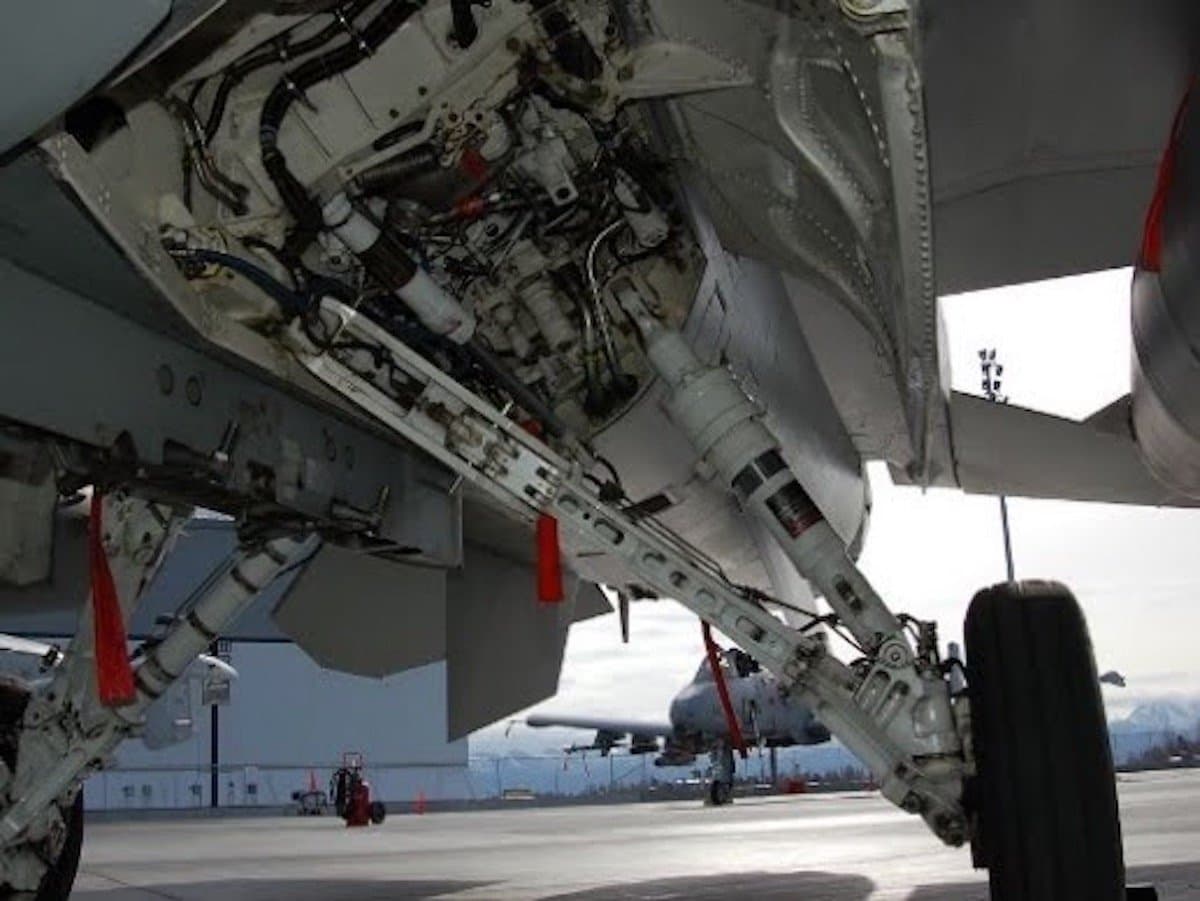
米国防総省(DoD)管轄のジェット機は、1時間飛行するごとに約12時間のメンテナンスが行われます。各航空機が安全かつ最高のパフォーマンスを発揮するためには、メンテナンス、修理、総点検(MRO)の作業が欠かせませんが、手作業や旧式のプロセスが多く存在し、作業時間が長引くことも日常茶飯事です。
このオペレーションの改善とワークフローの効率化を模索する国防総省から依頼を受けたFigure Engineeringは、Formlabsの新しいオープンエコシステムを活用し、手頃な価格ながら革新的なソリューションを生み出すことに成功しました。
Figure Engineeringは、FormlabsのForm 4 SLA光造形3Dプリンタのスピードを活かし、電解めっき処理を行う際のマスキングに使用できる新たな材料を開発しました。Figure Engineeringの共同創設者 Jonathon McDaniels氏率いる同社チームは、PreForm設定エディタとOpen Material Modeの利用で材料開発プロセスを最適化し、数百万ドル規模の課題に対する新たな解決策を見つけることができました。
「汚い」「退屈」「危険」が革新的なソリューションの始まり
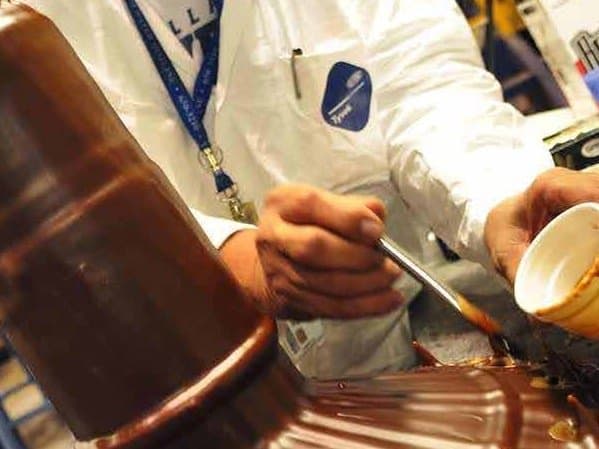
電解めっき処理を行う部品に手作業でラッカーを塗ってマスキングするが、使用材料が人体に有害な場合は危険が伴う。作業者がこの成分に一定以上晒されるとプロジェクト全体が中断され、航空機が長時間飛び立てなくなる可能性がある。
