英国の自動車産業の中心に本拠を置くVital Autoは、自動車デザインに深く精通した工業デザインスタジオです。同社のクライアントには、ボルボ、日産、ロータス、マクラーレン、ジーリー、タタ等多くの大手自動車メーカーが名を連ねています。
「お客様の多くは、最新技術を活用することで実現可能なボーダーラインを押し広げられないかと、当社に相談にきます」と語るのは、VitalのInnovation & Experiential Technology部長のShay Moradi氏です。メーカーが自社内で実験的な試みを行う時間がない場合、アイデアや初期のスケッチ、図面、あるいは技術仕様を完全に形にするための課題がVital Autoに持ち込まれます。
ここでは英国で急成長中のFormlabs正規代理店、Solid Print 3DのクライアントであるVital Autoが、複数台のForm 3LやFuse 1をはじめとする多数の高度機器を活用して、試作・検証工程を高速に回すことで忠実な試作品やコンセプトカーを製作している方法をご紹介します。
コンセプトカーの開発
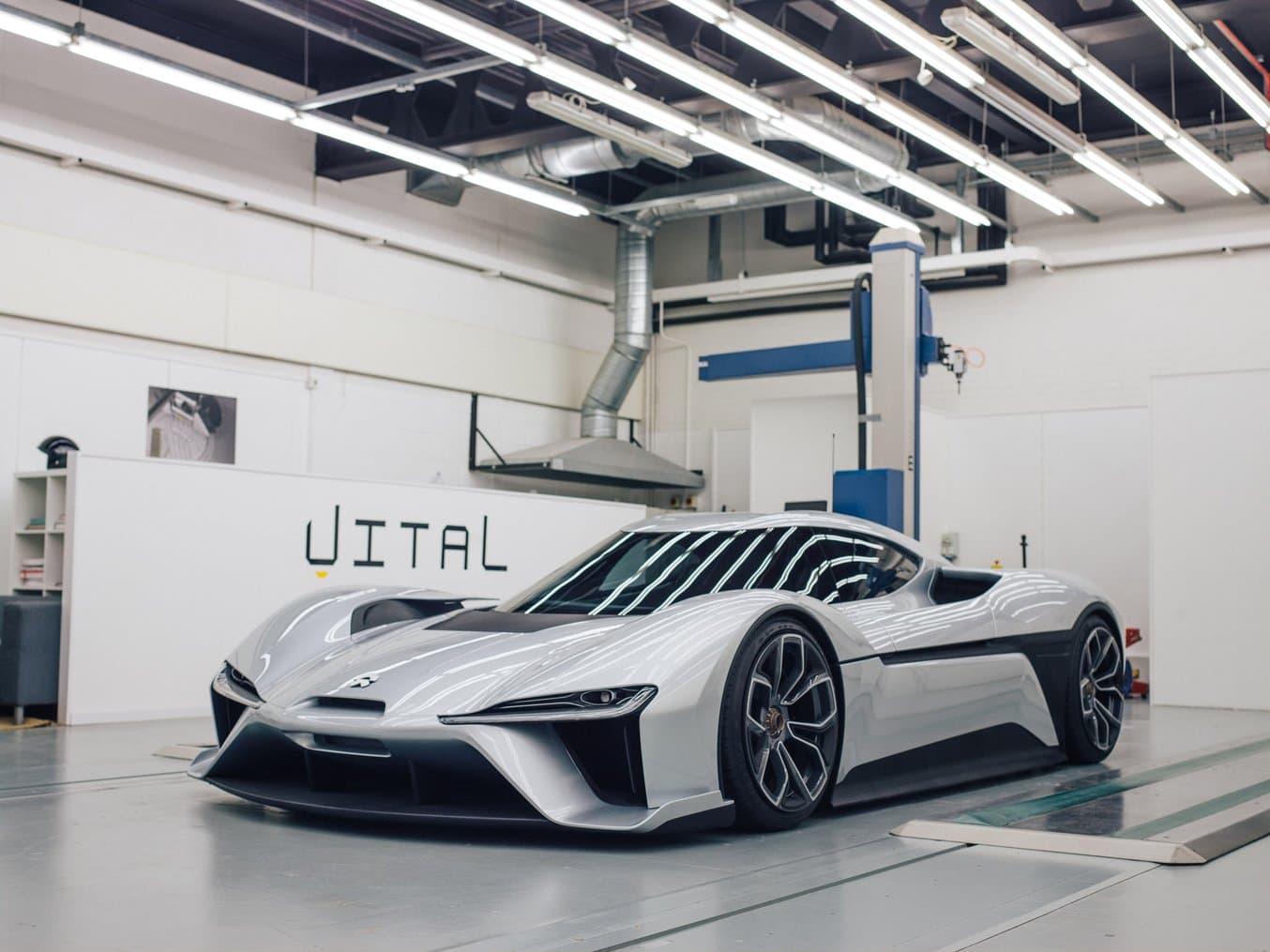
Vital Autoは、2015年に一緒に仕事を辞めた3人の友人たちがガレージで始めた会社です。彼らが最初に受注した案件は、スーパーカーNIO EP9のコンセプトカー製作でした。この案件をきっかけに、同社は極めてリアルで忠実なコンセプトカーの製作を手掛けるようになります。
