Now Available: True, High-Performing Polyurethane Parts Produced by Desktop 3D Printers
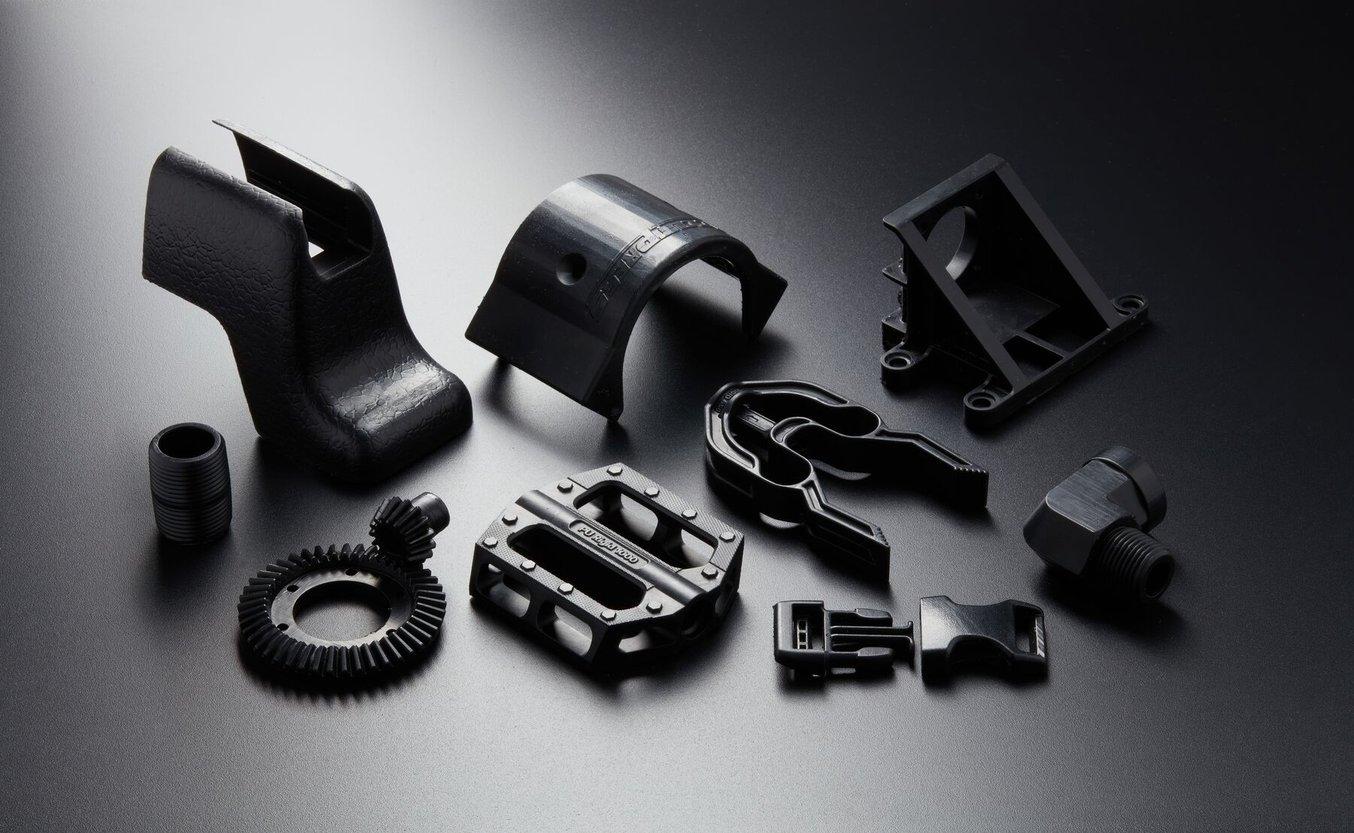
Formlabs is pleased to announce two polyurethane SLA 3D printing materials in our new Polyurethane Resin Family, PU Rigid 650 Resin and PU Rigid 1000 Resin, representing our toughest and longest lasting resins yet.
