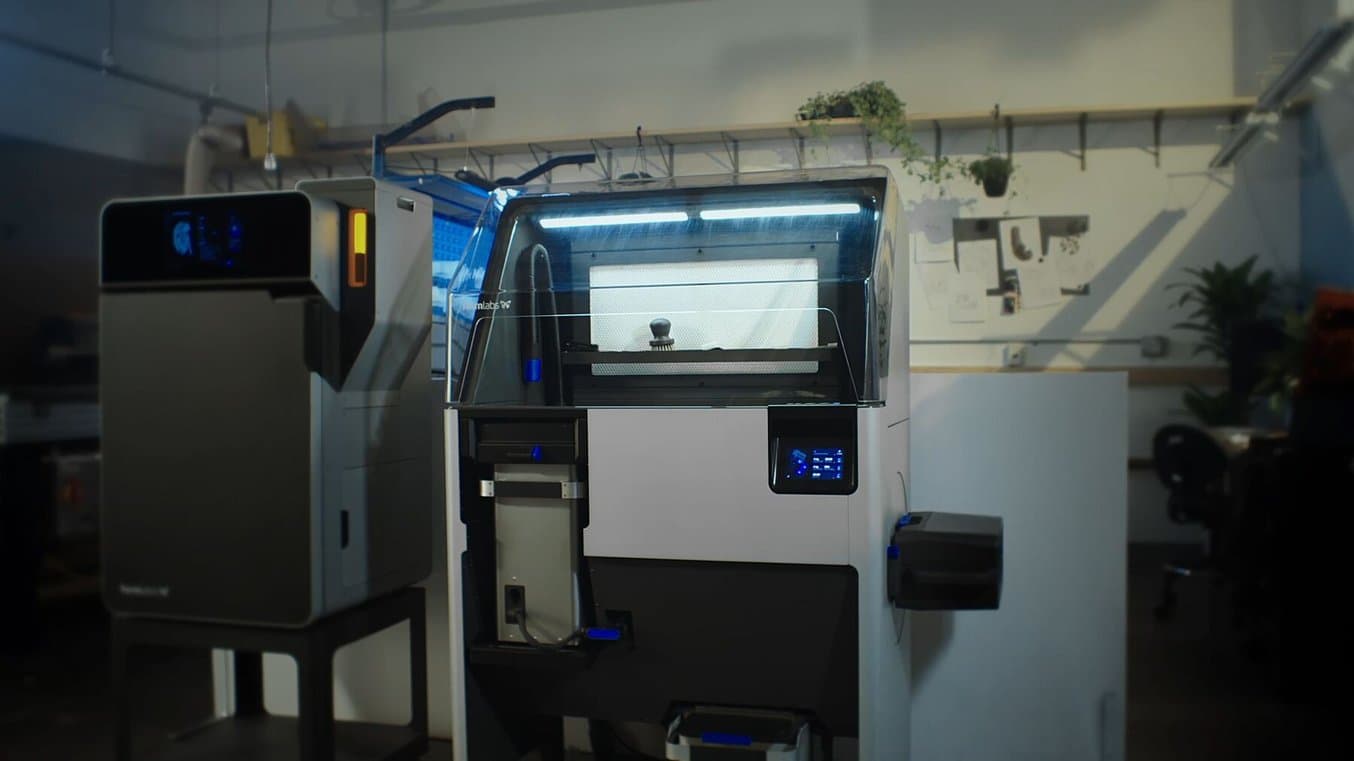
The Fuse 1 is now the best selling selective laser sintering (SLS) solution on the market, but it was a long road to mass production. Creating the Fuse Sift, the post-processing and powder recycling machine that streamlines the SLS workflow, was a new challenge for the Formlabs engineering team, and it required unique approaches and solutions to succeed.
One particular challenge arose when designing parts for the powder containment system on the final stage prototypes of the Fuse Sift. The powder containment subsystems needed to dissipate the static electricity generated by fast moving powder particles, but couldn’t be prohibitively expensive or slow to make.
Learn how the development team was able to quickly and inexpensively prototype Fuse Sift parts using an ESD-safe resin, allowing the team to ship prototype units to beta testers.
