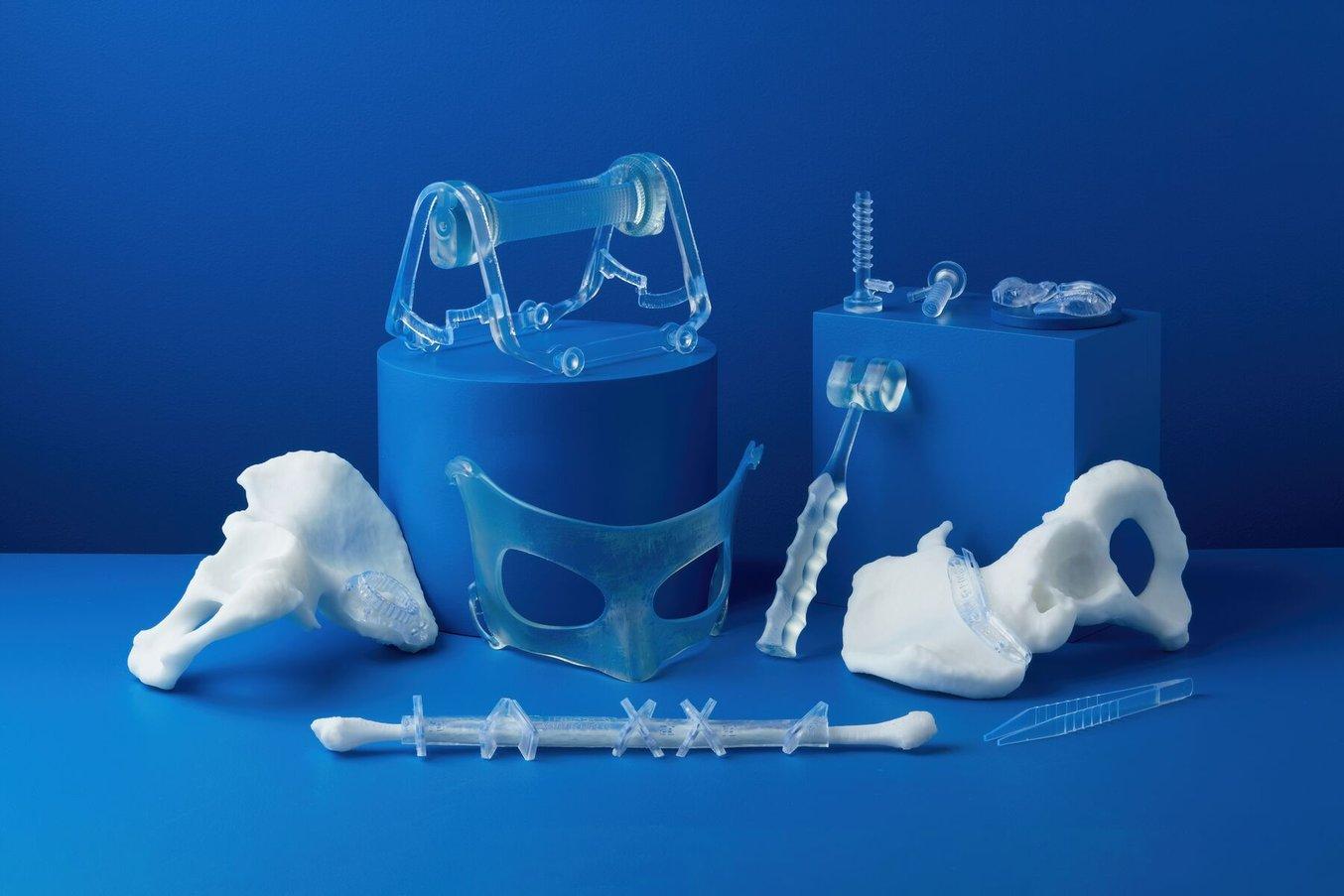
Formlabs is proud to introduce BioMed Durable Resin, a new formulation developed specifically to address the need for a biocompatible material that can withstand impact, rough handling, and pressure.