クライアントの要望に応じて、紙に描いたスケッチから既に設計済の車両まで、どんな形からでもプロジェクトをスタートします。同社は白紙の状態からクルマを開発し、メインフレーム、外装、内装、開閉部、インタラクティブな要素すべてのデザインを手掛けます。1つのコンセプトに5名から30名が携わり、通常は3~12か月間でプロジェクトを完了します。
この間、一般的なショーカーは最大で十数回のコア設計を繰り返し、その中でクライアントの期待に沿えるよう更に小さな部品までを繰り返し設計し直すこともあります。
「私たちの業界では、市場投入前の製品評価手段として、バーチャル・プロパティに注目することは珍しくありません。しかし、物理的に製造されたモノにとっても同様の機会が必ずあると思うのです。正しい重量、正しい形の物体を手にしたときの感覚や感触、そして物理的環境がそのモノに対する認識をどのように変えるかという力学に勝るものはありません」とMoradi氏は言います。
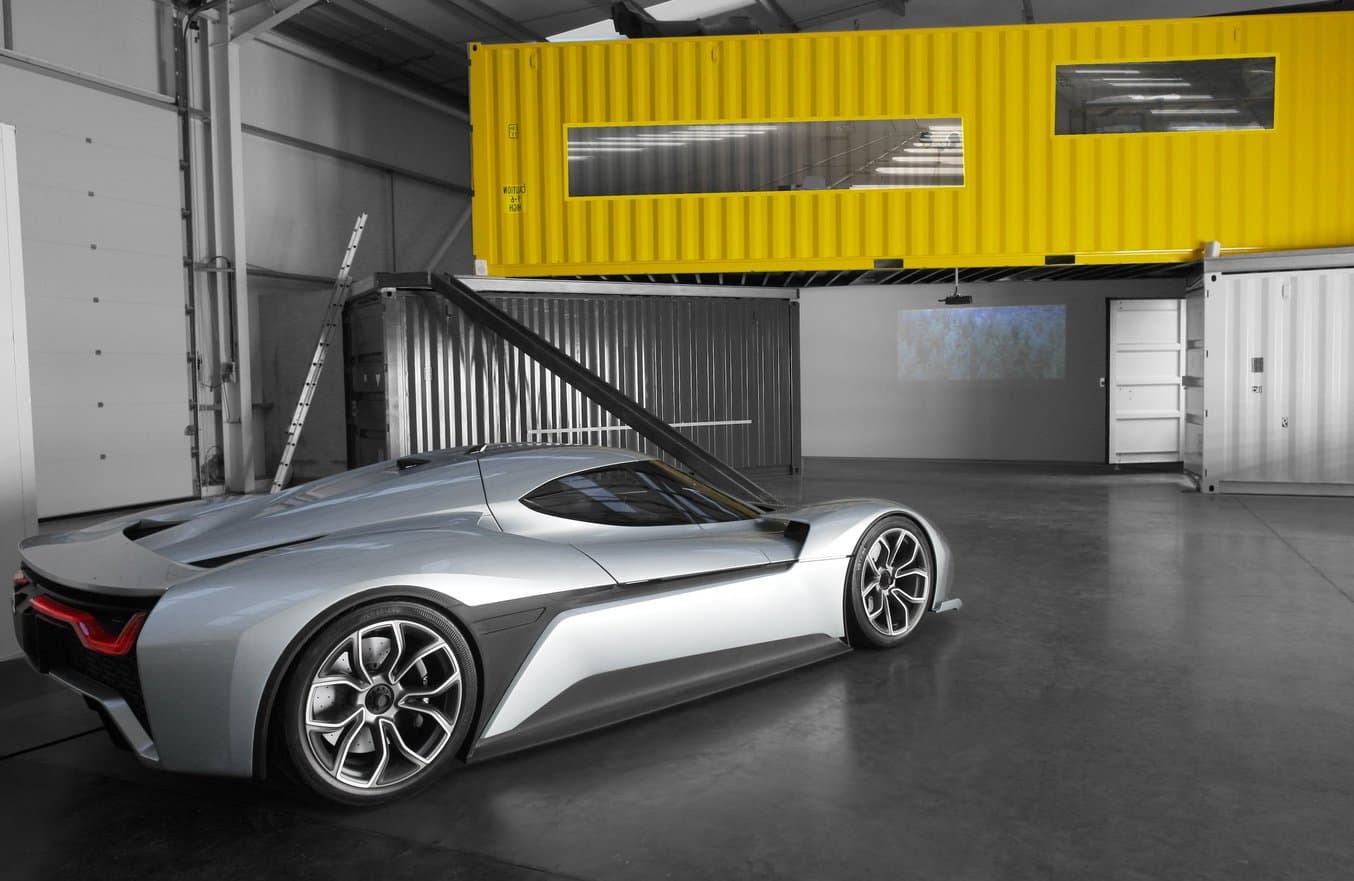
「私たちのお客様の多くは、新しいアイデア、革新的なアイデア、そして前例のない何かを持って相談に来られます。だから私たちにとっても毎日が新たな挑戦で、終わりがありません」と語るのは、アディティブマニュファクチャリングを担当するデザインエンジニア、Anthony Barnicott氏です。「これらの課題は、限られた時間でこの数の部品をどう作るかという所から始まり、持続可能な製品をどのように制作できるか、あるいは特定の性能と重量を満たした部品を製作できるかという点まで及ぶこともあります」
