The drone industry has many distinct requirements, a major one being the ability to combine extreme ruggedness and durability with lightweighted components. Success in the this relatively new industry relies on the ability to manufacture in new ways, and drone companies that excel are using additive manufacturing for its ability to provide unique solutions.
heliguy, one of the UK’s leading drone specialists, has long been exploring how they could integrate 3D printing into their design, product development, and manufacturing processes.
Learn from Ross Embleton, Lead Product Designer, how heliguy was able to streamline its product development process and bring manufacturing in-house — improving lead times, reducing costs, and gaining more control over its workflows with stereolithography (SLA) and selective laser sintering (SLS) 3D printing technology from Formlabs.
Flying High and Wide
Since the company’s inception in 2008, heliguy has focused on driving innovation in the drone industry, providing businesses of all sizes with expert support and training. As the adoption of drone technology has evolved, the breadth of heliguy’s customer base and the variety of applications has grown exponentially.
Independent businesses in the construction industry fly drones for quoting building repair jobs faster and safer, agricultural corporations to monitor large swaths of land, police and defence organisations for search and rescue operations, entertainment industry giants such as the BBC for filming, and scientists and researchers to reach remote or treacherous areas. The sky really is the limit when it comes to heliguy’s client base. With the applications seemingly boundless, more sectors are adopting drones into their workflow.
Leading Innovation With In-House 3D Printers
With drones predicted to contribute up to £45bn to the UK economy by 2030, heliguy has focused on consistently increasing their capabilities and leading innovation in this rapid-growth market.
They created an in-house lab, heliguy Lab, that includes a design department and in-house manufacturing for creating add-ons for drones to enhance their capabilities. A significant investment in 3D printing technology has enabled heliguy Lab to conduct onsite product development and manufacturing at a commercial-grade level.
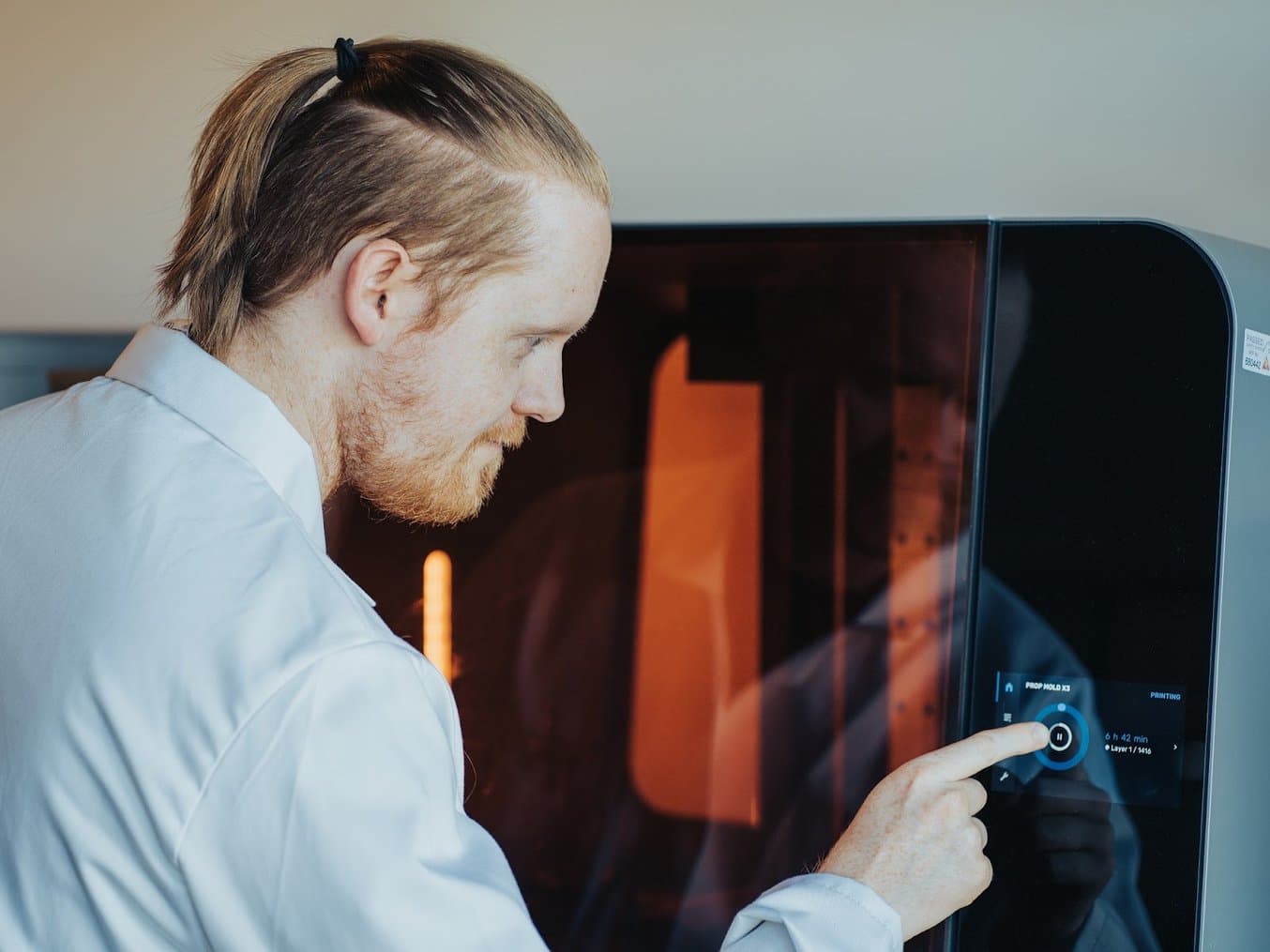
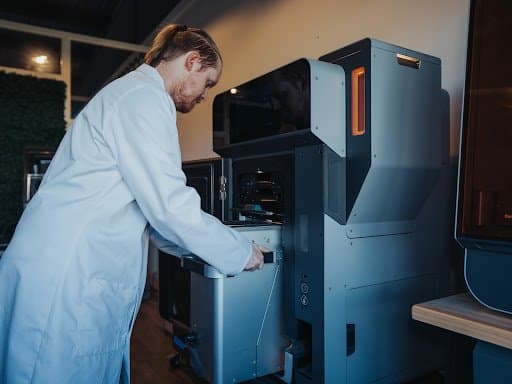
