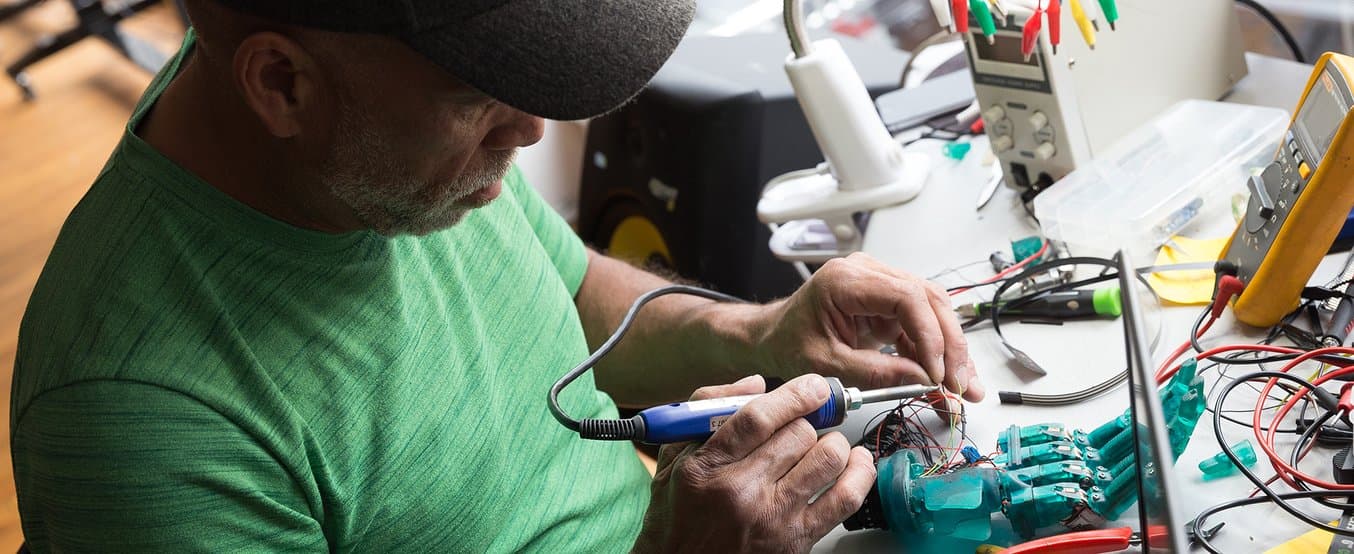
“Intestinal fortitude” is a phrase Lyman Connor uses to describe what it takes to tackle big challenges. And he’s been tested.
A near-fatal bicycle accident in 2013 led to a chance encounter in a hospital elevator that inspired Lyman to reimagine the way prosthetics are made. For the past several years he’s been designing a customizable bionic hand that can be manufactured and sold at a fraction of the price of the top-of-the-line models currently on the market, which can cost upwards of $70,000.
Using a small facility of four desktop 3D printers, Lyman completed and fit his first production prosthesis at the end of 2016. He’s aiming to build hands for 30 more patients this year.
By day, Lyman Connor works as a software engineer at General Electric. By night, he builds 3D printed prosthetic hands. Watch the video to explore his story.
The Boy in the Elevator
Lyman’s bicycle accident broke nearly all of his ribs, punctured a lung, and left him with over 10 fractures in his skull. On the day he was discharged from the hospital, after weeks of healing and rehabilitation, he encountered a young boy with his parents in the elevator. Feeling a tense atmosphere, Lyman tried to lighten the mood.
“I said, ‘Hey, things can’t be that bad. Take a look at my face,’ because my face was still pretty messed up at the time,” Lyman said. “Right away the boy just raised his hand and said ‘At least you were born with your whole hand,’ and his mother immediately replied ‘If we had $50,000, we’d get you one.’ I didn’t know what to say.”
Captivated by the cost of $50,000 for a hand, Lyman spent his recovery researching the prosthetics industry. Frustrated by what he found, he began to form a plan to flip it on its head.
Changing an Industry
According to the Amputee Coalition of America, over 60,000 people a year in the U.S. lose an upper limb, and only about half use prostheses.
“You get racked and stacked based on your age, physical attributes, how active your life is, things of that nature,” Lyman said. “That defines what kind of prosthesis you actually end up with. So just because you may want a prosthetic hand, doesn’t mean that you’ll qualify for it, even if your insurance will pay.”
Upper-limb prostheses range from hooks to bionic devices designed to mimic the motions and grips of real hands. Often, these devices are myoelectrically controlled, relying on muscles in a person’s residual limb to control their functions.
Prosthetics are also traditionally only available in a few sizes, so patients must make do with what fits best.

