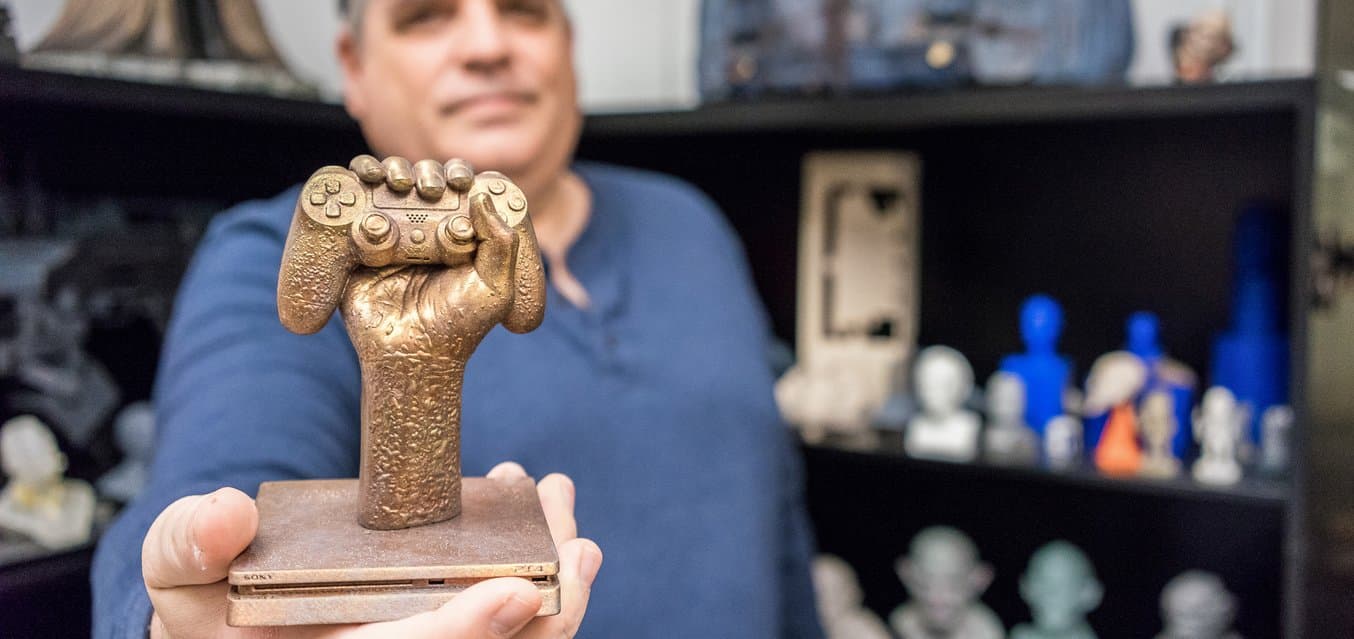
In Gary Barth’s line of work, a successful pitch comes down to the details. Nailing the likeness of a character’s face could make or break a project.
“Game designers are extremely particular about their characters and how they’re displayed, so the accuracy is really important,” said Barth, senior manager of the Fabrication Arts and Design group at PlayStation.
Barth is the man behind some of the magic that brings video games to life, having a hand in countless collectibles, promo items, costumes and props for live action trailers, which allow fans and players to interact with the characters, storylines, and games they love.
While Barth has a rolodex (look it up, kids) of talented artists and vendors who he works with to make many of these creations, he does have a small workshop on the PlayStation campus where he can produce prototypes of collectibles fairly quickly.
In 2016, he began using desktop stereolithography (SLA) 3D printing to prototype and create proofs of concept to help shorten the distance between idea and product.
Juggling Projects as a One-Man Team
Barth began his career at PlayStation decades ago, helping shape the multimedia department.
“We were at the point where we wanted to start bringing set pieces and props into our behind-the-scenes videos. Then people starting asking for other things for trade shows, contests, promotional items–it sort of blossomed into what I do now,” Barth said.
Now, Barth manages projects that include designing collectibles based on PlayStation games and creating set pieces for a variety of PlayStation events. Often, these creations begin as loose concepts.
“Someone will come to me with an idea—sometimes a clear vision and other times more abstract–and it’s my job to help bring the project to life in a way that accurately represents the in-game characters and items,” Barth said.
The flexibility of in-house 3D printing helps Barth quickly develop these ideas.
Rapid Prototyping, From Idea to Winning the Pitch
For confidentiality reasons, Barth often can’t send early models to outside vendors, so the ability to prototype high-resolution models in-house is crucial.
Last fall, Barth wanted to make a 20-inch statue of Nathan Drake, the protagonist in PlayStation’s Uncharted video game series. In order to move forward, he needed to successfully print Drake’s face.

“There’s something that happens between looking at a likeness on screen and looking at a 3D print. Sometimes it just doesn’t translate as well as you would think, which is why some collectible statues look nothing like their on-screen character,“ Barth said. "Having the ability to 3D print on-site is awesome because it allows me to easily provide that visual.”
Barth used the Form 2 to 3D print the detailed model of Drake’s head. He had previously used a fused deposition modeling (FDM) machine and a PolyJet, but chose to work with the SLA printer for its detail, easy post-processing, and lower material costs.

“Because my work area is in the center of a corporate building, I couldn’t get a water source and drain near the PolyJet printer, so a WaterJet option was out. I would have to clean the prints by soaking them overnight, and then spend hours with steel wool and sandpaper trying to get the support material and build lines off of them,” Barth said.
“If you’re making collectible statues, the minute you start sanding, you’re softening detail. With the Form 2, you snap the support material off pretty cleanly and with a little light sanding, you’re ready to primer.”
Prototyping in-house with SLA desktop 3D printing can also be extremely cost-efficient. Barth was able to design a trophy for an employee awards ceremony for a fraction of the price and time of outsourcing–even using the same printer.

The Future of Fabrication Arts
As 3D printing technology evolves, Barth sees wider adoption for professionals and hobbyists alike. Overall, it’s all about achieving the balance between quality of output and quality of experience.
“It’s been amazing to see the advances in print technology over past five years in terms of resolution,” Barth said. “Speed is important to a lot of people, but for me it’s not as big of a deal. The ease of cleanup, the cost of machine, the cost of materials–those are becoming more affordable, and are what make the day-to-day difference.”
Painting Tips and Tricks
To learn more about achieving professional polished finishes on 3D prints, check out our two-part series The Ultimate Guide to Painting 3D Printed Parts for a step-by-step how-to filled with heplful tips and techniques.