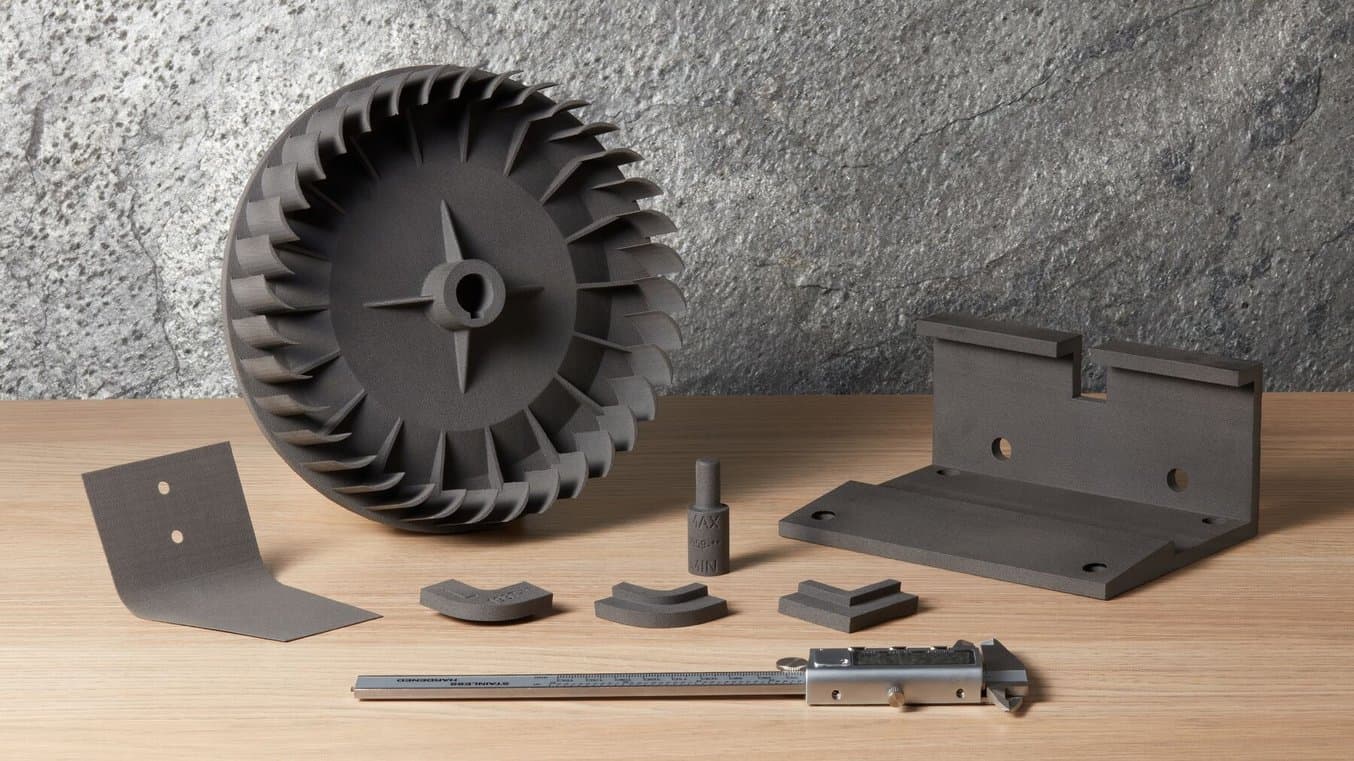
予備部品や交換部品は、機器に不具合が生じた場合の修理・改修中のダウンタイムや生産性の低下を防ぐ、製造現場にとっても消費者にとっても欠かせない存在です。企業が重要な予備部品を入手・供給するためには、高額な在庫を抱え、常に変わりゆくサプライチェーンをうまく乗り切らなければなりません。
しかし、サプライヤーが廃業したり、部品の製作期間が長すぎる場合にはどうなるでしょうか?
予備部品や交換部品の3Dプリントは、サプライチェーンの混乱や予備部品の入手可能性に対処するソリューションとして、ますます強力な方法になってきています。3Dプリンタがあれば、顧客から依頼されたDIYの予備部品から一時的な交換部品、さらには金型で製作した部品の代わりとなる高耐久性の交換部品まで、あらゆる部品を製作できます。メーカーは大量の在庫を抱えることなく、必要な時に必要なだけ予備部品を作るオンデマンド製作が可能になります。
本ガイドでは、アディティブマニュファクチャリングを活用して予備部品をデジタル製作する方法、最適な3Dプリント方式の選択方法、そして実際の活用事例をご紹介します。
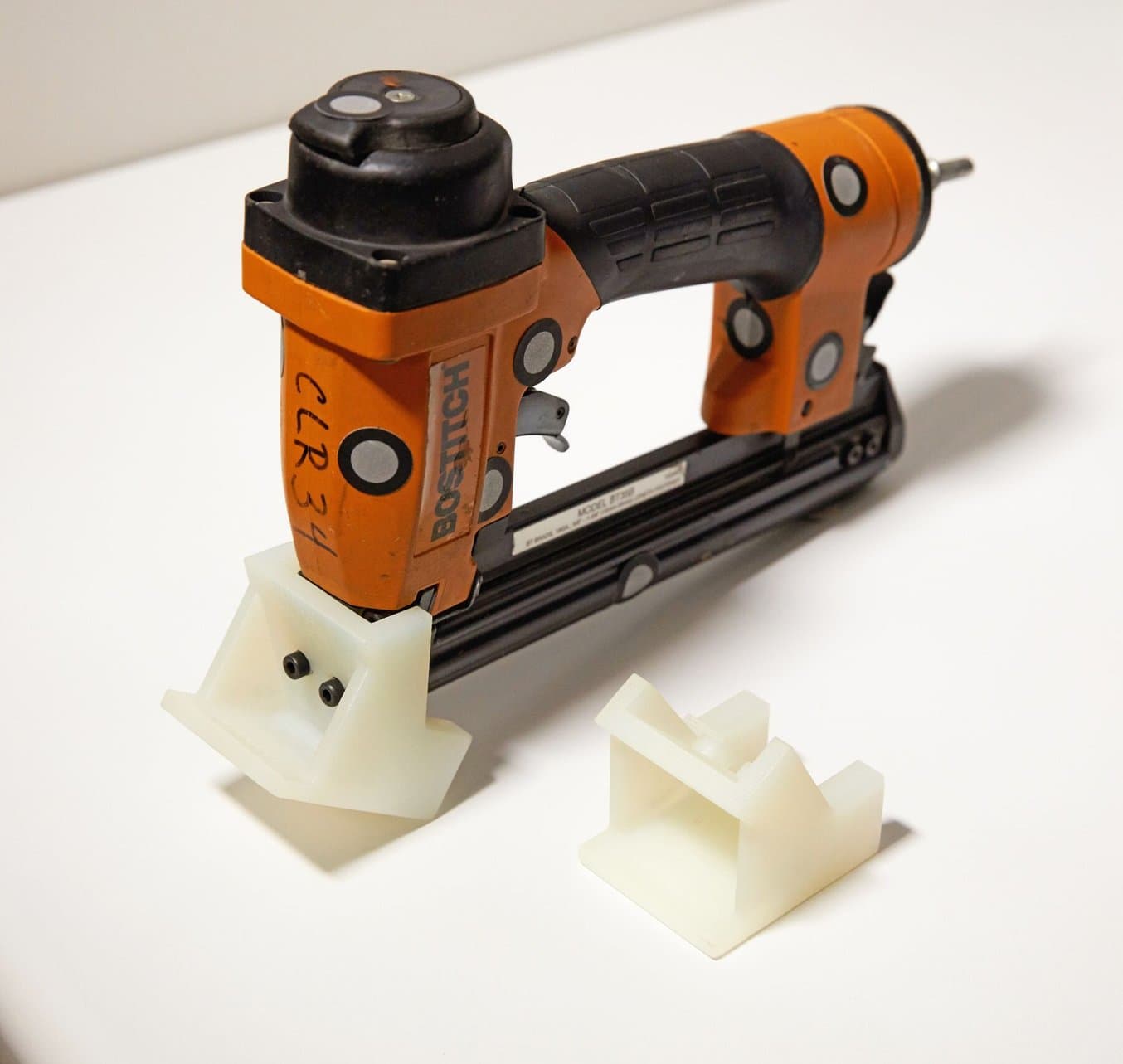
3Dプリントで予備・交換部品を製作する方法
1. 製作可否を確認する
予備部品は既存の機器の一部として機能します。そのため、3Dプリントで製作した予備部品が期待通りの機能を果たせるよう、形状や用途、機械的ストレスの要因など、部品に求められる技術要件をしっかりと確認しておく必要があります。いくつかの基準をご紹介します。
-
形状: 3Dプリンタではほとんど制約のない自由な設計が可能です。そのため、金型を使った従来の方法で製作された部品はほぼ3Dプリントできる可能性があります。さらに、低コストかつ高速でこれまでより優れた強度を備えた部品を製作するためには、設計の微調整が推奨される場合があります。
-
サイズ: 製作する部品は、使用する3Dプリンタの最大造形サイズ以下である必要があります。デスクトップまたはベンチトップサイズのプリンタでは、一般的に縦・横・奥行がどれも150~300mm程度です。一回で収まりきらない場合には、複数の部品に分けて製作した後に組み合わせ、アセンブリ式の交換部品としても製作が可能です。
-
