
Eyewear, from reading glasses, to safety goggles, to celebrity-endorsed sunglasses, are the rare example of a product that can be endlessly personalized in terms of both style and functionality. Eyewear manufacturers make adjustments on things as big as material choice or as small as micron-level differences in lens thickness. As resolution, accuracy, material versatility, and finishing processes for 3D printing become more advanced, the technology presents a costeffective method of designing and manufacturing eyewear.
3Dプリント製アイウェアの登場
実製品用途としての3Dプリント製アイウェアの活用は過去5年間で大幅に増加し、大小を問わず様々な企業が3Dプリントによって得られる設計の自由度、小ロット生産能力、持続可能性といったメリットを享受しています。
作業現場における保護具、機能的性能、ファッションなど、3Dプリントは様々な用途でアイウェア業界に浸透し、デザイナーやメーカーの生産に対する考え方を変えてきました。
3Dプリントの主な利点は、製品の一貫性と品質を高いレベルで維持しながら、生産工程における組立作業を削減できることにあります。アイウェアメーカーの中にはアセテートフレームの製造には60もの工程が必要だと言うところもあるほど、数多くの作業が必要になります。
3Dプリントの基本的な工程は以下の通りですが、これにより組立工程の複雑さとそれに関連して発生する作業を大幅に削減できます。
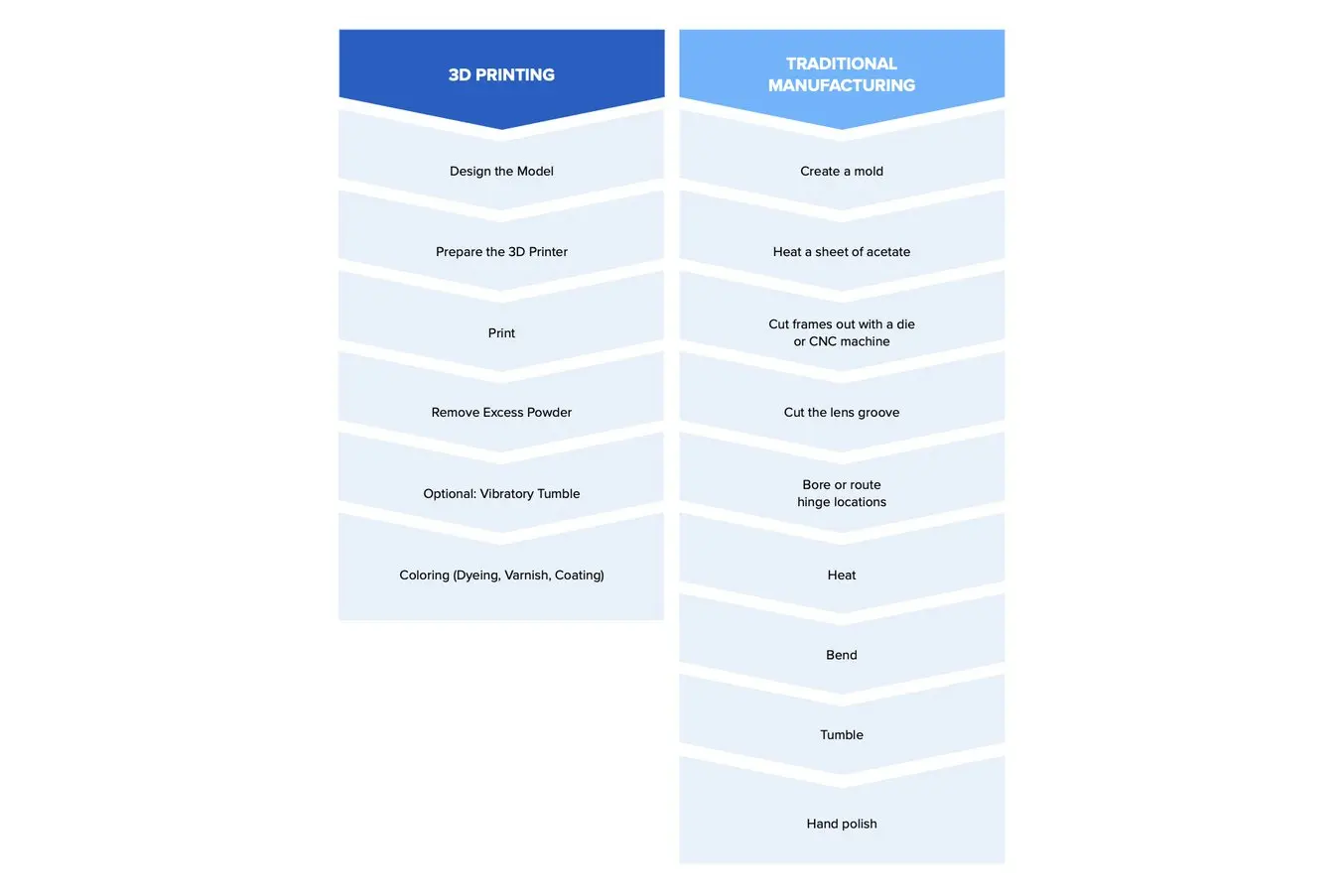
SLS(粉末焼結積層造形)方式3Dプリントは、高強度な機能部品が製作できることから、さまざまな業界のエンジニアやメーカーから信頼され、工業用途で最も普及しているアディティブマニュファクチャリング技術です。
SLS 3Dプリンタは、高出力レーザーでポリマー粒子を焼結することで造形します。プリント中は未焼結パウダーが造形品を支えるため専用のサポート材が不要で、内部構造やアンダーカット、薄壁や凹面等、複雑な形状の造形に最適です。SLS方式で3Dプリントした造形品は、射出成形品に匹敵するほどの高い強度など非常に優れた機械的特性を発揮できるため、アイウェアの3Dプリントには最適な方式と言えます。
ここからは、市場投入までのスピードの向上、作業量の削減、アイウェアフレームやテンプルの外注時に発生する最低注文数量(MOQ)が不要になるなど、3Dプリントの活用で得られるメリットをご紹介します。
Value Propositions of 3D Printed Eyewear
Manufacturing Sustainability
Current eyewear frame production is primarily accomplished through injection molding, die cutting, or precision CNC milling, forcing manufacturers to invest in significant mold and equipment costs. Outsourcing production of molds or machined parts can take weeks and cost thousands of dollars. To justify the expense, the manufacturer has to commit to extremely high
quantities of the product which can result in lower profits and high volumes of unsellable stock.
This system is unsustainable both financially and environmentally. 3D printing allows companies to own their manufacturing with no mold investment, lowering the risk of starting a new product line substantially. In-house 3D printing frees manufacturers from high MOQ requirements and commitments to unpopular product designs by enabling the production of small, on-demand batches with no upfront molding costs.
Most pieces of eyewear today are created through injection molding or a subtractive process where acetate is cut into the designated shape. The cutting process takes large sheets of acetate and cuts away the frame shape, leaving all resulting material as waste.

