コンピューターサイエンスとエンジニアリングの融合により、ロボティクスは製造業や物流業だけでなく、ヘルスケア産業においても大きな可能性を示してると言えるでしょう。病室の消毒から検査助手としての作業まで、ロボットは医療においても実に幅広い用途で活用される技術となっています。例えば、外科手術のような医療行為では、言うまでもなく正確さが極めて重要です。北米では、医療ミスが毎年40万人以上の死因を占め、がん、心臓病に次いで3番目に高い不自然死の原因となっていると言われています。では、ロボティクスはそこでどのように役立つでしょうか。
2018年に設立されたモントリオールを拠点とするHaply Roboticsでは、外科医の手術手順の微調整をサポートするロボットを提供しています。同社は世界200万人以上の外科医に対し、最先端のVR(仮想現実)とAR(拡張現実)技術を駆使して次世代物理シミュレーションコンソールを構築しており、既に260以上の外科手術を同技術を用いて成功裏に完了したという実績を持っています。「外科医のプレイステーション」と呼ばれるHaplyのインバースフォースフィードバック・コンソールは、手術前に非常にリアルなシミュレーションを行うことを可能にし、患者側のリスクを低減しながら手術時間を短縮することを目標としています。
また、Haply Roboticsは製品開発において試作品製作の高速化のため3Dプリントの採用を決定し、トータルでFDM、SLA(光造形)、SLS(粉末焼結積層造形)の3方式の3Dプリントを導入しました。本記事では、Haply Roboticsが異なる3Dプリント方式をどのように使い分けてきたか、そしてSLS方式Fuse 1の導入背景についてもご紹介します。
