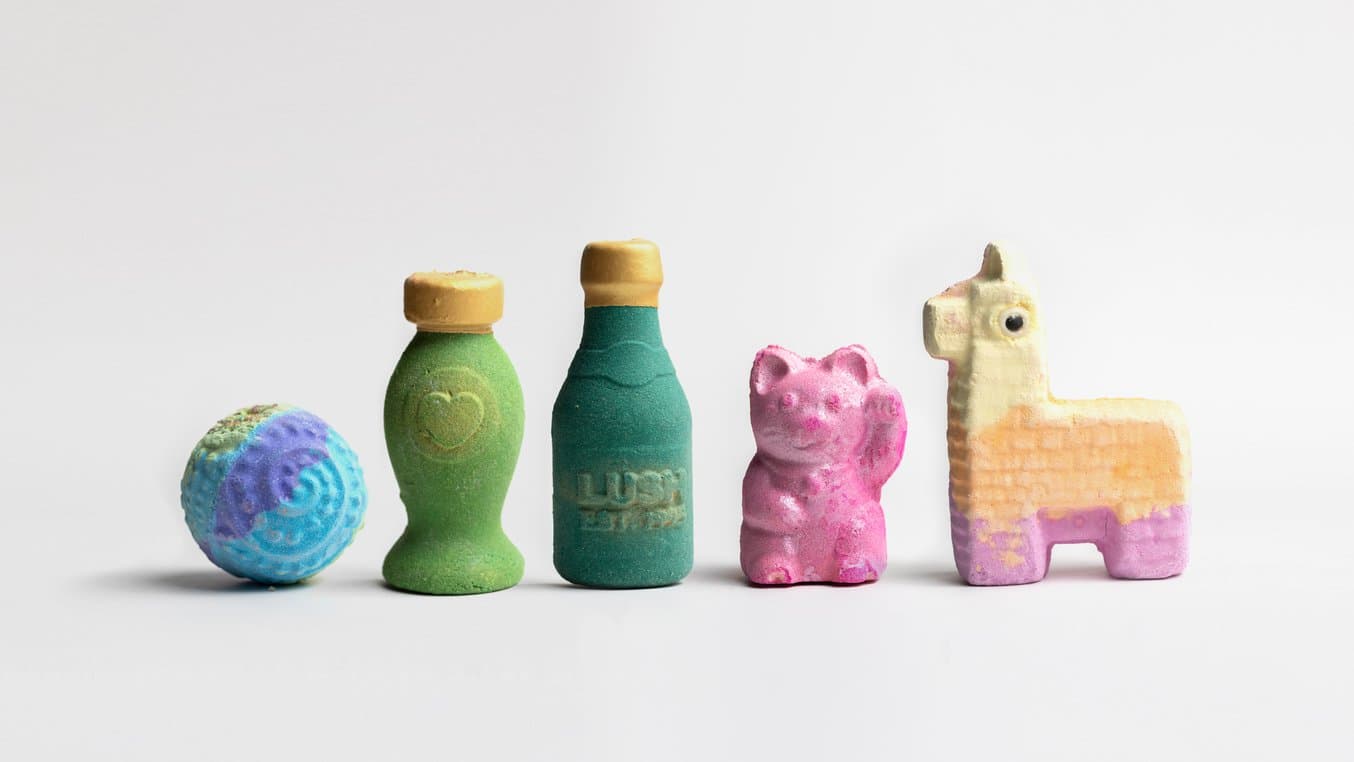
世界のどこであってもLUSHの店舗に一歩足を踏み入れれば、様々な形やサイズ、カラーで展開される様々な商品に夢中になってしまいます。英国の起業家Mark Constantine氏とLiz Weir氏によって1995年に設立された同社は、コスメ業界に新たな風を吹き込み、エシカル(倫理的に賢い)買い物と動物性油脂を使用しない100%のベジタリアン材料での商品展開を打ち出し、世界中の街を活性化することを目指して設立されました。
同社は現在、世界48カ国に928店舗を展開し、マッサージバー、ボディバター、バスボムなど、クリエイティブで多くの人に喜ばれる商品を作ることで知られるハンドメイドコスメのブランドとなっていますが、同社ではこれまでの成功の要因はトレンドや顧客ニーズへの迅速な対応にあると考えています。
プロダクトデザインの能力を強化するため、同ブランドは2018年、多彩なアディティブマニュファクチャリング技術を有した最先端の研究開発施設を設置しました。
小売業の大手企業がどのように3Dプリントを活用しているのか、同社のイノベーションラボマネージャー、Damien Carter氏にお話を伺いました。3Dデザインの天才と呼ばれ、金型職人でもあるDamien氏は、Formlabsの欧州最大の代理店であるAdditive-Xが供給した9台のFormlabs 3Dプリンタを活用し、唯一無二の新商品を次々と迅速に市場投入し、同社の競争力の源となっています。
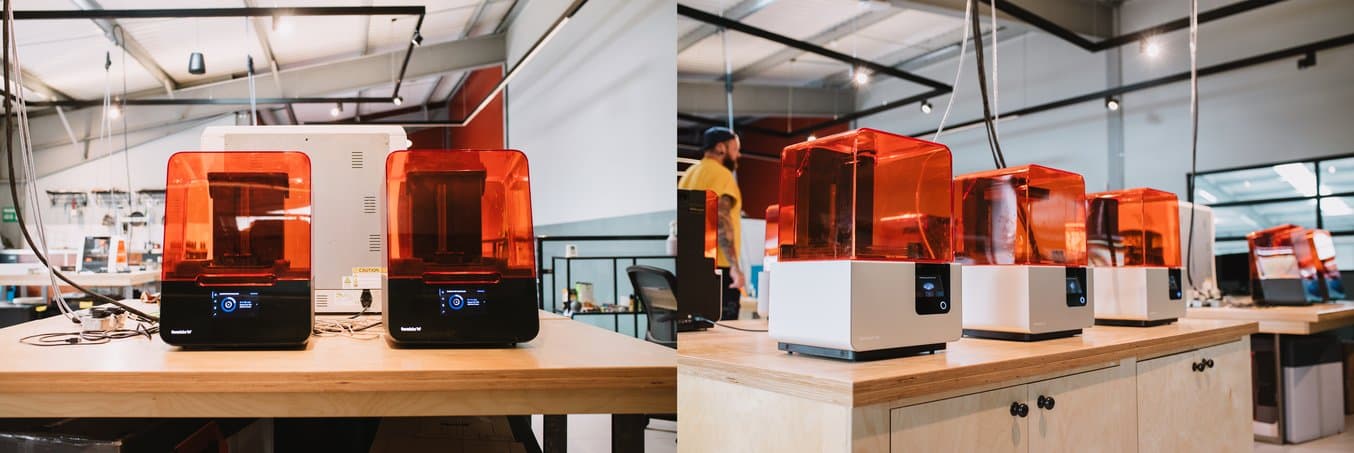
英国のプールにあるLUSHの研究開発施設では9台のFormlabs 3Dプリンタを活用して新たなデザインを具現化している。
LUSHの最新研究開発施設の舞台裏
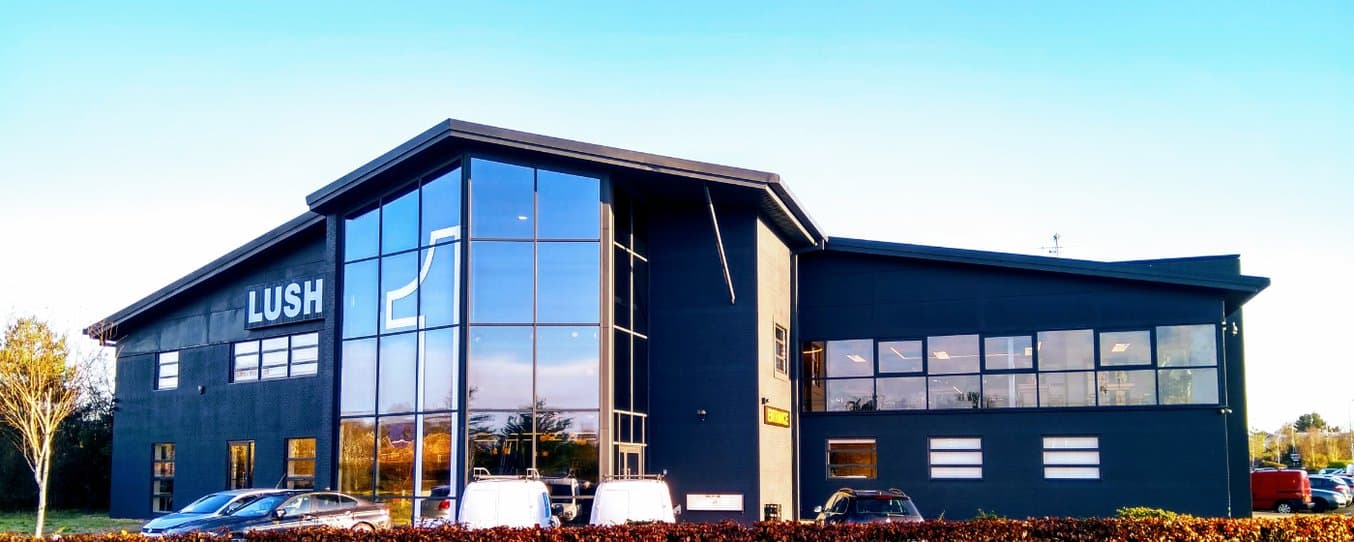
