Leitfaden zum 3D-Druck von Medizinprodukten: von der Prototypenfertigung bis zur Kommerzialisierung
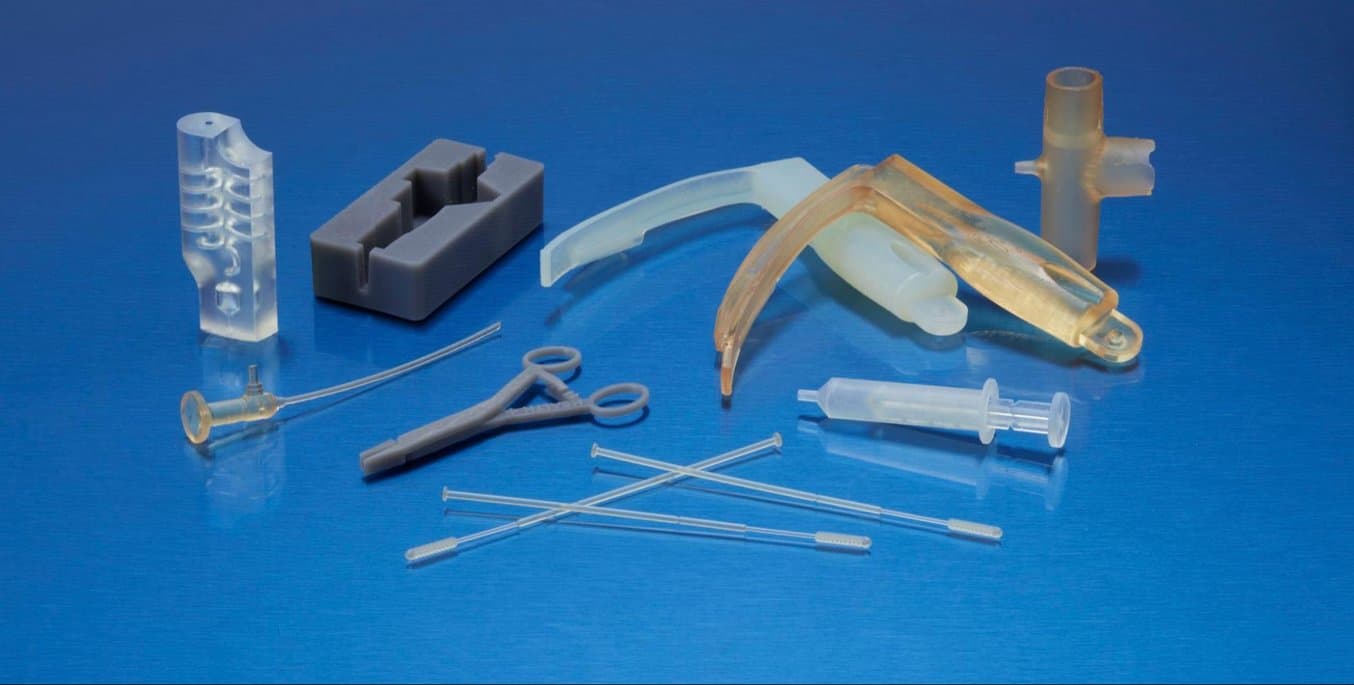
In der Medizintechnik hat der 3D-Druck seit Jahrzehnten innovative Lösungen hervorgebracht und die Entwicklung von Medizinprodukten wesentlich beeinflusst – von der F&E bis zur Produktion. Da 3D-Drucker erschwinglicher geworden sind und die Investitionen in Geräte und Materialien zunehmen, erhalten immer mehr Unternehmen Zugang zum 3D-Druck und brechen mit dem Status quo in der Gesundheitsbranche.
Durch betriebsinternen 3D-Druck senken Entwickler und Hersteller von Medizinprodukten sowohl die Kosten als auch die Markteinführungszeit. Diese Technologie ermöglicht eine flexiblere Produktentwicklung, neuartige Endanwendungsteile und die Erstellung personalisierter Medizinprodukte, wie sie mit herkömmlichen Werkzeugen unvorstellbar wäre. Wie seit Anfang 2020 gezeigt, ermöglicht die additive Fertigung bei medizinischem Notfallmaterial eine beispiellose Geschwindigkeit vom Konzept bis zur Massenproduktion.
In diesem umfassenden Leitfaden betrachten wir die verschiedenen Anwendungsbereiche des 3D-Drucks für Medizinprodukte, vergleichen die gängigsten 3D-Druckverfahren für die Medizinbranche und geben einen kurzen Überblick über den Zulassungsprozess für 3D-gedruckte Medizinprodukte (mit Links zu weiteren Ressourcen).
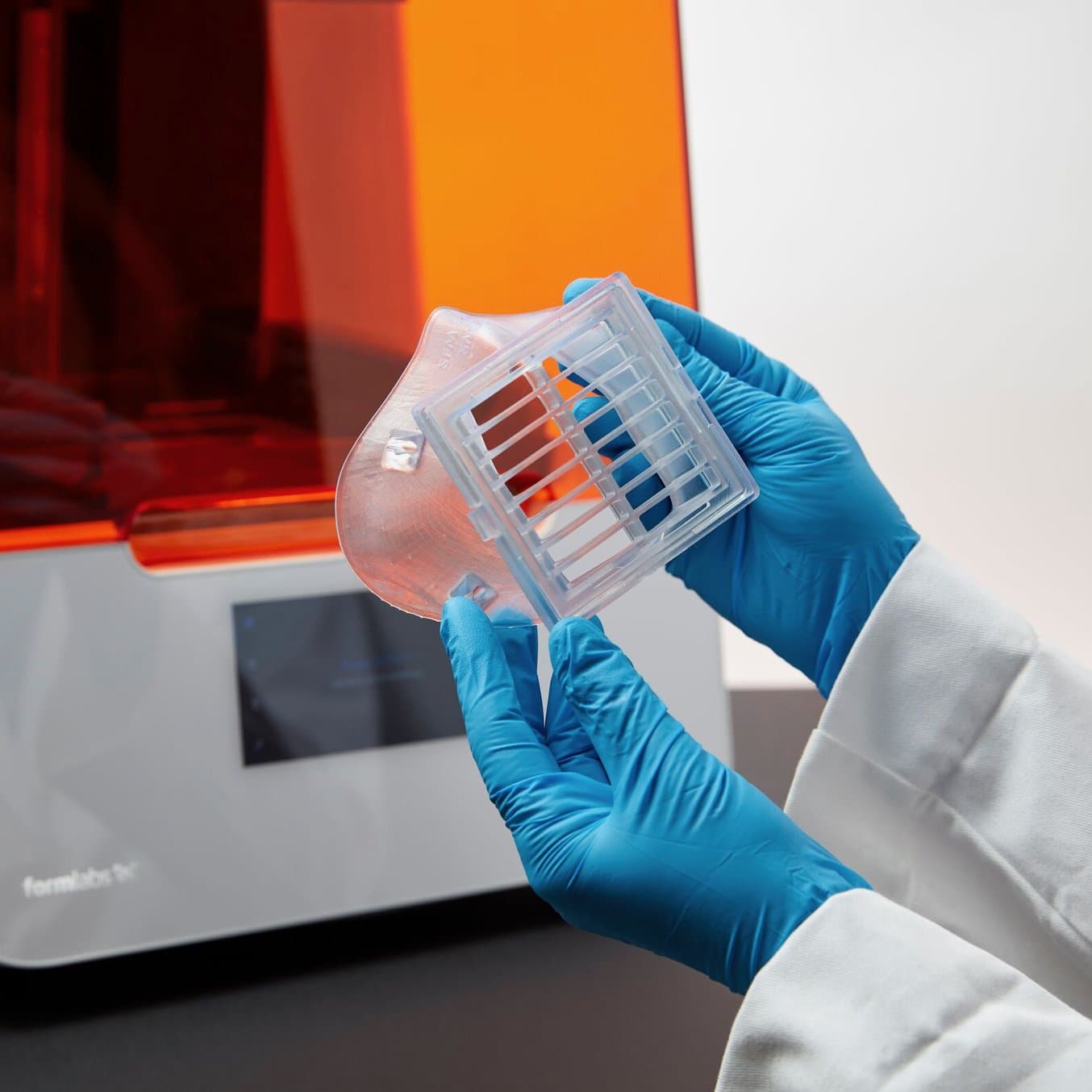
Mehr Erfolg beim 3D-Druck medizinischer Produkte
Dieser Bericht verdeutlicht, wie Formlabs Medical Unternehmen aus der Medizintechnik hilft, die digitale Fertigung im eigenen Haus zu etablieren. Lassen Sie sich von vier Unternehmen inspirieren, die derzeit mithilfe des 3D-Drucks bahnbrechende Medizinprodukte entwickeln.
3D-Druckanwendungen für Medizinprodukte
Die Kombination aus Geschwindigkeit, Erschwinglichkeit, Anpassbarkeit und Gestaltungsfreiheit des 3D-Drucks ermöglicht eine Vielzahl von Anwendungsfällen in der Medizinproduktbranche. Schauen wir uns die häufigsten praktischen Anwendungen und Beispiele an, um die Vielseitigkeit des 3D-Drucks kennenzulernen.
Rapid Prototyping von Medizinprodukten
Die Entwicklung innovativer Produkte geht Hand in Hand mit der Weiterentwicklung der Patientenversorgung und Verbesserungen im Gesundheitswesen. Die Prototypenfertigung ist ein Schlüsselelement dieses iterativen Prozesses, in dem Revisionen in einer kontrollierten Umgebung vorgenommen, implementiert und getestet werden.
Rapid Prototyping bezeichnet verschiedene Techniken zur schnellen Herstellung eines physischen Teils oder einer Baugruppe in Originalgröße unter Verwendung dreidimensionaler Daten für das computerunterstützte Entwerfen (CAD von Englisch computer-aided design). Der 3D-Druck ist eine natürliche Ergänzung für die Prototypenfertigung. Er bietet nahezu unbegrenzte Formfreiheit, erfordert keine Spezialwerkzeuge und kann Teile mit ähnlichen mechanischen Eigenschaften herstellen wie herkömmliche Fertigungsverfahren.
"Früher waren wir für Prototypen fast ausschließlich auf externe Dienstleister angewiesen. Heute haben wir vier Formlabs-Geräte im Einsatz, und die Vorteile liegen auf der Hand. Unsere 3D-Druckrate hat sich verdoppelt, die Kosten wurden um 70 Prozent gesenkt und die Detailgenauigkeit der Drucke ermöglicht eine klare Kommunikation der Entwürfe mit den orthopädischen Chirurgen."
Alex Drew, Mechanical Project Engineer, DJO Surgical
3D-Druck bietet Herstellern die Flexibilität, selbst für komplexeste Medizinprodukte funktionsfähige, optische und haptisch ähnliche Prototypen zu entwickeln. Neue Iterationen innerhalb weniger Stunden abgeschlossen und validiert werden, um festzustellen, ob es weiterer Anpassungen bedarf. Auch falls Eigenschaften wie Festigkeit, Flexibilität oder Hitzebeständigkeit wichtige Kriterien des Medizinprodukts sind, erlaubt der 3D-Druck die Entwicklung von Prototypen unter Verwendung vielseitiger Materialien.
Durch Tests eines funktionsfähigen Prototyps mit Validierungsprozessen aus der Praxis erhält der Hersteller Ergebnisse, die er für weitere Iterationen nutzen kann. Darüber hinaus können Prototypen aus dem 3D-Druck auch als Präsentationsmodelle dienen, falls Sie Investoren überzeugen oder zukünftige Kunden gewinnen wollen.
Die Benutzerfreundlichkeit und die niedrigen Kosten des betriebsinternen 3D-Drucks haben auch die Produktentwicklung revolutioniert. Über 85 % der 50 größten Hersteller von Medizinprodukten nutzen Formlabs' Technologie zur Herstellung von Prototypen, Fertigungshilfsmitteln oder Endprodukten. Aufgrund der überschaubaren Investitionsausgaben von unter 5000 € nutzen auch viele Start-ups und kleine Unternehmen die Vorteile der Technologie.
Zum Beispiel entwickelt das in Großbritannien ansässige Medizinprodukt-Designunternehmen Coalesce Product Development Geräte zur Arzneimittelverabreichung wie Inhalatoren und Injektoren. Das Unternehmen hatte aufgrund der hohen Anlaufkosten und der zeitaufwändigen herkömmlichen Fertigungsverfahren und -werkzeuge Probleme mit der Entwicklung komplexer Prototypen von Medizinprodukten.