従来のショーカーは粘土をフライス加工して作るのが普通でしたが、同社は3軸・5軸CNC工作機、手加工、手作業でのクレイモデル製作、ガラス繊維強化プラスチック(GRP)などを活用します。しかし、こうした従来型の工法は、一回限りのカスタム部品を製作する場合には必ずしも最適な方法とは言えません。
「弊社では創業当初から3Dプリントを活用しています。製造工程に3Dプリントを導入しようと思ったのは、コスト削減のためだけではなく、お客様がさまざまなデザインやアイデアを実現できるようになると考えたからです」
現在、Barnicott氏は14台の大容量FDMプリンタに加え、Formlabsの大容量SLA光造形プリンタForm 3Lを3台と、SLS方式プリンタのFuse 1を5台も抱える3Dプリント部門全体を統括しています。
「キャパシティに関しては、すべてのプリンタが創業当初からほぼ100%稼働しています。私たちは、コンセプトから設計に至る全領域で3Dプリンタを活用しています。通常、生産ベースの部品はFuse 1で、コンセプトベースの部品はForm 3Lで製作しています」とBarnicott氏は言います。
Form 3Lで複数の材料から複雑な設計を実現
「高度な表面品質が求められるものは全て、Form 3Lを使って製作しています。自動車の内装には通常、レザーやアルカンターラ、または他の布類で縁取りされていない部品があります。Formlabsの材料は塗装職人が作業しやすい、きれいで滑らかな表面品質に仕上がるため、プリンタから取り出した部品をそのまま車両に使用することができます」とBarnicott氏。
彼はさらにこう付け加えます。「私が最も注目しているのは、Form 3Lの多機能性です。5分以内に材料の切り替えができ、その材料も柔らかで弾性のあるものから硬く高強度なものまで揃っており、その材料の幅が私たちにとっては非常に重要なことなのです」
