Einführung in den medizinischen 3D-Druck und 3D-Drucker für das Gesundheitswesen
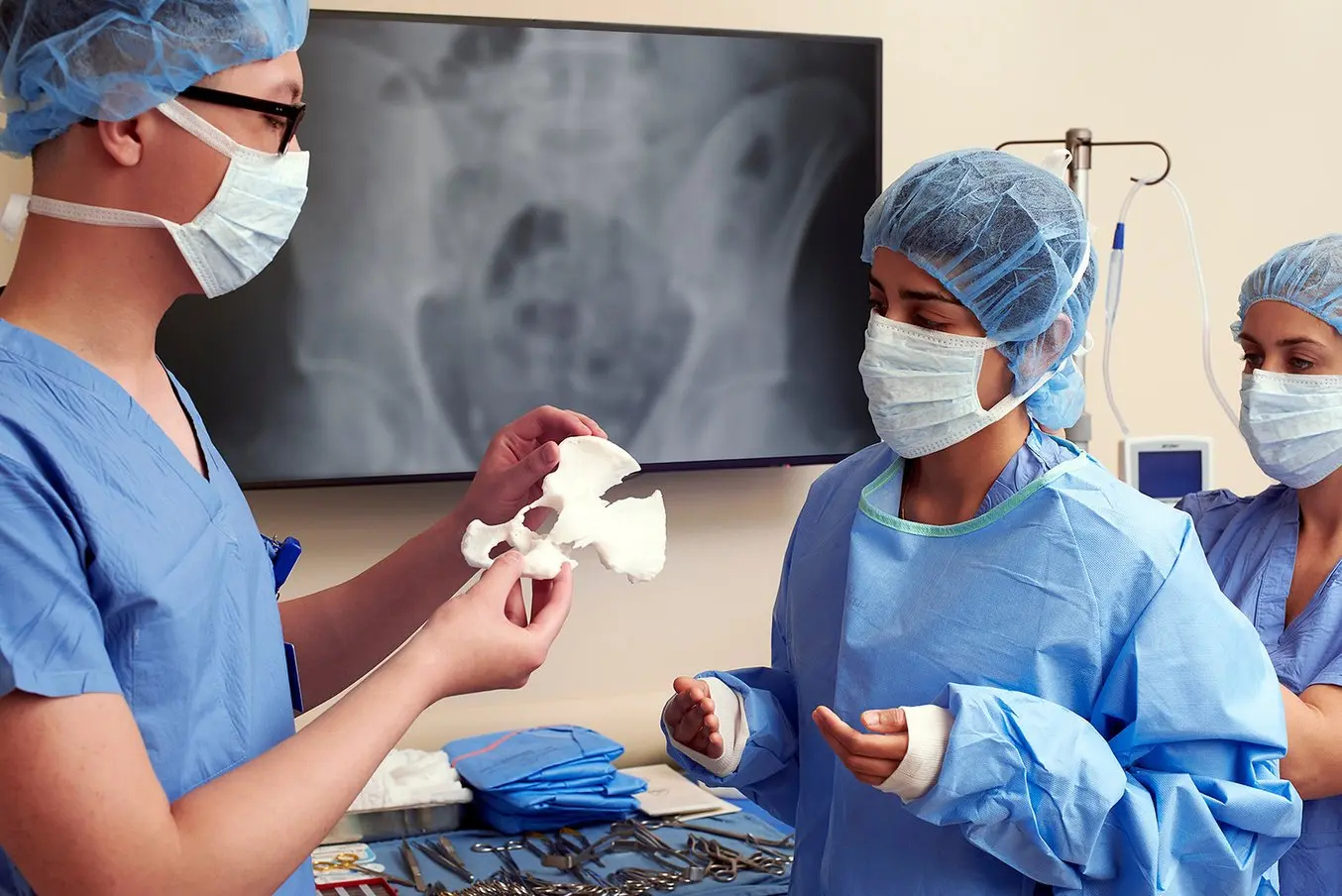
Personalisierte Präzisionsmedizin ist auf dem Vormarsch. Fortschrittliche Technologien und neue Werkzeuge bringen die Medizin näher an den Menschen und ermöglichen Behandlungen und Geräte, die auf die individuellen Bedürfnisse abgestimmt sind.
Fortschritte im 3D-Druck für die Medizin haben in allen Bereichen des Gesundheitswesen entscheidende Beiträge geleistet. Auf Patientenseite bieten neue, mit 3D-Druck entwickelte Werkzeuge und Therapiemethoden mehr Komfort und Individualisierung bei der Behandlung. Für medizinische Fachleute bietet die neu erschlossene Technologie ein besseres Verständnis komplexer Fälle sowie neue Werkzeuge, die letztendlich den Qualitätsstandard der Behandlung erhöhen.
Angefangen von patientenspezifischen chirurgischen Modellen bis hin zu 3D-gedruckten Medizinprodukten stellen wir im Folgenden sechs Bereiche vor, in denen der medizinische 3D-Druck auf dem Vormarsch ist. Sie erfahren außerdem, warum zahlreiche medizinische Fachleute vom Potenzial des 3D-Drucks für das Gesundheitswesen begeistert sind und wie unterschiedliche 3D-Drucktechnologien in bestimmten Gesundheitsanwendungen eingesetzt werden können.
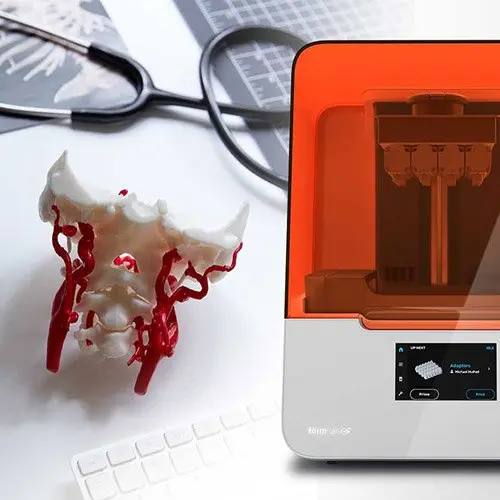
Einführung in den medizinischen 3D-Druck
Nehmen Sie an unserer Einführung teil, um bewährte Praktiken für den medizinischen 3D-Druck kennenzulernen. Außerdem stellen wir Ihnen das neueste Ecosystem von Formlabs Medical vor, einschließlich mehrerer neuer medizinisch geprüfter Produkte.
3D-Druck im Gesundheitswesen
1. Patientenspezifische Operationsmodelle
3D-gedruckte Anatomiemodelle erstellt aus Scandaten der Patient*innen werden in der heutigen personalisierten Präzisionsmedizin immer nützlicher. Die Fälle werden immer komplexer. Und bei Routineeingriffen wird die Effizienz im OP-Saal immer wichtiger. Deshalb helfen greifbare Anschauungsmodelle viel beim Verständnis und bei der Kommunikation innerhalb des Teams sowie mit den Behandelten.
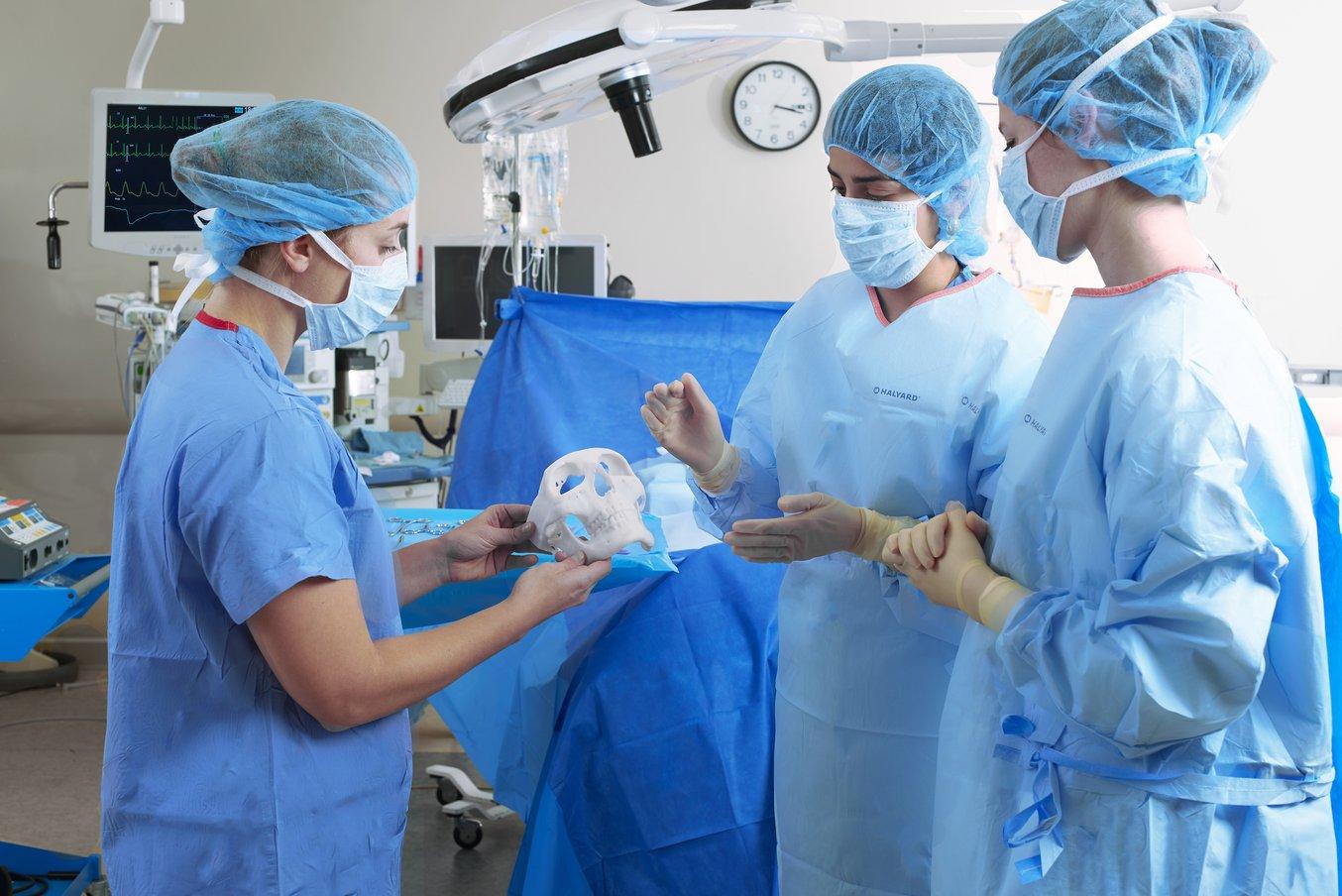
3D-gedruckte Anatomiemodelle für die vorbereitende Operationsplanung und verbesserte Patientengespräche
Dieses Whitepaper bietet eine praktische Anleitung für Ärzte und technische Assistenten, um 3D-gedruckte Anatomiemodelle aus Patientenscans zu erstellen, bewährte Praktiken für die Einrichtung eines CT/MRT-Scans nachzuvollziehen, Datensätze zu segmentieren und Dateien in druckbaren Formate zu konvertieren.
Medizinisches Personal, Krankenhäuser und Forschungsinstitute auf der ganzen Welt nutzen 3D-gedruckte Anatomiemodelle als Referenzen – bei der vorbereitenden Operationsplanung, der intraoperativen Darstellung sowie für die Größenbestimmung oder Voreinstellung medizinischer Ausrüstung – sowohl bei Routineeingriffen als auch bei höchst komplizierten Prozeduren, wie in Hunderten von Publikationen dokumentiert.
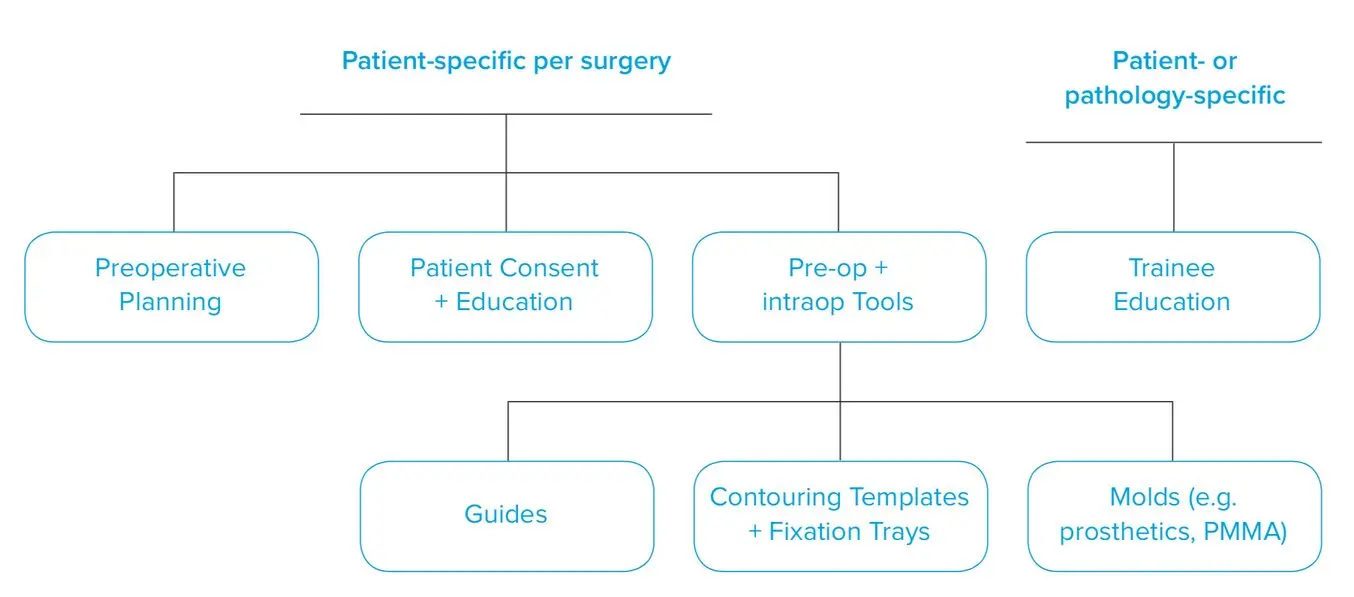
Mit 3D-Druck ist die Anfertigung patientenspezifischer Referenzmodelle zum Anfassen aus CT- oder MRT-Scans unkompliziert und erschwinglich. In Peer-Review begutachtete Fachliteratur zeigt auf, wie diese zusätzliche Perspektive medizinischen Teams bei der Operationsvorbereitung hilft. Das wiederum verringert die Kosten und die Operationszeit und erhöht die Patientenzufriedenheit, da ihre Bedenken gemildert und Genesungszeiten verkürzt werden.
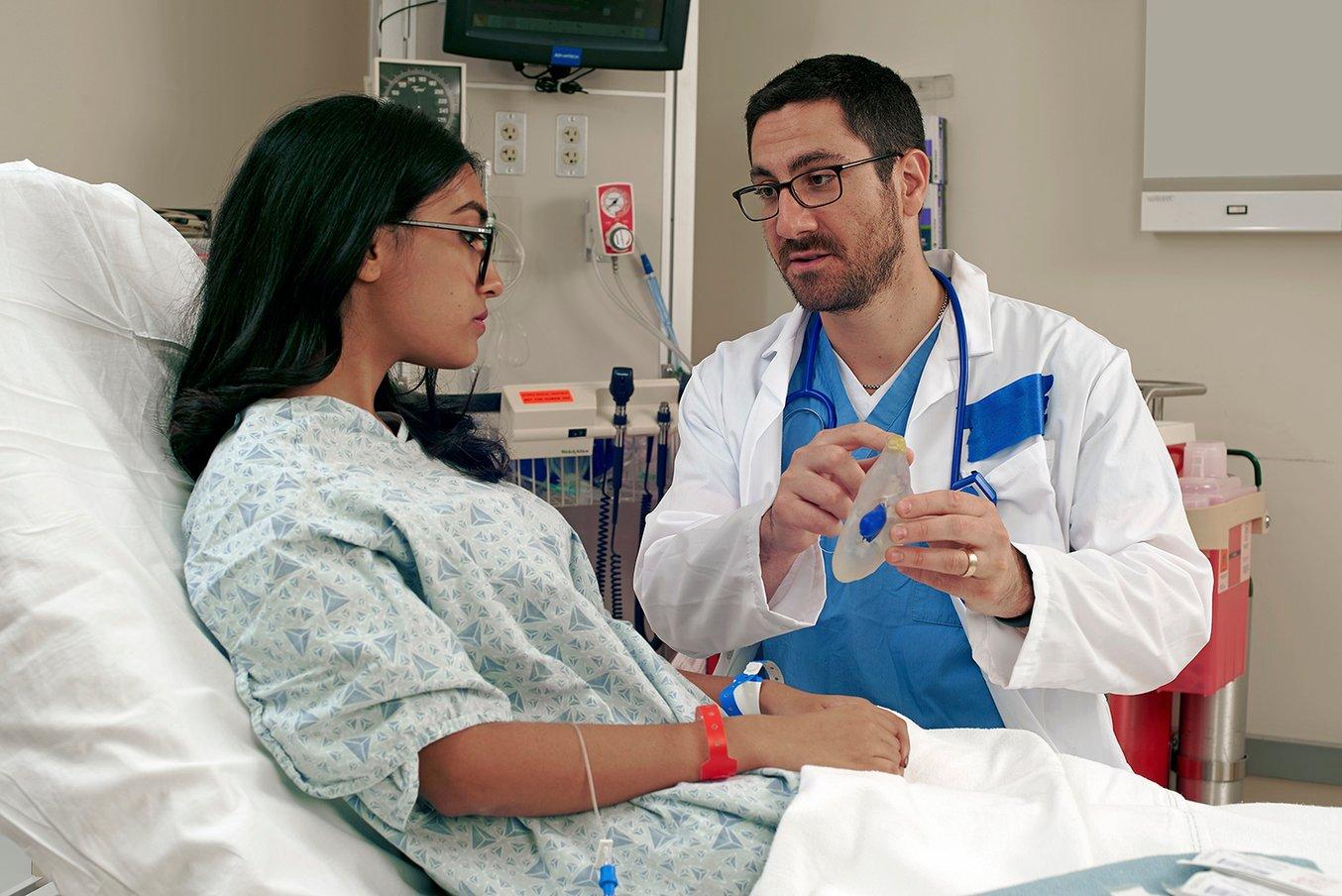
Vor einem Eingriff können Behandlungsteams patientenspezifische Operationsmodelle zur Aufklärung der Patient*innen nutzen, wodurch Sorgen genommen und Zustimmung und Akzeptanz gefördert werden.
