As 3D printing technologies — including 3D printing hardware, software, and materials — have rapidly evolved in recent years, 3D printers have transitioned from early adopter novelties to integral parts of design, engineering, and manufacturing workflows in every industry.
Fused deposition modeling (FDM), stereolithography (SLA), and selective laser sintering (SLS) are the three most popular types of 3D printers on the market. Innovation has accelerated over the last decade and all three 3D printing technologies are now accessible to more businesses, but choosing between the various competing 3D printing solutions can be difficult.
In this comprehensive buyer's guide, we take a closer look at FDM, SLA, and SLS (also known as filament, resin, and powder) 3D printers, and how they compare in terms of print quality, materials, applications, workflow, speed, costs, and more, to help you decide which technique is ideal for your business.

How to Choose a 3D Printing Technology
Having trouble finding the best 3D printing technology for your needs? In this video guide, we compare FDM, SLA, and SLS technologies across popular buying considerations.
What Is FDM 3D Printing?
Fused deposition modeling (FDM), also known as fused filament fabrication (FFF), or filament 3D printing, is the most widely used type of 3D printing at the consumer level, and the most recognizable for the average layperson, who may associate the broader concept of 3D printing with this ‘hot-glue gun’ method of building parts.
FDM 3D printers are many people’s first introduction to 3D printing technology; they are the most common type of 3D printer in K-12 schools and even in many university makerspaces. In design, engineering, and manufacturing businesses, FDM printers are mostly relied upon for quick proof of concept models that can be agreed upon by design teams before moving on to more functional prototypes.
FDM 3D printers come in a wide range of sizes and prices. The simplicity of the printing technology and workflow can make FDM 3D printing an attractive low-commitment option for those looking to get started with 3D printing. However, FDM printers often trade simplicity and affordability for part quality and performance — and for those looking for functional performance, watertightness, isotropy, or smooth surfaces, SLA and SLS 3D printers are far superior alternatives.
What Is SLA 3D Printing?
Stereolithography (SLA) 3D printing was the world’s first 3D printing technology, invented in the 1980s. Despite this, SLA has taken longer than FDM 3D printing to achieve widespread adoption and awareness due to typically higher prices and a slightly more complex printing process.
Stereolithography, or resin 3D printing, refers to a process in which a light source cures liquid resin, hardening it layer by layer. This light source was originally a laser, but, more recently, has been replaced by a digital light projector in DLP 3D printers or light emitting diodes (LEDs) in MSLA or LCD 3D printers. In essence, all resin 3D printers today are stereolithography 3D printers, though the term has been most commonly associated with 3D printers that cure resin with a laser.
SLA 3D printers produce parts with smoother surface finishes, tighter tolerances, and higher dimensional accuracy than other 3D printing technologies. These printers are ideally suited for functional prototyping (because they can closely match the look and performance of injection-molded parts) as well as for creating end-use products and tooling due to their excellent surface finish and extremely diverse sets of material properties.
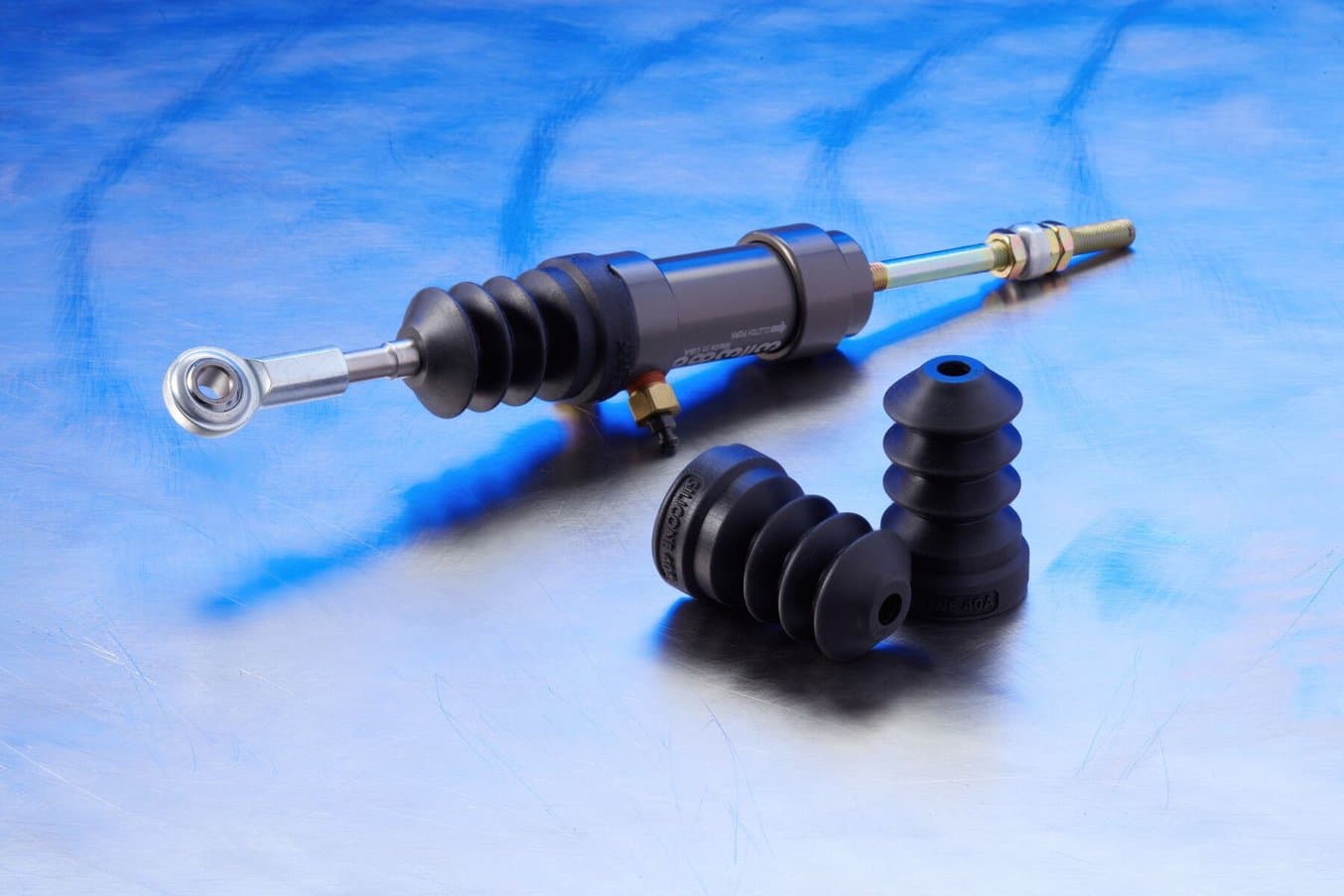
One of SLA technology’s biggest advantages is the range of materials available and the applications they enable. This clutch boot was printed on a Formlabs Form 4 MSLA 3D printer in Silicone 40A Resin.
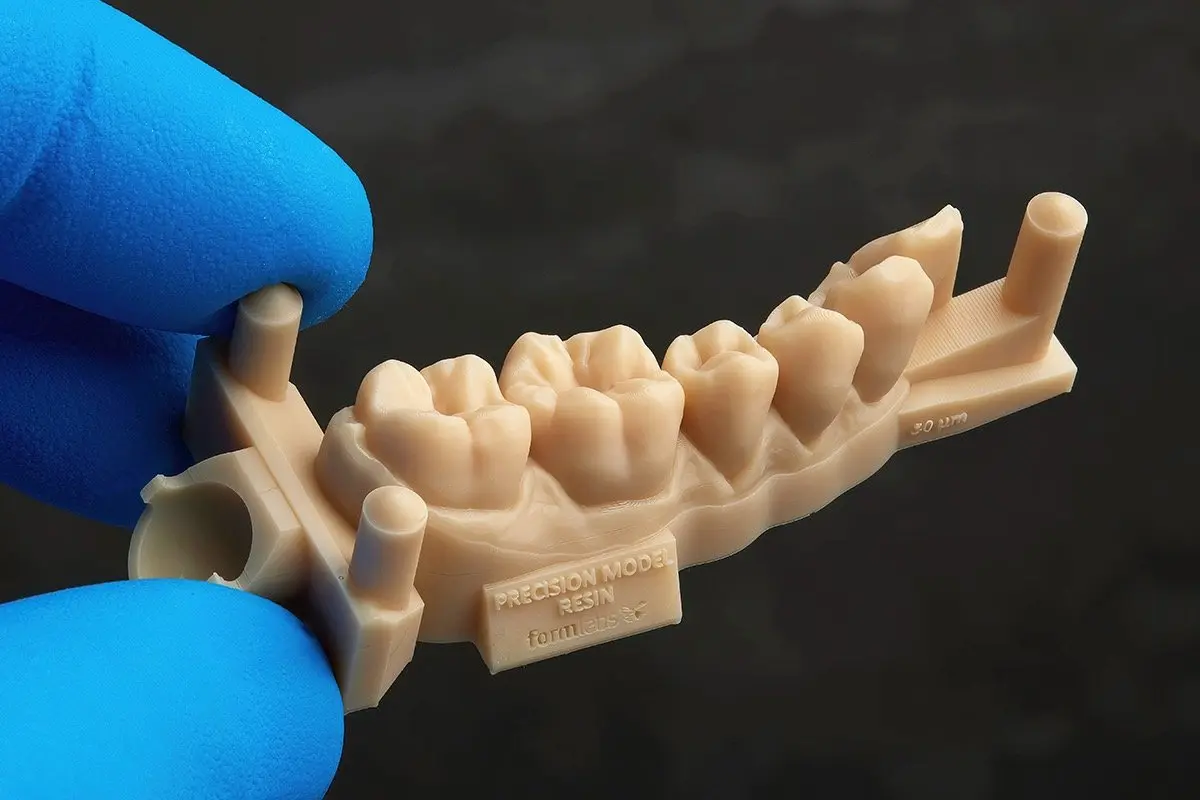
SLA parts have smooth surfaces, extremely tight tolerances, and superior dimensional accuracy — which make it an ideal technology for demanding applications, like restorative models in dentistry.
SLA materials are uniquely formulated, as opposed to the industry-standard thermoplastics used in FDM and SLS 3D printing. One of the main benefits of SLA lies in this material versatility — manufacturers have created innovative SLA photopolymer resin formulations with a wide range of optical, mechanical, and thermal properties to match those of standard, engineering, and industrial thermoplastics, as well as for specific applications requiring specialized features like flame retardancy, electrostatic dissipation, or biocompatibility. This wide range of properties, combined with the accuracy and surface finish of SLA parts, enables applications in every industry, including aerospace, automotive, consumer goods manufacturing, healthcare, dentistry, and more.
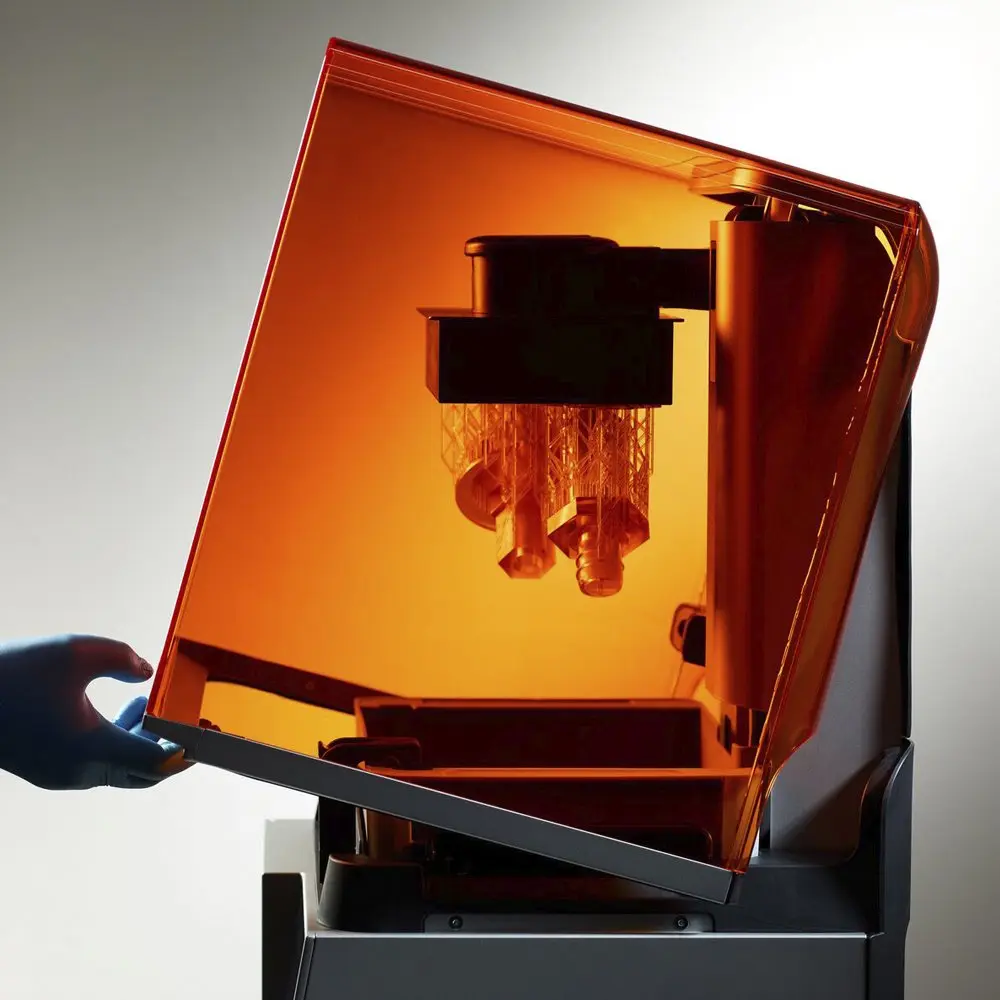
Introduction to 3D Printing With Desktop Stereolithography (SLA)
Looking for a 3D printer to produce high resolution models fast? Download our white paper to learn how SLA printing works and why it's the most popular 3D printing process for creating parts with incredible detail, high dimensional accuracy, and superior surface finish.
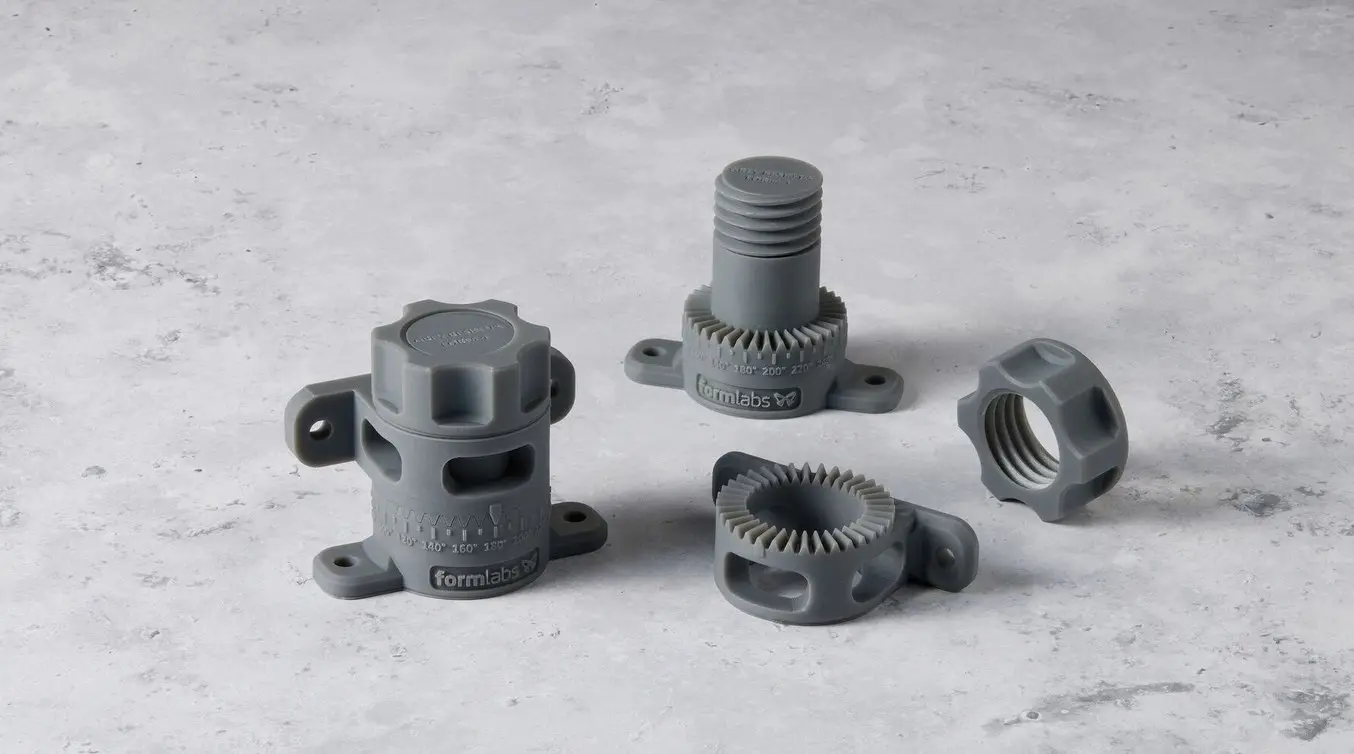
Request a Free Sample Part
See and feel Formlabs quality firsthand. We’ll ship a free SLA sample part to your office.
What Is SLS 3D Printing?
Selective laser sintering (SLS) is the most common additive manufacturing technology for industrial applications, trusted by engineers and manufacturers across different industries for its ability to produce strong, functional parts.
SLS 3D printers use a high-powered laser to fuse small particles of polymer powder. The unfused powder supports the part during printing and eliminates the need for dedicated support structures. This makes SLS 3D printing ideal for complex geometries, including interior features, undercuts, thin walls, and negative features, as well as enabling higher-volume production applications — the self-supporting print bed allows parts to ‘nest,’ so that customers can fully pack the build chamber and reach production volumes, even with only one printer.
Parts produced with SLS printing have excellent mechanical characteristics with strength resembling that of injection-molded parts. The most common SLS material is nylon, a popular engineering thermoplastic with excellent mechanical properties. Nylon is lightweight, strong, and flexible, as well as stable against impact, chemicals, heat, UV light, water, and dirt. Other popular SLS 3D printing materials include nylon composites, polypropylene (PP), and flexible TPU.
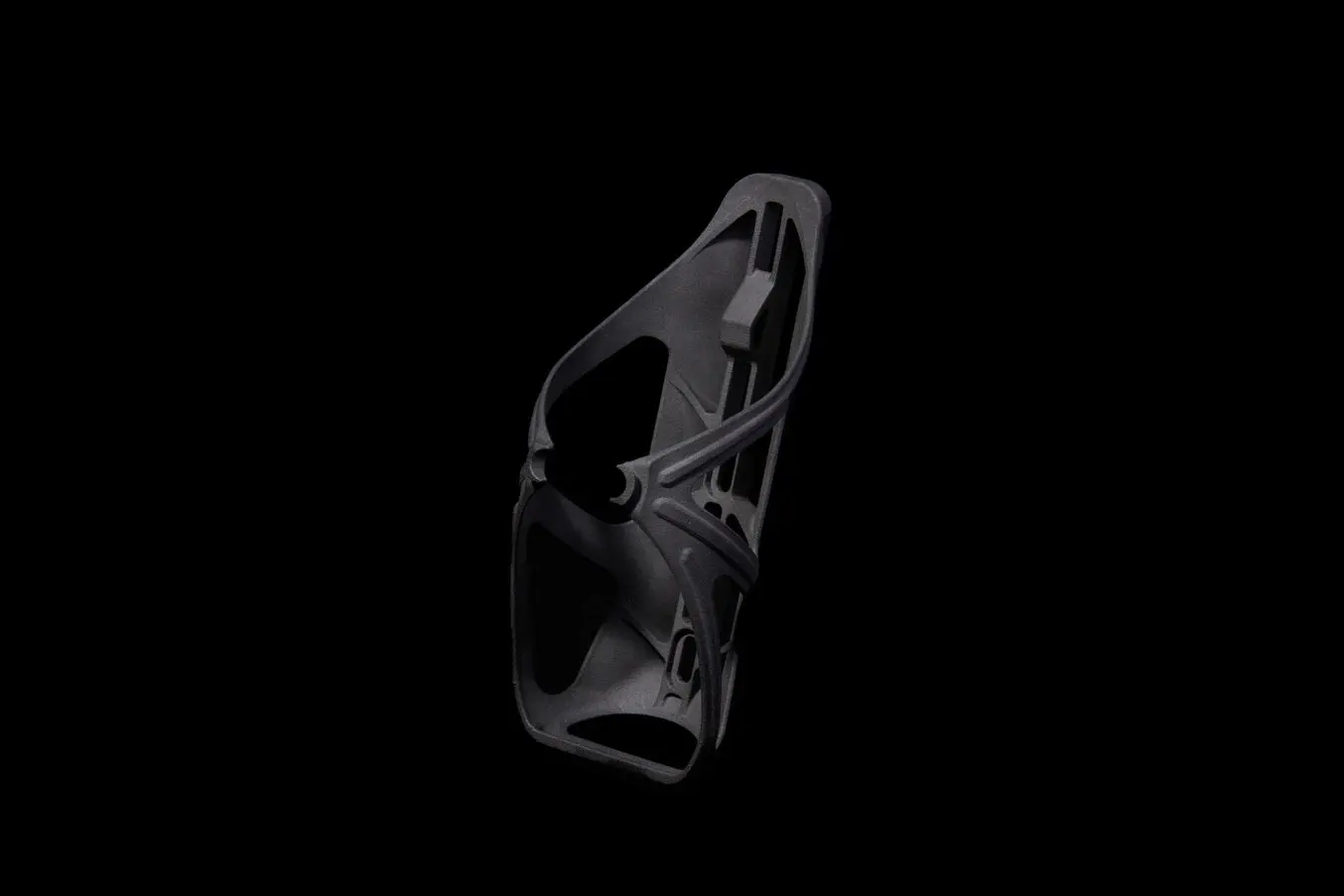
SLS 3D printing is ideal for functional prototyping and is a cost-effective alternative to injection molding for low-volume or bridge manufacturing.