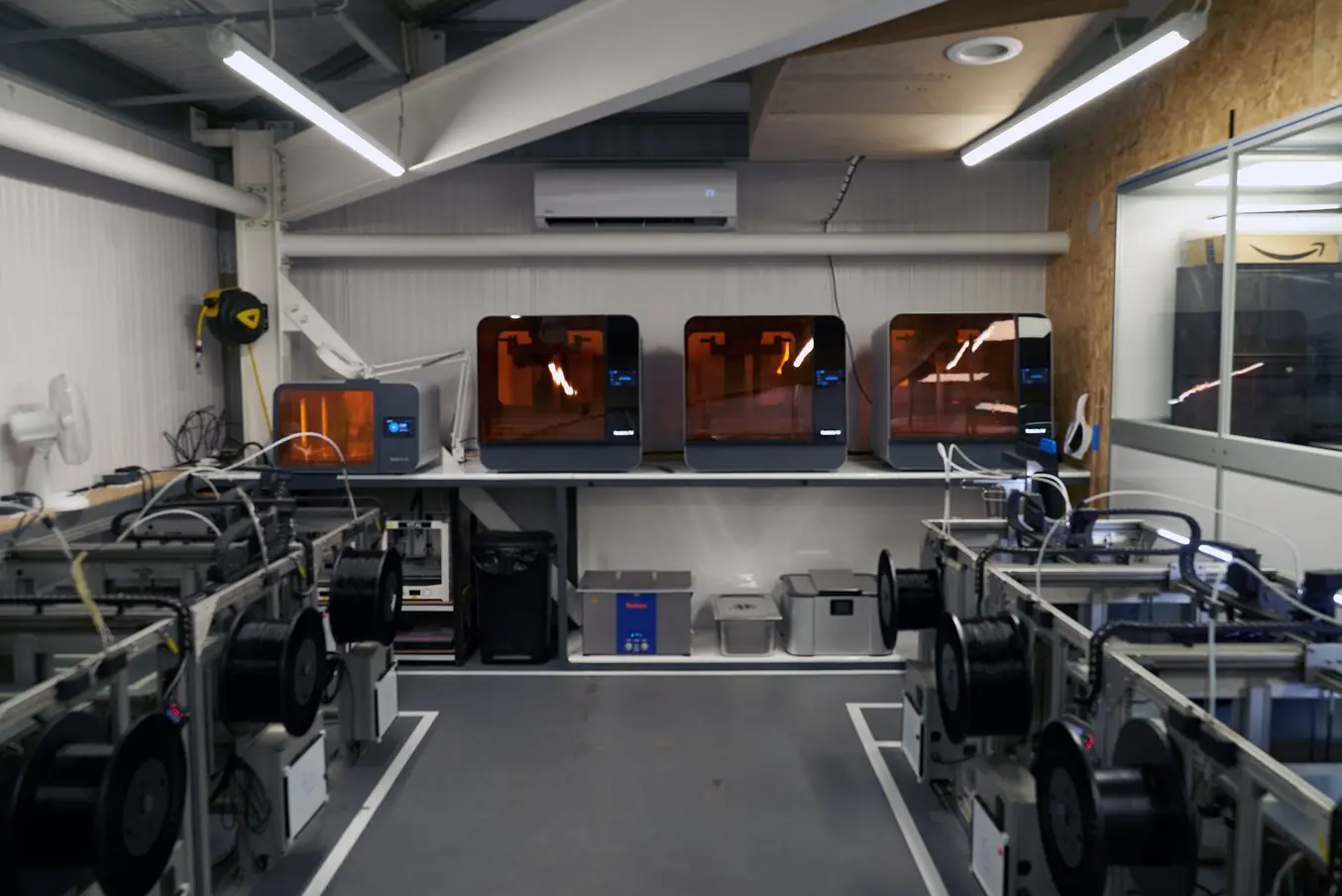
同社はForm 3Lで使用できる多種多様な材料を、以下のような様々な用途で活用しています。
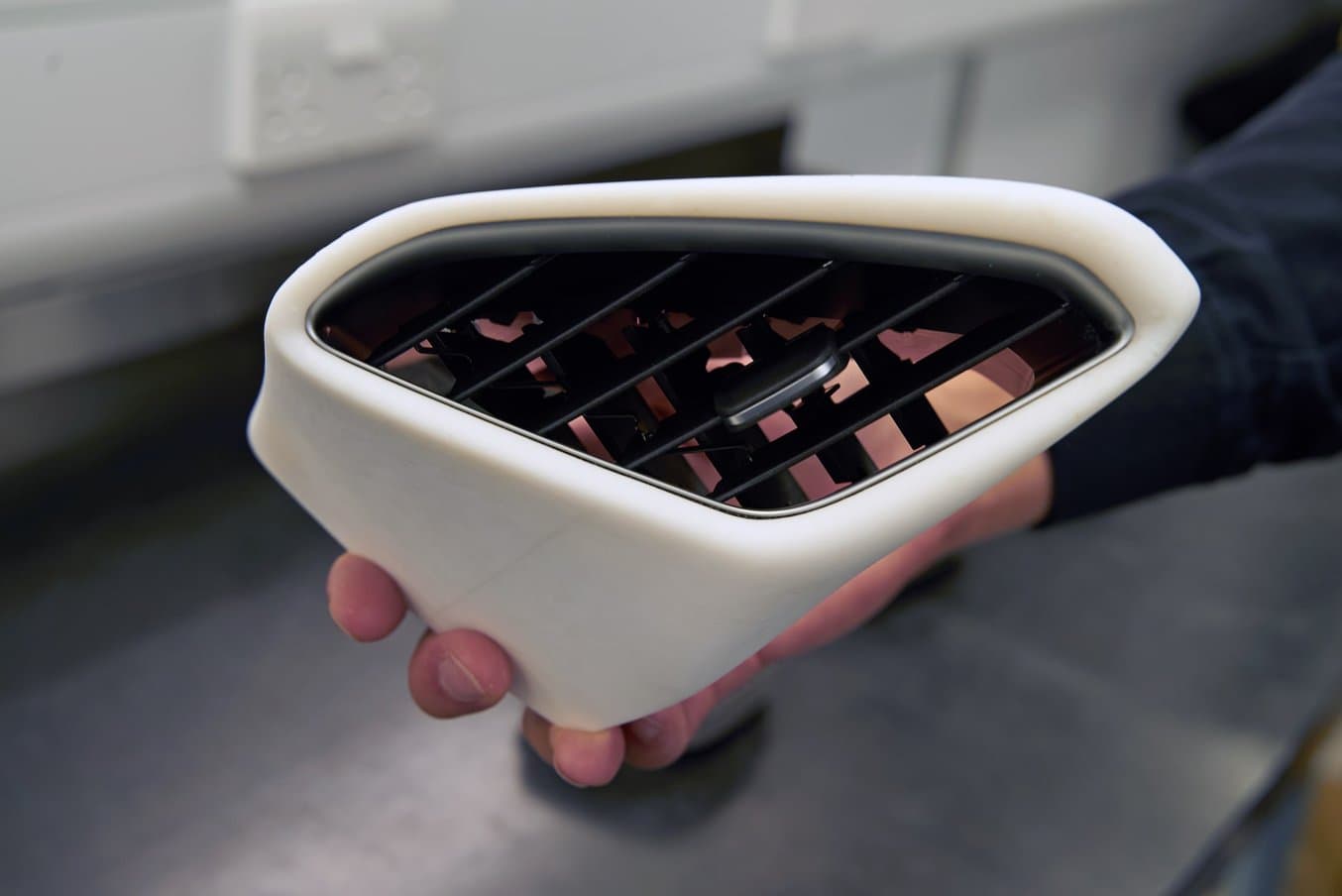
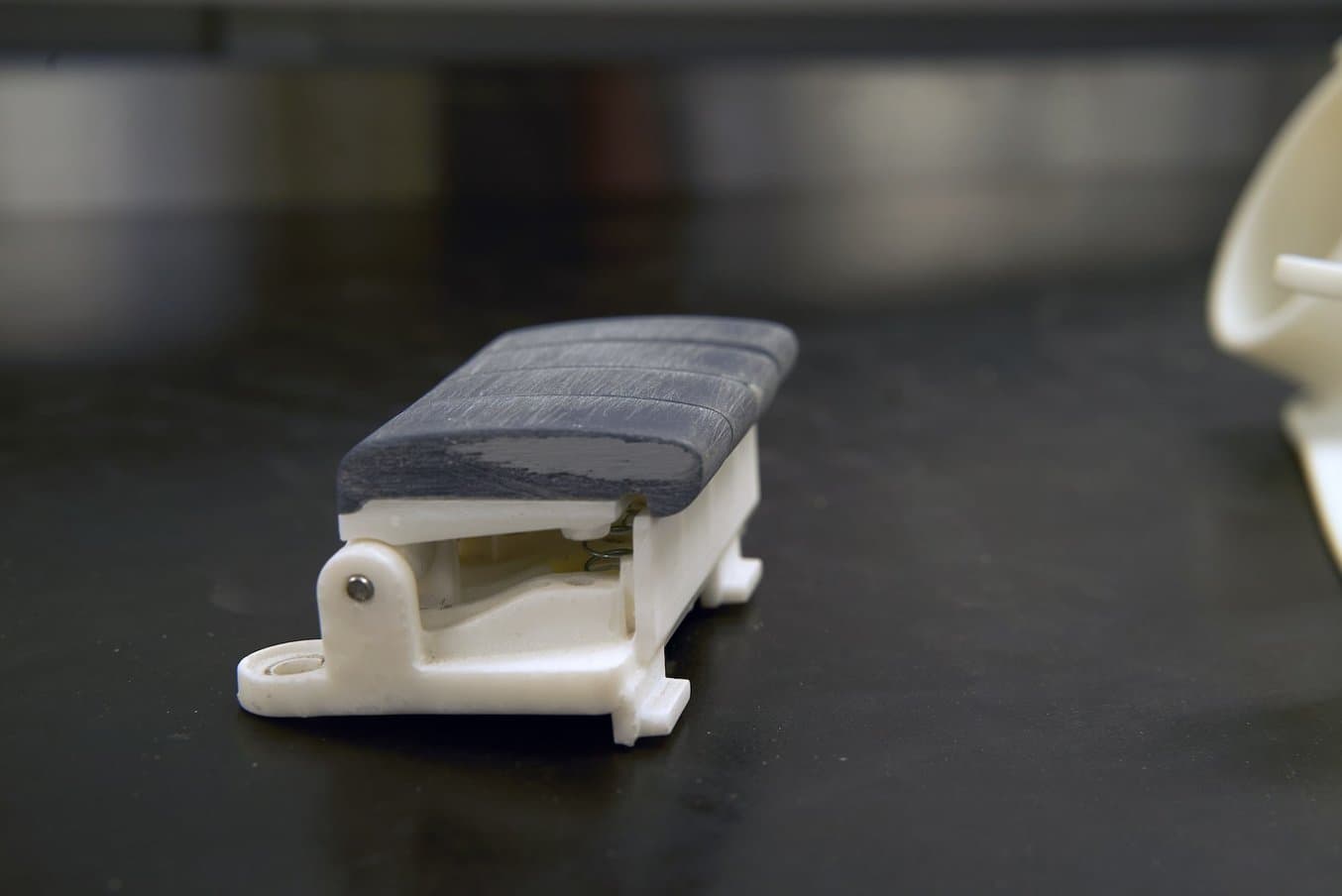
スイッチパック
「小型スイッチパックのような非常に複雑な設計の場合、複数の材料を用いて、正しく機能するだけでなく実際の環境での使用にも耐えられる機能製品を作る必要があります。[このスイッチパックの]表面にはTough 2000レジンのような硬質材料を、内部には軽量でコストパフォーマンスの高い材料を採用しました」
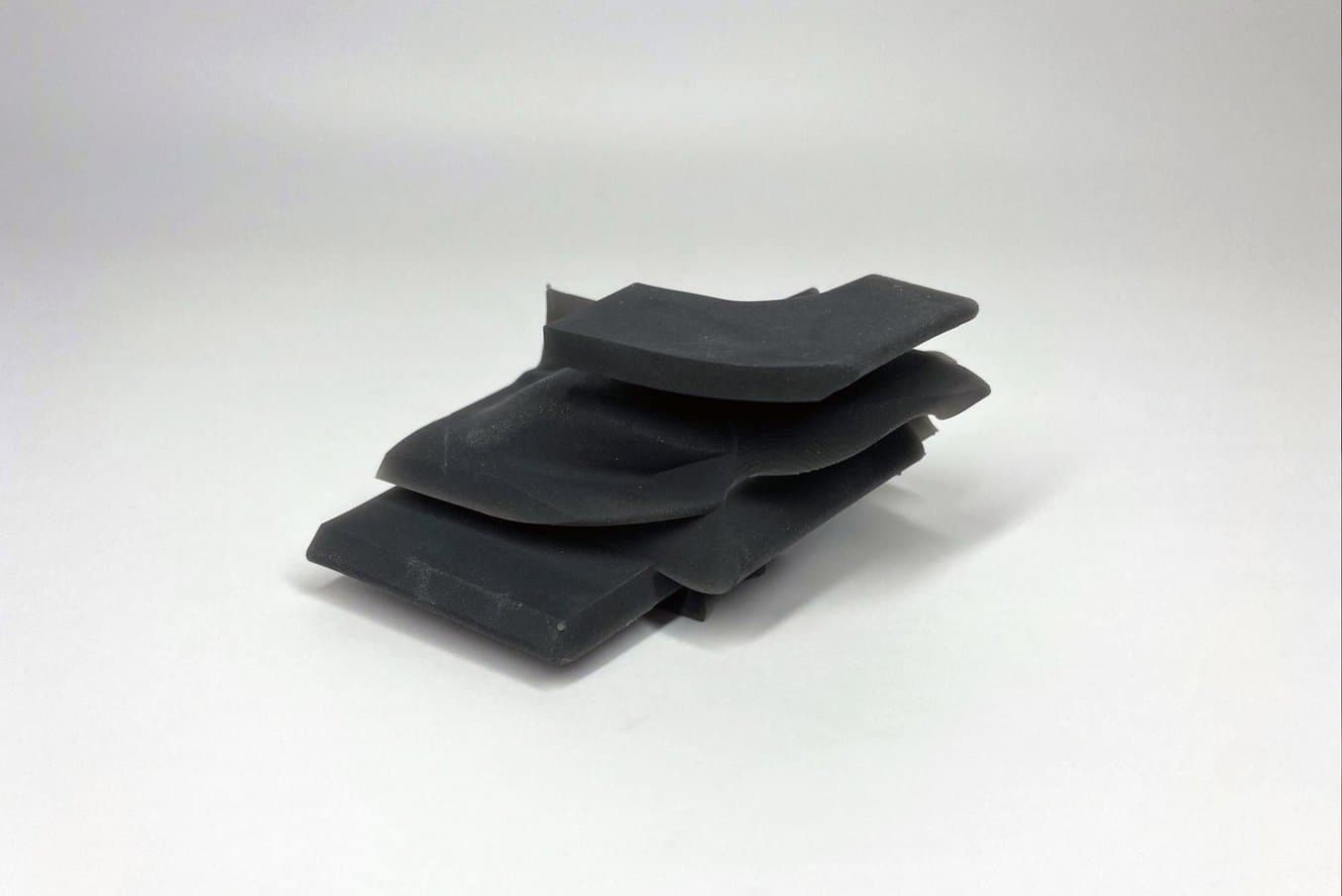
ドアシール
「一般的に自動車のドアシールは製造コストが非常に高く、押出成形以外に現実的な製造方法がありません。ですが、金型製作に莫大な費用がかかるうえ、製作期間も長くなってしまいます。そこで私たちは、Formlabsの新材料の1つであるFlexible 80Aレジンを試すことができました。Form 3Lのおかげで、様々な形状をテストするために必要なドアシールの一部を夜のうちに製作することができました。しかも、実際の設計の50ミクロン以内で造形できたんです」
