SLS 3D Printed Tools Help Digitalize Oil Pipeline Operations and Maintenance
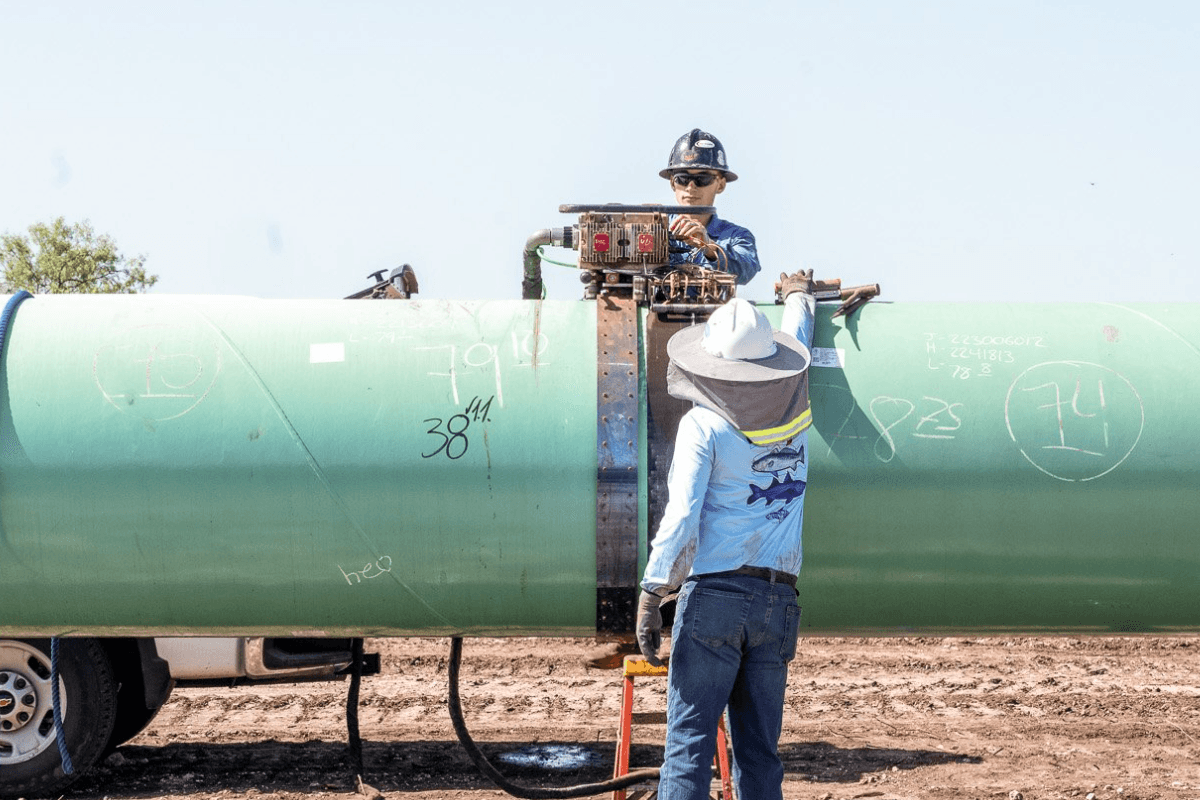
Prime Inspections started exploring 3D printing for fabricating custom inspection tools when they started to transition away from bulkier, traditional X-Ray assemblies like this one.
To extract, process, and transport the world’s most common energy resources, oil and gas, energy companies rely on extensive networks of pipelines that cover hundreds of square miles. These vast networks need to be monitored and maintained regularly to prevent leaks that could lead to natural disasters. To meet these demands, energy companies often enlist the help of businesses like Prime Inspections.
Prime Inspections helps oil and gas companies construct, monitor, and maintain pipeline systems by providing nondestructive testing (NDT) and field-joint coating (FJC) services. SLS 3D printing has significantly enhanced their ability to complete this work faster, safer, and more efficiently.
We spoke with Craig Burke, who shared how he has used the Fuse Series and Polypropylene Powder to digitize a time-consuming and complex process. Burke explained how this technology introduced a new revenue stream for his business, enhanced safety, and increased reliability for pipeline operators. “I don’t think we could have done it without having the Fuse printers. Going metal, the cost would outweigh the benefit. Not only are these printers fast, but as soon as I can dream up a part, 10 hours later it’s in my hands,” Burke says.
