Selective laser sintering (SLS) 3D printing is an ideal solution for creating affordable, on-demand consumable parts like these collet pads, which act as the bridge between always-changing products and the CNC turning machine.
The Factory Amsterdam (TFA), a New York-based machine shop that focuses on automation and quick turnaround production for customers in consumer electronics, gas turbines, and more, has no shortage of manufacturing methods at their disposal — from CNC machining to lathes, laser cutting, sheet metal forming, and more. But when it comes to making peripheral tooling — the tools, jigs, fixtures, masks, or aids that help make the parts — TFA needs an inexpensive, flexible, and reliable solution in-house. We spoke to TFA’s owner Bradley Matheus about how the Fuse Series SLS 3D printer has helped them reduce costs for manufacturing aids significantly and improve their efficiency.
“Most of the work that I'm doing is a very quick turnaround, so I don't even have to think about it. If it's something weird that my existing tooling can't grab onto, I just throw some of these in and it's done. [The Fuse] really is a problem solver.”
Bradley Matheus, Owner, The Factory Amsterdam
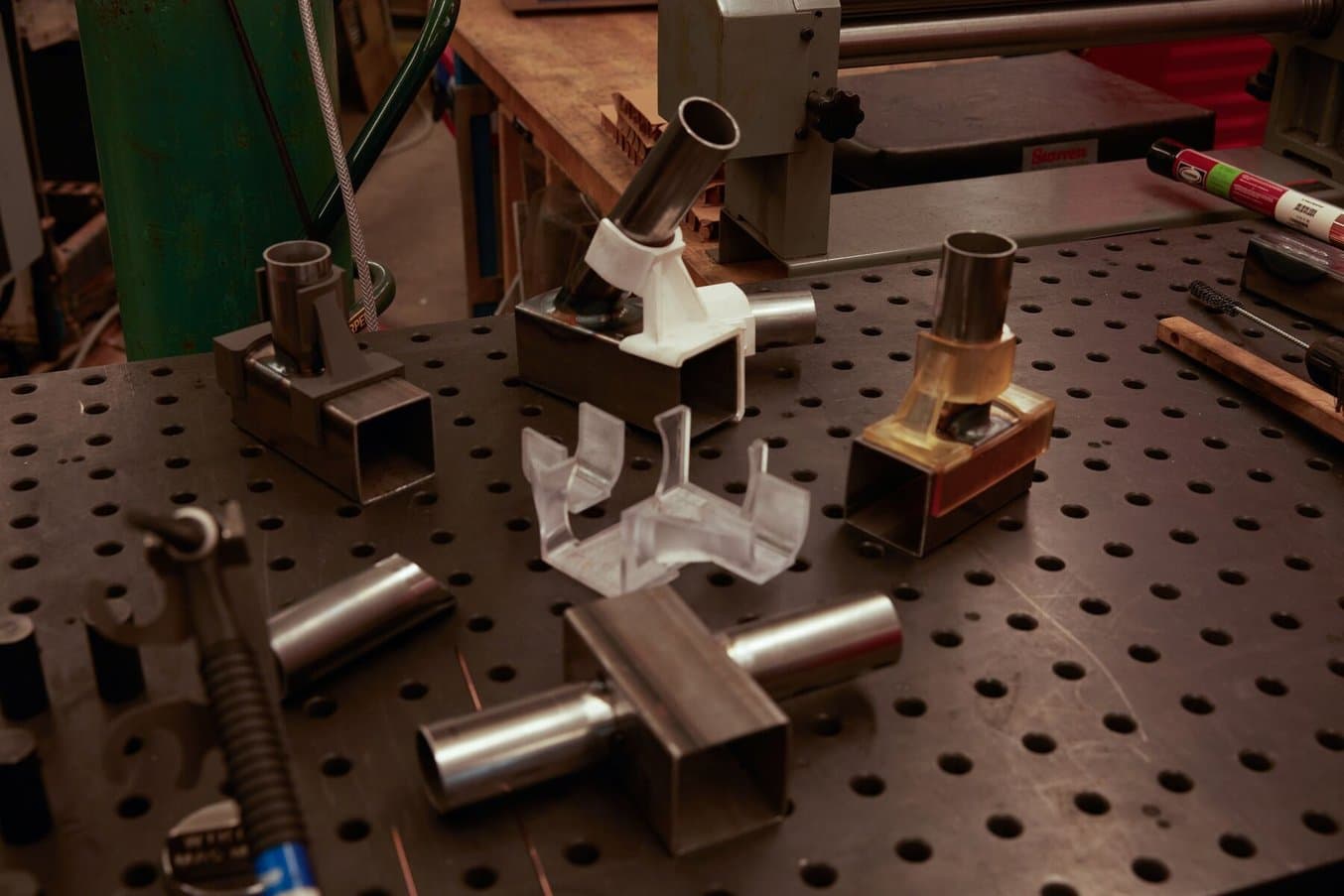
Low-Cost and Rapid Jigs and Fixtures for Metal Fabrication
The Factory Amsterdam (TFA), a CNC Machine Shop focused on automation, leverages Formlabs SLS technology to gain flexibility and adapt faster to customer needs. This webinar provides an overview of the step-by-step method as well as practical examples with cost analysis, design considerations, and best practices to 3D print jigs, fixtures, and other tools.
