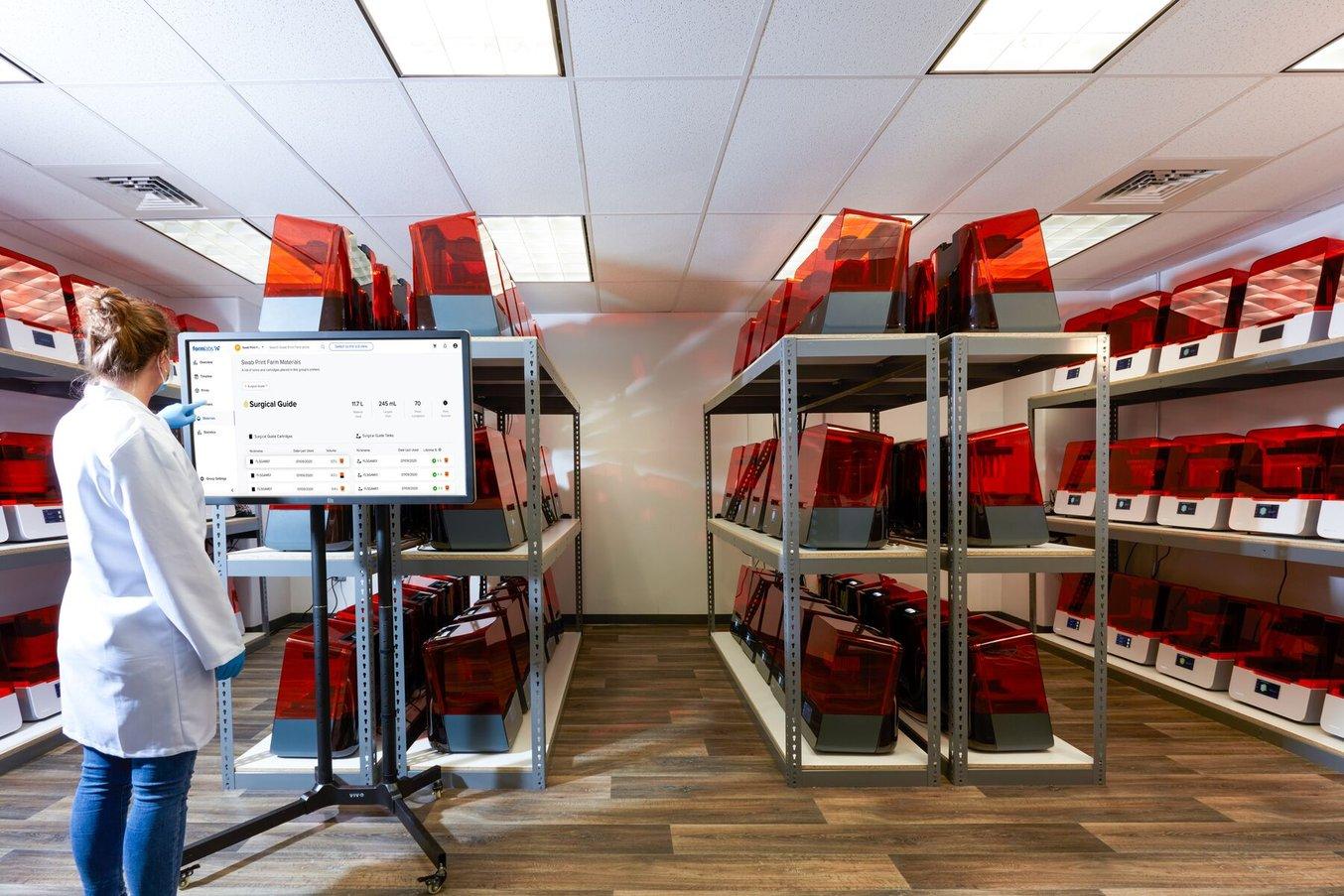
As businesses, universities, and healthcare providers have adopted and scaled their use of additive manufacturing, multi-printer facilities have become more common. Creating an additive manufacturing center increases supply chain resilience and flexibility, improves overall efficiency, and reduces costs. From dentistry, to aerospace manufacturing, to luxury jewelry, 3D printing at production levels can reduce costs, improve the agility and efficiency of your enterprise, and enable new products and market reach.
Bringing higher volume 3D printing in-house was traditionally expensive and required extensive infrastructure to support the large, industrial machines. Now, with affordable desktop and benchtop resin 3D printers and compact yet powerful SLS options, managing a fleet of 3D printers is simplified and efficient.
Managing multiple SLA and SLS printers doesn’t have to be complicated — with the right organizational system and a few helpful pieces of equipment, any business can get a fleet of SLA and SLS printers up and running in just a day or two. To illustrate the infrastructure necessary for a fleet and provide tips for managing it, we’ll provide examples of an SLA printer fleet and an SLS printer fleet — businesses that have hybrid manufacturing approaches can take learnings from both to create an effective SLA and SLS hybrid workflow.
To see further in-depth guidelines and different configurations of fleets, download our white paper.