For the first time, print polyurethane parts in-house on a Formlabs Stereolithography (SLA) 3D printer for models that are durable, tough, and long-lasting, even in extreme conditions. Elevate your 3D printing operation with our high-quality Polyurethane Resin Family that will enable product designers, engineers and alike to break free of the limitations of traditional polyurethane manufacturing with new workflows and applications. Our Polyurethane Resin Family is now comprised of:
-
[New] PU Rigid 650 Resin. Produce tough and pliable polyurethane parts with the ability to withstand extreme impacts and rugged applications while maintaining dimensional accuracy under load.
-
[New] PU Rigid 1000 Resin. Create semi-stiff, sturdy, and unyielding polyurethane parts that repeatedly tolerate high impacts and harsh environments.
-
Rebound Resin. Launched in 2019, Rebound Resin is a production-ready elastic 3D printing material. New Balance used this material in their TripleCell powered shoes.
Keep reading to learn more about the technical details of PU Rigid 650 Resin and PU Rigid 1000 Resin, which applications we recommend for each material, what steps are required to achieve optimal material properties, and how we created a high-performance, printable polyurethane material.
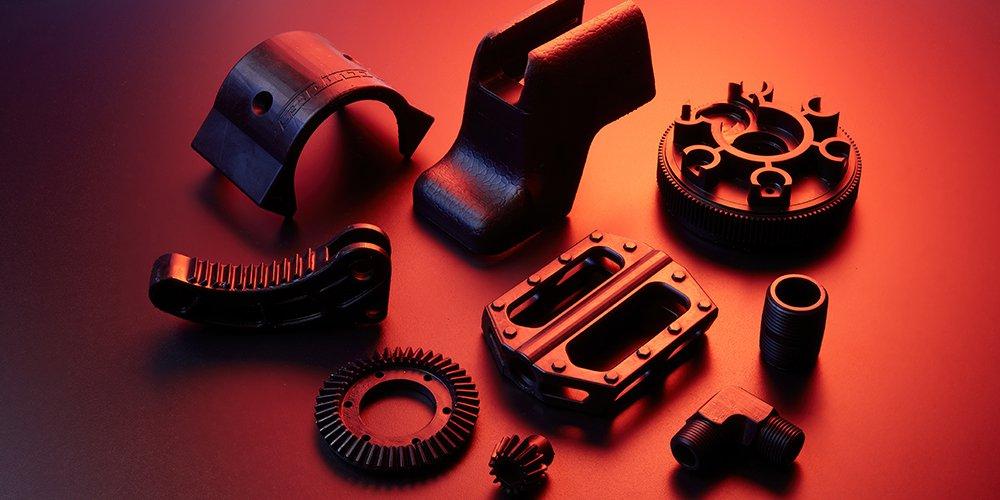
Introducing Polyurethane Rigid Resins: Pushing the Limits of 3D Printing
Join our materials experts as they discuss how the incredible properties of PU Rigid Resins paired with the benefits of 3D printing are eliminating previous limitations of traditional polyurethane manufacturing.
Polyurethane Materials for a Range of Applications
Polyurethane resins are durable, tough, and long-lasting and are ideal for printing parts for all stages of prototyping and end-use production. Traditional SLA resins are produced from acrylate polymers, and thus may experience a degradation in their durability long-term.
However, polyurethane resins are an uncommon 3D printing material because they require a complex chemistry to produce them. After years of testing, the Formlabs materials team settled on a hybrid chemistry. A custom combination of acrylate and urethane in our polyurethane resins enables use with Formlabs’ professional 3D printers, bringing the same standards and quality you would expect from our conventional materials. This hybrid chemistry combined with a humidity cure brings the printed parts to their finished, elevated polyurethane state.
