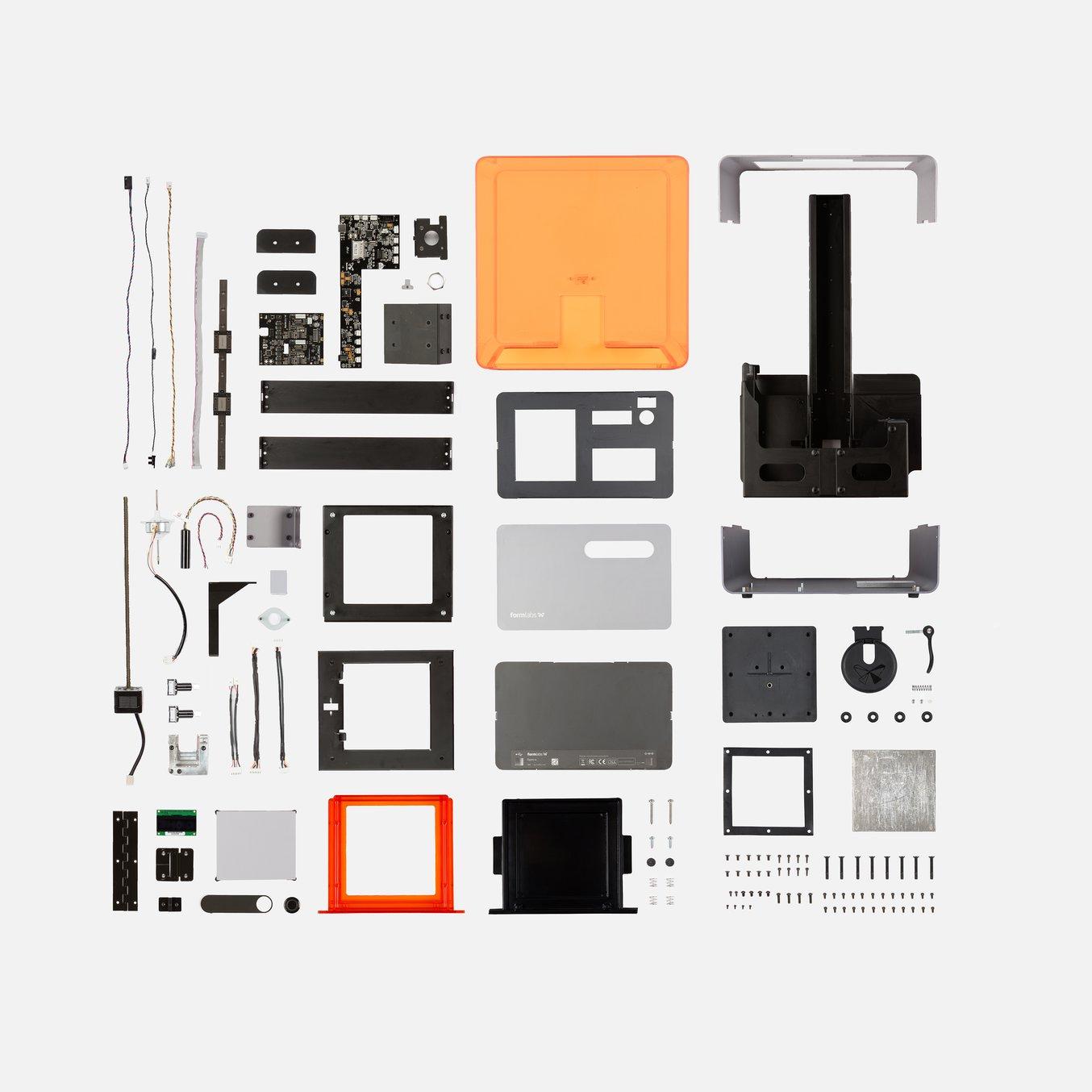
In September of 2012, Formlabs was introduced to the world with the launch of our Kickstarter campaign. Our Form 1 high-resolution desktop 3D printer successfully raised $3 million dollars in three wild, exhilarating weeks. At the time we were a small team of 12 people. We were equal parts elated and terrified: this meant we had to refine, build, and ship hundreds of printers within months.

“The first day of the Kickstarter was so wild and euphoric and crazy. Towards the end of the Kickstarter, that’s when it started to become like, okay Kickstarter is going to end soon and the new deadline is all this stuff that we just promised.”
— Jason Livingston, Industrial Designer
As the Kickstarter campaign ended, the real challenge began. For months, we worked closely with our manufacturers — the Form 1 3D printer demanded precise and careful assembly of the different mechanical parts. In March of 2013, the first printers started rolling out of the factory, and we haven’t stopped shipping since.
Since then, we’ve learned a lot about what it takes to design and ship a hardware product. These lessons have been essential in making Formlabs into what it is today.
1. Keep engineering and design as tight-knit as possible.
“The Form 1 is a manifestation of a very, very tightly engineered and designed product. It was clear to everybody in the company from day one that our engineering couldn’t be done without a design focus or an awareness of what the feel and experience should be.
We all realized that the right solution mechanically is also beautiful.”
-Yoav Reches, Industrial Designer
2. Prototype, Prototype, Prototype.

“The first five prototypes were all created within a year. The more these chapters of prototypes were realized in front of us, the more we slowly understood what we were aiming towards.”
— Jason Livingston, Industrial Designer
3. For Good Design, First Aim Simple.
“There’s a reason why this device costs less and why it functions well despite being at a much lower cost. A lot of that came from simplifying until we got to the bare elements. That design decision is reflected in the shell and other components of the machine as well.”
— Ian Ferguson, Lead Engineer
It’s been nearly three years since our Kickstarter campaign. From a team of twelve, we have grown to over a hundred people. While the team has grown far larger, our core still remains the same: keep teams tight-knit and close, prototype early and often, and most of all, keep building.
Check out more of our journey in our Medium post for What it Takes to Build a Kickstarter Product!