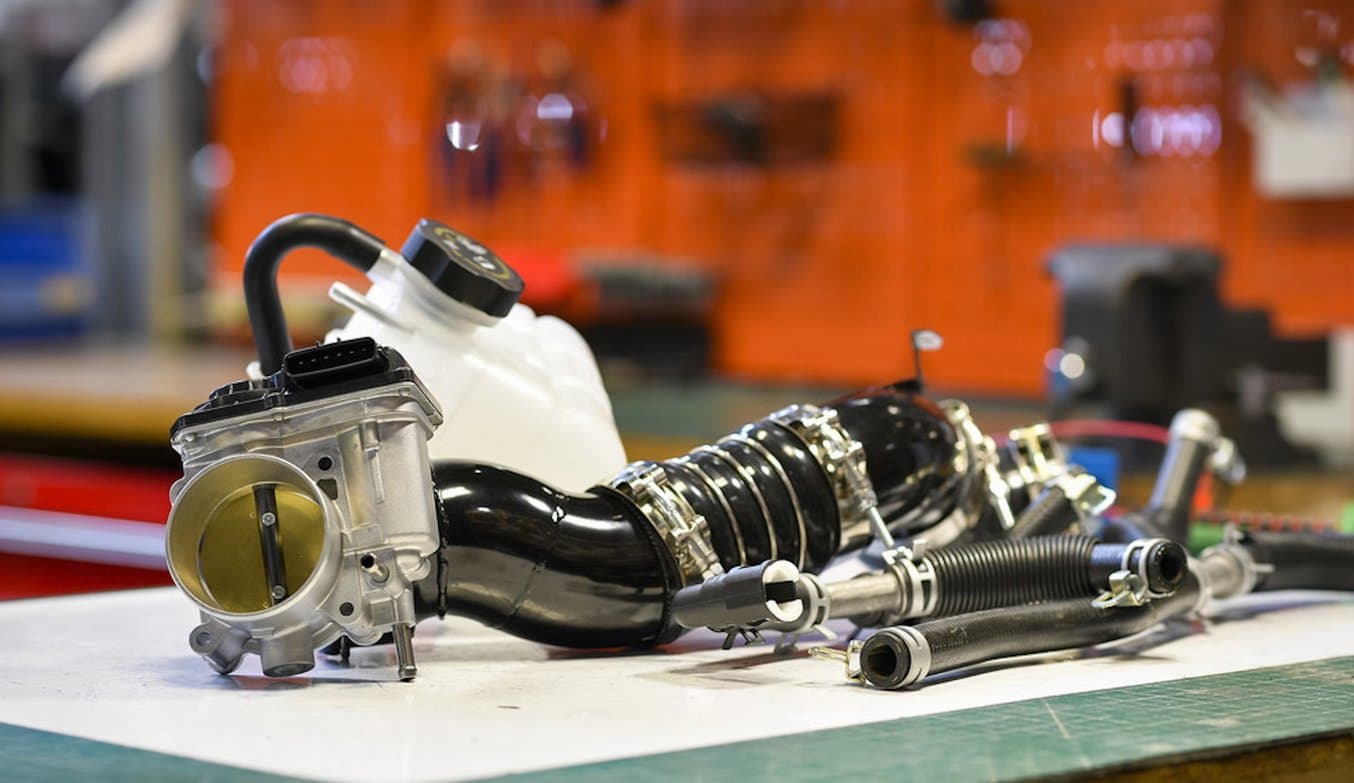
全世界に広がった半導体不足と製造の遅延、工場の操業停止などが原因で、過去2年間で自動車の販売価格は新車・旧車ともに急騰しました。車両のオーナーは、現在の車の保証が切れた後に新しい車やトラックを購入できないことが多く、そのためにも車を常に良好な状態に保つためのメンテナンスや車検がますます重要になってきています。自動車メーカーはディーラーを通して交換部品や補給部品を販売したりサービスの提供を行っているものの、同じようなサプライチェーンの問題に直面しており、一般のドライバーにとっては独立系の修理工場ほど手頃な価格でサービスを依頼できないこともあります。
Dorman Productsは、乗用車と大型トラックのアフターマーケット用自動車部品メーカーとして100年の歴史を誇るメーカーですが、生産期間の短縮と部品の品質向上を目指して3Dプリントを導入しました。常に新しい製造工程やモデルを追加するOEM元のメーカーに遅れずに対応するため、12台の3Dプリンタを2拠点で分散稼働させています。
Dormanのアディティブマニュファクチャリング部門でリーダーを務めるChris Allebach氏とメカニカルデザインチームのマネージャーEric Tryson氏は、FDM(熱溶解積層)方式プリンタ数台の他、SLA光造形方式プリンタのForm 2、Form 3、Form 3Lを駆使して新しい部品のラピッドプロトタイピングや検証試験で使用する治工具の製作を行っています。
「OEMさんには1つの部品に専属の設計チームがいて、早い時には新車が発売される2年前から設計を開始しています。なので、私たちは信頼できる交換部品や補給部品を確実に作りながら、迅速に市場投入できる方法を見つけないといけません。3Dプリンタを導入したことで設計の試作・検証が高速化でき、以前は試せなかったプロジェクトにも挑戦できるようになりました。高品質な部品ができるとわかっていれば、自信を持って目の前の作業に取り組めます。」と語ってくれたのはAllebach氏です。
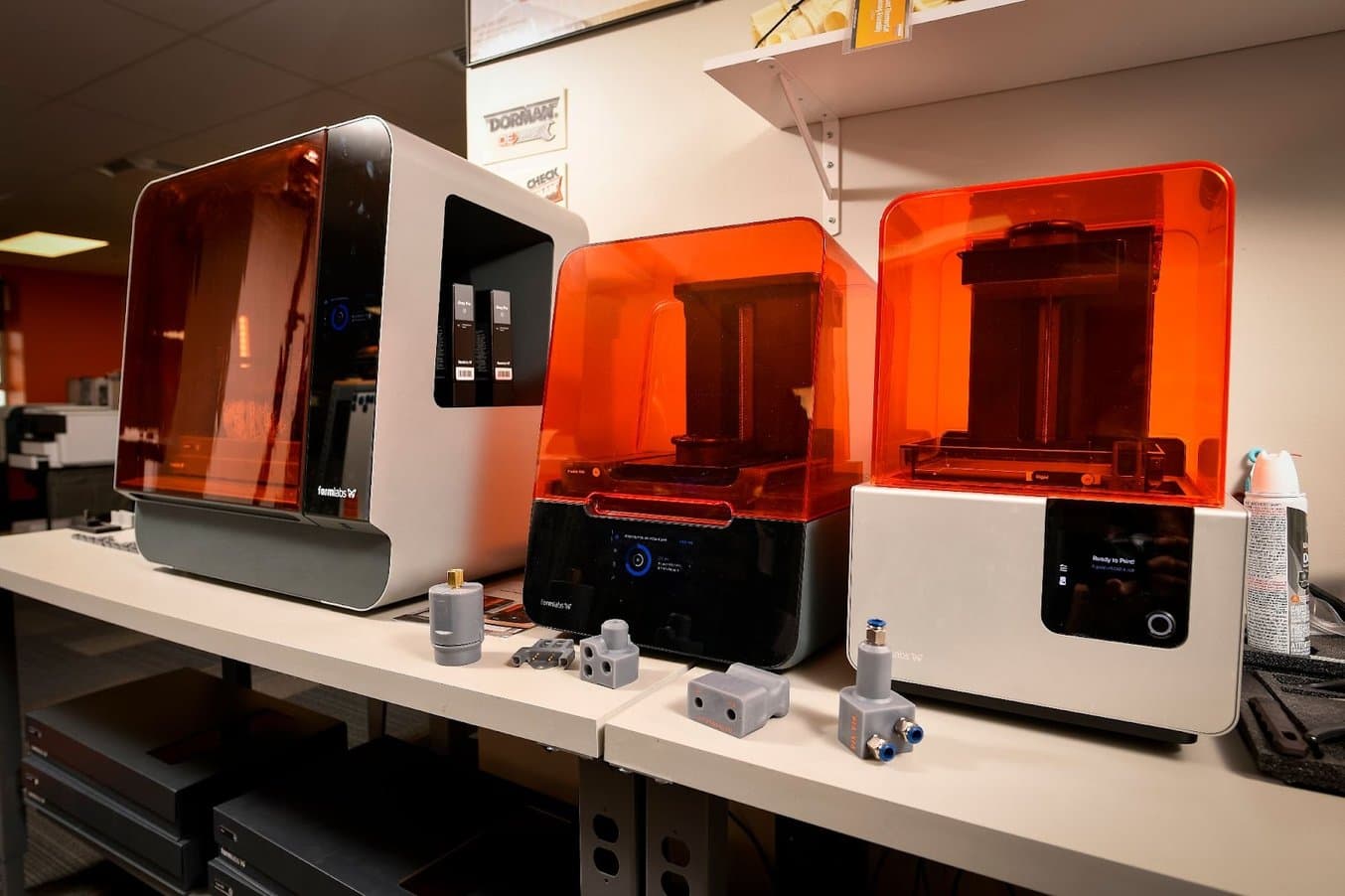
Dorman Productsのエンジニアが使用するForm 2、Form 3+、Form 3L。
10万点以上の多彩な部品を供給
