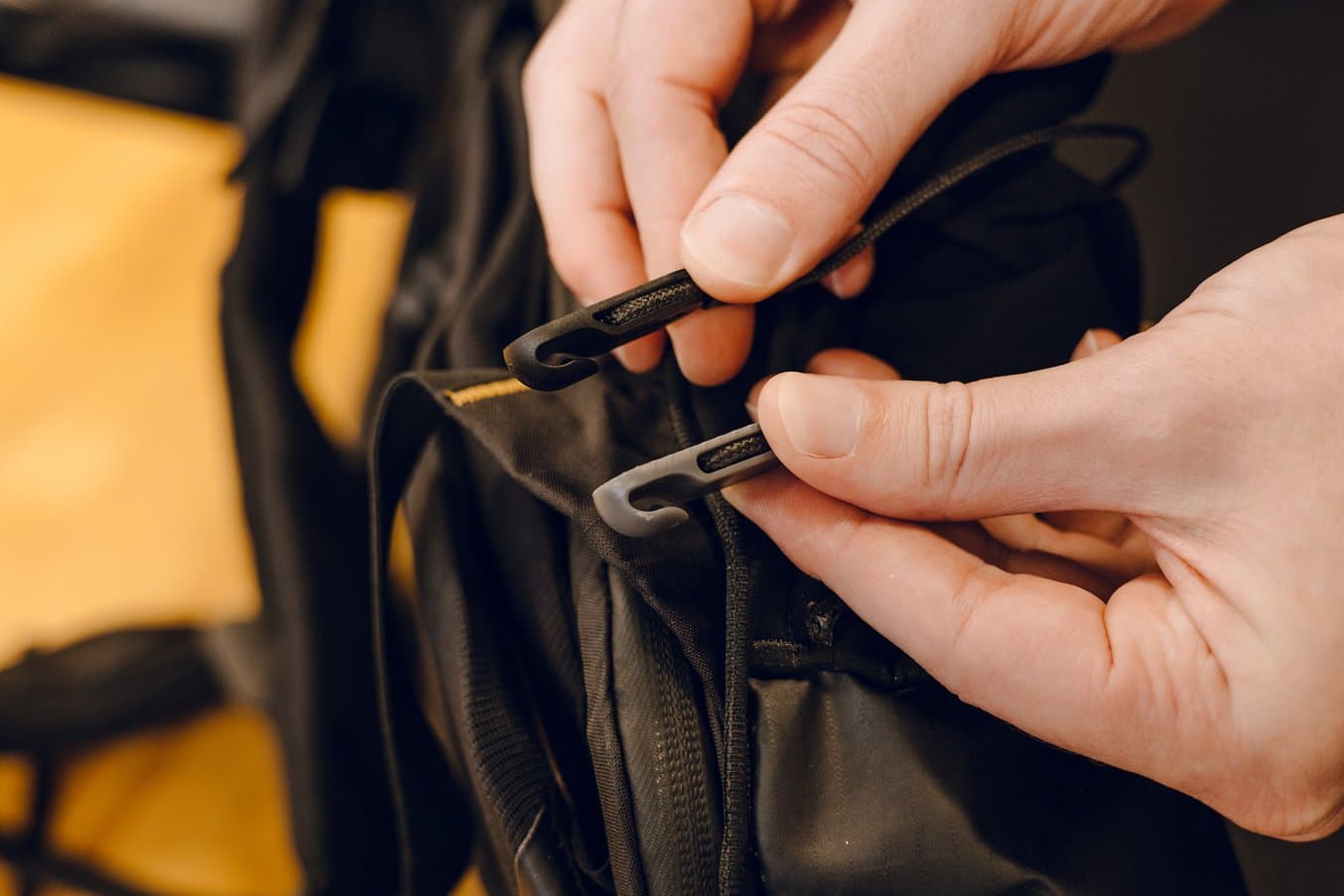
Peak Design products, from bags and luggage to camera straps and cases, are set apart because they feature design-forward hardware that’s highly functional without fiddling or adjusting. This means that every aspect of their gear — including a cinch hook, tension lock, or flat hook — is customized.
“The custom hardware aspect of Peak Design has been baked in the DNA since our first bag. You're interacting with these touch points on the bag all day, multiple times a day. For us, it’s incredibly important to have that feeling be tuned.”
Dane Jones, Senior Design Engineer, Peak Design
Prototyping each piece of custom hardware requires dozens of iterations, and since Form 2, Formlabs stereolithography (SLA) 3D printing has been a key part of the process. But upgrading to Form 4 revolutionized the prototyping process, enabling three to four iterations a day, less time spent on post-processing and finishing, and finer surfaces.
