フランスのスタートアップ企業Holimakerは、零細企業向けにプラスチック加工用成形型を製作することで、プラスチック製品の製造をより身近なものにしたいと考えていました。同社の主力製品であるHolipressは、試作品やパイロット生産、限られた数量だけ必要になる実製品用部品用に、エンジニアやプロダクトデザイナーが卓上でプラスチックを成形できるようにする手作業方式の射出成形機です。
Holimakerでは、3Dプリント製の型を使用して短期間かつ低コストで、顧客の製品構想の実現可能性を調査するサービスを提供しています。これにより、Holimakerの顧客は新製品のパイロット生産段階において、短期間かつ低コストで試作品を製作して設計内容を繰り返し見直し、最終的な製造条件を確定できるようになります。また、型の設計や使用する材料を含めすべて同じ製法を使うことで、現場での部品検証が可能になり、量産用の設計も確定することができます。3Dプリント製の型の設計は、大量生産時にスチールを加工して作る金型にも簡単に応用できます。
Holimakerでは、現在取り組んでいる射出成形プロジェクトの8割から9割に3Dプリント製の型を使用しています。Formlabsの取材チームは、同社のAurélien Stoky社長とマーケティング部門を統括するVivien Salamone本部長を訪ね、Holimakerが3Dプリントと射出成形の両技術をどのように融合させているかをお伺いしました。
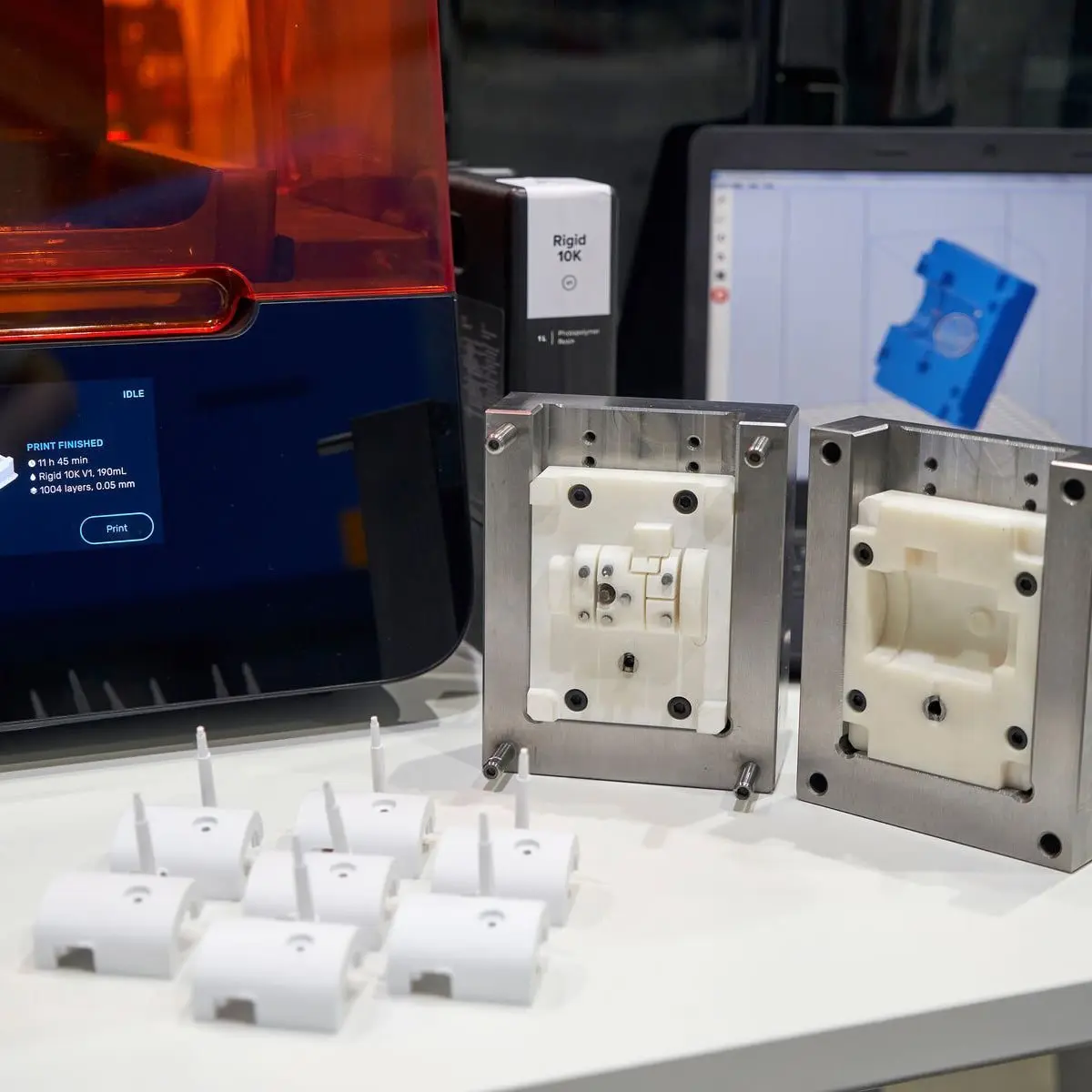
3Dプリントした金型を使った少量高速射出成形
