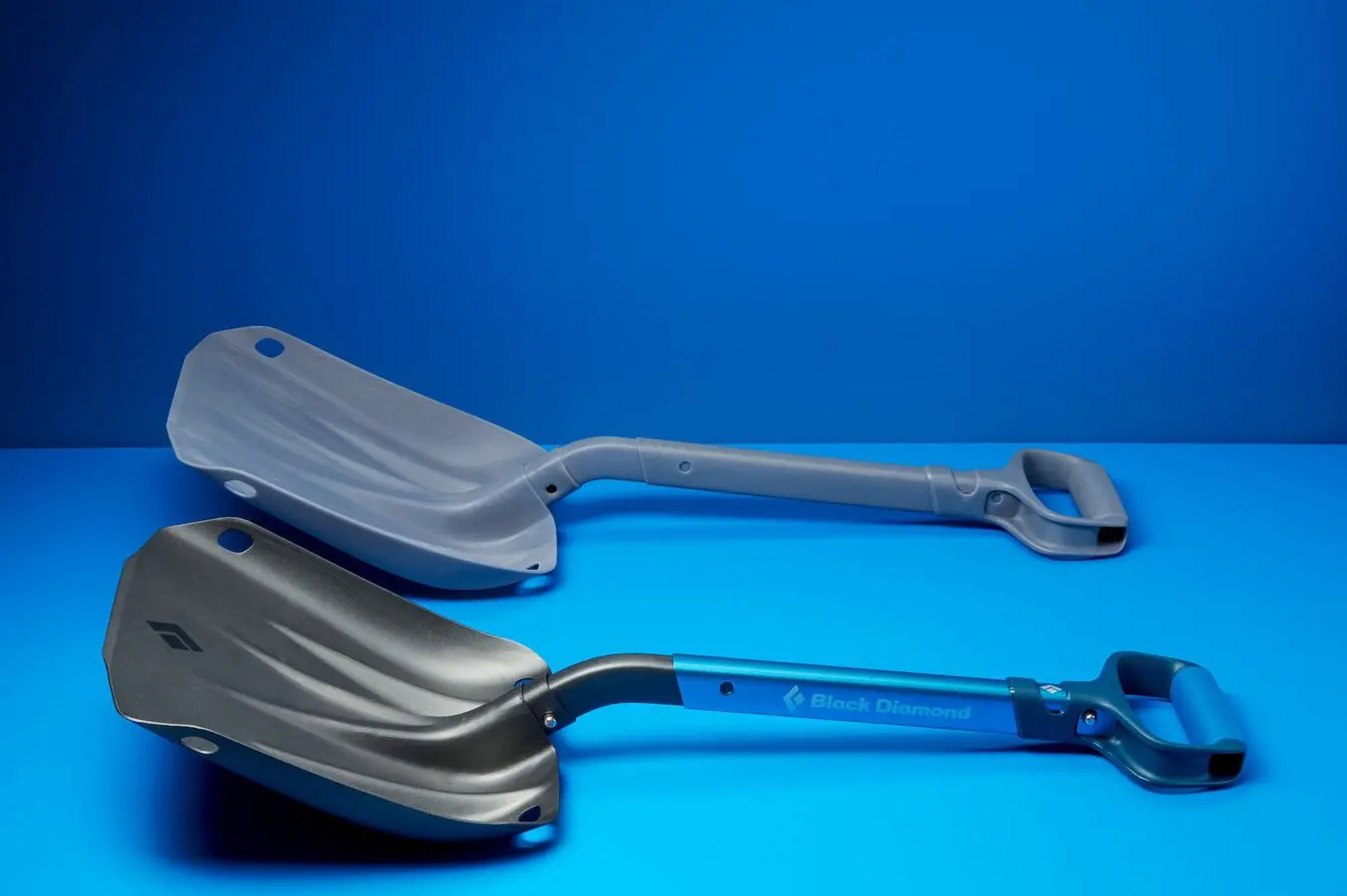
Black Diamond Equipment has one deal-breaking requirement for people to work on their design team — unbridled, infectious enthusiasm for the gear they’re making. For the outdoor climbing and mountaineering experts who go to work at Black Diamond every day, it’s not a hard demand to meet.
The Black Diamond design team is obsessed with the details and holds their gear to an extremely high standard; creating reliable, high-performance gear ensures safety and enjoyment, even while hanging off a mountain cliff. They have similar standards for the tools they use in the design process and have grown their 3D printing fleet over the years to include large-format resin 3D printing, a fleet of desktop resin printers, and in-house selective laser sintering (SLS) technology.
Product Design Lab Manager Matt Tetzl spoke with us about the Black Diamond design process and how using Form 4, Form 3L, and the Fuse Series has helped them spend more time testing their products in the Wasatch Mountains, and less time waiting in the lab for prints to finish.