材料: 3Dプリンタで使用できる材料は、ほとんどのプラスチック部品を代用できるほか、一部の金属部品も代用できます。元の部品に使用されていた材料の特性に最も近い材料をご検討ください。
-
応力: 交換部品にかかる応力や衝撃の考慮が必要です。高い耐久性を備えた部品の製作には、より高度な3Dプリント方式とエンジニアリング系材料をお選びください。
3Dプリント製の予備部品ですべての基準を満たせなくても、機器を停止することによるダウンタイムを回避するための一時的な代用品として、十分な機能を果たせることが多くあります。このような場合には、長期的な耐久性には限界があるものの必要な機能は果たせる3Dプリント製交換部品を製作し、より耐久性の高い部品が入手できるまで使用します。
2. 3Dモデルの準備
3Dプリント製部品で代用しても問題ないことが確認できたら、予備部品の3Dモデルを準備します。自社製品の交換部品を製作する場合、そしてその部品がCADソフトウェアを使って設計されたものであれば、デジタルファイルがすでにお手元にあるはずです。サードパーティ製の金型を使って製作した部品の場合は、メーカーからその部品のCADモデルを入手できる場合があります。
設計図が入手できない場合は、CADソフトウェアを使ってモデルを作成するか、設計サービスを提供している企業に依頼します。シンプルな形状の部品であれば、手作業で部品を測定して3Dモデルを作成することも可能ですが、形状が複雑な部品の場合、3Dスキャンによるリバースエンジニアリングで部品の複製を設計・作成すると便利です。
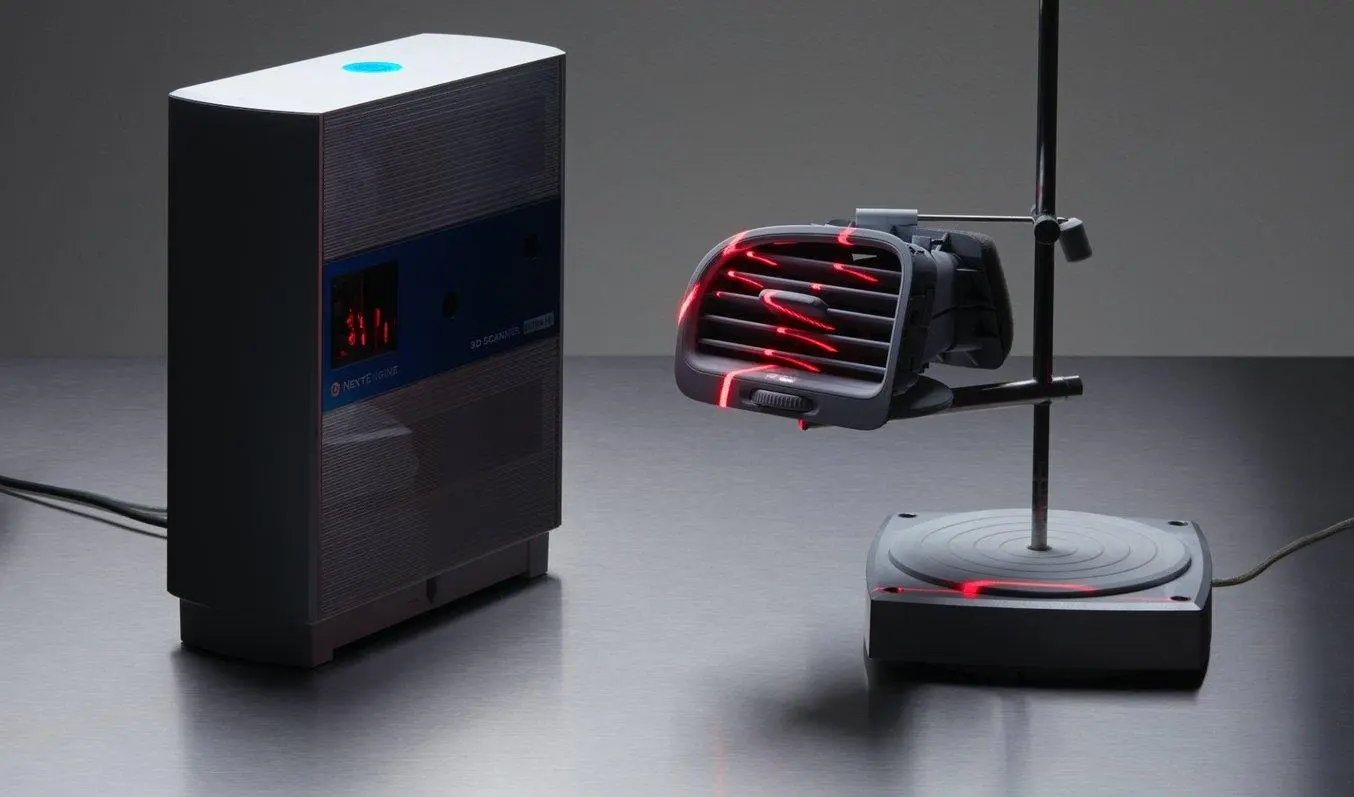
リバースエンジニアリングでは、3Dスキャナを使用して3Dモデルの作成に必要なメッシュデータを取得する。
3. 予備部品を3Dプリント
造形準備ソフトウェアを使用して3Dプリント用のCADモデルを準備し、出来上がったファイルを3Dプリンタに送信します。この段階では、適切な方式と材料を選ぶことが大切です。具体的な推奨事項については、次のセクションをご覧ください。
3Dプリント製の部品には、洗浄、粉末除去、サポート材の除去、二次硬化、やすりがけなど、何らかの後処理が必要になります。後処理を施した部品は用途に応じて、そのまま使用するか、もしくはスムージングや塗装、コーティング、その他さらに高度な表面処理を施します。
4. 検証と反復
