Marco De Rossi moved from Colombia to Europe to study product design at the Politecnico di Milano. Back then, 3D printers were more rare sights even at universities, but after having a chance to work with the technology during his studies, he wa s convinced of its potential and decided to pursue a PhD in digital manufacturing in medicine at the Politechnic University of Valencia in Spain.
While the university in Milan was well-equipped with laser scanners, 3D printers, and advanced visualization equipment, the new institution lacked access to digital manufacturing tools, so he had to start with setting up a lab from scratch. “I had to create a 3D printing lab before I even had a chance to start my PhD,” said Mr. De Rossi.
Starting with a very limited budget, Mr. De Rossi became an advocate for digital manufacturing and built a three-room lab with a wide range of tools that can now self-sustain itself. Along the way, he worked with researchers, engineers, and doctors on numerous projects including anatomical models, replacement parts for an X-ray machine, and reverse engineering for aerospace analysis.
Read on to see these applications and learn practical tips for setting up a lab, including how to acquire the right resources, collaborate with the local community, and hire engaged personnel.
Four Tips for Setting Up a Digital Manufacturing Lab
Start Small and Get Experience
Starting a lab from scratch might sound like a daunting task at first, but Mr. De Rossi found that it’s easier to break it down into smaller steps with clear goals.
“In the beginning, it's very difficult, but you need to have a starting point. My suggestion would be, get authorization to have a space at the university and get some experience with digital fabrication. With that experience, look for a grant. You simply cannot wait until you have the money to start. You have to start somewhere, even if it's an inexpensive printer at the beginning to experiment with and to show and get people excited about,” said Mr. De Rossi.
“Then, apply for grants and support from other researchers. All I started with was a room and secondhand, inexpensive equipment. Probably our biggest breakthrough was when we managed to have a grant. We had $25,000 to buy equipment. But you will not get to a $25,000 grant if you don't have something to show” said Mr. De Rossi.
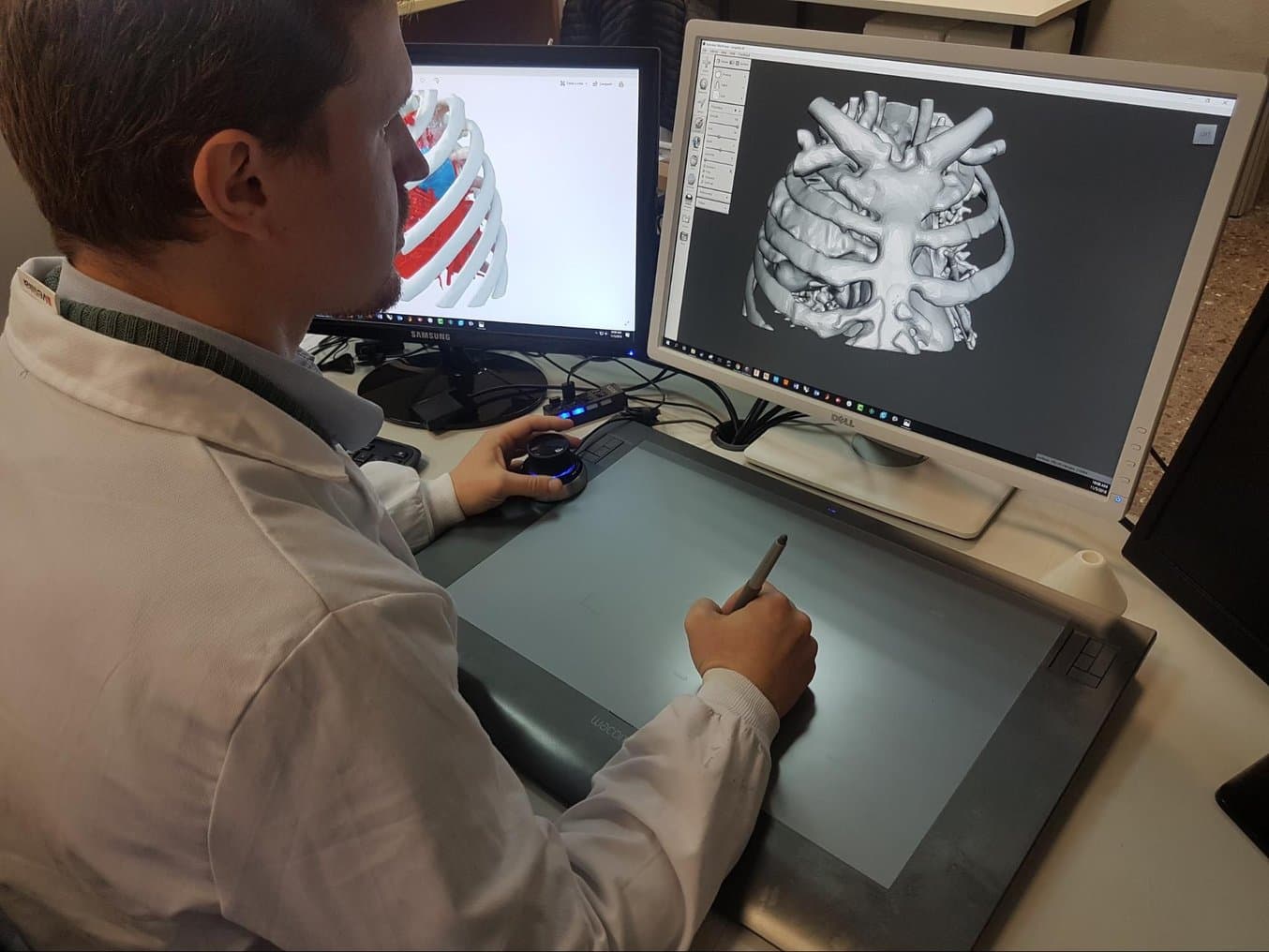
Anatomical models are based on CT or MRI scans of a patient. The scan data needs to be segmented in software to isolate the areas of interest for the 3D printed model.
Collaborate With Other Researchers
Mr. De Rossi found that collaborating with other researchers and offering his knowledge and access to digital fabrication tools in exchange for resources was beneficial for both his PhD and the 3D printing lab.
“You have to find a way to make money to maintain the project. You can work with other researchers to find ways to buy equipment and materials. Universities are very big entities and they have very strict budgets. Once you stumble on a project that has the budget to buy equipment, then you can coordinate with them and say ‘we have the knowledge, we will help you with your project [in exchange for letting us keep the printer at the end of the project]’,” said Mr. De Rossi.
Share Resources With the Community
“I have seen research projects that have a lot of money at the beginning, but they spend it all on a printer and they keep it in a corner. They use it a couple of times and that's it. When you have a big project that manages to build a lab only for itself, in the end, it will not be used enough. This idea that you want to have it all for yourself because you want to control it, in the long run, is detrimental for your own project and also for the community in general,” said Mr. De Rossi.
“A lot of resources could be shared, we're in the era of the sharing economy. You want to have an investment used by as many people as possible. When you manage to collaborate, you can invest in better equipment, better-trained personnel, better infrastructure. That is a nice thing about the university,” said Mr. De Rossi.
Mr. De Rossi found that often people would drop by the lab to proudly showcase a little project they did by themselves, but would always find themselves blocked from developing the project further because they did not have access to prototyping equipment. If they had to invest the time and money to buy a printer and learn all the necessary skills by themselves they’d probably simply abandon their project. But when they have access to machinery and help from others with experience, most projects continue and have a chance at becoming a reality.
“That is probably why fab labs are a big success, because it's a place where you have concentrated resources and you can go and really take advantage of all that. You will only use a little fraction of the resources and help a little bit, but you're collaborating to sustain a big project,” said Mr. De Rossi.
Maintain Human Resources
“You have to guarantee there is a way to maintain human resources at the lab. Otherwise, you will have the space, the machines, the materials, but you will not have someone who knows how to use them. You need to have a long-term strategy on how to always have people working at the lab,” said Mr. De Rossi.
