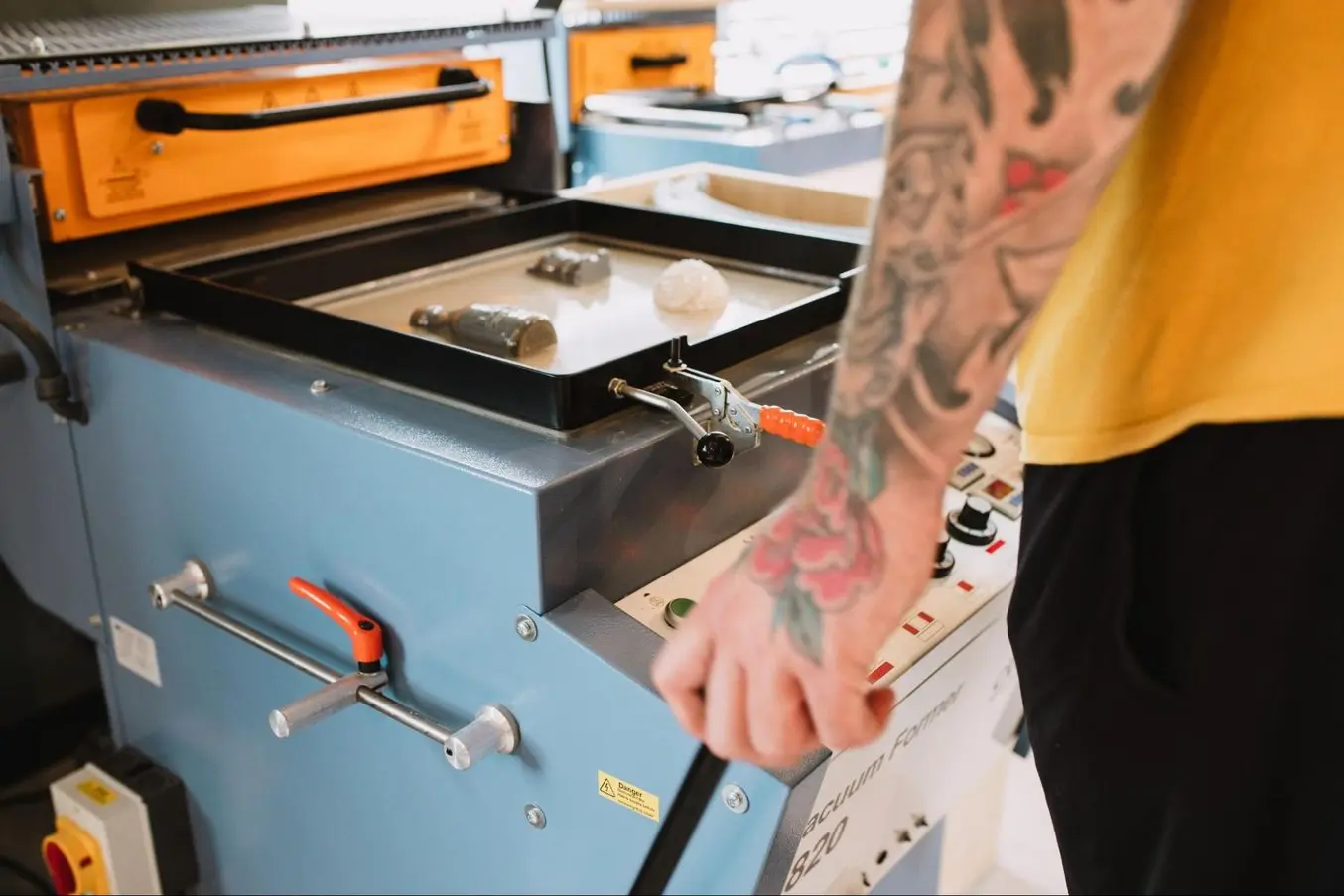
プラスチックには様々な大きさ、種類、色合いがあり、材料特性もそれぞれ異なります。バラエティに富むプラスチックは、試作品の製作や実製品用部品を生産するメーカーにとって欠かせない材料です。熱成形はプラスチックを加工する製造プロセスで、メーカーはそれぞれに合った多様な方法を取り入れています。
このガイドでは、様々な熱成形プロセスの種類、材料、設備、および熱成形用の型の製作方法について、3Dプリントなどの最新技術を活用したプロセスも交えて概要を解説します。
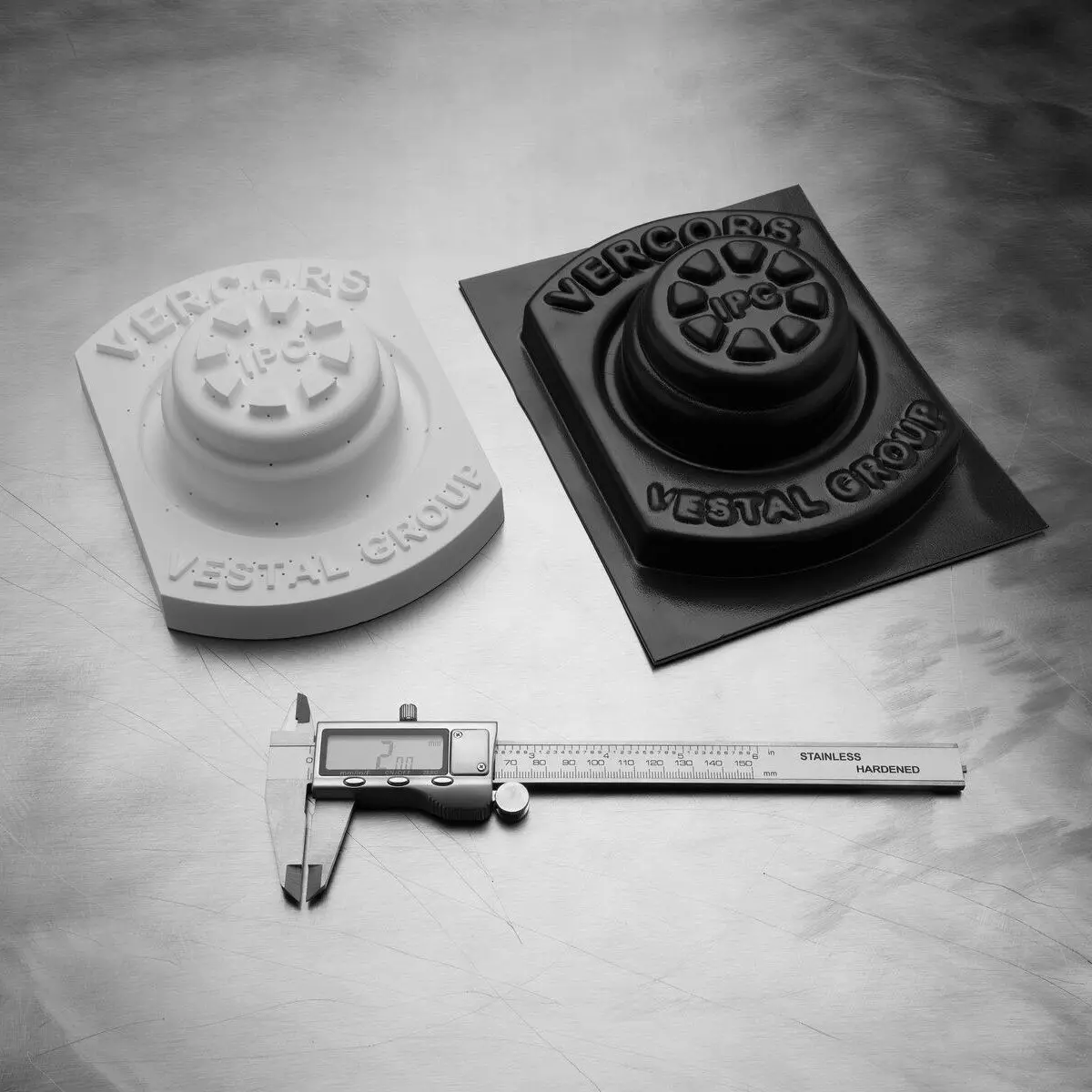
3Dプリント製の型を使用した少量高速熱成形
こちらの技術資料では、3Dプリントで複雑な成形型を短時間で製作する方法や、成形型を製作する際に参考になるヒントやガイドラインをご紹介しています。ダウンロードしてご覧ください。
熱成形とは
熱成形とは、加熱したプラスチックシートを成形型に押し込み、様々な形に成形するプラスチック製品の生産プロセスです。成形後のプラスチックは冷却やトリミングを経て完成品になります。熱成形機を用いて熱可塑性プラスチックシートを熱して伸ばし、成形型の上に乗せて加工します。最新の熱成形機には基本的にトリミングやカット機能も備わっていますが、従来型の成形機では冷却やトリミングは別々に行う場合もあります。
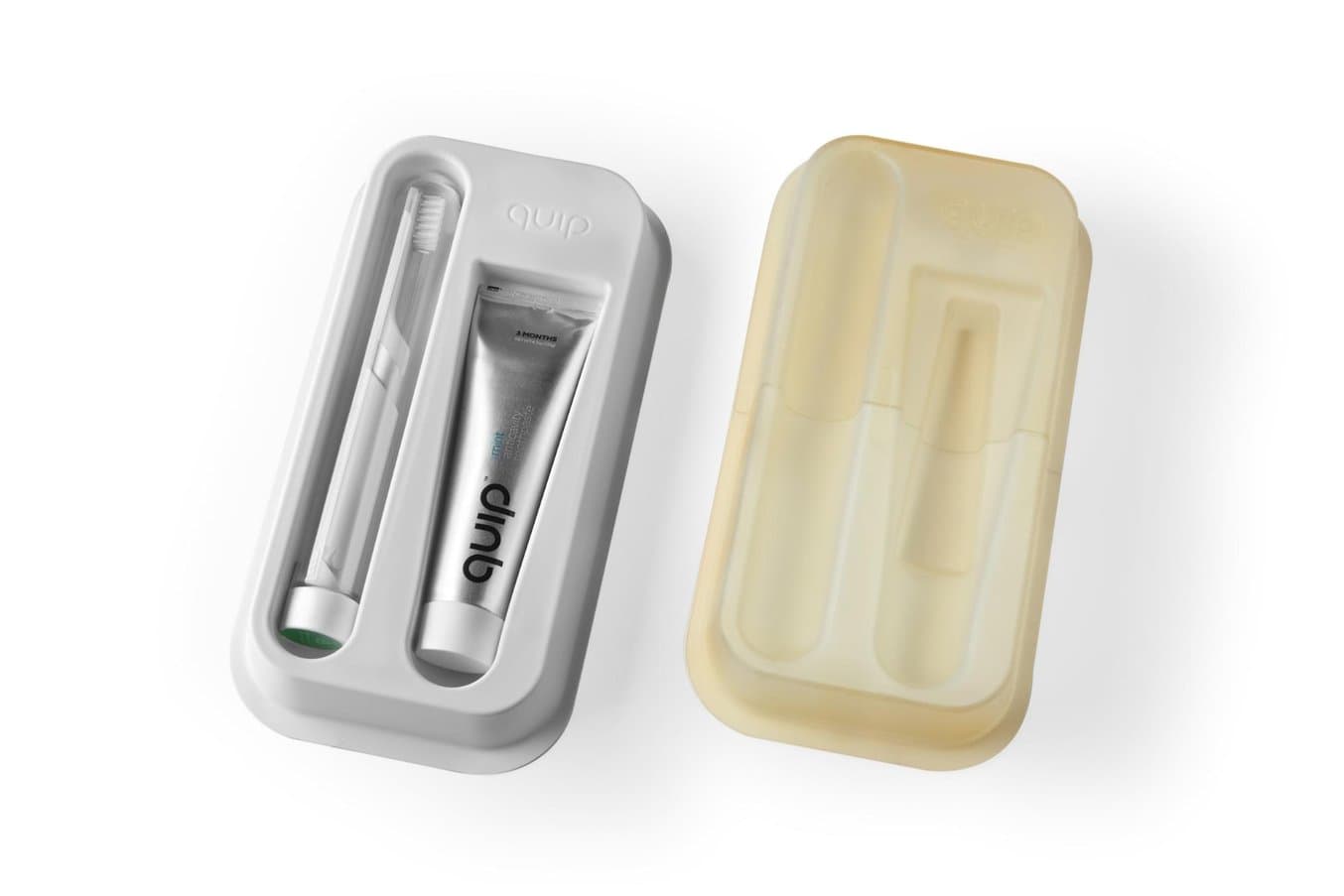
プラスチック容器の製造は熱成形が一般的。
熱成形で使用する熱可塑性プラスチックには、ABS、PS(ポリスチレン)、ポリカーボネート、PETG(変性ポリエチレンテレフタレートグリコール)などがあります。どの材料を選ぶかは、生産プロジェクトの内容や完成品に求められる特性によって異なります。
熱成形は、農業製品、医薬品、消費者製品、家電製品、その他たくさんの製品の梱包容器の生産に使用されています。また、航空機の部品やマテリアルハンドリング装置、自動車の内装、医療機器といった高耐久の実製品用部品の生産にも用いられます。
熱成形では、生産量の大小に関わらず従来の他の製造工程より安価に梱包材を製造できます。熱可塑性プラスチックならほとんどすべての材料が使用でき、高品質な実製品用アイテムを製造できることも、熱成形のもう一つの重要なメリットとなっています。
熱成形のデメリットとしては、作る製品が薄肉構造だったり厚さが不均一な場合には成形ができないこと、そして複雑形状の生産が難しいことがあります。熱成形にご関心をお持ちの方は、このガイドで熱成形機のメリットを最大限に活用する方法やデメリットを最小限に抑えて生産性を向上する方法、コスト削減を叶える方法などについてご覧いただけます。
熱成形のプロセス
熱成形とは、プラスチックシートを加熱して成形する様々な生産プロセスをまとめた総称です。真空成形や加圧成形も、熱成形のメリットを活かしたプロセスです。
様々な熱成形プロセスが存在する中で、最も広く用いられている技術は以下の通りです。
-