BioMed Durable Resin is ideal for patient-specific instruments (PSI) and customizable surgical instruments, as well as product development workflows that require biocompatibility through any stage, from design to low-volume production.
This USP Class VI material is made in an FDA-registered, ISO 13485 facility and can be used in applications for long-term skin and short-term tissue, bone, and dentin contact.
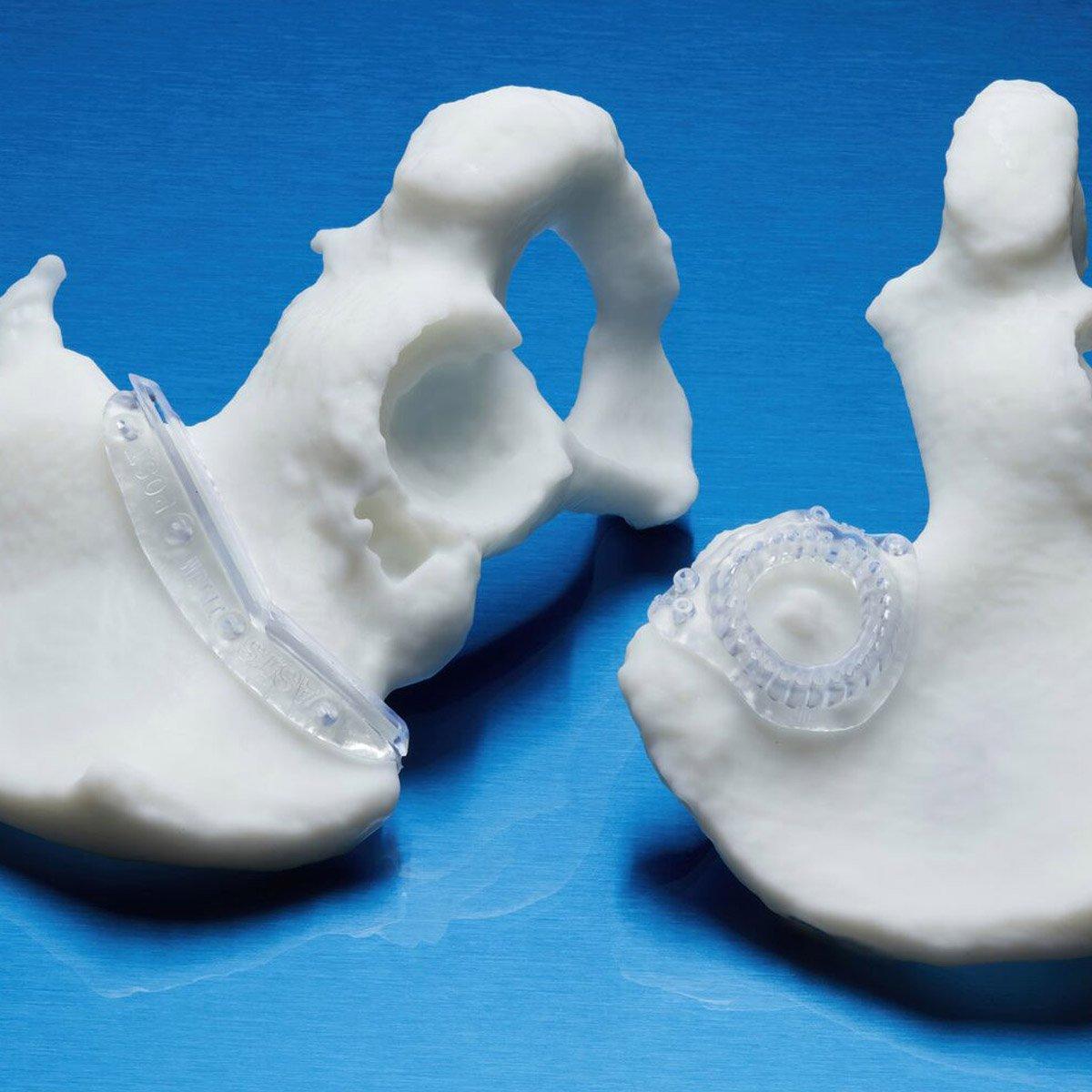
BioMed Durable Resin: Announcing Formlabs Most Impact-Resistant Material
Discover our new biocompatible material for medical devices that can withstand impact, rough handling, and pressure. During this webinar, our medical 3D printing experts will walk you through the key benefits and applications of BioMed Durable Resin.