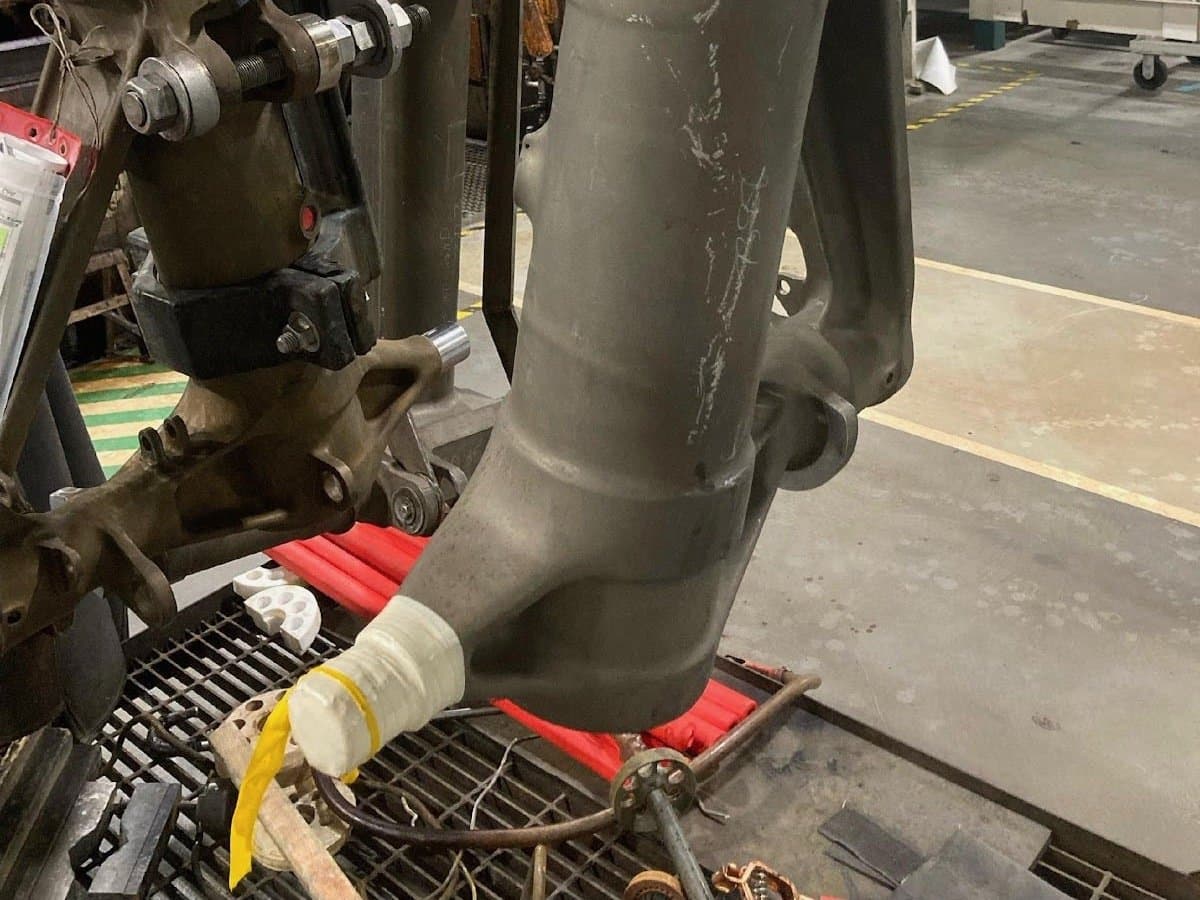
同様に、手作業でテープを貼ってマスキングする場合にも膨大な時間と作業量が必要。すべての部品に対してこの作業を繰り返すため過剰な人件費が発生する。
Figure Engineeringは、主にDoDのさまざまな部門の請負業者として先進的な製造及び維持管理ソリューションを開発していますが、民間企業とも提携しています。米国空軍、海軍、陸軍、ならびに民間航空会社が運航する航空機について、Figure EngineeringはMROプロセスの中で見落とされがちな処理、つまり研磨、塗装、電解めっき、コーティングに焦点を当てた解決策の提案を求められました。
これらの作業は俗に、Dirty(汚い)、Dull(退屈)、Dangerous(危険)を意味する「3D」と呼ばれています。こういった作業はエンジンの交換や新しいウィングチップの技術開発などと比べて目立つ功績や理解が得られない分野ではありますが、航空機のパフォーマンスに影響する大切な要素です。ワークフローが非効率で作業に時間がかかると、軍事的な準備態勢に影響を与えたり運用コストの大幅な増加を招いたりするだけでなく、有害な化学物質を扱うためにMRO作業者の安全にも影響を及ぼす可能性があります。
こういったプロセスをより安全で高効率なものにするための革新的なソリューションの開発を専門とするFigure Engineeringは、米国空軍のデポ(修理施設)と長年協力してきました。「最良のソリューションを生み出すためには、実地でプロセスに関わる人たちとの協力関係が不可欠です。