Developing a Complete SLS Workflow
In 2019 Formlabs had a powerful SLS printer prototype, but without a high quality post-processing system to go with it, the printer wasn’t truly an industrial solution. Most SLS customers print end-use parts in professional and manufacturing environments, so containing the small powder particles is of utmost importance in maintaining a safe and clean workspace.
To address this concern, the Fuse 1 team started working on the Fuse Sift, a powder reclamation and recycling station that processed parts out of the Fuse 1 printer. The goal of the Fuse Sift was to create an end-to-end solution and streamline the workflow for SLS printing. In 2019 both the Fuse 1 and Fuse Sift prototypes were almost ready for external beta testing, but powder control on the Fuse Sift prototype wasn’t ready for launch.
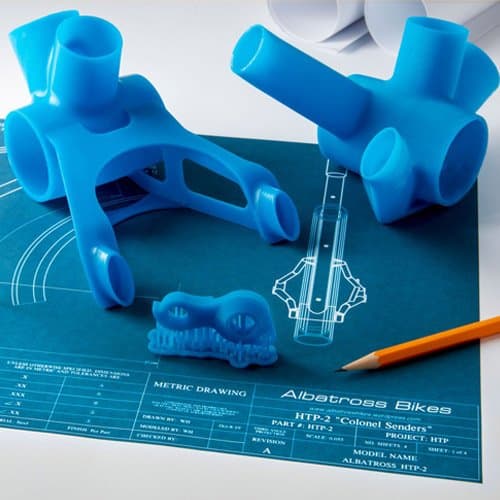
How to Find Success With 3D Printed Rapid Prototyping
This e-book covers six real-world case studies of companies driving innovation and improvement over
traditional processes with 3D printing.
Upon print completion, the user removes the build chamber from the Fuse 1 printer and inserts it into the Fuse Sift where the finished parts can be separated from the unsintered powder cake. Air is pulled through a HEPA filter at the back of the hooded work surface to maintain negative pressure in the working area and reduce the risk of powder escaping the machine. The unsintered powder cake from the build chamber is sifted and stored in a hopper where it can be dispensed along with the appropriate ratio of fresh powder to refill powder cartridges for printing.
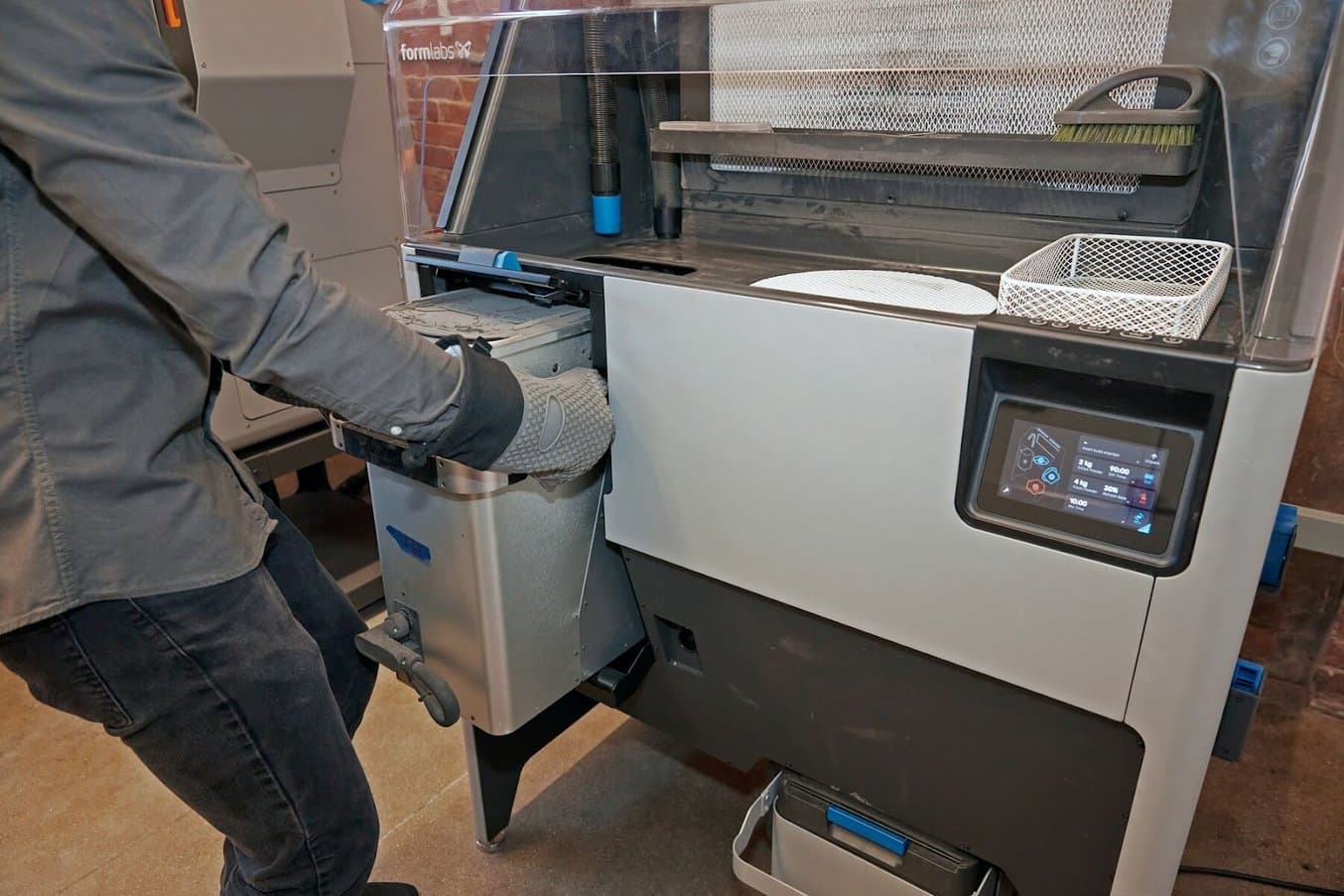
Powder Control and Monitoring Issues
