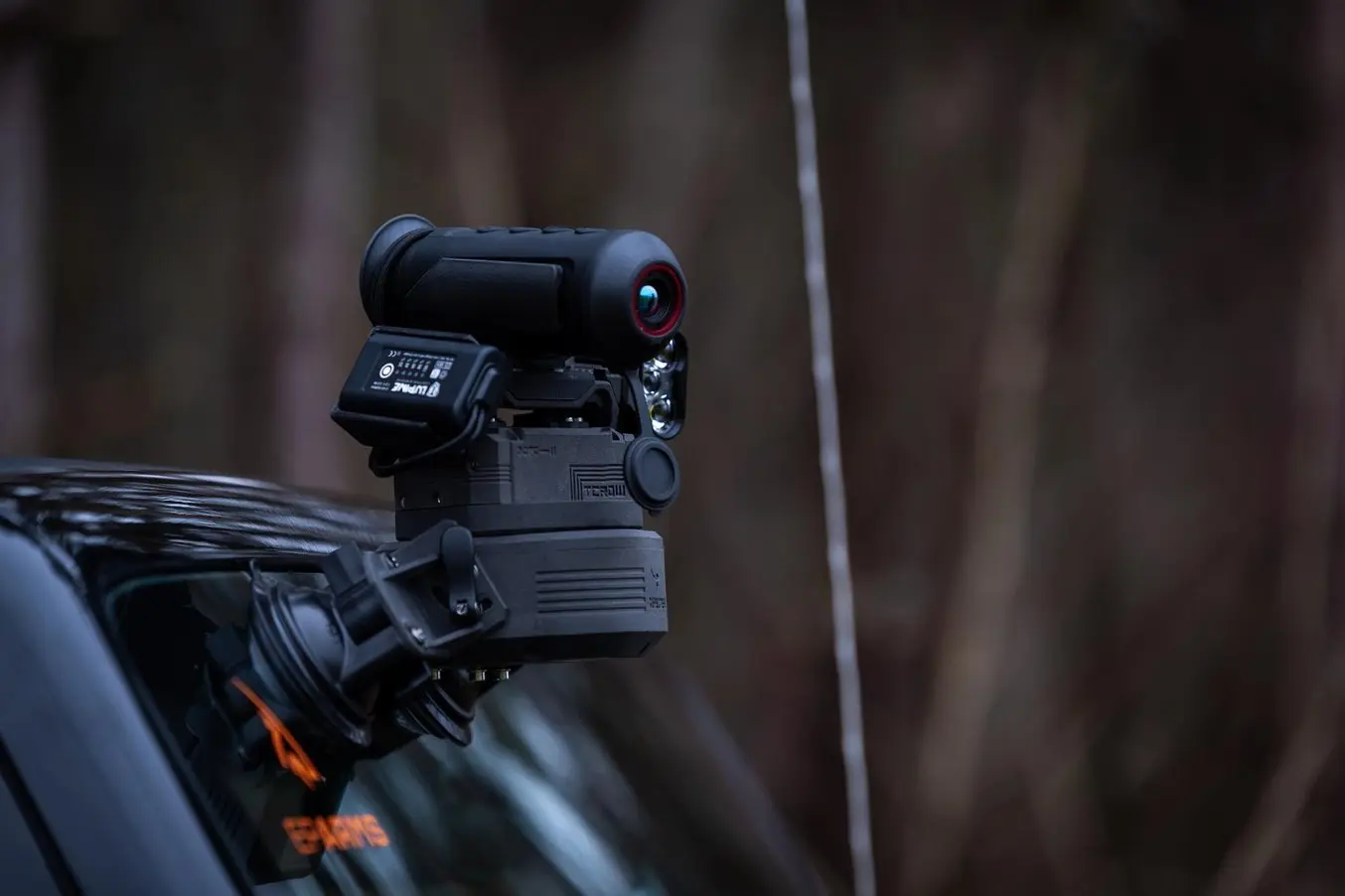
革新的なアイデアと熱い思いを持った多くの起業家たちが、市場のニーズのギャップを埋める様々な取り組みをしています。既製品の中に自らが思い描くような製品が見つからなかったMatthias Mähler氏は、暗視カメラや小型サーマルカメラ用の特殊な三脚の試作品を製作しようと考えました。
その際に彼が直面した主な課題の1つは、複雑な製品設計を実現する方法を見つけることでした。射出成形を選択していたら、金型製作だけでおそらく€100,000以上の初期投資が必要になっていたでしょう。この新製品が市場でどう受け止められるか定かではない中、小さなスタートアップ企業にとってこの投資はリスクになります。そこでMähler氏は開発・生産の両段階で3Dプリントを活用し、高額な投資を回避することに成功しました。彼が代表を務めるXSPECTERでは現在、初めての自社開発製品となるカメラ用三脚、T-Crow XRIIを内製し、独占代理店経由での販売に成功しています。
