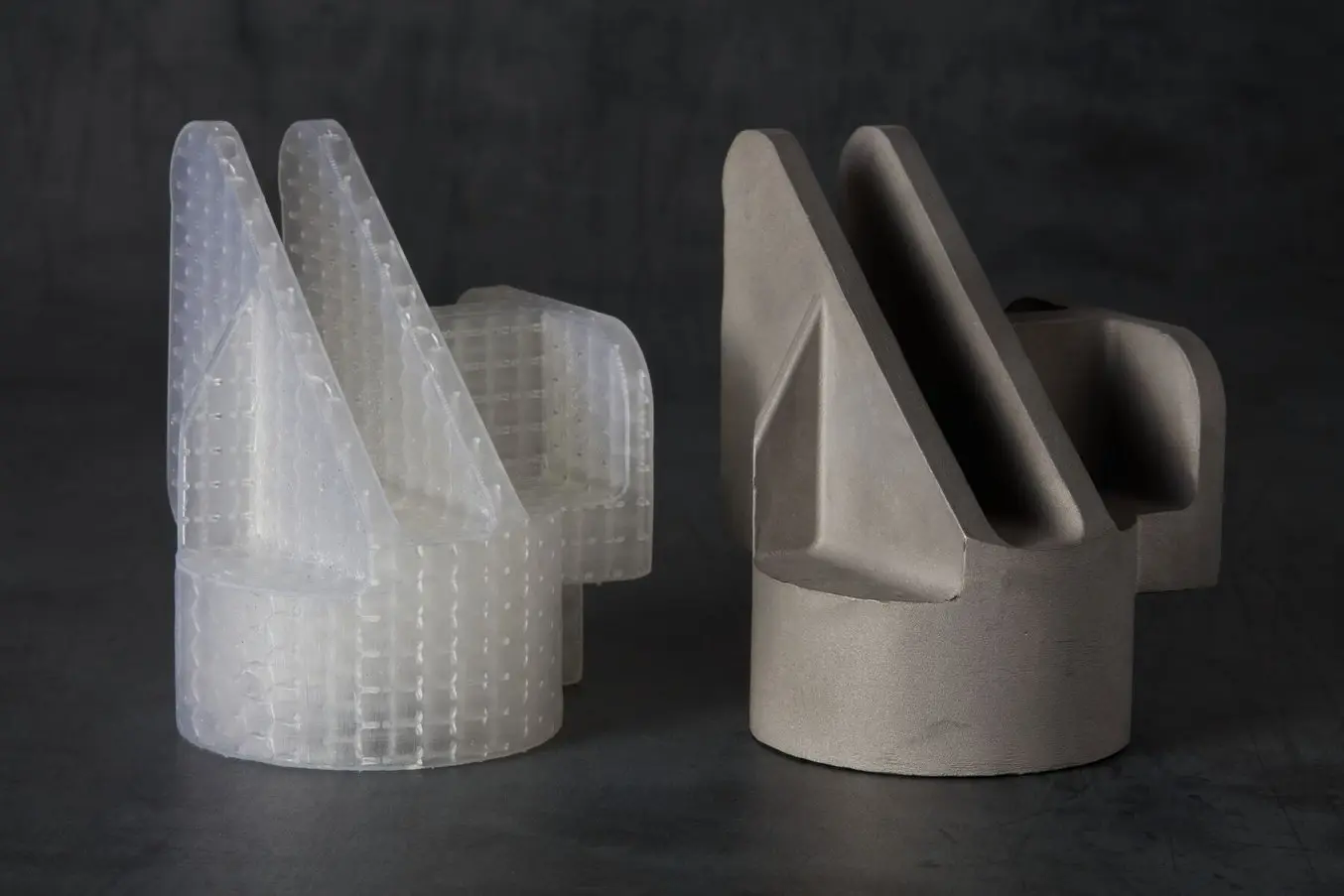
Clear Castレジンで3Dプリントしたインベストメント鋳造用の原型。
金属鋳造は長い歴史を持つ金属加工技術で、溶かした金属を鋳型に流し込み、冷やし固めることで金属部品を製造します。長い歴史のある技術ではあるものの、鋳造は金属部品の製造において今でも尚、最も広く採用される加工技術のひとつでもあります。
本記事では、金属鋳造の概要と最も一般的な鋳造工程、そして3Dプリントなどの最新のデジタルツールを従来の鋳造作業に取り入れることでメーカーはどのようなメリットが得られるのかを詳しく解説します。
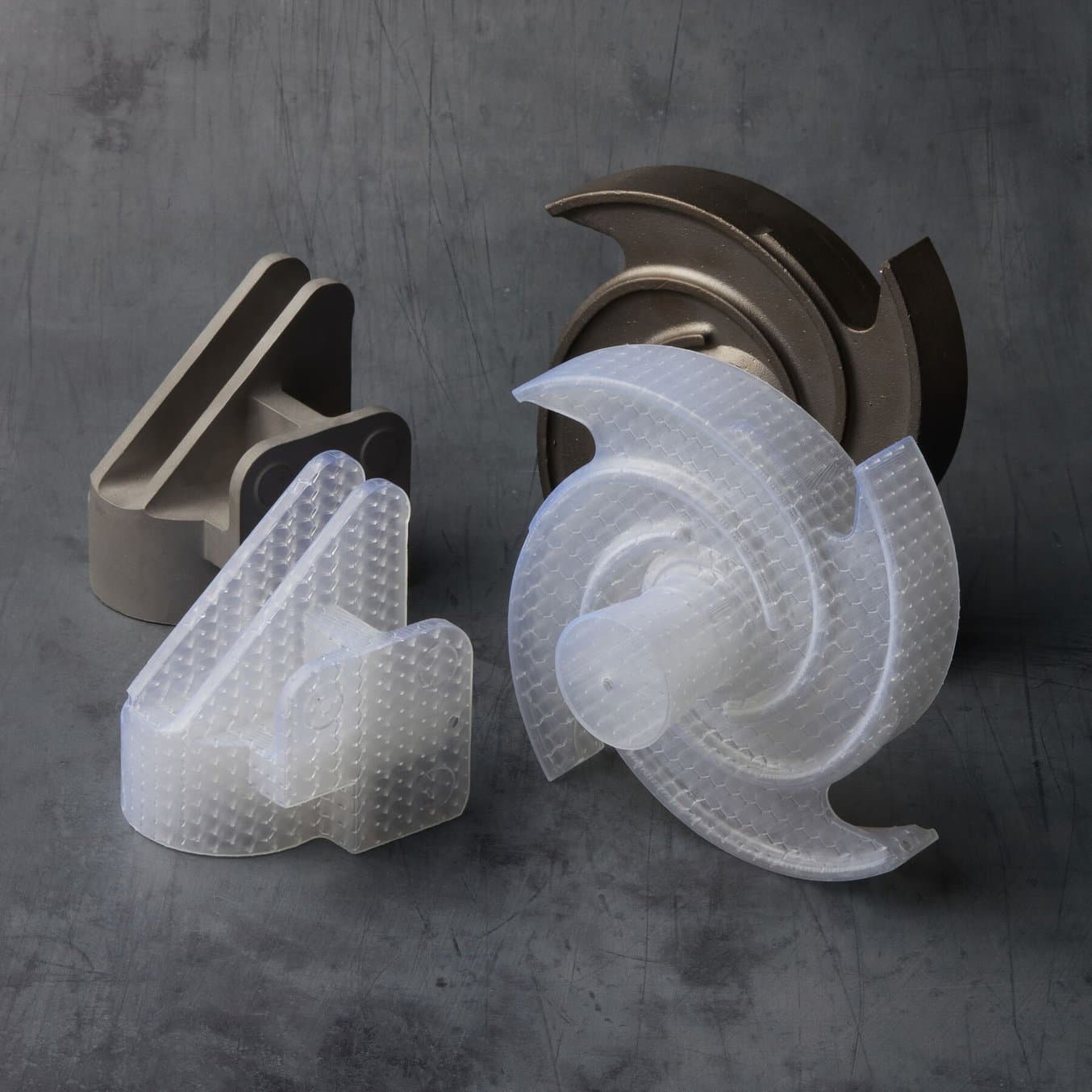
高精度・高効率な鋳造を実現 3Dプリントを活用した金属鋳造
本ウェビナーでは、実績ある複数の鋳物工場が、Formlabsの3Dプリンタで造形した3Dプリント製の原型を使って金属部品の鋳造に成功した方法を解説します。FormlabsのClear CastレジンやMaterialise Magicsのラティス構造生成ソフトウェアを従来の鋳造方法に組み入れることで、金属部品の品質を向上させながら、コストや製作期間を削減した方法をご覧いただけます。
金属鋳造の概要
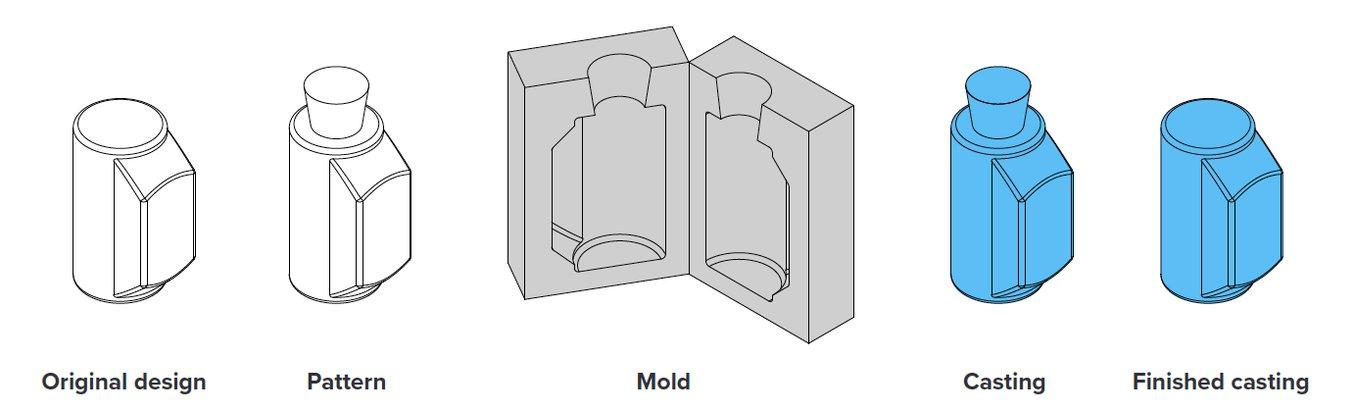
設計から最終的な鋳造まで、鋳造工程をステップごとに表した概要図。
鋳造技術の誕生以来、その方法は常に進化し変化を遂げてきましたが、核となる技術は変わりません。ここでは、鋳造の一般的な工程をステップごとにご紹介します。
ステップ1:原型製作
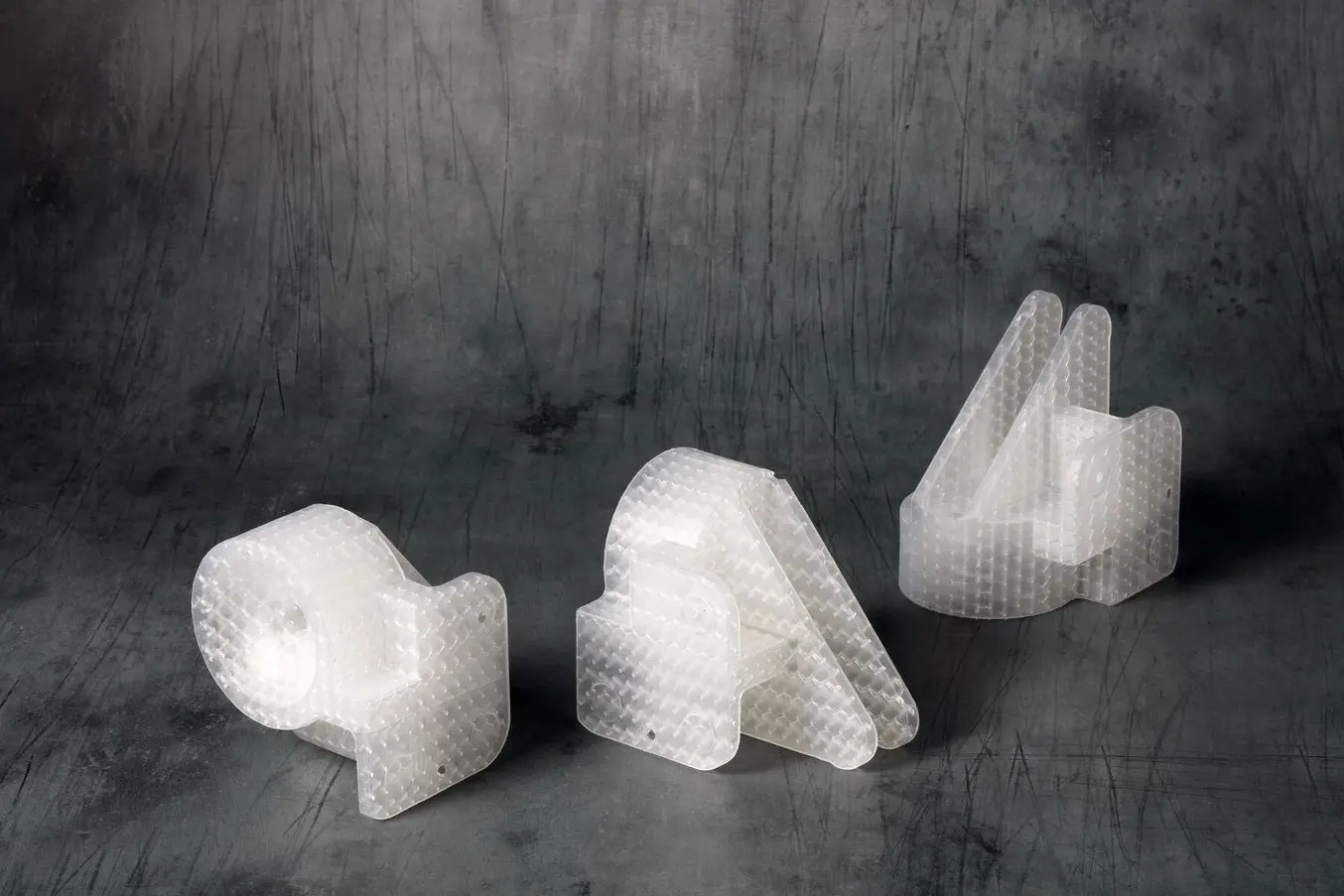
Clear Castレジンで3Dプリントしたインベストメント鋳造用の原型。
まず、実際の鋳造工程に入る前に、メーカーは希望する製品の形を再現するための原型を作る必要があります。鋳造で使用する鋳型の設計には、この原型が欠かせません。原型は正確な形状と寸法で金属の完成品を作るためのもので、従来の方法では原型は木材、発泡スチロール、プラスチック、またはワックス(蝋)で作るのが一般的でした。現在では、3Dプリンタを使った原型製作も一般的になってきており、設計者はデジタルのCADソフトウェアで正確な原型を直接製作することができるようになっています。
原型は、製品の完全なレプリカではありません。溶かした金属(溶湯)を一定の速度で流し込むための湯口や、ガスを逃がすための通気穴など、鋳造工程に必要な要素が付加されています。さらに、冷却中に発生する収縮を考慮し、原型は実際に製作する部品よりも大きめに作るのが一般的です。
鋳造品が中空構造を持つ場合、メーカーは内部形状を正確に再現するために砂や金属で中子も製作し、鋳型に入れて鋳造した後、この中子を取り出します。
