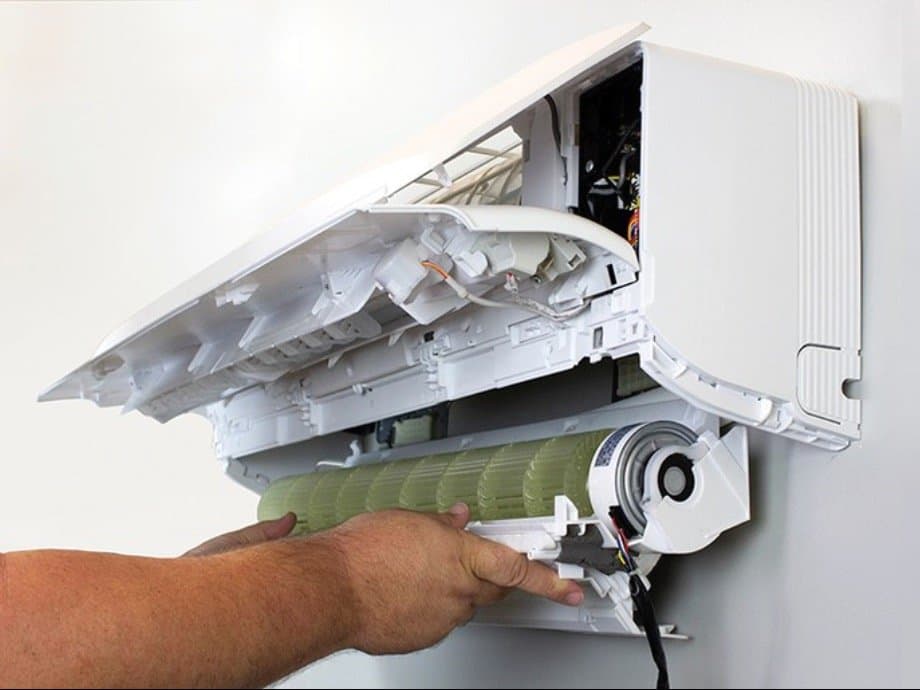
Friedrich's re-engineered Floating Air Pro® and Floating Air Premier ductless solutions featuring FastPro™ are designed with the HVAC contractor and installer in mind. Photos courtesy of Friedrich AC.
As anyone who’s spent a sleepless summer night wishing for a reprieve from the heat knows, an air conditioner can dramatically, and instantly, improve quality of life. At least, when the AC unit is up to the job.
Air conditioners are complex machines to design, balancing the optimization of airflow, heat exchange efficiency, and form factor. To stay competitive and bring industry-leading products to market, Friedrich AC has leveled up their entire design process by bringing 3D printing in-house. They’ve built a high-tech prototyping facility around the Formlabs Form 3L large-format resin 3D printer, and in doing so, have created even superior products while fostering a culture of innovation.
140 Years of Innovation
Friedrich AC has been in business since 1883, when founder and inventor Ed Friedrich began designing and manufacturing home goods in San Antonio, Texas. Over the last 140 years, Friedrich has developed into a premier brand for room air conditioning units, proving their ability to adapt to a changing regulatory landscape and market conditions.
Today, Friedrich has a state-of-the-art UL testing lab in-house at their Design and Development Center, still based in San Antonio. As a part of the UL Client Test Data Program and an Intertek Satellite 3 facility, the Design and Development Center is one of only a handful of private UL-certified testing facilities in the country.
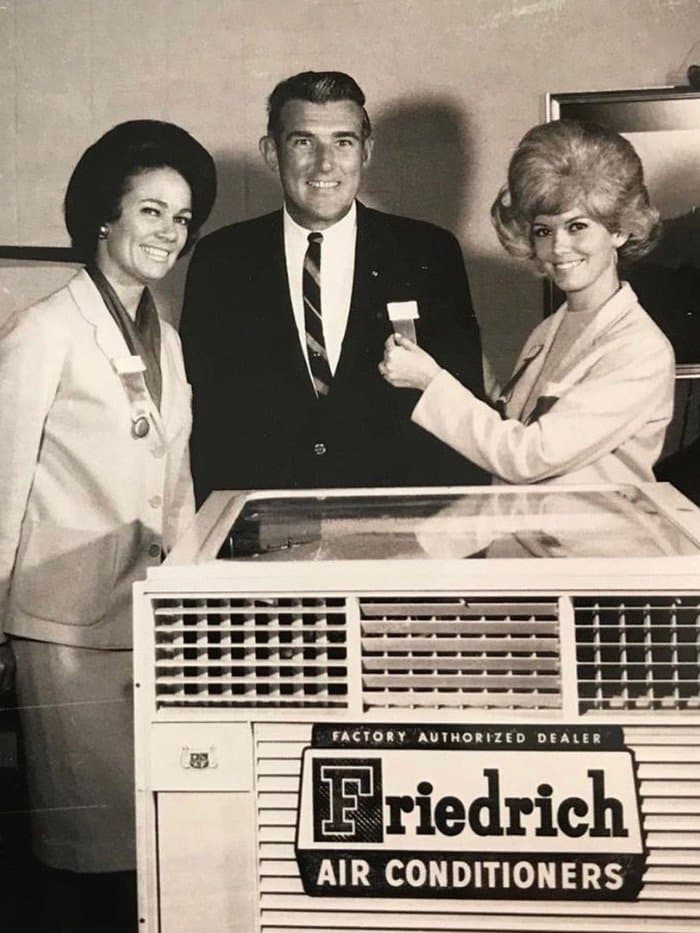
Friedrich AC has a long history of innovation and excellence.