FormlabsのWebサイトでは、3Dプリント製の型を使ってコストと時間を削減しながら射出成形を行う際のガイドライン、また実際にこの手法を導入しているBraskemやHolimaker、Novus Applicationsの事例を掲載した技術資料をダウンロードできます。
3Dプリント製の射出成形型を使う理由
従来、射出成形で使う金型はCNC加工や放電加工(EDM)など、高価な製法で製作されるのが一般的でした。しかし、部品を小ロット量産する場合、従来の金属加工で金型を製作するために必要なコスト、時間、特殊設備や熟練工の高度な技術をそのまま導入するのは難しく、この規模の射出成形では採算が合わなくなってしまいます。試作品製作や小ロット量産用の射出成形型を3Dプリントすることで、高品質の試作品を繰り返し製作でき、かつ金属加工による金型製作と比べてコストも時間も大幅に削減することができます。
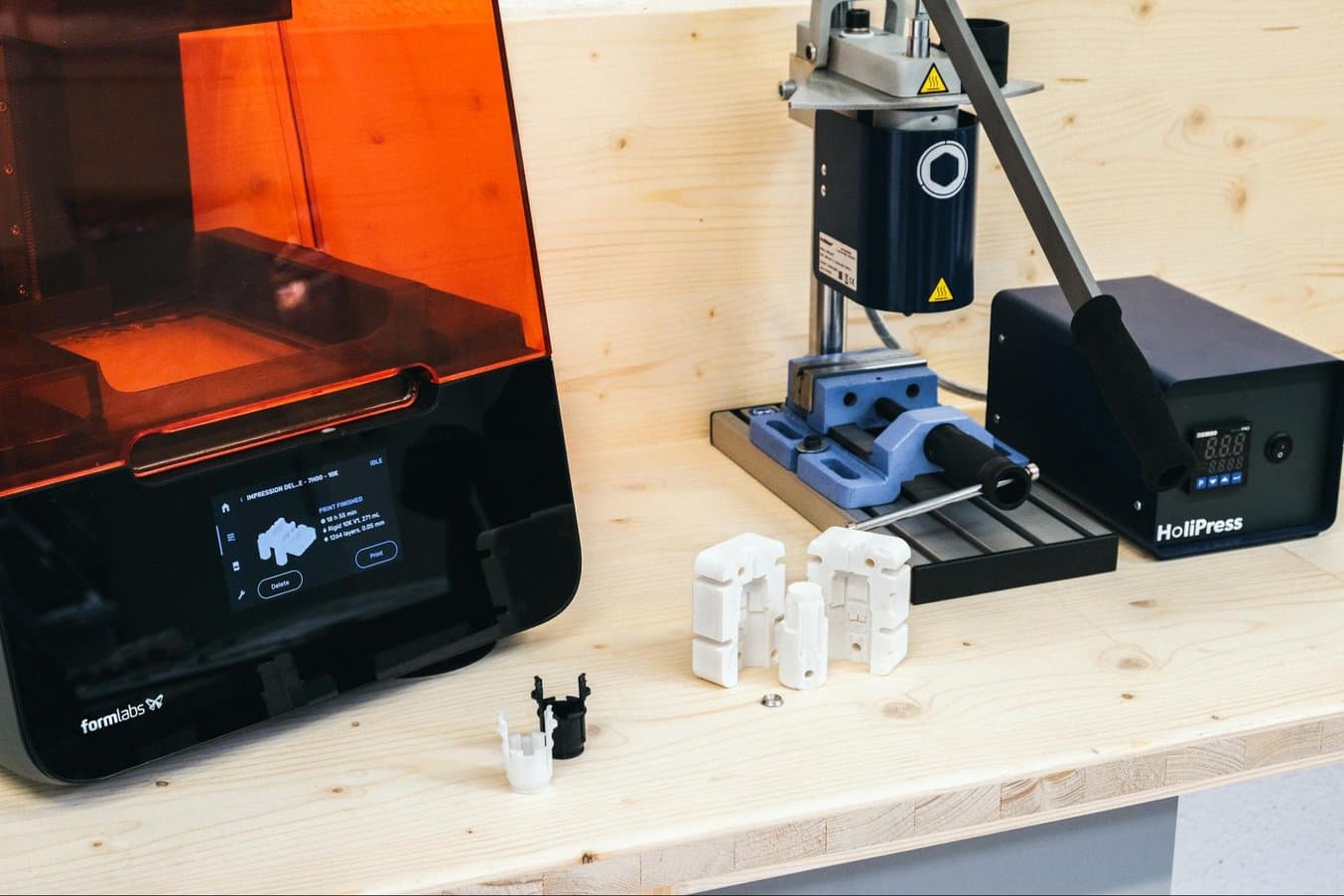
Holipress(右)、Form 3+ プリンタ(左)、Rigid 10Kレジンで製作した成形型(中央手前)。
「射出成形の成否は、金型の製作がうまく行くかどうかに懸かっています。射出成形をより多くの人が利用できるようにするためには、当社で型を容易に製作できる技術を開発して提供する必要があると考えていました。デスクトップ型の3Dプリンタはまさにこの用途にぴったりでした。私たちは、3Dプリントの柔軟性と射出成形のプラスチック製品の生産性と品質の高さを融合させたソリューションを展開しています」とStoky氏とSalamone氏が語ってくれました。
