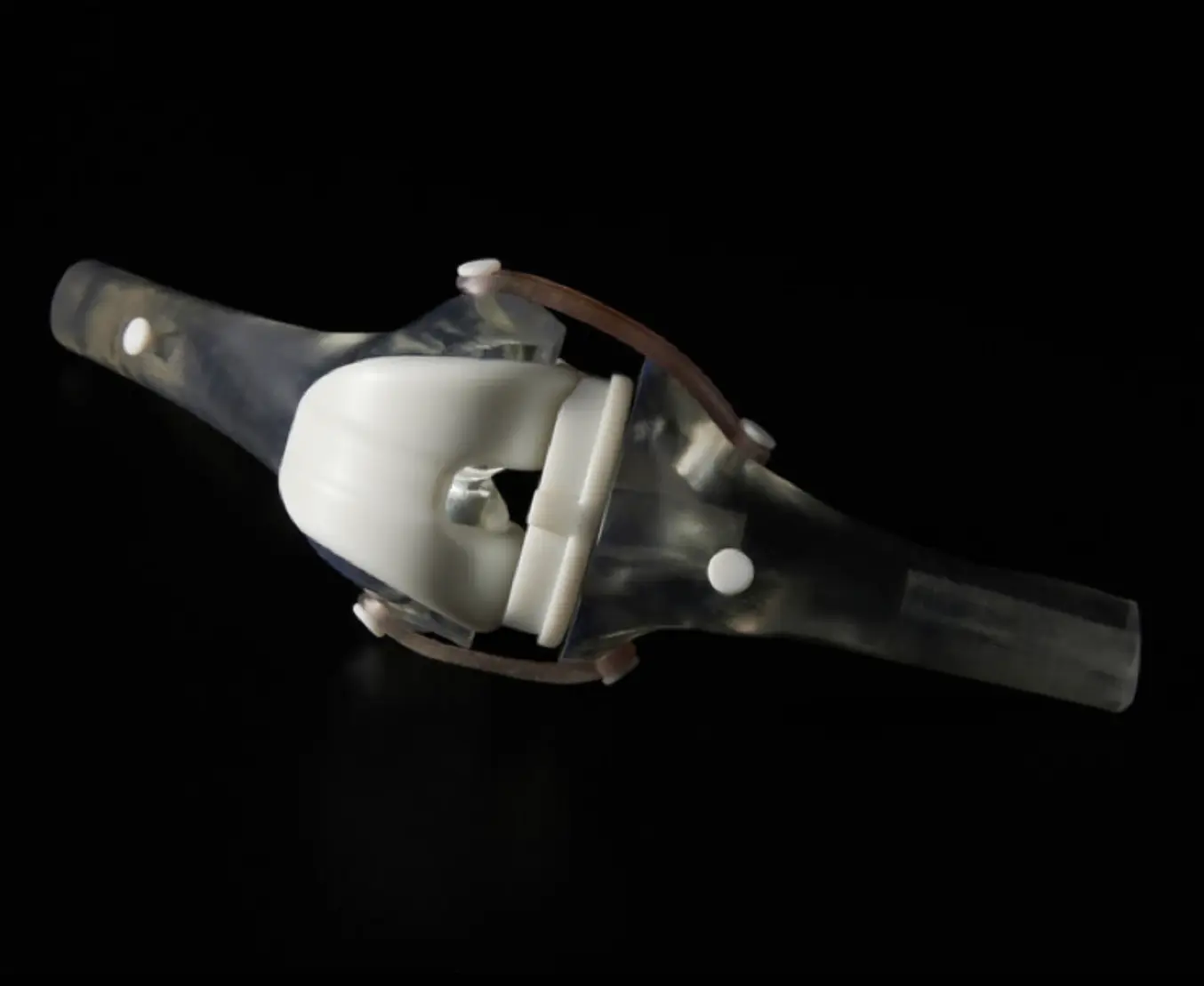
3D printed bone-simulation models are revolutionizing medical training, surgical planning, research, and medical device development by putting realistic, patient-specific replicas of skeletal structures in the hands of healthcare professionals, researchers, and engineers.
The in-house production of bone-simulation models offers a number of advantages over traditional methods that use cadaver bones or generic outsourced models: decreased costs, shortened wait times, and the opportunity to create custom or patient-specific geometries.
To determine the most bone-like materials from our extensive material offerings, we collected detailed feedback from eight clinical collaborators, and some of their colleagues, with extensive bone-cutting/drilling experience.
- Each collaborator was provided with a series of bone models that were based on their own patients’ scans and printed in a series of different materials.
- The collaborators performed standard procedures on these models including cutting and drilling with bone drills, saws, and reamers.
- Qualitative feedback was collected via video call, and quantitative feedback was collected via a scoring matrix that encompassed a series of bone-like qualities.