Coalesce entschied sich schließlich für Stereolithografie-3D-Drucker (SLA), um betriebsintern Prototypen zu erstellen, zu testen und verschiedene Produkte in einer Vielzahl unterschiedlicher Formen und Größen zu entwickeln. Mithilfe des 3D-Drucks erstellte der Hersteller neue Prototypen in weniger als 24 Stunden zu 10–20-mal niedrigeren Kosten als beim Outsourcing. Neben den Prototypen druckt man dort auch Testhalterungen und -vorrichtungen in 3D, um die Tests der Inhalatoren zu beschleunigen.
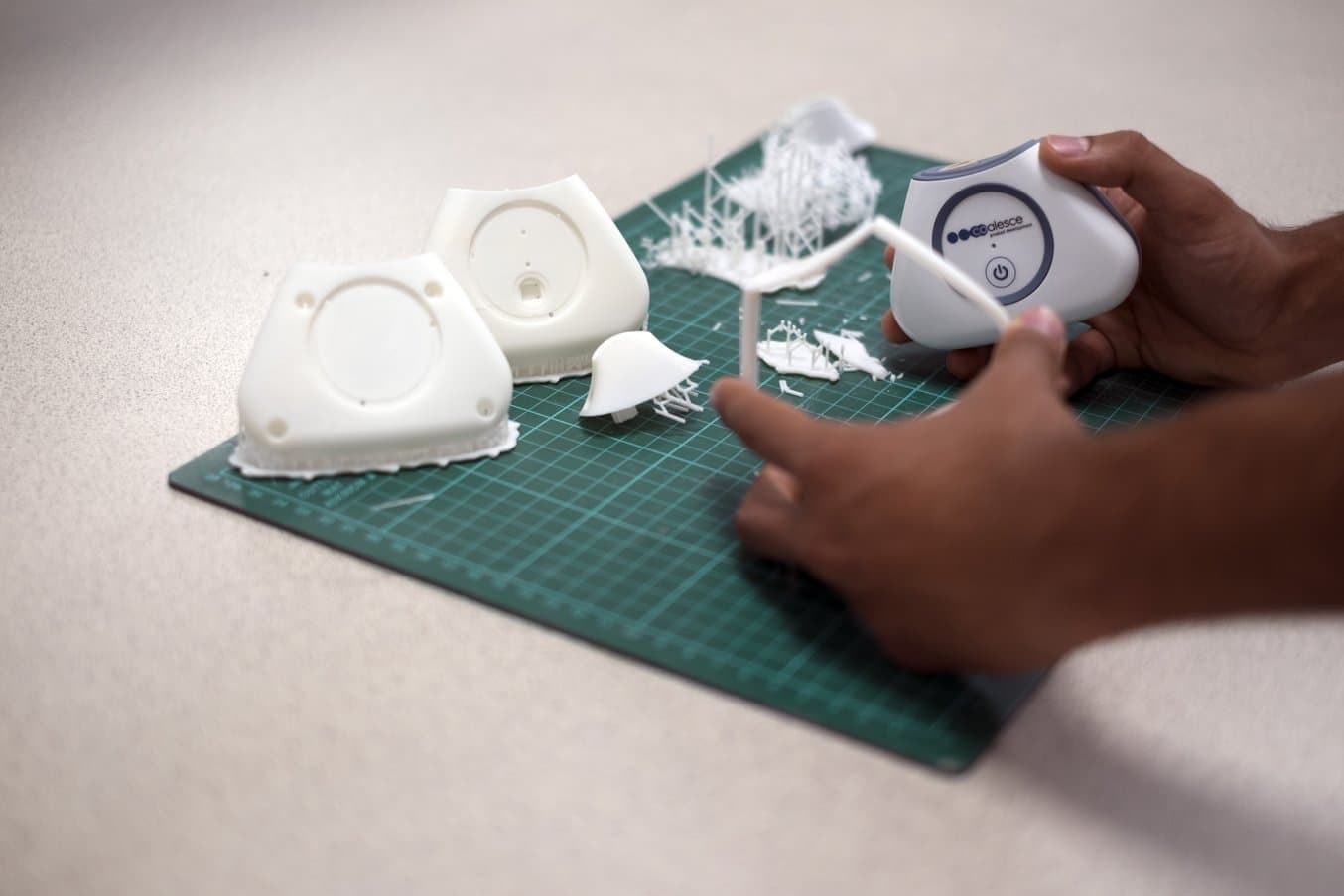
Das Medizinprodukt-Designunternehmen Coalesce produziert im 3D-Druck Prototypen für Geräte zur Arzneimittelverabreichung, beispielsweise für Inhalatoren.
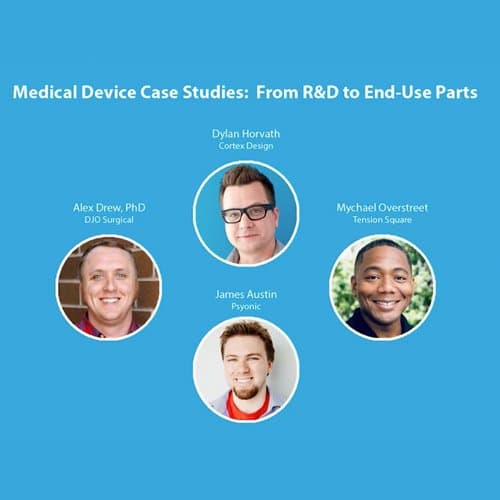
Medizinprodukt-Fallstudien: Von F&E bis zu Endverbrauchsteilen
In diesem Webinar spricht Gaurav Manchanda, Director of Medical Market Development bei Formlabs, mit Formlabs-Kunden aus dem Gesundheitswesen. Zu den Unternehmen zählen Start-ups, aber auch große Unternehmen mit einem Umsatz von mehr als 1 Mrd. US-Dollar wie Cortex Design, DJO Surgical, Psyonic und TensionSquare.
Herstellung patientenspezifischer Medizinprodukte
Die meisten herkömmlichen Fertigungsverfahren wie Spritzgießen oder Thermoformen erfordern teure Werkzeuge, daher sind sie ineffizient bei der Herstellung personalisierter oder maßgefertigter Teile. Der 3D-Druck löst diese Herausforderung auf zweierlei Art.
Rapid Tooling für traditionelle Fertigungsverfahren
Erstens erlaubt der 3D-Druck maßgefertigtes Rapid Tooling anhand von Formen, Mustern, Gussteilen und Matrizen für diverse herkömmliche Fertigungsprozesse wie Spritzguss, Thermoformen, Silikonformenbau, Umspritzen, Insert-Molding, Formpressen, Gießen usw.
Ein Beispiel für Vakuumformen ist die Herstellung von Alignern und Retainern, wobei die individuellen Patientenanatomiedaten durch intraorale oder durch Desktop-Scanner erfasst werden. Bei der Herstellung dieser Vorrichtungen wird eine Kunststoffplatte über ein maßgefertigtes Modell des jeweiligen Behandlungsschritts gelegt und durch Vakuumformen in Form gebracht. Da 3D-Drucker solche Modelle innerhalb weniger Stunden direkt aus den digitalen Dateien herstellen können, ist der 3D-Druck für diese zunehmend beliebteren kieferorthopädischen Vorrichtungen die erste Wahl.
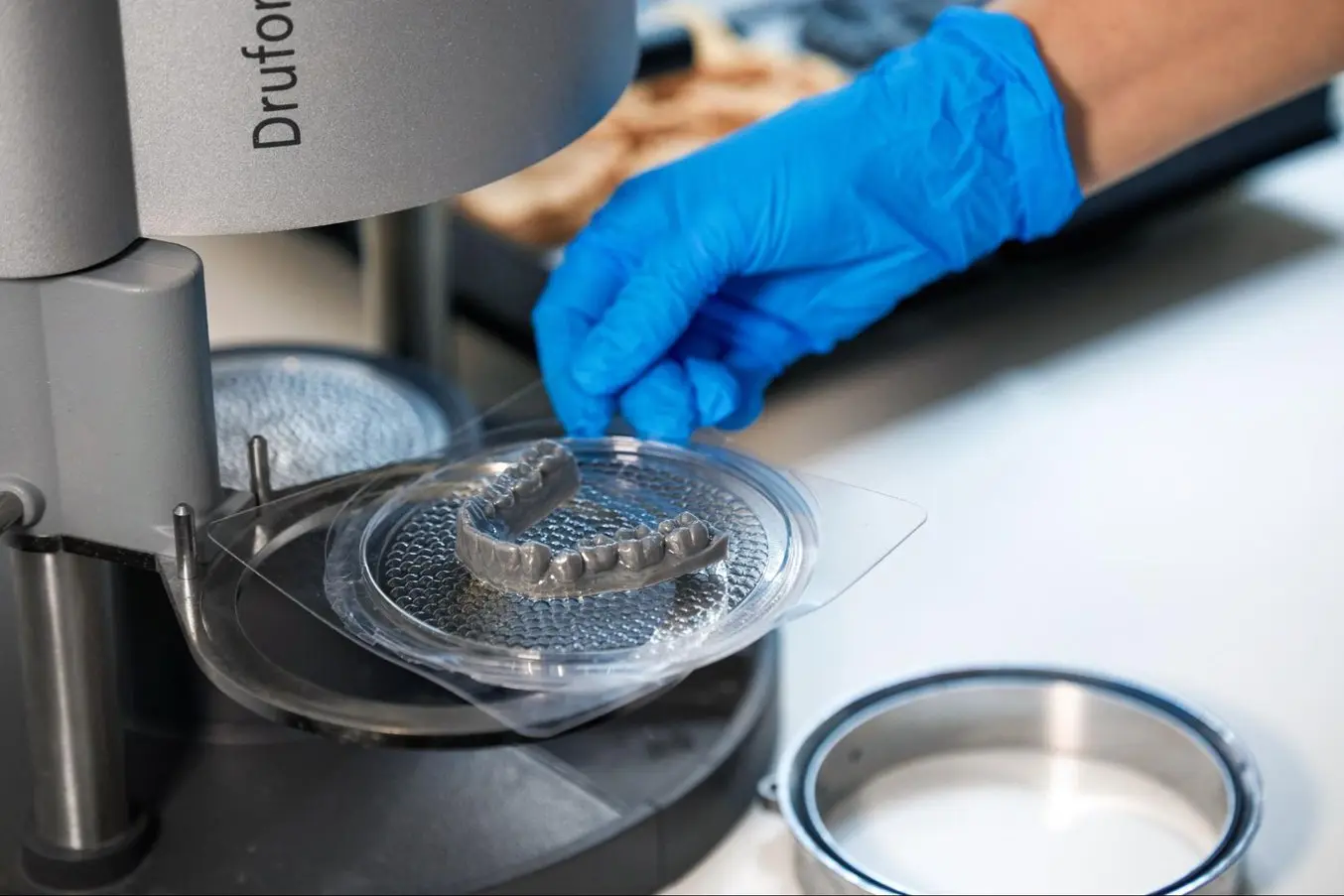
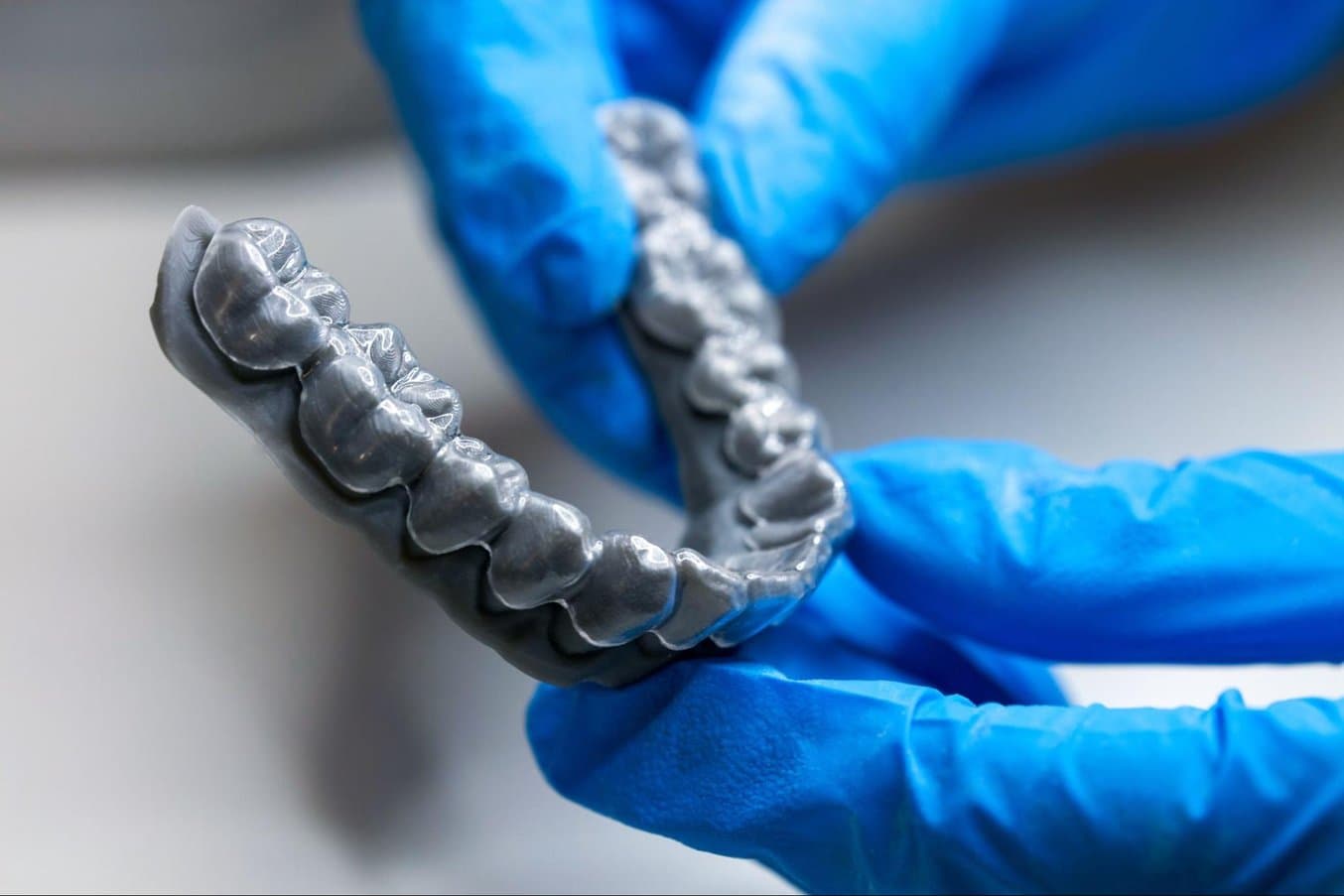
3D-Druck ist das Mittel der Wahl zur Herstellung von Modellen für die Vakuumformung transparenter Aligner und Retainer.