機械加工で金型を製作する代わりに3Dプリント製の型を内製化することができれば、製品の構想段階から実際に生産を開始するまでの時間を短縮しつつ、従来の熱可塑性プラスチック部品の生産も同時に進めることができるようになります。Holipressのおかげで、試作品やプリプロダクション部品を少量だけ製作し、大量生産で使用する実材料や製品ラインを検証することができるようになった他、実製品用部品を少量だけ生産することも可能になりました。また、デスクトップ型SLA光造形方式3Dプリンタを導入したことで、この工程をわずか数日で完了できるようになりました。熟練のオペレーターも特殊な設備も不要です。
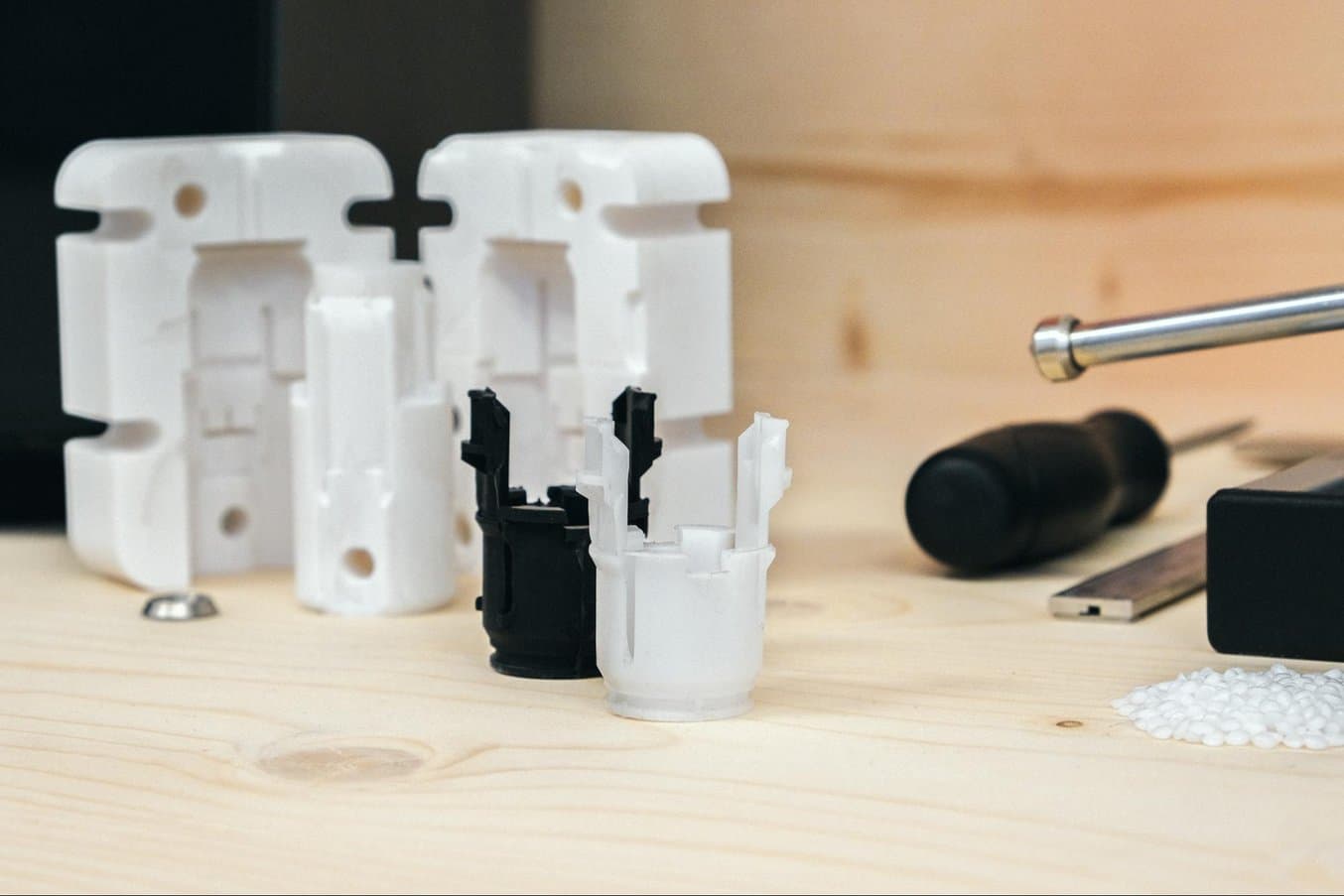
Holimakerは、顧客が水圧試験で使うバルブコネクタの試作品を製作。3Dプリント製の型を使用してPOM樹脂を射出成形して作ったバルブコネクタは25barの圧力に耐えることができた一方、POM樹脂を加工して作った同部品は8barが限界だった。
3Dプリント製の型を導入したことで、Holimakerのチームは金型の製作期間を大幅に短縮し、1日以内に何度も設計を試作・検証しながら最適な設計を見つけることができるようになりました。
午前中に型を設計してお昼時にプリントし、午後には試作品を射出成形して検証、その結果に応じてCADモデルを修正し、夜間に2度目のプリントを行う、という流れになることが多いです。従来の製法では金属加工で金型を作り直さなければならず、それだけで数週間はかかっていました」とStoky氏は言います。
Holimakerは、これまでとは違う成形型の製作方法を見つける必要に迫られていました。千点以上の部品を量産する場合には機械加工で作ったアルミ製の金型を使用しますが、小ロット量産では3Dプリント製の型を使って成形しています。従来の製法と3Dプリントを組み合わせることもあります。例えば形状に関する要件が厳しい製品を大量生産する場合は、型の外側は機械加工、インサート部分は3Dプリントで製作し、繰り返し使用したらインサート部分を入れ替えるという方法を取っています。
