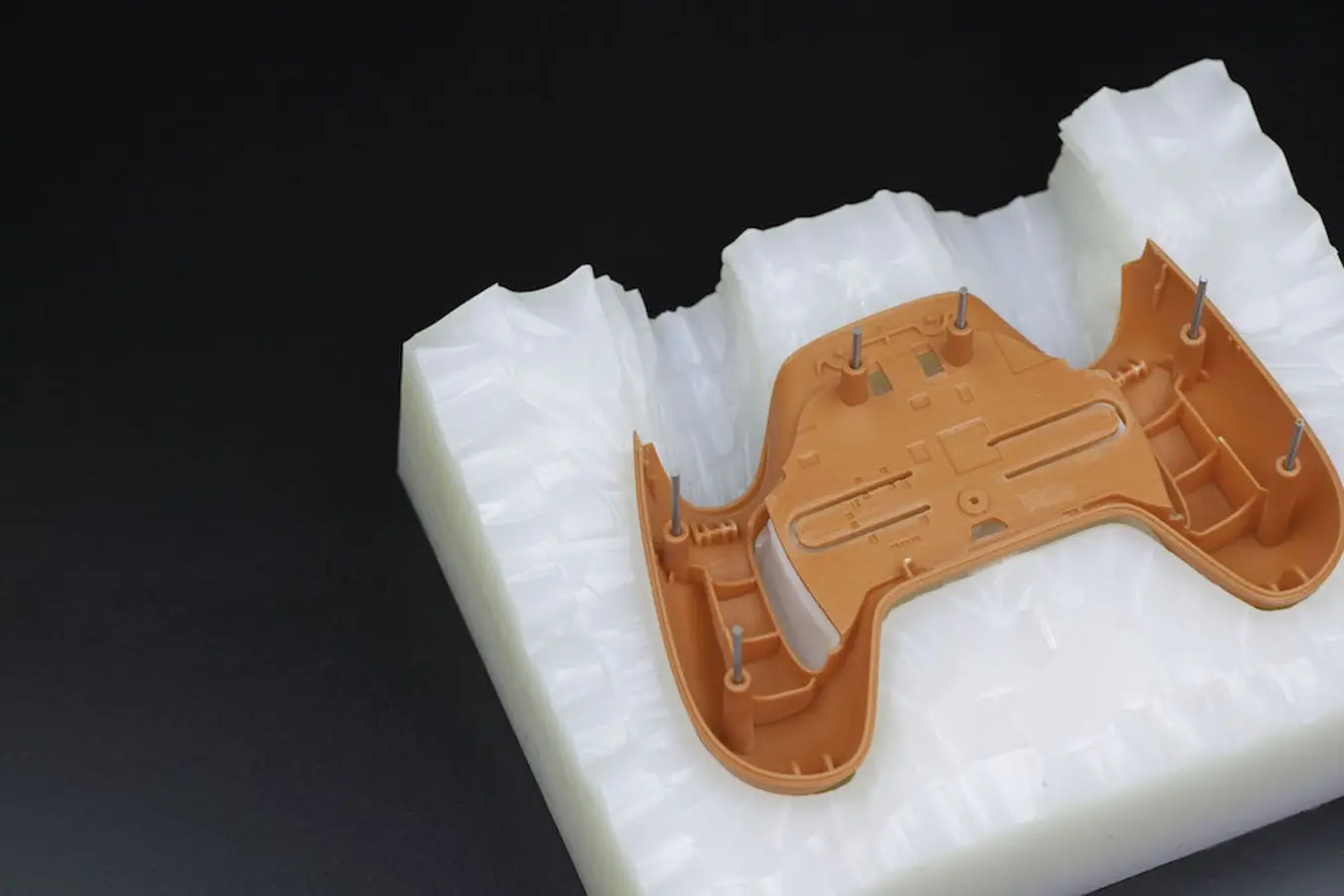
ウレタン鋳造で製作した試作品。(画像出典:Fictiv)
真空鋳造は、市場化テスト用の試作品やパーソナライズされた医療器具、その他製品を少量でバッチ生産する際によく使われる製造方法です。
本ガイドでは、真空鋳造プロセスの詳細、他の製造技術との比較、最適なウレタン鋳造装置、真空鋳造用の型を3Dプリントで製作する方法について詳しく解説していきます。
真空鋳造(ウレタン鋳造)とは
真空鋳造は射出成形に似た製造技術で、二つ割のシリコン型のキャビティにウレタン樹脂を流し込んで鋳造します。
原型の周囲にシリコンを流し込むことで、原型の複製となるシリコン型を作ります。高度なスキルが求められる工程で型を2つにスライスして原型を取り出し、湯道と通気孔を追加します。その後、型職人がウレタンベースの樹脂を型のキャビティに流し込み、気泡の侵入を防ぐために真空状態で樹脂を硬化させます。
その結果、原型を細部まで忠実に再現した製品ができあがります。
注:米国では、「真空鋳造」のことを「ウレタン鋳造」や「ポリウレタン鋳造」と呼ぶことがあります。本記事では、これらの用語をすべて同一のものとして扱っています。
真空鋳造の代表的な用途
真空鋳造は、量産グレードの品質が求められる製品を少量製作する際に最適な製造プロセスです。
最終的な製品とほとんど見分けのつかない、非常に細かな部分まで忠実に再現したモデルを製作できるため、ウレタン鋳造で製作したモデルは投資家向けのプレゼンテーションや展示会、広告写真の撮影用に最適です。1つのシリコン型でおよそ50個もの製品を鋳造できるため、製品の初期シリーズをリリースして早期の市場化テストも実施できます。
さらに多くの数量が必要になる場合にも、以下のようにいくつかの方法で対処が可能です。
-
同じ原型を再利用して複数のシリコン型を製作
-
複数の原型を使用してマルチキャビティ型を製作
-
室温硬化型(RTV)シリコンの代わりに高温加硫(HTV)シリコンやゴムを使用してより耐久性の高い型を製作し、1つの型で300~500個の鋳造を行う
原型の製作から鋳造品の受け取りまで僅か10日程度と製作期間が短い真空鋳造は、射出成形や熱成形、スピン鋳造のような工業レベルの製造技術と比べて多額の先行投資が必要なく、ラピッドプロトタイピングだけでなく量産移行前のテスト生産などにも活用できます。
真空鋳造では、さまざまな機械的特性をもつ多様な材料を使って非常に細かなディテールの再現や完璧に滑らかな表面品質を実現できるため、以下のような実製品用途での少量製作に最適です。
-
義肢、装具、補聴器などのカスタムフィット医療器具
-
ダッシュボードパネル、ノブ、メーター、エンブレム、ボンネットマスコット、照明レンズ、インレットマニホールドなどの自動車部品
-
エンクロージャやコントローラー、ユーザーインターフェースパネル、センサー統合などの消費者向け電子製品
-
ロボットや産業機械の重要部品や予備部品
-
限定サングラスやペン、携帯ケースなどの消費者製品
-
楽器
-
科学機器
-
スポーツ用品のアドオン
-
美術品、フィギュア、スケールモデル、小道具
真空鋳造はまた、手順が複雑なリバースエンジニアリングに頼ることなく既存製品を複製したい場合にもよく採用されます。一般的には、CADモデルや他の形式での設計図が手に入らない、彫刻や化石、歴史的遺物、骨董品、収集品、工芸品モデルなど、希少品や既に廃盤になっている品目です。
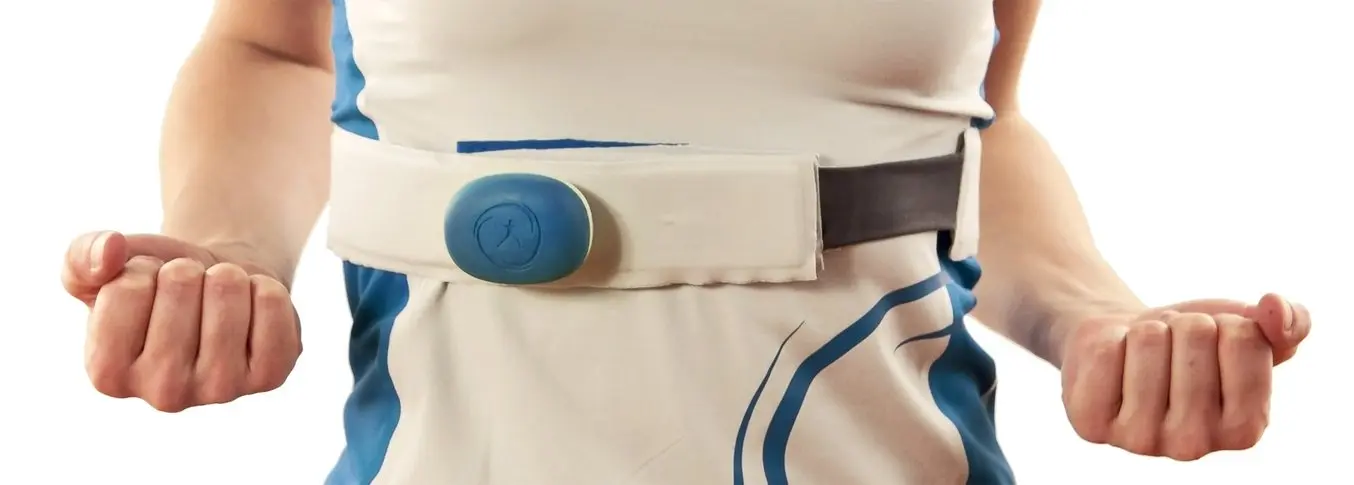
シリコンオーバーモールドによる真空鋳造で製作した、呼気センサーの電子機器ハウジング。(画像出典:IDZone Product Design)鋳造メーカー:Venture Rapid Technologies
ウレタン鋳造 vs. その他の製造方法
真空鋳造 vs. 射出成形