真空成形:真空を利用してシートを成形する熱成形プロセスです。まず、プラスチックシートを加熱して柔らかくします。その後、真空成形機がポンプで空気を吸引して真空状態を作り、シートを型に押し付けます。真空プロセスは、コスト効率が高く短時間で生産が可能なことで知られています。
-
加圧成形:加圧成形も真空成形と同様、プラスチックシートを熱して真空ポンプで空気を吸引し、シートを型に押し付けます。加圧成形の場合はここからさらにもう1ステップあり、真空状態を作った後にさらに圧力を加えることで、型にはめたプラスチックシートが最終形状をより確実に維持できるようにします。加圧成形は、細かなディテールを持った製品を作る場合に用いられます。
-
機械的成形:加熱したプラスチックシートに直接機械的な負荷を加えることで成形するプロセスです。コアプラグから熱可塑性プラスチックシートに対し、プラグと成形型の間に隙間がなくなるまで負荷を加えることでプラスチックシートを成形します。機械的成形は、高い精度と高度なディテール表現が求められる場合に使用します。
-
ドレープ成形:ドレープ成形は、加熱したプラスチックシートを特定の模様をつけて設計されたマンドレルに被せて成形する方法です。マンドレルの模様がプラスチックシートに押し付けられることで、完成品の形が成形されます。必要な金型が少なく済むため、最も経済的な熱成形手法の一つです。 材料の厚さを維持できることで、脆弱な部分のない部品を作ることができます。
-
マッチモールド成形(マッチフォーミング):高い精度が求められる製品の生産に用いられる熱成形方法です。マッチモールド成形では、オス型とメス型を使用して加熱したプラスチックシートを成形します。2つの成形型の間にプラスチックシートを挟み、成形機で圧力をかけることで成形型を噛み合わせます。シートはオス型とメス型の内側に設計された模様や形状に成形されます。
-
ツインシート成形:2層のシートを成形したものを合わせて1つの製品を作る方法です。2枚のプラスチックシートを同時に加熱・成形し、繋ぎ合わせることで1つの製品を生産します。ツインシート成形は、中空構造や二重壁構造の製品の生産に最適です。
-
ブロー成形:金型に頼らず、加熱したプラスチックシートを自由な形に成形する方法です。成形機がエアージェットでプラスチックに空気を吹きつけて中空構造にし、最終的な形状に成形します。
熱成形プロセス | コスト効率 | 生産量 | 用途 |
---|---|---|---|
真空成形 | 非常に安価、短時間の生産プロセス | 小~大量生産 | 家庭用や梱包など、精密性や正確性が重要ではない製品の生産 |
加圧成形 | 安価な生産プロセス | 小~大量生産 | 耐久性と均一性が要求される製品の生産 |
機械的成形 | 安価な生産プロセス | 中~大量生産 | 高品質、高精度な製品の生産 |
ドレープ成形 | 非常に安価、短時間の生産プロセス | 中~大量生産 | 大型のコンポーネントや一部厚みのある部品など、単純な曲面形状の部品 |
マッチモールド成形 | 金型製作にコストがかかるため、高額な生産プロセス | 中~大量生産 | 車両のトリミングや治具等、高耐久部品やコンポーネントの生産 |