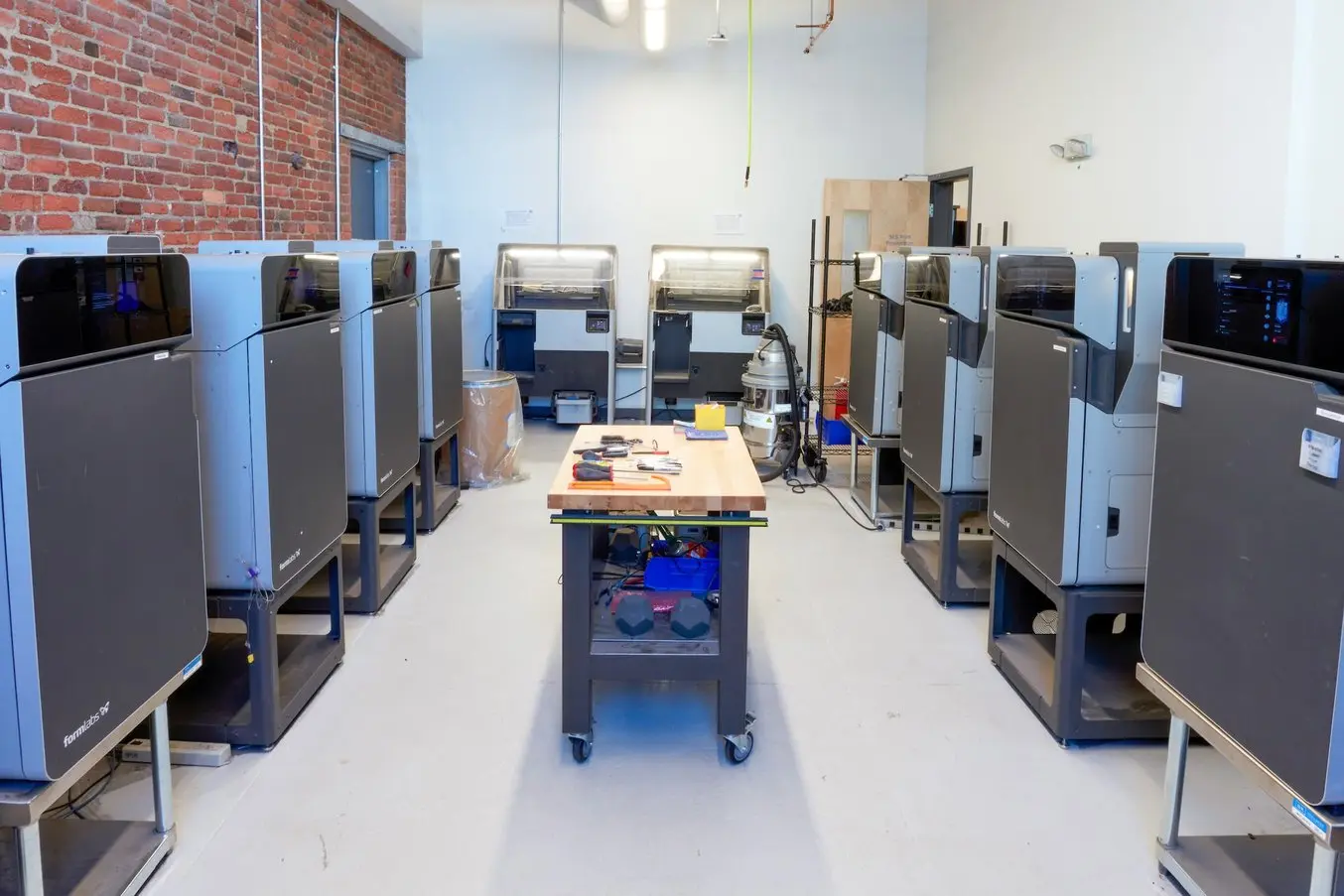
Managing 3D Printer Fleets
Managing multiple SLA and SLS printers doesn’t have to be complicated — any business can get a fleet of SLA and SLS printers up and running in just a day or two. By reviewing four different successful multi-printer scenarios, this guide will help you set up an efficient workflow for any volume or part type.
Production Volume SLA Printer Fleet
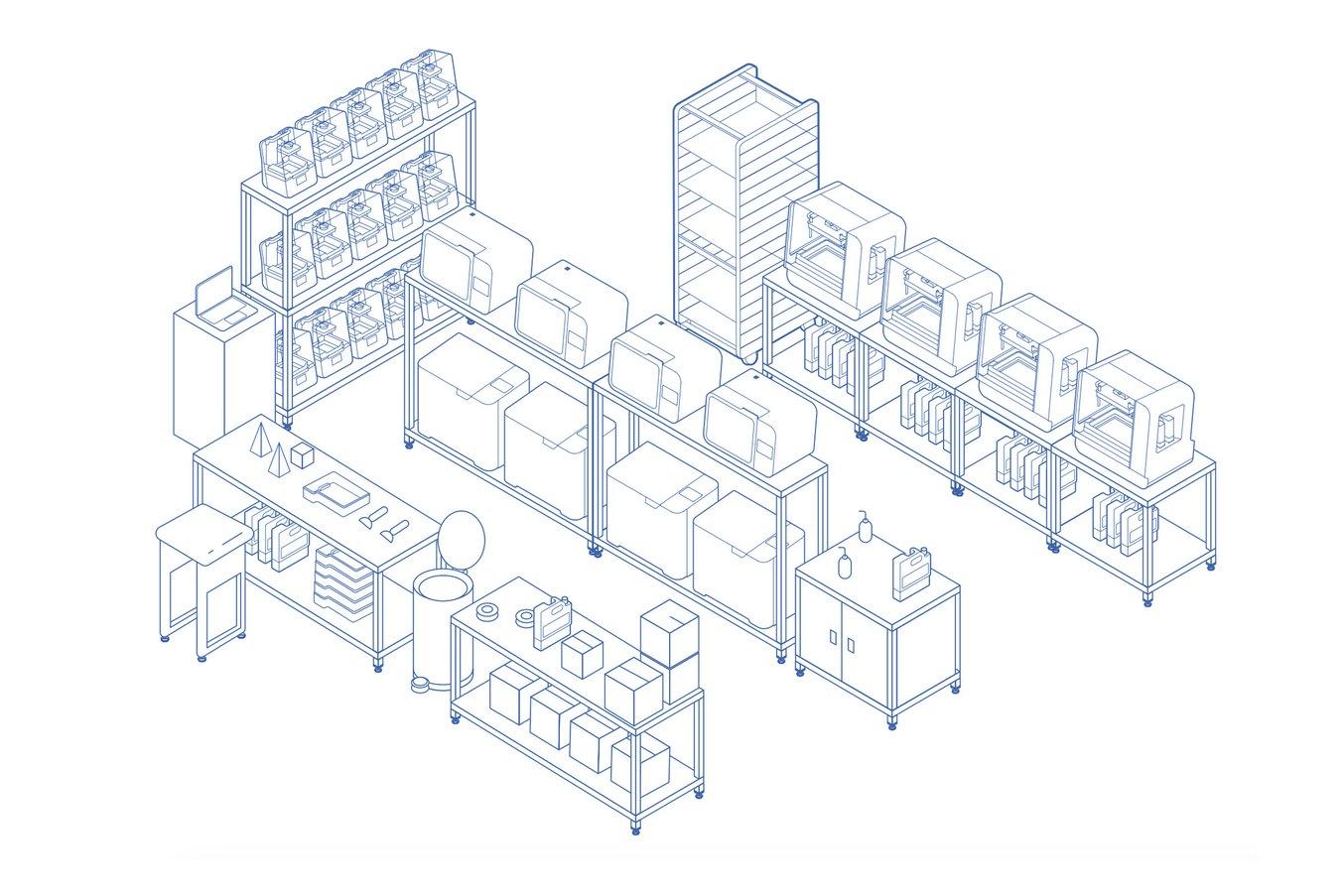
Equipment:
- 15 Form 3+/3B+ desktop printers
- 4 Form 3L/3BL benchtop printers
- 4 Form Cure L
- 4 Form Wash L
- 1 Finishing Tools
- 1 Baker’s rack
- 2 Finishing table
- 1 Pegboard
- 1 IPA storage cabinet
- Gloves, IPA
- Disposal solution
Total cost: ~$105,000
Facility Requirements:
- Dimensions (W × D × H)
- Form 3+
- 40.5 × 37.5 × 53 cm
- 15.9 × 14.8 × 20.9 in
- Form 3L
- 77 × 52 × 74 cm
- 30.3 × 20.5 × 29.1 in
- Wash L
- 78.0 x 46.0 x 67.0 cm
- 30.7 x 18.1 x 26.4 in
- Cure L
- 69.0 x 54.0 x 44.5 cm
- 27.2 x 21.3 x 17.5 in
- Form 3+
- Separate room with adequate ventilation (standard HVAC office systems are appropriate)
- 3 dedicated AC electrical circuits
- Environment: 18 – 28 °C/64 – 82 °F
Production volumes are not only possible with Formlabs SLA 3D printers, they can be a profitable and efficient manufacturing method for many situations, including mass customization, stopgap production or supply chain solutions, and repair and aftermarket parts.
There are several considerations when scaling up from a mid-size SLA fleet to a production-level capacity. Though things like enlarged footprint and power consumption may be obvious, other considerations, such as safe IPA handling and storage, may be less so.
Consumables Management
Post-curing can be done to many parts at once, regardless of the material type, unlike the washing step. For this reason, having only one Form Cure L is the most efficient use of space and power.
For washing immediately post-print, certain materials can be washed together, while others should be separately washed to avoid any particles dissolved in the isopropyl alcohol from affecting the color, finish, or performance of others.
For full compliance and biocompatibility, biocompatible resins require dedicated Resin Tanks, Build Platform, and Finish Kits or Form Washes, which should only be used with other Formlabs biocompatible resins.
This chart details which resins can be washed together. Properly labeling Form Wash machines as ‘Light’ or ‘Dark’ can be helpful.
Light | Dark | Biocompatible | Other (wash separately by themselves) |
---|---|---|---|
Clear Resin, White Resin, Rigid 4000 Resin, Rigid 10k Resin, Durable Resin, Elastic 50A Resin, Flexible 80A Resin, High Temp Resin | Black Resin, Grey Resin, Grey Pro Resin, Draft Resin, Model Resin, Tough 2000 Resin, Tough 1500 Resin, Flame Retardant Resin | Biomed White Resin, Biomed Black Resin, Biomed Clear Resin, Biomed Amber Resin, Surgical Guide Resin, Dental LT Clear Resin, Custom Tray Resin, IBT Resin, Temporary CB Resin, Permanent Crown Resin, Denture Teeth Resin, Denture Base Resin | ESD Resin, Color Kit, Castable Wax Resin, Castable Wax 40 Resin |
IPA Handling, Storage, and Disposal