Ein weiteres Beispiel ist Cosm, ein Medizinproduktunternehmen, das eine unterstützende Behandlung für Patientinnen mit Beckenbodenerkrankungen entwickelt. Das Unternehmen verwendet 3D-gedruckte Formen für den Silikonformenbau, um für jede Patientin ein passgenaues Pessar herzustellen.
Durch 3D-Druck fertigt Cosm flexibel innerhalb von 24 Stunden erschwingliche, passgenaue Pessarformen.
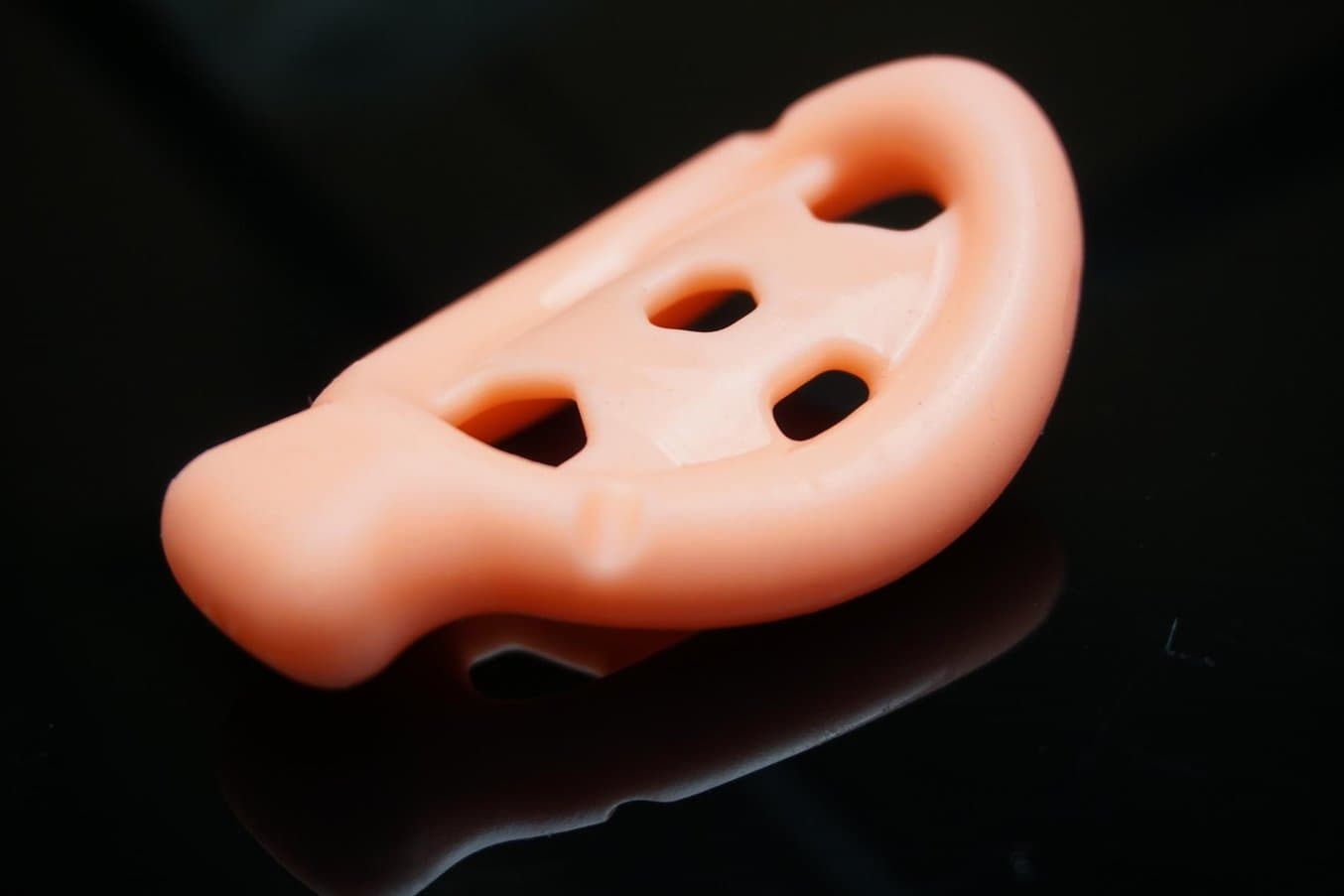
Cosm fertigt passgenaue Pessare mithilfe des Silikonformenbaus.
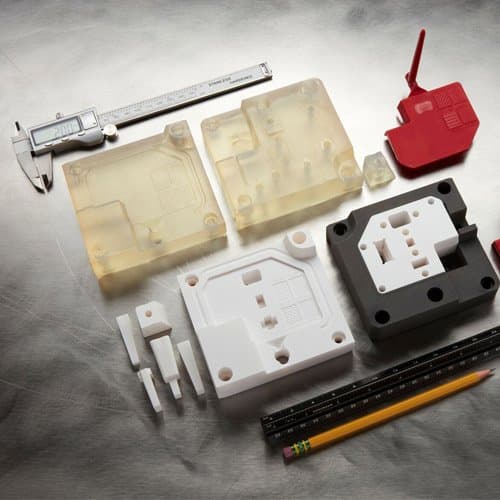
Formenbau durch 3D-Druck: Techniken für Prototyping und Produktion
Laden Sie unser Whitepaper über sechs Arten von (Guss-)Formen herunter, die sich mit einem betriebsinternen SLA-3D-Drucker herstellen lassen, für Spritzguss, Vakuumformen, Silikonformenbau usw.
Direkter 3D-Druck patientenspezifischer Medizinprodukte
Zweitens wird der 3D-Druck zunehmend auch zur Herstellung patientenspezifischer Medizinprodukte für Endverbraucher eingesetzt. Da der 3D-Druck keine Werkzeugbestückung erfordert, lassen sich Sonderanfertigungen und komplexe Designs rationell und kosteneffizient erstellen.
Besonders die Zahnmedizin ist Vorreiter beim medizinischen 3D-Druck. Bohrschablonen, Schienen, provisorischer und permanenter Zahnersatz sowie Zahnprothesen lassen sich direkt 3D-drucken.
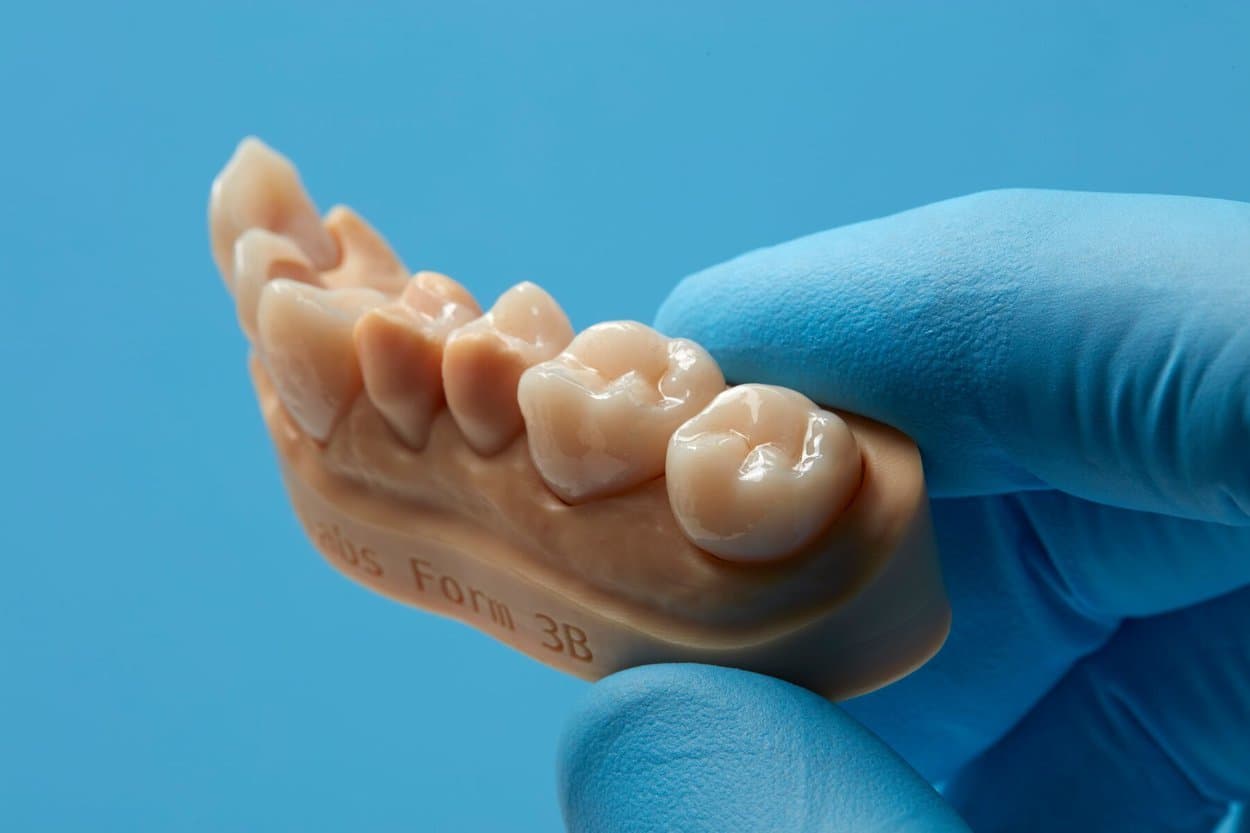
Permanente Kronen, hergestellt aus einem keramikgefüllten Kunstharzmaterial
Andere medizinische 3D-Druckanwendungen für Endverbraucher sind passgenaue Audiogeräte (wie Hörgeräte und Lärmschutz) sowie stabile und langlebige kundenspezifische Prothesen, Orthesen und darüber hinaus.