ステップ2:鋳型製作
次のステップは鋳型の製作です。鋳型には再利用できるもの(非消耗品)と再利用できないもの(消耗品)があります。再利用できない鋳型は通常、砂、石膏、ワックス、または3Dプリント製で、鋳造工程で破壊されます。再利用できる鋳型は金属やその他耐久性のある材料で作られており、鋳造工程で繰り返し使用することができます。
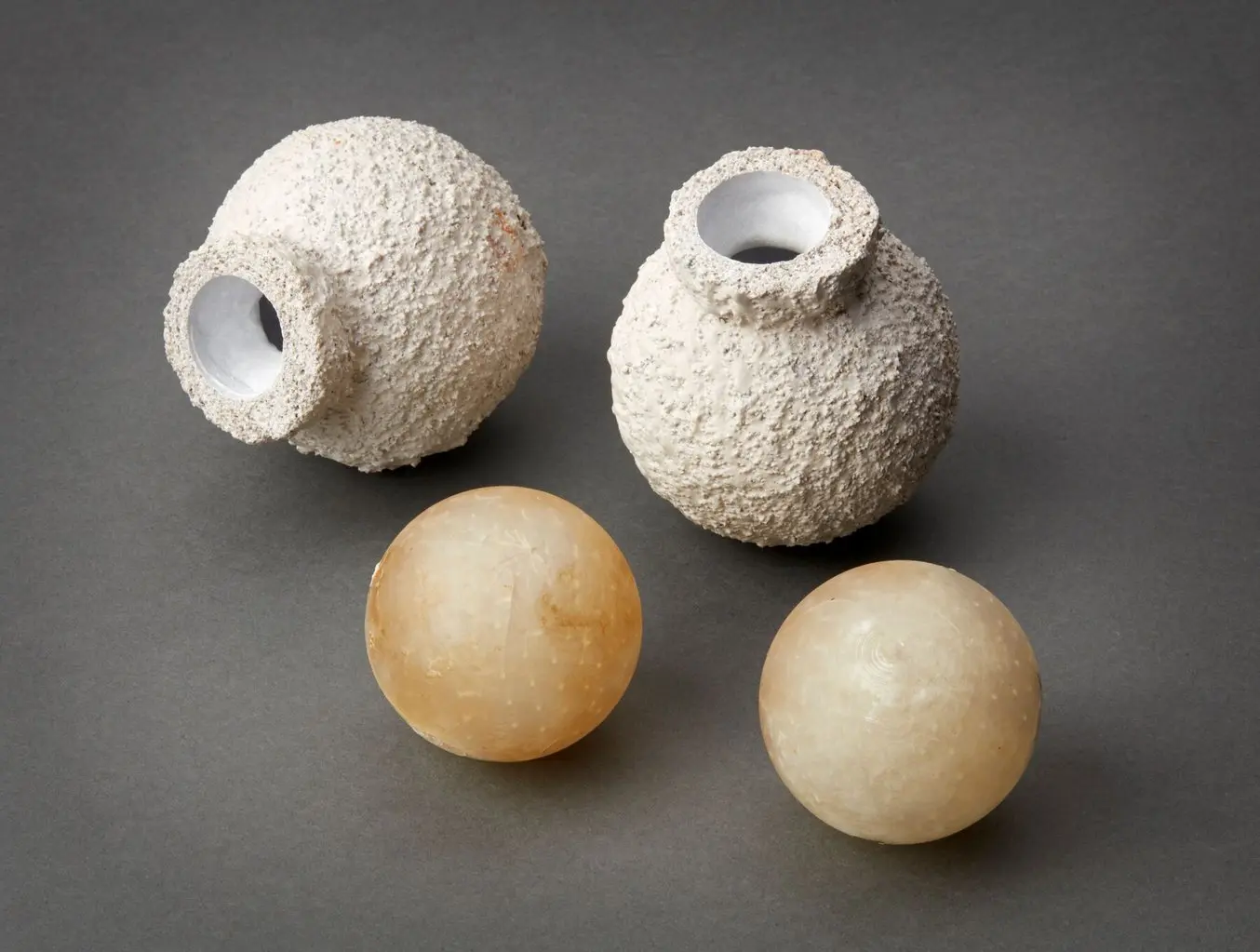
焼成後のセラミックシェル鋳型と
Clearレジンで3Dプリントした原型。ステップ3:溶かした金属の流し込み
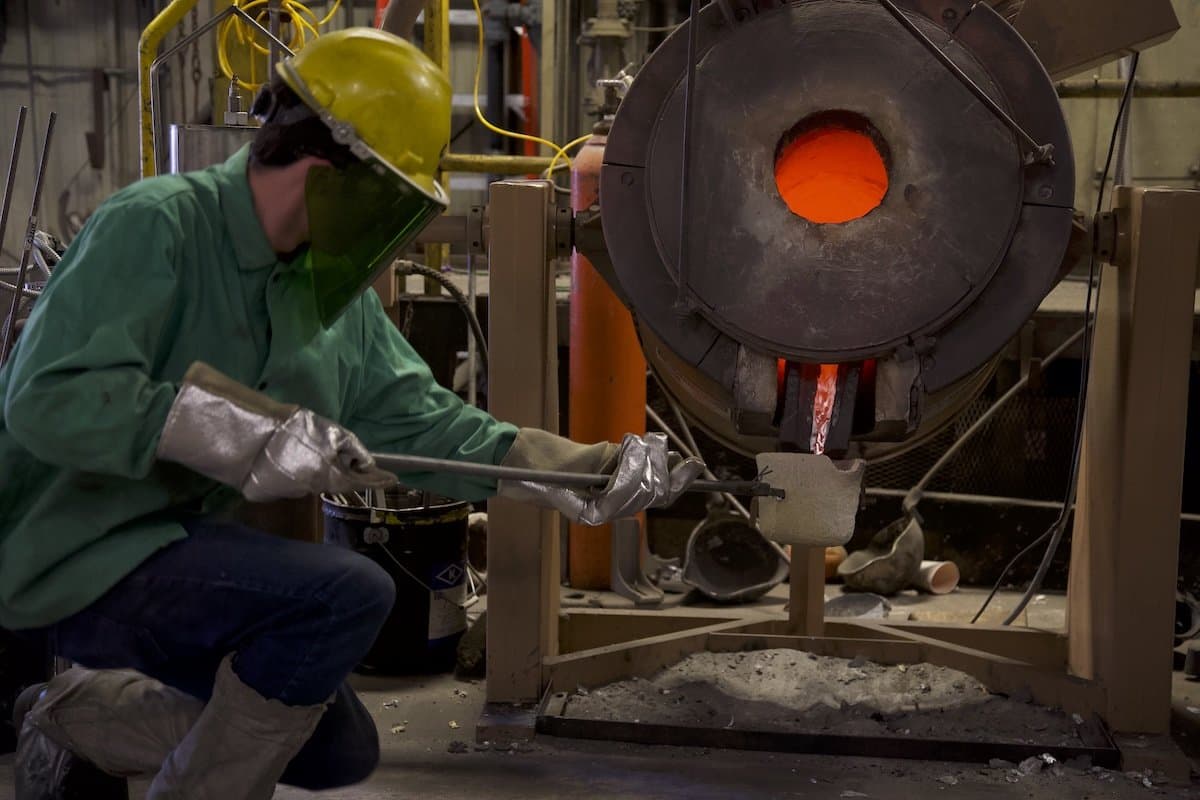
溶かしたアルミニウムを空洞部分に流し込みます。
このステップでは、炉で金属を加熱して溶かします。鋳造で使われる金属で最も一般的なのは、鉄、アルミニウム、アルミニウム合金、鋼鉄、銅、亜鉛ですが、金や銀のような貴金属も使用が可能で、メーカーは用途に応じて様々な材料を選ぶことができます。金属が溶けたら鋳型のキャビティに流し込み、冷やし固めます。
ステップ4:鋳型の取り外しと洗浄
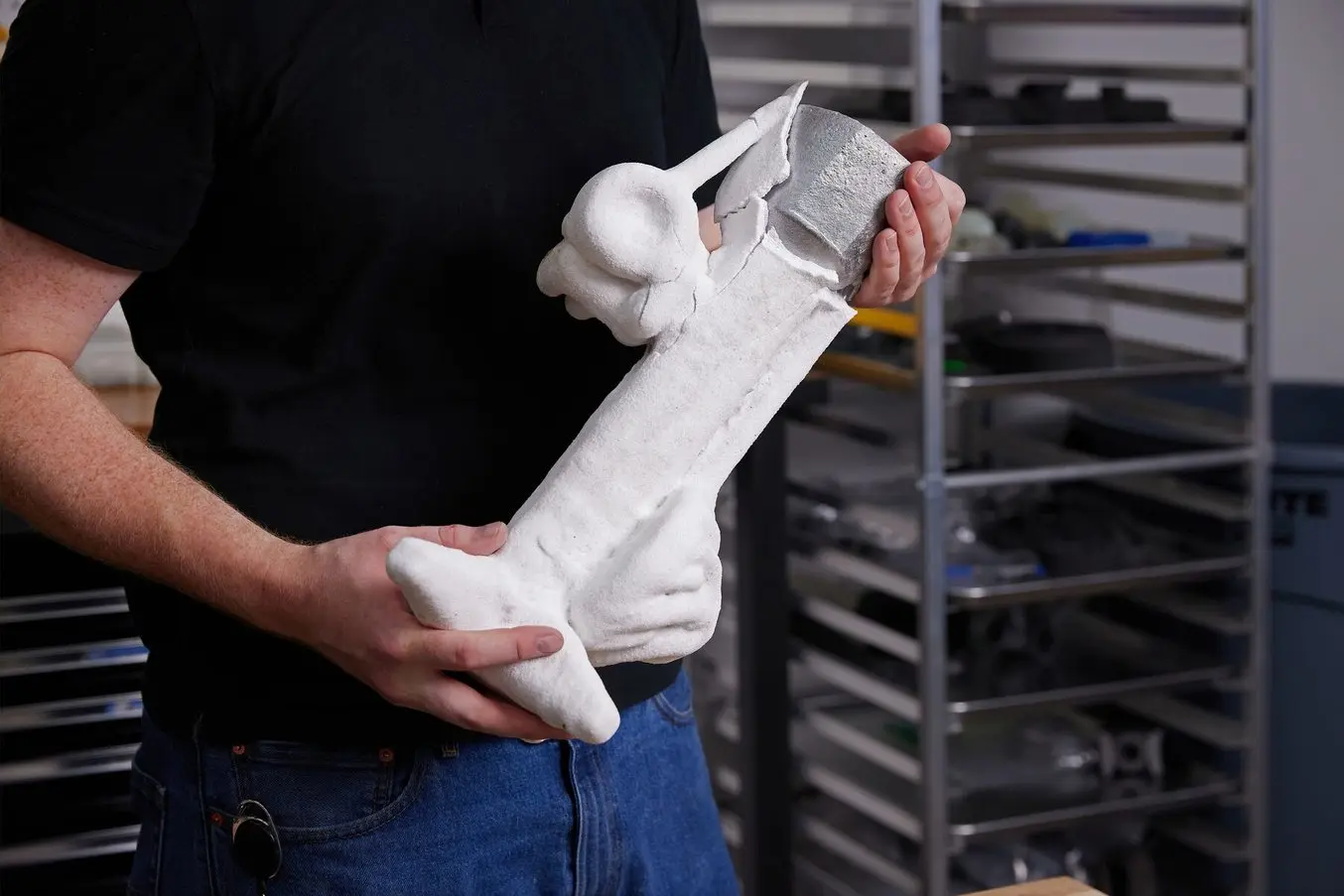
鋳造品の表面処理をしている様子。
金属が冷えて固まったら、鋳型から取り出します。鋳型の種類にもよりますが、振動を与えて鋳造品を鋳型から取り出す型ばらし、インベストメント材の洗い流し、エジェクタピンを使った押し出しなどがあります。次に、通気穴、堰、湯口などの余分な部分を鋳造品から取り除きます。最後に、やすりがけ、研磨、切削、サンドブラスト処理を施し、最終的な形状や表面の仕上げを行います。
鋳造工程の種類
すべての鋳造技術で核となる工程は同じですが、用途に応じて様々な方法があります。最も一般的な方法は、ダイキャスト、インベストメント鋳造、砂型鋳造などです。
ダイカスト
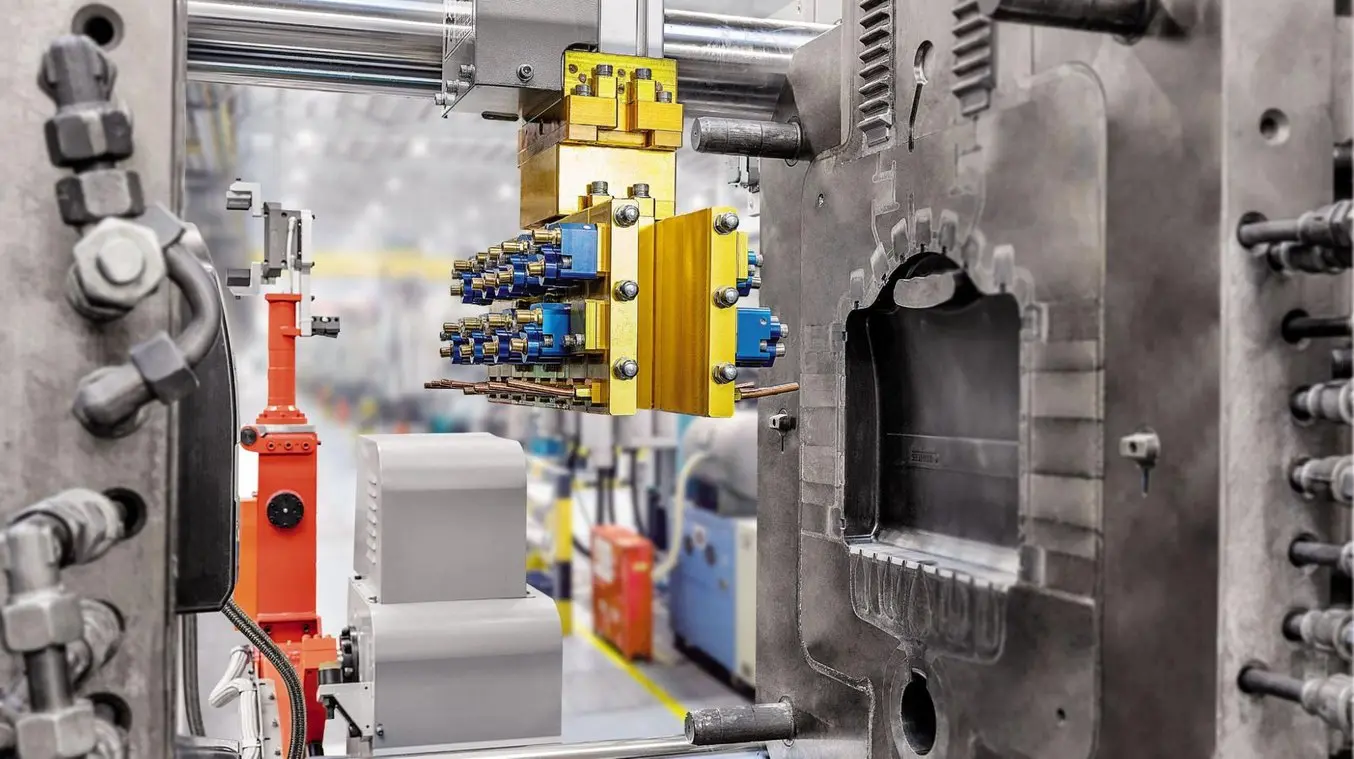
ダイキャストでは、鋼鉄製の金型に圧力をかけて金属を流していく。(写真提供:buhlergroup.com)
ダイキャストは、溶かした金属を鋼鉄製金型のキャビティに高圧で流し込み、金属部品を高速で製造できる鋳造手法です。この手法ではダイキャスト金型もしくは再利用可能な金型の中間部を機械で固定し、ノズルから押し出される金属を高圧で金型に注入していきます。金属が冷えると金型が開き、エジェクタピンで鋳造品を押し出します。
ダイキャスト工程で最も一般的なのは、ホットチャンバーダイキャストとコールドチャンバーダイキャストの2つです。各工程の詳細は異なるものの、全体としてはダイキャスト工程に共通する特徴がいくつかあります。
ホットチャンバーダイカスト