Printing at production volumes requires close monitoring of the saturation level of your IPA containers — washing large volumes of parts consistently will necessitate changing out the IPA in Form Wash and Form Wash L often. For the Form Wash L, used in the above illustration, there is a ‘Replace Solvent’ mode that provides instructions on pumping out used IPA and replacing it with fresh IPA. Full, detailed instructions are listed on our website. IPA should be stored in a flammable-safe container or cabinet, like the one pictured directly to the right of the Form Wash L machines for ease of use. Disposal of used IPA is dependent on local regulations, but in most cases, should be handled by a hazardous waste company.
IPA Recycling
For many 3D printer fleet managers, solvent recycling becomes a concern, and there are different solvent recycling systems available depending on the need of your facility. Solvent recycling systems use distillation and fractionation processes to remove solutes from waste solvents, making it possible to reuse a high percentage of the original IPA to wash parts. Recycling IPA reduces waste disposal costs, emissions that are required to produce solvents, and the cost of purchasing IPA, while also giving the end user greater control of their IPA supply and making them less susceptible to supply chain interruptions
Spectra Photopolymers (owned by Formlabs) has been using the CBG Biotech SolvTrue™ S1500 Solvent Recycler for the past six months to recycle IPA used to clean parts for over 100 Form 3 3D printers.
Fleet Management, Dashboard, and Organization
When overseeing this many printers, including two different formats (desktop and benchtop), you need a strategy for management and organization. Formlabs has developed tools to help oversee the machines and stay on top of consumables management as well as maintenance schedules, warranty status, and service plans.
Dashboard: Simplify Multi-Printer Management
Dashboard has a host of features that can make overseeing multiple units easier. The Dashboard view will update users on the status of each cartridge in the printers — this is especially helpful if printers are used with one material only — so it’s easy to tell when a cartridge or tank needs to be replaced. Printer serial names have warranty and service plan statuses tied to them in Dashboard, making it part of an annual routine to update warranty or service plans as needed. Dashboard also allows users to create Printer Groups — these can be based on material type, the origination of the print job, the destination of the finished part, or any designation that makes the most sense for your workflow. From there, Dashboard will determine which printer makes the most sense to start the next job and will empty the print queue in the most efficient way possible. Users managing a print queue only have to ensure that prints are uploaded and that printers are set up to start the next print when the first one finishes; they don’t have to spend time evaluating print jobs for an optimal place in the queue or search through PreForm to find a printer with the right material already preloaded.
