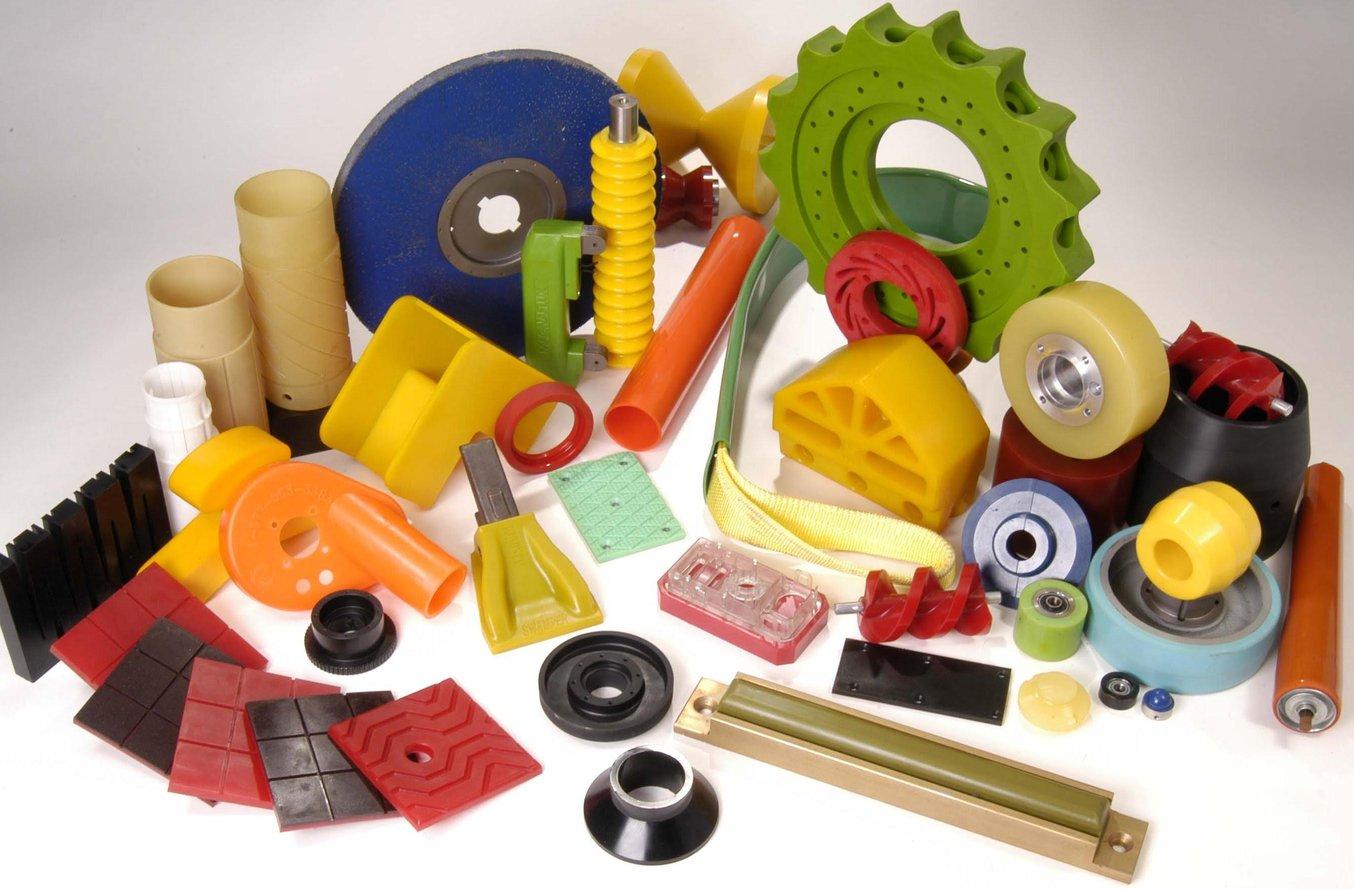
組立ラインのコンベアローラー、ジェットコースターのブレーキパッド、戦闘機を固定するホイールチョックなど、製品として欠かせない要素でありながら、見落とされがちなポリウレタン部品の数々。製品名を聞いてすぐに思い浮かぶ部品ではないかもしれませんが、ポリウレタン部品はシステム全体としての動作に欠かせない重要な部品です。より大きなアセンブリの一部としてスムーズに機能するよう、ポリウレタン部品の設計には最適な材料使用量、厳しい公差要件、長時間の負荷にも耐えられる耐荷重性や変形といった様々な考慮が必要です。
イリノイ州のポリウレタンメーカー Kastalonは、何十年にも渡って問題解決を繰り返しながら、多様な要件を満たすカスタム品のポリウレタン部品を数多く製造してきました。私たちは同社のプロダクトエンジニア Brian Baer氏にお話を伺い、大容量SLA光造形3DプリンタのForm 3Lが成形型や治具の製作、新製品の研究開発にもたらす新たな可能性についてお話を伺いました。
「成形型を3Dプリントで製作できるというのは、特に設計上の細かな変更や調整に即座に対応できるという点で非常に大きなメリットになります。±.005の公差要件を達成できるのも心強いですし、これまで不可能だったことが可能になり、製造量も着実に伸びています」
エンジニア、Brian Baer氏
Kastalonが実現する、3Dプリントと従来製法の融合
Kastalonでは、数十万点ものポリウレタン部品の製作に必要なカスタム成形型を、何百点も設計・製造しています。 これまで、顧客から実製品用部品の注文を受けると、その部品用の成形型の製作可否を評価してから、実際にアルミやスチールを加工して型を製作していました。