Technical Data - PU Rigid Resins
Property | Formlabs PU Rigid 650 Resin | Formlabs PU Rigid 1000 Resin | ||
---|---|---|---|---|
Ultimate Tensile Strength | 34 ± 3.4 MPa | 35 ± 3.5 MPa | ||
Tensile Modulus | 0.67 ± 0.06 GPa | . 0.92 ± 0.09 GPa | ||
Elongation | 170 ± 17 % | 80 ± 8% | ||
Notched Izod | 375 J/m | 170 J/m | ||
Flex Cycles | >50,000 | >50,000 |
You can view the full technical data sheets here. Now, let’s explore applications where these new materials excel.
Applications for PU Rigid 650 Resin
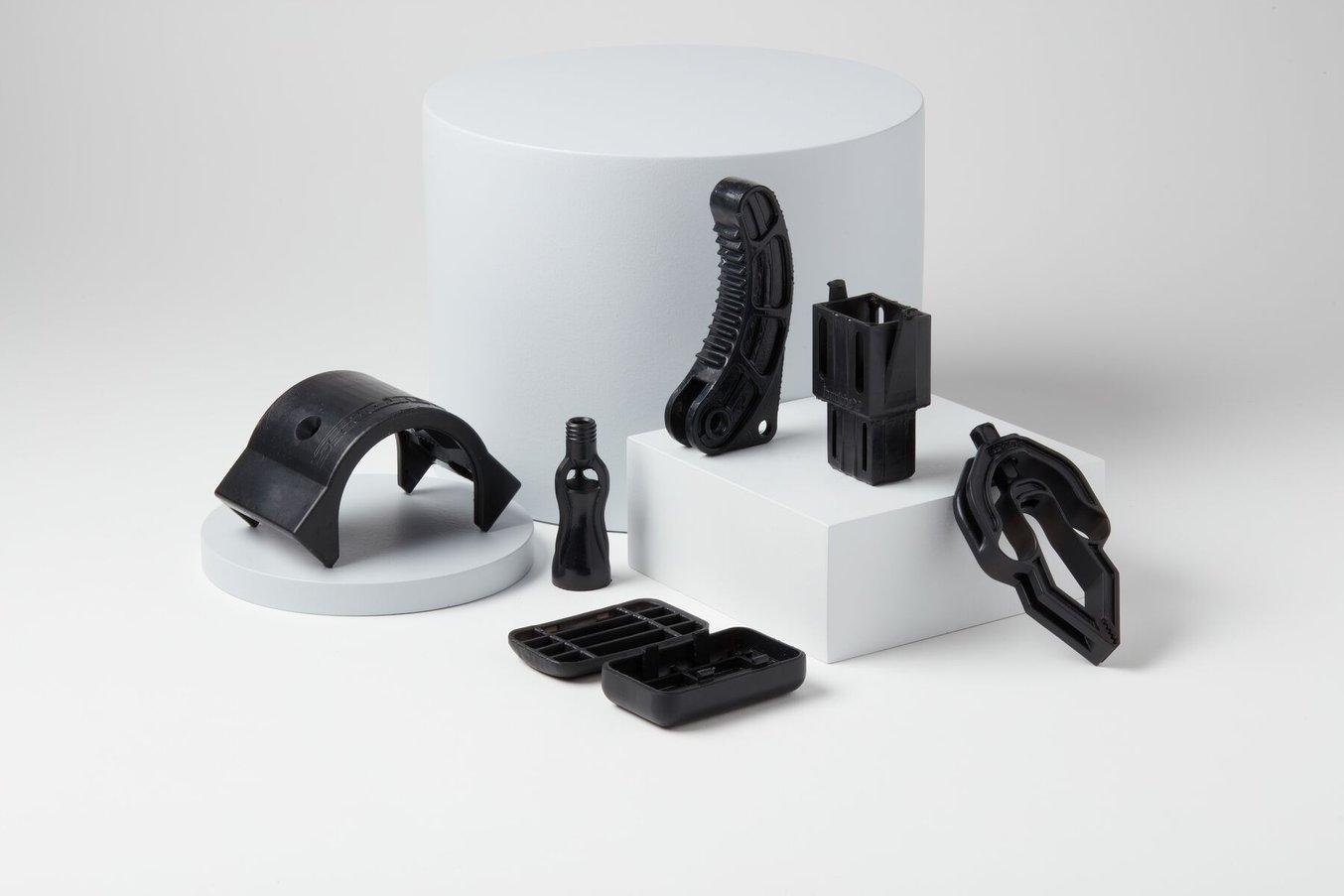
Our toughest material yet, PU Rigid 650 Resin excels when creating parts that can withstand prolonged loading while maintaining their true shape long-term. This includes impact resistant and shock-absorbent parts such as:
- Wheels
- Bumpers
- Grippers and end-effectors
- Dampeners
- Grommets
Oftentimes, the best way to create parts for load-bearing or continuous functional use is to join two parts together. Because PU Rigid 650 Resin holds its form over long periods of use, it is perfect for creating:
- Living hinges
- Assembled hinges
- Snap fits
Applications for PU Rigid 1000 Resin
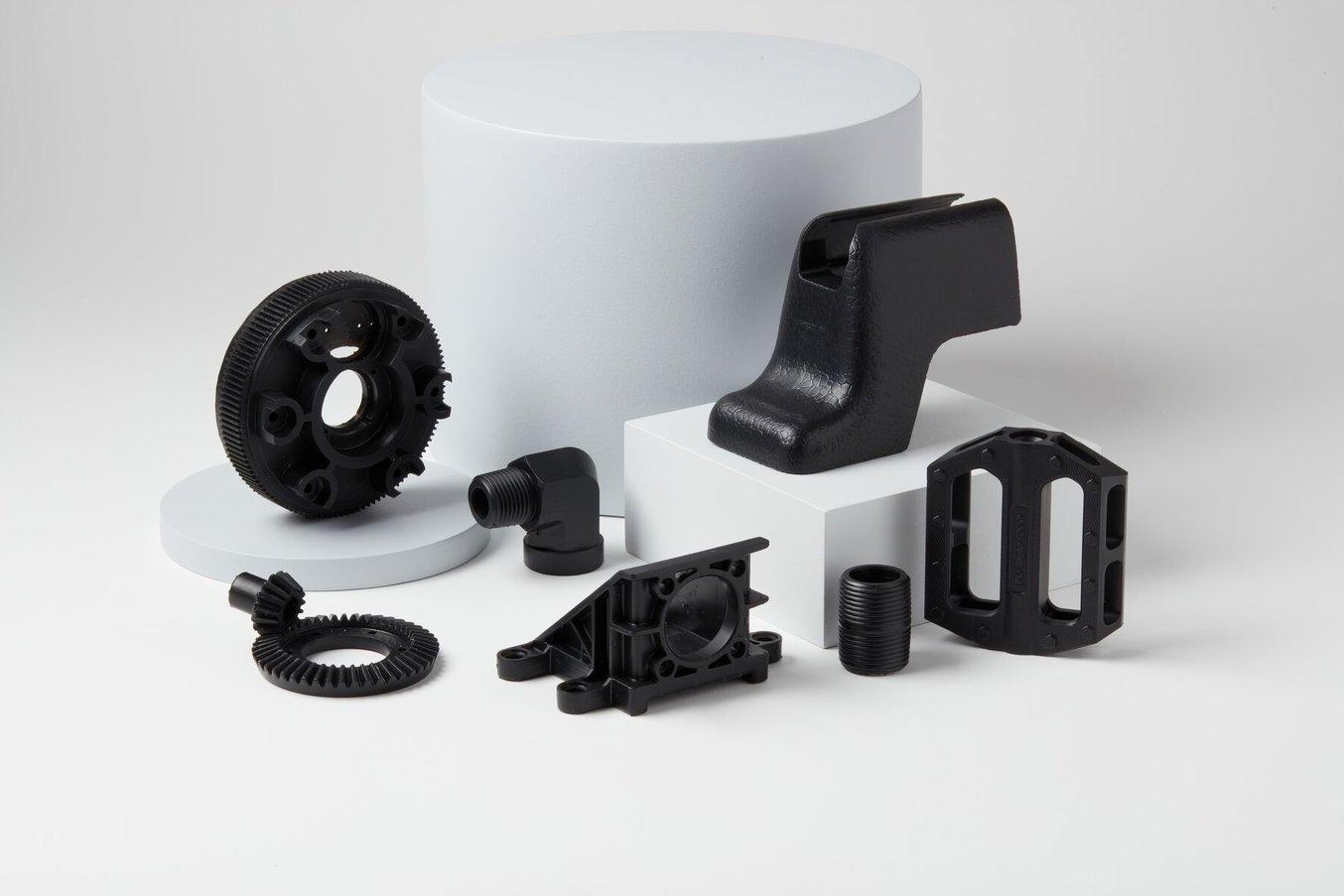