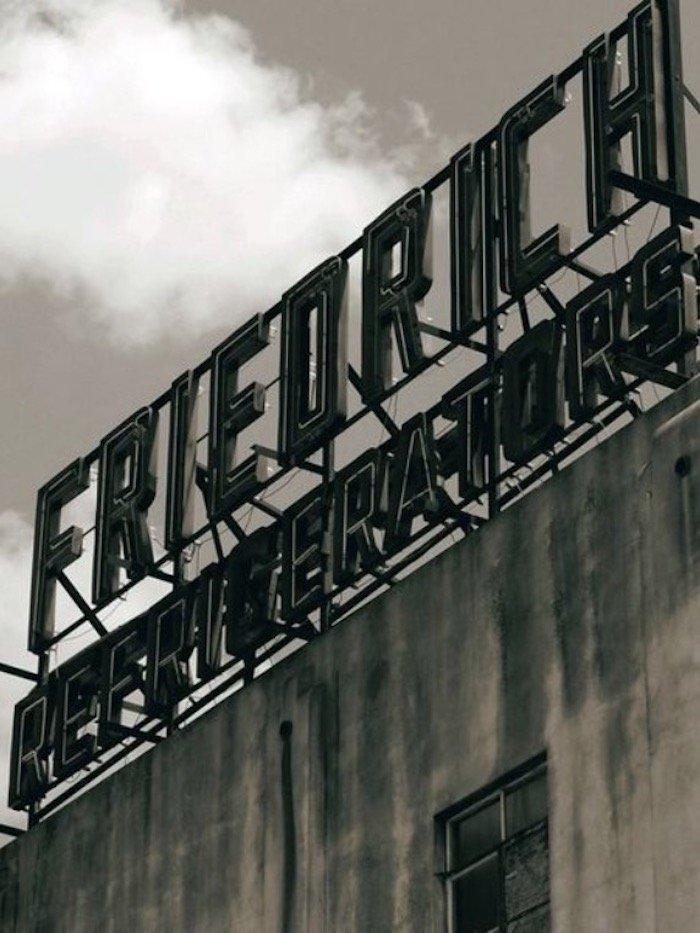
Their Design and Development Center is one of only a handful of private UL-certified testing facilities in the country.
Compromising No More: High Speed, Low Cost
At the Design and Development Center, Mechanical Engineer Noah Trent works on refrigeration system development, and is in charge of handling requests from all over the company for 3D printed parts. Operating as Friedrich’s primary fabrication space for multiple engineering teams, the lab has processes for sheet metal fabrication, tube bending, assembly, and performance testing. Before bringing the Form 3L in-house, the team was usually prototyping with simplified sheet metal parts or sending requests to external vendors. “We were doing simplified designs and basic geometries with sheet metal, and reaching out to fabrication vendors for more complicated items,” says Trent.
Sheet metal fabrication limited them to iterating only the most basic shapes in-house. When sending parts out, they could get them from large 3D printing vendors fairly quickly, but the price was exorbitant. Some product development cycles would require as many as 10 prototypes of the same part, and the costs added up. Design supervisor Emma Flores added, “It was super pricey. We could order from China, but it might take months to get there. We couldn’t have both a good price and fast delivery.”
Flores was determined to find a prototyping solution that could be both fast and inexpensive. When preparing for a particularly involved design sprint, the team started to evaluate the ROI of bringing a high-quality 3D printer in-house. “We chose the Form 3L because it had the Wash L and Cure L, was a good price, good size, high quality, and because of the support Formlabs offers,” says Flores.