Customized Consumables from $150 to $7
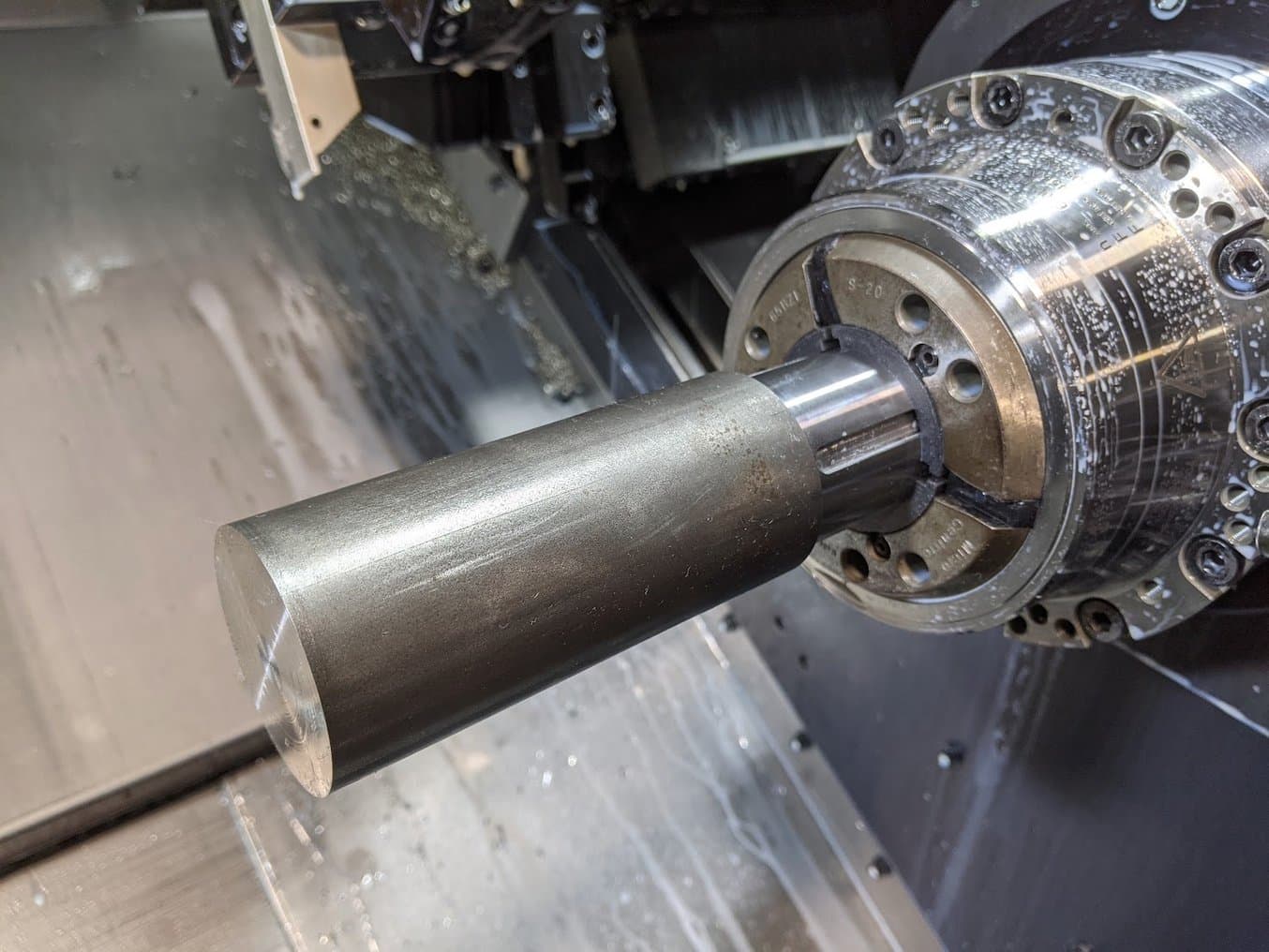
Customized collet pads are needed to hold the metal part securely inside the spindle for each part in the production run.