“Formlabs printers are basically the backbone of our research and development here at Peak Design.”
Dane Jones, Senior Design Engineer, Peak Design
Prototyping Custom Hardware With 3D Printing
Dane Jones, Senior Design Engineer, has worked on numerous projects at Peak Design, including the custom hardware that enables outdoor bags like the Outdoor Backpack to be uniquely versatile.
“Hardware development is incredibly time and resource intensive — these parts are deceptively complex,” says Jones. For many companies, who are concerned primarily with aesthetics, Jones says, “it’s easy to order a part that is close to the part needed, and works just okay.” But at Peak Design, okay isn’t good enough.
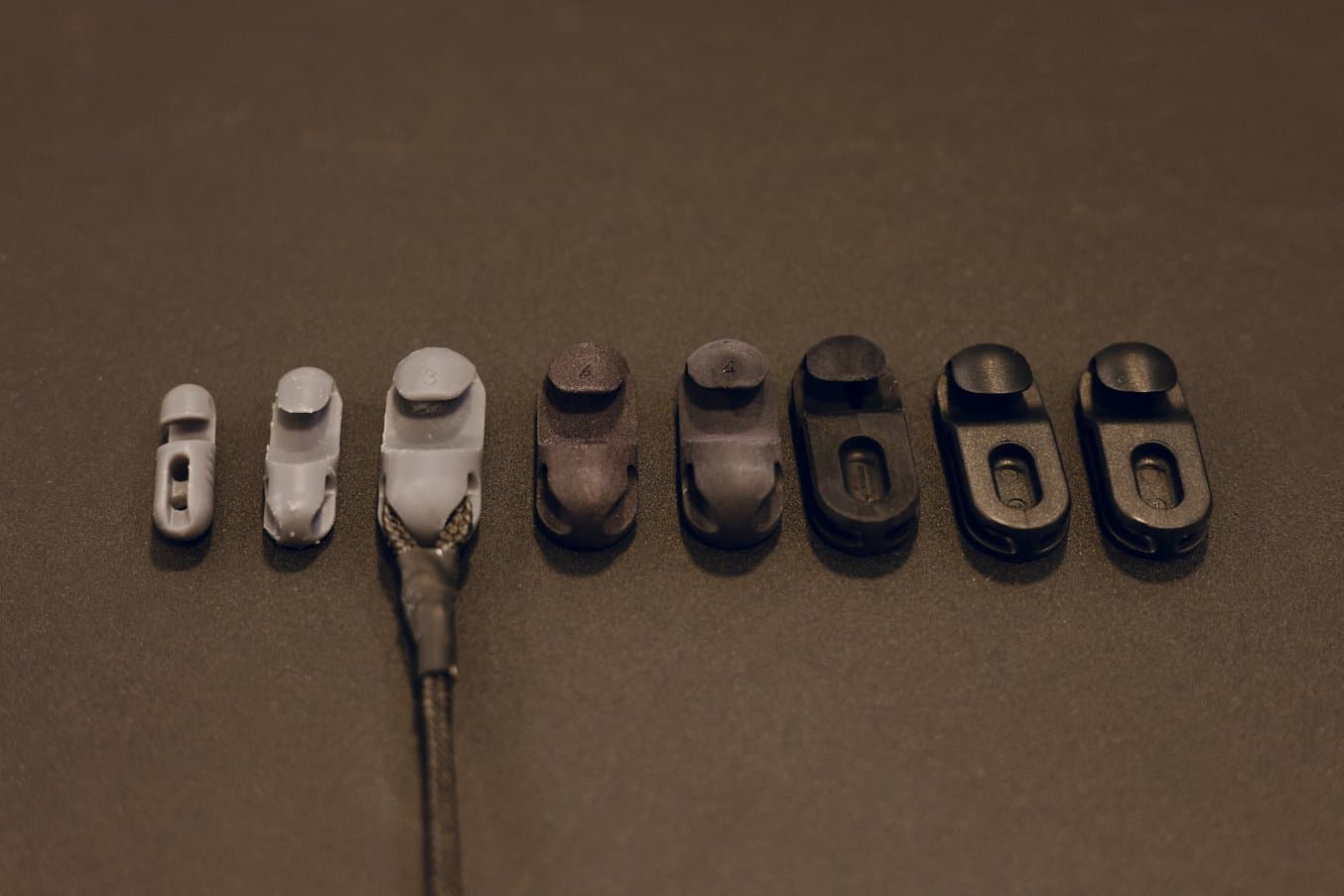
At left, prototypes SLA 3D printed in Tough 2000 Resin (left). Middle prototypes are SLS 3D printed in Nylon 12 Powder, and CNC and PA66. Parts at far right are injection molded from PA66.
