Yuko Oda has a background in fine art; she received a M.F.A. in Sculpture from Rhode Island School of Design before taking a job at the New York Institute of Technology (NYIT). There, she first used 3D printing technologies such as Fused Deposition Modeling (FDM) and Stereolithography (SLA) printing in a college level curriculum, before joining UMass Lowell in 2017. Colleges have increasingly implemented 3D printing into a host of courses, from design to animation and sculpture, in order to better serve students and to keep courses relevant as new technology changes traditional methods.
Read on to see how Yuko Oda uses 3D printing to create artwork, and how she’s using it to modernize 3D Design, Sculpture, and 3D Modeling and Animation courses at UMass Lowell.
Technology and Art at UMass Lowell
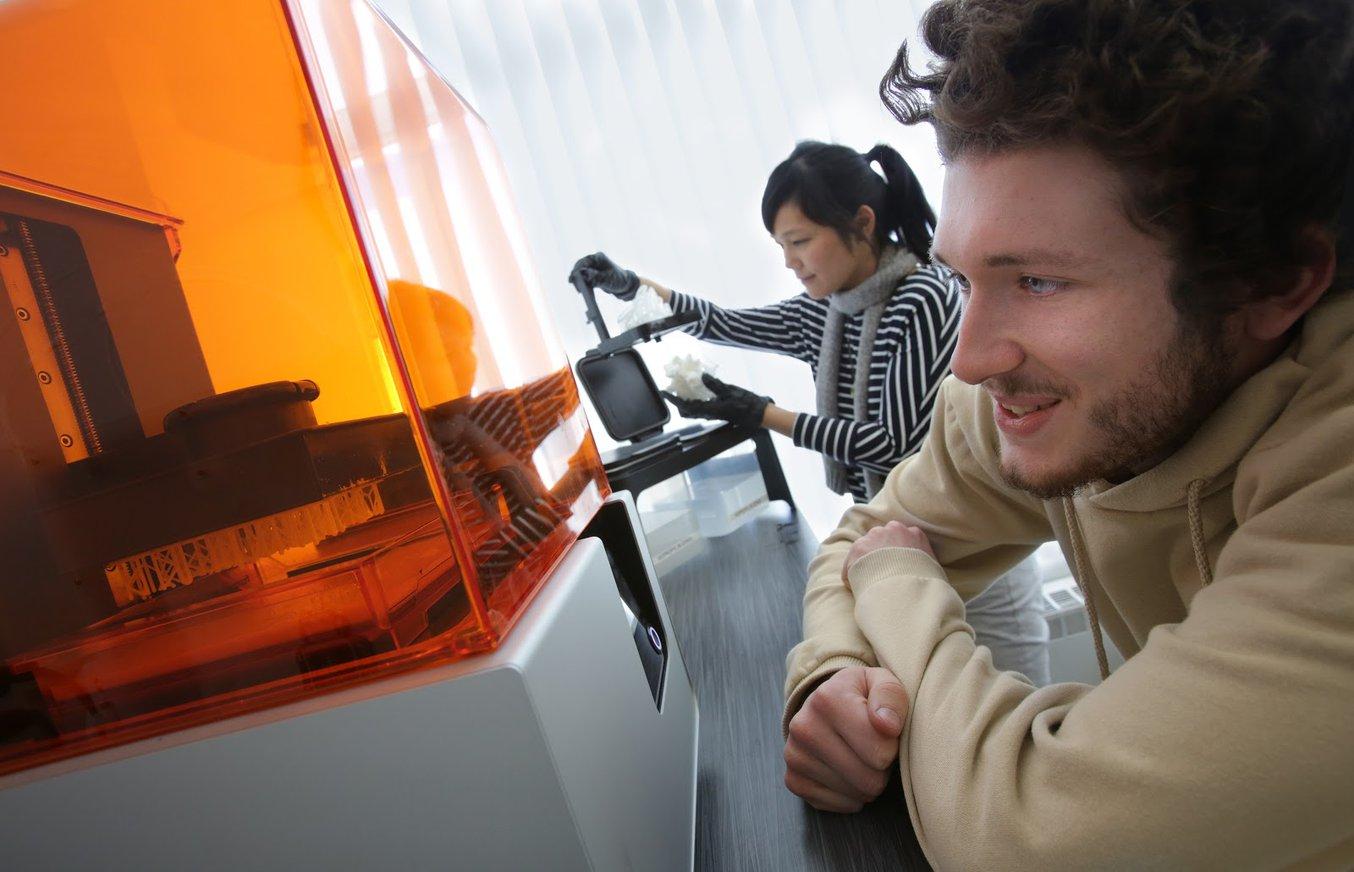
Yuko and students print projects on the Form 2. Photo Credit: Jim Higgins
3D printers are becoming a common sight in colleges and technical schools around the world, and many educators have integrated this technology into their lesson plans. As in-house desktop printing becomes ubiquitous in the workforce, educational institutions need to technologize curriculum to properly equip students for future employment. At UMass Lowell, that meant modernizing its sculpting and 3D design courses for the 21st century. Enter Yuko Oda, who joined the university in 2017 and got started by ordering a multitude of 3D printers, including a Formlabs SLA machine.