カット工程で作られる従来のアセテートフレーム。(写真出典:Visio Optical)
一方、3Dプリントはアディティブ工法といって材料を層にして積み重ねていくことで造形します。FormlabsのSLS製品では未焼結パウダーをリサイクルして次のプリントで再利用できるため、材料の無駄がほとんどありません。

Nylon 11 Powder 3D printed frames being extracted from the powder cake in the Fuse Sift.
The small footprint and affordable price point of the Fuse SLS ecosystem allows manufacturers to purchase multiple machines for multiple locations, thus distributing production capacity to regions that are physically close to consumers, and reducing the reliance on overseas production that can be slowed by global supply chain complications. Having distributed production also reduces the negative environmental impact associated with overproduction and shipping.
設計の自由度
Unlike other polymer 3D printing technologies, parts produced through SLS 3D printing do not require support structures, as they are supported by the surrounding powder bed. With no support structures, sprues, or restrictions on draft angles and undercuts common in traditional molding or cutting processes, SLS 3D printing offers almost unlimited design freedom, enabling advanced designs that were previously too costly or even impossible to produce.
Manufacturing restrictions no longer prevent product designers from creating the most functional, best fitting, and most fashionable designs. 3D printed eyewear enables responsiveness to consumer trends faster than ever before, allowing brands to capture new and emerging market segments.

従来工法では効率的な製造が困難または不可能だった複雑なテンプル設計も3Dプリントで実現。
Customization and Personalization
金型や最低発注量が必要ないことで、製品のパーソナライゼーションにもついに手を伸ばせるようになります。お客様の好みに合わせてサイズやデザインをカスタマイズし、最高のフィット感と誰とも被らないユニークな製品を提供できます。
人工装具やアクションフィギュア、オーディオ製品などの分野ではすでに3Dプリントによってカスタマイゼーションが可能になっており、製品の機能向上や個人的な嗜好に近い製品を出せた場合に最も成功しやすくなることがわかっています。年齢、人種、顔の特徴が多種多様な現代において、プロダクトデザイナーは「誰にでも合う製品」という考え方から脱却し、一人ひとりに合わせたパーソナライゼーションの世界に足を踏み込まざるを得なくなっています。
“With 3D printing, I can do it immediately. If you are familiar with CAD design, you can easily make adjustments to the 3D model, upload it to the software, and print it directly. When it comes to milling, on the other hand, I would always need an individual and expensive tool development to hold the elements in the machine."
Marcus Marienfeld, Eyewear Designer and Manufacturer
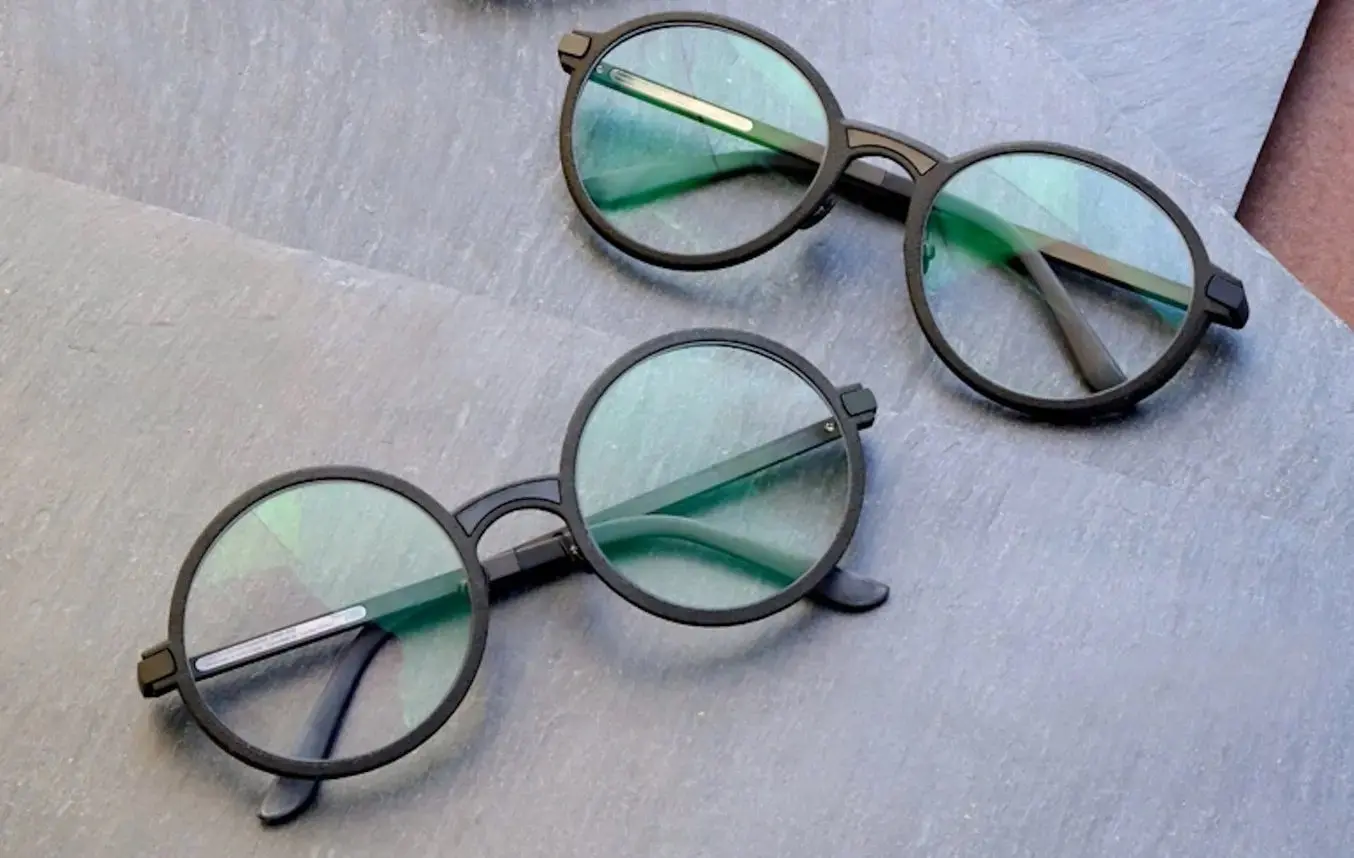
スイスのアイウェアメーカーMarcus Marienfeldは、Fuse 1+ 30W SLS 3Dプリンタを使用して写真のような実製品用アイウェアを3Dプリントで生産している。
3Dプリント製アイウェアの製造方法
設計
3Dプリントで実製品用アイウェアを製造する場合、この分野独自のメリットと課題があります。このセクションでは、質感やヒンジのオプション、成形では実現できない形状の設計、カスタマイゼーションについてご説明します。