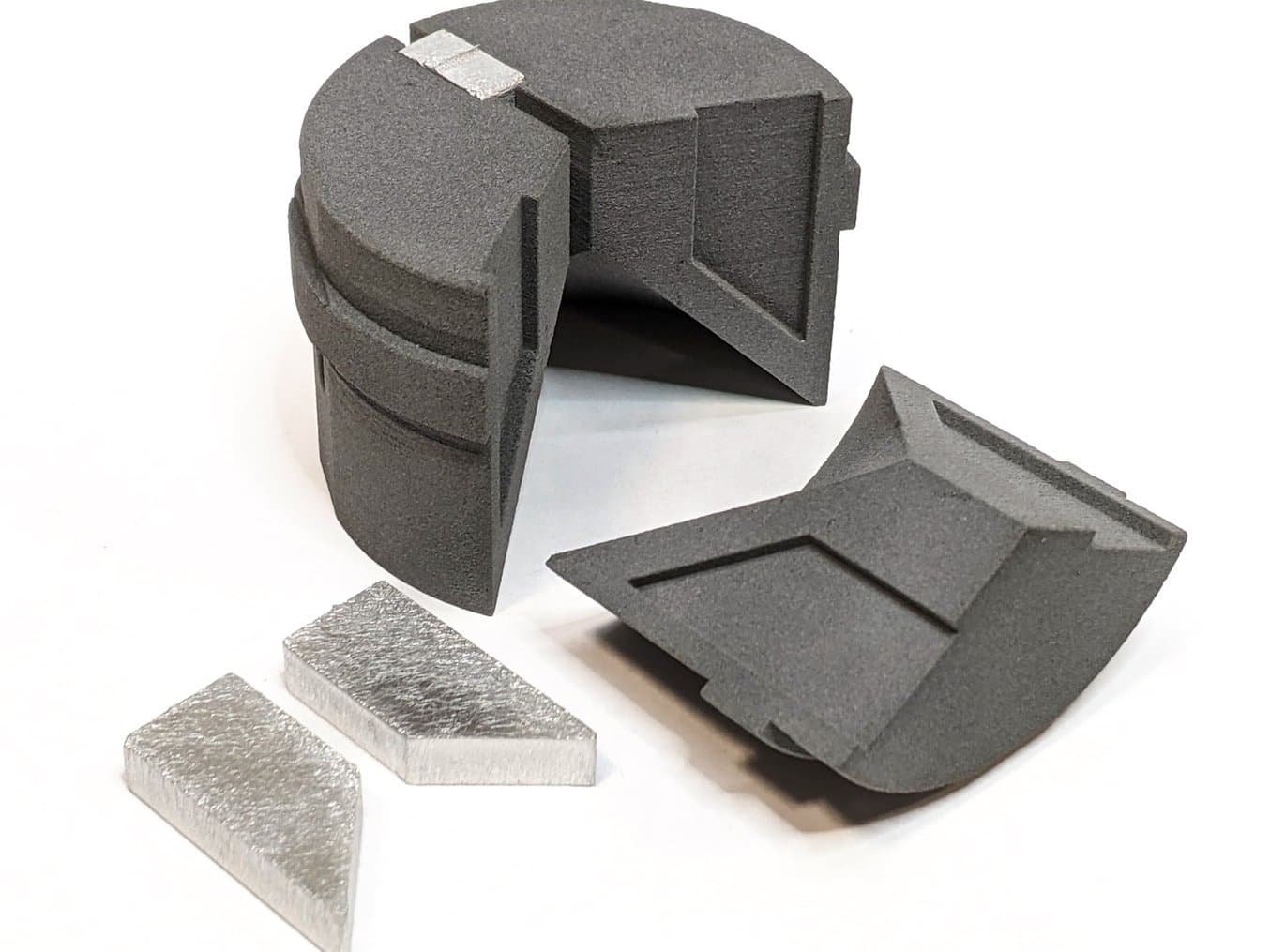
SLS 3D printing excels at producing small parts like these collet pads — consumable parts that nevertheless have to hold up through an entire production run of 3,000 to 4,000 parts and withstand radial forces generated from the lathe turning at 3,000 rpm.
TFA regularly fulfills production orders for machined metal parts in order volumes between 1,000 and 10,000 units. Their CNC turning machine has to be adjusted for each new type of product, and one way to do that is to purchase steel collets featuring interchangeable pads. The collets fit inside the spindle to hold the raw metal part securely in place while the pads are removable inserts to adapt to various shapes of workpieces without the need to change the entire collet.
These collet pads are consumables, as they need to be customized for each job — they’re the integration point between a standardized machine and a uniquely designed product. “The part these collets are grabbing onto might already be machined and have a weird shape, so a standard collet isn’t the best way to hold that part,” says Matheus.
To adjust for new product designs, you could purchase machineable or master collets that can be altered for your part and machine, or a set of swappable collets. But for each of these solutions, there is still a cost and lead time associated. “Machineable collet pads are still a couple of hundred dollars apiece, and they take about three weeks to get here,” says Matheus. On the Fuse Series, Matheus can 3D print as many sets as he needs on-demand, for just $7 each.
CNC Turning Fixture
Alternative Method | 3D Printing In-House | |
---|---|---|
Equipment | Metal CNC Machined, Outsourced | Fuse Series, Nylon 12 Powder |
Cost | $150 | $7 |
Time | 3 - 4 weeks | 1 day |
Matheus had tried producing these parts with other technologies, like fused deposition modeling (FDM) 3D printing, but found that the parts exhibited signs of creep and delamination and didn’t have the chemical resistance necessary to interact with the coolants used during the turning process. The coolant is a mix of 10% petroleum-based oil and 90% water and can be quite abrasive to most plastics. Nylon 12 Powder parts showed excellent chemical resistance throughout the process. “Nylon 12 was actually quite resistant and held up extremely well,” says Matheus.