Why Develop BioMed Durable Resin
Despite the mounting body of evidence pointing to the positive benefits of 3D printed models, devices, guides, and products in the healthcare industry, many providers are hesitant to make them an integral part of every physician’s workflow. This hesitancy is understandable — when responsible for a patient’s health, every precaution must be taken to ensure the materials and workflows are up to the task. In the past, many available 3D printing materials weren’t able to provide a complete solution that was certified, safe, and proven by research.
Each Formlabs biocompatible material seeks to provide the best performance for a specific application within healthcare. Though materials like BioMed Amber Resin and BioMed White Resin have proved enormously successful for use in surgical guide and patient-specific instruments, many hospitals and medical device manufacturers reported that physicians often ask for something more impact- and abrasion-resistant. For patient-specific devices and surgical instruments, physicians are wary of parts that are delicate or that may shatter under rigorous use. In a high-stakes environment like the operating room, every component needs to be reliable, durable, and consistent.
For medical device manufacturing companies, having access to an impact-resistant material for surgical single-use instruments that is both strong and biocompatible can help streamline the product development lifecycle.
The answer to all these needs is BioMed Durable Resin — with a USP Class VI rating, certified compatibility for a wide range of medical applications, and the strength of engineering-focused materials, this new material fills the gap in existing 3D printing healthcare materials.
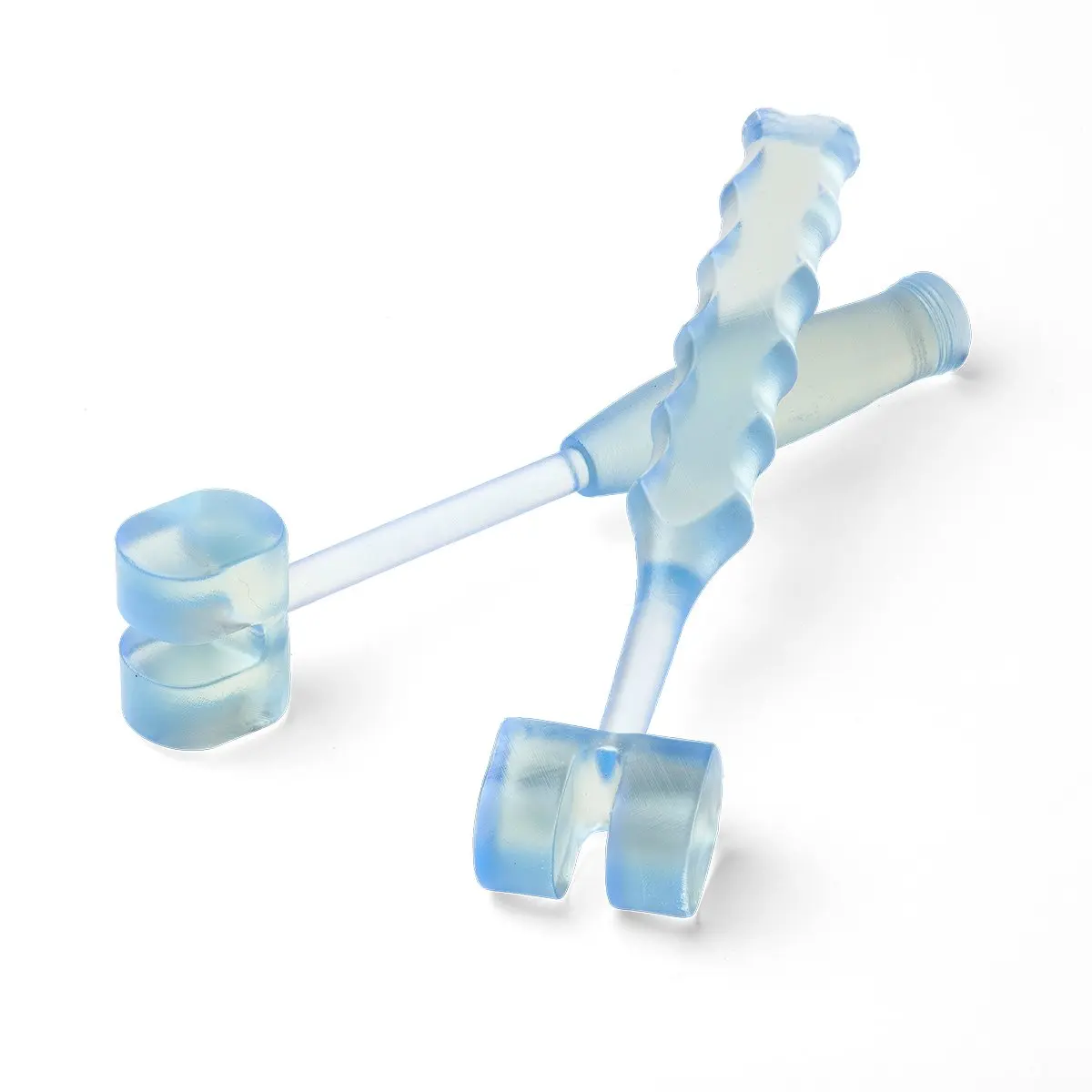
Request a Free Sample Part