工程における課題を最もよく理解しているのは彼らですから。電解めっき処理のプロセスについては、『航空機がもっと早く飛び立てる状態にしたいし、大量の廃棄物が出ていることも気になる』というコメントがありました」と、McDaniels氏は当時を振り返ります。
課題は航空機の電解めっき処理にあり
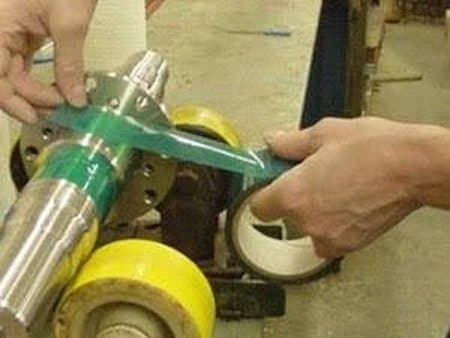
手作業でテープを貼る。
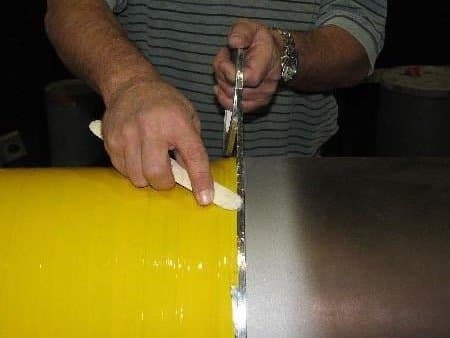
手作業でテープを整える。

マスキングを施した部品を電解めっき処理用の槽に浸す。
航空機のMRO作業の中で最も困難で時間のかかる工程のひとつが、大型着陸装置の電解めっき処理です。その作業工程には、非常に強力な薬液に部品を浸したり、後で除去可能なラッカーを塗布したりテープを貼ったりしてめっき処理を施さない部分のマスキングをするなど、何時間にも及ぶ骨の折れる手作業が含まれます。
「コーティングを必要な場所のみに正確に施し、それ以外の場所に影響を与えないようにするには、手作業では非常に労力がかかり、作業自体も単調で、コストがかさみます。修理施設は、この手作業の時間を短縮し、クランプやボルトで固定できるマスキングを開発したいと考えていました」とMcDaniels氏は言います。
しかし、電解めっき用のマスキングの設計・試作を開始した時、Figure Engineeringは一筋縄ではいかない課題にぶつかりました。「最初の調査でわかったのは、電解めっき処理の過酷さに耐えられる材料がないということです。常に落下やハンマーによる強い衝撃に耐える必要があるので、強力な耐薬品性の他にかなり高い耐衝撃性を備えた高強度材料が求められます」と、McDaniels氏は言います。