ここまで完了したら、検証により3Dプリント製の交換部品が意図した通りに機能することを確認します。検証によって何らかの不具合が判明した場合でも、3Dプリントなら簡単に試作・検証を繰り返して設計を微調整し、部品性能を高めることが可能です。
どの程度広範な検証を行うかは、部品を使用する用途によって異なります。一時的な交換部品として使用する場合は、限られた期間だけ意図した通りに機能すれば十分ですが、3Dプリント製の交換部品を従来の製造法で作った部品の代わりとして使用する場合には、3Dプリント製の部品に以前の部品と同じ検証サイクルを行うと同時に、3Dプリント時の向きに応じた強度の違いなど、3Dプリント工程特有の特性も考慮が必要です。
交換部品の3Dプリントに最適な方式と材料の選定
何十年もの間、3Dプリントは試作品製作や製品開発などで活用されることが一般的でしたが、技術の成熟に伴い、量産でも幅広く使用されるようになってきています。製品開発工程では、さまざまなメーカーが既に3Dプリントの柔軟性を活用し、治具や固定具など社内で使用する部品の製作や、射出成形や熱成形用のラピッドツーリングを行っています。
装置や材料、ソフトウェアの近年の発展により、実製品用部品としての使用にも耐えられる機能部品を高精度で3Dプリントできるようになりました。
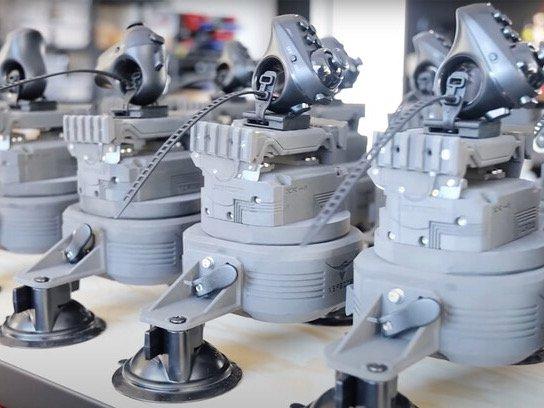
実製品用3Dプリント製部品の負荷テスト
本製品仕様では、実製品用部品の製作に最適なFormlabsの3Dプリンタと材料をご紹介します。様々なユーザー事例とともに、実製品用途での3Dプリント材料の適合性を検証する負荷テストの結果も掲載しています。
3Dプリンタが最もよく使用されるのは、プラスチック部品の製作です。金属の造形が可能な金属3Dプリンタもありますが、コストが大幅に高くなります。3Dプリンタにはさまざまな種類がありますが、プラスチック部品の製造によく使われるのはFDM(熱溶融積層)方式、SLA光造形方式、SLS(粉末焼結積層造形)方式の3つです。
以下の表では、方式ごとに使用可能な材料の種類、予備部品としての最適な用途を簡単に比較しています。
FDM(熱溶解積層)方式 | SLA光造形方式 | SLS(粉末焼結積層造形)方式 | |
---|---|---|---|
精度 | ★★★★☆ | ★★★★★ | ★★★★★ |
表面品質 | ★★☆☆☆ | ★★★★★ | ★★★★☆ |
スループット | ★★★☆☆ | ★★★★☆ | ★★★★★ |