対COVID-19用人工呼吸器の開発
Haply Roboticsの機械工学部門を率いるFelix Desourdy氏は、2018年にHaply Roboticsの共同創設者であるColin Gallacher氏とSteve Ding氏に会いました。「私たちはカナダ国立研究評議会で出会い、医療手術シミュレーションのためのハプティック開発をしているチームで仕事をしていました。私たちは皆、何かをデザインし、その反復検証を高速化でき、試作に次ぐ試作でこんなことをやりたいというアイデアをブラッシュアップしながら生み出すことができる、という新たな時代の到来にとても高揚していました。」
その挑戦は、COVID-19に苦しむ患者のために低コストかつ簡単で使いやすく、そして量産しやすい人工呼吸器を設計する装置メーカーを募集するCODE LiFEベンチレーター・チャレンジというプログラムに参加するというものでした。
果たして94カ国から1,000を超えるメーカーのチームが参加し、2,600以上の登録数がありました。Haplyの設計は、設計自体も操作もシンプルであること、製造コストが安価であること、簡単に使いこなせること、そしてそれらのバランスという評価項目において、最優秀作品に選出されました。
「CODE LiFEベンチレーター・チャレンジは、非常に難しいものでしたが、過去にチームとして経験したものの中で、最も実りあるものになりました。私たちは、COVID-19によってその重要性が再認識された人工呼吸器のような不可欠な医療技術へのアクセスにおいても先進国と途上国の間に大きな格差が存在するという悲しい現実に突き動かされていました。組織委員会、特にReza Farivar教授、モントリオール総合病院財団、RI-MUHC、マギル大学工学部の皆様には、このような有意義な取り組みを企画いただき、大変感謝しています」と、Haply Roboticsの共同創設者であるColin Gallacher氏は語ります。
Haplyは人工呼吸器の開発に3Dプリントを導入し、Formlabsの光造形3DプリンタForm 3とABSライク材料であるTough 2000レジンで人工呼吸器内部の試作品を製作しました。社内に3Dプリントを導入したことで、チームは人工呼吸器内部に使用する最終部品を内製で製作することができ、コンテストに入賞作品を短期間で完成させ、パンデミック時に国家間の格差に関わらず幅広い人々が簡単に人工呼吸器を利用できるようにしたのです。
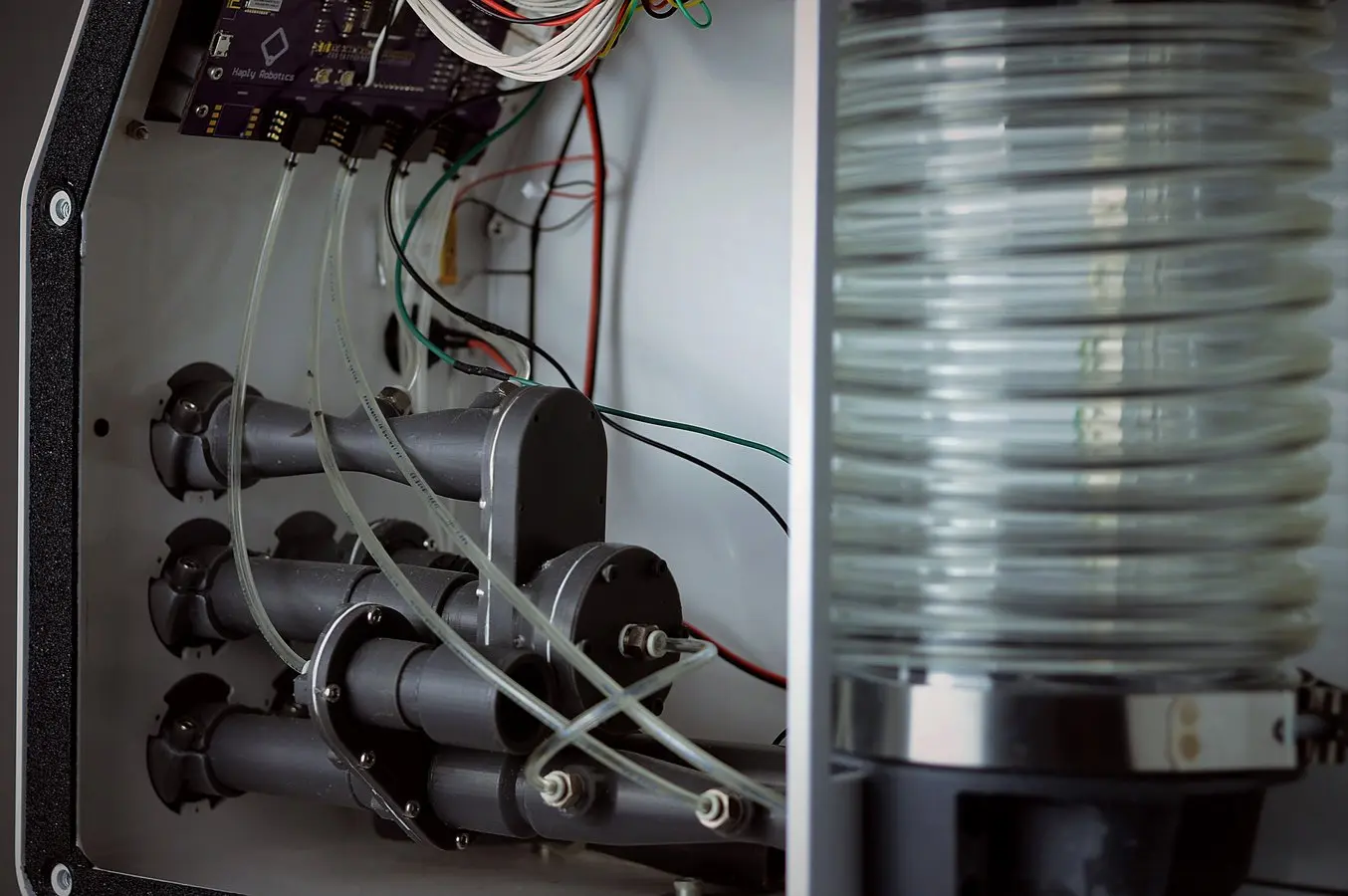
3Dプリント製のHaplyの人工呼吸器内部部品。
「Tough 2000レジンは特に機密性という意味で申し分なく、このプロジェクトに理想の材料でした。造形品に穴開けを行い、継手を入れても全く漏れることはありませんでした。ABSライクと言いますが、本当にABS樹脂と同じように仕上がります。」
高速試作で実現する完璧なデザイン