Analog X-Rays, Hundreds of Thousands of Times
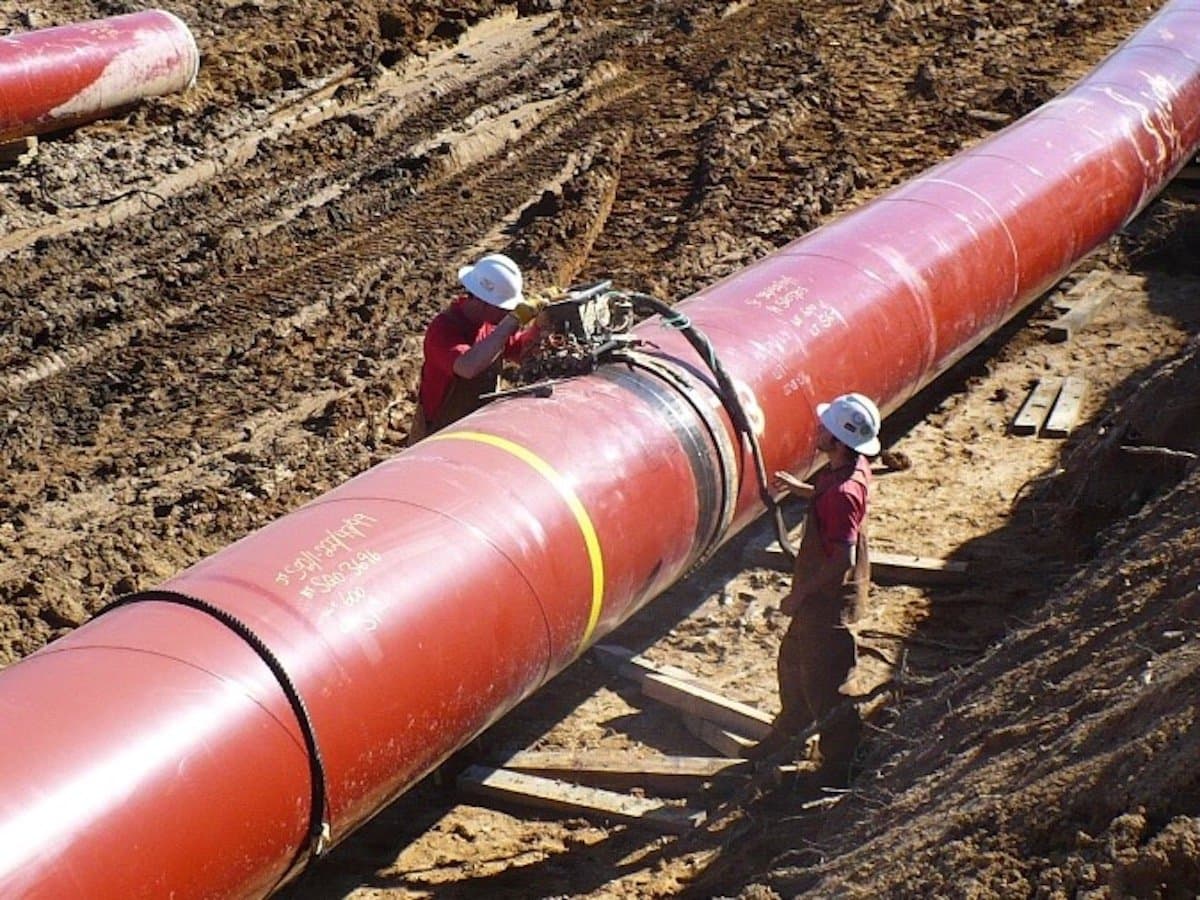
The analog X-ray process was time-consuming and difficult. Burke has led an effort to find solutions for the digitalization of the process using SLS 3D printing.
The systems Prime Inspections works on typically consist of large, nearly four-feet-in-diameter pipes, welded together every 40 feet over stretches of 10 to 15 miles. Each weld must be checked to ensure the pipeline remains watertight and safe, using X-rays. For a long time, the only workflow available involved an analog X-ray panel that required a darkroom to develop the images.
For every weld, the team would attach an X-ray machine to the pipe, move away from the radiation, and then develop the X-ray in a darkroom on the back of their truck before moving on to the next weld, 40 feet away. Since it took about two hours to develop each X-ray, defects were often discovered only after the team was already miles down the line, forcing them to drive back.
“That’s why we’re pushing digital,” says Burke. “The analog process was crude and time-consuming, and it put a lot of wear and tear on the teams out there in the field. But finding digital X-ray manufacturers that offered a solution for our workflow — not just clean medical environments — was difficult.”