ホットチャンバーダイキャストは、2つの手法の中で最も一般的な方法です。ホットチャンバーダイキャストマシンには、金属を加熱するための炉が組み込まれています。金属が溶湯状態になると、円筒形のチャンバーが溶湯の中に下りてきます。射出部のグースネックの形状により、チャンバーがすばやく充填され、空気圧やピストンで金属材料を金型に注入することができます。
射出部を溶湯の中に浸して注入を行うため、迅速かつ合理的な鋳造工程が実現できます。しかし、チャンバーが溶湯の熱を直接受けるため、ホットチャンバーダイキャストでは射出部の腐食がリスクとなり、融点の高い金属には不向きです。鉛、マグネシウム、亜鉛、銅のように融点が低く流動性の高い貴金属に適した製造手法です。
コールドチャンバーダイキャスト
ホットチャンバーダイキャストとは対照的に、コールドチャンバーダイキャストでは、腐食を避けるために低速で作業を行います。この手法では、鋳造作業者が射出部に溶湯を充填する必要があります。その後、ピストンにより金属を金型に注入します。
この工程では、ホットチャンバーダイキャストで懸念となる腐食の可能性が減ります。アルミニウムやアルミ合金のような融点の高い金属に最適な製造手法です。
ダイキャストの利点
ダイキャストでは迅速かつ非常に精細な鋳造品を製造できます。複雑な製品の大量生産に適しており、滑らかな表面品質を実現しながら丈夫な部品を製造することもできます。この大量生産能力により、自動車産業や航空宇宙産業では欠かせない鋳造手法となっています。
ダイキャストの欠点
ダイキャスト用の金型と機器が高額であるため、小ロットの量産では費用対効果が良いとは言えません。また、使用する金属の鍛造性によっては、複雑な製品を製造できるかどうかが左右される可能性があります。
インベストメント鋳造
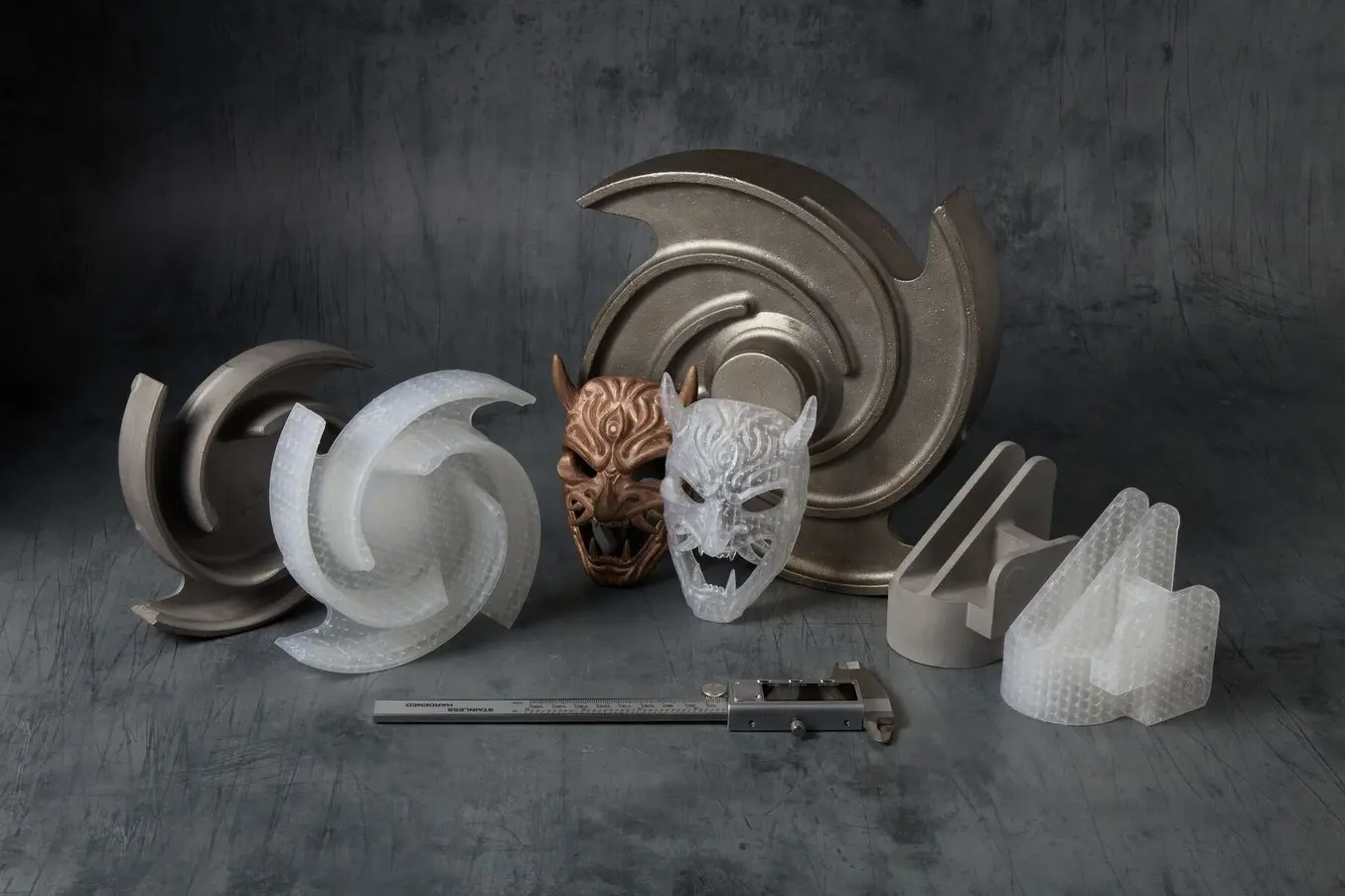
FormlabsのSLA光造形方式3DプリンタにてClear Castレジンで3Dプリントした原型を使った鋳造品。
ロストワックス鋳造としても知られるインベストメント鋳造は、ワックス、スラリー、鋳型を使用して複雑な鋳造品を製造できます。インベストメント鋳造は最も古い鋳造技術の1つですが、繊細な形状をした精密な金属部品を製造できる点が今でも人気の理由です。
この製法は今でもジュエリーや歯科、アートの分野を中心に広く活用されています。工業分野ではインベストメント製法と呼ばれ、エンジニアリングや製造業で精密な金属製品を作る際に使われます。
インベストメント鋳造の原型は通常、ワックスや3Dプリント製のポリマーで製作します。原型はツリーのような構造で、シリカのスラリーに浸すかフラスコに入れるかして液体のインベストメント石膏で囲みます。インベストメント材料が乾いたら、鋳型を上下逆さまの状態で釜に入れます。こうすることで原型が溶け、内側に原型と同形状の空洞ができあがります。金属を溶かし、重力や真空圧を利用して金属を空洞の中に引き込みます。鋳造品に、やすりがけ、研磨、切削、ブラスト処理を施し、最終的な形状や表面の仕上げを行います。