COVID-19用の人工呼吸器開発から得た学びを生かし、チームはメインプロジェクトである医療手術シミュレーション用のハプティック開発に引き続き取り組むことになりました。
ラピッドプロトタイピングは、Haplyが3Dプリンタ導入への投資を決断した大きな理由でした。デスクトップサイズの3Dプリンタで完璧な形状を見出すまで、チームは複雑なパーツを何度も繰り返しプリントし、検証を続けます。Desourdy氏はこの反復検証が重要となる理由として、人間工学と最適形状の実現という2点を挙げ、「私たちは、完璧な形状を見つけるまで試作に次ぐ試作を繰り返すという、新たな時代の到来にとても高揚しています。そしてこれは偶然ではありますが、私たちが作るものはすべて3Dプリントに最適なサイズなのです。」
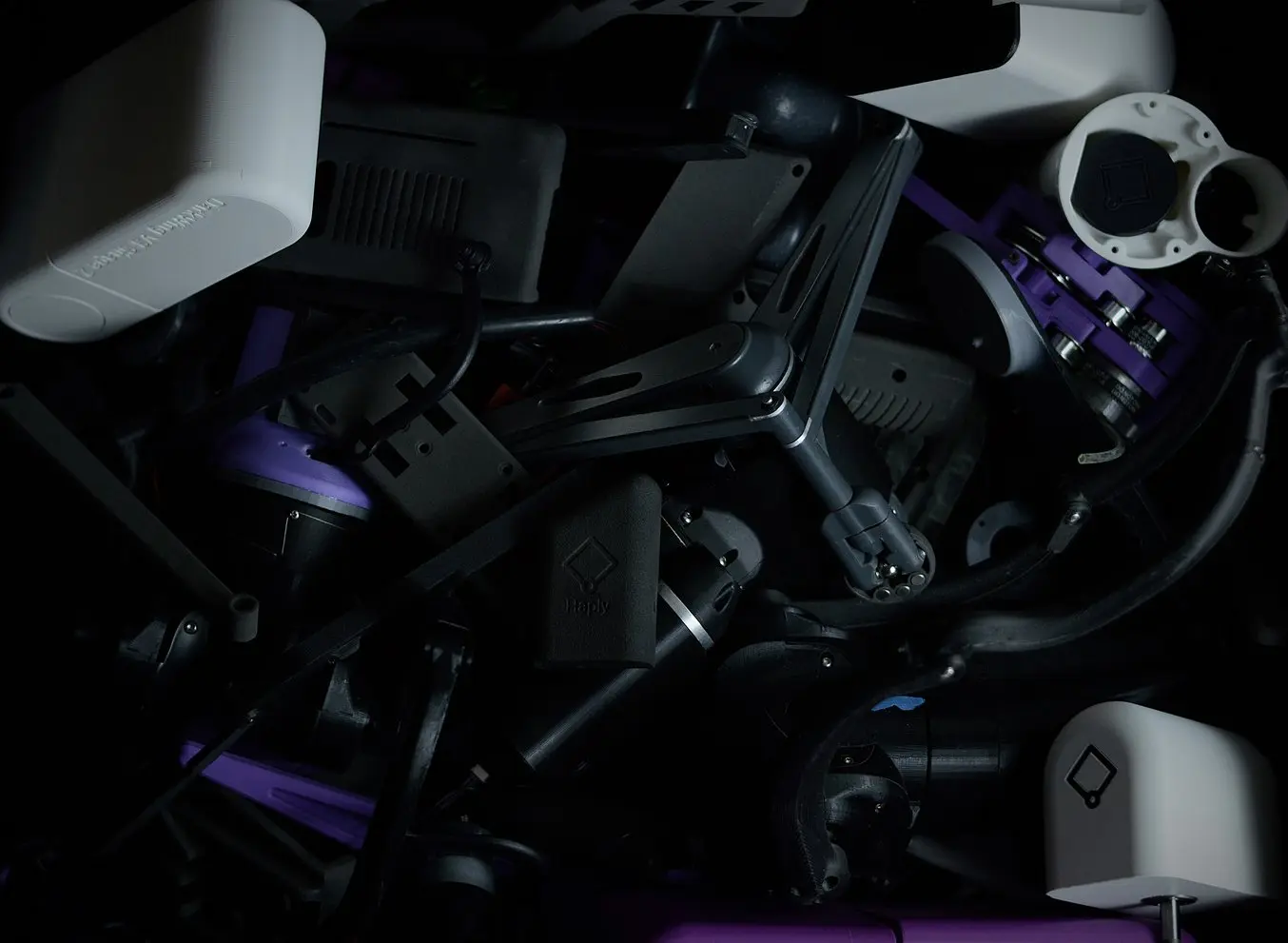
Haplyはインバースフォースフィードバック・コンソール開発のため何十回にも及ぶ反復検証を繰り返したという。
チームは当初、価格の安さからFDM方式の3Dプリンタを導入しました。これらのマシンは当初、ラピッドプロトタイピングというチームの目標を満たしていましたが、時間が経つに従い、チームはより高品質なプリントを要する、外観や機能を備えた試作品を作りたいと考えるようになりました。彼らは最終的に光造形3DプリンタForm 2を導入し、さらに精密度の高いプリントを行うためForm 3の導入も行っています。