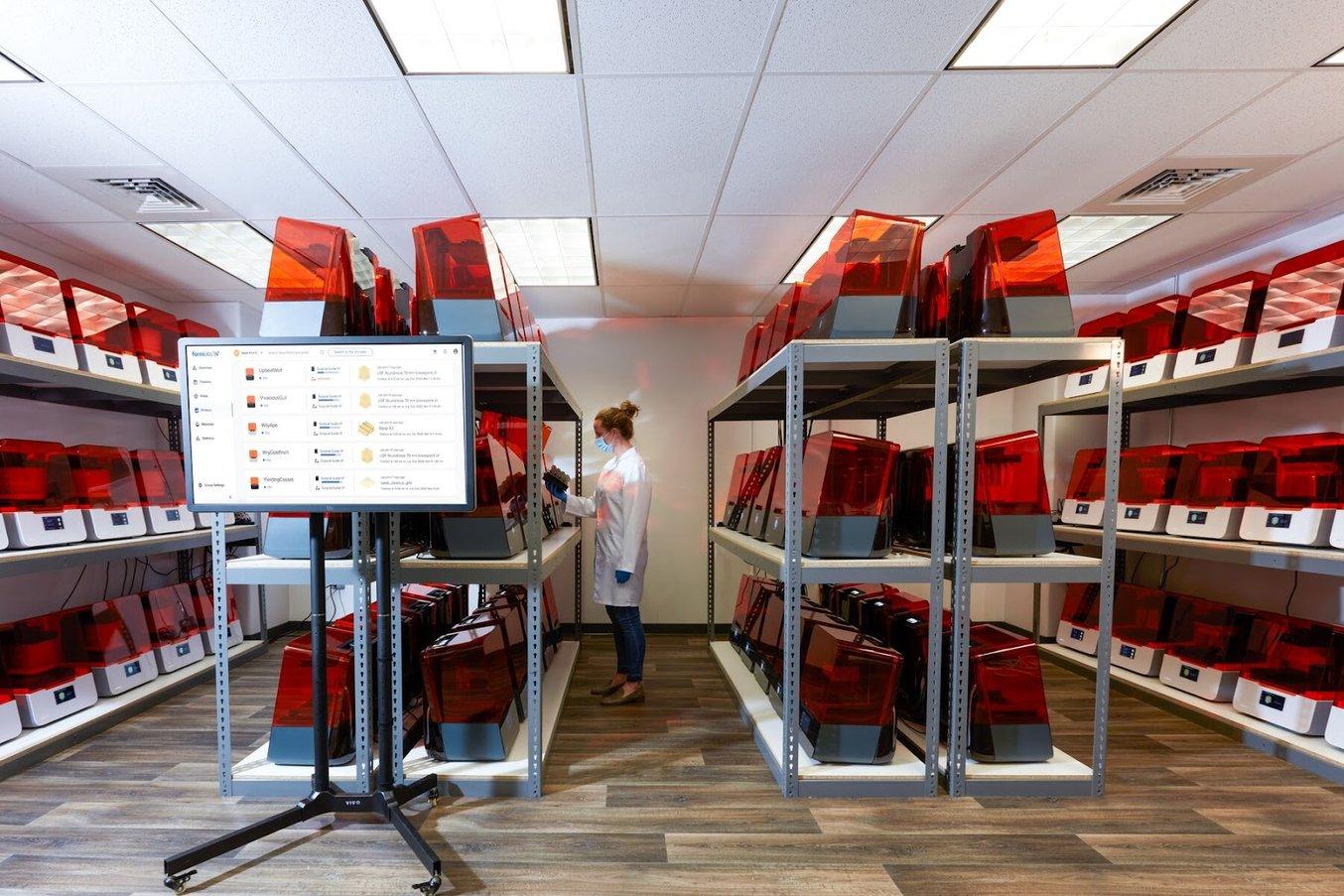
Batching Tasks Together for Streamlined Workflow
One successful technique employed by Formlabs production-level customers as well as at Formlabs’ own print farms is the grouping and batching of tasks in order to streamline workflow. Though one person can efficiently manage a group of 20+ printers, if your print volume is in the hundreds of parts per day or more range, it makes more sense to have each employee perform a specific task, rather than shepherd a single print job through every step of the workflow. At Formlabs’ Ohio location, where hundreds of sample parts are manufactured each day, the tasks are divided as follows:
- Load print jobs into queue
- Prime printer for print jobs (insert/changeover cartridges, platforms, and tanks, as needed)
- Remove parts from build platforms after a print is done
- Wash parts and post-cure parts
- Perform quality control checks and package parts
Siloing tasks in this way ensures that fewer people are handling the printer and consumables, and each task is performed with fresh eyes and experienced hands. This workflow is especially helpful in mass customization cases such as consumer product personalization or dental appliance manufacturing, where parts are similar, if not identical, to one another, and minimal post-processing or print preparation is needed.