複雑な形状 | ★★★☆☆ | ★★★★☆ | ★★★★★ |
使いやすさ | ★★★★★ | ★★★★★ | ★★★★☆ |
材料 | ABSやPLAなどの標準的な熱可塑性材料とそのブレンド材。 | 高度な材料特性(ABSライク、PPライク、柔軟性、耐熱性、硬度)を持つエンジニアリング系材料など、幅広いレジン | エンジニアリング系熱可塑性材料。Nylon 11、Nylon 12、そのブレンド材、柔軟部品向けのTPU。 |
最適な用途 | シンプルな形状の交換部品 一時的なソリューション | シンプルな形状、または複雑な形状の交換部品 一時的なソリューション 緻密かつ高精度で滑らかな表面品質が求められる部品 | シンプルな形状、または複雑な形状の交換部品 一時的なソリューション 頑丈で安定性と耐久性のある実製品用部品の交換品 |
従来型の製造工程では高価な工業用機械や専用の施設、熟練のオペレーターが必要になることがほとんどですが、3Dプリントの場合はコストが低く、かつ最小限のインフラで内製が可能です。プラスチック部品の製造目的でコンパクトなデスクトップサイズ、またはベンチトップサイズの3Dプリンタを導入する場合、手頃な価格で購入できるほか、設置スペースもわずかな面積で済み、特別なスキルも必要ありません。
急いで製作する必要のない交換部品であれば外注も選択肢の1つですが、これには物理的に予備部品の在庫を抱えるのと同様の課題が伴うことがあります。製作期間は数週間に渡ることもあり、3Dプリント製部品ならほとんどを24時間以内に製作できることを考えると、外注の場合は機械のダウンタイムが長くなり生産性が低下する可能性が高まります。
予備部品をデジタル製作
予備部品の在庫管理や交換部品の製作をデジタル化することで、メーカーにとってはサプライチェーンの問題、最低発注数量、古くなった部品による無駄、などのよくある課題を解消できる可能性があります。
デジタル倉庫をセットアップすることで、コスト効率良く在庫管理にかかる費用を削減できます。このシステムを3Dプリントなどのデジタル内製が可能なツールと組み合わせることで、メーカーのオンデマンド戦略をサポートし、コストや製作期間を削減しながらレジリエンスを高め、ダウンタイムを軽減できるようになります。
デジタル倉庫や予備部品のインベントリでは、予備部品の設計の保存、コンポーネントの体系的な分類、部品表の最適化、在庫管理を行えます。そこで管理する予備部品の設計を3Dプリンタやその他のデジタル製造ツールで製造することで、物理的な在庫確保や必要に応じた部品の交換が可能です。
