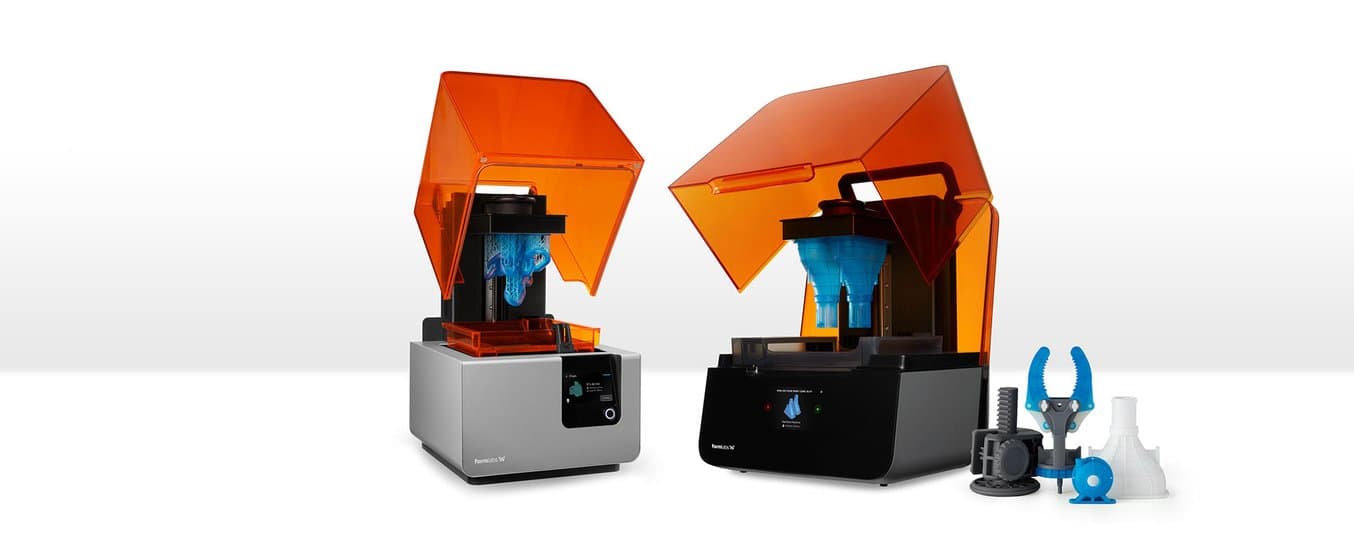
With the release of the latest Formlabs 3D printer—the Form 3+ and Form 3B+—you may be wondering how our re-engineered Low Force Stereolithography (LFS)™ print engine differs from desktop stereolithography (SLA) printers like the Form 2, which has become a staple in the workflows of tens of thousands of designers and manufacturers across industries.
In this post, we’ll spell out the main improvements we’ve made in the SLA printing process over the years, starting with the launch of LFS™ in 2019, and then our latest refinements packaged with the Form 3+. You will learn why we re-engineered the stereolithography print process and optics engine, and what has changed to make the latest printers the most intuitive, reliable Formlabs printers yet. We’ll focus on the differences between our professional 3D printers, the Form 3+ and the Form 2.
- If you’ve never used a Formlabs 3D printer before and are looking for the latest in affordable, professional 3D printing, we recommend getting started with the Form 3+.
- If you’re looking for a large-format 3D printer, the Form 3L is the best choice, with five times the build volume of the Form 3+.
- Read our Ongoing Support Statement for information on our commitment to continuing to provide industry-leading support and consumables for the Form 2.