“We had focused a lot on the HEPA filter that successfully pulled powder back from the hood. But there was still this layer of powder on the floor and we were trying to figure out where it came from. I took a couple videos, and as you’re dosing, you can see this avalanche of microscopic nylon powder pluming up out of the cartridge, and after a week your Fuse Sift, cartridges and floor are all covered in powder,” says Larry Cheung, the mechanical engineering lead on the Fuse Sift team.
The team evaluated a couple options, like a hood or a skirt that enclosed both the dosing system and the new cartridge. But because the cartridge needs to be continuously weighed while dosing to ensure the optimal mix of fresh and used powder, anything that touched the cartridge would affect the weighing system and wouldn’t work.
“We thought, since we already have a vacuum, why don’t we just use it to keep things clean. So we started testing a prototype with a wye splitter connecting tubes from both the work surface and dosing port to the vacuum. Just to understand if it worked, we printed it in Draft Resin and wrapped it in copper tape,” says Cheung.
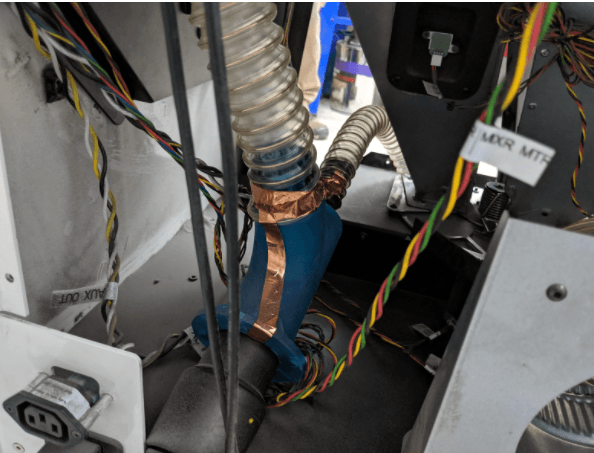
First wye splitter prototype in Draft Resin with Copper Tape
The copper tape, though a temporary solution, provided the important function of dissipating any static charge caused by the nylon powder moving through the tube. Effectively dissipating this charge is important to prevent electrostatic discharges that could pose a risk to the electronics in Fuse Sift as well as being a potential ignition source for the combustible nylon powder in the system.
Larry Cheung
“If non-static dissipative components are used, you can often feel and even see ESD shocks when you’re quickly running a ton of powder through the system. So, ESD is a real problem. All of our subsystems are grounded, and we can’t allow electrostatic discharge to run through them."