ツインシート成形 | 安価な生産プロセス | 中~大量生産 | 中空構造、二重構造の製品など、梱包製品の生産 |
ブロー成形 | 他の成形方式よりも高コスト | 小量生産 | 天窓やドーム等の生産 |
熱成形で使用する材料
熱成形は、食品用包装、航空機部品、玩具、パレット、その他プラスチック製品の生産に用いられています。したがって、メーカーは生産サイクルに入る前に多様なプラスチック材料の中から使用する材料を選ぶ必要があります。熱成形で一般的に用いられている材料は以下の通りです。
-
ポリプロピレン(PP):PPは、価格的にも量的にも熱成形で最も人気の高いプラスチック材料で、包装容器、換気扇、玩具、その他プラスチック製品に広く用いられています。薬品や劣化、熱に強い特性が人気の理由です。ポリプロピレンは価格も安価で、本ページで紹介した様々な熱成形プロセスにも対応しています。
-
ポリスチレン(PS):芳香族炭化水素ポリマーで構成される透明な硬質プラスチックです。ポリスチレンは水や空気への耐性に優れ、包装材料の熱成形に広く使用されているほか、食品用包装材、ジュエリーケース、CDケース、家庭用製品等の生産にも用いられています。
-
ポリエチレンテレフタラート(PET):PETは、アルコールや精油を遮断する力が極めて高く、優れた耐薬品性、耐衝撃性、そして引張強さを備えています。PETは、炭酸飲料や水のボトル、その他多くの食品製品の容器として広く用いられています。
-
低密度ポリエチレン(LDPE):LDPEは薬品や紫外線への耐性を備えた熱可塑性プラスチックで、柔軟性と引張強さにも優れています。LDPEは、梱包用フィルム、DVD、電線を覆う絶縁体、コンテナ、耐薬品性の製品の製造に適しています。
-
高密度ポリエチレン(HDPE):基本的な特性はLDPEと似ていますが、なかでも薬品、紫外線、水への耐性に優れた材料です。耐久性に優れた熱可塑性プラスチックであることから、梱包用フィルム材や、ボトルのブロー成形、コンテナ、配管、プラスチック袋の製造に適しています。
-
ポリ塩化ビニル(PVC):PVCも一般的なプラスチック材料で、配管や窓枠、自動車の内装、家庭用品、梱包材、靴の製造などに広く使用されています。PVC材料は、メーカーの要件によって硬質にも軟質にも調整することが可能です。また、この熱可塑性プラスチックは高密度で耐久性が高く、耐水性もあります。PVCの耐薬品性は完全ではなく、塩素に対しては化学反応を起こす場合があります。
-
ポリカーボネート(PC):強度の高い材料で、亀裂や破損が生じることなく大幅な変形が可能です。耐熱性、難燃性、絶縁特性にも優れています。一部の等級のポリカーボネートは透明性が高く、光に当てると透き通って見えます。ポリカーボネートは、メガネのプラスチックレンズや医療機器、自動車部品、保護具(メガネ、ヘルメット)、防弾ガラス、自動車のヘッドライト、建設資材といった用途に使用されています。
-