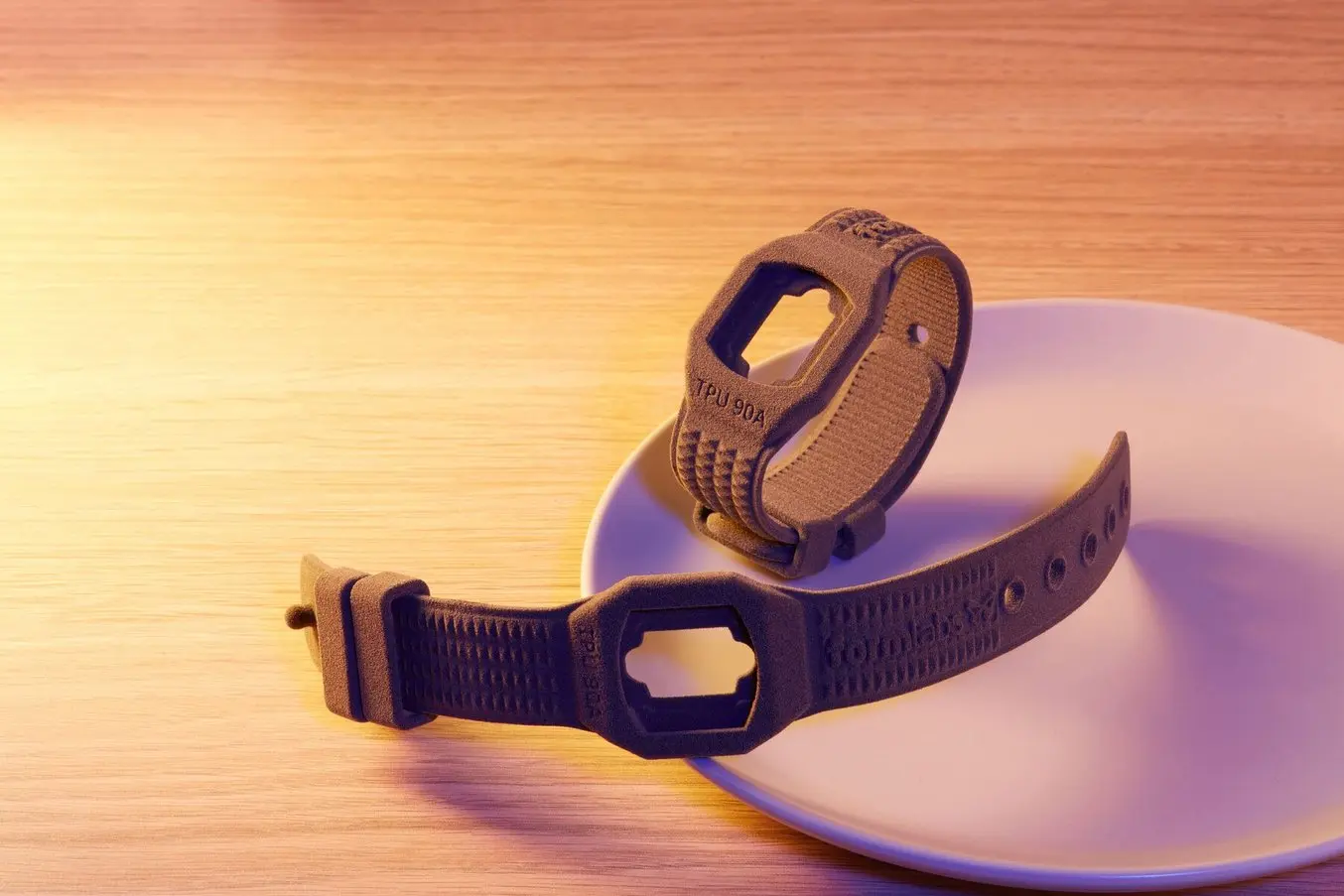
SLS 3D printing technology makes the production of end-use goods possible, even in flexible materials like this watch strap printed in TPU 90A Powder on the Fuse 1+ 30W SLS 3D printer.
The combination of low cost per part, high productivity, and established materials make SLS a popular choice among engineers for functional prototyping, and a cost-effective alternative to injection molding for low-volume or bridge manufacturing. As the SLS workflow and entry price point have become much more accessible in recent years, more and more businesses are bringing SLS in-house to shore up their supply chain and speed up prototyping to production workflows.
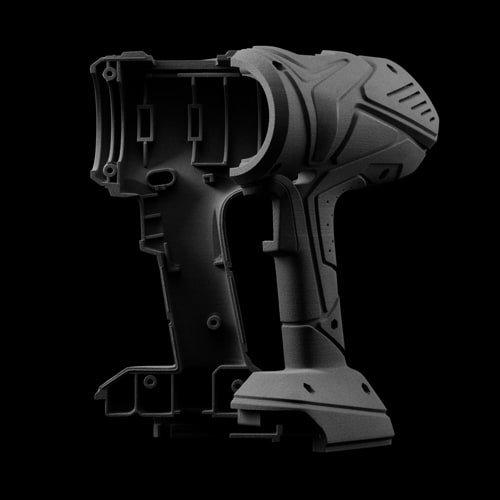
Introduction to Selective Laser Sintering (SLS) 3D Printing
Looking for a 3D printer to create strong, functional parts? Download our white paper to learn how SLS printing works and why it's a popular 3D printing process for functional prototyping and end-use production.
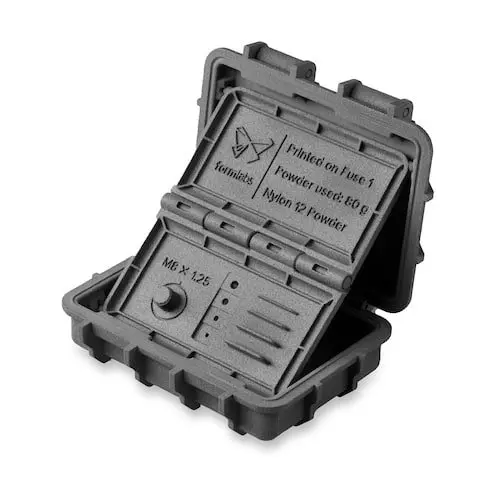
Request a Free Sample Part
See and feel Formlabs SLS quality firsthand. We’ll ship a free SLS sample part to your office.
FDM vs. SLA vs. SLS: Compare Filament, Resin, and Powder 3D Printers
Most businesses that have invested in 3D printing use more than one type of 3D technology. Each has its own advantages and disadvantages, and the most complete workflow is typically one that can treat each technology as a tool to be used in different situations.
For businesses looking to choose one type of technology for their unique needs, several factors should be considered. The following is a summary of the major factors to consider when choosing between FDM, SLA, and SLS 3D printers.
Fused Deposition Modeling (FDM) | Stereolithography (SLA) | Selective Laser Sintering (SLS) | |
---|---|---|---|
Resolution | ★★☆☆☆ | ★★★★★ | ★★★★☆ |
Accuracy | ★★★★☆ | ★★★★★ | ★★★★★ |
Surface Finish | ★★☆☆☆ | ★★★★★ | ★★★★☆ |
Throughput | ★★★☆☆ | ★★★★☆ | ★★★★★ |
Complex Designs | ★★★☆☆ | ★★★★☆ | ★★★★★ |
Ease of Use | ★★★★★ | ★★★★★ | ★★★★☆ |
Pros | Low-cost consumer machines and materials Fast and easy for simple, small parts | Great value High accuracy Smooth surface finish Fast printing speeds Range of functional applications | Strong functional parts Design freedom No need for support structures |
Cons | Low accuracy Low details Limited design freedom | Some materials are sensitive to long exposure to UV light | Slightly rough surface finish Limited material options |
Applications | Concept modeling Rapid prototyping Functional prototyping Manufacturing aids | Concept modeling Rapid prototyping Functional prototyping Rapid tooling Manufacturing aids Low volume, bridge, or custom manufacturing Dental models and appliances Medical models and medical devices Jewelry prototyping and casting Models and props | Rapid prototyping Functional prototyping Low volume, bridge, or custom manufacturing Long-lasting, durable manufacturing aids Medical devices, prosthetics, and orthotics |
Print Volume | Up to 300 x 300 x 600 mm (desktop and benchtop 3D printers) | Up to 353 x 196 x 350 mm (desktop and benchtop 3D printers) | Up to 165 x 165 x 300 mm (benchtop industrial 3D printers) |
Materials | Standard thermoplastics, such as ABS, PLA, and their various blends. | Varieties of resin (thermosetting plastics). Standard, engineering (ABS-like, PP-like, flexible, heat-resistant, rigid glass-filled), castable, and dental and medical (biocompatible). Pure silicone and ceramic. | Engineering thermoplastics. Nylon 12, nylon 11, glass or carbon-filled nylon composites, polypropylene, TPU (elastomer). |
Training | Minor training on build setup, machine operation, and finishing; moderate training on maintenance. | Plug and play. Minor training on build setup, maintenance, machine operation, and finishing. | Moderate training on build setup, maintenance, machine operation, and finishing. |
Facility Requirements | Air-conditioned environment or preferably custom ventilation for desktop machines. | Desktop and benchtop machines are suitable for an office environment. | Workshop environment with moderate space requirements for benchtop systems. |
Ancillary Equipment | Support removal system for machines with soluble supports (optionally automated), finishing tools. | Washing station and post-curing station (both can be automated), finishing tools. | Post-processing stations for powder management and part cleaning. |
Equipment Costs | Budget FDM printers and 3D printer kits start at around $200. Professional desktop FDM printers range from $2,000 to $8,000, and industrial systems are available from $15,000. | Low-cost resin 3D printers are available for $200 to $1000, professional SLA 3D printers are in the $2,500 to $10,000 range, and large-format resin 3D printers are in the $5,000 to $25,000 range. | Benchtop industrial SLS 3D printers start just under $30,000 for the printer and $60,000 for the entire ecosystem, including powder management and cleaning stations. Traditional industrial SLS printers start at around $200,000. |
Material Costs | $50-$150/kg for most standard filaments, and $100-$200/kg for support materials or engineering filaments. | $100-$200/L for most standard and engineering resins, $200-$500/L for biocompatible materials. | $100/kg for nylon. SLS requires no support structures, and unfused powder can be reused, which lowers material costs. |
Labor Needs | Manual support removal (can be mostly automated for industrial systems with soluble supports). Lengthy post-processing is required for a high-quality finish. | Washing and post-curing (both can be mostly automated). Simple post-processing to remove support marks. | Simple and semi-automated workflow for cleaning parts and recovering powder. |
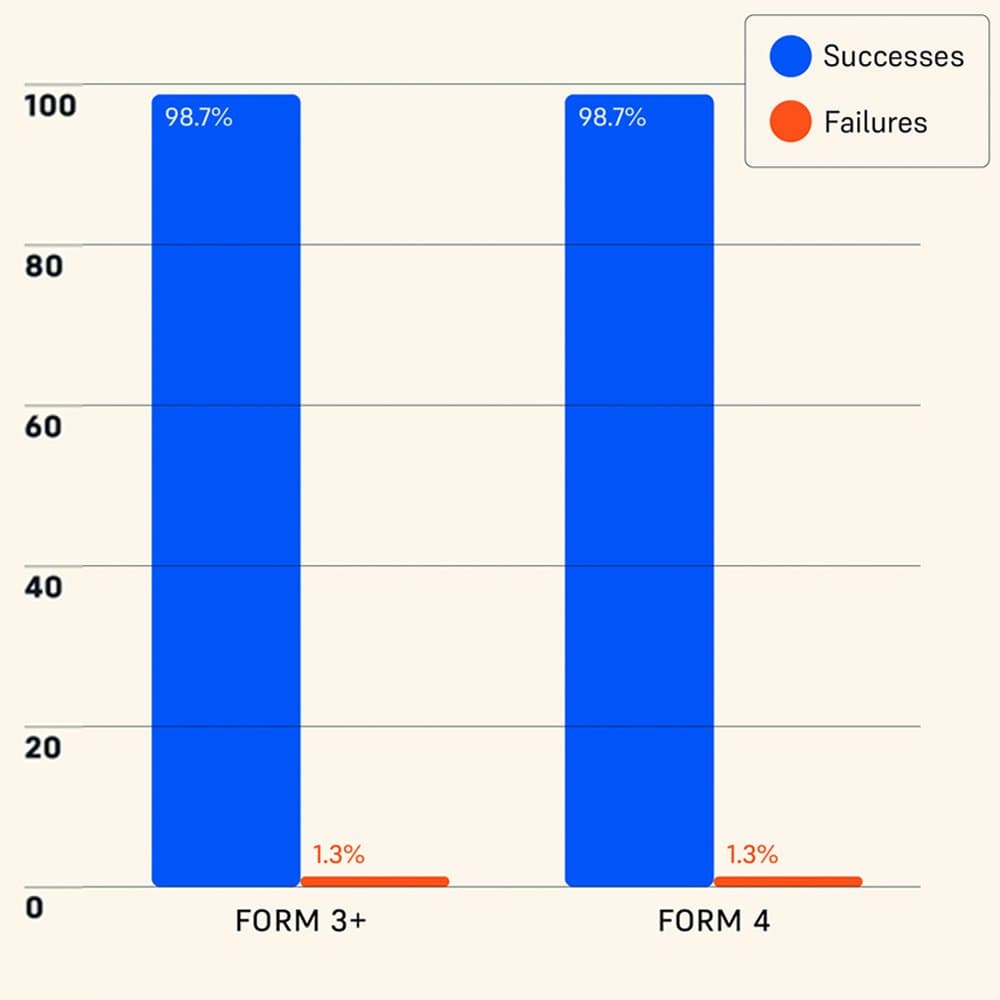
Independently Tested Reliability of Form 4 and Other Resin 3D Printers
Formlabs Form 4 was measured to have a 98.7% print success rate by an independent global leader in product testing. Read a complete description of the test methodology and see the results in our white paper.
Resolution
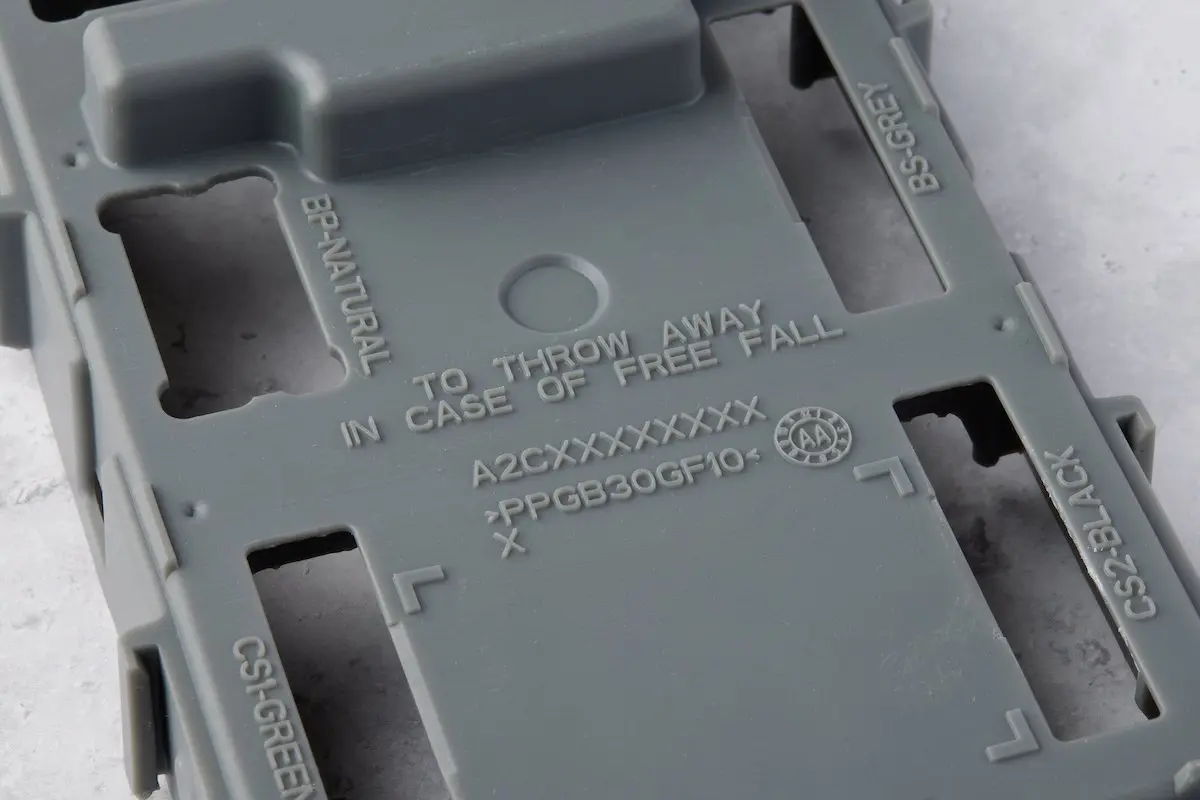
SLA 3D printed parts, like this enclosure printed on Formlabs’ Form 4, have sharp edges, sleek surfaces, and minimal visible layer lines.
Resolution is a commonly misunderstood specification, and the ways to measure it often change between manufacturers and different 3D printing processes. It typically refers to the smallest features, finest degree of detail, or level of intricate surface texturing a 3D printer can reproduce, and can be measured by metrics like minimum feature size. The mechanics of the three different 3D printing processes (fused deposition modeling (FDM), stereolithography (SLA) or selective laser sintering (SLS)) have a large impact on part resolution.
FDM 3D printers form layers by extruding molten plastic through a nozzle in a prescribed shape, then moving up and depositing the next layer on top. The resolution of FDM 3D printed parts is therefore dependent on the nozzle’s size, the material properties of the molten material, and the control with which the motor can move the nozzle in the XY axes as well as the Z axis between layers. FDM 3D printers can typically create around 0.8 mm thick walls, and embossed or engraved details have to be around 0.6 mm wide and 2 mm high to be visible.
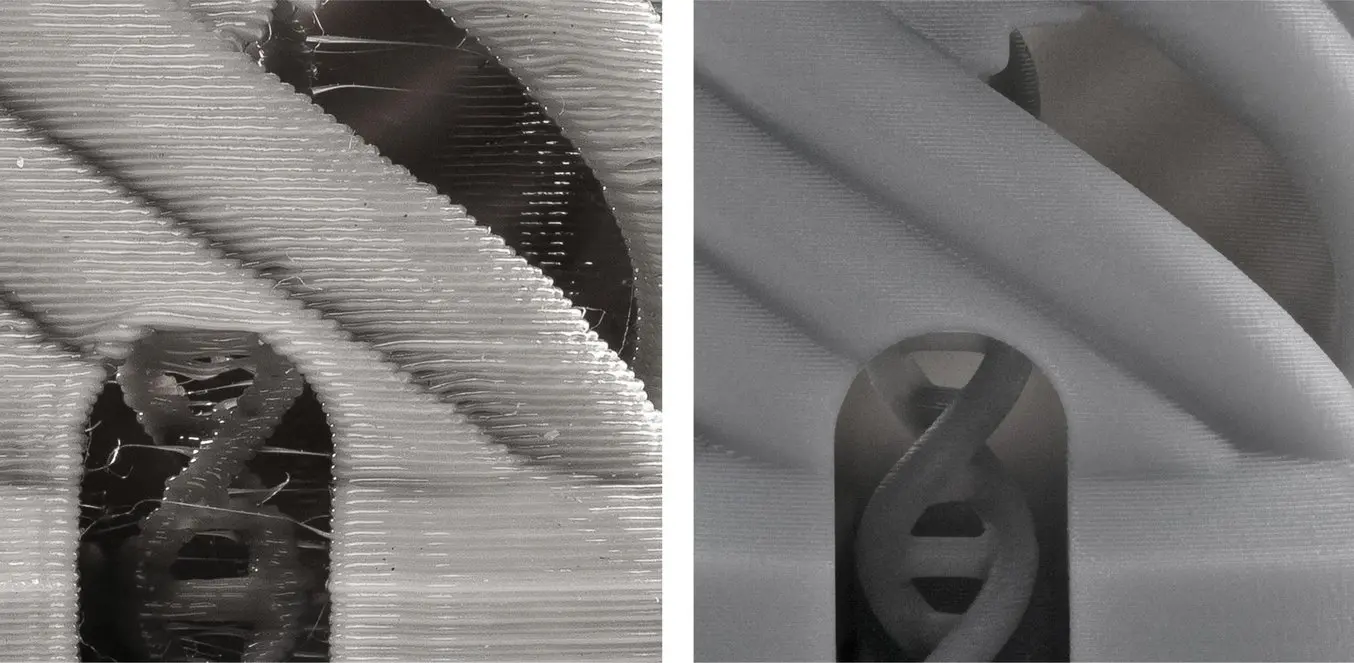
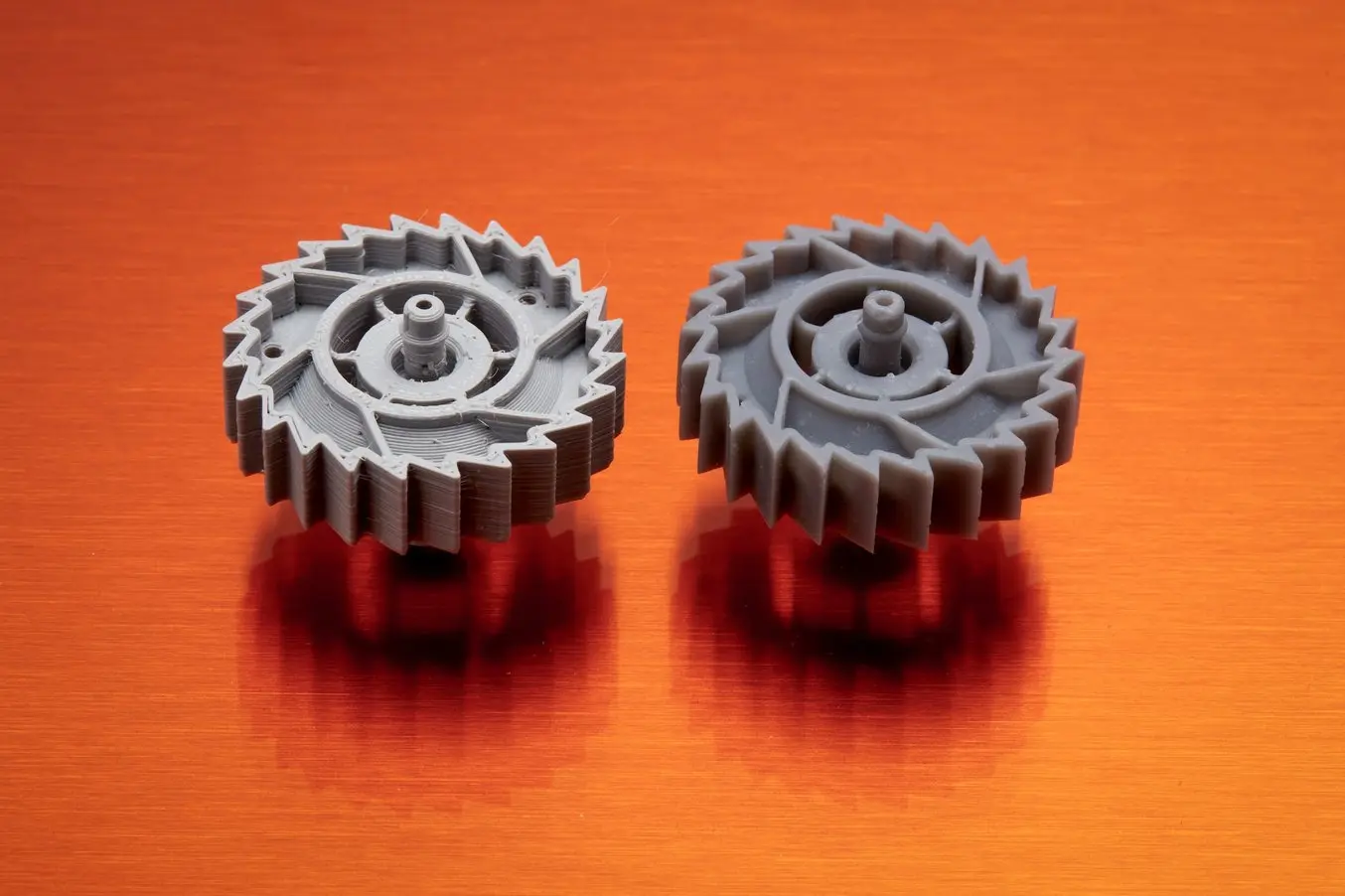
FDM printers struggle with complex designs or parts with intricate features (left), compared to SLA printers (right).