インタビューの中でMähler氏は、さまざまな3Dプリント技術を組み合わせて実製品を製造する方法、そして今の工程を選んだ理由を教えてくれました。
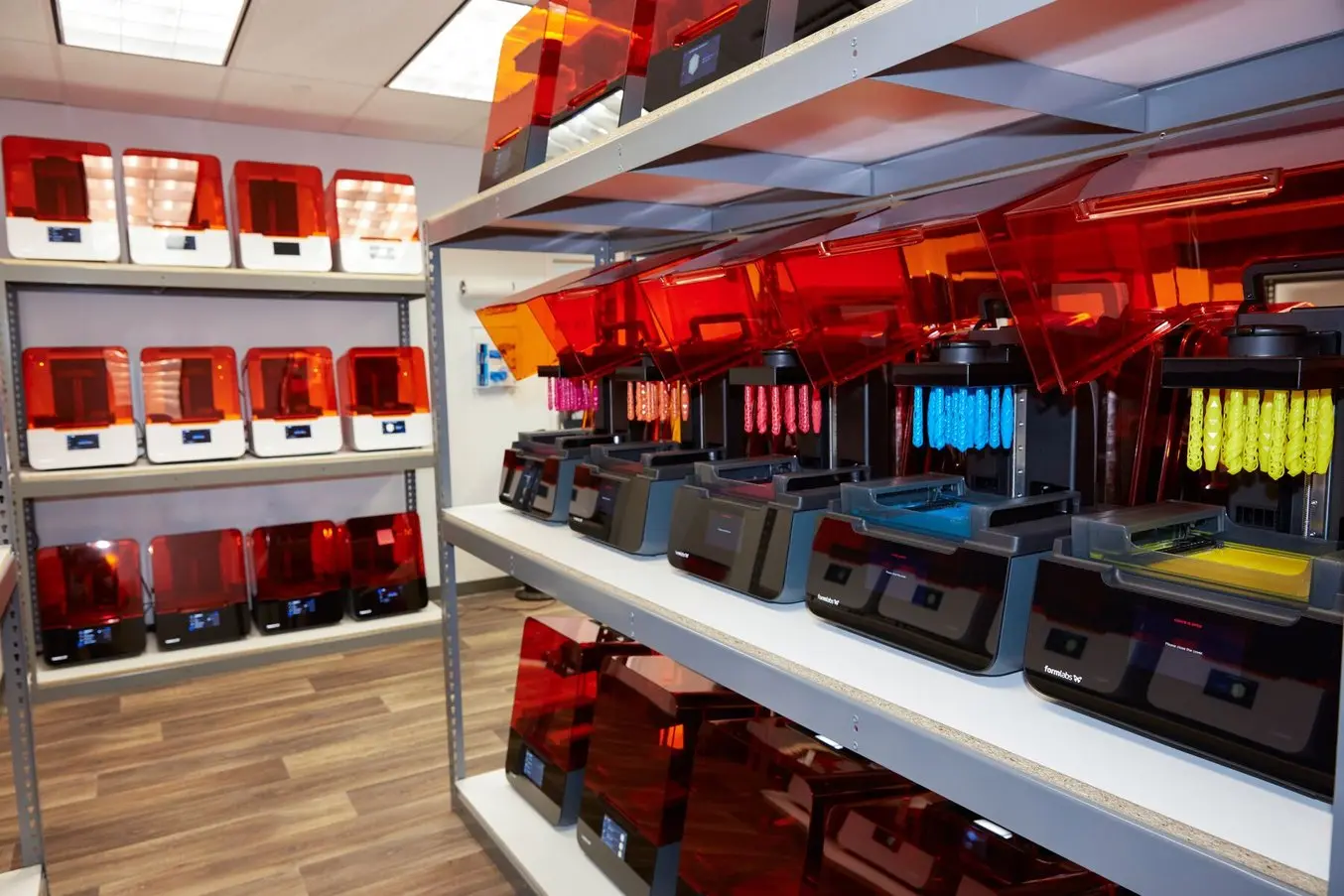
3Dプリント製の実製品用部品で少ロット量産とカスタム製造を行う方法
このウェビナーでは、カスタム製造と少量の実製品用部品生産を素早くコスト効率良く行う方法についてご紹介します。
360度自由自在に制御可能な三脚の開発
暗視カメラや小型のサーマルカメラは、狩猟や船舶、警備業界には欠かせない機器ですが、ガラスや窓ガラス越しでの使用ができないことが難点です。夜間に車を走らせる場合などは、窓の外側に直接カメラを取り付けなければならず、何度も車から出入りする必要があります。
趣味で狩猟を楽しむ起業家のMatthias Mähler氏は、自分の車の外側にカメラを取り付ける良い方法はないかと既製品を探し始めました。
やがて現在の市場には彼のニーズを満たすようなマウント機器や三脚がないことを知った彼は、自分で製作することを決断します。彼はまず、暗視カメラやサーマルカメラを安定して取り付けられ、かつ様々な制御が可能な三脚の試作品を作るところから始めました。サクションカップやマグネットで車のルーフや窓ガラスの外側に取り付けられるようなものが理想です。