Production Volume SLS Printer Fleets
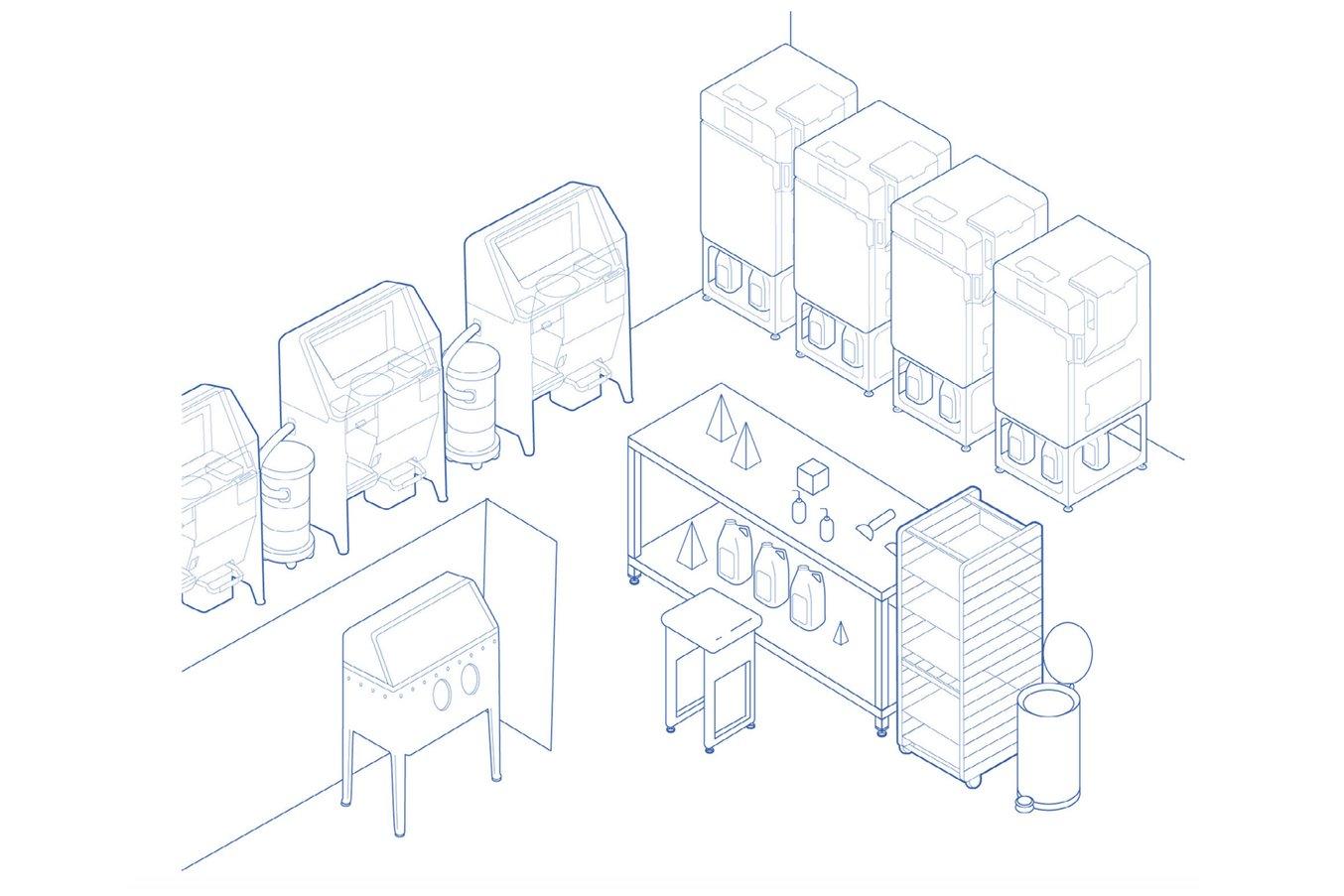
Equipment:
- 4 Fuse 1+ 30W SLS printers
- 3 Fuse Sift post-processing machines
- 2 industrial vacuums
- 1 media blaster
- 1 work table
- 1 baker’s rack
- Disposal solution
Total Cost: ~$135,000
Facility Requirements:
- Dimensions (W × D × H)
- Fuse
- 64.5 × 68.5 × 107 cm (165.5 cm with stand)
- 25.4 × 27 × 42 in (65.0 in with stand)
- Fuse Sift
- 101.5 × 61.0 × 154.5 cm
- 39.9 × 24.0 × 60.8 in
- Fuse
- Separate room with adequate ventilation (standard HVAC office systems are appropriate)
- 9 dedicated AC electrical circuits
- Environment: 18 – 28 °C/64 – 82 °F
3D printing hundreds or even thousands of parts a week can be accomplished easily with the Fuse Series SLS printers’ packing algorithm and self-supporting print bed. For service bureaus, contract manufacturers, or OEMs with customized or intricate parts, 3D printing for end-use production makes sense and can be done efficiently and cost-effectively with the Fuse Series workflow.
Increasing Productivity Through Packing Efficiency
One of the main advantages of printing with the Fuse Series is that the self-supporting powder bed technology allows you to stack parts vertically and nest parts within cavities. The Formlabs packing algorithm determines how to most efficiently pack parts within the build chamber, resulting in faster print times and significant material savings.
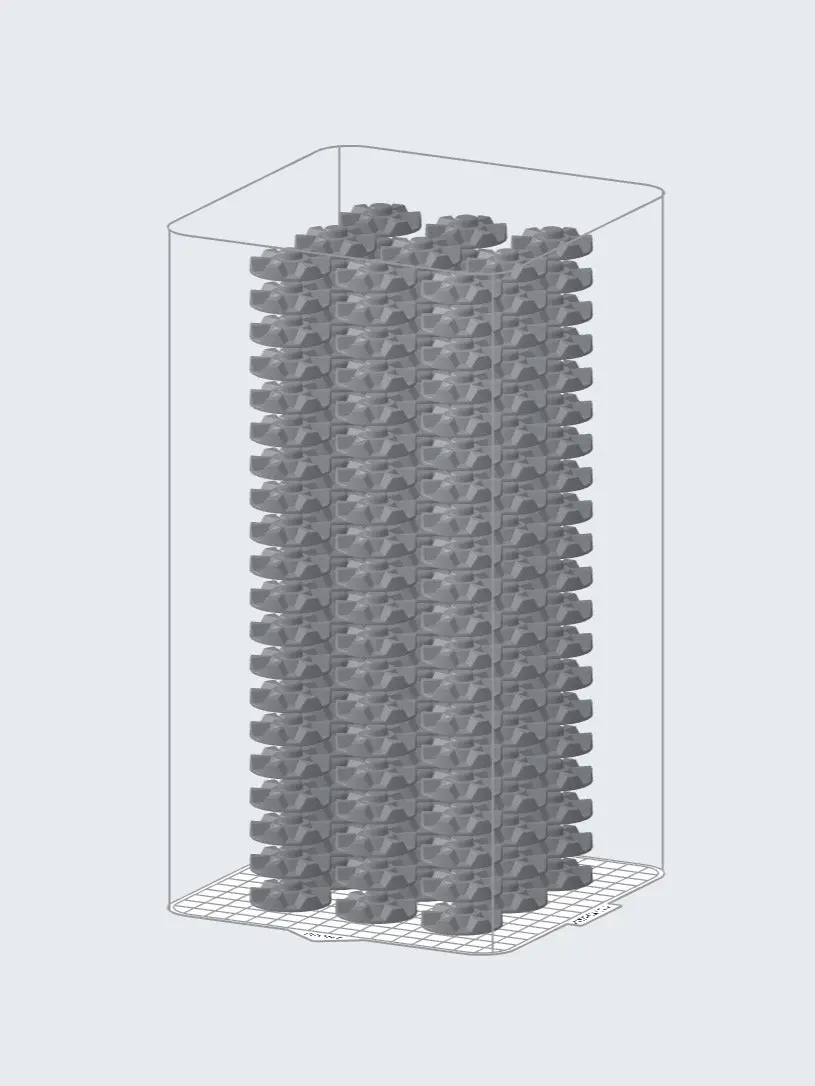
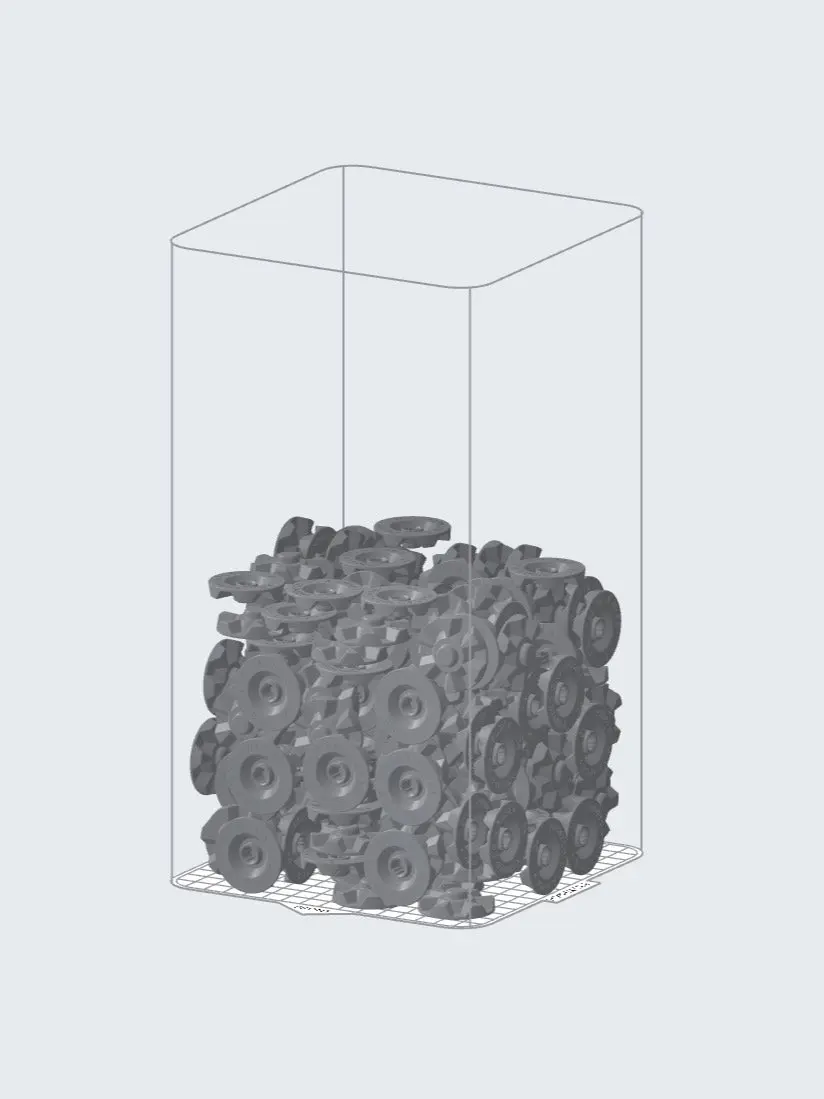
Form Cure Turntable Coupling