3D printed in Nylon 12 Powder, these frames are dyed black and maroon in a water bath.
テクスチャ
Additively manufactured parts are formed layer by layer, meaning that some surfaces may have visible layer lines. Layer lines can be mitigated through part orientation optimization, part design, and additional post-processing to smoothen the surface. Adding embossed or debossed texture to the surface of frames and temples is a well-known strategy to mask layer lines on end-use 3D printed goods. Formlabs recommends a minimum 0.35 mm high emboss and 0.15 mm deep deboss to ensure sufficient masking of any layer lines. Finally, part layer lines can be used as a tool to increase grip and friction, preventing slippage on the face.
ヒンジのオプション
3D printed eyewear hinges can be achieved in four main ways:
- Traditional screws
- Heat set inserts
- Snap-fit
- Print-in-place hinges
Hinge threads can be added to the design of 3D printed parts, but traditional eyewear screw threads are typically too small to resolve consistently. Stick to thread sizes of at least ¼”–20 (imperial) or M6 (metric) or larger.

Eyewear assembled with a printed thread and metal screw.
Nylon 11 Powder, Nylon 12 Powder, and Nylon 12 White Powder allow for the use of heat-set inserts and tapped threads, which can be longer lasting and more durable than other options. Read the step-by-step guide here.
Lastly, due to the lack of support structures, SLS 3D printing enables the use of print-in-place geometries. Frames can be designed and printed with temples already attached, with no further assembly required. Formlabs recommends 0.3 mm of clearance on features less than 20 mm2, and 0.6 mm of clearance on features greater than 20 mm2. Read the entire SLS design guide here.
成形では実現できない形状

