Sinn Spezialuhren, a manufacturer of feature-rich, mechanical watches, had originally purchased a Form 3 stereolithography (SLA) 3D printer for prototyping. You can read more about how their product development team used 3D printing to create high-precision prototypes for watches in our story here.
However, the company’s development team quickly realized that they can leverage 3D printing for producing manufacturing tools, such as mounts, fixtures, and testing equipment.
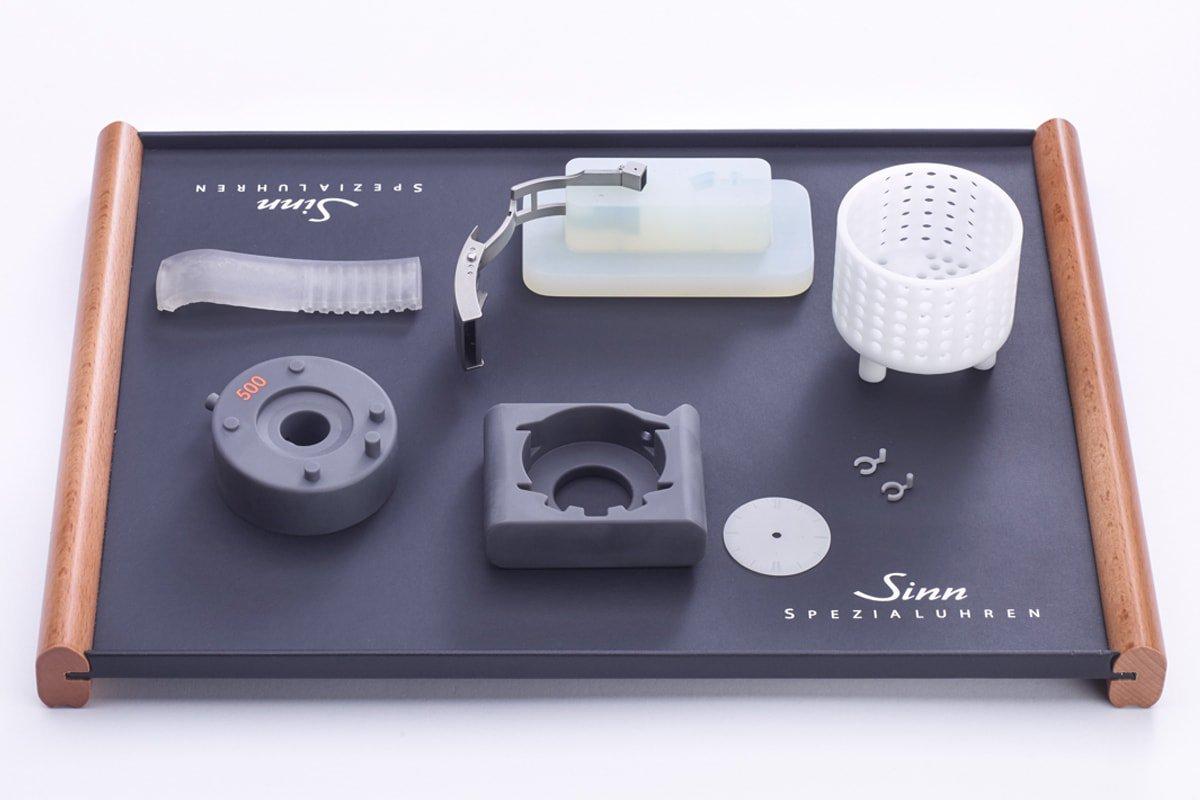
3D printed, prototype watch parts, fixtures, and testing equipment produced using the Form 3.
From Custom Tools to Serial Production Parts
As soon as the company received its first in-house 3D printer, employees quickly became enthusiastic about using the technology for other applications beyond prototyping, such as manufacturing custom equipment. Nils Hunder, who is responsible for the watch designs and the development of prototypes and 3D printing at Sinn Spezialuhren said, “We noticed that the printer is serving us very well in this area.”
“We can make mounts and fixtures overnight, very quickly and at low cost.”
Nils Hunder, Head of Engineering, Product Development and Prototyping
Before 3D printing, custom tools for the company had primarily been manufactured by external service providers. This meant high outsourcing costs and long lead times, with an average of 1-2 weeks for mounts and fixtures. Even then, the employees at Sinn Spezialuhren could never be completely sure whether they would serve the desired purpose or, in the worst case, whether the costs would be in vain.