成形型の製作にかかる費用が高すぎたり形状が複雑すぎたりした場合、他の多くのプラスチックメーカーと同様、Kastalonも成形型の製作が難しい部品や、短期製造・試作品製作目的ではコスト効率が悪い部品などは注文を断らざるを得ませんでした。連結部分や細かな溝、ピンの数が多い金型は設計や加工が非効率になりやすく、時には完全にやり直しが必要になる場合もあるからです。それでも、注文を断るというのはやはり難しい決断です。そこで、学生時代に様々な3Dプリント方式を学んだ経験のあるBaer氏が、成形型を製作する他の方法を模索し始めました。
同社チームの中には、数年前に3Dプリントを試して苦い経験をしたことのあるメンバーが数人おり、Baer氏は特定の要件にマッチする製品を探さなければなりませんでした。彼らが必要としていたのは、±.005インチという厳しい公差要件を満たしながら、成形時には180〜300°Fほどの高温にも耐えられる材料が使用でき、さらに価格帯が手頃な3Dプリンタです。
「Formlabsの製品を知り、高温にも耐えられて非常に特殊な要件も満たせる幅広い材料が使用できるとわかるまでは、[我々の用途で]3Dプリンタを実際に導入できるとは思っていませんでした」
エンジニア、Brian Baer氏
2022年末にKastalonのオフィスにForm 3Lが到着してから、全員が3Dプリントの実力を実感するまで何度かテストを重ねました。最初は使用できる材料や公差要件への適応性に懐疑的だった同僚たちも、Baer氏が3Dプリントしたサンプル品を見て考えが変わります。Baer士はその時の様子をこう教えてくれました。「サンプル品をプリントして機械工場に渡し、彼らが表目粗さ(RA)テストをしたんです。工場長は、私が渡した製品仕様と一致する結果が出たこと、そして部品の滑らかさに非常に驚いていました」
また、今では工場長が加工のためではなく3Dプリントのために真っ先に部品を送ってくる、とも付け足します。「応用できそうな注文があった時に、真っ先に3Dプリントを推奨するメンバーの一人が工場長なんです。工場は他の大型案件で大忙しですから、小型部品で3Dプリントできるものがあれば可能な限り3Dプリントで対応し、工場に余裕を持たせたいんです」とBaer氏は言います。