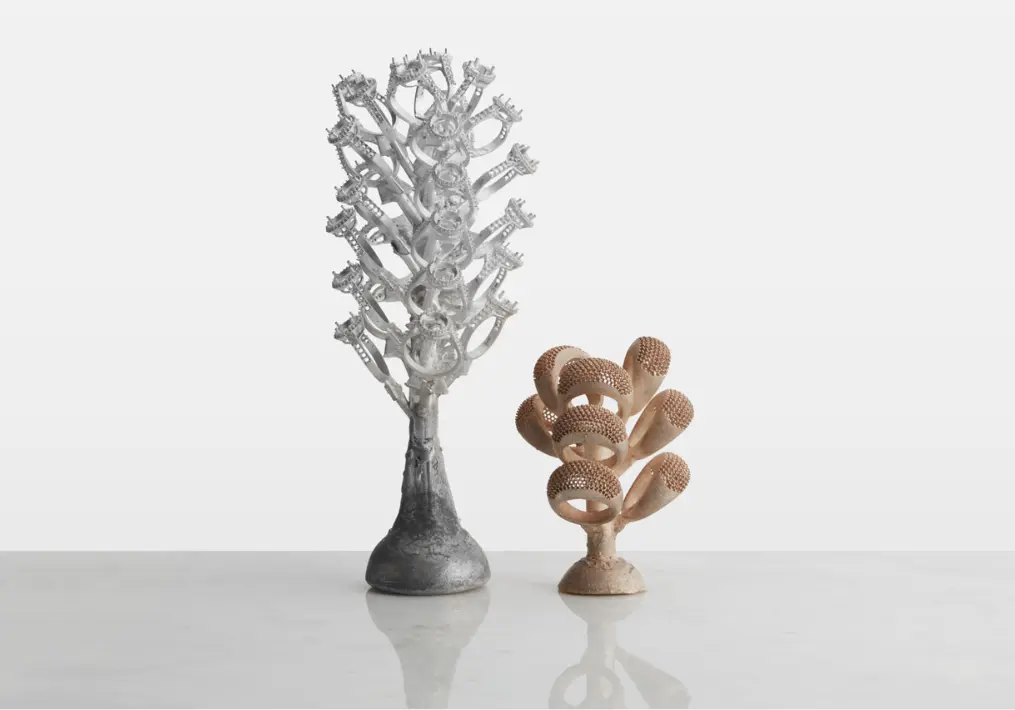
鋳造したリングがついた状態の鋳造ツリー。
Clear Castレジン、Castable Waxレジン、Castable Wax 40レジン、True Castレジンはすべて、インベストメント鋳造用の3Dプリントパーツ製作にご使用いただけます。製作するパーツによって向いている材料が異なり、Castable Waxレジンは軽量から中重量のジュエリーに、True Castレジンは中重量のジュエリーや厚さ5mmまでのエンジニアリング用部品に、Clear Castレジンは厚さ3mm以上の部品製作に最適です。
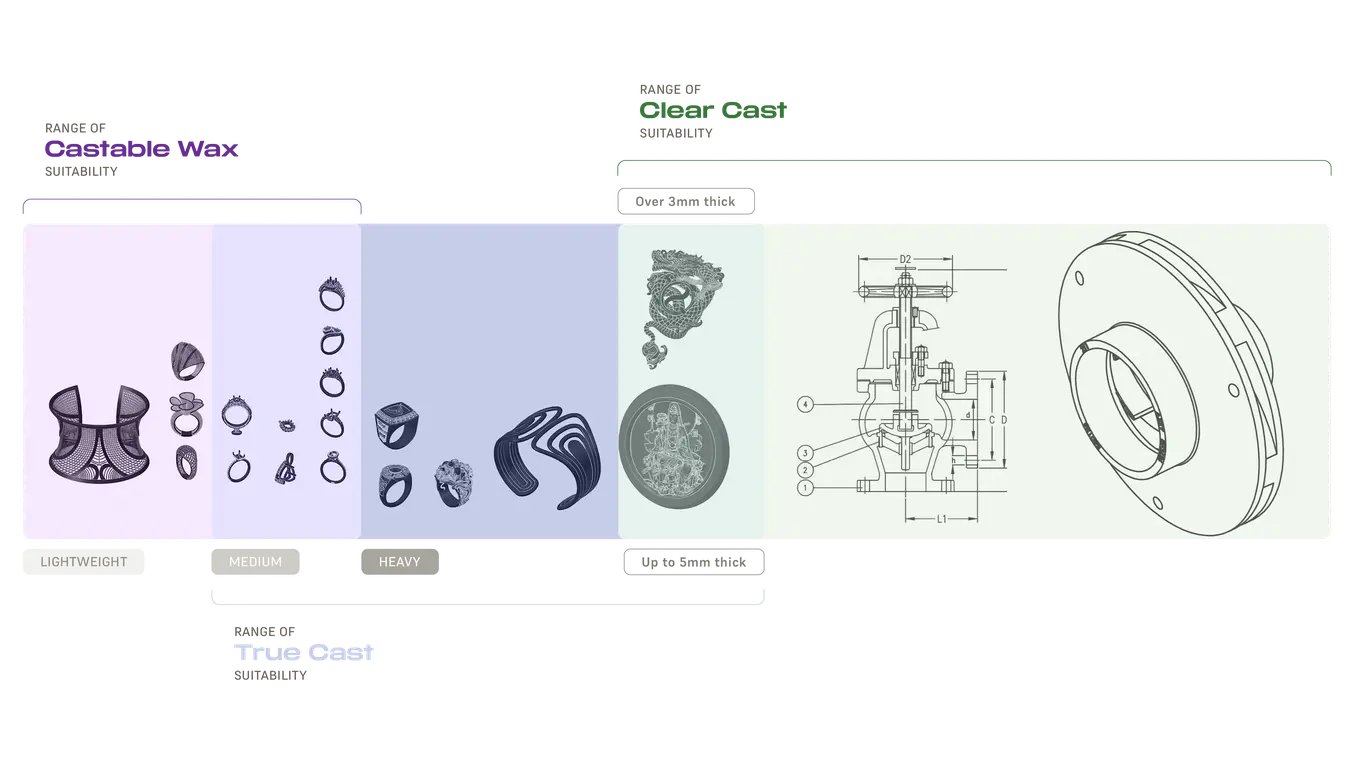
インベストメント鋳造の利点
インベストメント鋳造は汎用性の高い技術です。他の鋳造方法では実現が難しい、または不可能な複雑な形状でも、ほぼすべての金属から正確で再現性の高い鋳造品を製造することができます。また、出来上がった鋳造品の表面品質が高いため必要な表面処理や機械加工が最小限に抑えられ、公差も低いことが特徴です。
こういった特徴により、インベストメント鋳造品は自動車、航空宇宙、産業用製品、医療器具、歯科インプラントなどの複雑な形状が求められる製品、そして高級ジュエリーや美術品の鋳造に最適です。
インベストメント鋳造の欠点
その一方で、インベストメント鋳造は複雑で手間のかかる工程でもあります。鋳型を作るには特殊な設備と高価な難溶性材料や結合剤、そして多くの手作業が求められます。中子を必要とする鋳造品の製造は難しく、小さな部品の鋳造に向いている手法です。
砂型鋳造
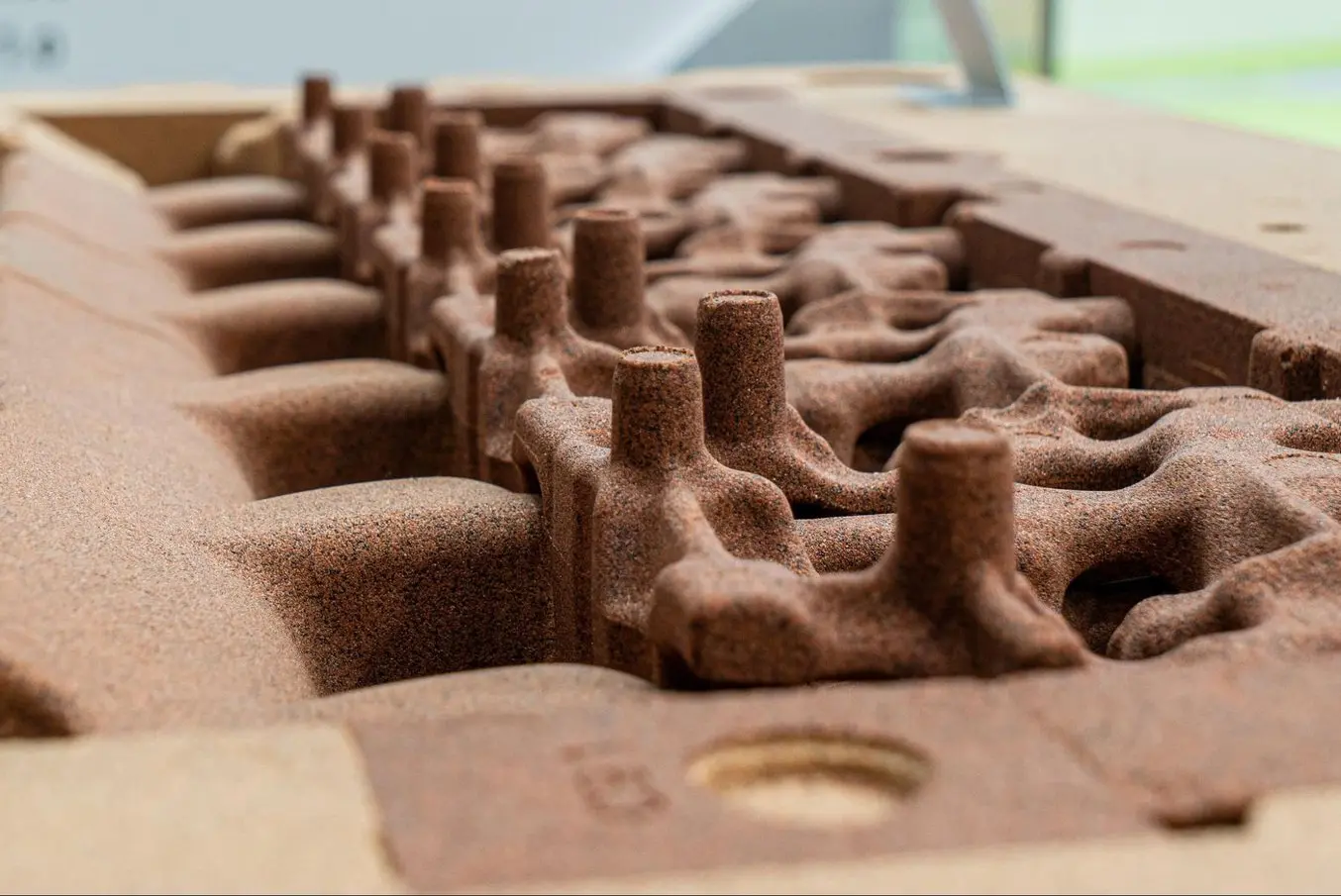
砂型鋳造の鋳型の半分。
砂型鋳造は、3000年前に初めて使用が始まって以来、現在まで最も広く使用されてきた鋳造方法です。この手法により、メーカーは機械加工に頼らず鋳造することができます。
砂型鋳造では、まず原型、または鋳造品のレプリカを作成します。原型の製作には、木材やプラスチックが使われるのが一般的です。原型は収縮を考慮して大きめに製作します。片面に特徴的な形状を持つ部品の場合、上の画像のように開いた形の鋳型が必要になります。複雑な形状を持つ面が複数ある部品の場合、原型を2つの鋳造ボックスに分け、中にキャビティのある密閉型の鋳型を製作します。上半分をコープ、下半分をドラッグと呼びます。
原型を作成したら、原型の周りに隙間なく砂を敷き詰めていきます。次に、溶湯が鋳型のキャビティ内をスムーズに流れるように湯道と堰を追加します。原型を取り除いた後、砂型の中央をクランプで固定します。金属が溶けて溶湯状態になったら、型に流し込んで冷やし、冷めた後は振動や高圧水を使って砂型を取り除きます。最後に、鋳造品から湯道や堰を取り除き、最終的な形状に仕上げていきます。