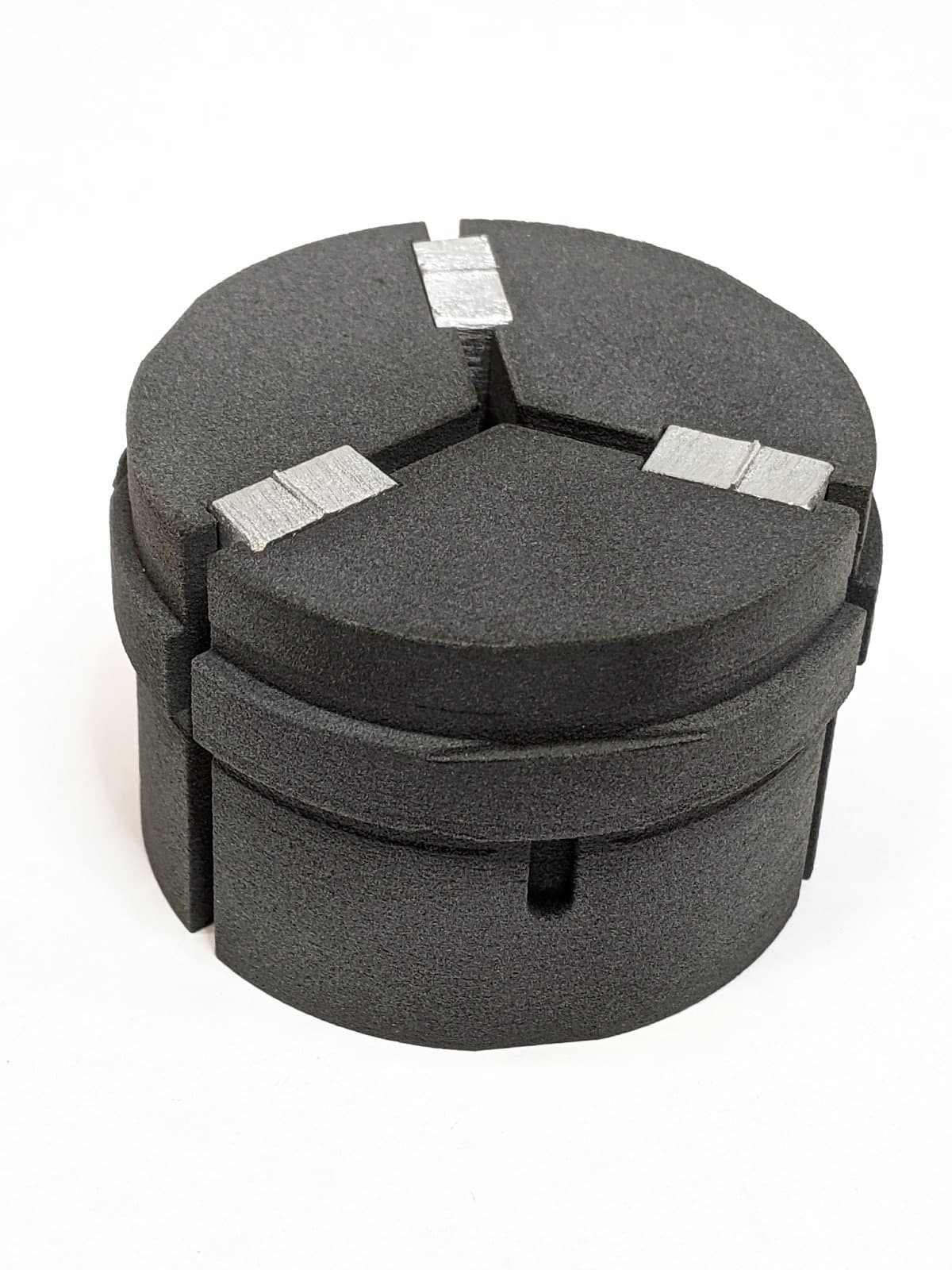
The SLS 3D printed collet pads need to be dimensionally accurate and highly precise in order to fit seamlessly together and integrate into the spindle. Any deviation could cause issues in the integrity of the turning process.
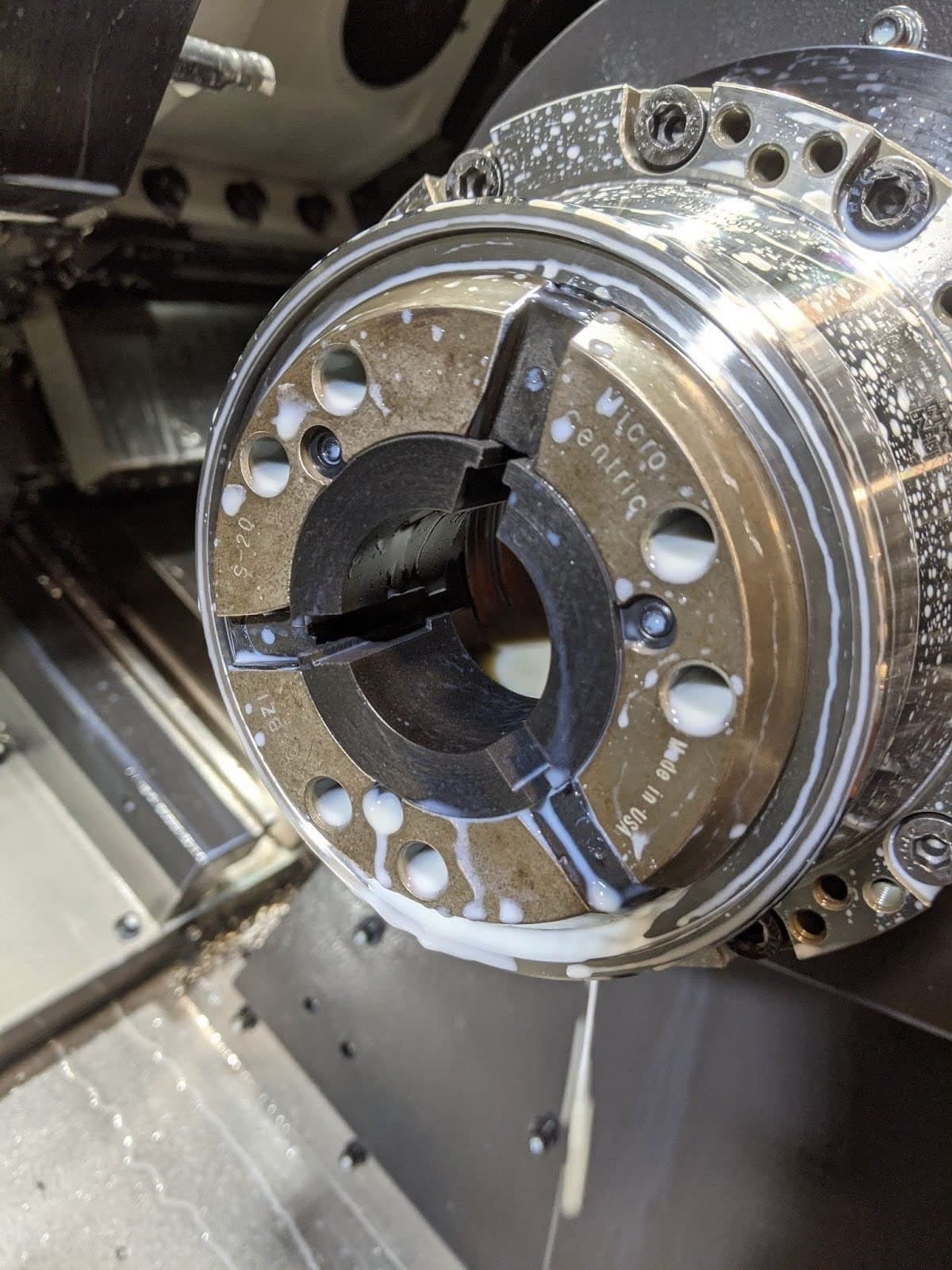
The tools are continuously in contact with the coolants inside the lathe. It is a semisynthetic oil that is aggressive on a lot of plastics and dissolves FDM materials. Nylon 12 Powder is chemically resistant and does not wear from it.