形状、検証、運用で生まれる新たな可能性
3Dプリントでポリウレタン成形に新たな選択肢を切り拓きます。Kastalonのエンジニアリングチームは、3Dプリントのおかげで金型では実現できない新しいデザインや形状を試せるようになっただけでなく、設計に細かな変更が発生した場合でも加工済みの金型を無駄にする心配をせずに変更点を反映できるようになりました。また、細かな変更を加えても加工場の作業が止まる心配がなくなり、徹底的に試作・検証を繰り返せるようになったことで、自信を持って新しいデザインを打ち出すことができます。
3Dプリントで実現する、テールプラーのクランプ成形型
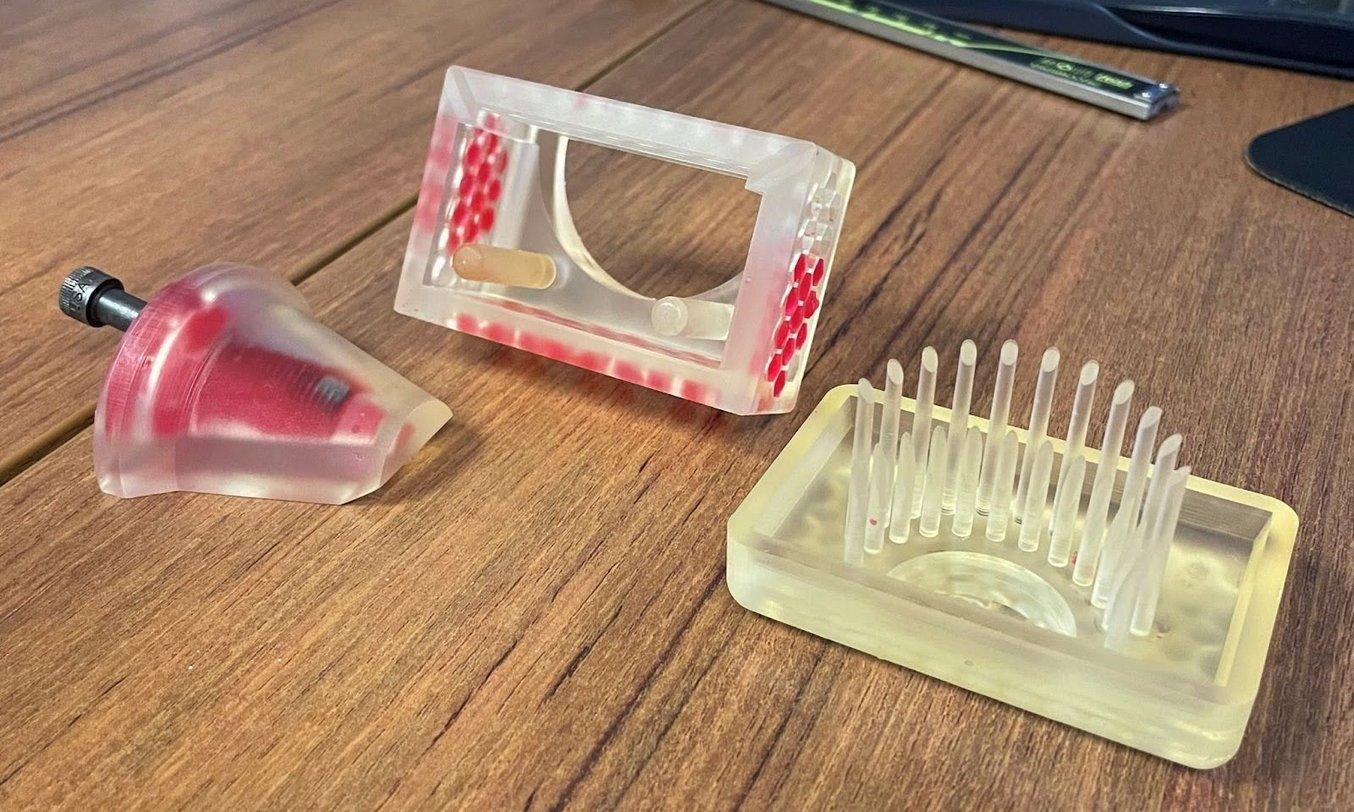
Kastalonはこれまで、上面からオフセットした止まり穴が24個ある部品は、加工による成形型の製作が難しすぎるために注文を断らざるを得なかった。
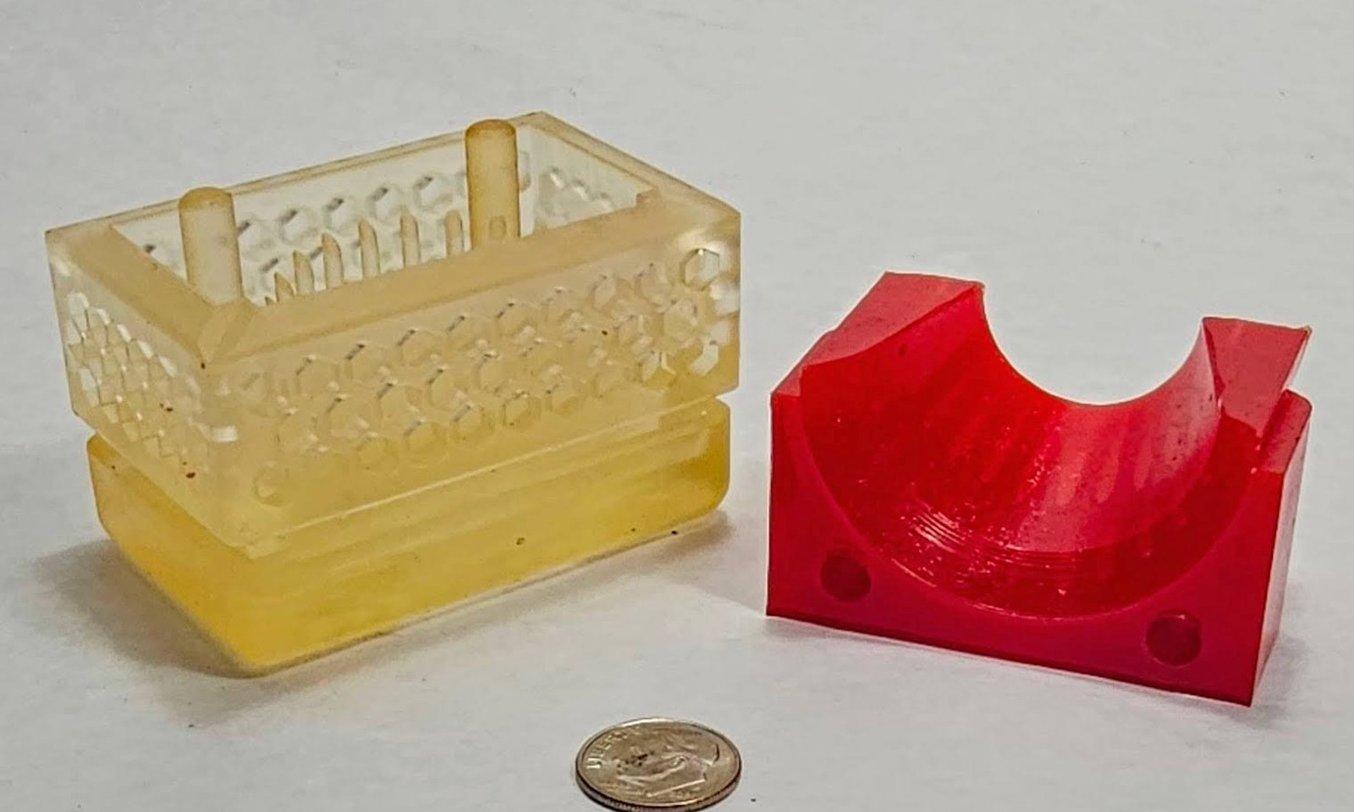
Form 3LとHigh Tempレジンの活用で、Baer氏は僅か1日以内で型の3Dプリントからポリウレタン部品(右)の製作を終えることができた。
Form 3Lを導入する前は、テールプラーのクランプ成形型で作る部品の注文は断らざるを得ませんでした。何度も試行錯誤を重ねれば実現できたかもしれませんが、24個の長いピンを貫通させず、さらにピン同士の間隔は0.03125インチ以内に収める必要があったためです。
ピン同士の間隔が非常に狭いことと、穴を貫通させず、上面からのオフセットがそこで終わるという設計上、部品の加工が非常に難しく、繊細で長い刃が必要になります。他には、ピンをそれぞれ個別で製作し、後からすべて正しい方向に整列させて固定するという方法もありますが、ピンの直径が0.104インチしかないことを考えるとこれも大変な作業です。
様々な加工法を評価した結果、同社チームはこの注文を断るしかないという決断に至りました。「長い時間をかけて実現できる方法がないか協議しましたし、顧客にこの部品は作れませんと言うのは非常に勇気のいる決断です」とBaer氏は振り返ります。