Yuko is able to take her passion for art and technology into the classroom, currently teaching sculpture, 3D modeling and animation, and interactive media. Most students know that they’re required to understand 3D animation and 3D modeling for future careers in various fields, including sculpture design for cinema. For studio artists, 3D modeling has become an essential skill.
UMass Lowell wants to equip students with the necessary skills to navigate a job market constantly adapting to new technology. According to Yuko, graphic design students are also starting to notice increased demand for 3D skill sets. For example, gone are the days of generic, low quality in-store packaging. Consumer’s buying decisions are impacted by package design, and 3D printing allows for the creation of realistic prototypes, reducing time to market and increasing sales.
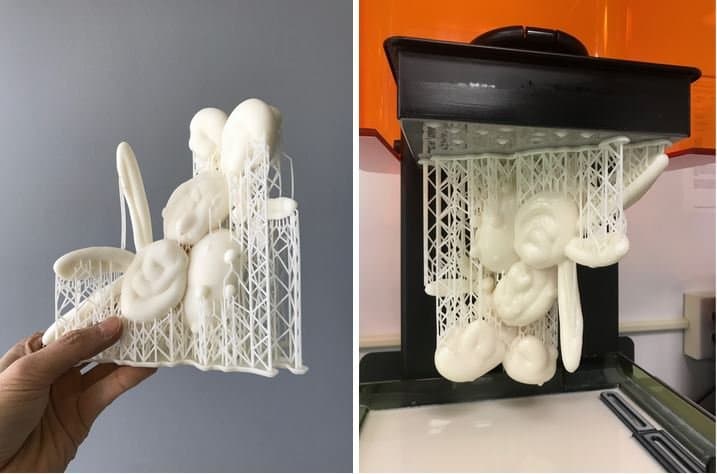
Sculpture I VR Sculpting Project by UML Art and Design student Cecilia Chi
Formlabs 3D printers produce high quality and precise parts required for her courses. Because of the smooth surface finish, students are able to easily sand and coat parts to consumer quality level. It’s also beneficial for the students that they can gain experience with the same Formlabs machines that are being used by major consumer brands such as New Balance and Ashley Furniture.
“Students sculpt a 3D model, import it into Zbrush, then print in various resins, including Clear Resin. The ability for Formlabs machines to show intricacies that were modified in Zbrush is unparalleled when compared to other printers in the lab.”
