Bureau of Labor Statisticsによると、米国では半数の企業が、起業後5年以内に廃業しているといいます。長く事業を継続していくことが難しいという状況の中で、彼ら起業家はいかにして失敗を回避し、ビジネスの安定を維持しているのでしょうか?
BTI Gaugesを設立、所有するBrandon Talkmitt氏はこの難題に対する答えを、Fuse 1 粉末焼結積層造形方式 (SLS) プリンタによる3Dプリントに見出しました。ニッチな市場に舵を切った後は、この3Dプリンタを使用した事業を、サイドビジネス的なレベルから、COVID-19のパンデミックや世界のサプライチェーンの問題、そして原材料費の高騰にも負けない、完全な一企業としてのビジネスのレベルにまで成長させることに成功しました。
すき間を見つける
多くの成功企業と同様、BTI Gaugesも市場のすき間を見つけるところから始まっていますが、Talkmitt氏が目をつけたのは、ハイパフォーマンスカー向けのカスタマイズ可能なテレメトリーディスプレイでした。標準的な乗用車の場合は、ダッシュボードのインパネに表示される内容は、速度計やタコメーター (RPM) といった一定の項目と決まっています。これに対してハイパフォーマンスカーの場合は、時速240kmで安全走行するために、ドライバーは自動車の走行中のパフォーマンスをもっと詳細に知る必要があります。高速走行するハイパワーなクルマの場合、例えばクーラント圧一つとっても安全走行には欠かせない情報になります。これらすべての情報を表示させるため、ドライバーは空燃比やターボチャージャーのブーストゲージ、クーラント圧、その他を表示するメーターを複数追加します。