その数週間後に到着したForm 3Lを使って、Baer氏はその成形型を僅か半日で設計・プリントし、このように複雑な形状でも3Dプリントなら実現できるというビジネスケースを実証しました。材料コストは$30を僅かに超えるのみで、設計も2時間程度で完成しました。「すぐに、全員が3Dプリントの可能性を見直しました。工場の作業員も考えが変わり、『こんなことができるようになるなら、もっと注文を受けられるようになる』と言っていました」
アンチクラッシュホイール
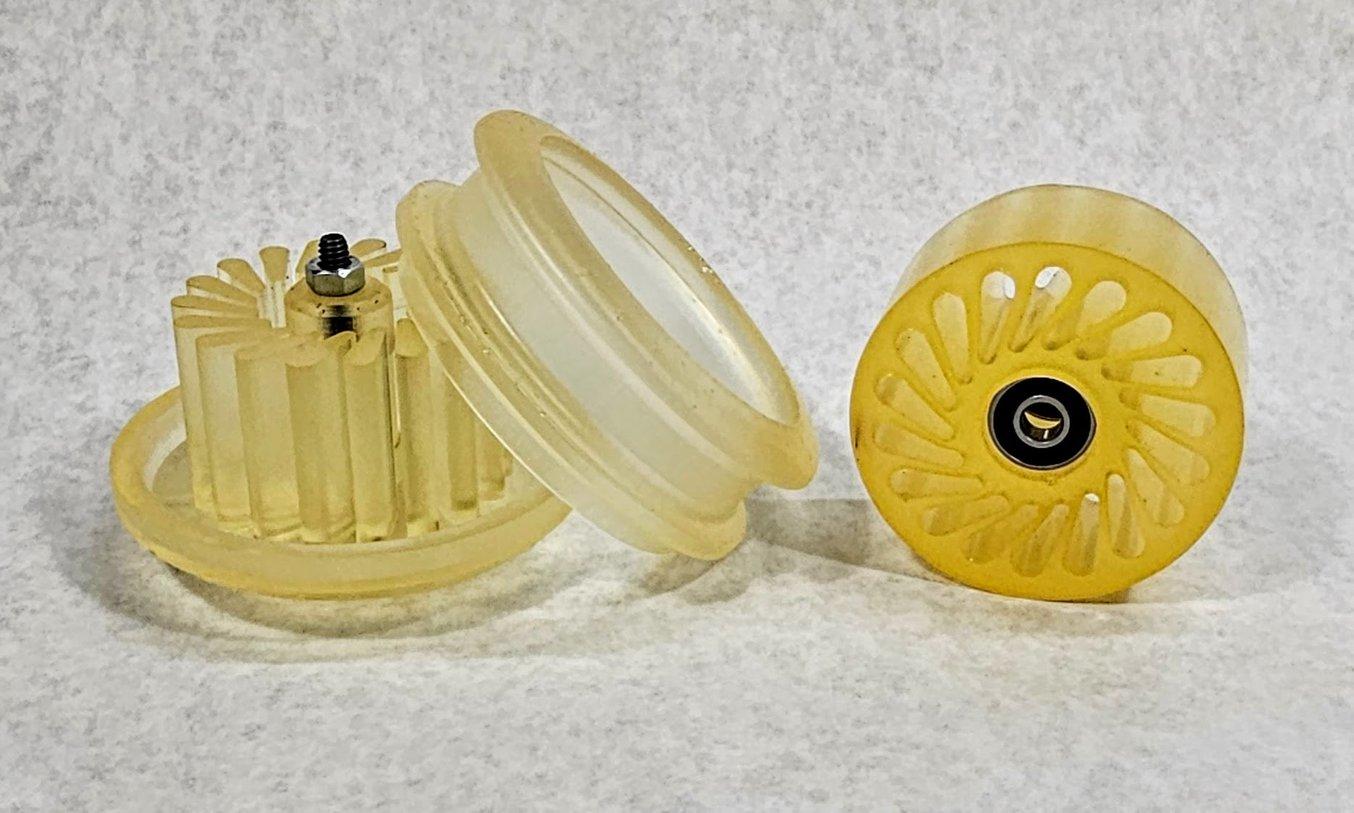
ホイール用の成形型(写真左、上、下)と成形したホイール(右)は、過度な負荷かかった際に均等に変形するよう設計されている。雫型の空洞が荷重を均等に分配し、ホイールが製品を押しつぶさない仕組みになっている。
Form 3Lは、細かな工夫が必要な設計のために加工では実現が難しい成形型の製作に最適です。写真の小型のアンチクラッシュホイールは、スプリングアセンブリの代わりとして、柔らかい製品(ダンボールの梱包資材など)をベルトコンベア上で押さえる役割を果たします。バネ式のアームでダンボールに圧力をかけるのではなく、ホイール自体が均等に変形することでダンボールを所定の位置で優しく押さえます。
しかし、このホイールを作るための成形型は従来の方法では製作がほぼ不可能でした。ホイールに複数空いている雫型の空洞を成形するために使う「フィン」の間隔が非常に狭いためです。
ホイールの幅は2インチほどで、フィン同士の間の壁の厚みは僅か0.125インチです。「深さが2インチでフィン同士の間隔が0.125インチというのは不可能ではないかもしれませんが、この設計を送ったら工場の人たちは怒るでしょうね」とBaer氏は言います。