Dormanが提供する製品の種類は驚くべき数に上ります。何百種類もの車両に向けて設計・管理する部品点数はなんと118,000種類(2021年12月25日現在)。Tryson氏は「うちでは車両の大半をカバーできるほどの種類を扱っていて、創業以来毎年4,000点〜5,000点の新たな部品をリリースしてきました。」と言います。
Dormanが取り扱う製品は、キーフォブやエンジンの基本部品から、複雑な電子モジュールや大型トラックの部品まで多岐に渡ります。OEM部品の不具合を分析し、製品のリバースエンジニアリングを行い、場合によっては最初から設計を見直して改良します。そのために元の部品を探して購入したり、時には仕組みを完全に理解するために対象の車両を丸ごと購入し、改良版の設計を検証することもあります。
設計工程ではまず、変更を加えられるよう部品の設計をデジタルで再現します。その後部品をDormanの計測ラボに送り、非接触式のレーザースキャンを行います。より高い精度が必要な部品には接触プローブを使用します。Allebach氏とTryson氏のチームがベンチマークデータを受け取り、CADソフトウェアのSolidworksを使って部品のリバースエンジニアリングを行います。
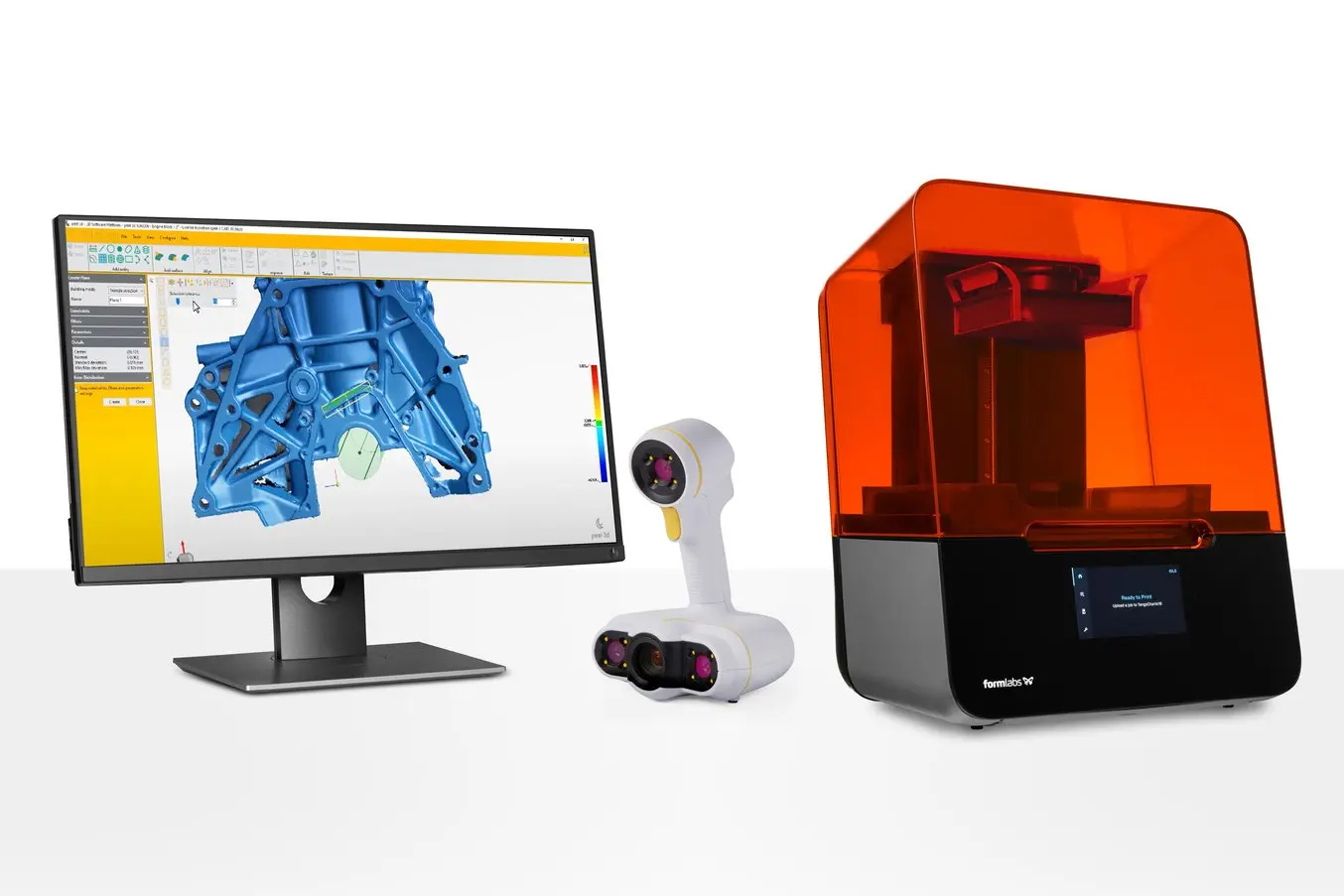
リバースエンジニアリングやその他用途向けの3Dスキャンと3Dプリント
本技術資料では、3Dスキャンと3Dプリントの主な活用事例をご紹介するとともに、現在の3Dスキャナ市場の概要を解説しています。
「まず試作品を作って形状や寸法が合っているかをデザイナーにダブルチェックしてもらいます。その後、3Dプリントで別の試作品を作ってプロダクトデザイナーにレビューしてもらいます。やはり部品を実際に目で見て、車両に嵌合構造などがあれば実際にはめ合わせて確認するためにも、部品が手元に必要なんです。」とTryson氏は言います。
Allebach氏とTryson氏の部門が担うのは、交換部品や補給部品の量産だけではありません。DormanのOE FIX™ ラインでは、純正部品の設計改良も担当しています。「ただリバースエンジニアリングをするだけでなく、部品の不具合がなぜ発生したのか、どうすれば改善できるのかを分析して見極めるんです。結果的に材料を変更することもあれば、設計自体を変更することもあります。再設計を行う場合には、試作品を作って機能確認試験も必要になります。」とTryson氏。
OE FIX™の試作品製作