ケーススタディ:3Dプリントを使った交換部品の製作事例
3Dプリントの最も一般的な用途の1つが、交換部品の製作です。自動車からカスタムロボットグリッパーの予備部品に至るまで、Formlabsのお客様による3Dプリントの活用例をご紹介します。
受賞歴もある自動車修理工場のRingbrothersは、試作品製作を内製化し、より高速かつコスト効率よく試作・検証サイクルを繰り返せるよう、SLA光造形方式3Dプリントを導入しました。3Dプリントを導入して以来、クラシックカーの予備部品のほか、実製品用部品にも3Dプリントを活用して品質と設計を向上さえています。
ミラーの製造案件では、3Dプリント製の部品を最終的なアセンブリの一部として使用しました。カーボンシェル内に接着して恒久的な固定具として機能させ、そのシェルの上には他の部品をボルトで搭載します。別の案件では、鋳造可能な3Dプリント用材料を使用してカスタムカー用の金属エンブレムを製作しました。
製品開発スペシャリストのMatt Moseman氏は「ワックスを3Dプリントし、[地元の宝石職人に]社内で鋳造してもらったおかげで、このような繊細なディテールが実現できました」と述べています。
世界最大の家具メーカーであるAshley Furnitureは、3Dプリントからロボティクスに至るまで、新しい技術を工場に次々と取り入れています。ウィスコンシン州アルカディアにある同社工場では、組立から加工まで、700点もの造形品が工業用ロボットやCNCフライス盤と共に活躍しています。
治具製作以外で3Dプリントの最も実用的な用途となっているのが、製造現場で使用する交換部品の製作です。ポイントツーポイントの切削機用の真空リテーナーリングが単体で購入できなかった時、アセンブリを一式購入するしか選択肢がありませんでしたが、それではコストが高くつきます。
「リングだけを販売してもらえず、ポッド全体を$700で購入するしかないということでした」と製造エンジニアのBrian Konkel氏は振り返ります。「代案として、必要な部品の形状データを3Dスキャンで取得して3Dプリントしたところ、わずか$1で交換部品を製作できました。アセンブリ一式を購入することなく、切削機を再稼働させることができました」

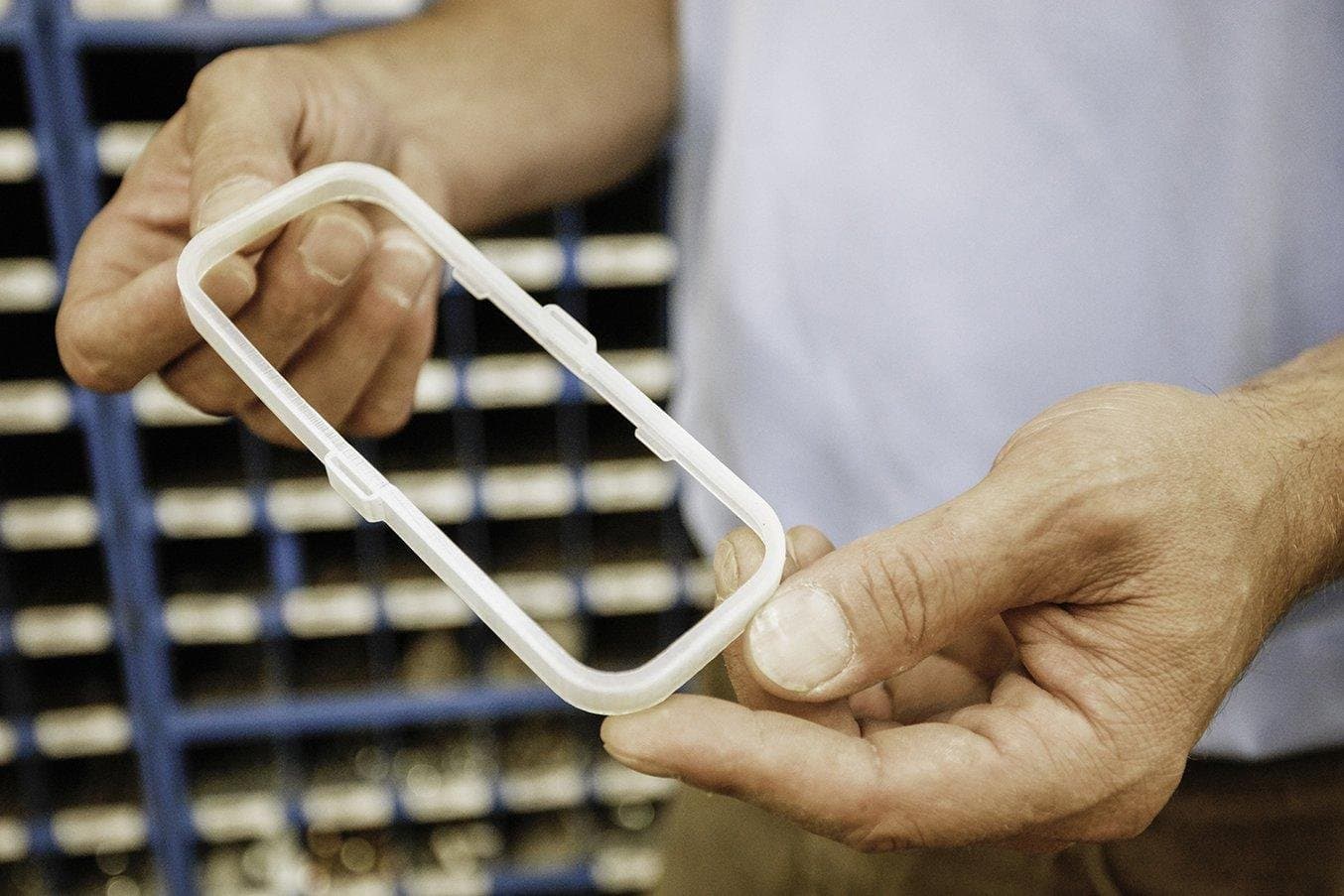