While digitalization promised better efficiency and improved ease of use for operators, it also presented new challenges. The new digital X-ray panels were designed for sterile, predictable medical environments, not for outdoor elements or the oversized geometries of pipelines. “The digital X-ray panels cost upwards of $100K. We don’t want them strapped or taped or bungee corded to the pipeline, so we had to find a solution to easily attach and detach them in all sorts of conditions,” Burke says.
Evaluating Solutions: Metal, Filament, Resin, and Powder
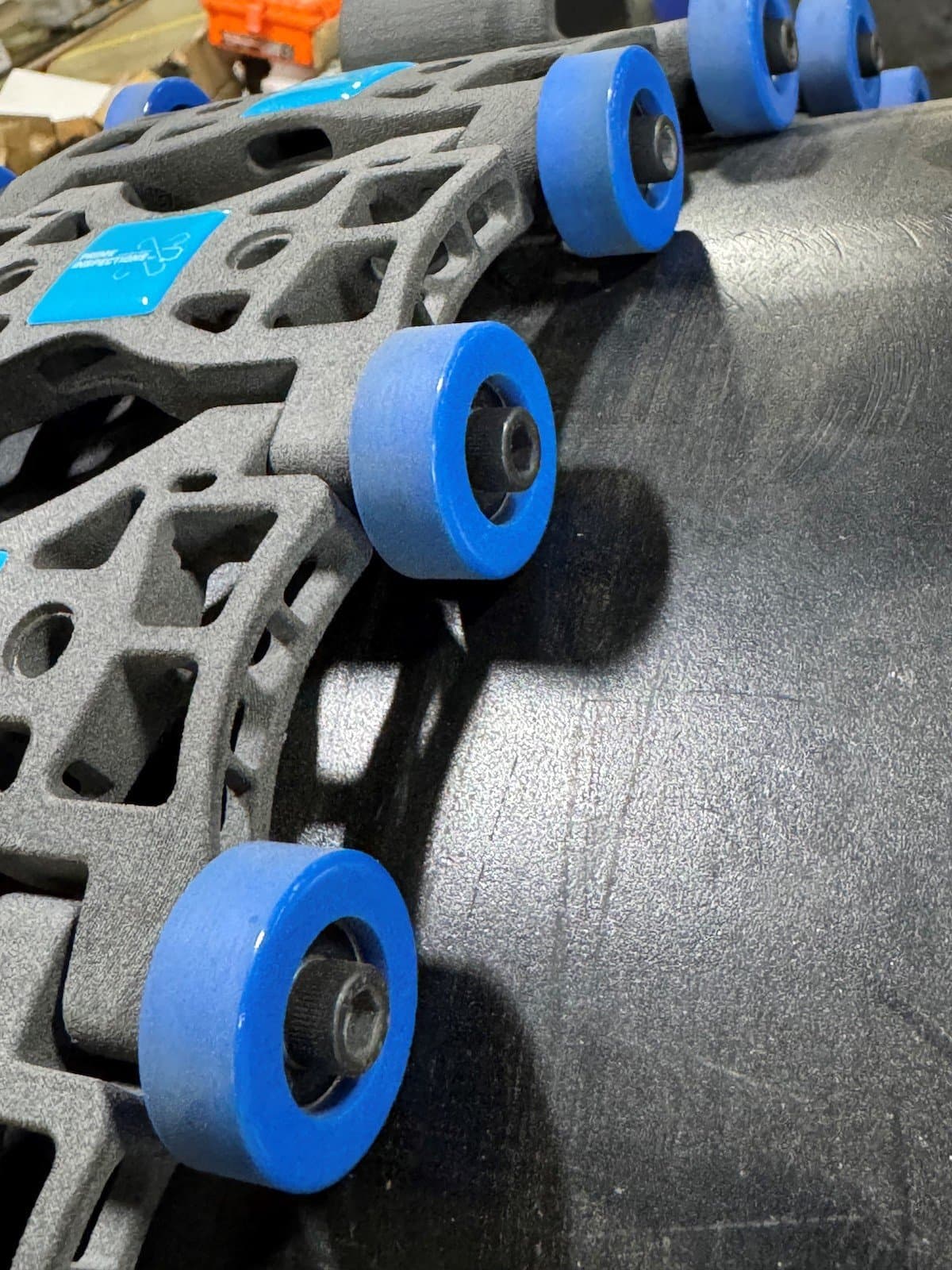
For the final version of the X-ray holding device, Burke uses Polypropylene Powder on the Fuse 1+ 30W printers along with off-the-shelf roller wheels and metal bolts.