Some universities hire technicians to operate the equipment and maintain the lab, but that’s only part of the deal. Mr. De Rossi found that there needs to be someone who is also willing to assist with the tools and help others learn how the technology works. It could be a professor, a PhD student, or someone who is passionate about teaching anyone who comes through the door.
“It's a good idea to have a PhD student in that situation. Because that is the purpose of a PhD student. To learn how to research, how to explain, and how to teach. People are here because they want to learn. If you offer them the opportunity to use the machines, the materials, and the opportunity to get involved with the project, they will give you their time in exchange,” said Mr. De Rossi.
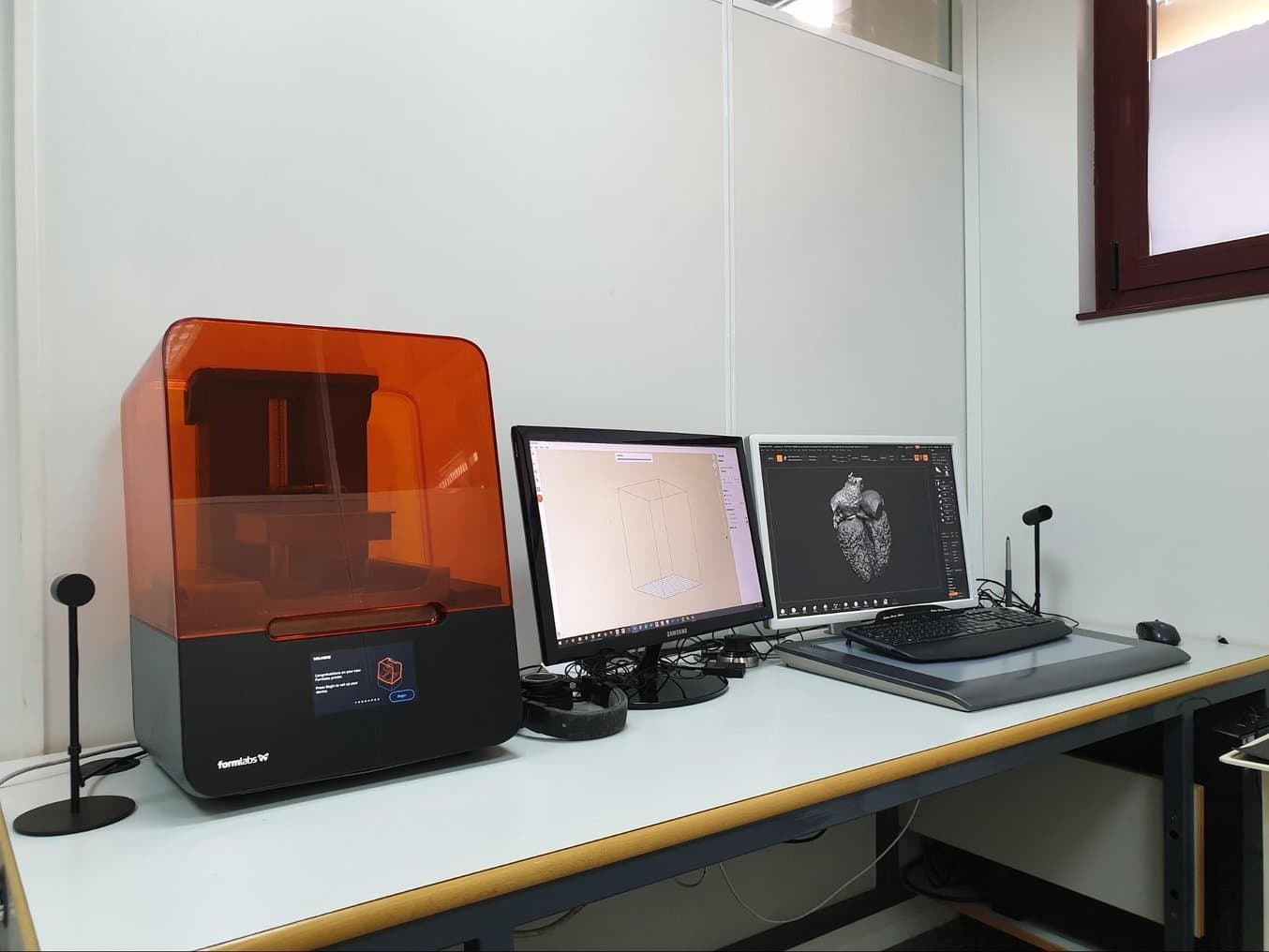
The lab consists of three specialized independent rooms. A clean design room hosts the desktop 3D printers, including this workstation with a Form 3 SLA printer.
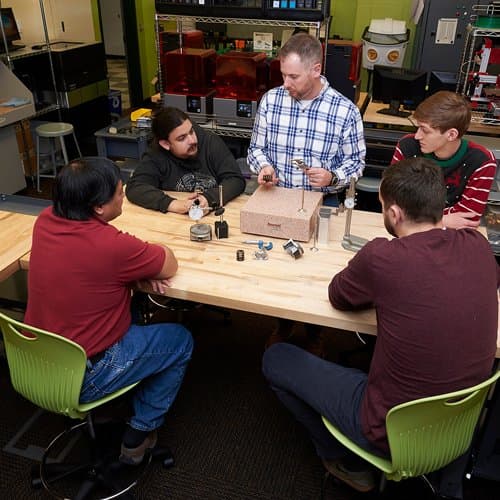
Guide to 3D Printing In Education
In this guide, we’ll discuss the benefits of 3D printing in education, from improved student collaboration to workforce development and empowered creativity.
Projects From Reverse Engineering to Anatomical Models
The lab at Universitat Politècnica de València currently consists of three specialized independent rooms. One room has different digital fabrication tools, such as a laser cutter, small CNC machines, a powder-based binder jetting 3D printer, and some designated place for painting and other activities that can be messy. The next room has traditional tools, such as saws, drilling machines, and other hand tools.
At last, there’s a clean design room that hosts the desktop 3D printers, including a Form 2 and a Form 3 stereolithography (SLA) 3D printer, multiple fused deposition modeling (FDM) printers, and a design station. As the lab's toolset grew, the more colleagues at the university became interested in bringing their projects into the lab.
“If you build it, they will come as they say. We constantly do work for researchers, for students, for the industry,” said Mr. De Rossi.
One of the most common applications is reverse engineering specific components, for example for aerospace analysis of jet turbine components.