製造ソリューションプロバイダのMultiplusが、機械加工で作るアルミ製の型枠と3Dプリント製の型を組み合わせて活用している事例について、詳しくはこちらをご覧ください。
3Dプリントによる内製が可能になったことで、機械加工の制約を超えた挑戦もできるようになりました。同社は様々なプロジェクトにおいて、従来の製法では実現が難しかった複雑な形状の型も製作できるようになり、顧客のイノベーションを促進しています。
「形状によっては、3Dプリントを導入していなければ実現できなかったプロジェクトがいくつもあります」と教えてくれたのはStoky氏です。
プロセス
設計
Holimakerの社内チームは通常、1件のプロジェクトにつき3つか4つのモデルを繰り返し試作・検証しながら設計を最適化します。設計の際は抜き勾配を設けるなど、製造分野で一般的に定められている成形・設計の推奨事項に従っています。扱うのは大抵が小さな部品で、通気口を0.1mm、ランナー部分を0.5mmに設定しています。
また、ビルドプラットフォームから造形品を取り外しやすくするために取り代を設け、センタリングピンを使って2つの造形品の位置を固定し、スクリュードライバーで開けやすくするための刻み目も入れるなど、プリント用のルールにも従っています。型の厚みは通常10mmに設定し、薄い横断面は設けないようにしています。厚みが1~2mm程度しかない部品は、高温に耐えることができないためです。