新品のアセンブリ一式を$700で購入する代わりに、交換が必要な部品をわずか$1ドルで3Dプリントした。
Productive Plasticsは、熱成形によるプラスチック部品のカスタム製作や設計サービスを提供する業界大手のメーカーです。6つの生産セルが稼働しており、複数の生産プロジェクトを同時並行で進めることができます。各セルには工業用の熱成形機、CNC加工機、組立エリア、コンピュータシステムがあり、生産の管理・監視を行っています。
ある時には熱成形機の冷却ファンが破損し、成形機が使用できず、生産セル全体の停止を余儀なくされたことがありました。その時、同社はサプライヤーに交換部品を注文しましたが、その製作期間は6〜8週間というもので、交換部品の到着を待つ間に成形機の稼働を再開すべく、破損したインペラの交換部品を暫定的に3Dプリント品で代用することにしました。
Solidworksでインペラの交換部品を2種類設計して試作・検証し、Fuse 1 SLS 3DプリンタにてNyron 12パウダーを使い、わずか1日でプリントすることができました。SLS方式のプリント品はサポート材が不要なため、インペラ中央部の穴も含めて両面に必要な設計を施すことができ、プリントしたインペラはすぐに成形機に取り付けることができました。
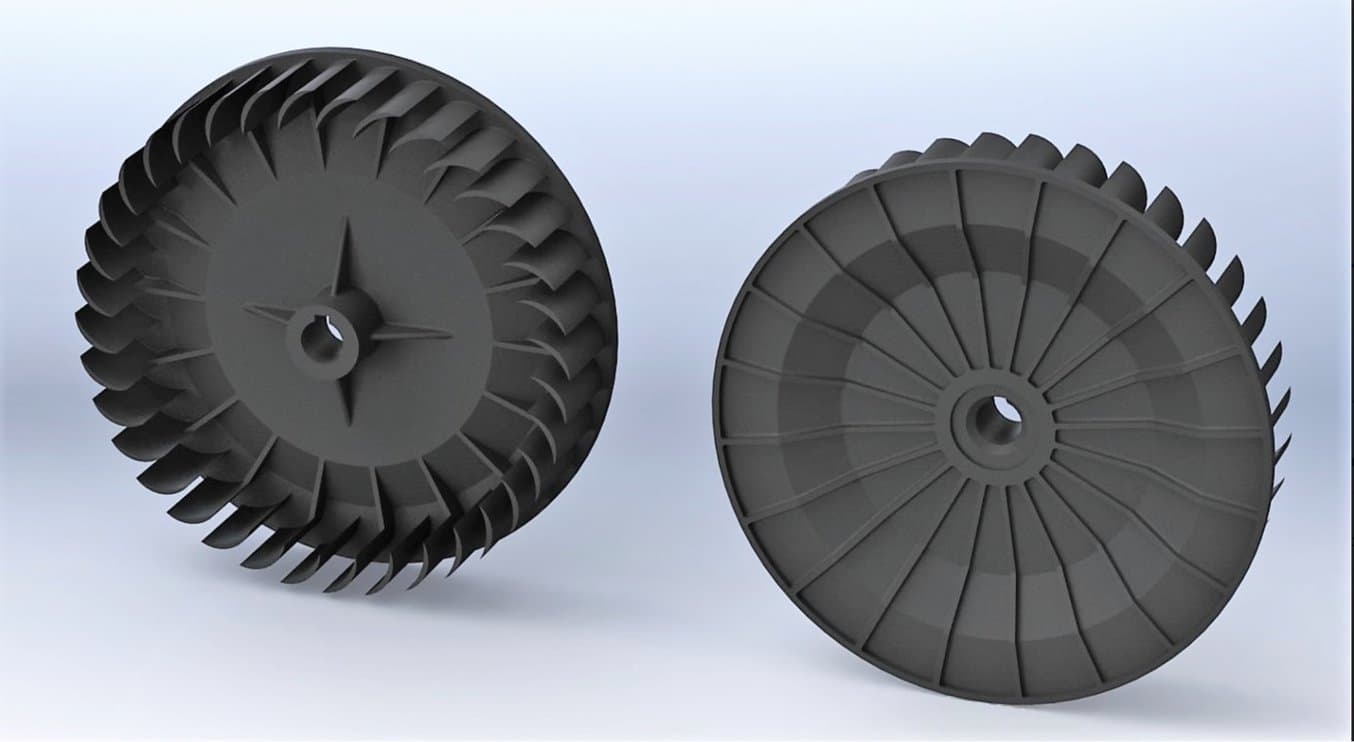
インペラの一時的な交換に使用する3DファイルをSolidworksで製作。
「他の造形方式では、インペラの裏側、特にリブや中央の穴をプリントするのは難しかったと思います。こういう形状は射出成形向きですから。[…] サポート材が不要というのも、Fuse 1を選んだ理由の1つです。この部品は、複雑な形状もプリントできるFuse 1の強みをよく表しているのではないかと思います」と、Productive Plastics セールス&マーケティングダイレクターのKyle Davidson氏は言います。
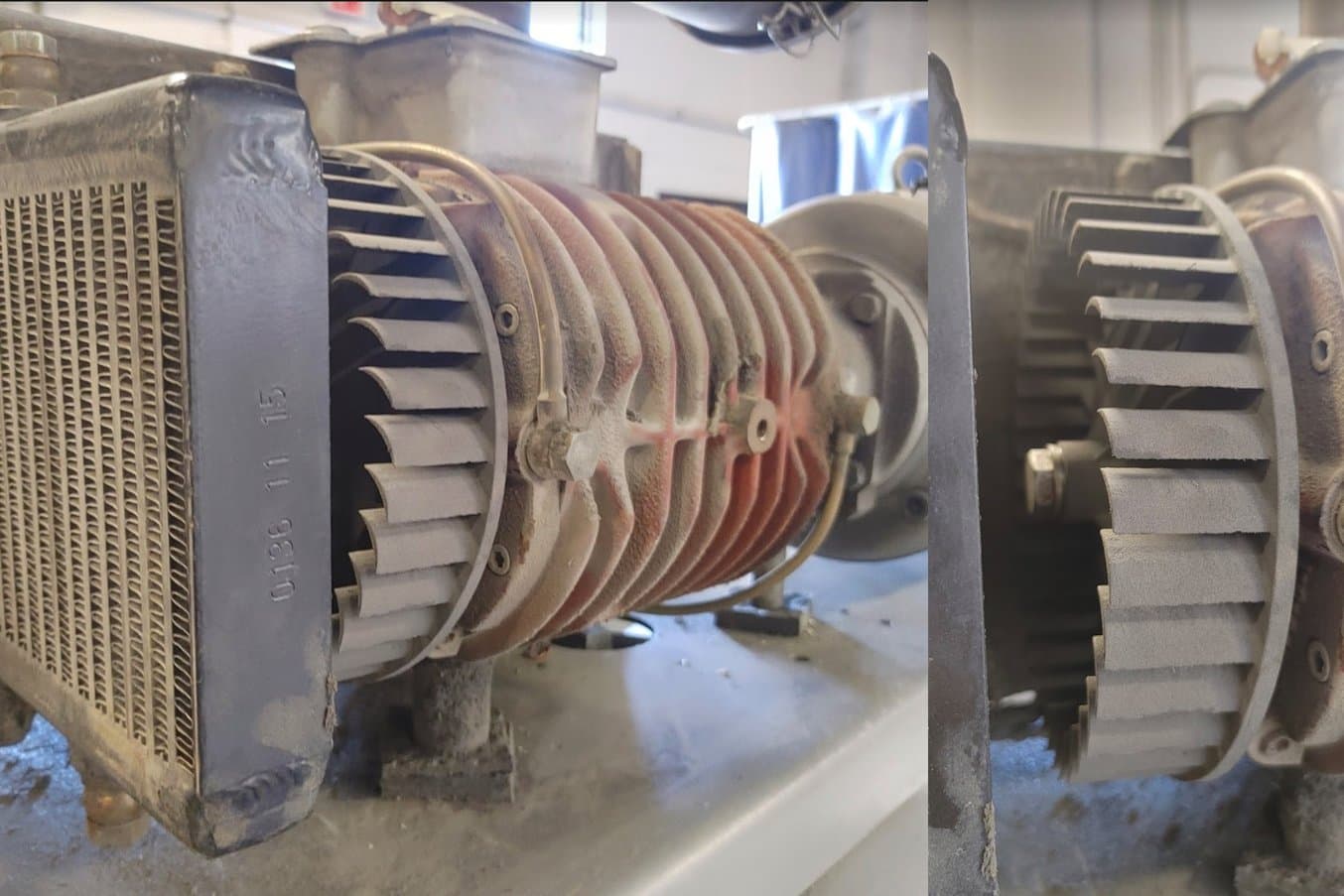
熱成形機のポンプに取り付けられた3Dプリント製インペラの拡大写真(右)と全体図(左)。
インペラはすぐに稼働を始め、故障が発生した翌日には停止していたセルでの生産が再開でき、6週間後に純正の交換部品が届くまで問題なく稼働し続けました。