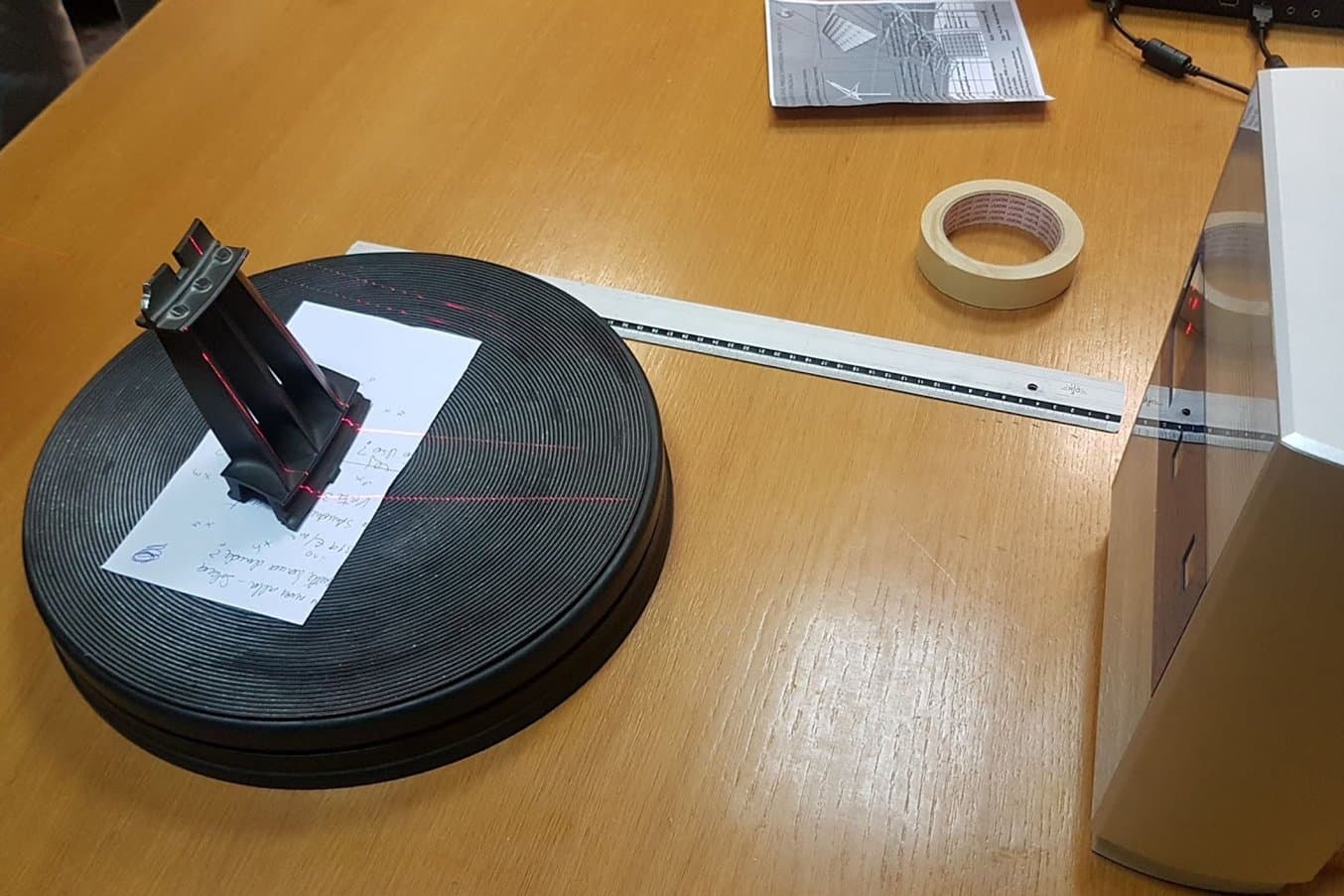
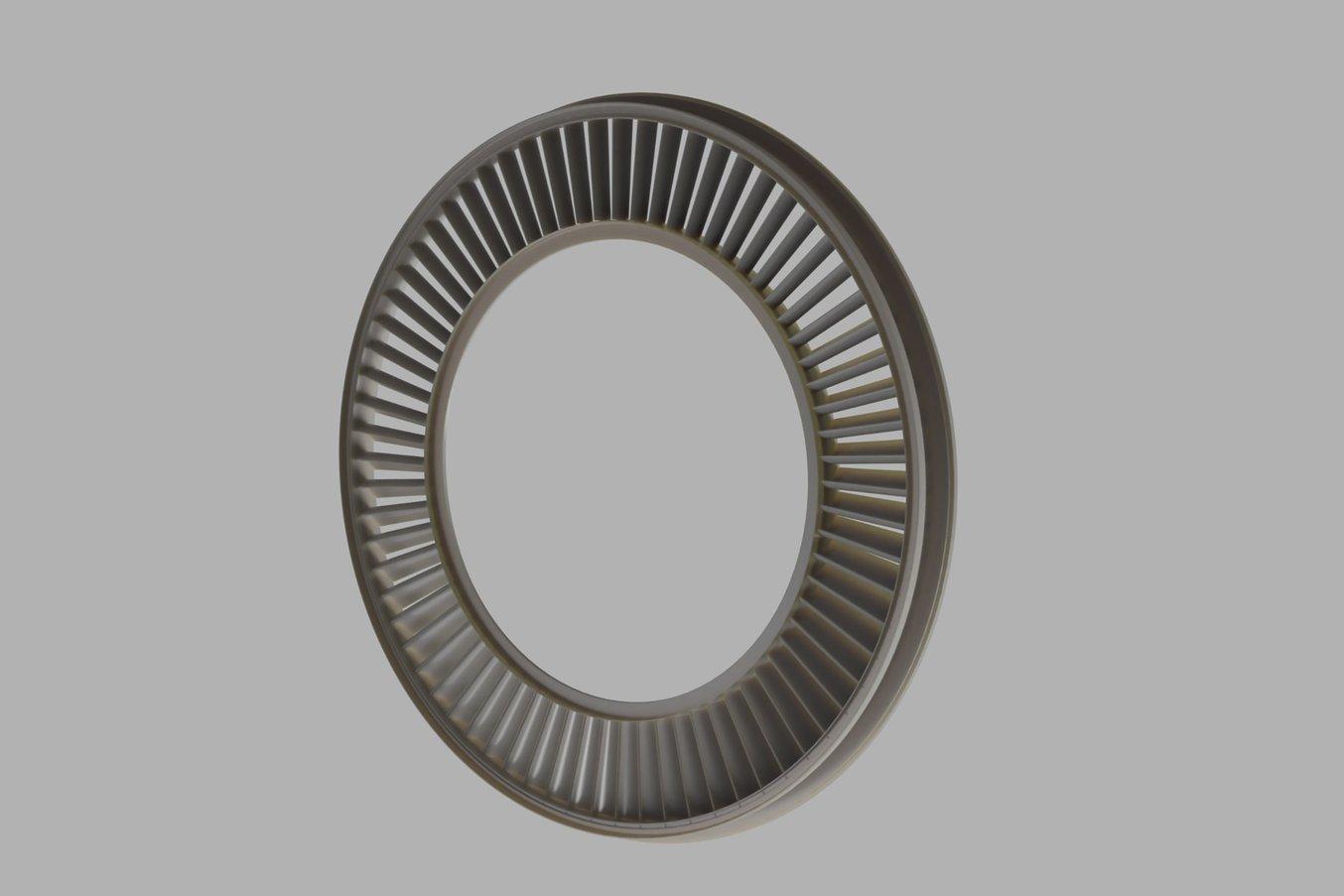
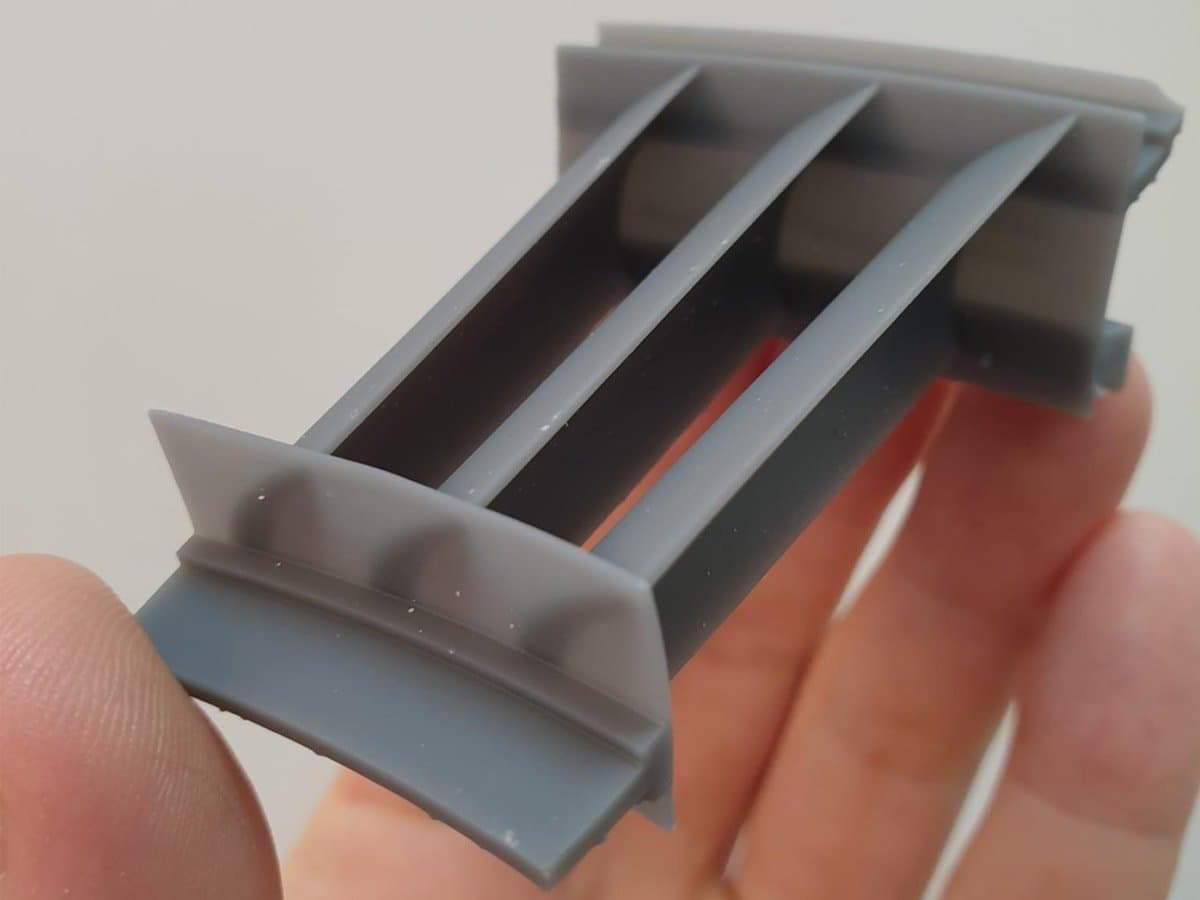
3D scanning of a section of airplane turbine compressor (top left) and the 3D reconstruction of the complete compressor ring (top right). The part was 3D printed on the Form 3 and used in an air tunnel test (bottom).