nTopologyソフトウェアのラティス化オプションで設計しNylon 11パウダーで造形したテンプル。

Eyewear frames and temples printed on the Fuse 1+ 30W printer, designed and manufactured by Alvaro Planchart.
主にファッション性の高い用途になりますが、3Dプリントによってデザイナーは成形や打ち抜き加工では作れないアイウェアのデザインができるようになりました。上の写真のテンプルは、成形では実現できない形状です。3Dプリントでこういった形状も可能になることで、使用者の自己表現という新たな領域にフォーカスしながら軽量化によって使用感の改善も狙えます。
3Dプリント
アイウェア製造に最適な3Dプリンタ
The Fuse Series SLS ecosystem offers an accessible and scalable production solution for eyewear, due to its reliable hardware, industrial grade materials, and intuitive user interface. The sections below will cover tips and tricks specific to producing eyewear with SLS 3D printing.
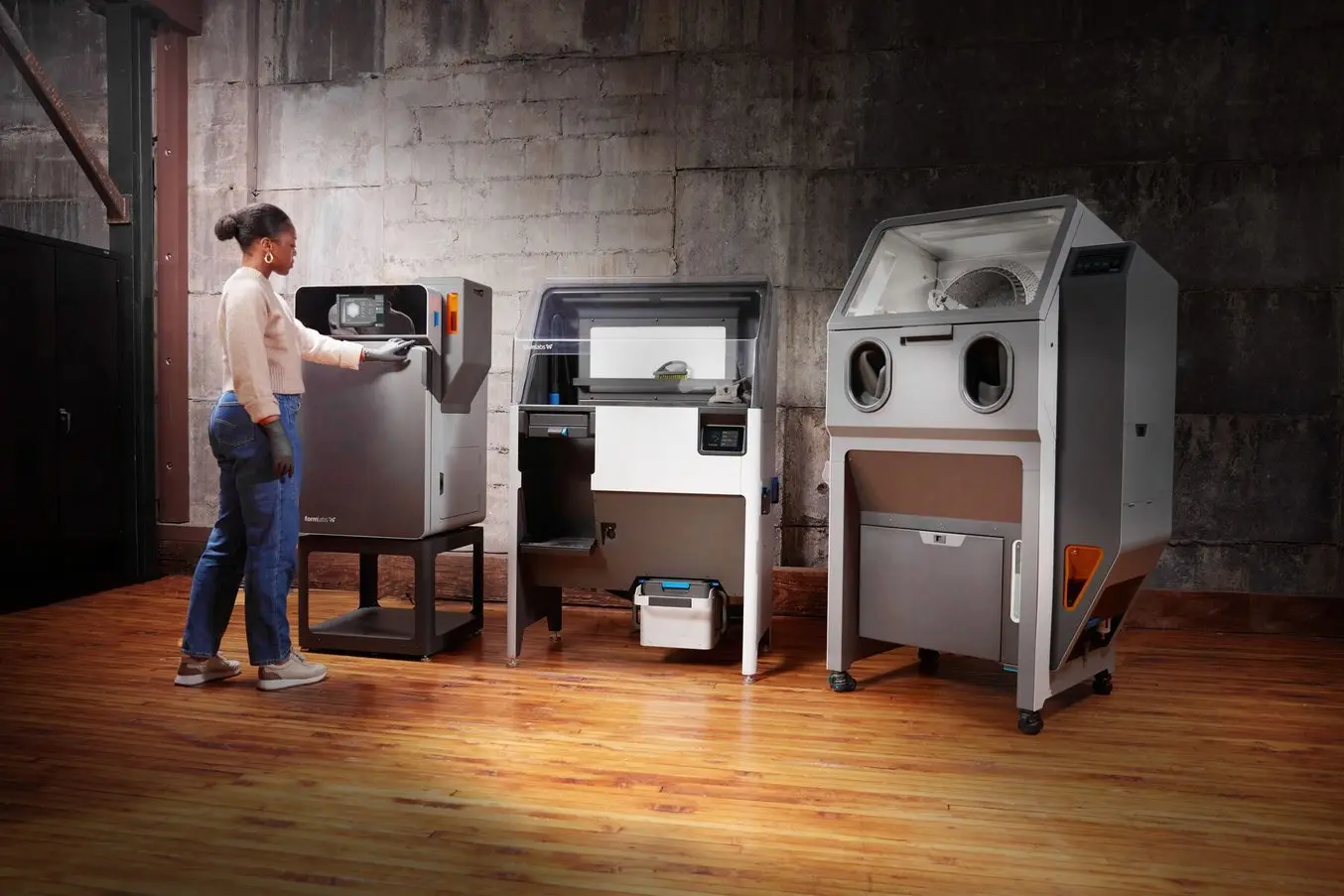
The Fuse Series SLS ecosystem is comprised of the Fuse 1+ 30W printer, Fuse Sift powder recovery station, and automated Fuse Blast media blasting and polishing solution.
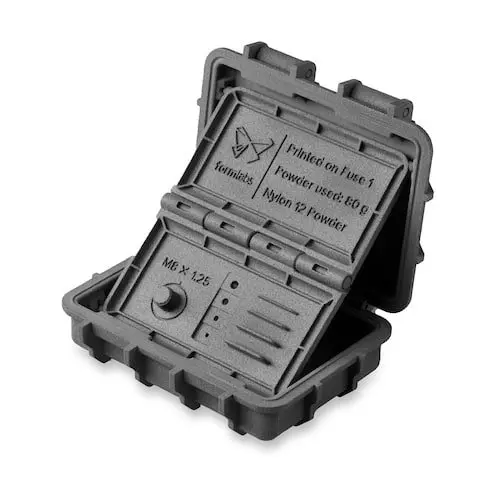
アイウェアの3Dプリントに適した材料
The Fuse Series offers three material candidates sufficient for eyewear production: Nylon 11 Powder, Nylon 12 Powder, and Nylon 12 White Powder. These three materials are thermoplastics, just like acetate, meaning that opticians can heat the frames and temples to better fit the face after printing.
When comparing functional performance against acetate, TR90, and polycarbonate, all three SLS materials are extremely comparable, with Nylon 11 Powder being preferred by some customers due to its superior elongation at break and sustainability benefits.
Cellulose Acetate | グリルアミドTR90** | Nylon 11パウダー | Nylon 12パウダー | Nylon 12 Whiteパウダー | |
---|---|---|---|---|---|
最大引張強さ | 30MPa | 60MPa | 49MPa | 50MPa | 47 MPa |
引張弾性率 | 1700MPa | 1500MPa | 1600MPa | 1850MPa | 1950 MPa |
破断伸び | 30% | 50% | 40% | 11% | 8% |
曲げ強さ | 40MPa | N/A | 55MPa | 66MPa | 56 MPa |
実際の機能試験においても、Nylon 11パウダーの優れた靱性と耐衝撃性が実証されました。
Additional environmental and material properties should be considered when creating a long- lasting, sustainable product that will be exposed to the elements.
酢酸セルロース* | グリルアミドTR90** | Nylon 11パウダー | Nylon 12パウダー | Nylon 12 Whiteパウダー | |
---|---|---|---|---|---|
ISO 10993-10:2010/(R)2014, Tests for Irritation and Skin Safety | Not an irritant | Not an irritant | Not an irritant | Not an irritant | Not an irritant |
Bio-Based Content | >50% bio-based | N/A | 100% bio-based | N/A | N/A |
密度 | 1.3 g/cm3 | 1.0 g/cm3 | 1.0 g/cm3 | 0.99 g/cm3 | 0.95 g/cm³ |
Water Absorption | 2.3% | 3% | 0.07% | 0.66% | 1.40% |
Solvent Compatibility, Salt Water (3 .5% NaCL), 24-HR Weight Gain | N/A | N/A | 0.1% | 0.2% | 0.1% |
Heat Deflection Temperature (HDT) @ 0 .45MPa | 75°C/170°F | 100°C/212°F | 182°C/360°F | 171°C/340°F | 177°C/350°F |
Flammability, UL 94 Section 7 | N/A | HB | HB | HB | HB |
*Source: https://www.makeitfrom.com/material-properties/High-Plasticizer-CA
**Source: https://www.picoplast.nl/uploads/bab8c3f16780cb5b51b67be4baece673Grilamid%20TR90%20LX%20-%20MDS%20-%20EN.pdf
表面品質
Surface finish is highly dependent on model design, and different orientations will yield varying surface finishes. Formlabs has conducted extensive part orientation testing, finding that a 45-degree frame print orientation in Nylon 11 Powder, Nylon 12 Powder, and Nylon 12 White Powder results in the most optimal aesthetic surface finish on an example round frame design. Whichever side of the part is facing towards the bottom of the build chamber will have a slightly smoother surface finish.