High-Volume Printing and Testing for High-Performance Gear
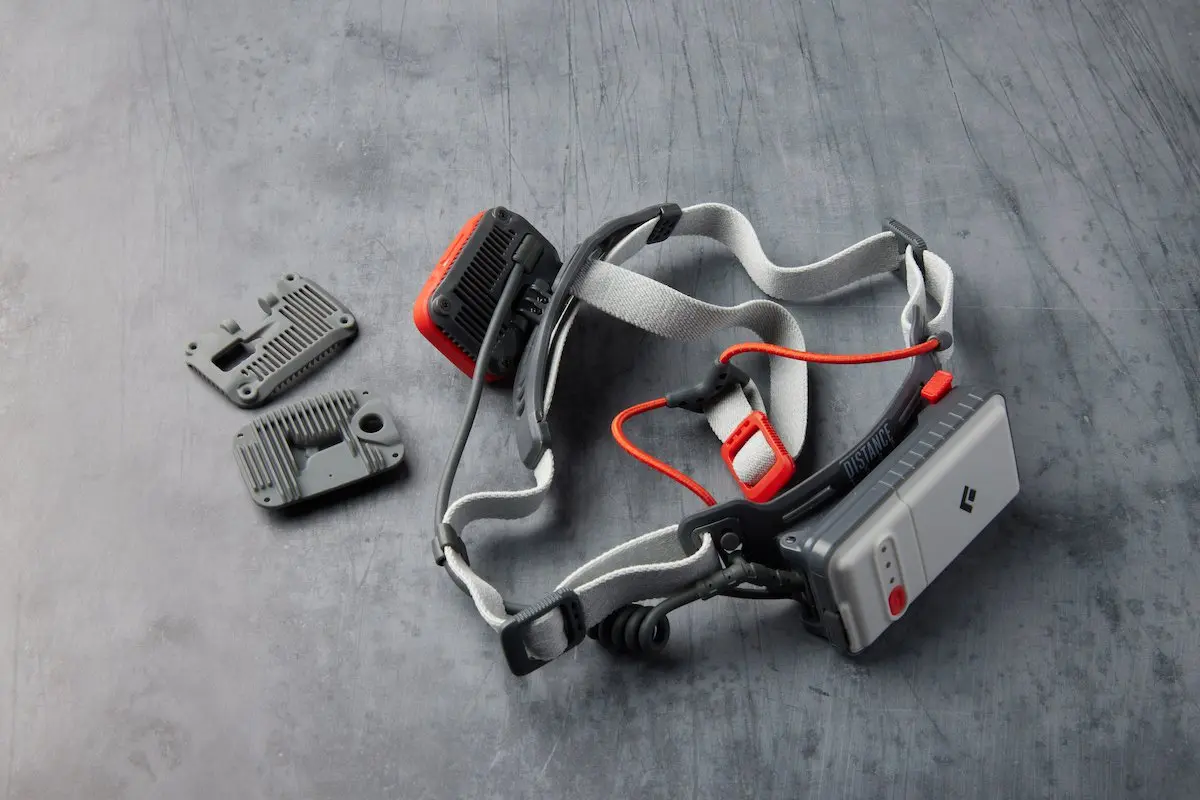
Form 4’s speed enabled Tetzl to run three different iterations of this headlamp component (left, Grey Resin V5) in a day.
Black Diamond’s design team has to make sure that their products are up to the challenge of helping a new climber get comfortable or a professional hit a new record. That commitment means extensive testing — millions of cycles for some products. To handle that volume of testing, the 3D printing lab is working around the clock. “We have printers, both SLA and SLS, running every day,” says Tetzl. “My whole thing is promising next-day delivery of parts.”
Tetzl manages incoming requests for multiple teams for both resin and powder 3D printed parts using Dashboard, Formlabs printers’ online print management system. Though he had been sending most parts for functional testing to the Fuse Series, printing them in Nylon 12 Powder for its strength and durability, Form 4 provided an incentive to switch back to resin for many parts. “We’ve been running the Fuse every day since we got it, but with the Form 4, we’ve been getting back into resin printing. I can get parts back to people on the same day they request them.”
Same-day delivery of early prototypes or end-use functional test prints is a huge advantage for the design team. “For design reviews, it’s been really awesome. Instead of having a printing day and a testing or iteration day, we can do it all in one,” says Tetzl.
“On one lighting project, we did three iterations in a single day — designed and printed three different parts before we had a meeting in the afternoon.”