プロダクトデザイナーやエンジニアは、設計の検証には3Dプリントを活用し、量産フェーズの検証には射出成形を採用することがよくあります。しかし、ここで問題になるのが射出成形にかかるコストです。高品質なスチールをCNC加工して型を作るため、部品を何百個も製作する場合には良いのですが、型のサイズや形状の複雑さによって$5,000〜$100,000という多額のコストがかかります。
そこで、耐久性の高さを補う妥協案として、品質をやや下げた金型が使用されることが多いのです。アルミ製の金型であれば、コストを大幅に削減しながら1,000~5,000回の成形サイクルにも耐えることができます。シンプルな形状の場合はソフト金型なら加工速度がはるかに速く、射出成形用の金型製作に比べて製作期間を約半分にまで短縮できます。
必要な数量や成形品に求められる品質によっては、アクリル金型や3Dプリント製の型を使った少量射出成形も選択肢になります。FormlabsのSLA光造形方式3Dプリンタで型を製作する場合、通常コストは$100以下で、品質を大きく損なうことなく100個以上の成形品を製作できます。
見落とされることの多いアプローチですが、試作品製作から量産へ移行する前のテスト生産に真空鋳造を採用すると、よりスマートな工程が実現します。初期段階の試作品製作では、樹脂を使った鋳造で射出成形品に匹敵する製品を製作できます。さらに、費用対効果も非常に高く、鋳造型の製作コストは$200~1,000、成形品の単価は$10~100程度に抑えられます。
ウレタン鋳造用のシリコン型は、射出成形用の金型と同様、コアとキャビティを持つ二つ割構成で、型の間に溶かした材料を注入して成形します。しかし、射出成形とウレタン鋳造にはいくつか違いがあります。
-
射出成形では、ホッパーや送りねじを使って溶かしたポリマーを高圧・高温下で金型のキャビティに押し込みます。一方の真空鋳造は、低温で行われます。溶かしたプラスチックの代わりに液体レジンを真空環境で型に流し込むことで、植物の毛細管現象のようにレジンが細部まで引き込まれていきます。様々なポリマーに似せた樹脂が多数利用可能ではありますが、最終的に射出成形で使用する材料を使った試作品製作はできません。
-
オーブンで硬化させた後も1週間ほどは二次硬化が続くので、その間、造形品は紫外線や高温に弱い状態が続きます。
-
型が柔軟なため、成形可能なサイズや形状にも限界があります。ただし、工夫次第ではこれに対処することが可能です。例えば、段階的な鋳造では、3分割または4分割式の型で細長い形状を成形する際に金属材でサポートすることで重力に負けずに鋳造が可能です。
-
真空鋳造には鋳造材料の加熱・冷却サイクルがないため、射出成形よりも肉厚を柔軟に設定でき、その結果、部品の歪みが少なくなります。
-
シリコン製の型を使用する場合、大きなアンダーカットがある形状でも成形が可能です。しかし、射出成形向けのテストを行う際は、可能な限り射出成形用の設計を踏襲し、最終的な成形品に通常求められる抜き勾配を組み込むことをお勧めします。
-
射出成形ではスクラップ率や残留物、過剰製作によって使用済みポリマーの最大20%を廃棄しなければならないのに対し、真空鋳造では無駄をほぼゼロに抑えられます。
真空鋳造で作るモデルと最終的に射出成形で作る製品にはほとんど差異がなく忠実に再現できるため、エンジニアは量産に向けて事前に設計を最適化できます。つまり、射出成形メーカーへの外注にかかる天文学的な固定費用を会社の上層部に負担させることなく、高品質の製品プレビューを提供することができるのです。
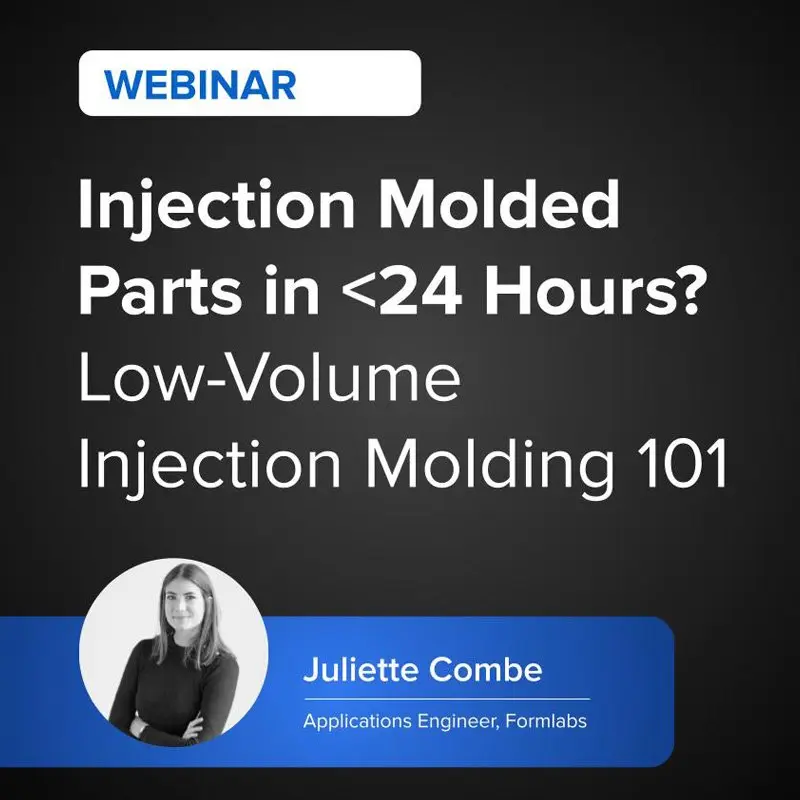
24時間以内に射出成形を完了する方法とは?小ロット量産用の射出成形 101
本ウェビナーでは、射出成形でSLA光造形3Dプリント製型を使用してコストを削減し、製作期間を短縮し、より高品質な製品を市場投入する方法を解説します。