“We grab a small section of a wing or a jet turbine. Then we 3D scan it, reverse engineer it to a model and 3D print it with an SLA 3D printer. Because it has a very small surface and very fine details, it's important to be able to reproduce all those laser thin parts. In the end, we put it in a wind tunnel to make sure that it would work. There are a lot of very complex objects that you cannot easily design again,” said Mr. De Rossi.
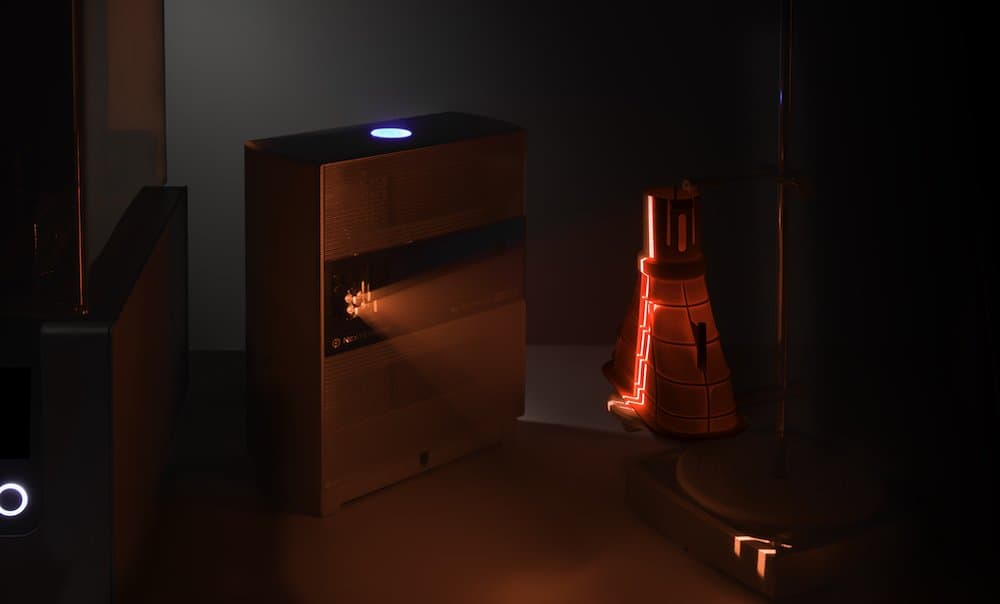
3D Scanning for Reverse Engineering, Restoration, and Metrology
This white paper provides a detailed look into how to start using 3D scanning to improve part design and production and how, paired with 3D printing, scanning technology workflows can be effectively applied to replication and restoration, reverse engineering, and metrology.
