3D printed parts need to hold up to real-world applications, and toughness is therefore an important material characteristic. Notched Izod, while a popular way to measure toughness, is only one way to evaluate a material.
With so many tough materials available, it can be difficult to compare their suitability for a given application if only looking at Notched Izod. When Formlabs material engineers set out to create an even tougher version of our Tough 1500 Resin, Tough 1500 Resin V2, they optimized it for performance across a number of different ways of measuring toughness – not just Notched Izod.
By looking at various ways to quantify toughness, it’s easier to evaluate and select the optimal material for an application.
Why Is Measuring Toughness Important?
Toughness is an important material characteristic for real-world performance. A classic hypothetical proves this point – ceramic materials like silica or alumina have a much higher strength-to-weight ratio and stiffness-to-weight ratio than metals like aluminum or steel, and yet you would never build an airplane out of a ceramic material. The critical reason for this is toughness.
Ceramic materials tend to experience brittle fractures rather than absorbing the energy of the load or impact by plastically deforming. Any small crack or defect in a ceramic material can lead to brittle fracture. This brittle fracture would be catastrophic in a safety-critical application, and is why you would not build an airplane out of ceramic materials.
Metal Materials tend to be extremely tough and will deform rather than elongate, which allows them to absorb impacts without breaking. Because metals can elongate through plastic deformation, they can redistribute stresses away from cracks or defects, reducing stress concentrations and preventing a catastrophic failure. While metals like steel and aluminum alloys are very tough materials, other metals like cast iron are more brittle.
Plastic materials as a category have a wide range of toughness. Some materials like acrylic (PMMA) or polystyrene (PS) are known for being brittle, whereas materials like acrylonitrile butadiene styrene (ABS), polyethylene (PE), and polypropylene (PP) exhibit excellent toughness and are used to make rugged, durable, long-lasting parts. One of the toughest polymers, polycarbonate (PC), is used to make impact shields and safety glasses.
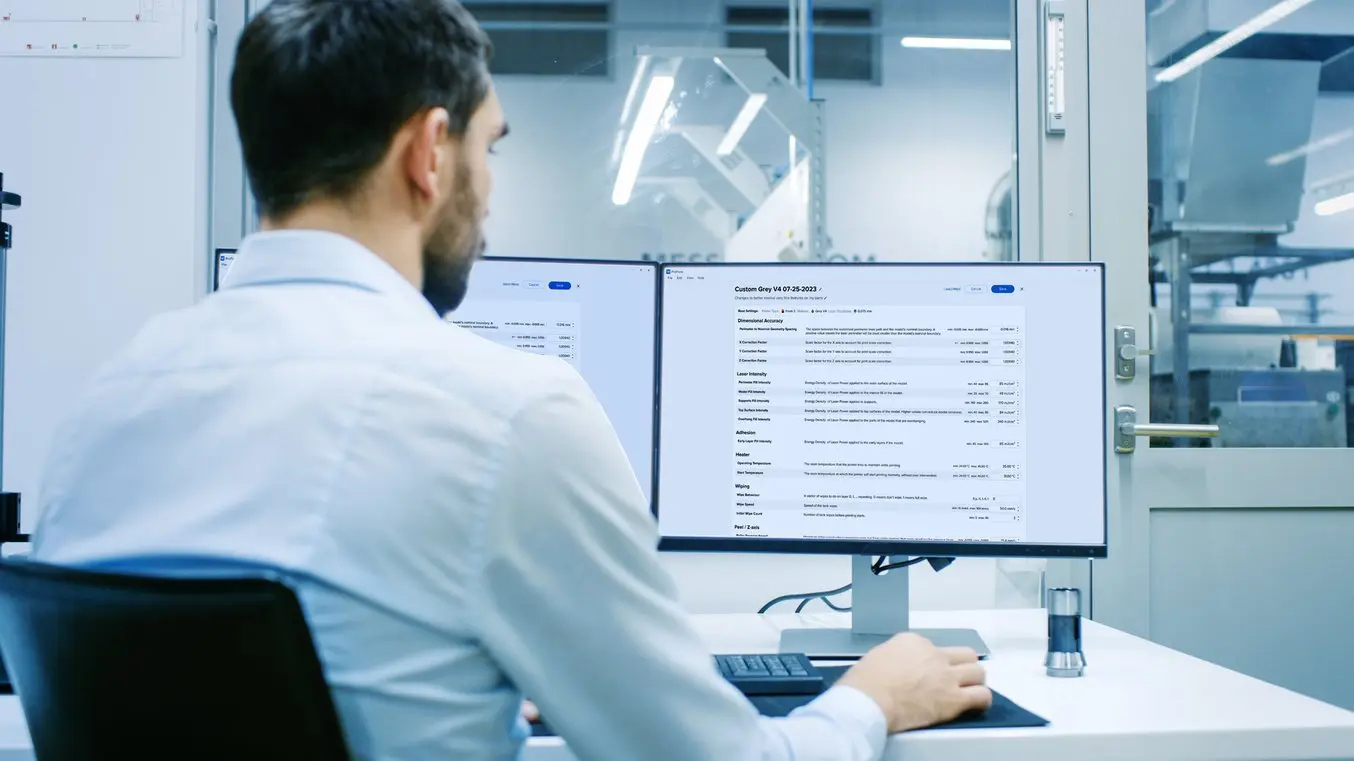
Talk to Our Sales Team
Whether you need to prototype at speed, or are producing end-use parts, we’re here to help. The Formlabs Sales team is composed of dedicated specialists who know exactly how to support you and your company's needs.