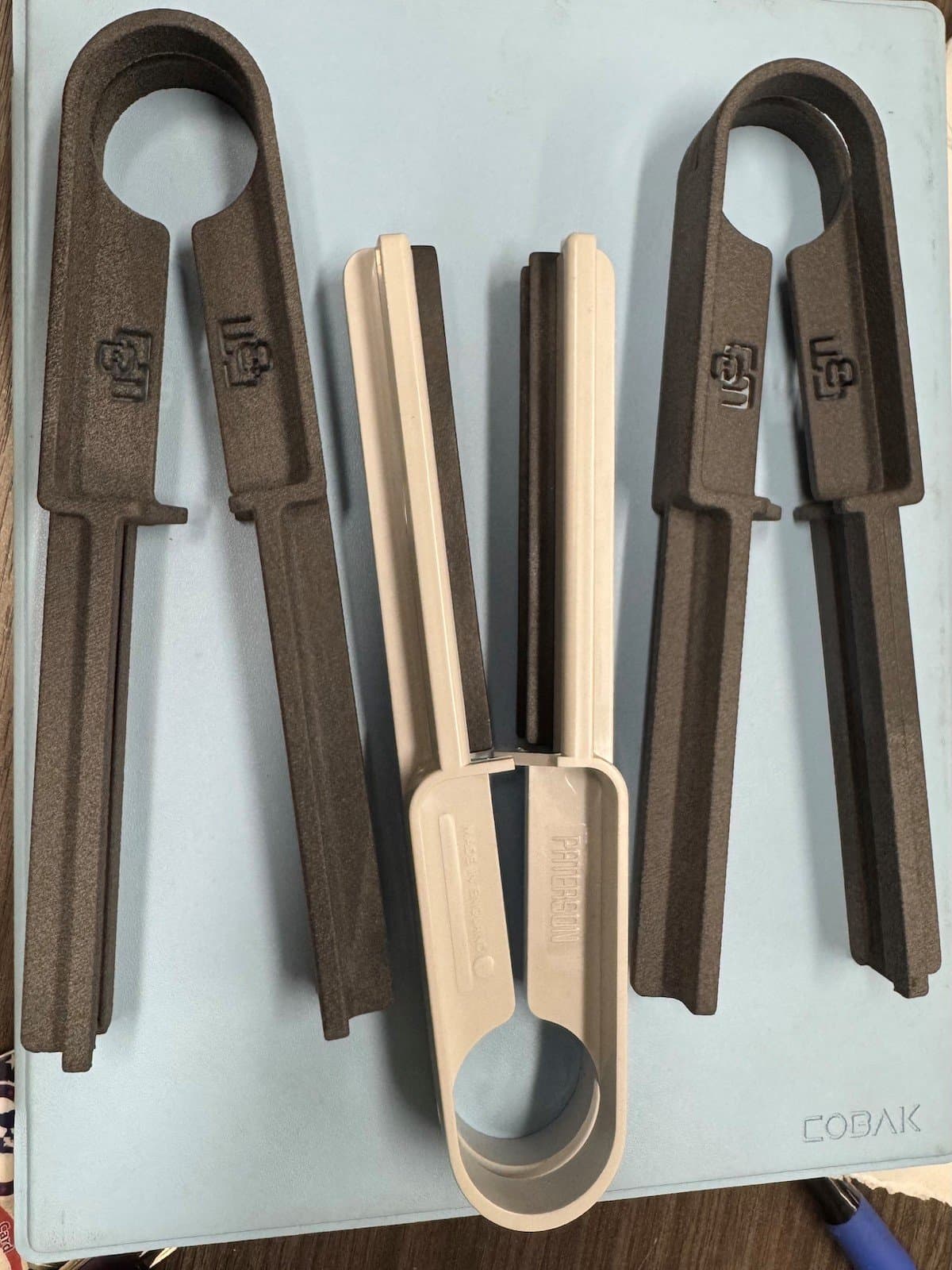
Burke compared SLS 3D printed Polypropylene Powder (left and right) to injection molded plastics (center) for this new flexible component.