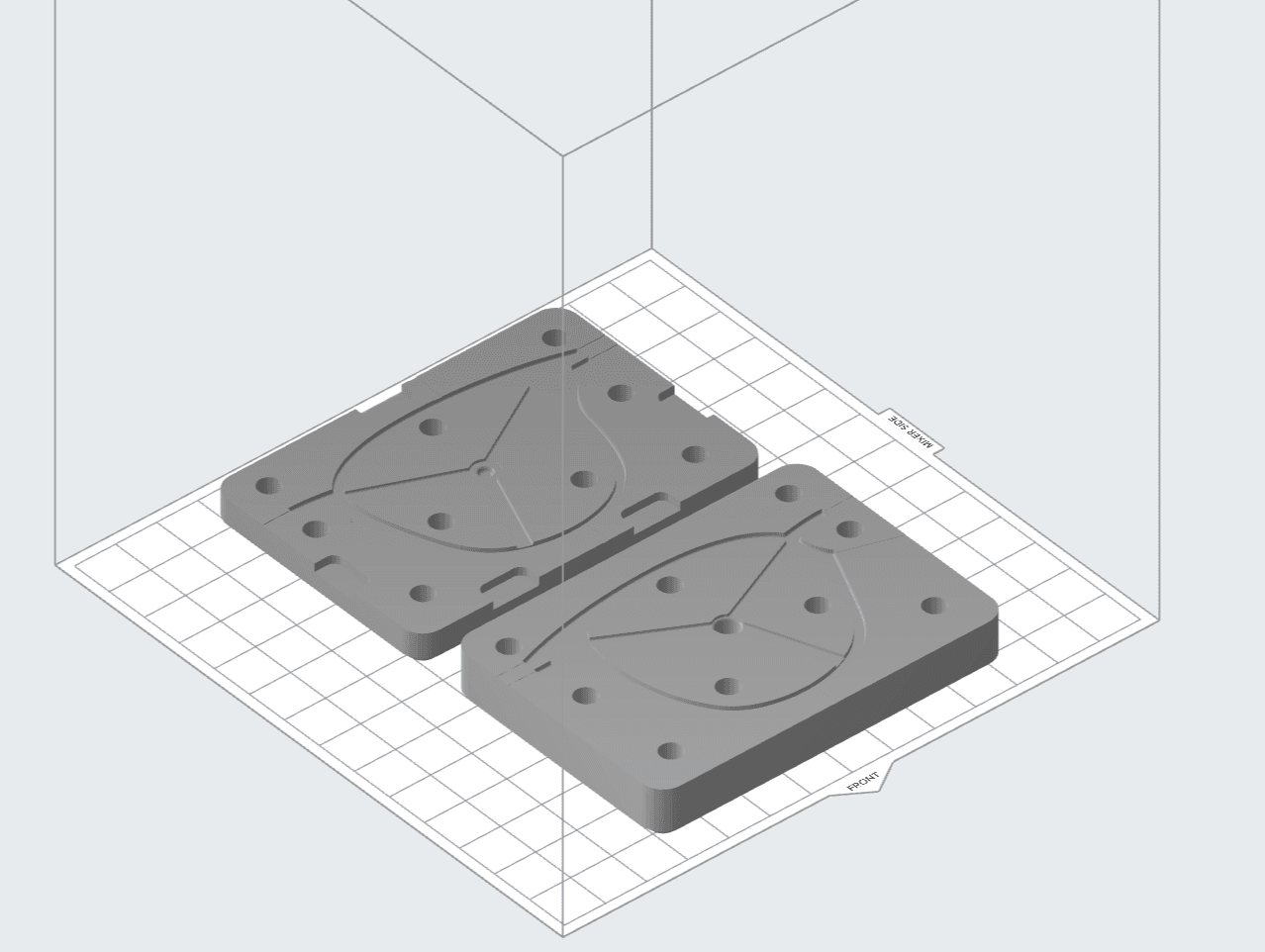
Formlabsの造形準備用ソフトウェアPreFormで様々なバージョンの射出成形型を表示している様子。
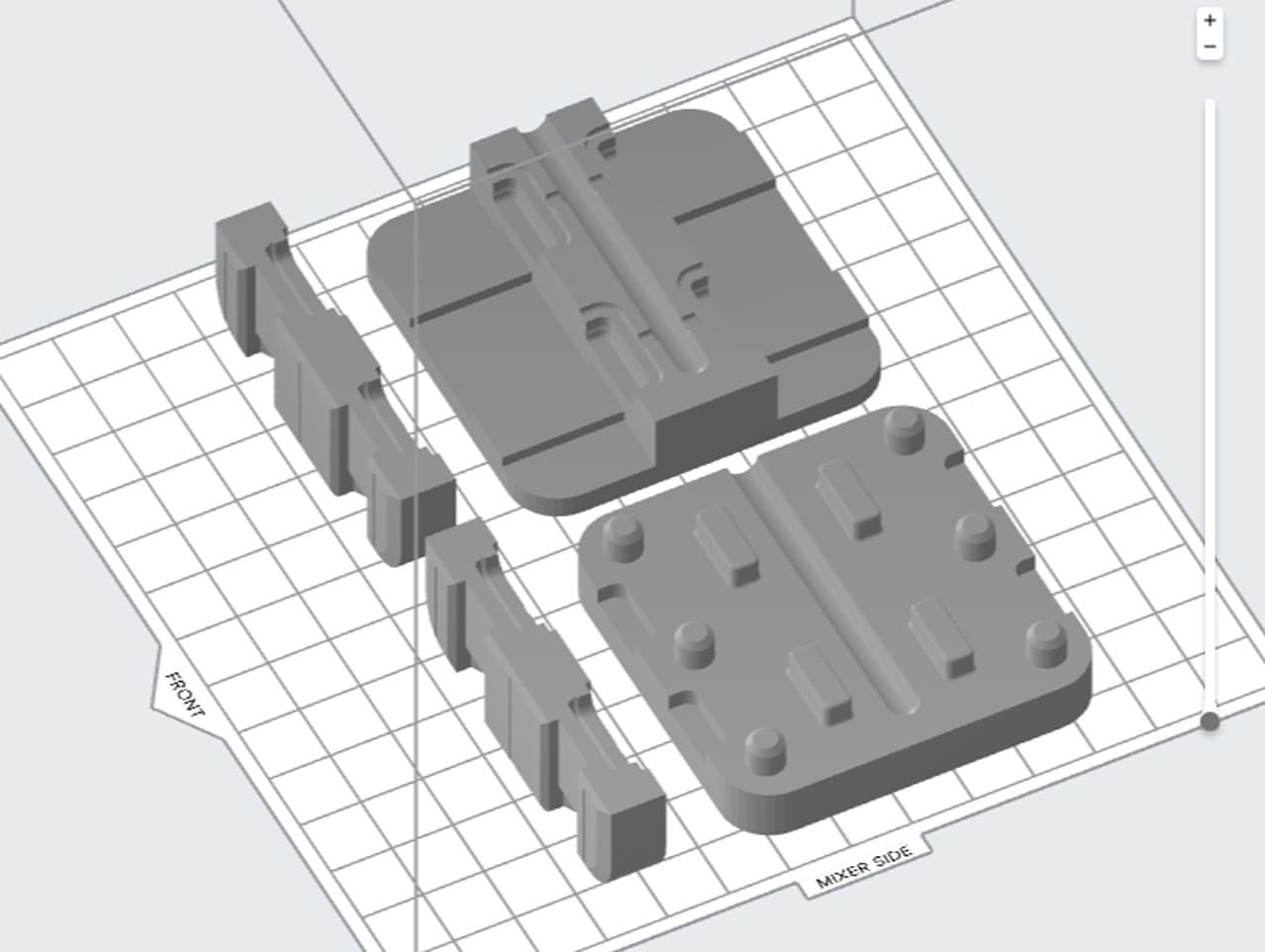
小ロット量産では3Dプリント製の型を使用し、大量生産では機械加工で製作した金型を使用する、という切り替えもシームレスに行えますが、抜き勾配や間口、通気孔の寸法は多少変更が必要な場合があります。
3Dプリント
Holimakerの社内チームは型を3Dプリントする際、ビルドプラットフォームにモデルを直置きし、積層ピッチを50ミクロンに設定しています。小さい部品の場合、ビルドプラットフォームに直置きすることでサポート材が不要になり、造形時間とレジンの使用量も削減できます。また、チームは硬化後の型の表面の寸法精度が向上したことも確認しました。寸法に大きな誤差が発生する際はブロックの外側に問題があることが多く、この場合は型の外枠にぴったり収まるよう手作業でサンディングを施します。
Holimakerは、Rigid 10KレジンとGrey Proレジンの両方を使ってプリントしています。Grey Proレジンは価格がより手頃で、低圧で小型部品を数ユニット成形するのに適しています。ただし、Grey Proレジンでプリントした型は使用回数が増えると変形する可能性があるため、技術的な精巧さが求められるプロジェクトにはRigid 10Kレジンが適しています。
射出成形
Holimakerでは、すべての実現可能性調査で自社製の射出成形機Holipressを使用しています。手作業方式のこのプレス機は使いやすく、工業用プレス機の10分の1の価格で導入できます。