真空鋳造 vs. 3Dプリント
3Dプリントに対するよくある誤解として、「一回限りの製作にしか使用できない」というものがあります。実際にはその逆で、3Dプリントで実製品用部品の少量生産が可能なのです。また、社内の3Dプリント設備に投資する会社も増えてきています。複数台の3Dプリンタを導入することで、数百個、時には数千個もの製品を少量バッチで製作できます。
3Dプリントと真空鋳造のどちらを採用すべきか、という選択に影響を与える主な要素は製品の形状にあります。真空鋳造は、射出成形品とほぼ同じ製品を作ることを目的としています。本物の射出成形品に変わる低コストな投資として、オーバーモールドで柔軟材料と硬質材料を組み合わせたり、インサート成形で金属部品を直接追加した試作品を製作することができます。射出成形可能な部品を少量製作する場合、真空鋳造は3Dプリントよりもコスト効率が高い方法です。
真空鋳造のもう一つの利点は、3Dプリントよりもはるかに速く低コストで大型部品を製作できることです。真空鋳造では、最長寸法が約50cm、鋳造重量が最大1.5kgの型を使用できます。
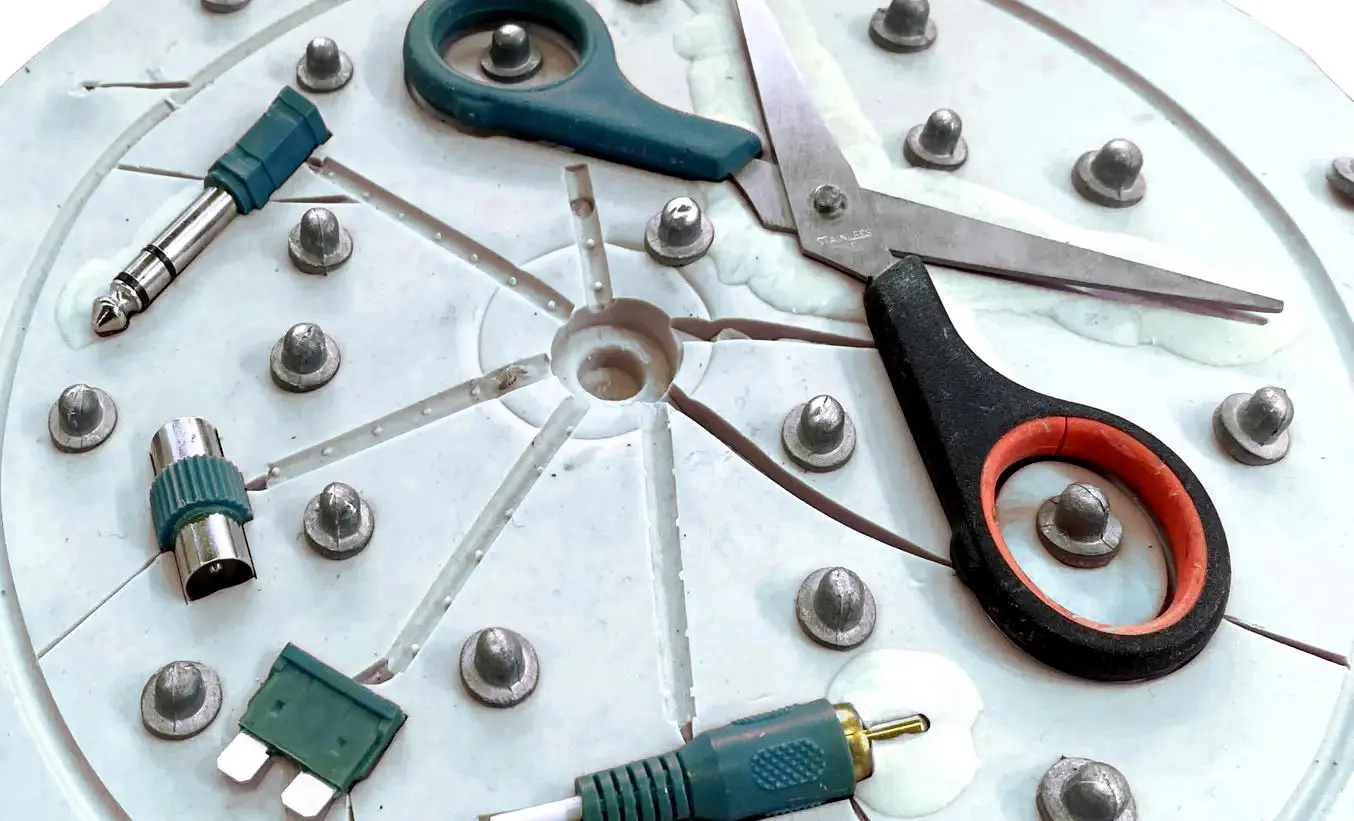
金属インサートをつけたシリコン型で真空鋳造する様子。
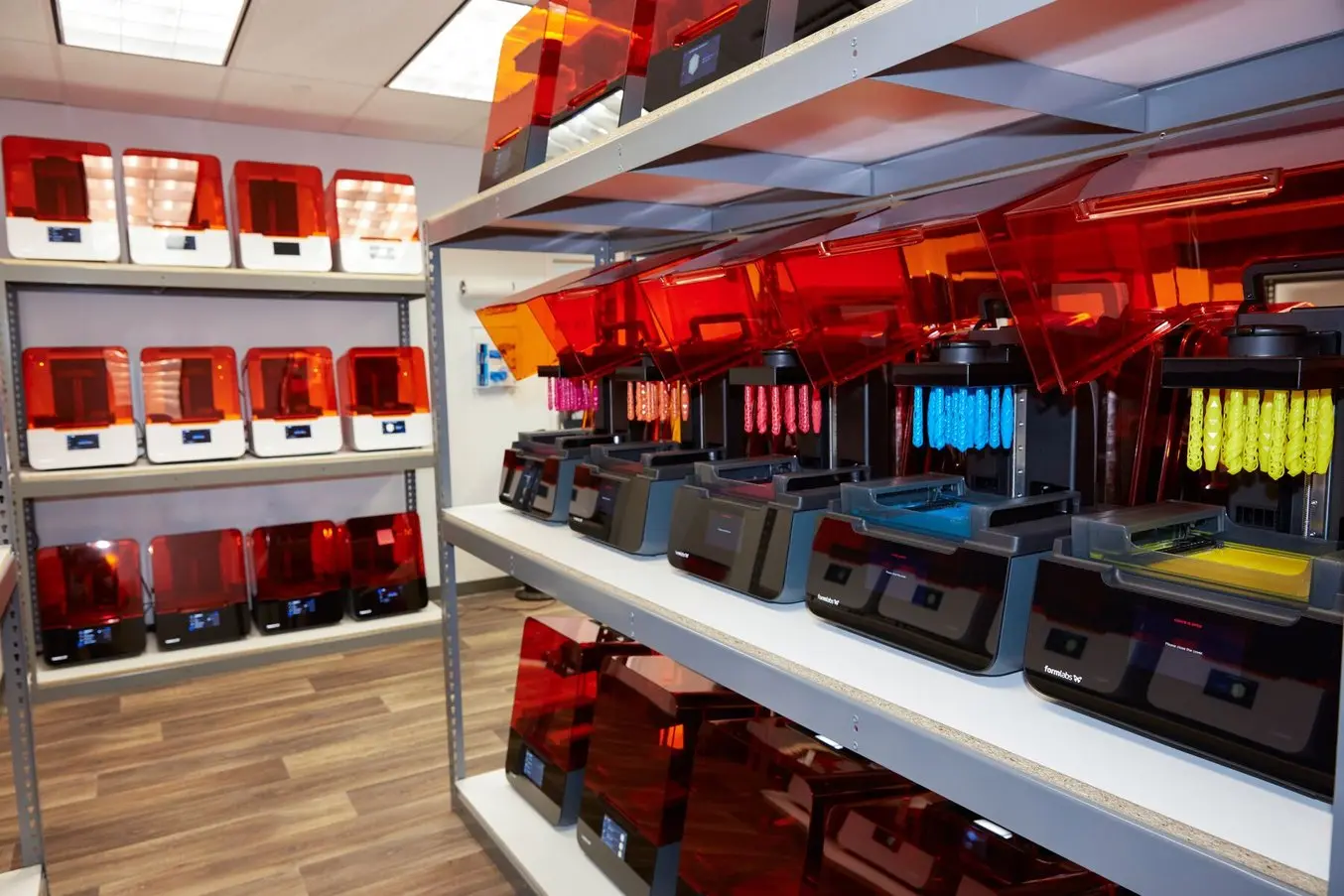
3Dプリント製の実製品用部品で少ロット量産とカスタム製造を行う方法
このウェビナーでは、カスタム製造と少量の実製品用部品生産を素早くコスト効率良く行う方法についてご紹介します。
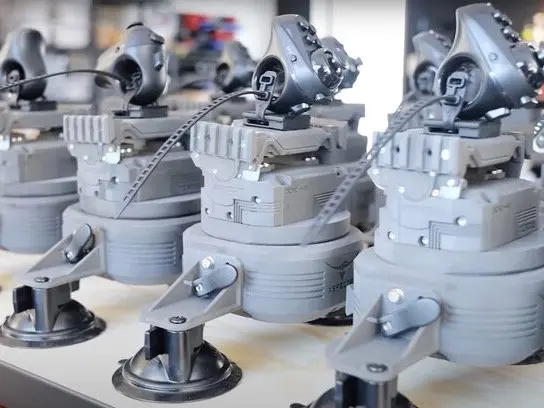
実製品用3Dプリント製部品の負荷テスト
この製品仕様では、実製品用部品の製作が可能なFormlabsの3Dプリンタや3Dプリント用材料のほか、実製品用途での3Dプリント用材料の安定性を証明する活用事例や負荷テストの結果をご紹介します。
比較:真空鋳造 vs. その他の製造方法
それぞれの製造方法について、利点と欠点を見ていきましょう。
真空鋳造 | 射出成形 | 3Dプリント | ラピッドツーリング | 加工 | 手作業 | ||
---|---|---|---|---|---|---|---|
設計の自由度 | ★★★☆☆ | ★★☆☆☆ | ★★★★★ | ★★☆☆☆ | ★★★★☆ | ★★★☆☆ | |
サイズ | ★★★★☆ | ★★★★☆ | ★★★☆☆ | ★★★☆☆ | ★★★★☆ | ★★★★★ | |
スループット | ★★★☆☆ | ★★★★★ | ★★★☆☆ | ★★★★☆ | ★★☆☆☆ | ★☆☆☆☆ | |
材料の種類 | ★★★☆☆ | ★★★★☆ | ★★★★☆ | ★★★★☆ | ★★★★★ | ★★★☆☆ | |
投資コスト | ★★★☆☆ | ★☆☆☆☆ | ★★★☆☆ | ★★☆☆☆ | ★★★★★ | ★★☆☆☆ | |
造形単価 | ★★★★☆ | ★★★★★ | ★★★☆☆ | ★★★★☆ | ★★★☆☆ | ★★★☆☆ | |
製作期間 | ★★★★☆ | ★☆☆☆☆ | ★★★★★ | ★★★☆☆ | ★★★★☆ | ★★☆☆☆ |
真空鋳造プロセス
真空鋳造は、4つのステップから成る高度なスキルが必要な製造工程です。
1. CAD設計
デザイナーやエンジニアは、Fusion 360やSolidWorksのようなCADソフトウェアを使用して、製造するオブジェクトのデジタル設計を作成します。ウレタン鋳造では、以下に注意して設計を行う必要があります。
-
肉厚は1.5 mm~4mmにします。肉厚の絶対最小値は1mmです。
-
リブは肉厚の60%まで薄くできます。
-
半径は3mm以上と余裕を持たせてください。
-
部品の強度を向上させるため、壁が直角にならないようにします。
-
製品の外観を向上させるため、2つのシェルの間に0.5mmの溝を作ります。
-