加工が難しいだけでなく、分割式のアルミ成形型を使用する場合は組立工程がさらに複雑になります。トレードオフとして、フィン同士の間隔の加工が非常に難しくなることを承知でフィンも一体型になった成形型(上の画像参照)を作るか、すべてのフィンを個別に製作して後で組み立てるか、の選択肢がありますが、後者の場合も準備や小型部品の組立作業が増えるために結局は工場の作業量やフラストレーションが高まることになります。
そこで、3Dプリントが最も合理的なオプションになったのです。Baer氏は、取り外し可能なベアリングをつけた二つ割の成形型をSolidworksで設計し、High TempレジンとRegid 10Kレジンを使ってForm 3Lでプリントしました。Rigid 10Kレジンを使用したことで、金型製作にかかっていたであろうコストに比べてほんの僅かな金額で顧客向けに25個のホイールを製作できました。「極小のホイールを、バリエーションやスタイルを様々に変えていくつも製作しました。Form 3Lの導入前であれば、コスト効率が悪くて実現できなかったでしょう」とBaer氏は言います。
加工 | 3Dプリント | |
---|---|---|
部品数 | 21 | 3 |
設計時間 | 7時間 | 3時間 |
準備時間 | 5時間 | - |
製作時間 | 35時間 | 12時間 |
合計時間 | 47時間 | 15時間 |
大型スプリングの社内検証用成形型
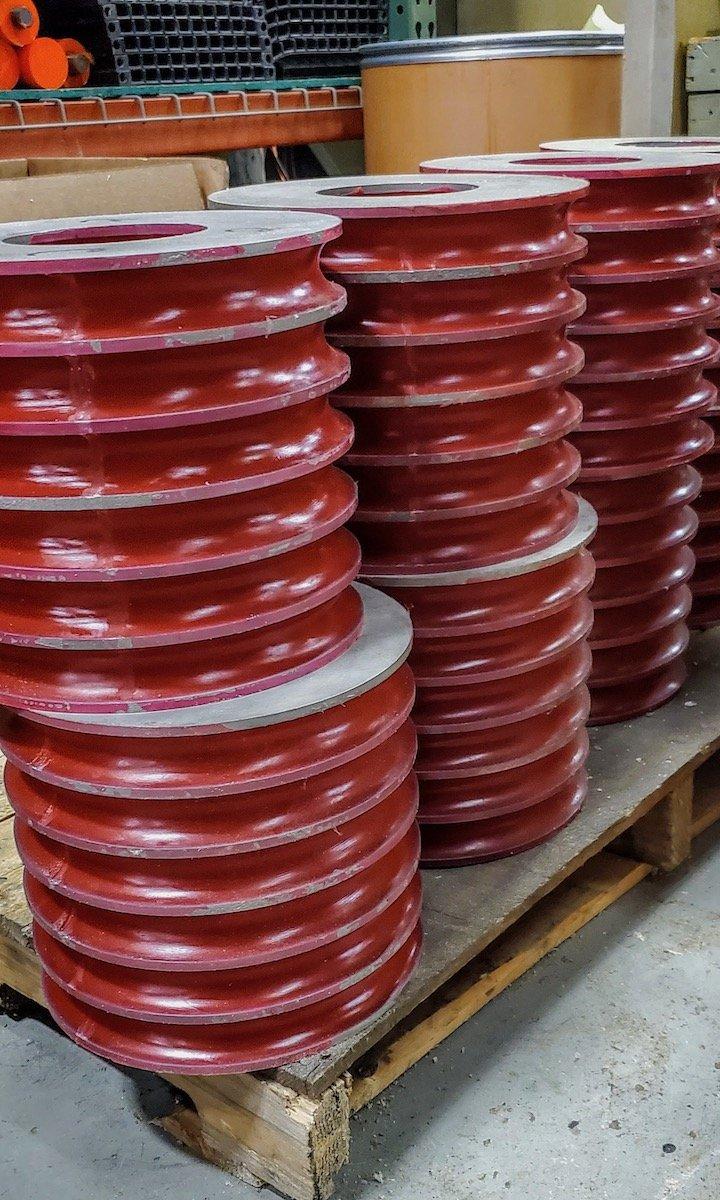
写真の赤色のスプリングのように、ポリウレタン部品は従来、大型のアルミ型を使って鋳造していた。
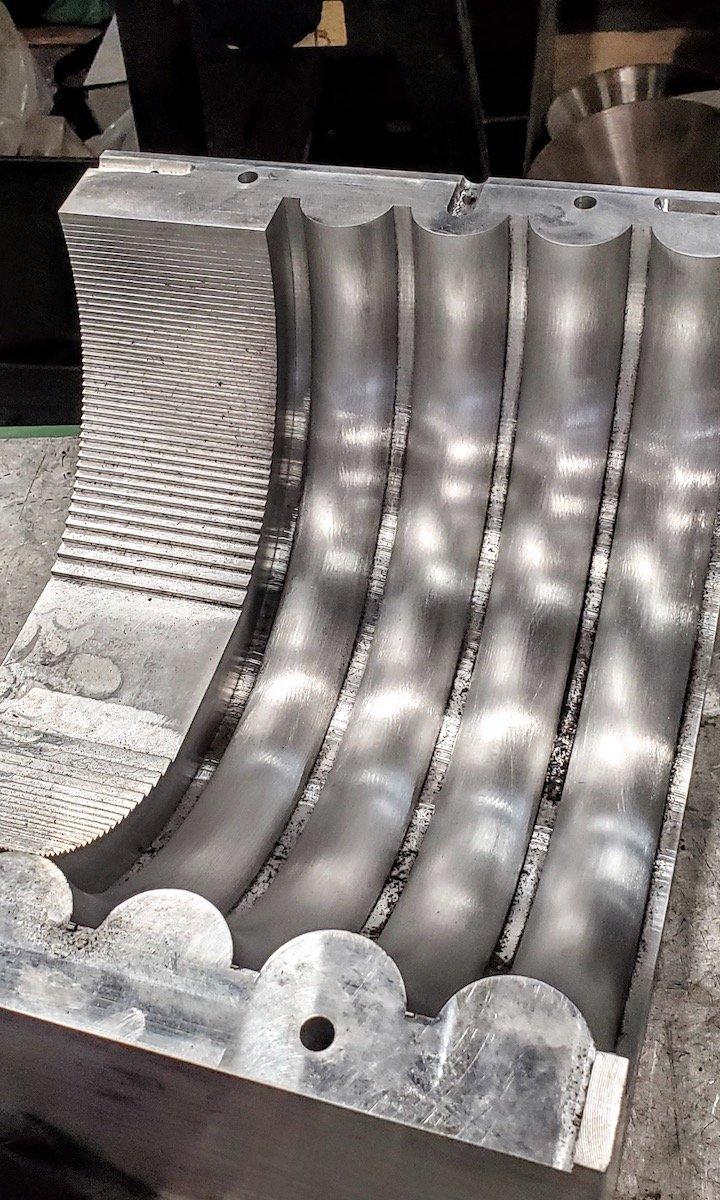
アルミやスチールを使った成形型は高額で、加工にも時間がかかる。
ヒューストン・アストロズの本拠地球場には、悪天候の時に使用する開閉式のドームが備えつけられていますが、ハリケーンでもドームの張りと機能性を維持できるスプリングの製作を担当しているのが、Kastalonです。