「これだけの出力を出すレーシングカーでは、ちょっとしたきっかけがあっという間に大規模な故障につながり、修理費もおそろしいほどの額になります」とTalkmitt氏は語っています。被害の規模を最小限に抑えるために、エンジンの圧縮圧力や温度が超過していないか、ドライバーは常に複数のメーターを見ていなければなりません。しかし、常時チェックの必要な数字が増えすぎると、ダッシュボード周りはメーターまみれになってしまいます。
Talkmitt氏は、フロントガラス付近まで積み上がったメーターの確認のわずらわしさを解消してくれるような、複数の車両情報を1台で表示可能なメーターを探したのですが、見つけることはできませんでした。そこで、ほかの多くの起業家らの 話 と同様に、Talkmitt氏もまた、市場にない製品を自分で作ることにしたのです。氏は「私の欲しかったメーターを作った人は誰もいなかった。だから、これだけの情報を1台で表示する、タッチスクリーンを使った丸型のメーターを自分で作りました」と語っています。まず熱溶解積層法 (FDM) 3Dプリンタでメーターのケーシングを試作し、車室内の高温環境にケーシングを放置、さらに試験用オーブンを用いた耐熱性試験を自身で実施。そして様々な車種を考慮した設計修正を行いました。
外観、パフォーマンス、共に良好
メーターが完成するとすぐに、普段から付き合いのある90年代の日本製レーシングカーや、ランボルギーニ、ダッジバイパー、その他のハイパフォーマンスカーのオーナーが関心を示しました。クルマの外観を愛する熱狂的な車好きにとって、ダッシュボード周りのごちゃごちゃしたメーターは見づらい上に耐え難いものです。1つのタッチ画面で複数の数値を表示するメーターは効率面でも外観の点でも、車好きを喜ばせることとなりました。