Matt Tetzl, Product Design Lab Manager, Black Diamond
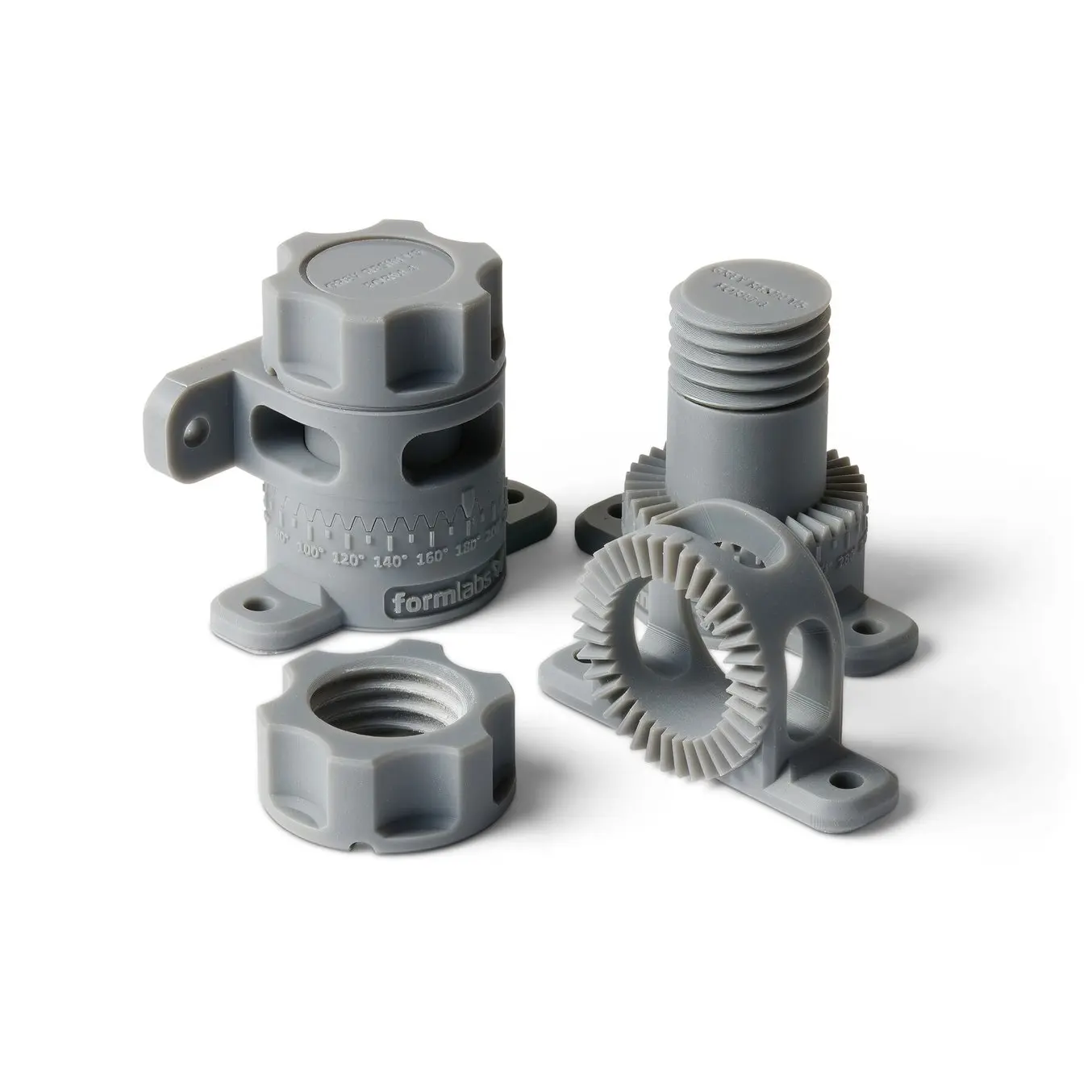
Request a Free Sample Part
See and feel Formlabs quality firsthand. We’ll ship a free Grey Resin V5 sample part to your office.
Reliability in the Lab and on the Mountain
For mountaineering newbies or seasoned climbers alike, the focus should be the trail or rock face in front of you, not worrying whether your gear is up to the challenge. The same goes for working on the design of this gear — Tetzl and his colleagues are focusing on ergonomic design, material selection, fatigue testing, and a host of other factors that go into designing top-of-the-line gear. They can’t worry about whether or not they’ll get a print failure, or if the prints themselves are out of tolerance. The Form 4 has let them keep their focus on the products from the first day they set it up. “It’s been plug and play. As soon as you get it connected to the network, it’s the familiar Formlabs ecosystem — upload parts, push a button, get your parts back,” says Tetzl.
From set-up to integration into the workflow, Form 4 simplifies every process. “It was pretty straightforward. Standard, out of the box, level it, and get started. It feels just as approachable as all the other Formlabs systems I’ve had,” says Tetzl.
Continued ease of use and reliability make sending parts to Form 4 an easy decision. “99% of the time, I know I’ll have a successful print. And the other 1%, I know I can fix it myself. If a printer were to go down, I can get it operating on the same day. It’s super nice to have that reliability,” says Tetzl.