LUSHの新商品のコンセプトの殆どは英国・プールにあるグローバル本社のユニット1と呼ばれる施設で生み出される。
イングランド南部、プールにあるLUSHグローバル本社のユニット1は、LUSHのプロダクトデザイナーたちがアイデアを検討し、新たな商品開発プロセスにトライできる10億円規模の研究開発センターです。
同センターには、6台のForm 2と2台のForm 3というFormlabsのSLA光造形3Dプリンタに加え、FDM方式の3Dプリンタ数台、そして真空成形機、CNCフライス盤、3Dスキャナ、その他のデザイン設備など、多彩なアディティブマニュファクチャリング関連技術が導入されています。ユニット1のチームは最終のデザインが量産に送られる前に、商品開発担当チームと密に連携して製造プロセスの決定も行います。
同施設は、英国、日本、オーストラリア、クロアチア、そしてドイツにあるLUSHの各製造拠点のサポートも行うことで、すべての店舗にフレッシュな状態で商品を届けるという顧客との約束事を忠実に守り続けています。
「ユニット1では、商品開発のほとんどをFormlabsのプリンターで行っています。低コストで非常に高水準な精度を発揮するという我々の基準を常にクリアしてくれるため、他にない商品を作ることができるんです。英国や日本の主要な開発拠点にFormlabs製品を導入することで、商品のデザインをすぐに、しかも簡単に世界中で共有できるようになっています。」
Damien Carter氏 Lush Cosmetics イノベーションラボマネージャー
3Dプリントが従来の工程を見直すきっかけに
3Dプリントの導入前、LUSHはクレイモデルや石膏を用いて新商品のマスターを手作業で作っていました。開発チームにとってこの作業はかなりの時間と労力を要する作業でしたが、それが当たり前であったため疑問を持たれることもなく、改善すべきという課題感もありませんでした。