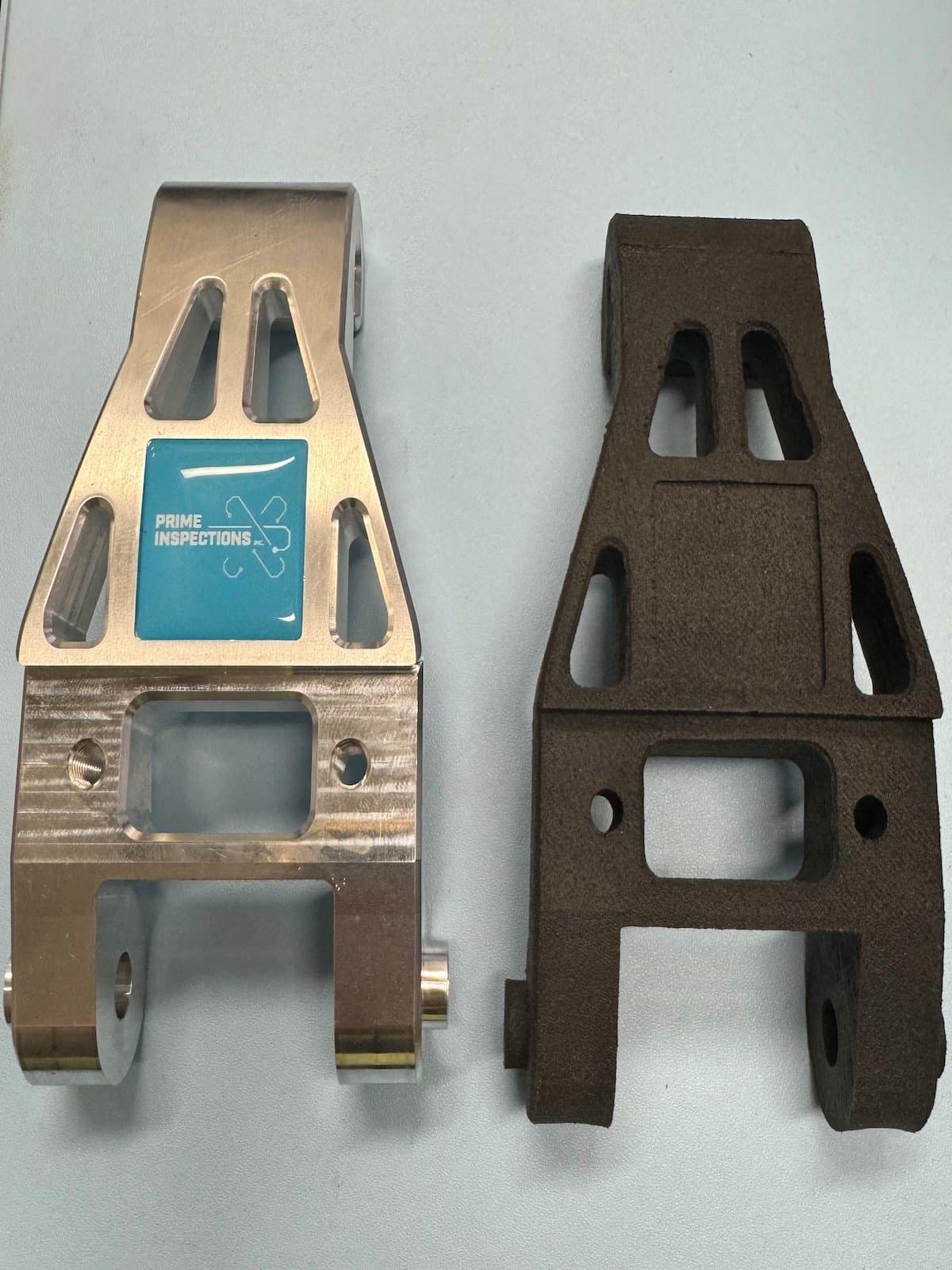
For these prototypes of a new type of connector-link, Burke tried machined aluminum (left) and Nylon 11 CF Powder on the Fuse 1+ 30W printer.
Craig began prototyping solutions to hold the digital X-ray panels securely during imaging and allow for easy detachment. He designed a modular product made of links resembling a giant watch band for a 42-inch diameter pipe. Initially, these links were machined from metal, but the process became prohibitively expensive, especially with the need for iterative changes. Burke turned to 3D printing, aiming to move quickly from proof-of-concept prototypes to end-use parts for fieldwork.
“We started about a year ago. As with most people, we started with FDM, then SLA, then eventually dipped into powders. I was looking at the HP, Fuse, Lisa X, and some metal printers as well, but then you’re talking $200K-$300K,” Burke explains.
The performance criteria for these parts were demanding. The individual links needed to be strong, impact-resistant, and lightweight to allow the team to detach and carry them between locations. Additionally, the parts had to withstand freezing temperatures, as pipelines often span areas where temperatures fall well below zero.