Yuko
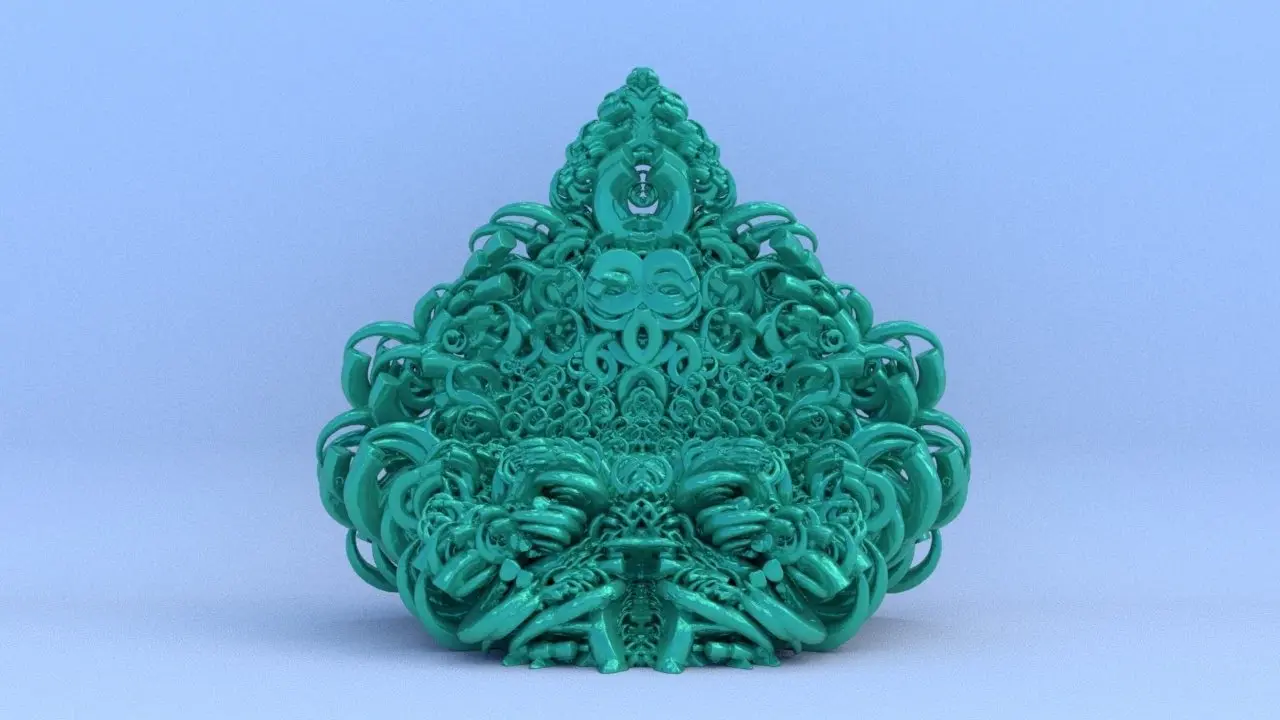
Students are able to create incredibly complex prints on Formlabs printers VR Sculpted Model by Alex Twyman, UML Art and Design student
All printers used in courses at UMass Lowell are under $10,000. The Formlabs 3D printer consistently produces the highest quality prints with the least amount of failures, compared to other printers in a similar price range. And while fast, cheap FDM machines will always have a place in the colleges, high quality SLA does as well.
“Our FDM printers, if I was to print 3 student projects, I would expect 1 of the 3 to fail. With the Formlabs machine, all 3 of the prints would be successful.”
One of the most promising new developments in sculpture is the integration of 3D printing and Virtual Reality (VR). This is especially salient for students intimidated by 3D design. VR is rapidly reducing barriers for 3D design, allowing artists and students to create with their hands in programs such as Oculus Medium. Yuko has taught 8th graders how to create a 3D object in 30 minutes in VR, and then print the artwork on a 3D printer. Even for seasoned sculptors, VR reduces the time it takes to go from an idea to a physical object, potentially opening up new areas of experimental art.
Organic and Synthetic Collide
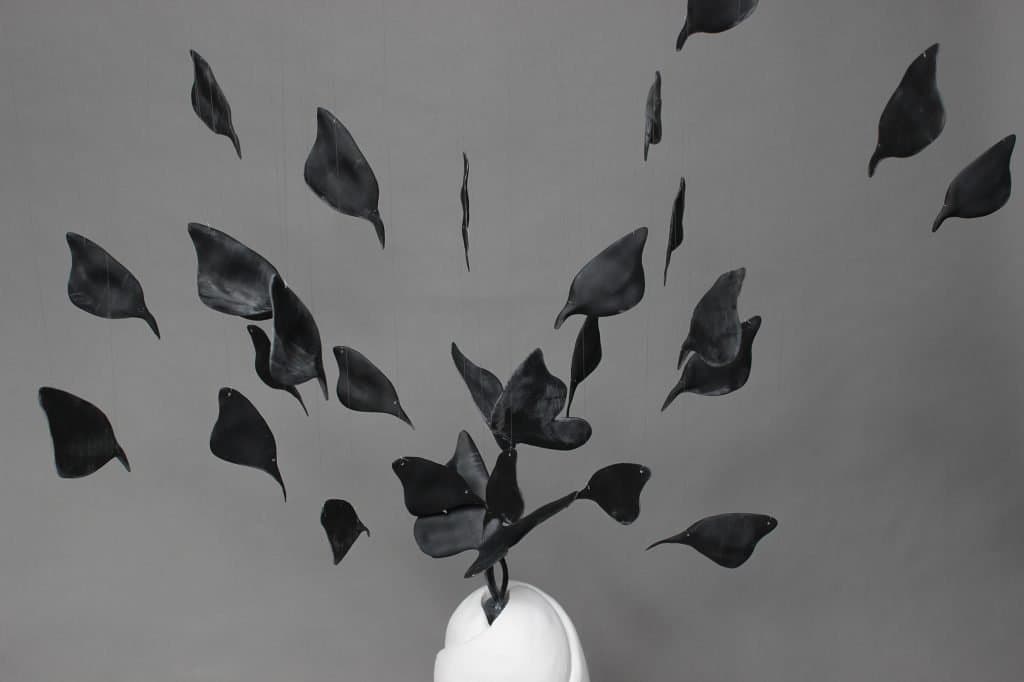
While working in higher education, Yuko continues to sculpt in her free time. She’s crafted various projects that explore the intersection of organic and inorganic matter, which reflects how human-made objects, such as trash, consume the planet. Yuko wants to investigate how synthetic and organic material can coexist.