Productive Plasticsでは、生産セル1つあたりのサイクルタイムは5〜15分ほどで、1セルあたりの最小生産数が40個/日という生産能力を実現しています。機械を6週間も停止した場合、その間生産できない部品点数は1,200個にも上り、金額にして$30,000、部品1点あたり平均$25の損失になっていました。
3Dプリントによる内製 | 交換部品のオーダー | |
---|---|---|
製作期間 | 1日 | 6〜8週間 |
ダウンタイムによる損失 | $1,000 | $30,000 |
AMRC複合材料センターの研究者たちは、ピックアンドプレースロボットを使って炭素繊維の束を正確かつ高速に自動で移動させる方法を模索していました。しかし、長期間の使用によってジョイント周りの圧縮空気グリッパを固定するLブラケットが曲がり始め、うまく動作しなくなってしまいました。センターの研究者たちは3Dプリントを活用し、複雑形状で伸縮性のある新しいカスタム部品を迅速に開発することができました。金型を使った従来の製造方法では実現できなかったでしょう。
「グリッパを6つ1セットにして5回ほど試作・検証を繰り返しました。加工で作っていたら、検証する前に10〜15週間はかかっていたところです」と、複合材料センターでプロジェクトに取り組むMatthew Williams氏は言います。
アメリカの設計開発会社、STS Technical Groupは、標準品のロボットグリッパを、SLA光造形方式で製作した更に高性能な3Dプリント製グリッパに置き換えました。同社が製作したグリッパは、製造現場で燃料噴射装置の移動と位置決めの機能を担っています。
スチールを切削して作ったグリッパから樹脂3Dプリント製のグリッパに変更したことで、柔らかい部品の表面を傷付けるリスクを低減することができました。さらに、グリッパの形状を一般的なV字形状から燃料噴射装置に合わせた形状に変更することで、グリップの接触精度や安定性が向上し、作業時に必要な圧力も減らすことができています。
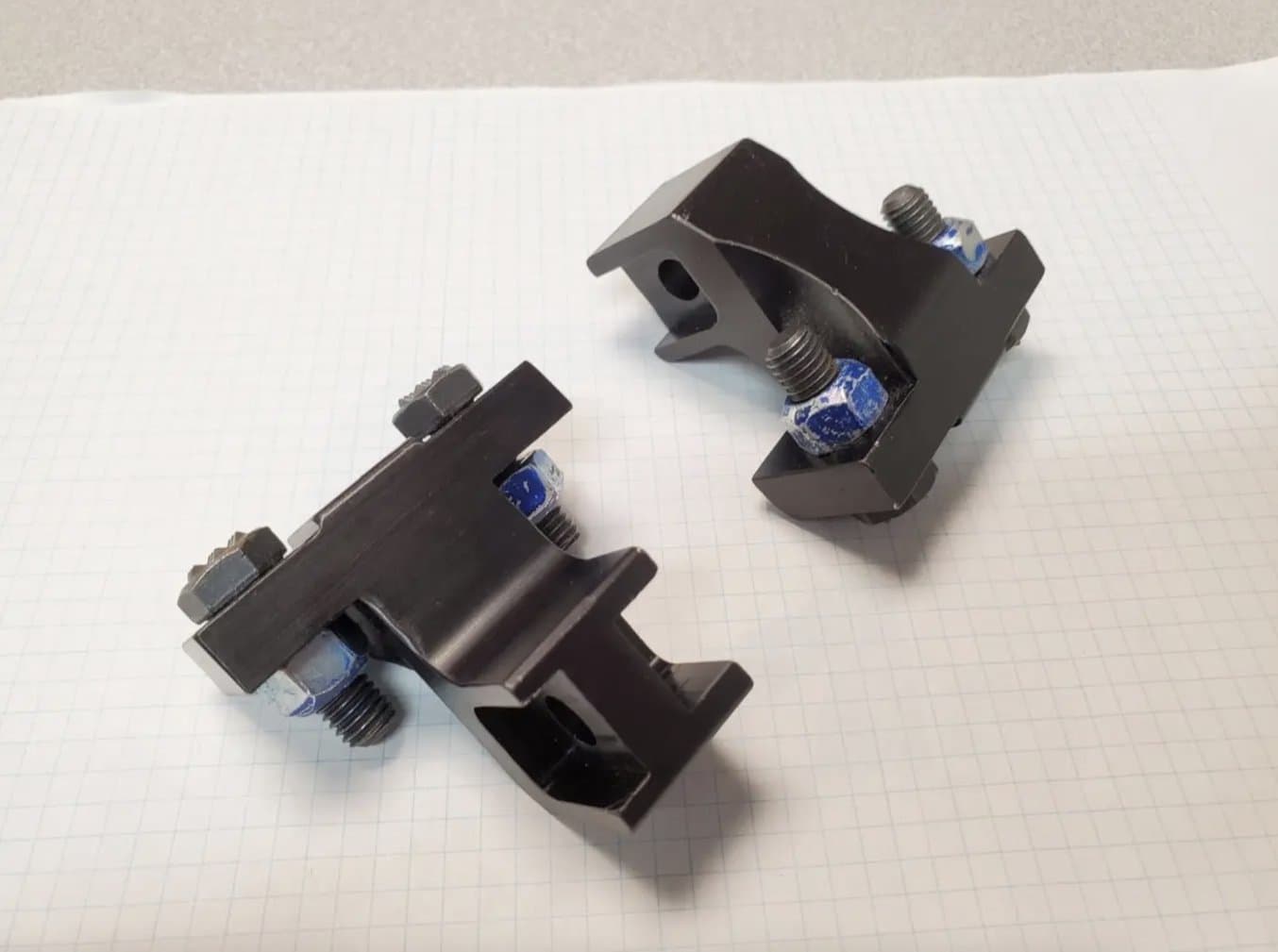
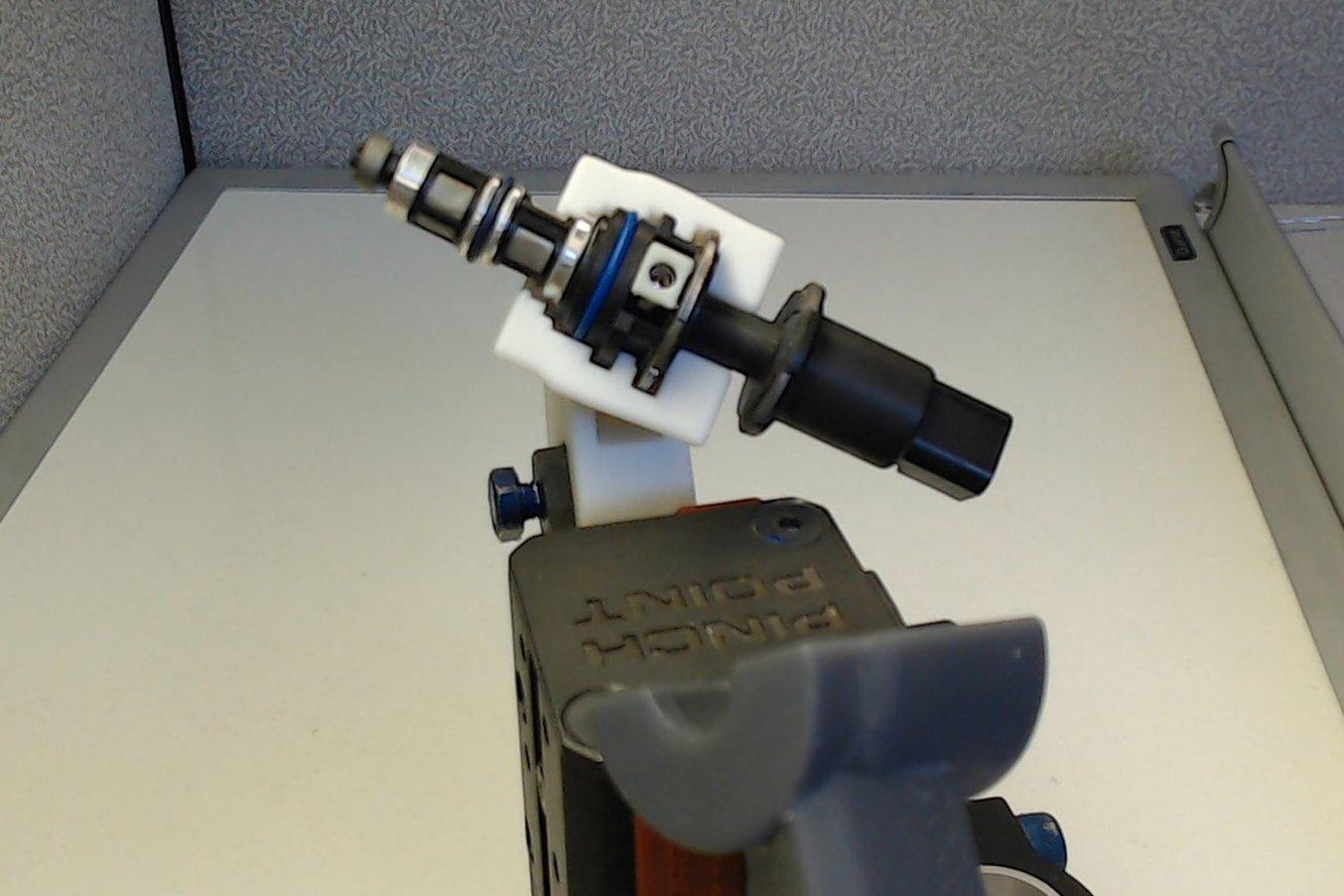
空圧シリンダーに設置されていた標準品のグリッパ(上)と燃料噴射装置を固定するRigid 4000レジンで3Dプリントしたグリッパ(下)。