See and feel Formlabs quality firsthand. We’ll ship a free sample part of BioMed Durable Resin to your office.
Key Benefits of BioMed Durable Resin
By working closely with Formlabs partners in hospitals, manufacturing centers, and research facilities across the world, we developed BioMed Durable Resin in adherence to rigorous standards for strength and biocompatibility. The superior surface finish and clarity of the resin also mean prototypes used in the final iterative stages have the look and feel of injection-molded parts.
The new material has an ultimate tensile strength of 29.1 MPa, comparable to that of Formlabs’ popular engineering material, Durable Resin, and the familiar industrial plastic, polypropylene. With a notched izod rating of 98 J/m, BioMed Durable Resin is nearly three times as tough as BioMed Clear Resin, while still maintaining the same biocompatible standards. These mechanical properties are indicative of the anti-shatter, impact-absorbent qualities of this new material. For instruments used in the operating room and products used in functional testing stages, BioMed Durable Resin can be relied upon to create rugged, abrasion-resistant components.
Ultimate Tensile Strength | Tensile Modulus | Elongation at Break | Notched Izod | |
---|---|---|---|---|
BioMed Durable Resin | 29.1 MPa | .99 GPa | 33% | 98 J/m |
BioMed Clear Resin | 52 MPa | 2.1 GPa | 12% | 35 J/m |
Durable Resin | 28 MPa | 1.0 GPa | 55% | 114 J/m |
To ensure that physicians and manufacturers can rely on this new material for use in contact with patients, Formlabs strictly adhered to USP Class VI procedures in order to gain the certification for use in applications with long-term skin (more than 30 days), and short-term tissue, bone, and dentin contact (less than 24h). The Formlabs resin manufacturing site is an ISO 13485 facility, and strict quality-control measures are rigorously observed.