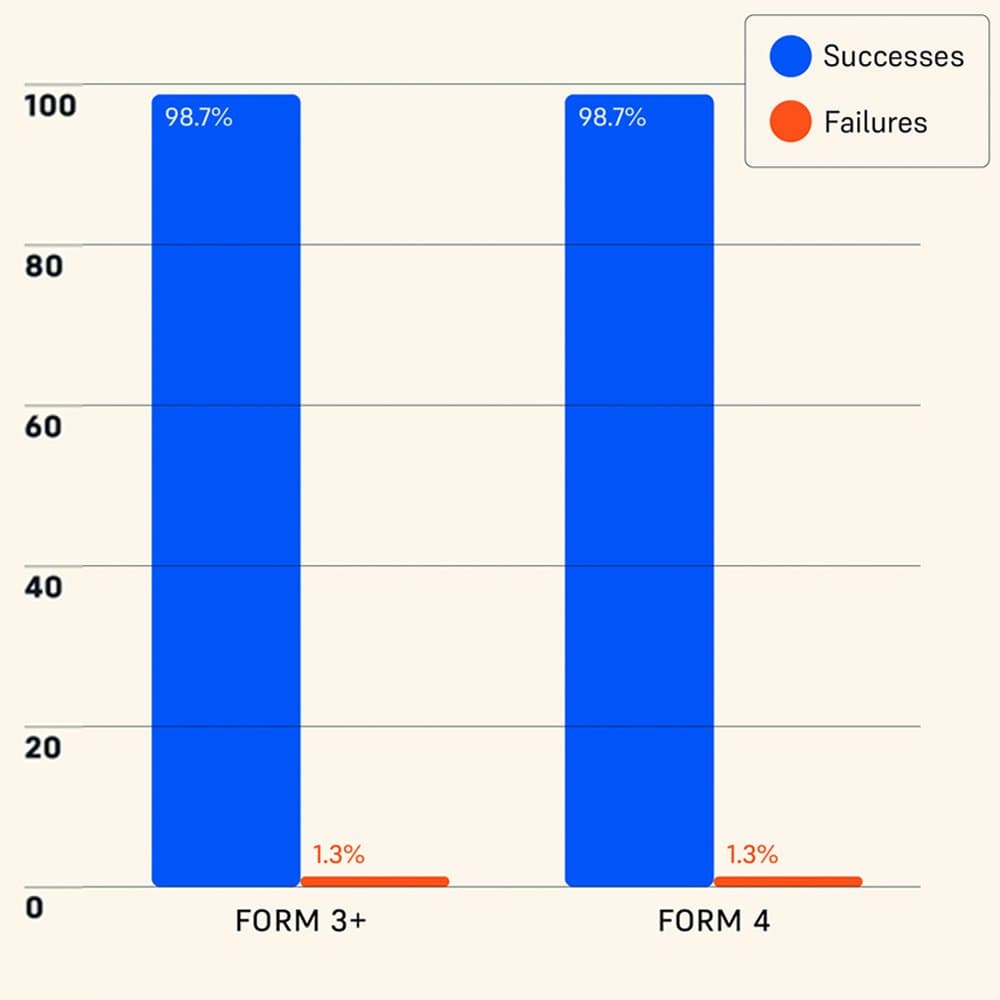
Independently Tested Reliability of Form 4 and Other Resin 3D Printers
Formlabs Form 4 was measured to have a 98.7% print success rate by an independent global leader in product testing. Read a complete description of the test methodology and see the results in our white paper.
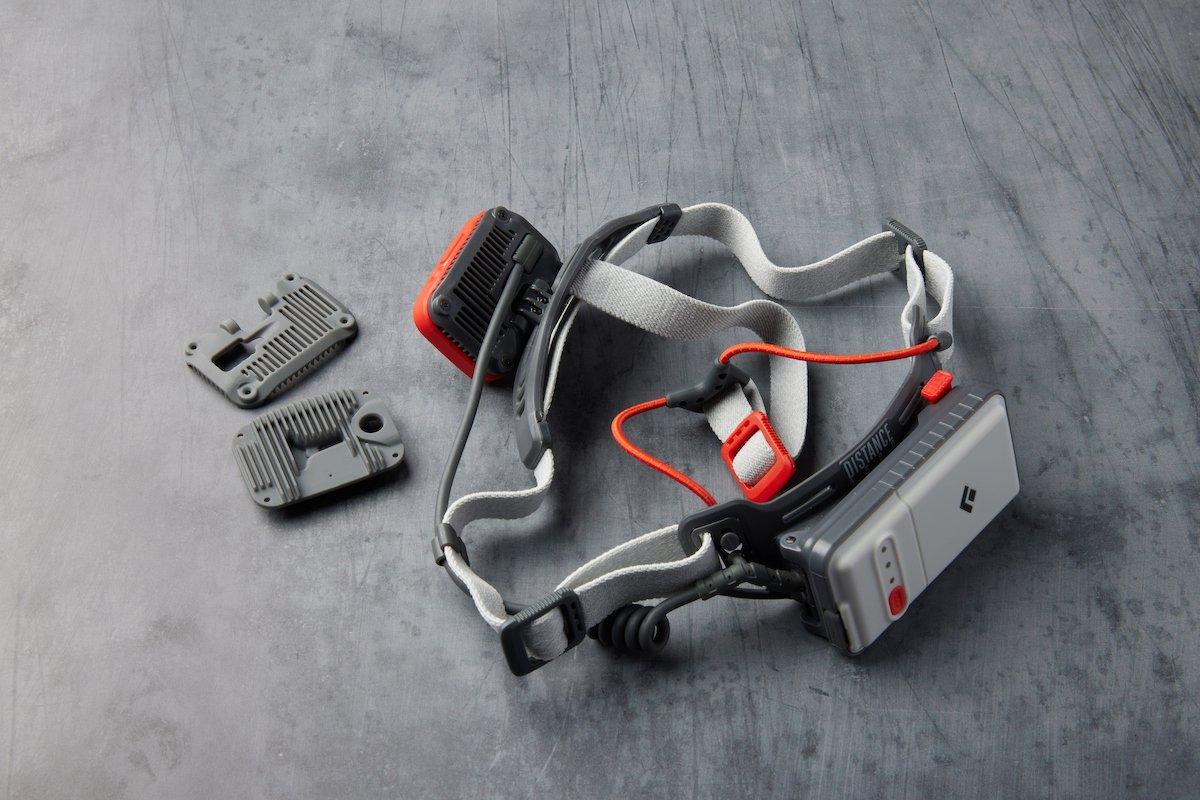
Guide to Rapid Prototyping for Product Development
In this guide, you’ll learn how rapid prototyping fits into the product development process, its applications, and what rapid prototyping tools are available to today’s product development teams.