「手術シミュレーターでは特にそうです。特に手術シミュレーターでは、人の手の周りで作業することが多いのです。私たちはより硬さのある部品を求めて試作を繰り返し、剛性を向上する要因に対してより深い理解を得ました。私の経験では、より良い形状を求めて何度も試作と検証を繰り返し、形状が確定した後により硬いものに材料を変えるのは簡単です。しかし形状を変更するには、設計面でもっと踏み込んだ作業や考慮が必要になります。」
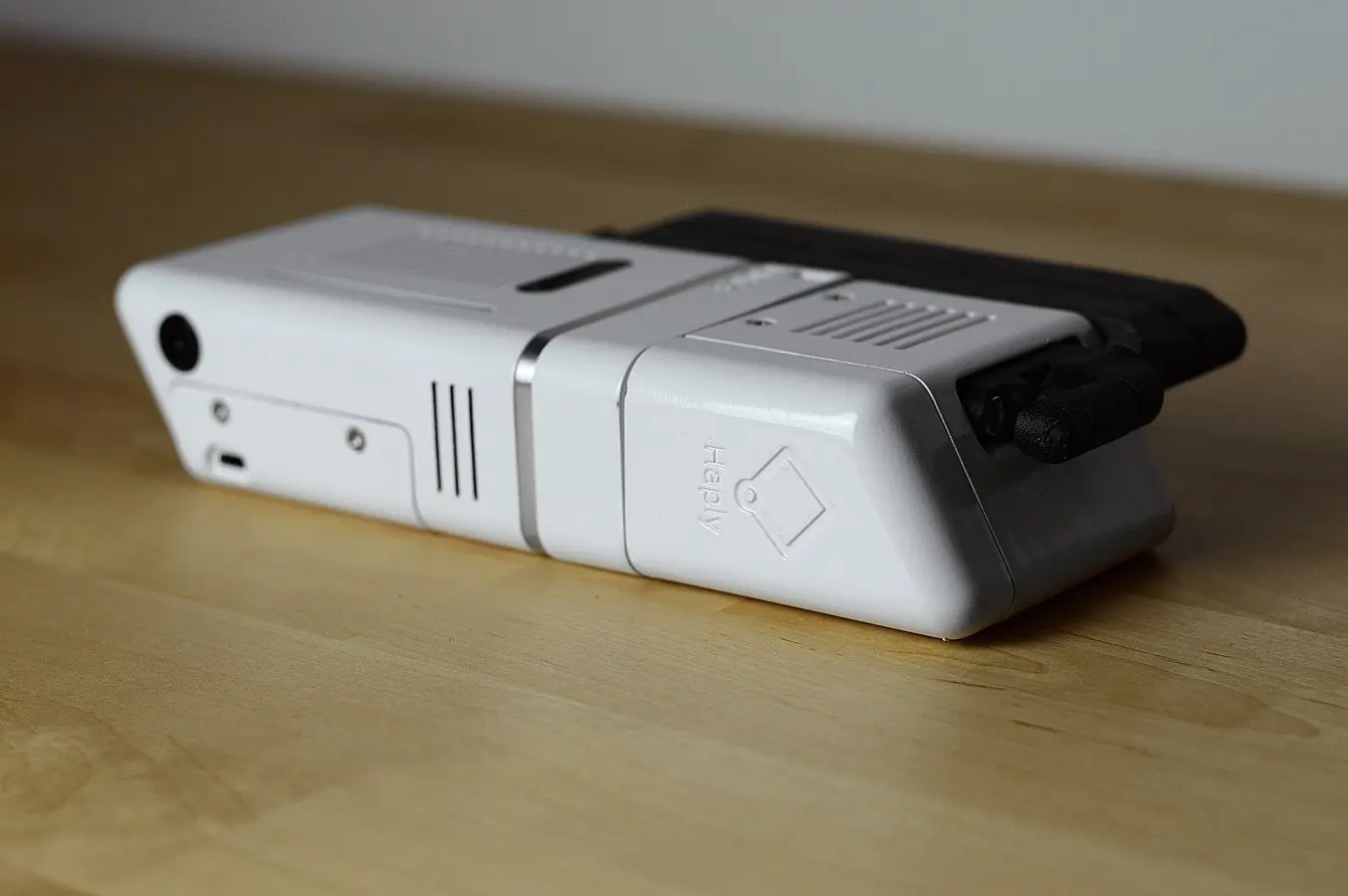
密閉式のロボットアーム。
Fuse 1で実製品用の部品を試作
Haply Roboticsはロボットアームのプロトタイプを作り続ける中で、SLS 3DプリンタのFuse 1を導入しました。これはFuse 1でプリントするナイロン部品がチームが求める最終部品に近いという理由からです。それまでは外注でナイロン材料を用いて試作品を製作していましたが、課題も多くありました。「Fuse 1では全くレベルの違う試作が行えます。最終部品に近いナイロン部品を作っていますが、社内ですぐにプリントができるので、機械のクセや材料の公差も理解した設計が行えます。すべての精度が格段に向上しました」とDesourdy氏は言います。
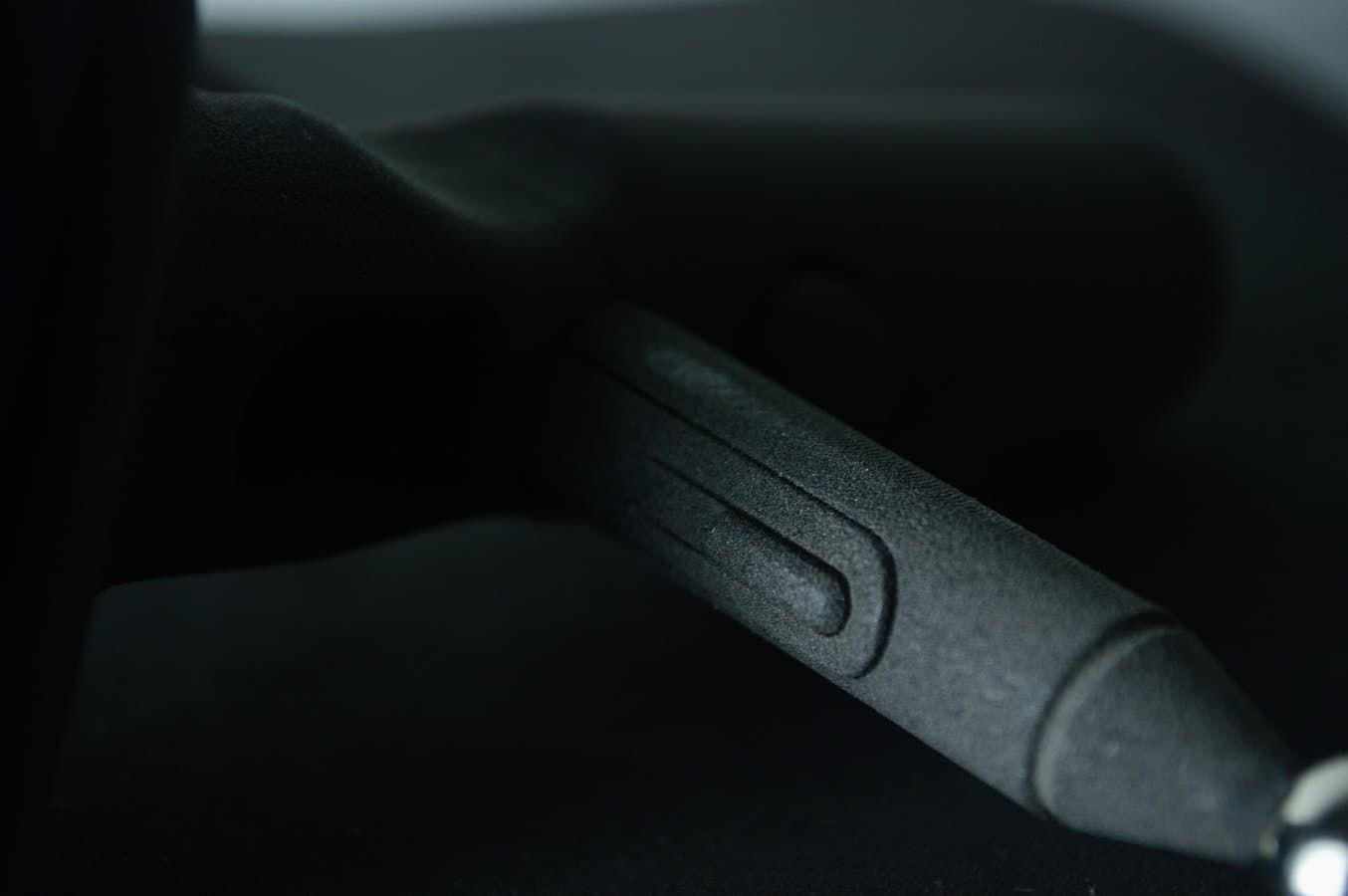
HaplyはFuse 1でファンクションボタンを備えた試作品も製作した。