その例の1つが、複数のオーナーから報告されたエンジン部品の不具合です。元の部品はプラスチック製で、エンジンから発生する熱に繰り返し晒されることで割れてしまっていたのです。Dormanのチームは部品を分析し、計測チームによるスキャンの結果、設計を見直してアルミ鋳造で作り直すことにしました。元の材料から材料を変更して部品を設計する場合、単に材料を入れ替えれば良いというわけではなく、部品自体を新しい材料に合わせて設計し直す必要があります。再設計後も元の部品と全く同じ機能を維持できるよう、何度も試作・検証プロセスを繰り返しました。
「設計の試作・検証プロセスをわずか数時間で行えること、そしてその工程を2回繰り返しても1日以内に完了できたことは非常に助かりました。3Dプリントを導入する前は、1回目で完璧なものができるよう願うしかなかったのです。そうでないと、数週間〜数ヶ月も待って部品を手に入れたのに、結局改良しなければいけないとわかり、また外注先に送り返すことになりますからね。」とTryson氏が教えてくれます。
設計の試作品を内製できるようになってからは、機能試験を行なって部品の機能性が失われていないかを確認することができています。
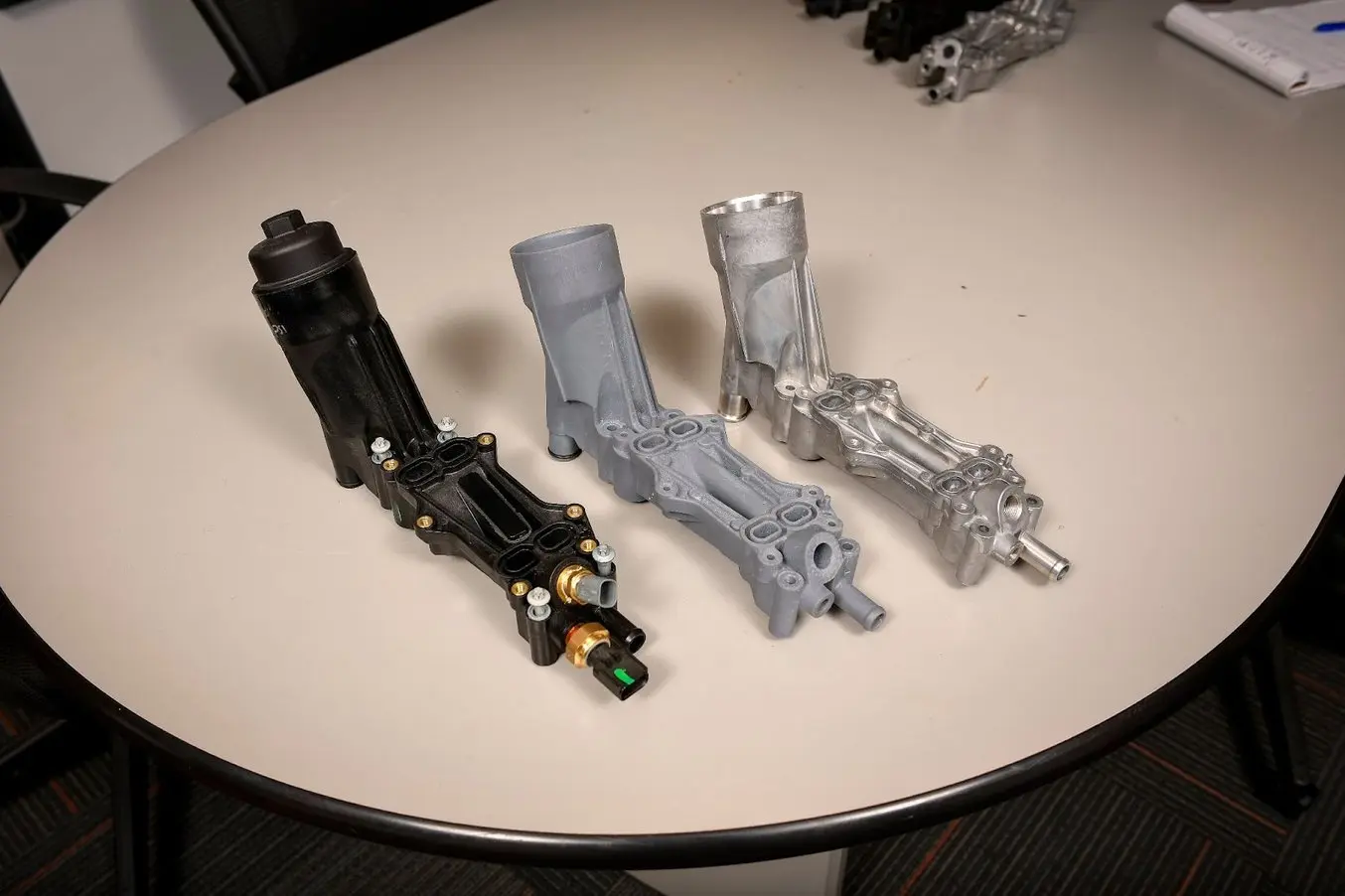
何人もの所有者から不具合の報告があったエンジン部品。写真は再設計後に製作した試作品。
検証工程
すべての部品がそれぞれ異なる機能を持っているため、試験条件や方法、検証プロセスも部品によって異なります。例えば2種の異なる部品を検証するのに流体試験が必要な場合、部品の形状が違っていれば、試験中に部品を固定する治具もそれぞれ別のものが必要になります。
テストで使う治工具の製作はFormlabsプリンタの最も得意とするところです。軟質のElastic 50Aレジンから硬度と耐熱性の高いRigid 10Kレジンなど、いろいろな特徴を持つ材料がかなり豊富に揃っていますし、製作期間やコスト削減の面で非常に大きな助けになってくれています。
Chris Allebach氏、Dorman Products、アディティブマニュファクチャリング部門リーダー
3Dプリンタを使った試作・検証工程を取り入れる前は、カスタム治工具の製作が開発工程を遅らせる原因となっていました。新モデルを毎年生産するOEM元のスピードについていかなければならないDormanのような会社にとって、製造工程の遅れは新製品の機会損失を意味します。