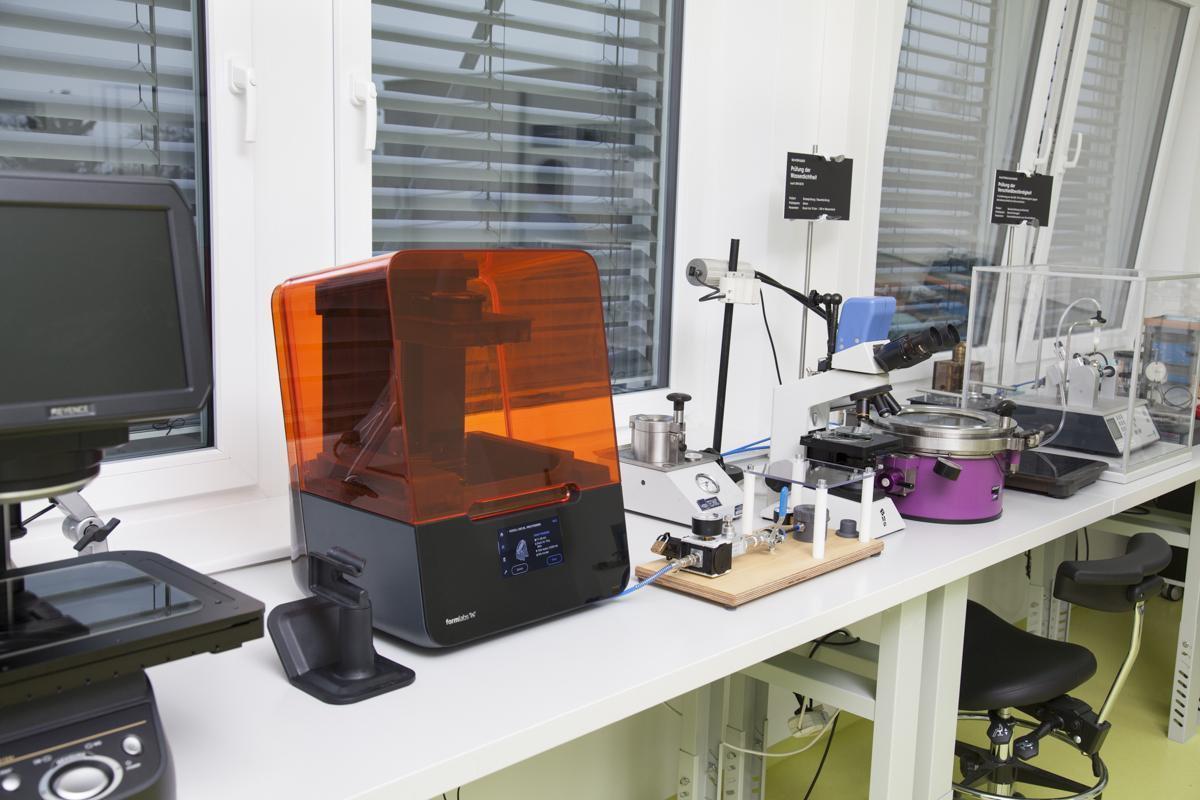
The Form 3 in the Sinn Spezialuhren laboratory.
Now the Form 3 is increasingly being used in equipment manufacturing. The only costs incurred are the material costs and the time required for post-processing. Parts can be printed overnight and if the printed parts or designs do not meet the requirements, any adjustments can be made quickly.
Nils Hunder mainly uses Tough 1500 Resin and Tough 2000 Resin, as they produce strong parts with minimal deflection. In one case, the Form 3 was used to print the serial parts for 500 crown stoppers of quartz watches that were not available as mass-produced goods. When watches are held in stock, these crown stoppers are inserted between the case and the crown to prevent the battery from engaging during storage. Sinn Spezialuhren's regular supplier had no capacity for the crown stoppers due to the coronavirus pandemic and their production costs would have otherwise been too expensive, with a minimum quantity order of 10,000 pieces. Fortunately, 50 of these crown stoppers could be printed in a single build using the Form 3. Thanks to the slight flexibility of Tough 1500 Resin, the printed parts do not scratch the watches and are reusable.
In another application, watch cases made of Damascus steel are etched in-house for testing purposes and the acid used in the process must be stirred for better temperature distribution. Sinn's team uses baskets 3D printed from Rigid 4000 Resin, due to the material’s high resistance to chemicals and acids.