“During evaluation, we did outsource some parts, and made some with MJF, SLS, etc. The evaluation of the other parts came in and we were happy with SLS — much cheaper than MJF. On a cost comparison, the Fuse was more than the Sinterit Lisa X, but their material is a lot more expensive,” Burke says.
Burke and his team started with one Fuse 1+ 30W and a Fuse Sift powder recycling accessory, using Nylon 11 CF Powder at first. He was able to dial in the design of the individual links in the ‘watch band,’ and iterate without driving up overall costs by machining or ordering tooling made.
Moving to End-Use and Production Volumes
After finalizing the design of the individual links and brackets, Burke packed a full build chamber with 41 links, which took approximately 25 hours to complete. Another full build chamber of brackets took another day, meaning the team could deliver a fully completed X-ray device in just two days.
After testing several parts printed in Nylon 11 CF Powder in their facilities, the devices were ready for field use. When temperatures started to drop, however, Burke realized they needed a material that could handle impact in colder climates. “When I saw the option for polypropylene pop up in PreForm, I thought, this is great, let’s trial this out,” says Burke.
Polypropylene Powder proved to be an immediate success. The lightweight parts were easy for operators to carry between welds and they remained impact-resistant even in cold conditions. PP Powder enabled a faster and easier workflow for operators working along a 10-mile long pipeline. “The operators will take one complete device with some spare individual links on the job with them. They wrap it around the pipe, take 10 minutes to shoot the X-ray film, and then take it off like a watch. Adding or removing links is simple,” Burke adds.
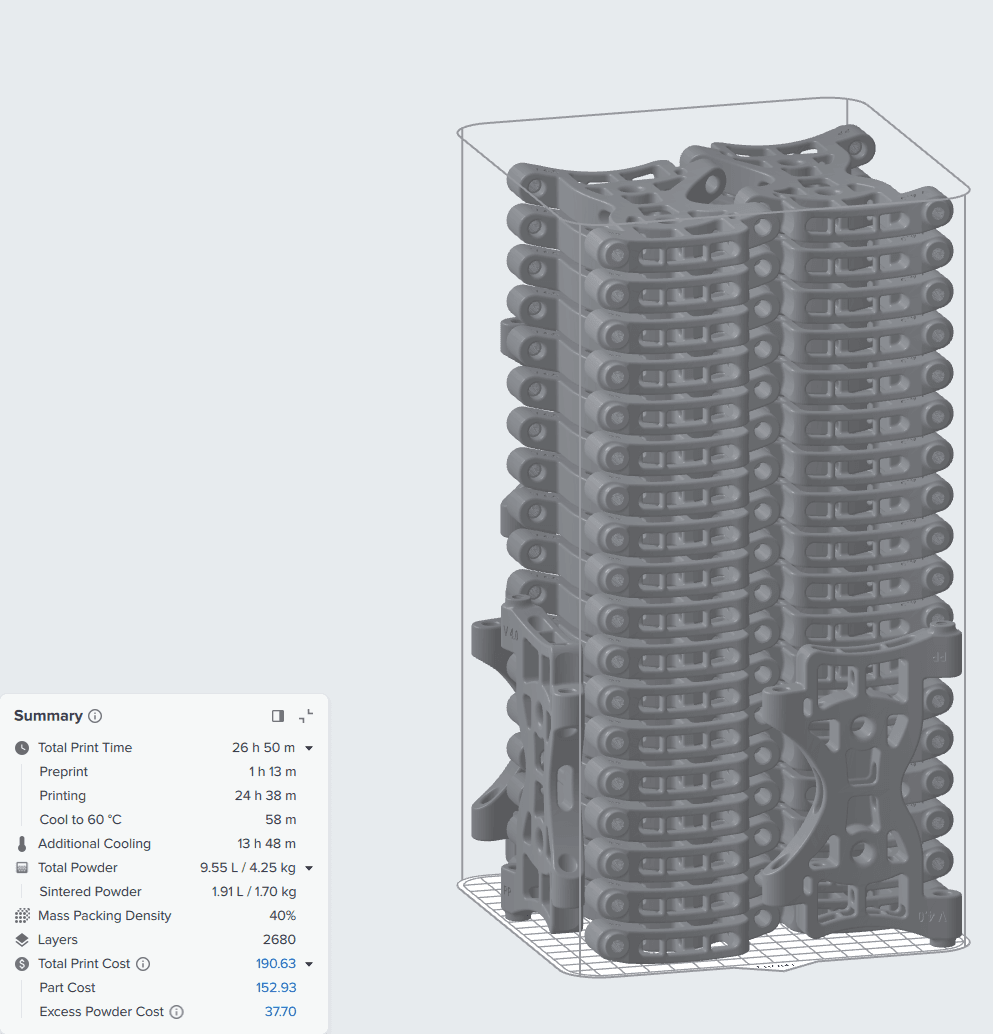
Burke can fit 41 links inside each Fuse 1+ 30W build chamber, making it easy to match his refresh rate to his packing density and lowering his cost per part.