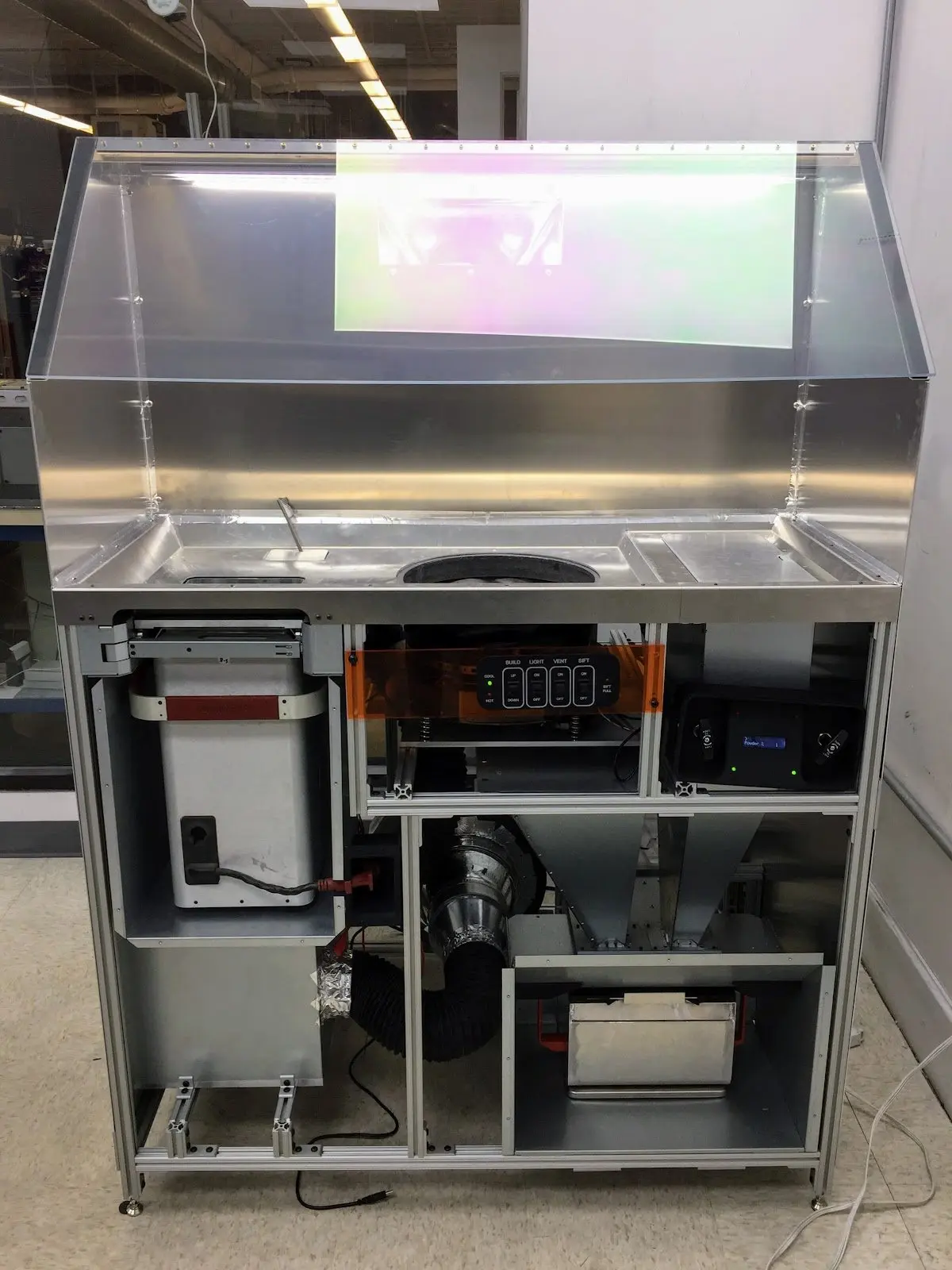
One of the first Fuse Sift prototypes.
Static and unmonitored electrical currents are a concern for any manufacturer, with multiple implications. There is employee safety, and the need to protect workers from harmful shocks when handling equipment. There is also the headache of determining where shocks are coming from–they could be coming from electrical components, or just static electricity. Without being able to pinpoint the source of a shorted circuit, entire product lines can be damaged, costing manufacturers time and money.