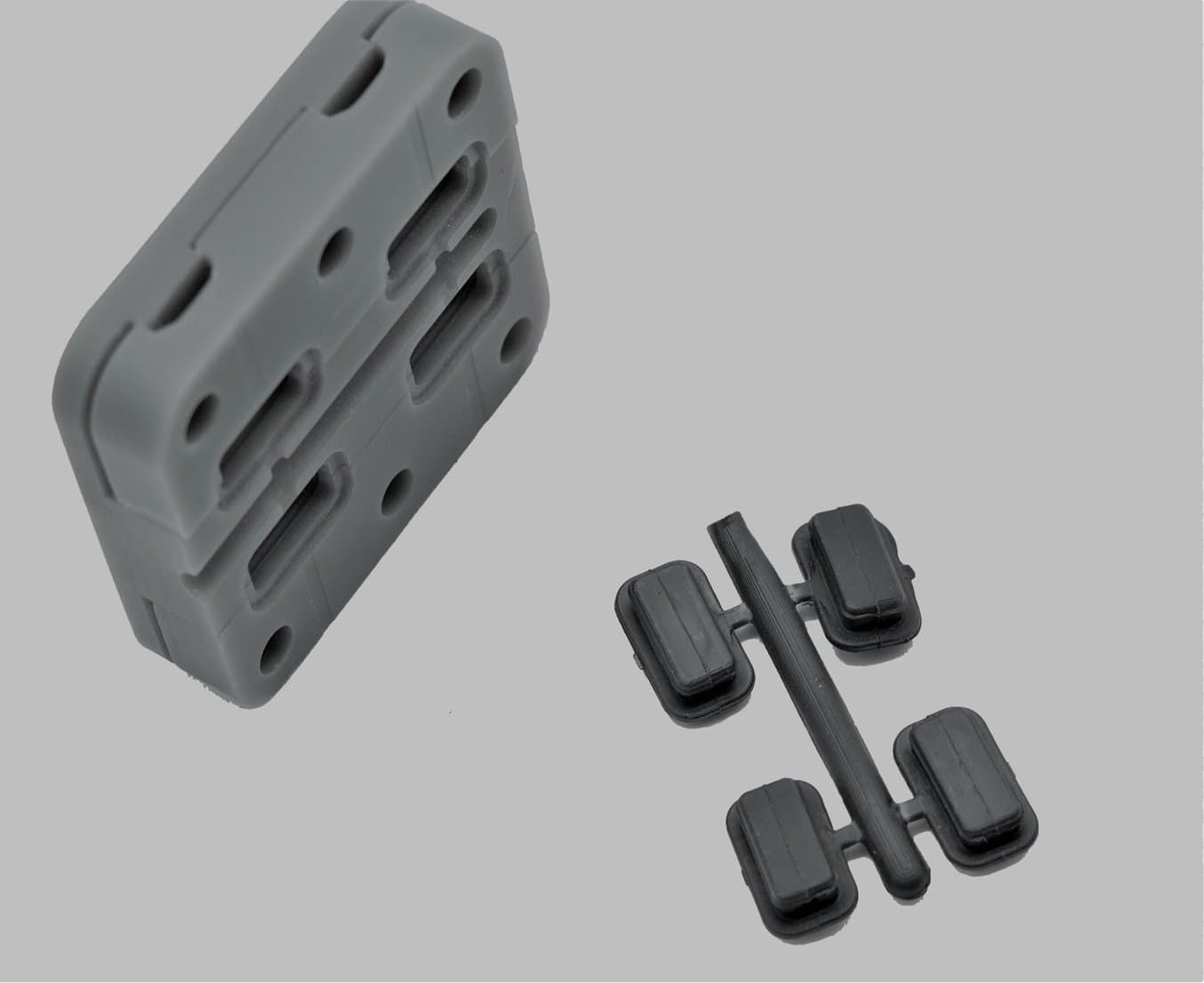
ポリプロピレン(PP)を使用して射出成形したフェイスシールドクリップ(食品グレード、220°C)。
3Dプリント製の型は予め製作しておいた圧力への耐性が高いアルミ製の枠の中に設置し、射出ノズルがプリントした型に直接触れないようにします。
Holimakerでは、Formlabsの材料でプリントした型を使用し、3分〜5分のサイクル時間でショア硬度40A〜90Aまでの多様な熱可塑性プラスチックを射出成形しています。1つの型の耐用回数は成型条件によって異なります。270°CでPAを射出した場合は約10点、より低温でPP、TPE、POMを射出する場合は100点の成形が可能です。Holimakerでは現在、離型前の冷却工程を短くする統合冷却システムを開発中です。
評価結果
HolimakerがFormlabsのSLA光造形3Dプリンタを導入する決め手になったのは、造形品質の高さとプリンタの使いやすさでした。「我々のマシンで射出したパーツの品質が大変良かったのは、そもそも型の品質がとても高かったためです。夕方にプリントを開始したとしても、心配することなく翌日には見事な型が出来上がっています」と両氏は語ります。
2人は以前、他社製のデスクトップ型プリンタを使用したことがありますが、射出成形に入る前の段階で既に3Dプリント製の型が変形してしまうことが頻繁にありました。
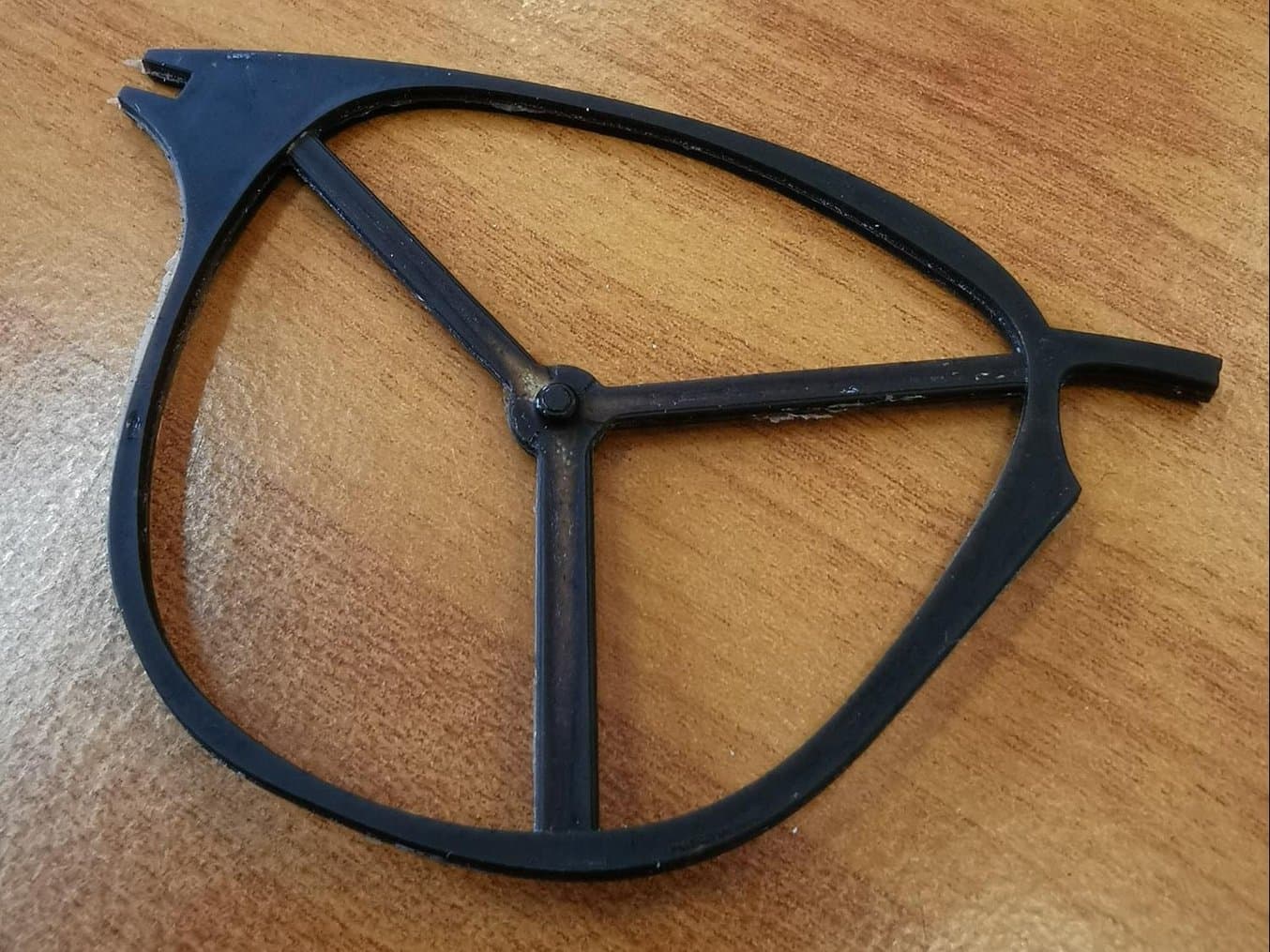
3Dプリント製の型を使って製作した眼鏡フレーム。