Formlabs has found that printing eyewear frames at a 45° angle to the bottom of the build chamber helps ensure the smoothest, most even surface finish.
生産量
When oriented at a 45-degree angle, 77 example frames can fit in the Fuse 1+ 30W build chamber. This scenario offers a 11% pack density and a build time of just 11 hours when using Nylon 12 Powder as of March 2023. Formlabs is continually improving print settings. To recieve an analysis of your own files to determine cost, print time, and ROI, contact our team.

77 eyewear frames packed in PreForm, Formlabs' print preparation software, which can automatically pack files for optimal print density and print time.

PreForm can also calculate material cost, including both sintered powder and the unsintered powder surrounding the parts, to use in total powder cost analysis.
Nylon 12パウダー | Nylon 11パウダー | |
---|---|---|
1回のプリントでの造形数 | 77 | 60点* |
パッキング率** | 10% | 11% |
造形時間 | 11 h | 22 h 30 m |
Max Yearly Production | 36,960*** | 14,000*** |
*The number of parts was reduced to achieve a print time of sub-24 hours, resulting in a higher production throughput. Nylon 11 is also capable of printing 77 frames at one time, but with a >24 hour print time.
** Read more about pack density and refresh rate here.
***Assuming one print per day, five days per week, for 48 weeks a year. A second build chamber is required to quickly change over and start new prints.
Finishing Options
The natural aesthetic finish of both Nylon 11 Powder and Nylon 12 Powder is an opaque gray color with a surface finish rougher than that of polished acetate. Nylon 12 White Powder has a similar rougher surface finish, with a blue-ish white color. To achieve a finish more similar to that of traditional acetate or TR90 eyewear, a variety of finishing options should be considered.

Frames printed in PA11, from left to right: raw off the printer; vibratory tumbled; vapor smoothed; dyed black; dyed blue; white Cerakote.
表面処理の準備
従来のアセテートフレームには木製メディアを使った研磨を施すことが多いですが、3Dプリント製のフレームも数時間のバレル研磨で大きな効果が得られます。Formlabsでは、潤滑剤入りのセラミックメディアを使用した結果、表面の粗さが80%減少し滑らかな手触りになりました。Formlabsがバレル研磨に使用したのは、低コストで使いやすいMr.Deburr 300DBです。
製作期間 | Nylon 11 Powder Surface Roughness Reduction | Nylon 12 Powder Surface Roughness Reduction | |
---|---|---|---|
Ceramic* | 8 h | 80.87% | 82.43% |
Organic** | 24 h | 80.53% | 82.77% |
*Ceramic angle cut triangle shapes, with side dimensions of ¼ inch with Kramco 1010 finishing compound
**Walnut Shell Grit 14/30 Mesh Medium

PA11でプリントしたフレームに表面処理を施したもの:バレル研磨(下)、Cerakote(中央左)、ベーパースムージング(中央右)、Cerakote(上)。

Parts being tumbled in walnut media to smoothen the surface.
着色オプション

Dye can still penetrate the darker grey colors of Nylon 12 Powder and Nylon 11 Powder, but the results can become a bit muted and dark.
A simple and cost-effective option for part coloring is to utilize a water bath dye system. Parts are submerged in a heated water bath with a color dye that penetrates all surfaces of the part, permanently altering the color of the part. Though the grey powders (Nylon 11 Powder and Nylon 12 Powder) can be dyed, printing in Nylon 12 White Powder is the best way to ensure you can achieve a range of vibrant colors.
There are industrial options for dyeing SLS 3D printed parts, like machines from Dyemansion. These can cost tens of thousands of dollars, however, and for small-batch production or prototyping, may not make sense. To learn more about using an inexpensive and effective dyeing method for Nylon 12 White Powder end-use parts, watch our webinar with engineer and product designer Ken Pillonel.
Formlabs also utilizes Cerakote coating to both improve the mechanical properties of the part and enable a wide variety of colorways. Cerakote is a thin-film ceramic coating that ranges in thickness from 0.00635 mm to 0.0254 mm and does not require a primer. Once applied, SLS 3D printed parts can expect an improvement in chemical and scratch resistance. Cerakote can also be used to achieve a glossy surface finish, with colors ranging from pastels to metallics and everything in between. Additionally, once coated, parts can be laserimaged to achieve interesting patterns or to carry information, such as logos or serialization. Cerakote can also be used to achieve a glossy finish, through their customizable gloss curing schedules.

