
“We beat out huge names in defense contracting to win the AFWERX challenge, and we were able to deliver a better solution, the Advanced Inflight Relief Universal System (AIRUS), because of our ‘fly, fix, fly’ approach to design and testing. That approach was only possible because of our SLS 3D printers.”
Colt Seman, AIRION co-founder and CEO
Sky-High Requirements
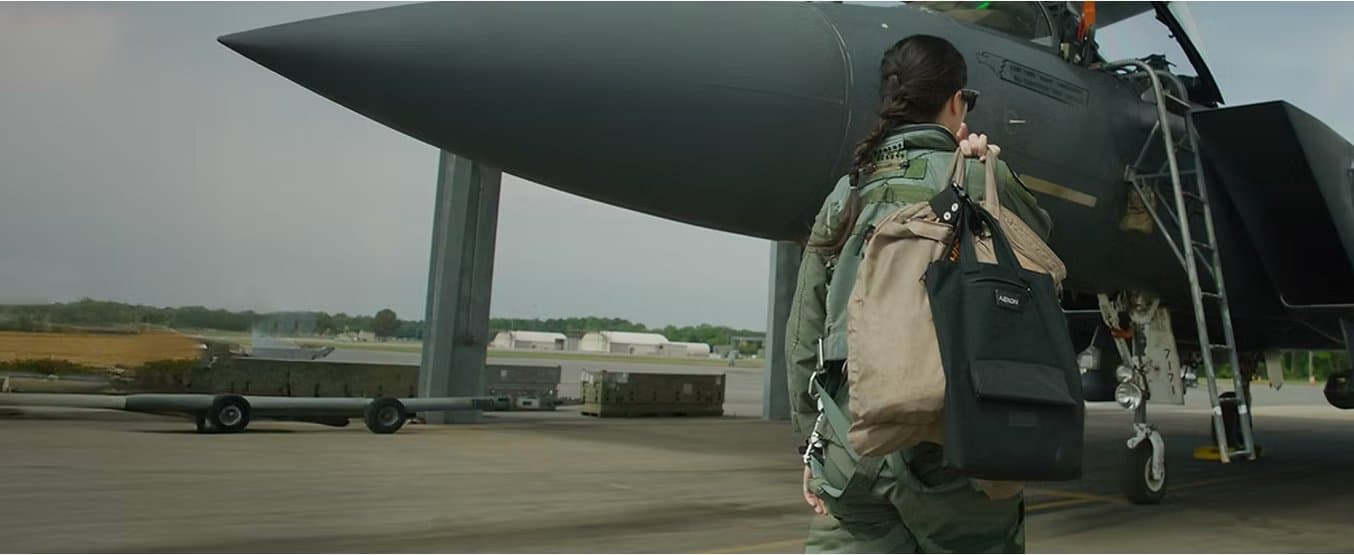
The AIRION team worked with several active and retired pilots in the Air Force to understand the demands of their job and what they needed from a bladder relief device, often testing and iterating in one day.
The team at AIRION, including Chief Engineer Justin Jacob and Jennifer West, didn’t see anything on the market they could build off of, and because of their blank-slate opportunity, they knew they needed a special design workflow to make it happen.
“We really wanted to be nimble and able to adapt as we saw the needs come from the pilots, who are the real key customer here. We need the device to perform in extreme conditions, and we needed to have a reliable ecosystem that could get us working parts quickly for us to turn around and test,” says Jacob.
Collaborating directly with active duty Air Force pilots was essential to the project’s success. The team continuously refined designs based on feedback from the pilots who urgently needed a better solution. “For nearly three decades, our female aviators have had to rely on uncomfortable and potentially risky options just to relieve themselves,” says West.