Desourdy氏は、外注では成果物の品質が完全には管理できないと言います。「外注に出す場合、必ずしもそのプリントを行う際に適性な向きや造形設定で行われているとは限りません。また、外注先がどのようなプリンタを持っているのか、どの程度メンテナンスが行き届いているのかも知りようがありません。これほど迅速に反復検証が行えることは、かなりの価値だと思っています。」
Haply Roboticsのような小規模だが急速な成長を続ける新興企業にとって、もう1つ考慮すべきことは拠点の物理的なスペースです。旧来のSLS方式3Dプリンタはかなりのスペースを取ってしまうため、スペース的な問題を抱えるケースも多くあります。Fuse 1は省スペースでありながら高出力レーザーを備えたコンパクトながら高機能な装置です。「Fuseはそれほど大きくないので非常に助かりました。当然デスクトップ3Dプリンタより大きなスペースは必要ですが、正直に言ってこの種の量産に対応している3Dプリンタの中では非常に省スペースです」とDesourdy氏。同氏によると、チームは当初、HPのMJFプリンタへの投資を検討したものの、装置サイズが合わないことが障壁になったと言います。産業用の機械と比べると、Fuseは他のものよりかなり小型なのです。」
Haplyの製品オーナーであるJessica Henry氏は、Fuse 1での3Dプリント作業は非常に効率化されたプロセスであると言います。一方でHenry氏は、3Dプリントでは細部を捉え、微細なデザインも漏らさず表現できることが重要だと言います。「ディテールを少し変えるだけで、ロボットアームはスムースに動いたり、逆に動作しなくなることもあります。