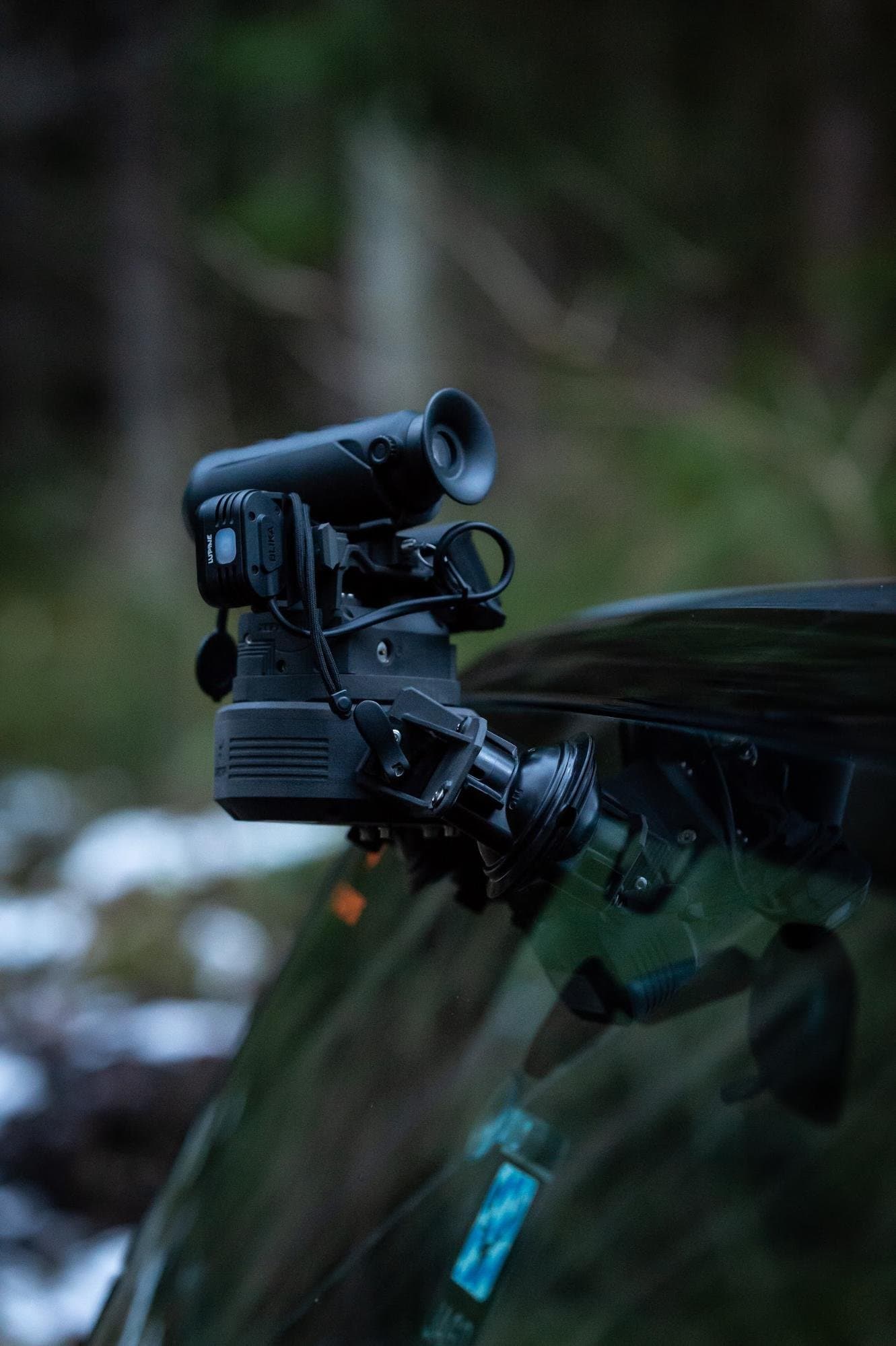
T-Crow XRIIを使って2種類のカメラを車の窓ガラス(左)とルーフ(右)に取り付けた様子。
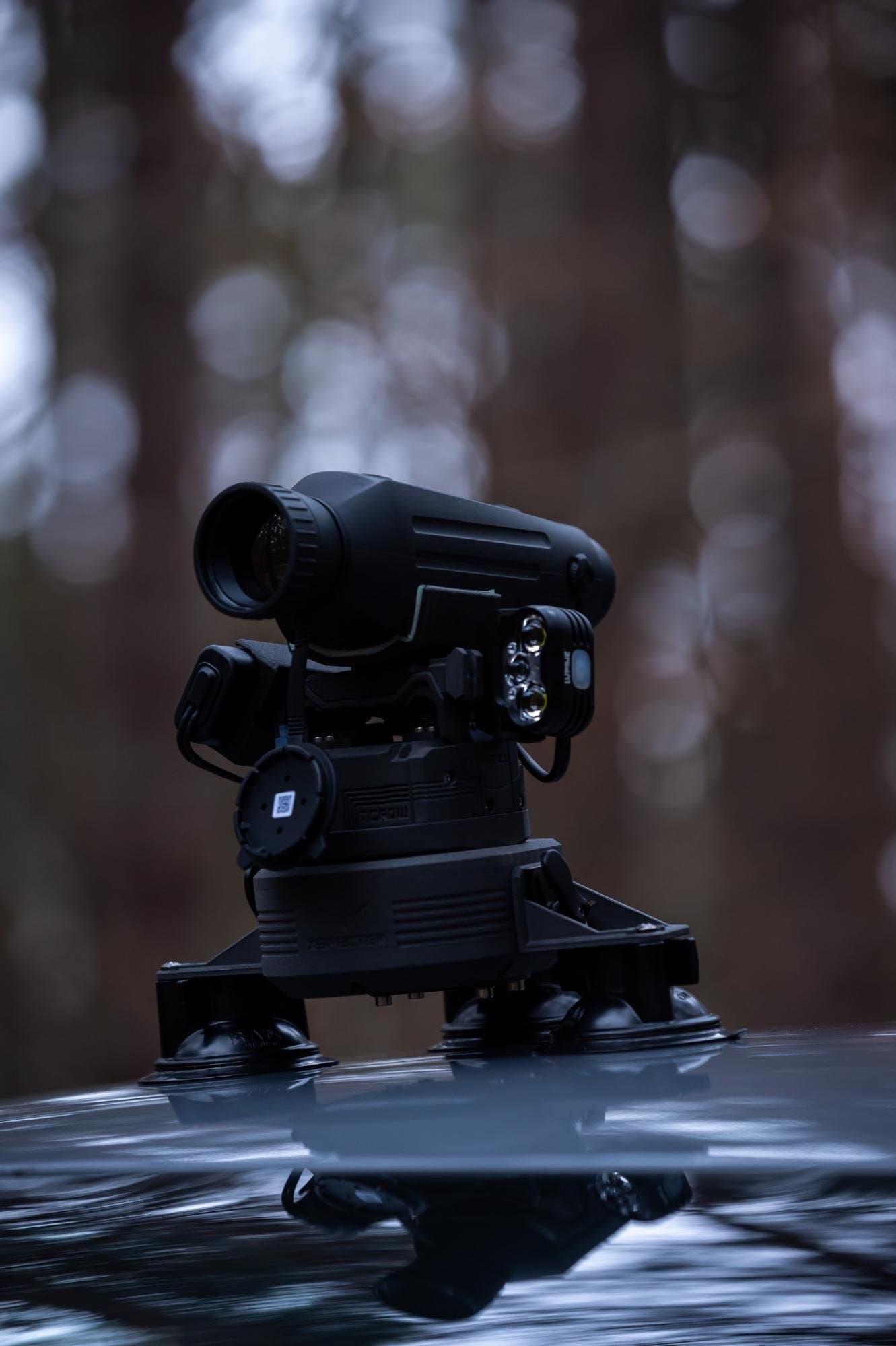
360度回転に加え、最大55度まで傾けることのできるXSPECTERのT-Crow三脚は、車の中から快適に動物や障害物を追跡することができます。
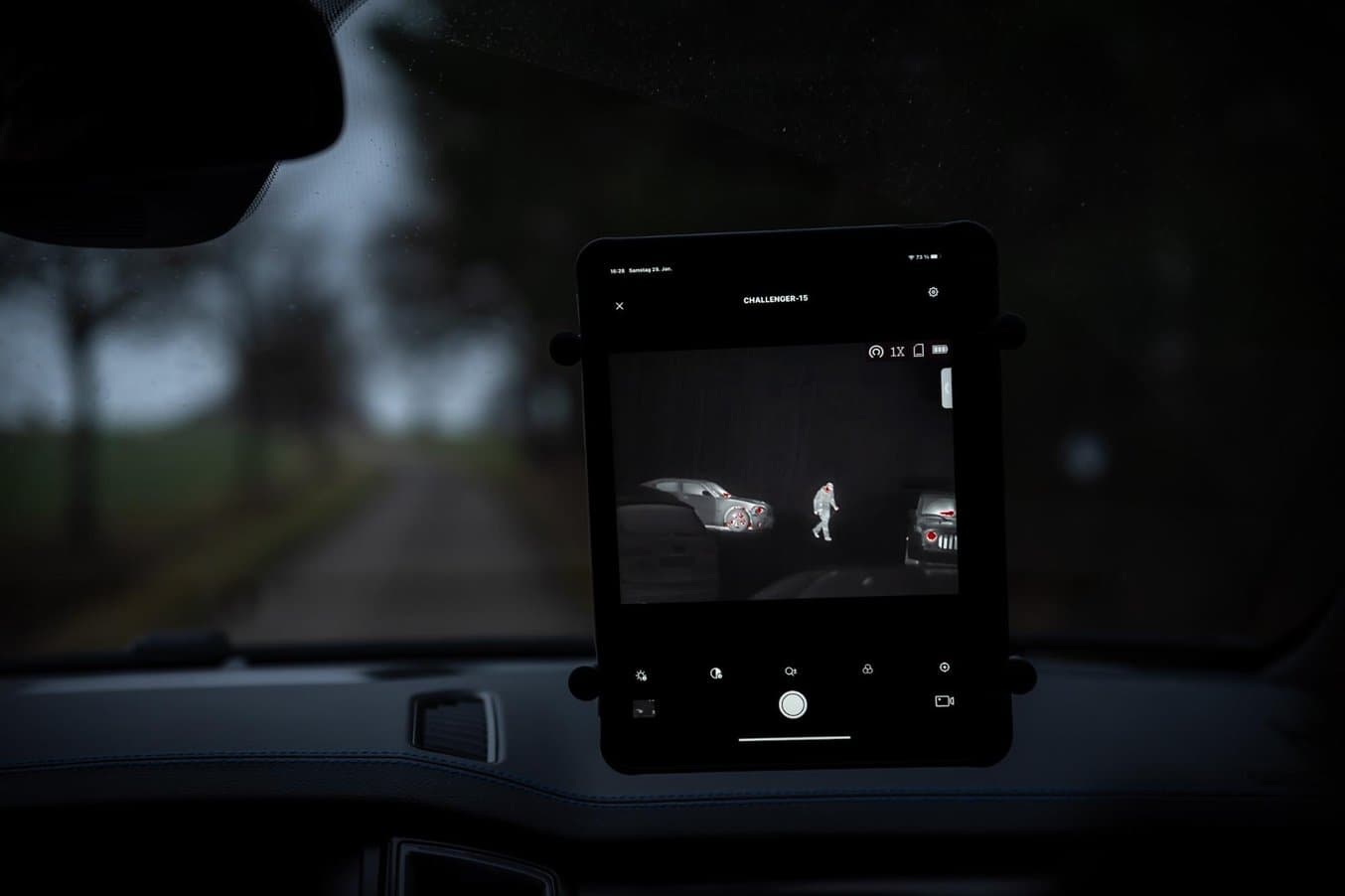
車の中に搭載されたタブレットでサーマル画像を確認できる。
試作品製作から連続生産へ
「製品の試作品製作ですでに3Dプリントを使用していたので、そのまま生産ラインにも組み込むことにしました。試作品製作の仕上がりに非常に満足したので、実製品も丸ごと様々な3Dプリント技術を組み合わせて作ることにしたんです。そして現在までずっと3Dプリントで製造しています」とMähler氏は言います。