SLA 3D printers form parts by using a light source (a laser, digital light projector, LEDs) to cure liquid resin one layer at a time. The resolution of an SLA 3D printer depends on many factors, including the type of light source it uses and the scattering, bleeding, and polymerization characteristics of the resin, but generally can be thought of as the ability to specifically trace a part in the XY planes combined with the minimum Z-axis layer height.
Even with differences in the type of light source used in various SLA 3D printers, the technology has the highest resolution when compared to FDM or SLS 3D printing. Whether the light source is a laser or digital projector or LEDs with light controlled by a masking LCD screen, the light is capable of being very precisely directed at the liquid resin. SLA 3D printed resin parts display this superior resolution through their fine features, intricate surface textures or perfect smoothness, and high dimensional accuracy. Professional SLA 3D printers, like Formlabs' Form 4, can produce walls as thin as 0.2 mm, and embossed and engraved details as intricate as 0.1 mm and 0.15 mm respectively.
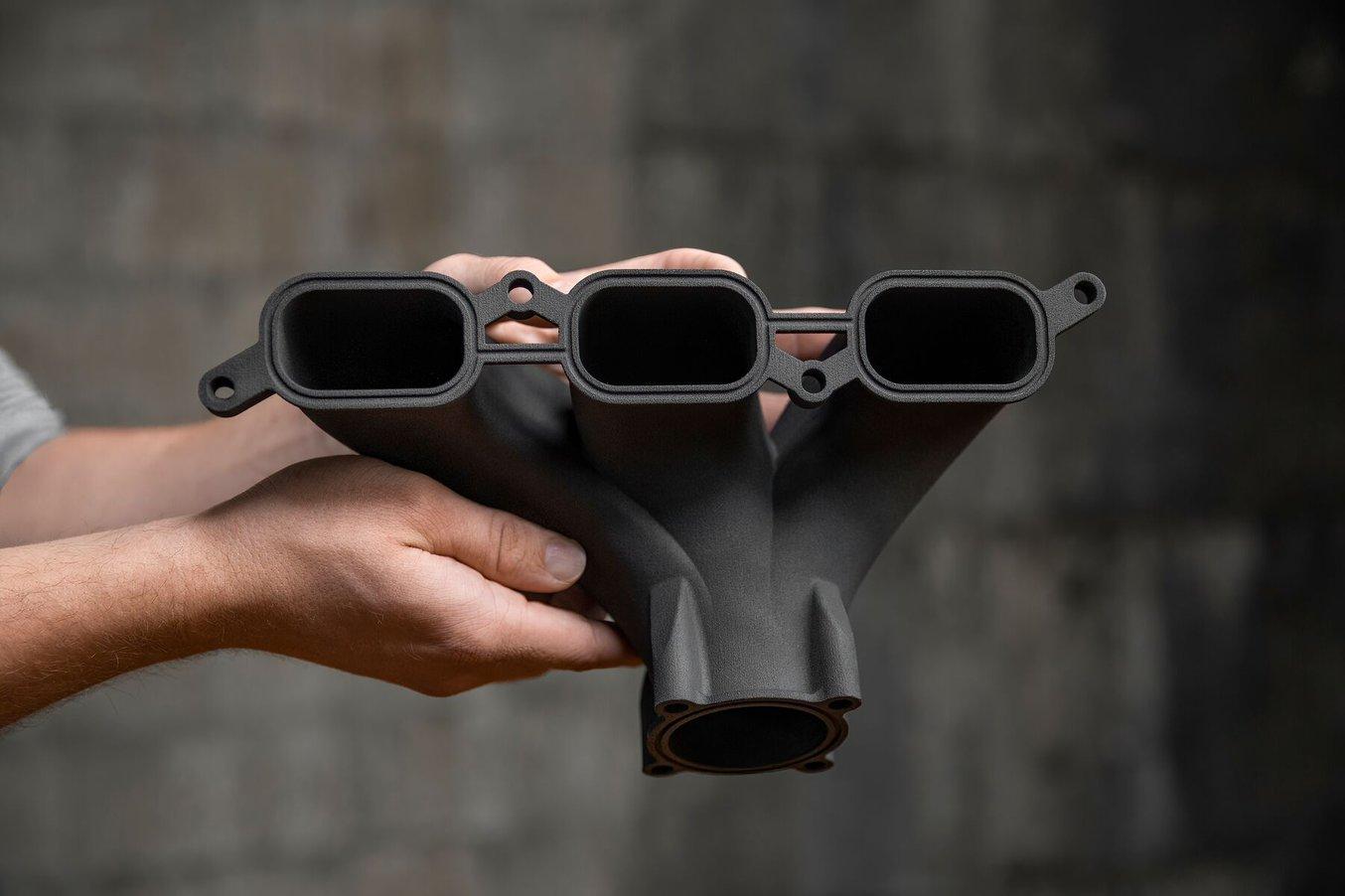
Industrial-quality SLS 3D printers, like the Fuse 1+ 30W, have excellent resolution and can create highly detailed parts that combine strength with organically curved features and precise negative or positive features.
SLS 3D printers form parts by using a high-powered laser to sinter together particles of polymer powder. SLS resolution depends on how precisely the laser can be controlled by the galvanometers — a function of the laser quality, software, and firmware programming, and the calibration of the overall laser assembly. The self-supporting nature of the SLS powder bed technology also enables the creation of highly intricate geometries with fine features that don’t need to be compromised by support structures. The Fuse 1+ 30W can produce 0.3 mm thick horizontal and 0.6 mm thick vertical walls, while embossed and engraved details have to be at least 0.1 to 0.4 mm deep and wide, depending on the layout within the build.
Design Rules Comparison
Fused Deposition Modeling (FDM) | Stereolithography (SLA) | Selective Laser Sintering (SLS) | |
---|---|---|---|
Minimum supported wall thickness | 0.8 mm | 0.2 mm | 0.3 mm (horizontal walls) 0.6 mm (vertical walls) |
Minimum unsupported wall thickness | 0.8 mm | 0.2 mm | 0.3 mm (horizontal walls) 0.6 mm (vertical walls) |
Minimum vertical wire diameter | 3 mm | 0.3 mm (7 mm tall) 0.6 mm (30 mm tall) | 0.8 mm |
Minimum embossed detail | 0.6 mm wide 2 mm high | 0.1 mm | 0.15 mm (depth, horizontal faces) 0.35 mm (width, horizontal faces) 0.35 mm (depth, vertical faces) 0.4 mm (width, vertical faces) |
Minimum Engraved Detail | 0.6 mm wide 2 mm high | 0.15 mm | 0.1 mm (depth, horizontal faces) 0.3 mm (width, horizontal faces) 0.15 mm (depth, vertical faces) 0.35 mm (width, vertical faces) |
Design rules may vary by printer model. The listed values are based on estimates by Protolabs / Hubs for FDM 3D printers, Form 4 design rules for SLA 3D printers, and Fuse Series design rules for SLS 3D printers.
Out of the three 3D printing technologies, SLA offers the best resolution, with SLS being a close second. Both processes can reproduce the minuscule details of the original CAD design, while FDM 3D printers generally struggle at precisely delineating textures from flat surfaces, or defining small features clearly.
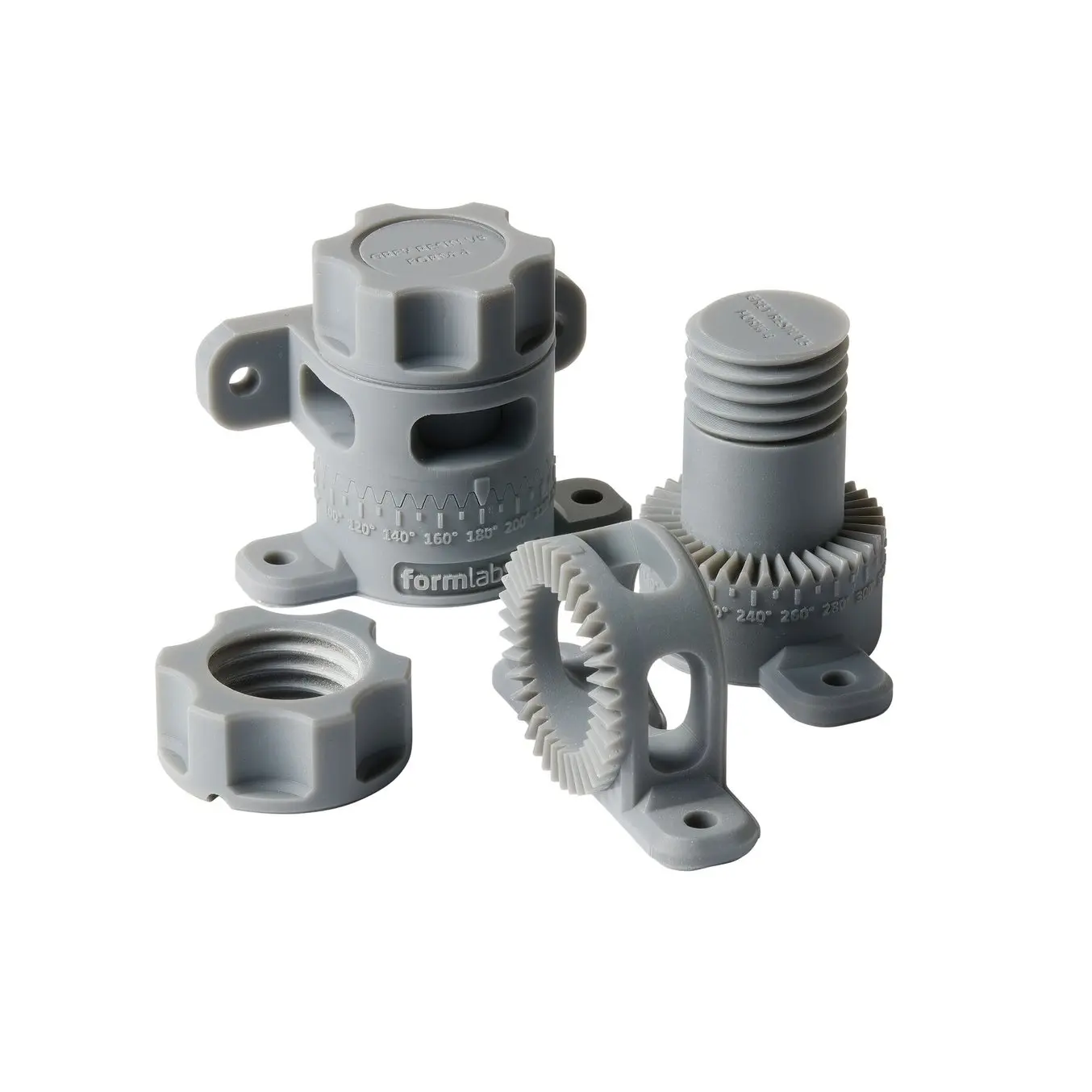
Form 4 Series Design Guide
A successful 3D print starts with a well-designed model. Follow our best practices to optimize designs and reduce failures.
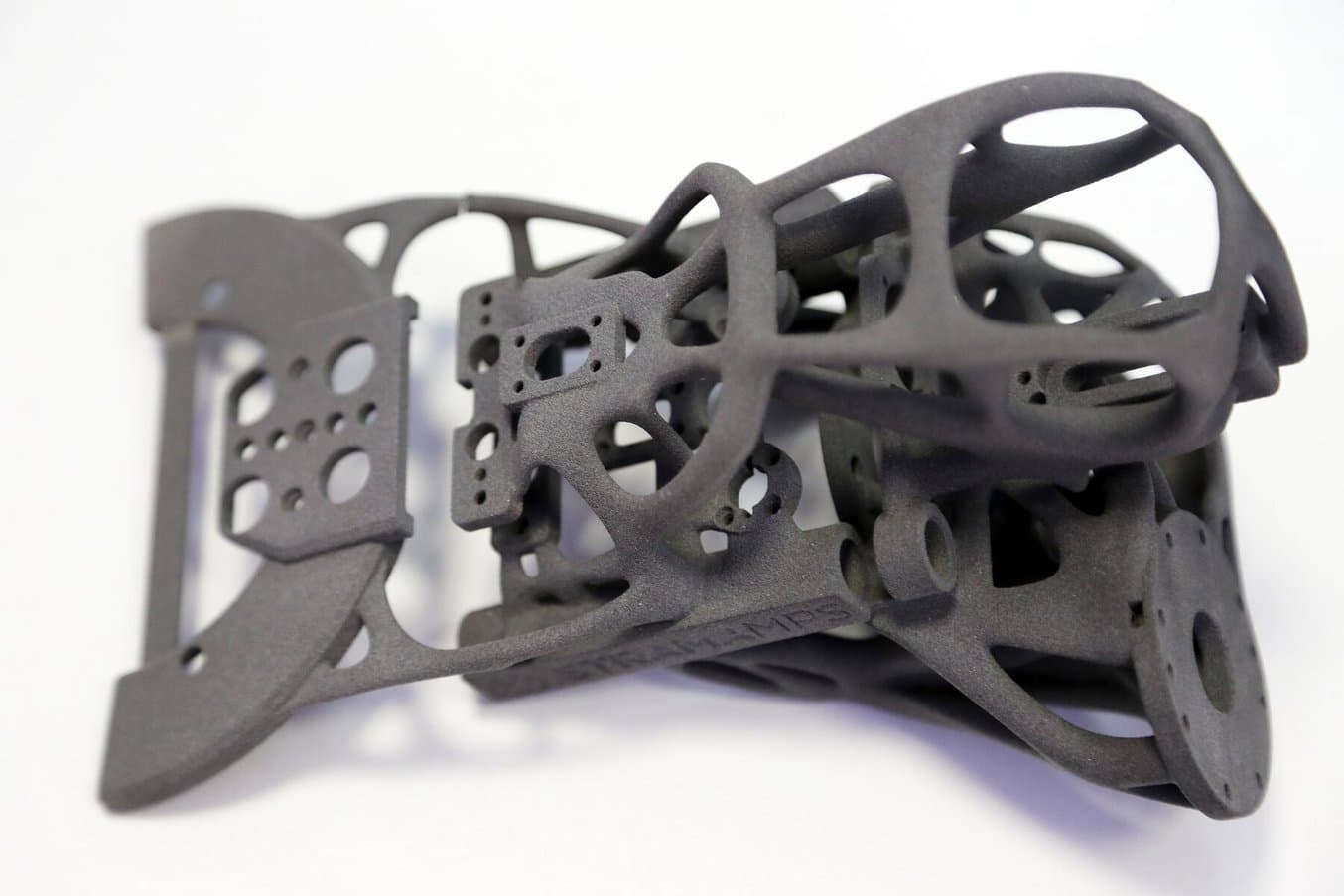
Fuse Series Design Guide
In this design guide, you’ll learn about some of the important considerations for designing for SLS 3D printing on the Fuse Series, and how you can leverage these practices to create successful parts.
Dimensional Accuracy and Precision
Accuracy — how closely each cross-section of the part can reproduce the intended shape from the 3D file, and precision — how consistently that accuracy is repeated throughout the part, varies between types of 3D printing technology as well as between manufacturers.
For FDM 3D printers, accuracy is affected by the uniformity and repeatability of the extrusion process and the properties of the filament as it melts and is extruded. The extrusion process can introduce inconsistencies within and between layers; for example, if it doesn’t move smoothly, the diameter of the filament is not consistent, the extrusion temperature varies, or when the material doesn’t get deposited at the same rate and volume everywhere.
When looking at overall precision, the ‘squishing’ effect of semi-hardened layers can present further inconsistencies. The heat used in the extrusion process can lead to warping or distortion in the parts, though some manufacturers use heated beds and enclosed build chambers to maintain a consistent temperature for a more controlled process.
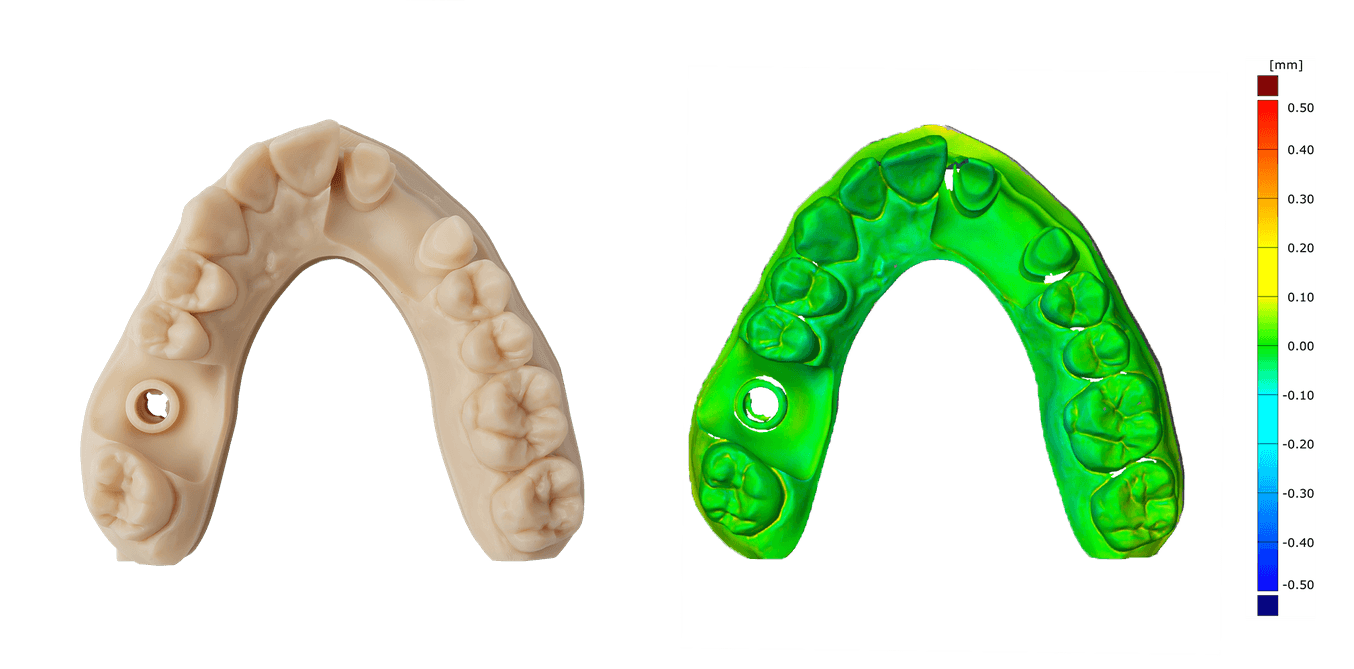
Accuracy can be measured by 3D scanning the 3D printed parts and comparing them to the original model. Even better, ask for a sample part, or a custom sample of your own design, to check the fit or measure against the original design. This dental model was produced on a Form 4B MSLA printer and the test shows that over 99% of its printed surface area is within 100 μm of the design parameters.
SLA printers’ accuracy depends on the optical performance of the printer, the forces that a part experiences during printing, and the properties of the liquid resin inside the printer. Different light sources and optical units will be able to cure each cross-layer with varying degrees of accuracy, though overall performance still generally outperforms the accuracy of FDM 3D printers.
Additionally, as each layer finishes and the build platform moves away from the light source, that peeling motion puts a great deal of stress on the newly formed layer, which can lead to slight distortion. Professional resin printers use different solutions to mitigate these forces. For example, Formlabs’ Form 4 uses a dual-layer flexible film tank that minimizes peel forces and a proprietary, microtextured optical film, called the Release Texture, that provides airflow between the resin tank and LCD screen, preventing suction forces and increasing accuracy.
The third factor affecting resin 3D printers’ accuracy is material properties. The process of curing liquid resin depends on many variables including resin: temperature, homogeneity, scattering, viscosity, and more. Small changes to any of these variables can cause more or less resin to cure, which can cause up to hundreds of micrometers of deviation in the size or shape of cured layers. Most resin 3D printers do not control these variables, resulting in frequent and unpredictable changes in dimensional accuracy.
Formlabs Form 4 addresses this issue by precisely controlling the temperature and homogeneity of the liquid resin using precision heaters, infrared temperature sensing, and a high-speed resin mixer. Formlabs also develops and manufactures its own materials, and tightly controls the reactivity, viscosity, and scattering properties of every material.
To determine dimensional accuracy measurements that are achievable, one test model with various feature sizes was 3D printed on three different printers using Grey Resin V5 and 100 µm layer height, and post-cured for five minutes at room temperature. The measured accuracy on these models was the following:
- 1–30 mm features: ±0.15% (lower limit: ±0.02 mm)
- 31–80 mm features: ±0.2% (lower limit: ±0.06 mm)
- 81–150 mm features: ±0.3% (lower limit: ±0.15 mm)
SLS 3D printers are typically quite accurate; the laser and galvanometers can provide precise control. SLS 3D printers’ accuracy is determined by the optical performance of that laser, how well the print parameters are tuned to the powder settings, and how well controlled the build environment is. SLS 3D printing requires very consistent, precisely tuned temperatures to print accurate parts. Open settings to be used with third-party materials increase the possibility of poor part quality and performance as well as print defects like warping.
In general, resin and powder 3D printers are the most accurate and precise types of 3D printing technologies. Compared to standard CNC machining tolerances of +/- 0.3 mm, Formlabs’ Form 4 SLA printers and Fuse Series SLS printers perform on par.