Fuse 1では1回で多くのパーツがプリントでき、1回のプリントで製作できるロボットアームの数が飛躍的に増えました。このレベルの生産能力を手に入れるには何台ものFDM機を購入する必要がありましたが、それでも造形品質という点で部品の性能要件を満たすことはできません。」
最後に、FDMやSLAと比べたFuse 1のもうひとつの大きな利点は、サポート材が不要なことです。
Desourdy氏は、この利点にすぐ気が付いたと言います。「FDM用に設計する場合、サポート材を立てる平坦な面が必要だったり、サポート痕が残って表面が荒れてしまう”犠牲になる面”が必要です。光造形でもサポート材を付ける面は必要です。ところがFuse 1はサポート材がいらないため、デザインのアプローチも変わりました。どんな向きでもディテールが維持でき、サポートを除去した後で研磨を行うためのスペースを考慮する必要もありません。」この変化は設計にも影響を及ぼすと言うDesourdy氏は「3Dプリントの懸念材料が大きく軽減され、設計に集中できるようになった」とも語っています。
Fuse 1での試作品を更にもう一歩上のレベルに向上させるべく、チームはプリント後のワークに染色や塗装を行うことも検討しています。
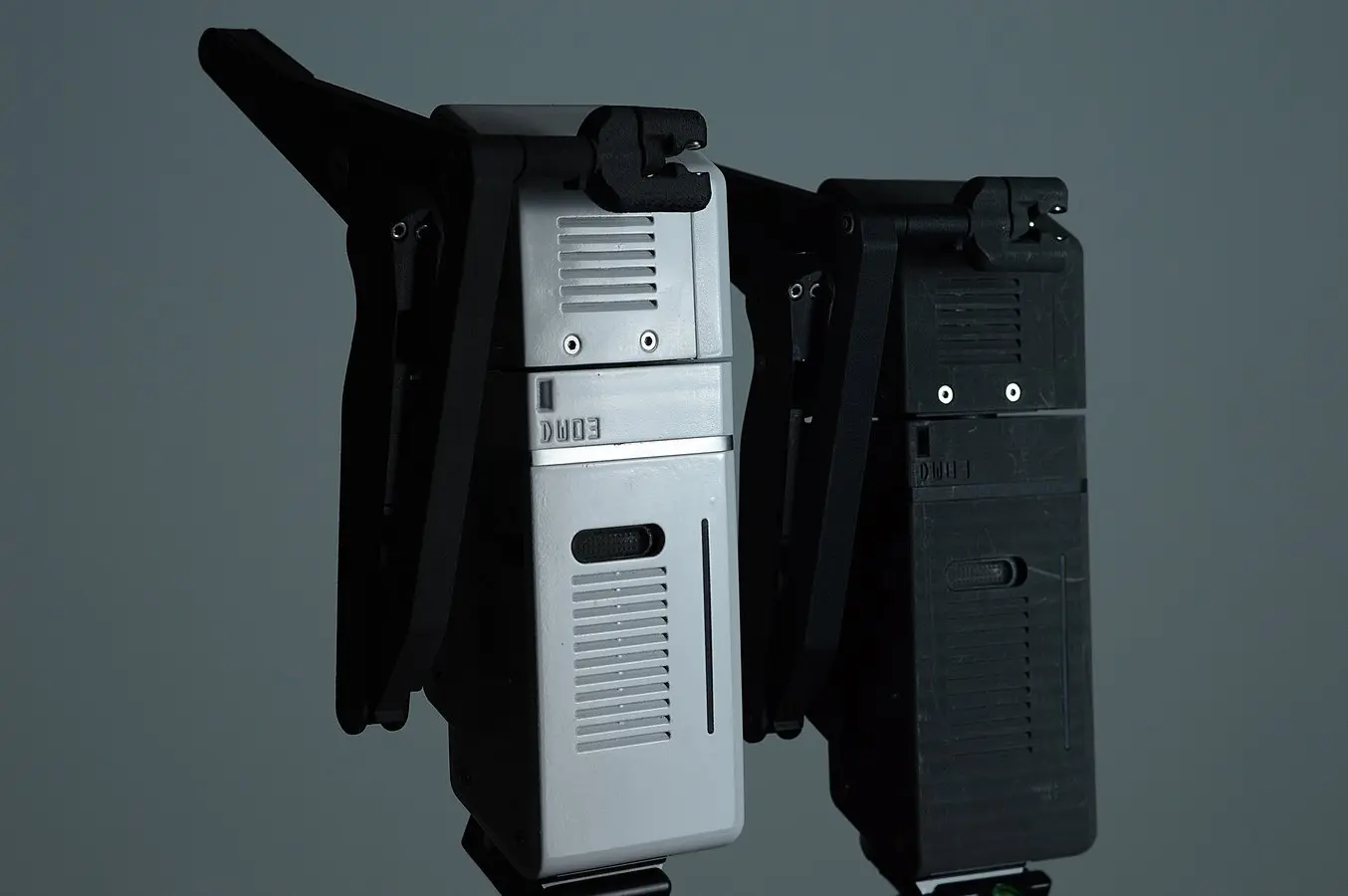
Fuse 1でプリントしたナイロン製のロボットアーム筐体。塗装によって仕上げられている。
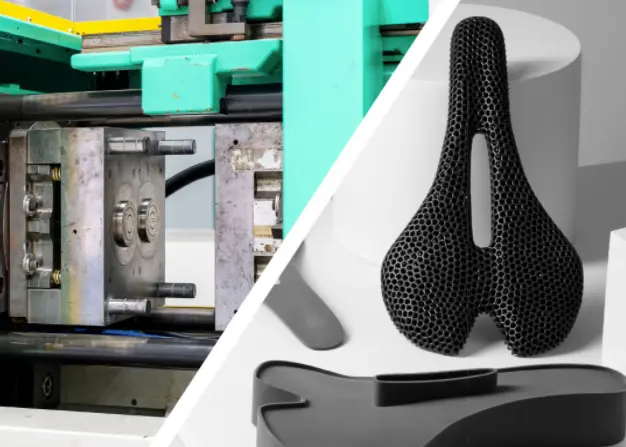
SLS 3Dプリント vs 射出成形:金型レスに切り替えるべき時は?