A further field of application is the Ar-Dehumidifying Technology, which was developed by Sinn Spezialuhren for diving watches. These watches contain a protective gas filling and require a mount for the watch case for adding the protective gas into the case. Using the conventional production technique of milling, the two parts of the mount for this production phase cost around €200 and required 1-2 weeks of production time. With a material cost of €30, the total cost per printed part using the Form 3, including post-processing, is less than half that amount. The production time has also been dramatically reduced, as the engineers can print the parts overnight.
Additionally, the team can engrave the mounts with custom labels to make it clear at first glance which watch model the mounts belong to, making everyday work much easier. With conventional production tools, such a custom equipment marking would incur extra costs.
In-House Development of a Testing System Certified by the German Technical Inspection Association (TÜV)
The UX diving watch, one of the models in the Sinn’s watch range, is filled with crystal-clear oil. This liquid changes its volume when the temperature changes, so the watch has a membrane base that extends when heated or retracts into the case when the temperature cools down. This membrane base provided the biggest wow factor for Mr. Hunder and his team during the development of a testing system.
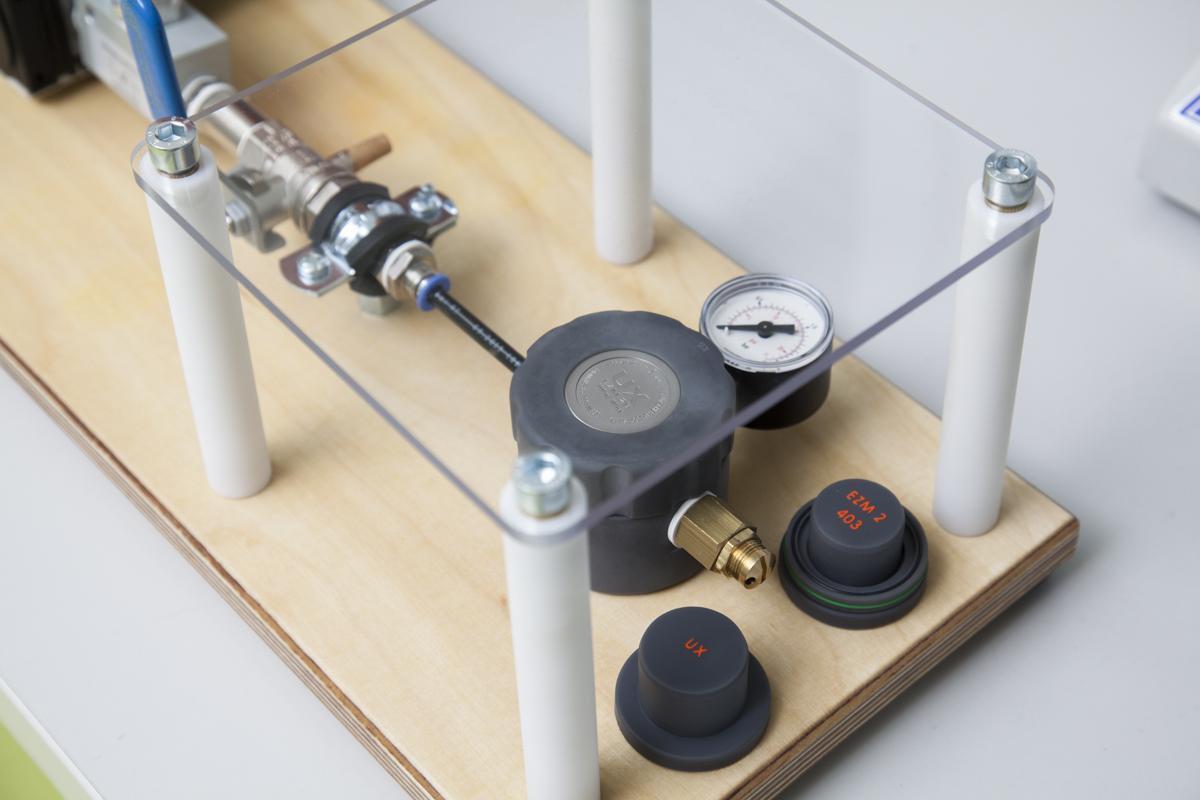
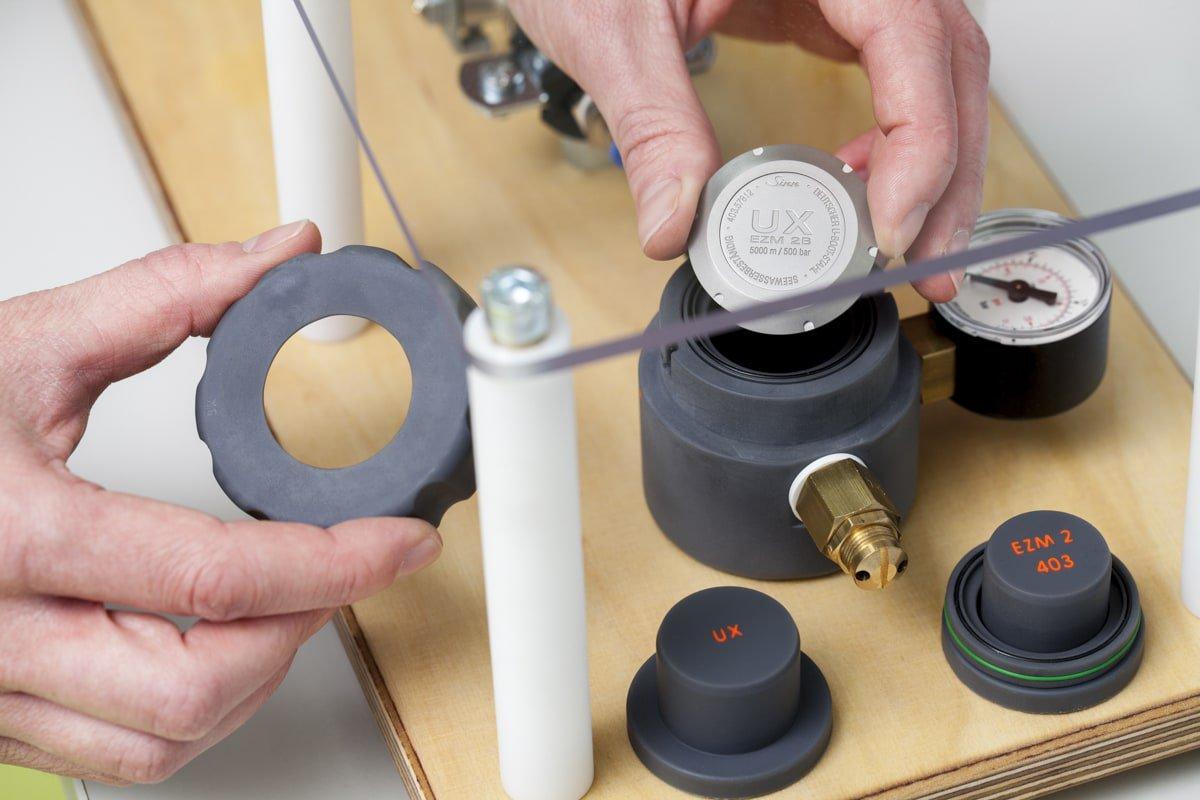
Membrane bottom testing system for the UX watch model with a 3D printed bracket.
The aim of the testing system is to check the swing of the membrane base, whether it extends straight or slightly angled, which can then be aligned accordingly. Previously, a complete watch had to be built and heated for this purpose. This was a very time-consuming process, as all the components were contaminated with liquid and subsequently had to be cleaned again.
To make this laborious work easier, a test system was developed that uses air pressure to simulate the behavior of the liquid.
Watch the video: The 3D printed membrane base testing system in action.
Tough 2000 Resin was used to print the pressure pot with different insert rings into which different cases fit, as well as the locking, which closes with a bayonet mount. This bayonet mount presented the greatest challenge because it is very difficult to manufacture in conventional production. Additionally, supports for an acrylic glass cover were made from Rigid 4000 Resin.
The 3D printed testing bench was originally only intended to test the general feasibility of the test rig and the use of the bayonet mount. In the end, it worked so well that conventional production was no longer necessary. The 3D printed testing bench has also been inspected and approved by the German Technical Inspection Association (TÜV).
“When you establish that you can print the part you need, you can then concentrate purely on functionality, which is a huge advantage.”
Nils Hunder, Head of Engineering, Product Development and Prototyping
Mr. Hunder’s team originally asked their supplier responsible for the serial production of their watch cases to manufacture the testing system. However, the supplier would have used the same milling machine as they use to manufacture the watch cases, which would have led to a delay in watch production. In the end, Sinn Spezialuhren sent the testing system that they had designed in-house to the supplier, thus becoming a supplier themselves in the process—a completely new experience for the team.