Materials Matter: Versatility, Accuracy and Performance
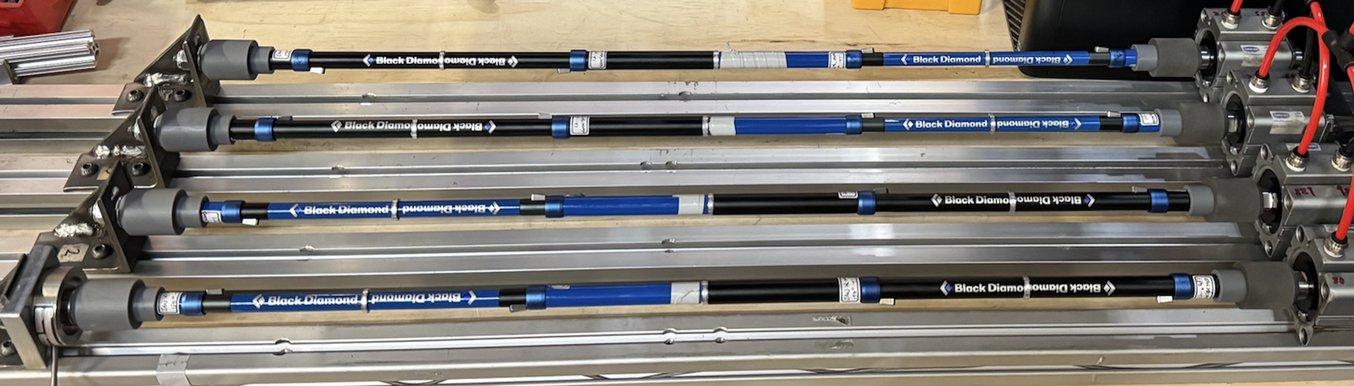
This set-up for fatigue testing a trekking pole uses fixtures printed on Form 4 in Grey Resin V5 (left) and on Fuse 1+ 30W in Nylon 12 Powder (right).
For highly technical products like Black Diamond’s gear, the development process needs to cover a wide range of material properties and extensive testing. One recent product design cycle for a lightweight trekking pole put Form 4 and the new Grey Resin V5 to the test.
They had previously tested the components that go into the trekking pole in Nylon 12 Powder on the Fuse. “Most of our functional testing is in nylon, but we did this fixture on Form 4 because we could try a couple of designs out within hours,” says Tetzl.
Though they were at first unsure if SLA resin could stand up to the extensive pressure and friction testing the trekking pole is put through, the Grey Resin V5 buttons on the pole mechanism lasted for over a million cycles with 35 pounds of pressure each cycle… and then for over a million more. “It’s stronger than previous versions. On helmets we’re seeing more detail than we did on Form 3,” says Tetzl.
That detail is important for the large prototypes of helmets that the team prints on the desktop and benchtop printers — Form 4 and Form 3L. “The surface finish has been really good. The team is really impressed with all the parts we’ve printed off for them on Form 4 in Grey Resin and Clear Resin.”
Expanding the Footprint of What’s Possible With Form 3L
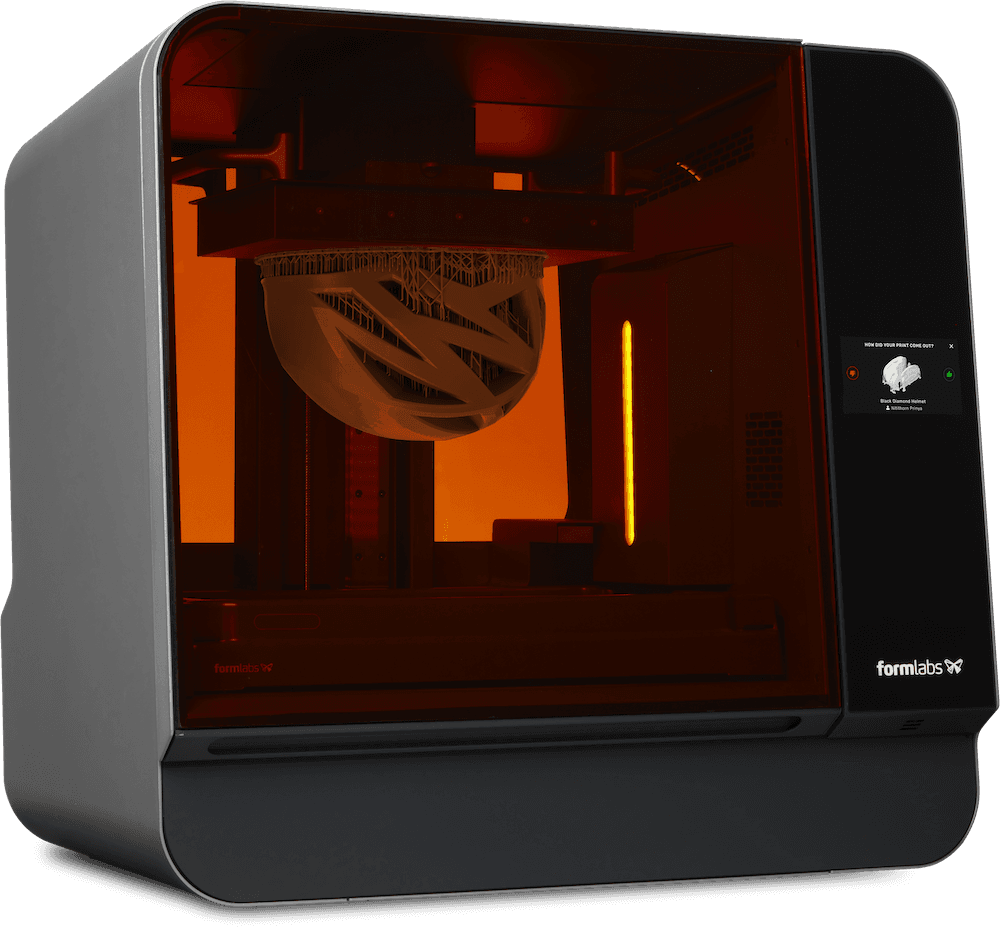
Benchtop resin 3D printing makes human-scale prototypes possible, without sacrificing surface finish or material versatility.