Download White Paper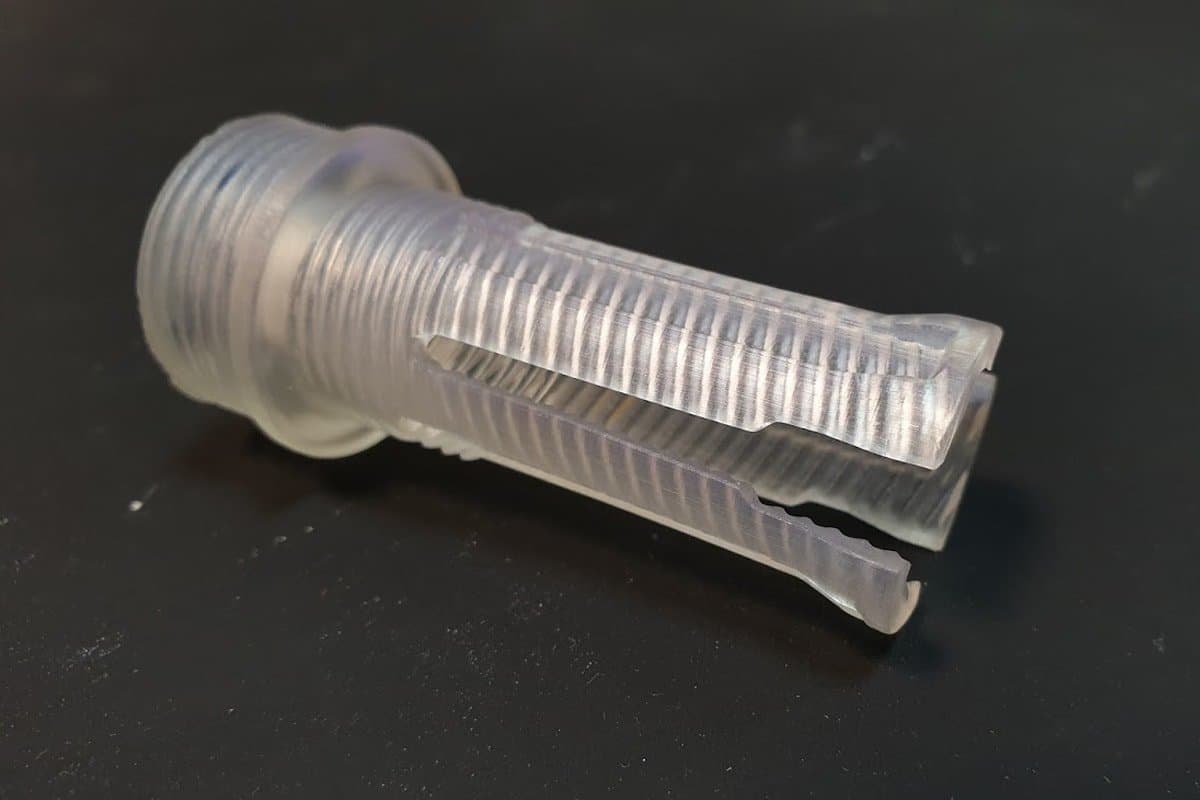
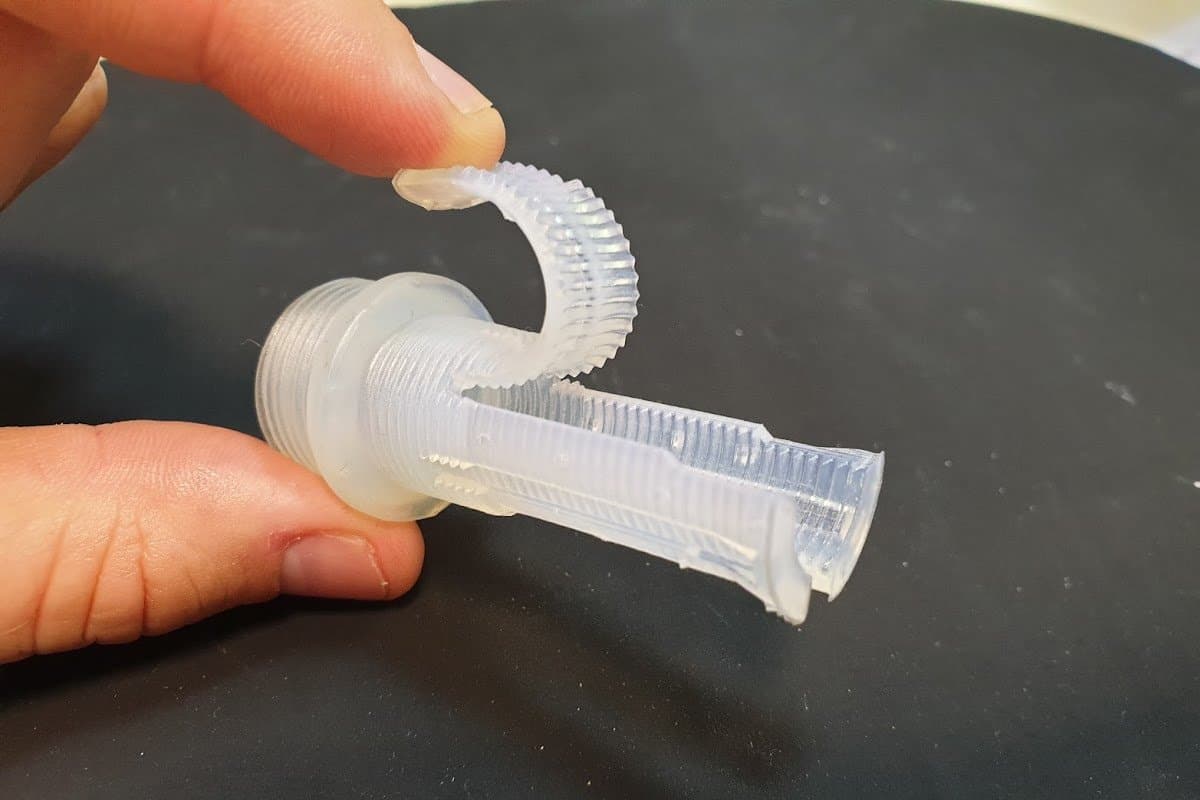
This replacement part for an X-ray machine was 3D printed with Durable Resin to withstand the expected use.
“Once we reverse-engineered a part for an X-ray machine. X-ray machines are expensive and hospitals might use them for a decade or more. At the end of their lifetime, many of the components are unavailable, but you still need the machine. There was a small part that was failing. Just because of that little plastic part, we were going to have to stop using a machine that’s worth over $100,000. They brought me the part, we 3D scanned it and reverse engineered it with multiple