しかし金型を1つ製作するには1週間程度は必要です。そのためデザインのイテレーション(試作→確認→デザイン調整→再試作の反復作業)には大きなコストと時間が必要であるため、同社は金型を作ってイテレーションを進めるというやり方は商品開発のポテンシャルを制限してしまっているのではないかと考えたのです。
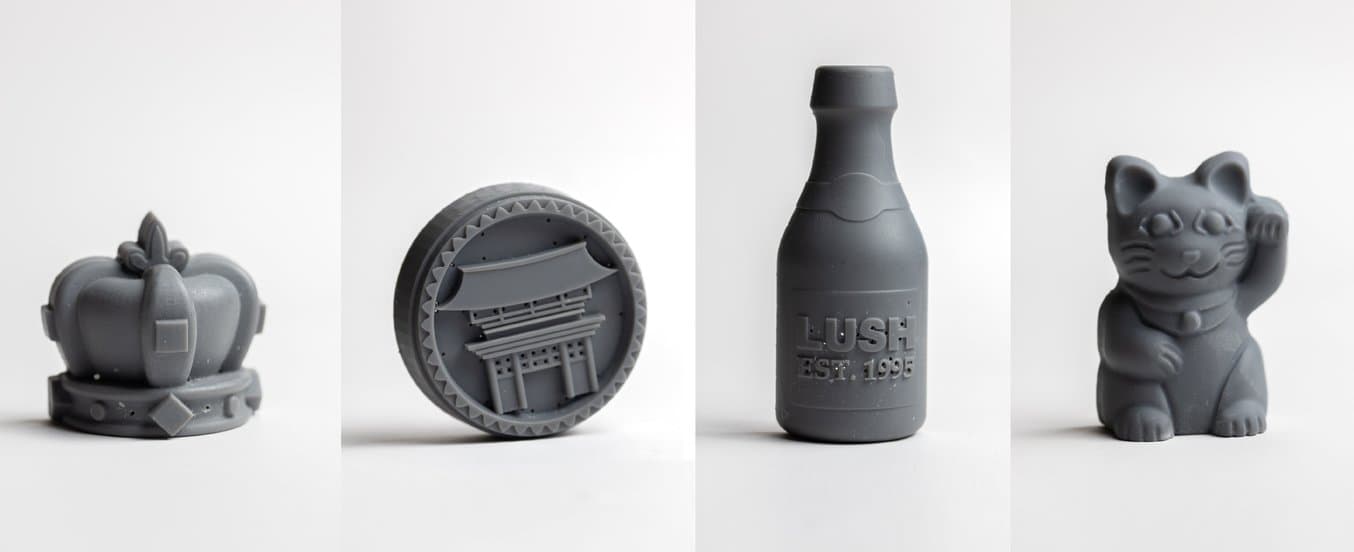
極めて高精度なSLA光造形3Dプリントを活用し、Damien氏は思うままのテイストでレタリングやデザインのディテールを表現する。
手作業での金型製作では特に難しい微細なデザインを反映するプロセスを改善すべく、LUSHは2016年に初めてFormlabsのSLA光造形3Dプリンタを導入しました。同社がFormlabs製プリンタを選択した理由は、その高い精度でした。SLA光造形方式は精密に制御されたレーザーで液体の光硬化性樹脂を硬化させ、光重合と呼ばれる化学反応で個体のプラスチックを得るもので、レタリングなどの細かいデザインにも十分に対応できます。また、非常に滑らかな表面に仕上がるため、造形後に磨いて表面を平滑にするといった作業も必要ありません。
また同社は、ソープディッシュの試作品などのように、それほど高い精度が必要でない場合は、ノズルから押し出す方式のFDMプリンタを使用するという作業を併用しています。
「私たちは、金型や治具関係、そして実際の商品に使うパーツにもFormlabsの3Dプリンタを使っています。私たちのビジネスはトレンドやお客様のニーズを受けて柔軟かつ速いサイクルで商品開発を行うため、内製で作れるということは商品開発プロセスすべてを自社内で管理でき、開発中のデザインを社外に出すリスクを冒す必要もなくなりました。」
Damien Carter氏 Lush Cosmetics イノベーションラボマネージャー
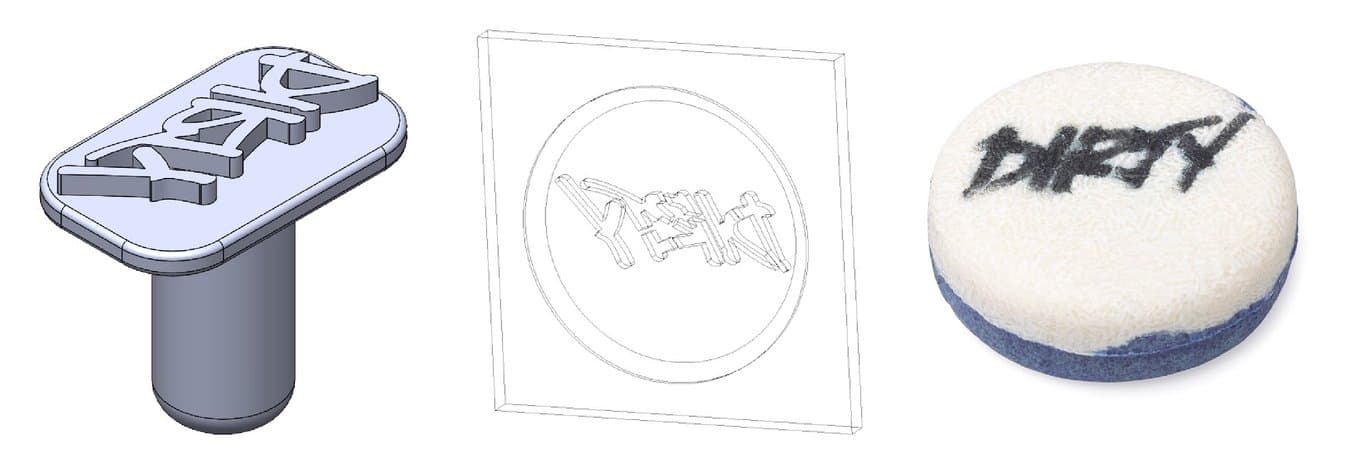