Instead, the engineers and designers and Peak Design work to create the optimal part. They start by taking a look at what’s on the market, and learn from these available parts what’s working well. Then, Jones and his team ask the questions, “What's still wrong with this? Is it an aesthetic thing? Is it a UX thing? Is it not very intuitive?" From there, a list of design requirements is generated: color, material, cost, branding, number of moving parts, etc.
Custom hardware has to be developed in concert with trim, the softgoods like webbing or cord. Jones says, “It is very challenging to maintain forward momentum in a project when hardware, which usually has the longest lead time for tooling, can't really finalize until the trim is finalized.”
Therefore, in order to keep momentum on a project, hardware prototyping needs to keep pace with the trim department, meaning the speed and reliability of prototyping processes are key.
“The single most important prototyping tool that we have in house at Peak Design is 3D printing. Formlabs has been really pleasant to work with and it's very easy for us to make a decision in terms of increasing our prototyping capability.”
Dane Jones, Senior Design Engineer, Peak Design
Multiple Iterations a Day With the Form 4 Ecosystem
“We use SLA for the majority of the prototyping here at Peak Design just because in one day you can get several turns on a round of prototypes. For us, it's a big deal to have a lot of added manufacturing capability in-house for prototyping.”
Dane Jones, Senior Design Engineer, Peak Design
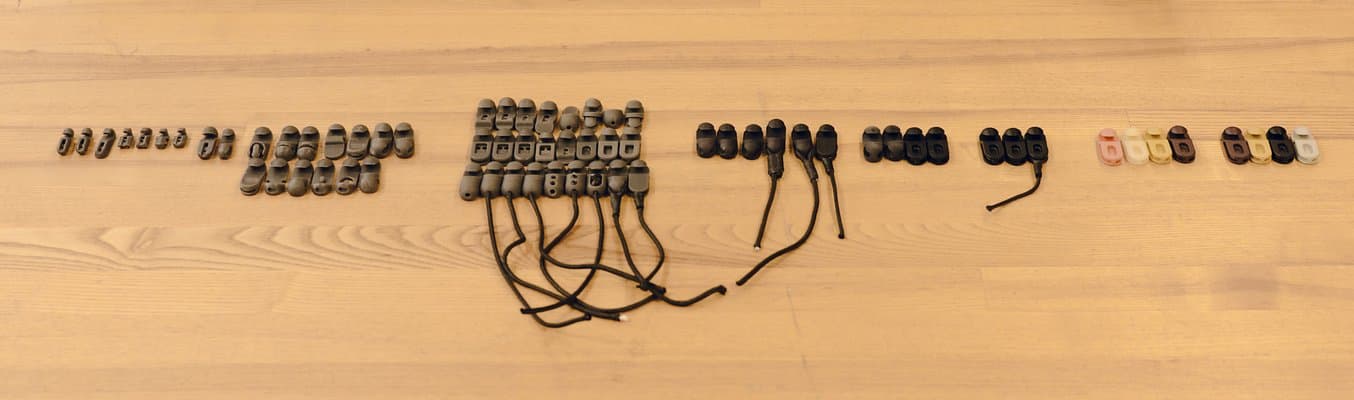
Hardware, like these cord hook prototypes, go through dozens of iterations so that even the smallest detail is optimized. The grey hooks on the left are 3D printed with Tough 2000 Resin, with final hardware on the far right.
Peak Design has been using Formlabs 3D printers since Form 2, as “It’s super accessible. Nothing else comes close to the accessibility for new designers and engineers. In a relatively short amount of time, you can teach somebody how to interact with a printer, upload a part, post-process, validate, and move on to the next step.”
To maintain momentum, rapid iteration is required, and any time-savings during printing, post-processing, or finishing mean more iterations can be completed in a day or week. Therefore, when Jones and the other design engineers saw the specs for Form 4, they knew they needed to add it to the in-house lab. Peak Design added three Form 4s to the four Form 3s they already had.