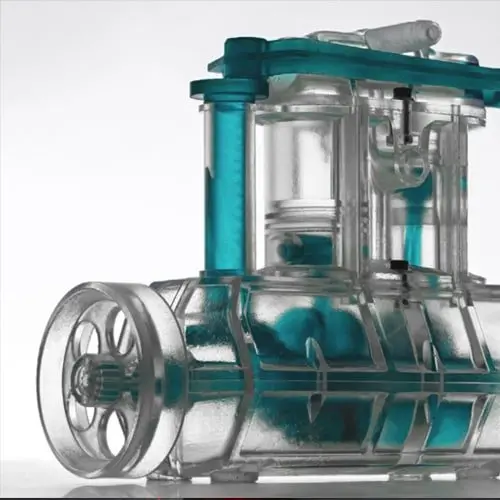
Optimizing Design for Functional 3D Printed Assemblies
Tolerance and fit are essential concepts that engineers use to optimize the functionality of mechanical assemblies and the cost of production. Use this white paper as a resource when designing functional 3D printed assemblies, or as a starting point when designing the fit between parts printed.
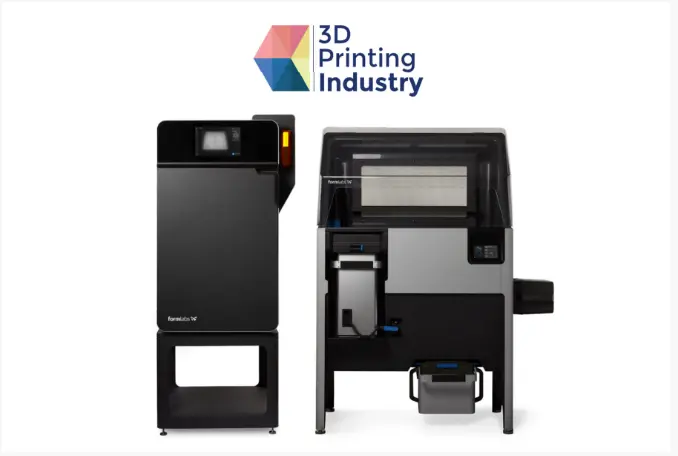
3D Printing Industry: Formlabs' Fuse 1 & Sift In-Depth Review
Read this in-depth engineer's report by 3D Printing Industry that includes a review of Formlabs' SLS 3D printers and detailed results of accuracy testing.
Isotropy and Watertightness
Isotropy vs. anisotropy is a concept discussed often in 3D printing — because 3D printing creates parts one layer at a time, completed prints may have variations in strength based on the orientation of the part relative to the printing process, with different properties in X, Y, and Z axes.
FDM 3D printed parts are known for being anisotropic due to layer-to-layer differences created by the print process. This anisotropy limits the usefulness of FDM for certain applications or requires more adjustments to part geometry to compensate for it.
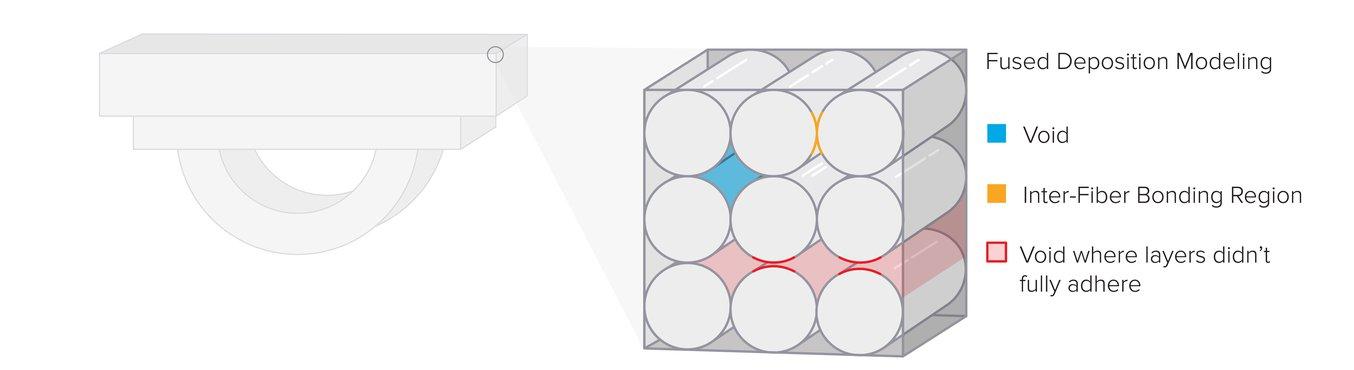
FDM 3D printers form layers by depositing lines of thermoplastics. This process means that layers are not bonded together as strongly as the lines (filament extrusion) themselves; there are voids in between the rounded lines and it’s possible that layers may not fully adhere to one another.
In contrast, SLA resin 3D printers create highly isotropic parts. Achieving part isotropy is based on a number of factors that can be tightly controlled by integrating material chemistry with the print process. During printing, resin components form covalent bonds, but from layer to layer, the part remains in a semi-reacted “green state.”
While in the green state, the resin retains polymerizable groups that can form bonds across layers, imparting isotropy and watertightness to the part upon final cure. On the molecular level, there is no difference between X, Y, or Z planes. This results in parts with predictable mechanical performance critical for applications like jigs and fixtures, end-use parts, and functional prototyping.
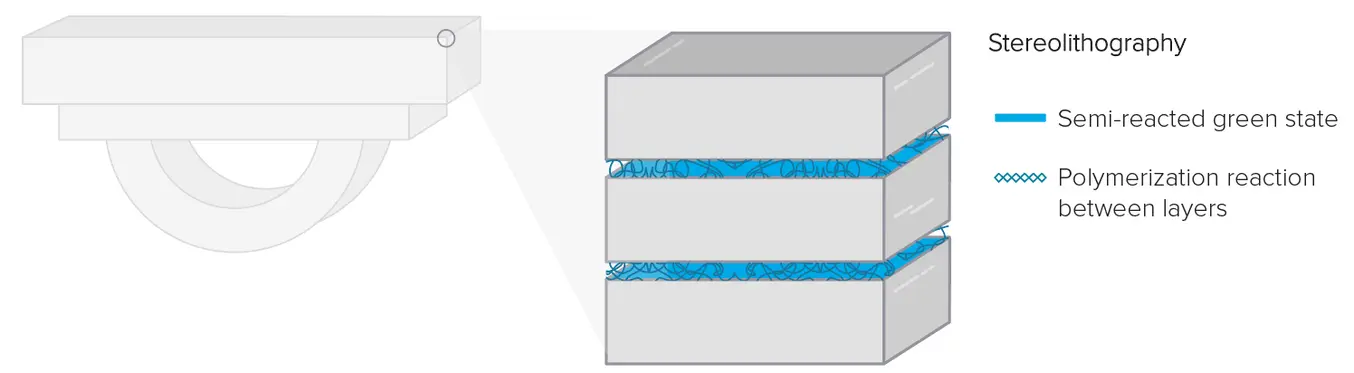
In SLA prints, there is no difference between the Z-axis and the XY plane in terms of chemical bonds; each part printed on an SLA machine is a continuous polymer network.
SLS 3D printers create parts that are mostly isotropic. Unlike FDM 3D printing, where the filament is melted before extrusion and coming in contact with previous layers, SLS 3D printer sinter particles that are already in contact with the surrounding material — so the particles fuse with the material in the same plane or layer, as well as partially to the plane/layer below. However, because different materials hold heat and remain in a semi-sintered state for different lengths of time, SLS isotropy can vary between types of powders. Certain powders will be able to fuse together with layers below them at different rates, some more completely than others.
Isotropy is related to surface porosity and particle density, and these features all impact the watertightness and waterproofness of a part. Watertightness refers to the ability of a part or assembly to prevent liquid from seeping in or out, and waterproofness refers to the ability of an outside surface to repel water. For 3D printed parts, watertightness is a more comprehensive way of looking at this feature because 3D printed parts and assemblies often want to protect something inside them, like underwater electronics enclosures, rather than merely repel water they come in contact with.
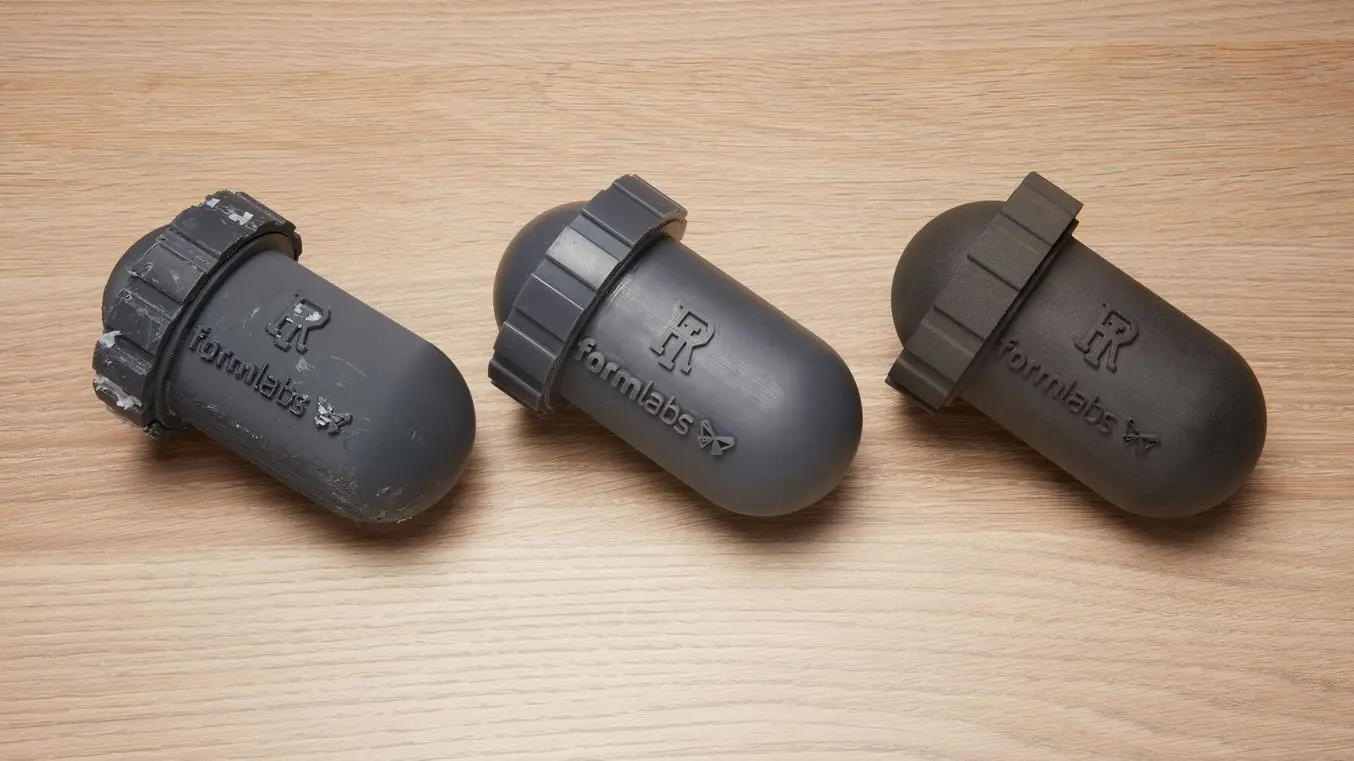
In extensive testing conducted by the University of Rhode Island Underwater Robotics and Imaging Laboratory (URIL), FDM (left), SLA (center), and SLS (right) 3D printed enclosures were tested using a pressurization chamber.
In an extensive study done by the University of Rhode Island Underwater Robotics and Imaging Laboratory, FDM 3D printed robotics enclosures failed to keep internal mechanics dry underwater for even a few seconds. SLA 3D printed parts were deemed watertight up to very high pressurization levels, and SLS 3D printed parts kept inner electronics dry under moderate pressurization levels. SLS enclosures that had been vapor smoothed were able to stay watertight under increased pressure.
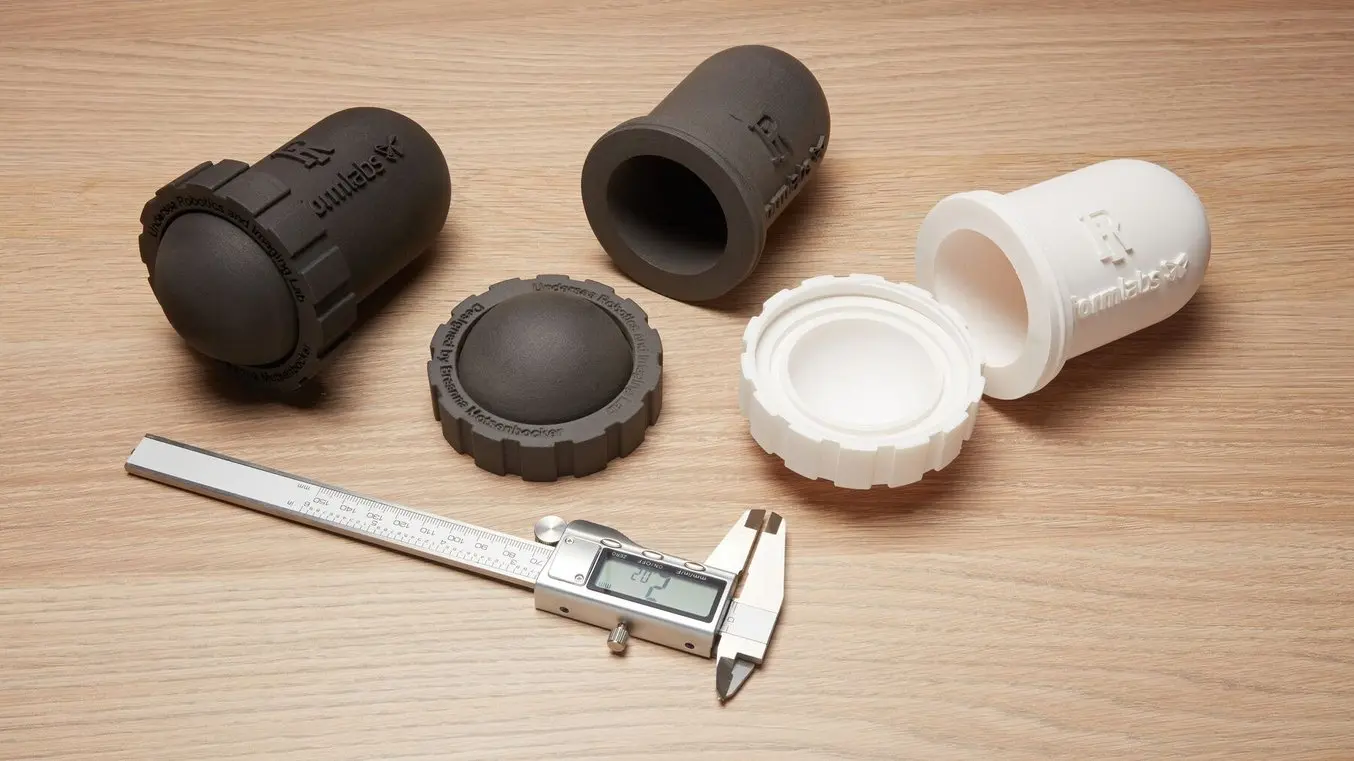
3D Printing Watertight Enclosures and Pressure Testing Results
In this white paper, we will provide the testing results and clear guidelines on how to affordably 3D print customized watertight enclosures.
Surface Finish
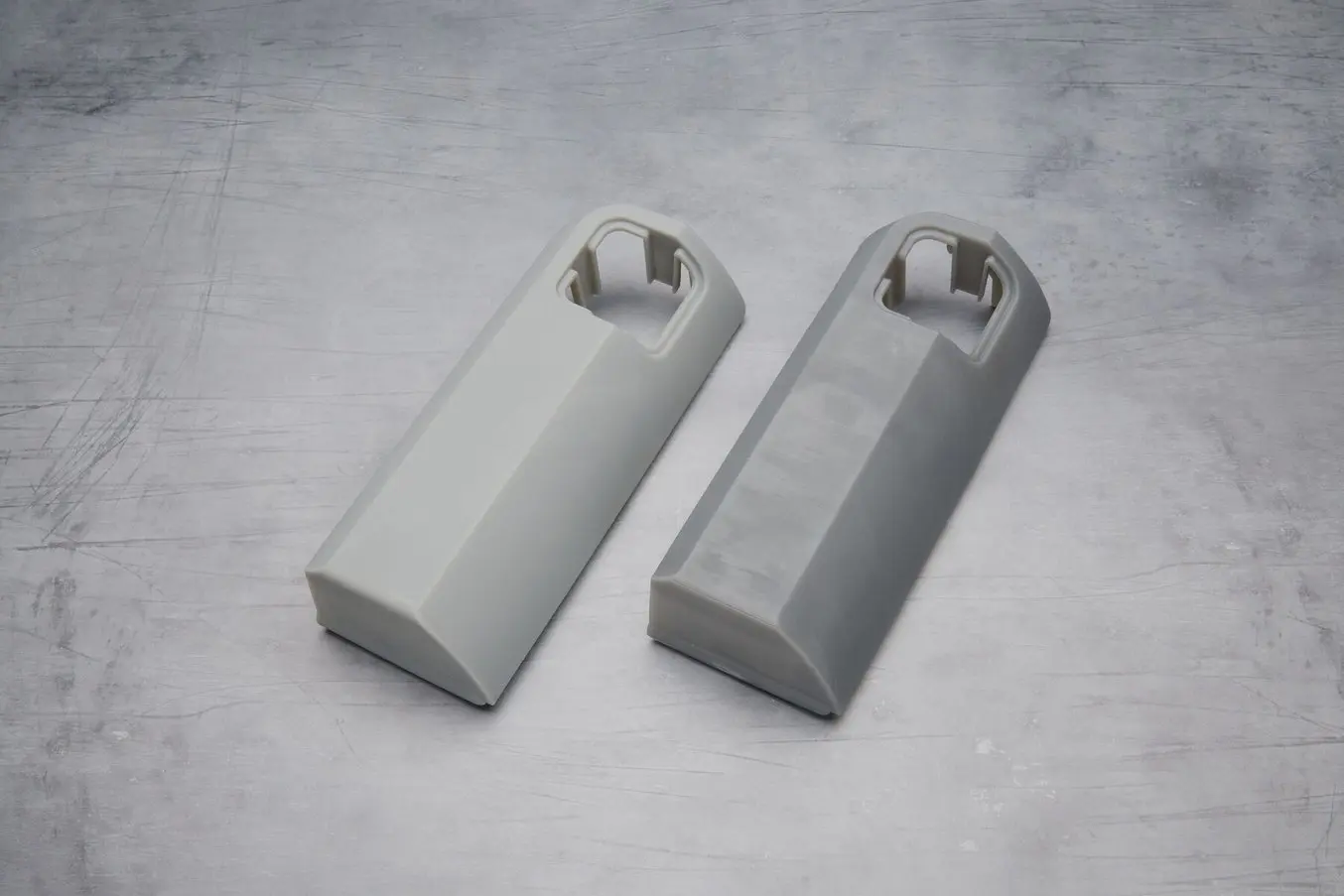
SLA 3D printers produce parts with the best surface finish, which translates to parts with smooth, matte finishes. These results have improved as both the 3D printing industry overall, and SLA technology specifically, have become more advanced.
One of the most well-known differences between FDM, SLA, and SLS 3D printed parts is the difference in surface finish. FDM’s layer-by-layer ‘hot glue gun’ method results in layer lines that can be seen upon close inspection. These parts require greater post-processing and add extra labor to the overall part production time. Layer lines also prevent semi-clear or translucent materials from creating truly translucent parts; the light refracts off of even tiny lines in the part, clouding the transparency of the finished part.
SLA 3D printers create parts that are nearly indistinguishable from injection molded plastics. Their superior surface finish is ideal for final design review prototypes and end-use products, even in the consumer goods category where surface finish and smoothness are of utmost importance. Furthermore, the lack of layer lines allows SLA 3D printers to create almost completely transparent parts. Clear parts are helpful for molding applications where the injection can be observed, product design applications for eventual clear plastics, microfluidics, medical applications, and more. In the dental 3D printing industry, SLA resins like Premium Teeth Resin can simulate the smooth look of enamel, so dentures are indistinguishable from real teeth.
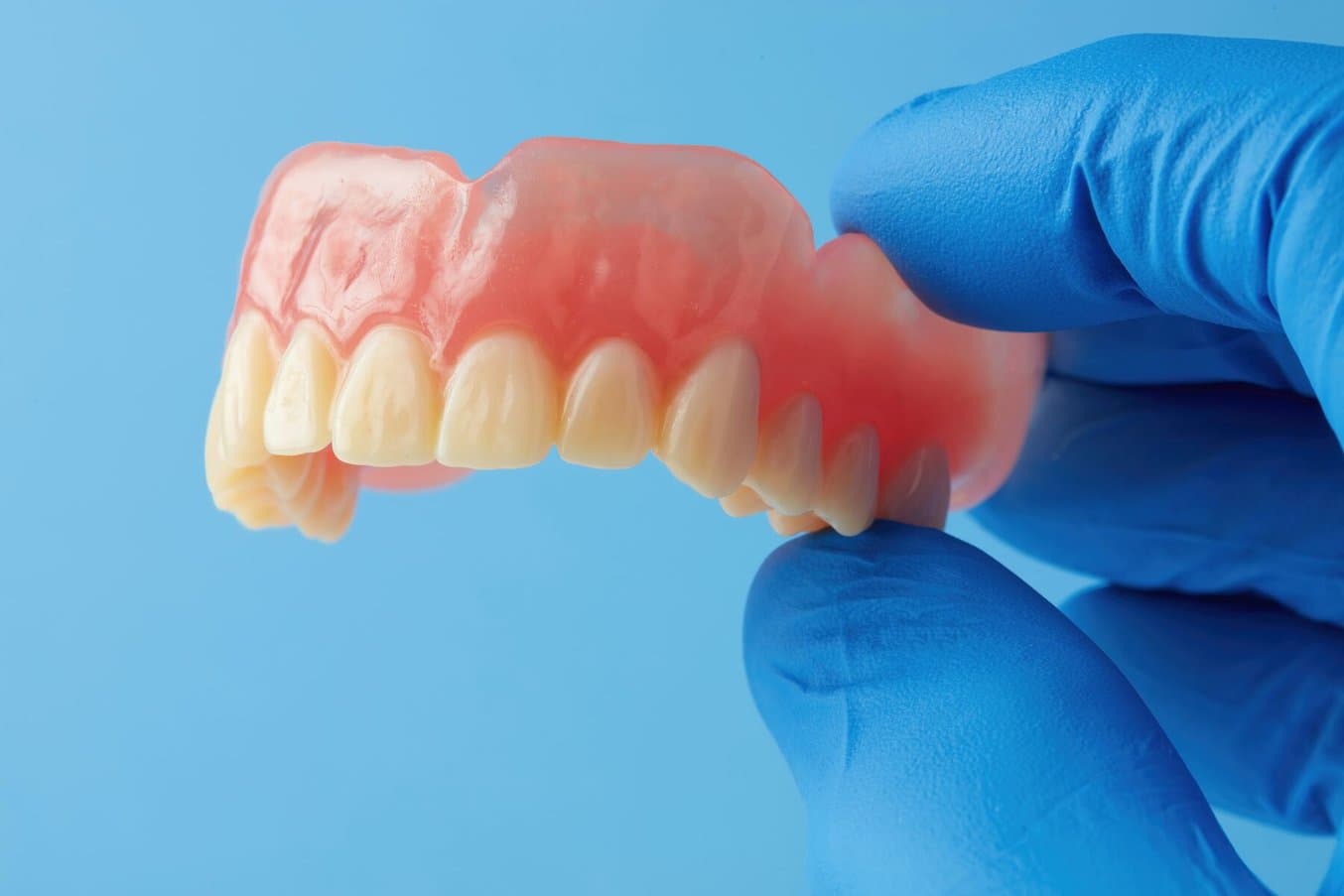
SLA 3D printed parts have excellent surface finish, so that parts like these 3D printed dentures are indistinguishable from real teeth.