Die Lehren aus präoperativen Modellen können sich auch auf den Verlauf der Behandlung auswirken. Diese Erfahrung machte Dr. Michael Eames. Nachdem er die Unterarmknochen eines jungen Patienten nachgebildet hatte, bemerkte er, dass die Verletzung nicht mit seiner ursprünglichen Annahme übereinstimmte.
Dr. Eames entschloss sich für eine neue Weichgewebeprozedur, einen weitaus weniger invasiven Eingriff, der die Genesungszeit verringerte und die Narbenbildung minimierte. Mit der gedruckten Nachbildung der Knochen erklärte Dr. Eames dem jungen Patienten und seinen Eltern den Eingriff, die daraufhin einwilligten.
Das Ergebnis? Die Operationszeit beschränkte sich auf unter 30 Minuten, anstatt der ursprünglich angesetzten drei Stunden. Diese Verkürzung der Operationsdauer sparte dem Krankenhaus geschätzte 5500 USD und beschleunigte die Genesung des Patienten, der nun weniger Zeit in postoperativer Pflege verbringen musste.
„Jeder einzelne unserer festen orthopädischen Chirurgen und nahezu alle unserer Teilzeitchirurgen am San Francisco VA haben bereits 3D-gedruckte Modelle zur Patientenbehandlung eingesetzt. Wir haben alle festgestellt, dass 3D-Druck am Tag des Eingriffs unsere Arbeit verbessert.“
Dr. Alexis Dang, orthopädischer Chirurg an der University of California San Francisco (UCSF) und dem San Francisco Veteran's Affairs Medical Center
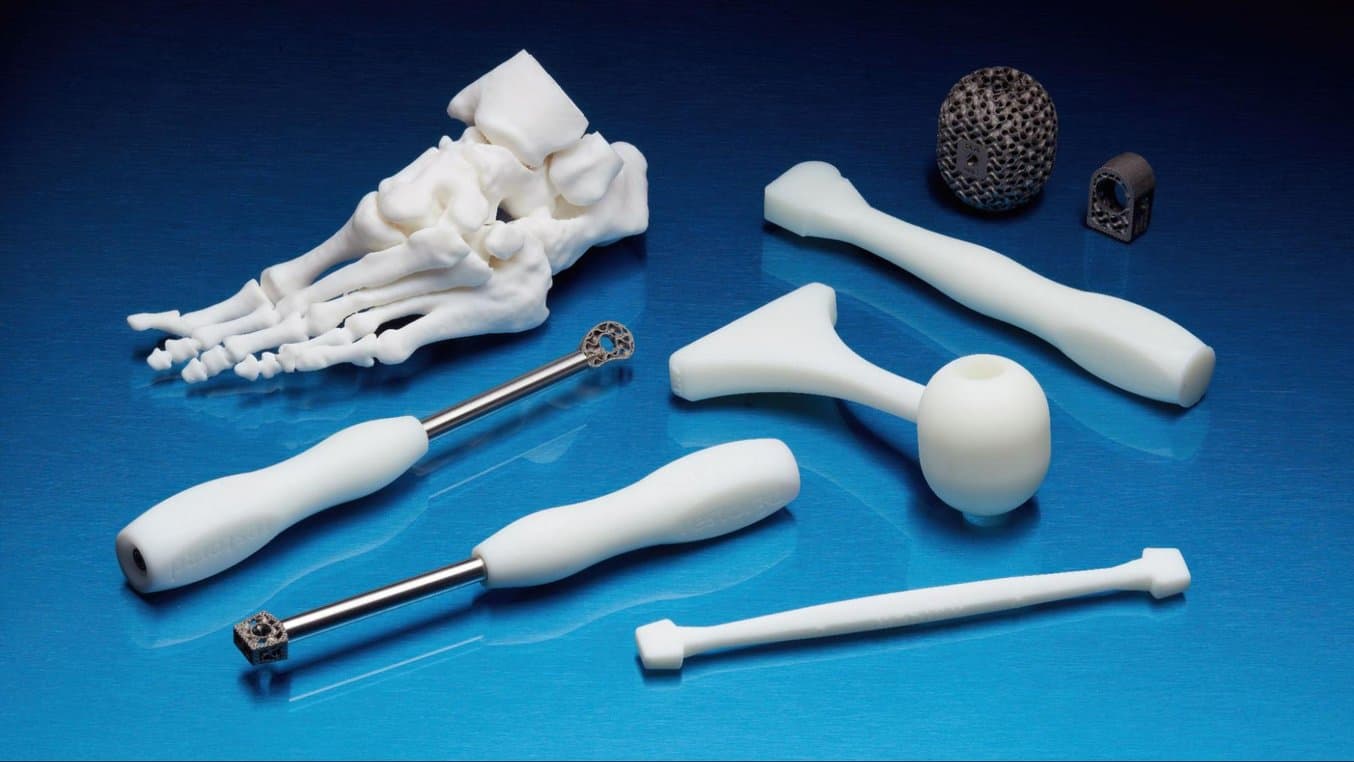
Personalisierte Chirurgie durch 3D-Druck: Fragerunde mit Insight Surgery (ehemals 3D LifePrints)
Seien Sie in dieser Fragerunde zum medizinischen 3D-Druck mit 3D LifePrints dabei und erfahren Sie, wie das Team auf innovative und vielseitige Weise patientenspezifische Medizinprodukte entwickelt.
Dr. Frederik Verstreken bei AZ Monica in der Region Antwerpen in Belgien ist Spezialist für Hand-, Handgelenks- und Unterarmchirurgie. Er berichtet, dass die Kombination aus Visualisierung, digitaler Planung und 3D-gedruckten Modellen die Zeit im Operationssaal um etwa 30–40 % verkürzt. Bei Fällen komplexer Osteotomie war es manchmal nicht möglich, die Anatomie wiederherzustellen. 3D-gedruckte chirurgische Modelle erlauben es den Behandelnden jedoch, sich deutlich besser auf die OP vorzubereiten als ohne digitale Hilfsmittel, sowie bei deutlich höherer Genauigkeit weniger Strahlung einzusetzen. Patient*innen können so ihre normale Beweglichkeit zurückgewinnen und schmerzfrei werden.
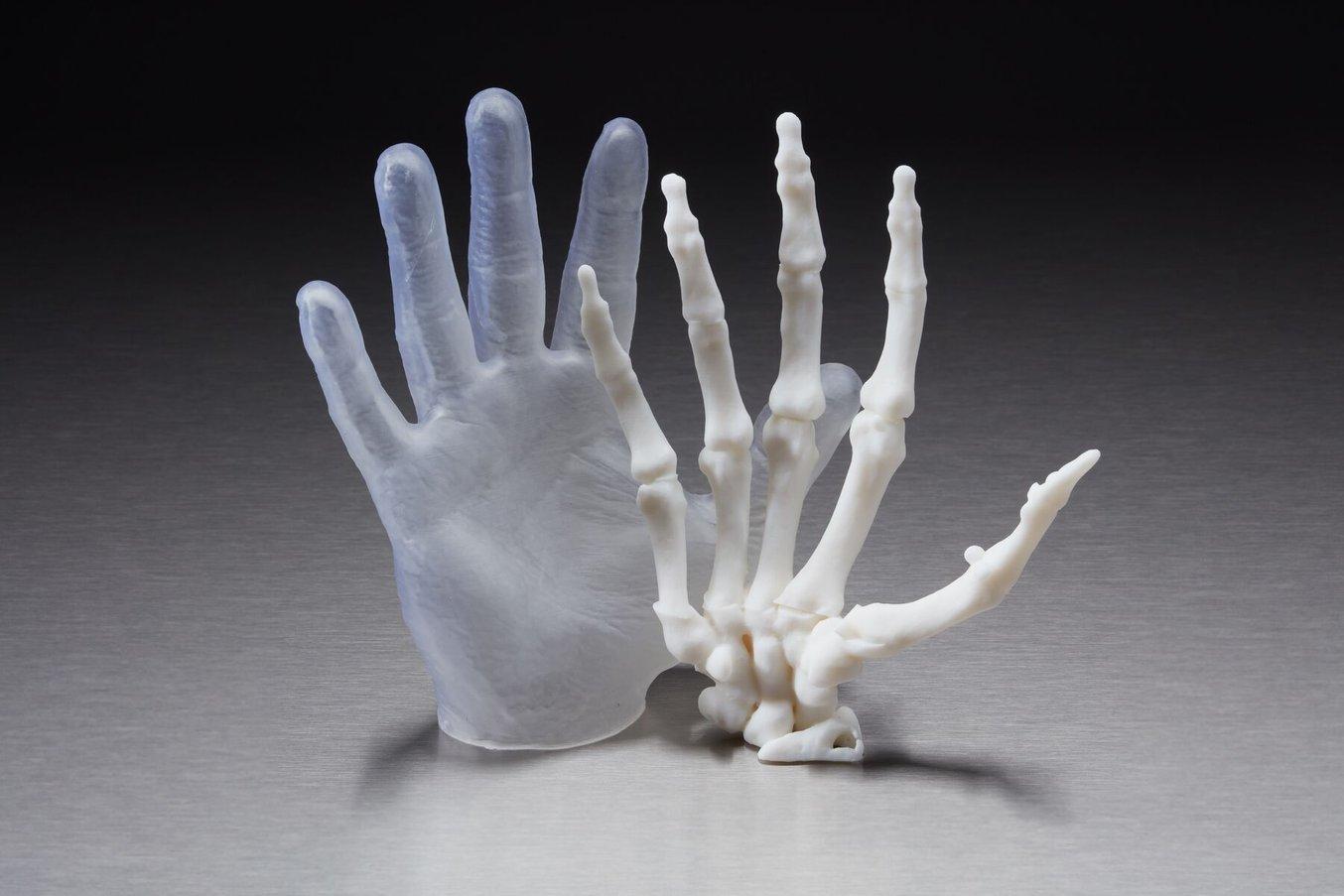
Anatomisches Modell einer Hand einschließlich einer „Haut“ aus elastischem 3D-Druckmaterial.
Für Todd Goldstein, PhD, Ausbilder am Feinstein Institute for Medical Research, ist es offensichtlich, welche zentrale Rolle 3D-Drucktechnologie in seiner Abteilung einnimmt. Seinen Einschätzungen zufolge könnte Northwell Health durch den Einsatz von 3D-gedruckten Modellen schon für 10–15 % aller Fälle 1 750 000 USD pro Jahr sparen.
Bohrschablonen können chirurgische Fachkräfte dabei unterstützen, ein Verständnis der individuellen Patientenanatomie und der Pathologie zu erlangen, Risiken zu analysieren, Ansätze zu planen und sich mit dem Fall vertraut zu machen, noch bevor sie den OP betreten. Die Materialauswahl anhand von spezifischen Eigenschaften wie etwa Elastizität macht es Chirurg*innen möglich, Eingriffe an Modellen zu proben, was die Operationsdauer verkürzt und bessere Ergebnisse erzielt.
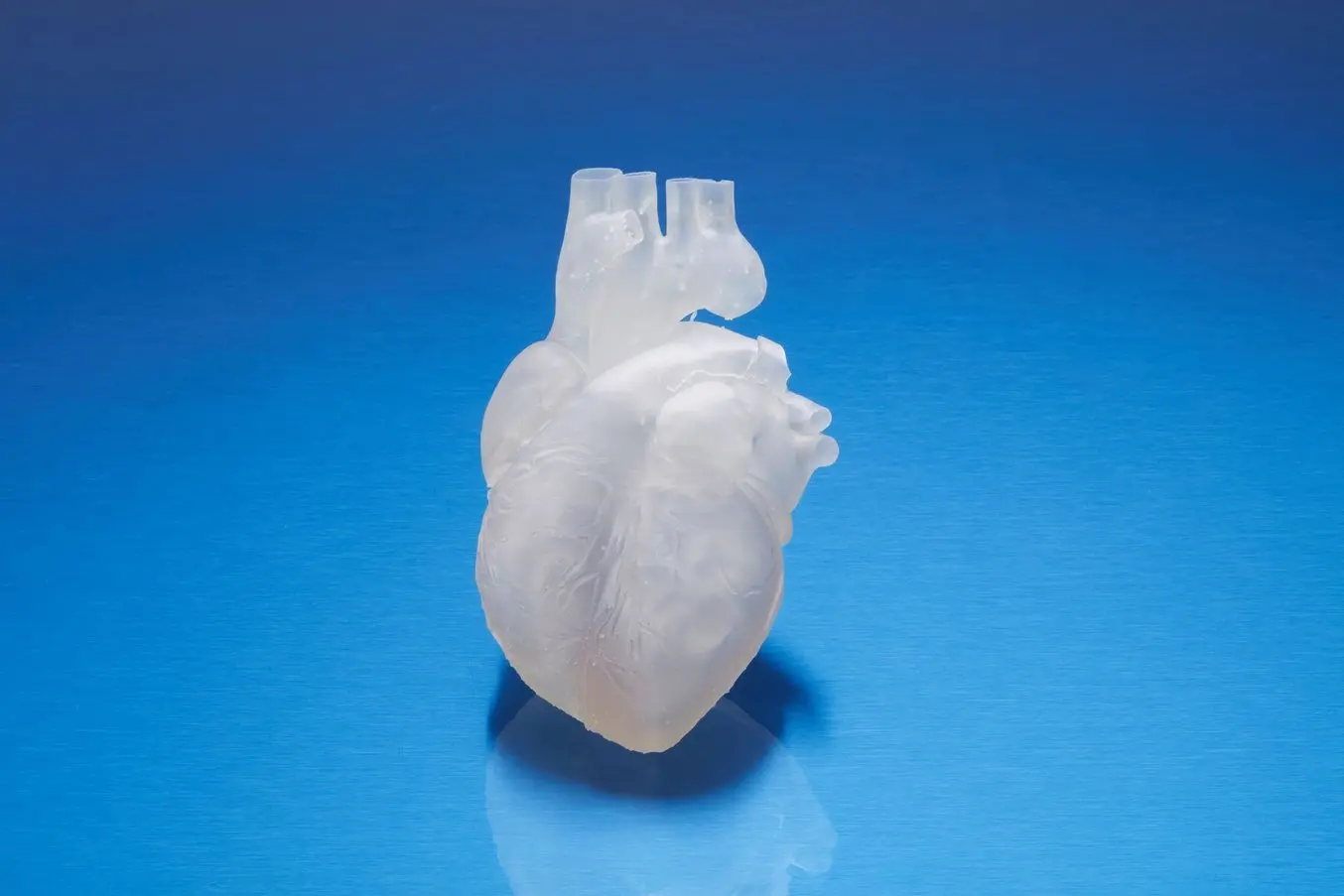
Einsatz der biokompatiblen Elastomere von Formlabs für Modelle vaskulärer Anatomie
Erfahren Sie, wie die medizinische Fachwelt biokompatible Elastomermaterialien in innovative 3D-Druckprozesse einbinden kann, mit Formlabs' neuesten Kunstharzen BioMed Flex 80A Resin und BioMed Elastic 50A Resin.
2. Patientenspezifische chirurgische Instrumente
Neue biokompatible 3D-Druckmaterialien haben außerdem zur Entwicklung neuer Operationswerkzeuge und -techniken geführt, die speziell die klinische Erfahrung während der Eingriffe verbessern. Traditionelle Instrumentensysteme werden nur langsam weiterentwickelt, verursachen erhebliche Vorlaufkosten und führen häufig zu Komplikationen im chirurgischen Arbeitsablauf. 3D-Drucker und biokompatible Materialien erleichtern die Herstellung eingriffsspezifischer und häufig patientenspezifischer Implantate, chirurgischer Instrumente sowie Bohrschablonen und machen diese kosteneffizienter.
3D-gedruckte, individualisierte Bohrschablonen können chirurgische Fachkräfte dabei unterstützen, ein Verständnis der individuellen Patientenanatomie und der Pathologie zu erlangen, Risiken zu analysieren, Ansätze zu planen und sich mit dem Fall vertraut zu machen, noch bevor sie den OP betreten. Gut geplante Bohrschablonen verringern den Zeitaufwand für einzelne Fälle und verkürzen die Dauer, während derer intraoperative Navigationssysteme von Behandelnden benutzt werden. Das hat eine geringere Strahlungsbelastung von Patient*innen und eine noch kürzere Operationsdauer zur Folge.