Form 3Lの導入により、同社では殆どのケースで24時間以内に何度も繰り返し部品を生産することが可能になりました。同社は最終的に3台のForm 3Lを導入し、その結果3種類の異なる材料を使った場合でも最大3種類の部品を同時に製作できるようになりました。同社は削減できたコストをクライアントに還元、あるいは同額でさらに多くの設計パターンを提示することで、付加価値を提供しています。
「アディティブマニュファクチャリングの最大のメリットの1つは、製作期間が短縮できることです。ですから、短縮できた時間で何ができるか、が大切なのです。私たちは、その時間を別の設計案を考えることに費やし、より多くの試作・検証を行えるようにしています」とMoradi氏。
「既にForm 3L無くしては作ることができない製品も多々あるのです。7軸加工などの最先端の工法ならこうした部品を製作することもできますが、その代わり莫大なコストがかかります」とBarinicott氏は言います。
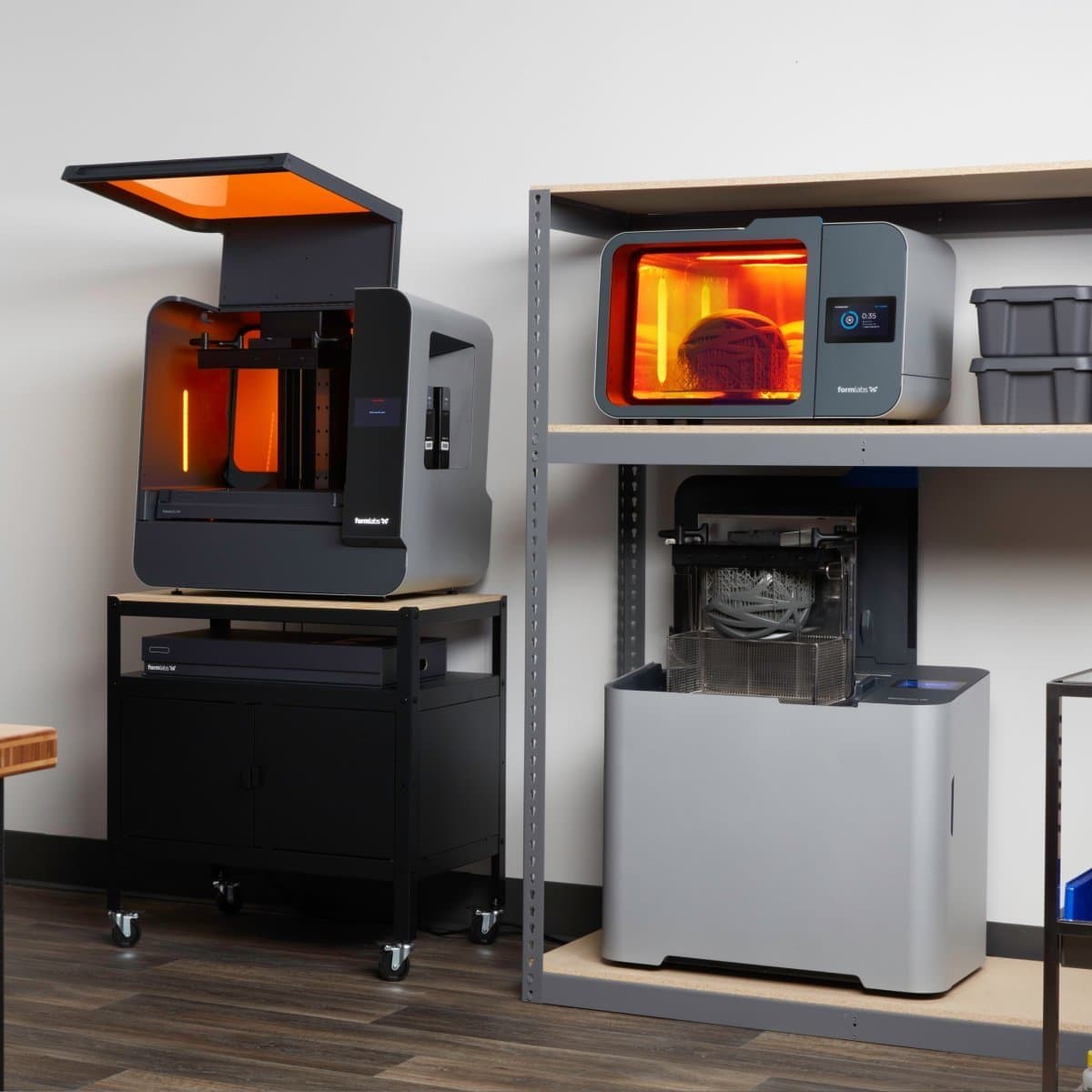
Form 3Lプリンタ製品のデモ
Form 3LやForm 3BLプリンタ製品の詳細、大型造形に対応した最新の後処理機について詳しく知りたい方は、KyleとChrisによるこちらのデモにて、後処理を含むForm 3Lの作業手順をご確認いただけます。
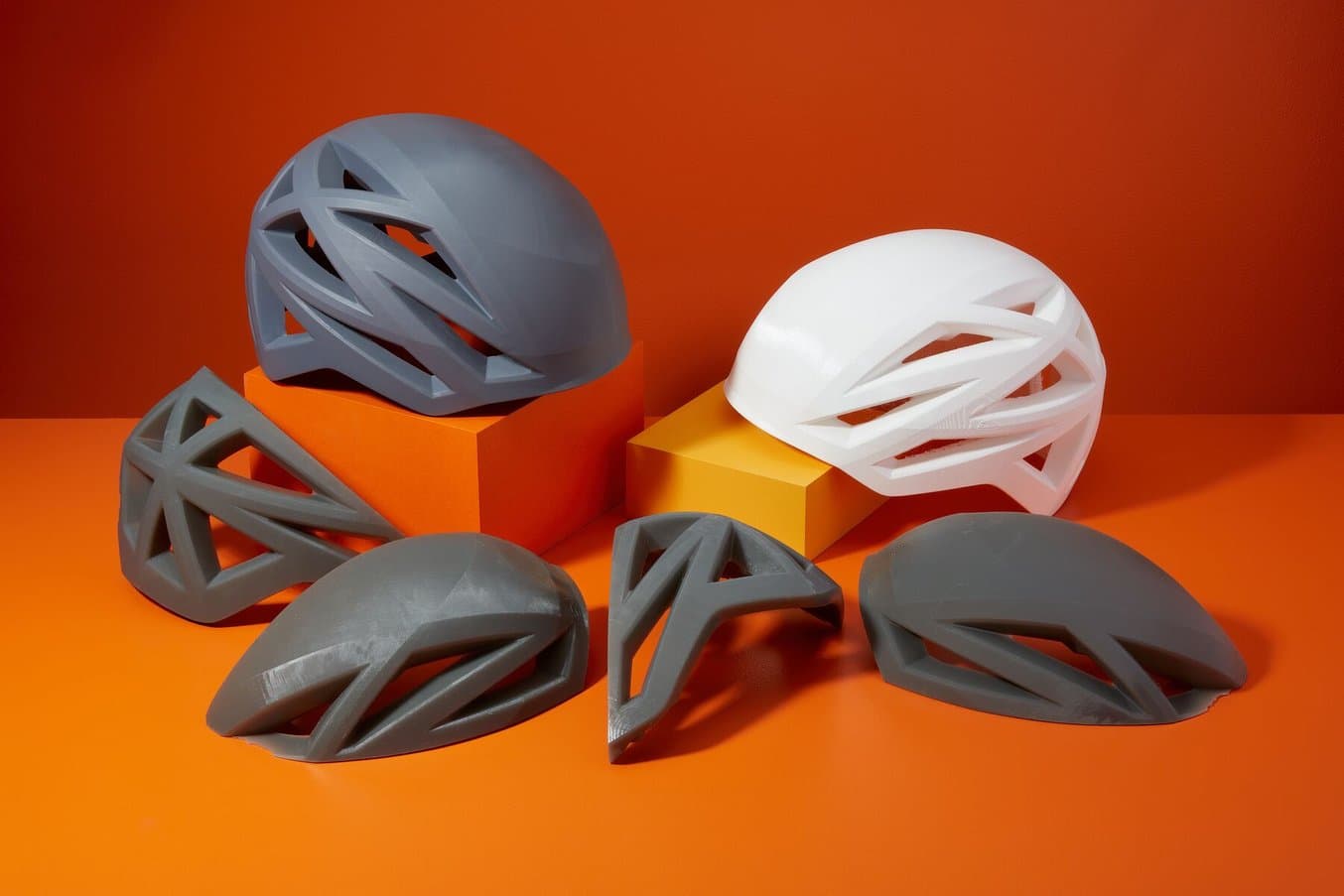
大容量3Dプリンタが有用になるケースとは
本資料では、Form 3L製品の詳細、そしてその他の大容量プリント方式との違いについてご説明します。この無料レポートでは、Form 3Lを使った大容量3Dプリントの内製化と、外注やFDMプリンタによる生産を中心とした他の方法とを比較し、どのような違いがあるかを見ていきます。