ネジボスの肉厚は穴の直径と同じにします。
-
文字をデボス加工する場合、最適な深さは0.25mmです。
完成したらCADモデルをSTL形式でエクスポートし、原型を製作します。
2. 原型の製作
原型とは、その形に沿って鋳造で複製を作るための型のことを指します。真空鋳造のシリコン型は原型の完璧なレプリカとなるため、3Dプリント製の原型を作る際はCADモデルを正確に具現化すること、特に非常に滑らかな表面品質を忠実に再現することが何よりも大切です。優れた原型の二次的な特性として、硬度や耐薬品性、耐熱性、そして経年劣化を防ぐ耐久性を備えていることが挙げられます。
以前はCNC加工で作る金型が一般的でしたが、それらの製作にはコストと時間がかかります。また、表現できる穴や溝、内側の半径、有機的な形状の表面などに限界があります。3Dプリントは原型を製作する最先端の代替手段として、現在主流となりつつあります。
メインストリームや商業用途で利用可能な3Dプリンタはいくつかありますが、ウレタン鋳造に最もよく使用される3Dプリント方式はSLA光造形方式とSLS方式です。
SLA光造形方式では3Dプリントの中で最も滑らかな表面品質を実現できるため、真空鋳造の原型として最適です。適切な造形設定でプリントされたSLA光造形品はプリント完了時点で既に表面が非常に滑らかですが、完璧な表面に仕上げるためには、サポート材を除去した後にやすりがけや研磨処理が必要です。また、Rigid 10Kレジンなどの高機能材料は、非常に優れた機械的特性や耐熱性、耐久性を備えています。
ナイロンを使用したSLS 3Dプリントでは、高強度で耐熱性に優れた高精細な造形品を製作できます。SLS方式では専用のサポート材が不要なため、薄肉構造やエンボス加工などのディテール、スナップフィットやヒンジ、入れ子構造や格子構造など複雑な形状にも最適です。SLS造形品の表面品質はウレタン鋳造の原型としてはやや粗すぎるものの、プリント後にブラスト処理やバレル研磨を施すことで表面の粗さを軽減できます。
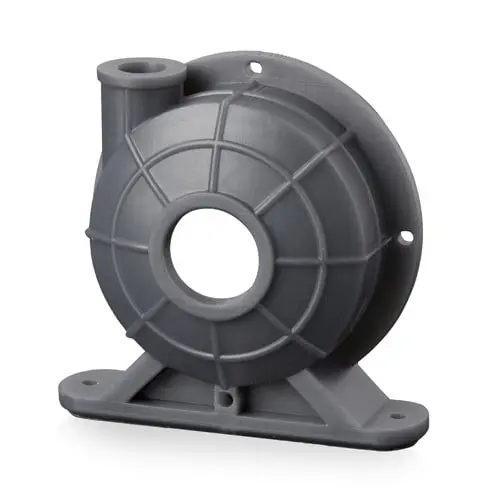
3. 型の製作
このステップが最も手間のかかる工程で、型職人がメラミン化粧板とホットボンドで型枠を作ります。その後、CA接着剤を少量垂らして原型を底に固定します。回転工具を使ってポケットを作り、そこに原型の設計に組み込まれたリップをはめ込んで固定することもあります。
二つ割の型でしっかりとしたパーティングラインを出すために、原型とボトムパネルの間にあるすべての穴を埋める必要があります。これには、スチレンブロックとプラスタリナモデリングクレイが最適です。次に、位置決めピンとレジストレーションエイドを追加して、型のもう一方と完璧に位置合わせをします。
二液型シリコンをしっかりと混ぜ合わせてから型に流し込み、真空チャンバー内で脱ガスをします。しかしその前に、内部に空気が閉じ込められてしまうことを防ぐため、型職人が酸ブラシを使って原型に空いている小さな隙間をすべてシリコン混合物で巧みに埋めていき、シリコンを逆流させて型の半分を形成します。
数時間硬化させた後、型枠から外し、逆さまにします。その後、型職人がアクリル製の通気孔や立ち上がり、そして後半の工程で必要となる湯口を取り付けていきます。シリコンの上に離型剤をスプレーで塗布し、内側の深い箇所には刷毛などで塗っていきます。その後、新しい型枠を作り、同じ要領で型のもう半分となる部分を流し込んで製作します。
真空鋳造の準備として、型を型枠から取り出した後にE236ウレタン用離型剤を均一にスプレーします。型同士を結合させて単一のブロックを形成し、位置決めピンとレジストレーションエイドを再挿入して位置を調整します。
4. 真空ウレタン鋳造
この工程では、真空チャンバー内で原型を使って鋳造することで複製を作ります。まず、型を木板にテープで固定し、通気用のストローとじょうごを追加します。