„Die Schablonen zeigen uns, wo wir die Löcher und Schnitte ansetzen müssen, damit mit einer Platte alles wieder in die richtige Position kommt. Die Präzision ist um einiges höher als ohne Schablonen. Dabei sparen wir ca. 50 % der Zeit gegenüber Eingriffen mit freier Hand. Und die Präzision ist so viel besser.“
Dr. Frederik Verstreken, Hand- und Handgelenkschirurg, AZ Monica Hospital
Die kurze Durchlaufzeit des 3D-Drucks lässt schnelle Designiterationen zu. Chirurgische Fachleute können Feedback geben, welches schnell eingearbeitet werden kann, woraufhin das Instrument oder die Schablone neugedruckt wird.
Restor3d verfolgt die Mission, Chirurg*innen und Gesundheitsversorger dabei zu unterstützen, den menschlichen Körper zu heilen und zu rekonstruieren, wofür sie Innovationen in der Präzisionschirurgie vorantreiben. Das Team von restor3d konnte mithilfe von 3D-Druck die chirurgische Versorgung erheblich verbessern, indem es eingriffsspezifische und oft auch patientenspezifische Metallimplantate und Polymerinstrumente druckt.
Restor3d hat sich beim Einsatz von 3D-Druck zur Innovation des OP-Saals als führendes Unternehmen etabliert. Ihre branchenführenden Sets für die präoperative Planung, die hochpräzisen und innovativen Implantate und die umfassenden Lösungen der Instrumentenkassette haben Krankenhäuser dabei unterstützt, Kosten zu senken und die Patientenerfahrung zu verbessern.
„Wir erhalten ständig Rückmeldungen von den Chirurgen. Durch den 3D-Druck ist es uns möglich, das Design schnell zu iterieren, um das Feedback der Chirurgen einzuarbeiten und in kurzer Zeit eine neue Lösung zu liefern.“
Nathan Evans, Senior Vice President der Produktentwicklung, restor3d
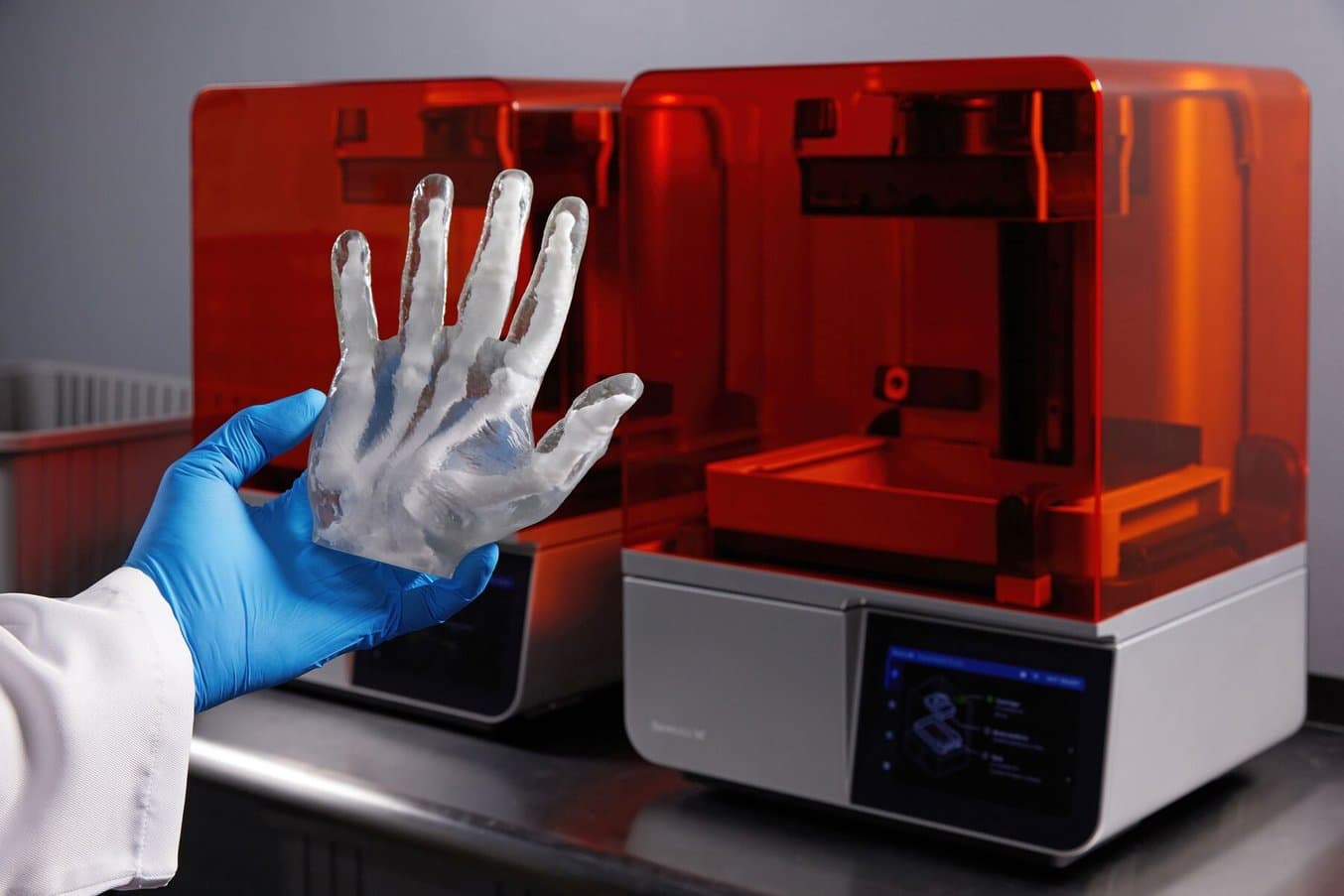
Formlabs' biokompatible Kunstharze: Ein umfassender Leitfaden zur Wahl des richtigen Materials
Formlabs bietet derzeit mehr als 40 einzigartige Materialien für den Stereolithografie-3D-Druck (SLA).Dieses Dokument hilft dabei, unsere biokompatiblen Angebote zu vergleichen und die beste Lösung für Ihre medizinischen Anwendungen zu finden.
3. Neue Medizinprodukte
3D-Druck ist für viele mittlerweile fast synonym mit Rapid Prototyping. Die Benutzerfreundlichkeit und die niedrigen Kosten des betriebsinternen 3D-Drucks haben auch die Produktentwicklung revolutioniert. Viele Hersteller von Medizinprodukten und chirurgischen Instrumenten setzen bei der Entwicklung brandneuer Produkte bereits auf diese Technologie.
Über 90 Prozent der Medizinproduktfirmen nutzen bereits 3D-Druck, um präzise Prototypen von Medizinprodukten oder Halterungen und Vorrichtungen zur Vereinfachung Ihrer Tests herzustellen, sowie auch für die direkte Produktion 3D-gedruckter Medizinprodukte.
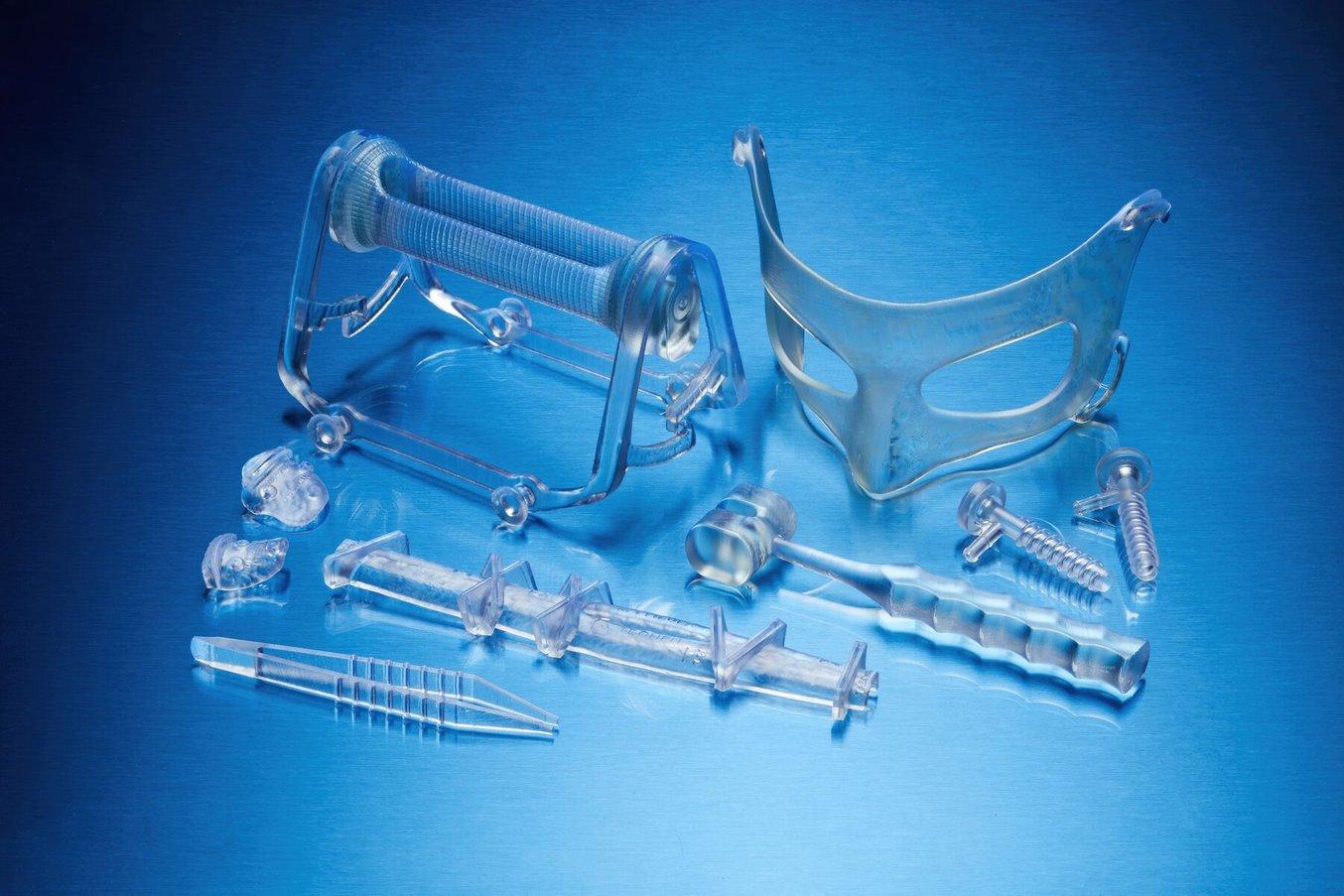
Aufbau eines neuen Medizintechnikunternehmens mit additiver Fertigung von Formlabs
Hören Sie von drei inspirierenden Startups alles über ihre Erfahrungen beim Aufbau eines brandneuen Unternehmens, während sie zugleich ihre ersten Medizinprodukte auf den Markt brachten. Die Unternehmen gewähren uns Einblick darin, warum sie sich als Partner in diesem Prozess für Formlabs entschieden haben und wie sie die additive Fertigung eingesetzt haben.
„Bevor DJO Surgical den [3D-Drucker von Formlabs] anschaffte, mussten wir uns für Prototypen fast ausschließlich auf externe Druckanbieter verlassen. Heute setzen wir vier Formlabs-Geräte ein, und die Auswirkungen sind tiefgreifend. Unsere 3D-Druckrate hat sich verdoppelt, die Kosten wurden um 70 Prozent reduziert und das hohe Druckdetail ermöglicht eine klare Kommunikation der Entwürfe bei Gesprächen mit orthopädischen Chirurgen.“
Alex Drew, Mechanical Project Engineer, DJO Surgical
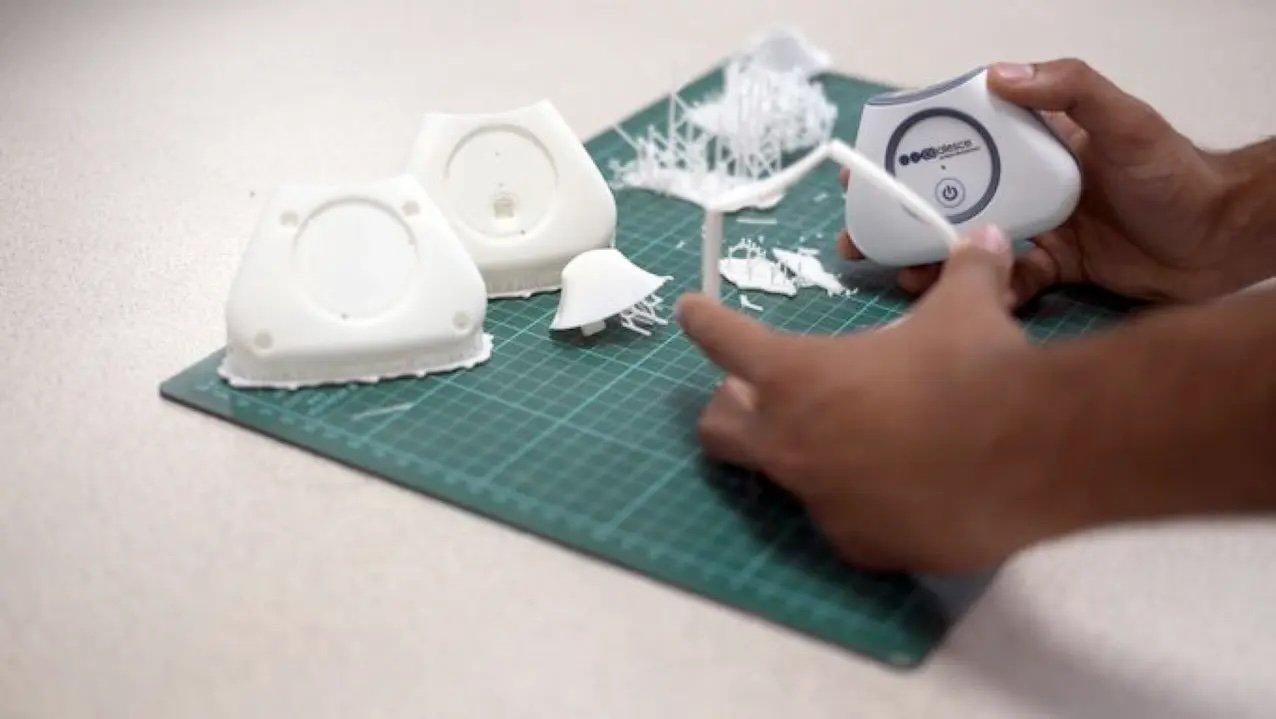
Medizinproduktfirmen wie Coalesce nutzen 3D-Druck, um präzise Prototypen medizinischen Geräts herzustellen.
3D-Druck beschleunigt den Designprozess, da komplexe Entwürfe innerhalb von Tagen iteriert werden können anstatt von Wochen. Als Coalesce den Auftrag hatte, einen Inhalator zu erstellen, der digital das Atemprofil von Asthmapatienten misst, hätte das Outsourcing zu einem Dienstleister bei jedem einzelnen Prototypen zu langwierigen Durchlaufzeiten geführt. Die Designdateien hätten über mehrere Iterationen hinweg mühsam verfeinert werden müssen, bevor sie dann außer Haus angefertigt würden.
Stattdessen setzte Coalesce auf SLA-3D-Druck für den Desktop und konnte so den gesamten Prozess der Prototypenentwicklung betriebsintern durchführen. Die Prototypen eigneten sich für klinische Studien und sahen aus wie das fertige Produkt. Bei der Vorführung des Geräts hielt sogar die Kundschaft den Prototypen für das Endprodukt.
Insgesamt verkürzte die betriebsinterne Fertigung die Durchlaufzeit der Prototypen um sagenhafte 80 bis 90 %. Darüber hinaus wurden die Teile in nur acht Stunden gedruckt und konnten innerhalb weniger Tage fertiggestellt und lackiert werden. Bei einem externen Dienstleister hätte der Prozess ein oder zwei Wochen in Anspruch genommen.