材料の選定に加え、最適なプリンタ選びも難航しました。「最初はあらゆる選択肢を検討しました。使いやすく安定していて、修理施設にいながらでも広範なサポートを提供してくれる、信頼できるメーカーのプリンタを見つける必要がありました」と、McDaniels氏は続けます。
FDM(熱溶解積層法)方式やSLS(粉末焼結積層造形)方式の3Dプリンタで何度か試作品を製作したところ、造形品の表面を完全に非多孔質にする必要があることがわかりました。FDMやSLSの造形品の場合、電解めっきプロセスで使用する薬品が表面から内側に浸透してしまい、槽から取り出した後も造形品から有害な薬品が漏れ続けてしまうためです。そこで、光造形方式が選ばれました。Figure Engineeringは複数の3Dプリンタを試しましたが、Formlabsのプリンタが群を抜いていたと言います。
「かなり早い段階から、Formlabsと仕事をしたいと明確に感じるようになりました。他より低コストながら機器の品質は高く、プリンタ自体も非常に信頼性が高い。ブランドの知名度が高いことからも、Formlabsが最適な選択肢でした」
Figure Engineering 共同創設者、Jonathon McDaniels氏
McDaniels氏はForm 3+からスタートし、Open Material Modeを使って造形設定の微調整やカスタムレジンの配合を繰り返しました。Form 4が登場すると、この反復プロセスが大幅に加速し、カスタムレジンの開発が一気に進展したと言います。