ところがここで、Talkmitt氏は別の問題にぶつかります。FDM方式の表面の仕上がりのレベルが、ハイエンドなクルマ用のゲージに必要な質感に届かなかったのです。Talkmitt氏は、「この積層痕が気に入らないという人もいる」ため、「研磨で積層痕を消してボディ用のフィラーで整える作業が必要だったのですが、これに相当、手間がかかりました」 と語っています。
積層痕の問題を解消するため、樹脂材料のパウダーベッドを溶融結合するタイプのレジン用3Dプリンタや、廉価なコンパクトタイプ、SLS方式プリンタの導入検討を開始。1台50万ドルと高価格なことや、別の販売元から材料を購入するための複雑な手順が必要でしたが、ほかに選択肢はありませんでした。このような流れの中でFuse 1の存在を知ったというTalkmitt氏は、「サンプルを取り寄せてみて、自分のメーターもこの外観なら文句ないと思いましたね。このサンプルを使って、どこまで高温に耐えられるか、耐熱試験をしてみました。さらに表面仕上げと塗装をしてみて、これでいけると判断しました」と語っています。
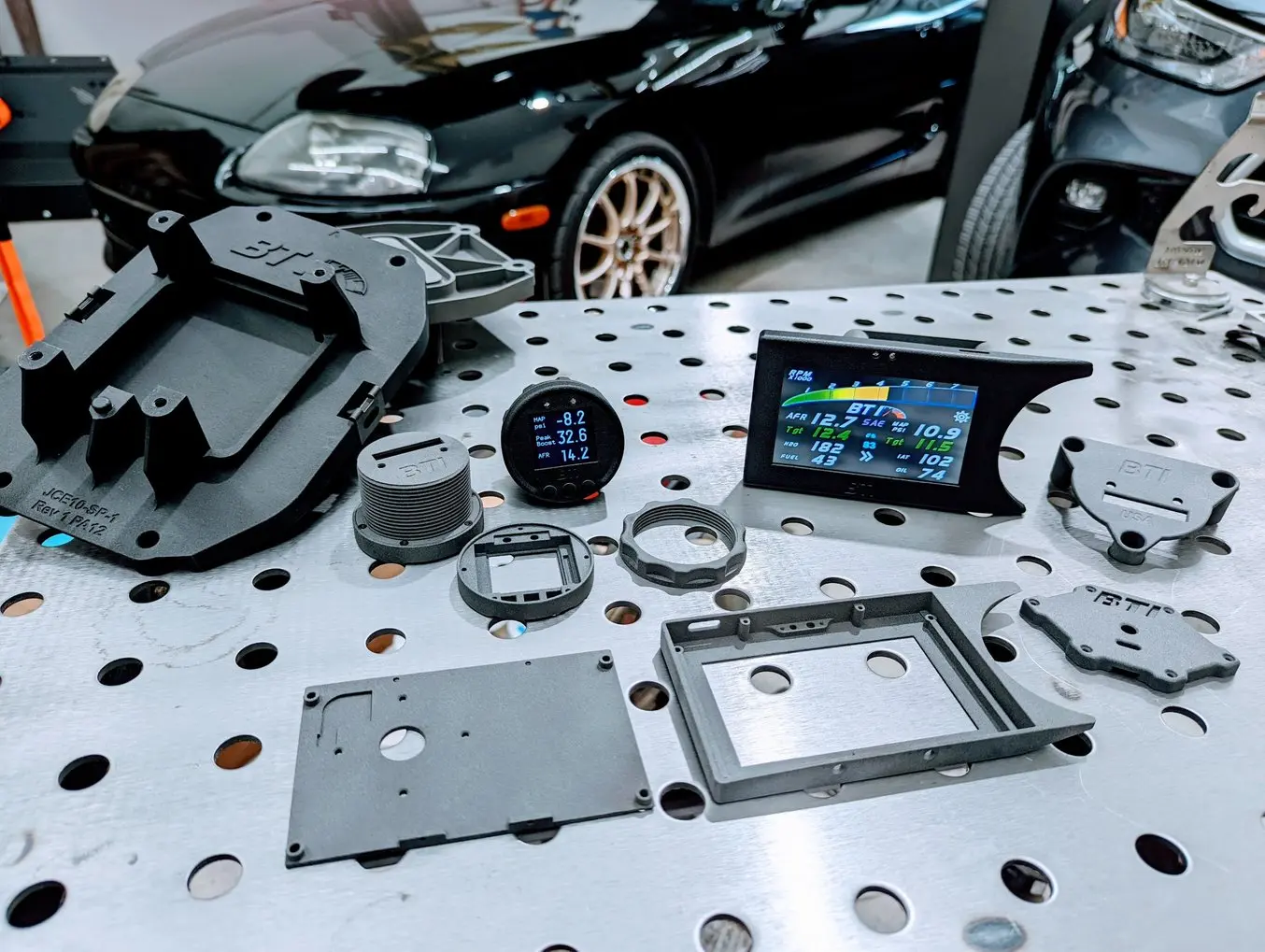
極めて高い精度
Fuse 1で生産量を上げていく前に、まだもう一つクリアにしておかなければならないことがありました。生産数量を上げてもぶれない精度です。最終的にTalkmitt氏は、厳密な公差で繰り返し生産が可能なプリンタを入手しました。Fuse 1を使用して設計通りの形状のパーツを高精度でプリントできることは事前に理解していたため、作業としては設計データファイルを設計精度どおりに正確に入力することでした。
「40 mm x 40 mmの穴を設計していましたが、Fuse 1で40 x 40のピンのプリントが可能なので、これで確実にフィットするでしょう。あとはネジ山を切るのと、その他の形状も正確にプリントする必要があります。車載環境ではパーツが反ることがあるのですが、Fuse 1に移行してからはパーツに反りが出ることはなくなりました」