Mähler氏はまず、3Dプリントの受託メーカーに依頼してFDM(熱溶解積層)方式で三脚の様々な試作品を繰り返し製作しました。大まかな製品設計が出来上がると、FormlabsのパートナーであるAMPro 3Dに連絡し、初めての連続生産に最適な3Dプリント方式と材料に関するアドバイスをもらいました。
「設計を全てSLS方式に合わせることにしました。SLS方式はサポート材なしで高度なディテールの表現が可能なので、実現できることが自然と増えるからです。試作品から連続生産への移行もほぼシームレスに行えました」
Matthias Mähler氏
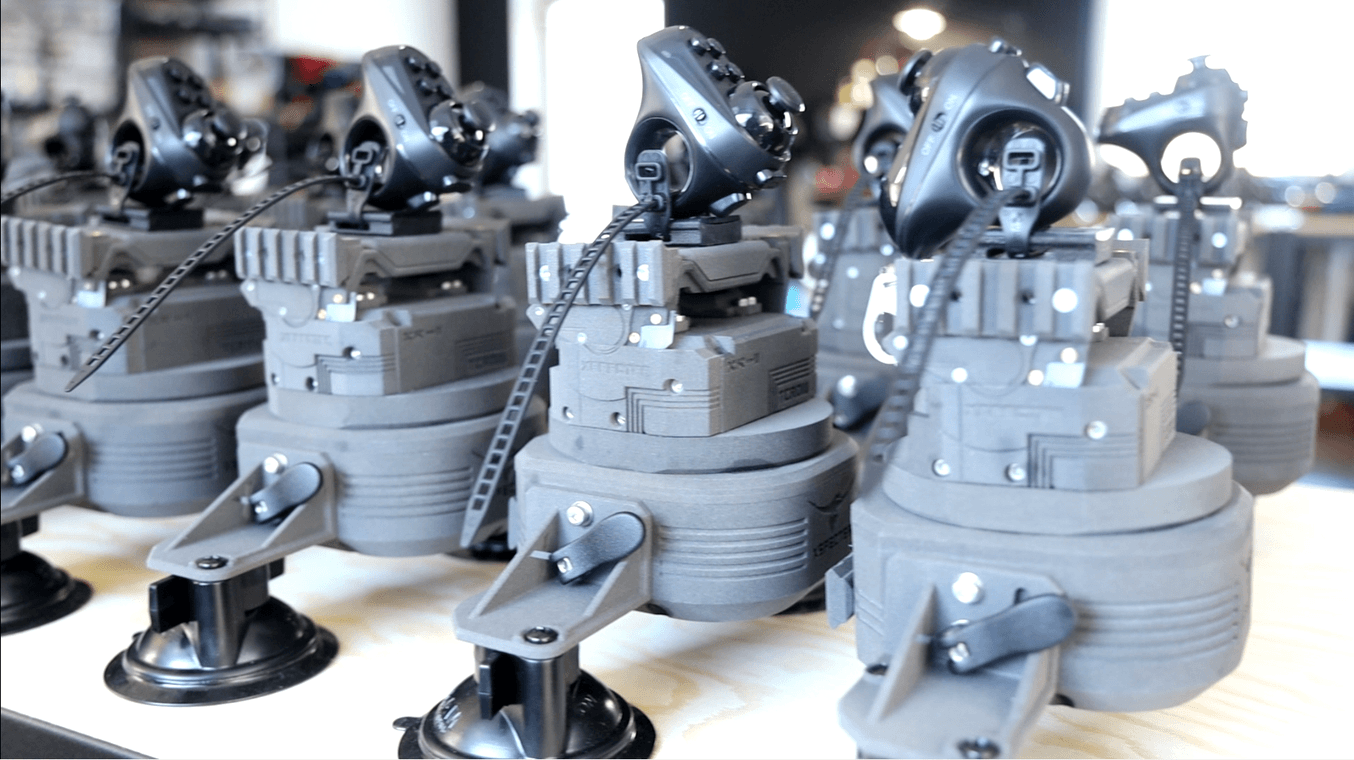
Nylon 12パウダーで造形したハウジングの上で出荷を待つT-Crowシリーズの三脚。
T-Crowの大量生産を開始するにあたり、FormlabsのSLS方式3DプリンタFuse 1と大容量SLA光造形方式3Dプリンタの
Form 3Lを選んだMähler氏は、こう言います。「コストパフォーマンスという点で、Formlabsのプリンタは現在市場に出ているプリンタの中で最高の製品だと思います」