LUSHは金型や治具の製作、実製品用の部品にFormlabsのプリンタを使用している。
Damien氏は、新商品のデザインを試作する際に真空成形を用いています。真空成形は非常にシンプルで、最終部品を作る精密な金型や治具、樹脂のシート、熱源、真空装置の4つの要素を活用して成形を行います。
プラスチックのシートは均等に加熱することで柔らかく、しなやかにします。これを金型の上に被せて真空で空気を取り除くことで、熱可塑性樹脂のシートを金型の形状に成形します。成形した樹脂のシートが十分に冷却されたら離型し、不要な部分を切除すれば完成です。
Formlabsのプリンタで金型を3Dプリントすることで、新たな試作品がすぐにその場で製作できるようになり、LUSHでは商品開発プロセスが非常に高速化できました。更に、3Dプリント製の金型であれば、レタリングや複雑なテクスチャなどの微細なデザインを簡単に反映でき、そのために追加のコストが発生することもありません。
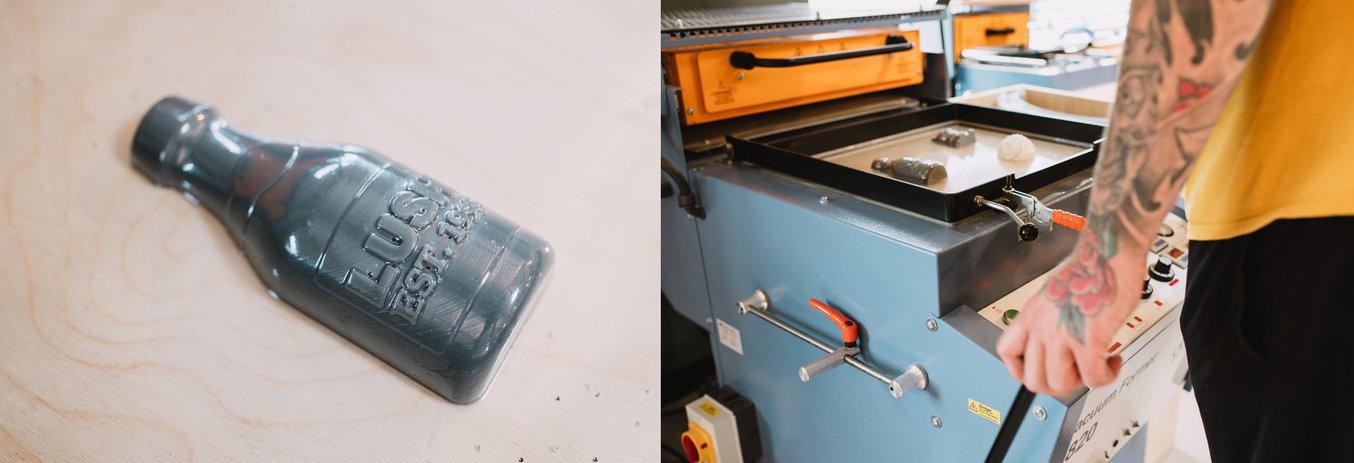
LUSHでは上画像のような3Dプリント製の金型で真空成形を行っている。
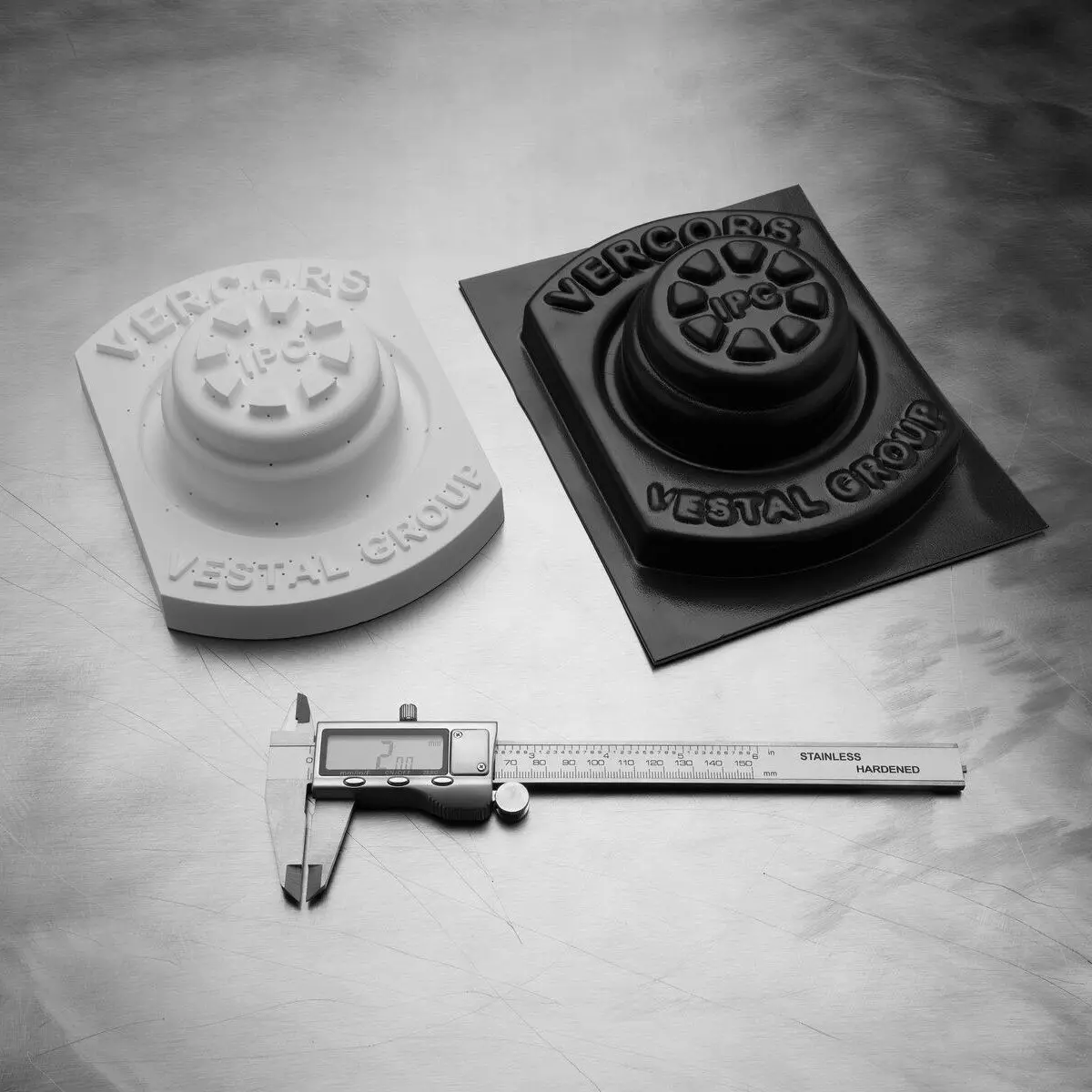
熱成形での少量生産を3Dプリント製金型で行う方法
本ホワイトペーパーでは、3Dプリントで複雑な形状の金型を高速で製作する方法や、金型設計時のガイドラインを解説しています。
※本資料は現在翻訳中です。近日のアップデートをお待ちください。お急ぎのお客様は[email protected]よりFormlabsのエキスパートまでお問合せください。
デザインから数分でプリント