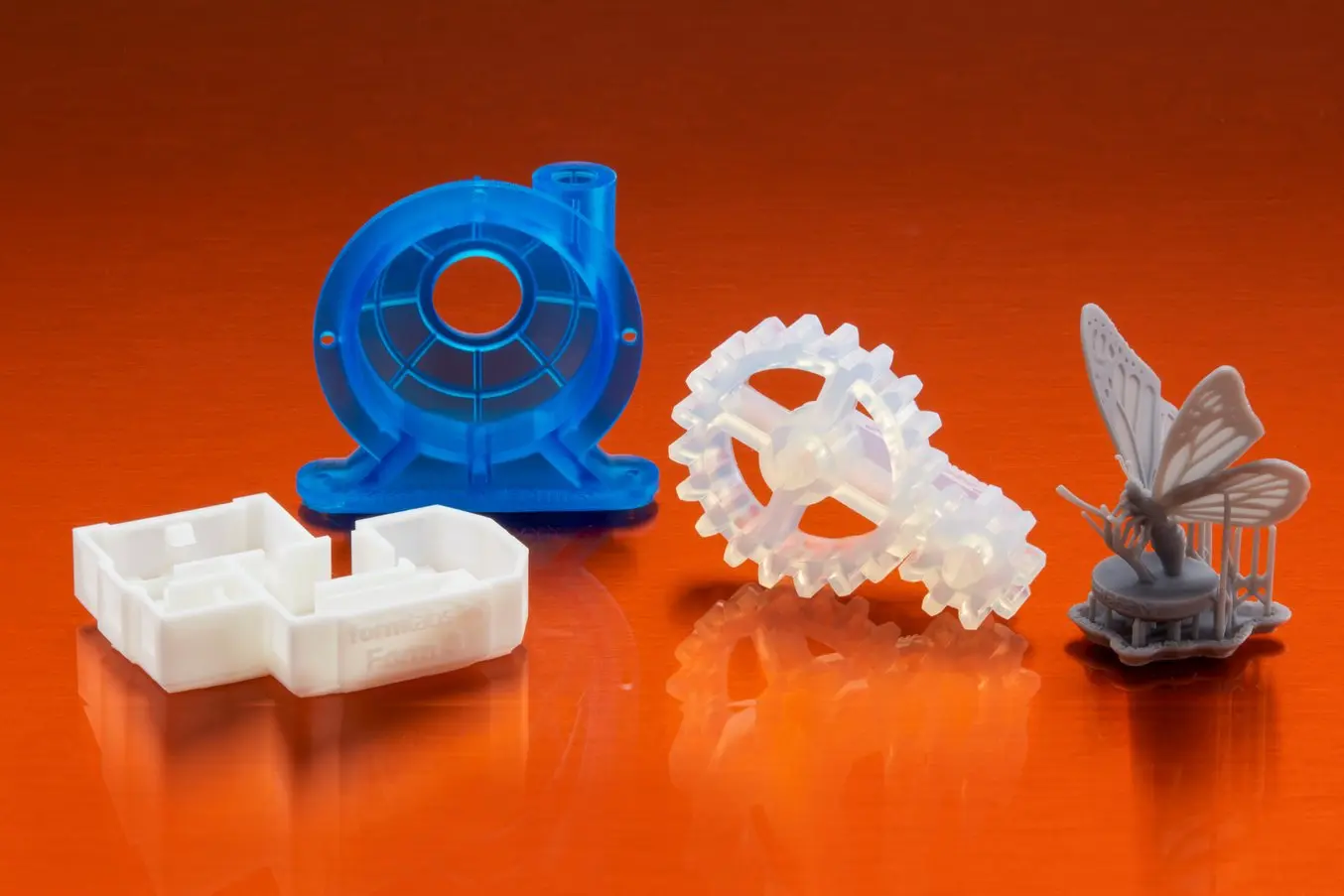
Request a Free Sample Part
Curious to see the quality of the Form 3+ firsthand? Pick an application and we'll ship a sample part printed on the Form 3+ to your office.
Request a Free Sample PartLow Force Stereolithography (Form 3+) vs. Stereolithography (Form 2)
In 2015, Formlabs was the first to bring high-resolution SLA 3D printing to the desktop, in a much smaller and more affordable setup than existing industrial SLA machines. The Form 2 quickly became the industry-leading desktop 3D printer, with tens of millions of parts printed in the field by engineers, designers, manufacturers, dentists, jewelers, and more. In 2019, the Form 3 launched, building on the success of the Form 2, and now over 100 million parts have been printed by Formlabs machines.
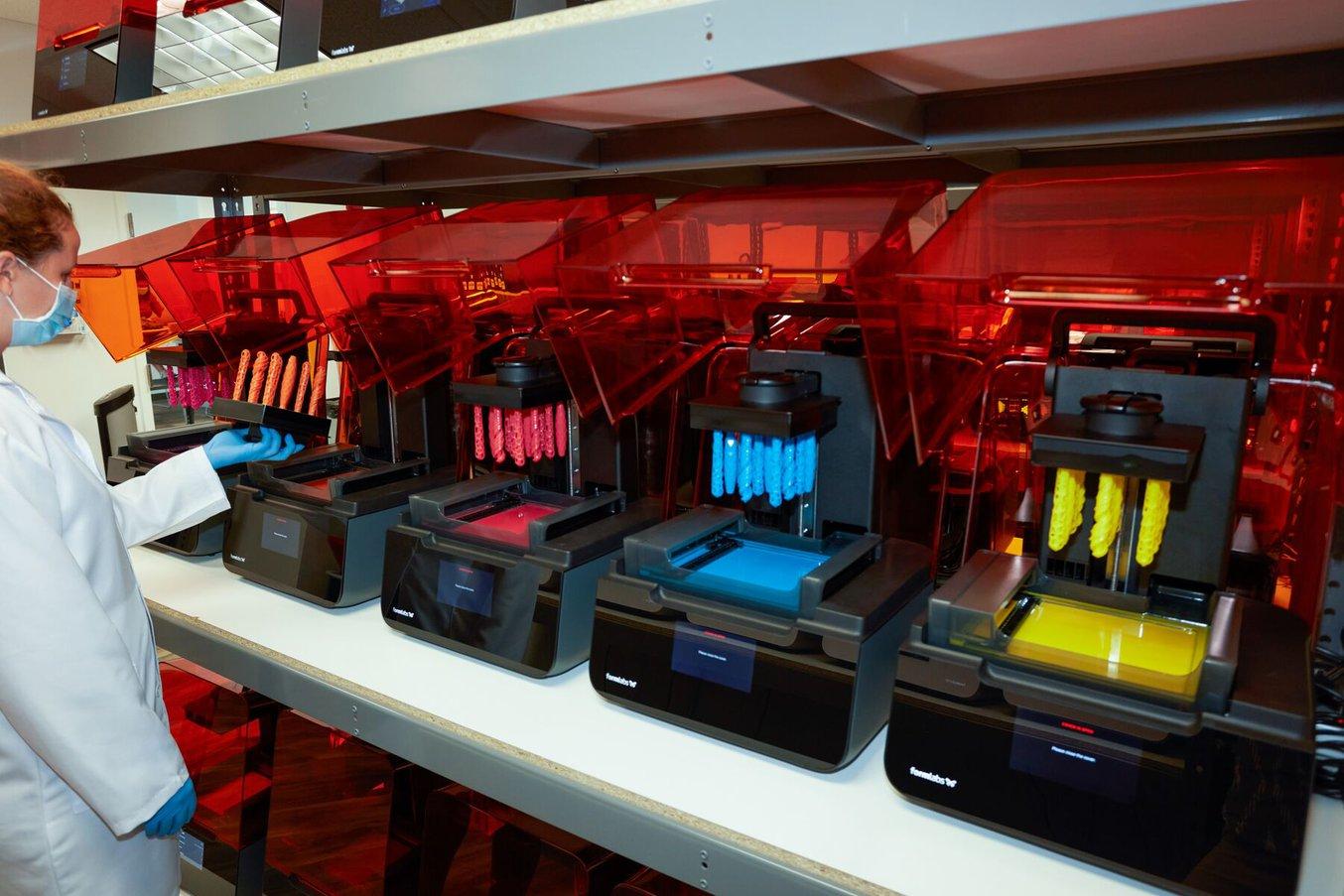
In 2019 we re-built SLA printing from the ground up, launching Low Force Stereolithography (LFS) with the Form 3. LFS is an advanced form of stereolithography that leverages a flexible tank and linear illumination to offer a huge leap forward in print quality and printer reliability. LFS resulted in better print quality, smooth surface finish, enabled light-touch supports, and more.