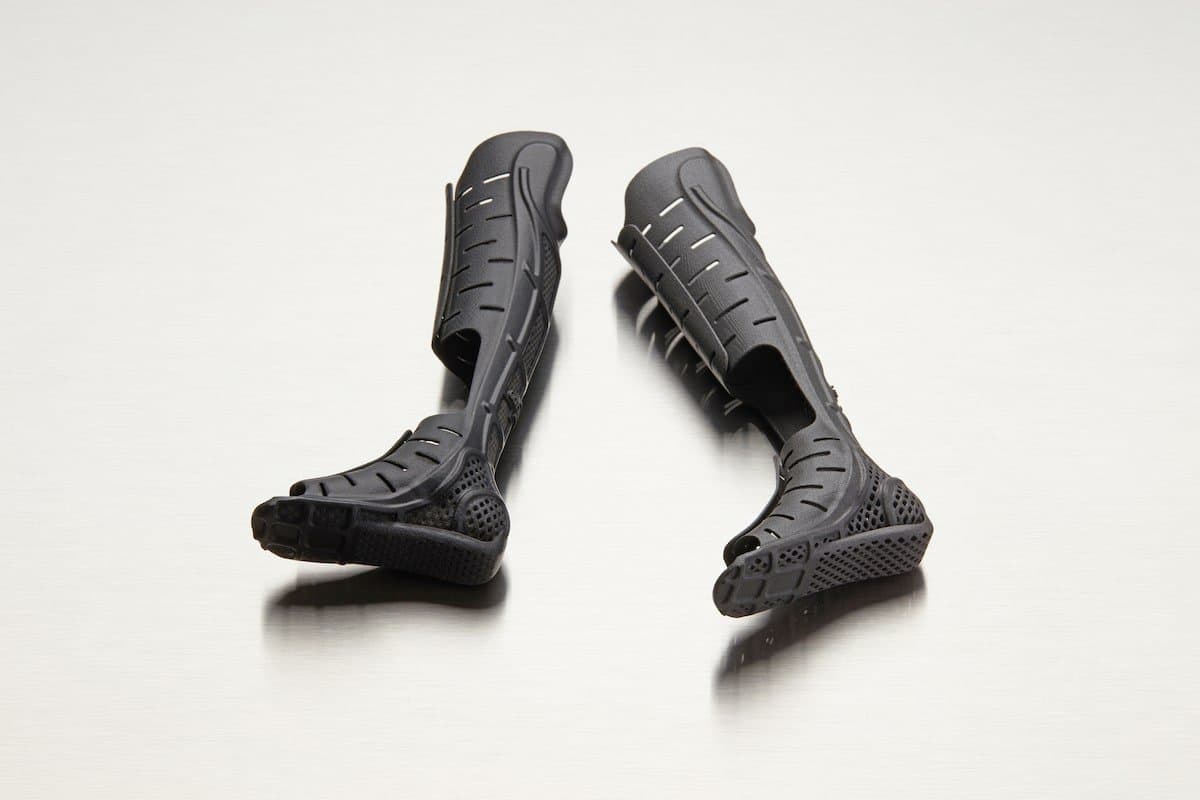
Mit 3D-Druck lassen sich haltbare, biokompatible und passgenaue Prothesen und Orthesen für Patienten erstellen – und das günstiger und schneller als je zuvor.
Das Unternehmen restor3d als Hersteller chirurgischer Instrumente konnte dank des 3D-Drucks die chirurgische Versorgung erheblich verbessern, indem es auf Implantate der Halswirbelsäule zugeschnittene verfahrensspezifische Instrumente im 3D-Druck herstellt. Durch den 3D-Druck erstellt man dort sterile, von Chirurgen entworfene Werkzeuge in einem äußerst agilen Entwicklungsprozess. Der Ansatz von restor3d senkt die Sterilisations-, Lager- und OP-Kosten für Krankenhäuser und chirurgische Kliniken. Die Nachfrage ist groß: Über 25 Formlabs-Drucker stellen rund um die Uhr Teile her.
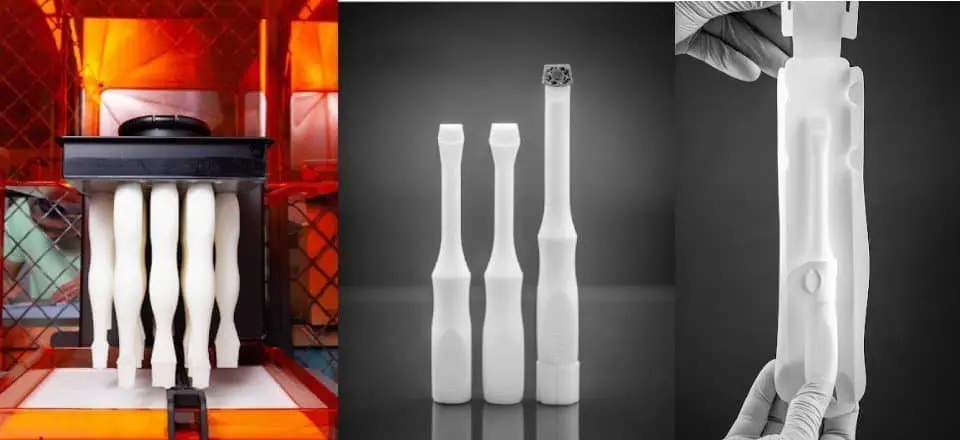
restor3d druckt prozedurspezifische Chirurgieinstrumente.
Herstellung von Medizinprodukten für die Endverwendung
Der 3D-Druck wird nicht nur für chirurgische Instrumente, sondern auch zur Herstellung von Medizinprodukten oder deren Komponenten immer beliebter, besonders bei komplexen Entwürfen, die mit herkömmlichen Prozessen nur ineffizient oder gar nicht möglich wären.
TensionSquare hat ein Gerät auf den Markt gebracht, das eine Dekompressionsnadel sicher an Ort und Stelle hält und gleichzeitig ein Knicken, Falten oder Lösen (was oft zu vermeidbaren Todesfällen führt) verhindert. Nach jahrelanger F&E druckt das Unternehmen jetzt Endverbrauchsteile auf einem SLS-3D-Drucker (selektives Lasersintern) des Typs Fuse 1. So verringert sich die Abhängigkeit von Dienstleistern und man produziert innerhalb von 24 Stunden pro Drucker mehr als 100 Teile. Das von einem Veteranen und Sanitäter gegründete Unternehmen beabsichtigt, pro Jahr Millionen Teile in seinen US-amerikanischen Produktionsstätten zu drucken.
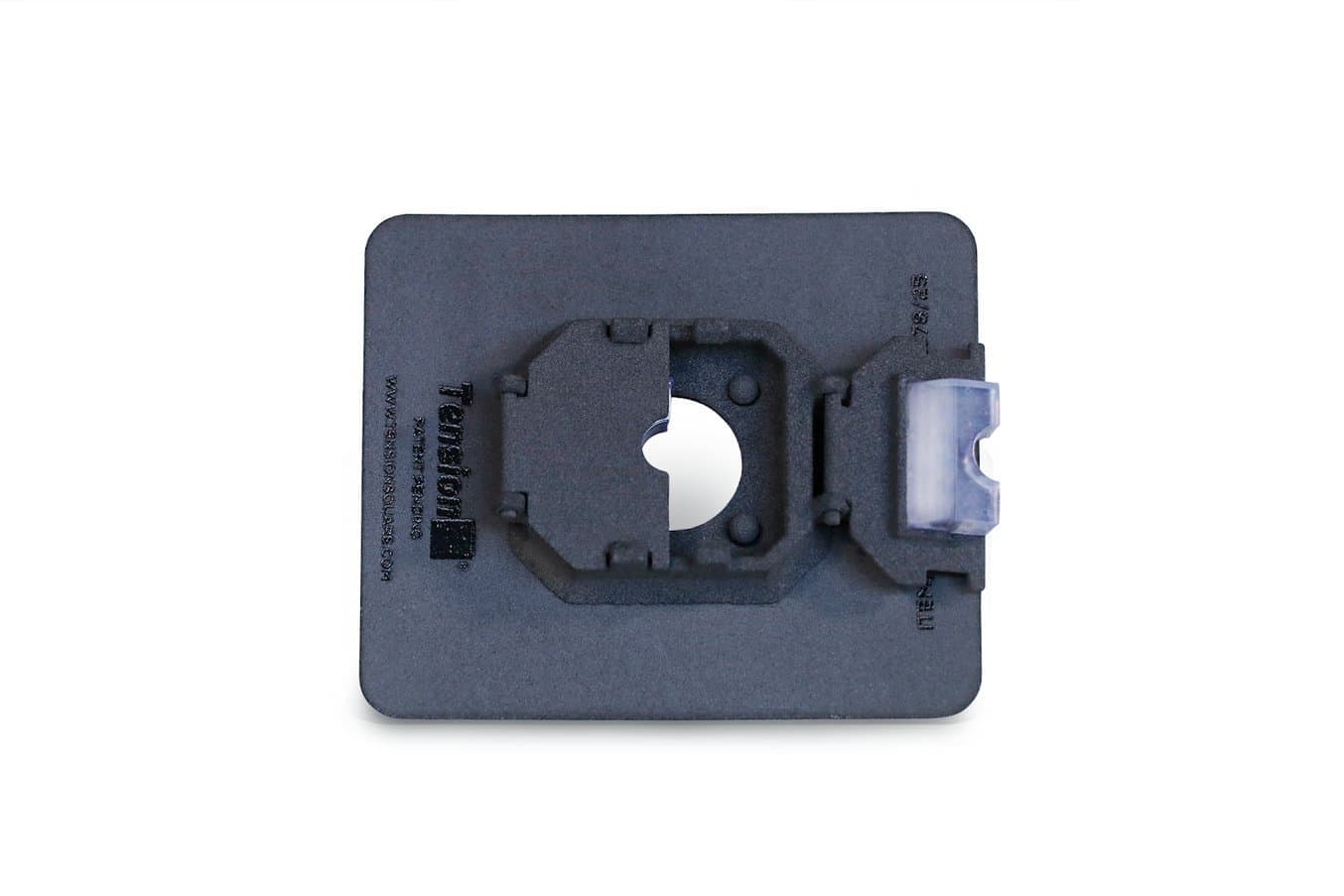
TensionSquare fertigt ein PTX-Dekompressionskatheter-Stabilisierungsgerät direkt im SLS-3D-Druck.
VO2 Master entwickelt einen tragbaren Stoffwechselanalysator, der benutzerfreundlicher und erschwinglicher ist als existierende Geräte. Nachdem das Unternehmen den 3D-Druck ausgiebig in der Prototypenerstellung eingesetzt hatte, wollte es auch das Gehäuse für das fertige Gerät drucken, um eine schnellere Markteinführung zu gewährleisten. Die Gehäuse werden auf SLA-3D-Druckern mit Tough 1500 Resin gedruckt, einem robusten Material, das in Festigkeit und Steifigkeit Polypropylen ähnelt. Die Gehäuse werden weiß lackiert, bevor sie auf der Maske befestigt werden, um die Oberflächenbeschaffenheit, die Farbgebung der Prägung und die Haltbarkeit zu verbessern.