Nylon 11パウダーで造形しCerakoteHシリーズでコーティングしたフレーム。
Hydro dipping is also achievable with SLS 3D printed parts. Similarly, varnishing and pad printing processes are compatible with SLS technology. Lastly, vapor smoothing is a process to chemically seal and smooth the surface of SLS 3D prints. Vapor smoothing offers an injection molded-like surface with greatly improved surface roughness, as well as resistance to moisture and bacteria growth, while enabling glossy surface finishes. Formlabs utilizes Additive Manufacturing Technologies (AMT) to vapor smooth eyewear components. Additionally, parts can be dyed in a water bath before or after vapor smoothing, thus sealing in the new part color with additional glossiness.

Vapor smoothed eyewear frames.
Try It Yourself
While Formlabs has explored and developed many finishing options to improve the surface finish of SLS 3D printed parts, there are still many more avenues not yet explored. Many customers have had success with ordering a free custom sample part of their eyewear and then applying their own proprietary finishing techniques (different tumbling media, varnishing, coatings, etc) to achieve unique aesthetics. Contact our sales team to order a free sample of your own design, or order a standard Nylon 11 Powder, Nylon 12 Powder, or Nylon 12 White Powder sample part on which to try confidential or proprietary finishing techniques.
アイウェア業界における3Dプリントのその他の活用例
In addition to its production capabilities, the versatility of the Fuse 1+ 30W system allows for other applications to drive value in the eyewear industry.
プロトタイピング
Both the Fuse Series and the Form Series system can be used to prototype eyewear to test for dimensionality, fit, and overall design. Choose nylon materials on the Fuse 1+ 30W system to create functional prototypes that can be worn and tested for long periods of time. Choose the Form 4 or Form 4L system to create aesthetic prototypes that demonstrate looks-like designs with translucency similar to acetate and polycarbonate. SLA printed prototypes can be worn for weeks at a time, but are not suitable for long-term wear unless applied with a UV-blocking coating.

Plastinax uses the Form Series SLA printer to produce looks-like prototypes for semi-translucent materials.
ユーザーテスト
Utilize the Fuse 1+ 30W to create eyewear that can be tested and evaluated during lifetime and user testing to quickly gain feedback and iterate on dimensions and design.

Plastinax designs their custom eyewear frames in Fusion 360 and then prints them directly on the Fuse 1+ 30W SLS 3D printer.