それぞれの部品に異なる治工具が必要なため、大量に外注することもできず、費用対効果の高い射出成形は選択肢から外すしかありませんでした。残りの選択肢は機械加工ですが、費用が高額かつ時間もかかります。まず設計を完璧な状態にしてから加工に送り、数週間後に出来上がった治工具を受け取り、ようやく部品の検証に進めます。
「治工具やゲージは加工工場に送っていましたが、出来上がるまでに通常5〜6週間かかります。コスト面では単価が5倍〜10倍に膨れ上がり、かつ従来工法では実現できる形状も限られていました。それが3Dプリンタを導入したことで、部品を試作しながら試験用の治具やゲージも製作できるようになり、今では部品の最終設計が決まる頃には試験で使う治具も出来上がっているという状態です。生産性を最大限に高めようとしているんです。」とAllebach氏は言います。
加圧ホースのテストであれば、1つの検証工程につき3Dプリント製の治具が2つ必要になります。そのうちの1つでホースの片側に栓をして流体を流しこみ、どれだけの圧力に耐えられるかを計測します。もう1つは、実際の車両でボンネットの下の大型ラジエーターに組み込まれる嵌合構造のシミュレーションに使われます。ラジエーターの嵌合構造部分だけを3Dプリントすることで、検証チームがいろいろなテストを行えるようになります。また、その部品を製造アセンブリラインに送り、追加の品質管理プロセスとして完成品でも検証を行うこともできます。
「大型のラジエーターの嵌合構造をテストする様な場合には、ラジエーターを複数購入して送るわけにはいかないので、一部だけ3Dプリントして検証します。これなら好きなように検証でき、のちに量産して供給することができます。仮に壊れてしまっても、数ドルで別のものを3Dプリントできるんです。」とTrysion氏は教えてくれます。
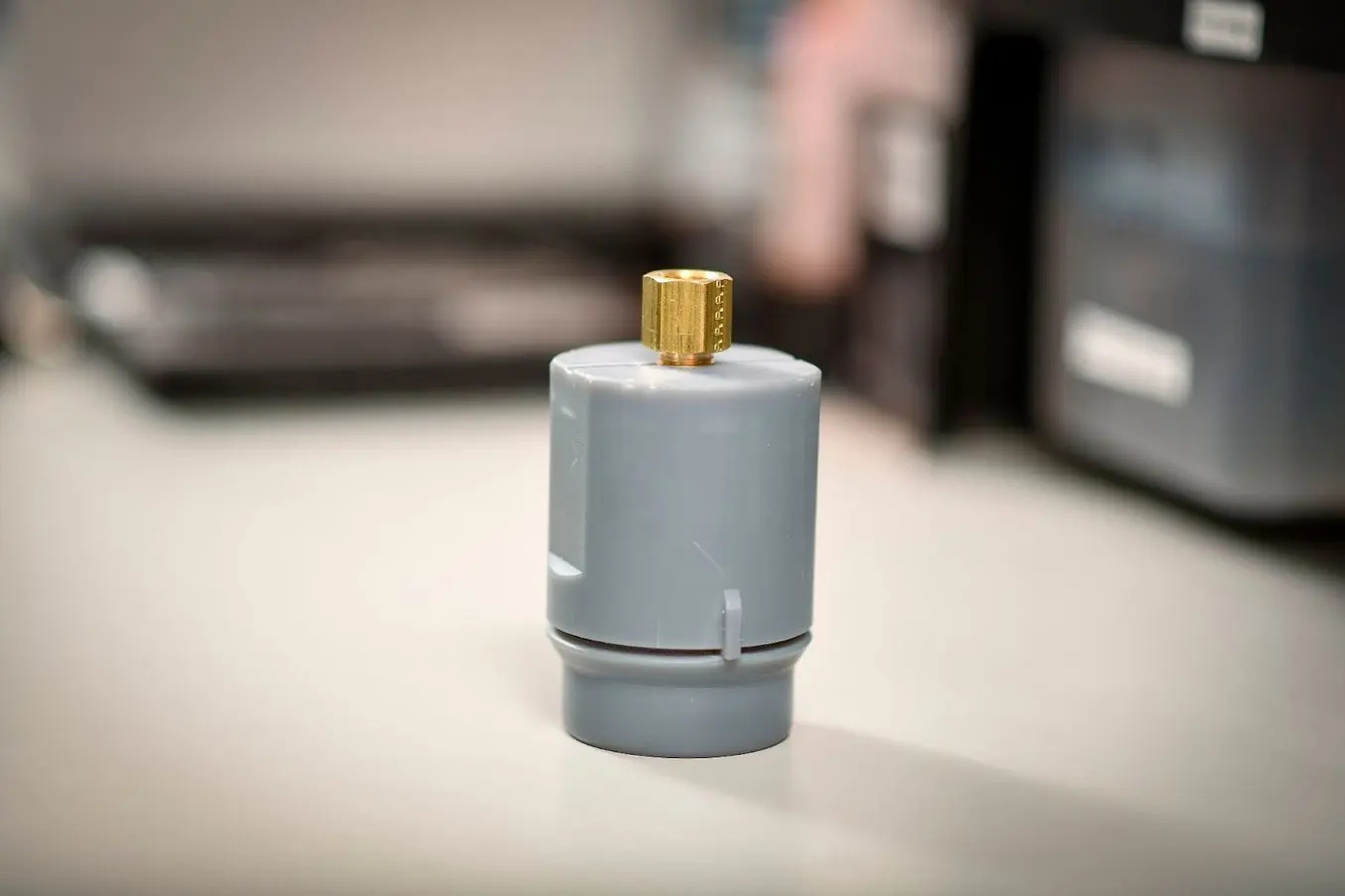
2つの治工具のうち1つは加圧ホースのテストで使用される。
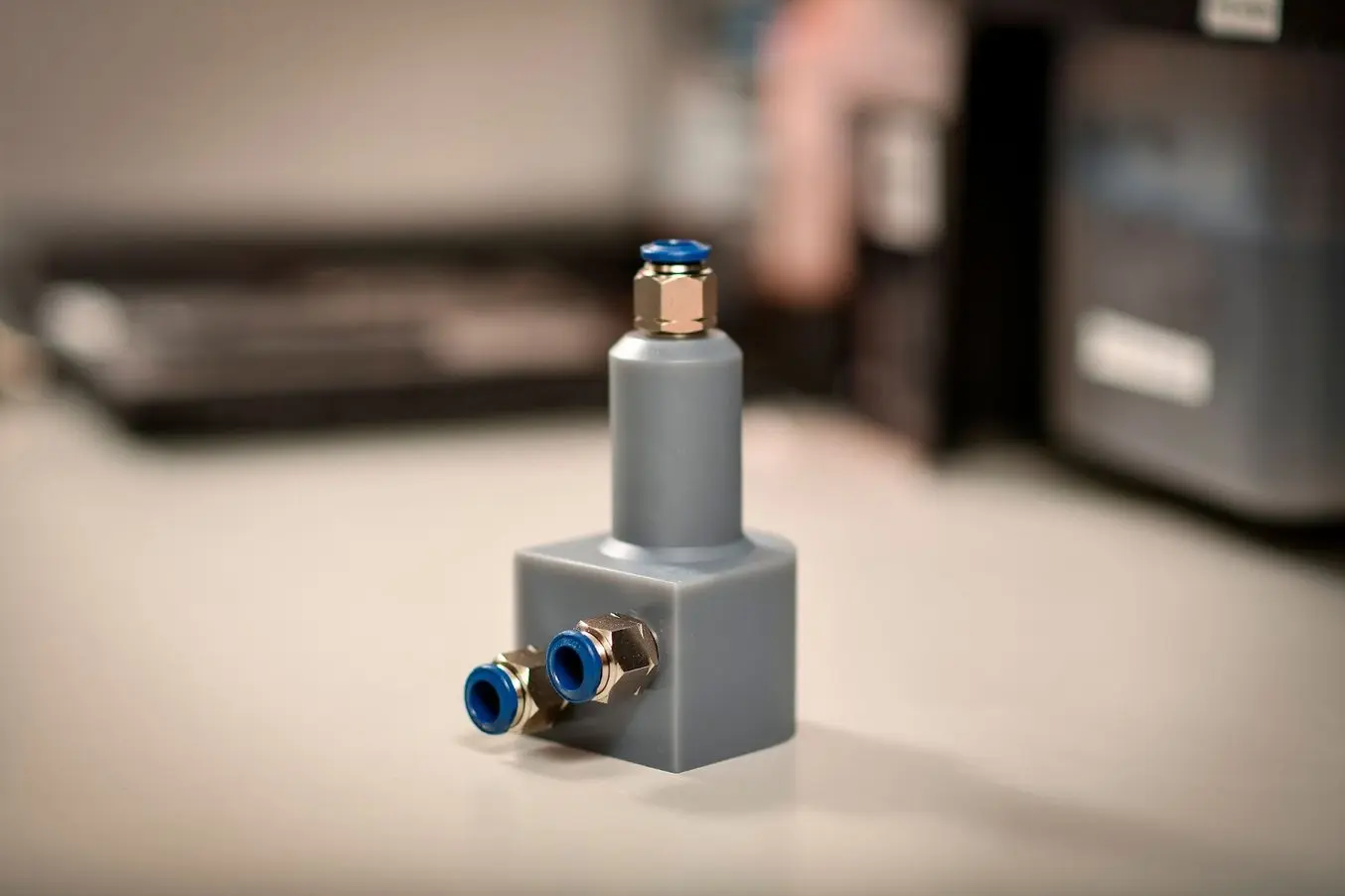
カスタム治工具を嵌合構造のシミュレーションに使用することで、ラジエーターを丸ごと購入することなくテストができる。
合否判定の厳格な公差に挑む
完成した製品が店頭に並び、お客様の車に搭載される前に、Dormanのチームは部品ごとに許容される寸法公差をしっかりと把握しておく必要があります。寸法分析によって部品の合否を判断するためです。公差が厳しい部品もあります。Tryson氏とAllebach氏は、Form 3+とForm 3Lを導入する前は3Dプリント製のゲージでこのような厳しい公差に対応できるか懸念を持っていました。