software. We printed it with Durable Resin on a Formlabs printer. It came out perfectly. The machine has been working for over a year without any problem,” said Mr. De Rossi.
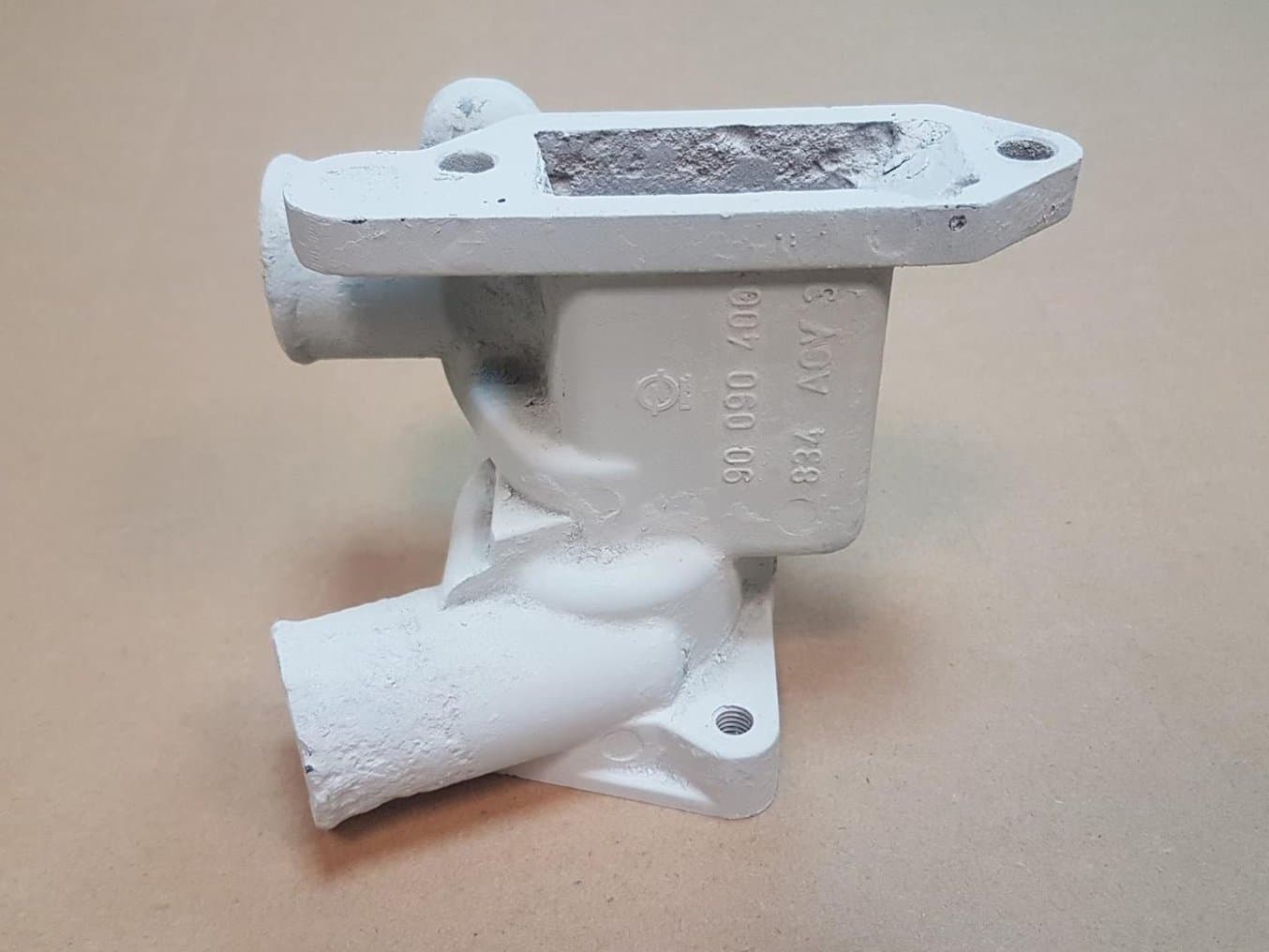
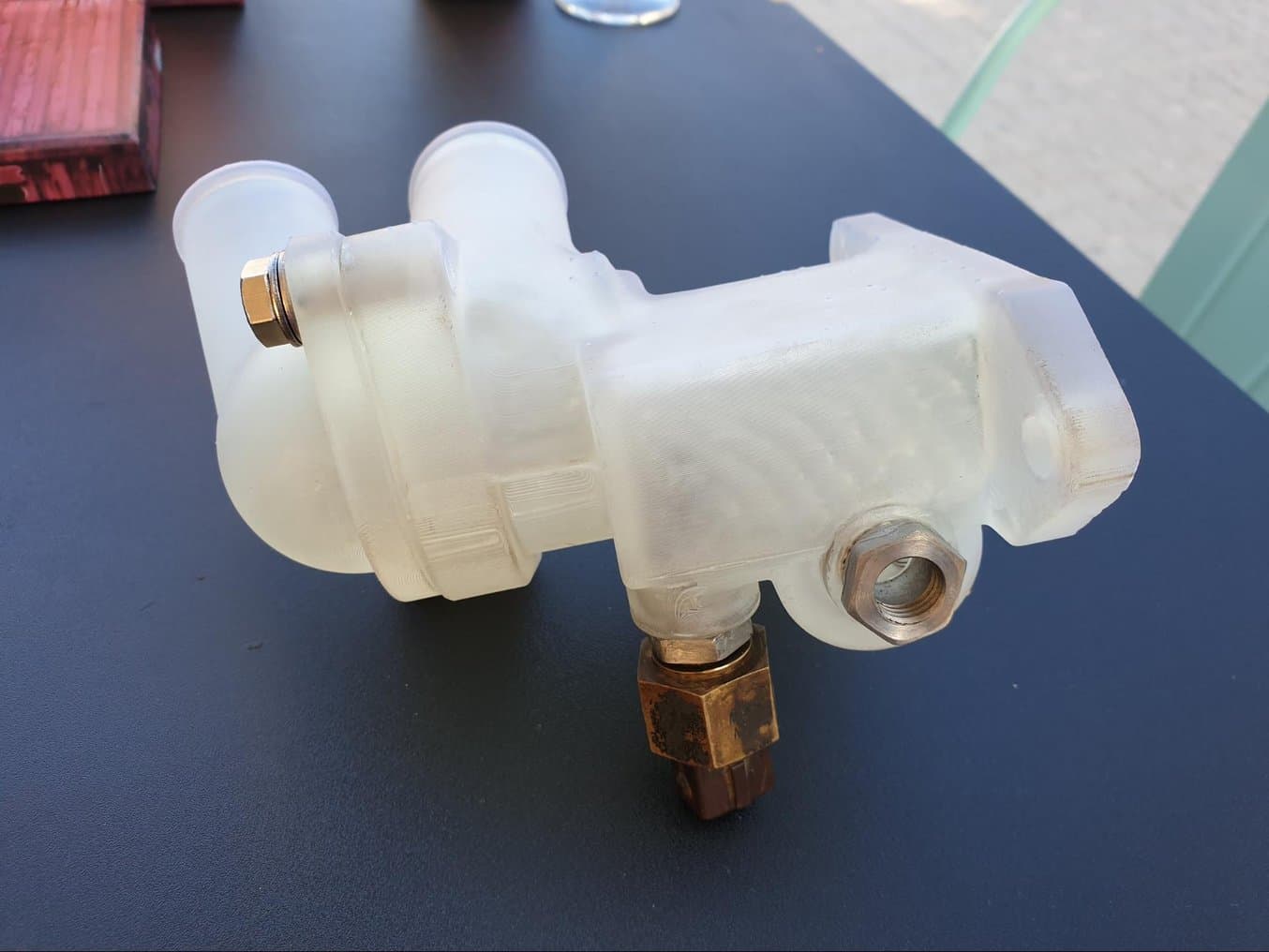
One of the projects involved reverse engineering a corroded thermostat for a vintage car. The failing part was painted in white for scanning, reverse engineered in CAD, 3D printed in High Temp Resin for thermal resistance, and then assembled with threads and metal components by a traditional milling specialist.
True to the topic of his PhD, Mr. De Rossi has done a lot of projects for the medical field.
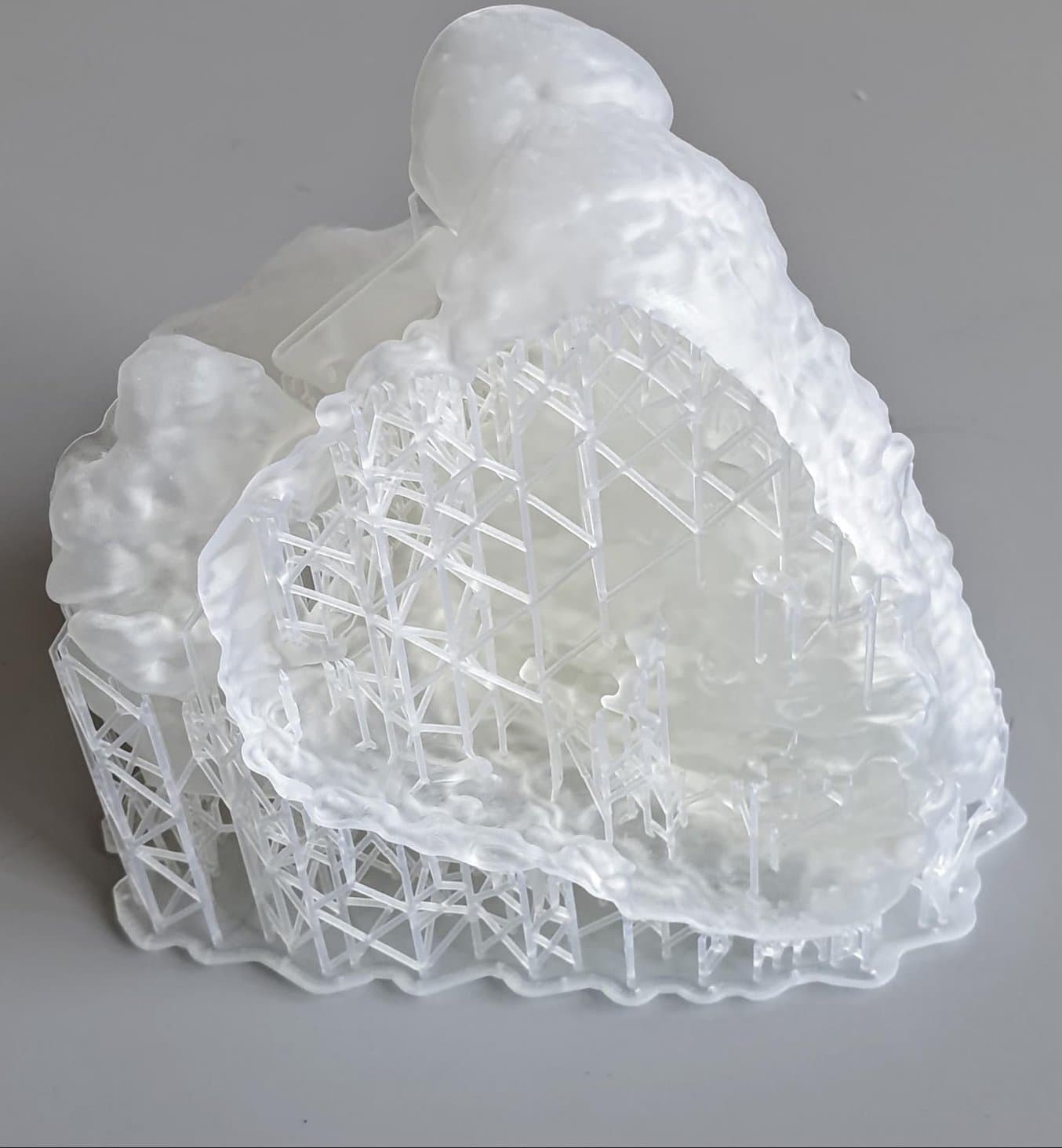
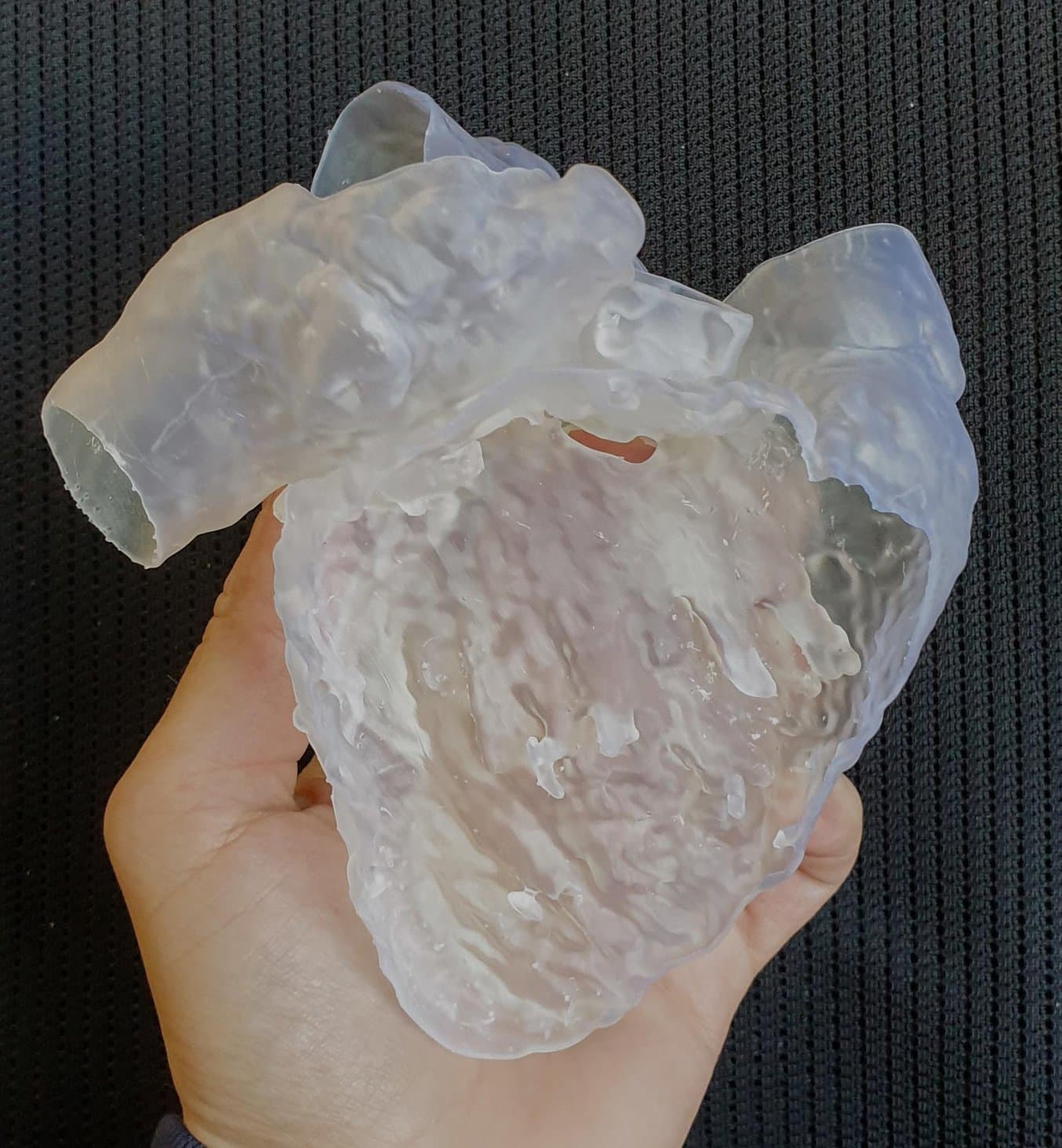