Like PU Rigid 650 Resin, PU Rigid 1000 Resin can withstand prolonged loads without losing its initial shape or design. Due to its higher tensile strength, this material can handle a greater load without snapping. This means PU Rigid 1000 Resin excels when printing stiff and sturdy end-use parts such as parts intended to protect vulnerable components. These include:
- Mounts
- Brackets
- Safety structures
- Ducts
- Bumpers
Other rugged applications can also be printed with PU Rigid 1000 Resin, such as:
- Bottle caps
- Buckles
- Bike pedals
Post-Processing With Polyurethane Materials
Polyurethane has a more involved workflow and requires additional equipment and set-up costs. More attention is needed when setting up your prints and post-processing your parts in order to get consistent, high-quality results.
The following workflow is similar to printing with other materials, but will require additional equipment and post-processing time:
-
Produce 3D File. Use PreForm to prepare your file, with custom settings to help guide you through the process of adding supports and choosing the print correct orientation.
-
Prepare the Printer. Formlabs PU Rigid Resins come in an aluminum bottle with a funnel and empty cartridge to preserve usable shelf life. After shaking the bottle to ensure the resin is thoroughly mixed, use the funnel to pour it from the bottle into the empty printing cartridge. Your printer must be in a dry cabinet for printing with either PU Rigid Resins. When ready, load your printer with the resin cartridge and build platform, and click print!
-
Print. Same as always, follow the prompts on the easy-to-use touchscreen to get your print started.
-
Post-Processing. Place your Build Platform in a brief PGDA wash, then allow parts to air dry or use an air compressor. Once dry, and supports are removed, you must set the parts in a humidity cure chamber for post-curing. Humidity based curing completes the urethane reaction, making a true polyurethane part. No IPA or traditional washing solvent is used in this process. A part with two mm thickness will take three days to fully cure when using either PU Rigid 650 Resin or PU Rigid 1000 Resin.
While some equipment is optional, such as an air compressor to air dry excess PDGA solvent off the surface of your prints, other equipment is necessary. This includes a dry cabinet with low humidity settings and the humidity cure chamber. These are required to reduce moisture that hinders end-use performance.
For additional details on the step-by-step workflow of PU materials, including recommendations for a humidity cure chamber or dry cabinet, talk to one of our 3D printing experts. Due to the additional post-processing times required, polyurethane materials are not ideal for rapid same-day prototyping. For those applications, try Draft Resin.