機械部品のCNC加工をFuse 1で補完
「Fuse 1は、私たちにとって初挑戦となるSLS方式技術でした。私たちのような小さな会社にとって、SLS方式は決して現場に置くことができないと思っていた技術です。ところが、Fuse 1は1台だけでなく、実は5台も現場に設置することができています。5台のFuse1によって、検証用だけでなく実際にコンセプトカーで物理的に使用するための複雑な構造の機械部品を非常に高速に作れるようになりました。この工程は通常CNC加工が必要で、形状によって内製か外注かを決めるのですが、部品が手元に届くまでには2日から4日は待つ必要がありました。Fuse 1の導入によってこれら全てを内製できるようになり、大抵は24時間もかからずに部品が完成するようになりました」と Barnicott氏は言います。
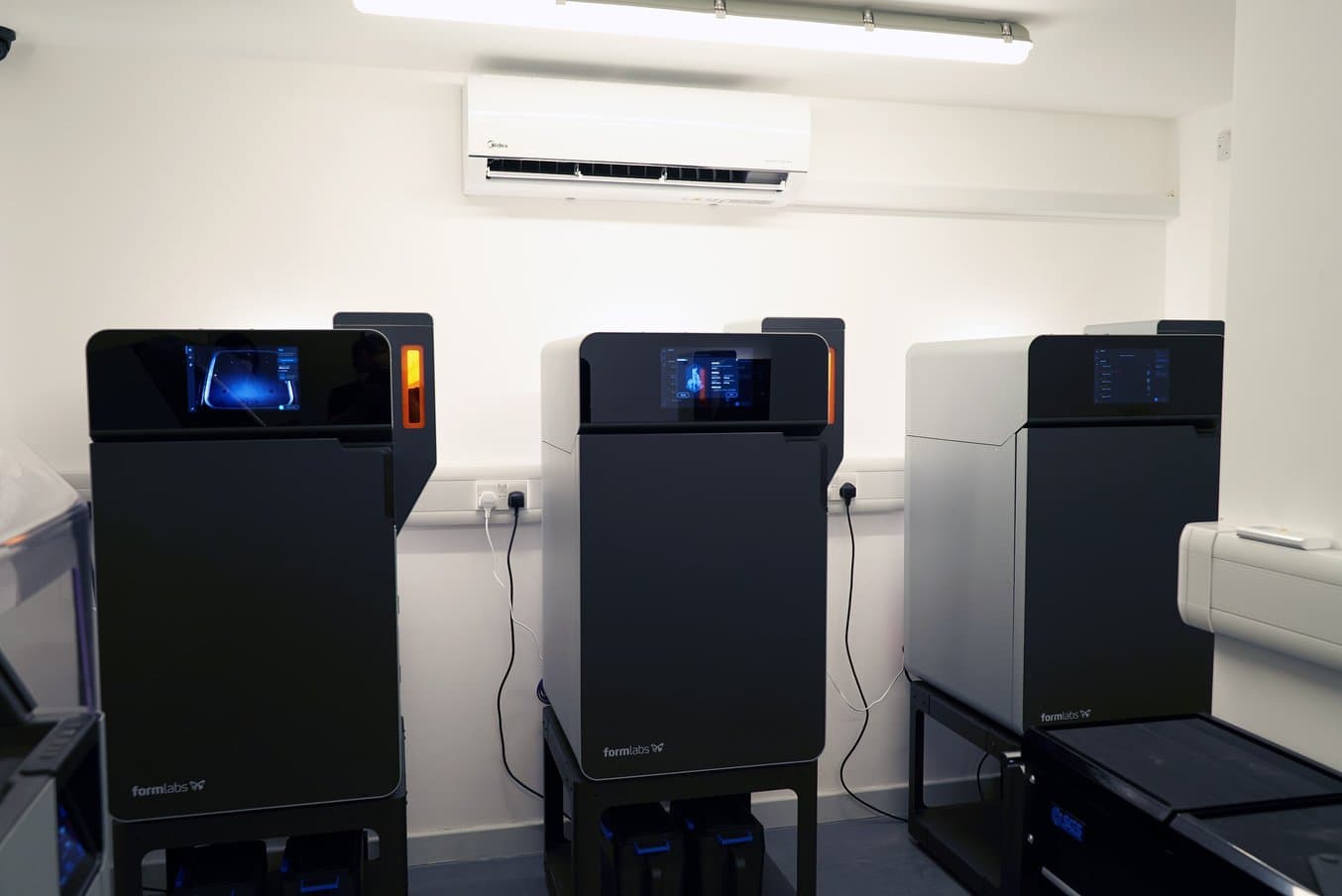
チームは主に、ドアヒンジ、インナードアハンドル、ドアの内部構造、車体構造に用いる機械部品の製作にFuse 1を使用しており、造形後は最小限の表面処理だけで、すぐに使える部品が出来上がります。同社がFuse 1で製作した部品には以下のようなものがあります:
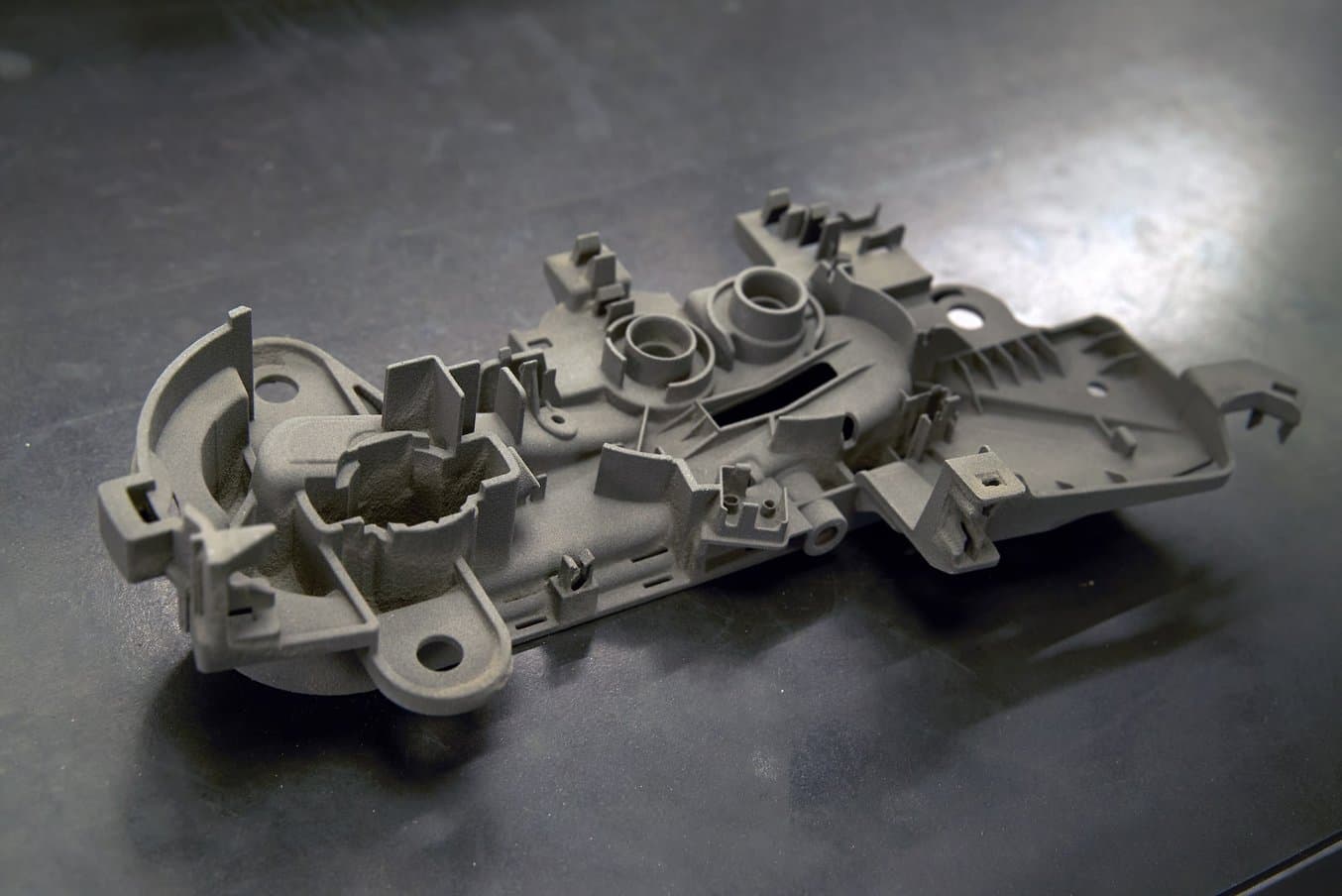
ドアハンドル
「自動車の内装部品の多くは、射出成形でないと製作が非常に難しいのです。内部エアダクトや通気口などは決して目に見えるものではありませんが、製作には高額な費用がかかります。そこで私たちは、こうした部品の製作にもFuse 1を活用しています。従来のように巨額なコストをかけることなく、車両に搭載するデザインの幅を大きく広げることができています」