SolidworksやZBrushなどのCADソフトウェアで、Damien氏らの開発メンバーは新商品をデザインし、Formlabsのリモートプリント機能で造形ファイルをプリンタにアップロードしています。デザインのイテレーション(試作・確認後のデザイン調整)ごとのデータが履歴として簡単に管理できるため、以前のデザインを部分的に再利用するなど、作業時間や製作コストを削減し、開発作業全体の効率化を図ることができるのです。
「私たちがFormlabsのプリンタを使い続けている理由は、使いやすさと安定した造形品質です。特に難しい操作をする必要もなく、誰でも簡単に素晴らしいプリントが毎回安定して行えます。またデザインをプリントする前にPreForm上でデザインのディテールを視覚的に確認できるため、プリント前に手直しが必要な場合は事前に把握することもでき、助かっています。」
Damien Carter氏 Lush Cosmetics イノベーションラボマネージャー
加えて、Formlabsの無料造形準備ソフトウェアPreFormでは、3Dプリントの向きや角度、サポート材の付け方や使用する材料などの造形設定をすべて「.form」という独自のファイル形式でコンピュータ上に保存することが可能で、Damien氏が自らのデザインをこの.form形式のファイルを世界中のメンバーにメールで展開すれば、世界中の拠点で同じ品質のプリントが行えます。これにより、どれだけ開発が立て込んでいる時期でもアイデアをグローバルに前進させることができるようになっています。以前はテストのために新しい金型を各拠点に送って、到着まで数日から数週間かかることもありました。また、CADデータがない場合は既存の商品を3Dスキャンしてからプリントしたり、日常生活から得たインスピレーションをすぐに商品のアイデアに反映するといった機能も、今ではチームの頼みの綱となっています。
オーストラリア山火事支援プロジェクト:コアラソープ