Speed, materials versatility, and surface quality allow the Black Diamond design team to prototype faster, with more control over each step in the process. “We initially purchased the Form 3L with the intent to use it solely for helmet prototyping — we even called it the ‘helmet printer’ for the first few months. Then we realized that we can use it for a number of other projects where it’s super important to have that volume,” says Tetzl.
A few years ago the Black Diamond team took several steps to bring the development in-house of a competitive and highly-technical product category — footwear. They brought in an in-house cobbler, and when the Form 3L was purchased for helmets, the footwear team saw an opportunity. “We realized we can do full-size midsoles with really good detail and surface finish. The footwear team is doing tons of really tiny changes in the midsole design, so having in-house large-format capacity is pretty major for our footwear development,” says Tetzl.
Though the Form 3L may have started as just the ‘helmet printer,’ it quickly turned into a versatile tool that enables a few different projects around the department. For the final stages of an ice tool project, the Form 3L let the team print full-size prototypes so they can test out grip feel and hanging, without worrying about an assembled prototype breaking apart in mid-air. After four years of design versions, large-format resin 3D printing in-house sped up the final iterative stages.
“With ice tools, you can look at it all day, but it’s going to come down to grip feel. Being able to 3D print it and get a rough idea of grip feel and hanging is super important,” says Tetzl.
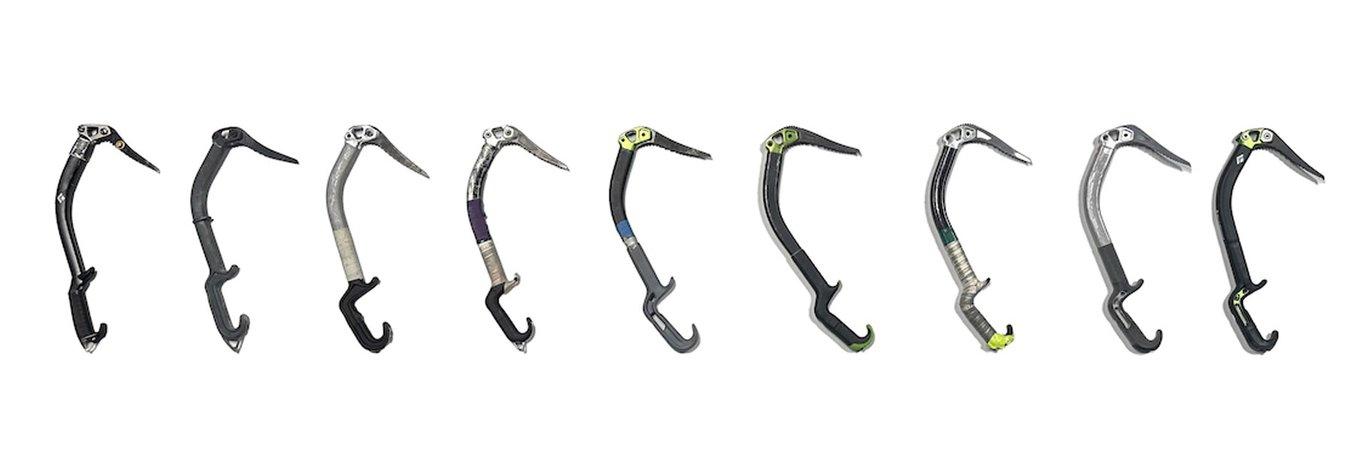
3D printing and in-house SLA and SLS capabilities have made it possible to prototype this ice tool without worrying about assembled components affecting the grip feel or swing.
Specific feedback on the feel of parts also comes down to materials. Though Tetzl prints the vast majority of parts in Grey Resin, he utilizes Clear Resin for making multi-part urethane molds. “We’ve been doing Clear on the Form 3L as our platform for molds, especially when they’re made of quite a few parts. Clear Resin prints super well, and it’s nice being able to see the urethane as it fills the mold cavity,” says Tetzl. The Clear Resin molds get washed and post-cured, then sprayed with a urethane mold release before injection and a 15-minute set time. In-house 3D printed molds can enable a fully functional prototype with softer materials, like urethane, that are UV resistant, without having to outsource tooling.