砂型鋳造の利点
砂型鋳造は機械の制約を受けない適応性の高い製造手法で、事実上、あらゆるサイズの複雑な鋳造品を製造できます。砂は安価で豊富に手に入るため設備コストも低く、様々な改良を加えることが可能です。大型の鋳造品を作りたい場合は、砂型鋳造が唯一現実的で経済的な方法と言えるでしょう。製造期間も短く、短納期の生産に適した工程です。
砂型鋳造はこの多用途性を理由に幅広い産業で採用されており、医療機器、自動車部品、電子機器、ガスタンク、エンジンブロックなどの製造が可能です。
砂型鋳造の欠点
砂型鋳造で作った製品は、水密性が低くざらついた質感に仕上がります。また、鋳造工程で発生する収縮と表面品質の粗さによって部品の寸法精度が下がるため、実製品の強度も下がり、より高品質な仕上がりにするためには時間をかけて表面処理を行う必要があります。
最適な鋳造工程の選択
産業用途で最適な鋳造工程を選択するには、いくつかの点を考慮する必要があります。以下の表では、ダイキャスト、インベストメント鋳造、砂型鋳造の3つの製造手法を、使用可能な金属材料の種類、生産量、コスト、製造期間、実現できる形状の複雑さ、一般的に採用されている業界などの観点から比較します。
ダイカスト | インベストメント鋳造 | 砂型鋳造 | |
---|---|---|---|
使用可能な金属 | アルミニウム、銅、鉛、マグネシウム、亜鉛 | ほとんどの金属 | ほとんどの金属 |
生産量 | 大規模 | 中〜大規模 | ワンオフ品〜中規模 |
製造単価 | 低 | 中〜高 | 中 |
金型製作コスト | 高 | 中 | 低 |
サイクル時間 | 短 | 長 | 中 |
業界 | 自動車、航空宇宙、消費者製品、家具、電動工具 | 自動車、航空宇宙、ジュエリー、医薬品、歯科、アート | 自動車、航空宇宙、産業機器、電子機器、消費者製品 |
3Dプリントを鋳造に活用
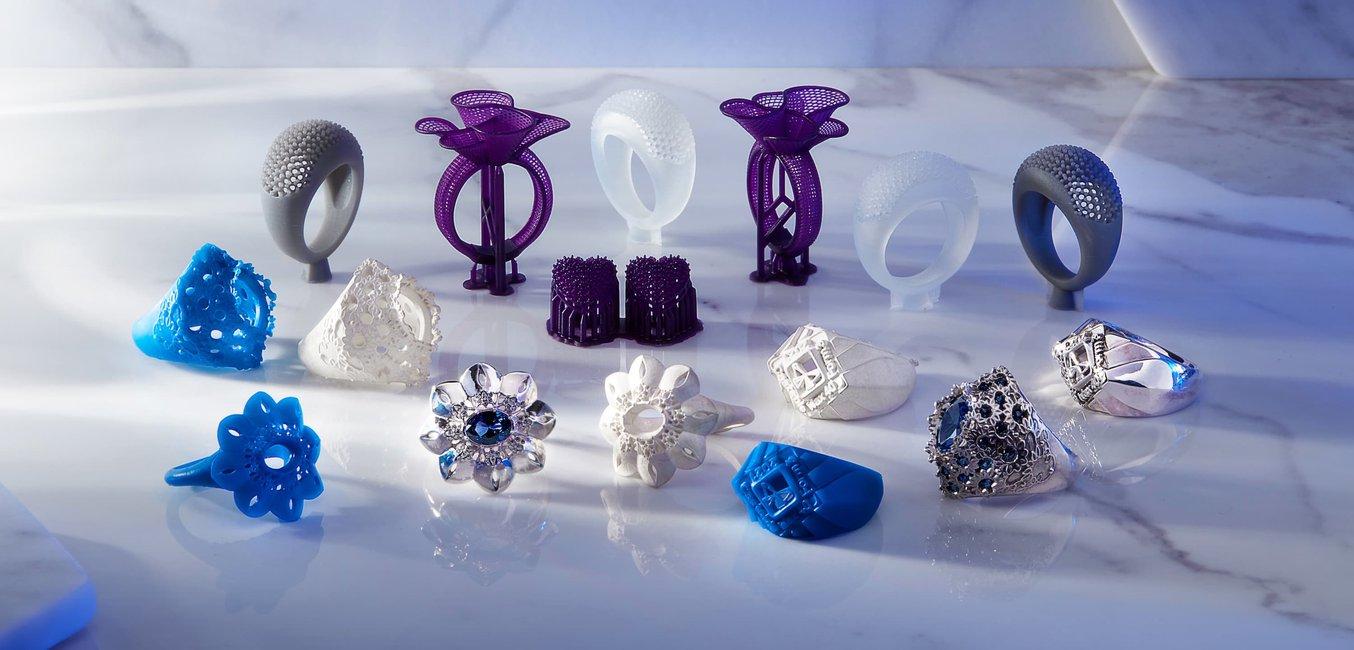
3Dプリント製のリングの原型と実際に貴金属で鋳造したリング。
エンジニア、デザイナー、ジュエラー、ホビイストたちは、間接的なインベストメント鋳造、ダイレクトインベストメント鋳造、ピューター鋳造、砂型鋳造といったの金属鋳造法と3Dプリント製の原型を組み合わせる、あるいは3Dプリント製の鋳型に金属を直接流し込むことで、3Dプリントのスピードと柔軟性を存分に活かすことができます。3Dプリントによるラピッドツーリングで製作された金属鋳造品は、従来の鋳造の数分の一の短時間かつ金属3Dプリントより遥かに安いコストで製造することができます。
SLA光造形方式3Dプリンタには鋳造に対応した高精度材料が豊富にあり、従来型の鋳造方法に比べ、金属部品をデザイン上の制約なく、低コストかつ短時間で製作することができます。
間接インベストメント鋳造