酢酸セルロース:環境に優しい熱可塑性プラスチック材料をお探しの場合は、酢酸セルロースを検討してみるのもよいかもしれません。この熱可塑性プラスチックは、加工された木材パルプなどの再生資源から作られています。酢酸セルロースは基本的に無色透明で、家庭用品や、梱包用フィルム、メガネフレーム、錠剤のコーティングに用いられます。
-
ポリメタクリル酸メチル(PMMA):高い強度、気候要素への耐性、耐久性、透明性を備えた材料です。このような特性を活かし、レンズや自動車のヘッドライト、透明な梱包材等の生産に用いられます。PMMAは耐久性に優れていることから、実製品用部品の長寿命化にも貢献します。
-
アクリロニトリル・ブタジエン・スチレン(ABS):ABSの特性には、剛性、耐摩耗性、低温耐性などがあります。ABSを使った熱成形により、電子部品用の包装材、食品容器、家電機器の生産が行えます。
熱成形にはその他、ポリテトラフルオロエチレン(PTFE)、ポリアミド、HIPS等の材料が使用可能です。どの材料を選ぶかは、使用する熱成形技術とプロジェクトの要件によって異なります。以下の用途別一覧をご参考に、お客様のプロジェクトに適した材料をお選びください。
代表的な用途 | 材料 | 一般に使用される熱成形方法 |
---|---|---|
パッケージング | ABS、PP、PMMA、PVC、PET、LDPE | 加圧成形、真空成形、マッチモールド成形、ツインシート成形、機械的成形 |
家庭用および消費者向け製品 | ABS、PS、PVC、PP、PC | 加圧成形、真空成形、機械的成形 |
自動車の内装およびコンポーネント | PC、PMMA, HDPE、LDPE | ドレープ成形、マッチモールド成形、加圧成形 |
ヘルスケアおよび医療機器 | 酢酸セルロース、LDPE、PC | 加圧成形、機械的成形、真空成形 |
建設/建築、空調、配管 | PVC、HDPE、PC | 機械的成形、加圧成形、真空成形、ドレープ成形 |
ヘビーゲージ vs シンゲージ
熱成形で使用するプラスチックシートの寸法の違いによって、熱成形をシンゲージで行うかヘビーゲージで行うかが変わります。シンゲージ熱成形機には、プラスチックシートのロールから薄手のプラスチックシートを使用します。ヘビーゲージ熱成形機には、厚手のプラスチックシートを使用します。熱成形機を選定する際は、このプラスチックの厚みが重要な要素となります。
例えば、薄いプラスチックコップや食品包装容器を生産したい場合には、シンゲージ熱成形を用います。逆に、パレットやコンテナを生産する場合にはヘビーゲージ熱成形機とその周辺機器が必要です。ヘビーゲージ熱成形機は小量から中量の生産用に、シンゲージ熱成形機は大量生産用に設計されています。
以下に、ヘビーゲージとシンゲージの熱成形の違いをまとめました。
プラスチック熱成形 | ヘビーゲージ | シンゲージ |
---|---|---|
製品の厚み | 1.5~9.5mm | < 3mm |
機械のタイプ | プラスチックシートを補給 | 薄いロールを補給 |
使用する熱可塑性プラスチック材料 | ABS、HDPE、PP | PETG、PET、PVC |
生産量 | 小量~中量 | 中量~大量 |