「Form 4が登場した時、多くの問題が一夜にして解決しました。Form 4では非常に難しい材料の造形が可能になるので、状況が一変しましたね。今は電解めっき処理のプロセスに耐えられるような材料を開発するべく、ポリマーを使ったアディティブマニュファクチャリングの限界に挑戦しているところです」と、McDaniels氏は未来を見据えます。
Formlabsのオープンエコシステムで独自材料を開発
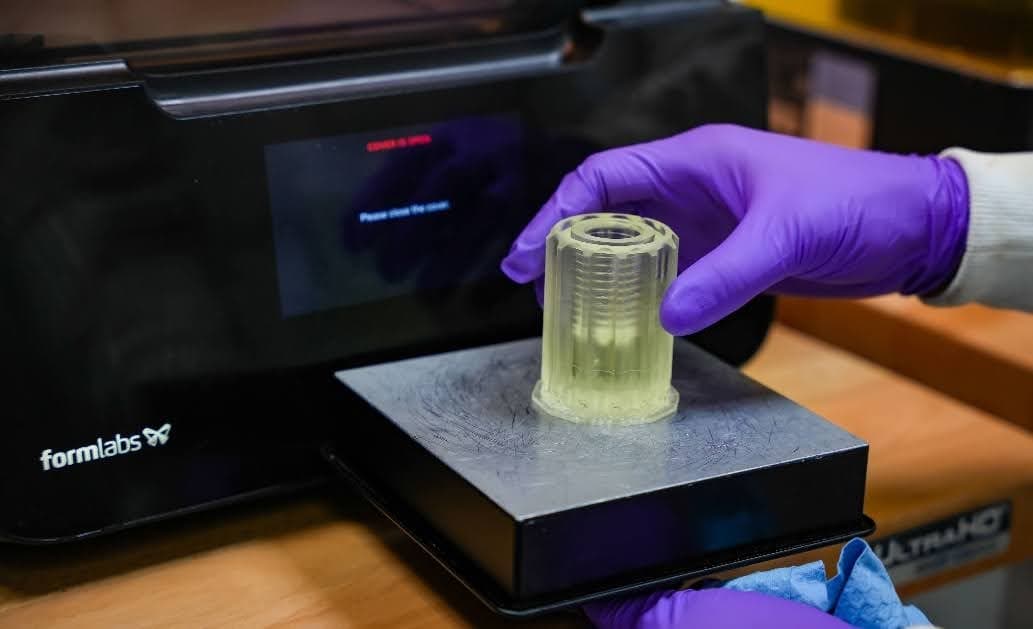
Form 4によって勢いを手にいれたFigure Engineeringは、1日に試せる反復回数が3倍に増えたことで迅速なフィードバックを取得し、短期間でより多くの造形設定を試せるように。
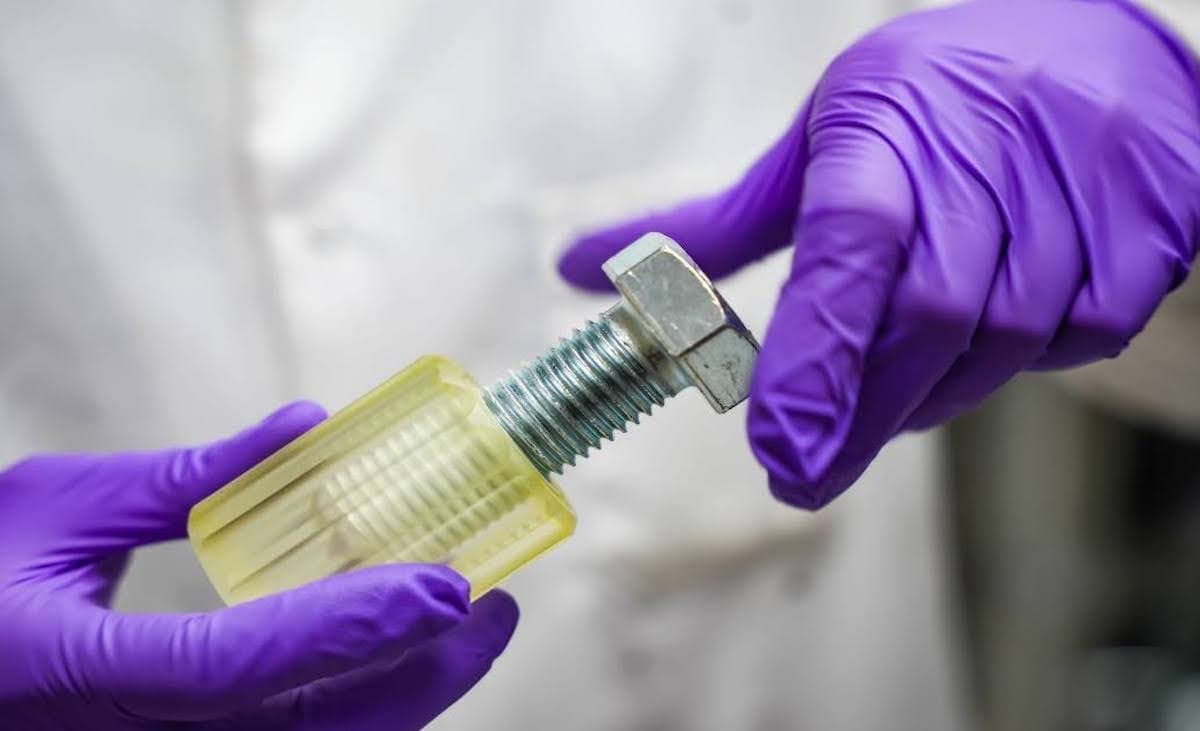
Figure Engineeringが開発した独自材料は強力な耐薬品性を備え、丈夫で再利用可能なマスキングツールを製作できるように。写真のツールは大型のボルトに直接回しはめることができる設計で、電解めっき処理で使用する。
Form 4の高速造形により、Figure Engineeringはこれまでの2倍以上ものテストを実施できるようになりました。しかし、完全に機能的で技術的にも高度な新材料の開発に繋がったのは、造形設定の微調整でした。
「Open Material Modeと造形設定の編集機能がなければ、実現できなかったと思います」とMcDaniels氏は言います。新材料を開発し、造形設定を調整するには、各設定が造形品にどのような影響を与えるかを正確に理解している必要があります。