“Formlabsプリンタの造形品は、寸法精度と表面品質が素晴らしいです。寸法エラーが発生する際も、違いは非常に小さなもので、三軸に均等にずれるので、予測もしやすく、後処理も容易です。他社のデスクトップ型プリンタでは、プリントしたパーツの変形を制御することはできませんでした」とStoky社長は言います。
同社チームはまた、Form WashやForm Cureでプリント後の洗浄や二次硬化プロセスを完全に自動化できることなど、Formlabs製品の作業手順がシンプルで覚えやすく、操作しやすい点も評価しています。型を設計してから成形品が出来上がるまでわずか1営業日で完了し、そこから設計を繰り返し見直してモデルを最適化できるようになりました。「頻繁に、午前中に型を設計し、お昼時に設計した型をプリントし、午後には試作品を射出成形して、その内容に応じてCADモデルを修正し、二度目のプリントを翌日の朝までに完成できるよう開始するまでの作業を1日のうちに済ませています」
以下はHolimakerが提供してくれた顧客プロジェクトの事例で、製作した部品、成型条件、実現可能性調査の結果をより詳細に確認することができます。
企業情報 | バルブおよび継手メーカー | FERME 3D | 眼鏡メーカー | |
---|---|---|---|---|
製品 | バルブコネクタ | フェイスシールドクリップ | 眼鏡フレーム | |
要件 | 水圧試験のためにバルブコネクタの試作品を高速製作。 | 短時間で1万点の部品を量産するソリューションを検証。 | 3Dプリント製の型と眼鏡フレームに使う材料の適合性を検証し、最終的に眼鏡フレームを200点生産。 | |
型の材料 | Rigid 10Kレジン | Grey Proレジン | Grey Proレジン | |