使用事例 | 電子部品のエンクロージャ、内装パーツ、産業用機器、永久構造物、パレット、浴槽、シャワートレイ、スーツケース。 | 硬質または半硬質梱包材、使い捨て製品(食品容器、使い捨てコップ、皿、トレイ)、小型医療機器用包装。 |
熱成形機
真空成形、加圧成形、ツインシート成形、ドレープ成形など、使用する熱成形方式に応じて専用の機器が必要です。
これらの熱成形機はさらに、用途に応じて、デスクトップ、産業用、DIY用のカテゴリーに分類できます。専門業者や専門性の高いホビイストの場合は、用途に応じて適切な機械を選択するとよいでしょう。
適切な熱成形機を選択する際に考慮すべき製品仕様は以下のとおりです。
-
成形面積:プラスチックを使って模様や形状を成形する面積を指します。成形面積には、最終製品の形状に合わせて設計した金型、コアプラグ、加熱したプラスチックシートに模様をつけるための機器などを配置します。
-
絞りの深さ:絞りの深さ、または絞り率は、熱成形プロセスの理解に欠かせない要素です。絞り率がわかれば、個々の熱成形プロジェクトに必要なプラスチックのゲージがわかります。熱成形機の「絞りの深さ」の値がわかれば、メーカーはその値を元にプラスチック製品の厚みを決定し、熱成形プロセス中にプラスチックシートが覆うべき表面積を求めることができます。
-
熱成形機の寸法:熱成形機の寸法により、製造できるコンポーネントやプラスチック製品のサイズが決まります。デスクトップサイズの熱成形機の場合は本体サイズがコンパクトなため、成形品の寸法も小さくなります。対して産業用の成形機は遥かに大型の製品を成形できます。
-
クランプ力:加圧成形、ツインシート成形、マッチモールド成形で使用する熱成形機等では、型にプラスチックシートを挟み万力(クランプ)で押さえつけることで最終的な製品の形に成形します。この時の挟み込む力(クランプ力)が、どんな材料が使用できるかを決定する重要な要素となります。
-
金型の変更機能:熱成形機の金型変更機能を確認しておくと、金型の交換がどの程度早く実行できるかを見定めるのに役立ちます。迅速に交換可能なタイプであれば、生産効率とコスト効率を高めることができます。
熱成形機の種類
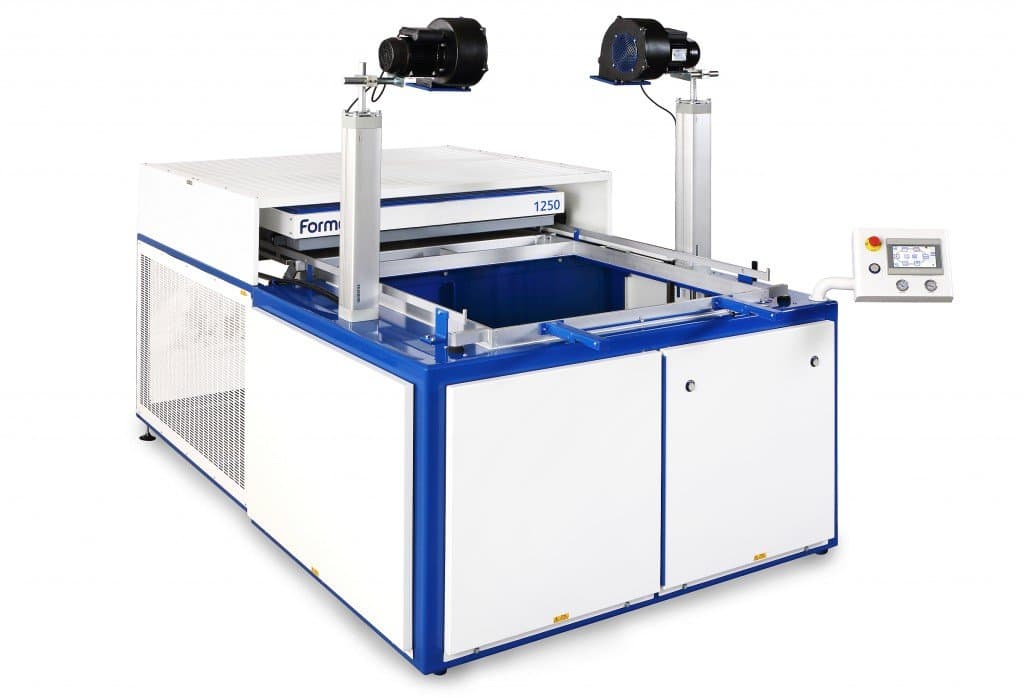
Formechの産業用大型真空成形機
熱成形機の製品仕様がわかったら、用途に応じて以下のいずれかのカテゴリーに合致する熱成形機を選びます。
-
産業用熱成形機:中量~大量生産に適した大型の機械です。産業用の真空成形機は、豊富な種類の材料とシートの厚み、および絞りの深さに対応しており、さらに吸引力や圧力も高く複雑形状や繊細な形状を成形できるため、射出成形品に近い品質の成形品を生産できます。産業用熱成形機の例として、GN、Ridat、Formech、Belovacなどの真空成形機があります。産業用熱成形機の最低価格は大体$10,000ほどで、それ以上のものもあります。
-