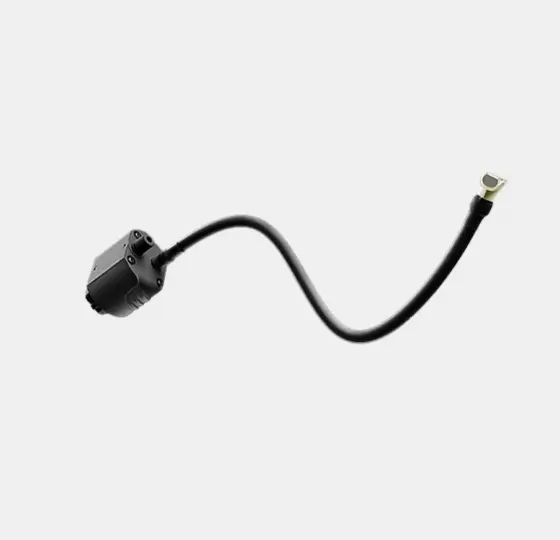
AIRUS Pump
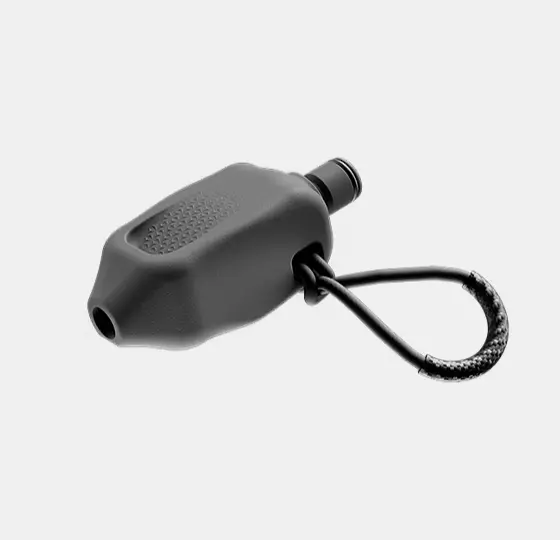
AIRUS Cleaning Connector
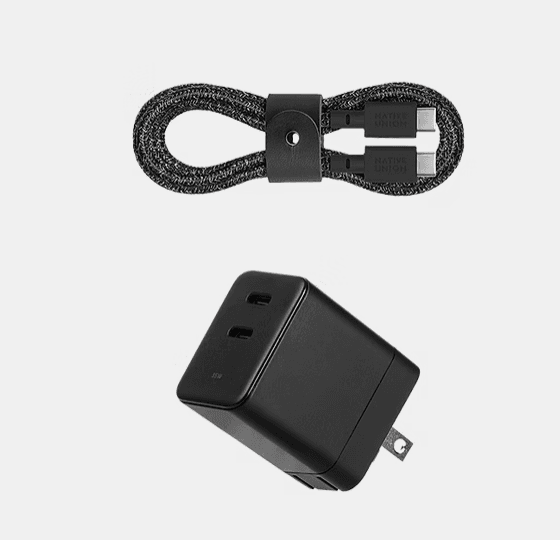
AIRUS USB-C Charging System
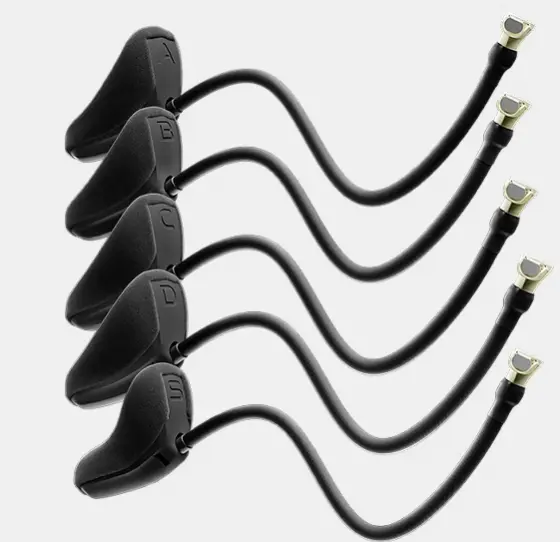
AIRUS Sizing Kit A, B, C, D, S Cups
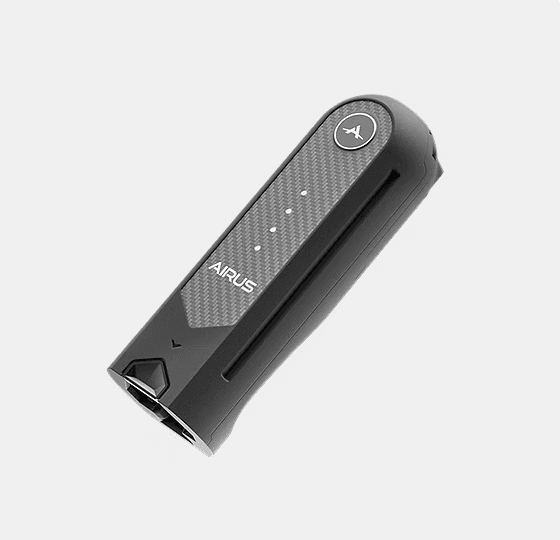
AIRUS Controller
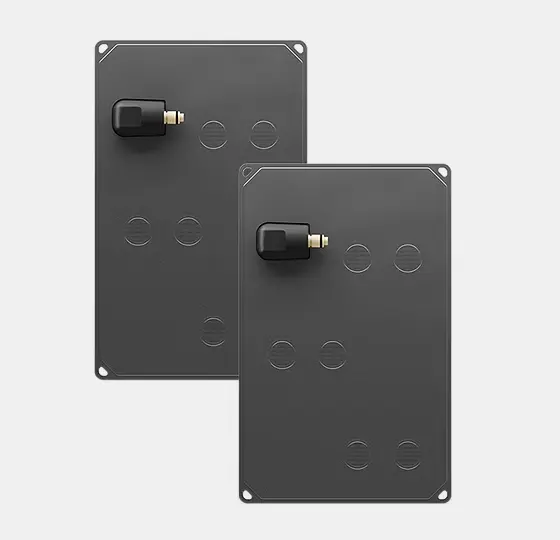
AIRUS Collection Bags
Additionally, the design had to change based on which aircraft the pilots were flying, resulting in more iterations and feedback. “As we transitioned between aircraft, we realized how different the needs and requirements are — flying an A-10 versus an F-35 involves distinct harness configurations,” says West.
All these iterations meant that 3D printing was the only fabrication method that could deliver functional parts for same-day iterative testing, but choosing a 3D printing system to bring in-house was a big step.
Minimizing Risk With Accessible SLS
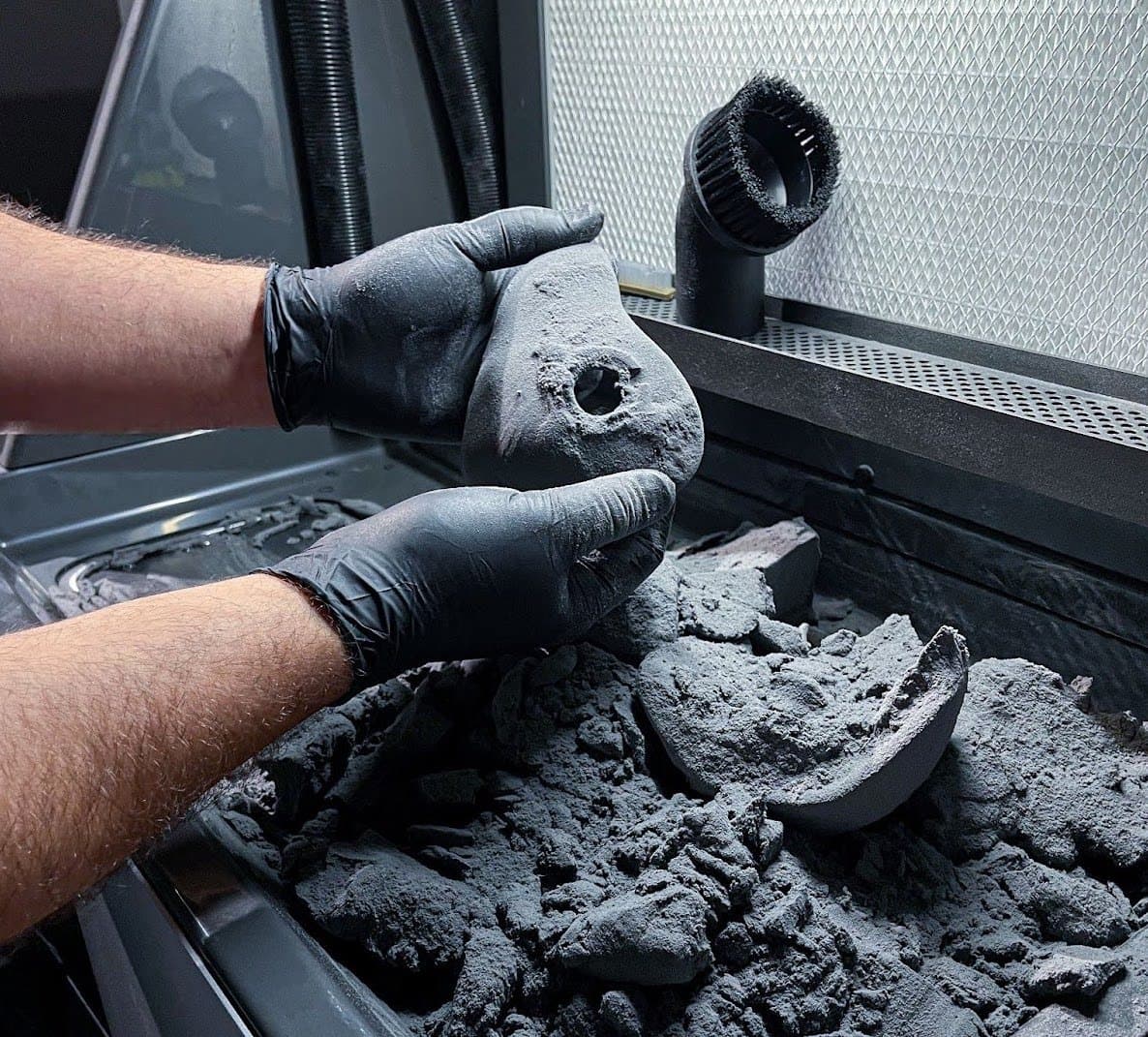
The Fuse Series Ecosystem, including the Fuse Sift (above) and Fuse Blast, make it possible to print full production volumes overnight, and half builds during the day.
The design and engineering team knew they had to move quickly in order to deliver a working product faster than the established competitors who were also submitting ideas for the AFWERX funding.