3DプリンタによってLUSHの商品開発が高速化されたもう1つの例として、2020年に行われた「All The Wild Things」救済プロジェクトです。2020年1月、LUSHはオーストラリアの山火事で住処を追われた野生動物を支援する慈善団体「Bush Animal Fund」への寄付を募るため、コアラ型のソープを販売しました。
このソープはすぐに完売し、オーストラリアに生息するコアラの個体数と同じ5万個が全世界で生産されました。このソープは熱烈なファンを獲得し、LUSHにはこの限定商品の復活を望む声が殺到することになります。
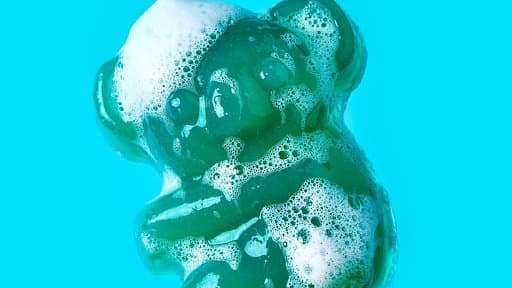
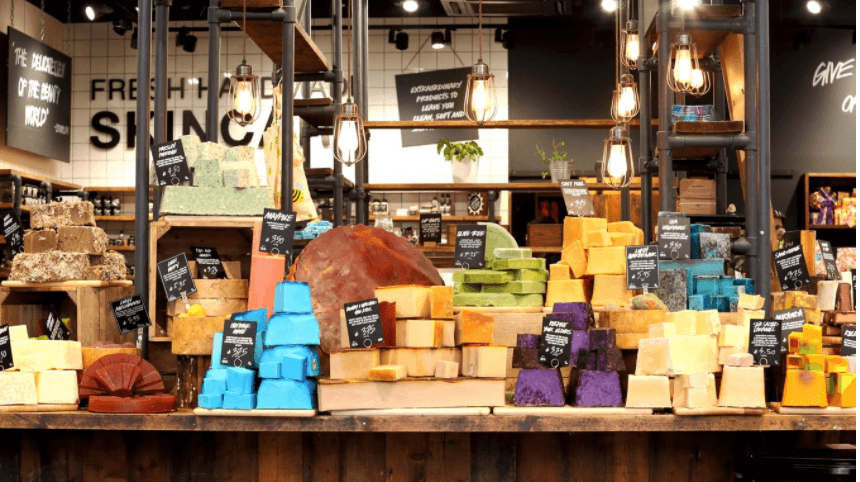
「私はオーストラリアの山火事で被災した動物たちの義援金を募る「All The Wild Things」プロジェクトの一員になれたことを非常に誇りに思っています。Formlabsのプリンタで24時間以内に金型のデザインを完成させ、コアラソープは1週間とかからずに量産に入ることができました。」
Damien Carter氏 Lush Cosmetics イノベーションラボマネージャー
コスメの枠に囚われない発想を
Formlabsの3Dプリンタは、LUSH店内で販売する商品を作ること以外にも役立っています。同社が新たにアディティブマニュファクチャリングの施設、ユニット1の設計時、LUSHのエンジニアたちは建物を視覚化して広いオープンスペースをフルに活用できるようにしたいと考えました。
新しい施設の計画や、本社内に設置する店舗の模型を製作するために、ユニット1の縮尺建築模型を作りたいと考えた同社が設計事務所に依頼したところ、人件費や材料費、輸送費を含めたコストの総額の見積が、約250万円という金額になりました。