Before bringing large-format 3D printing in-house, outsourcing molds and large-format prototypes like the helmets was expensive and added additional lead time to the design process. Now, having more control over the workflow for helmets, footwear midsoles, and molds keeps costs low and lead times even lower.
In-House Nylon Parts for Field Testing and More
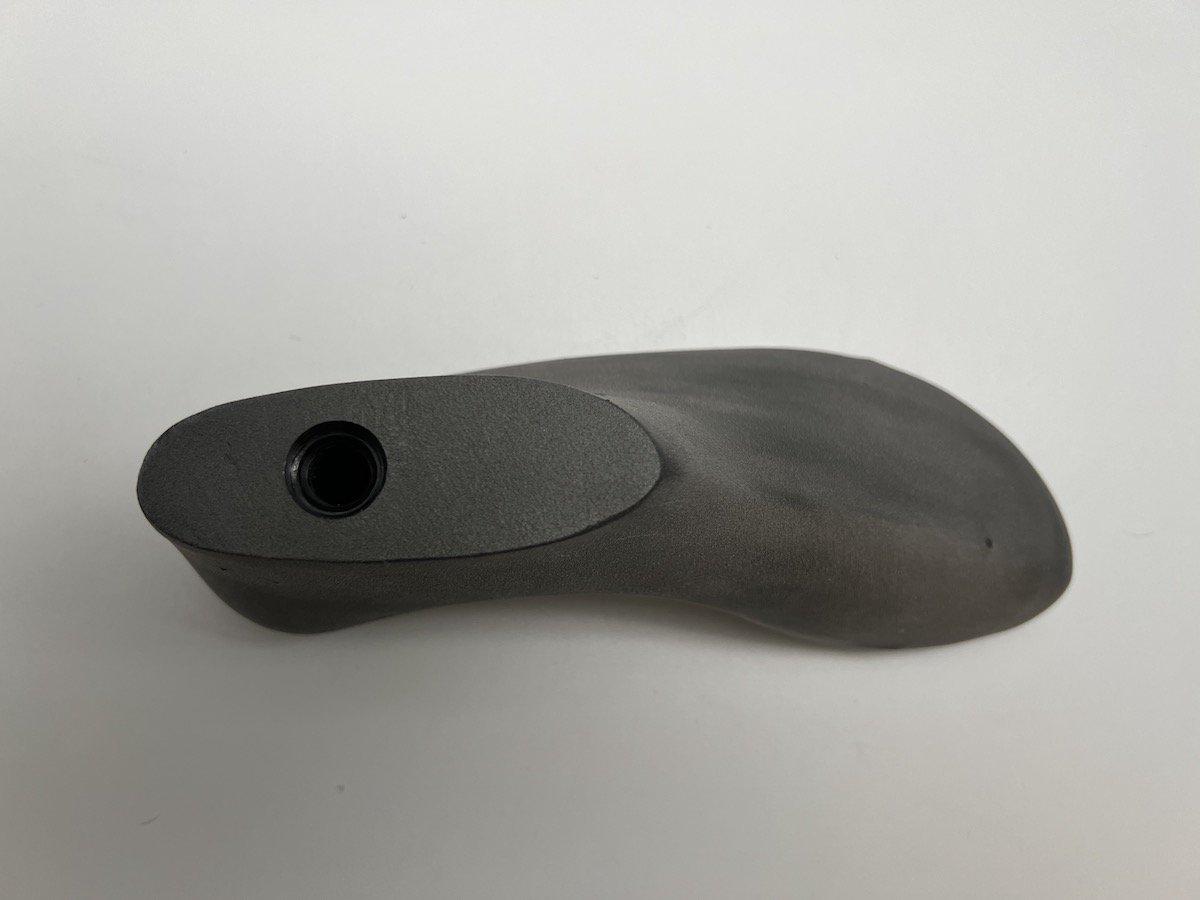
This shoe last printed in-house in Nylon 12 Powder on the Fuse 1+ 30W cuts costs — outsourcing lathed nylon like this could cost up to $2,000, but costs just $65 to print in-house.
In addition to large-format resin 3D printing, Tetzl’s team brought SLS 3D printing in-house as well. After conducting design reviews with resin, they used more durable, end-use materials for functional testing in the field.
Tetzl had been sending parts out to a 3D printing service with an MJF printer, but the costs were steep. “It was the same process using the same materials, so it made sense to bring in-house, to speed things up and bring down the cost. It’s been exactly what we wanted, we’re getting most parts 80% cheaper,” says Tetzl.
It’s important that these field-testing prototypes can withstand some heavy impact and rigorous use. Nylon 12 Powder’s strength and durability have let the Black Diamond team use prototypes in their favorite environment — outdoors on a mountain. At the 2023 Ice Climbing World Championships in Edmonton, Canada, a competitor was using an ice tool with a grip printed on the Fuse 1+ 30W in Nylon 12 Powder. At one point, the tool fell 80 ft to the ice below but survived the impact without any cracks or damage. “We’ve had functional components in skis, made internal components for a drop-tester that have to take considerable load repeatedly. We can finally do high-strength 3D printed parts in-house,” says Tetzl.
The Fuse 1+ 30W helps bring down footwear development costs. Their in-house cobbler uses large lasts, typically lathed out of nylon, during the shaping of the shoe or boot. The team had previously been getting these large parts from a service, but printing them in Nylon 12 Powder on the Fuse 1+ 30W brings down costs from $2,000 to just $65, and reduces lead times. “The Fuse has been an enabler for scaling up what we’re doing in nylon for our new footwear projects.”