“We had initially tested some MJF parts and some other SLS printed parts from some third-party providers, and they seemed pretty good, but these are way too expensive and took too long to continually iterate with by outsourcing. We realized we needed to bring the machine in-house. It's gonna let us move just at light speed in comparison,” says Jacob.
The task at hand was inherently a pretty risky business endeavor — spending a year designing a part to potentially not receive a contract at the end of it. AIRION had to look and see where they could minimize their risk. For them, that came from choosing a scalable, accessible fabrication method that could take them all the way from prototyping to production.
“We wanted to de-risk as much as possible. From the beginning, that was the Formlabs Fuse. Then, once we got in with Formlabs, producing at volume and working with services, I am so happy we did go this way, because they were always so willing to work with us on material validation, or wall thickness testing, or cost calculations.”
Justin Jacob, Chief Engineer, AIRION
One Workflow: From Concept to Production
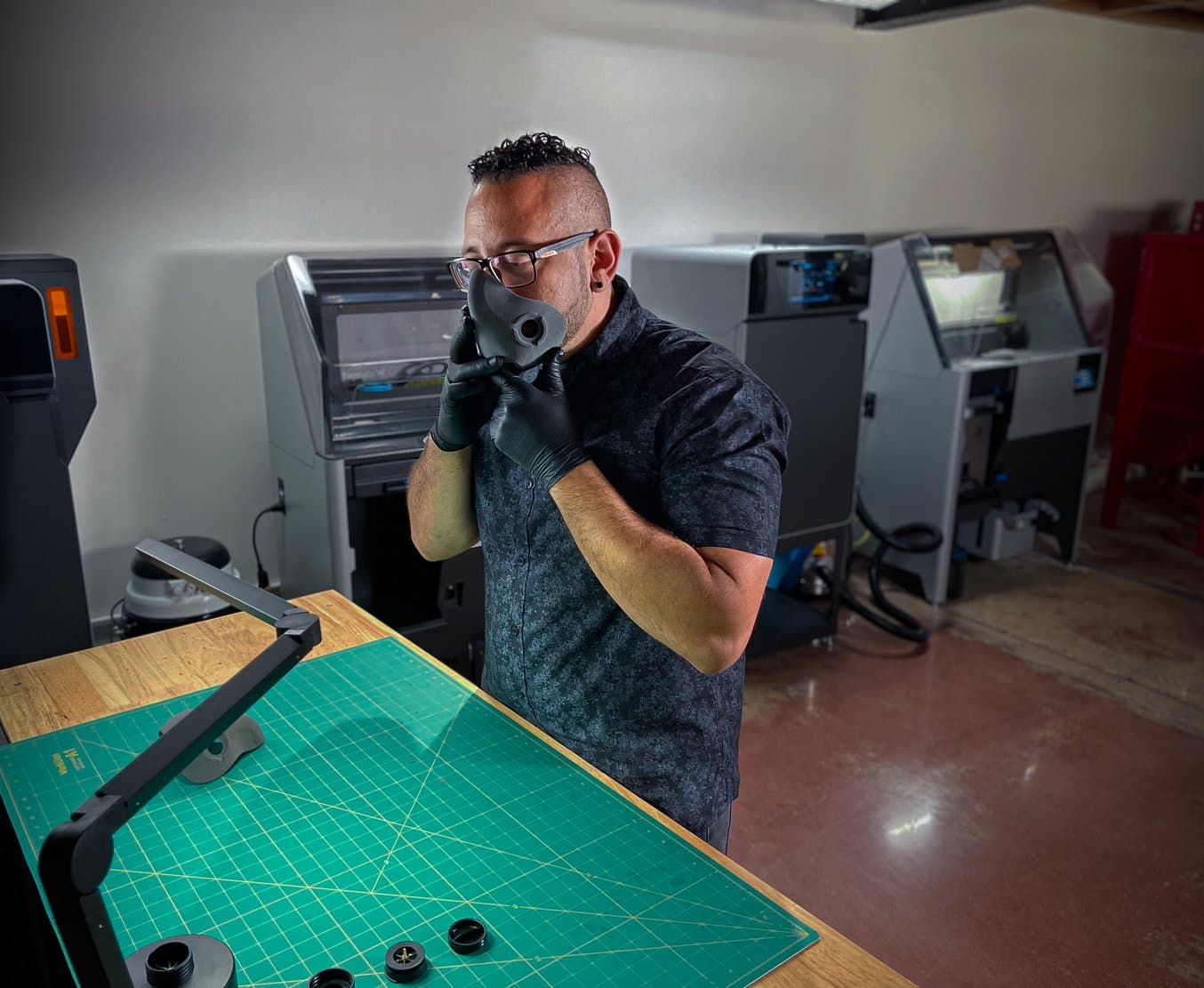