「公差に合わせて、Formlabsのプリンタでたくさんの通止めゲージを作っています。一度、これは無理だろうと思うような通止めゲージを作らなければならなかったことがあります。エンジニアがやってきて、部品の寸法公差を+/-.05mmに収めなければいけないと言ったんです。なんとか、寸法交差0.25mmでプリントすることができました。Form 3Lでここまで厳しい公差に対応できたことに、本当に驚きました。」とAllebach氏は言います。
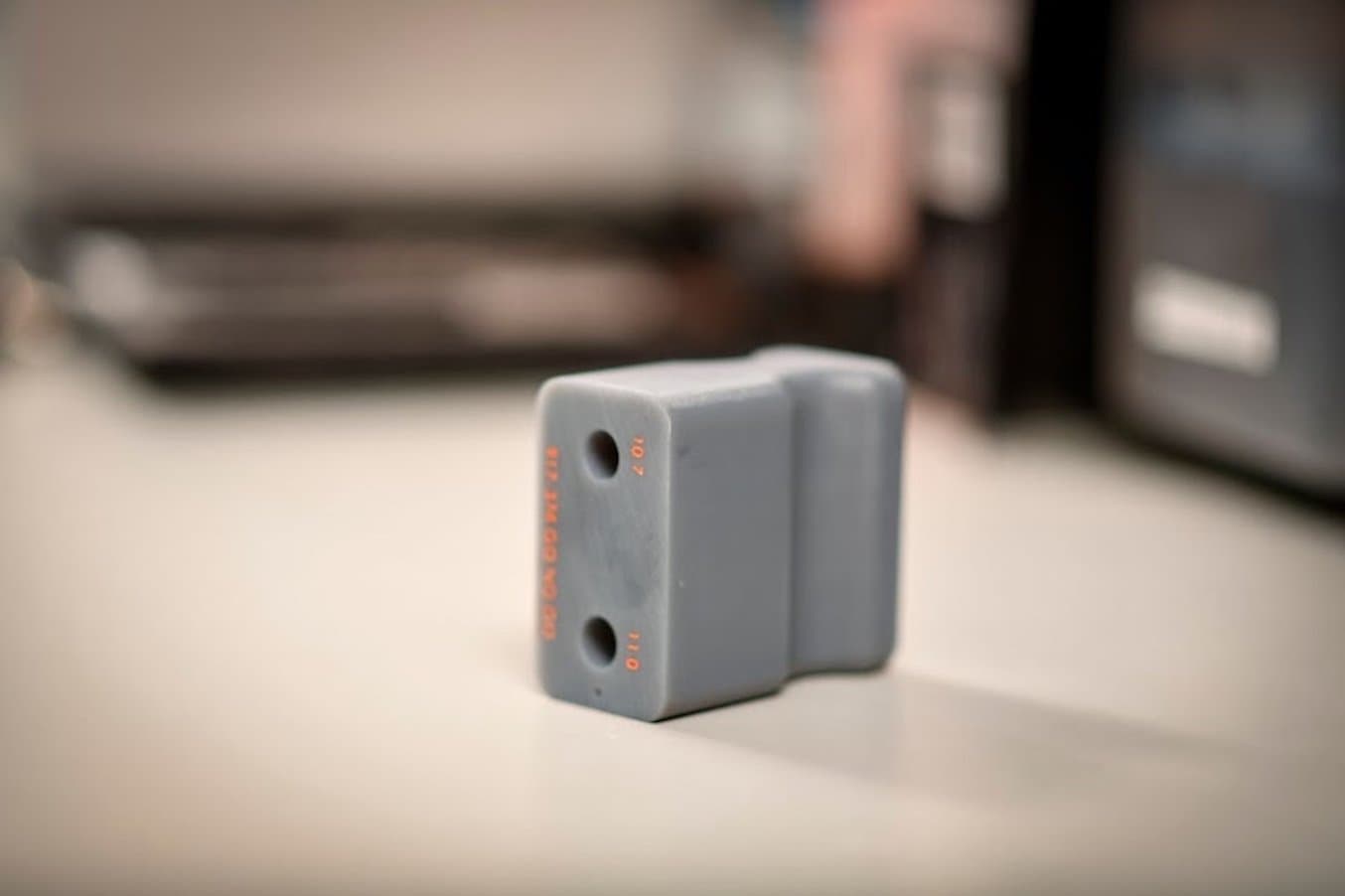
Greyレジンでプリントした合否判定用ゲージ。
シリコンの3Dプリントで圧力試験用ガスケットを製作
新しい設計を検証する際に行う圧力試験として、部品の特定のポートや面を密閉する必要がありますが、すべての部分が嵌合形状になっているとは限らず、密閉するためには独創的なアイデアを考えなければなりません。結果的に、カスタムのガスケットや治工具を製作することになるのです。
従来は研究室で部品を測定してから金属製のダイを作り、そのダイを使ってアーバープレスでカスタムのガスケットを切り出していました。「シートからクッキーをくり抜くようなイメージです。材料の使用率や研究室の技術者が費やす時間を考えると、非常に効率が悪いやり方でした」とAllebach氏。
3Dプリントに切り替えたことで、膨大な数の新部品があったにも関わらず、製作期間とコストを大幅に削減することができました。「スロットルボディの両端を密閉するスロットルボディテスター用にカスタムガスケットを何百個もプリントして、流量試験を行いました」とAllebach氏は言います。
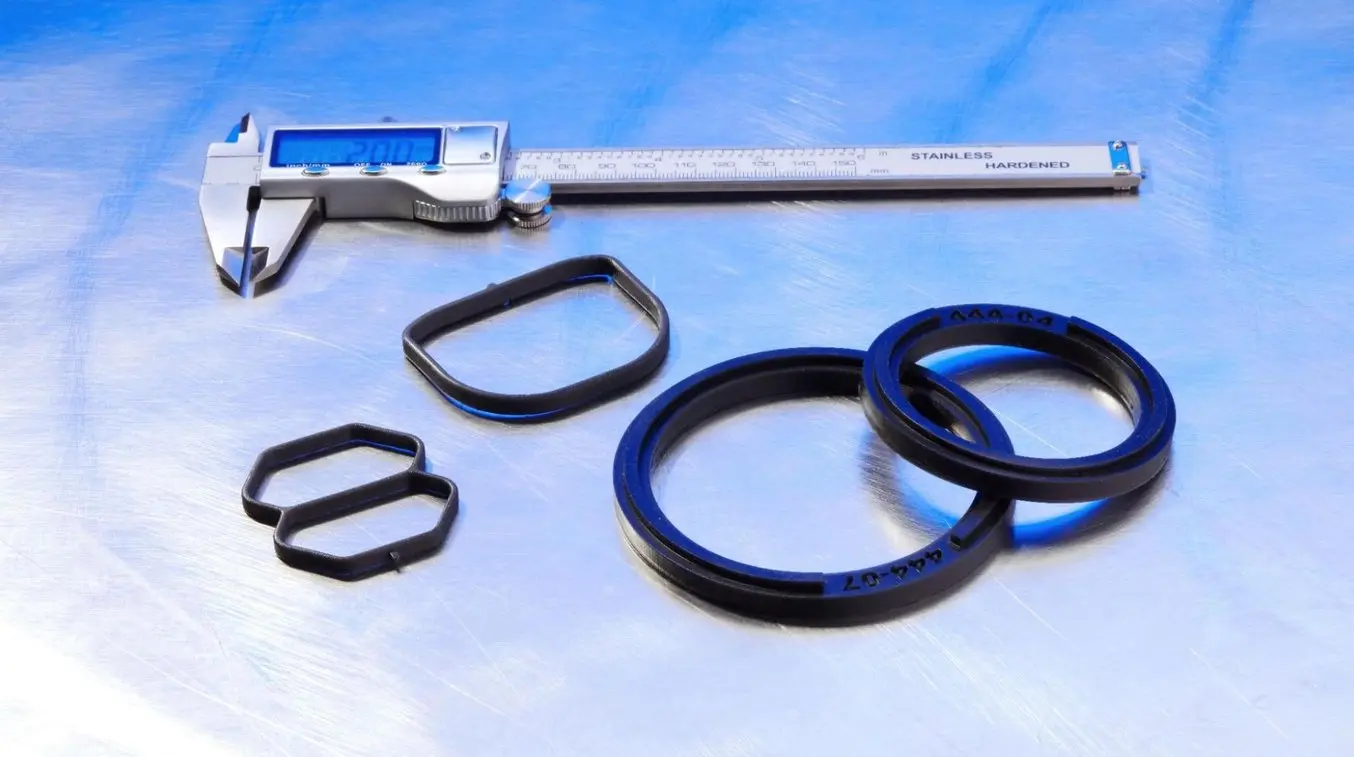
Silicone 40AレジンでプリントしたDorman Productsのカスタムガスケット。
この目的を果たすだけならFormlabsのシリコンライクな3Dプリント用材料のElastic 50Aレジンでも十分でしたが、初めて手頃な価格を実現した新登場の純シリコン材料Silicone40Aレジンではさらに用途の幅が広がります。 「[シリコンライクの材料に比べると]Silicone 40Aレジンの耐久性は秀逸です。基本的にはシリコン樹脂なので期待値もそれ相応だったのですが、成形射出したシリコンと同じような機能を発揮してくれました」