3D Printing Materials vs. Materials for Injection-Molding
3D printing materials often sacrifice mechanical properties for printability compared to their extruded and injection-molded counterparts.
In fused deposition modeling (FDM), the standard material is PLA, which has poor toughness. PETG, ABS, ASA, and PC offer superior toughness to PLA, but in order for these materials to print well, the material grades need to have lower molecular weights, co-polymers, or other components that reduce the performance of the final parts when compared to polymers that have been molded or extruded.
Stereolithography (SLA) is also known for using brittle plastics, as most standard acrylate resins have relatively poor toughness. Over time, tougher materials have been introduced, like Formlabs’ Tough 1500 Resin and Tough 2000 Resin. While these materials have significantly better toughness than most standard acrylate materials, they still lag behind most thermoplastic polymers in terms of toughness.
The printing process with the toughest materials is selective laser sintering (SLS). The default Nylon 12 Powder is much tougher than PLA or most acrylic resins, and even tougher options like Nylon 11 Powder create incredibly tough parts. These materials do not need to be modified for printability in the way that FDM materials need to be. Additionally, SLS has much better isotropy for toughness in all axes.
When considering such a broad array of available formulations, measuring the toughness of 3D printed materials is incredibly important to be able to quantitatively assess their fitness for more demanding applications outside of prototyping.
Quantifying Toughness
Tensile Toughness
Toughness is the ability of a material to absorb energy and plastically deform without fracturing, but there are several ways to quantify toughness.
One way is to perform a tensile test like ASTM D638, where a specimen is pulled apart by a pair of grips. The force on the cross-sectional area of the part, or stress, can be plotted relative to the elongation, or strain. Work is the dot product of force and distance. By taking the integral to calculate the area underneath the stress-strain curve, the energy absorbed before fracture can be determined.
ASTM D638 tensile test on Tough 1500 Resin V1.
ASTM D638 tensile test on Tough 1500 Resin V2.
This particular way of measuring toughness is often called “Tensile Toughness,” and while it’s useful for helping understand the meaning of toughness, it is not commonly measured or reported, making it more difficult to quantitatively compare toughness values and is rarely reported in a technical data sheet (TDS).

Elongation at Break
Elongation at Break: How long a material can be stretched before breaking, calculated by the difference between the changed length before breaking and the initial length.Elongation at break is sometimes used as a stand-in for toughness. When materials have a similar ultimate tensile strength, it is a reasonable approximation of the area underneath the stress-strain curve. This approximation is less useful when comparing materials with significantly different ultimate tensile strengths. Elongation at break on its own is a measure of ductility and not toughness.
Material | Tensile Strength (MPa) | Elongation at Break (%) |
---|---|---|
Tough 1500 Resin V2 | 36 | 165 |
Tough 1500 Resin V1 | 34 | 63 |
Loctite IND 405 | 38 | 119 |
Polypropylene (extrusion homopolymer grade)* | 29.2 | 125 |
*Densetec extrusion grade homopolymer samples were obtained from McMaster-Carr (Item # 8742K129) and tested internally by Formlabs under identical conditions as the printed resin samples.