In 2022, we’ve made substantial refinements to LFS with the Form 3+, further boosting print quality and print speed. Optimal clarity for Clear Resin was significantly improved when comparing prints on the Form 2 and Form 3; on the Form 3+ Clear Resin is even more translucent.
A Lower Force Print Process
The Form 2 achieved a substantially smaller footprint than industrial stereolithography printers by inverting the print process—a transition you can delve deeper into in our Ultimate Guide to Stereolithography.
Inverted SLA introduces peel forces that affect the print as it separates from the surface of the tank, so the build volume is limited and sturdy support structures are required. The Form 2 was calibrated to account for the forces of the peel process and produce high quality parts (the wiper moves left and right between each layer, which can cause strain along the XY axis and lead to warping), putting industrial quality in the hands of more businesses at an affordable price point.
The Low Force Stereolithography technology that powers the Form 3 was developed specifically to drastically reduce peel forces for significant increases in print quality and printer reliability. One key improvement is the flexible film at the base of the tank, which allows for a less intense peel between layers during printing.
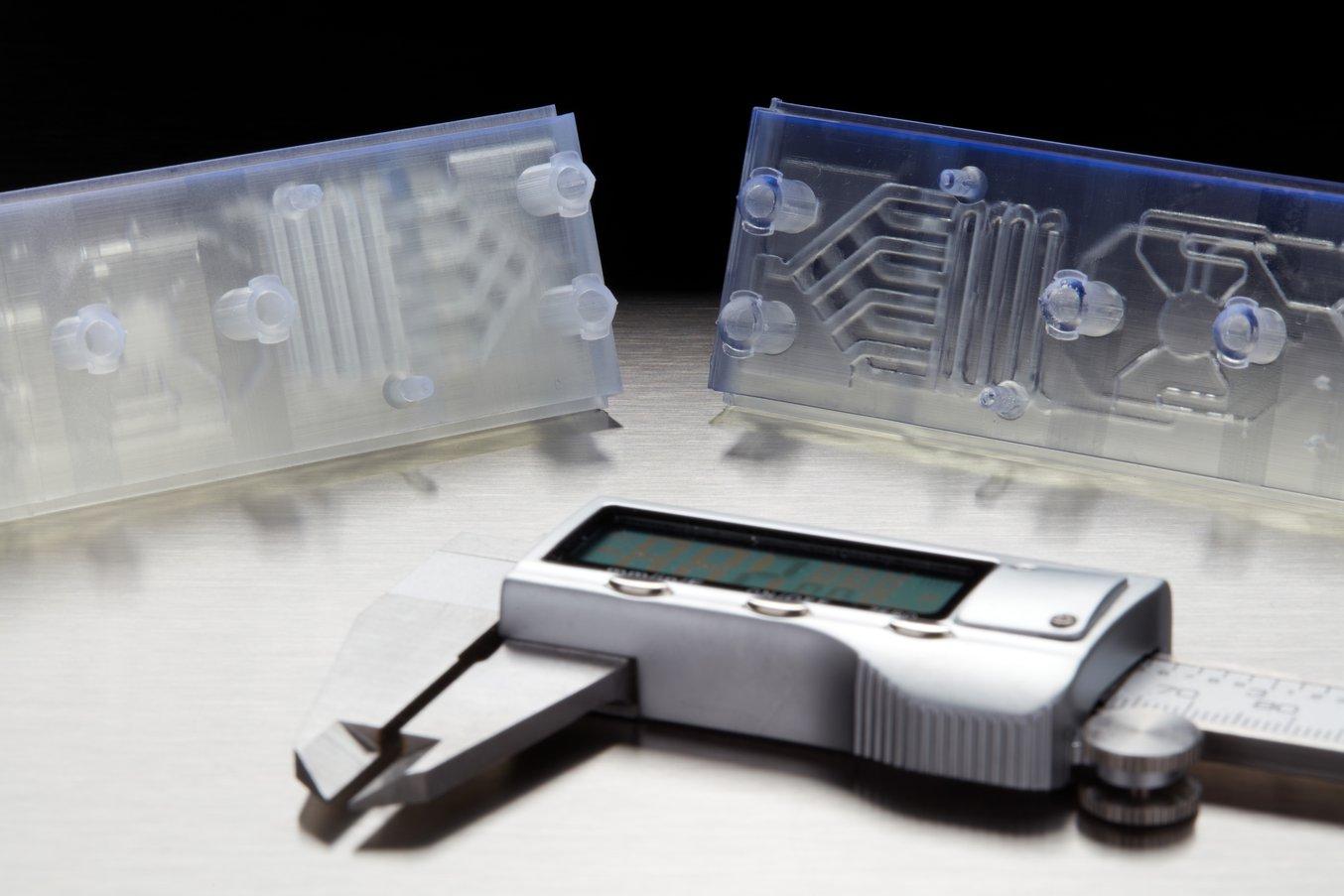
The same model printed on the Form 2 (left) and Form 3+ (right).