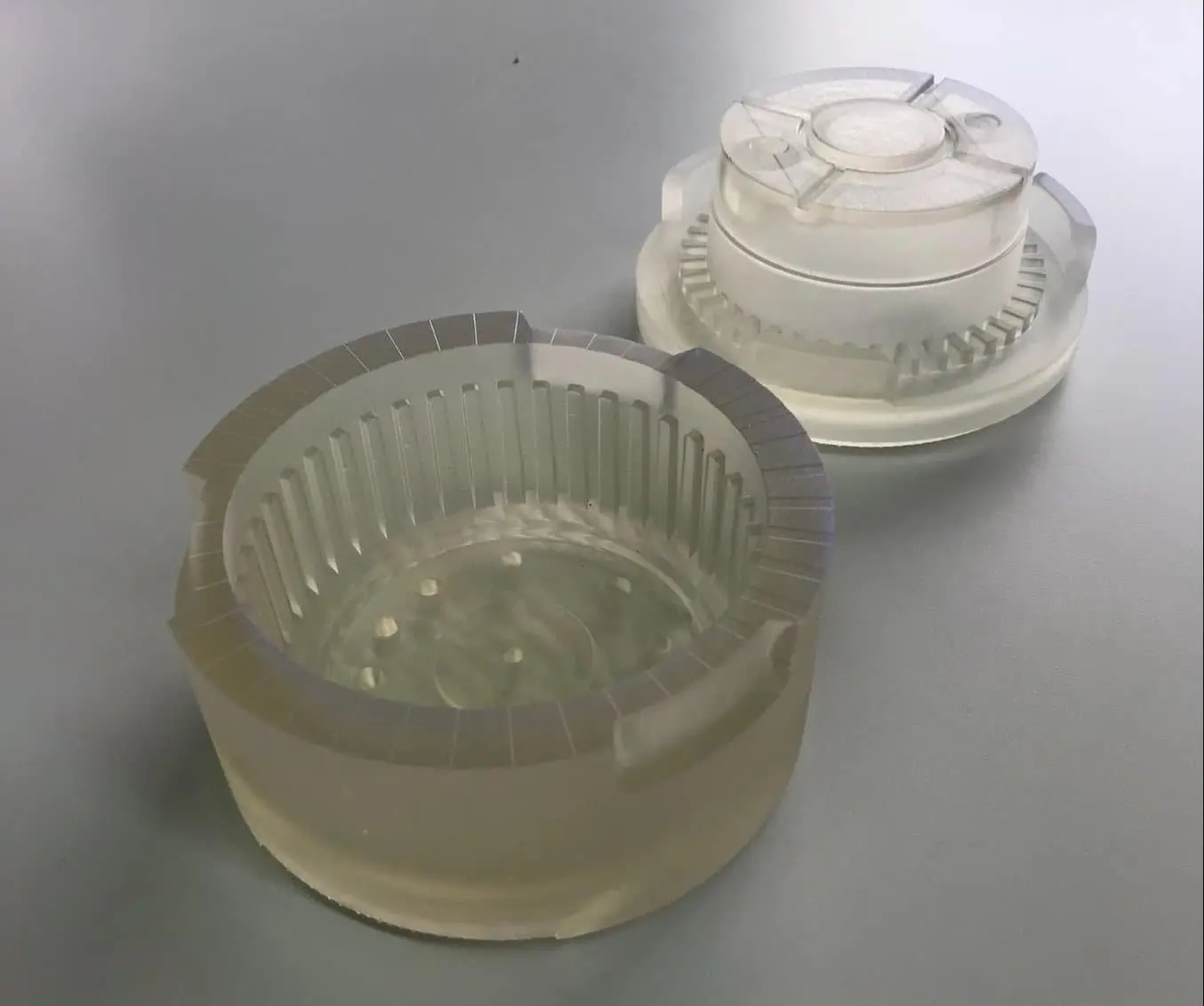
ワックス注入用にClearレジンで製作した金型。
鋳型や金型から原型を作る工程を間接インベストメント鋳造と呼びますが、これは最終的なインベストメント鋳型に加えて、原型を作るための型を製作する必要があるためです。
ワックス用の硬い鋳型(金型と呼ばれることも多いです)は、アルミニウムやスチールを切削して作るのが一般的です。機械加工による鋳型製作は数千ドルにのぼる費用がかかり、最初に鋳型を製作してから実際に鋳造工程で原型を評価できるようになるまで、加工と研磨作業に数週間かかります。
3Dプリントなら、High TempレジンやRigid 10Kレジンといった高い耐熱性をもつレジンを材料として金型を直接3Dプリントすることが可能になります。鋳造品の表面品質を最適化するには、金型の内面をやすりがけもしくは研磨処理することで滑らかな外観にするか、均一でマットな外観がお好みの場合はビーズブラスト処理が可能です。出来上がった鋳造品の寸法精度を保つために、実際の製品より大きめに鋳型を3Dプリントし、収縮分を補います。ワックスと各鋳造工程で発生する正確な収縮率については、サプライヤーの仕様書で確認ができます。
鋳造用の鋳型を3Dプリント製の成形型に置き換えると、メーカーが金型を直接3Dプリントして機能を評価できるため、企画・構想段階から最初のテストまでの時間をわずか数日に短縮できます。
鋳造品は成形性の面で設計規則(アンダーカットがない、抜き勾配がある方が経済的、など)を満たしていなければなりませんが、組立治具を使用して複数の部品を1つに組み合わせることで、複雑な原型も作ることができます。
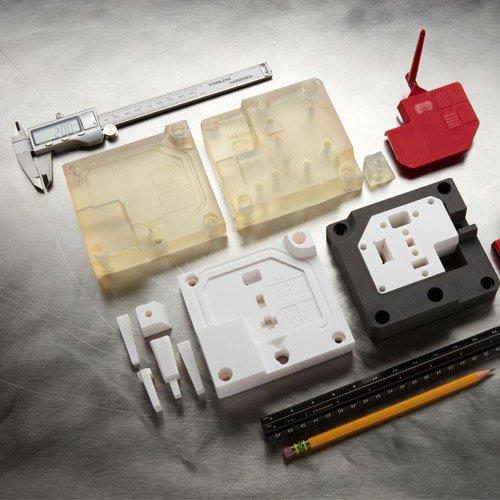
3Dプリントで成形型を製作し、試作品製作や量産で活用
本技術資料では、SLA光造形3Dプリンタで成形型を内製する6つの方法をまとめました。ダウンロードいただくと、 射出成形、真空成形、シリコン成形、その他の方法について詳細をご覧いただけます。
ダイレクトインベストメント鋳造
ダイレクトインベストメント鋳造とは、原型を製作してからそのまま造形材で原型を囲むところまで移行できる工程のことです。鋳造するには複雑すぎる形状の部品や、広範囲に渡ってアンダーカットやディテールの凝ったテクスチャが広がっているような部品の製造に最適です。通常の手順で行う場合、金型製作に高額なコストがかかります。
従来は、特注品や数個しか製造されないと予想される部品の場合には、ダイレクトインベストメント鋳造で使う原型は手作業で彫るか機械加工で製作していました。しかし3Dプリントを取り入れると、メーカーが原型を直接3Dプリントできるため、他のプロセスでよくあるデザインや時間の制約を受けることがありません。