Brandon Talkmitt
反脆弱性マニュファクチャリングを実現
この種のパーツは多様な生産手段で生産することが可能ですが、SLS方式のプリンタを自社内に設置することの、メリットとは何でしょうか?BTI Gaugesの事例は、 作家Nassim Nicholas Taleb (ナシム・ニコラス・タレブ) の言う"Antifragility (反脆弱)" にもあてはまる一つの成功例だと言えると考えます。 ナシム・タレブ氏の言う半脆弱/反脆さを備えたものとは、プレッシャーや衝撃に耐えるばかりでなく、これらによってより強く、より良く、より効率さを増すもののことです。この2年間、サプライチェーンの問題が生じるなかで、BTI Gaugesでは、メーター製品の生産に必要なタッチスクリーンのディスプレイパーツなど、9種の構成部品の調達が数回滞りました。脆弱なメーカーであれば、このような供給の遅滞は生産や販売の停止、あるいは収益ゼロにつながったかもしれません。この間Talkmitt氏の会社では、別の種類のディスプレイ部品の調達を強いられ、この部品変更の影響は、同時に搭載するプロセッサや回路基板、さらにはメーターの形状そのものにまで及びました。
Fuse 1を導入し3Dプリントを内製化していたことで、数千万ドルかかる新しい装置の購入や旧モデルの受注残への対処といったことに時間を取られることなく、新たなデザインへと迅速に舵を切ることができたTalkmitt氏。「プラスチックパーツが用意できない状態になっていたところですが、Fuse 1を持っていたおかげで、すぐに設計を変更することが可能でした。かかった時間としては、ファイルの差し替えの30分だけです。Fuse 1がなければ、今頃は間違いなく生産に行き詰まっていたと思います」と話しています。