彼らがSilicone 40Aレジンに求めるのは、耐薬品性と耐熱性です。3Dプリント製の部品を2か月間に渡りオイル、洗浄液、UV環境に晒して化学テストを行い、その後さらに圧縮永久歪み率のテストも行った結果、スプリングバックやその他の機械的特性も同社の要件を満たすことがわかりました。
検証用のガスケット
製作期間 | コスト | |
---|---|---|
金属製のダイを使ったシリコンシートカッティング | 1セットあたり2週間 | 1セットあたり$250 |
Silicone 40Aレジンで内製 | 1セットあたり3時間 | 1セットあたり$12 |
「ギヤーオーブンで熱老化試験を行うカスタムガスケットを作ったり、テストの観点からエンジンルームを模倣した環境でガスケットを密封したり、空中、水中、冷却水、オイルなど、部品が実際に使われる環境でテストできるということが、私たちにとっては非常に重要なんです」
Chris Allebach氏、Dorman Products、アディティブマニュファクチャリング部門リーダー
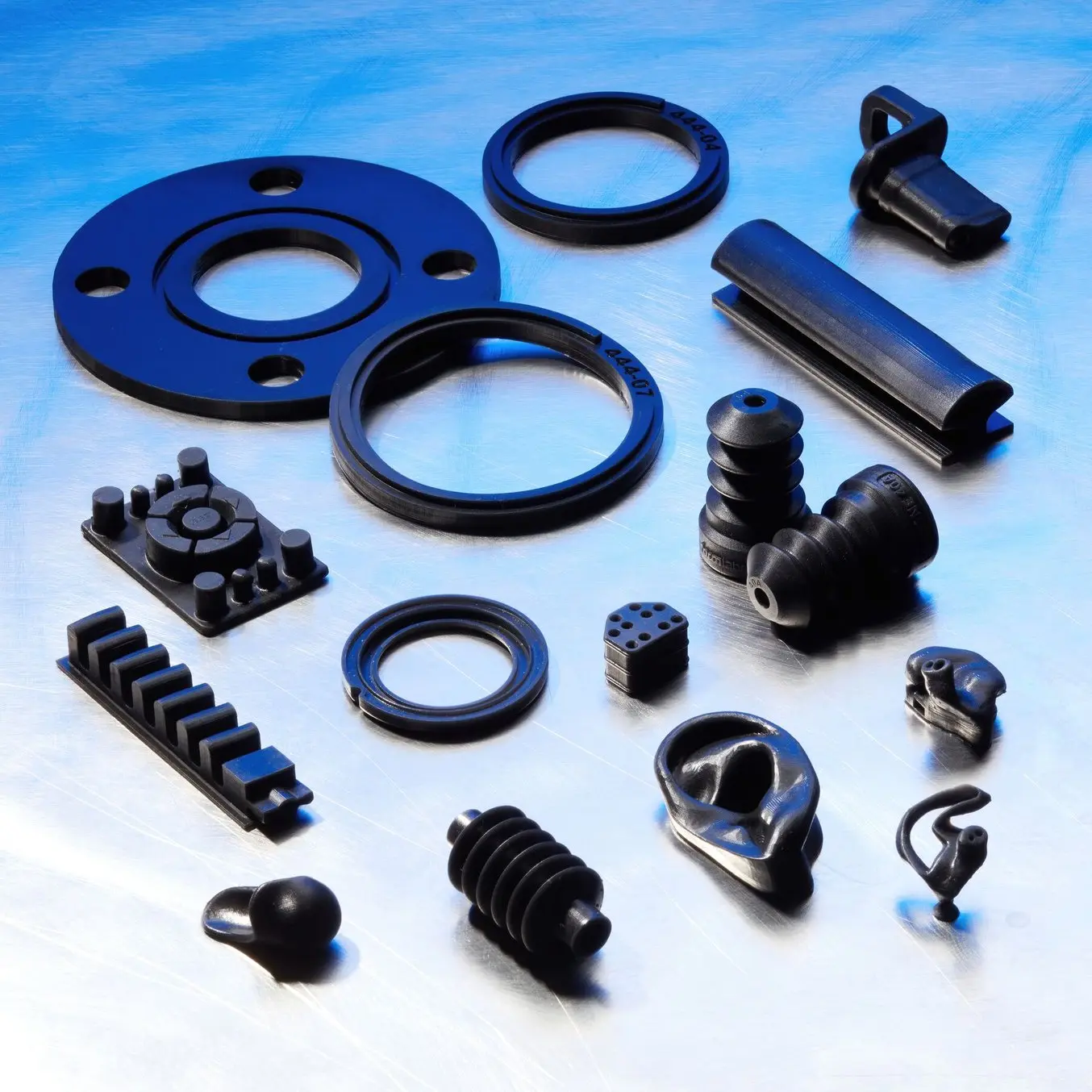
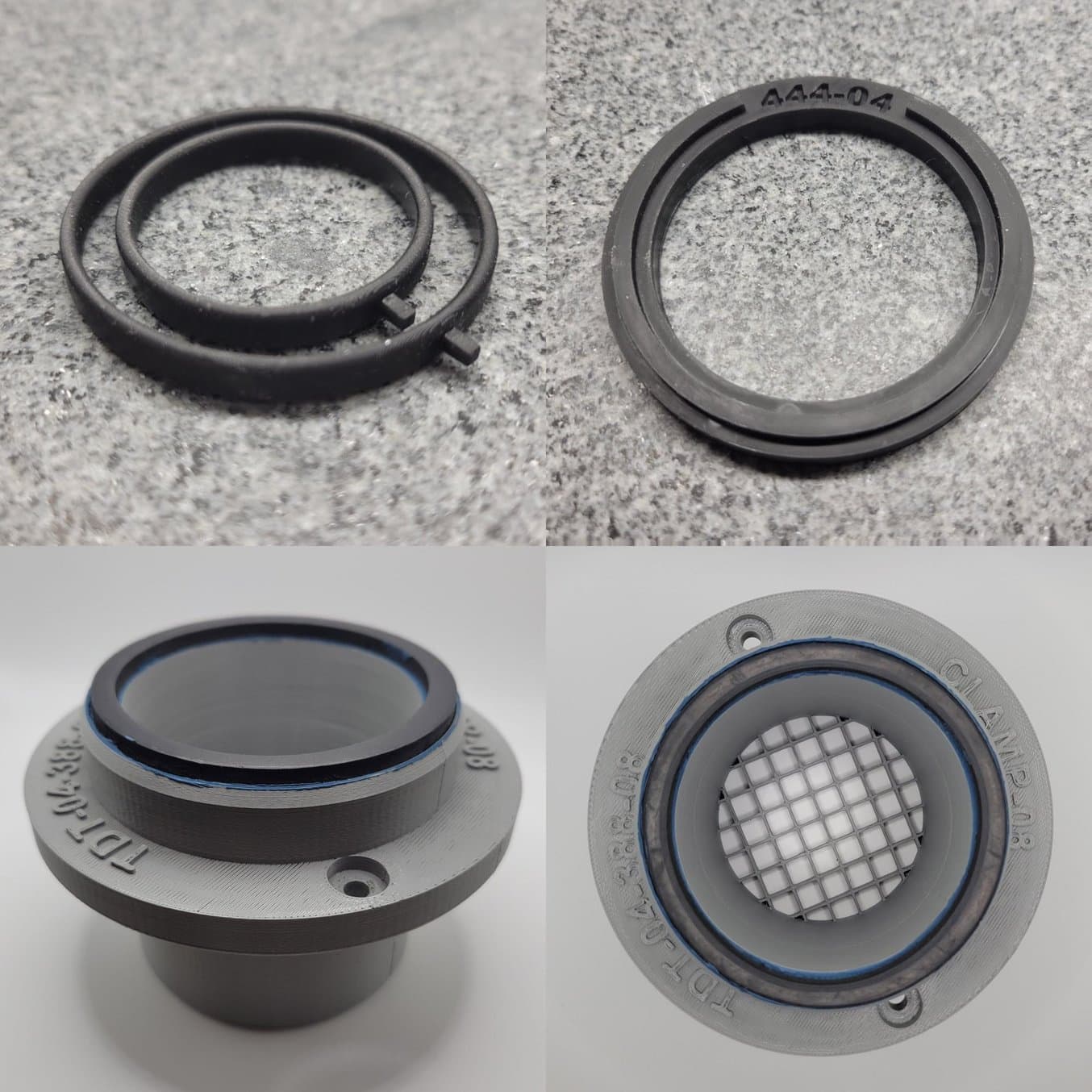
カスタムインテークマニホールドガスケットと3Dプリント製の気流テスト用アダプタ。
Allebach氏は、3Dプリント用の軟質材料でここまで高い設計の自由度が得られたことにも驚いています。
「このレジンのプリント適性には驚きました。こんなに柔らかい材料で、ここまでしっかりと細かい形状がプリントできるとは思いもしませんでした。40A材料では決して作らないような部品もプリントしてみたのですが、これまでは射出成形に頼っていたものが、このレベルで3Dプリントできたということに、ただただ驚いています。完成品の細部の品質は信じられないくらいでした。社員も全員、材料の肌触りと弾力性に驚いていましたよ」
Chris Allebach氏、Dorman Products、アディティブマニュファクチャリング部門リーダー
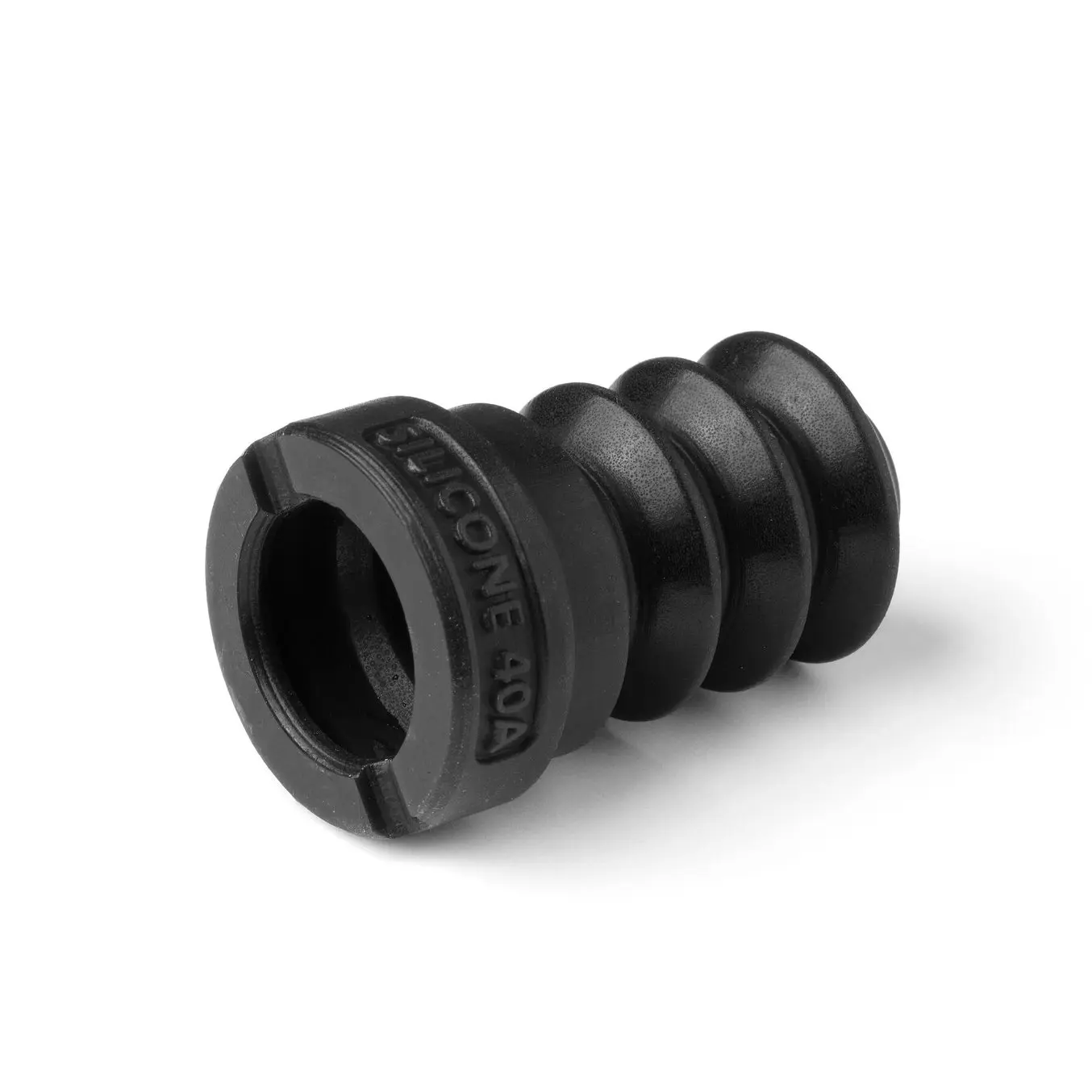
金属部品も、驚きの品質で