また、エンジニアが直接原型を製作できるため、工程全体にかかる期間を短縮したり、従来のDFM(Design For Manufacturability/製造容易性設計)による制約下では実現できなかった設計の自由度が得られるようになります。Formlabsは、特に工業用インベストメント鋳造やジュエリー鋳造向けの、ダイレクトインベストメント鋳造に適した鋳造用3Dプリント材料を開発しました。
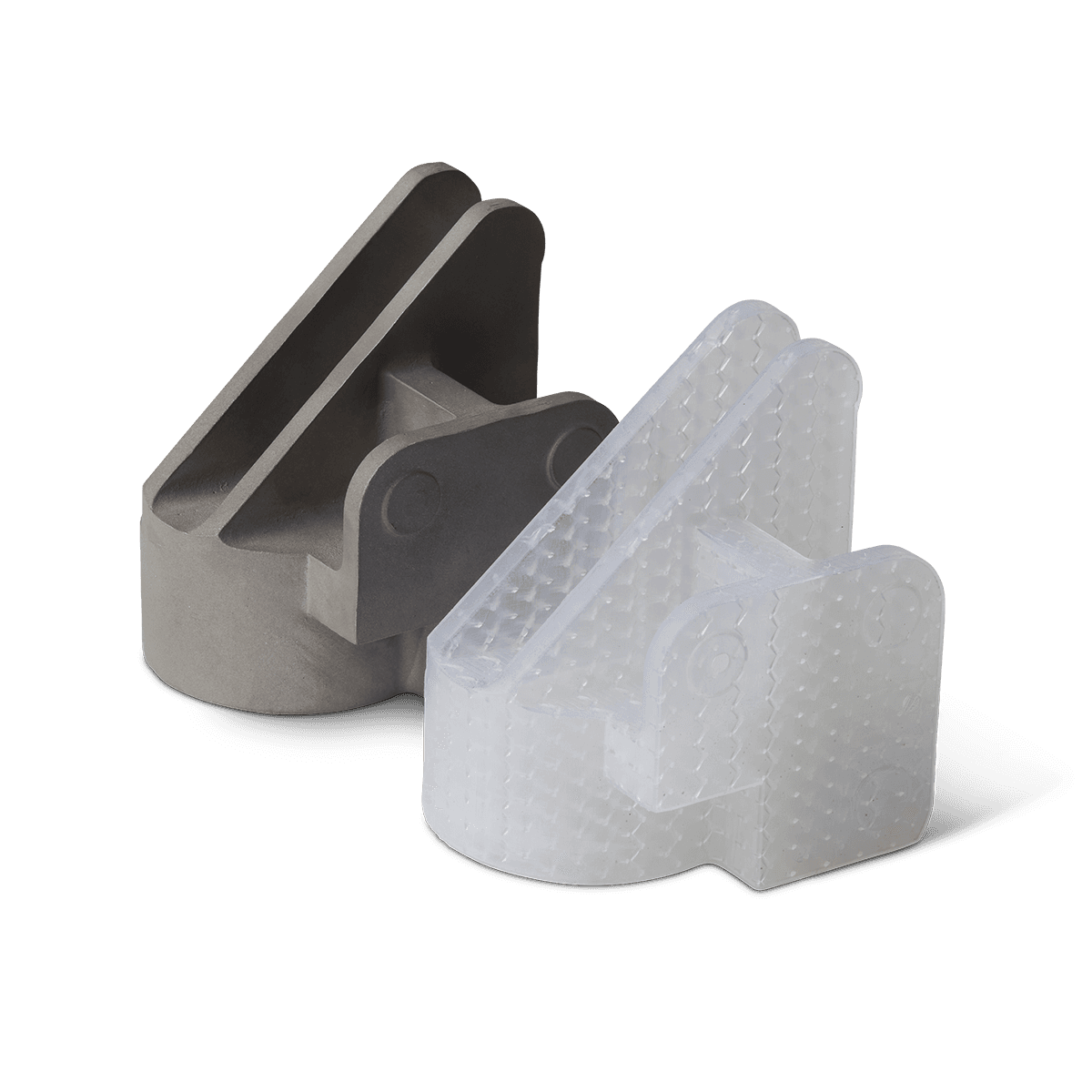
工業品質のインベストメント鋳造を3Dプリント製の原型で Formlabs Clear Castレジンの活用法
本技術資料では、実績ある複数の鋳物工場が、FormlabsのSLA光造形プリンタで造形した3Dプリント製の原型を使って金属部品の鋳造に成功した方法をご紹介します。
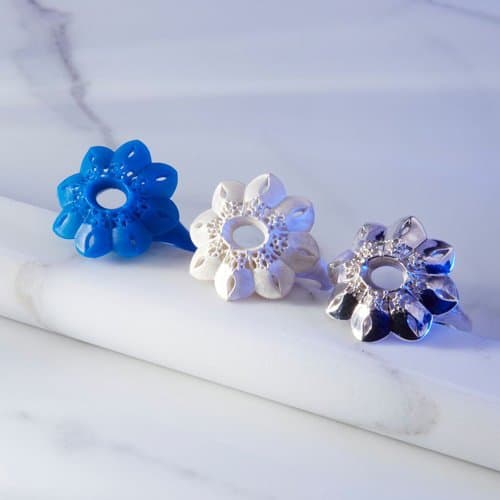
3Dプリント製のジュエリー型の鋳造
鋳造に対応した光硬化性レジンによって、ジュエリーの製作方法が変わりつつあります。本技術資料では、Formlabsの3Dプリンタを使って高級ジュエリーを鋳造する方法を解説します。
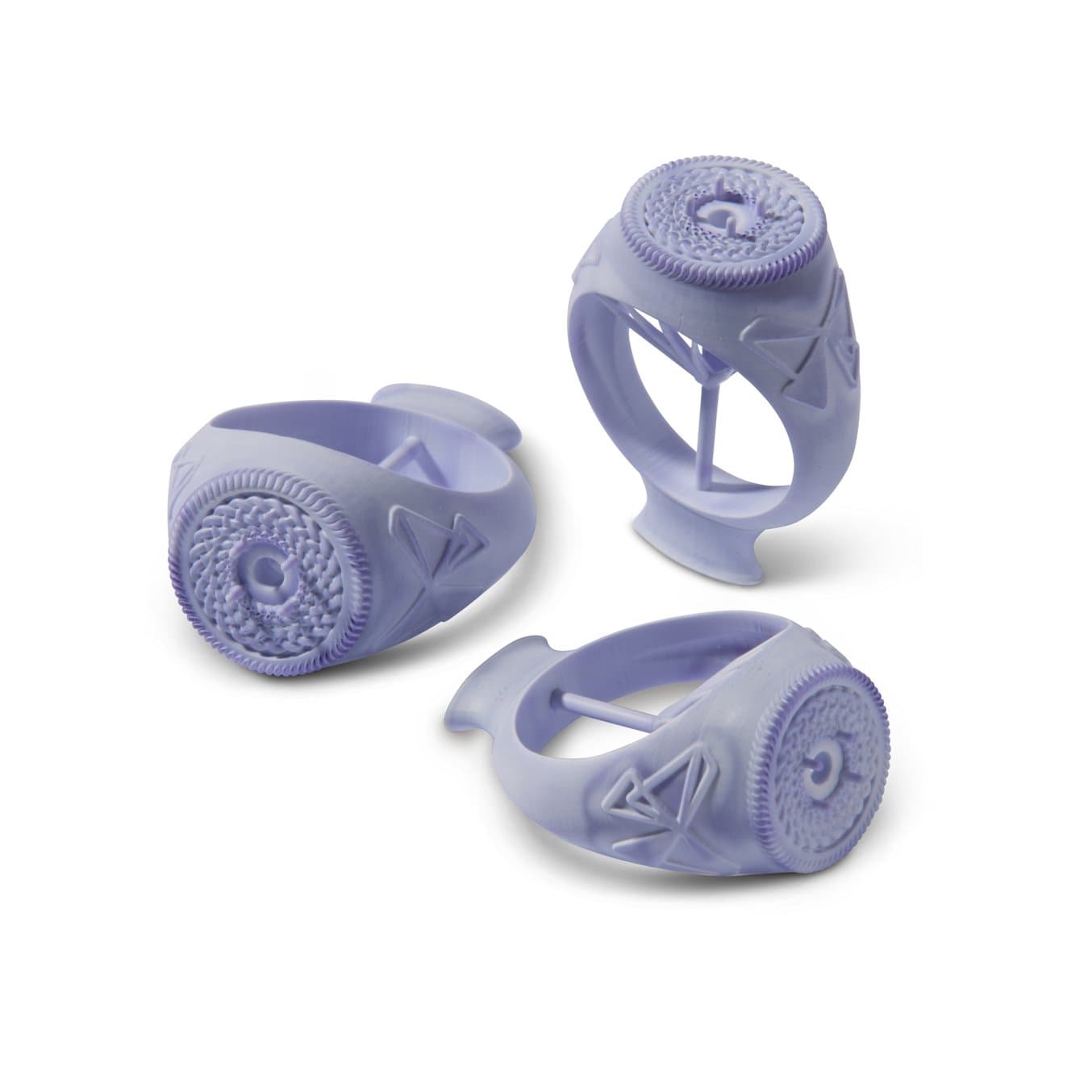
砂型鋳造
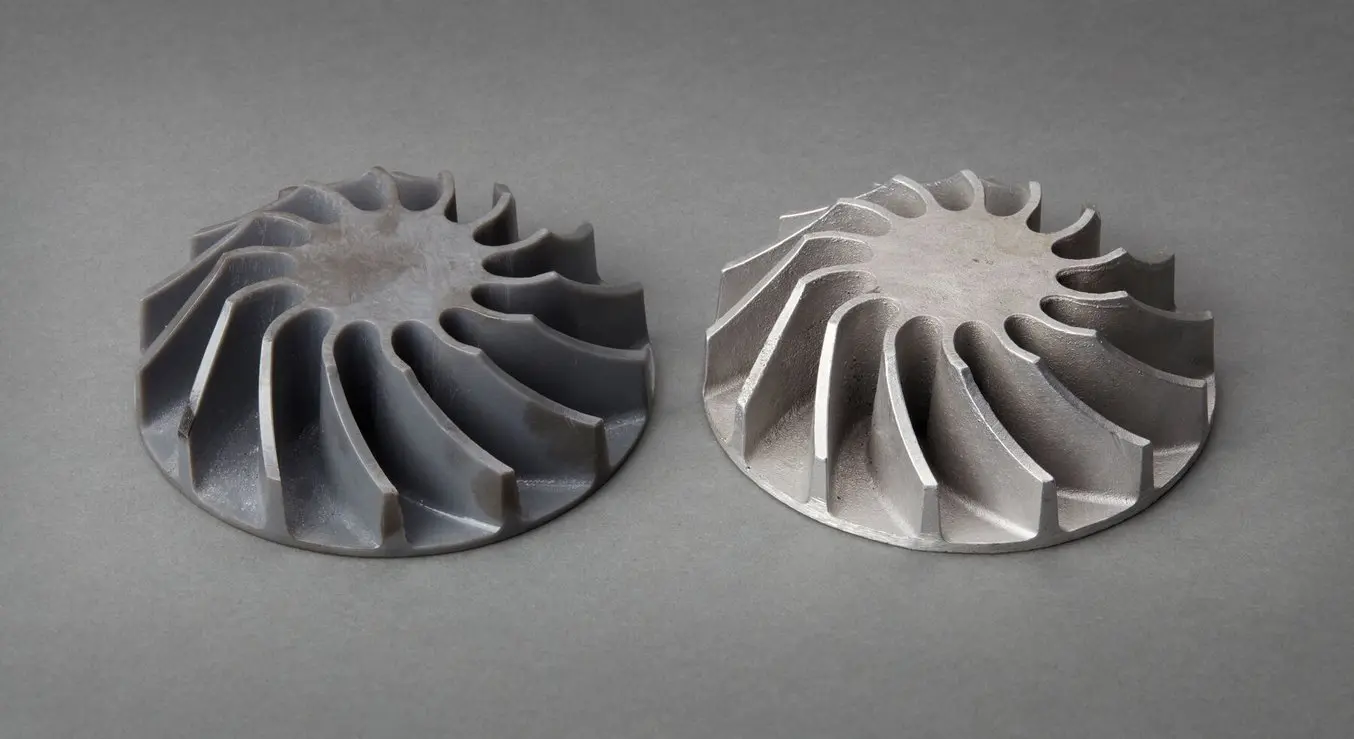
Greyレジンで造形した原型とアルミを砂型で鋳造した完成品。
砂型鋳造の場合も、インベストメント鋳造同様に原型を3Dプリントで製作できます。
木材等の古くから用いられる材料に比べ、3Dプリンタでは非常に複雑な形状が表現でき、デザインからそのまま実際の鋳造が行えます。
ピューター鋳造
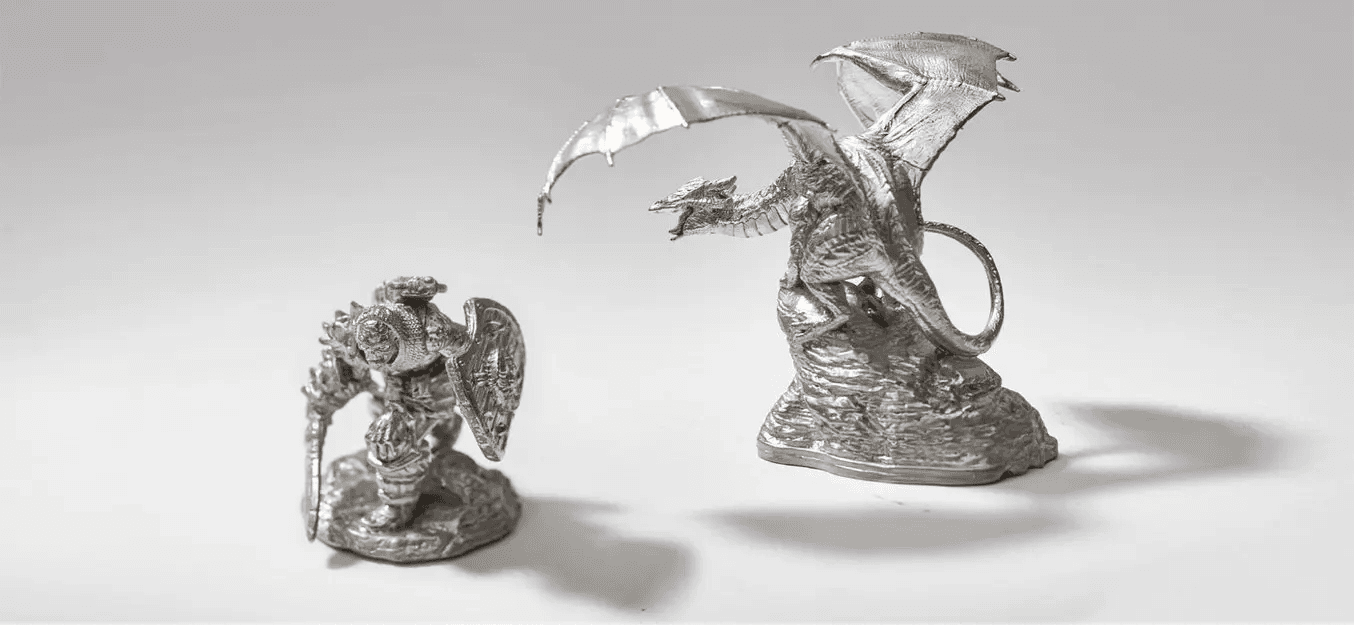
ピューター鋳造と3Dプリントを組み合わせて製作したメタルフィギュア。
ピューターは融点が低く鍛造性の高い金属合金で、繊細な形状のメタルフィギュア、ジュエリー、スケールモデル、骨董品のレプリカなど、装飾用途の金属製オブジェクトを製造できます。
Formlabs SLA造形方式3Dプリンタで使用できるHigh Tempレジンのような高耐熱性材料の誕生により、ピューターで直接鋳造に使用する鋳型を3Dプリントで製作できるようになりました。
鋳型の設計には、犠牲鋳型法と強制剥離型の2つがあります。犠牲鋳型法では、鋳造工程の途中で破壊することを前提としてシェルを作ります。強制剥離型は、鋳型が半面ずつに分かれて再利用できるようになっています。
3Dプリント製の鋳型でピューターを鋳造すると、金属材料を使った3Dプリントに比べてわずかなコストで細部や表面品質を大幅に向上させることができます。ワックス鋳造と比較しても、直接3Dプリントした鋳型の場合は工程に必要なステップや手作業を削減しながら、ディテールを最大限に表現することができます。