加工工場のA&M Tool and Designは、3Dプリントの使用を拡大し、治具や実製品用部品などの機能部品も製作し始めました。例えば、大型のレンズ研磨機の1つで使用するスパイダーカップリングが大規模な展示会の2日前にサイズ違いで届いたことがありました。そこで、メカニカルエンジニアのRyan Little氏は急いで正しいサイズの交換部品をSLA光造形3Dプリンタで製作しました。3Dプリント製のカップリングを使った研磨機で、2馬力のモーターを動かすことができました。
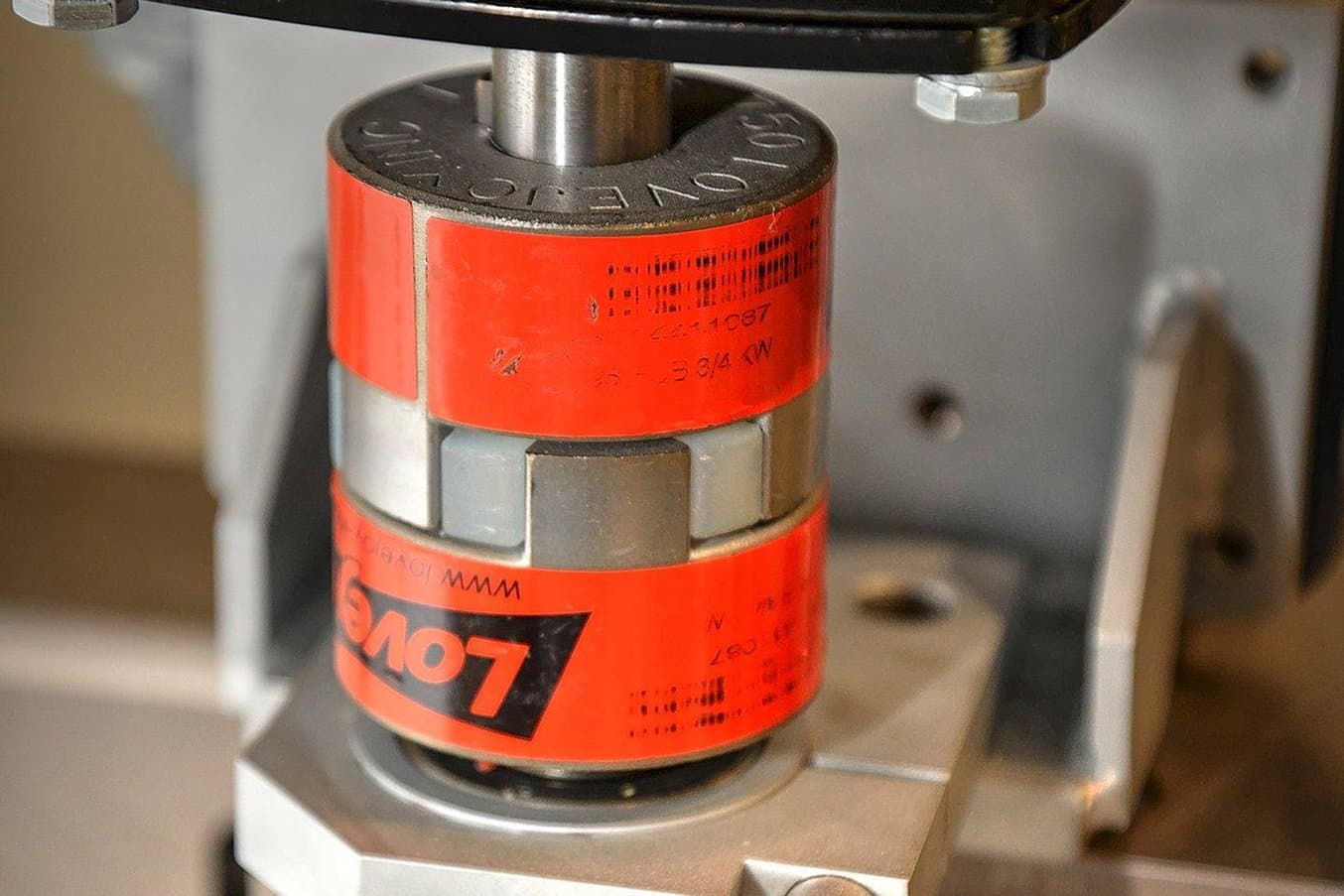
外注したレンズ研磨機用のスパイダーカップリングがサイズ違いで届いた時、A&M Tool and Designは3Dプリント製の交換部品をDurableレジンで製作し、大規模な展示会に間に合わせることができた。
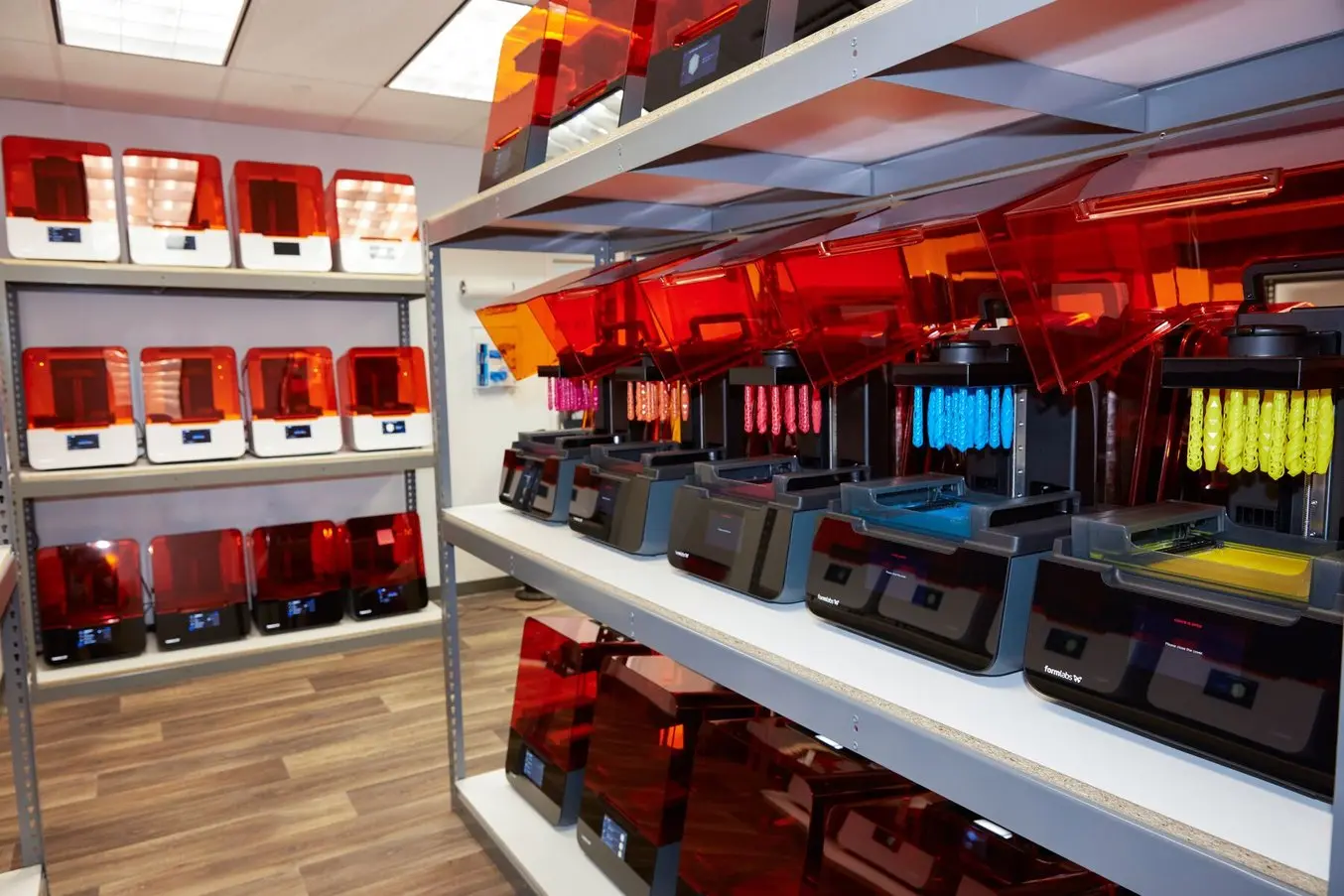
3Dプリント製の実製品用部品で少ロット量産とカスタム製造を行う方法
このウェビナーでは、カスタム製造と少量の実製品用部品生産を素早くコスト効率良く行う方法についてご紹介します。
3Dプリント製の交換部品の合法性
3Dプリント製の交換部品は一般的には合法ですが、それぞれのケースによって異なる場合があります。
リバースエンジニアリングは一般的には合法な手法で、メーカーはトレードシークレット法(営業秘密法)を侵害することなく自社設計を使って予備部品を3Dプリントできます。
ただし、商業目的で3Dプリント製の予備部品を製作する場合は、適用法に従い、契約上定められた安全品質要件を遵守した設計または製品を提供する義務が発生する場合があります。
英国政府が行なった予備部品の3Dプリントに関する法的要件と責任に関する広範な調査では、本工程の合法性について非常に有益な情報が提供されています。この調査では、予備部品と交換部品の両方の製造、および米国、英国、欧州、カナダ、日本、中国における製造サイクルのすべての工程の法的要件が網羅されています。
3Dプリントで予備・交換部品の製作を開始する
3Dプリントを活用して交換部品や予備部品を内製することで、手頃な価格で迅速かつ効果的にダウンタイムや生産性の低下を回避できます。
Formlabsでは、予備・交換部品の製造に最適な最先端のSLA光造形およびSLS 3Dプリンタ、工業グレードの材料を提供しています。ぜひ、弊社Webサイトで3Dプリンタの詳細をご覧ください。また、理想的な作業手順を確立する方法については、弊社スペシャリストまでお気軽にご相談ください。