Kastalonは、実際にスタジアムで使用する巨大なスプリング用の成形型を製作する前に、まず縮小版の部品を作り設計や使用材料の検証を徹底的に行いました。実製品が長時間過度な負荷に晒されても耐えられる最適な設計にするため、細かな変更を加えながら、様々な形状やポリウレタンの配合でスプリングレート(ばね定数)の変化を検証しました。
社内検証で使用する場合には特にそうですが、検証用にサイズを小さくしているとはいえ、アルミ型はやはりコストが嵩みます。Form 3Lを導入した今、同社はスプリングの様々な設計を遥かに低価格で、そして工場の稼働を独占してしまうことなく検証できるようになりました。
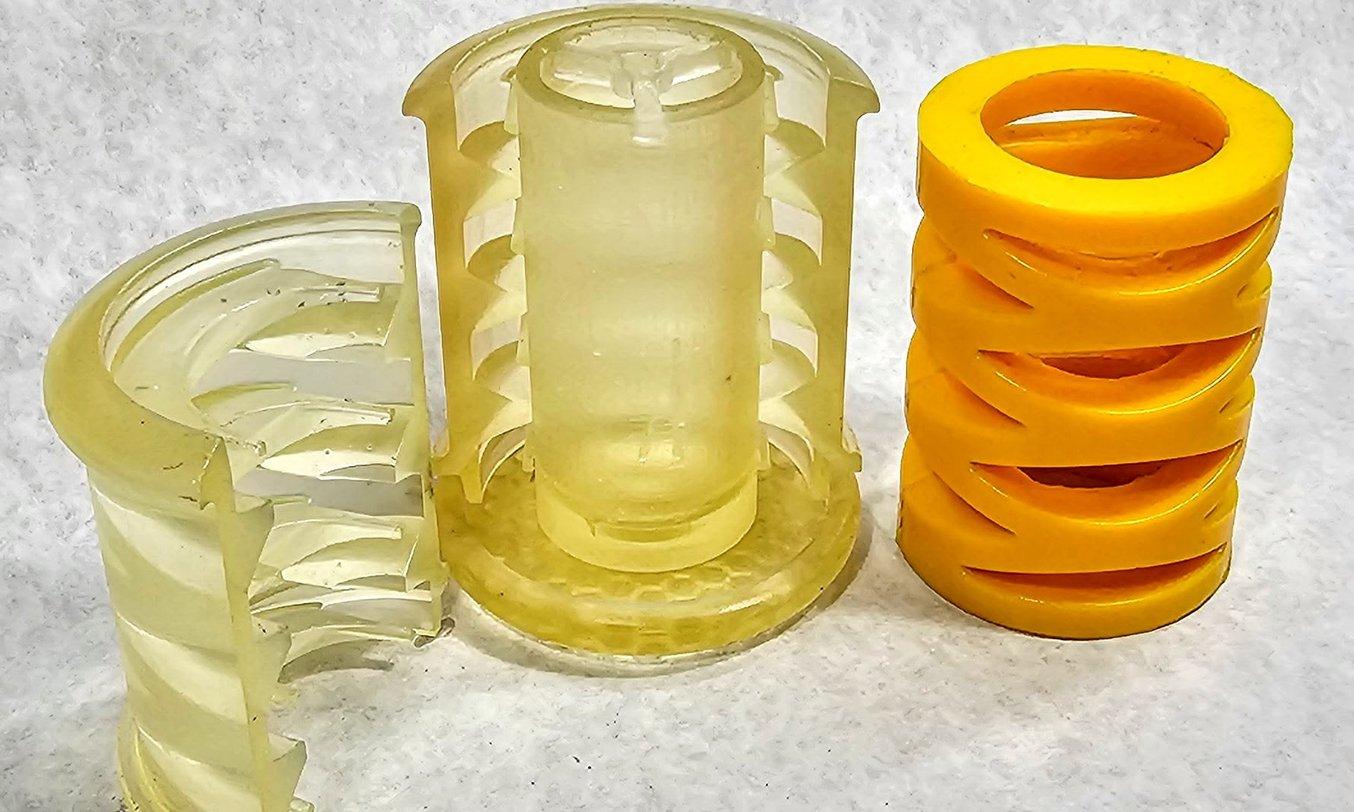
成形型(写真左、High Tempレジン使用)とポリウレタンを鋳造して作ったスプリング(写真右、オレンジ色の部品)は、ディスクスプリングの形状を複製した試作品。
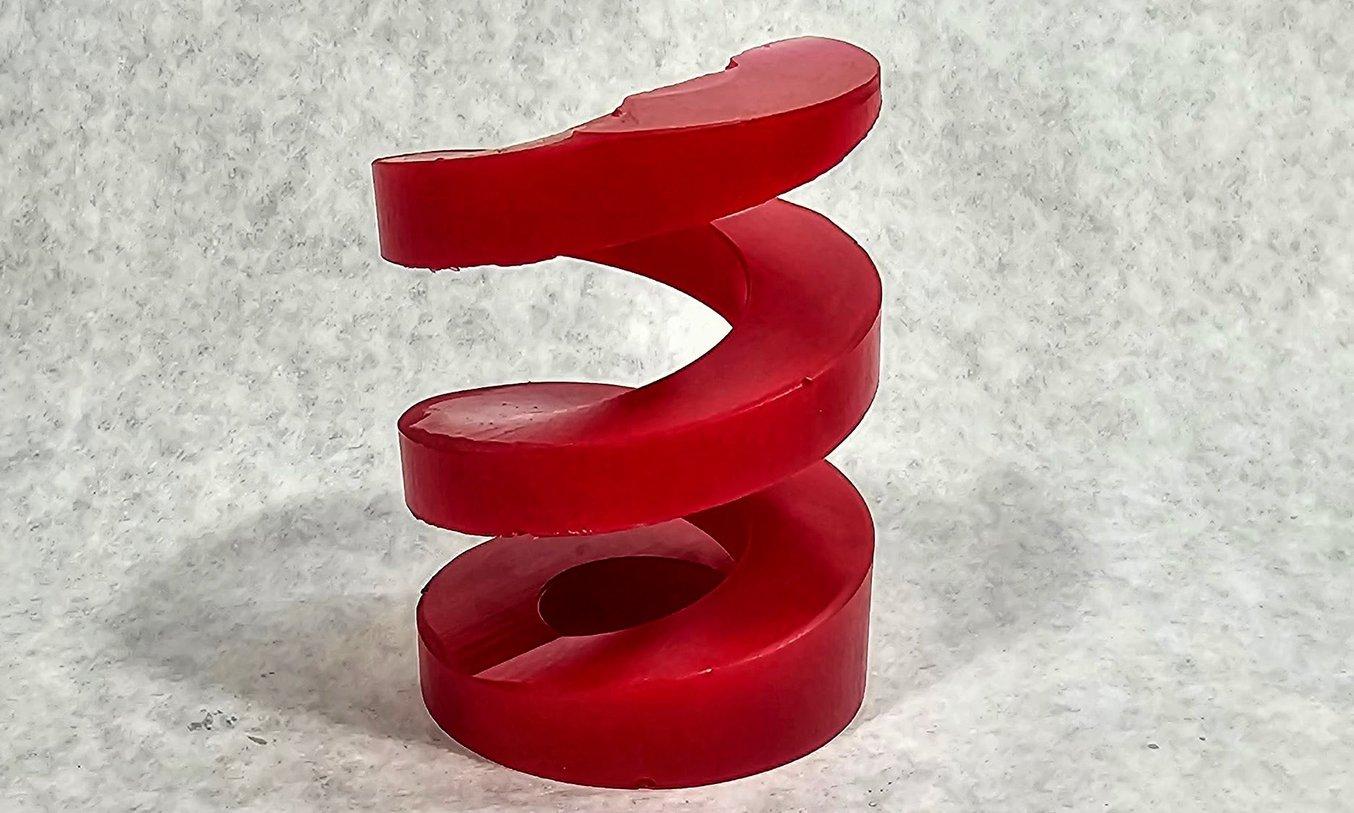
3Dプリントの導入により、Baer氏率いるチームは工場の作業量を増やすことなく新しい形状や設計を試せるようになった。
Baer氏はこう言います。「ちょっと変わった様々な形状も3Dプリントして検証できるようになりました。3Dプリントの導入前であれば、検証や研究開発のためだけに莫大な費用がかかっていたところです」新しく、複雑な形状も加工に高額な費用や膨大な作業量を費やすことなく検証できるようになったことで、Kastalonはより多くの注文を受けられるようになっただけでなく、既存顧客向けにより良い部品を提供できるようになっています。
ローラー用の成形型:軟質ポリウレタン部品の加工を不要に
コーティング済みのローラーやローラー用のスリーブなどを製作する場合、従来の製法ではポリウレタン材料を筒状に鋳造し、希望のサイズや表面品質に仕上げるために外径を加工で削り落とす工程が必要でした。加工で溝を削るステップでは、ローラーの用途によって様々な形式やサイズが採用されます。 今回のケースでは、軟質のポリウレタンに対して横方向に長い溝を加工する手強い作業です。