With the Fuse 1+ 30W running almost daily at 15% to 20% packing density, SLS 3D printing is an efficient and cost-effective way for Black Diamond to scale their footwear development and increase their functional testing capacity.
Adding Capacity With Form 4
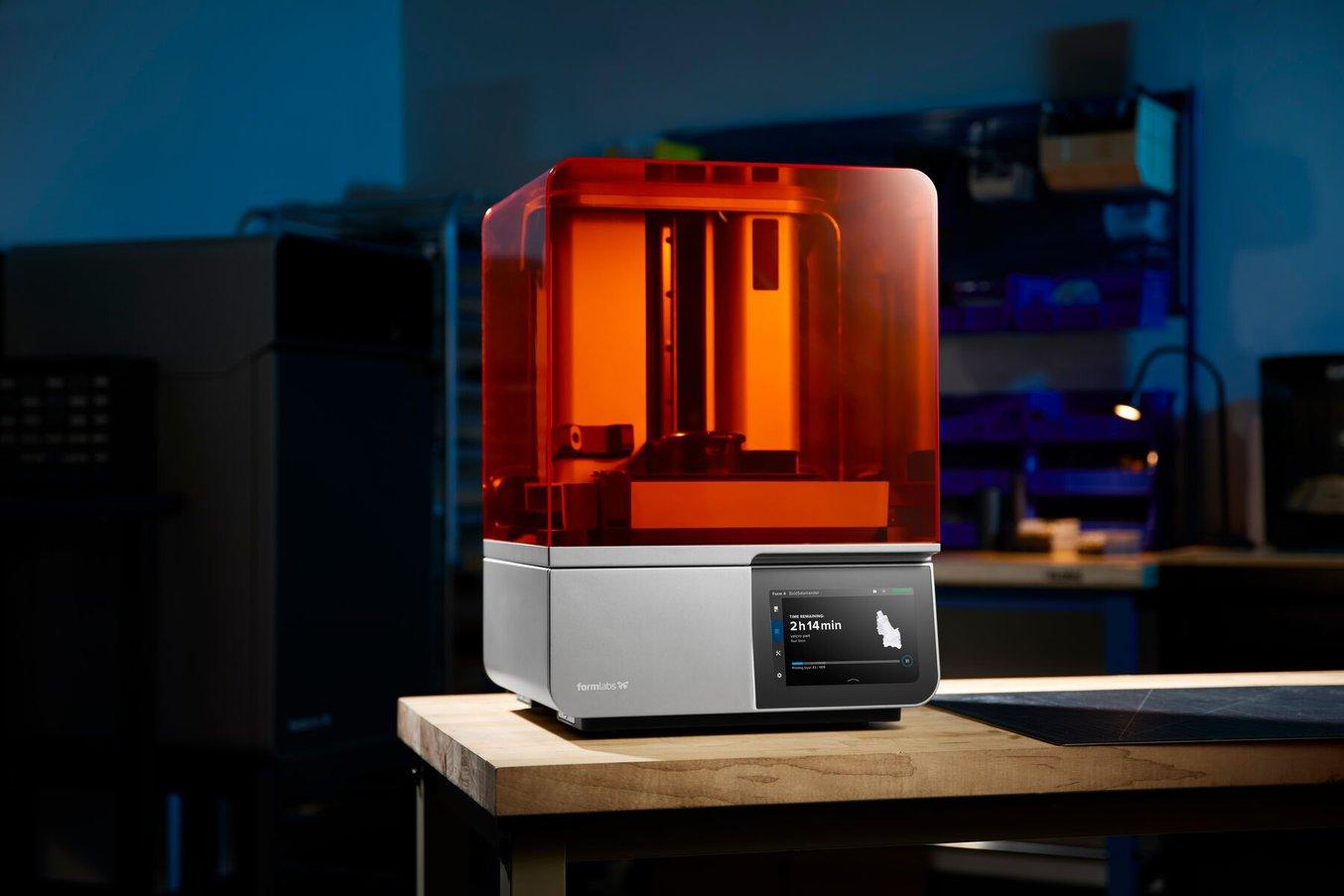
Form 4’s reliability and speed make it a valuable addition to Black Diamond’s 3D printing fleet. Printing multiple iterations a day helps the team spend less time waiting for parts and more time dreaming up the next big innovation in mountaineering gear.
With hundreds of products and a print queue that never seems to get shorter, Tetzl needs reliability, speed, and consistent quality from his 3D printers. Black Diamond has bet on Formlabs printers again and again, creating a workflow around the Form 2, Form 3, Form 3+, Form 3L, Fuse, and now Form 4. For gear that climbers, hikers, and mountaineers trust with their leisure, and sometimes their lives, the Black Diamond design team has to have tools they can trust as well. That reliability can’t be compromised, even for speed or materials range, but Tetzl has found it to be the same system he’s gotten familiar with.
“We haven’t had a single failure on the Form 4.”
Matt Tetzl, Product Design Lab Manager, Black Diamond
Form 4’s speed lets the Black Diamond team spend as much time as possible doing what they love most — testing out their industry-leading products on the Wasatch Mountains, and less time waiting for prints.