Pictured above is her project called Darkness Meets Light. The base was created with plaster, while the black objects were printed on a Formlabs 3D printer using Black Resin.
“Darkness Meets Light” is a digital sculpture installation that explores the intersection of technology with fine art, bringing together traditional and digital methodologies in one piece. The base of the sculpture, an organic form that resembles a cocoon, is carved plaster. This structure serves as the landing, birthplace, and home for the black 3D-printed butterfly wing-like forms swarming on and out of its crevice. These black forms embody a frozen moment of contrasting energies; they are both emitting out and pointing into their origin.”

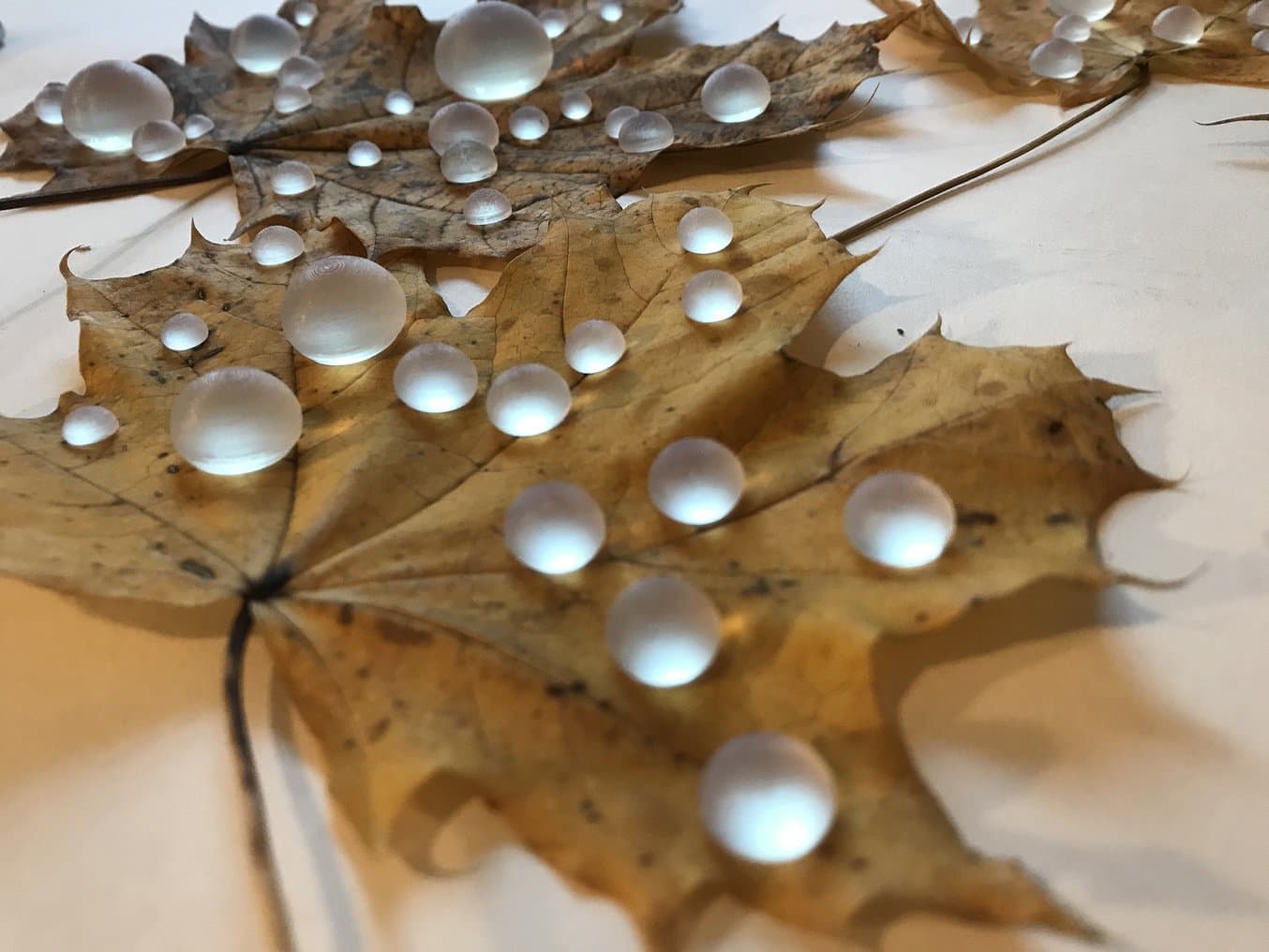
Another project, called Morning Dew, mixes real leaves with 3D printing dew drops. The laser on an SLA 3D printer is capable of creating highly accurate tiny objects, in this case water droplets, with repeated precision.