McDaniels氏の化学工学分野での経験のおかげで、Figure EngineeringはFormlabsチームと協力して特定の設定を最適化することができました。「造形設定の編集はとても簡単でした。プリンタの仕組みや、どのようにしてレジンがモデルの形に積層されていくのか、最初の数レイヤーがどう固着するのか、といった情報についてもガイダンスをもらうことができました。数値が適正の範囲内に収まるようにさえすれば正しく造形できるので、そこだけ理解すれば使い方はとても簡単です」とMcDanielsは言います。
作業量とコストを削減
電解めっき処理で使用するマスキングツールに適したレジンの開発には、既存のシステムでは利用できない独自の材料特性が必要でした。Formlabsは、Figure Engineeringが研究の基盤として使用できるプラットフォームとして、高速で信頼性の高い3Dプリンタと必要な造形設定やソフトウェアへのアクセスを提供したほか、McDaniels氏のチームと協力してサポートを提供するチームも割り当てました。
Figure Engineeringが開発した独自レジンは、すでに米空軍のMROデポ(修理施設)1か所で導入されています。マスキングツールの設計・造形が完了しさえすれば、マスキング作業に取り入れるだけで航空機部品の電解めっき処理の準備にかかる時間が大幅に短縮されます。「このプロセスで手作業にかかる時間を削減し、化学薬品で満たされた槽から作業員をできるだけ遠ざけることが目標です」とMcDaniels氏は言います。
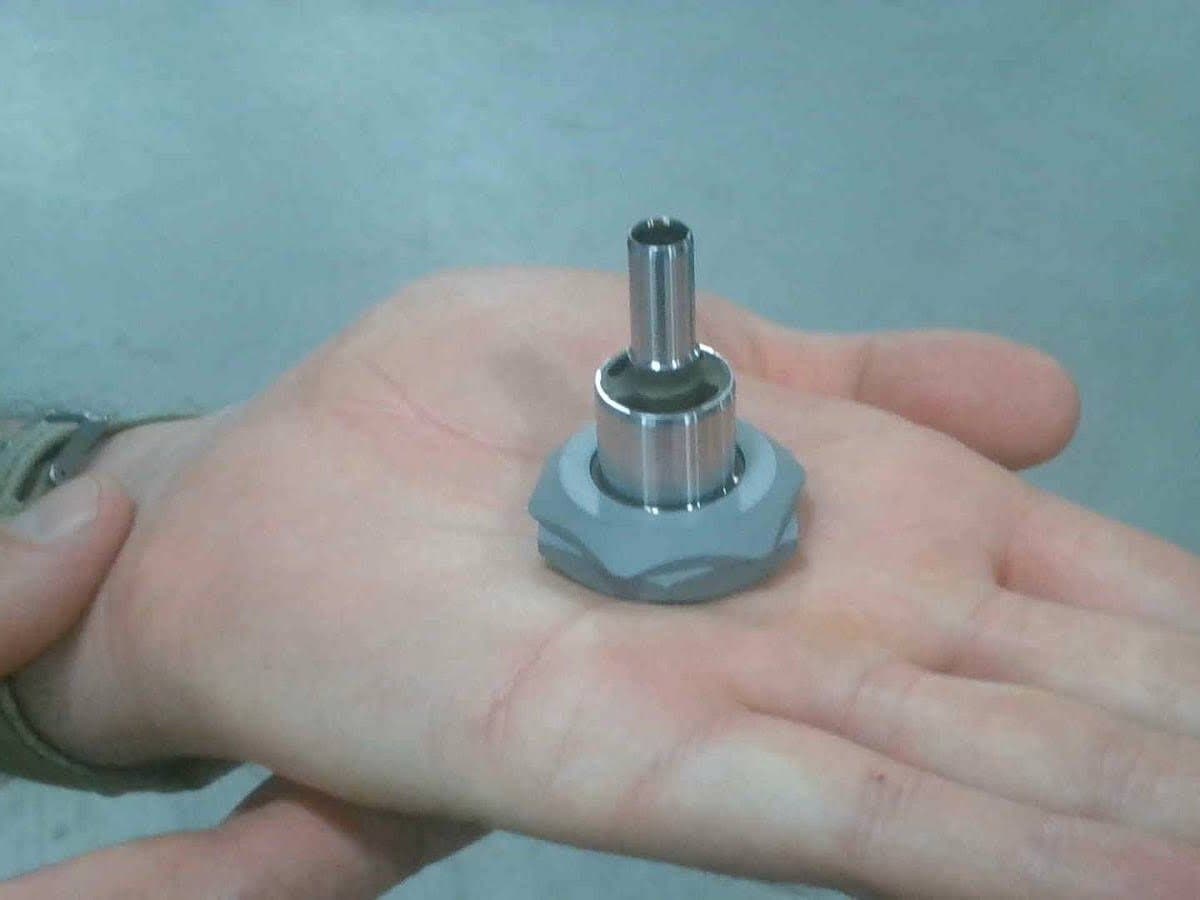