Low Force Stereolithography 3D printing significantly reduces peel forces that can create rough surfaces, leading to improved surface finish and part clarity.
This decrease in peel forces brings several key benefits:
- Improved surface quality, with less visible layer lines and decreased surface roughness for incredible smooth surface finish and clarity even at 100 microns.
- Light-touch support structures with smaller touchpoints that easily tear away from the part for faster cleanup and finishing.
- Better print success across all materials, most noticeably for materials with high viscosity and low green strength.
Decreased peel forces lead to incredible surface quality, easier support removal, and cutting-edge material possibilities. Choose the Form 3+ for the best surface finish and the easiest post-processing.
Justen England, Managing Director, Delve
"The improvements to the light-touch supports that break away are game-changing. There is no way to describe the first time you take a part and pull at it and it just seamlessly pops completely free. It takes the stress out of building and cleaning parts and lets us keep our focus on design and creation."
Optics
The precision optics engine within the Form 2 has proven over time that it can meet the accuracy requirements of the most demanding applications. This includes users in dental labs, who often run their printers 24/7 and need to produce many highly accurate parts on a repeated basis.
The Form 2 uses two galvanometers for X and Y positioning, directing laser light from the back of the printer to a large stationary mirror that delivers the beam to the print plane.
For the Form 3+, we focused on further refining accuracy and consistency, and making the system scalable. LFS 3D printing houses the optics inside a Light Processing Unit (LPU) that moves in the X direction. One galvanometer positions the laser beam in the Y direction, then directs it along across a fold mirror and parabolic mirror to deliver a beam that is always perpendicular to the build plane.
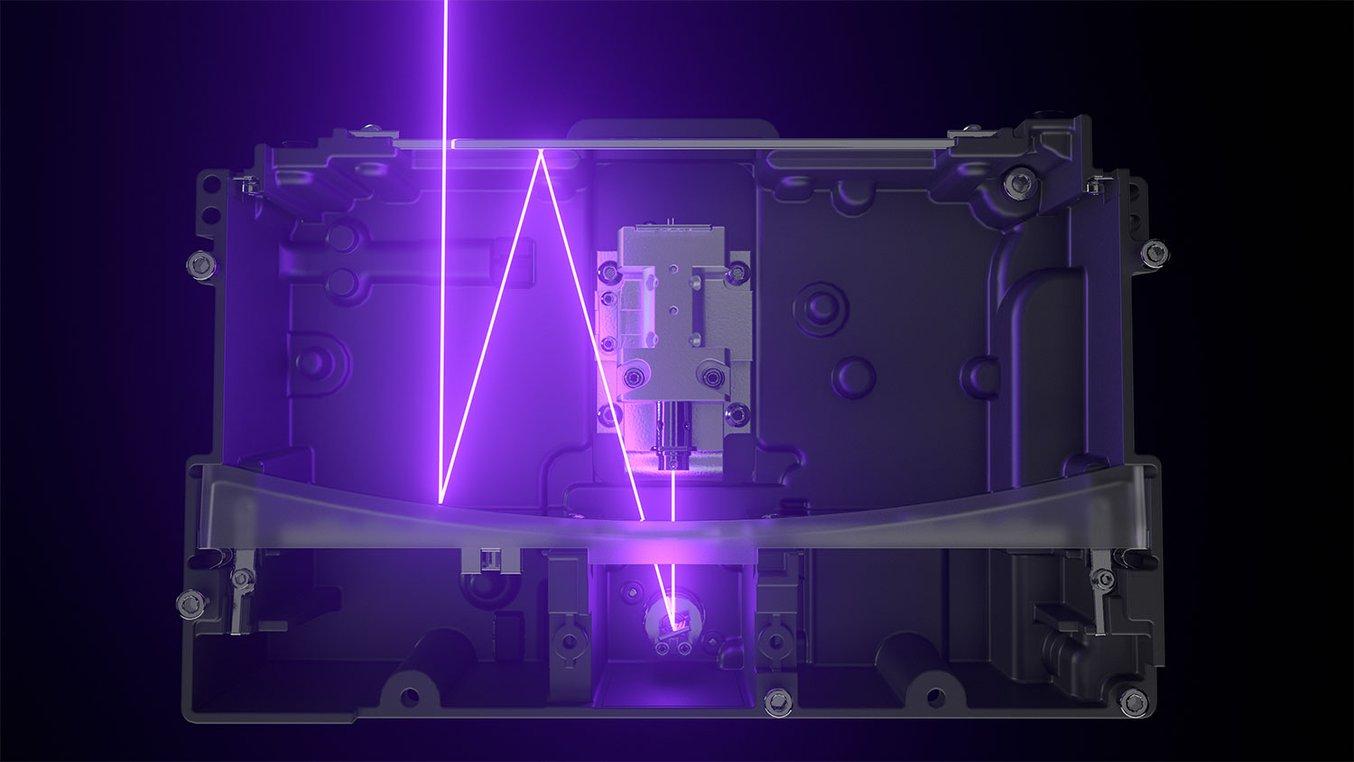
The Light Processing Unit (LPU) inside the Form 3+ contains a system of lenses and mirrors that ensures an accurate, consistent laser spot.