Talkmitt氏の場合は外注という手段に頼っていなかったため、社内における可能な限りの垂直統合の状態が維持されていました。何度かの部品不足に見舞われたことが、予備部品のデジタル在庫の作成につながり、今後また発生するかもしれないサプライチェーンの不足から自身を守ることにもつながったのです。自分一人では動かしようもない経済的なプレッシャーに対処した経験が、彼のビジネスモデルを強くし、将来の衝撃からも守る反脆弱性を与えてくれたのだと言えるでしょう。
高い生産性
Talkmitt氏は現在の生産環境のコスト効率と持続性を維持するために、生産プロセス全体をFuseシリーズで構成しています。PreFormに搭載された最先端のパッキングアルゴリズムを活用してパーツ内に別のパーツを設置し、全体的なパッキング密度を上げて、Nylon 12 Powderのリフレッシュレートである30%に可能な限り近づけています。「弊社製品の1つである4.3 mmのメーターは、前後1個ずつのパーツで構成するのですが、間にこれだけすき間ができます。そこへ3.5 mmのパーツを入れ込みます。造形サイズをいっぱいまで使って平均で25%のパッキング密度にしています」とTalkmitt氏。
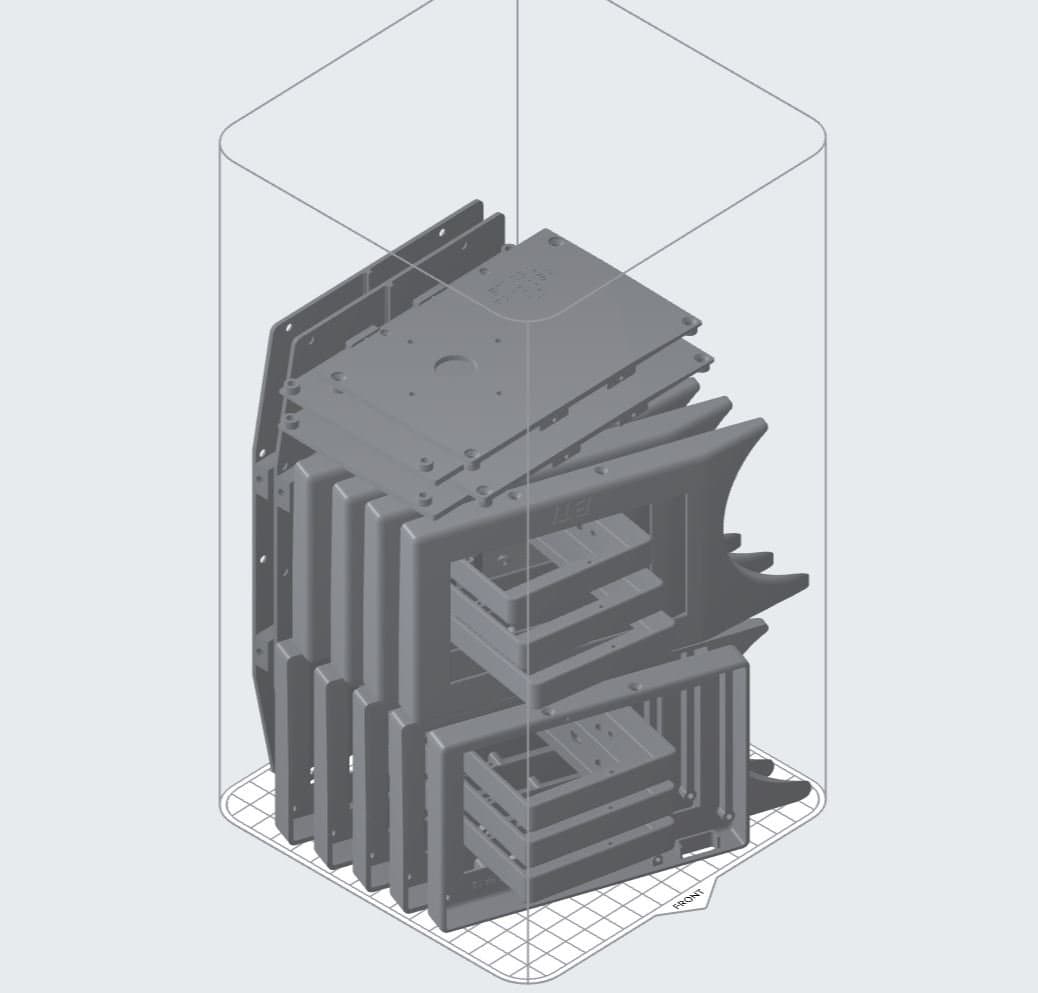
PreFormで表示したFuse 1ビルドチャンバー内のパッキングの状態 (左) と、Fuse 1でプリントしたパーツの後処理段階 (右)。
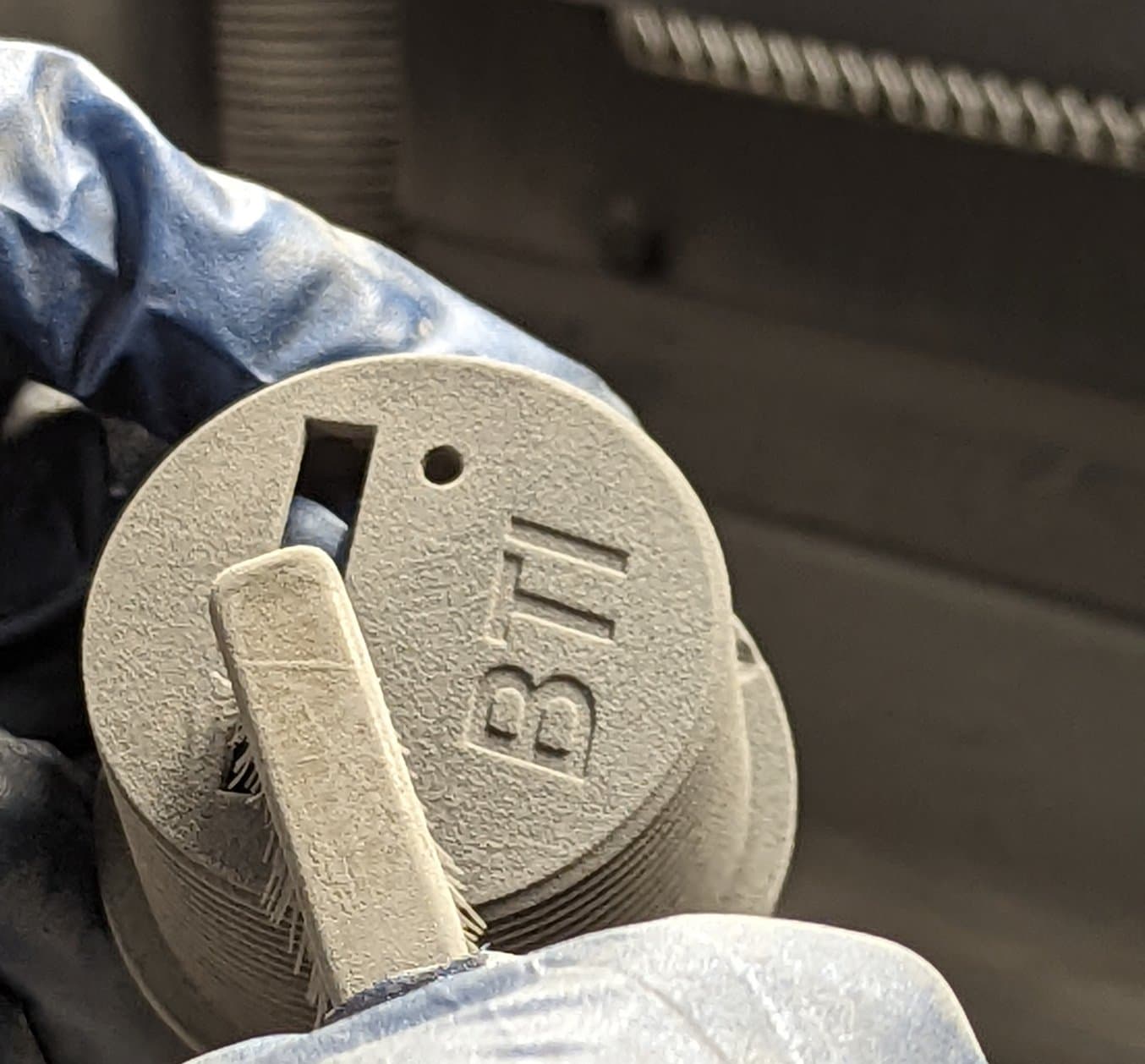