二液型樹脂を計量し、着色剤と混ぜます。次に、鋳造に使う材料を真空チャンバーで数分間脱ガスします。
これで、ポリウレタンの混合材を注ぐ準備が整いました。ライザーストローの状態により、キャビティが完全に充填されたことがわかります。70℃で硬化させてから型を開くと、原型のディテールや表面の質感まですべて再現したカーボン製のレプリカのできあがりです。
最終的な仕上げとして、余分な材料のエッジを整え、1000番のサンドペーパーでさらに研磨を行うほか、オーブンで加熱してすることで造形品の材料特性を向上できます。
役立つヒント
上記の手順は、電子機器の筐体や収納容器などの薄肉構造の製品、または製品の表面にパーティングラインを残したくない場合に採用されることが多い手順です。
そういった要素が特に気にならない他の用途では、シリコンブロックで原型を覆い、手作業で切り開くだけでも十分です。しかし、切り開く際に正弦波状に切断する必要があり、ある程度の経験とスキルが必要になります。
ウレタン鋳造の出来栄えをさらに高めるためのベストプラクティスをいくつかご紹介します。
-
型に直接離型剤をスプレーする場合は丁寧に行ってください。成形品表面に僅かにテクスチャが残ることがあります。
-
できれば使用する前日までに樹脂を40℃に予熱しておき、結晶化を防ぐために時々ボトルを反転させてください。
-
レジンボトルに湿気などの水分が侵入しないようにしてください。PUに水分が混じると気泡が生じてしまいます。対策として、使用後すぐにアルゴンガスをボトルに充填するのも一つの方法です。
-
ニ液型材料を混ぜる際は、必ずダブルカップ混合法で行ってください。最初の容器から直接材料を注ぐと、混ざりきっていない箇所に筋ができ、鋳造が失敗する原因になります。
-
後で再利用するために型枠を解体する際は、消毒用アルコールを使ってホットグルーを柔らかくしてから解体してください。
-
部品の様々な箇所への平均距離が最短になるよう、湯口は製品の隅に設置してください。こうすることで、すべての箇所にしっかりと材料を充填できます。
-
気泡の発生を防ぐため、細かなディテールが施された繊細な箇所には一点から材料を注ぐようにし、上から被せるような注入の仕方は避けてください。
-
ゲートは低い位置、通気孔は高い位置に設定してください。
-
メタリックパウダーを載せることで非常に鮮やかな仕上がりになり、ポリピロールやグラファイトパウダーを使用すると導電性が高まります。
-
ウレタンを混ぜるときは、表面上に余裕を持たせてください。混合液が、マシュマロを電子レンジで加熱した時のように真空チャンバー内で泡立ち、膨らむためです。
-
工程を高速化し、より安定的な結果を得るためには、工業グレードの真空鋳造機の使用をお勧めします。
真空鋳造機
ウレタン鋳造は工程が複雑なため、ほとんどの企業が外部の鋳造メーカーに委託しています。
真空鋳造の内製化を検討している企業にとっては、試作品の品質を一段と引き上げ、量産に向けた工程を一気に高速化できる工業グレードの真空鋳造機が欠かせません。2日以内で50個もの鋳造が可能で、必要に応じて異なる色や材料を使用できます。
樹脂を使うタイプの真空鋳造機はのサイズは冷蔵庫程度で、材料の混ぜ合わせから鋳造、硬化までのプロセスをすべて自動化します。チャンバーの加圧具合やミキサーの速度、加熱カップ、オーブンの加熱など様々なパラメータもオペレーターが制御できます。最新のシステムはプログラム可能なため、カスタムシーケンスを作成することで特定の材料や製品種別に合わせて鋳造サイクルを最適化できます。
真空鋳造機には様々なサイズがあるため、色々な大きさの型を製作できます。ほとんどの機種では、樹脂だけでなく、射出成形品に匹敵するナイロン、セラミック、ワックス、さらに低融点合金の鋳造も可能です。
ウレタン鋳造機は、チャンバー内が真空になるまでの時間が早く手作業を最小限に抑えられるため、プリプロダクション段階での使用に最適です。欠点としては、本体価格が数万ドルにも上ることです。ジュエリー用の真空鋳造機ならより小型で、価格も通常数千ドル程度で済みます。