Bringing the Fuse Series in-house allowed Matheus to custom-design these collet pads with the accuracy and strength necessary to handle the clamping pressure and radial forces of the CNC turning process. Matheus has used a single set of collet pads for production runs up to 3,000 parts for more than one hundred hours of production, with no signs of wear.
“I ran them nonstop. It’s quite a demanding application. The pads need pretty high-precision interfaces and it’s really hard to produce that accurately with 3D printing. That’s where the Fuse really shines.”
Bradley Matheus, Owner, The Factory Amsterdam
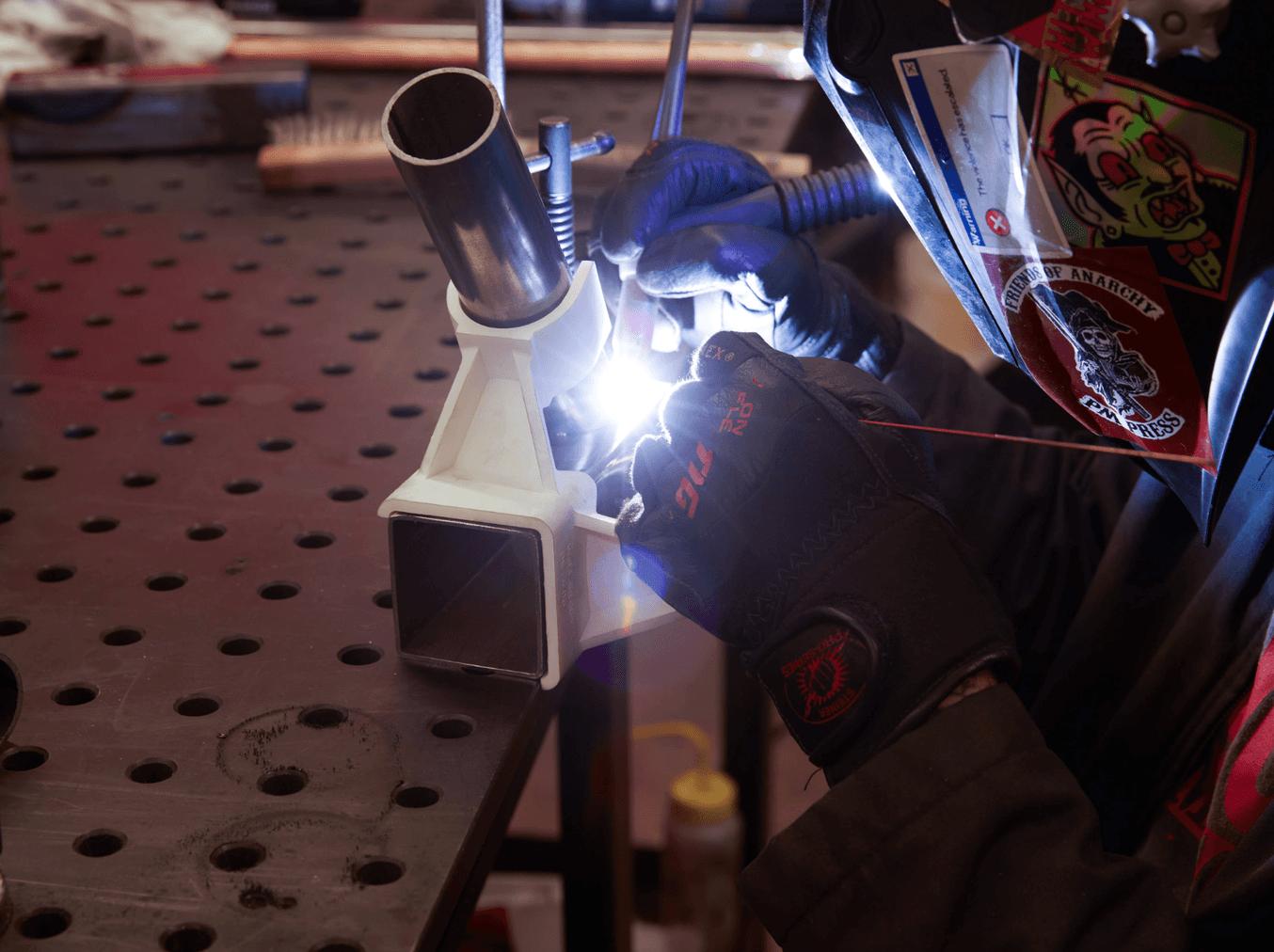
Low-Cost and Rapid Jigs and Fixtures for Metal Fabrication