デスクトップ型の熱成形機:卓上型の熱成形機はサイズが小さく、対応する材料の種類も少なめで加圧力も小さくなります。このタイプの熱成形機はメーカーや製品開発部門での試作品や特注部品の製作、小量生産から趣味の工作まで、幅広く利用されています。デスクトップ型の熱成形機は$1,000未満から販売されており、各種機能を搭載しても$10,000以下で購入が可能です。このタイプの熱成形機は、Formech、Mayku、Smartform等のメーカーが販売しています。
-
DIY向けの熱成形機:熱成形を試してみたいという個人の場合は、少量生産向けのDIY機がよいでしょう。DIY向けの製品は標準的な熱成形機よりも遥かに低予算で購入できますが、手作業で行う部分が多く専門知識も必要になります。
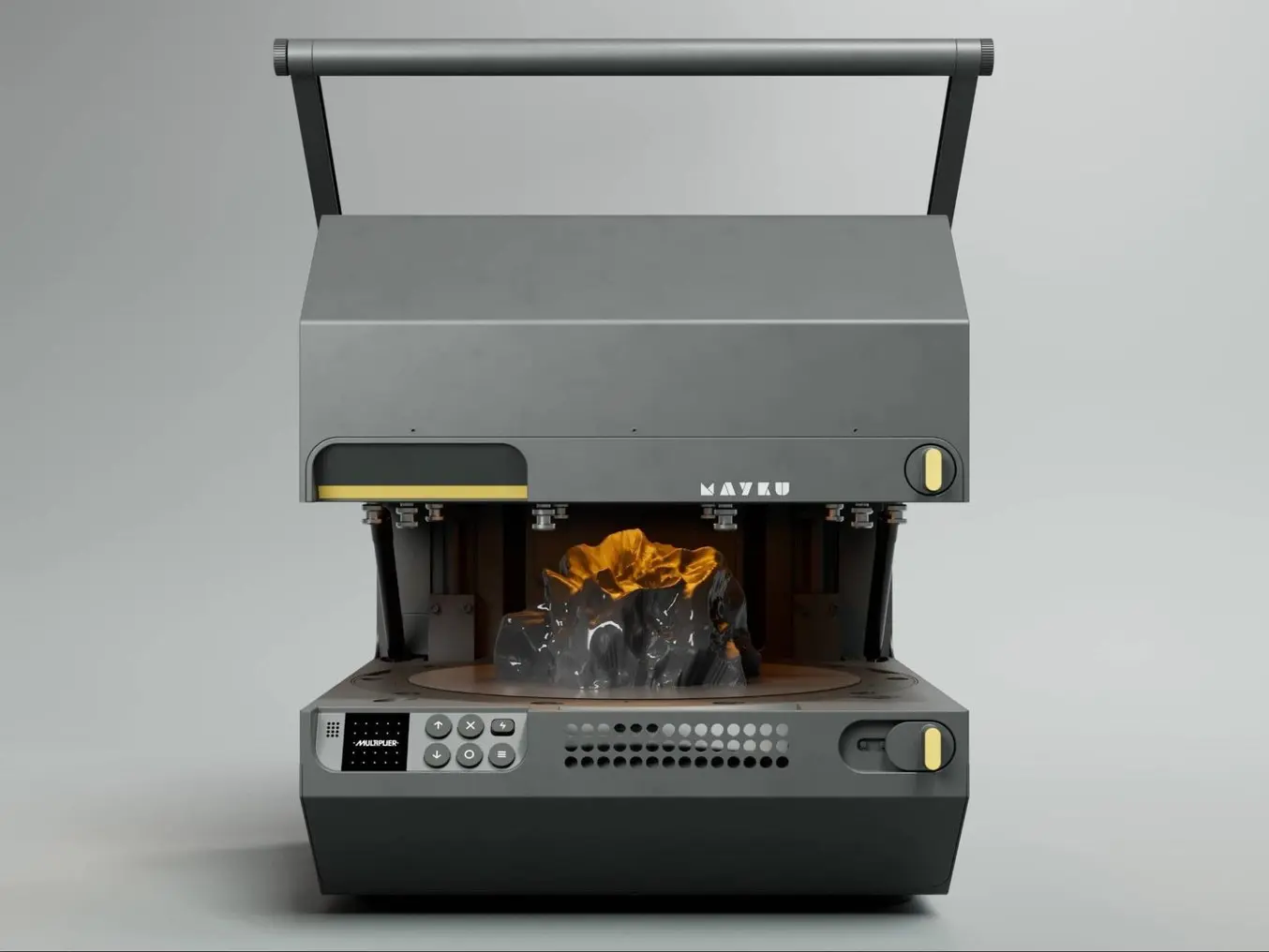
Mayky製のデスクトップタイプの加圧成形機。
熱成形で使う成形型
熱成形で最も広く使用されている手法は、真空成形、加圧成形、マッチモールド成形、 機械的成形、ツインシート成形などのように、成形型を使用してプラスチックシートから製品を作る方法です。
熱成形で必要となる成形型は、手作業で木材を彫り出したものからプラスチックや発泡スチロール、ガラス繊維、複合材料、金属等をCNC加工したもの、ポリマー材を3Dプリントしたもの、石膏や金属を鋳造したものまで様々です。
金型の設計や適した成形型の製作方法は、製品の設計のほかに次のような要素によっても変わります。
-
生産数量:カスタムパーツ、試作品、および小量生産向けには木材、石こう材、複合材、および3Dプリントによる成形型が最もコスト効率がよく、中程度の数量の生産には3Dプリントや機械加工、プラスチック鋳造、合成材料の成形型が適しています。 大量生産の場合は優れた熱伝導性と強度を備えた金属製の金型が適しており、金型の表面温度の精密制御が可能、毎回品質が均一な成形品が作れる、サイクルタイムが短い、耐久性に優れる、といった長所があります。
-
製品の設計:木材から手彫りで成形型を製作する方法はシンプルな成形型には適しているかもしれませんが、複雑な精密形状を正確に再現する必要のあるパーツには、鋳造、機械加工、または3Dプリントといったデジタル加工が適しています。
-
熱成形温度:熱成形に使用する材料によっては、成形型に高温への耐性が求められる場合があります。成形型の冷却経路の設計が冷却効率の高低や製品の均一性を左右し、サイクルタイムの短縮にもつながります。
-
熱成形時に受ける力:成形型は、真空成形や加圧成形、機械的成形など、成形時に受ける力に耐える十分な強度を備えている必要があります。成形型が受ける各種応力は、材料の種類やシートゲージのほか、表面仕上げや精細度といった成形品の品質に関わる要件によっても異なります。
-
成形型のフィーチャー:成形型には、成形プロセスで生じた空気を逃すための複数のエアベントや、離型をしやすくするための抜き勾配などの重要なフィーチャーを設定する必要があります。
-
成形型の表面仕上げ:成形型を製作する時は、表面品質や精細度、寸法精度、安定性など、成形品の品質に関する各種要件を考慮する必要があります。
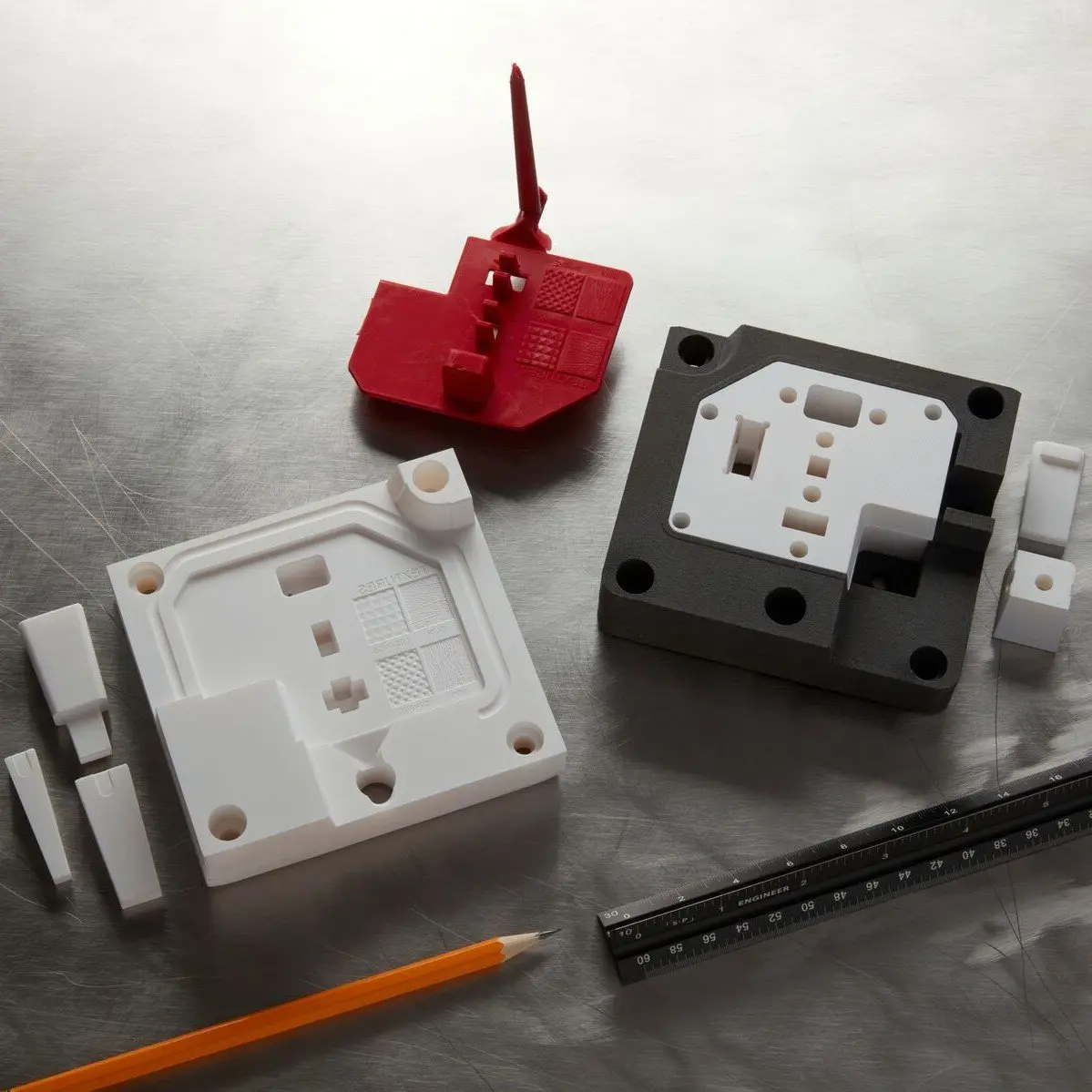