heliguy’s team runs both 3D printing processes that Formlabs offers, using a Form 3L large-format SLA and a Fuse 1 SLS 3D printer.
As with all rapid-growth markets, the ability to deliver on customer needs as quickly and efficiently as possible is a huge focus. 3D printing allows heliguy to produce prototypes and end-use parts overnight, which represents a considerable competitive advantage in this fast-paced industry.
“Working in the drone industry, one of the main problems that we encounter is lightweighting. Being able to do that traditionally would mean a lot of complex 5-axis milling. Whereas with 3D printing, we can just make the part in one go. Time is also a massive thing for us, being able to run something overnight and not have to wait weeks to get parts back has been a huge advantage for us.”
Ross Embleton, Lead Product Designer, heliguy
Finding the Right Technology Partnership
“When we first looked at buying 3D printers, one of the questions that we had was, who do we align ourselves with? We're quite fond of following a particular brand and staying within that ecosystem. Formlabs have such a wide range of fantastic technology, it was very difficult to ignore them,” said Embleton.
During the research phase of the 3D printing implementation and integration into their business, heliguy worked with Formlabs UK Partners SolidPrint 3D and Additive-X, and had multiple test parts printed on both the Form 3L large-format SLA 3D printer and the Fuse 1 benchtop SLS 3D printer.
“[As] soon as we got the parts back, we knew immediately that Formlabs was going to be our choice. And the support that we got from SolidPrint 3D as well was fantastic. So we couldn't ignore that,” said Embleton.
Unlocking the Power of Additive Manufacturing
Having previously outsourced the majority of its production, heliguy is now leveraging additive manufacturing to create end-use parts in-house, speeding up and refining its workflow. Moving the production in-house meant that the team has been able to increase quality and drastically reduce lead times. Most importantly in their industry, they now also have more control over production, for example when it comes to adapting designs and optimizing for reducing the weight of certain parts.
The team has unlocked the power of designing for additive manufacturing, which has allowed them to increase the complexity of their products, without incurring excessively high costs.