This white paper outlines a methodology for using 3D printers to produce jigs, fixtures, and other tools for metalworking. Real-world case studies show how Formlabs printers create durable, precise, and heat-resistant tools that perform well in demanding environments. It highlights how companies can cut lead times and costs by up to 90% while improving tool customization and complexity.
Magnet Assembly Tools
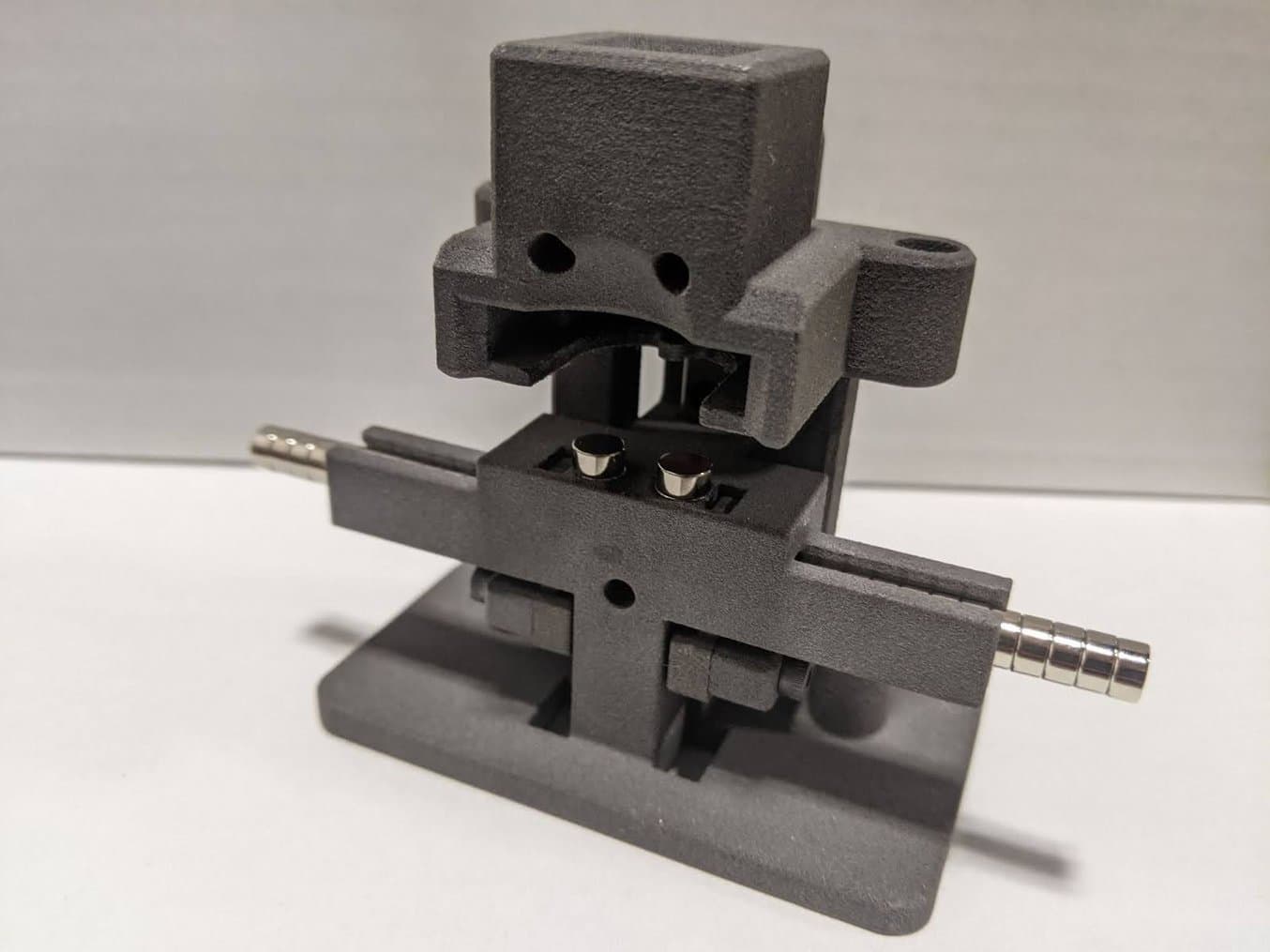
This magnet assembly jig makes the process of assembling magnetized parts much easier, reducing wear on operators and improving productivity.