以下では、優れた真空鋳造機のいくつかをご紹介します。
-
Renishaw 5/01 PLC: 最大型サイズ530 x 450 x 420mm、価格は約$45,000。さらに大型の5/04モデルでは、最大750 x 750 x 900mm の型を使った鋳造が可能で、ガラス繊維強化ナイロンやワックスなど使用できる材料も増えますが、価格はほぼ2倍になります。
-
SLM VCM 04: 最大型サイズ750 x 750 x 900mm、鋳造量2.2L、ナイロンやワックスでの鋳造が可能です。
-
MCP 5/01: 鋳造可能な最大サイズ400 x 400 x 400mm。MCPは、MCP 003(560 x 600 x 600mm)、4/04(900 x 750 x 600mm)、4/05(1300 x 750 x 800mm)など、より大型の機器を多数提供しています。これらの機械は完全にプログラムが可能で、ワックス、シリコン、ナイロン、PU樹脂を使用したバリオ圧力鋳造が可能です。また、3Dプリント製の射出成形型も使用できます。
-
Scott AM 1000: 最大型サイズ500 x 450 x 425 mm、鋳造重量1kg。4000モデルは最大型サイズが750 x 750 x 900 mm、鋳造重量が5kgです。樹脂のほか、セラミックや金属の真空インベストメント鋳造にも使用できます。
-
Multistation CSV 340: 最大型サイズ340 x 340 x 435 mm、鋳造量600mL。CSV500型は、最大型サイズが500 x 500 x 635 mm、鋳造量が最大1Lです。
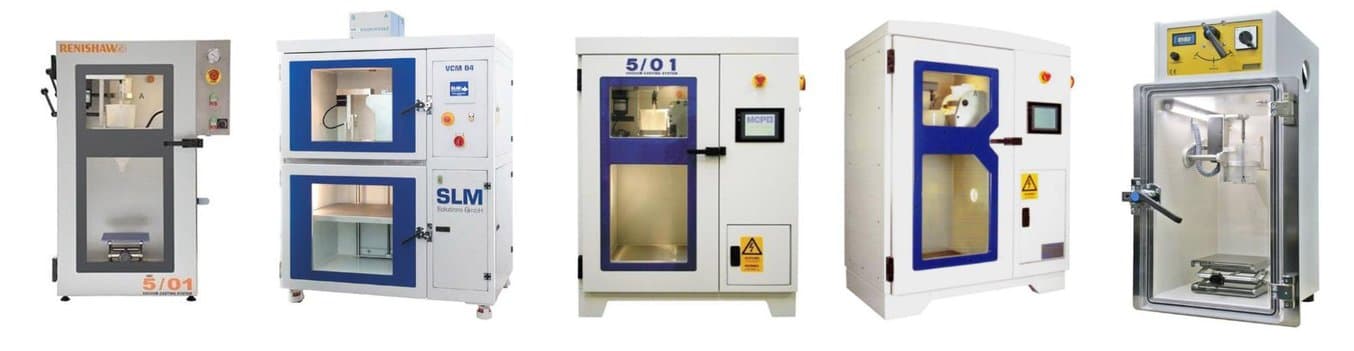
Renishaw、SLM、MCP、Scott AM、Multistationの真空鋳造機のラインナップ。
真空鋳造機 vs. 圧力チャンバー
低コストな代替案として、真空重力鋳造機を自作することも可能です。型の中に気泡が1つでも残っていると鋳造品全体が台無しになってしまうため、樹脂鋳造工程の根本的な課題となるのは脱ガスです。
DIY真空鋳造機を自作する場合に、混合材からすべての気泡を取り除くために使用できる2つの方法として、真空チャンバーと加圧器があります。
真空チャンバーは、型を作る前にシリコンゴムから空気を抜くために使用するものです。真空引きは高圧をかける方法よりも時間がかかるため、真空チャンバーが使用できるのは硬化時間が20分以上かかる硬化の遅い樹脂のみです。
真空チャンバーには2つのレバーがあり、1つは空気注入用、もう1つは真空吸引用です。真空に達したかどうかを確認するためのゲージと、脱ガス具合を確認するための透明なアクリル蓋が付いています。蓋は強化ガラス製で、プラスチックの蓋と違って経年劣化で割れることがなく、高い値段を払う価値があります。
加圧器はエアーコンプレッサーが必要なため、値段は少し高くなります。しかしその反面、気泡のない樹脂混合材や鋳造品を作るためには最適な手段です。真空チャンバーとは異なり型と一緒に使用することができるほか、硬化が早く製作時間の短い樹脂の使用に適しており、100%空気が排除された鋳造品の製作が可能です。
真空チャンバーは、石膏、コンクリート、または木材注入など多数の用途で空気抜きが可能ですが、加圧器はシリコンバッチのガス抜きにのみ使用するのが一般的です。
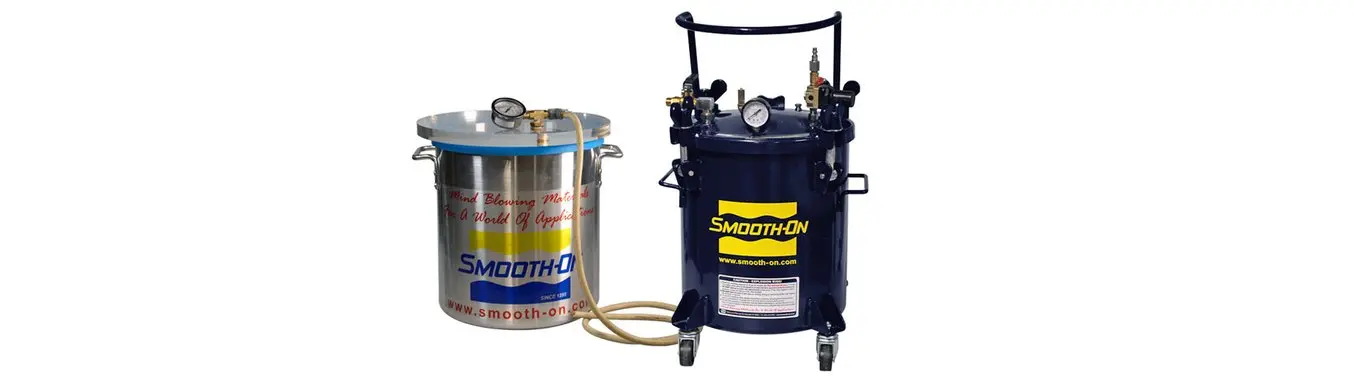
真空チャンバー(左)と加圧器(右)。
真空鋳造の材料
シリコン型の材料
鋳造用のシリコンは、Tin-cure(縮合タイプ)とPlatinum-cure(付加タイプ)に分けられます。縮合タイプとも呼ばれるTin-cureシリコンは、収縮率が1~4%です。模型メーカーは収縮率を可能な限り抑えているものの、厳格な公差が要求される用途ではより高品質のPlatinum-cureシリコンや高温加硫(HTV)ゴムの方が向いています。