写真の金属ボルト用のマスキングを手作業で行う場合は1個あたり約$250かかるところ、Resist™で内部をネジ山形にしたマスキングツールをプリントする場合は1個あたりわずか$5で済む。
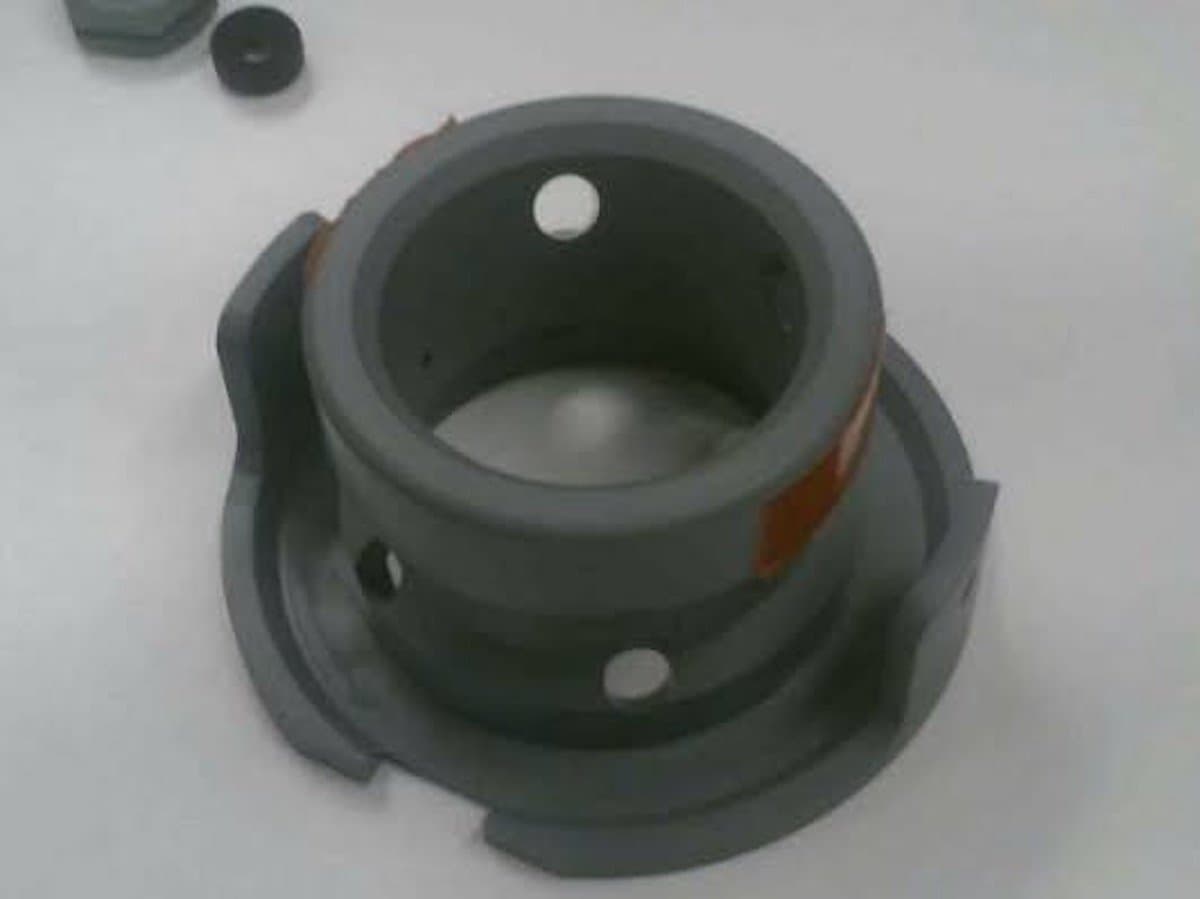
写真の大型パーツの製作にかかる費用は材料費と人件費を合わせて約$550。手作業による従来のマスキングプロセスでは$2000~$4000かかる。
3Dプリント製のマスキングツールは、最大20回の電解めっきサイクルに耐えることができます。一方、ラッカーやテープは一回しか使用できないため、処理工場では年間数百万ドル相当のラッカーやテープを使い捨てています。3Dプリントのデザイン、造形、後処理に時間がかかることは確かです。しかし、デザインは部門や修理施設、さらには軍の各部隊間で共有が可能なため、電解めっき処理でマスキングが必要な部品がある場合には同じデザインを使ってオンデマンドで製作できる可能性があります。さらに、一度に大量のマスキングツールを3Dプリントし、保管しておくことも可能です。マスキング作業は電解めっき工程の中でボトルネックになりやすい箇所ですが、3Dプリント製のマスキングツールの活用でそのボトルネックを解消できます。
可能性は無限大
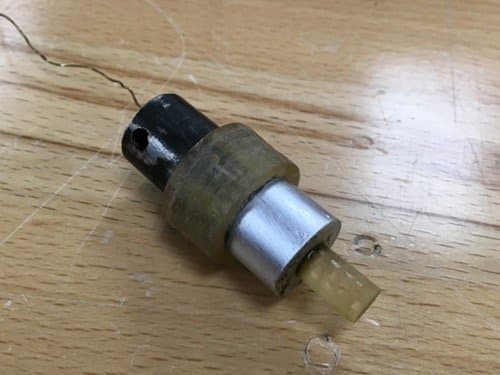
フェーズ1:実現可否の確認
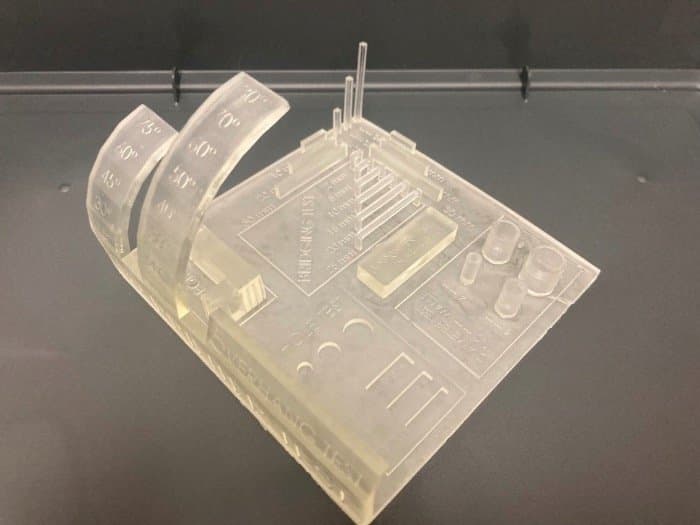
フェーズ2:開発
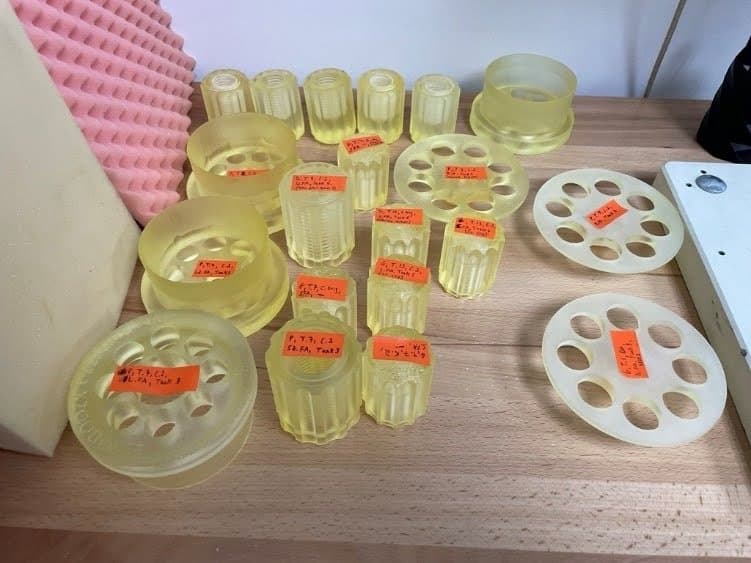