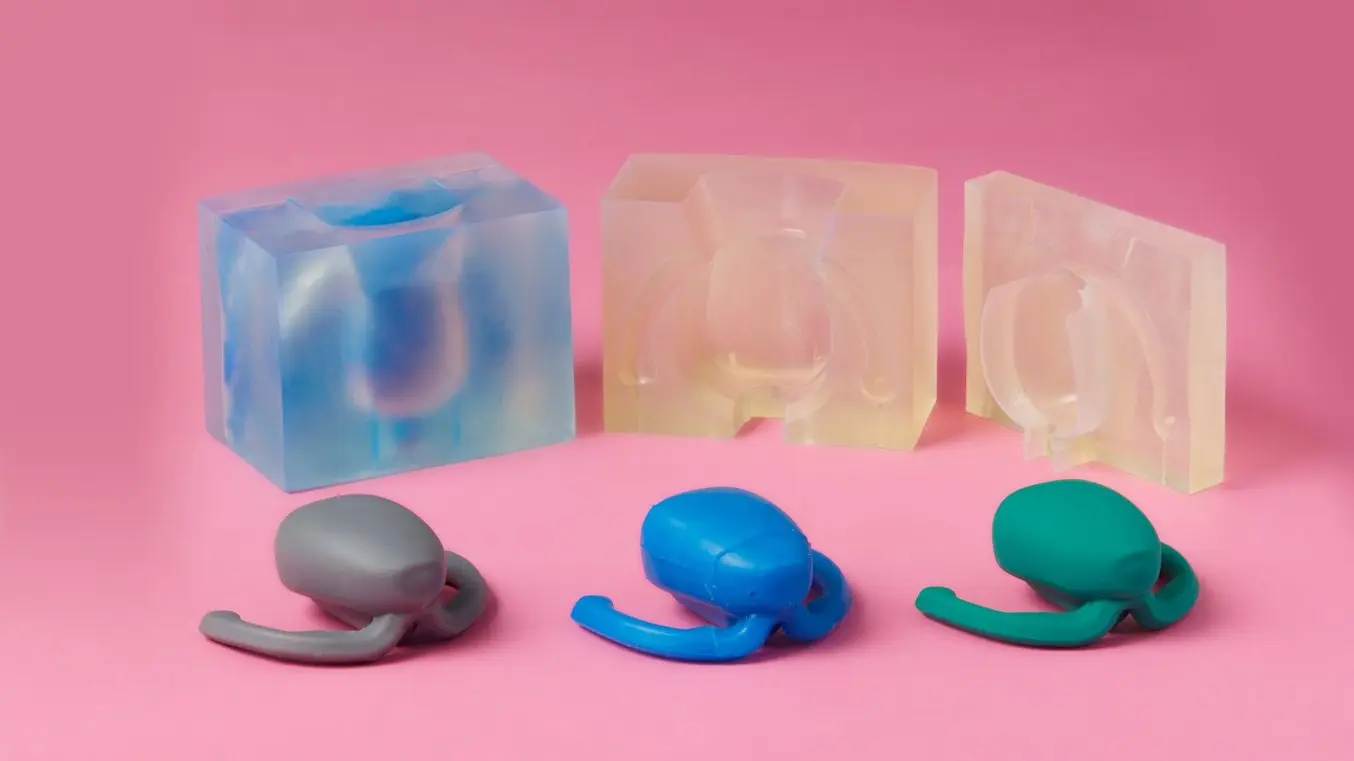
Herstellung von Medizinprodukten aus Silikon
Dieser Leitfaden dient als Entscheidungshilfe bei der Wahl der besten Produktionsmethode für Silikonteile je nach Verwendungszweck und bietet eine Schritt-für-Schritt-Anleitung für den Druck mit Silicone 40A Resin sowie für den Silikonguss mit SLA-3D-gedrucktem Werkzeug (einschließlich zweiteiliger Gussformen sowie Formen für Umspritzung und für das Formpressen).
Bei der Entwicklung von OxiWear, einem im Ohr tragbaren Gerät zur Überwachung der Lebensfunktionen und zur Notfallbenachrichtigung, stützte sich Shavini Fernando auf den 3D-Druck. Ihr Team nutzte SLA-3D-Druck sowohl für die Prototypenfertigung als auch für die Herstellung statisch ableitender Halterungen.
Fernando sagt: „Für uns als junges Unternehmen war der betriebsinterne 3D-Druck eine große Hilfe und konnte unsere Kosten über den gesamten Entwicklungsprozess hinweg immens senken. Er machte es uns möglich, mehrere Prototypendesigns gleichzeitig zu testen. Vor dem 3D-Druck kostete jeder ausgelagerte Prototyp etwa 200 USD. Auf dem Form 3B können wir jedes Teil für ein paar Pennys ausdrucken.“
4. Erschwingliche und fortschrittliche individualisierte Prothetik
Weltweit gibt es mehr als 50 Millionen Menschen, die aufgrund traumatischer Ursachen eine Amputation von Gliedmaßen durchlaufen haben. Für Betroffene, die sich von einem Notfalleingriff erholen, kann es eine schmerzvolle Erfahrung bedeuten, sich mit dem Feld der Prothetik auseinanderzusetzen. Die meisten von ihnen möchten in ihr normales Leben zurückkehren: Sie wollen Auto fahren, Sport treiben, ihren Haushalt führen. Traditionelle Prothesen für Gliedmaßen sind jedoch meist plump, teuer und empfindlich. Nur etwa 10 % aller Patienten, die eine fortschrittliche Armprothese benötigen, können sie sich derzeit leisten.
Einfache Prothesen gibt es nur in wenigen Größen, also müssen Betroffene mit dem zurechtkommen, was am besten passt. Maßgeschneiderte bionische Geräte, die die Bewegung und Funktion echter Extremitäten nachahmen und über die Muskeln im Extremitätsstumpf gesteuert werden, sind derart teuer, dass nur Patient*innen in Industrieländern mit bester Krankenversicherung sich diese leisten können. Diese Tatsache betrifft insbesondere Prothesen für Kinder. Da Kinder wachsen, wird ihre Prothese unausweichlich irgendwann zu klein und benötigt teuren Ersatz. Es mangelt an Fertigungsverfahren, die maßgeschneiderte Teile zu erschwinglichen Preisen herstellen. Allerdings können immer mehr Prothesenhersteller die Vorteile der oft angepriesenen Designfreiheit im 3D-Druck nutzen, um diese finanziellen Hürden in der Behandlung zu umgehen.
Ein Unternehmen, das diesen Markt auf den Kopf stellen will, ist PSYONIC, der Entwickler der Ability Hand. Diese wurde mittels hybrider Fertigungsmethoden betriebsintern entworfen und gefertigt und verspricht, das Leben und die Mobilität Betroffener wieder auf ihr ursprüngliches Niveau zu bringen. PSYONIC nutzt den 3D-Druck, um Prototypen in kürzester Zeit herzustellen, erschwinglicher und zugänglicher zu werden und langlebige Endverwendungsteile aus haltbaren und schlagfesten Materialien zu produzieren.
Bei Initiativen wie e-NABLE kommen weltweit ganze Communitys für 3D-gedruckte Prothesen zusammen. Es bildet sich eine unabhängige Bewegung der Prothesenproduktion, indem Informationen und offene Designs kostenlos online geteilt werden. So erhalten Patienten eine individuell designte und auf sie angepasste Prothese zum Preis von gerade einmal 50 USD.
Andere Erfinder wie Lyman Connor gehen noch einen Schritt weiter. Mit nur einer kleinen Anlage aus vier 3D-Druckern für den Desktop konnte Lyman seine erste produktionsreife Prothese fertigstellen und anpassen. Was ist sein Ziel? Er möchte eine individualisierbare und vollständig bionische Hand erstellen, die zu einem Bruchteil der üblichen Kosten verkauft werden kann – welche sich bei einer solch fortgeschrittenen Prothese meist über Zehntausende Dollar belaufen.
Wieder andere, wie die Forscher vom MIT, haben in 3D-Druck das ideale Mittel entdeckt, um wesentlich bequemere Prothesenverankerungen herzustellen.
Dass sich die niedrigen Produktionskosten dieser Prothesen gepaart mit der Designfreiheit als Offenbarung erwiesen haben, muss man gar nicht erwähnen. 3D-gedruckte Prothesen lassen sich schon in nur zwei Wochen anfertigen und können dann zu wesentlich geringeren Kosten ausprobiert und gewartet werden, als das bei ihren handelsüblichen Pendants der Fall ist.
Da die Kosten immer mehr sinken und sich die Materialeigenschaften weiter verbessern, wird die Rolle des 3D-Drucks in diesem Bereich des Gesundheitswesens in Zukunft unweigerlich zunehmend wichtiger.
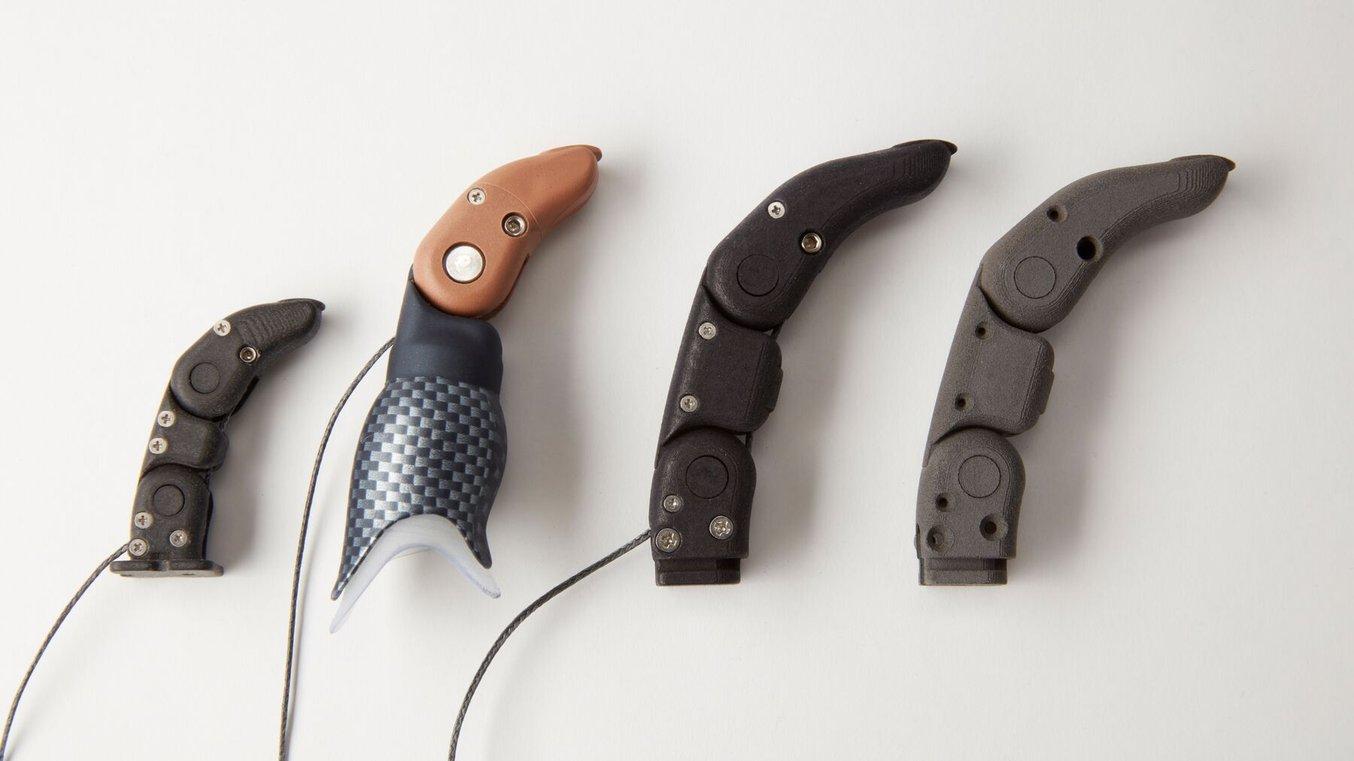
3D-Druck in der Orthetik und Prothetik
Dieses Whitepaper bietet eine Einführung zum Einsatz von 3D-Drucktechnologien bei der Herstellung neuartiger Orthesen und Prothesen.
5. Maßgefertigte Orthesen
Viele der finanziellen Hürden, die von Prothesen bekannt sind, findet man auch im Bereich der Orthesen. Wie die meisten patientenspezifischen Medizinprodukte haben auch maßgeschneiderte Orthesen oft unerschwingliche Preise und ihre Anfertigung nimmt Wochen oder Monate in Anspruch. Mit 3D-Druck kann das der Vergangenheit angehören.
Viele medizinische Fachleute steigen derzeit auf die Produktion individueller orthopädischer Lösungen mittels 3D-Druck um. Durch die Anwendung geprüfter Arbeitsprozesse spart der 3D-Druck Zeit und Ressourcen und ermöglicht so die Herstellung patientenspezifischer Orthesen in Rekordgeschwindigkeit.
Digitale Prozesse zur Fertigung individueller Orthesen beinhalten neue Optionen für Design, Prüfung und Fertigung, die die Kosten der Individualisierung verringern und Produktionszyklen beschleunigen, wodurch kürzere Durchlaufzeiten, besser passende Vorrichtungen und verbesserte Behandlungsergebnisse erzielt werden. 3D-gedruckte Orthesen bieten eine leistungsstarke Lösung, die schnell und kostengünstig individuelle Ergebnisse liefert.
Die Kriwat GmbH ist ein auf orthopädische Schuhtechnik spezialisiertes Sanitätshaus mit Sitz in Kiel, das sich mit dem Problem des Fachkräftemangels konfrontiert sah. Hinzu kam, dass die traditionellen Arbeitsabläufe eine mit Staub und chemischen Dämpfen belastete Umgebung erzeugten. Um diesen Problemen entgegenzuwirken, entwickelte Orthopädieschuhtechnikmeister Lais Kriwat einen digitalen Arbeitsprozess für die Einlagenproduktion mit zwei SLS-3D-Druckern des Typs Fuse 1+ 30W und Nylon 11 Powder.
Der digitale Prozess senkte Material- und Arbeitskosten enorm. Nach Lais' Schätzung reduzierten sich die Produktionskosten dank des 3D-Drucks um etwa 15 bis 17 %. Zudem beschleunigte er die Produktion, was es möglich machte, mehr Personen zu behandeln. „Jetzt haben wir die Möglichkeit, innerhalb von 24 Stunden eine perfekt passende Einlage für den Patienten zu schaffen“, so Lais Kriwat.
Die Gestaltungsfreiheit des SLS-3D-Drucks ermöglicht unter anderem die Umverteilung des Drucks beim Gehen, individuelle Premium-Produkte, bestimmte Arten von Stützen, die sich mit traditionellen Methoden nicht fertigen lassen, und dünnere Produkte, die dennoch optimalen Halt für den Fuß bei Sportarten wie Joggen oder Fußball bieten.
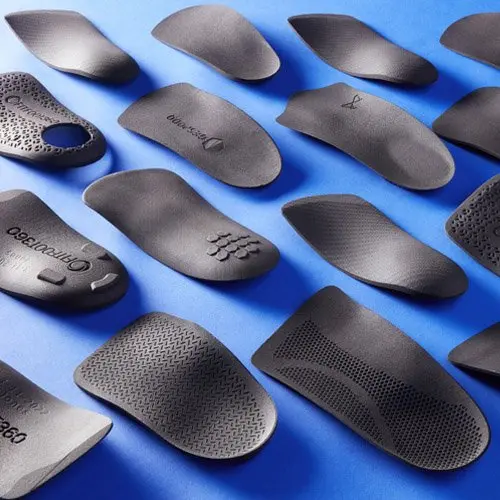
3D-Druck von Einlagenrohlingen mit dem Fuse 1+ 30W und Nylon 11 Powder
Diese Studie untersucht die Materialeigenschaften und Fertigungsmethoden für maßgefertigte orthopädische Einlegesohlen – hergestellt mit dem Fuse 1+ 30W und Nylon 11 Powder von Formlabs, HP 3D High Reusability PA 11 bzw. traditionell verarbeitetem Polypropylen.
Matej und sein Sohn Nik sind ein Beispiel für die Leistungsfähigkeit 3D-gedruckter individueller Orthesen. Durch Schwierigkeiten bei seiner Frühgeburt in 2011 leidet Nik unter Zerebralparese, einer Krankheit, von der weltweit fast 20 Millionen Menschen betroffen sind. Matej wurde inspiriert durch den unablässigen Willen seines Sohnes, sich nicht von seiner Krankheit einschränken zu lassen. Doch stand er bei der Orthese vor der Wahl eines Standardmodells, das für seinen Sohn unzureichend und unbequem gewesen wäre, oder einer teuren Maßanfertigung, die erst nach Wochen oder Monaten geliefert würde und aus der sein Sohn schnell herauswächst.
Er nahm die Sache selbst in die Hand und suchte nach einer neuen Lösung des Problems. Dank der Freiheiten digitaler Technologien wie 3D-Scans und 3D-Druck konnte Matej mit Niks Physiotherapeuten frei experimentieren und einen gänzlich neuen und innovativen Arbeitsprozess für Unterschenkelorthesen (AFOs) entwickeln.
Das Ergebnis war eine maßgefertigte, 3D-gedruckte Orthese, die Nik an den richtigen Stellen Stabilisierung, Tragekomfort und Korrektur bot. So konnte Nik endlich allein seine ersten Schritte tun. Diese individuelle Orthese entspricht den stark angepassten Charakteristika hochwertiger Orthetik – und das zu einem Bruchteil des Preises und ohne zusätzliche Nachkorrekturen.
Der 3D-Druck ermöglicht die Produktion patientenspezifischer Orthesen in effizienten Prozessen, die Zeit und Ressourcen sparen. Für Patient*innen bedeutet dies weniger Behandlungstermine, kürzere Behandlungen und präzise Individualisierung für gesteigerten Komfort. Im Vergleich zu konventionellen Fertigungsmethoden spart der 3D-Druck Zeit und Material, während er zudem die Kosten senkt und für eine angenehmere Arbeitsumgebung sorgt.
6. Bioprinting, Gewebezüchtung, 3D-gedruckte Organe und mehr
3D-Bioprinting beschreibt die Nutzung additiver Fertigungsverfahren, bei denen als „Bio-Tinten“ bezeichnete Materialien aufgeschichtet werden, um neue gewebeähnliche Strukturen für die Medizin zu erschaffen. Gewebezüchtung oder „Tissue Engineering“ bezieht sich auf die Vielzahl aufkeimender Technologien, bei denen Ersatzgewebe und -organe im Labor gezüchtet werden, um damit Verletzungen und Krankheiten zu behandeln. Darunter fällt auch Bioprinting.