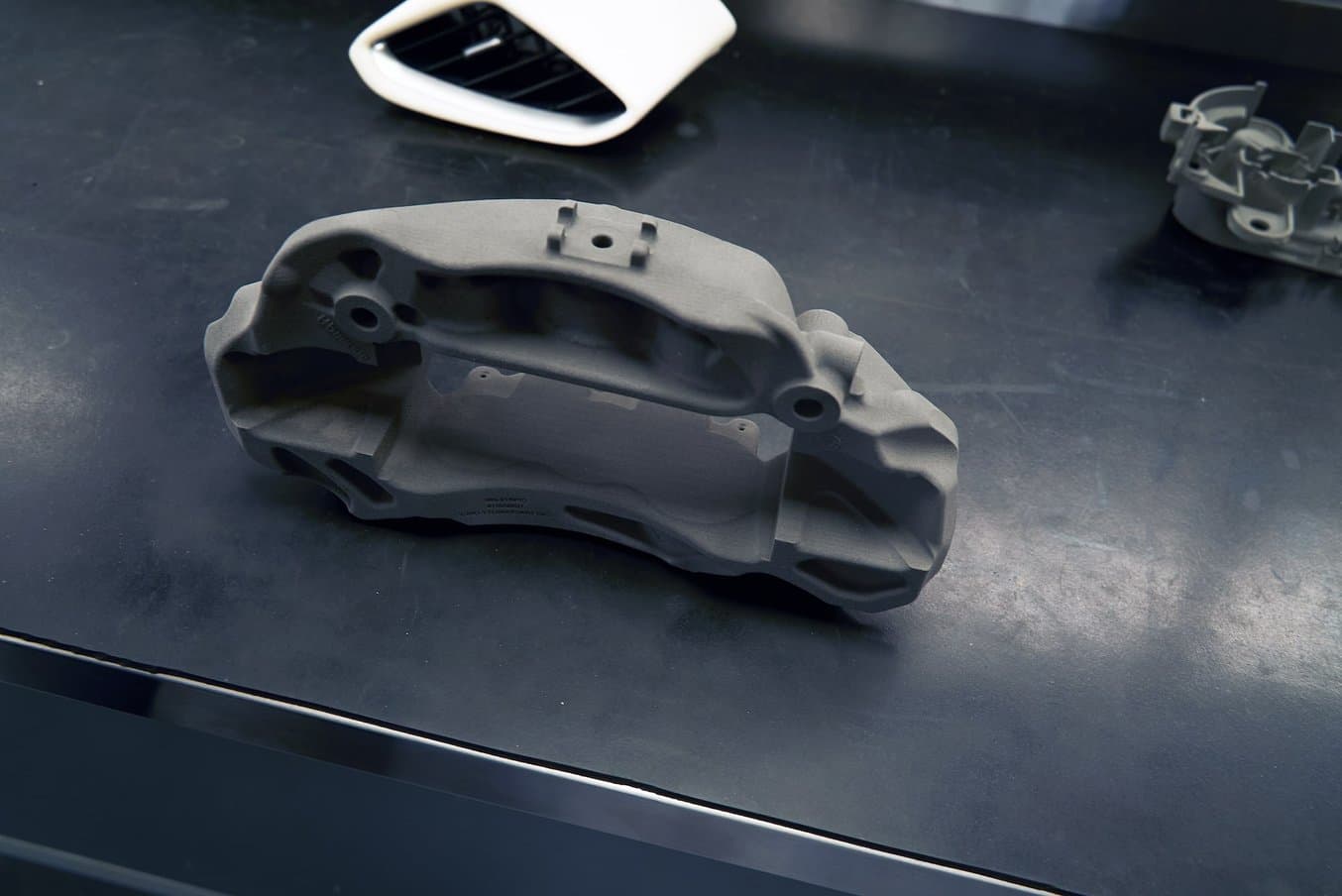
ブレーキキャリパ
「ある特定の部品で会社のロゴの見栄えを確認するためだけに、部品製作が必要になることもあります。部品製作の後にロゴをつける工程が発生するので、他のケースより迅速な部品製作が求められます。Fuse 1を使用することで、ブレーキキャリパ等の部品を製作した後、様々な場所に様々な色のロゴを入れ、お客様に確認してもらうことができています」
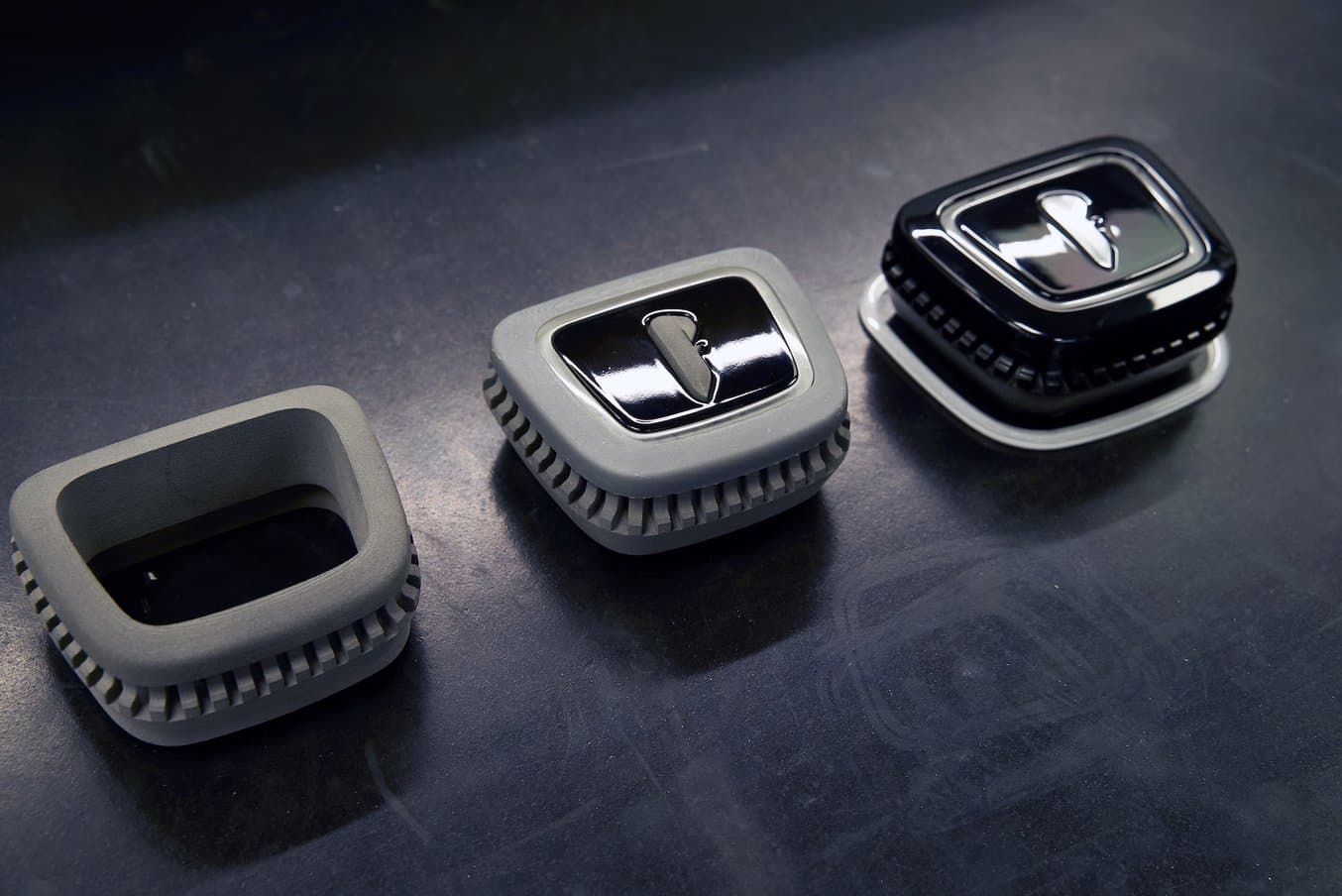
スーパーカー向けインタラクティブ・コンセプト
「3Dプリントを導入したことで、SLA光造形用とSLS方式用の両方の材料を組み合わせて、設計パターンを何度も確認できるようになりました。これにより、それぞれの材料特性を生かしながら、最終的な設計が確定するまで何度も高速で試作製作を行うことができます。機械部品から透明部品に至るまで、あらゆる部品の外観や機能検証でも同じです」
アディティブマニュファクチャリングはサブトラクティブマニュファクチャリングに取って代わる工法だと言われる中、Vital Autoのチームは両方の技術を組み合わせ、それぞれの長所を生かすことにメリットを感じています。
「弊社では、2つの工法を組み合わせることで互いの足りないところを補完しあっています。サブトラクティブマニュファクチャリングで作る部品も数多くありますし、きめ細かなディテールを表現したい場合にはアディティブマニュファクチャリングを使います。これにより、多くのコンセプトモデルをより費用対効果の高い方法で製作することが可能になりました」とBarinicott氏は言います。