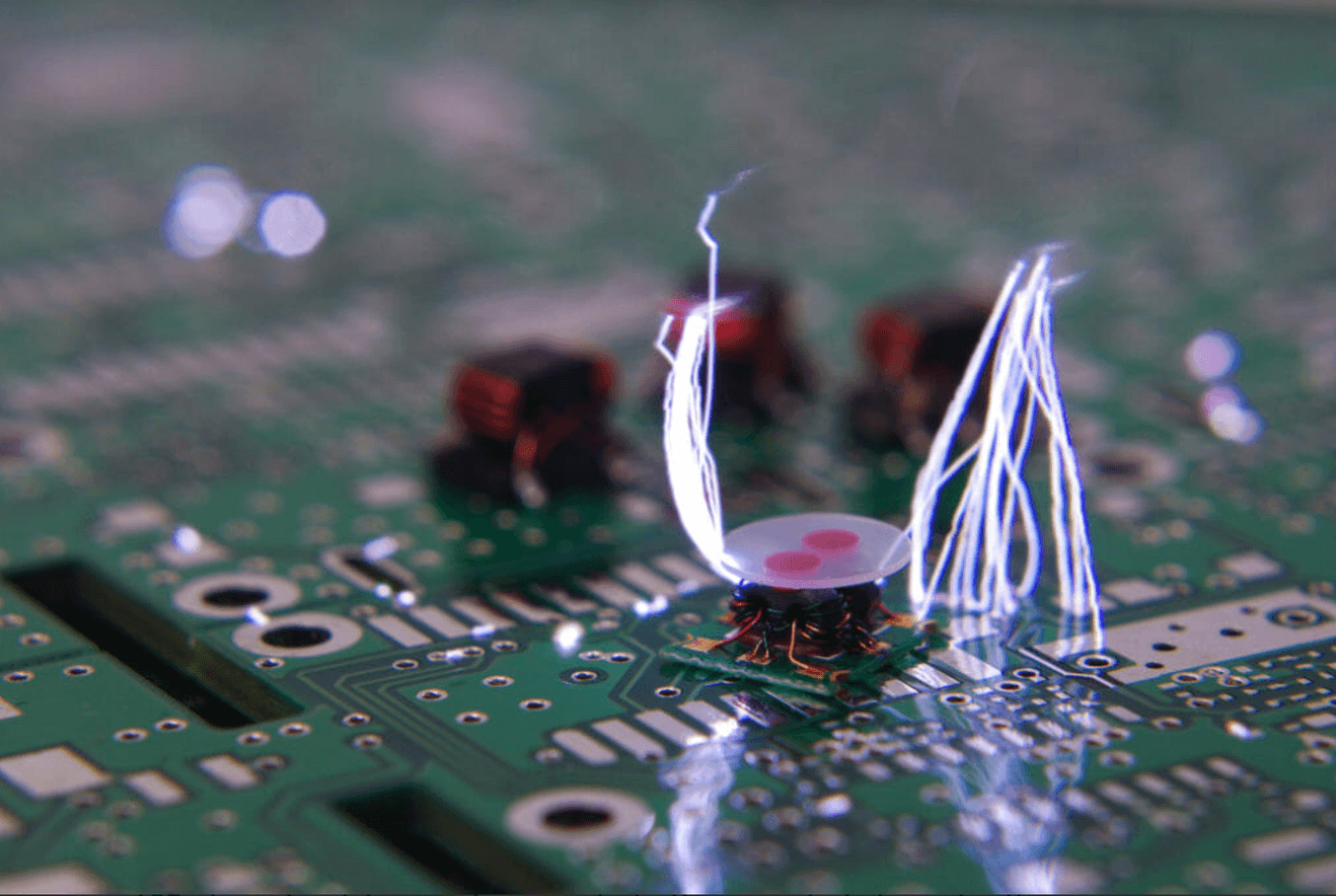
Static shocks destroying a circuit board.
In some cases, like with Formlabs customer HAVEN, uncontrolled electrostatic charges can short out electrical circuits in final products, which led to customers receiving a product that was immediately unusable. HAVEN used ESD Resin to create ESD safe jigs and fixtures on their assembly line and control electrostatic discharge.
There are four types of materials related to electrostatic discharge:
-
Conductive (e.g. metal) allows electrons to pass freely across their surface, which is why tooling for electronics components is often machined from metal.