High Performance Engineering Materials For Everyone
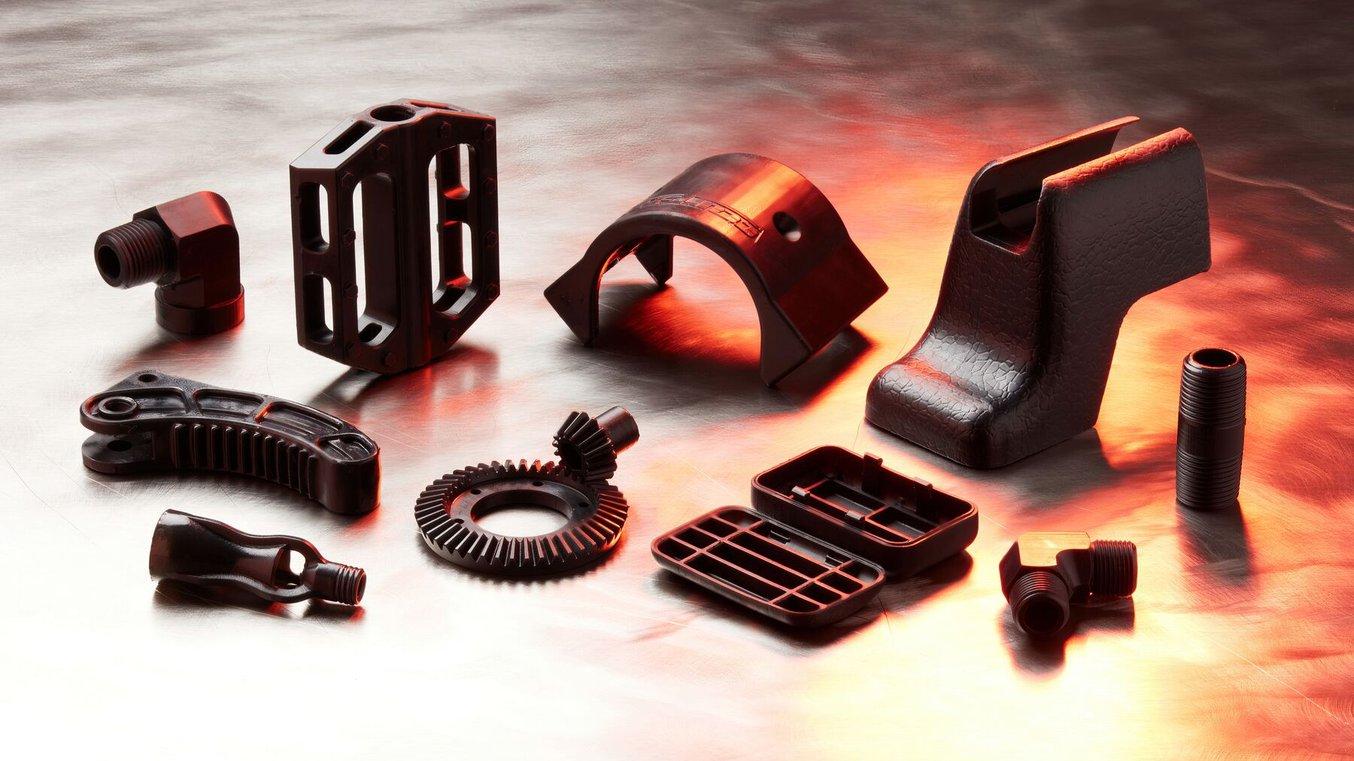
Our new PU Rigid 650 Resin and PU Rigid 1000 Resin are now available for the Form 2, Form 3+, and Form 3B+. Formlabs is proud to introduce these previously inaccessible materials to a wide audience at an affordable entry point, supporting our mission of making professional in-house fabrication tools accessible to every business.
Our PU Rigid Resins are the latest of many advanced materials to be added to the Formlabs Materials Library. To view our complete library of engineering materials for Formlabs SLA 3D printers, visit our Engineering Resins page. To buy PU Rigid Resins, follow the links below.