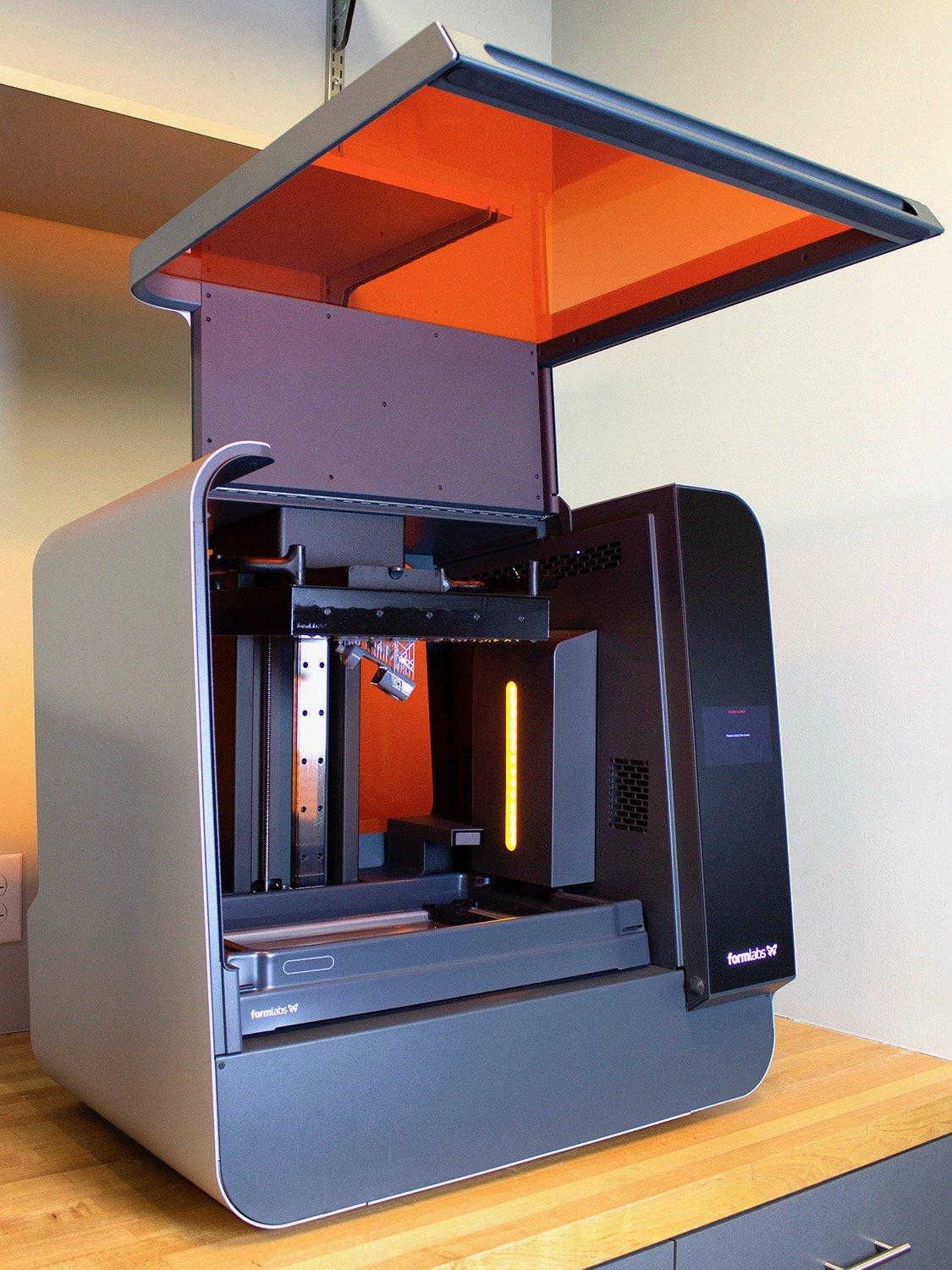
The Form 3L printer expands the team's capabilities for prototyping large parts quickly.