While beam deviation at the print plane is small on a printer the size of Form 2 and Form 3+, a perpendicular beam allows for uniformity as hardware scales up, which is why it was possible to develop the large format Form 3L.
The Light Processing Unit uses a spatial filter to create a crisp, clean laser spot for greater precision, and a higher-frequency galvanometer, which leads to some gains in print speed over the Form 2.
Form 3+ | Form 2 | |
---|---|---|
XY Resolution | 25 microns (0.001 in) | n/a |
Laser Spot Size | 85 microns (0.0033 in) | 140 microns (0.0055 in) |
Laser Wavelength | 405 nm wavelength | 405 nm wavelength |
Laser Specifications | EN 60825-1:2007 certified | EN 60825-1:2007 certified |
Note: The Form 3+ uses 180mW maximum laser power at the print plane.This power is not maxed out all the time and depends heavily on geometry of the part / stage of the print. The Form 2 maxes out at 96 mW at the print plane.
The LPU delivers more uniform, precise optics to the Form 3+ and Form 3L than the Form 2, and is easier to replace in the rare case that optical issues arise. Further improvements to LPU stabilization were delivered on the Form 3+ beyond what was capable on the Form 3, further resulting in tighter alignment between layers, and ultimately better surface finish.
Choose Form 3+ and Form 3L for the highest optical precision, part accuracy, and consistent printing over time.
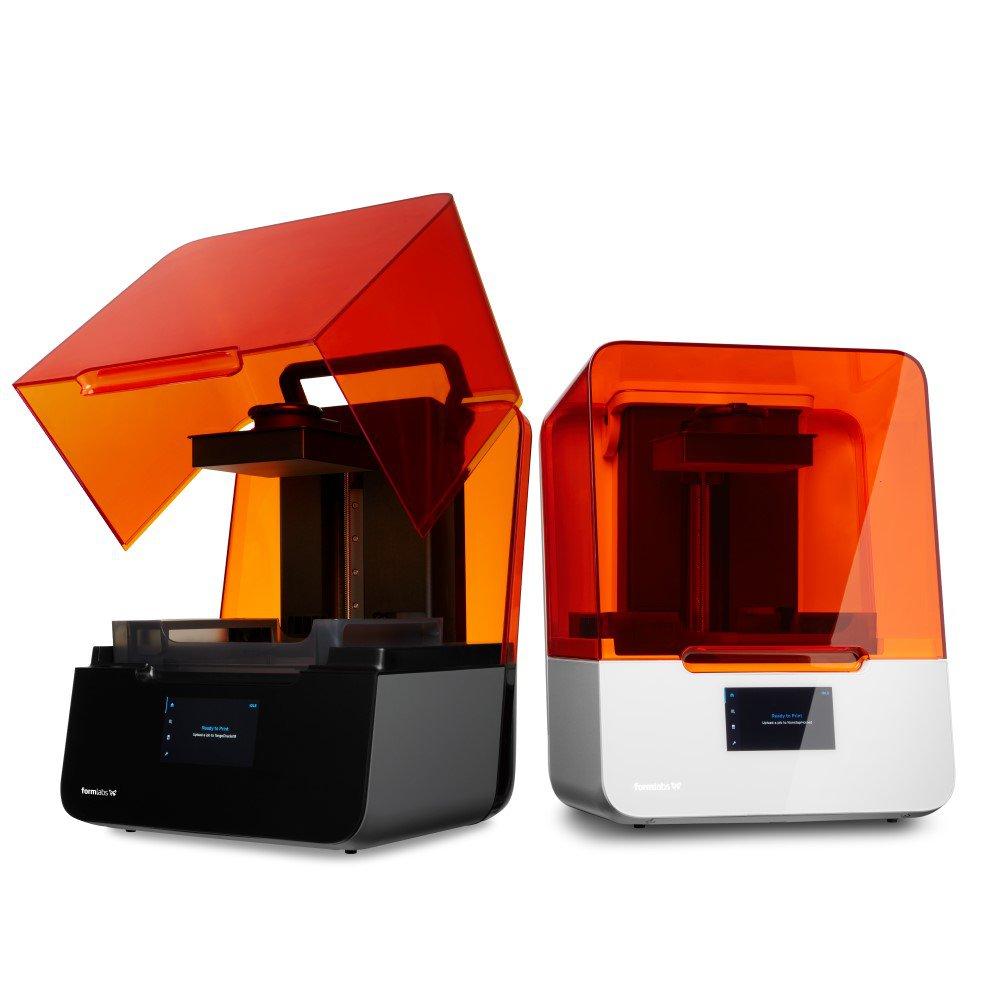
Introducing the Form 3+ and Build Platform 2
See how the new Form 3+ and Build Platform 2 allow you to fabricate parts faster than ever with a hands-on overview.
Truly Nonstop, Printing
With the Form 3+, we set out to create the most reliable 3D printer on the market. It’s been incredible seeing businesses from trailblazing consumer companies such a Peak Design to product design company Glassboard using multiple resins on a single printer to drive innovation and grow their business.