Once the design was finalized and PP Powder was performing well, scaling to production volumes with the Fuse Ecosystem was the next step. Burke purchased a second printer, allowing for near-daily production of fully packed build chambers in both machines.
Parts Per Build Chamber | Pack Density | Total Used Powder Per Build | Cost Per Part |
---|---|---|---|
41 | 40% | $152.93 | $3.82 |
“There weren’t stumbling blocks. Once we got used to the process, it’s as easy as it gets.”
Craig Burke, Prime Inspections
New Products and New Revenue Streams, Built on SLS
The self-supporting nature of the SLS build chamber enabled Burke to create lightweight parts with complex geometries that snap together as part of a larger device. After successfully producing the pipeline X-ray device, new ideas started flowing.
“Anything with welds needs to be inspected, so when we have requests for large oil holding tanks, the SLS printers start to become even more helpful in imagining solutions,” says Burke.
Unlike pipelines, large holding tanks cannot be encircled easily by Prime Inspections’ new watch-type design. Burke used his two Fuse 1+ 30W printers to design a magnetic holder for the X-ray devices that can attach to and move along the side of large holding tanks. “The R&D to get here was all SLS 3D printed Nylon 11 CF Powder. This saved us a lot of time and money versus having to pay and wait for multiple versions to be machined and tested,” Burke shares.
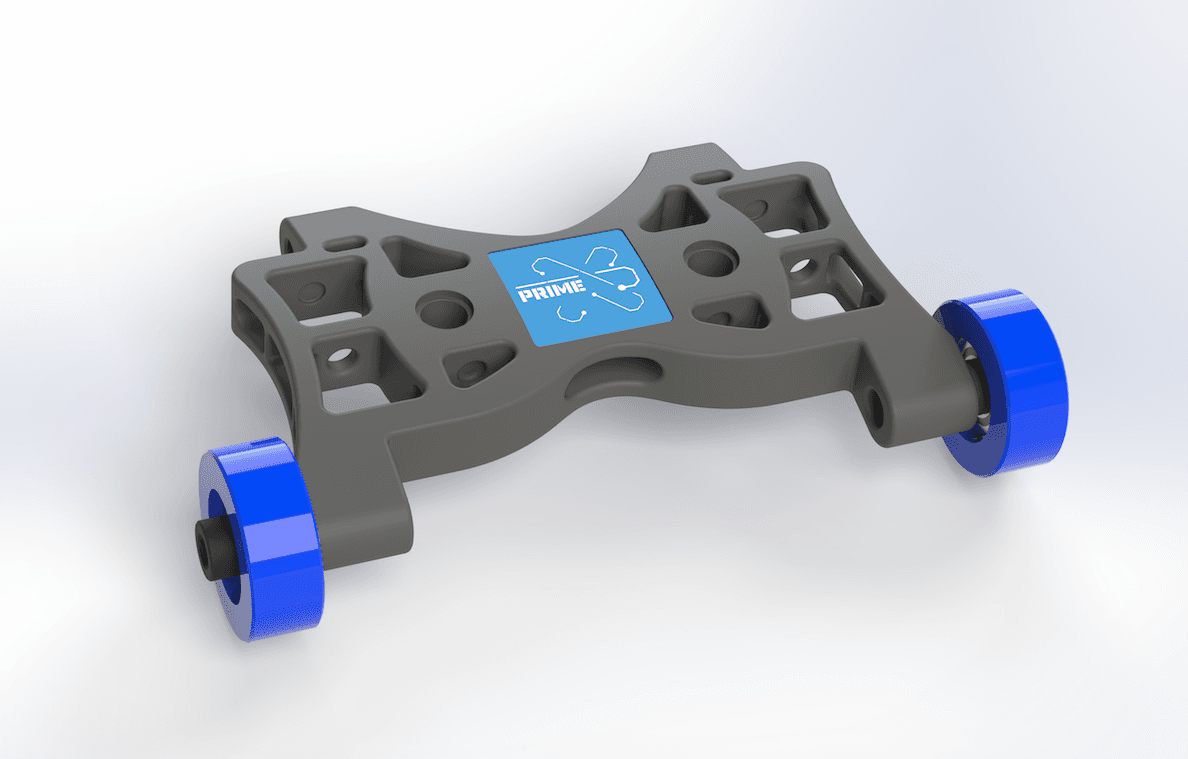
Digitizing the design and production workflow for these 3D printed links allowed Burke to make changes throughout the validation process and presented opportunities to lightweight the part without sacrificing strength.