Izod Impact Strength
Izod Impact Strength: The energy absorbed during the impact.The most common way to distill toughness down to a single number in a simple, easy-to-repeat test, is with Notched Izod impact testing. In this test, a hammer on a pendulum swings through a part, and the height of the hammer after the impact is measured. The difference between the hammer’s starting position and ending position represents a difference in gravitational potential energy, and this difference corresponds with the energy absorbed during the impact with the test specimen. This energy value is typically divided by the length or area of the test specimen, which gives us a value in J/m or J/m2.
Charpy impact strength is a similar test, but with a slightly different setup, and is used more commonly with metals. Either test can be “notched” or “unnotched.” With the notched variation a small notch is cut into the part to act as an initial crack source. Formlabs uses ASTM D256-10 for evaluating our materials.
Material | Notched Izod Impact Strength (J/m) |
---|---|
Tough 1500 Resin V2 | 45 |
Tough 1500 Resin V1 | 62 |
Loctite IND 405 | 42 |
Polypropylene (extrusion homopolymer grade)* | 36 |
In this Tough 1500 Resin V1 unnotched impact test, the hammer swings clean through the part.
In this Tough 1500 Resin V2 unnotched impact test, the part almost fully stops the hammer.
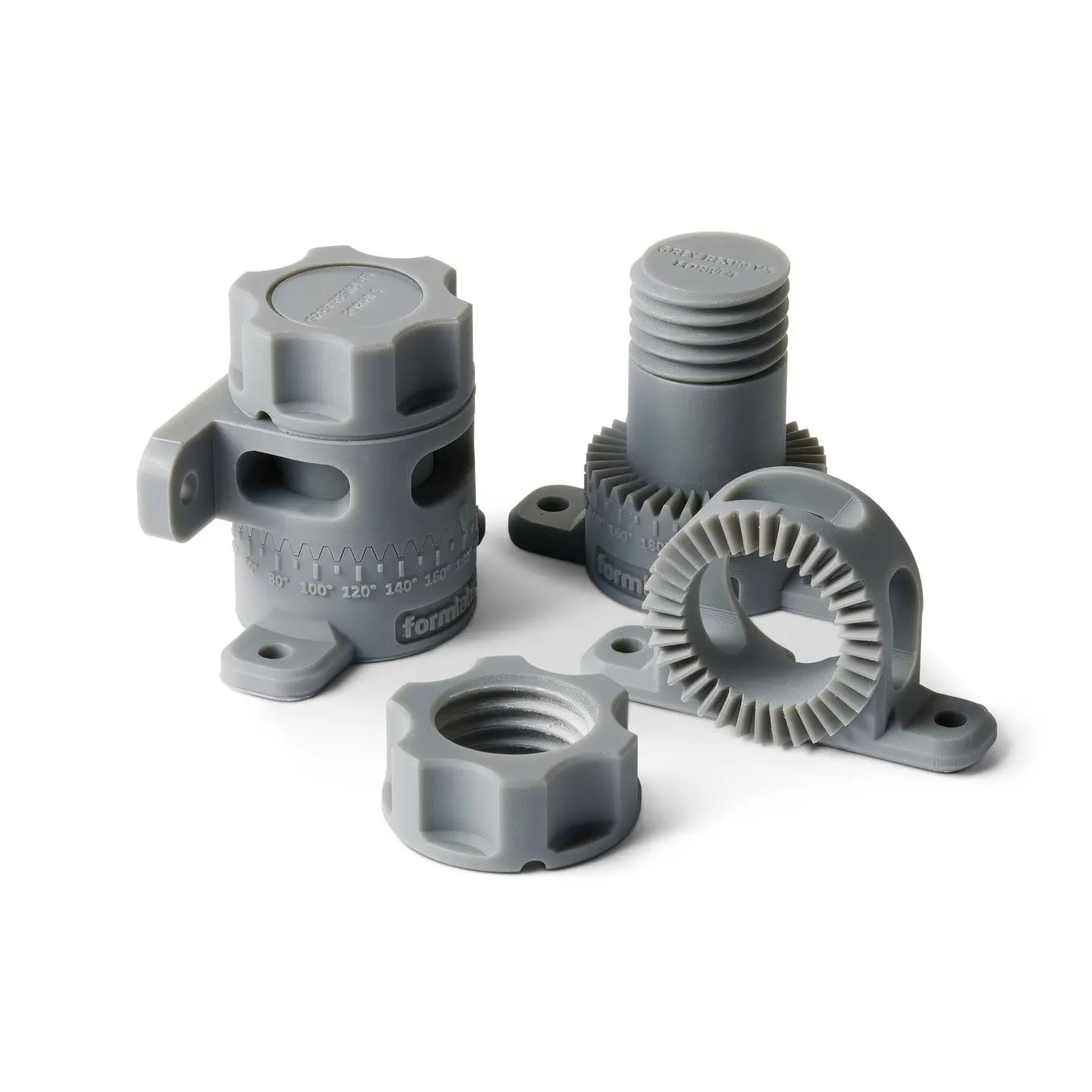
Request a Free Sample Part
See and feel Formlabs quality firsthand. We’ll ship a free 3D printed sample part to your office.