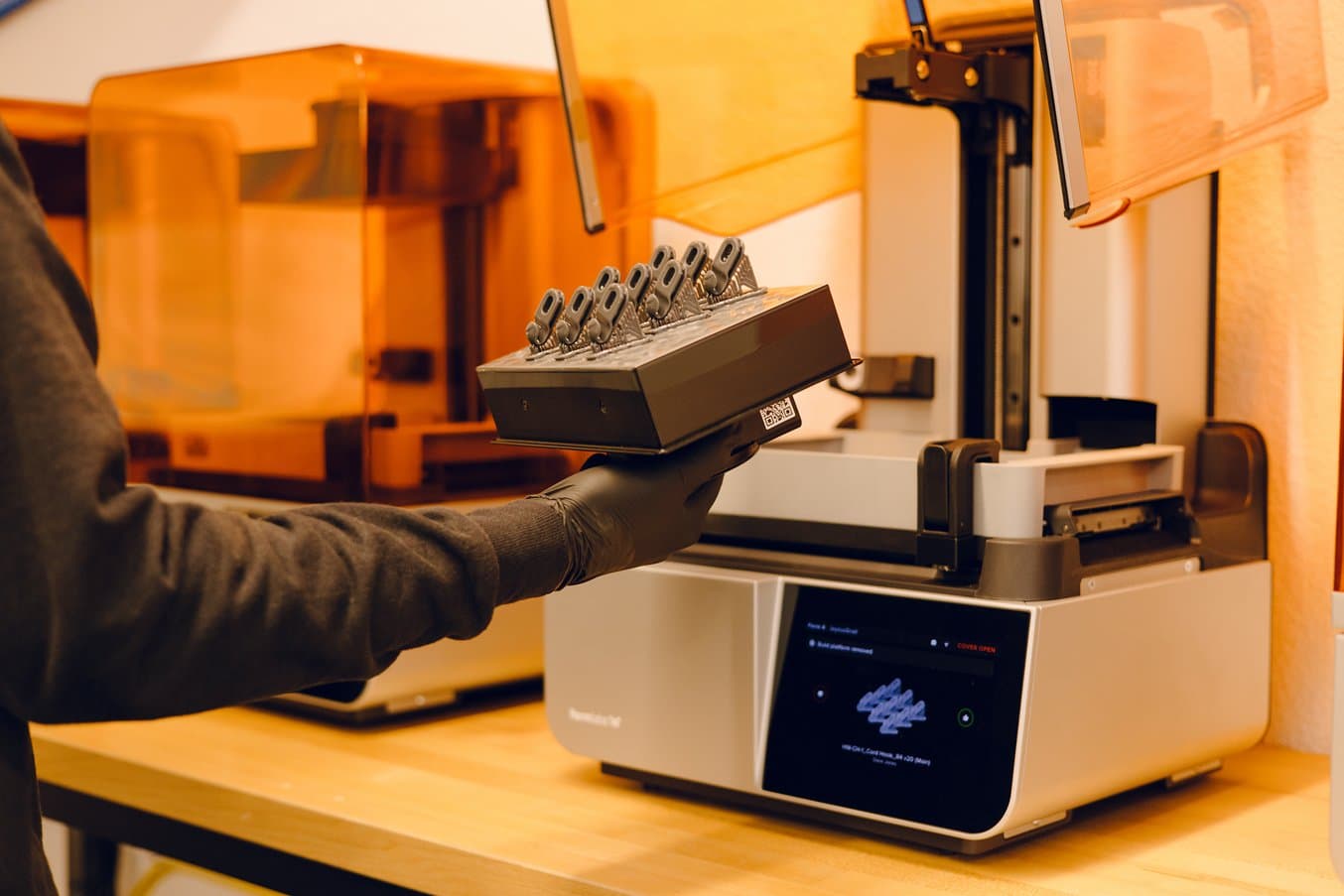
These cinch hooks in Tough 2000 Resin take just one hour to print on Form 4, enabling more iterations per day.
“Within an hour of having the Form 4s hooked up and online, they were all going constantly. The big thing that we noticed was the speed — prints done within an hour. Previously, you would get maybe one or two turns on a prototype in a day, now it’s three or four.”
Dane Jones, Senior Design Engineer, Peak Design
Moving from Form 3 to Form 4, Jones noticed more than speed. “The parts look better and the dimensional accuracy appears to be better on the Form 4s. Not only are we seeing much higher resolution, I don't see a huge difference now between the fidelity of a Tough 2000 part and the standard resin part on the Form 4s.”
Jones has also found that he can use fewer and smaller support points on Form 4 prints, thanks to updated settings for Tough 2000 Resin that make it easier to remove supports and achieve fine surface finishes with less finishing — all without affecting print time.
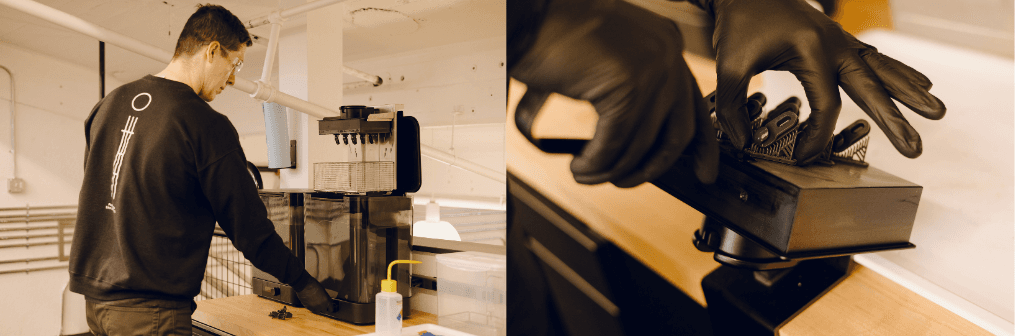
Streamlining workflows from printing through post-processing and finishing saves time, enabling more iterations a day.