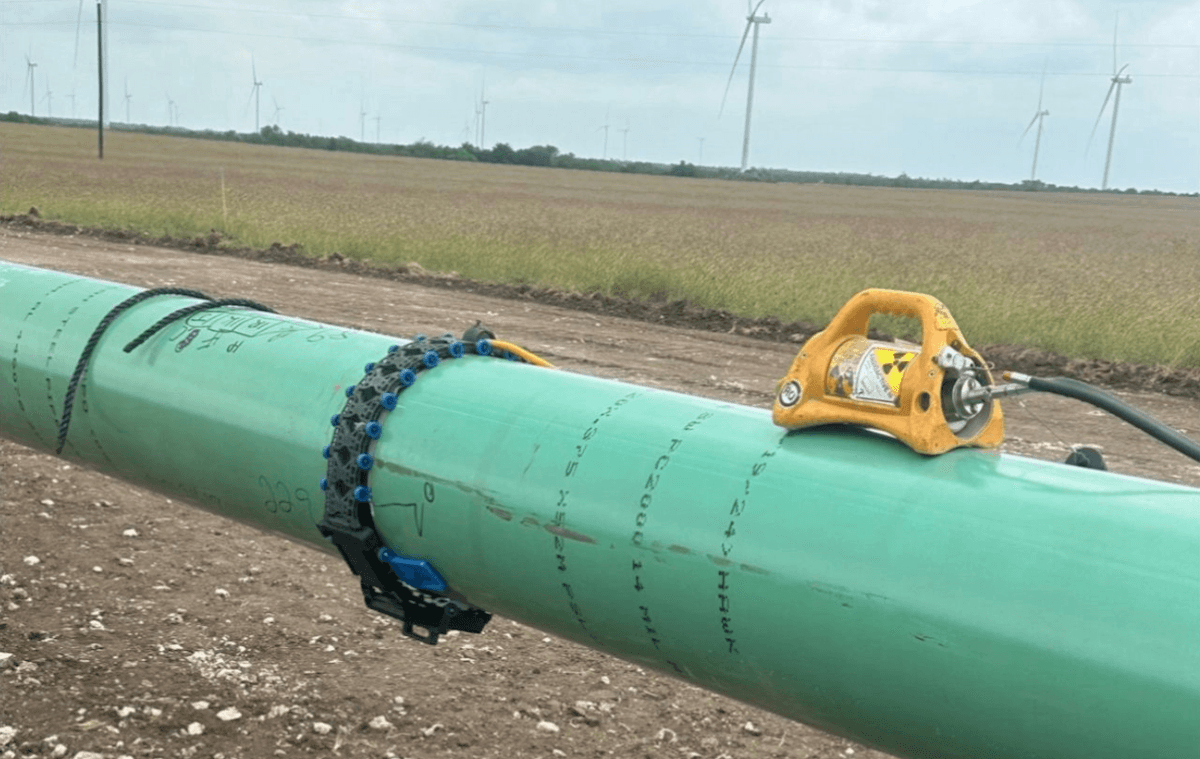
The strength of Polypropylene Powder and the geometries made possible by the Fuse Series print technology allow these rings of interlocking links to wrap securely around the pipelines and attach the X-ray to each weld.
With the band X-ray device in the field, Prime Inspections began attracting interest from others in the industry. Every pipeline inspection company faces the challenge of capturing high-quality images of welds in extreme environments. Burke’s design offers a modular, flexible solution that delivers precise images while reducing labor demands on the X-ray team.
“We never foresaw this demand, but it’s been great. Our main customer has been the supplier of pipeline inspection equipment, and they have a broader audience than we do. They ordered about 20 sets a month ago, and they sell them throughout the US and Canada,” Burke says.
Bringing SLS in-house has not only improved Prime Inspections’ workflow but also created a new revenue stream and opened the door for different types of inspections and projects.
“The SLS process and the Fuse printers have changed the way we do business, especially as we look to expand.”
Craig Burke, Prime Inspections
Learn more about using the Fuse Series for end-use production or contact our team to discuss your specific application. To see the material properties of our powders for yourself, request a sample.