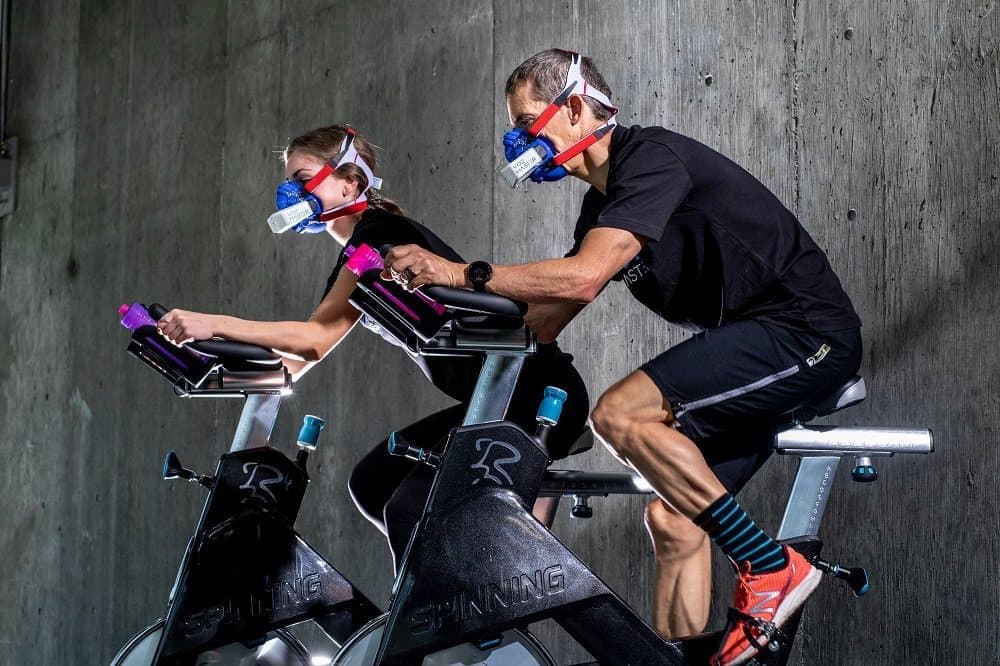
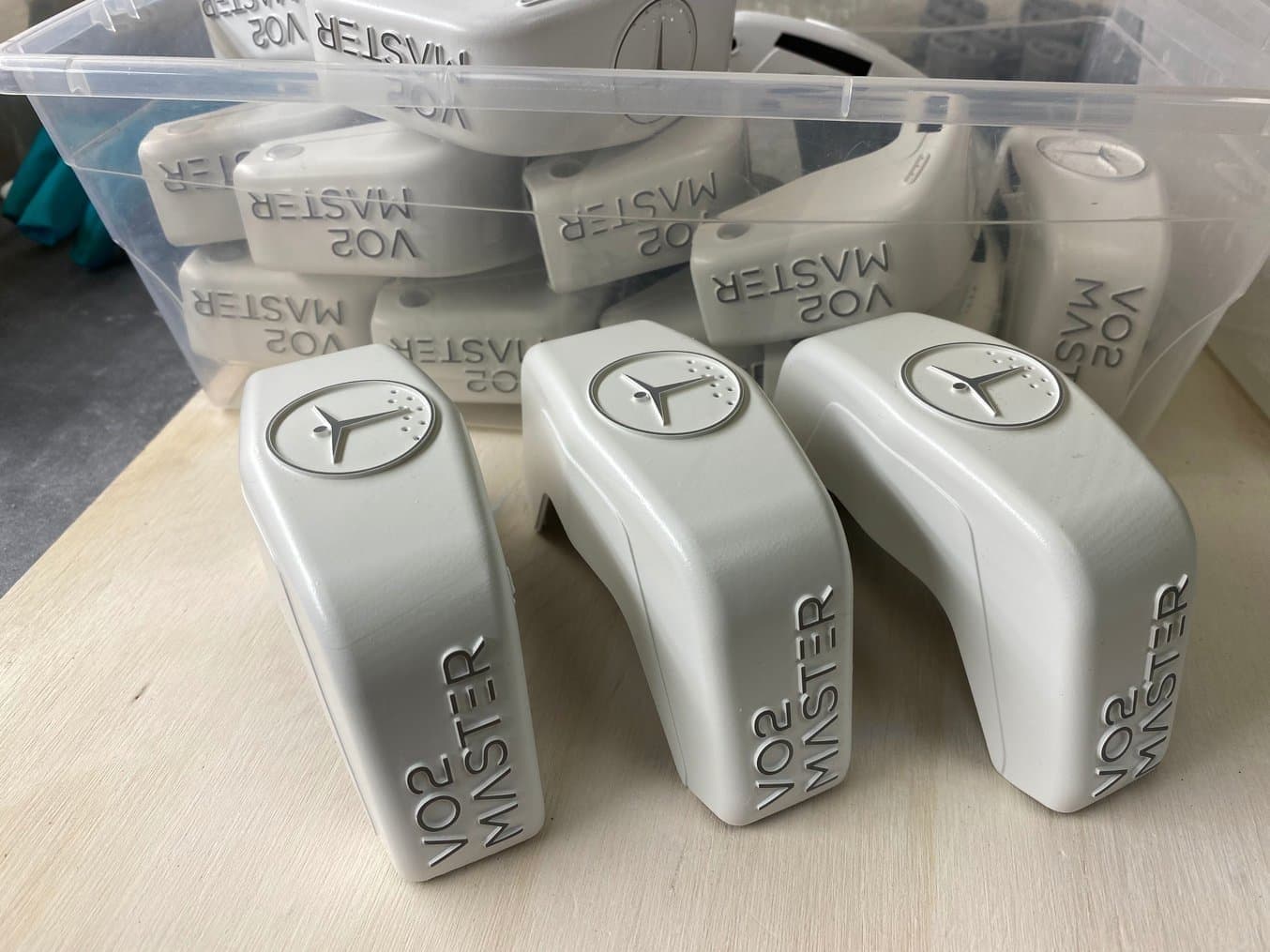
VO2 Master druckt das Gehäuse für seinen tragbaren Stoffwechselanalysator, um die Markteinführung zu beschleunigen.
Herstellung medizinischen Notfallmaterials
Die COVID-19-Pandemie forderte das Gesundheitswesen auf beispiellose Art und Weise, sodass viele Regierungen an außergewöhnlichen Stellen nach Ressourcen suchen mussten. Zur Deckung des riesigen Bedarfs an Notfallmaterial fertigten Automobilhersteller Atemschutzmasken und Modehäuser Schutzausrüstung, um die mit der Pandemie verbundenen Herausforderungen zu meistern.
Mit den explodierenden COVID-19-Fallzahlen stieg auch der Bedarf an Tests massiv an und es kam zu einem weltweiten Mangel an Nasenrachenabstrichtupfern, wie sie zur Entnahme von Proben für COVID-19-Tests benötigt werden. Als klar wurde, dass Nasenrachenabstrichtupfer für COVID-19-Tests sehr gefragt und nur extrem begrenzt verfügbar waren, arbeiteten USF Health, Northwell Health und Formlabs zusammen, um eine 3D-gedruckte Alternative zu entwickeln. Innerhalb einer Woche entwickelten die Teams gemeinsam den Prototyp eines Abstrichtupfers und testeten ihn in den Laboren von USF Health und Northwell Health. Innerhalb von zwei Tagen fertigten USF Health und Northwell Health mithilfe der 3D-Drucker von Formlabs sowie biokompatibler und autoklavierbarer Kunstharze erste Prototypen. Ganze 12 Tage nach der ersten Idee wurde das endgültige Design für den klinischen Einsatz freigegeben und die 3D-Datei den weltweiten Gesundheitssystemen zur Verfügung gestellt. Zeitgleich mit der Druckdatei erstellten die Teams für qualifizierte Nutzer im Gesundheitswesen einen detaillierten Arbeitsablauf mit Leitfäden zum Druck der Abstrichtupfer und zur Gewährleistung der Gesundheit und Sicherheit der Patienten.
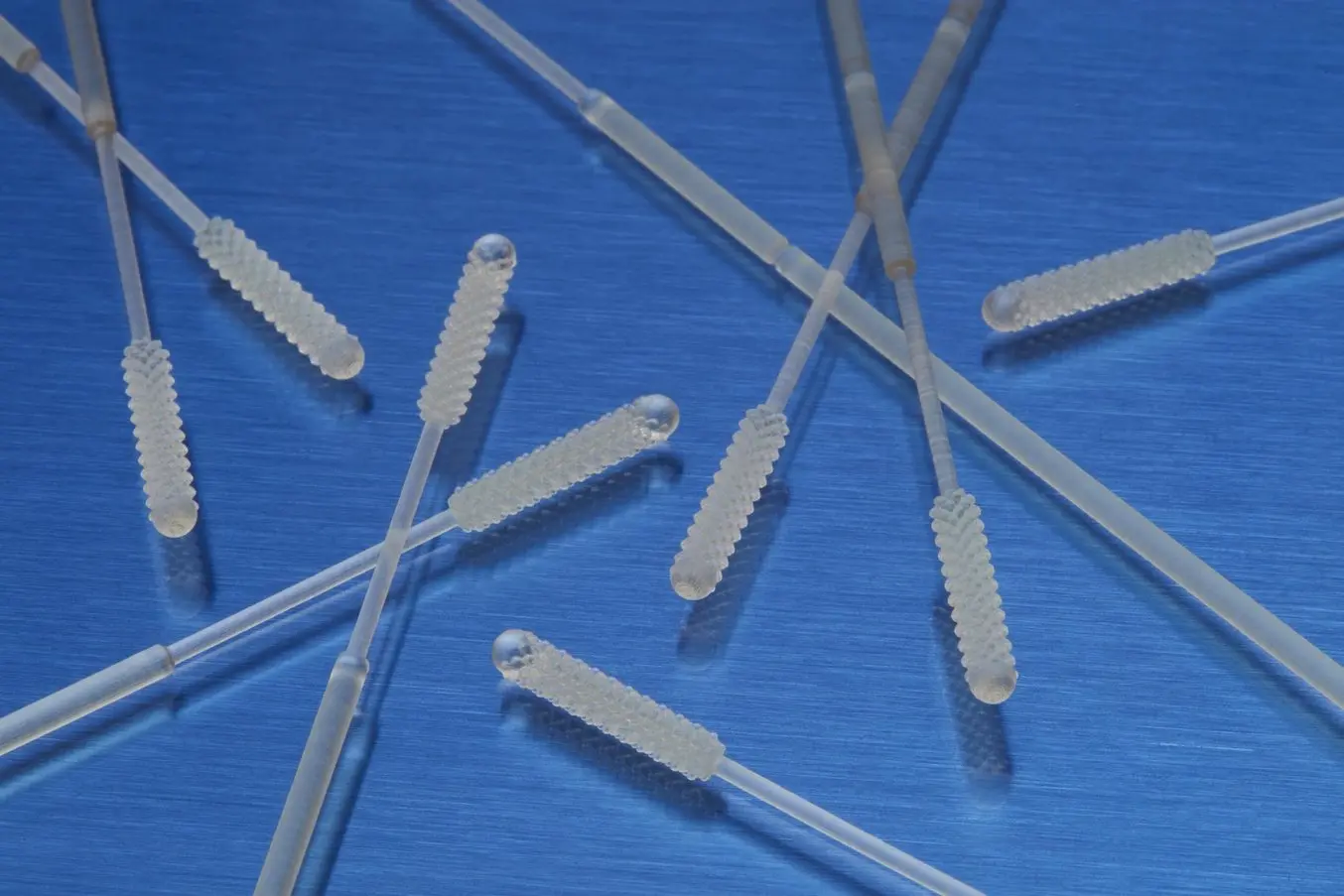
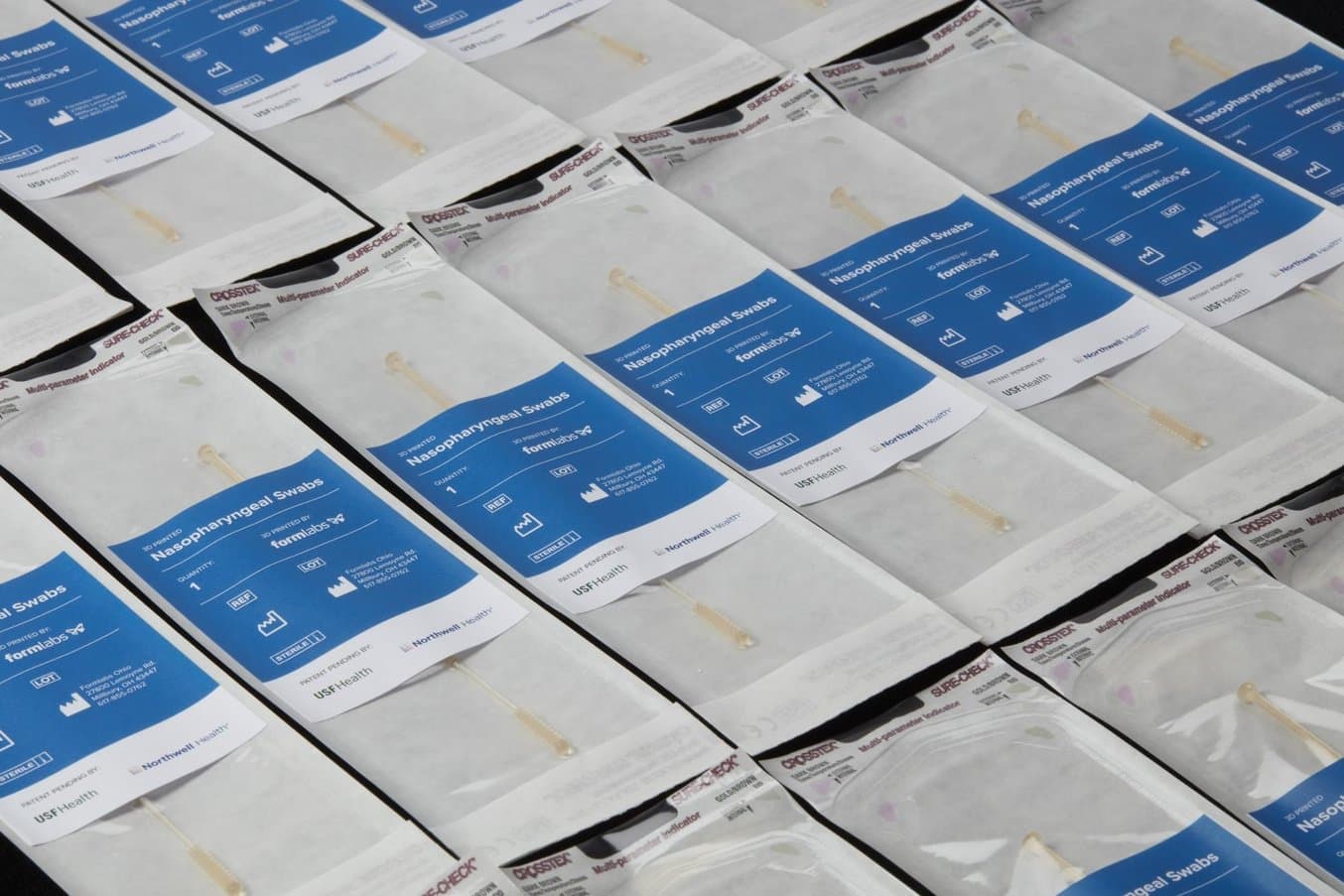
3D-gedruckte Abstrichtupfer ermöglichten in den Frühstadien der COVID-19-Pandemie über 70 Millionen COVID-Tests in 25 Ländern.