3Dプリントによる熱成形型の製作
従来の金型の生産手法は高価で作業量も多く、長い製作期間が必要だったために、熱成形プロセス全体の効率を押さえつける原因となっていました。
特に小量生産やカスタムパーツの生産、あるいは試作品の設計などを目的とした熱成形プロセスで使う成形型の製作には、SLA光造形3Dプリントを活用して高速に成形型を製作するラピッドツーリングという手法を採用する企業が増えています。短時間かつ低コストで成形型を製作できるうえ、複雑形状にも精密形状にも対応可能な柔軟性が手に入るためです。小型の成形型の製作にはデスクトップサイズのSLA光造形プリンタ Form 3+を、最大335 × 200 × 300mmまでの大きめの成形型の製作には大容量SLA光造形プリンタ Form 3Lのご使用をおすすめします。
熱成形型の製作に3Dプリンタを使用するメリットは、次のとおりです。
-
スピード:3Dプリンタは、小型から中型までの熱成形型を24時間以内で製作できます。
-
コスト効率:3Dプリンタの活用で成形型の製作コストを削減でき、小量生産パーツやカスタムパーツ等を熱成形する際のコスト効率を大幅に向上させることが可能です。
-
複雑な成形型の設計:従来型の生産プロセスにつきものの複雑形状の成形型の開発に関する悩みを解決します。3Dプリントでは例えば、機械切削では実現が難しかった形状にも対応が可能で、成形型にエアベント数を増やすことで排気と成形型内圧力を調整し、成形プロセスの質を向上することができます。工業品質の3Dプリンタでは、ツインシート成形やマッチモールド成形といった熱成形プロセス向けの複雑形状の成形型も製作可能です。
-
成形型のラピッドプロトタイピング:試作品用の成形型の試作・検証を短時間で繰り返す必要がある場合に役立ちます。3Dプリントで製作した成形型は、カスタムパーツの生産や量産前のテスト生産のように、小量生産用にそのまま使用可能です。
-
材料の種類が豊富:3Dプリントは様々な種類の材料に対応しているため、コストや品質、耐熱性、耐久性がそれぞれ異なる成形型を試すことが可能です。
-
表面品質:SLAおよびその他の光造形3Dプリントでは、表面の滑らかな高精細パーツの製作が可能です。
-
使いやすさ:デスクや作業台の上にも設置可能なSLA光造形3Dプリンタは、既存の熱成形工程にスムーズに統合が可能です。操作やメンテナンス手順もシンプルで、CNC加工時間を短縮でき、熟練の技術者がより重要な作業に集中することができます。
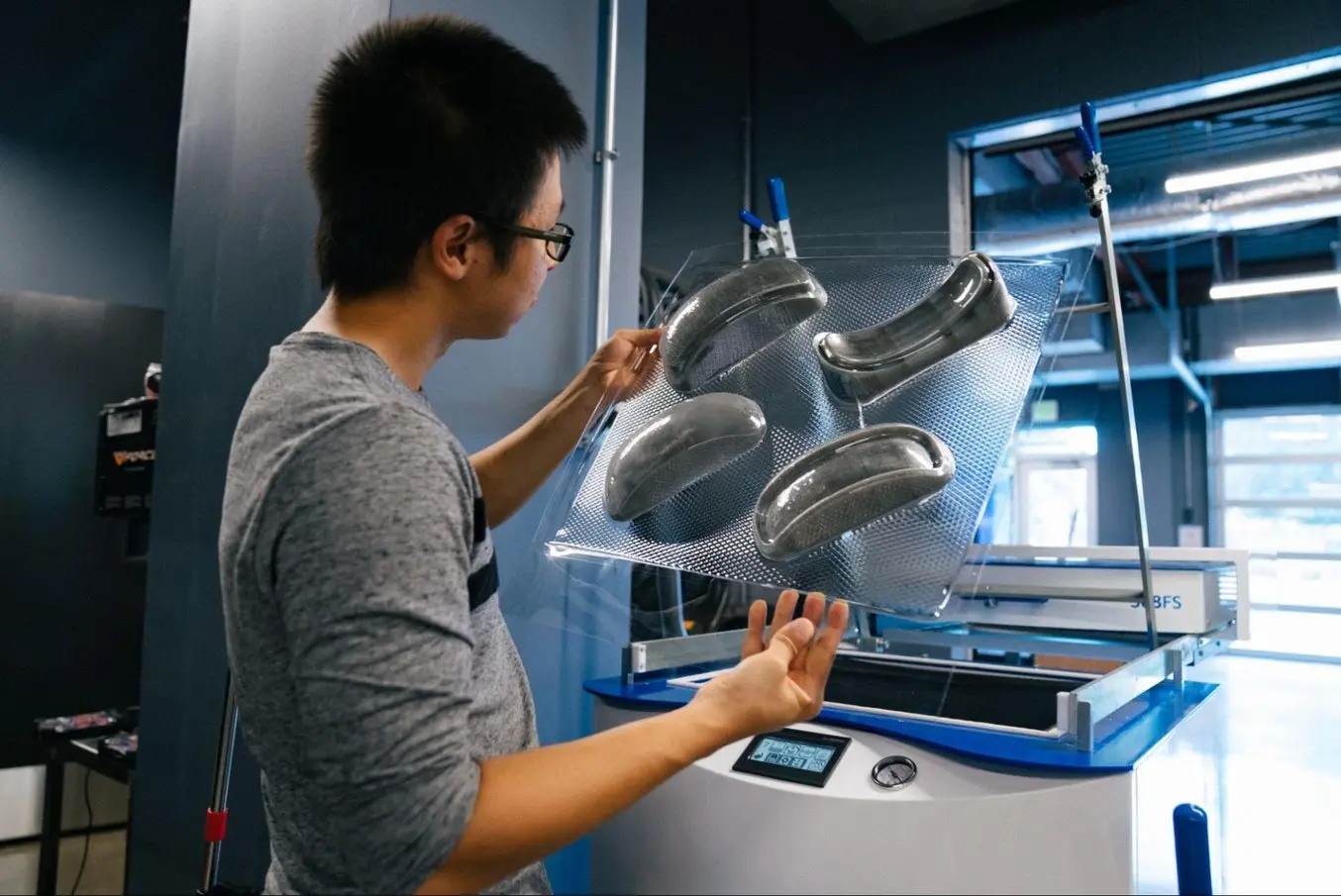
製品開発会社のGlassboardは3Dプリント製の成形型を用いてヘルメット外郭やパッケージ等のポリカーボネート製品の試作品を熱成形で製作している。
製品開発会社のGlassboardでは、熱可塑性プラスチックを使用した試作品に高速プリントが可能なDraftレジンを使用。短時間で成形型を製作し、ポリカーボネート製のヘルメットや梱包材の試作品を熱成形で製造しています。同社はこの方法で、従来の製作方法では難しい複雑な形状をもつ成形型の製作や、成形型内全面をより確実に真空引きするための細かな形状調整や穴あけ等も簡単に行えるようになりました。