- Recommended materials were determined based on overall performance score and these results were supported by qualitative feedback.
Two materials, BioMed Durable Resin and Rigid 4000 Resin, are currently recommended for bone-simulation models. Download the entire guide on using stereolithography (SLA) 3D printing for in-house manufacturing for bone-like anatomical models intended for cutting and drilling for a complete step-by-step process.
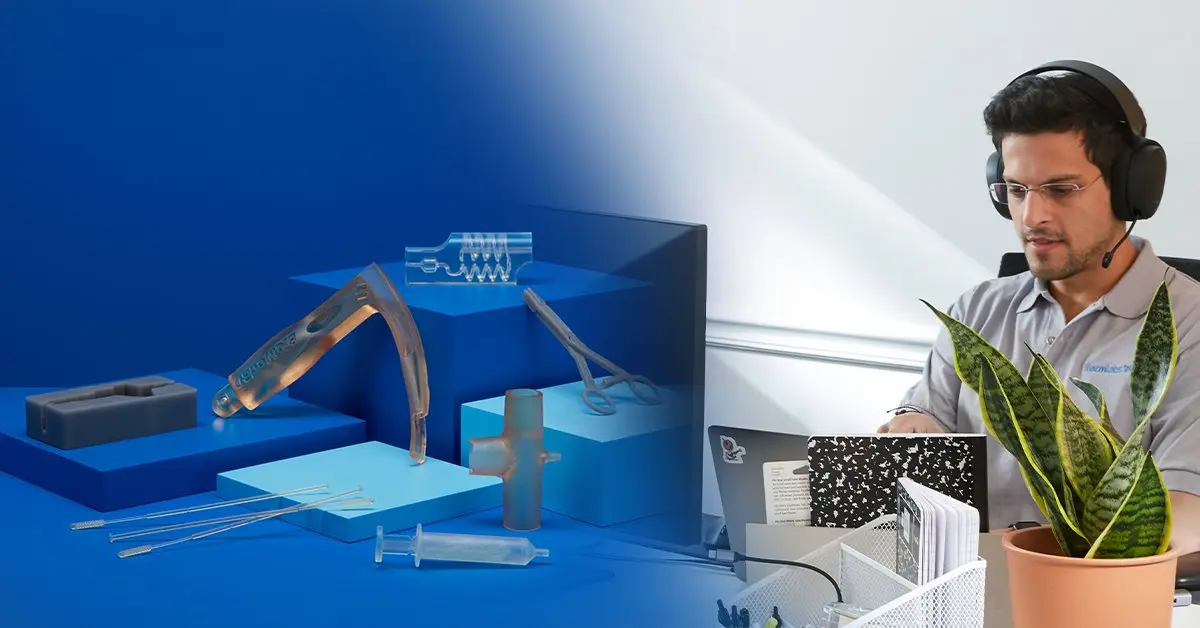
Talk to Our Medical Sales Team
Whether you need to make patient-matched surgical tools or are prototyping for a cardiac medical device, we’re here to help. Formlabs Medical team are dedicated specialists who know exactly how to support you and your company's needs.
What Is a Bone-Simulation Model?
Bone-simulation models are functional anatomical models that exhibit mechanical properties similar to real bone when cut or drilled. These models are often used in medical education settings for surgical practice and training. Sometimes, these models are created based on patient scans to model the anatomy associated with a specific surgical case. In these cases, the models are used by clinicians to practice a particular approach prior to the real operation, and may even be sterilized to go into the operating room (OR) with the surgeon. In other cases, bone-simulation models may be used by medical device developers to test the fit and function of bone-interfacing tools, such as cutting guides and templates.