Krankenhäuser, Dentallabore und Universitätskliniken, die schon vorher mit 3D-Druckern patientenspezifische chirurgische Produkte herstellten, konnten so Lücken in ihren Lieferketten selbst schließen, indem sie 3D-gedruckte Abstrichtupfer betriebsintern produzierten. Das Abstrichtupferdesign ermöglichte dank der freien Verfügbarkeit, der erschwinglichen Geräte und validierten Prozesse über 70 Millionen COVID-Tests in 25 Ländern.
Zur Deckung des zusätzlichen Bedarfs an Beatmungsgeräten wurden biphasische Überdruckbeatmungsgeräte (BiPAP), wie sie normalerweise zur Linderung von Schlafapnoe eingesetzt werden, entsprechend umgebaut. Durch Einbau eines BiPAP-Adapters ließen sich diese Geräte als funktionelle invasive mechanische Beatmungsgeräte nutzen.
Damit schnell genügend BiPAP-Adapter zur Atemunterstützung der Patienten verfügbar waren, entwarf der größte Gesundheitsdienstleister in New York, Northwell Health, 3D-druckbare BiPAP-Adapter. Die FDA erteilte Formlabs eine Notzulassung für den 3D-Druck dieser Adapter, bis herkömmliche Beatmungsgeräte wieder verfügbar sein würden, um die Kliniken zu unterstützen.
Arbeitsabläufe beim 3D-Druck von Medizinprodukten
Für den 3D-Druck von Medizinprodukten sind nicht alle Methoden gleichwertig. Es ist wichtig, für den jeweiligen Anwendungsfall die richtige Drucktechnologie zu wählen.
Zu den beliebtesten 3D-Drucktechnologien für Medizinprodukte aus Kunststoff zählen u. a. Stereolithografie (SLA), selektives Lasersintern (SLS) und Schmelzschichtung (FDM). Für Metallteile eignen sich Direct Metal Laser Sintering (DMLS) sowie selektives Laserschmelzen (SLM).
Stereolithografie (SLA)
SLA-3D-Drucker verwenden einen Laser, um flüssige Kunstharze zu festen Kunststoffteilen auszuhärten. Dieser Prozess wird als Photopolymerisation bezeichnet. SLA ist bei medizinischen Fachkräften besonders beliebt, da die Technologie eine hohe Auflösung, Präzision und eine große Materialauswahl bietet.
-
Vorteile von SLA
SLA-Teile bieten die höchste Auflösung und Präzision, die filigransten Details und die glattesten Oberflächen aller 3D-Drucktechnologien für Kunststoffe. Allerdings liegt der Hauptvorteil von SLA in der Vielseitigkeit. SLA-Kunstharzformulierungen gibt es mit unterschiedlichen optischen, mechanischen und thermischen Eigenschaften, die denen von Standard-, technischen und industriellen Thermoplasten in nichts nachstehen.
So eignet sich SLA hervorragend für detailreiche Prototypen von Medizinprodukten mit engen Toleranzen und glatten Oberflächen sowie für Gussformen, Werkzeuge, Muster, medizinische Modelle und funktionsfähige Endverbrauchsteile. SLA glänzt auch mit der größten Auswahl an biokompatiblen Materialien für zahnmedizinische und medizinische Anwendungen. Mit Draft Resin sind die SLA-Drucker von Formlabs zudem die schnellste Option zum 3D-Druck großer Prototypen – bis zu zehnmal schneller als FDM.
-
Nachteile von SLA
Die Vielseitigkeit von SLA bedingt etwas höhere Kosten als FDM, die Technologie ist aber immer noch günstiger als alle anderen 3D-Druckprozesse. SLA-Kunstharzteile müssen nach dem Druck nachbearbeitet werden, das heißt gewaschen und nachgehärtet.
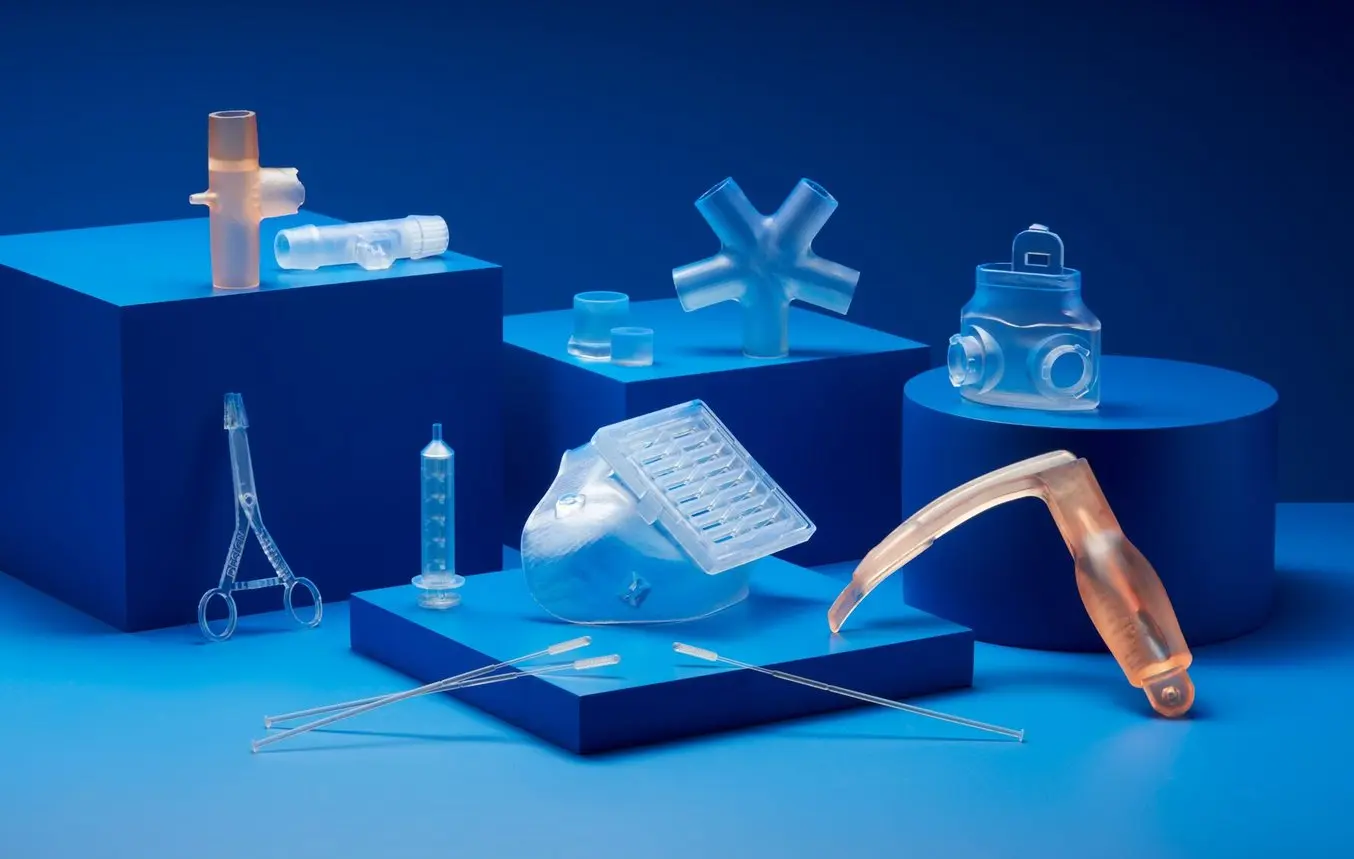
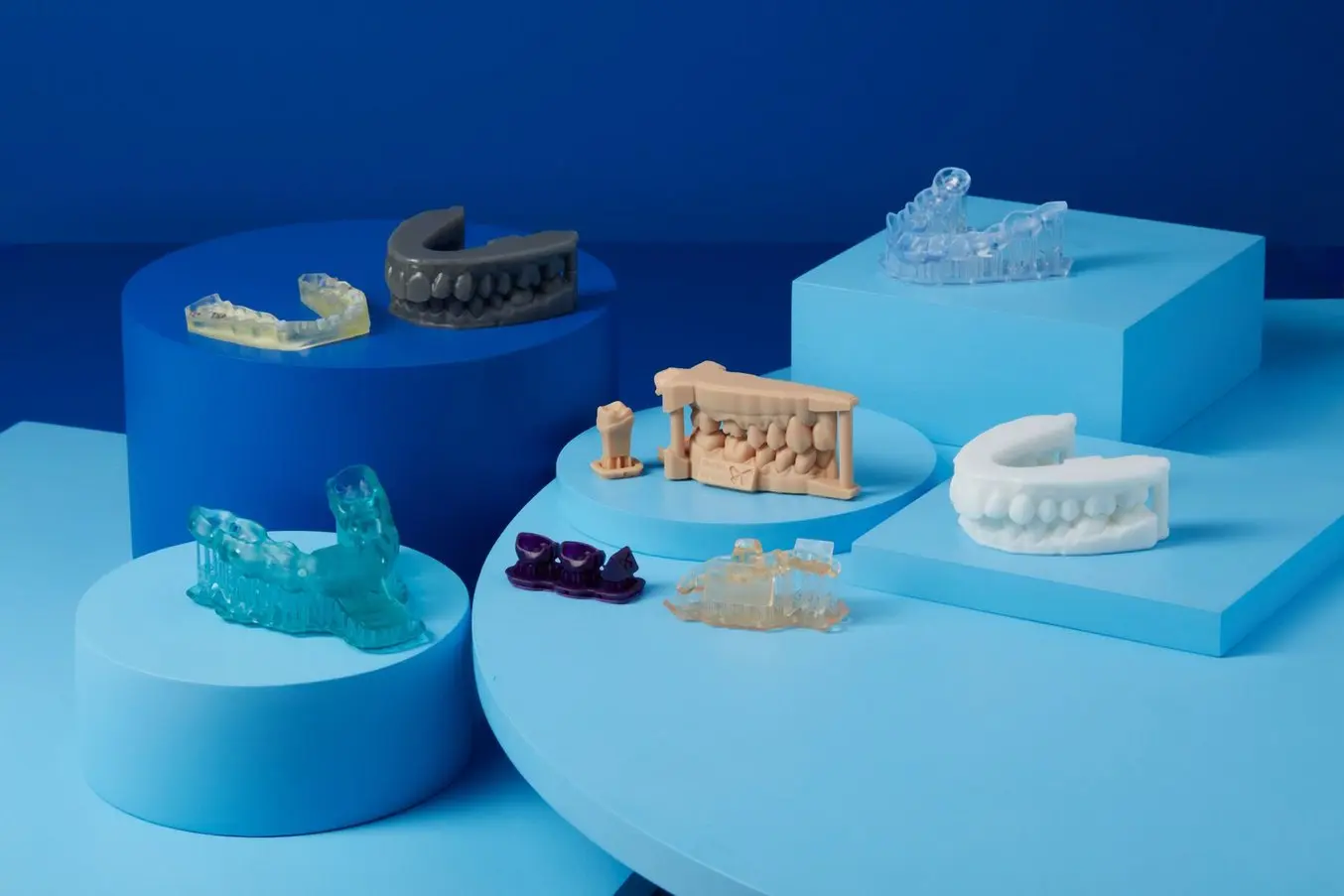
Für den SLA-3D-Druck existiert eine große Auswahl an 3D-Druckmaterialien, beispielsweise biokompatible Materialien, für eine Vielzahl medizinischer und zahnmedizinischer Anwendungen.