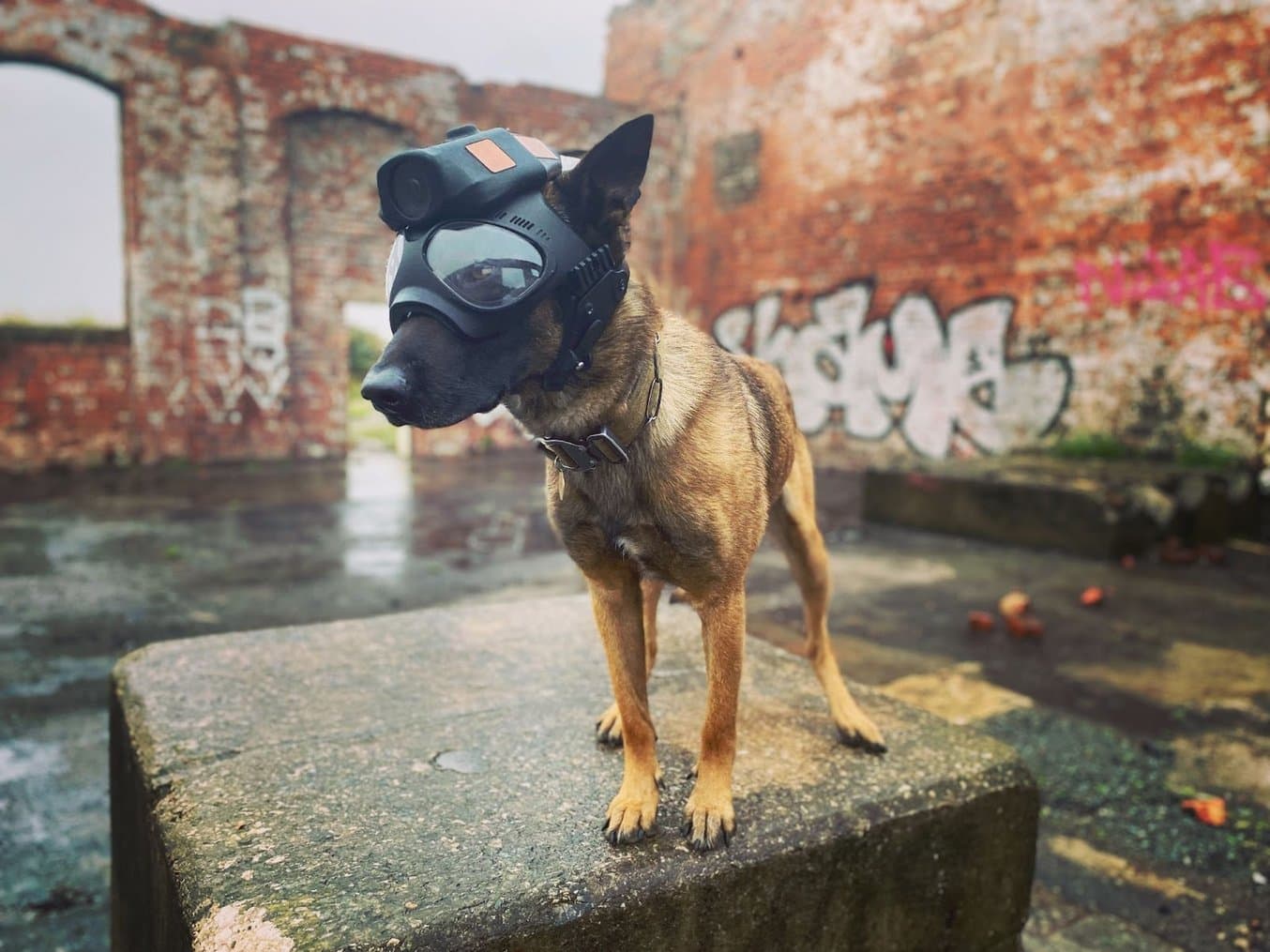
The tactical dog camera is built on technology from the drone industry, combined with SLS 3D printing.
For example, one of the latest unique projects heliguy’s team developed was a tactical dog camera to provide police with vital situational awareness. The dog camera benefits from advanced camera and image transmission technology from the drone industry.
The impact-resistant tactical helmet worn by the dog with a camera and SLS 3D printed parts combined into a custom assembly. The design freedom of SLS 3D printing and the materials enable a lightweight construction, with the camera module and housing weighing less than 500g. heliguy’s team can produce the camera housing in-house, on-demand, which means that they can control the quality and speed of production.
“Using 3D printing technology has enabled us to have the freedom to design parts in ways that we couldn't do any other way.”
Ross Embleton, Lead Product Designer, heliguy
By integrating 3D printing and bringing the Formlabs SLA and SLS ecosystems in-house, heliguy has increased its ability to spec parts, and benefit from previously unattainable manufacturing insights, so it can now deliver custom components that exceed its customers’ expectations.