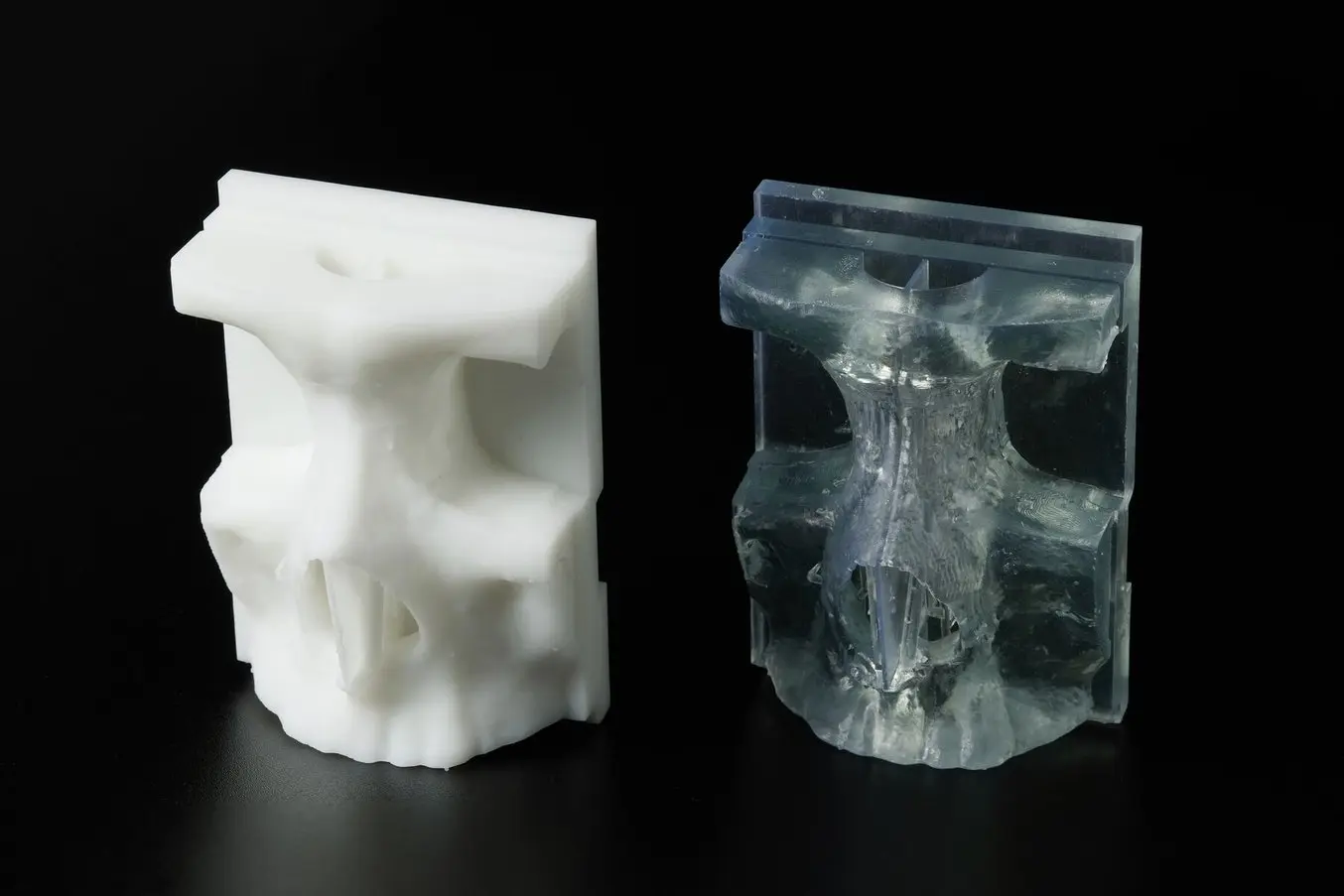
Models for practicing nasal osteotomies, printed in Rigid 4000 Resin and cured without heat (left) and BioMed Durable Resin (right), courtesy of Dr. Lauren Schlegel at Beth Israel Deaconess Medical Center.

Spine model printed in Rigid 4000 Resin and cured without heat.
Choosing the Right Material for 3D Printing Bone-Simulation Models
Our primary material recommendation for 3D printing bone-simulation models is BioMed Durable Resin. BioMed Durable Resin is a clear material developed for biocompatible applications requiring impact, shatter, and abrasion resistance. Despite being transparent, BioMed Durable Resin ranked the highest in mechanical performance similar to bone. Some testers even said that they preferred the material’s transparency over standard opaque bone models because it enabled better visualization of the procedure being practiced. The radiopacity of BioMed Durable Resin is approximately 84 HU, which is lower than most types of bone but still visible by CT. Parts printed with BioMed Durable Resin can be sterilized, and are therefore suitable for use in the OR for surgical planning purposes.
“Biomed Durable strikes the perfect match between the little flexibility that thinner bones provide with realistic fractures under pressure. Combined with the ease of printability, this material is a great fit for medical simulation.”
Dr. Lauren Schlegel, MD, Beth Israel Deaconess Medical Center
Our secondary recommendation for bone-simulation models is Rigid 4000 Resin cured without heat (CWH). Rigid 4000 Resin did not score quite as high as BioMed Durable Resin on mechanical likeness to bone, but was still a frontrunner. This material was particularly appealing to testers who wanted models to be opaque. Curing without heat allows the user to differentiate the mechanical properties on the outside of the model from the inside of the model, in an attempt to better simulate the mechanical differences between spongy bone and compact bone. The radiopacity of Rigid 4000 Resin is 341 HU, loosely within the range for cancellous bone.
More information on the procedure used to determine these radiopacity values can be found here.