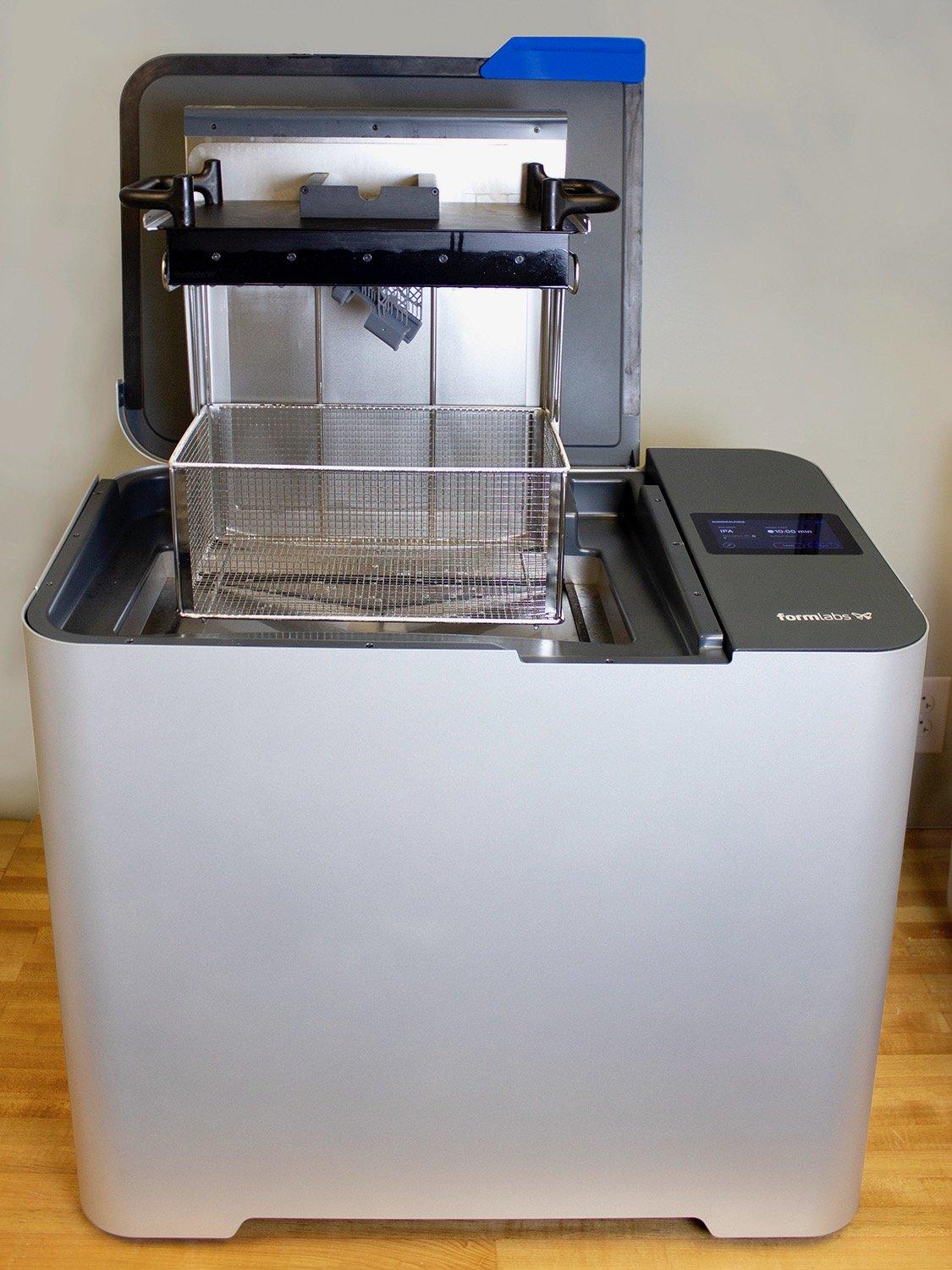
The Form Wash L streamlines the end-to-end workflow for large-format resin printing.
Building an Internal Additive Manufacturing Center
Since integrating the Form 3L into the Design Development Center workflow, Trent and Flores have established an organic system for internal requests from electrical engineers, industrial designers, and mechanical engineers across Friedrich’s different facilities and working groups. “Whenever someone has the need, from our locations in San Antonio, or Monterrey, Mexico, they send it to Noah — he’s become the expert,” says Flores.
The majority of requests Trent receives are for prototypes of plastic parts like fans, shrouds, housings, buttons, or panels. The design of these parts may be improved on from one design iteration to the next, to continually improve fit, feel, and function. In addition to the requests for prototype plastic components, the team also handles some requests for manufacturing aids, such as a probe housing prototype that will eventually be used on the manufacturing line.
“Everyone’s working on three or four different projects at a time. For a while, we had the printer running nearly 24 hours a day for a month. It’s constantly in use. You’re more likely to walk in and see it running than not,” says Trent.