Formlabs BioMed Resins Overview
Contact Type | Skin | Mucosal Membrane | Bone, Tissue, and Dentin | Pharmaceutical Containers, Drug Delivery & Medical Device Components | Mucosal Membrane | Breathing Gas Pathways |
---|---|---|---|---|---|---|
Contact Duration | > 30 days | <24 hours | <24 hours | - | >30 days | >30 days |
Applicable ISO Standard | EN ISO 10993-1 EN ISO 10993-3 EN ISO 10993-5 | EN ISO 10993-1 EN ISO 10993-3 EN ISO 10993-5 | USP <151> Pyrogen | USP <88> Class VI | EN ISO 10993-1 EN ISO 10993-3 EN ISO 10993-5 EN ISO 10993-10 EN ISO 10993-11 EN ISO 10993-23 | EN ISO 18562-1 EN ISO 18562-2 EN ISO 18562-3 EN ISO 18562-4 |
BioMed Clear Resin | ✅ | ✅ | ✅ | ✅ | ✅ | ✅ |
BioMed Durable Resin | ✅ | ✅ | ✅ | ✅ | Testing in progress | |
BioMed White Resin | ✅ | ✅ | ✅ | ✅ | ||
BioMed Amber Resin | ✅ | ✅ | ✅ | |||
BioMed Black Resin | ✅ | ✅ | ✅ |
Applications of BioMed Durable Resin
3D Printed Patient Specific Instruments
Patient-specific instruments (PSI) are guides tailored to fit a patient’s unique anatomy and pathology. Using PSIs has been shown to improve patient outcomes by 16%, reduce complications by almost 30%, and reduce operating time by 70 minutes on average. Surgeons can have the confidence that their tools will be perfectly matched to the job at hand, without worrying about using the one-size-fits-all instrumentation that requires small compromises to be made throughout the surgery. Decreased operating time is beneficial for the patient and for the hospital — hospitals can immediately see the positive ROI of 3D printed PSIs through their reduced OR time.