Nylon 12 Powder frames designed and printed by Plastinax.
スマートアイウェア
3Dプリントでは、複雑なデザインも無料で実装できます。電子機器のハウジングやウェアラブル用の複雑なアセンブリを追加しても、3Dプリンタ以外のコストはかかりません。他の工法ではコストが高く複数割の金型が必要になるようなスマートアイウェア用の複雑なエンクロージャには、SLS 3Dプリントの使用をご検討ください。
治具や固定具
Due to their high impact resistance, Nylon 12 Powder, Nylon 12 White Powder, and Nylon 11 Powder are well-suited for custom jigs and fixtures. Formlabs nylon powders are strong enough to bend some metals used in traditional frames and temples, such as titanium, with pressures of more than 90 kg.
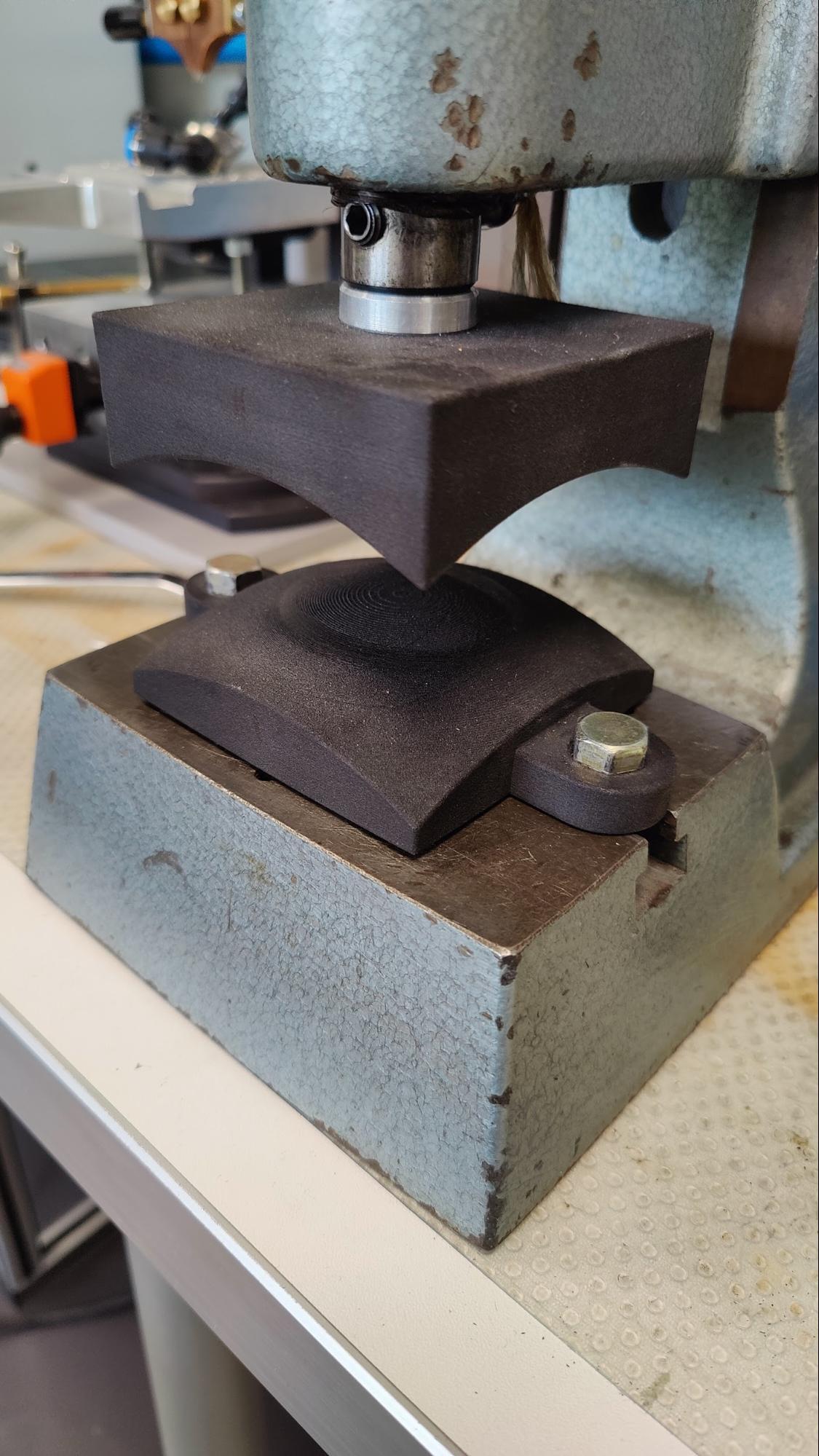
トグルプレス機に設置されたNylon 11による3Dプリント製成形型。
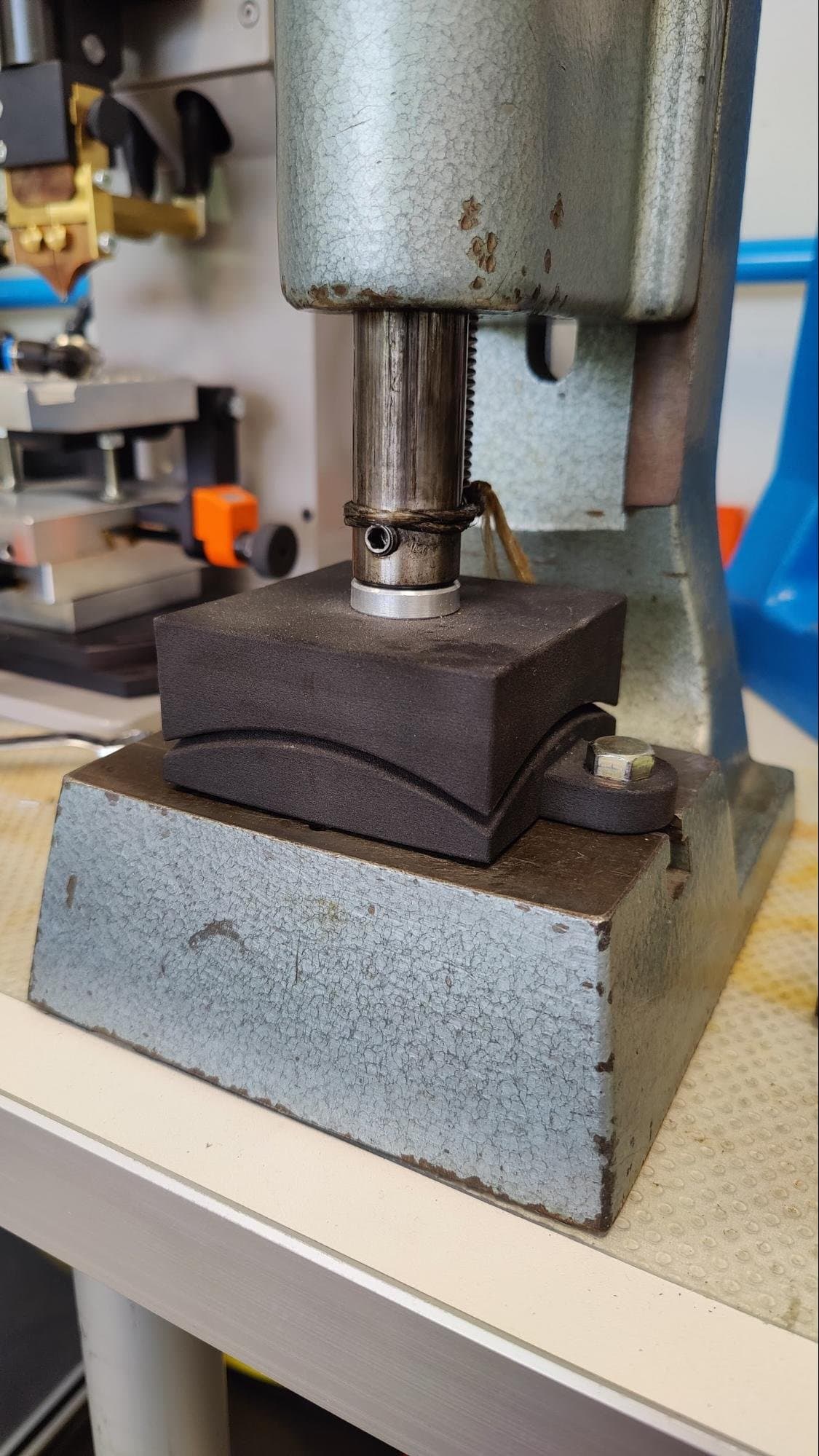
射出成形と真空成形による少量生産
Due to their high impact resistance, Nylon 12 Powder, Nylon 12 White Powder, and Nylon 11 Powder are well-suited for custom jigs and fixtures. Formlabs nylon powders are strong enough to bend some metals used in traditional frames and temples, such as titanium, with pressures of more than 90 kg.