射出成形の材料 | POM(190°C)/ PA6 15% GF(280°C)/ PP(210°C) | PP(食品グレード、220°C) | ASA(240°C)、PA(240°C) | |
1つの型で成形した部品数 | 12+ | 100 | 70 | |
サイクル時間 | 5分 | 2分 | 2分 | |
プロジェクト期間 | 2週間 | 1週間 | 2週間 |
3Dプリント製の成形型で射出成形にかかる時間とコストを削減
3Dプリント製の型を内製化できるようになると、金型を外注製作した場合に比べて時間とコストを大幅に削減することができます。
機械加工による金型製作を外注した場合 | 3Dプリント製の型を内製した場合 | |||
---|---|---|---|---|
設備 | Holipress、熱可塑性プラスチック | Holipress、熱可塑性プラスチック、Form 3+ プリンタ、Grey ProレジンまたはRigid 10Kレジン | ||
型の製作期間 | 3~5週間 | 1週間 | ||
型の製作費 | 4〜5倍 | 1倍 |
Holimakerは、デスクトップ型の射出成形機で高速製作した金型と3Dプリント製の型を組み合わせることで、少量の熱可塑性プラスチック部品をオンデマンドで高速製作できるようになりました。
「部品の構想段階から実際に成形するまでの時間を短縮できたことで柔軟な対応が可能になった他、製作にかかる時間とコストを削減できました」とStoky氏は教えてくれます。
無料ダウンロード可能な技術資料やウェビナーをご視聴いただくと、射出成形工程に3Dプリント製の型を導入する際の詳細な作業手順、設計ガイドライン、ベストプラクティス、そしてBraskemやNovusの導入事例をご確認いただけます。