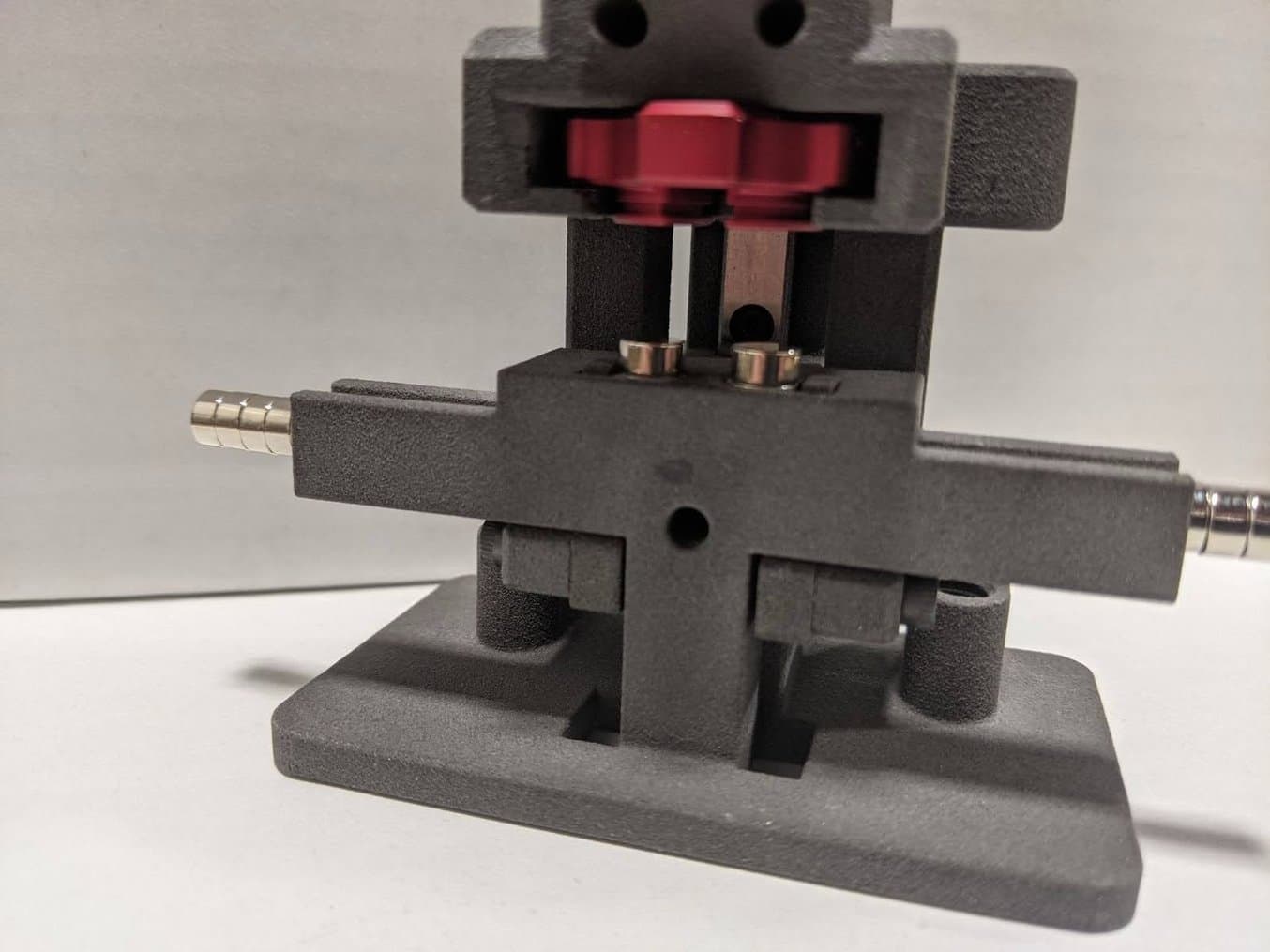
The production run called for 6,000 N52-grade magnets (a significant attraction force) to be installed on a part after it’s machined. This has improved the difficult and labor-intensive assembly process.
For one order of 3,000 units, parts were machined and then assembled with two N52-grade magnets. The labor involved was arduous, time-consuming, and hard on the operators’ bodies. Matheus designed a press jig that could feed and install the magnets with a manual lever press, automating the hardest part of the process. “Assembly tooling for magnet installation is highly customized for every application, so we’d be ordering a customized tool no matter what. But in-house SLS allows us to iterate a lot faster and produce very high-precision components. I could machine something like this, but the less time peripheral tooling takes, the better. We want to free up the production equipment,” says Matheus.