SLA parts need to be post-processed. Post-curing parts printed in Tough 2000 Resin with Form Cure (2nd Generation) can be done in seven minutes, saving 53 minutes from post-curing with Form Cure (1st Generation). Jones says, “Anything we can do to speed up the workflow considerably saves us a lot of time in the development process, and that ends up being money saved.”
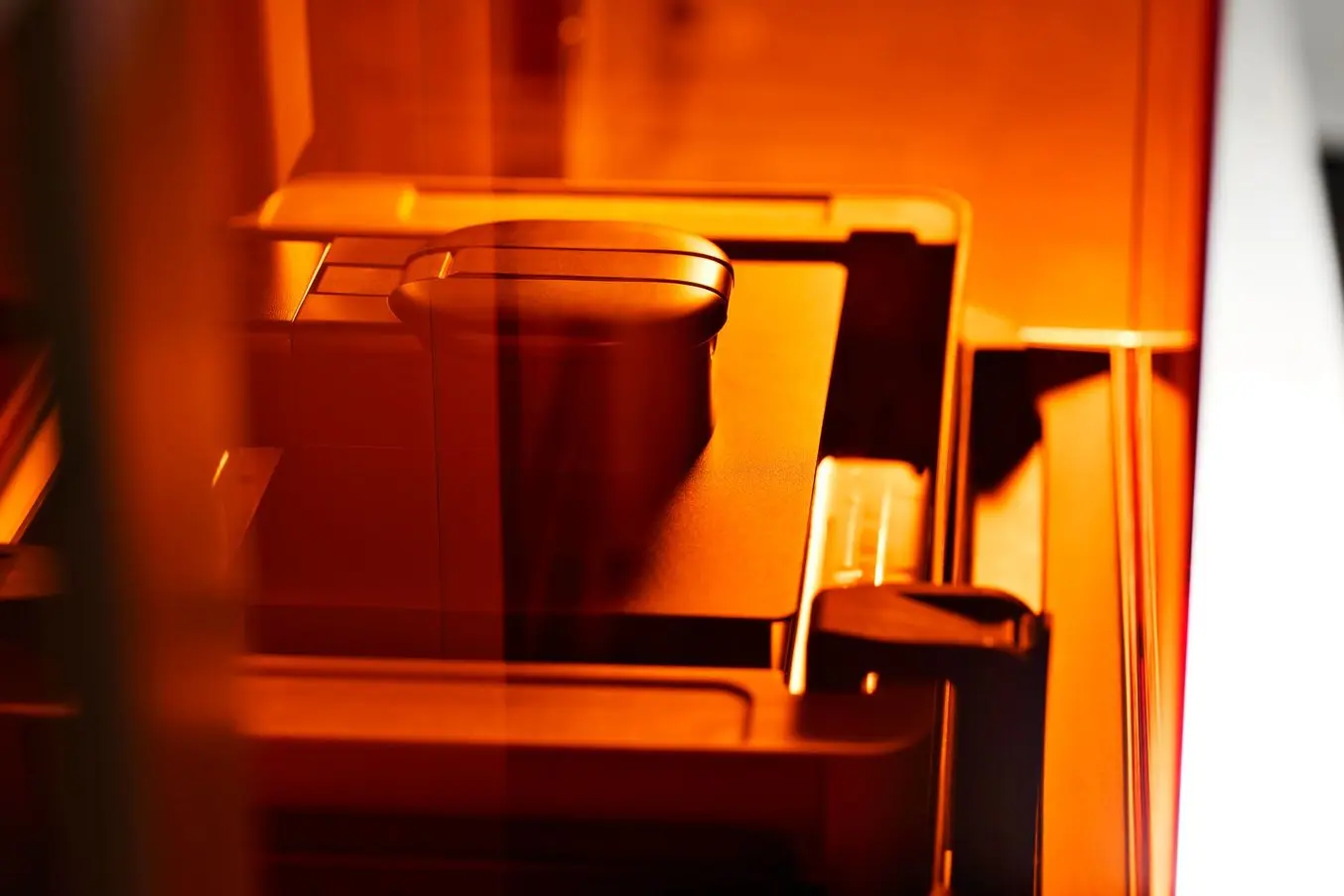
Product Demo: Form 4
See how Form 4 can enable new levels of productivity and innovation through its unmatched speed, accuracy, and reliability.