The Form 3B+ and BioMed Durable Resin provide a reliable, proven workflow with high accuracy and an accessible footprint for either manufacturers or in-house hospital labs. At TechFit, a PSI provider that works with physicians to design and 3D print surgical instrumentation, CEO and Co-Founder Mauricio Toro uses BioMed Durable Resin to produce patient-specific instrumentation that is impact, shatter, and abrasion resistant.
"We see Biomed Durable Resin as an ideal platform for the printing of single-use, patient-specific surgical instrumentation. The increased mechanical properties provide more design flexibility and increased indications while maintaining the biological properties required for reliably producing the best surgical results. "
Mauricio Toro, (CEO and Co-Founder), TechFit
Custom Surgical Guides at TrabTech
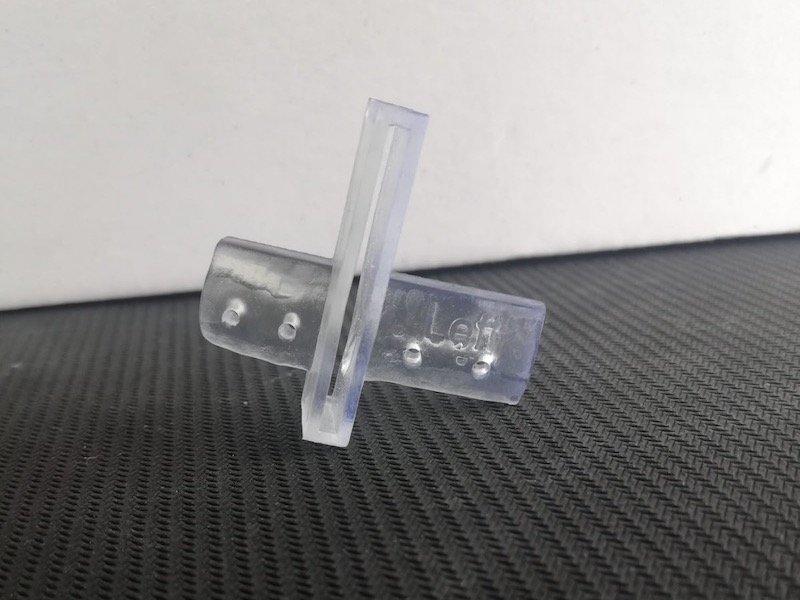
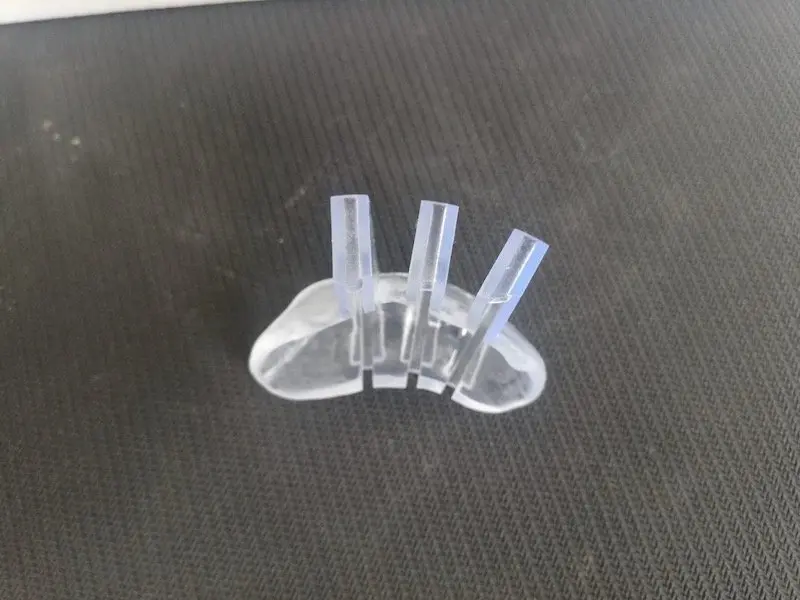
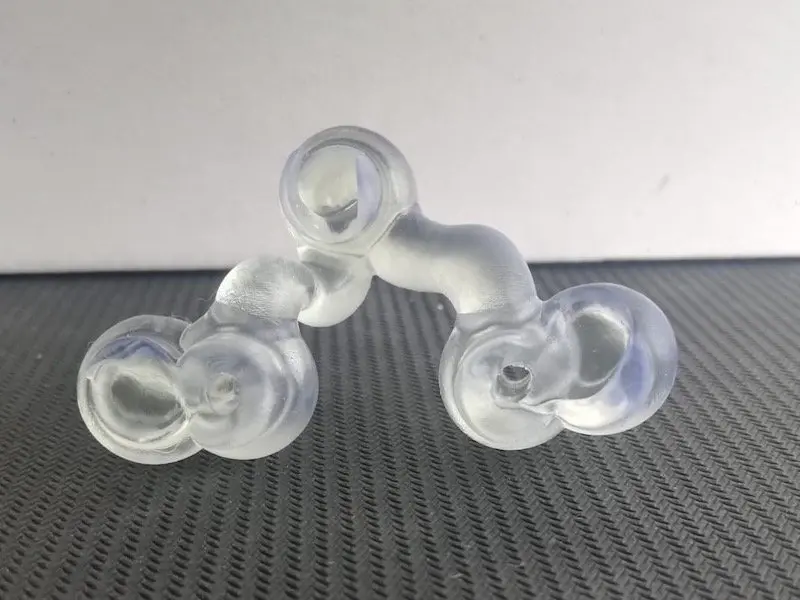
BioMed Durable Resin is ideal for patient-specific instruments like these surgical guides. Source: Trabtech
Trabtech, a medical technology development firm, specializes in designing and producing custom-made cutting and drilling guides using 3D printing, continually striving to enhance surgical procedures.
In 2022 they conducted a doctoral research project centered around the development of a vertebral anchor system, designed by Dr. Turan Najafov, one of the distinguished doctors in the Department of Orthopedics and Traumatology at Maltepe University. Their objective was to compare the pullout strength of Dr. Najafov’s newly designed system, referred to as the angled transpedicular screw anchor system (ATSAS), with the conventional 6.5 mm pedicle screws (PS) in a control group. The results of the study revealed that the pullout strength of the ATSAS was remarkably superior, boasting a 35% increase compared to the traditional PS.