In der Forschung wird Bioprinting für die Entwicklung von laborgezüchtetem Gewebe oder Organen genutzt. Die Verwirklichung dessen würde letzten Endes einen Fortschritt für die regenerative Medizin und Sicherheitstests bedeuten. Außerdem könnte die Möglichkeit, Organe durch Bioprinting zu erzeugen, die Erfolgsquote von Transplantationen deutlich erhöhen. Da Bioprinting entnommene Zellen der Betroffenen verwendet, besteht keine Gefahr, dass das Immunsystem das Transplantat abstößt – eine Komplikation, die heutzutage häufig bei Organtransplantationen auftritt.
An der Universität Osaka haben Forschende zellbasierte Tinte und eine Druckunterstützung verwendet, um bestimmte Formen zu erstellen, unter anderem eine Nase. Nach dem Druck bleiben die Zellen bis zu zwei Wochen lang lebensfähig, was einen bedeutenden Schritt in Richtung der laborgestützten Entwicklung von Organen darstellt.
Heutzutage werden die Regeneration der Haut und die Wundheilung mithilfe schmerzhafter Hauttransplantationen erzielt. Die Möglichkeit, Haut durch 3D-Druck zu erstellen, bietet eine Alternative, die die Regeneration und die Wundheilung unterstützen würde. 2023 hat ein Forschungsteam am Wake Forest Institute for Regenerative Medicine erfolgreich Haut in voller Dicke durch Bioprinting hergestellt, welche eine vollumfassende Wundheilung aufwies, als sie in vorklinischer Umgebung transplantiert wurde.
Dr. Atala, der Hauptautor des Papers, berichtet: „Die Ergebnisse zeigen, dass die Herstellung menschlicher Haut in voller Dicke durch Bioengineering möglich ist und dass diese eine schnellere Heilung und natürlicher aussehende Ergebnisse fördert.“
Wissenschaftler*innen am Terasaki Institute für biomedizinische Innovation haben eine Bio-Tinte für den Druck entwickelt, mit der die Formation von Skelettmuskelgewebe gesteigert wird. Letztendlich hofft das Team, dass die Technologie eingesetzt werden kann, um Menschen mit Muskelschwund oder Verletzungen zu helfen.
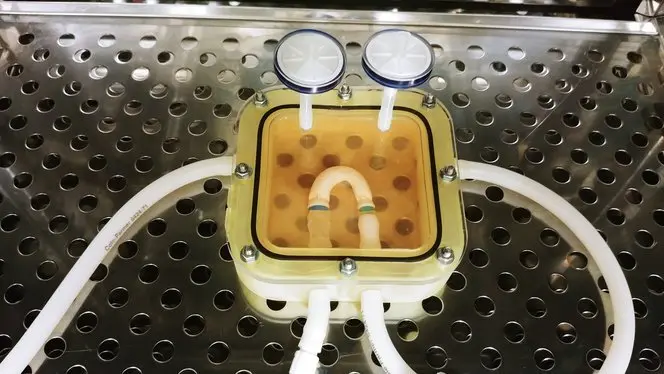
Eine 3D-gedruckte Biorekatorkammer, in der die gewebegezüchtete Aorta-Miniatur wächst. Das Gewebe wird im Bioreaktor kultiviert, um die mechanische und biologische Leistung des organischen Gewebes auszubilden.
Medizinischer 3D-Druck stellt sich der Herausforderung synthetischer Blutgefäße und löst die Probleme der exakten Form, Größe und Geometrie der betroffenen Gefäße. Die Möglichkeit der Anpassung der gedruckten Lösung an die Patientenbedürfnisse hat sich als unschätzbar wertvoll erwiesen.
Mit den Worten von Dr. Pashneh-Tala: „[Die Erstellung von Blutgefäßen mithilfe von 3D-Druck] öffnet die Tür für verbesserte Operationsoptionen und selbst für an die Patienten angepasste Blutgefäßdesigns. Ohne hochpräzisen, preiswerten 3D-Druck wäre die Erstellung dieser Strukturen nicht möglich.“
Bioprinting entwickelt sich rasant weiter, denn Forschende reizen die Grenzen des Möglichen immer weiter aus. Angefangen von Knochen und Blut bis hin zu Haut und Muskeln haben Entwicklungen beim Bioprinting das Fundament für zukünftige Verbesserungen in der Patientenversorgung gelegt.
Medizinischer 3D-Druck
Wenn es um 3D-Drucker für medizinische Anwendungen geht, sind nicht alle Methoden gleichwertig. Es ist wichtig, für den jeweiligen Anwendungsfall die richtige Drucktechnologie zu wählen.
Zu den beliebtesten 3D-Drucktechnologien für Medizinprodukte aus Kunststoff zählen u. a. Stereolithografie (SLA), selektives Lasersintern (SLS) und Schmelzschichtung (FDM). Für Metallteile eignen sich Direct Metal Laser Sintering (DMLS) sowie selektives Laserschmelzen (SLM).
Stereolithografie (SLA)
SLA-3D-Drucker verwenden einen Laser, um flüssige Kunstharze (auch Resin genannt) zu festen Kunststoffteilen auszuhärten. Dieser Prozess wird als Photopolymerisation bezeichnet. SLA ist bei medizinischen Fachkräften besonders beliebt, da die Technologie eine hohe Auflösung, Präzision und eine große Materialauswahl bietet.
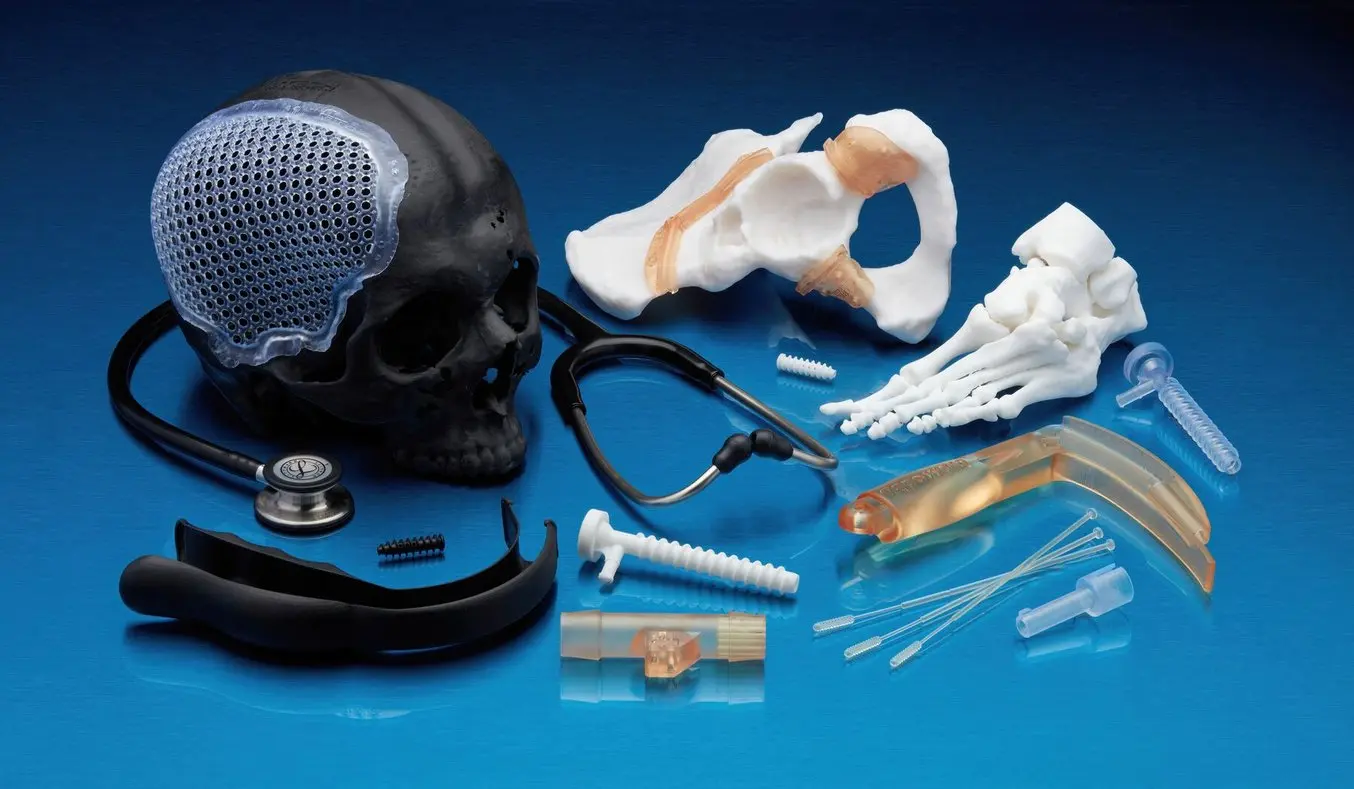
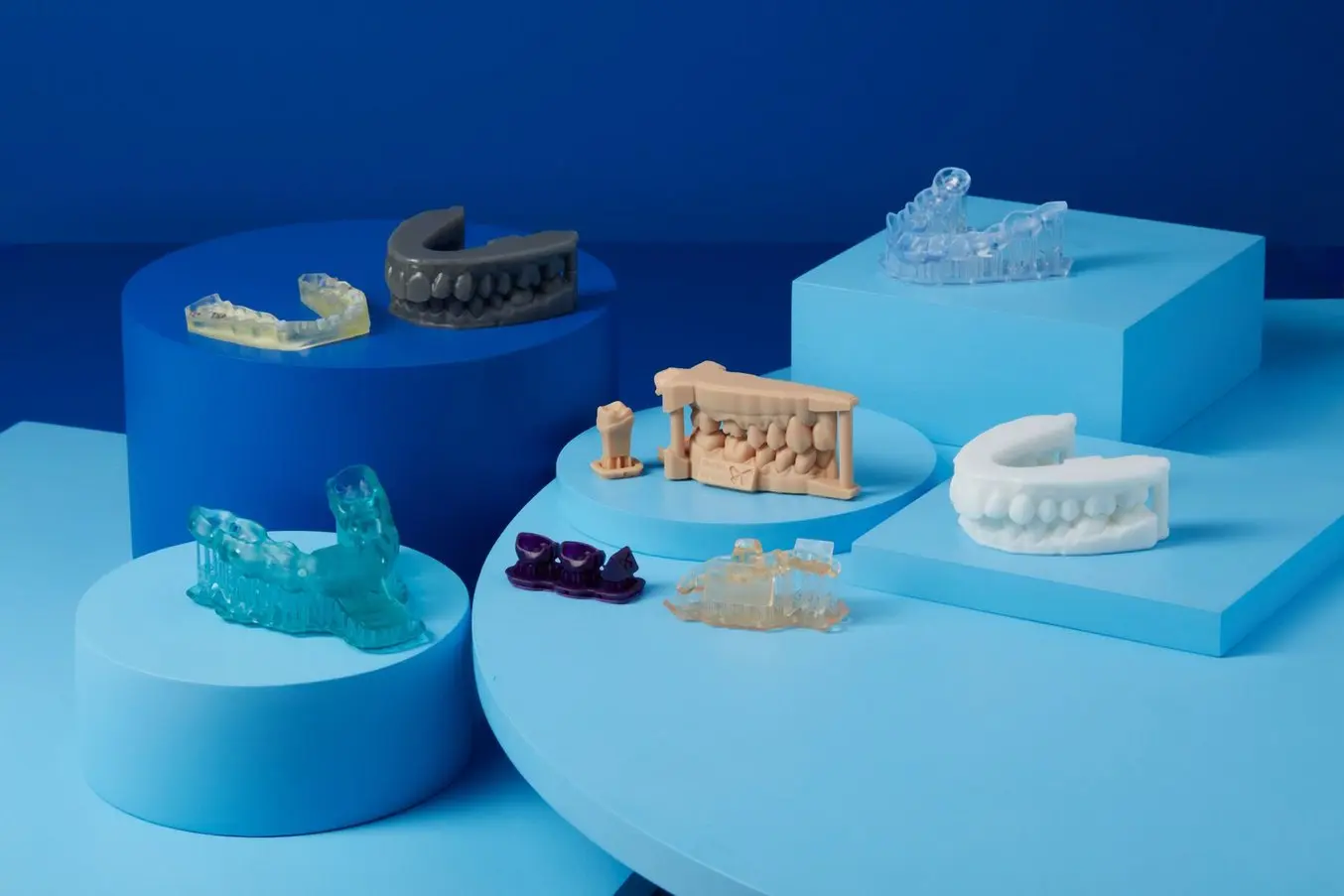
Für den SLA-3D-Druck existiert eine große Auswahl an 3D-Druckmaterialien, auch biokompatible Materialien für eine Vielzahl medizinischer und zahnmedizinischer Anwendungen.
Vorteile von SLA
SLA-Teile bieten die höchste Auflösung und Präzision, die filigransten Details und die glattesten Oberflächen aller 3D-Drucktechnologien für Kunststoffe. Allerdings liegt der Hauptvorteil von SLA in der Vielseitigkeit. SLA-Kunstharzformulierungen bieten unterschiedliche optische, mechanische und thermische Eigenschaften, die denen von Standard-, technischen und industriellen Thermoplasten in nichts nachstehen.
So eignet sich SLA hervorragend für detailreiche Anatomiemodelle, Prototypen von Medizinprodukten mit engen Toleranzen und glatten Oberflächen sowie für Gussformen, Werkzeuge, Muster und funktionsfähige Endverbrauchsteile. SLA bietet außerdem die größte Auswahl an biokompatiblen Materialien für dentale und medizinische Anwendungen, die Haut- oder Schleimhautkontakt erfordern, beispielsweise chirurgische Instrumente und medizinische Vorrichtungen.
Nachteile von SLA
Die Vielseitigkeit von SLA bedingt etwas höhere Kosten als FDM, die Technologie ist aber immer noch günstiger als alle anderen 3D-Druckprozesse. SLA-Teile aus Kunstharz müssen nach dem Druck nachbearbeitet, das heißt gewaschen und nachgehärtet werden.

Kostenlosen Probedruck anfordern
Sehen und fühlen Sie die SLA-Qualität von Formlabs aus erster Hand. Wir senden Ihnen einen kostenlosen Probedruck an Ihren Arbeitsplatz.
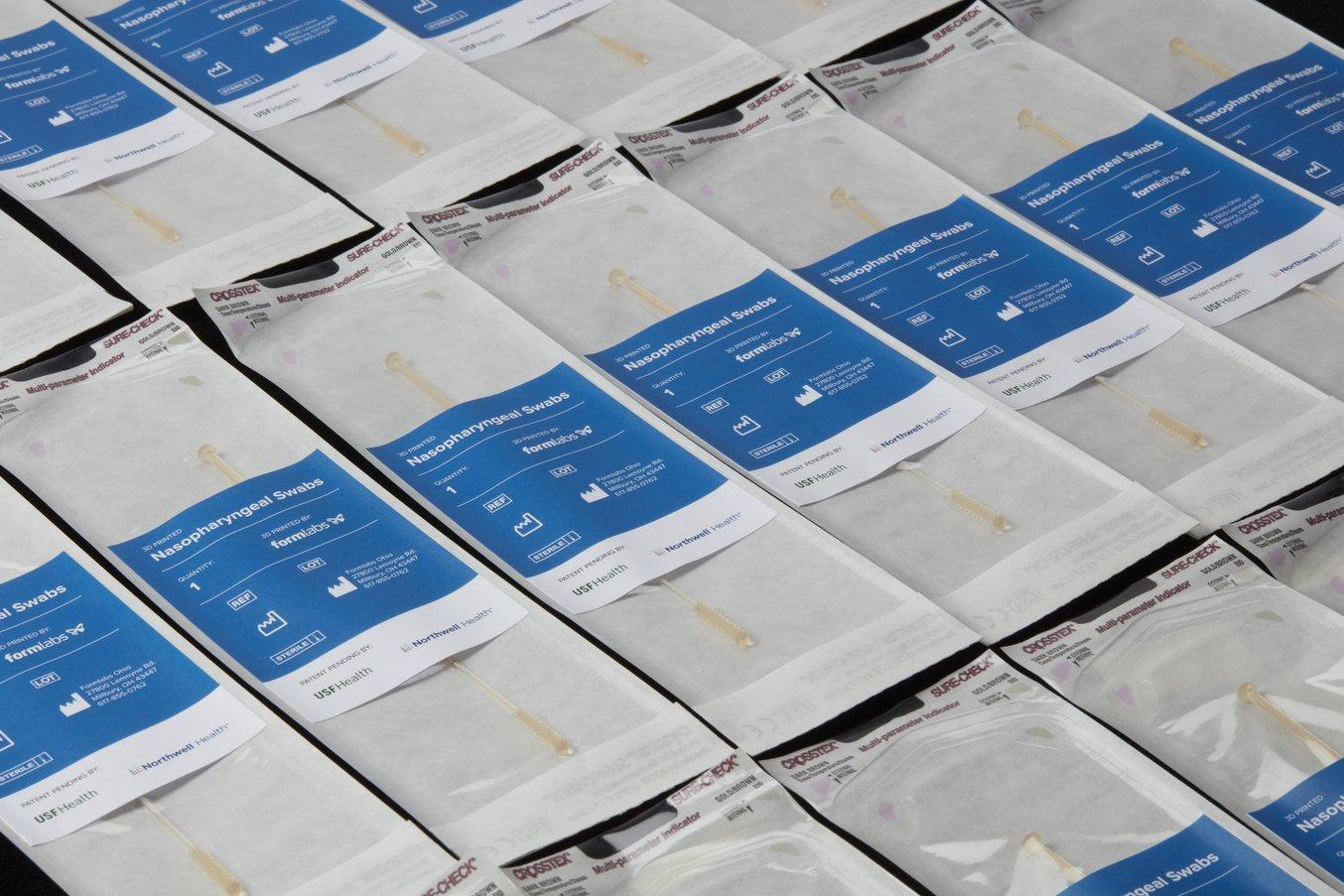
Formlabs-Leitfaden zur Qualitätskontrolle beim SLA-Druck für Innovatoren im Gesundheitswesen
In diesem Leitfaden erläutern wir die Schritte, mit denen Fachkräfte im Gesundheitswesen die Qualität 3D-gedruckter SLA-Teile überwachen und verbessern.