Matthias Mähler氏
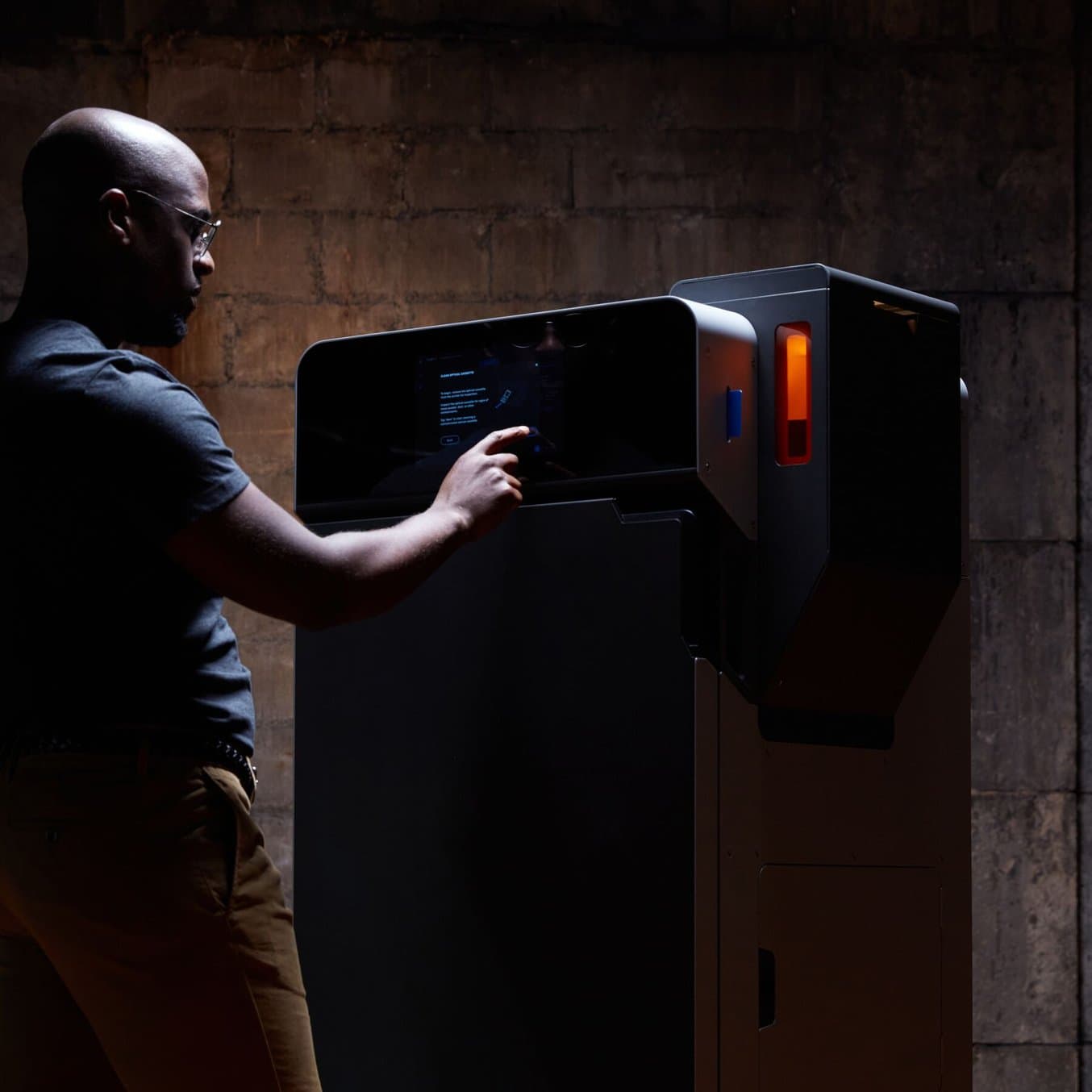
外注か内製か:SLS方式3Dプリントが適するケースとは?
本技術資料では、SLS方式3Dプリンタでの内製と、SLSプリント品を外注で製作した場合を比較し、SLS 3Dプリンタの導入の費用対効果の評価を行います。
SLA光造形方式とSLS方式を組み合わせた連続生産
T-Crowシリーズの生産にあたり、XSPECTERはSLA光造形方式とSLS方式を組み合わせて電子部品以外の部品はほぼ全て3Dプリントで製作し、三脚を完成させました。
ケースはFuse 1で製作したものです。FormlabsのSLS 3Dプリント用材料Nylon 12パウダーのおかげで、軽量かつ使用時の様々な状況にも耐えられるケースが出来上がりました。組立工程では溶接でねじ込み継手を取り付けますが、この時にも最適な材料でした。
心棒やギアは、Form 3Lを使ってDurableレジンでプリントしました。柔軟性がありながら耐衝撃性も備え、低摩擦という特性を持つDurableレジンにより、2軸制御を実現するために必要なしまりばめを実現することができました。