-
Dissipative (e.g. ESD Resin or other ESD safe plastics) allow electrons to move towards a grounding point at a slower rate than with metals.
-
Anti-static materials inhibit triboelectric charging, or the electric charge built up by rubbing or contact with another material.
-
Insulative prevents or limits the flow of electrons across their surface, meaning that static charges can build up and stay there for long periods of time, often damaging any electrical circuits in contact with them.
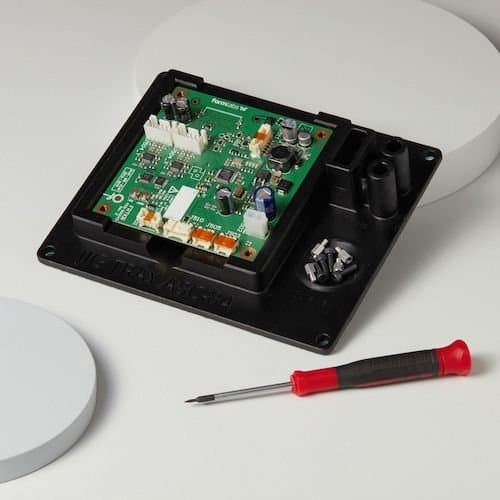
How 3D Printing with ESD Resin Streamlines Electronics Manufacturing
Hear from HAVEN Indoor Air Quality lead engineer Phil Tsao of how they used ESD Resin to reduce the cost and lead time of ESD-safe production fixtures by up to 90%.
Traditional ESD Safe Workflows
Typically end-use parts for ESD safe applications are made from either metal or statically dissipative plastics. Welding, casting, or machining are all options for outsourcing metal parts with varying costs and implications. During a prototyping stage, however, custom metal parts are sometimes difficult and expensive to design, create, and then fit, and might be rendered obsolete in the next iteration.
“We reached out to a few vendors that were experts in tube bending and welding to get an idea of the price and lead time for this part for both short and long term production. No matter who we quoted with, it was extremely expensive to produce, maybe $40 to $50 per part even at mass production quantities which was much higher than anticipated, and it would take weeks to get them back. Because of time constraints and cost, sending it out for our prototypes just wasn’t a favorable option. So the fact that we could do this in-house and get it immediately, that was a game changer, ” says Cheung.
Besides wrapping a part printed in Draft Resin in copper tape, the team also tried using anti-static sprays as well as a dip coating process to try coating the SLA resin part with a static dissipative material. The issue with this approach was that the static dissipative coatings were not very wear resistant and it was difficult to achieve the uniform coating required to achieve reliable performance. Luckily, the Fuse Sift team had heard rumors that a solution might not be so far away.
A Solution Close to Home
“We heard around the building that the Materials team was working on an ESD-safe resin, and we approached Kathy [Bui] (Product Lead, Engineering Business) to see if we could possibly print a couple parts for the Fuse Sift prototypes,” says Cheung.
"Since many of our customers do product design and engineering work with our resins, we often get asked about ESD-safety and that served as the basis for ESD Resin development. One of the great things about Formlabs is that because we do our own engineering in-house, we often have the same needs as our customers from our own products. When Larry described the challenges the Fuse Sift team was working through, it was exactly the kind of use case we had designed ESD Resin for, so we jumped on the opportunity to practice what we preach,” says Bui.
The ESD Resin from the Materials team couldn’t have come at a better time. The Fuse 1 prototypes were ready to go to external beta testers, and the Fuse Sift prototype was scheduled to go with them. There was no time to wait for parts from an external coating or tooling vendor, so the ability to print these parts in-house was critical for an on-schedule beta test.