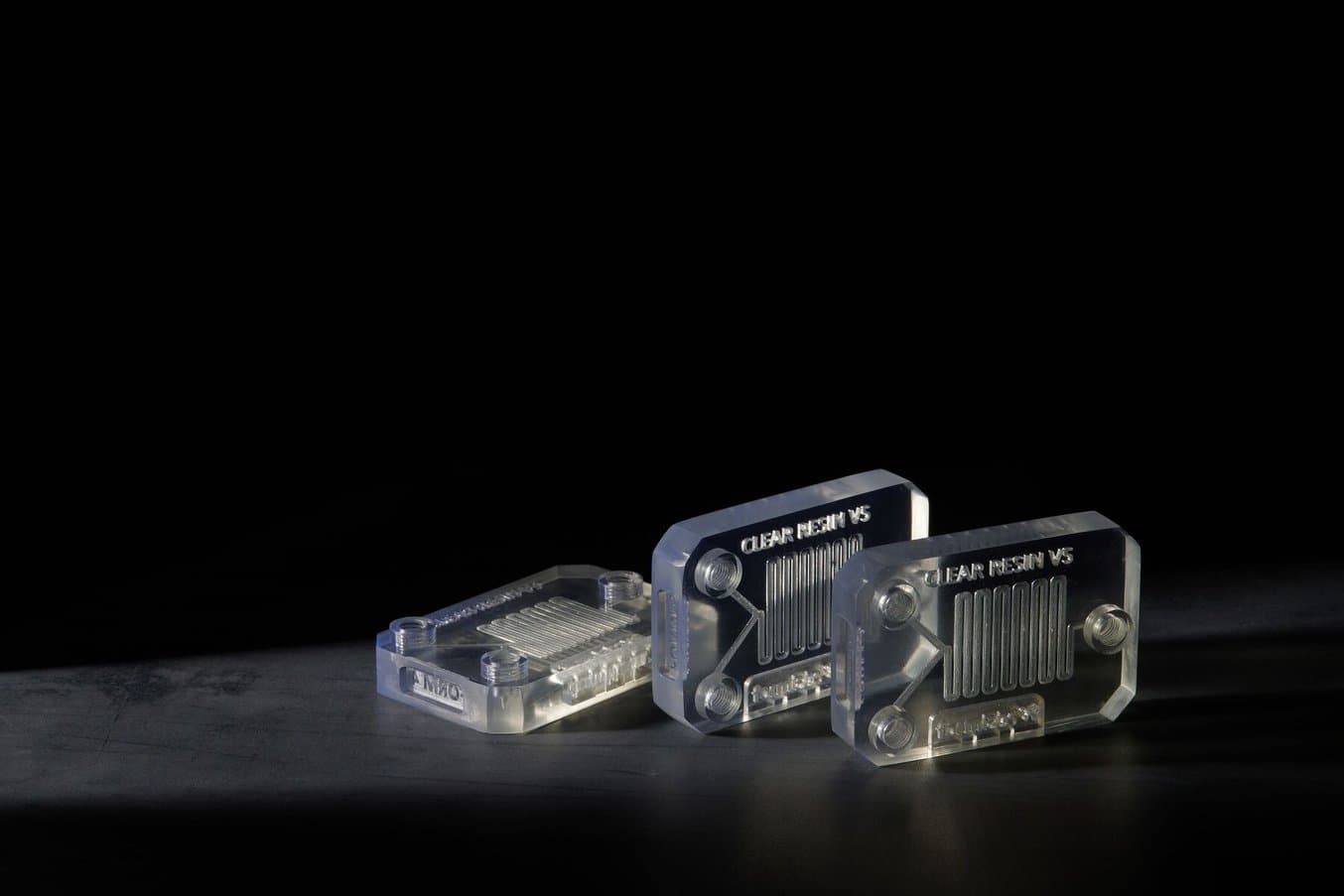
The lack of layer lines makes SLA 3D printed clear resin parts seem almost completely transparent because layer lines have a refractory effect on light as it passes through the parts.
SLS 3D printed parts have a slightly rough, or grainy, surface finish. However, SLS parts, because they don’t print with support structures, make it easy to have a uniform surface finish across the entire part. Comparatively, SLA and FDM 3D printed parts often need post-processing in order to remove small marks left by supports. Additionally, SLS 3D printed parts that have been vapor smoothed or media blasted and polished, can achieve a glossy, smooth surface, just like SLA.
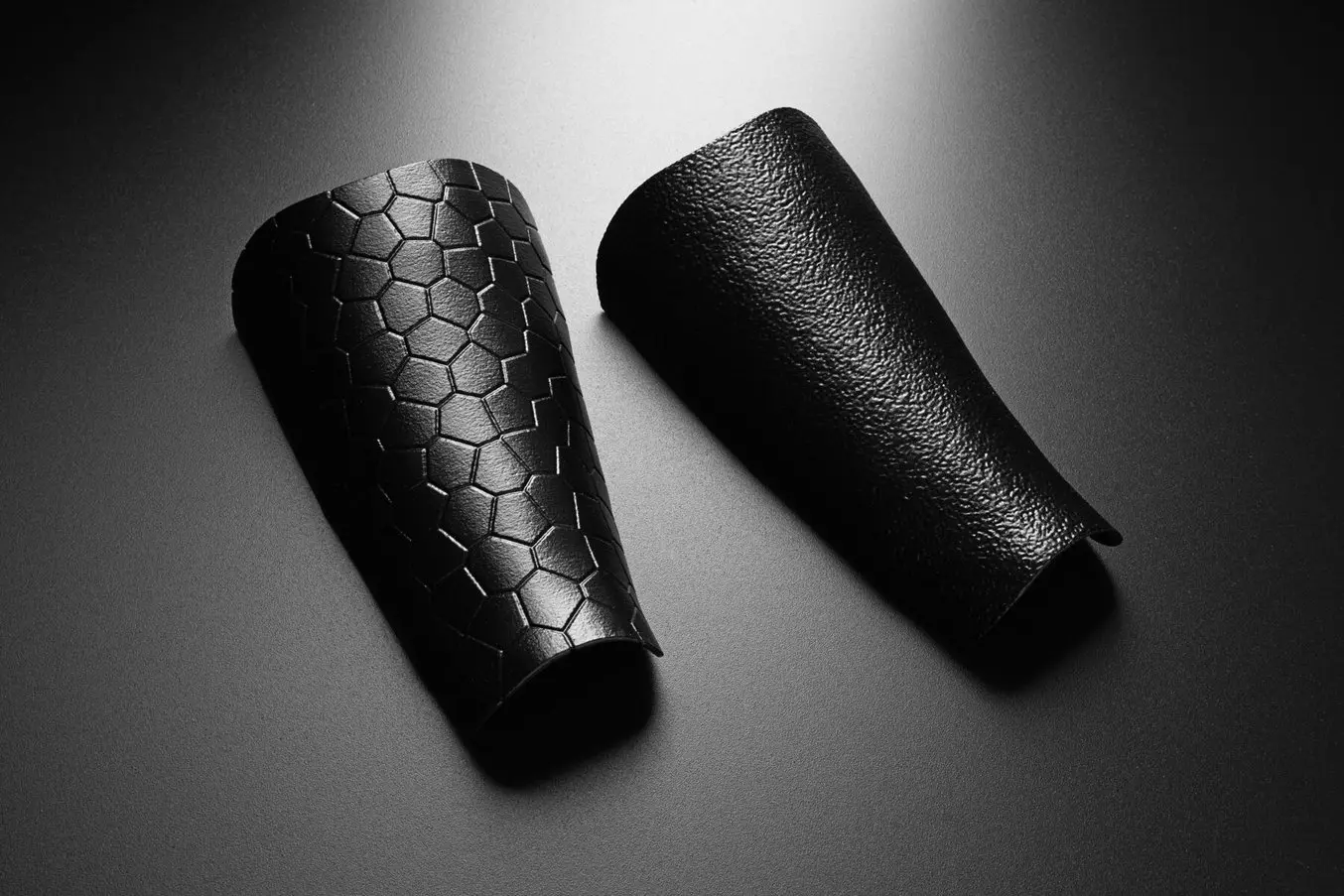
Though SLS parts may come out of the printer with a slightly grainy surface, post-processing methods like vapor smoothing can create parts with end-use quality surface finishes. These parts above were printed with different surface textures and then vapor smoothed to remove any rough surface areas.
Workflow and Ease of Use
The workflow for FDM, SLA, and SLS 3D printing consists of three steps: designing, 3D printing, and post-processing.
First, use any CAD software or 3D scan data to design a model, and export it in a 3D printable file format (STL or OBJ). 3D printers then require print preparation or slicer software to specify printing settings and slice the digital model into layers for printing. This print orientation step can be as simple as clicking 'One Click Print' in Formlabs' print preparation software PreForm, or as complicated as manually choosing print settings and fine-tuning material settings. Low-cost machines of each technology typically require the user to do more work on the front-end and this can lead to part failures, or inefficiencies in the print process.
See how to go from design to 3D print with the Form 4 SLA 3D printer. This video covers the basics of how to use Form 4, from the software and materials to printing and post-processing.
Professional 3D printers like the Form 4 SLA 3D printer or Fuse Series SLS 3D printer, often have the option or setting up your models automatically, relying on thoroughly tested settings and material tuning. The SLS packing function available in PreForm for the Fuse Series can even outperform third-party software; it efficiently stacks and nests parts within the build chamber, leading to a higher pack density and thus lower cost per part.
Once the 3D printing process begins, most 3D printers can run unattended, even overnight, until the print is complete. Advanced SLA 3D printers like Form 4 offer a cartridge system, that refills the material automatically, and there are even automation solutions like Form Auto for the the Form 3 Series that can automate the part removal and restarting of new prints.
Learn more about the SLS workflow with the Fuse Series SLS 3D printer. This video takes you through each step of the SLS 3D printing process, from design and build chamber packing, to powder recovery and media blasting.
The final step of the workflow is post-processing. There are basic post-processing tasks like removing supports (FDM and SLA), rinsing and post-curing parts (SLA), or removing excess powder and cleaning parts (SLS).
FDM parts often exhibit clearly defined layer lines, because of the 'hot glue gun' method of building parts. These layer lines require extensive sanding or smoothing in order for use the parts for more advanced applications. Though there are some soluble filaments used for supports, there are many parts where hard supports need to be cut away and the surfaces have to be sanded to remove support marks. These two steps can take up significant time, adding to overall hands-on labor time for FDM 3D printing and reducing throughput.
The foundational step in any SLA post-processing workflow is to remove any excess resin on the surface of the parts through an alcohol or ether wash. This washing step can be done manually or by using an automated washing solution that agitates the liquid for a pre-set amount of time. After a rinse, some SLA parts require a post-cure to help them reach optimal material properties, which can also be automated using advanced post-curing solutions.
Basic steps for SLS post-processing include removing excess, unsintered powder from the parts and media blasting the parts to fully clean the parts and smooth the surfaces. Some SLS manufacturers don't offer a specific media blasting machine or complete powder recovery system, while others offer them at extremely high prices. Formlabs SLS ecosystem includes the Fuse Sift and Fuse Blast, which make the powder recovery and part cleaning process faster, easier, and cleaner.
There are also advanced 3D print post-processing methods like coating, smoothing, painting, vapor smoothing, and electroplating that can improve aesthetics, mechanical properties, and overall performance to make your parts suitable for a wide range of applications. To learn more about post-processing, read our complete guides to post-processing for SLA and SLS 3D printing.
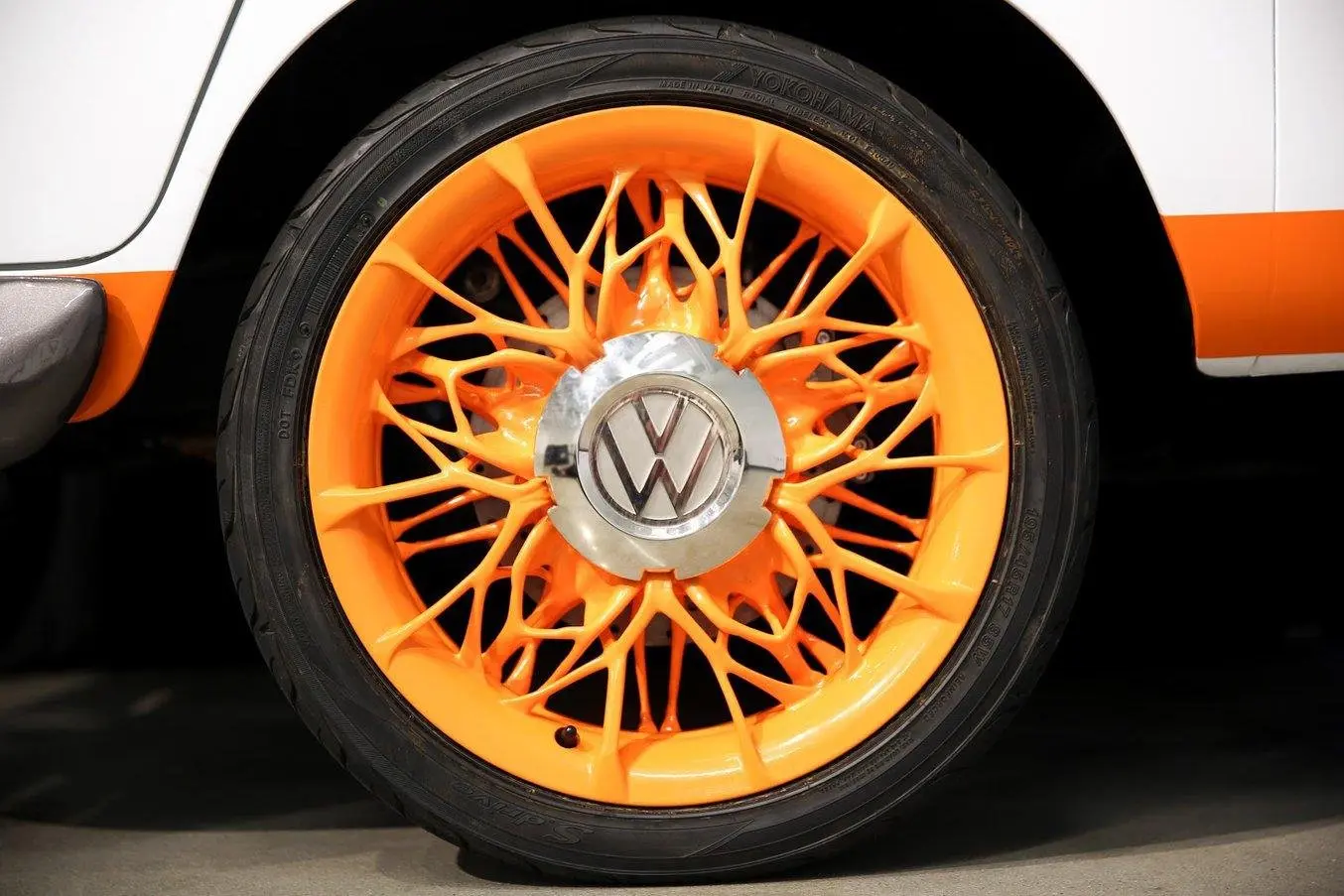
Advanced Post-Processing Techniques for 3D Printing
Watch this webinar to learn about 11+ advanced post-processing techniques for 3D printing, including Cerakote, electroplating, vapor smoothing, and more.
Materials and Applications
Choosing the right 3D printing process is just one side of the coin. Ultimately, it'll be largely up to the 3D printing materials to enable you to create parts with the desired mechanical properties, functional characteristics, or looks.
Performance from parts made of filament with FDM vs. resin with SLA vs. powder with SLS 3D printing can often be difficult to directly compare because the three technologies don’t use the same materials or form parts in the same process. However, there are analogous materials across all technologies, so achieving the same material properties (or very close) can be straightforward even when changing technologies.
Fused Deposition Modeling (FDM) Filaments | Stereolithography (SLA) Resins | Selective Laser Sintering (SLS) Powders | |
---|---|---|---|
General Use | PLA | General purpose resins (matte, clear, various colors) | Nylon 12 |
Tough Engineering Materials | ABS, nylon, PETG | Tough and durable resins | Nylon 12, nylon 11, polypropylene |
Stiff Engineering Materials | PEEK, ULTEM, composites (glass-filled or carbon fiber reinforced) | Stiff, strong, rigid resins (glass-filled) | Nylon composites (glass-filled or carbon fiber reinforced) |
Flexible Engineering Materials | TPU | Flexible or elastomeric resins, pure silicone | TPU, polypropylene, nylon 11 |
Specialty Materials | Composites (carbon fiber, kevlar, fiberglass) | Flame retardant resins, investment casting materials, technical ceramics, wax composites, dental and medical materials | Nylon composites (glass-filled or carbon fiber reinforced) |
FDM printers primarily use filaments of common and familiar thermoplastics like ABS, and PLA. Engineering materials, such as nylon, PETG, or TPU, and high-performance thermoplastics like PEEK or carbon fiber composites are also available, but are often only compatible with selected professional FDM printers.
FDM filaments are often the same materials that are used for mass production processes like injection molding or thermoforming. This shared language makes it easy for engineers to choose FDM as a prototyping option because they are confident the material will stay the same throughout the design and manufacturing process. However, the FDM 3D printing process, which leaves layer lines and inhibits functional strength, makes it difficult to use the parts for more functional applications.
FDM parts excel in applications where a designer might need a quick check to make sure a part has the right look, or in educational situations where students need to be trained on 3D printing technology. For consumer goods prototyping, FDM parts are a low-cost way to get an idea of how a part shape will look and feel in your hand.
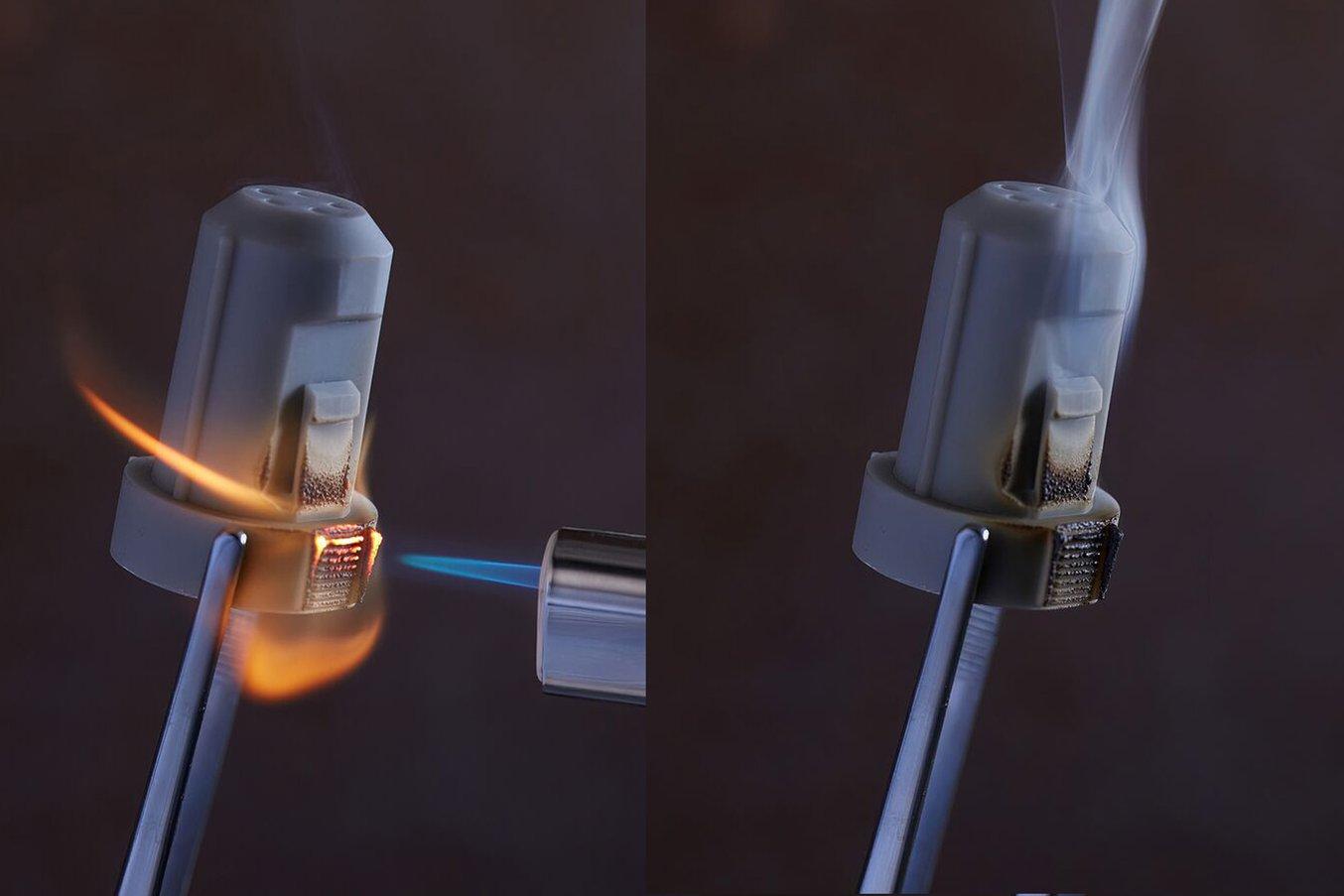
Formlabs' Flame Retardant Resin is a specialty UL 94 Blue Card certified material for creating self-extinguishing and halogen-free parts.