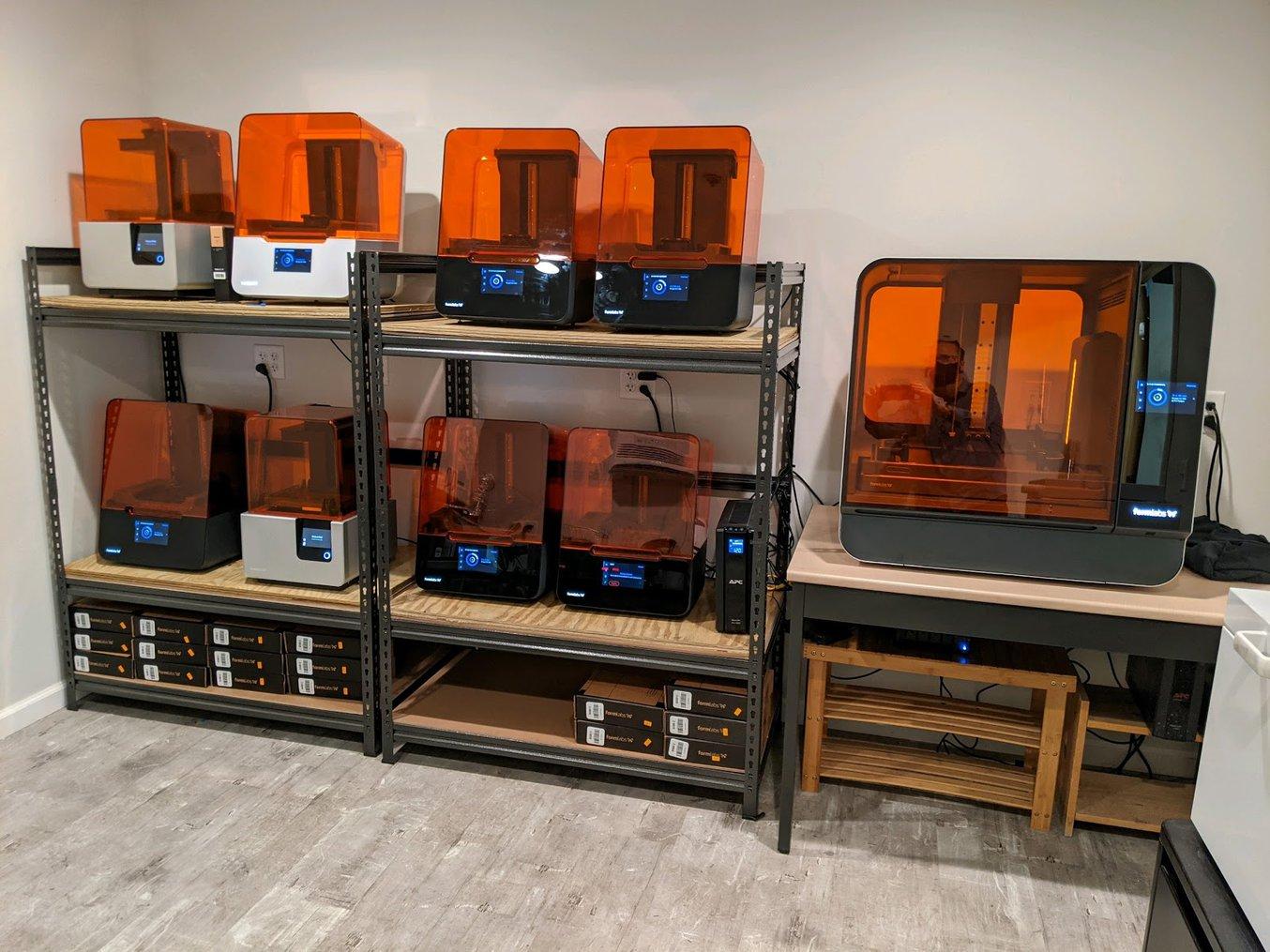
In the dental space, Perfect Finish Ortho Lab is using an in-house fleet of Formlabs printers to create over 700 appliances per week. After buying their first Form 2 in 2016, the lab has scaled with Formlabs and now deploys a Form 3, Form 3B, and Form 3BL. Now, their fleet runs all day and night, with lab President Phil Pelligra saying, “we don't have time for reprints of models, they need to be accurate all the time, and that is why we are Formlabs customers.”
Formlabs machines are designed to free up time so you can focus more on designing and creating and less on checking and maintaining your printer.
The Form 3+ has introduced several new features to push toward maximum uptime beyond what is capable on the Form 2:
- Even more integrated sensors across the printer detect and maintain ideal print conditions and alert you when the printer needs your attention. The optical sensor can even detect dust!
- Field Replaceable Components. The Light Processing Unit, optics window, and other components can be replaced in-house to ensure 24/7 uptime. Some Form 2 components are user-replaceable, and we’ve learned from working with users how to make these replacements even more intuitive.
- Improved failure detection and handling means you can experiment with challenging geometries with ease. If a print fails, the Form 3 can print a cleaning mesh for easy removal.
- Easier Print Cleanup. In the rare case a print fails, simply run a cleaning mesh print directly from the printer touch screen to capture and remove any solid resin remaining in the resin tank. Post-processing SLA parts has never been easier than on the Form 3+.
- Adaptive Layer Thickness. Adaptive Layer Thickness is an advanced print mode available for all materials. The feature analyzes parts imported into PreForm and assigns layer heights throughout the sliced model based on the geometry of the part, maximizing speed and preserving fine details.
- World Class Support. Because we know every business use case is unique, get helpful, human support when you need it from a Formlabs expert that understands your business.
With the launch of the Form 3+, Formlabs engineers also took extra time to improve the temperature controls up and beyond those in the Form 2 and Form 3.
Resin temperature is very important to control, as the curing process and viscosity of resins can be highly dependent on this being correct. Form 3(B) measured air temperature as air was leaving the printer, meaning its temperature readings were easily impacted by ambient temperature around the printer.