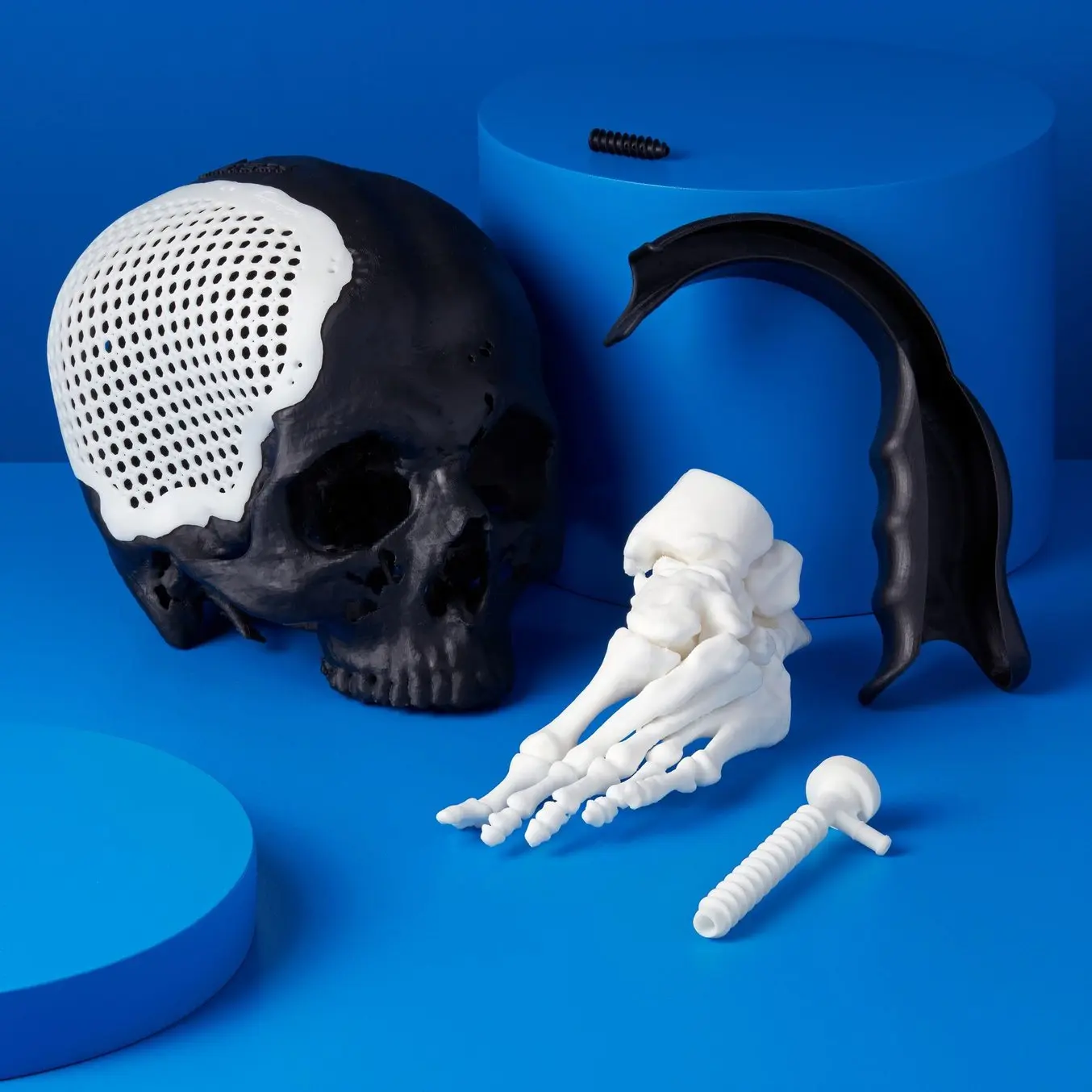
3D-gedruckte Medizinprodukte für die Präzisionschirurgie: Klinische, wirtschaftliche und regulatorische Gesichtspunkte
Tauchen Sie mit Formlabs und Nelson Labs in das Thema Biokompatibilität ein und lernen Sie unsere neuen Materialien sowie bewährte Praktiken für Hersteller von Medizinprodukten kennen, vorgestellt von Fachleuten der Branche.
Selektives Lasersintern (SLS)
SLS-3D-Drucker verwenden einen Hochleistungslaser, um kleine Polymerpulverpartikel zu sintern. Da das ungesinterte Pulver das Teil beim Drucken stützt, sind keine zusätzlichen Stützstrukturen erforderlich. Das macht SLS zu einer besonders effektiven Option für komplexe mechanische Teile.
Weil diese Technologie Teile mit herausragenden mechanischen Eigenschaften produziert, ist SLS das am weitesten verbreitete additive Fertigungsverfahren bei Industrieanwendungen. Abhängig vom Material können SLS-Teile auch biokompatibel und sterilisierbar sein, weshalb sie sich ideal für Medizinprodukte, Prototypen, chirurgische Bohrschablonen, Wearables und Orthesen eignen.
Vorteile von SLS
Bei dieser Technologie sind keine dedizierten Stützstrukturen erforderlich. SLS eignet sich somit ideal für komplexe Geometrien, auch im Inneren von Teilen, für Hinterschneidungen, dünne Wände und Vertiefungen. SLS-Teile bieten Teile mit herausragenden mechanischen Eigenschaften, deren Festigkeit mit der von Spritzgussteilen vergleichbar ist.
Hersteller von Medizinprodukten bevorzugen SLS oft zur Herstellung funktionsfähiger Prototypen aufgrund der geringen Kosten pro Teil, hoher Produktivität, bewährter Materialien und aufgrund der Biokompatibilität.
Nachteile von SLS
Der Einstiegspreis für SLS-3D-Drucker ist höher als bei FDM oder SLA. Obwohl eine Vielzahl verschiedener Materialien zur Verfügung steht, ist die Materialauswahl bei SLS geringer als bei FDM und SLA. Die Teile kommen mit einer etwas rauen Oberflächenbeschaffenheit aus dem Drucker und erfordern Nachbearbeitung (z. B. Sandstrahlen), um eine glatte Oberfläche zu erreichen.

Der SLS-3D-Druck eignet sich ideal für stabile, funktionsfähige Prototypen und Endverbrauchsteile wie Prothesen und Orthesen.
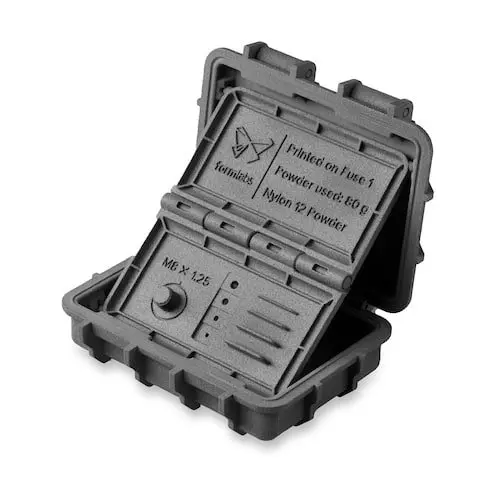
Kostenlosen Probedruck anfordern
Sehen und fühlen Sie die SLS-Qualität von Formlabs aus erster Hand. Wir senden Ihnen einen kostenlosen Probedruck an Ihren Arbeitsplatz.
Schmelzschichtung (FDM)
Bei der Schmelzschichtung (auch FDM für Fused Deposition Modeling oder FFF für Fused Filament Fabrication) werden Teile durch Schmelzen und Extrudieren eines drahtförmigen thermoplastischen Kunststoffs (genannt Filament) aufgebaut, der von einer Druckdüse schichtweise im Konstruktionsbereich aufgetragen wird.
FDM ist die bei Privatpersonen am häufigsten verbreitete Form des 3D-Drucks, da viele Hobbybastler damit den Einstieg in den 3D-Druck wagen. Industrielle FDM-Drucker sind aber auch bei Fachleuten beliebt.
Vorteile von FDM
FDM funktioniert mit verschiedenen Standardthermoplasten wie ABS, PLA und deren Mischungen. Das ermöglicht niedrige Einstiegs- und Materialpreise. FDM eignet sich vor allem für Machbarkeitsstudien und kostengünstige Prototypen einfacher Teile. Manche FDM-Materialien sind auch biokompatibel.
Nachteile von FDM
Schmelzschichtung hat die niedrigste Auflösung und Präzision der 3D-Druckprozesse für Kunststoffe (verglichen mit z. B. SLA oder SLS) und eignet sich deshalb nur bedingt für den Druck komplexer Designs oder filigraner Details, die etwa für Anatomiemodelle erforderlich wären. Hochwertigere Oberflächen erfordern arbeits- und zeitintensive chemische und mechanische Polierverfahren. Einige industrielle FDM-3D-Drucker verringern dieses Problem teilweise durch chemisch auflösbare Stützstrukturen. Außerdem bieten sie eine breitere Auswahl an technischen Thermoplasten. Jedoch kosten solche Geräte eine Menge Geld. Bei größeren Teilen ist FDM zudem meist langsamer als SLA oder SLS.
Direct Metal Laser Sintering (DMLS) und selektives Laserschmelzen (SLM)
DMLS und SLM funktionieren ähnlich wie SLS, doch statt Polymerpulver werden Metallpulverpartikel Schicht für Schicht durch einen Laser verschmolzen.
DMLS- und SLM-3D-Drucker erstellen stabile, präzise und komplexe Metallprodukte, deshalb eignet sich dieses Verfahren ideal für eine Reihe medizinischer Anwendungen.
Vorteile von DMLS und SLM
Der größte Vorteil dieser Prozesse sind natürlich die Materialien, da DMLS- und SLM-3D-Drucker in der Lage sind, Hochleistungsmedizinprodukte für den Endgebrauch und Komponenten mit hochwertigen Eigenschaften aus Metall herzustellen. Diese Prozesse können komplexe Geometrien reproduzieren. Die fertigen Produkte sind stabil, langlebig und biokompatibel. Sie können in der Medizin zur Herstellung generischer Implantate (für Hüfte, Knie, Wirbelsäule usw.), maßgefertigte Implantate für die Krebs- oder Traumabehandlung, Zahnersatz sowie für medizinische und orthopädische Technologieprodukte verwendet werden.
Nachteile von DMLS und SLM
Auch wenn die Preise für Metall-3D-Drucker langsam sinken, sind diese Systeme mit 200 000 bis über 1 Mio. USD für die meisten Unternehmen noch immer unerschwinglich. Zudem erfordern Metall-3D-Druckprozesse aufwendige und komplexe Arbeitsabläufe.
Als Alternative bietet sich SLA-Druck in Verbindung mit Metallgussverfahren an. So fertigen Sie Metallteile zu niedrigen Kosten, mit mehr Gestaltungsfreiheit und in kürzerer Zeit als bei herkömmlichen Verfahren.
Medizinische 3D-Drucker vergleichen
Stereolithografie (SLA) | Selektives Lasersintern (SLS) | Schmelzschichtung (FDM) | Metall-3D-Druck (DMLS, SLM) | |
---|---|---|---|---|
Fertigungsvolumen | Bis zu 300 × 335 × 200 mm (Desktop- und Benchtop-3D-Drucker) | Bis zu 165 × 165 × 300 mm (industrielle Benchtop-3D-Drucker) | Bis zu 300 × 300 × 600 mm (Desktop- und Benchtop-3D-Drucker) | Bis zu 400 × 400 × 400 mm (große industrielle DMLS-/SLM-Drucker) |
Preisspanne | Professionelle Desktop-3D-Drucker beginnen bei 2399 €, großformatige Benchtop-Drucker bei 8999 €, und industrielle Großmaschinen sind ab ca. 80 000 € erhältlich. | Industrielle Benchtop-Systeme beginnen bei ca. 23 899 € und traditionelle industrielle Drucker sind ab ca. 100 000 € erhältlich. | Billigdrucker und 3D-Drucker-Kits beginnen bei wenigen 100 Euro. Desktop-3D-Drucker im mittleren Preisbereich mit höherer Qualität gibt es ab ca. 2000 € und industrielle Systeme sind ab ca. 15 000 € erhältlich. | Ab 200 000 USD |
Materialien | Verschiedene Kunstharze (Duroplaste); Standard-Kunstharze, technische Kunstharze (ABS-ähnlich, PP-ähnlich, flexibel, wärmebeständig), Gusskunstharze, biokompatible Kunstharze (zahnmedizinische und medizinische Anwendungen) Pures Silikon und Keramik. | Technische Thermoplaste (einschließlich biokompatibler Materialien). PA 11, PA 12, glas- oder carbonfaserverstärkte Nylon-Verbundstoffe, Polypropylen, TPU (Elastomer). | Standardthermoplaste wie ABS, PLA und deren Mischungen. | Edelstahl, Werkzeugstahl, Titan, Cobalt-Chrom-Legierung, Aluminium |
Ideale Anwendungen | Anatomische Modelle (biokompatibel), chirurgische Instrumente (biokompatibel), Medizinprodukte (biokompatibel), dentale Anwendungen (biokompatibel), Rapid Prototyping, Rapid Tooling, Fertigungshilfsmittel und Endverbrauchsteile. | Anatomische Modelle (biokompatibel), chirurgische Instrumente (biokompatibel), Medizinprodukte (biokompatibel), Orthesen und Prothesen, Rapid Prototyping, Rapid Tooling, Fertigungshilfsmittel und Endverbrauchsteile. | Einfache Konzeptnachweismodelle. Günstige Prototypen einfacher Teile. | Stabile haltbare Teile mit komplexen Geometrien, Implantate, Zahnersatz, medizinische und orthopädische Komponenten aus Metall. |
Materialien für medizinischen 3D-Druck
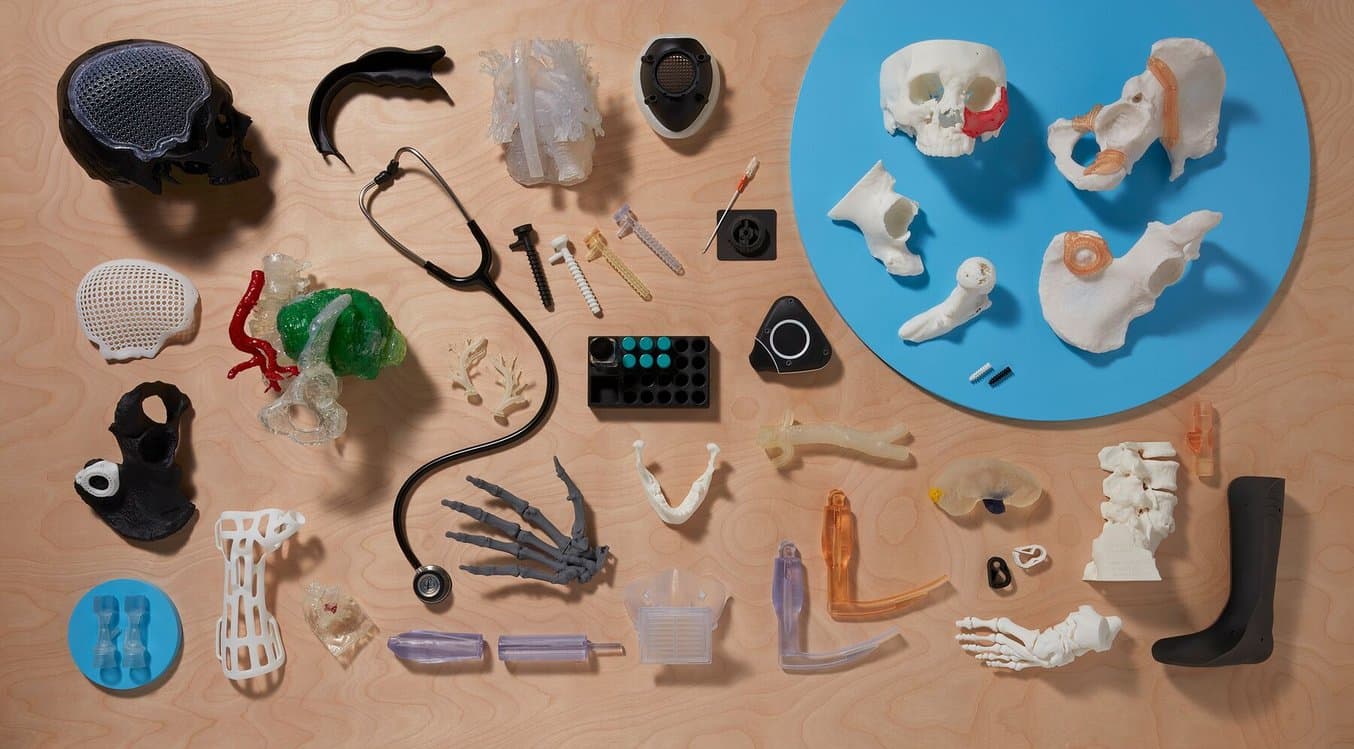
Formlabs' Materialbibliothek umfasst Kunstharze für den SLA-Druck und Pulver für den SLS-Druck, die für eine Vielzahl medizinischer Anwendungen optimiert sind.