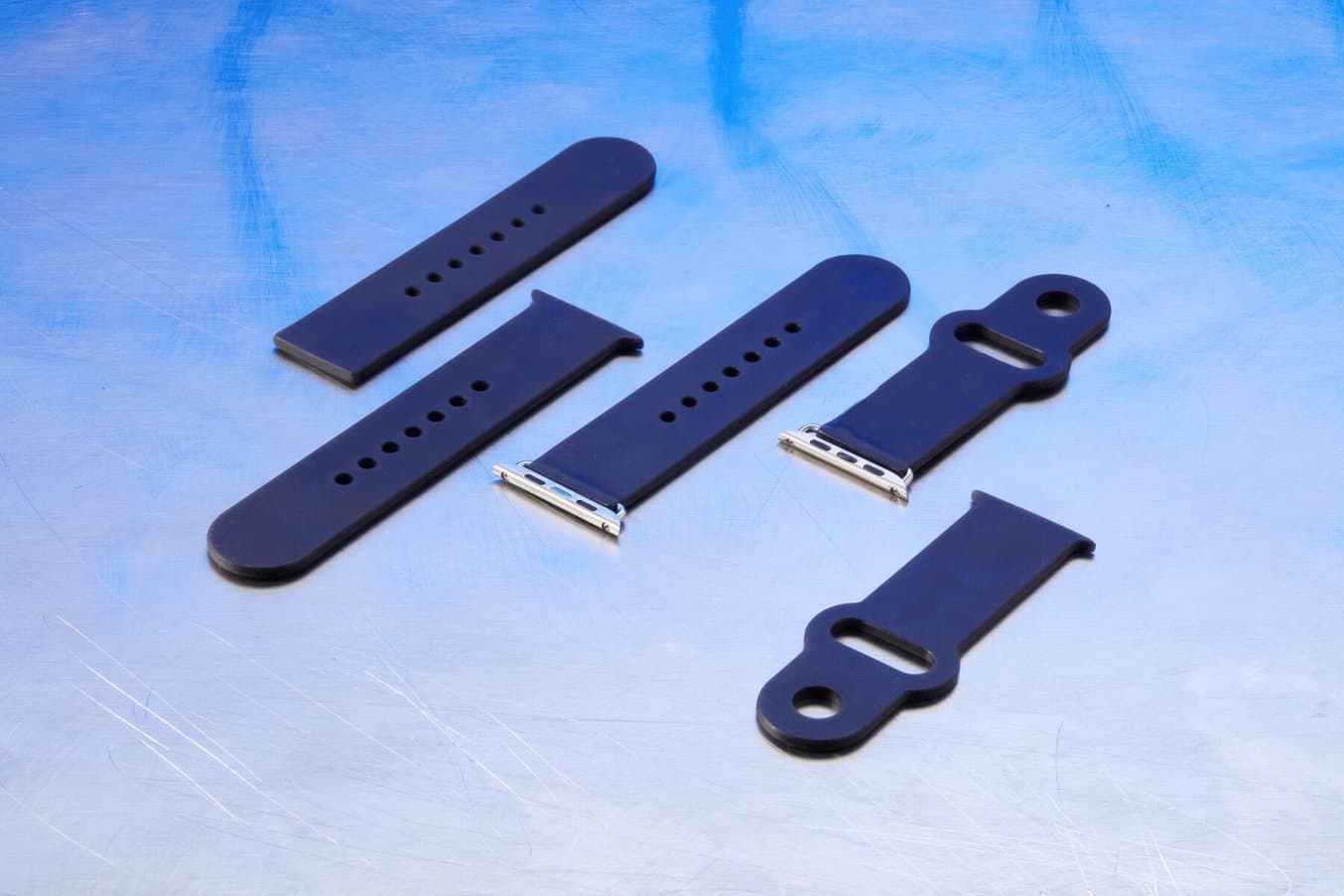
Silicone 40A Resin is a true silicone, with mechanical properties that are familiar to engineers and product designers.
SLA 3D printers have custom-formulated materials, and these vary between manufacturers. The benefits of this customization are that manufacturers can extensively calibrate their machines to be used with their specific resin formulations, ensuring better accuracy and repeatable results. The downside is that many customers don’t have the same familiarity with SLA resins, and this can lead to a knowledge gap and therefore lack of adoption. Custom-formulated resins allow SLA manufacturers to offer specific materials for advanced applications, such as dental resins for long-term appliances or technical ceramic materials.
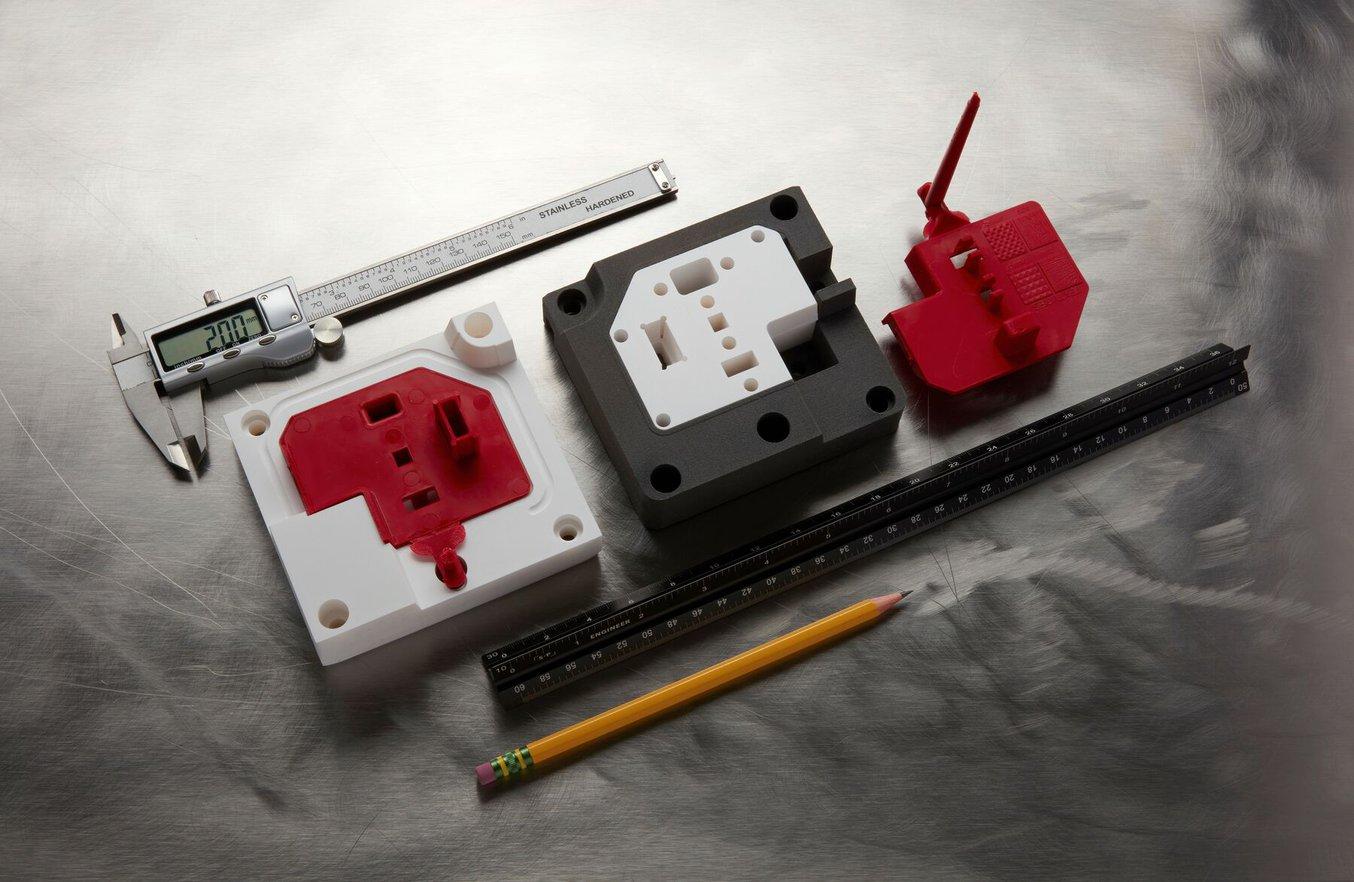
Rigid 10K Resin is a highly glass-filled and extremely stiff material that is similar to glass and fiber-filled thermoplastics. It is ideal for rapid tooling applications like injection molding, blow molding, or thermoforming.
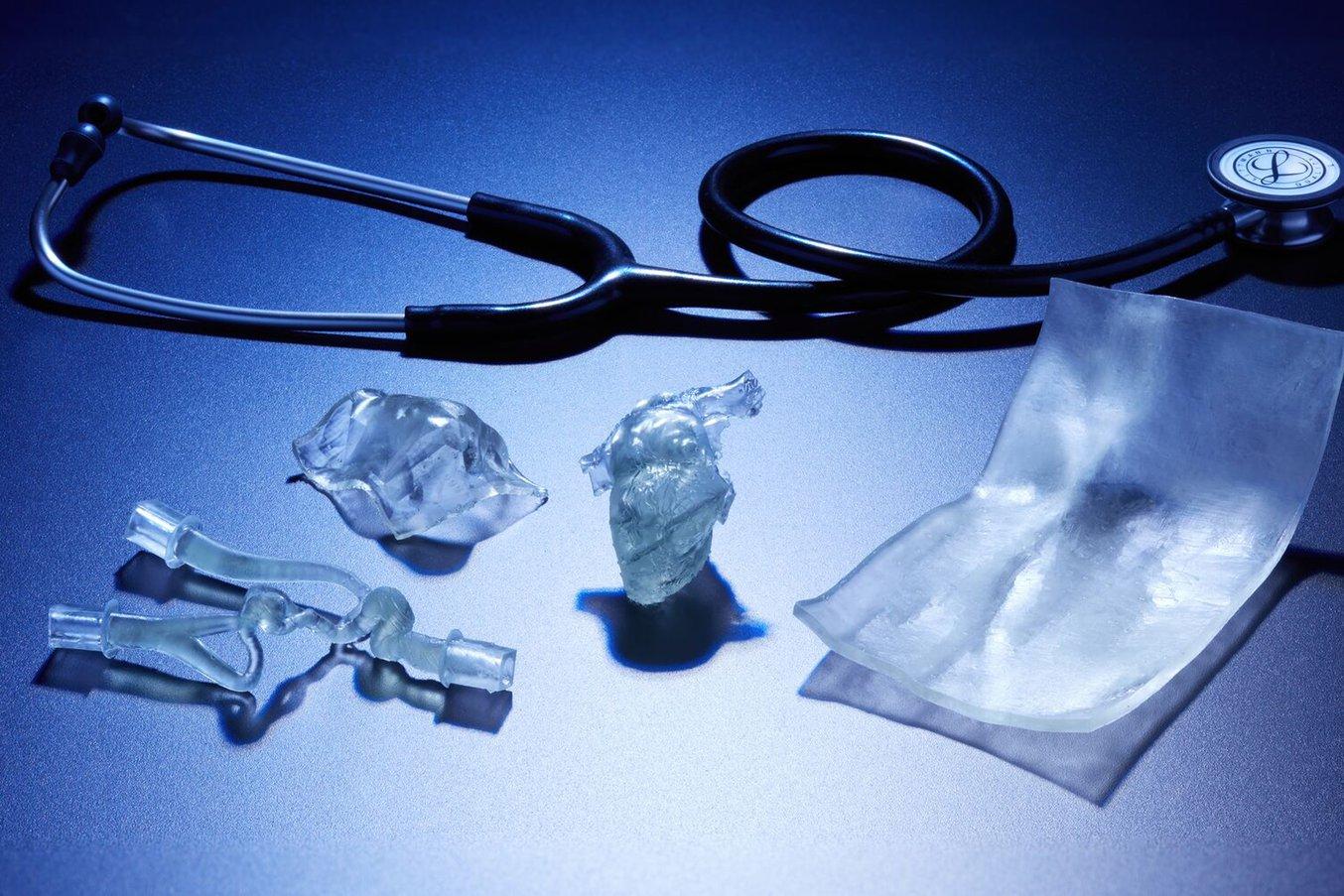
BioMed Elastic 50A Resin enables healthcare providers to 3D print soft, elastic, biocompatible parts with complex shapes such as patient-specific medical devices or soft tissue medical models.
In general, SLA 3D printed parts can be used in every design-to-manufacturing stage. Their isotropic material properties and excellent surface finish make them ideal for functional prototyping, go/no-go testing, end-use part production, and manufacturing aids. The ability to design unique, new formulations like technical ceramics or wax composites that can be burnt out makes SLA a uniquely perfect fit for certain industries and applications. For more general applications that cross multiple industries, SLA resins have the durability and strength to be used as end-of-arm tooling, robotics enclosures, seals, surgical guides, and more. The range of possible formulations makes the possibilities nearly limitless for resin parts.
Formlabs offers 40+ unique, custom-formulated resins for SLA 3D printing, including advanced technical ceramics, flame-retardant resin with favorable smoke and toxicity ratings, electro-static dissipative materials, and even materials for end-use medical devices like dentures or permanent crowns.
SLS 3D printing materials are familiar thermoplastics in powder form, like nylon, TPU, and polypropylene. These powders offer high performance and have well-understood material behaviors. SLS 3D printer manufacturers may offer their unique formulations of these powders or white label bulk powder from manufacturers. The industry-familiar materials combined with SLS 3D printing’s geometric flexibility, production capacity, and strength make SLS materials ideal for every application — from prototyping to functional testing and manufacturing aids, to end-use production.
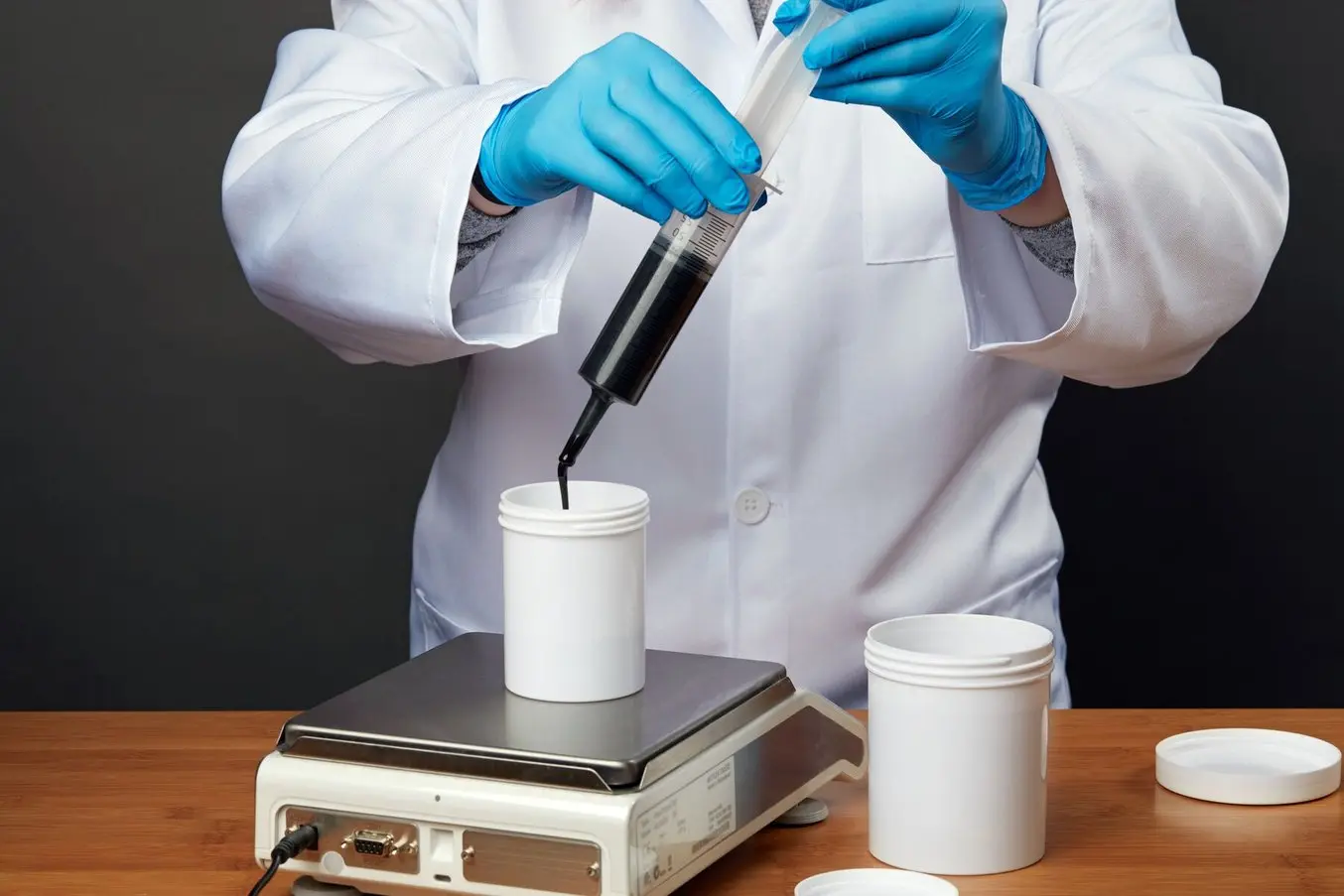
Formlabs is Open
Maximize your 3D printer’s potential with Formlabs Developer Platform. Unlock the possibility of printing with any 405 nm photopolymer resin or 1064 nm powder on Formlabs 3D printers, customize your print settings, or build software integrations.
Build Volume
Build volume across FDM, SLA, and SLS technologies varies widely. Though large sizes are available in each technology, the most common FDM 3D printers and SLA printers are desktop-sized or benchtop-sized, while the most common SLS 3D printers are benchtop-sized or larger.
FDM 3D printers come in a wide array of sizes and build volumes. FDM technology isn’t limited or affected by size; a highly accurate nozzle could still create a large part, but the motor system will simply be bigger and slower as it would have to cover more ground. There are massive FDM 3D printers available, with printing enclosures that resemble small rooms more so than benchtop or desktop tools, but these are extremely niche and uncommon. More commonly, FDM 3D printers are desktop or benchtop-sized and are typically found as quick prototyping solutions or educational tools in classrooms and fab labs. Build volumes for common desktop FDM 3D printers are usually in the range of 200 x 200 x 200 mm.
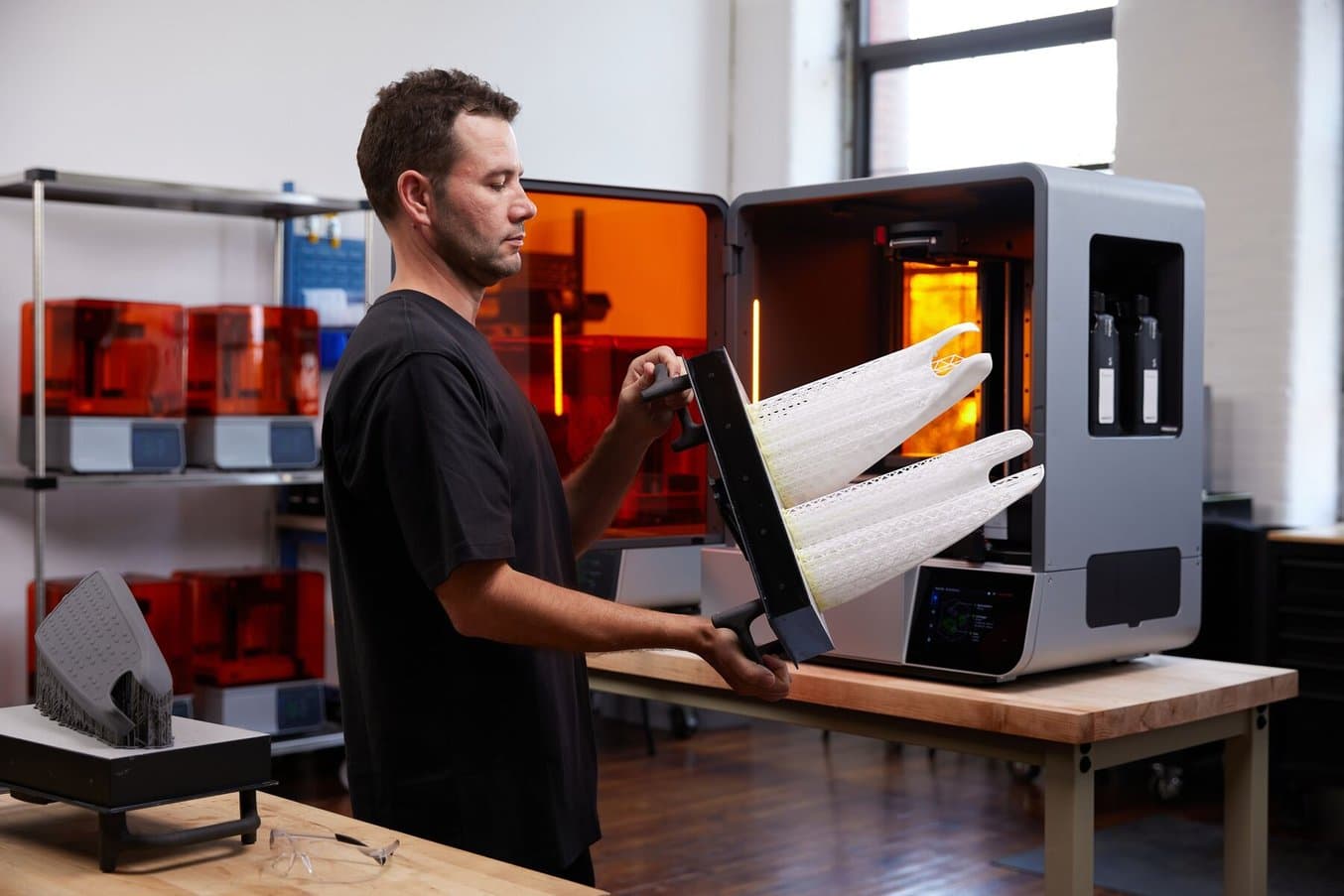
Form 4L is a large-format SLA 3D printer that is ideal for human-scale prototyping or higher volume applications at blazing fast speeds — most parts finish in under six hours and even builds that are the full height of the build platform print in less than a day.
SLA 3D printers also come in multiple sizes ranging from desktop to large industrial printers. Historically, ‘top-down’ laser-powered SLA 3D printers were monolithic and very large; they took up meters of floor space and required auxiliary ventilation systems and dedicated circuitry. These industrial-sized systems were more common in previous decades for large corporations who could afford both the high cost of purchase and maintenance as well as the higher square footage and infrastructure requirements of top-down stereolithography printing.
Desktop-sized resin 3D printers were enabled by the invention of inverted SLA 3D printing, and as the technology was adopted by more manufacturers, smaller printers with cuboid build space of around 10-20 cm in each direction became the norm. For example, Formlabs' Form 3+ offers a 14.5 × 14.5 × 19.3 cm build volume, while Form 4 offers a 30% larger build volume at 20.0 × 12.5 × 21.0 cm.