フェーズ3:初めてのデモンストレーション
Figure EngineeringとFormlabsのパートナーシップは、大規模かつ複雑な課題に対する解決策がコラボレーションによって最短で見つかることを証明しました。もちろん、Figure Engineeringが持つ化学工学の専門知識と課題に対する深い理解があったことが前提です。しかし、そんな彼らが適切な解決策を見つけるためには、単なる3Dプリンタ以上のものが必要でした。強力な「3Dプリントプラットフォーム」へのアクセスとサポートが必要だったのです。
McDaniels氏率いるチームは、FormlabsオープンエコシステムとOpen Material Modeの活用により、DoD向けに数百万ドルに相当する材料費や人件費を削減し、さらには米国全土のMROデポで働く技術者の安全性を向上させる可能性のある、全く新しい材料とワークフローの開発に成功しました。「Open Material Modeがなければ対応できなかったと思いますし、新しい案件をどう進めていくかについても考え方が変わりました。今後もさらに独自の3Dプリント用材料を開発していくことになると思います。国防総省の他の部署とも提携しているほか、民間航空会社やプライベート航空会社とも契約を結んでいるんです。Open Material Modeによって、こういった機会を手にいれる道筋ができました」
Formlabsオープンエコシステムの詳細は、以下からご確認いただけます。また、Form 4の品質を実際にお確かめになりたい場合は無償サンプルパーツのリクエストも受け付けています。お気軽にお申し込みください。