In “Morning Dew”, 3D printed dew drops are installed on leaves. Yuko was outside one early morning and was inspired by the simplicity and beauty of this natural phenomena. She is recreating it in her art studio using the Form 2 printer using Clear Resin.
Learn More About Yuko Oda
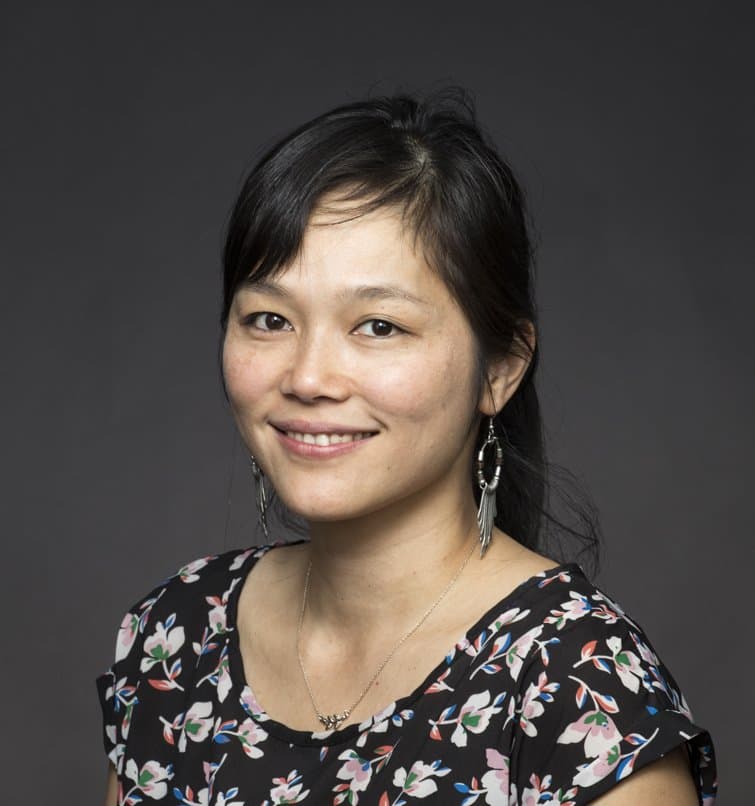
Yuko Oda is not alone in using 3D printing as a hobby, side business, or project, while also using it in their professional work. Low cost, desktop 3D printing is changing the way designers, educators, artists, and professionals across a wide spectrum of careers create.
Interested in learning more about Yuko Oda’s artwork? Check out her website or follow her on Instagram.
Want to get hands on with Black Resin, the same material used in Darkness Meets Light (featured above)?