Similarly, benchtop resin 3D printing was made possible by the combination of inverted SLA technology and improved peeling techniques. Benchtop 3D printers such as Form 4L, which offers a 35.3 x 19.6 x 35.0 cm build volume, are compact and easy to use while providing a build volume comparable to the traditional large industrial systems. These benchtop units excel at prototyping human-scale consumer goods, as well as creating end-use products through the use of 3D printed rapid tooling.
SLS 3D printers were also traditionally only available in large format, typically larger than desktop FDM or SLA printers, though recently there have been efforts to introduce desktop SLS to the market. However, the vast majority of SLS 3D printers are benchtop-sized or bigger — traditional industrial machines require large footprints. The Formlabs Fuse Series, which offers a 16.5 × 16.5 × 30 cm build volume, was the first printer to introduce accessible SLS technology in both cost and size — with the Fuse Series, small businesses with limited space could finally fit their equipment in-house.
Speed and Throughput
As more businesses turn to 3D printing for production as well as rapid iteration, 3D printing speed and throughput become a greater consideration when choosing a technology. The right 3D printer is one that produces high-quality parts quickly, without compromising on accuracy, reliability, or materials performance.
FDM 3D printing speed is limited by the extrusion process and the motor power. To create an accurate part, FDM 3D printers have to extrude filament at a specific rate, without deviation, and move the nozzle in the XY plane at an even, smooth pace. Speeding up that process can lead to variations in the mechanical properties of the filament and imprecise results.
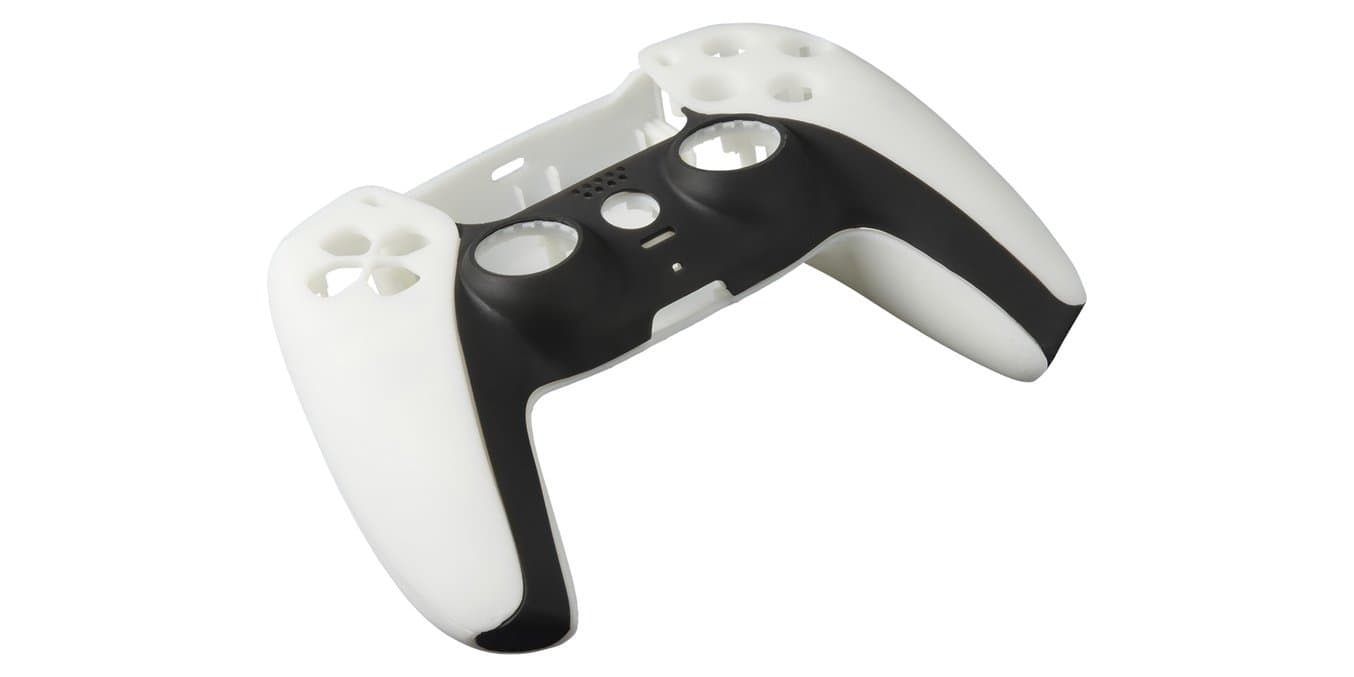
Print Speed Comparison: Gaming Controller
FDM 3D Printing | SLA 3D Printing | SLS 3D Printing | |
---|---|---|---|
1 assembly (3 parts) | 10 h 32 min | 2 h 36 m | 3 h 52 min printing (6 h 52 min cooling) |
5 assemblies (15 parts) | 52 h 40 min | 13 h | 9 h 38 min printing (13 h 47 min cooling) |
Compared printers and printing parameters:
- FDM 3D printer: Bambu Lab X1, PLA Basic, 120 microns layer height, 15% infill density
- SLA 3D printer: Form 4, Grey Resin, 100 microns layer height
- SLS 3D printer: Fuse 1+ 30W, Nylon 12 Powder, 110 microns layer height
For SLA 3D printing, typical print speeds vary by the type of 3D printing process, with the fastest type being MSLA technology. The latest generation of MSLA 3D printers, like Formlabs’ Form 4 and Form 4L, rely on a combination of a powerful print engine and advanced optics system to cure each layer almost instantly.
Form 4 and Form 4L have been engineered to build parts as fast as 100 mm per hour using specifically designed materials like Fast Model Resin. Most Form 4 builds finish in under two hours using any material, enabling multiple design iterations per day. With Form 4L, most builds finish in under six hours. Even builds that are the full height of the printer, or higher-volume production runs with multiple pieces covering the entire build platform, can print in less than a day, making same-day iterations of large parts or production at higher volumes possible.
All 3D printing processes have become faster over time, but none can match the progress in resin printing. When that speed is compounded day by day and week by week, the throughput benefits are extraordinary. Form 4 and Form 4L can now match the speed of high-throughput technologies such as injection molding. Printing full build chambers over the course of a few hours, multiple times a day, can rival the output of a medium-volume injection molding machine, without the high up-front cost of tooling.
SLS 3D printers are faster than FDM 3D printers because their high-powered lasers can be directed at each layer of powder and scanned across it faster than an extruder nozzle can move above an FDM print bed. However, the laser still moves slower than the light source flashing in DLP or MSLA resin 3D printer technologies. Though not technically print speed, SLS 3D printing processes also have to account for the cooldown time of the build chamber — because the laser sinters the powder at such a high temperature, the build chamber has to cool down before being post-processed, which can add to increased overall lead time for parts.
This combined print and processing time for SLS parts, however, is often not a concern for production. Though print speed for single parts may be slightly longer than other technologies, overall throughput is excellent for SLS 3D printers because of their ability to pack many parts into one build chamber. Their larger build volumes and nesting ability enable customers to densely pack parts within the chamber, utilizing the entire volume. For example, a fully packed print job on the Fuse 1+ 30W can be completed overnight during ‘dead time’ and the cooldown can finish outside the printer during the day, enabling same-day parts and 24/7 throughput. Additionally, post-processing can be quite short, since many steps can be automated with machines like Fuse Sift and Fuse Blast, and there are no supports to remove.
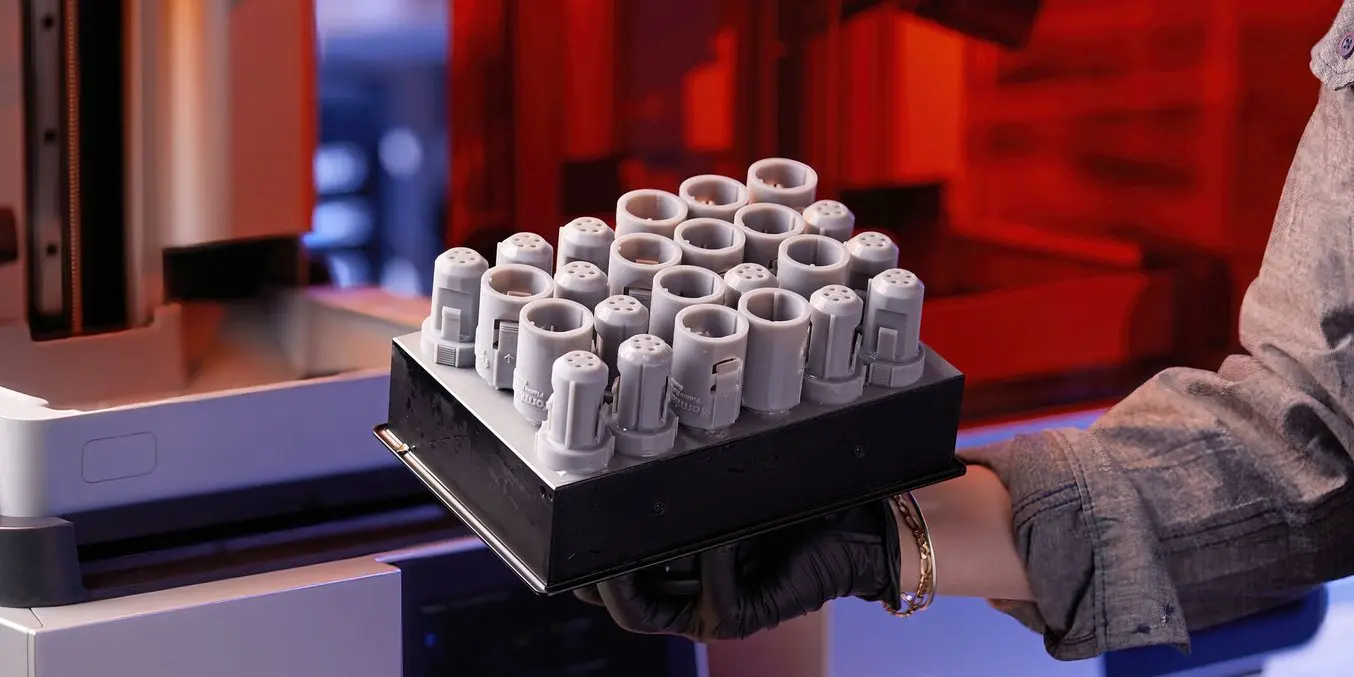
Print Speed Comparison: Electrical Connector
FDM 3D Printing | SLA 3D Printing | SLS 3D Printing | |
---|---|---|---|
1 assembly (2 parts) | 2 h 38 min | 1 h 3 min | 3 h 30 min printing (6 h 27 min cooling) |
50 assemblies (100 parts) | 84 h | 13 h 2 min | 12 h 59 min printing (13 h 49 min cooling) |
Compared printers and printing parameters:
- FDM 3D printer: Bambu Lab X1, PLA Basic, 120 microns layer height, 15% infill density
- SLA 3D printer: Form 4, Grey Resin, 100 microns layer height
- SLS 3D printer: Fuse 1+ 30W, Nylon 12 Powder, 110 microns layer height
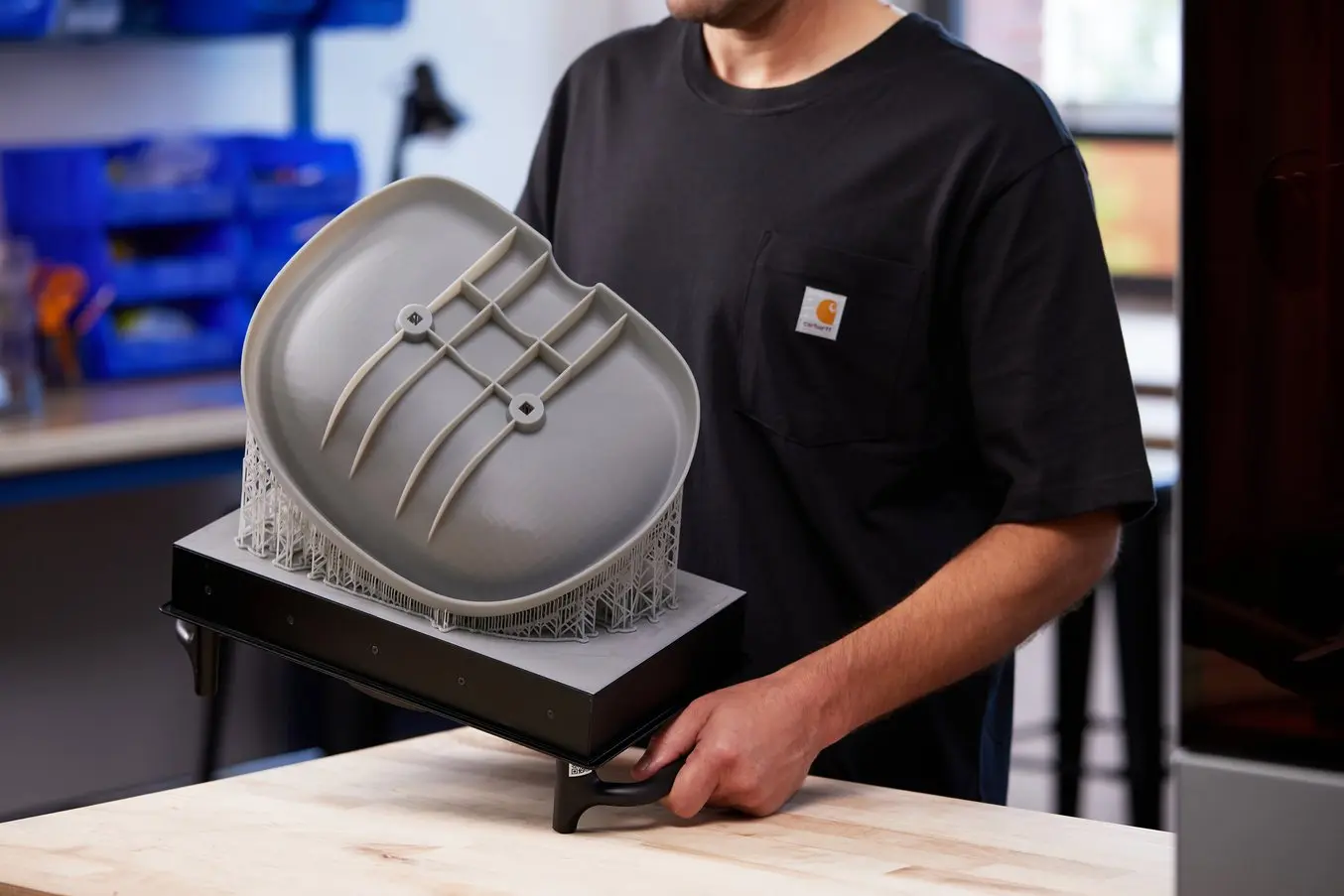
Print Speed Comparison: Radio Flyer Seat Prototype
FDM 3D Printing | SLA 3D Printing | |
---|---|---|
1 prototype | 42 hr 3 min | 2 hr 37 min |
Compared printers and printing parameters:
- FDM 3D printer: Ultimaker S7, PLA, 100 microns layer height, 20% infill density
- SLA 3D printer: Form 4, Fast Model Resin, 200 microns layer height
Costs and ROI
How much does an FDM, SLA, or SLS 3D printer cost and how fast does each help you achieve a ROI? To calculate ROI, you need an understanding of equipment purchase price, ongoing ownership costs, material costs, and labor.
One of the main selling points for FDM 3D printers is the low machine cost. With entry-level FDM printers available for only a few hundred dollars, hobbyists and small businesses can try FDM to see if 3D printing is something worth adding to their toolset. For those unsure of where to start, the lower cost of an entry-level FDM machine is often persuasive enough to justify a purchase. However, these low-cost FDM printers can be unreliable and often require an expert to keep them running in the long term.
Professional desktop FDM printers are easier to use and more tailored to businesses, with prices ranging from $2,000 to $8,000, while industrial systems are available from $15,000. These 3D printers generally provide better reliability, higher print quality, and larger build volumes. While these machines are suitable for producing functional parts, competition at this price point is fierce, as SLA machines offer a wider range of applications and better quality prints.
At the lower end of the range, low-cost resin 3D printers are available for $200 to $1000. These machines might be suitable for hobbyists or beginners, but they require calibration and fine-tuning for each resin type, and they are generally not reliable or durable, which will often lead to higher costs in terms of maintenance, sunk time, failed parts, and wasted material.
Professional SLA 3D printers are generally priced in the $2,500 to $10,000 range, while large-format resin 3D printers are typically more in the $5,000 to $25,000 range.
There are fewer options for SLS technology. Typically, SLS 3D printers have a higher price range than FDM or SLA, though accessible SLS has become possible in the last few years, which has given control over production to small businesses and enabled agile manufacturing options for larger businesses.
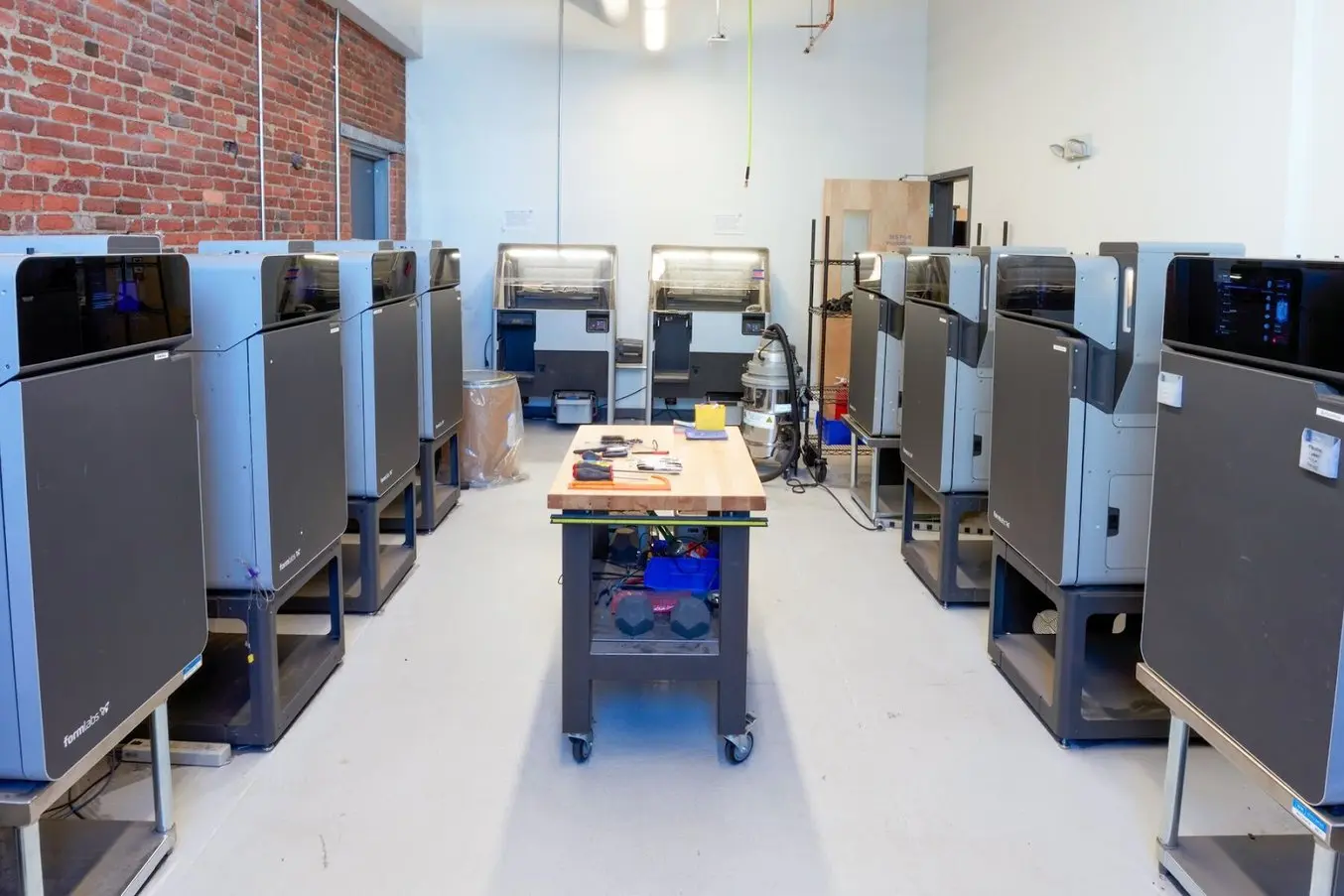
Affordable SLS has made it possible to scale up even with this industrial-power technology. The creation of accessible, affordable fleets like this SLS printer fleet makes 3D printing a cost-effective way to produce parts.
Historically SLS printers have been almost exclusively in the $200,000 and above range. With the introduction of the Fuse Series, accessible SLS was made available for the first time, and the ability to purchase an SLS printer for under $30,000 (printer and depowdering kit) was a completely unique idea. The Fuse Series set a new standard of accessibility, without compromising on industrial quality parts or power. For the entire ecosystem, including powder recycling and cleaning with Fuse Sift and Fuse Blast, to be available for under $60,000 is revolutionary, and has opened up opportunities for small businesses, individuals, and educational institutions to bring powerful powder bed 3D printing in-house for the first time. The next priced option is hundreds of thousands of dollars to purchase, with service plans that can run $30,000 each year. Formlabs makes SLS even more accessible by continuing to offer the previous iteration of the Fuse Series (the Fuse 1 printer) for an even lower price. For prototyping labs where high volumes and throughput aren’t top of mind, the Fuse 1 still delivers high quality SLS parts consistently.
When considering 3D printer ownership costs, printing material and consumables costs are important parts of the equation. FDM filaments are relatively low-cost compared to SLA 3D printing resins, both due to their ubiquity and their less complex manufacturing process.
Common FDM materials like ABS, PLA, and their various blends generally start around $30/kg, while specialized FDM filaments for engineering applications can be $100-$150/kg. Soluble support materials for dual extrusion FDM 3D printers sell for $100-$200/kg. These filaments are easily sourced, and due to their widespread use in a range of manufacturing processes, competition has driven prices down. Filament is shelf-stable and does not expire, so providers can set prices without factoring in shortages or demand shifts.
SLA resins have a more complex formulation, manufacturing, and storage process, all factors contributing to their higher price. Though more low-cost resins are available — and typically sold separately from printers as third-party solutions to existing machines — they require more fine-tuning, and come with issues like strong odors or potentially harmful chemicals.
General Purpose Resins from Formlabs are priced at $99 per liter, making high quality 3D printed parts more accessible and enabling wider access across multiple applications and industries.