Gardner Impact
While Izod impact strength is more commonly reported since it is quick and easy to get a quantitative value, it is tested on a thick (~12 mm) specimen, which is often not representative of the geometries used in plastic parts.
Gardner impact strength (ASTM D4226) is a better test for measuring the impact toughness of a thinner sheet of material. The test uses a dropped weight to impact a thin specimen, which is then examined to see if the plunger penetrated the specimen. The result is expressed either in terms of the maximum height achieved before failure, or the maximum energy absorbed.
Because the specimen geometry for a Gardner impact strength test is more representative of most plastic parts, this is a more meaningful metric for impact performance in the real world. Formlabs material engineers therefore optimized the formulation of Tough 1500 Resin V2 to perform better in this metric.
Material | GARDNER AT 1/32” (J) |
---|---|
Tough 1500 Resin V2 | 5.9 J |
Tough 1500 Resin V1 | 2.5 J |
Loctite IND 405 | 3.4 J |
Polypropylene (extrusion homopolymer grade)* | 2.7 J |
Tough 1500 Resin V1 reaches a Gardner impact strength of 2.5 J. This is one stage of the tests.
Tough 1500 Resin V2 reaches a Gardner impact strength of 5.9 J. This is one stage of the tests.
Fracture Toughness
Plastics behave differently based on the rate that loads are applied to them. With impact testing, a load is applied very quickly, but real-world materials also need to absorb energy when forces are applied more gradually.
One way to measure toughness at lower strain rates is by measuring fracture toughness.
This can either be expressed as a value called KC, which is the critical stress intensity factor for a crack to propagate and cause brittle fracture; or Wf, which is the work (or energy) required to propagate a crack through the material.
Fracture toughness is one of the most important toughness measurements because it represents resistance to brittle fracture under most non-impact loads.
Material | Work of Fracture (Wf) |
---|---|
Tough 1500 Resin V2 | 1011 |
Tough 1500 Resin V1 | 102 |
Loctite IND 405 | 407 |
Polypropylene (extrusion homopolymer grade)* | ~2000 |
In this ASTM D5045 fracture toughness test on a Tough 1500 Resin V1 part, there is a brittle, fast fracture.
In this ASTM D5045 fracture toughness test on the Tough 1500 Resin V2 part, the part fails with more ductility and absorbs 10x more energy than the Tough 1500 Resin V1 part.