ショア硬度40~50Aのものであれば、何十回も再利用が可能な高耐久性の型が製作できる一方、ドラフトに問題があり硬い型内に閉じ込められてしまうような部品でも離型が簡単に行えます。エアトラップや気泡、異物の混在など、型内部で起こっていることをすべて確認できる、半透明のシリコンがおすすめです。
優れた二液型シリコンを提供するメーカーには、SmoothOn、Elastosil、V-Sure、Silicones and More(S.A.M.)などがあります。特に大量に注文する場合は、海外の化学工場に直接注文することで購入者が求める仕様に従って工業品質の製品を提供してくれるほか、ディスカウントを提供してくれるところもあります。
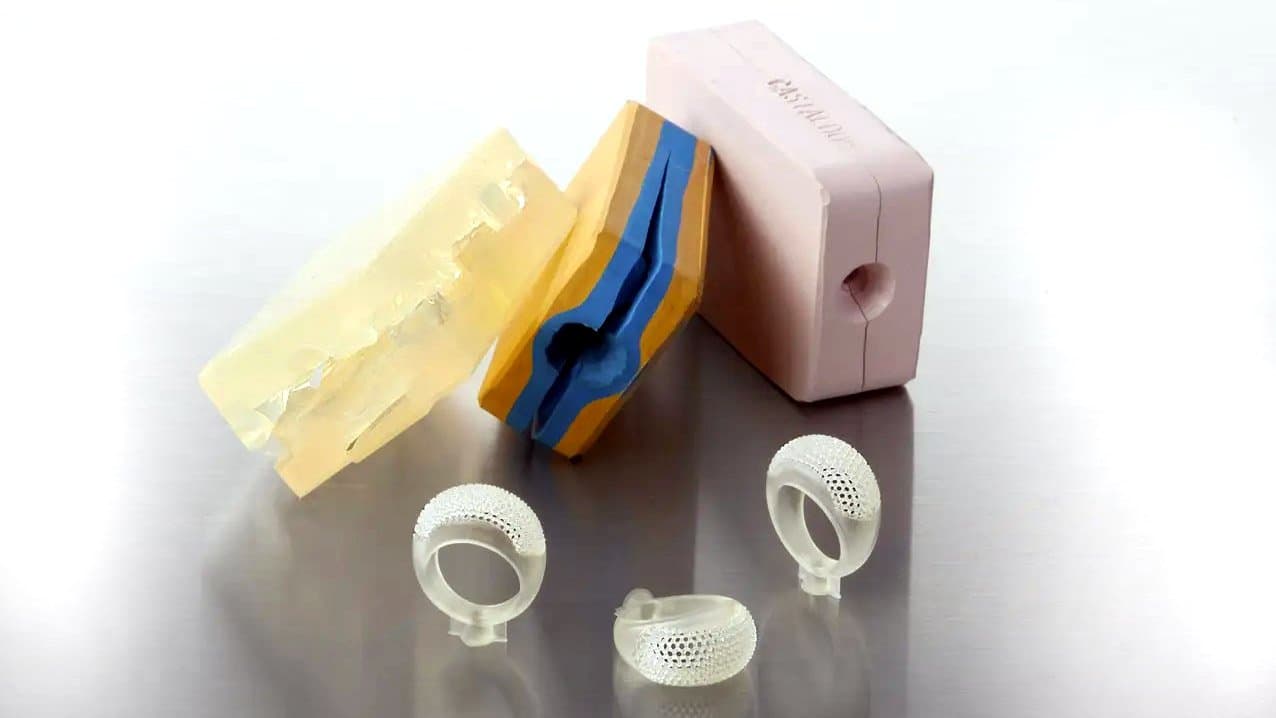
RTVやHTVを使用したジュエリー用の型は実際にジュエリー業界で量産に使用されており、複雑なフィリグリーのディテールをしっかりと再現できる。
鋳造用のウレタン樹脂
柔軟性、弾力性、剛性、硬度など、さまざまな特性を持つ材料を鋳造で使用できます。
-
ABSライクの多用途樹脂
-
優れた剛性を備えたガラス繊維入りナイロンライク材料
-
ウェアラブル、ハンドグリップ、ボタン、ガスケット、シールなどの用途向けのエラストマーTPEライク材料
-
PCライク材料(ポリカーボネート)
-
半透明または透明の鋳造用ウレタン(PMMAライク)
-
POM、PUライクの耐熱材料
また、粉砕ガラス、ワックス、エポキシ、セラミック、複合材料や、食品グレード、導電性、低密度、難燃性を備えた材料など、エキゾチックなウレタン鋳造材料もいくつかあります。有名なブランドとしては、FastCastのウレタン鋳造用樹脂、Smooth-On、SRC Specialty Resinなどがあります。
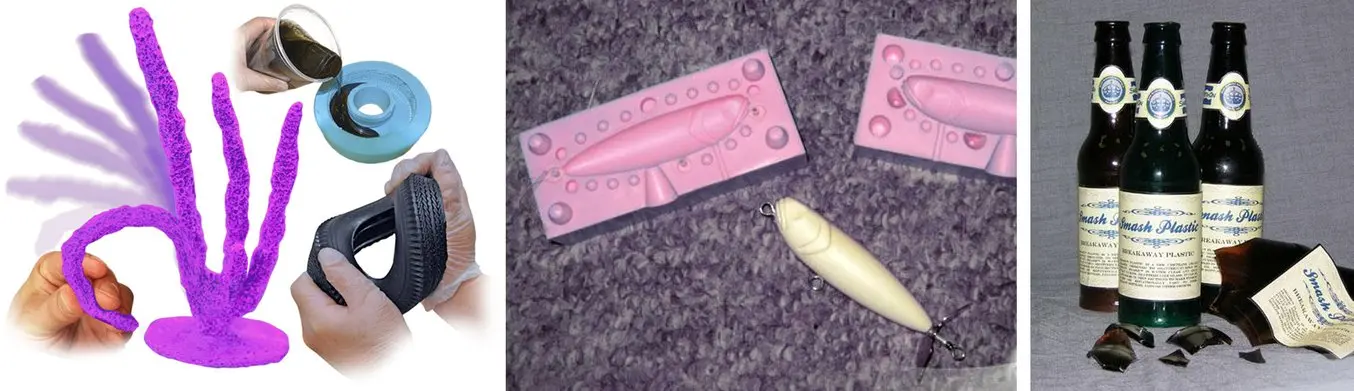
ゴム状から浮遊性、ガラス状まで、ウレタン樹脂の品揃え。ゴムライクから浮遊性のある材料、ガラスライクの材料まで、様々なウレタン樹脂がある。
活用事例:3Dプリント製の原型を使ったウレタン鋳造
Calibur Fencing
真空鋳造は、射出成形で量産を行うための金型製作に投資する前に、プリプロダクションで最終製品をテストし微調整を加えるための試作品製作に最適です。この成功事例の1つに、フェンシングでスコアを記録するためのワイヤレスウェアラブルデバイス、Calibur Fencingがあります。
設計者はまず、デバイスの機能をテストするためのシンプルな試作品製作から始め、適切なフォームファクターを見つけるために大まかなモックアップをFDMで3Dプリントしました。最終的に、実製品と同等の高品質な試作品を製作するためにはFormlabsのForm 3 SLA光造形プリンタが不可欠であることがわかりました。
同社チームはその後、SLA光造形3Dプリントで原型を製作して真空鋳造メーカーに送り、そこで顧客向けのベータテスト品を製作しました。こうすることで、常に最先端で品質管理を行いながら、実製品製作に向けて高速にプロセスを進めることができました。
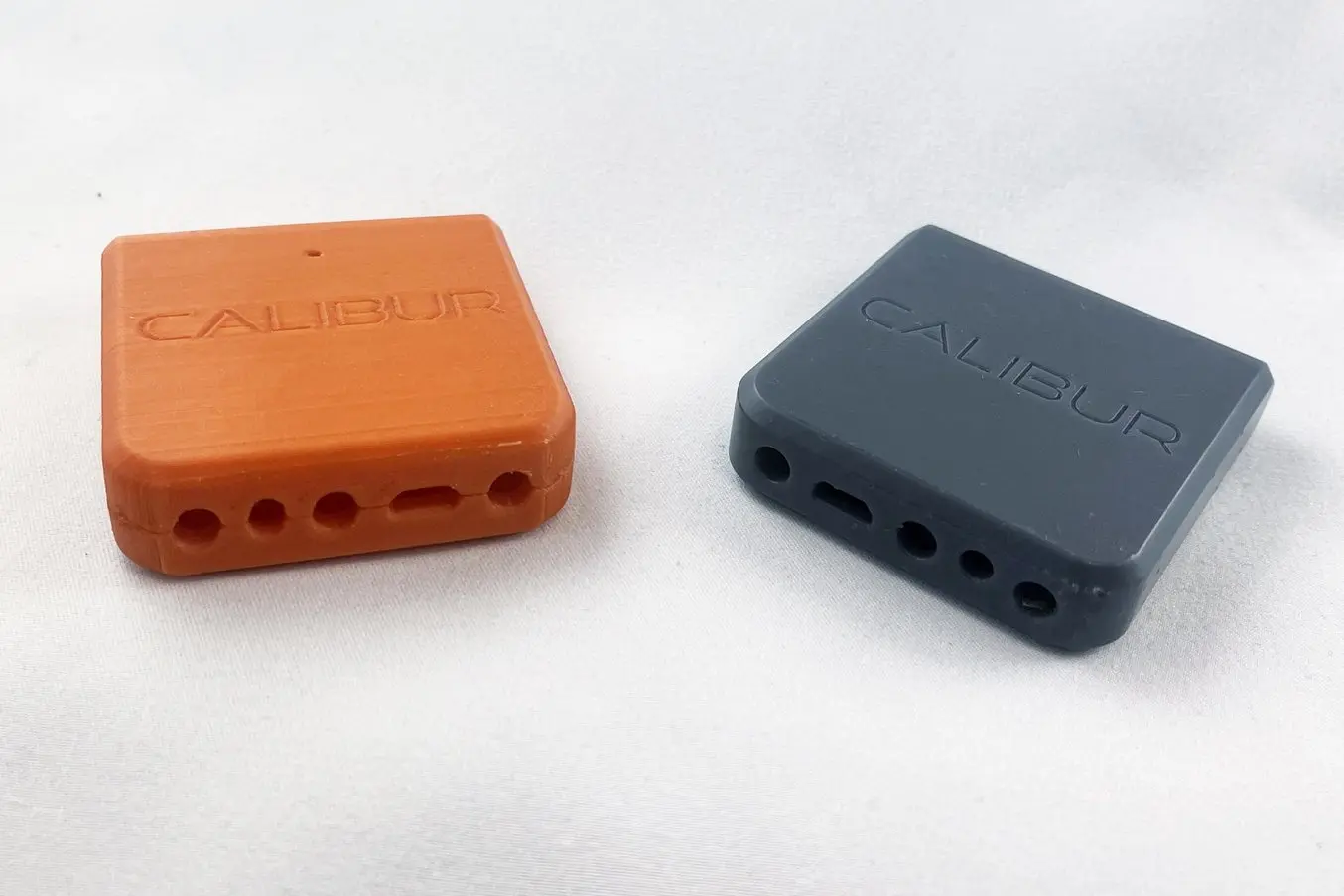
最初のモックアップにはFDM 3Dプリンタを使用していた同社だが、よりリアルで機能的な試作品を作るためにSLA光造形3Dプリンタに移行した。
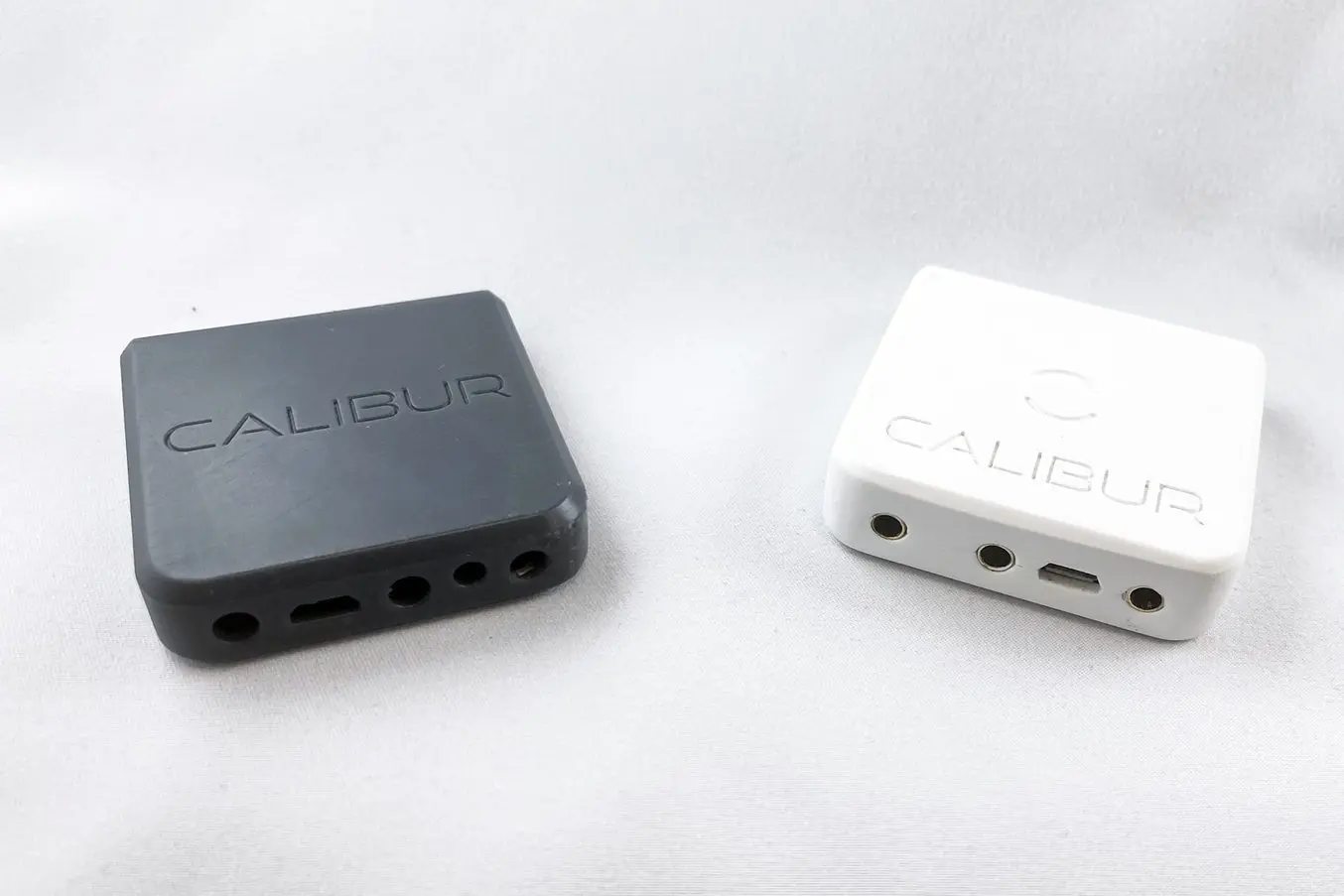
その後、SLA光造形で真空鋳造用の原型を3Dプリントし、実テスト品の初回少量製作を行った。
Louisville Slugger