Strong and Flexible SLA Materials
“The standard resins are great because they’re incredibly fast and high resolution. For small parts with a lot of loading, we use Tough 2000 Resin. We found it had this great combination of good enough resolution for a part that had tiny features, quite strong, and quite flexible if you had small flexures in it.”
Dane Jones, Senior Design Engineer, Peak Design
General Purpose Resins are formulated to print quickly on Form 4 and are used for looks-like prototypes. But Tough 2000 Resin is used to prototype parts that are later molded in glass-filled PA66 or Delrin, another common material for hardware. These parts need to be robust, accurately print tiny features, and be flexible enough for the production of compliant mechanisms. Jones says that Tough 2000 Resin “does a pretty good job of approximating those material characteristics that we use in the actual manufacturing of the hardware.”
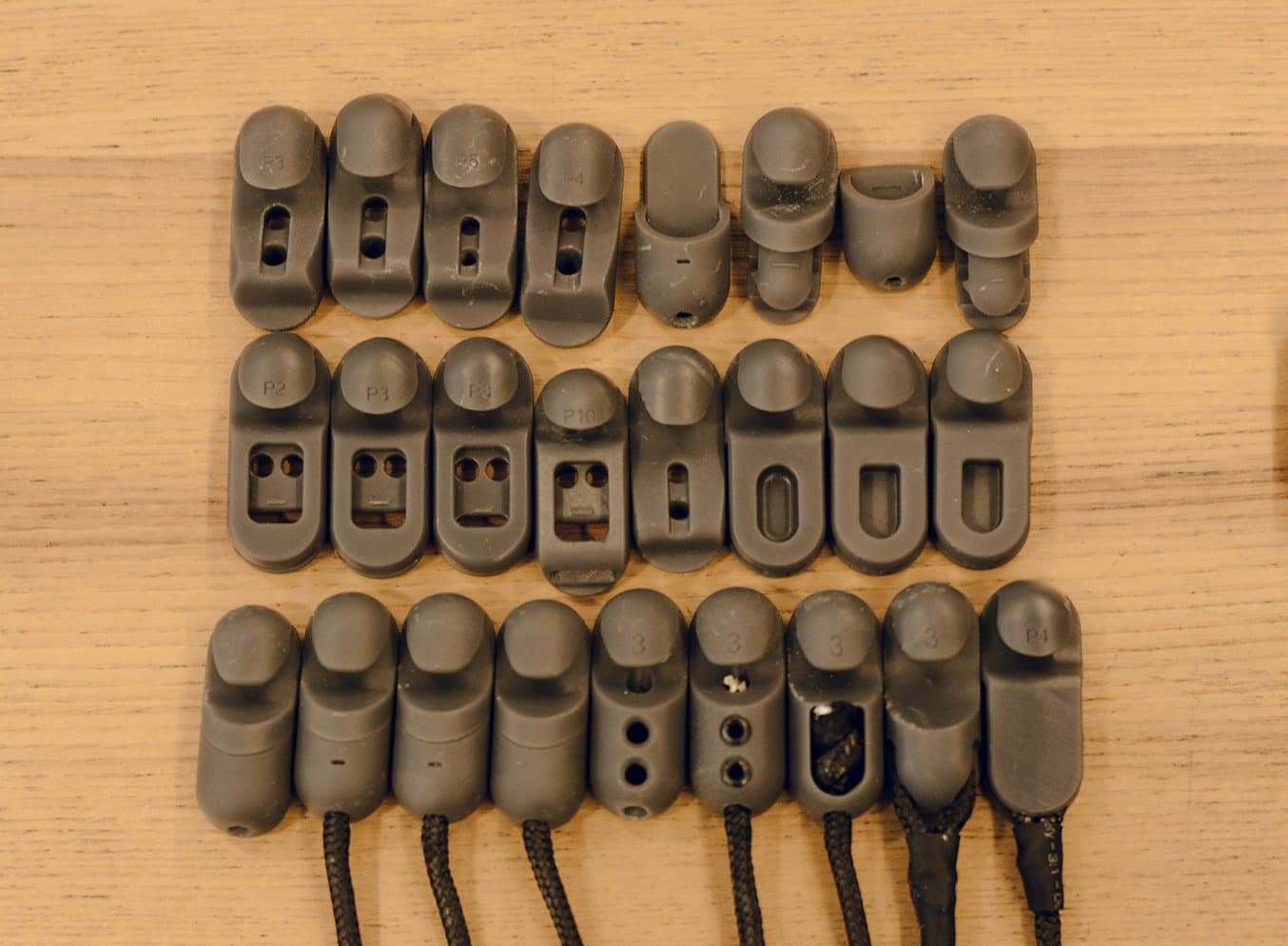
Fine features, including numbers and letters, are visible on these parts.