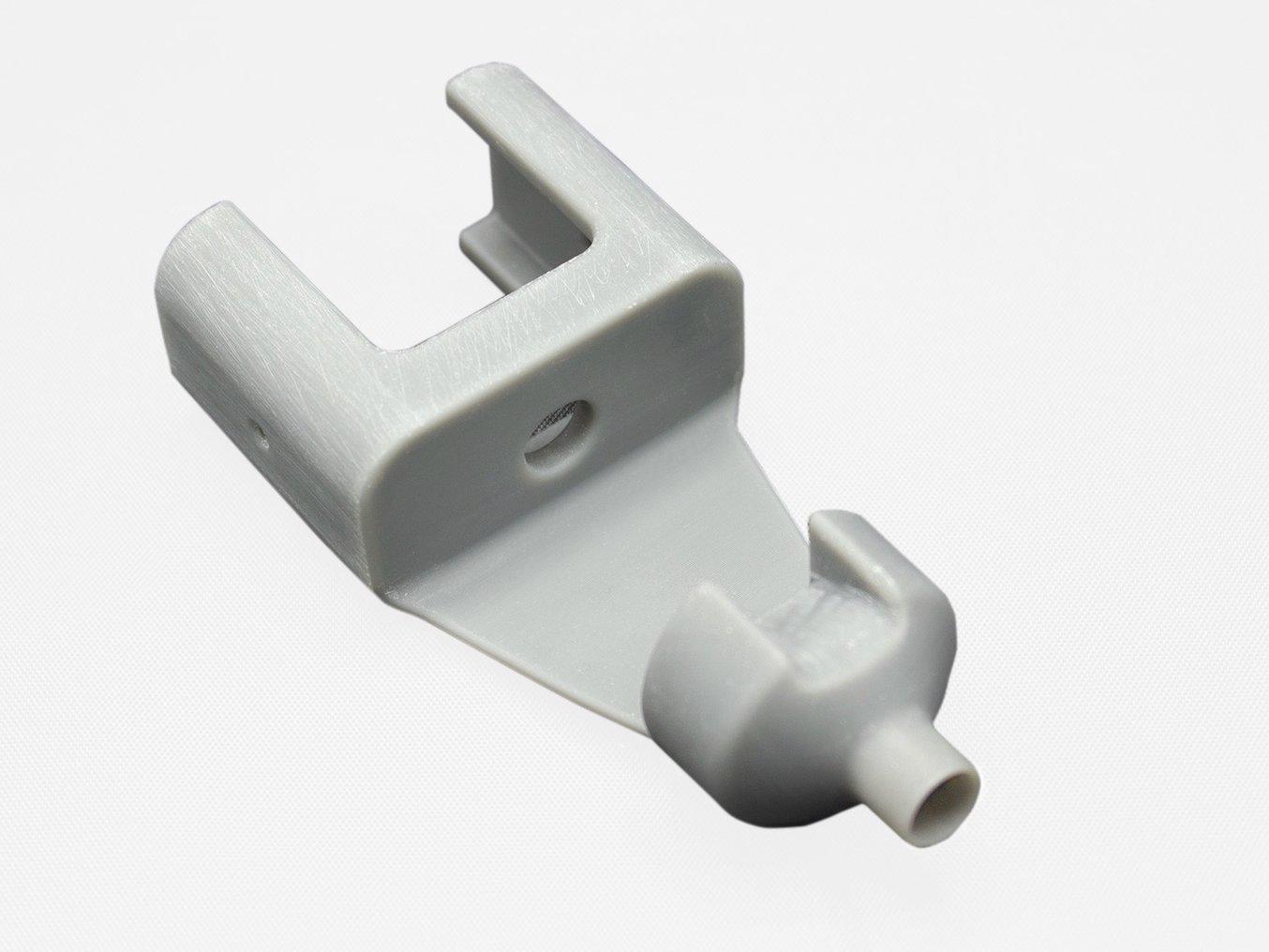
This probe housing, printed on the Form 3L in Rigid 10K Resin, was prototyped for use in an internal process on the manufacturing line.
3D Printing for Performance, Manufacturability, and Serviceability
When designing an air conditioner many things need to be considered to ensure performance. One of several very important considerations is airflow. “We design for performance first and foremost. One of the most important things in AC design is having enough air moving through. We spend a fair bit of time creating geometries that improve our airflow,” says Trent. The large build volume of the Form 3L and the smooth surfaces created by the low-force stereolithography (LFS) printing process allows them to test full-scale prototypes to exacting specifications for maximum cooling efficiency.
Though 3D printing can open up new possibilities for those geometries, it’s not the whole story. Because these parts will eventually be injection molded, the components also need to be designed for manufacturability. “We have to design 3D printed prototypes that can then be manufactured at high volumes with injection molding. We get the 3D printed parts as close as we can to the eventual injection molded material. Then we test them. Sometimes it’s in a wind tunnel, sometimes it’s for fit, and sometimes it’s for strength,” says Trent. The Friedrich team uses General Purpose Resins for their smooth surface finish and high dimensional accuracy, and Tough 2000 Resin for strength and durability.
Along with optimal performance and manufacturability, the team needs to ensure these units are easily maintained, whether by the owner or an HVAC technician. “These are high quality units, and built to last. They need to be easily assembled and disassembled, with access for maintenance,” says Flores.