Tryson氏とAllebach氏はいつも、後処理を施してから同社のマーケティングおよびセールスチームに部品を送ります。のちのち金属で大量生産されることになる部品には、SLA光造形方式でプリントした部品に後処理を施してから、お客様と実際に相対する部門に送ります。最近では、Grey Proレジンでプリントしたボールスタッドに電解めっき処理を施してから、マーケティング用サンプルとして車体を担当するチームに送りました(電解めっき処理はRepliform INCによるもの)。ここで、3Dプリント製部品の表面品質が良すぎることが問題になりました。「マーケティングチームにこう言われました。『普段この部品は鍛造や鋳造で作ってから亜鉛めっき処理を施すんですが、この3Dプリント品は既製品より見栄えが良くなってしまう』と言われました。」と教えてくれたのはAllebach氏です。
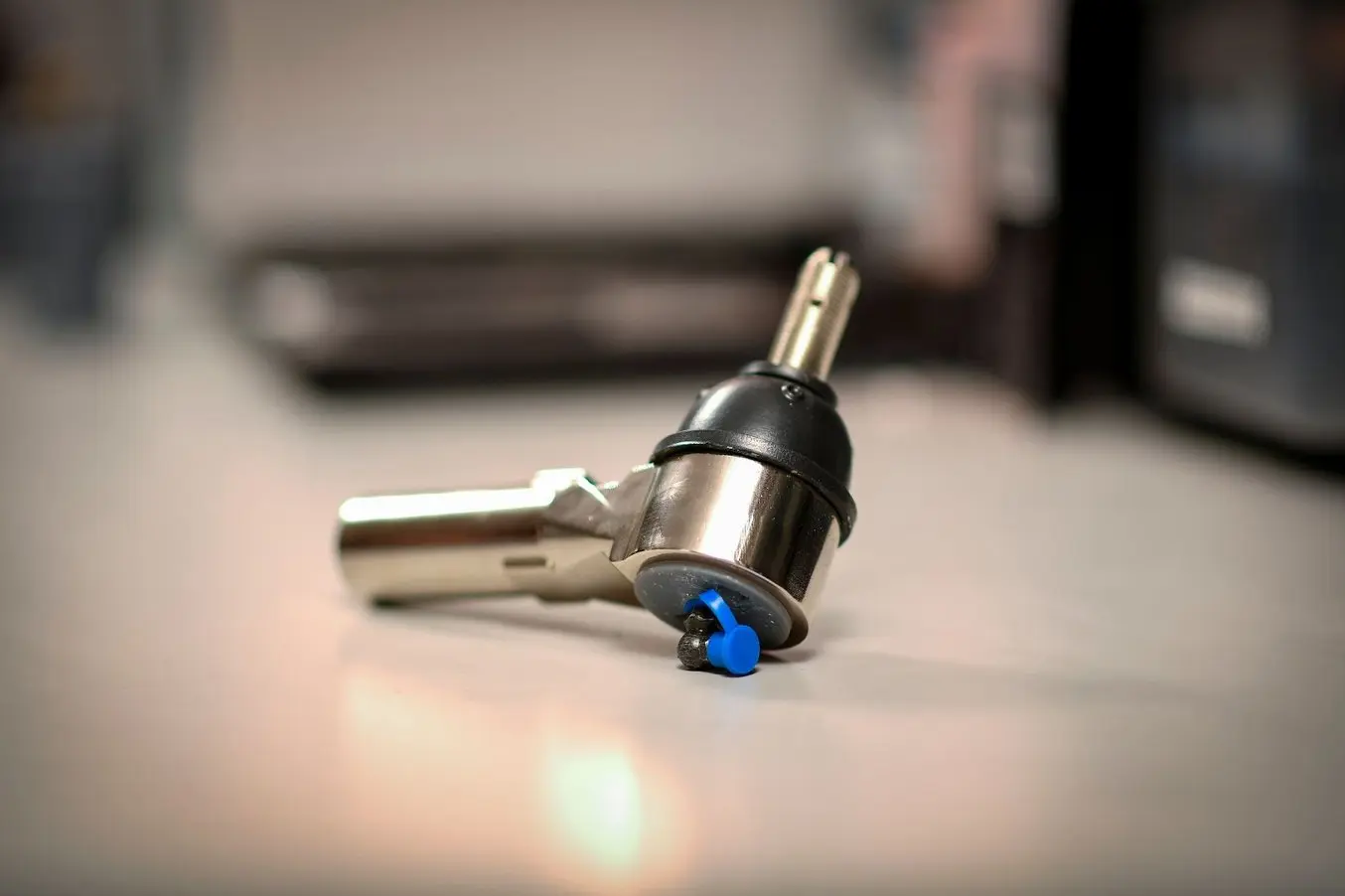
電解めっき処理を施した部品。
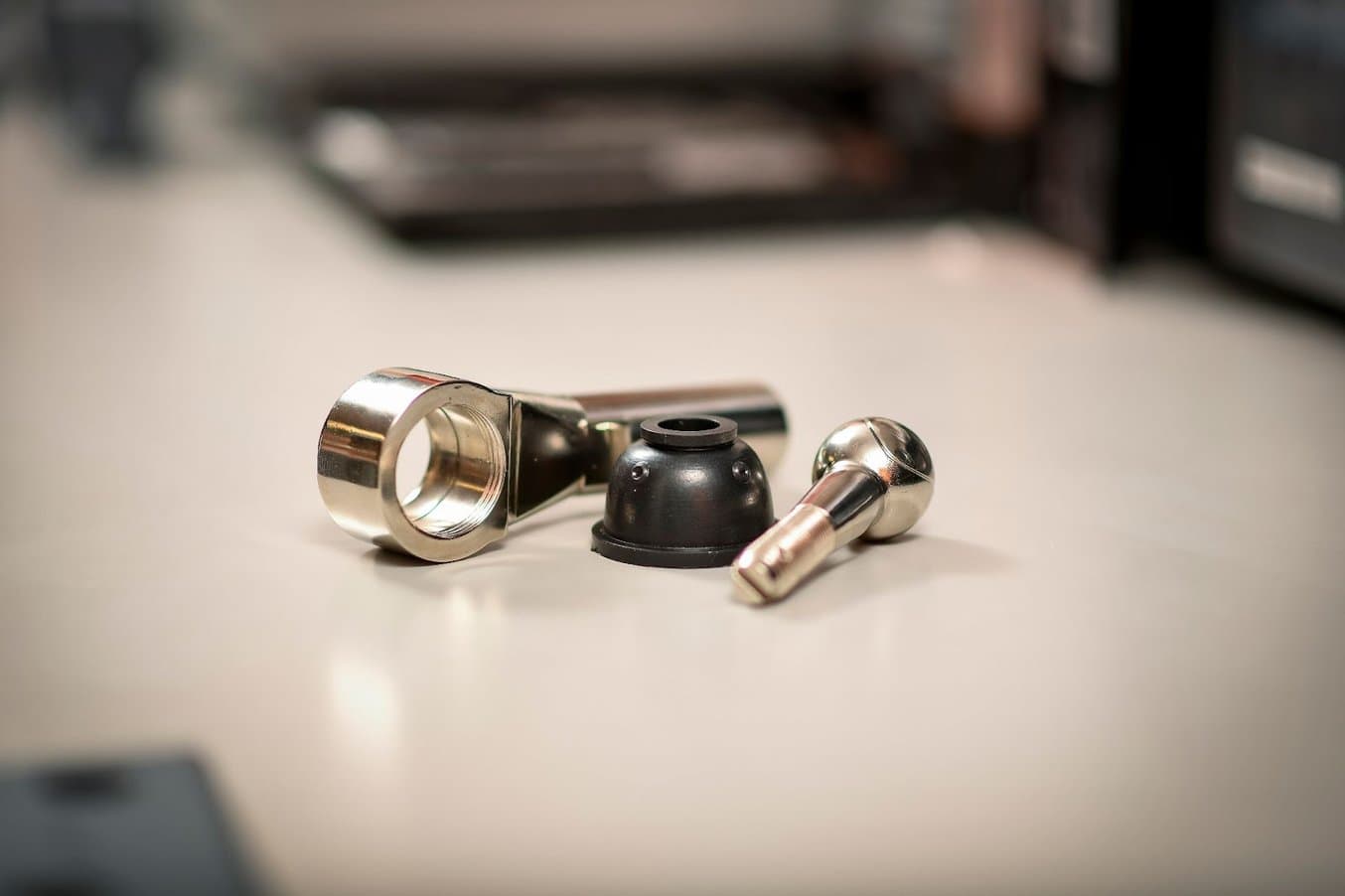
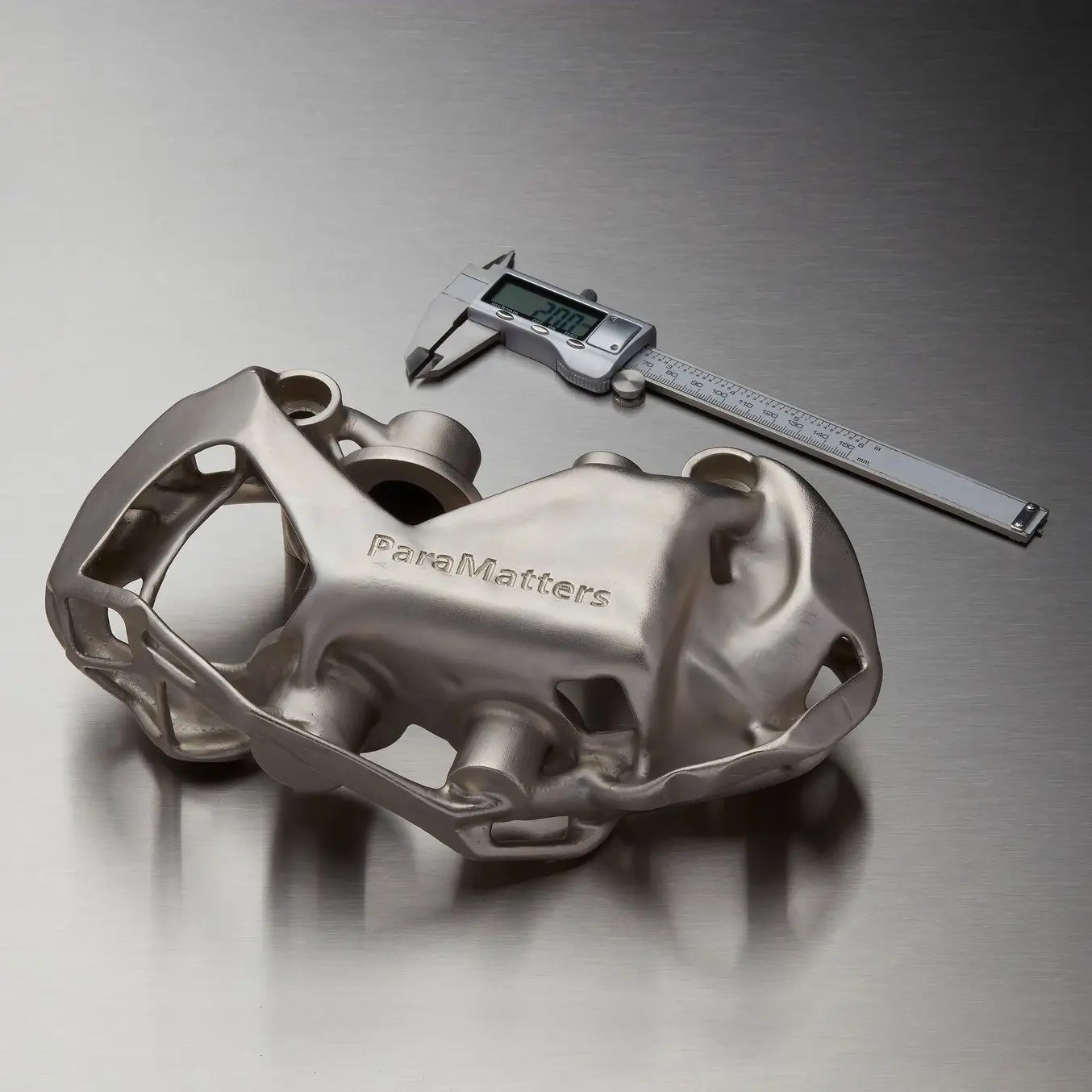
金属の強度を手に入れる:SLA光造形品の電解めっき方法と活用事例
本技術資料では、レジンで3Dプリントした部品のメタルコーティングに取り組むエンジニアの事例、そしてハイブリッド金属による実製品用部品の強度・耐久性の向上や用途の拡大といった新たな可能性について詳しく解説しています。
優れた馬力でROIを向上
Dormanが最初にFDMプリンタを導入したのは10年前。それ以来、Allebach氏とTryson氏は徐々にプリンタを追加していき、既存ユニットの生産能力を高め、FormlabsのSLA光造形プリンタで使える材料を最大限に活用してきました
Dormanの全世界年間売上高は約$13.5億(2021年12月25日時点)に上りますが、それでも設備購入時には妥当性の判断が必要です。「表面品質と寸法精度の高いForm 2を導入することにしました。私たちの使用方法なら、2ヶ月以内に採算が取れると思ったんです。Formlabsプリンタ導入のコストの妥当性や投資利益率(ROI)について検討したところ、2年どころかわずか数か月で投資を回収できることがわかり、3Dプリントへの投資価値を経営陣にも納得してもらうことができました。」とTryson氏。