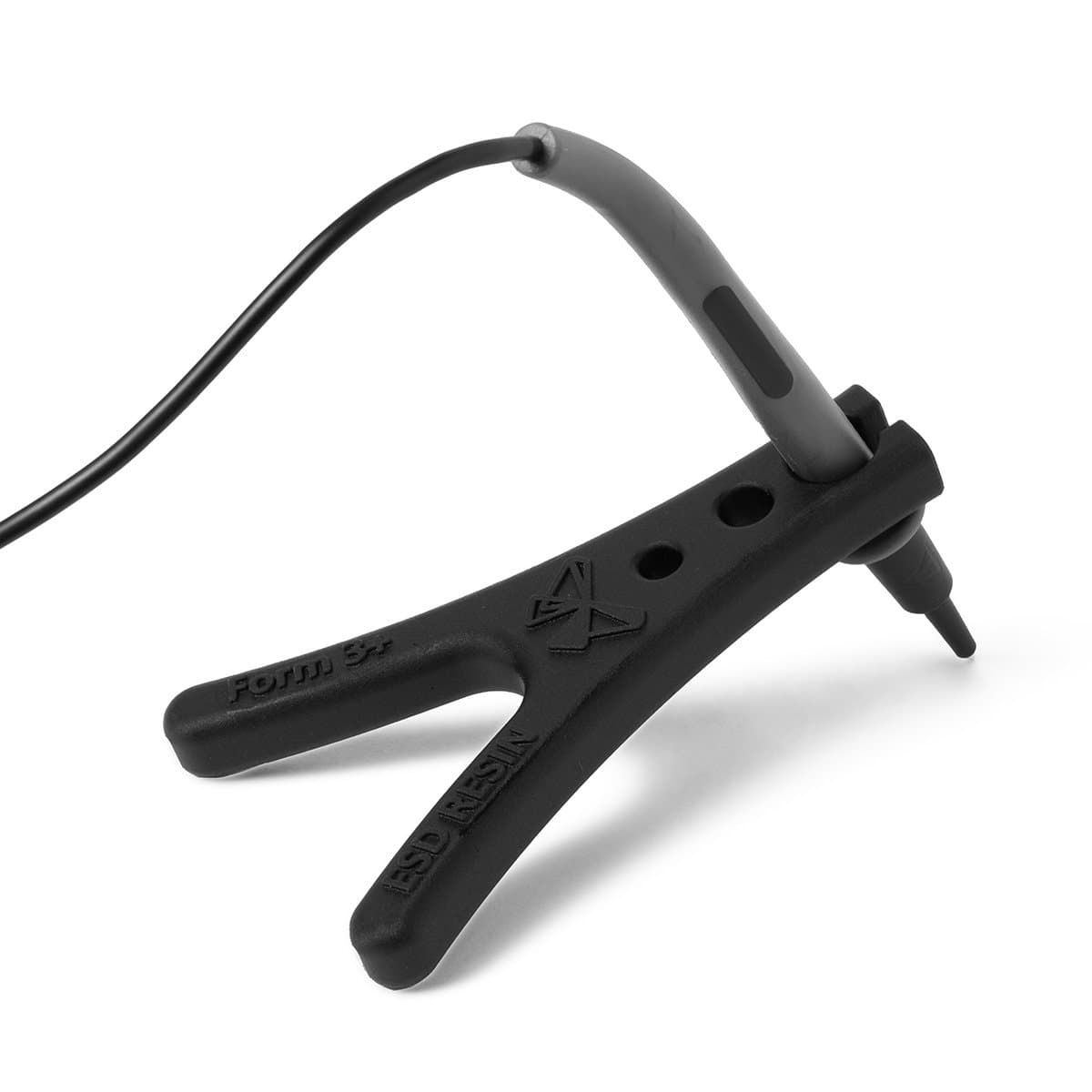
Request a Free Sample
Want to test ESD Resin for yourself? Request our free, ESD-safe, 3D printed multimeter probe holder for your electrical workbench. Test its surface resistivity to validate ESD-safety.
ESD Resin Parts Help Complete Nine Prototypes
The team printed nine prototypes in the material that would eventually be released as ESD Resin. The parts were validated on finished Fuse Sift prototypes which were then sent to potential contract manufacturers and used for internal and external beta testing. Using a surface resistivity meter, the team found that the ESD Resin printed parts were static dissipative, and perfect for the tubing that had large amounts of nylon powder running through it.