108 arrayed Form Cure turntable couplings, which highlights the value of packing for a production scenario.
Print time before: 32h 14m
Density before: 13%
Print time after: 26h 35m
Density after: 24%
Materials saving: 5.07kg - 2.73kg = 2.34kg (46%)
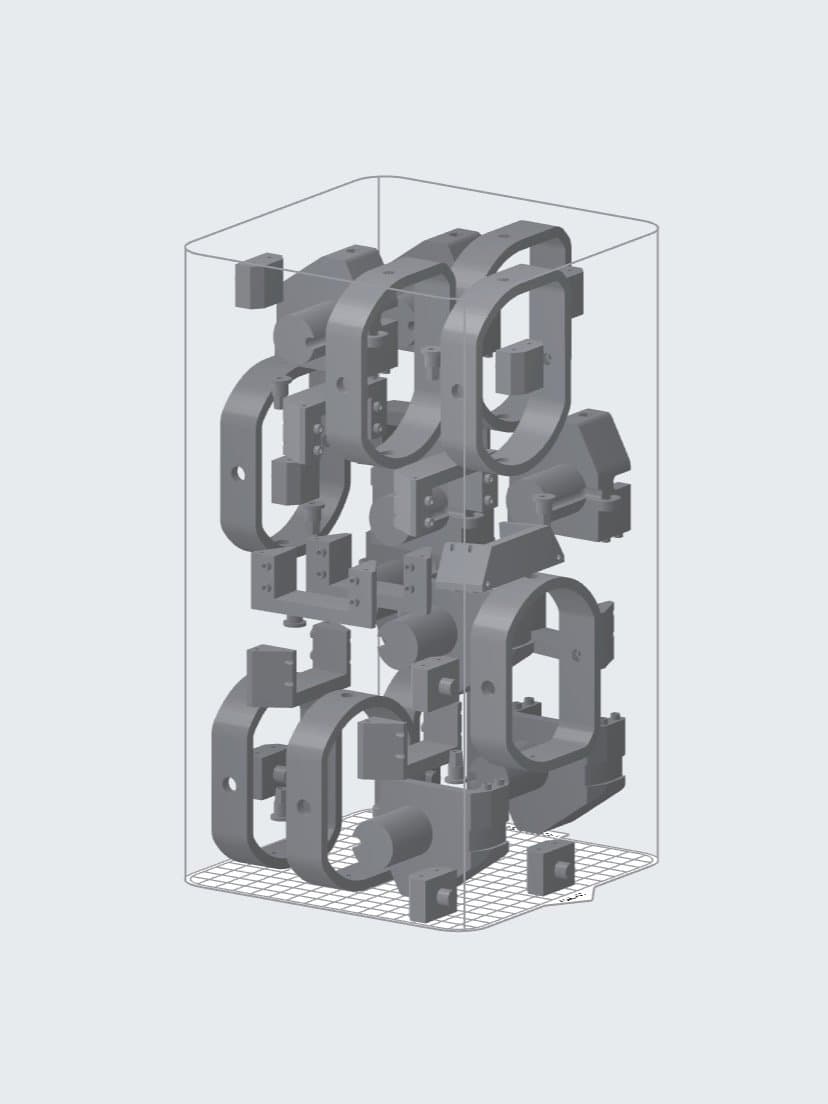
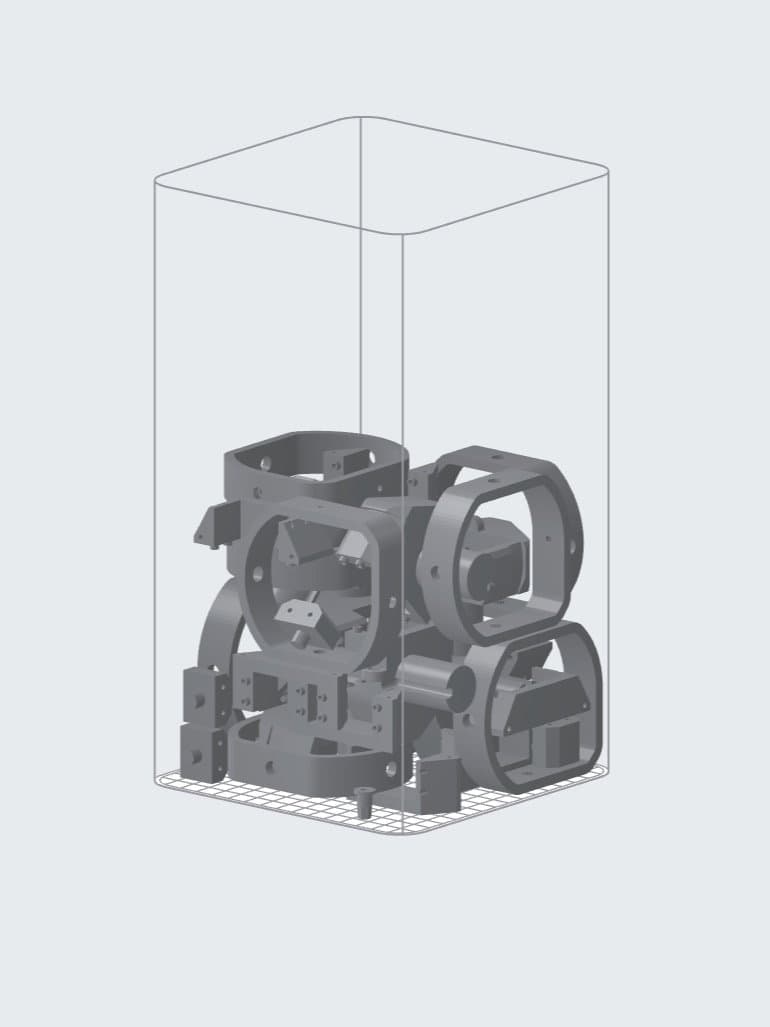
Spotlight Control Assemblies
Assembly for an internal project, which showcases a use case where packing can quickly get an optimal layout to save time without any effort needed.
Print time before: 33h 34m
Density before: 17%
Print time after: 24h 12m
Density after: 29%
Materials saving: 5.30kg - 3.05kg = 2.25kg (42%)
There are third-party software systems that can take this packing algorithm further, such as Materialise Magics software, which can arrange 3D models, generate protective cases for delicate parts, send parts to multiple machines, and optimize printing schedules. For users managing large fleets of SLS printers, incorporating a software management system can lead to further material savings and improved cycle time with shorter prints.
Electrical Power Solutions
Formlabs SLS Fuse Series does not require industrial power and complex HVAC systems, as many of the traditional large format powder bed printers do. While each printer does require its own circuit, the power usage is well below that of many typical office or workshop environments.
Fuse Series printers and the Fuse Sift each require a dedicated AC circuit, providing at least 7.5 A at 230 VAC (EU) or 15 A at 120 VAC (US), as well as reliable grounding. These circuits must be separate from other devices, including fans, vacuums, power tools, space heaters, or any large appliances or power tools.