Upon learning of the development of BioMed Durable Resin, Trabtech immediately saw the potential for a strong biocompatible version of the ATSAS. They requested a comparative evaluation of the pullout strength between the ATSAS designs fabricated from both the Tough 2000 Resin and Biomed Durable materials.
Diligently replicating the design and experiment, Trabtech found that the group utilizing the Biomed Durable Resin material showcased a pullout strength that surpassed the Tough 2000 Resin group by an impressive 20%.
“The introduction of Biomed Durable Resin represents a significant milestone in the evolution of surgical guides. Its exceptional mechanical properties, combined with the versatility of 3D printing, have empowered Trabtech to develop tools that enhance surgical precision and efficiency. As we continue to explore the potential of this remarkable material, we envision its applicability in diverse regions for cutting guides and surgical instruments that are currently undergoing trials. Our collaboration with Formlabs and the integration of this exceptional material into our designs have opened new possibilities in the field of medical technology.”
Dr. Turan Najafov, Department of Orthopedics and Traumatology at Maltepe University in partnership with Trabtech
Single-Use Surgical Instruments
restor3d, a provider of single-use surgical instruments, relies on a fleet of Formlabs SLA 3D printers to manufacture thousands of procedure-specific polymer instruments. Through the design freedom and lean manufacturing model of a 3D printing workflow, restor3d has disrupted the traditional model of surgical instruments.
Typical surgical instruments are machined from stainless steel, and a tray of generalized tools costs thousands of dollars — making it more likely that hospitals and surgeons will be hesitant to change their tools. Producing quick turnaround operation specific instruments increases the likelihood that surgeons are able to perform at their best and most comfortable, with the confidence that their tool has been specifically designed for the procedure at hand. Through an advanced 3D design and 3D printing workflow, restor3D closes the gap between surgeon feedback and product development.