本資料では、SLS 3Dプリントと射出成形の両方で最終部品を製造するメーカー2社のケーススタディと共に、2種の技術の比較分析を行っています。
Fuseシリーズの詳細
Fuse 1は現在Haplyにて試作で使用されているものの、同社はFuse 1を実製品の量産に使用することも視野に入れています。「私が見たところ、小ロットであれば簡単に量産ができると思います。これが実現すれば”超”が付くほど面白いことになるぞと思っているんです。試作での使用に留まる部品も、実製品の量産ができる部品も両方があります」とDesourdy氏。Henry氏は「3Dプリントで量産を行えば、部品設計のマイナーアップデートを繰り返し行えるようになるため、製品は常に最新モデルとして販売できるはずです」と付け加えています。
Fuse 1は現在、医療機器を扱う企業を含めたヘルスケア分野の様々なメーカーに導入されています。Partial Hand SolutionsやTension Squareなどの企業は、SLS 3Dプリンタを初めて導入し、個々の患者専用の補綴器具や肺虚脱支援装置を製作するためにFuse 1を活用しています。
「SLSプリンタはずっと欲しいと思っていたのですが、価格的に手が届きませんでした。それでもFuseであれば、価格的にも機能的にも我々のような小規模ビジネスにとっても現実的です。」
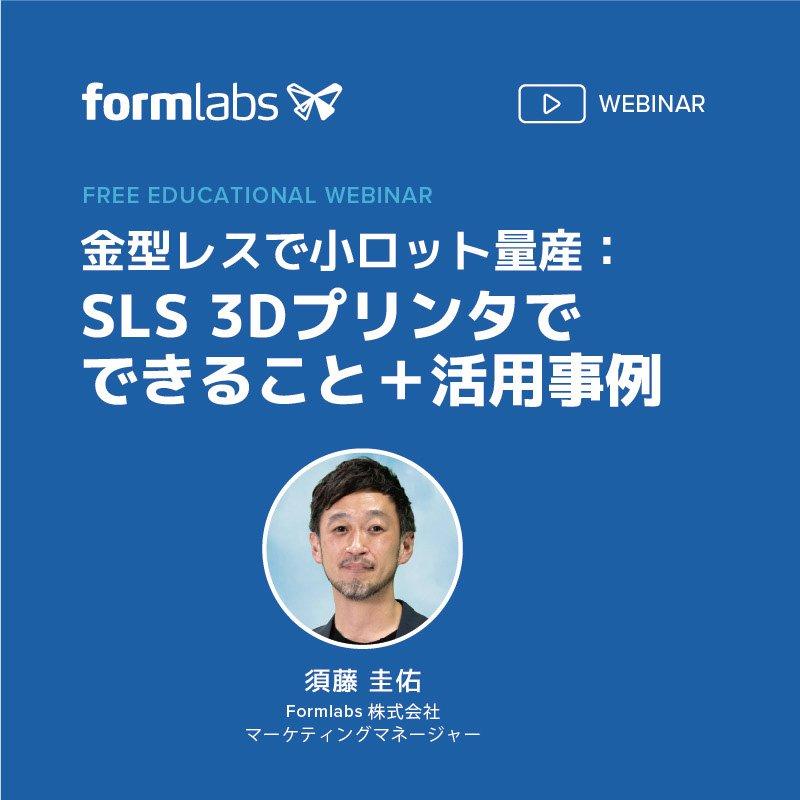
金型レスで小ロット量産:SLS 3Dプリンタでできること+活用事例
本ウェビナーでは、FormlabsのSLS方式3Dプリンタ、Fuseシリーズでの小ロット量産、国内外の採用事例と共にSLSでのものづくりの可能性を掘り下げます。