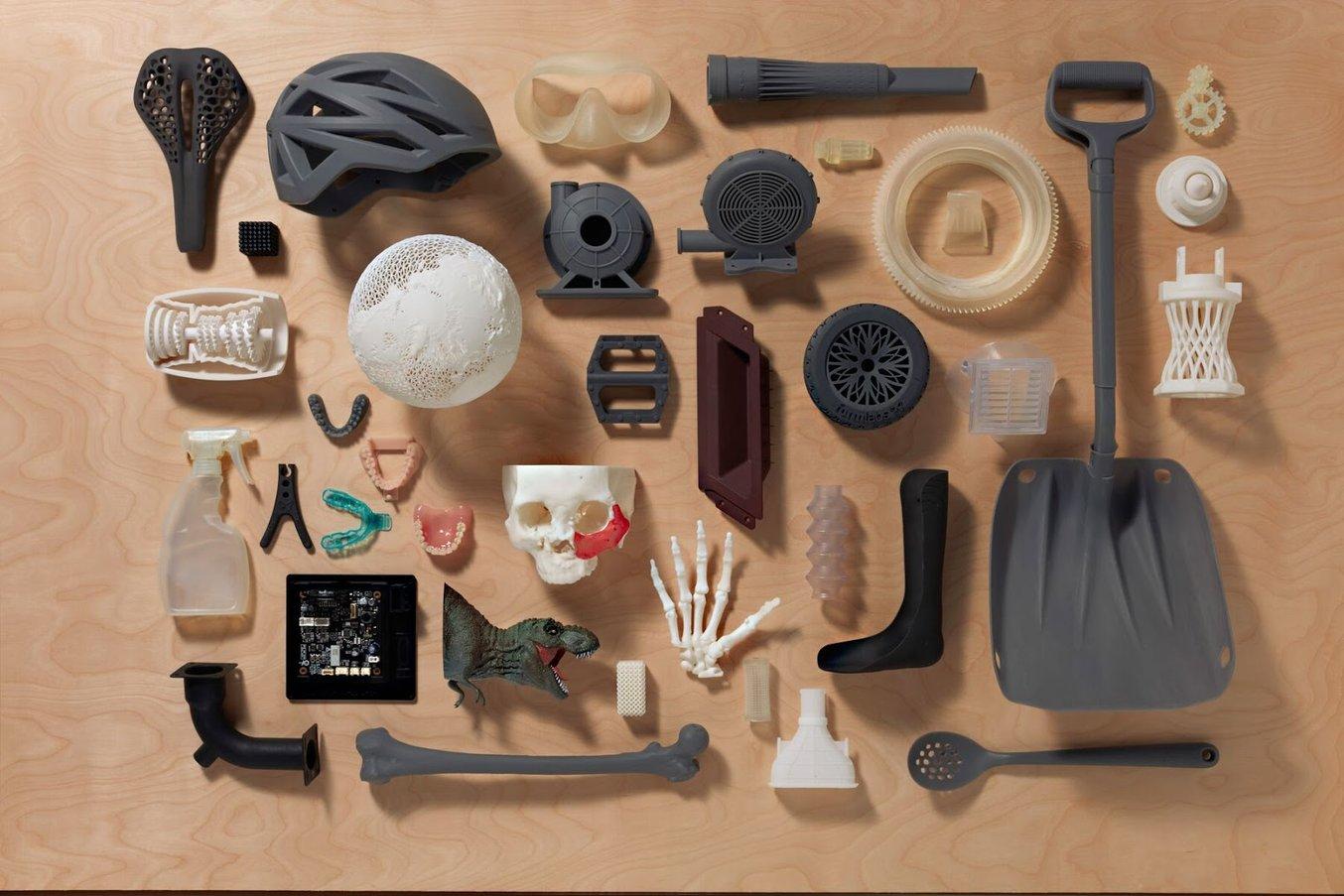
Rapid Prototyping: Find the Right Material for Your Application
Trent has shared this tool with the engineers he works with at Friedrich AC, so they can explore resins for specific material properties they might be interested in.
The Iterative Loop
Designing with performance, manufacturability, and serviceability in mind makes every improvement, no matter how small, count. To make tiny adjustments, Trent, Flores, and the team rely on the precision and speed of the Form 3L. They will frequently receive requests for a single component, designed with four or five slightly different variations. By utilizing the large build volume of the Form 3L, they can print every iteration at once and have them ready for comparative testing the next day. With one machine, the team can quadruple their iterative ability and find which design performs best, is the most easily injection molded, and can be maintained in the field.
"The loop that this 3D printer allows you to get into… if I have an idea and I want to see it, test it multiple times before sending it out, I can. It is so incredibly valuable for making a high quality product. Before, we were doing maybe one or two iterations, and now there are always at least three or four. There’s magic that can happen in those last two."