AIRION Chief Engineer Justin Jacob tries on a new prototype for an oxygen mask component. The skin-safe properties of TPU 90A Powder enable truly functional prototyping in the same material as the end product.
The timeline of the AFWERX challenge condensed and reconfigured the traditional product development timeline. The AIRION team had to know their end-use production method before they got chosen as the award recipient, so there could be no last-minute change during the iterative process. They had to lock in from the beginning. “Once you get that material approved, it's almost impossible to change when you switch to production — you can’t just say you’re going to use a different material,” says Jacob. The only solution that could make end-use parts and iteratively test at warp speed was the Fuse Series.
To add another complication, AIRION also needed biocompatibility — which is not always easy with 3D printing materials. “I come from a background of 3D printing and testing various resins, filaments, other methodologies, and we tried a lot of different materials for the main cup of the AIRUS device, and they didn’t hold up. The SLS 3D printed TPU that we get from Formlabs has been by far the best quality part we’ve been able to produce,” says Jacob. The cup itself is entirely 3D printed in TPU 90A Powder, which has been ISO-certified as non-toxic and skin-safe.
The team printed the cups in TPU 90A Powder so they would be comfortable and skin-safe, and other integration and pump features in Nylon 12 Powder to optimize for the best dimensional accuracy, repeatability, and lowest cost per part. “The Nylon 12 Powder has been critical because not only does it hold dimensional tolerances and accuracy, when we fasten parts together, we’re creating effective seals throughout. The Nylon 12 drive system is bearing the load of the whole thing, and it works fantastic, really, without a hiccup,” says Jacob.
Both materials need to be quite durable — these devices are going through a rugged lifecycle. From packaging and repackaging to installation, disassembly, and reinstallation, not to mention the extreme environment of a fighter jet while the device is in use, the AIRUS device has to withstand impact and stressors of all kinds. AIRION conducted every possible test to ensure these devices were up to the challenge.
“The Nylon 12 and the TPU had to go through mill standard testing, shock, vibration, extreme temperature, EMI, pressure testing, and more. The device passed all of those with flying colors.”