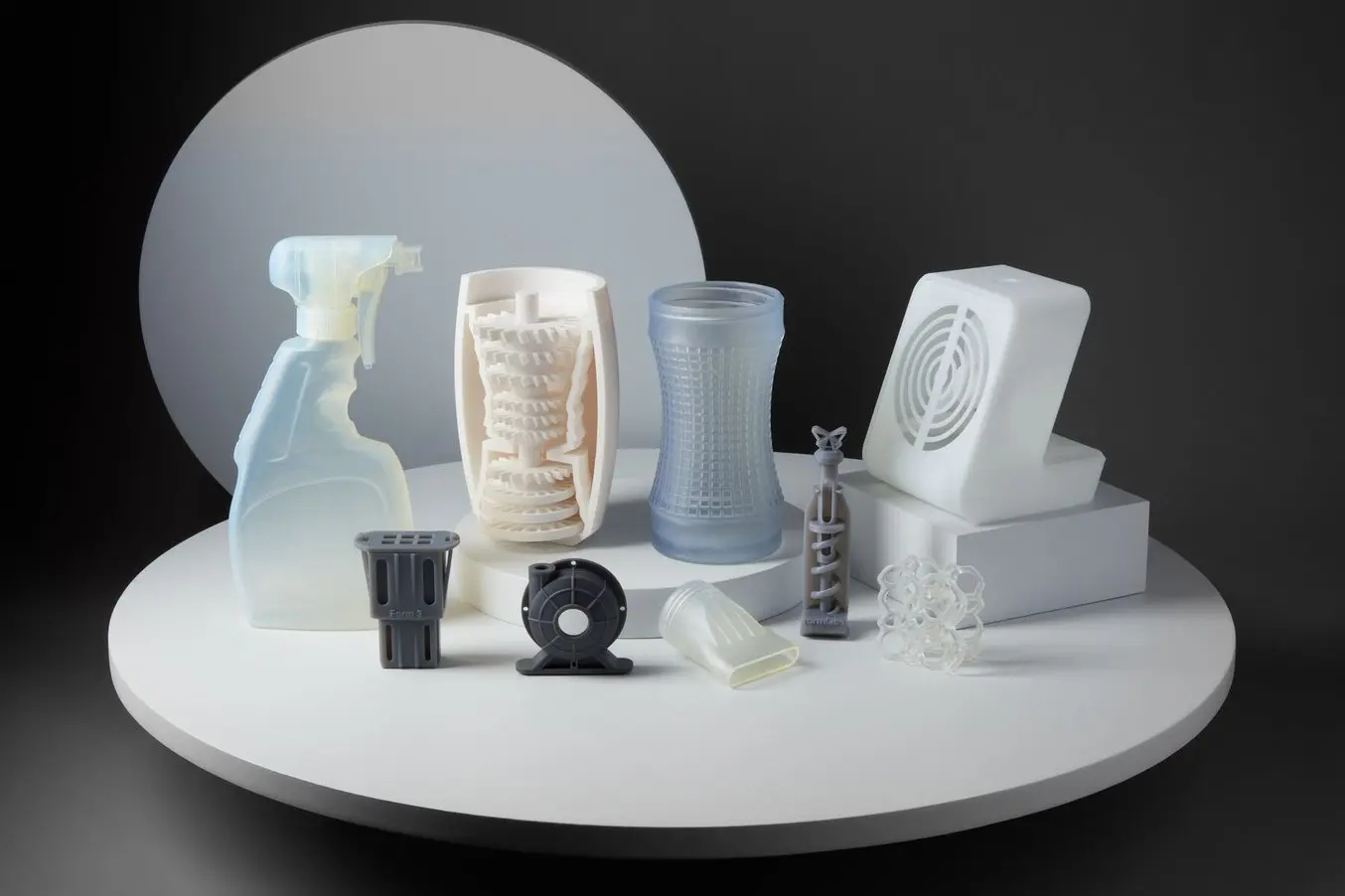
SLA resins are more costly than FDM filament for the simple fact that they are uniquely formulated for specific applications and manufacturing them costs more than purchasing industry-standard filament.
Resins are typically formulated by the printer manufacturer (though some manufacturers offer open platforms or simply white-labeled resins), and their price reflects the costly research that goes into their development. Manufacturers who produce their own resins also spend resources on testing and validating the settings for these resins to be used on the specific printer system. This investment into research and development has an impact on the cost to the consumer, but leads to better printing reliability and results. Manufacturer-specific resins are often brand new materials — not industry standards like ABS or PLA — and the work to develop them requires extensive resources.
Most SLS manufacturers offer powder at an industry-standard price of around $100/kg, though some, including Formlabs, offer discounts that are available for higher volumes. Lower cost per kg prices often come with a caveat: the powder costs less because those printers require you to space parts widely apart to reduce the potential for thermal buildup. Recommended pack density for these large monolithic systems is often limited to roughly 8-10%, which means that you’ll need to throw away as much material as the amount that goes into the printed parts. This means that those systems create a lot of unrecyclable powder, driving up the ongoing cost of printing. Formlabs’ SLS systems do not have a limit on packing density, and the higher the density, the more efficiently the printer is being run.
Labor costs are the final, often forgotten, part of the equation. FDM parts often require more extensive post-processing to achieve a smooth surface finish, especially if there are supports on the part. Some professional FDM printers offer soluble support materials, so that parts can be quickly post-processed in a solution that dissolves the support structure. However, FDM parts, even with soluble supports, may need more manual sanding to get them to the same quality and smoothness as SLA parts — if it’s even possible. For professional users, this added labor can often be the most significant factor driving up the overall cost per part of filament 3D printed parts.
SLA parts require washing and, depending on the material, also post-curing, but both of these processes can be mostly automated with accessories (like Formlabs Form Wash and Form Cure, and Form Wash L and Form Cure L) to minimize labor time. Professional SLA systems also come with software, firmware, and material engineering to enable light-touch supports and an easier post-processing experience.
Depending on the design, some SLA parts can also be printed without supports, while supported SLA prints only require a bit of sanding to remove support marks and achieve a high-quality finish.
SLS 3D printing requires post-processing to remove unsintered powder from the parts (but not supports, as none are needed) and media blasting to achieve a smooth surface finish. These processes can be easily streamlined and automated with post-processing solutions like the Fuse Sift and Fuse Blast, minimizing labor costs and ensuring consistency. Additionally, these automated tasks can be done in batches — lowering costs for labor in production volumes.
As a rule of thumb, FDM 3D printers will create the cheapest parts if you’re printing only relatively simple prototypes in limited numbers. SLA resin 3D printers offer higher resolution, better quality, and a wide variety of 3D printing materials at a slight premium, but the difference quickly diminishes when you print complex designs or larger batches due to the less labor-intensive post-processing. SLS 3D printers may have the highest up-front costs, but powder costs are competitive and labor costs can be minimal, making it the most cost-effective for high-throughput applications.
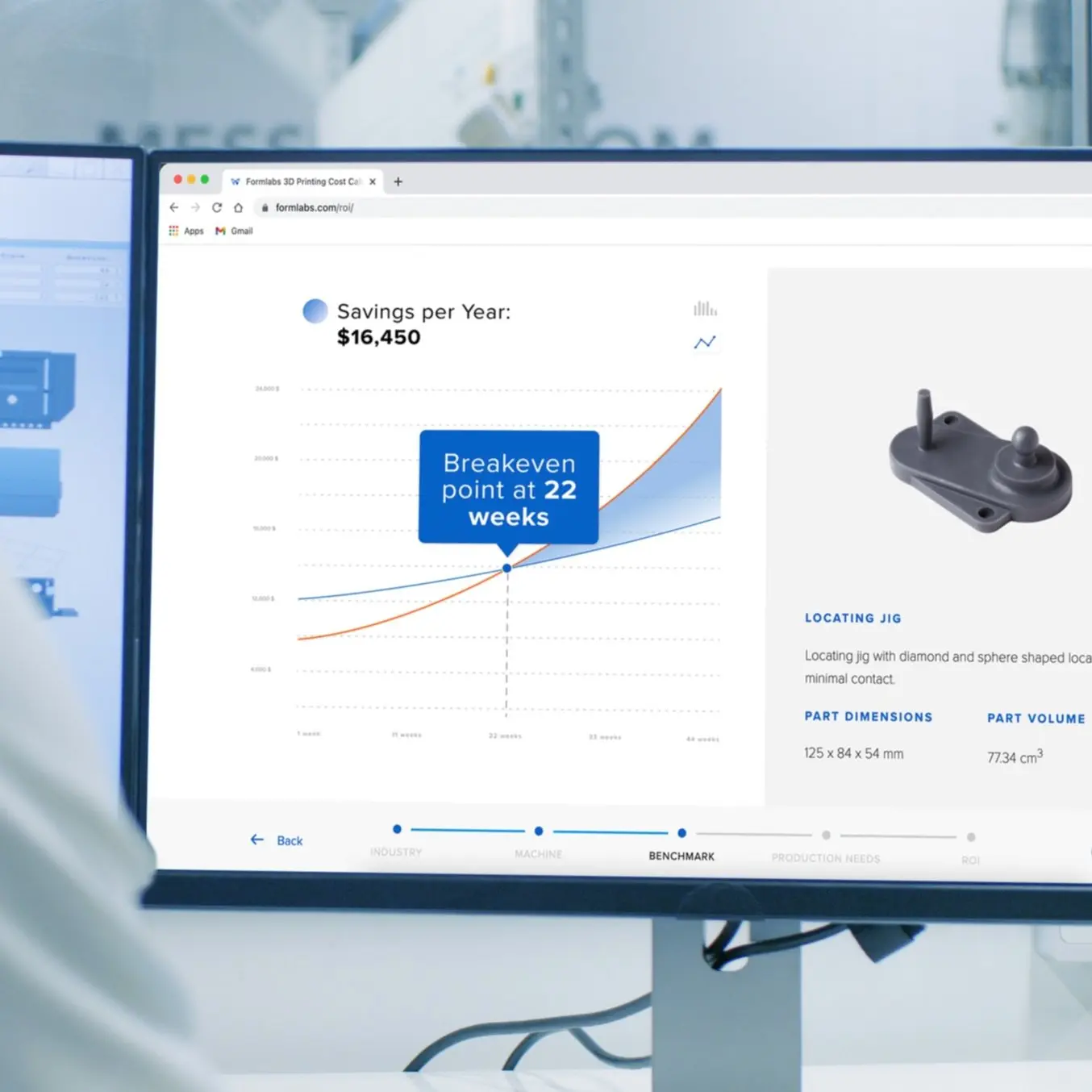
Calculate Your Time and Cost Savings
Try our interactive ROI tool to see how much time and cost you can save when 3D printing on Formlabs 3D printers.
Using FDM, SLA, and SLS 3D Printers Together
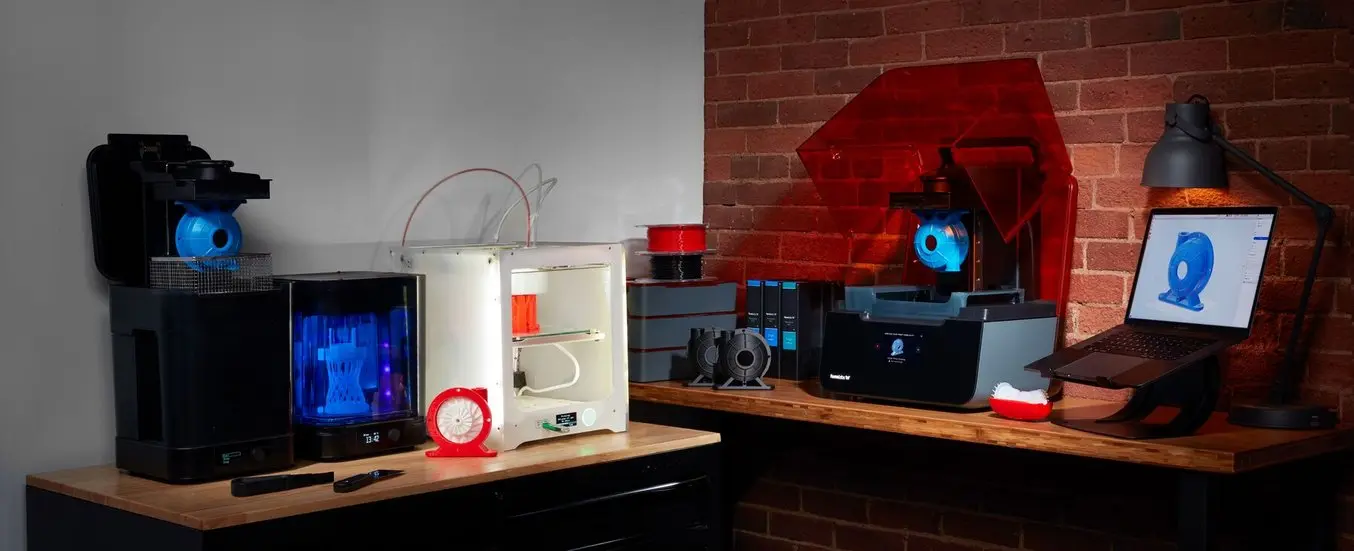
A majority of businesses that use 3D printing regularly in their workflow rely on more than one technology. Just like CNC or injection molding machines, 3D printers are seen as different tools in a toolbox for most engineers, designers, and manufacturers — there’s a right tool for each job depending on the needs of the part and the stage of the process. FDM, SLA, and SLS 3D printers excel in different areas and are best when used as complementary tools.
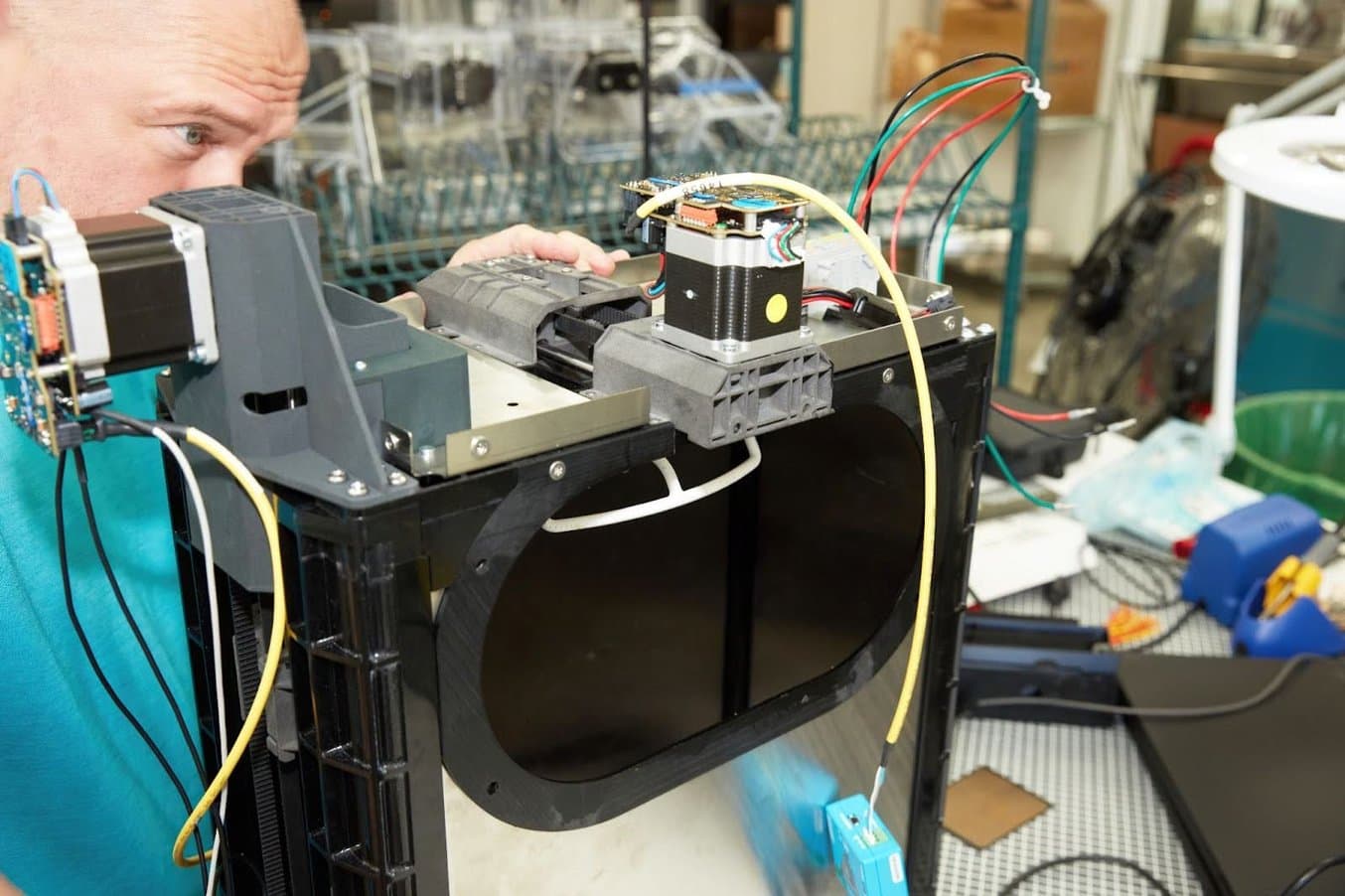
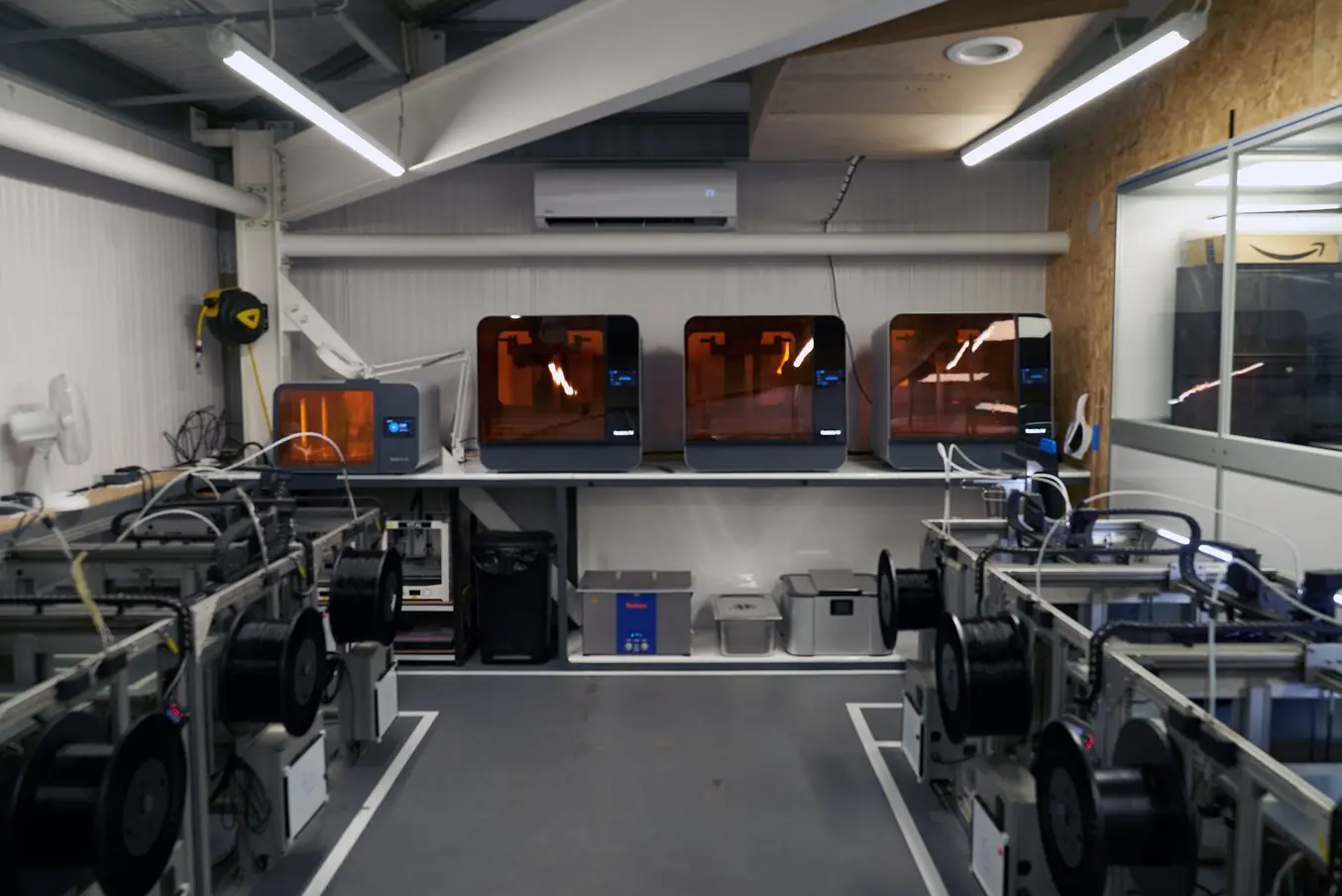
A few practical examples:
-
Brose uses FDM, SLA, and SLS technologies to produce everything from early-stage prototypes of automotive components to production runs of seat assembly parts in quantities of 250,000 or more.
-
Labconco utilizes SLA, FDM, and SLS technologies to produce end-use lab equipment product components, tooling, jigs, fixtures, and prototypes. Product Engineer Brent Griffith works through ideas on FDM printers to reduce prototyping costs before printing them with SLA or SLS for end-use deployment on their equipment or in their lab.
-
Hyphen leverages FDM 3D printers for quick design reviews, while they rely on their Form Series SLA printers for tooling parts and end-use components that require high accuracy and low friction. Their three Fuse Series SLS printers create end-use components that have to endure repeated stress and load-bearing or house delicate electronics components. Many structural pieces in their machinery are entirely SLS 3D printed.
-
Vital Auto lab manager Anthony Barnicott runs 14 large-format FDM printers, three large-format Form Series SLA printers, and five Fuse Series SLS printers to produce functional prototypes and design review parts for concept cars commissioned by brands like McLaren, Volvo, Nissan, Lotus, and more.
-
Black Diamond uses SLS 3D printing with the Fuse Series and Nylon 12 Powder to create end-use climbing gear components they’ll functionally test in real life in the Wasatch Mountains before investing in an injection molding tool. The Black Diamond team also uses desktop and benchtop Form Series SLA 3D printers for design reviews of large parts like helmets that need smooth, end-use quality surface finishes.
-
Foil Drive, a hydrofoil manufacturer in Australia, prints end-use electric engine enclosures on their Fuse Series SLS printer in volumes of 100-2000 parts. Nylon 12 Powder holds up to heavy use in underwater propeller assemblies, and SLS 3D printing makes sense for the mid-volume production levels they’re looking for. Foil Drive uses Form Series SLA 3D printers with Tough 2000 Resin and Rigid 10K Resin for propeller and impeller blades that can snap in and out — SLA is ideal because the tolerances make these small assemblies function smoothly.
Learn More About SLA and SLS 3D Printing
Download our white papers for a detailed overview of SLA and SLS ecosystems and the step-by-step 3D printing workflow.
Curious to see SLA or SLS quality first hand? Pick from our list of applications and request a complimentary sample part to find a material that meets the requirements for your project.