Noah Trent, Mechanical Engineer
Encouraging a Culture of Innovation
Having an in-house printer capable of functional prototypes has emboldened other teams to try new things. Outside of the 3D printing room, and even at other locations, engineers are seeing more possibilities after receiving parts from Trent and Flores. “Before we had the Form 3L, some of the engineers wouldn’t think about making a prototype of their ideas, but now that they have the tool, they think, ‘okay, maybe we can test this,’ and they come up with a new way of looking at things,” says Flores.
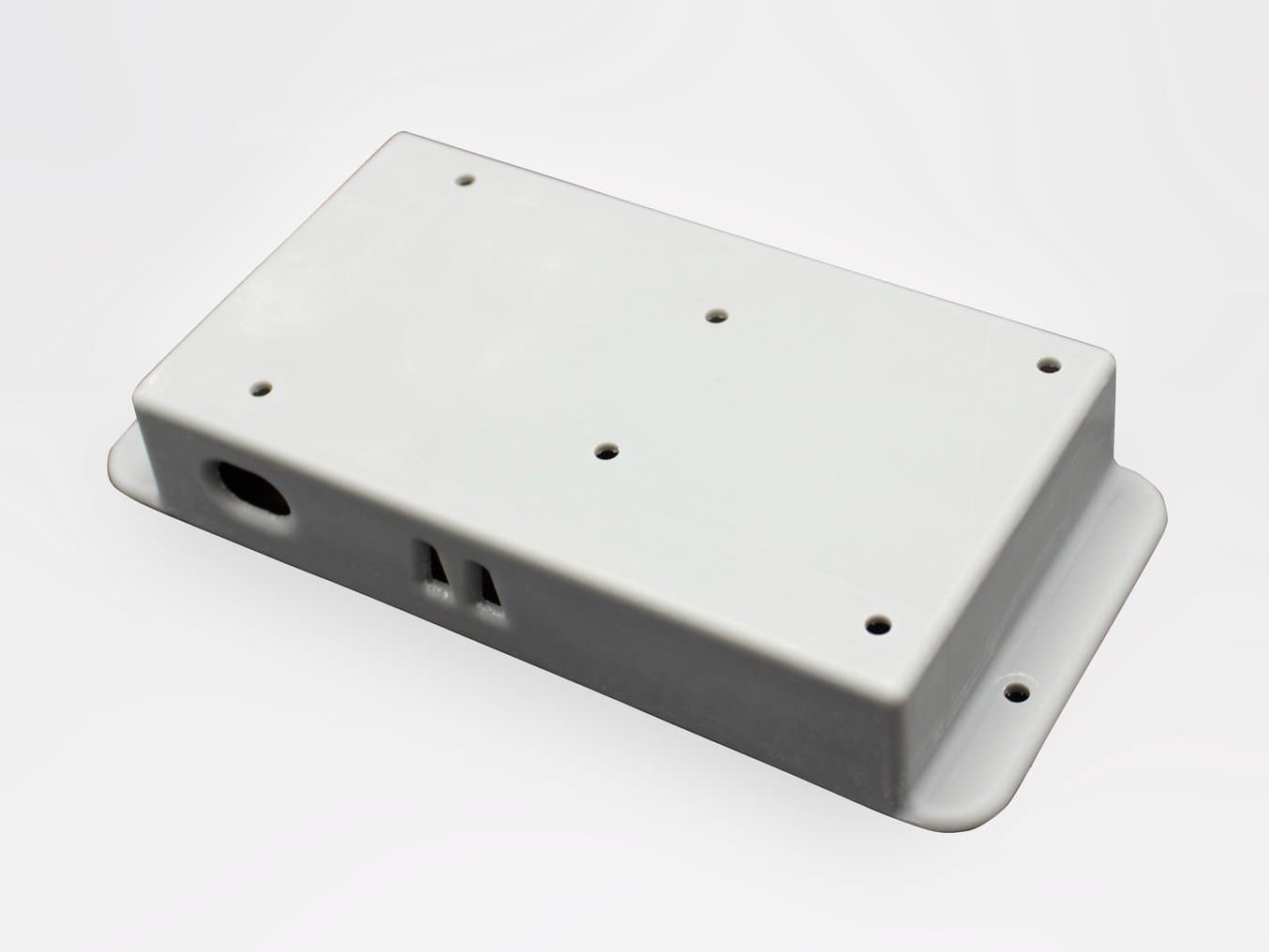
This electronics box (E-box) cover, printed in Rigid 10K Resin, was prototyped on the Form 3L for use in a new product line.