トグルプレス機に設置されたNylon 11による3Dプリント製成形型。

3D printed molds for vacuum forming packaging made with Rigid 10K Resin.
Building a Business Case
A New Wave of Independent Manufacturing
Owning a business or creating a new product line enabled by 3D printing is becoming more obtainable and cost-effective by the day. A single Fuse 1+ 30W 3D printer can enable a production run of 19,000+ frames per year or 50,000+ temples per year on an unoptimized five-day production schedule.
Nylon 12 Powder Frames* | Cost Per Part** | |
---|---|---|
Fuse 1+ 1台 | 36,960 | $1.27 |
Fuse 1+ 5台 | 184,800 | Contact for Pricing |
Fuse 1+ 10台 | 369,600 | Contact for Pricing |
Nylon 12 Powder Temples* | Cost Per Part** | |
---|---|---|
Fuse 1+ 1台 | 87,840 | $0.29 |
Fuse 1+ 5台 | 439,200 | Contact for Pricing |
Fuse 1+ 10台 | 878,400 | Contact for Pricing |
* Assuming a five day workweek with five prints per week, for 48 weeks a year.
**Material cost set at $69/kg, a 30% discount, typical for customers printing in this quantity.

These temples (both left and right) are ideal for printing efficiently, with a pack density of 31%, ensuring that all unsintered powder can be recycled into the next build, reducing cost per part significantly.

These eyewear frames don't pack as densely as the temples, leading to a slightly worse refresh rate and a higher cost per part. However, just one printer can still produce nearly 20,000 frames every year cost-effectively.
オプション1:社内に内製環境を整える
The most efficient and cost-effective way to produce 3D printed eyewear is to own the production equipment. This entails purchasing a Fuse Series SLS ecosystem. The benefits of vertically integrated 3D printing production include achieving faster ROI, tighter control over quality, agility to alter design and move from prototyping to production on the same machine, and the ability to utilize the ecosystem for other purposes, such as creating jigs and fixtures.
Designed to be as accessible as possible, the Fuse Series SLS ecosystem is extremely plug-and-play, with most users learning how to operate the equipment in a matter of hours. Similarly, the ecosystem has minimal facility requirements, allowing for quick installation and easy scalability as demand grows. It’s also important to note that a new Fuse Sift or Fuse Blast are not required with every additional Fuse 1+ 30W printer. Most customers keep a ratio of 4:1, printers to post-processing stations. The cost to incorporate a full Formlabs SLS printing ecosystem, including a Fuse 1+ 30W, a Fuse Sift post-processing unit, Fuse Blast media blaster, two build chambers, two cartridges, 20 kg of Nylon 12 Material, and two years of expert customer support is $64,190.

With the Fuse Series, it's easy and efficient to scale up as demand grows.
オプション2:受託メーカーへ外注
The most efficient and cost-effective way to produce 3D printed eyewear is to own the production equipment. This entails purchasing a Fuse Series SLS ecosystem. The benefits of vertically integrated 3D printing production include achieving faster ROI, tighter control over quality, agility to alter design and move from prototyping to production on the same machine, and the ability to utilize the ecosystem for other purposes, such as creating jigs and fixtures.
Designed to be as accessible as possible, the Fuse Series SLS ecosystem is extremely plug-and-play, with most users learning how to operate the equipment in a matter of hours. Similarly, the ecosystem has minimal facility requirements, allowing for quick installation and easy scalability as demand grows. It’s also important to note that a new Fuse Sift or Fuse Blast are not required with every additional Fuse 1+ 30W printer. Most customers keep a ratio of 4:1, printers to post-processing stations. The cost to incorporate a full Formlabs SLS printing ecosystem, including a Fuse 1+ 30W, a Fuse Sift post-processing unit, Fuse Blast media blaster, two build chambers, two cartridges, 20 kg of Nylon 12 Material, and two years of expert customer support is $64,190.

Service bureaus can be good options for initial tests and proof of concept.
Get Started With 3D Printed Glasses and Eyewear
Eyewear presents an exciting application for SLS 3D printing. Eyewear manufacturers make adjustments on things as big as material choice or as small as micron-level differences in lens thickness. As resolution, accuracy, material versatility, and finishing processes for 3D printing become more advanced, the technology presents a costeffective method of designing and manufacturing eyewear. With the Fuse Series SLS ecosystem, eyewear designers and manufacturers have an option to prototype faster than ever and produce end-use products without outsourcing or using a tooling manufacturer. SLS 3D printing can help businesses bring the entire design to production workflow under one roof, reducing costs and increasing efficiency.
To learn more about the Fuse Series, visit our website. To test one of our nylon powders for yourself, request a free SLS 3D printed sample.