Regional Power Requirements:
- NA: 120 V and at least 15 A, Type NEMA 5-20R socket
- EU: 230 V and at least 7.5 A, Type CEE 7/3 "Schuko" socket
- If your vacuum draws more than 6 A, your Fuse Sift needs an independent circuit supplying 230 V and 10 A to a Type CEE 7/3 "Schuko" socket.
- UK: 230 V and 13 A, Type G BS 1363 socket
Managing Multiple SLS Materials
The Fuse Series offers multiple different materials like nylon, nylon composites, TPU, and more that are already well known to the manufacturing community. A distinguishing feature of the Formlabs SLS technology is that it is possible to switch between materials — many industrial SLS solutions have a prohibitively difficult cleaning process, while the Fuse Series SLS printers can be cleaned and switched over in four to six hours. While not recommended to do often, this switchover process allows for a Fuse Series user to adapt to new demands or react to a new material release, without rendering their machine obsolete.
The compact size and affordability of the Fuse Series also make it easier to build out a fleet for running multiple different materials at once, for example, for service bureaus or product design and engineering firms. Previously, the $200,000+ cost of traditional SLS or MJF systems made it hard to justify running niche materials, such as carbon fiber or glass-filled nylon. Now, with the Fuse Series, the barrier to entry is drastically lower, and scaling up with the demand is easier.