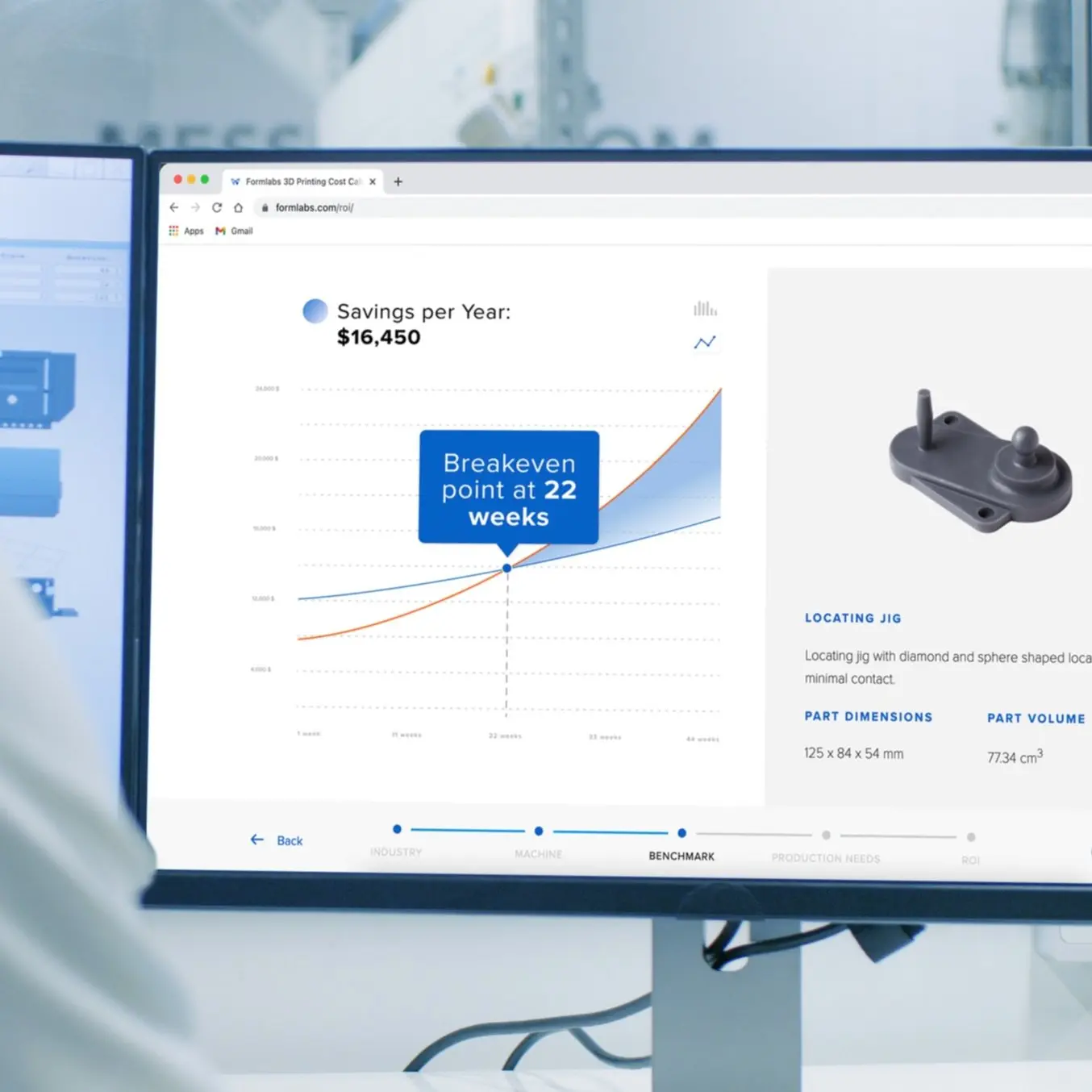
Calculate Your Time and Cost Savings
Try our interactive ROI tool to see how much time and cost you can save when 3D printing on Formlabs 3D printers.
Ross Flex
Cracks and fractures can also occur over time, rather than in loading like in fracture toughness. The gradual propagation of crack repeated loads is called fatigue.
To measure fatigue properties in plastics, we typically use a test called Ross Flex (ASTM D1052) which repeatedly bends bar-shaped specimens thousands of times.
Material | Ross Flex (cycles survived) |
---|---|
Tough 1500 Resin V2 | >8,000 |
Tough 1500 Resin V1 | ~5,300 |
Loctite IND 405 | ~6,800 |
3D Printing With Tough Resin
While there are many ways to measure the toughness of a material, some metrics are more relevant to 3D printed parts than others, especially for applications other than prototyping, such as rapid tooling, end-use parts, and manufacturing aids. Differentiating between different toughness measurements can help users select the optimal material.
Toughness can be quantified in a variety of ways, but parts in the real world need to be tough in multiple ways in order to perform with the rugged survivability that tough plastics are known for. Formlabs material engineers therefore optimized the formulation of Tough 1500 Resin V2 to perform well across all of these metrics rather than optimizing for just one marketable number like Izod impact strength. By focusing on the fundamental science of toughness, Formlabs Tough 1500 Resin V2 will enable users to print parts that don’t shatter, crack, or snap, allowing them to confidently pursue demanding applications.
To better support the comparison and selection of materials — including tough resins — Formlabs has added new toughness metrics to our TDS, including Gardner Impact Strength and Fracture Toughness. TDS can be found on each material page, and our material compare page makes it easy to view metrics side-by-side.
Explore the Formlabs material library, request a free sample part to evaluate a material for yourself, or contact sales to discuss your unique application.