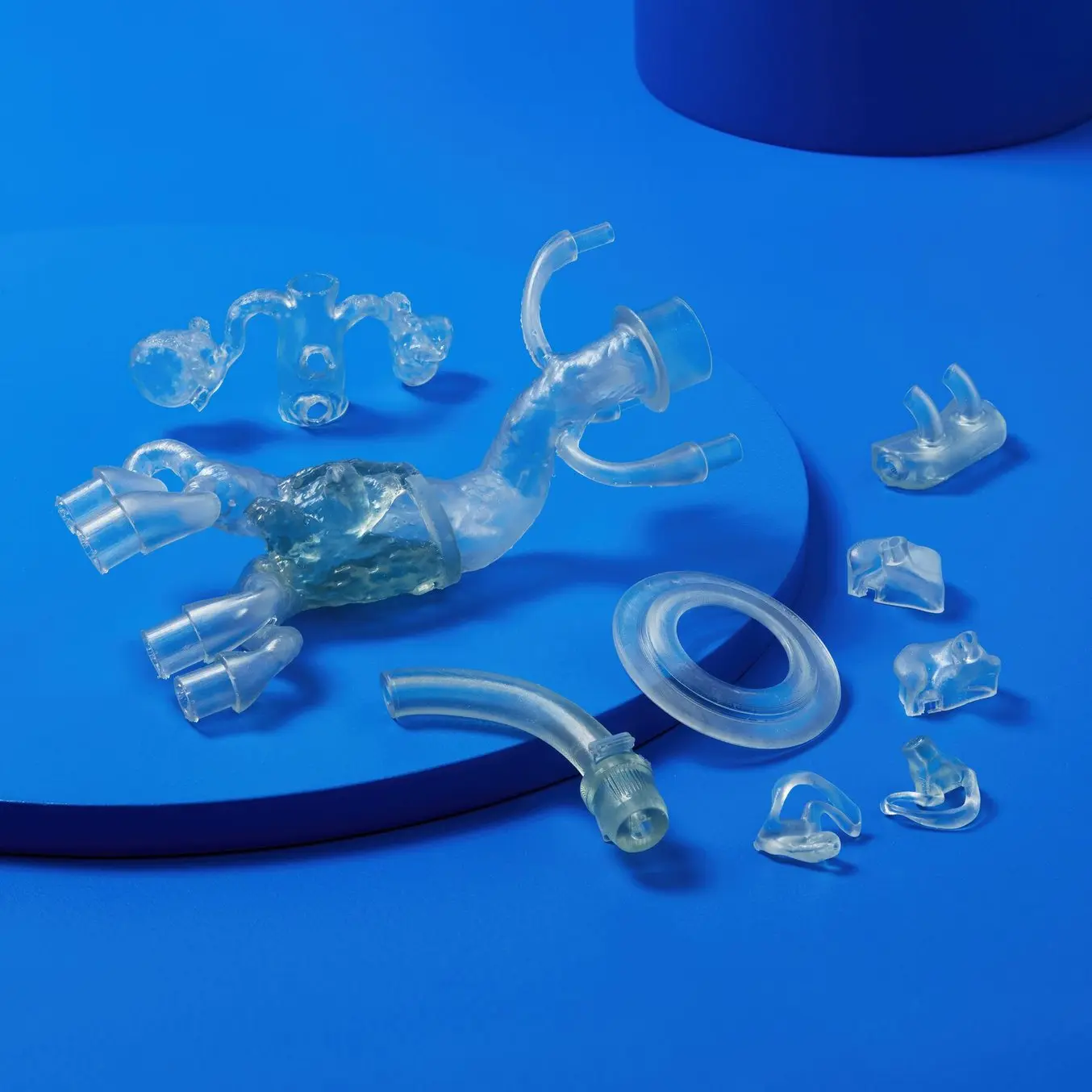
Meister der Materialien beim 3D-Druck von Medizinprodukten
In diesem Webinar stellt Ihnen Shiden Yohannes, Medical Engineer bei Formlabs, die verschiedenen für den 3D-Druck verfügbaren Materialien und ihre spezifischen Eigenschaften vor, damit Sie für Ihre individuellen Anforderungen eine fundierte Wahl treffen können.
Kunstharze für SLA
SLA unterstützt eine große Bandbreite an Anwendungsbereichen, einschließlich Maschinenbau, Fertigung und Gesundheitswesen. Für den SLA-Druck wurden Kunstharze mit spezifischen Materialeigenschaften entwickelt, beispielsweise elastische, robuste und biokompatible Optionen.
Für das Gesundheitswesen bieten die BioMed-Kunstharze von Formlabs Materialien in medizinischer Qualität für eine breite Palette an Anwendungen, bei denen Leistung und Biokompatibilität entscheidend sind. Die Materialien der BioMed-Familie werden in unserer nach ISO 13485 zertifizierten Einrichtung hergestellt. Sie sind mit den gängigen Desinfektions- und Sterilisierungsmethoden kompatibel.
Die Auswahl des passenden Kunstharzes hängt von der Verwendung, dem mechanischen Anforderungen an das Material und dem Anwendungsfall ab. Die BioMed-Kunstharze von Formlabs umfassen sowohl steife als auch elastische Optionen, einschließlich einiger Kunstharze für langzeitigen Hautkontakt oder Schleimhautkontakt.
Darüber hinaus wurde eine ganze Palette von Materialien speziell für die Anforderungen der zahnmedizinischen Fachwelt entwickelt. Das beinhaltet unter anderem das Kunstharz Premium Teeth Resin für den direkten 3D-Druck von Prothesenzähnen und Dental LT Comfort Resin für Okklusionsschienen. Einen vollständigen Materialkatalog und Informationen über die mehr als 17 Anwendungen für die zahnmedizinischen Kunstharze von Formlabs finden Sie bei Formlabs Dental.
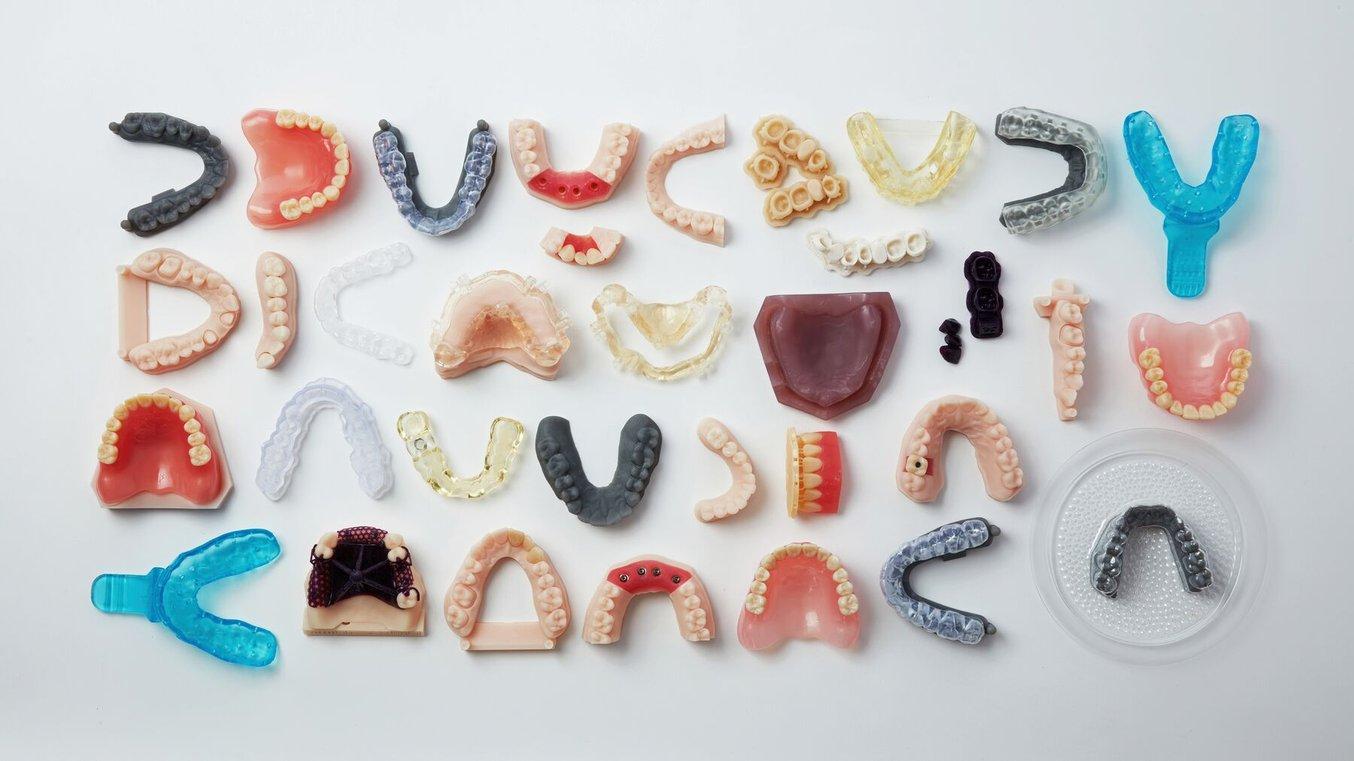
Die speziell für die Dentalbranche formulierten Formlabs-Kunstharze sind für den Druck von über 17 dentalen Anwendungen geeignet.
Eine Diversifizierung der medizinischen Kunstharze hilft medizinischen Fachleuten bei einer Vielzahl wichtiger Aufgaben wie der Erstellung von Medizinprodukten, der Operationsplanung, der Entwicklung individueller Implantate sowie bei Forschungsarbeiten. Die BioMed-Kunstharze bieten der medizinischen Fachwelt eine Reihe von Materialoptionen und dehnen die Möglichkeiten des 3D-Drucks weiter aus. In der untenstehenden Tabelle sind die Eigenschaften und Anwendungen der BioMed-Kunstharze von Formlabs gegenübergestellt.
Material | Beschreibung | Anwendungen |
---|---|---|
BioMed White Resin | Starr und opak weiß. Zugelassen für langzeitigen Hautkontakt (> 30 Tage) und kurzzeitigen Kontakt mit Knochen, Gewebe, Dentin oder Schleimhäuten (< 24 Std.). | Medizinprodukte für die Endverwendung und deren Komponenten, patientenspezifische Modelle und Formen zur Implantatsgrößenbestimmung, Schnitt- und Bohrschablonen, chirurgische Instrumente und Schablonen, biokompatible Formen, Halterungen und Vorrichtungen, Anatomiemodelle, die im OP eingesetzt werden können. |
BioMed Black Resin | Starr und mattschwarz. Zugelassen für langzeitigen Hautkontakt (> 30 Tage) und kurzzeitigen Kontakt mit Schleimhäuten (< 24 Std.). | Medizinprodukte und deren Komponenten, biokompatible Formen, Halterungen und Vorrichtungen, Endverbrauchsteile mit Patientenkontakt, Konsumgüter. |
BioMed Amber Resin | Starr und halbtransparent. Zugelassen für langzeitigen Hautkontakt (> 30 Tage) und kurzzeitigen Kontakt mit Knochen, Gewebe, Dentin oder Schleimhäuten (< 24 Std.). | Medizinprodukte für die Endverwendung, Modelle zur Implantatsgrößenbestimmung, Schnitt- und Bohrschablonen. |
BioMed Clear Resin | Starr und transparent. Zugelassen für langzeitigen Hautkontakt (> 30 Tage), Kontakt mit Atemgaswegen und Schleimhäuten (> 30 Std.) und kurzzeitigen Kontakt mit Knochen, Gewebe oder Dentin (< 24 Std.). | Produkte für die Endverwendung, auch für die Atemgaswege, biokompatible Prototypen, Formen, Halterungen und Vorrichtungen, Modelle zur Visualisierung und Implantatsgrößenbestimmung, Vorrichtungen für Zellkulturen und Bioprozesse. |
BioMed Durable Resin | Schlag-, bruch- und abriebfest. Transparent. Zugelassen für langzeitigen Hautkontakt (> 30 Tage), Schleimhautkontakt (> 30 Std.) und kurzzeitigen Kontakt mit Knochen, Gewebe oder Dentin (< 24 Std.). | Patientenspezifische Instrumente, Einweginstrumente, Produkte und Komponenten für die Endverwendung, die Biokompatibilität und Schlagfestigkeit erfordern. |
BioMed Elastic 50A Resin | Weichsilikonähnlich. Lichtdurchlässig. Zugelassen für langzeitigen Hautkontakt (> 30 Tage) und kurzzeitigen Kontakt mit Schleimhäuten (< 24 Std.). | Komfortable Medizinprodukte für langzeitigen Hautkontakt, biokompatible Weichgewebemodelle, die im OP als Referenz dienen können. |
BioMed Flex 80A Resin | Hartgummiähnlich. Lichtdurchlässig. Zugelassen für langzeitigen Hautkontakt (> 30 Tage) und kurzzeitigen Kontakt mit Schleimhäuten (< 24 Std.). | Flexible biokompatible Medizinprodukte und deren Komponenten, Medizinprodukte für kurzzeitigen Schleimhautkontakt, feste Gewebemodelle zur Nutzung im OP. |
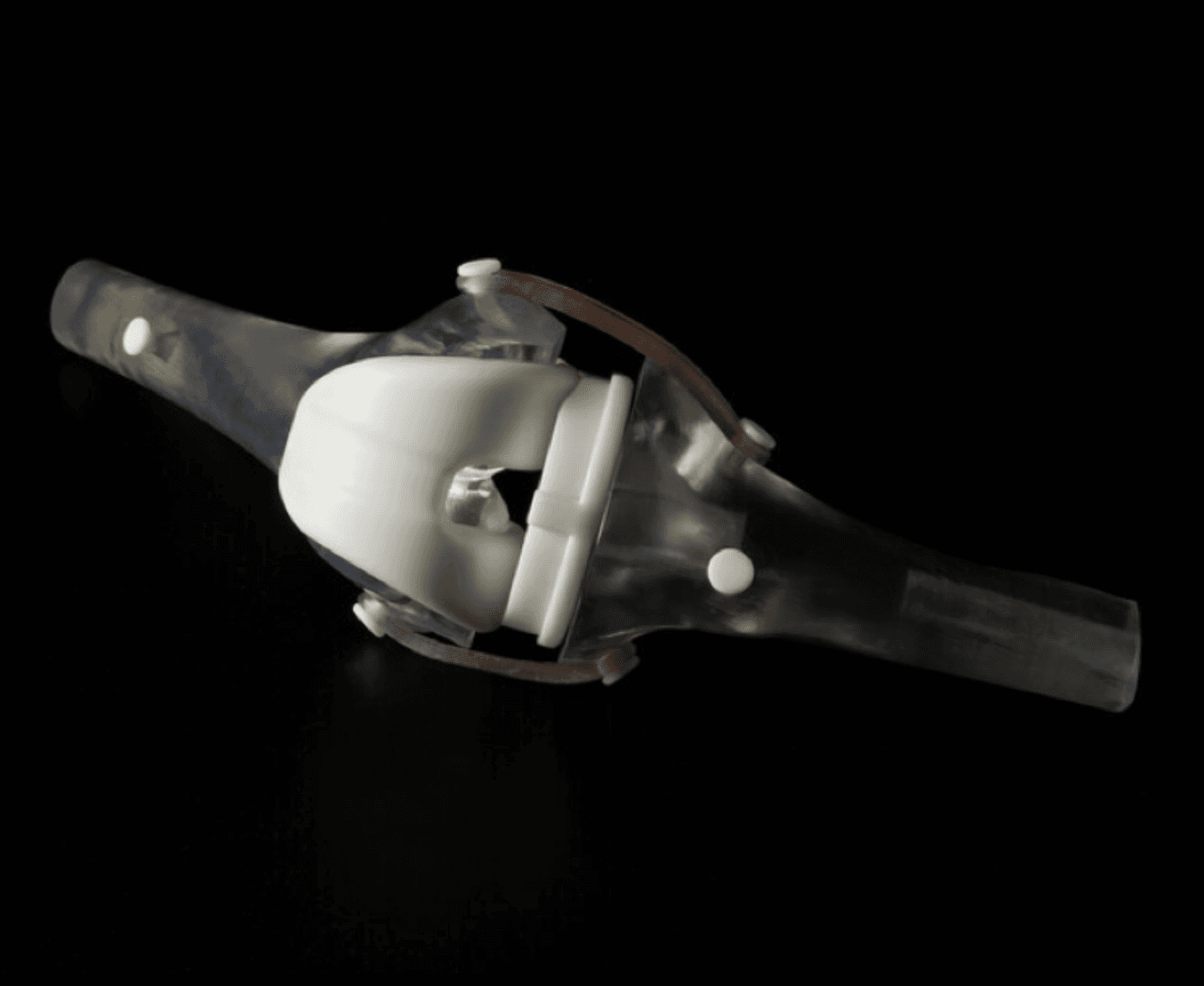
Erstellen von Knochensimulationsmodellen für das Schneiden und Bohren
3D-gedruckte Knochensimulationsmodelle revolutionieren die medizinische Ausbildung, die Operationsplanung, die Forschung und die Entwicklung von Medizinprodukten. In diesem Anwendungsleitfaden erläutern wir die Materialoptionen für die Knochensimulation mit SLA-3D-Druck (Stereolithographie) und den gesamten Fertigungsprozess für knochenähnliche anatomische Modelle zum Schneiden und Bohren.