restor3D’s Vice President of Product Development, Nathan Evans, spoke to us about the new BioMed Durable Resin, saying, “We’re constantly looking to find the best printing technologies, the best materials. This particular one, I could see a lot of different applications from cutting guides and drill guides, particularly where the ability to see through it would be very, very helpful. So you can see exactly where your K-wire or your drill bit is relative to the anatomy.”
Besides visual clarity, which makes in-use monitoring easier and gives the surgeon more confidence, the shatter resistance of the new material is a highly prized feature. restor3D needs to make sure their parts are durable enough to withstand rough handling and cross-country shipping.
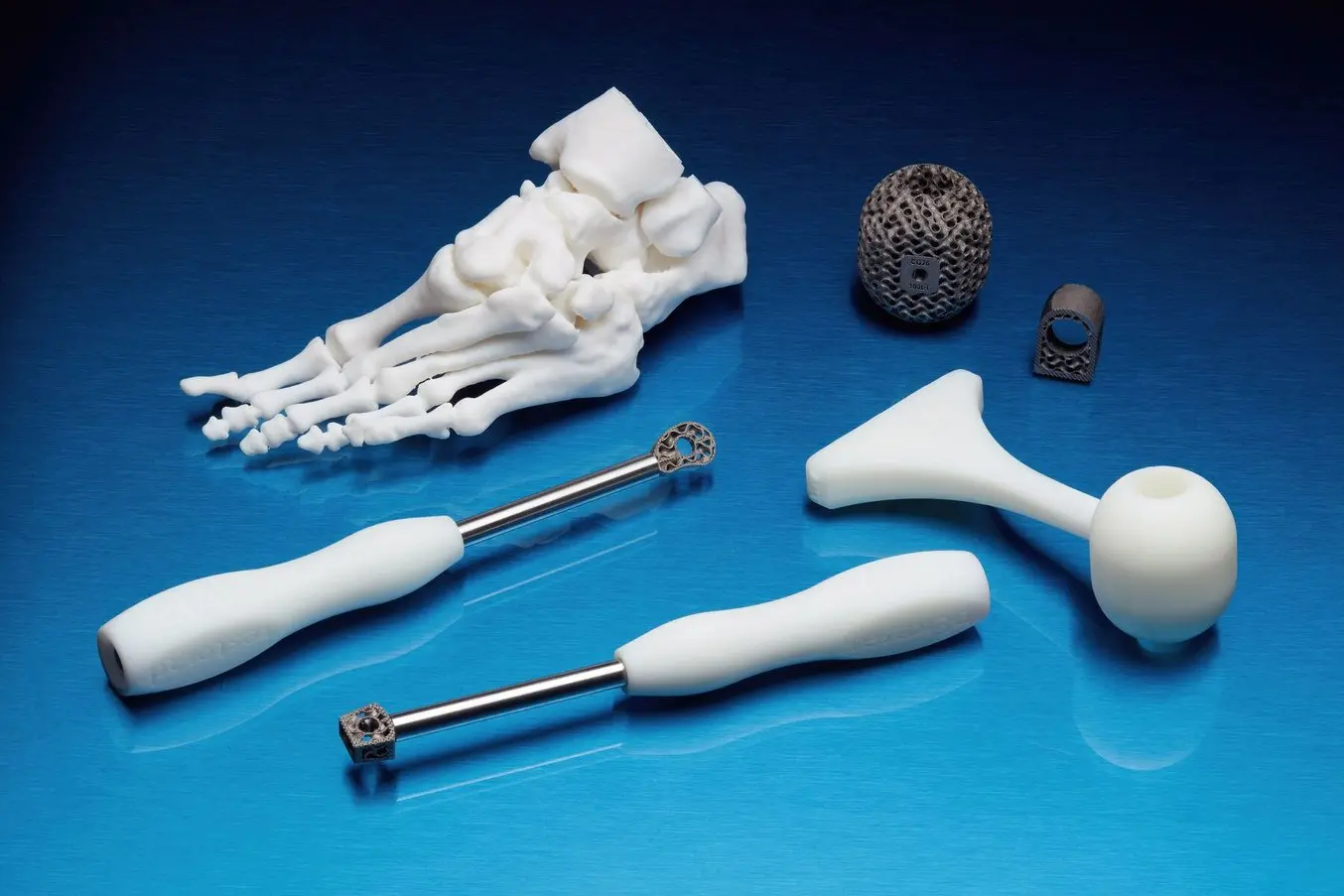
Producing quick turnaround operation specific instruments, like these developed by restor3d, increases the likelihood that surgeons are able to perform at their best and most comfortable, with the confidence that their tool has been specifically designed for the procedure at hand.
"It’s also important for us to have great mechanical properties. I actually took this in a lab and was just going to town on it with a hammer. You can’t even tell. I can’t even see which side I hit it because it just holds up really, really well to impact. And so it meets a lot of the needs that we’re looking for in a medical device, in an in-use device.”
Nathan Evans, VP of Product Development, restor3D
Getting Started With BioMed Durable Resin
BioMed Durable Resin is part of a streamlined and easy-to-use workflow on Formlabs’ Form 3B+ and Form 3BL printers. From surgical planning companies to hospitals with in-house 3D printing labs, the new material gives providers and physicians confidence that the entire process will be biocompatible from start to finish, and that the parts are sturdy enough to hold up to the challenges of transport and rough handling.
Formlabs’ software PreForm accepts all .stl, .obj, and 3MF file types and is design software agnostic — any medical segmentation or engineering design software, from Materialise to Solidworks, is easy to integrate with your 3D printing set-up.
To buy now and get started with rugged, biocompatible 3D printed parts, visit our store. To test out the strength and flexibility of this new material, request a sample.
To speak to our medical team about your unique workflow and find out if BioMed Durable Resin is a good fit for you, follow the link below.