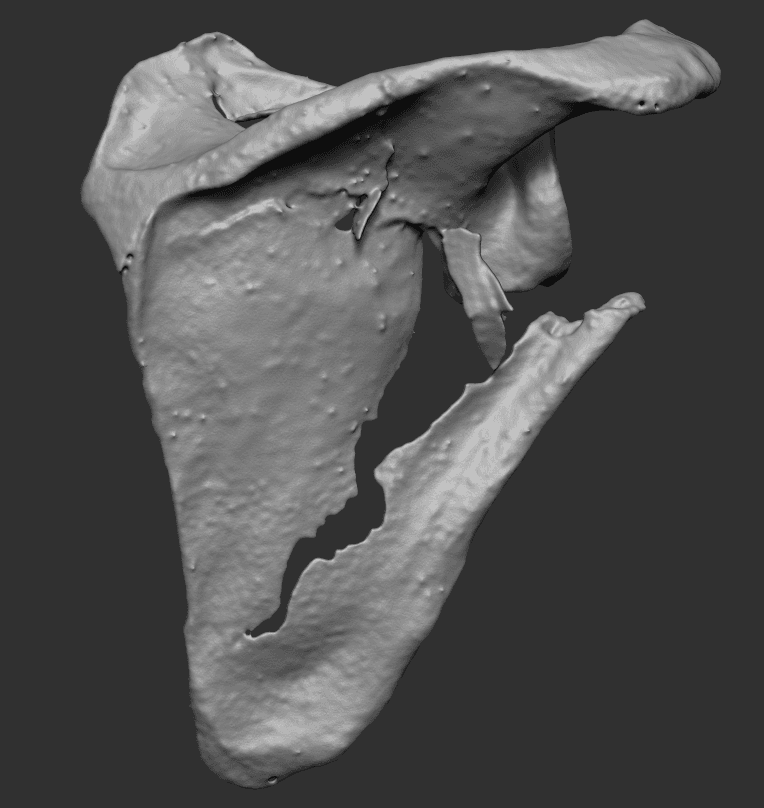
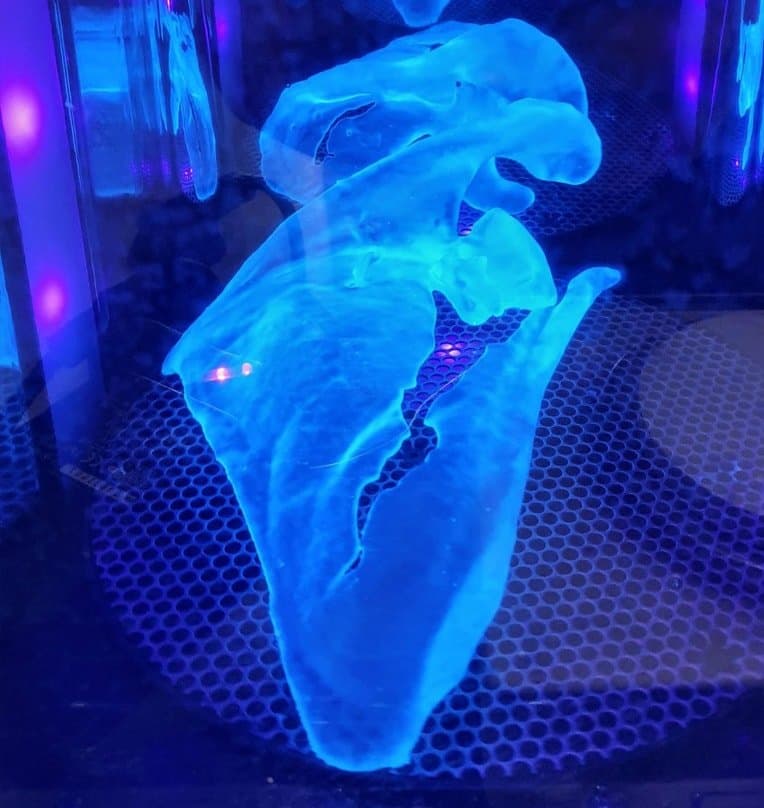
3D printed heart model for surgery preparation with supports (top left) and supports removed (top right). 3D digital model of a fractured scapula (bottom left) and the 3D printed model being post-cured in a Form Cure (bottom right) .
“Probably my most sophisticated and complex work is in pediatric cardiology models. It's super complex. You have tiny little hearts and surgeons need 3D models to really understand and visualize them. In some places, they use jetting 3D printers that cost a quarter of a million dollars. But we've been working with surgeons in hospitals and we do it with Formlabs 3D printers and they're more than satisfied. It's amazing,” said Mr. De Rossi.