そこでDamien氏は社内で試行錯誤を重ね、Solidworksでユニット1のモデルを制作しました。彼は、Formlabsの標準的なエンジニアリングレジンを駆使し、Formlabsの3DプリンタForm 2でそのデザインをプリントしました。構造部の主要な箇所にはWhiteレジン、内部の作業場はGreyレジン、窓にはClearレジンを使用しました。彼は人件費と材料費を含めたプロジェクト費用の総額を算出したところ、このユニット1の模型製作にかかった費用は15万円以下となり、設計事務所の見積に比べ、約94%のコスト削減が実現できました。
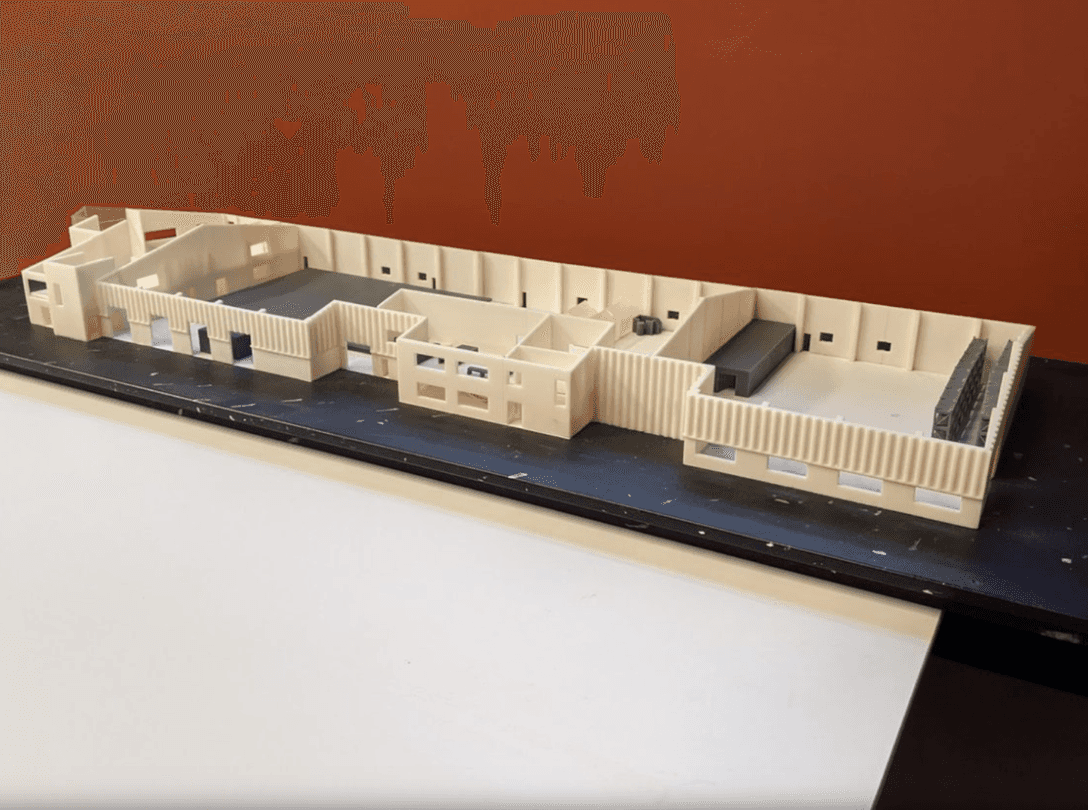
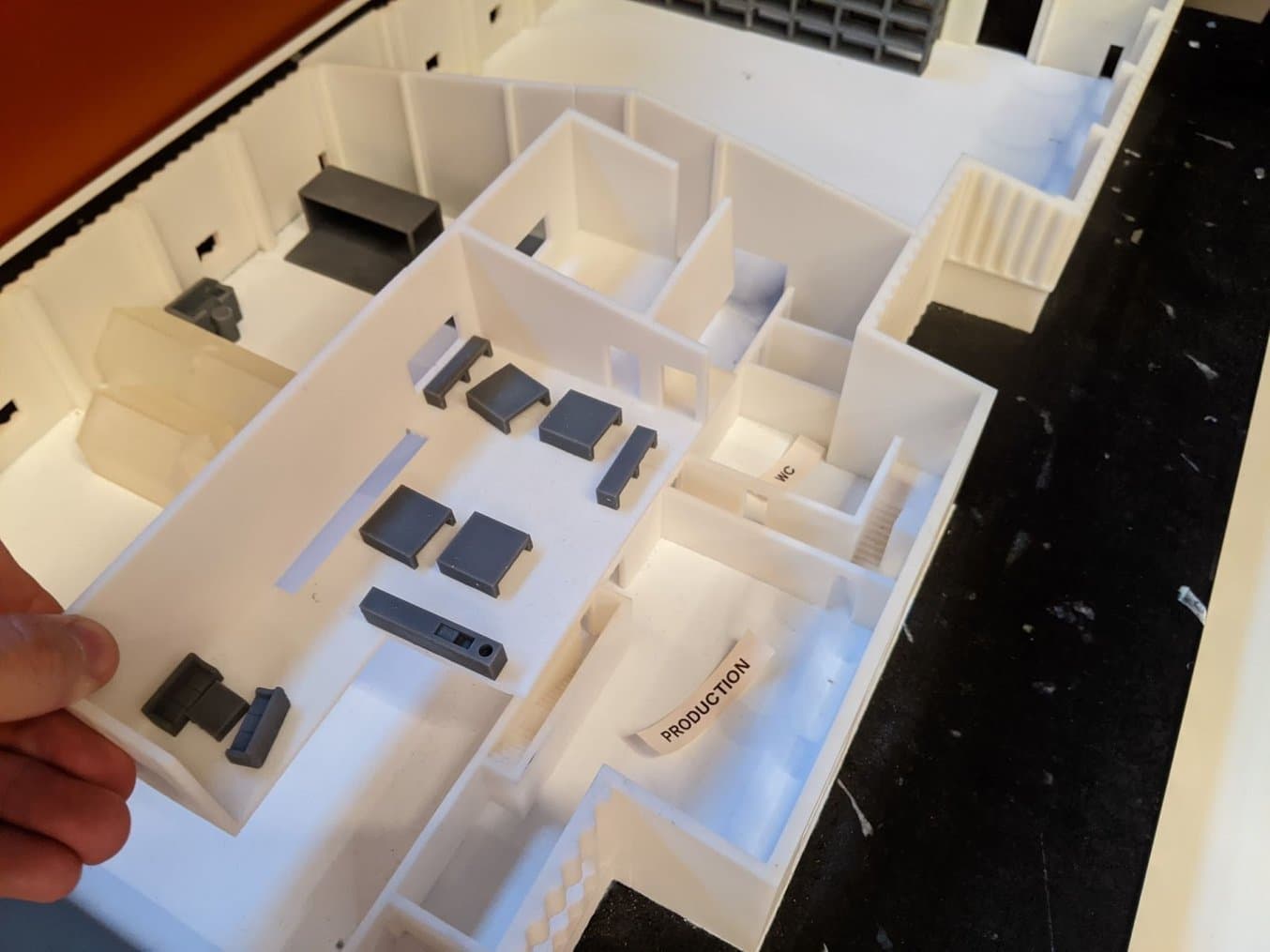
「我々の新しい研究開発施設の建築模型をFormlabsの3Dプリンタを使って社内でプリントしたことで、230万円以上のコストと数週間の製作期間を削減できました。これは建築設計の面でも素晴らしいツールです。つまり、私たちは施設丸ごとを3Dプリントで製作でき、各空間に何がどのように収まるかを実際に見て感じることができるんです。」
Damien Carter氏 Lush Cosmetics イノベーションラボマネージャー
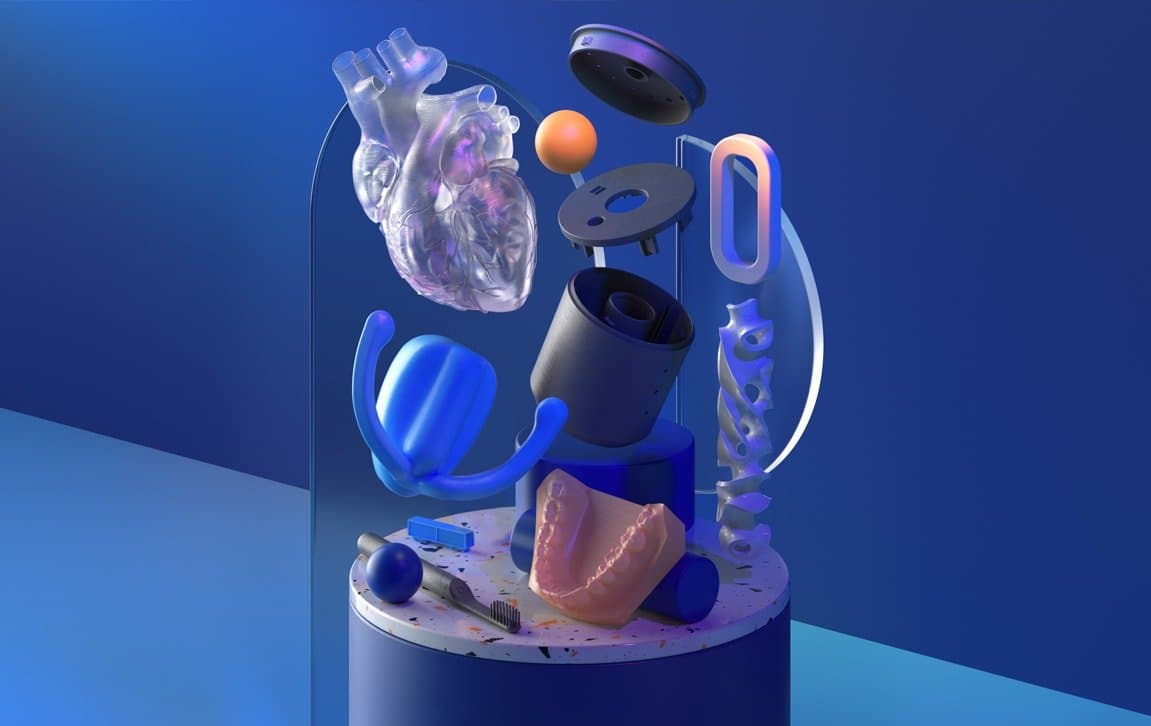
Formlabs User Summit 2020
Formlabs User Summit 2020でのDamien氏のキーノート、そして世界中のスピーカーによる50以上の他のセッションの録画をご覧いただけます(動画は英語となります)。
コスト削減と生産性向上が同時に実現
将来に向けて、Formlabs製品での3Dプリント内製化は、LUSHの社員がクリエイティブに問題を解決し、顧客ニーズに迅速に対応する手段をもたらしました。以前は金型製作だけでも1回のイテレーションで2~3日を要していましたが、現在ではアイデアのデザインから3Dプリントによる具現化までを24時間以内に行うことができ、平均的なデザインでは僅か4.5時間でプリントが完了します。