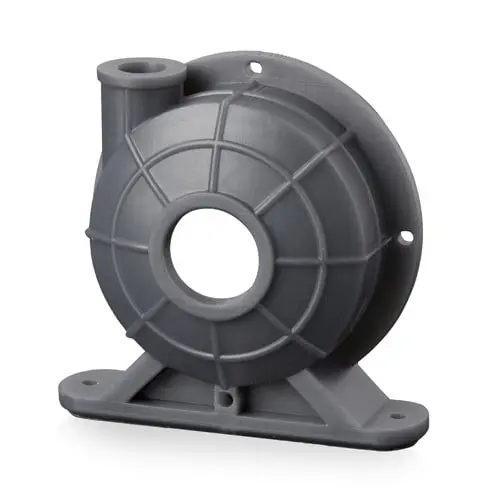
Kostenlosen Probedruck anfordern
Sehen und fühlen Sie selbst die Qualität von Formlabs. Wir senden Ihnen einen kostenlosen Probedruck an Ihren Arbeitsplatz.
Selektives Lasersintern (SLS)
SLS-3D-Drucker verwenden einen Hochleistungslaser, um kleine Polymerpulverpartikel zu sintern. Da das ungesinterte Pulver das Teil beim Drucken stützt, sind keine zusätzlichen Stützstrukturen erforderlich. SLS ist daher eine besonders effektive Option für komplexe mechanische Teile.
Weil diese Technologie Teile mit herausragenden mechanischen Eigenschaften produziert, ist SLS das am weitesten verbreitete additive Fertigungsverfahren bei Industrieanwendungen. Je nach Material können auch SLS-Teile aus Nylon biokompatibel und sterilisierbar sein.
-
Vorteile von SLS
Bei dieser Technologie sind keine dedizierten Stützstrukturen erforderlich. SLS eignet sich somit ideal für komplexe Geometrien, auch im Inneren von Teilen, für Hinterschneidungen, dünne Wände und Vertiefungen. SLS-Teile besitzen hervorragende mechanische Eigenschaften, deren Festigkeit mit Spritzgussteilen vergleichbar ist.
Das am häufigsten für SLS eingesetzte Material ist Nylon, ein beliebter technischer Thermoplast mit exzellenten mechanischen Eigenschaften. Nylon ist leicht, stark sowie flexibel widersteht Stößen, Chemikalien, Hitze, UV-Licht, Wasser und Schmutz. 3D-gedruckte Nylonteile können ebenfalls biokompatibel und nicht-sensibilisierend sein und lassen sich daher in vielen Situationen sicher tragen und verwenden.
Hersteller von Medizinprodukten bevorzugen SLS oft zur Herstellung funktionsfähiger Prototypen aufgrund der geringen Kosten pro Teil, hoher Produktivität, bewährter Materialien und aufgrund der Biokompatibilität. Selektives Lasersintern ist zudem eine kosteneffiziente Alternative zum Spritzguss bei der Kleinserienfertigung und beim Bridge Manufacturing.
-
Nachteile von SLS
Der Einstiegspreis für SLS-3D-Drucker ist höher als bei FDM oder SLA. Auch wenn Nylon ein hervorragendes Allzweckmaterial ist, ist die Materialauswahl bei SLS geringer als bei FDM und SLA. Die Teile kommen mit einer etwas rauen Oberflächenbeschaffenheit aus dem Drucker und müssen gestrahlt werden, um eine glatte Oberfläche zu erreichen.

Der SLS-3D-Druck eignet sich ideal für stabile, funktionsfähige Prototypen und Endverbrauchsteile wie Prothesen und Orthesen.
Schmelzschichtung (FDM)
Bei der Schmelzschichtung (FDM von Englisch Fused Deposition Modelling), auch bekannt als Fused Filament Fabrication (FFF), werden Teile durch Schmelzen und Extrudieren eines drahtförmigen thermoplastischen Kunststoffs (des sogenannten Filaments) aufgebaut, der anschließend von einer Druckdüse schichtweise im Konstruktionsbereich aufgetragen wird.
FDM ist die bei Privatpersonen am häufigsten verbreitete Form des 3D-Drucks, da viele Hobbybastler damit den Einstieg in den 3D-Druck wagen. Industrielle FDM-Drucker sind aber auch bei Fachleuten beliebt.
-
Vorteile von FDM
FDM funktioniert mit verschiedenen Standardthermoplasten wie ABS, PLA und deren Mischungen. Das ermöglicht niedrige Einstiegs- und Materialpreise. FDM eignet sich vor allem für Machbarkeitsstudien und kostengünstige Prototypen einfacher Teile. Manche FDM-Materialien sind auch biokompatibel.
-
Nachteile von FDM
Schmelzschichtung hat die niedrigste Auflösung und Präzision der 3D-Druckprozesse für Kunststoffe (verglichen mit z. B. SLA oder SLS) und eignet sich deshalb nur bedingt für den Druck komplexer Designs oder filigraner Details. Hochwertigere Oberflächen erfordern arbeits- und zeitintensive chemische und mechanische Polierverfahren. Einige industrielle FDM-3D-Drucker verringern dieses Problem teilweise durch chemisch auflösbare Stützstrukturen. Außerdem bieten sie eine breitere Auswahl an technischen Thermoplasten. Jedoch kosten solche Geräte eine Stange Geld. Bei größeren Teilen ist FDM zudem meist langsamer als SLA oder SLS.
Direct Metal Laser Sintering (DMLS) und selektives Laserschmelzen (SLM)
DMLS und SLM funktionieren ähnlich wie SLS, doch statt Polymerpulver werden Metallpulverpartikel Schicht für Schicht durch einen Laser verschmolzen.
DMLS- und SLM-3D-Drucker erstellen stabile, präzise und komplexe Metallprodukte, deshalb eignet sich dieses Verfahren ideal für eine Reihe medizinischer Anwendungen.
-
Vorteile von DMLS und SLM
Der größte Vorteil dieser Prozesse sind natürlich die Materialien, da DMLS- und SLM-3D-Drucker in der Lage sind, Hochleistungsmedizinprodukte für den Endgebrauch und Komponenten mit hochwertigen Eigenschaften aus Metall herzustellen. Diese Prozesse können komplexe Geometrien reproduzieren. Die fertigen Produkte sind stabil, langlebig und biokompatibel. Sie können zur Herstellung generischer Implantate (für Hüfte, Knie, Wirbelsäule usw.), maßgefertigte Implantate für die Krebs- oder Traumabehandlung, Zahnersatz sowie für medizinische und orthopädische Technologieprodukte verwendet werden.
-
Nachteile von DMLS und SLM
Auch wenn die Preise für Metall-3D-Drucker langsam sinken, sind diese Systeme mit 200 000 bis über 1 Mio. USD für die meisten Unternehmen noch immer unerschwinglich. Zudem erfordern Metall-3D-Druckprozesse aufwendige und komplexe Arbeitsabläufe.
Als Alternative bietet sich SLA-Druck an in Verbindung mit Gussverfahren. So fertigen Sie Metallteile zu niedrigen Kosten, mit mehr Gestaltungsfreiheit und in kürzerer Zeit als bei herkömmlichen Verfahren.
Arbeitsabläufe beim 3D-Druck von Medizinprodukten im Vergleich
Die folgende Tabelle zeigt die 3D-Drucktechnologien, die sich am besten für die verschiedenen Anwendungen von Medizinprodukten eignen.
Stereolithografie (SLA) | Selektives Lasersintern (SLS) | Schmelzschichtung (FDM) | Metall-3D-Druck (DMLS, SLM) | |
---|---|---|---|---|
Fertigungsvolumen | Bis zu 300 × 335 × 200 mm (Desktop- und Benchtop-3D-Drucker) | Bis zu 165 × 165 × 300 mm (industrielle Benchtop-3D-Drucker) | Bis zu 300 × 300 × 600 mm (Desktop- und Benchtop-3D-Drucker) | Bis zu 400 × 400 × 400 mm (große industrielle DMLS-/SLM-Drucker) |
Preisspanne | Ab 3500 USD | Ab 16 500 USD | Ab 2500 USD | Ab 200 000 USD |
Materialien | Verschiedene Kunstharze (Duroplaste) Standard, technisch (ABS-, PP-, silikonähnlich, flexibel, hitzebeständig, hart), gießbar, biokompatibel (Medizin und Zahnmedizin) | Technische Thermoplaste, meist Nylon und seine Verbundwerkstoffe (Nylon ist biokompatibel und für die Sterilisation geeignet) | Standardthermoplaste wie ABS, PLA und deren Mischungen | Edelstahl, Werkzeugstahl, Titan, Cobalt-Chrom-Legierung, Aluminium |
Ideale Anwendungen | Detailreiche Prototypen mit engen Toleranzen und glatten Oberflächen sowie Gussformen, Werkzeuge, Muster, medizinische Modelle, funktionsfähige Teile und (zahn)medizinische Endverbrauchsteile | Komplexe Geometrien, funktionsfähige Prototypen, Kleinserienfertigung oder Bridge Manufacturing, Orthesen und Prothesen | Grundlegende Proof-of-Concept-Modelle, kostengünstige Prototypenfertigung einfacher Teile | Strong, durable parts with complex geometries, implants, dentures, medical and orthopedic components out of metal. |
Biokompatibilität bei 3D-Druckmaterialien
Je nach Anwendungsfall sind biokompatible Teile eine Voraussetzung für Medizinprodukte. Informationen zur Biokompatibilität werden in den USA für Einreichungen im Rahmen der PMA- und 510(k)-Zulassungen sowie weltweit für andere behördliche Zulassungen benötigt. Sie belegen, ob ein Produkt mit dem biologischen System kompatibel ist, in dem es eingesetzt werden soll. Fehlende oder unzureichende Informationen können zu beträchtlichen Verzögerungen bei der Markteinführung des Produktes führen.
Die Testanforderungen für Biokompatibilität sollten auf der Grundlage des Verwendungszwecks des Produkts bestimmt werden (Typ, Bereich und Expositionsdauer). Die frühe Bestimmung der Testanforderungen innerhalb des Entwicklungsprozesses ermöglicht ausreichend Zeit, um die Tests abzuschließen, bevor eine Einreichung an die zuständigen Behörden erfolgen muss. Sie sollten aus dem erwarteten Kontakt zwischen Produkt und Menschenkörper hervorgehen.
Kontakt wird typischerweise durch drei verschiedene Kategorien definiert:
-
Direkter Kontakt: physischer Kontakt mit dem Patienten
-
Indirekter Kontakt: physischer Kontakt mit einer Flüssigkeit, Gas oder anderen Materialien, die direkten Kontakt zum Patienten haben
-
Kein Kontakt: weder direkter noch indirekter Kontakt mit dem Patienten, deshalb von Biokompatibilitätsanforderungen ausgeschlossen
Manche Hersteller von 3D-Druckern und 3D-Druckmaterialien, wie Formlabs, führen Biokompatibilitätstests nach den Normen ISO 10993, ISO 18562 und ISO 7405 durch und publizieren Informationen zu relevanten Materialien.
Da der Test an standardisierten Probedrucken durchgeführt wird, müssen die Hersteller die Druck- und Nachbearbeitungsanweisungen einhalten und die Biokompatibilität ihrer Teile unabhängig validieren.
Behördliche Zulassung bei 3D-gedruckten Medizinprodukten
3D-gedruckte Teile müssen den jeweiligen lokalen Zulassungsbestimmungen entsprechen.