この自信があったからこそ、Tryson氏とAlleback氏は約1年前にも、同社初となる大容量プリンタForm 3Lの導入に踏み切ったのです。既に導入済みのプリンタと同様、1日に10〜12時間、時には夜通し稼働させています。材料ライブラリで提供されているレジンの全てを利用している同社では、大型・小型のどちらの部品でも必要な機械的特性を実現することができ、それによって作業手順もさらに合理化することができています。
ここまで大きなSLA部品をたった$10,000でプリントできるなんて、信じられません。他では実現できませんよ。数種類の部品で製作にかかるコストや時間を削減できたことで、導入費用の回収もあっという間にできてしまいました。
Eric Tryson氏、Dorman Products、メカニカルデザインチーム マネージャー
3Dプリントで未来を見据える
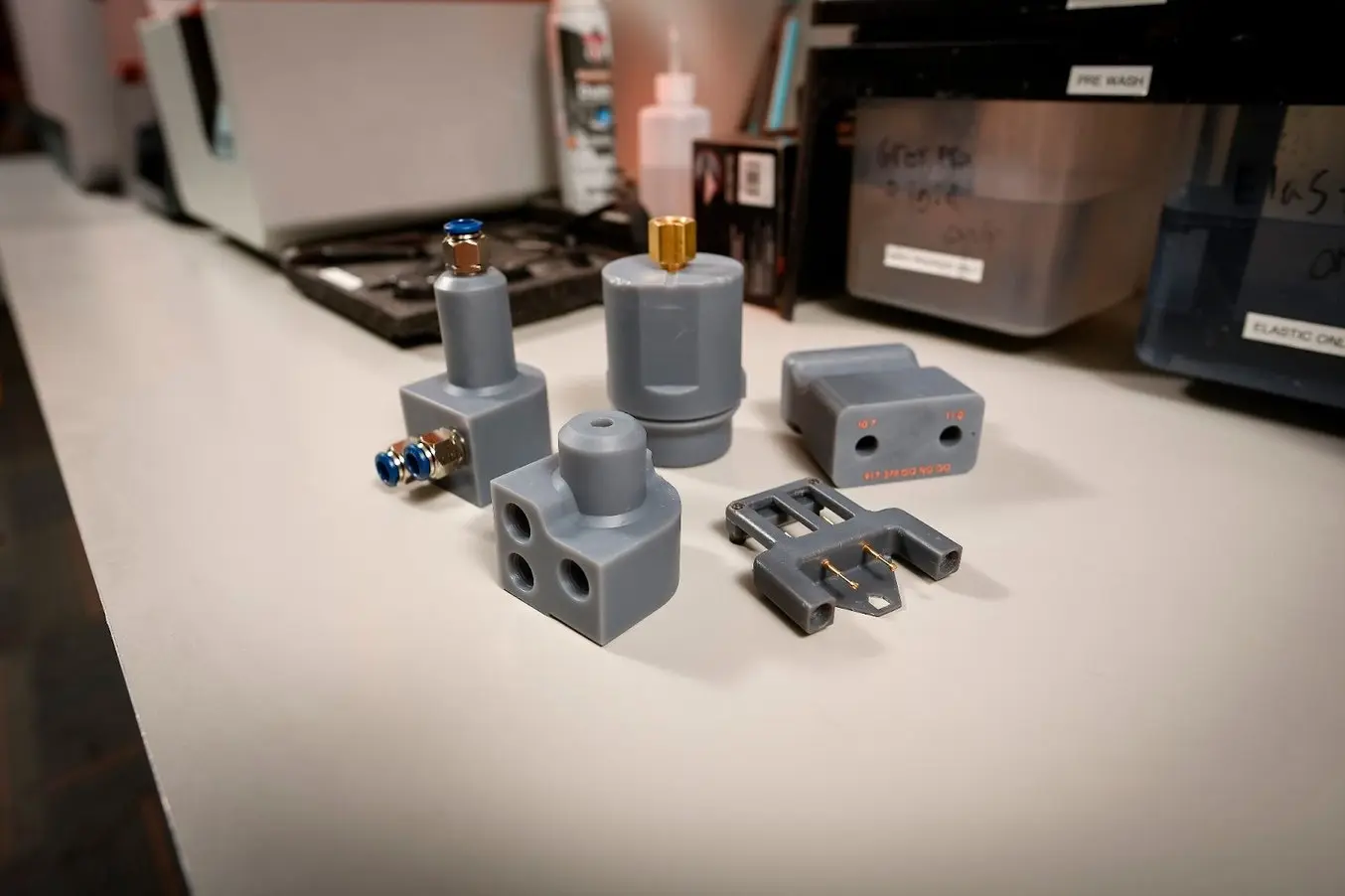
サプライチェーンの混乱は、まだまだ収まりそうにありません。それに伴い、新車・旧車に関わらず車の価格は依然として上がったままになるでしょう。OEMメーカーが電気自動車製造に次々と参入する中、新モデルの部品はますます軽量化され、新しい製造技術(多くの場合はアディティブマニュファクチャリング)に合わせて最適化され、これまで使用されてこなかった材料の活用が活発になっています。このような背景から、自動車業界は純正部品やアフターマーケット品の製造において、ますますアディティブマニュファクチャリングへの期待を高めています。既にその設備を導入済みのDorman Productsは他社の一歩先を行っていますが、Allebach氏とTryson氏の視線は常に未来に注がれています。
「私たちなら、簡単に部品の設計や生産ができます。従来の工法にとらわれていないので、部品の設計にアンダーカットや突き出し構造があっても、加工とは違って必ずしもコストが増えるとは限らないということを、他の部署にも伝えています。そのおかげで、希望通りの治工具をありのままに設計できるような、新しい可能性とアイデアが生まれています」とAllebach氏。
効果を実証してきたROI、そして社内でFDM方式やSLA光造形方式がますます普及してきた今、同社ではSLS(粉末焼結積層造形)方式を迎え入れる準備ができています。「作業場は汚れるけれど高速で生産できるFDM方式、精度と耐久性の高いSLA光造形方式。どちらも大いに役立っていますが、高い機能性を持った部品を少量生産するとなると、次はSLS方式かなと考えています」とTryson氏は言います。