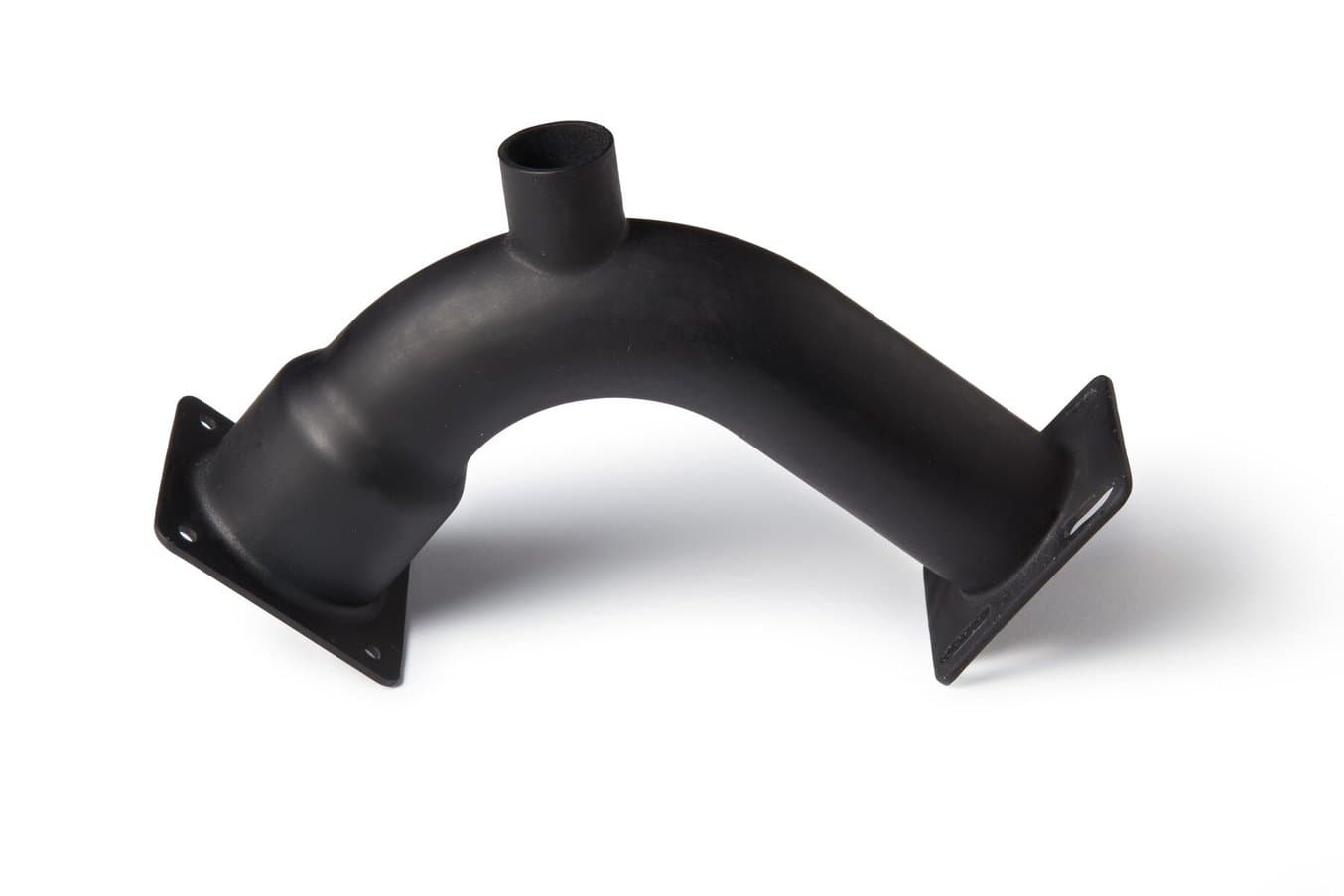
The final Sift Tube in ESD Resin
“Using our ESD Resin allowed us to bridge the gap between prototyping and production. 3D printing is the fastest way to prototype a part like this, but we couldn’t safely validate the concept of the splitter and tubing without an ESD safe solution. ESD Resin gave us the capabilities in-house to design and then validate our concept without spending hundreds or even thousands of dollars on tooling or outsourced parts,” says Cheung.
Using Formlabs’ own ESD Resin allowed the Fuse 1 and Fuse Sift teams to shorten the road to production by avoiding the high cost and long lead times associated with outsourcing ESD safe parts. For a hardware manufacturer, having the tools to create ESD safe parts in house meant that this product could launch faster and with minimized risk.
“If we didn’t print this in house, it would have been a couple weeks, and maybe a couple thousand dollars to get it out. Knowing that it was possible to do it ourselves, especially when we had a deadline to get it out to contract manufacturers, allowed us to plan better,” says Cheung.