Bestandteil dieses Prozesses ist der Aufbau eines Qualitätsmanagementsystems (QMS) mit einem Kernsatz von Richtlinien, Vorgehensweisen, Formularen und Arbeitsanweisungen sowie deren Reihenfolge, Interaktionen und Ressourcen, die zur Geschäftstätigkeit als Medizinproduktunternehmen benötigt werden.
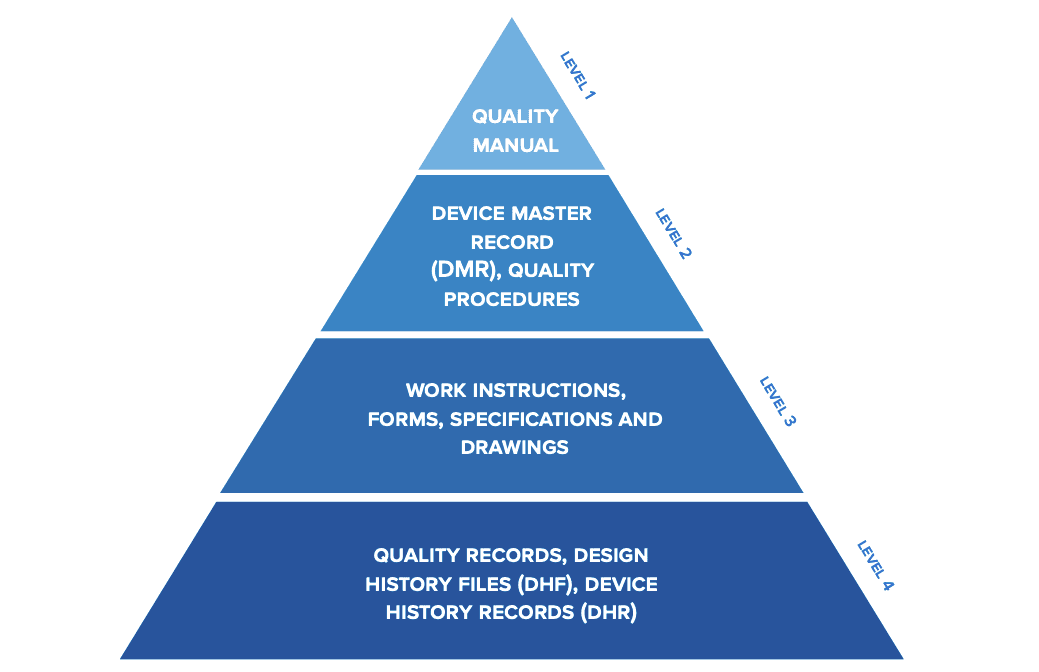
Beispiel einer QMS-Hierarchie
Qualitätsaufzeichnungen sind Dokumentationen, die die Ausführung und Einhaltung des QMS belegen und beschreiben, wie Ihr Unternehmen die Vorschriften zu Medizinprodukten umsetzt. Die amerikanische FDA definiert diese Regeln beispielsweise in 21 CFR Part 820. Wenn Sie auf den US-Markt gehen wollen, sind diese Vorschriften einzuhalten.
Auch in Europa ist die Einrichtung eines Qualitätssystems erforderlich, um die Medizinprodukteverordnungen (und/oder IVD-Verordnungen) einzuhalten. Viele Medizinproduktunternehmen implementieren ein Qualitätssystem, das nach ISO 13485:2016 zertifiziert ist, um den EU-Bedürfnissen gerecht zu werden.
Laden Sie unser umfassendes Whitepaper herunter, um mehr über die spezifischen gesetzlichen Anforderungen zu erfahren. Es wurde vom Formlabs-Partner Greenlight Guru mitverfasst und enthält eine Vielzahl von Ressourcen zur Unterstützung der Nutzer bei jedem Schritt des Prozesses.
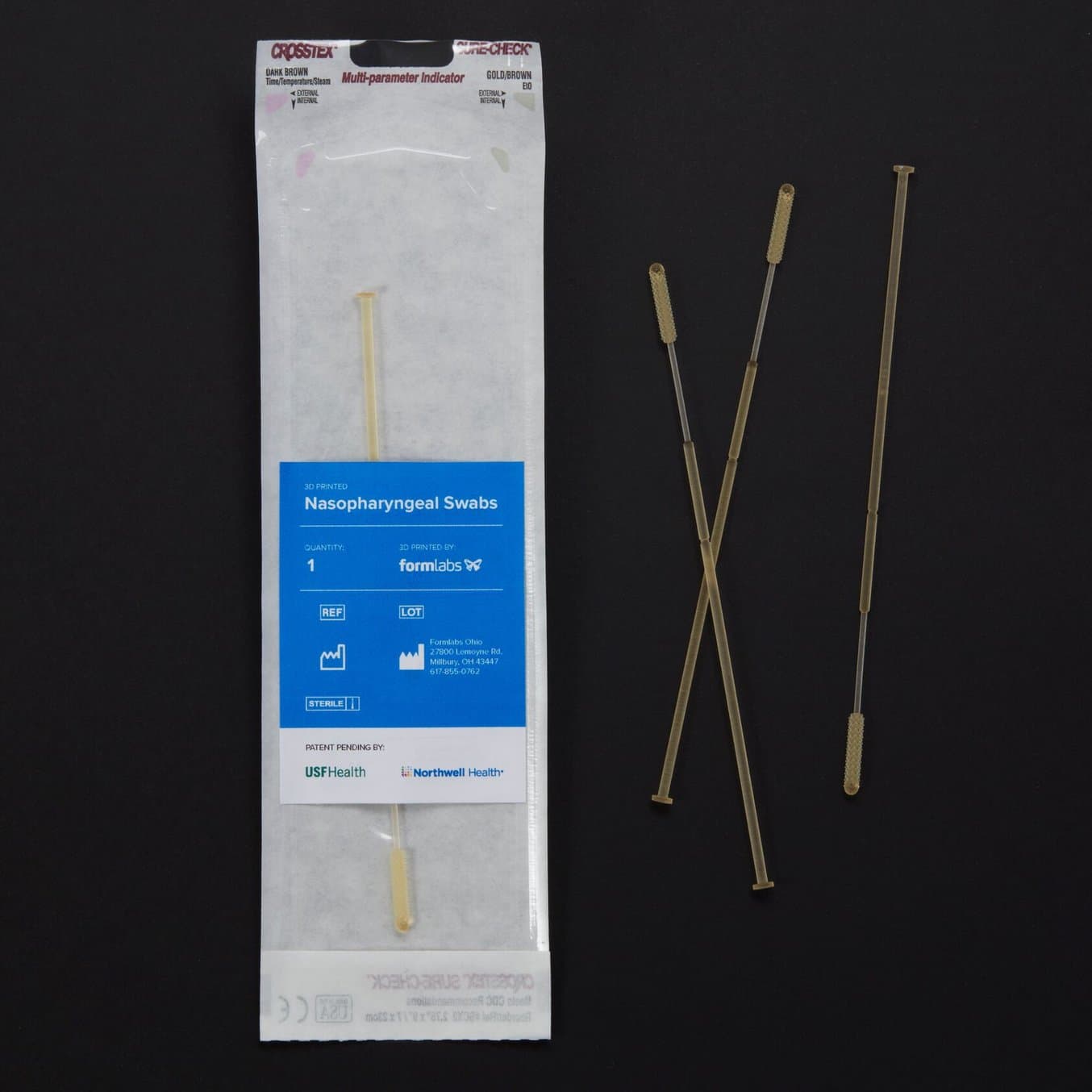
Der ultimative Leitfaden zu Qualitätssicherung und Regulierungsfragen im medizinischen 3D-Druck
Dieses Whitepaper soll Nutzer in der Medizinproduktbranche durch jede Phase des Produktentwicklungsprozesses begleiten, von der Bewertung von Fertigungsmethoden und 3D-Drucktechnologien bis zu spezifischen behördlichen Regulierungsanforderungen für die Kommerzialisierung und Vermarktung 3D-gedruckter Medizinprodukte für Endanwender.
Erste Schritte beim 3D-Druck von Medizinprodukten
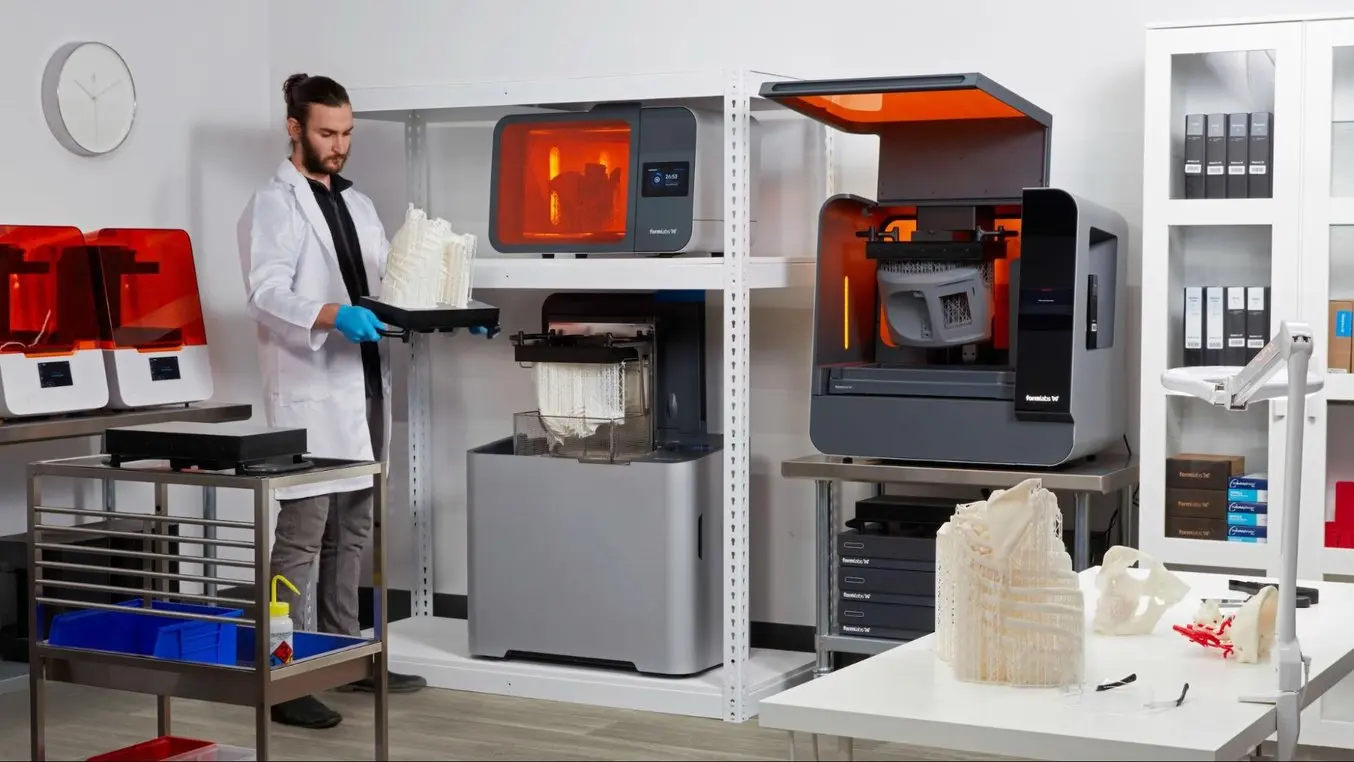
Der betriebsinterne 3D-Druck ermöglicht Medizinproduktherstellern kurze Iterationszyklen und kürzere Produktentwicklungszyklen und verschafft ihnen mehr Zeit, kreative Lösungen zu entwickeln.
Jeder medizinischen Einrichtung sollten die neusten Hilfsmittel zur Verfügung stehen, um die Versorgung zu verbessern und höchsten Patientenkomfort zu gewährleisten. Steigen Sie jetzt ein oder erweitern Sie Ihre betriebsinterne Fertigung mit Formlabs, einem bewährten und innovativen Partner für den 3D-Druck von Medizinprodukten.
Kontaktieren Sie unsere medizinischen Experten, um weitere Informationen dazu zu erhalten, wie ein betriebsinterner 3D-Drucker Ihren aktuellen Designprozess der Medizinprodukte sowie deren Fertigungsarbeitsabläufe ergänzt.