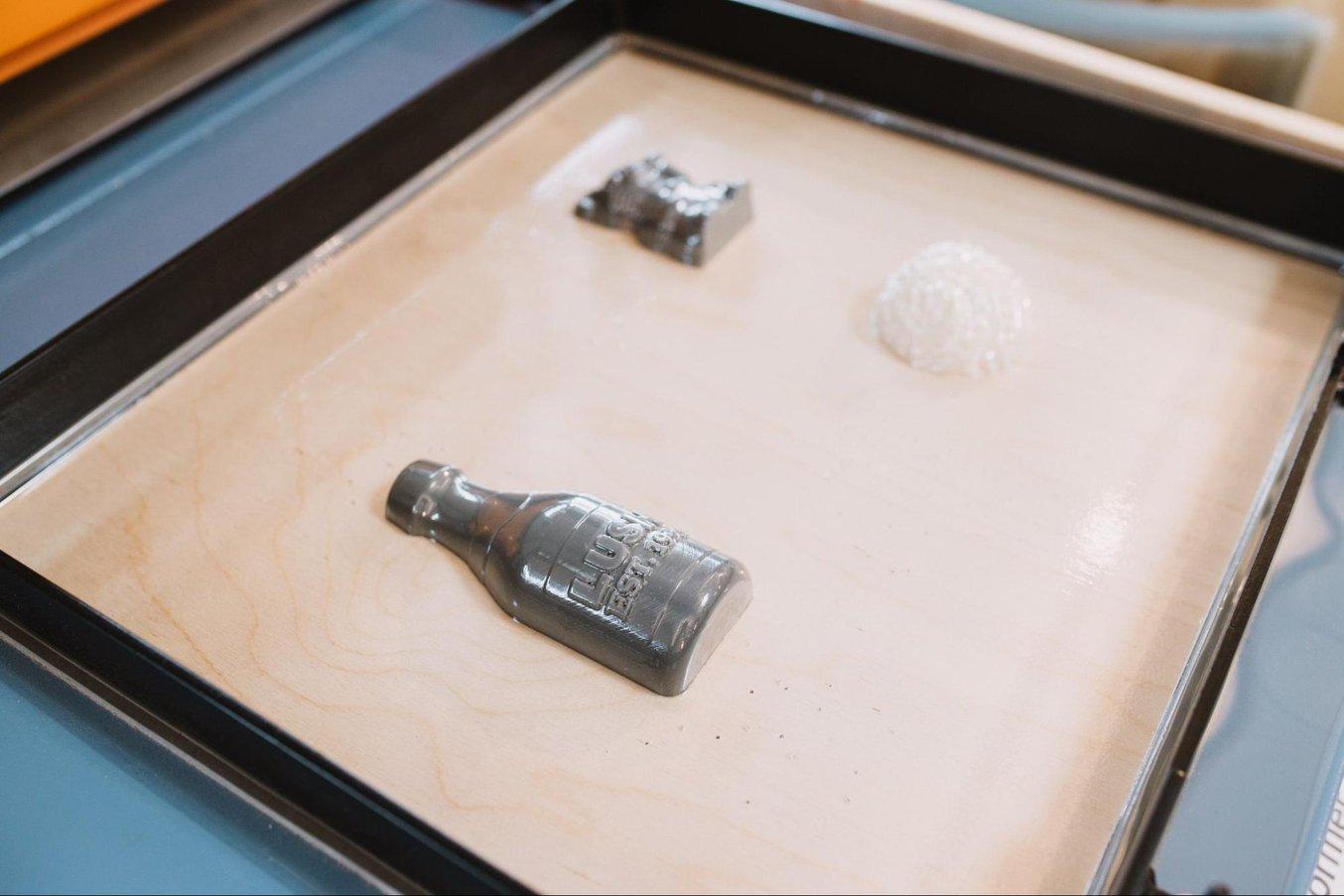
化粧品メーカーのLushは、3Dプリントで製作した成形型を使用して、精細で独特の質感を持つ同社製品用の真空成形型を24時間以内に製作。
化粧品メーカーのLUSHはこれまで、同社の大人気商品の原型を手作業で製作していました。しかし最近になって、同社は高精細なテクスチャがデザインされた真空成形用の型を3Dプリンタで製作するようになりました。同社はアイデアを24時間以内に形にするというポリシーを打ち立て、毎年1,000を超える新しいデザインをテストしています。
3Dプリントで製作した熱成形型はコスト効率に優れているため、特注品やカスタマイズ品にも適しています。たとえば3Dプリント製の成形型で真空成形あるいは加圧成形したクリアアライナーは、歯科でそのまま使用可能です。

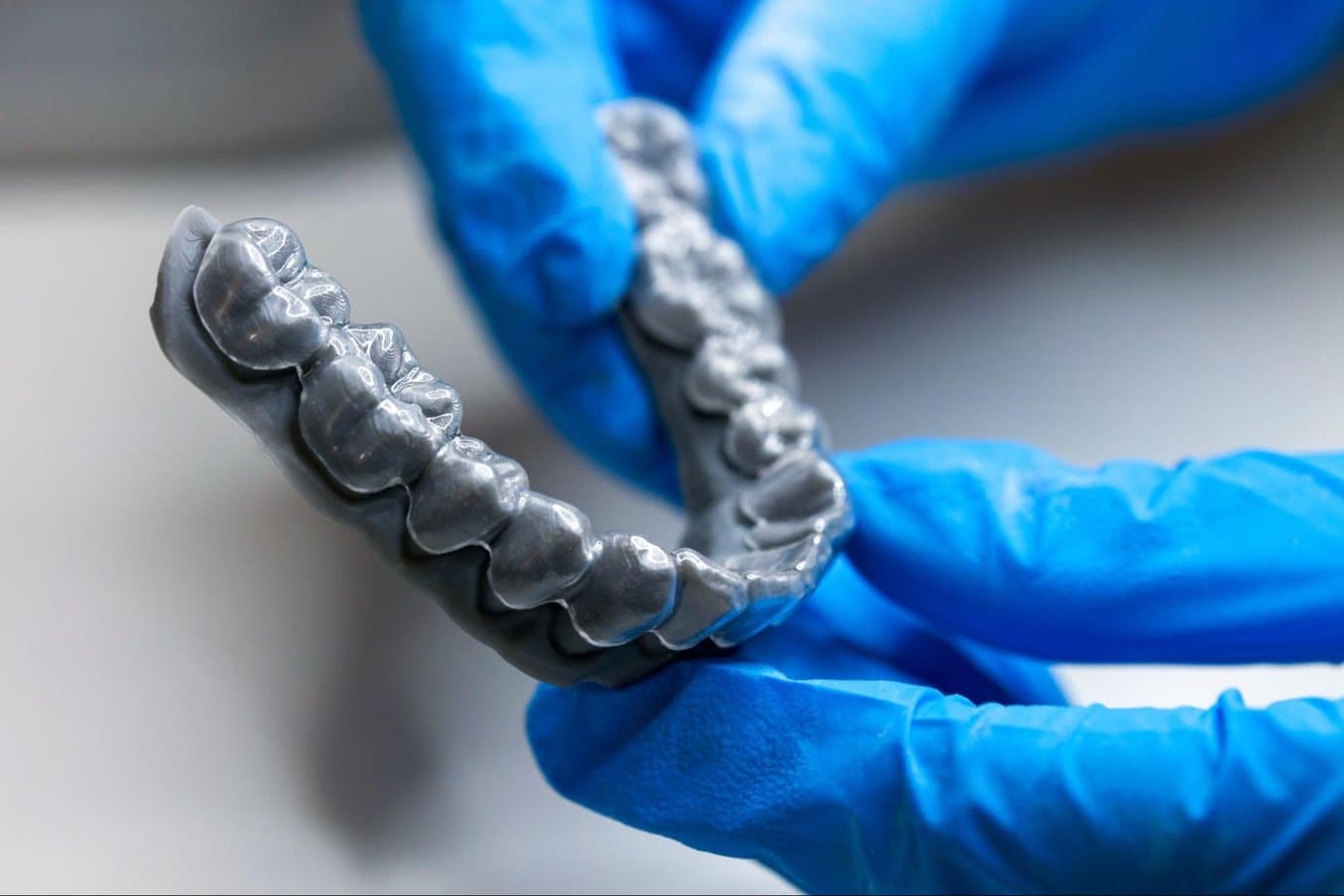
歯科矯正の透明アライナー製作では、3Dプリントしたモデルの上から真空成形や加圧成形を行う方法が一般的となっています。
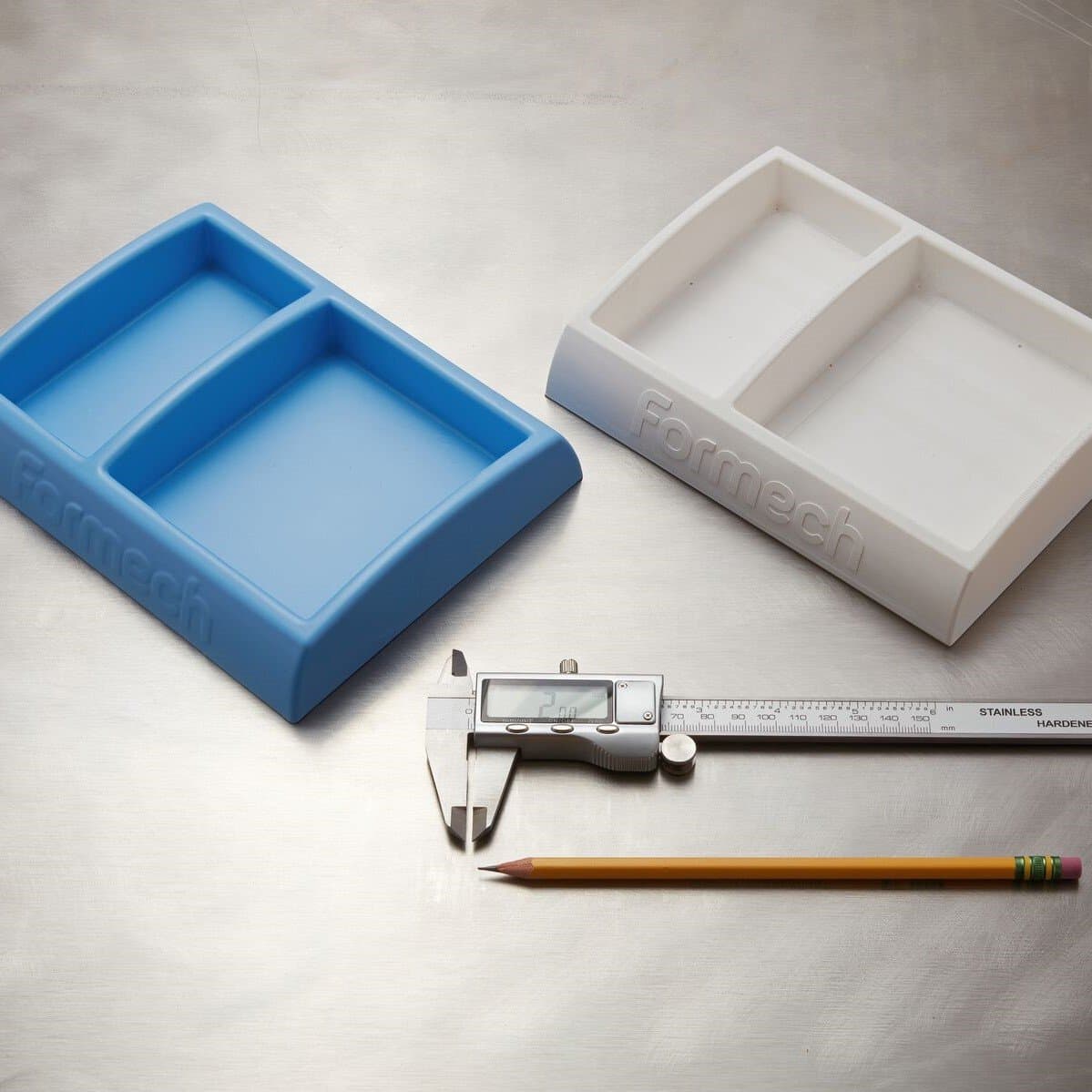
3Dプリント製の成形型を活用した熱成形: 実用ガイド
3Dプリント製の成形型と熱成形プロセスを組み合わせることで、製品開発の加速、コストと製作期間の削減、カスタム生産や少量生産を容易に叶えます。
3Dプリントを使用した熱成形用金型の製作方法
3Dプリントを活用することで熱成形プロセスに要する時間が短縮され、従来の生産ワークフローにも変化が起きています。3Dプリントを使用したワークフローは、次のような手順で構成されます。
-
CADアプリケーションを使用して金型を設計します。
-
Formlabsの充実した材料ライブラリから用途に合った材料を選択し、FormlabsのSLA光造形3Dプリンタでパーツをプリントします。
-
3Dプリントした成形型を熱成形機に取り付け、生産プロセスを実行します。
-
成形品を取り出して標準的な後処理を行い、使用できる状態にします。
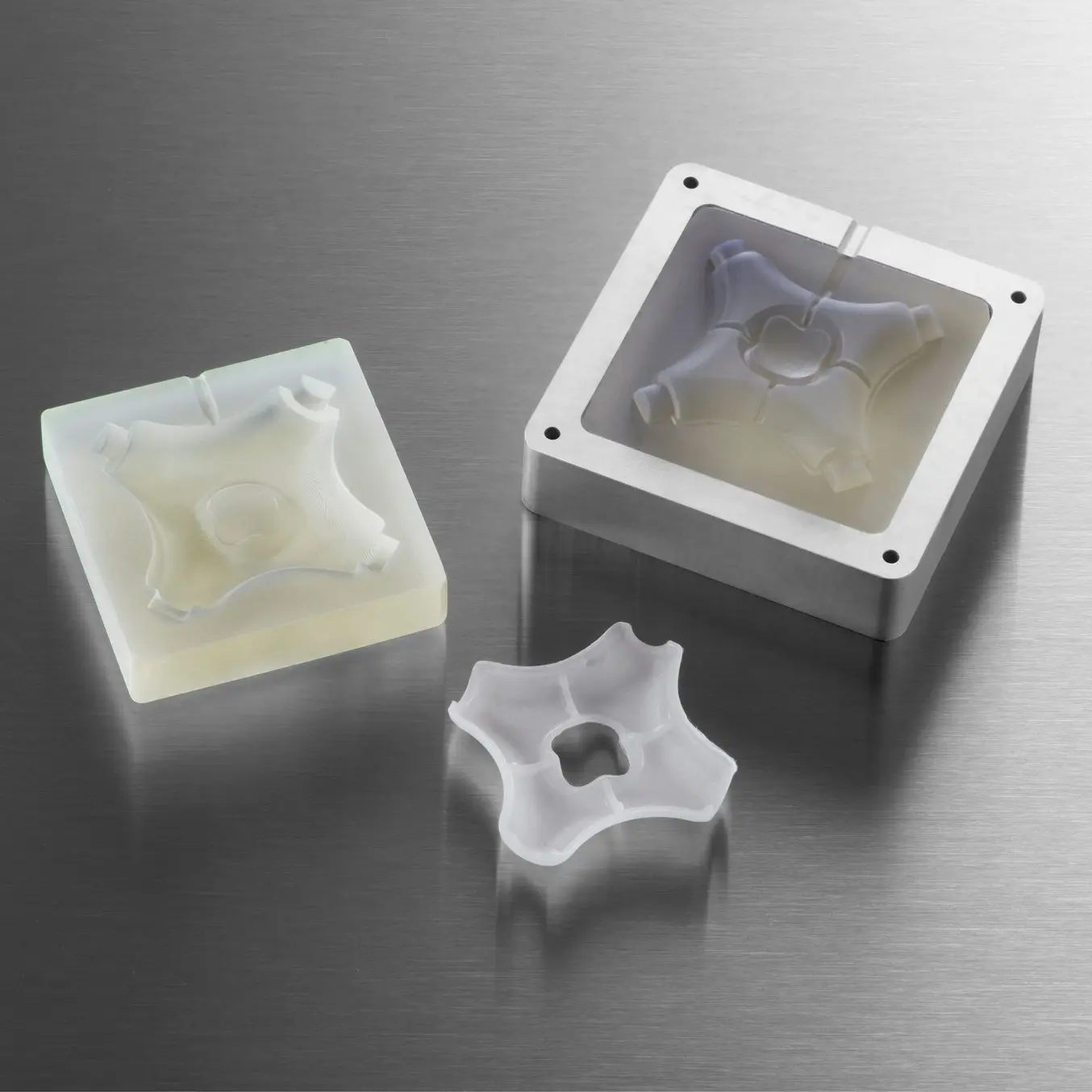
3Dプリントで成形型を製作し、試作品製作や量産で活用
本技術資料では、SLA光造形3Dプリンタで成形型を内製する6つの方法をまとめました。ダウンロードいただくと、 射出成形、真空成形、シリコン成形、その他の方法について詳細をご覧いただけます。
3Dプリンタで熱成形型を製作する
3Dプリント製の成形型と熱成形プロセスを組み合わせることで、工程全体の柔軟性、俊敏性、拡張性、コスト効率の向上が見込めるほか、量産移行前の設計検証や材料の確認、実製品用部品のカスタム生産や限定生産などが可能になります。
技術資料では、設計ガイドラインや詳細なワークフロー、成形プロセスの条件、3Dプリント製の成形型を実際に熱成形プロセスで使用した活用事例などをご紹介しています。以下からダウンロードしてご覧ください。