Justin Jacob, Chief Engineer, AIRION
Moving Into SLS Production For AIRUS
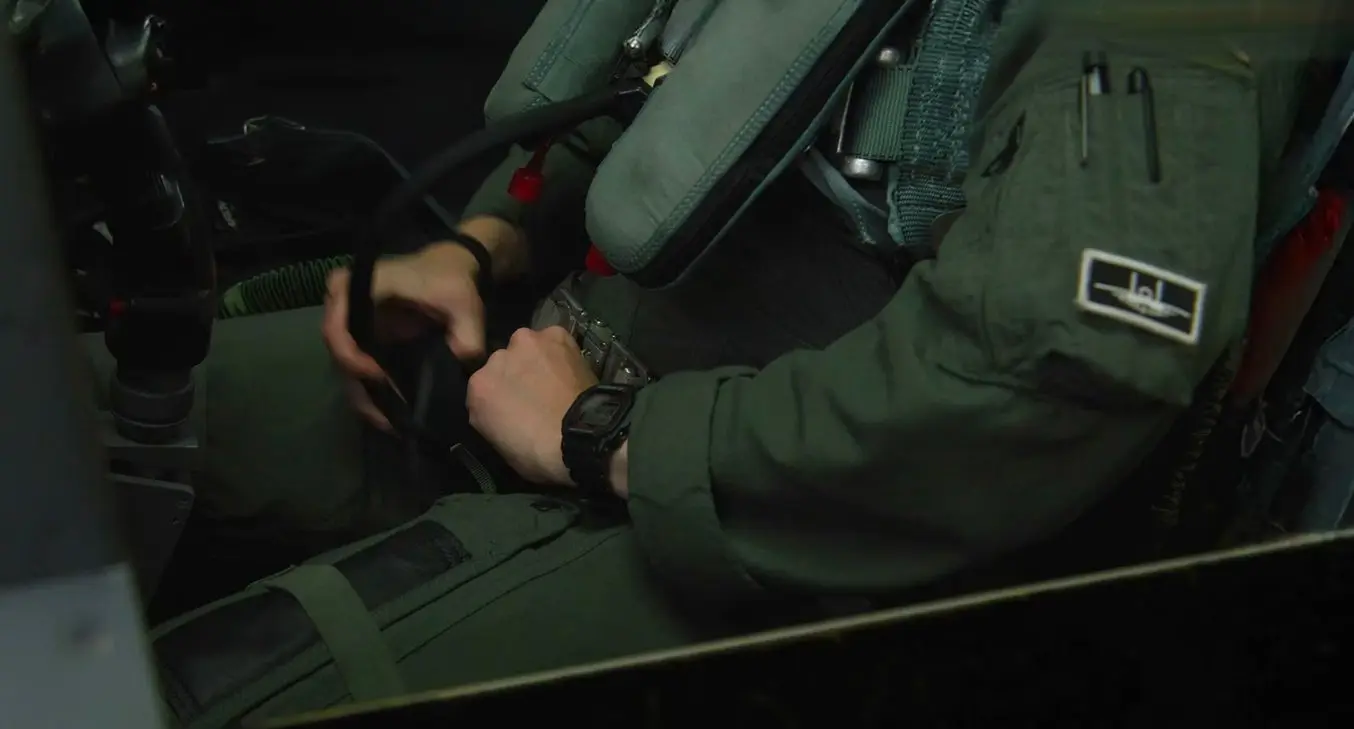
The positive impact of the AIRUS for fighter pilots cannot be overstated; it’s what keeps the AIRION team working hard on solving common problems through their innovative approach to design, testing, and manufacturing.
There are currently five sizes available of the AIRUS device, with more designs on their way, including a system for male pilots. To ramp up production to meet demand, AIRON scaled up with three more Fuse 1+ 30W SLS printers, the Fuse Sift, and the Fuse Blast. “In the Air Force, for redundancy, they always want ‘N+1,’ so there’s always a back-up. So with scaling a production fleet, you can buy Fuses as needed, instead of one massive $500K printer at a time,” says Jacob.
Over time, with different sizes and now the production of male-designed devices as well, the team has had to create a 24-hour production schedule with both Nylon 12 Powder and TPU 90A Powder. “You can print full days and half days, and set it up so I have a batch to post-process when I wake up and at the end of the day, and test in between. These printers are workhorses for us,” says Jacob.
Bringing SLS in-house has enabled AIRION to not only win the AFWERX challenge, but to go from a fledgling start-up to a busy government contractor with a plan to produce thousands of crucial pieces of equipment for the US Armed Forces. Even with all the success, they haven’t forgotten the daily impact their innovation has on their customer — the fighter pilot.
To learn more about AIRUS and AIRION’s innovations, visit their website. To test a Nylon 12 Powder or TPU 90A Powder for yourself, request a free 3D printed sample.