Louisville SluggerのInnovation Centerで働くチームは、細かなことで大きな変化を起こせると実感しました。同社は1884年から野球バットを製造し続けており、より速く、よりパワフルなスイングを実現する要因を知り尽くしています。
Slugger Innovation Centerのスタッフは、スポーツ向けの設計のために分析的なアプローチを常に採用し、Formlabsの3Dプリンタの助けを借りてグリップ用のアドオンを製作しました。段差のある形状により、打者が最高の打撃を決められるよう完璧なグリップをサポートします。
他の事例と同様、Sluggerの設計チームは、3Dプリントと真空鋳造の両方を一つの場所で行えることで試作・検証プロセスの反復スピードが向上し、より迅速に知見を生み出せることを実感しました。Form 3 SLA光造形プリンタで積層ピッチ50μmでプリントした高精細な試作品モデルは、金型のポジティブ形状の製作にも役立ちました。ウレタン鋳造の力により、シリコン射出成形品に匹敵する品質と耐久性を持つテスト品を製作できたのです。
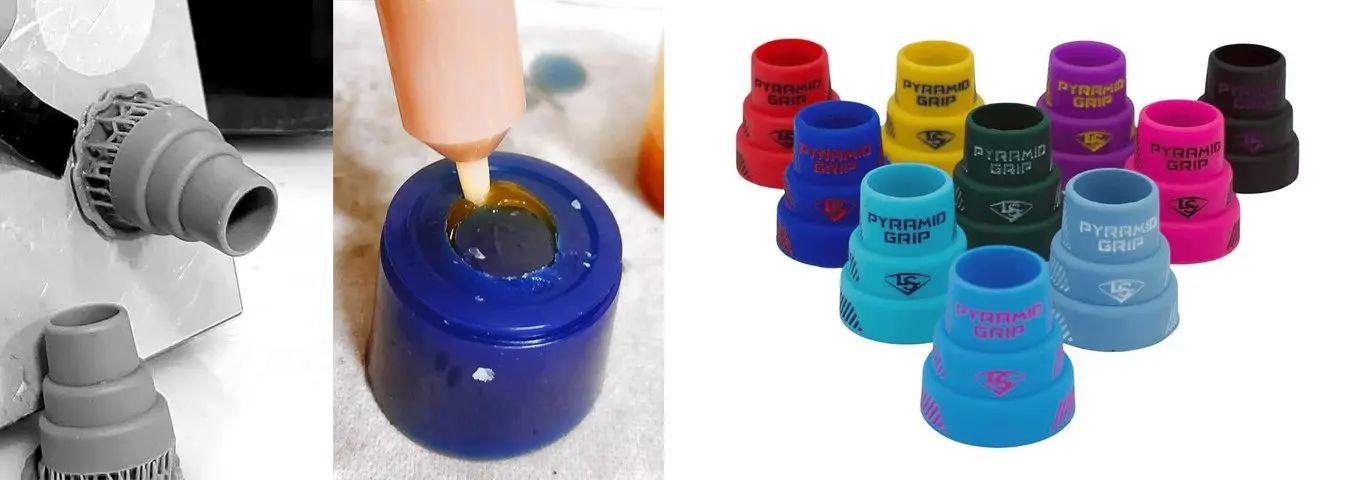
3Dプリント製のポジティブ形状モデルから実製品を社内鋳造し、完成品へ。
SiOCAST
SiOCASTは、3Dプリントと樹脂鋳造の組み合わせに関してユニークな背景を持っています。MMORPGオンラインゲームやRPGボードゲームの台頭により、カスタムミニチュアフィギュアの需要が急速に高まっています。コストのかかるスピン鋳造や真空鋳造用のシリコン型を使用した限定シリーズ製作の代わりに、同社はカスタム開発した機械とHTVゴム型を使った独自の樹脂射出成形機を開発し、特許を取得しました。
同社が独自開発したSiOresは、240℃までの熱可塑性液体樹脂にも耐えることができます。SiOCASTマシンは従来の樹脂鋳造の最大20倍の速さを誇り、自動化と回転式マルチキャビティ型で1時間あたり1,000個もの部品を製造することができます。
原型はすべてFormlabsのSLA光造形プリンタで3Dプリントし、その後洗浄および二次硬化工程を自動化したFormlabsのForm WashとForm Cureで後処理を行います。SLS 3Dプリントを活用して再利用可能な湯道を製作したことで工程はさらにスピードアップし、1回の鋳造で最大64個のミニチュアを製造することができるようになりました。
射出成型の場合はより厳しい条件や粘性のある材料に対処しなければならないため、どうしても失敗することがありますが、これらの真空鋳造型なら原型となるオリジナルモデルの完璧なレプリカを製作できるため、たくさんのゲーマーの心を掴めるでしょう。
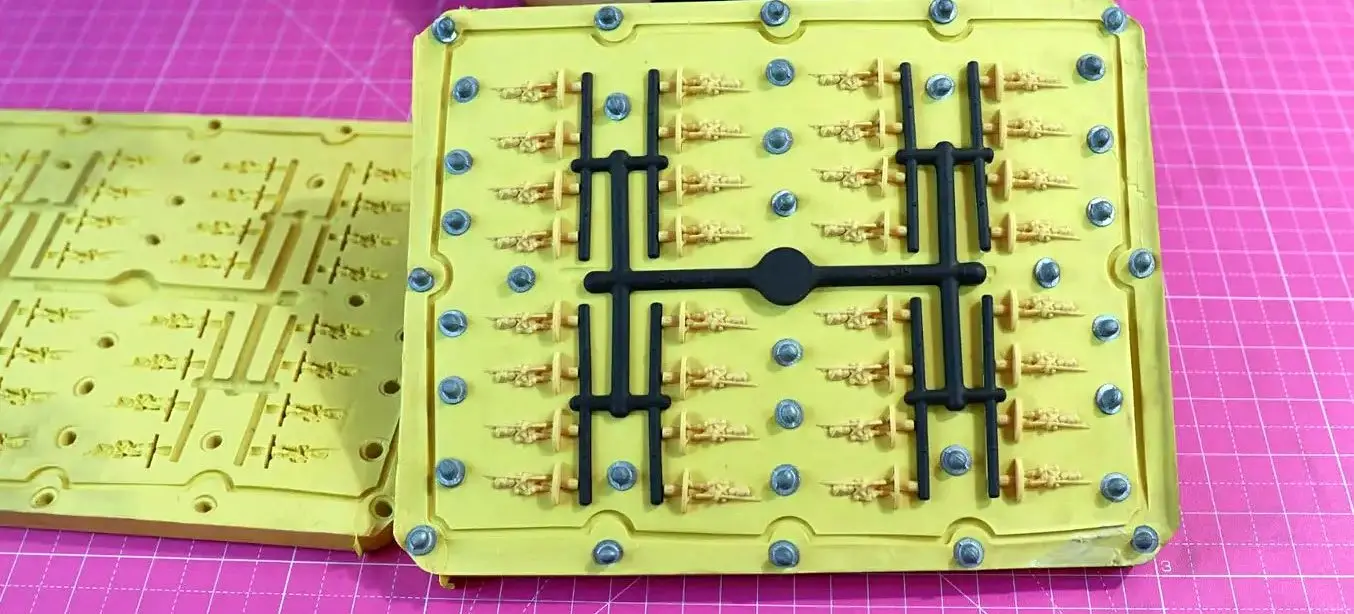
SiOCASTは、独自のHTVシリコン、SLA光造形による3Dプリント製の原型、SLS 3Dプリント製の再利用可能なナイロン材料の湯道を活用し、最大10,000個のミニチュアを製作。
真空鋳造と3Dプリントを組み合わせる
真空鋳造は、工業レベルの製造方法で必要となる大規模な先行投資を行わずに成形品を製作できる、理想的なプロセスです。様々な用途での実製品製作のほか、試作品製作や外観確認用モデル、プリプロダクション生産にも活用できます。製品の形状が真空鋳造固有の設計ガイドラインに従ったもので、離型がきちんと行える形状である限り、鋳造によって原型の忠実なレプリカが製作できます。
3Dプリントの発展により、真空鋳造にも様々なメリットがあります。3Dプリントでは非常に滑らかな表面品質を実現しながら高精細な原型を製作できるため、真空鋳造プロセスに組み込むのに最適な方法です。
3Dプリントとは異なり、真空鋳造を社内で自力で行うのは容易ではなく、厳格な手順に従う必要があります。高精細な表現とシンプルなワークフロー、そして製作期間の短さにより、3Dプリントは試作品製作や少量製作で真空鋳造に代わる現実的な手段としても活用できます。