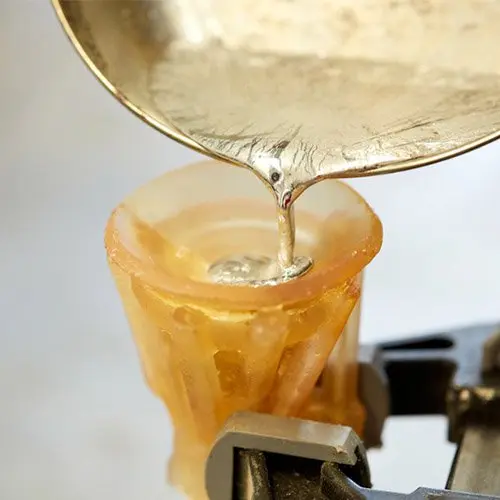
金属、セラミック、シリコン:3Dプリント製の成形型を用いた先進的な作業手順
本ウェビナーでは、3Dプリント製の原型と再利用可能な鋳型や使い捨ての鋳型を使用して、磁器、貴金属、非貴金属、シリコン、生体適合性と柔軟性のある材料で部品を製造する方法をご紹介しています。
鋳造工程に3Dプリントを取り入れるには
設計の自由度を高めつつ、コストと製造期間を削減したいとお考えの場合、鋳造工程への3Dプリントの組み込みが便利です。
断面のある大きな形状や複数の中子が必要な部品など、従来の鋳造法では実現が難しい複雑なデザインも、3Dプリントを鋳造工程に取り入れることで製造が可能になります。例えば鋳物工場やジュエラーの場合、3Dプリント製の原型なしでは製造が不可能だった複雑な特注品も製造できるようになります。
また、3Dプリントを導入することで、複数の機械や受託メーカーに依存する必要がなくなります。デジタルファイル、3Dプリンタ、材料さえあれば、誰でも製造できるようになり、使用する材料はすべて実製品の造形に使用されるため、コストと廃棄物も削減できます。
また、鋳造工程に3Dプリントを組み込むことでコストと製造期間も削減できます。実製品を鋳造するために高価な金型を何週間もかけて製作するより、3Dプリンタの活用でわずか数時間で原型や鋳型を製作できるようになります。
Diversified Metalsmiths, Inc.は、最新技術を既存の金属鋳造工程に取り入れ、コスト削減や製作期間の短縮を実現し、そして需要への反応を高めてきました。Diversifiedでは、Formシリーズ SLA光造形3DプリンタとClear Castレジンを活用し、これまでの鋳造工程を変更したり外注に依存したりすることなく、迅速かつ手頃な価格で鋳造に使う原型を3Dプリントで内製できるようになりました。
「Form 3Lを購入した主な理由は、原型製作にかかるコストの違いです。Form 3Lと関連機器を償却した場合でさえ、現在受けている注文分は収支均衡となりますし、今後の注文にいたっては部品1点あたり200ドル以上も節約できる想定です。アクリル製の原型を作る場合も、SLA光造形でClear Castレジンを使って原型を作る場合も、鋳造前後の工程にほとんど違いがありません」
Diversified Metalsmiths 技術部長、John Farr氏
鋳造工程に適した3Dプリンタ
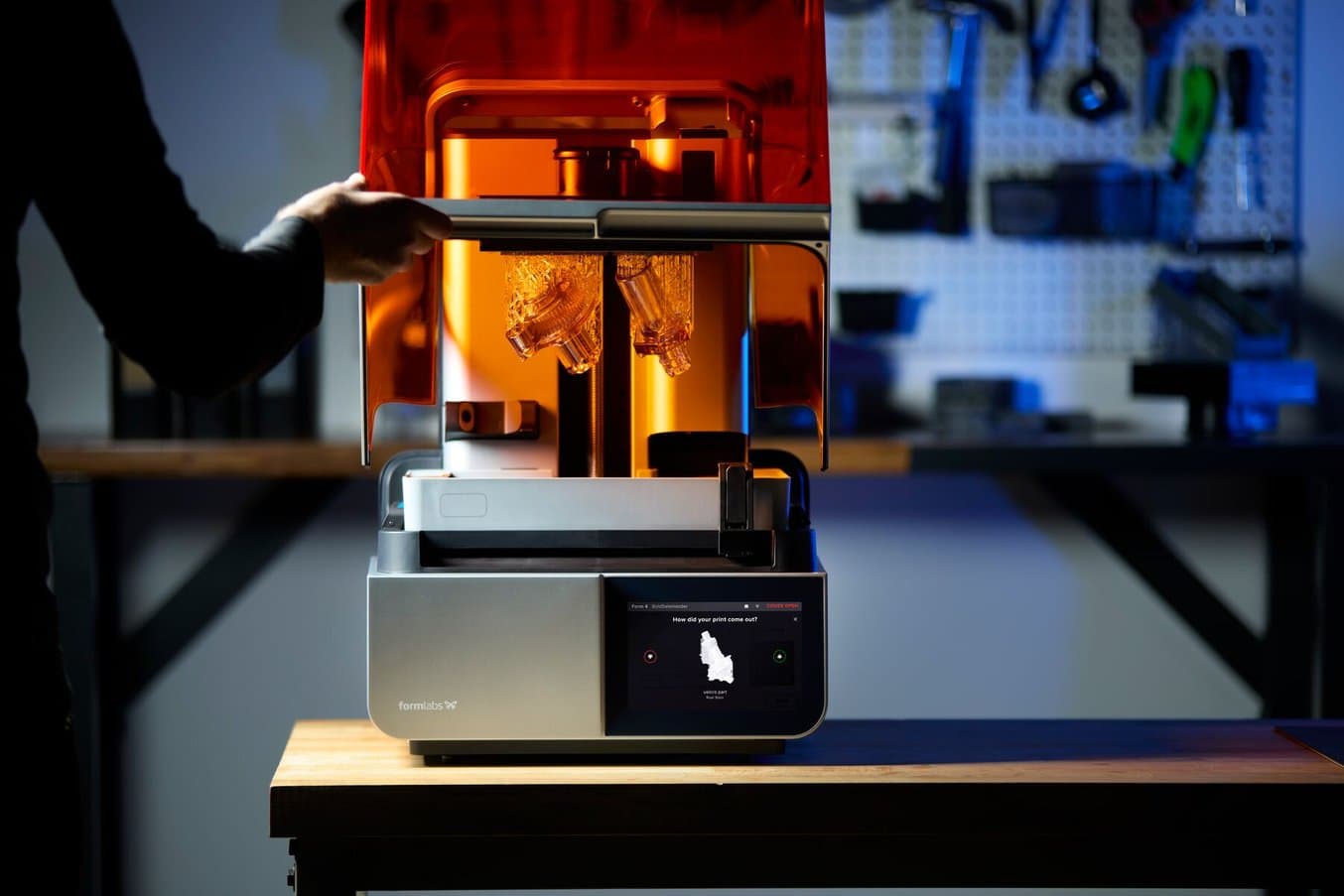
鋳造に3Dプリントを組み合わせることで、より高速かつ効率的な製造が実現できます。
FormlabsのSLA光造形方式3Dプリンタなら、鋳造工程にかかる時間やコストを削減できます。Formlabsの光造形3Dプリンタの詳細またはその他のご相談については、Formlabsまでお気軽にお問い合わせください。