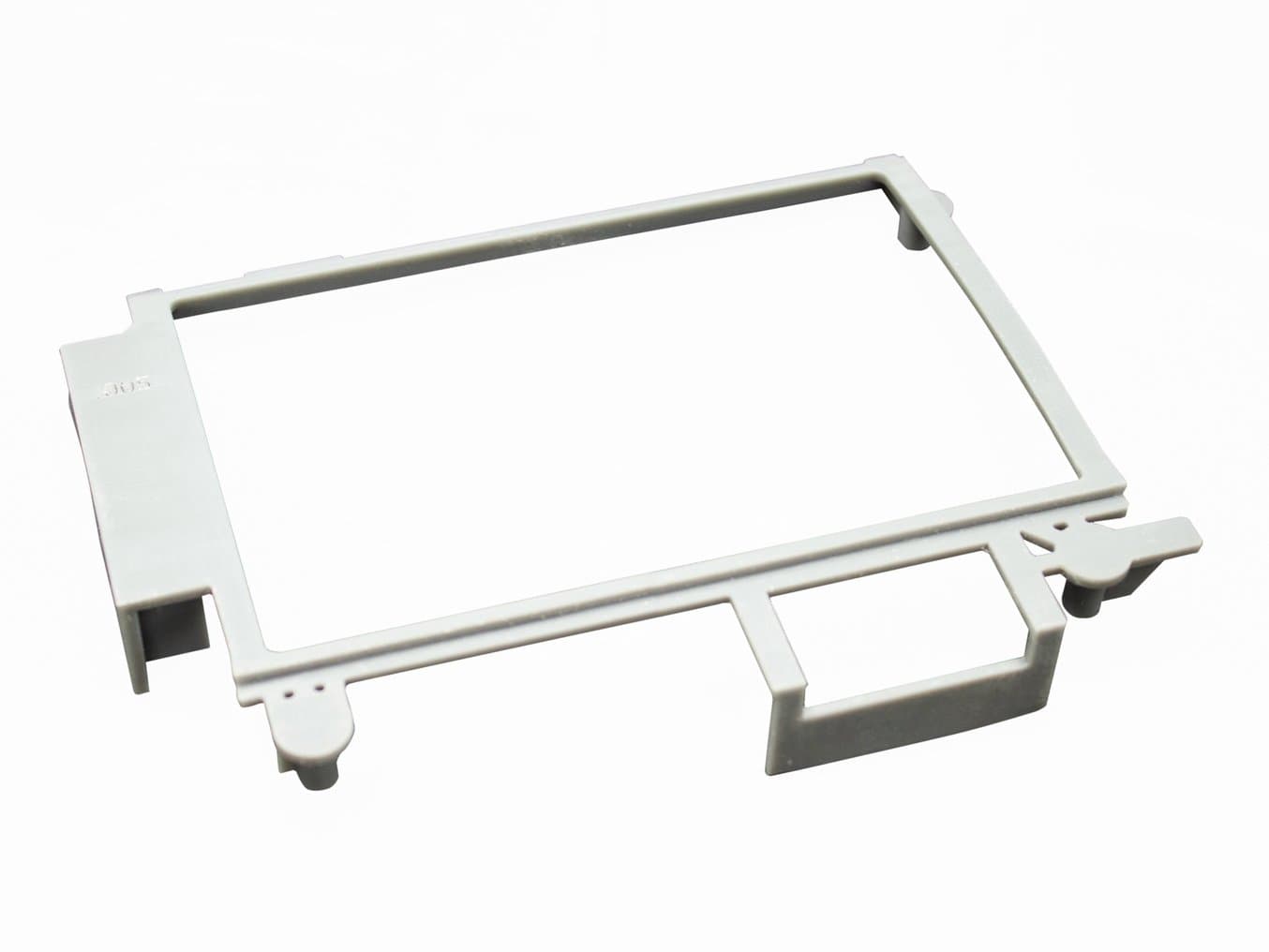
This user interface (UI) frame, also printed in Rigid 10K Resin, was used for internal testing to determine clearances related to form, fit, and function on a larger part.
Trying something new used to involve a lot of paperwork — a request would be made, then justified and approved before a requisition was created. Waiting for the part from an outside vendor could take weeks, and the extended timeline was stifling creativity. After seeing consistently high-performing parts coming from the in-house Form 3L, electrical engineers, designers, and even interns are pushing the boundaries on performance, and people are getting excited. “We used to only send something to an outsourced 3D printer that I really needed, but now we have more room for research and development. The team feels open to the creation and innovation,” says Flores.
As Friedrich has shown, it takes dedication to develop industry-leading products. The Form 3L can help designers and engineers increase their iterative speed for a wide variety of components by utilizing the extensive materials library. In addition to prototyping, 3D printing provides a low-cost solution to customization in manufacturing aids, such as Friedrich’s probe housing. To learn more about the Form 3L, visit our website.