While working on prototyping the automated assembly jig, Matheus developed an interim solution — an ergonomically designed magnet presser that pushes the magnets out without much manual effort.

This ergonomic magnet assembly aid makes it easier to separate and install magnets onto a product, removing much of the difficult labor the manual process demands. Nylon 12 Powder’s strength and light weight make it easy to use continuously, even when dispensing 6,000 magnets.
Though still a mostly manual process, the new assembly tool reduces wear and tear on the operators and speeds up the time it takes to install the two magnets. Costing only a few dollars of powder, tools like these drastically improve productivity and help Matheus get orders out the door quicker.
“The Fuse Series allows us to produce much more robust assembly tooling than we would otherwise be able to and in a cost-effective manner. It allows us to iterate faster and produce very highly accurate parts without a lot of effort.”
Bradley Matheus, Owner, The Factory Amsterdam
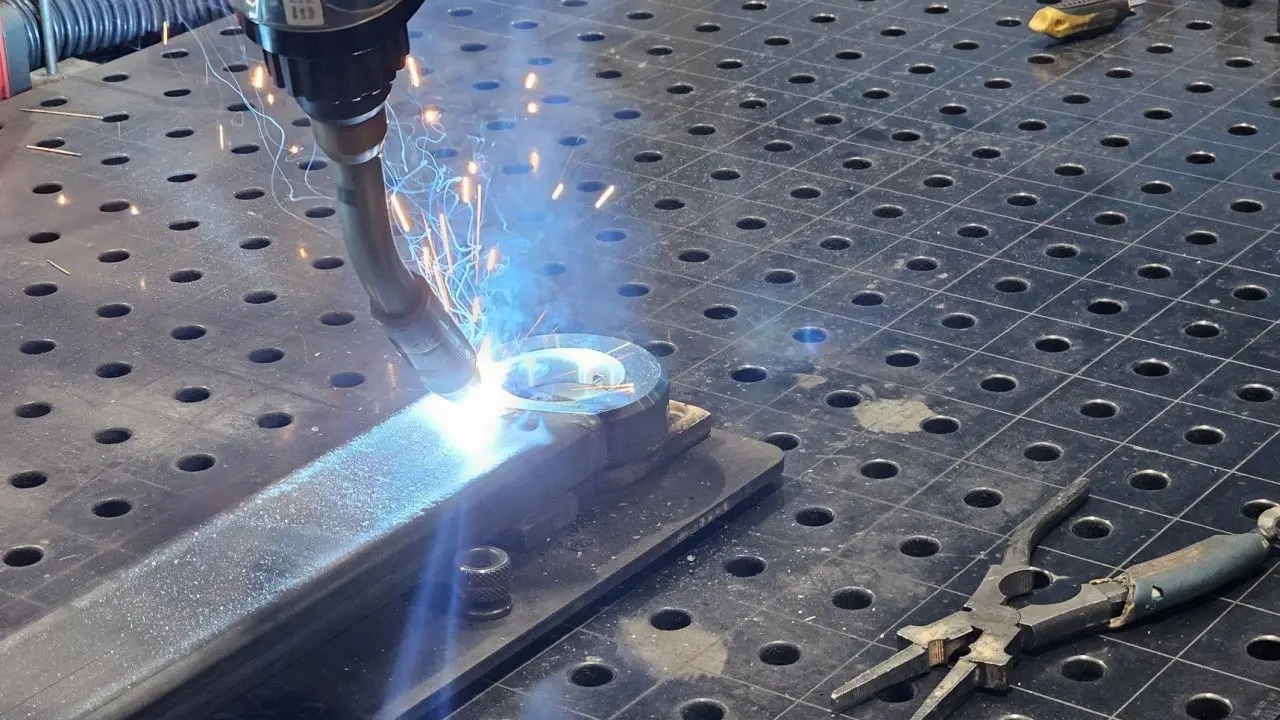
Quick Custom Welding Fixtures With 3D Printing
Discover how to streamline your tooling process to accelerate rapid prototyping and low-volume production of metal parts with quick and modulable welding fixtures. Our R&D machine shop coordinator shares methods and best practices for 3D printing welding fixtures, including design guidelines, tool temperature study, practical examples, and cost analysis.
The Unique Part of Mass Production
Manufacturers know that designing a product isn’t the hard part — figuring out the equipment, and processes needed to manufacture that part tens of thousands of times, is. Small and medium-sized businesses like TFA have the tools they need to make anything they need — but machining peripheral tooling isn’t efficient.
Bringing SLS 3D printing in-house has freed up Matheus’s production equipment while still delivering highly accurate and robust parts. Printing assembly jigs, grippers, workholding devices, and more, in-house on the Fuse Series SLS printer allows Matheus to focus on growing his business.
“When it comes to assembly processes, everything is bespoke, it's just not something you can often buy off the shelf. So having a highly flexible manufacturing option in-house is invaluable,” says Matheus.
To learn more about metalworking, watch our webinar with TFA, download our in-depth white paper,, or discuss your application with our experts. To see the robust quality of SLS 3D printed materials for yourself, request a free SLS 3D printed sample.