PreForm and Dashboard perform the same function as with other fleets; the two platforms enable users to oversee their material usage, current print status, availability of printers and Fuse Sifts, as well as warranty status, service plans, and maintenance schedules.
Fleets of Fuse Series SLS printers don’t require the same industrial infrastructure that many traditional SLS or MJF machines do. The accessibility and ease of use of Fuse Series printers enable agile, low-cost manufacturing for businesses of any size.
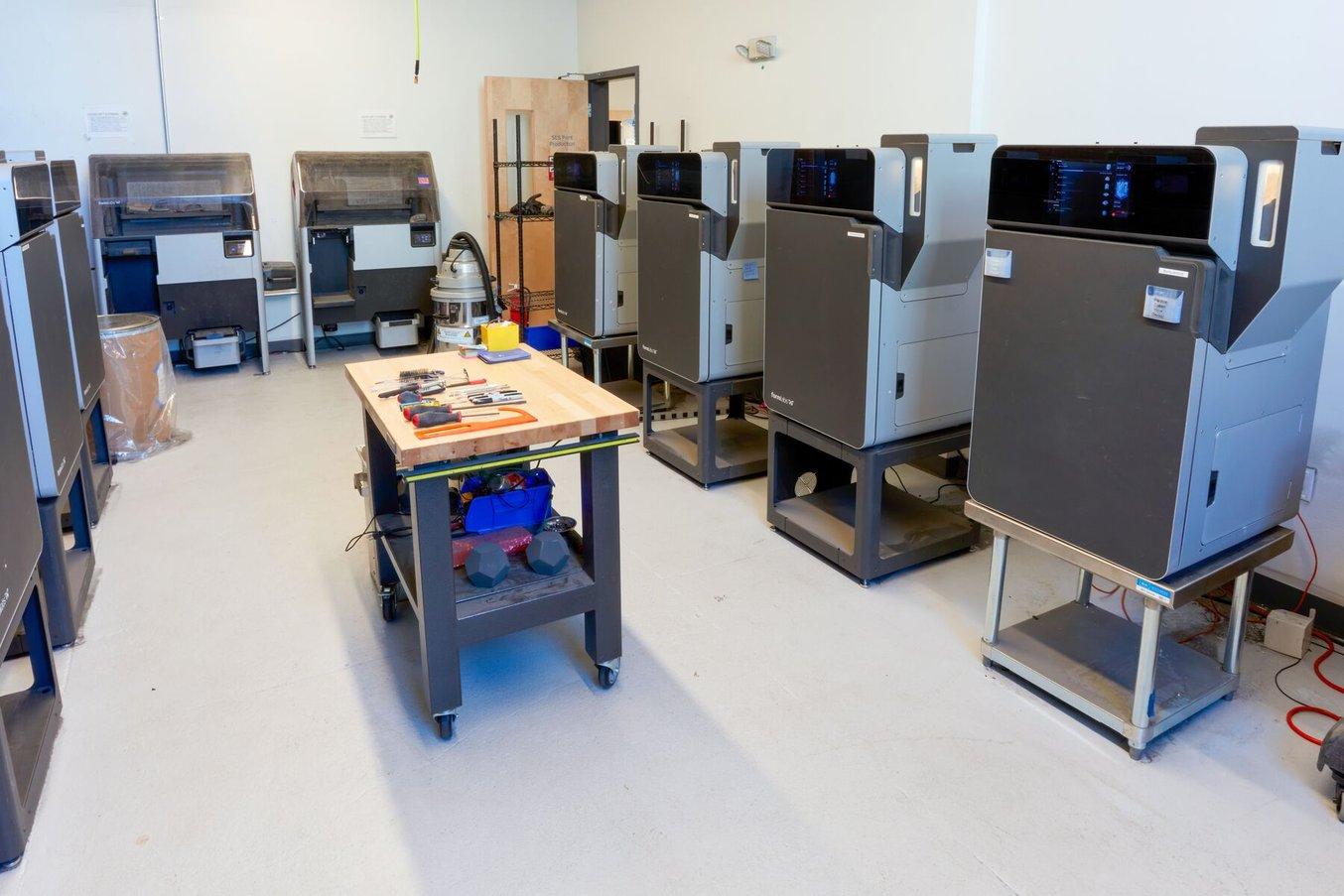
3D printing hundreds or even thousands of parts a week can be accomplished easily with the Fuse Series SLS printers’ packing algorithm and self-supporting print bed. For service bureaus, contract manufacturers, or OEMs with customized or intricate parts, 3D printing for end-use production makes sense and can be done efficiently and cost-effectively with the Fuse Series workflow.
Fuse Series Maintenance
Unlike the Formlabs SLA printer fleets, there are a few scheduled tasks that users should regularly complete to keep their Fuse Series printers running optimally. After each print, users should check to make sure the optical cassette and IR sensor are clear and clean. At about 15 seconds of labor, even when multiplied for a fleet of Fuse Series printers, this task only requires a couple of minutes. After five to 10 prints, cleaning the optical cassette is recommended. If users are printing regularly, there are tasks such as cleaning or replacing the Fuse Sift intake filter, all of which will be prompted by Dashboard or on the printer’s UI screen. The full list of scheduled maintenance tasks can be found on our website. Managing multiple Fuse printers requires much less maintenance than managing even one traditional SLS or MJF system.

Streamline Production With Fleets By Formlabs
Creating a lean, agile manufacturing process is possible with fleets of 3D printers. Relying on 3D printing for production can help businesses avoid the high costs of machining or tooling while bringing control over the means of production in-house.
Reducing reliance on external contract manufacturers or third-party suppliers can help businesses become more resilient and improve their ability to pivot in the face of supply chain disruptions or changes in market demand.
With Formlabs printers and tools, you can effectively manage a fleet with our streamlined software platforms and a support network of experts and technicians who can help optimize your 3D printing workflow for your business needs.
Download our white paper to see further in-depth guidelines and different configurations of fleets or contact our sales team to build your own fleet and calculate your production ROI.