Form 3(B)+ features a redesigned heating system that reads temperature closer to the resin itself, allowing prints to start faster and more consistently across a broader range of ambient conditions due to more accurate temperature detection.
The Form 3+ takes printer reliability to the next level with more features to help you spend less time checking on your printer so you can focus on designing and creating.
Nick Payton, Mechanical Engineer, RightHand Robotics
“The Form 3+ cuts down on the number of things that you have to know, in order to get good parts. That's good product design. The surface finish is better and the support sizes are smaller, so everything just comes out cleaner. Less work has to go into getting viable parts. That speeds everything up, especially when you're trying to get something from ‘we want to tweak the dimensions here’ to trying it on a robot within a couple of days. You can't do the same quick design cycles with out-of-house processes.”
Print From Anywhere With Remote Print
For those who receive urgent or last minute print requests, the Form 3+ introduces the ability to start prints from anywhere. Pre-prime the printer before you leave, then start the next print job from anywhere in the world (not just the local network).
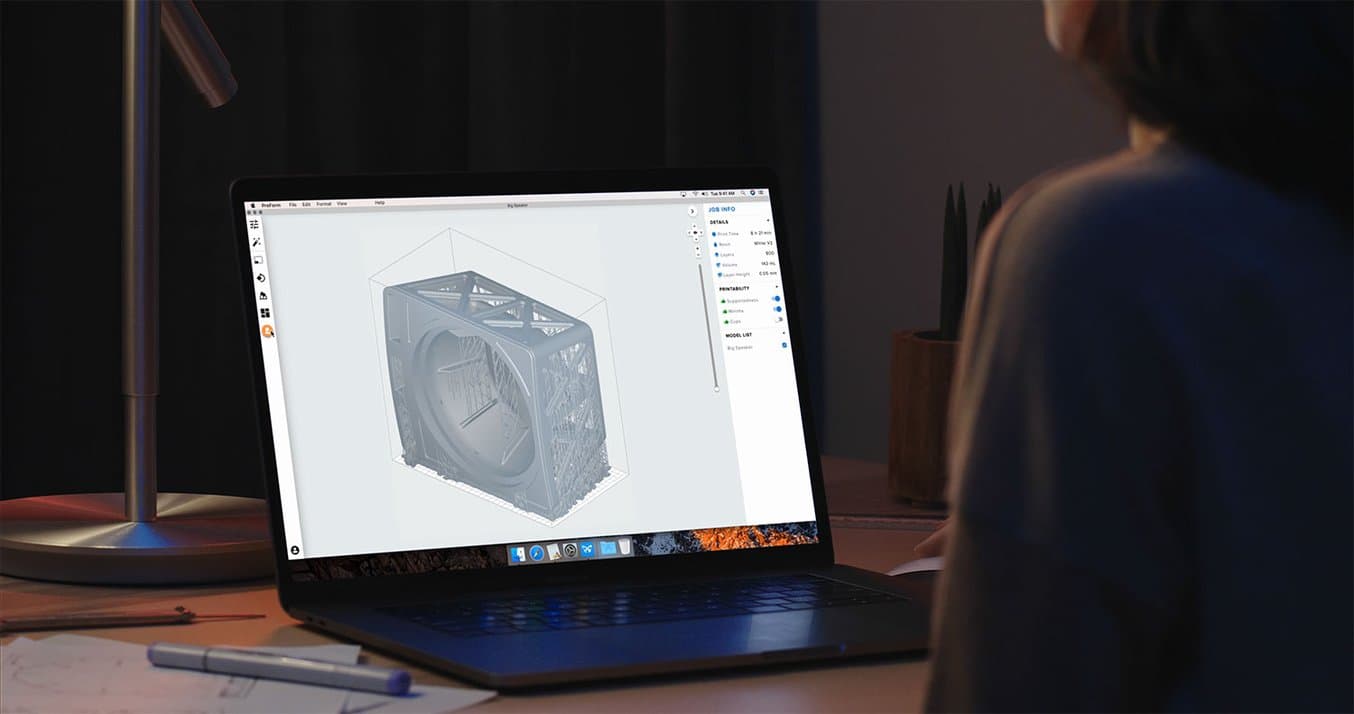
Start Form 3+ prints from anywhere with Remote Print.
Familiar Workflows, New Ways to Interact
If you’ve used a Form 2 before, the overall workflow for the Form 3+ should feel quite familiar. Even if you have never used a Formlabs printer, it’s easy to get started with either machine. To further empower beginners and accelerate the workflows of advanced users, Formlabs offers similar service and training options for each machine.
The basic printing process looks like this: Import your design into PreForm, choose a material from our extensive materials library and insert the cross-compatible cartridge, and click print. Our automated post-processing machines, Form Wash and Form Cure, are compatible with both Form 2 and Form 3+, which use the same build platform.
Similarly, the new Build Platform 2 which launched alongside the Form 3+ is compatible with the Form 2, Form 3, and Form 3+. The Build Platform 2 has patented Quick Release Technology that fundamentally changes the SLA workflow, making it significantly easier to remove parts from a build platform and reducing post processing time.
Some good news for Form 2 users: we’ve continued to issue software updates for PreForm, meaning that users across the Formlabs printer product line are all on the same software. This means one familiar set of software tools no matter your printer setup, allowing for different printers to easily operate side by side.
The Form 3+ has introduced a few new features to make interacting with the printer even easier:
- A larger, higher resolution touchscreen. The Form 3+ can be controlled completely digitally from the screen, while the Form 2 includes an additional button. A larger screen also enables future translations of the interface into new languages.
- Two LED status indicators and a speaker for ambient visual and audio alerts ideal for drawing the attention of anyone passing by.