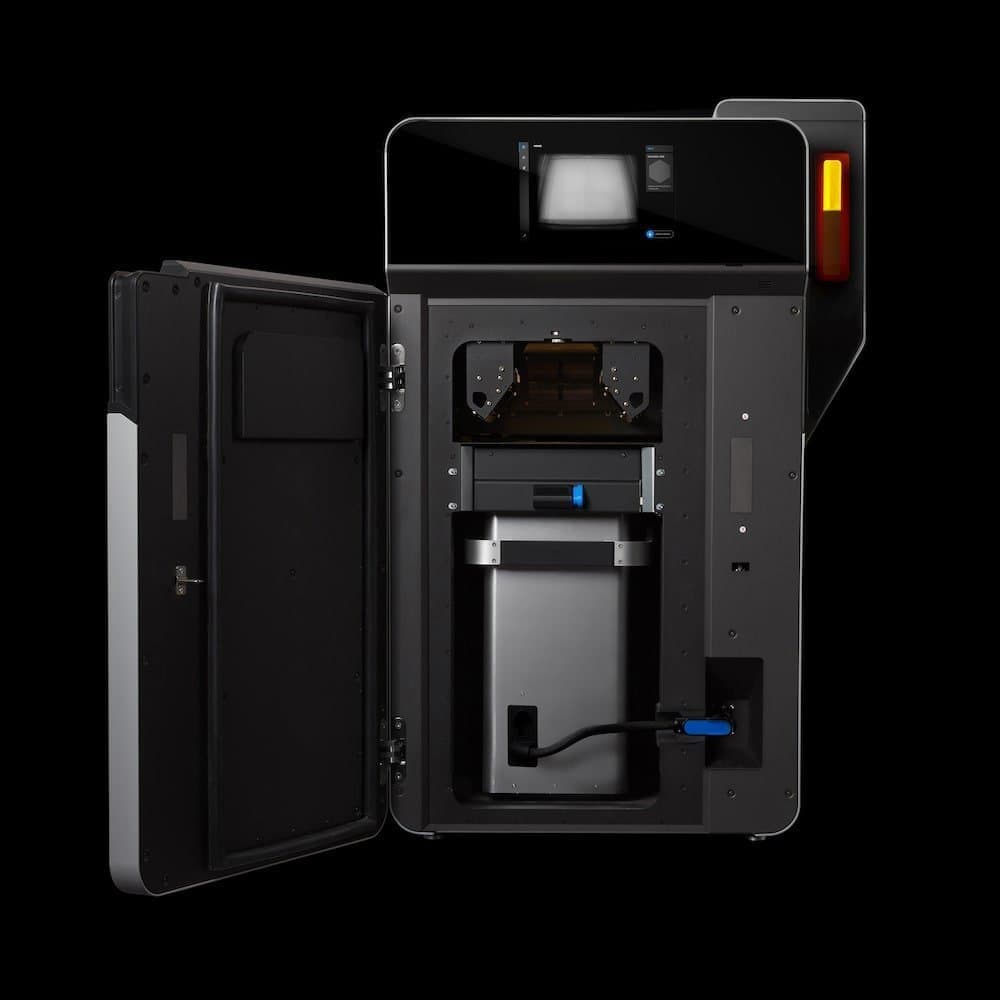
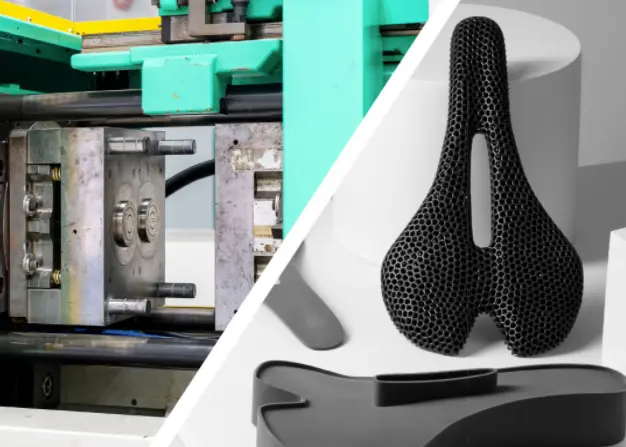
SLS 3Dプリント vs 射出成形:金型レスに切り替えるべき時は?
本技術資料では、実際のユースケースに基づいてコストの違いを解説するとともに、SLS方式3Dプリント、射出成形、またそれらの併用についてのガイドラインをご紹介します。
3Dプリントで再現性の高いコンセプトカーを製作
「過去10年間での3Dプリント技術の進歩は驚異的です。導入当初は少量生産のニッチな車両に使っていましたが、今では3Dプリンタ無しでは作れない製品もあります。そして、これらの部品を単に製作できるようになっただけでなく、非常にコスト効率良く、そして非常に高速で生産できるのです」とBarinicott氏は語ります。
3Dプリントは、チームがより良い製品をより速く作ることを可能にするだけでなく、新しいビジネスをも呼び込んでくれています。同社は、最新技術を使ってみたい、あるいは最先端の材料で部品製作をしたい、という思いから彼らを頼ってくれる顧客が多くいることに気がつきました。
「もはや新興技術とは呼べないようなテクノロジーがあり、3Dプリンタもその1つです。様々な工夫を凝らすことで最終製品として使えるレベルにまで進化しています。3Dプリンタは、もはや目新しいものではなくなり、私たちの仕事とは切り離せないものになりました」とMoradi氏は言います。