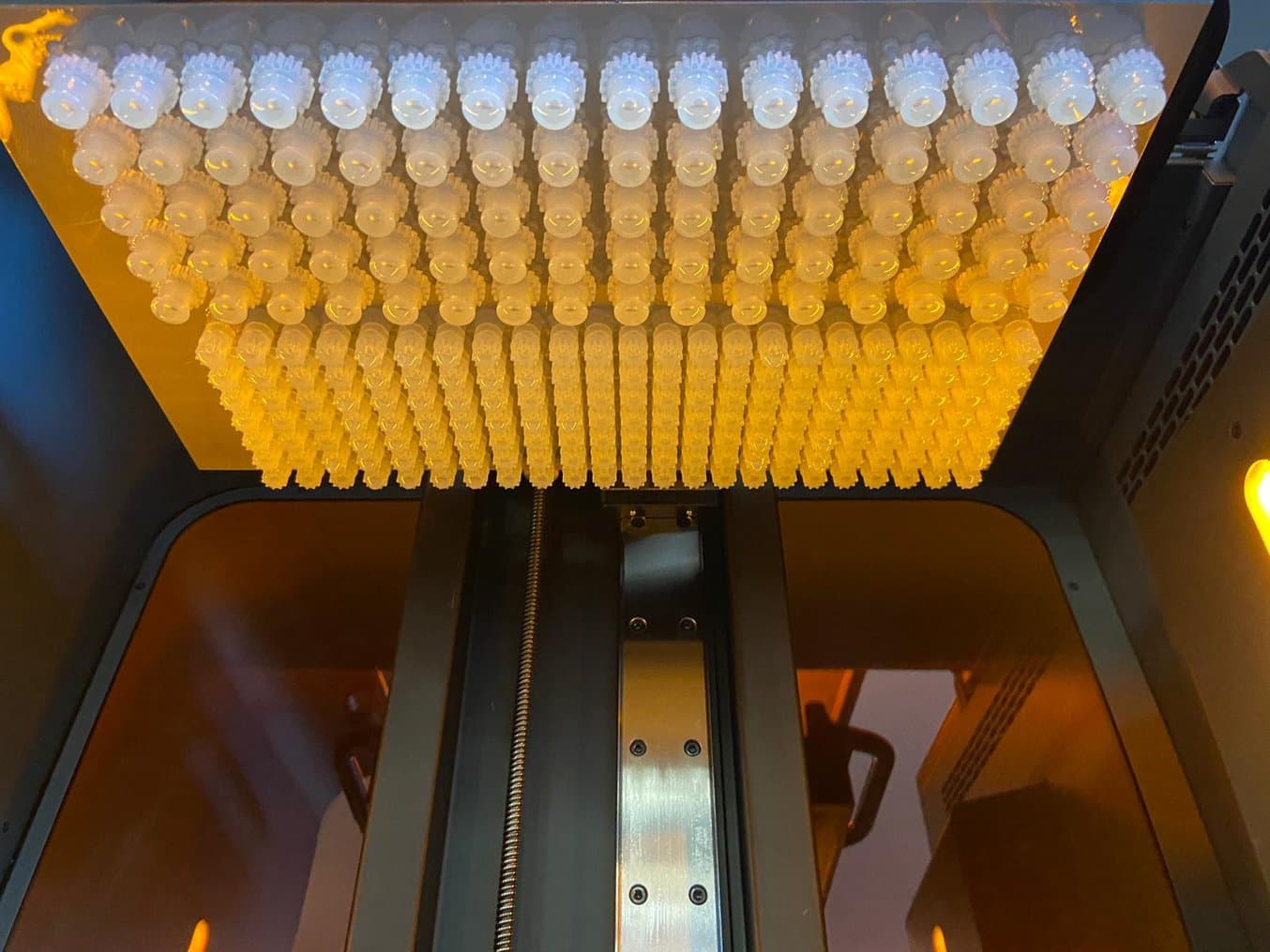
Form 3Lを使ってDurableレジンでプリントしたT-Crowのギア。
内製で各部品の3Dプリント・後処理まで完了したら、ねじ山ヘリサートを使って組み立て、わずか3日以内で出荷可能な状態の実製品が完成です。
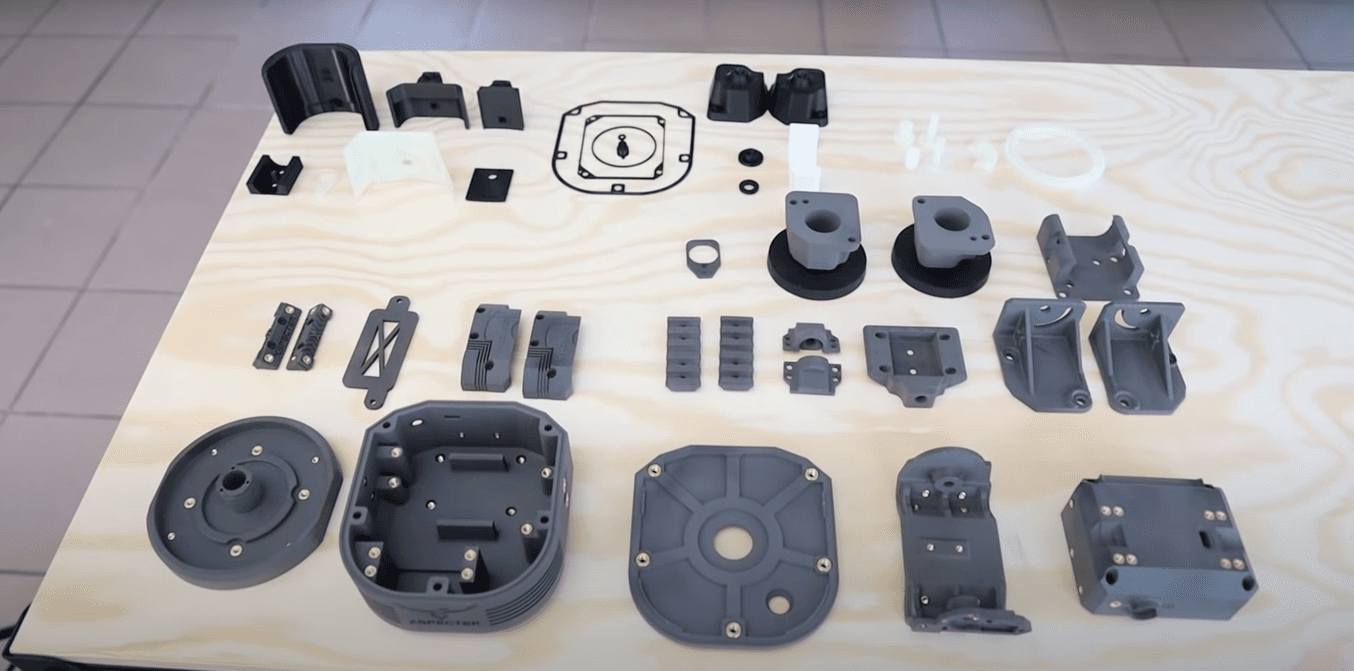
全て3Dプリントで製作した組み立て前のT-Crow全部品。
「今あるプリンタだけで、1年以内に出荷可能な状態のT-Crowを1500点製造できます」
とMähler氏は言います。3Dプリントならではの設計の自由さ
3Dプリンタを使った内製化に踏み切る決め手となったのは、3Dプリントで得られる設計の自由さでした。
「3Dプリントは、射出成形などの従来工法よりも単純に設計の自由度が高いんです。私たちは、製品は生き物だと思っています。設計に問題が見つかったりお客様からフィードバックをもらったりすることがあれば、それを反映した新しい設計を一夜にして作ることができます。これは他の方法では難しいことです」