Some usability tests are done using 3D printed parts, especially when it comes to force. For example, how much force it takes to snap a piece of hardware over a cord loop. Jones will also use a 3D printed prototype to test against an existing competitor part. “We’ll build that competitor or that third-party part in CAD, we'll print it out of resin, and then we'll do the same test with it.“
Once the basic design has been validated with 3D printing, the team sends it out for CNC prototypes, which takes anywhere from 7-14 days. End-use production is injection molding, creating parts that can hold up to being shut in a car trunk, exposed to the sun, and an adventurous lifestyle.
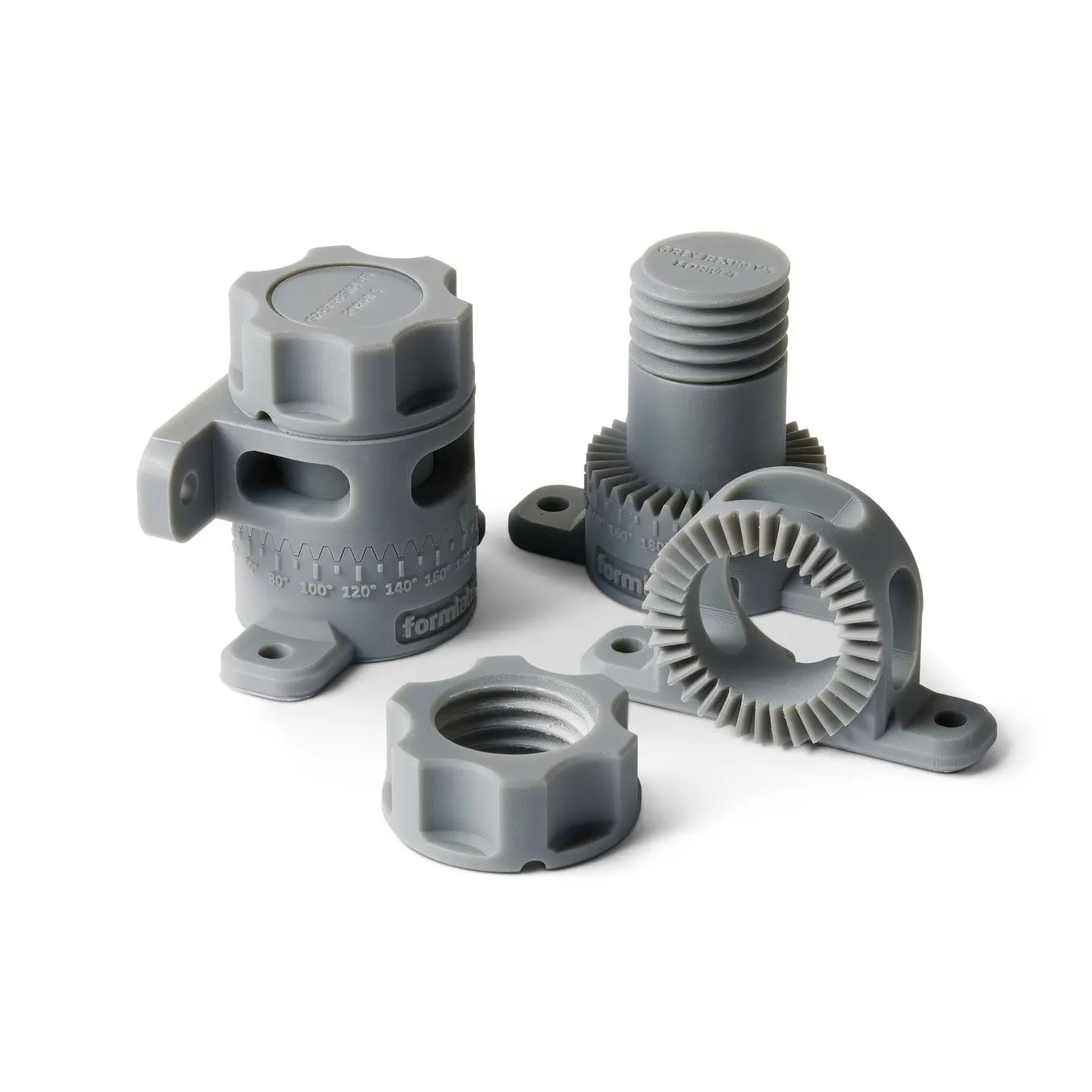
Request a Free Sample Part
See and feel Formlabs quality firsthand. We’ll ship a free 3D printed sample part to your office.