デジタルファブリケーションツールをフルに活用することで、研究開発施設は2020年前半に580件の開発を手掛けることができ、相当量の時間と労力を削減することに成功しました。また、パンデミック発生時にはより高速かつ効率的な対応ができ、ビジネスに大きな影響を与えるプロジェクトに適切な優先順位をつけて開発業務を継続することができました。
また、この新しいアプローチにより、将来の新商品に流用できるマスターのデジタルライブラリを構築したことで、将来にわたった業務効率化への取り組みもスタートできました。
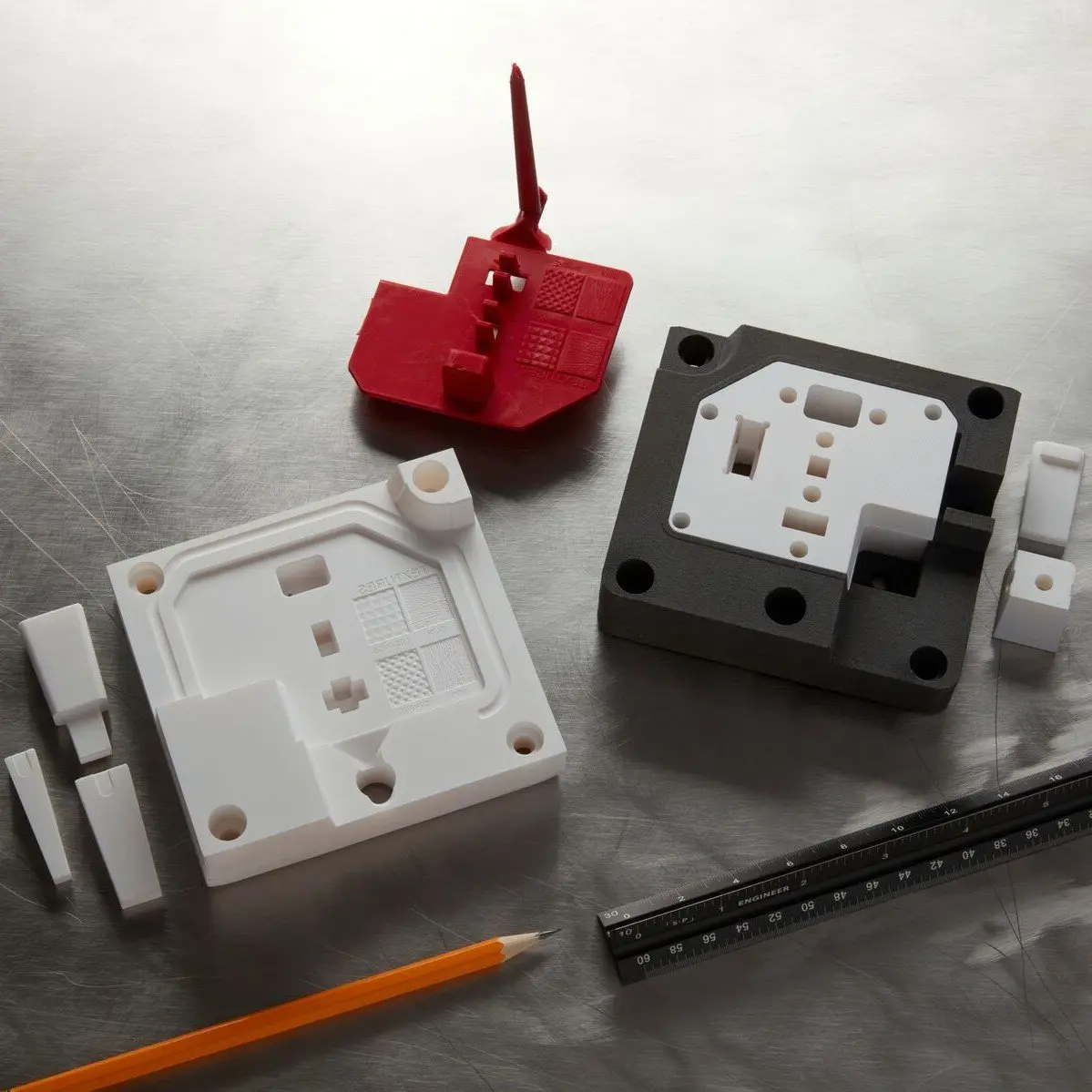
金型や治具製作を3Dプリントで効率化:ラピッドツーリング総合ガイド
本ホワイトペーパーでは、3Dプリントによる金型や治具製作のラピッドツーリングで射出成形、熱成形、鋳造などの成形工程を高速化・低コスト化する方法の概要を実際の事例を織り交ぜて解説しています。
LUSHの3Dプリント内製化によるROI分析結果
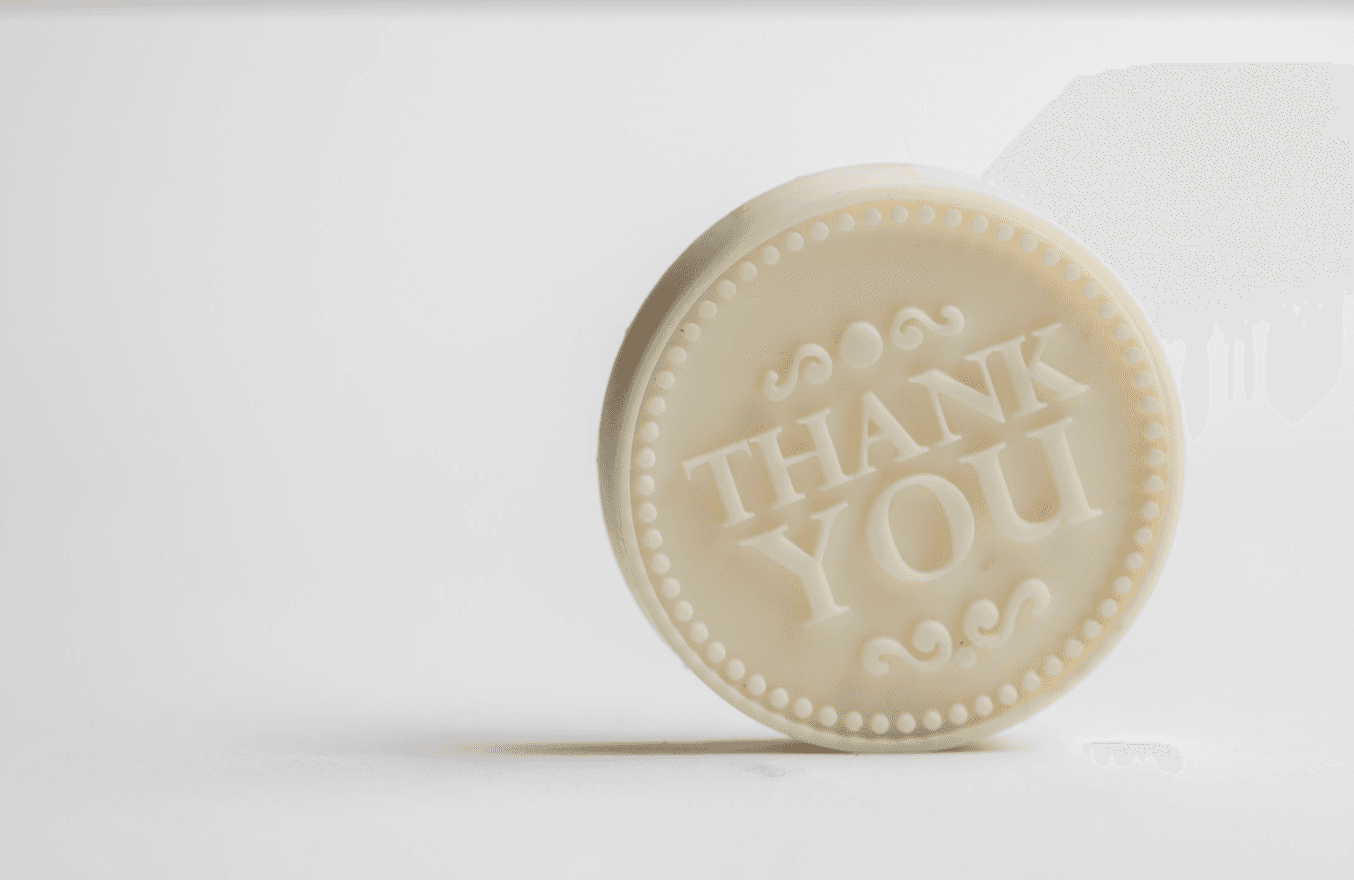
上画像のTHANK YOUコインのデザインは、外注での製作時には約16,500円を要していたがForm 3で3Dプリントする際には約867円で製作できたという。
Learn more about how product designers and engineers leverage 3D printing to improve efficiency and change the way they bring products to market.
3Dプリント製の金型を熱成形に使用する際の詳細なプロセスや作業手順、金型設計時のガイドラインなどの詳細は、Formlabsの無料ホワイトペーパー(翻訳中)をダウンロードいただくか、ウェビナーの視聴にてご覧いただけます。