ここまでの高密度でパーツをパッキングしてすべての未焼結パウダーを次のプリントに回すことで、ほぼゼロ・ウェイストでのプリントワークフローを達成しています。小規模なメーカーにおいては、この効率の差が、パーツあたり原価の低減とROIをより早期にプラスに転じることにつながります。
高いスループットのFuse 1の導入で、BTI Gaugesでは、FDM方式プリンタ3台を無休で稼働する状態から、ビルドチャンバーを最大限にパッキングしたFuse 1を週1回使う形への移行が実現しました。Fuse Siftで後処理プロセスの合理化も叶い、新たに生まれた余裕時間を、新たなパーツの設計やブランドの認知度向上といった活動に向けることが可能になりました。「Fuse 1とFuse Sift、ブラストキャビネットは、工場の奥に設置しています。それから、塗装、組立て、箱詰めまですべて工場内で行っています。Fuse 1は設置場所を取りませんし、全体の流れをスムーズに進めることができています」とTalkmitt氏。
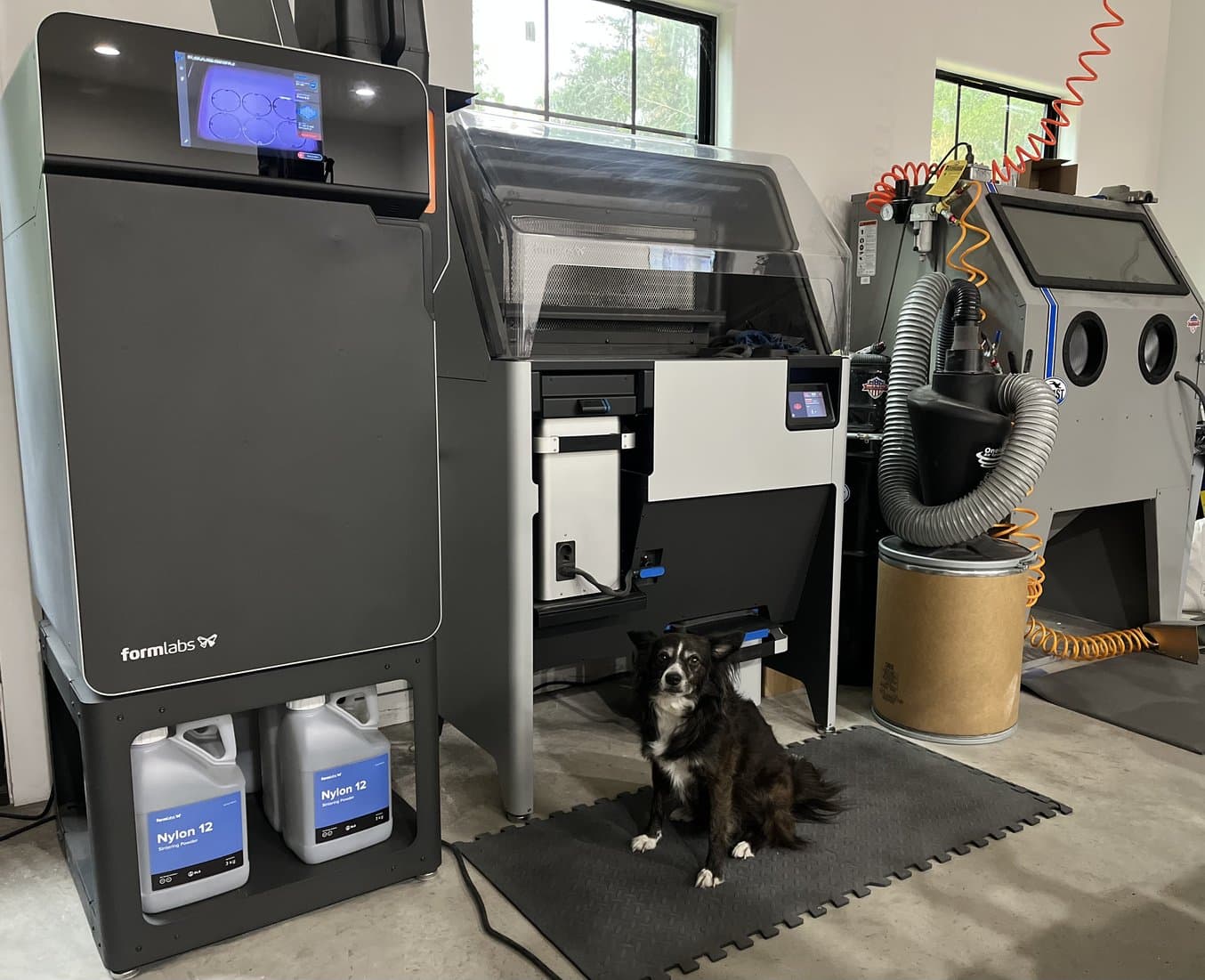
今ある作業スペース内で設置しやすいサイズ感で、スムーズなワークフローを可能にするFuse 1とFuse Sift。
将来に向けて
高額な自動車が日常的に販売されている自動車業界に、新興企業が切り込んでいくのは、難しいことです。世界で様々な活動が止まり、世界中のサプライチェーンや経済が混乱するなかでこれを実行することは、ほぼ不可能だと思えます。
しかしこのような条件下でも、Fuse 1のような高品質のSLS方式プリンタを社内に導入することで、BTI Gaugesでは自社の生産力をコントロールし、保持し、従来どおりの外注による生産手法に依存している多くの同業者の中から抜きん出ることができたのです。Talkmitt氏の言葉です。 「Fuse 1を皆さんにお勧めしたいと思います。Fuse 1は本当に大きな力になってくれました」