Achieving Design-Forward Hardware
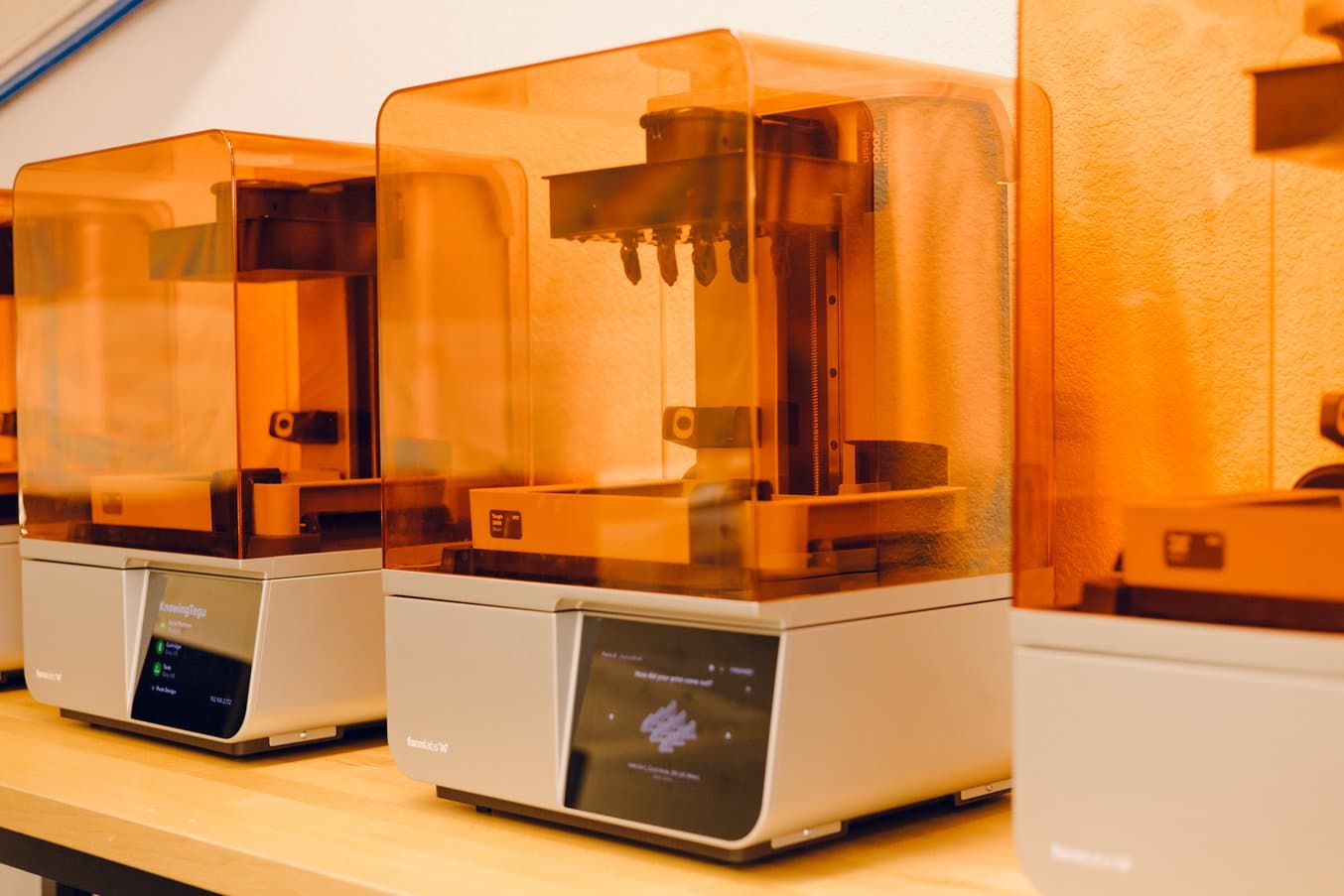
SLA 3D printers form the backbone of prototyping at Peak Design, enabling multiple iterations per day.
“Our users have come to expect that when they buy a Peak Design bag, it's not just a novel shape or construction. It's going to come with a bunch of really design-forward hardware that's highly functional.”
Dane Jones, Senior Design Engineer, Peak Design
In design, the less you notice something, the better it’s working. Using a Peak Design bag feels effortless — no fiddling or fixing — because it just works. To achieve these high standards, every piece of hardware is designed, tested, and redesigned, until it simply works. It’s a process of continual refinement — sometimes three to four iterations a day — enabled by the rapid prototyping power of the Form 4 ecosystem.
To learn how the Form 4 ecosystem can power your prototyping, explore Form 4 or contact sales.