Lyman set out on a mission to design a prosthetic that would be customizable to fit any patient, have the same capabilities as top-of-the-line $50,000 hands, and cost a fraction of the price.
“There’s no reason these devices have to be so expensive,” Lyman said. “I want to flip the whole paradigm with respect to who gets prosthesis, what type of prosthesis you get, and the lifecycle associated with them.”

Lyman’s nonprofit Handsmith helps to alleviate the costs of his product, named the Mano-matic, for those who cannot afford it. Learn more about how 3D printing is impacting the healthcare industry.
Rapid Prototyping with 3D Printing

Lyman realized early on that he wanted to use stereolithography (SLA) 3D printing for prototyping. After initially working with a service bureau to produce prototypes, he decided to invest in a Form 2.
“I started thinking, what’s going to be the aggregate cost of me sending these parts back and forth,” Lyman said. “I decided to make the investment to be able to print in-house, with the ability to choose between different resins and fully understand the different properties, and be able to do that overnight versus sending a part out and waiting two weeks to get it back.”

Lyman used Formlabs Tough Resin to construct the Mano-matic. Request a free sample of Tough.
Lyman connected with Eduardo Salcedo, a researcher in the mechanical engineering department at Indiana University–Purdue University Indianapolis (IUPUI) to help bring his prototyping to the next level.
“Eduardo came into the project to modify and perfect all the cosmetics for the hand and to help me get the hand to a level to where it was going to be production ready,” Lyman said.
Eduardo separated the components of Lyman’s design so that they could be easily modifiable for different sizes.
“If a part is ever damaged during use, we can go back and just reprint a piece of that specific hand. Or in the future, if we make improvements, we can easily swap pieces out and not need to redesign everything again,” Eduardo said.

Eduardo and Lyman worked together remotely for two months. Because Eduardo also had access to a Form 2, the duo was able to seamlessly collaborate on designs.
“Despite Lyman and I being in different parts of the country, we could start with one design one day, go through a critique process, change the files, and then hit print. Twelve hours later, we both have the same actual physical part in our hands,” Eduardo said.
“This means is that, in the future, if there’s someone in need of a prosthesis somewhere else in the world, we can just transfer those files, they can hit print, and within 24 hours they can have their own prosthesis without us ever meeting the patient.”
Choosing a Process for Agile Production
To make a truly affordable hand, Lyman knew he needed to be able to cost-effectively produce custom parts in volume. Initially, he was only going to use SLA 3D printing to prototype.
The cheapest manufacturing method in the long term was injection molding, but the initial cost of tooling for just one size of hand would exceed $160,000. Even after an angel donor offered to cover those costs, Lyman knew that working with injection molding was going to limit his ability to deliver a customized product economically.
“Choosing a tool and die manufacturer, I was going to be stuck with one size hand,” Lyman said. “I wanted to do something that I could scale according to what’s going to be most compatible with what a patient already has. The most affordable way to achieve that was 3D printing.”
Learn more about how 3D printing can improve manufacturing processes.
Lyman built his production facility around four Form 2 3D printers, and found that this arrangement enabled him to design, prototype, and manufacture all in the same space.
“I don’t need milling machines, I don’t need all this other pie-in-the-sky $70,000 pieces of equipment. I have everything that I need,” Lyman said. “It’s kind of like an assembly line. As things come off the printers, I can test fit, integrate the code, check functionality, and move on to the next part. It’s an amazing, real-time iterative process, all in one room.”

“The really cool thing about this is that anyone that has a passion and a vision to create a product can get started with just one printer,” Eduardo said. “Then, once you’re ready to scale up, start using multiple printers to ramp up production.”
Learn more about setting up and managing multiple 3D printers in our free white paper.
Bringing the Mano-matic to Market
The first person has been fitted with Lyman’s Mano-matic, and more are lined up to receive hands in 2017. With 3D printers whirring by his side, Lyman’s not done spending his evenings in the lab, producing a product that could revolutionize an industry.
“One of the most exciting aspects of this project is where I am at right now,” Lyman said “I initially set out to help one person, and now I’ve realized that I can impact the lives of thousands of people.”