Matthias Mähler氏
この種の設計変更は、三脚をどのようなカメラでも使えるようにするため、カメラの機種に応じたアダプタをカスタマイズしている時などに発生します。設計内容の変更は3Dプリント製のハウジングに直接反映することができるため、市場に新しいカメラが登場すると、Mähler氏はすぐに新種のカメラにも対応できるようT-Crowに変更を加えて販売します。
XSPECTERは、3Dプリントが持つ柔軟性のおかげで各部品を提供するサプライヤーの変更にも迅速に対応することができ、製造にかかる時間とコストを大幅に節約することができました。
一度、電源ボタンを供給してくれていたサプライヤーを別のサプライヤーに変えなければならないことがありました。サプライヤーが変わったことで電源ボタンの回路の開きを約2mm拡大しなければならなかったのですが、ほぼ一夜にして変更ができました」とMähler氏は教えてくれます。
射出成形の場合、金型製作だけでも費用見積りが€120,000と高額なうえ、型にこのような変更を加える場合は非常に時間とコストがかかります。
「3Dプリントは流行の先端になると思います。特にお客様の声を取り入れた製品を作りたいという企業にはうってつけです。現に私たちは、連続生産に入った今でも常にお客様からのフィードバックを受けて三脚を進化させています」
Matthias Mähler氏
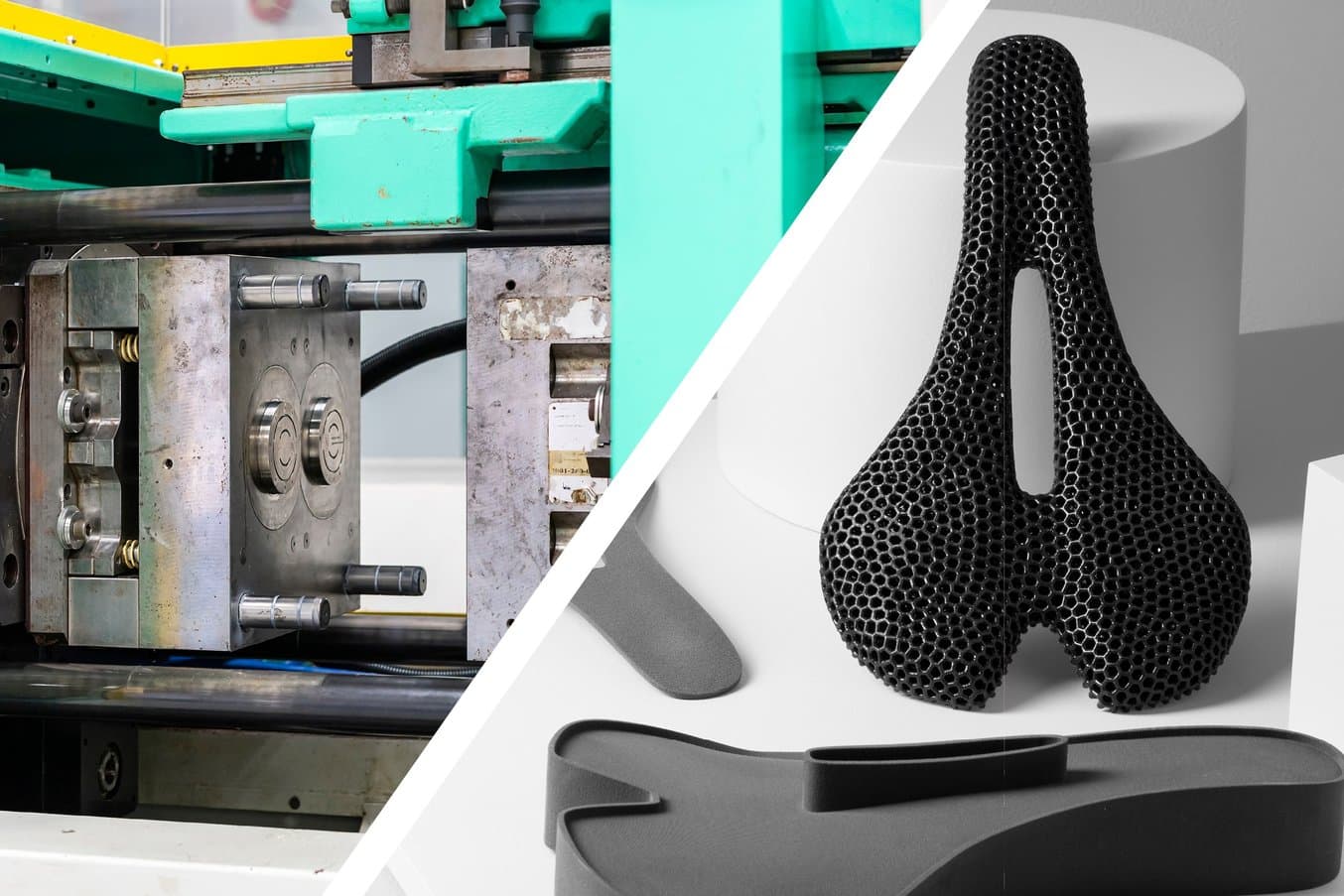
SLS 3Dプリント vs 射出成形:金型レスに切り替えるべき時は?
本技術資料では、実際のユースケースに基づいてコストの違いを解説するとともに、SLS方式3Dプリント、射出成形、またそれらの併用についてのガイドラインをご紹介します。
XPECTERは、3Dプリントを活用することで価格は低く抑えながらも射出成形と同等の品質を実現してきました。SLS方式で得られる柔軟性を大いに活かした戦略を展開するMähler氏は、製造に他の方法を用いることはしばらくは考えられないと言います。
Mähler氏は現在、Sea-Crowという新しいプロジェクトにも着手しています。T-Crow三脚の水中版で、サーチライトなど夜間の水中航行の補助となるような機能を搭載するべく、開発を続けています。