SLS-Pulver
SLS-Pulver können biokompatibel, hautverträglich und sterilisierbar sein, und die Designs können filigrane Details und dünne Wände beinhalten. Dank dieser Eigenschaften eignen sie sich ideal für Anwendungen in der Gesundheitsbranche, wie etwa Medizinprodukte, Prototypen, Prothesen, chirurgische Instrumente und Orthesen.
Das am häufigsten für SLS eingesetzte Material ist Nylon, ein beliebter technischer Thermoplast mit exzellenten mechanischen Eigenschaften. Nylon ist leicht, stark sowie flexibel widersteht Stößen, Chemikalien, Hitze, UV-Licht, Wasser und Schmutz. 3D-gedruckte Nylonteile können ebenfalls biokompatibel und nicht-sensibilisierend sein und lassen sich daher in vielen Situationen sicher tragen und verwenden.
Nylon 12 Powder vereint Festigkeit und Detailgenauigkeit bei einer Zugfestigkeit von 50 MPa. Es eignet sich für komplexe Baugruppen und robuste Teile mit hoher Umweltbeständigkeit und ist damit perfekt für hochleistungsfähige Prototypen, Kleinserienfertigung sowie permanente Halterungen, Vorrichtungen und Werkzeug. Teile aus Nylon 12 Powder sind biokompatibel und sterilisierbar, was sie ideal für medizinische Anwendungen wie chirurgische Bohrschablonen macht.
Nylon 11 Powder ist ein ideales Material für feste Orthesen mit hoher Duktilität und langfristiger Stabilität, beispielsweise Einlegesohlen. Erfahren Sie in dieser Leistungsanalyse mehr über die Haltbarkeit dieses Materials.
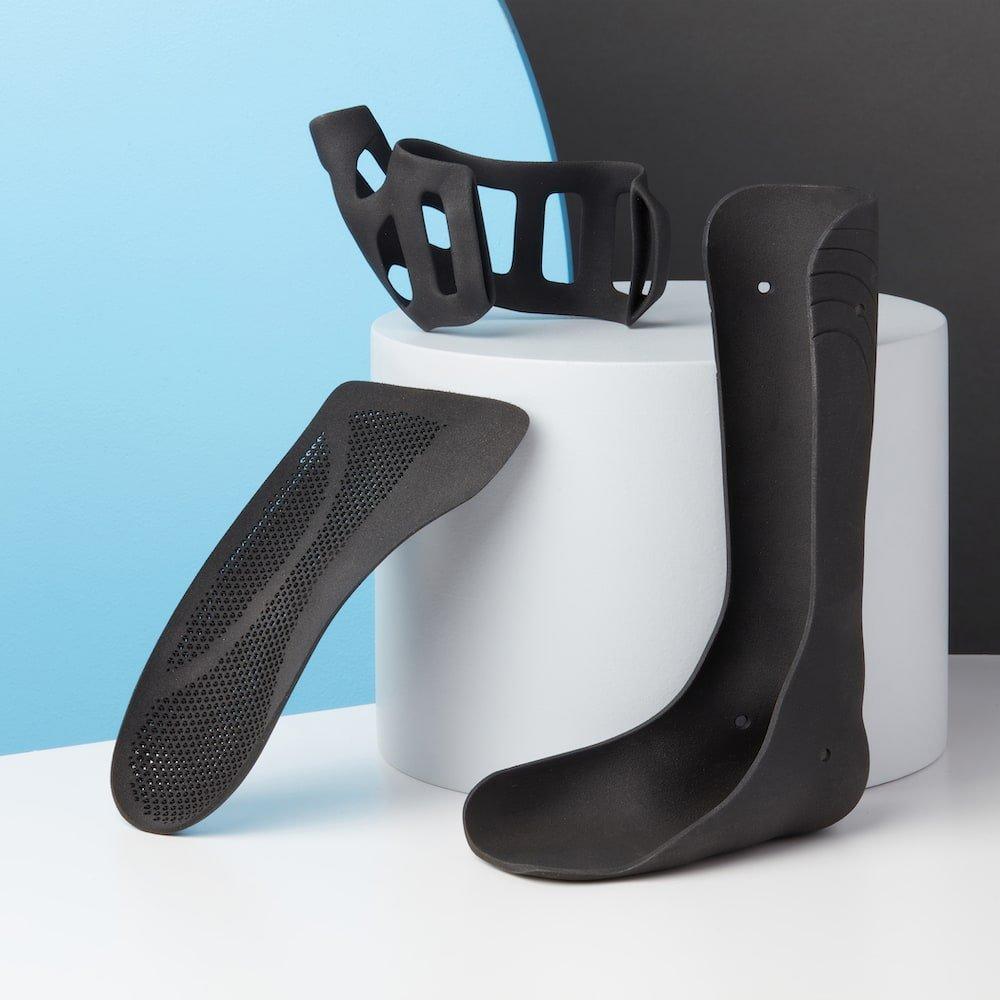
3D-gedruckte Orthesen aus Nylon 11 Powder.
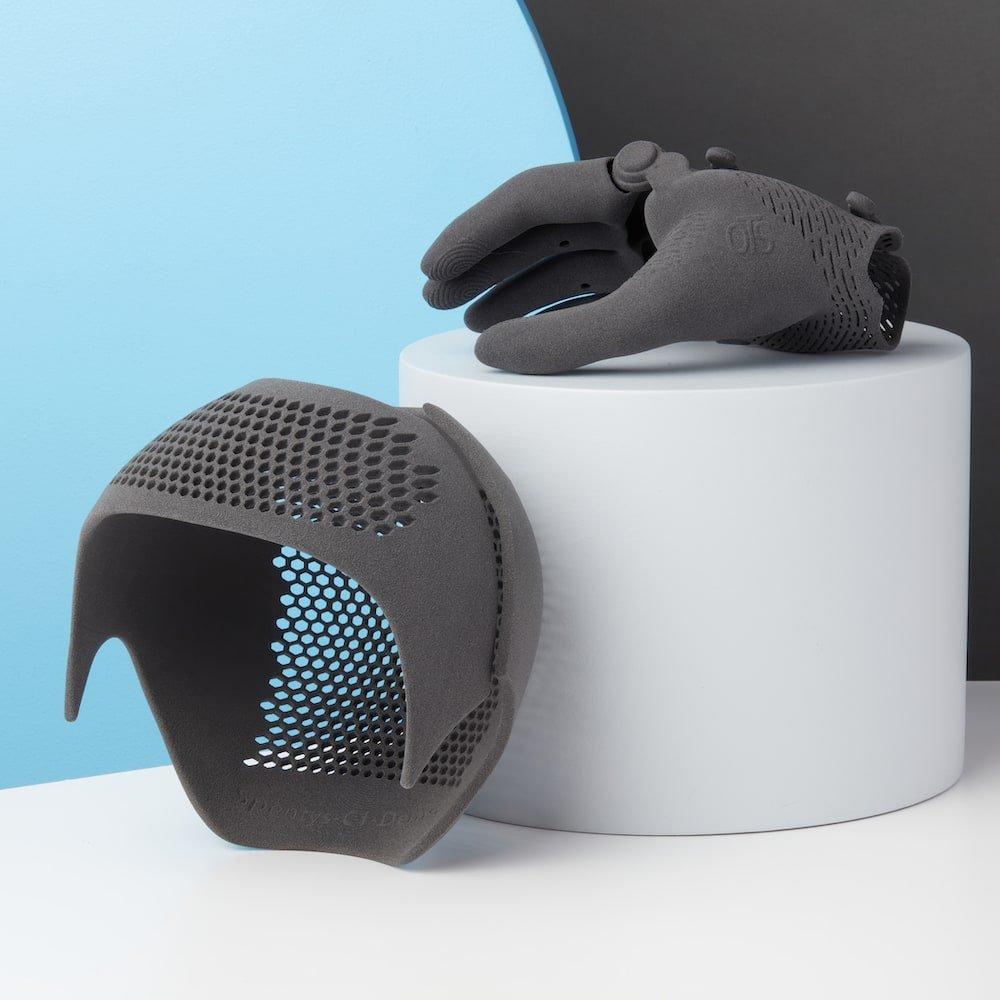
Eine Schädel-Orthese und ein Prototyp einer prothetischen Hand, 3D-gedruckt aus TPU 90A Powder.
Nutzen Sie Polypropylene Powder für die Produktion funktionaler Prototypen und robuster Endverbrauchsteile. Dank seiner hohen Duktilität lässt es sich wiederholt biegen, ohne an Langlebigkeit einzubüßen. Teile aus Polypropylene Powder sind chemisch beständig, verschweißbar und wasserdicht, weshalb sie sich ideal für Orthesen, Prothesen, Halterungen, Vorrichtungen und Werkzeuge eignen.
TPU 90A Powder ist ein flexibles Elastomer, das die hohe Reißfestigkeit und Bruchdehnung von Gummimaterialien mit der Gestaltungsfreiheit und Widerstandsfähigkeit des SLS-3D-Drucks vereint. TPU oder thermoplastisches Polyurethan ist ein gängiger elastomerischer Thermoplast. In der Orthetik wird dieses hautverträgliche Material häufig für Prototypen von Medizinprodukten sowie für Medizinprodukte für die Endverwendung und deren Komponenten, für orthetische Polsterungen und Prothesenauskleidungen, Schienen, Schädel-Orthesen und Sporteinlagen oder orthopädische Einlagen verwendet.
Die untenstehende Tabelle stellt einige der Materialeigenschaften und Anwendungsbereiche für die SLS-Pulver von Formlabs gegenüber.
Material | Beschreibung | Anwendungen |
---|---|---|
Nylon 12 Powder | Hohe Zugfestigkeit und Haltbarkeit, biokompatibel, sterilisierbar. | Medizinprodukte für die Endverwendung und deren Komponenten, patientenspezifische Modelle und Formen zur Implantatsgrößenbestimmung, Schnitt- und Bohrschablonen, chirurgische Instrumente und Schablonen, biokompatible Formen, Halterungen und Vorrichtungen, Anatomiemodelle, die im OP eingesetzt werden können. |
Nylon 11 Powder | Hochgradig duktil und robust. Flexibler, weniger spröde und besser für den Druck dünner Wände geeignet als Nylon 12 Powder. Biokompatibel, sterilisierbar. | Orthesen und Prothesen, schlagfeste Prototypen, Medizinprodukte, Endverbrauchsteile. |
Polypropylene Powder | Duktil und robust, chemisch resistent, wasserdicht, verschweißbar. | Orthesen und Prothesen, wasserdichte Gehäuse und Behälter, starke und chemisch beständige Halterungen, Vorrichtungen und Werkzeuge. |
TPU 90A Powder | Zähes Elastomer, hautverträglich, beständig gegenüber Verformung, hohe Bruchdehnung und hervorragende Reißfestigkeit. | Sohlen, Schienen, Orthetik und Prothetik. Wearables und Komponenten mit weicher Haptik. Polsterung, Dämpfer und Greifer. |
Die Materialeigenschaften können je nach Design und Fertigungsverfahren variieren. Es liegt in der Verantwortung des Herstellers, die Eignung der Druckteile für ihren Verwendungszweck zu überprüfen.
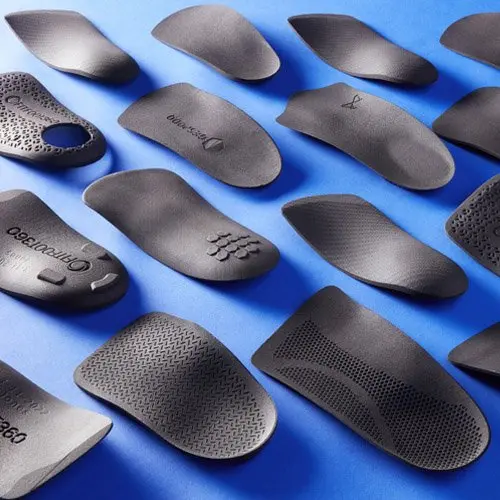
3D-Druck von Einlagenrohlingen
Erfahren Sie, wie Sie mit Formlabs' kompaktem, erschwinglichem SLS-Ecosystem starke, duktile Einlagenrohlinge herstellen, die mehr als 4 Millionen Biegeprüfungen standhalten. Dieser umfassende Leitfaden bringt Sie sofort auf Touren bei der Produktion von Einlagen mit dem Fuse 1+ 30W.
Tauchen Sie in die Welt des medizinischen 3D-Drucks ein
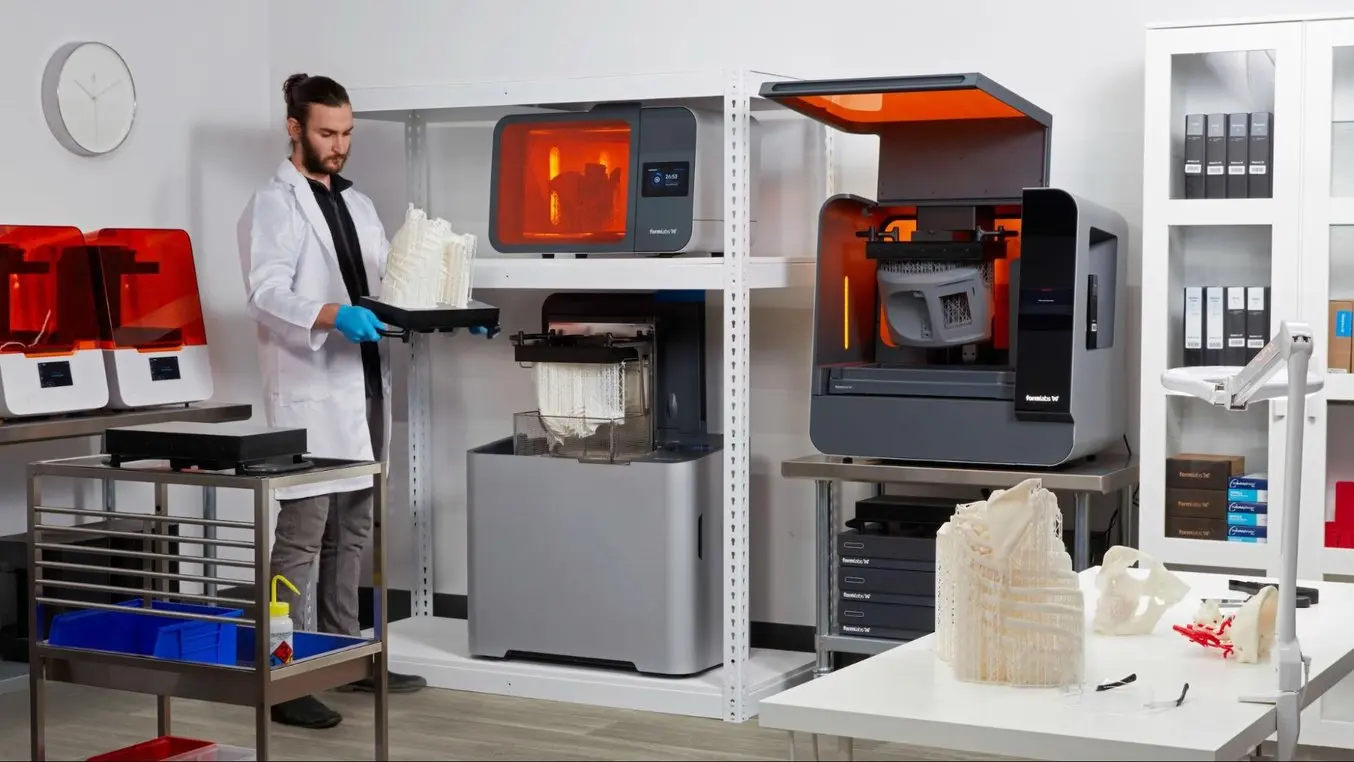
Präzise und erschwingliche 3D-Druckprozesse gewähren einer immer breiteren Masse Zugang zu dieser Technologie. So entdecken medizinische Fachkräfte neue klinische Lösungen und produzieren schnell maßgefertigte Vorrichtungen. Gleichermaßen finden Ärzteteams auf der ganzen Welt neue Behandlungswege. Die 3D-Drucktechnologien und -materialien werden immer besser und ebnen den Weg zu individualisierter Patientenbehandlung und wegweisenden medizinischen Anwendungen.
Jeder medizinischen Einrichtung sollten die neusten Hilfsmittel zur Verfügung stehen, um die Versorgung zu verbessern und höchsten Patientenkomfort zu gewährleisten. Steigen Sie jetzt ein oder erweitern Sie Ihre Eigenfertigung mit Formlabs, einem bewährten und innovativen Partner für den 3D-Druck im Gesundheitswesen.
Kontaktieren Sie unsere medizinischen Experten, um weitere Informationen dazu zu erhalten, wie ein betriebsinterner 3D-Drucker Ihren aktuellen Designprozess der Medizinprodukte sowie deren Fertigungsarbeitsabläufe ergänzt.