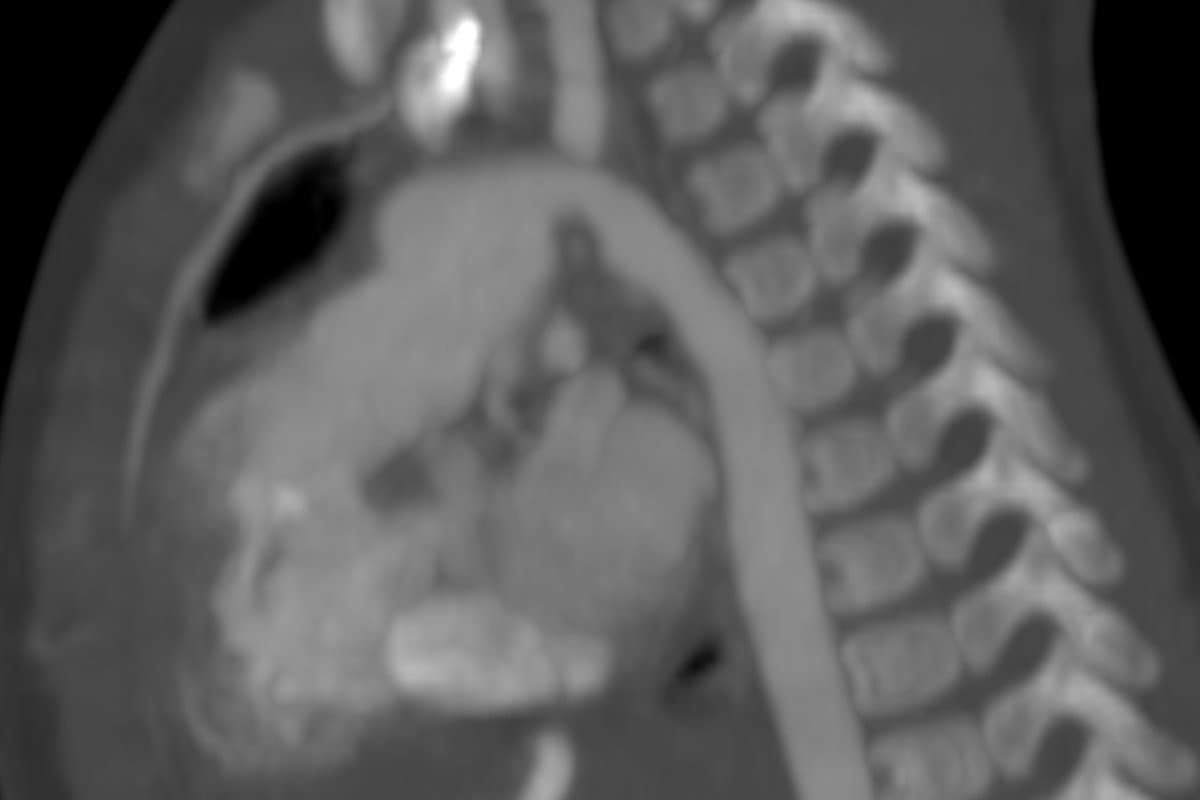
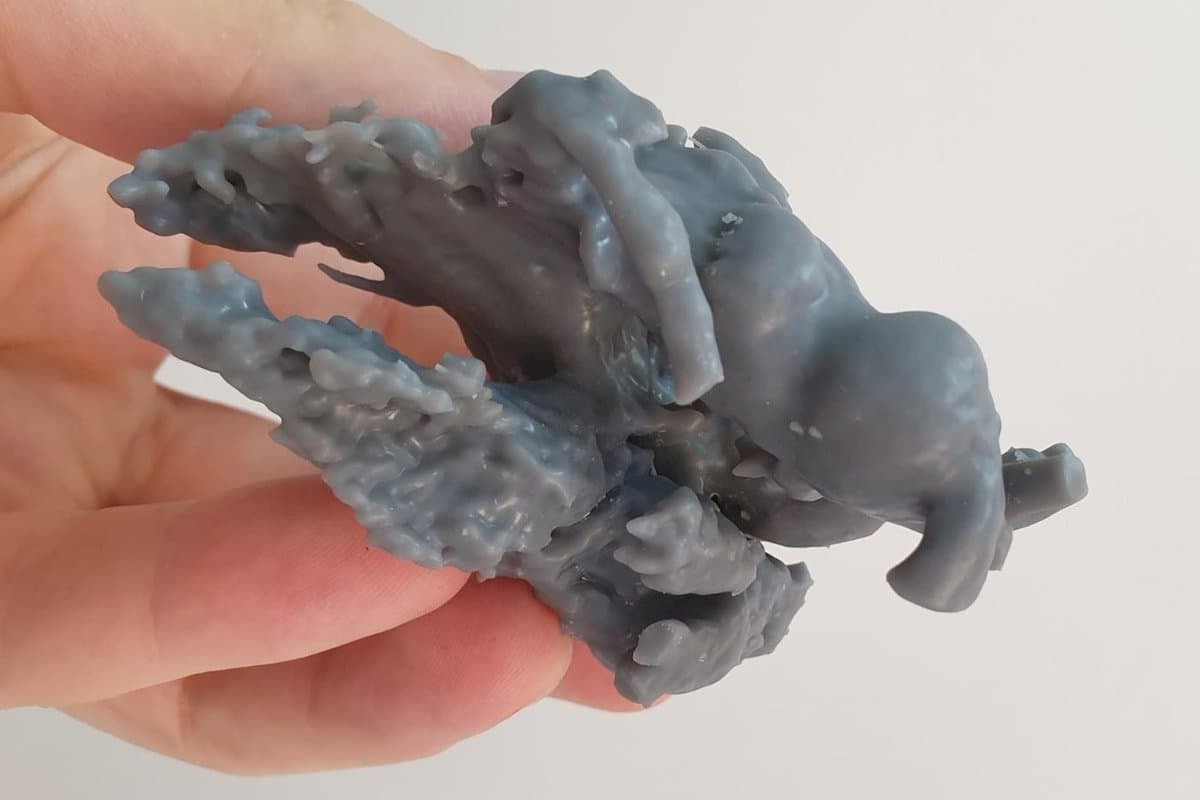
Traditional view of a CT scan (left) and a 3D printed model of the heart cavities for pediatric cardiology surgery planning (right).
Mr. De Rossi sees the wide range of materials one of the main benefits of SLA 3D printing.
“Once you know that you can achieve almost any shape, then what you need is different materials. Knowing that you have one machine that can use so many different materials is a big advantage. Especially when you don't know what’s going to come through the door the next morning. Maybe it's an artist who wants a castable part. Maybe it's an engineer who needs a tough, resistant shell. If you have a machine that can also use other materials, even ones you're not using at the moment, it's a big benefit for future-proofing the investment,” said Mr. De Rossi.
Knowing that you have one machine that can use so many different materials is a big advantage.
Marco De Rossi
Integrating Digital Manufacturing into the Curriculum
After finishing his PhD, Mr. De Rossi is hoping to become a professor at the university, start his own research group, and have new PhD students continue the work that he has been doing at the lab.
“You definitely need someone there who really wants to learn. I think that role is fundamental in a 3D printing lab. You constantly need to find someone who will get involved for a couple of years and then pass on the information to the next generation,” said Mr. De Rossi.
“I think that's one of the things I like about being at the university is that your purpose is to teach not so much to be the best in a very specific thing, but to be good enough at many things and have the flexibility to understand any project that comes to you. You have to give students enough tools to help them become the best in what they do,” said Mr. De Rossi.
“You have to have a systematic way of teaching the skills needed for digital manufacturing. Until now, some universities might have a 3D lab or they might have a course. But I think it's still not an integrated part [in the curriculum]. You need to have every aspect of a profession moving around digital manufacturing. That is the future. That is the present. If you're not teaching that, then you're already almost obsolete,” said Mr. De Rossi.