大型注文の場合、このような手作業かつ負荷の高い加工作業は注文の利益率を下げることになり、かつ工場での作業に膨大な時間がかかります。「軟質のポリウレタンを加工する場合は周りが散らかりやすく、必ずしも良い仕上がりになるとは限らないのです。切断した後の仕上がりもいつも綺麗にはいきません」とBaer氏。
加工で直接溝を削る作業は、ローラー1つに対して3時間ほどかかる作業です。しかし、これを一体型の金型として加工するには費用もリスクも高すぎます。このような形状の成形型をこれまでに作ったことがなく、成功するかどうかが定かでない場合には尚更です。金型を作るには、ワイヤーツールかインデックスヘッドのついたシェーパーが必要ですが、どちらも特定の形状や用途に特化した高価な装置です。
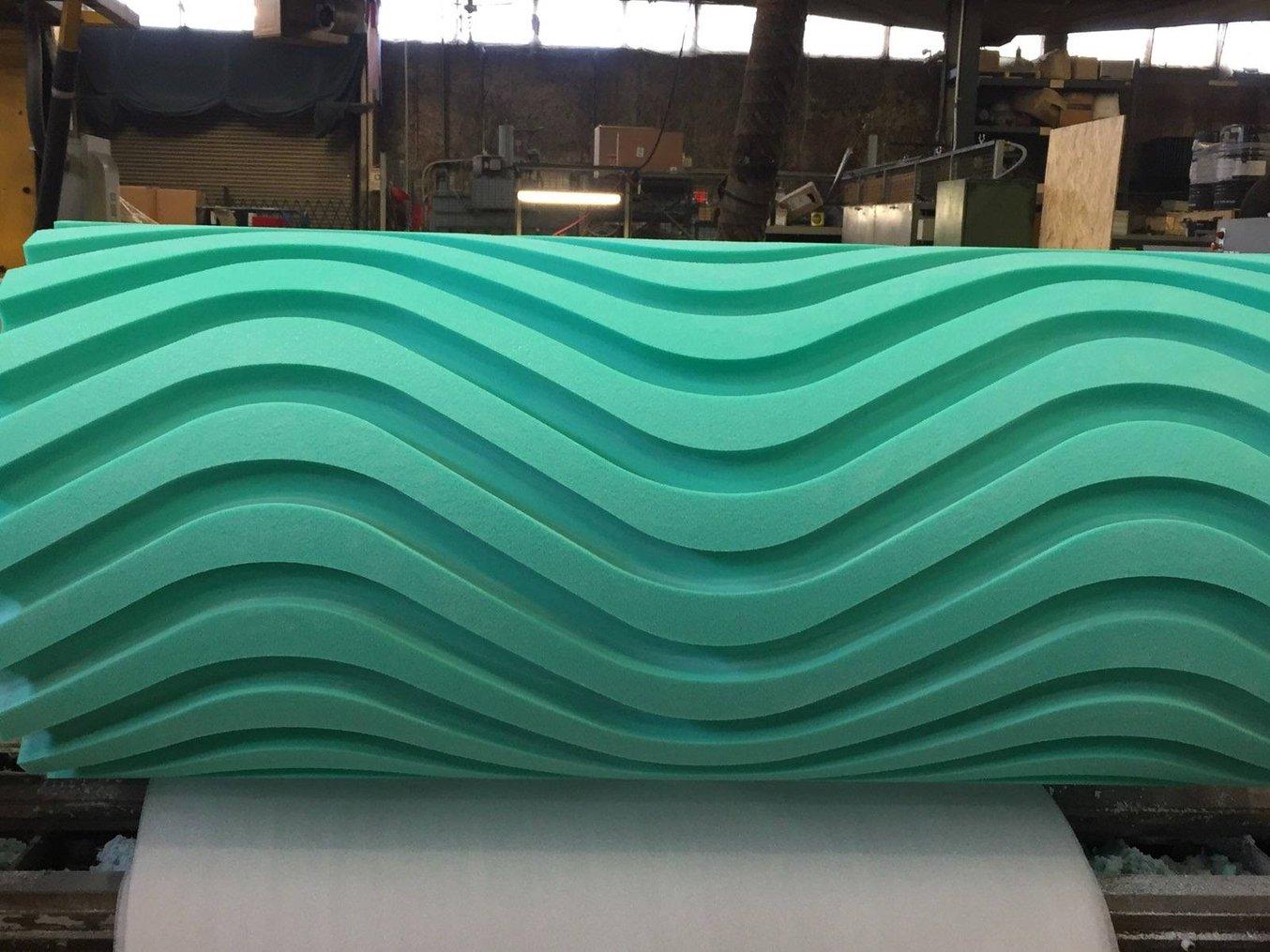
軟質のポリウレタンを加工する場合、散らかりやすく時間もかかる。特に写真のようなローラーを加工する場合は、筒状に鋳造してから完成形にするまでにさらに加工が必要。
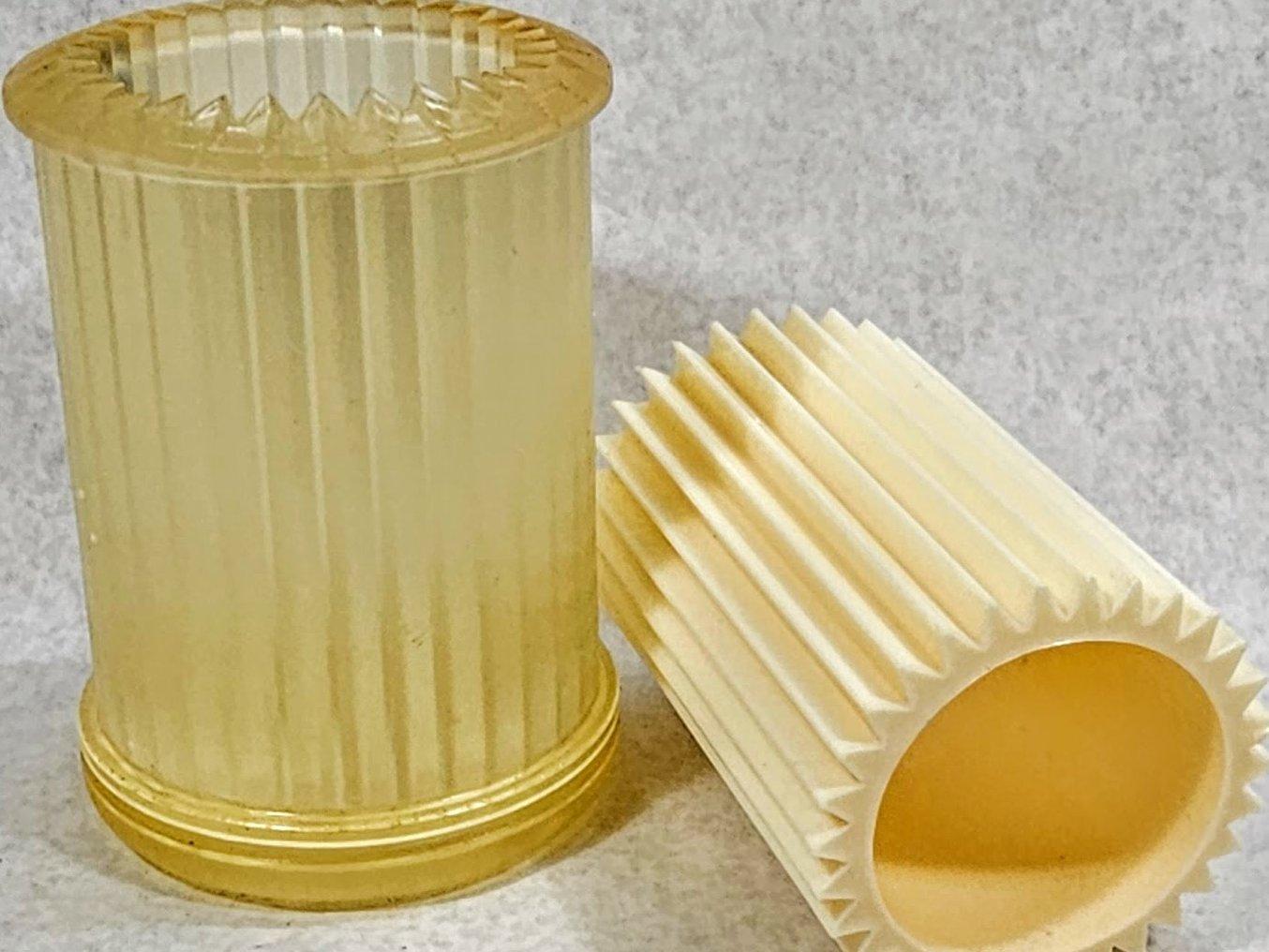
小型部品の場合、細かな溝を加工で作ることはほぼ不可能。Baer氏は、あらかじめ溝をつけた状態の成形型を3Dプリントで製作し、加工作業を排除することに成功。
Baer氏はこの状況を把握し、新しい挑戦をするチャンスと捉えました。ポリウレタンの鋳造時に予め溝をつけられるような成形型を設計・3Dプリントしたのです。Form 3LにてHigh TempレジンとRigid 10Kレジンを使って直接プリントしたことで、コスト効率良く、手作業で何時間もかかる作業を排除することに成功しました。
材料選定の際にBaer氏が重視しているのは、高精細さと積層ピッチ、リットルあたりのコスト、強度、色や透明度などですが、ほとんどの場合はHigh TempレジンかRigid 10Kレジンのいずれかを選ぶことになります。試作品や1回限りの製作、非常に数量の少ない成形型などの製作には、価格が安い透明材料のHigh Tempレジンを選びます。