- Sleek, redesigned hardware with a printer cover that opens up flat against the wall, optics protected from resin exposure, and components that are easily replaced by the user.
Form 3+ | Form 2 | |
---|---|---|
Printer Control | 5.5" interactive touchscreen 1280 × 720 resolution | 4.3" interactive touchscreen 480 × 272 resolution Push-button |
Alerts | Touchscreen alerts SMS/email via Dashboard Two LED status indicators Speaker for audio alerts | Touchscreen alerts SMS/email via Dashboard |
With cross-compatible materials and accessories and the same intuitive software, it’s just as easy to manage several Form 2 and Form 3+ printers side by side as it is to manage a uniform fleet.
Familiar Material Library, New Ways to Print
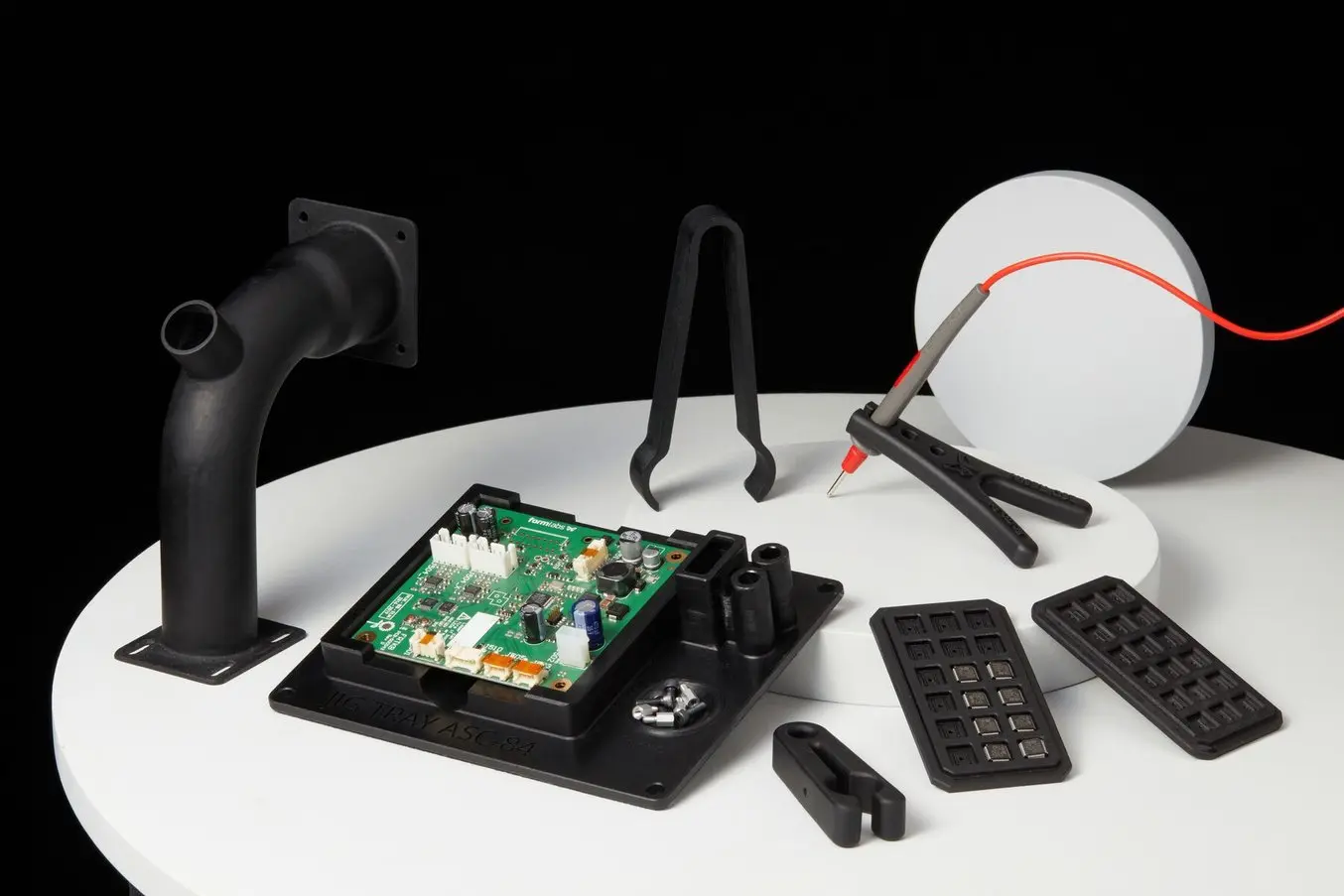
Due to advances in LFS, certain materials will only be printable on the Form 3 or Form 3+. The first of these is ESD Resin, a material designed for manufacturers to reduce risk and increase yield on their electronics manufacturing lines. ESD Resin is a cost-effective solution for producing static-dissipative parts designed for use on the factory floor.
Formlabs continues to support the Form 2, and new materials continue to ship with support for it. However, it is not a guarantee that future materials will be compatible with the printer, as advanced workflows may require LFS.
The Form 3+: The Next Generation of Industrial SLA
Today, Formlabs users are leading the way in scaling 3D printing operations, from using printers as prototyping tools to indispensable drivers of business. The Form 2, the 3D printer that changed the standard, is now available at an even more affordable price point to bring industrial-quality 3D printing in-house.
With the Low Force Stereolithography (LFS) print process behind the Form 3+ (and its large format counterpart, the Form 3L), Formlabs has re-engineered the print process to create an in-house fabrication platform that’s more reliable and versatile than ever.