試作品用途では、設計変更などの必要性を確認するためにも、部品の中の様子が見える透明材料が便利なのです。一方、大量に鋳造される部品などには、優れた材料特性を持つRigid 10Kレジンを使用します。「最近では、離型時の荷重にも耐えられるRigid 10Kレジンをメインで使うようになっています」
加工 | 3Dプリント製の成形型 | |
---|---|---|
年間生産数 | 40 | 40 |
成形型の準備時間 | 1時間 | 1時間 |
成形後の手作業にかかる時間(部品あたり) | 3時間 | 0時間 |
合計時間 | 160時間 | 40時間 |
生産量を拡大しながら、より良い製品を提供
導入から僅か1年足らずで、Form 3LはKastalonにとって意思決定を左右する重要な存在となりました。加工による従来の制約に悩まされることがなくなり、エンジニアリングチームはこれまでは不可能だった新たな注文も受けられるようになった一方、人件費や材料費で何千ドルもかかっていた工程の最適化にも成功しました。
「生産量は伸び続けています。使用するごとに経験を重ねていて、Form 3L向けの注文数も増えています。新しいことにもチャレンジできるようになり、営業担当がお客様の要望に応える手助けもできてきています。例え作る数が1つや2つであっても、希望の部品はうちで製作が可能だとお客様にアピールできるんです」
エンジニア、Brian Baer氏
Kastalonの作業員たちは、その精度や一貫した品質、質の高さで評判を集めてきました。当初は信頼を得ることが難しかった3Dプリント製の成形型ですが、その効果は導入後の結果が物語っています。SLA光造形3Dプリントで実現できる機械的特性、公差、形状の自由度で、工場長からも部品の3Dプリントの依頼を受けるほどの信頼を獲得したのです。
ラピッドツーリングについての詳細は、活用事例ページでご覧いただけます。また、Form 3Lにご興味がある方は、ぜひ製品ページから詳細をご確認ください。