BioMed Durable Resin | Rigid 4000 Resin* | |
---|---|---|
Mechanical Performance | ★★★★★ | ★★★☆☆ |
Visual Likeness to Bone | ☆☆☆☆☆ | ★★★★☆ |
Radiopacity Likeness to Bone | ★★☆☆☆ | ★★★★☆ |
Biocompatible | ✔ | ✘ |
Sterilizable | ✔ | ✘ |
*When producing these models, Rigid 400 Resin is cured without heat. For complete post-curing instructions, download the guide.
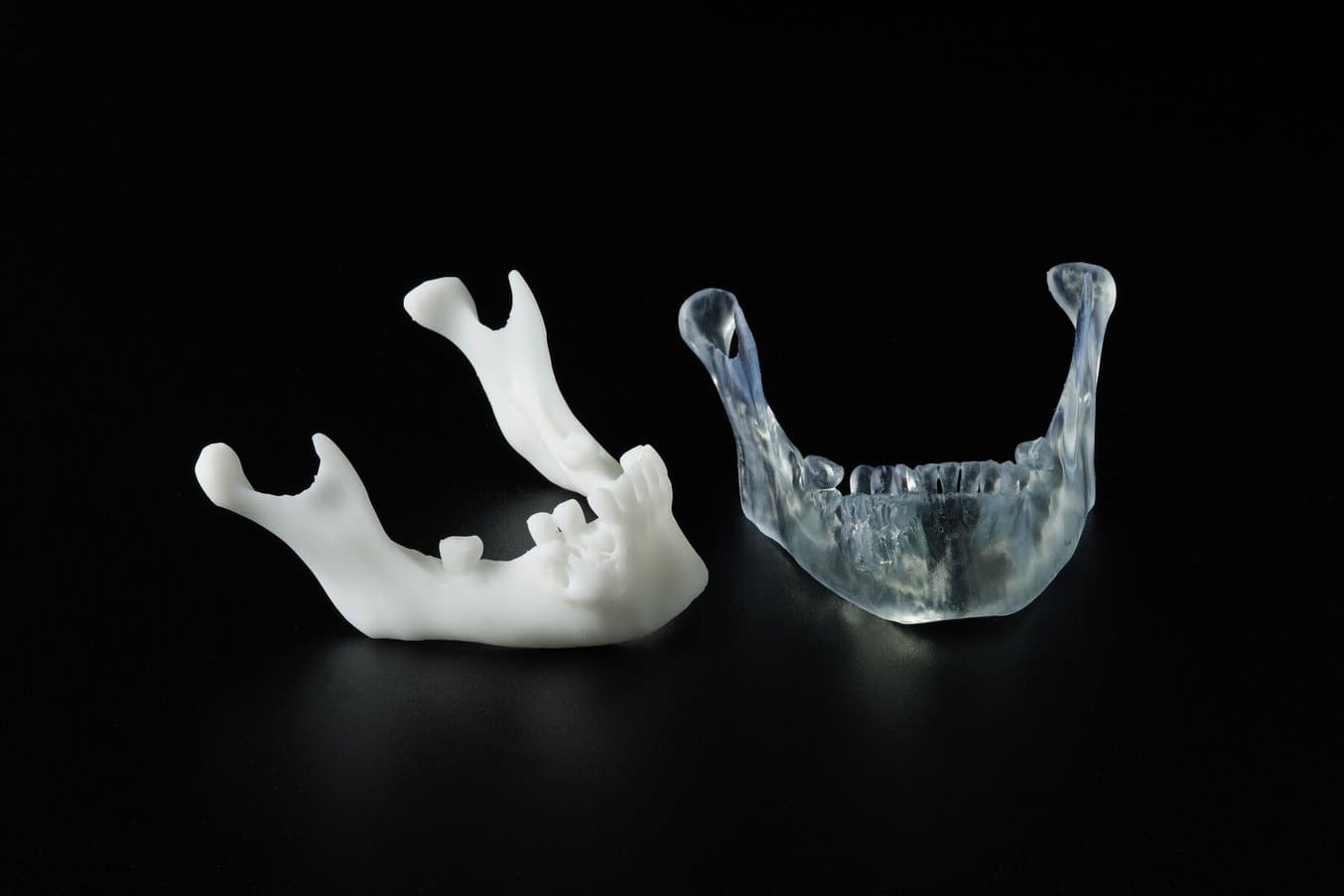
Bone-simulation anatomical models printed in Rigid 4000 Resin cured without heat (left) and BioMed Durable Resin (right).
"Formlabs Biomed Durable is my preferred resin for creating bone-like models. The clear nature of this material is what I find most useful in clinical cases, allowing all vital anatomic landmarks to be easily identified in preparation for surgery. In my practice, Biomed Durable is also used for teaching/training, giving novices full visibility of important structures to be encountered during procedures."
Desmond Tan BVSc (Hons), DACVS-SA, Alfred Veterinary Orthopedics
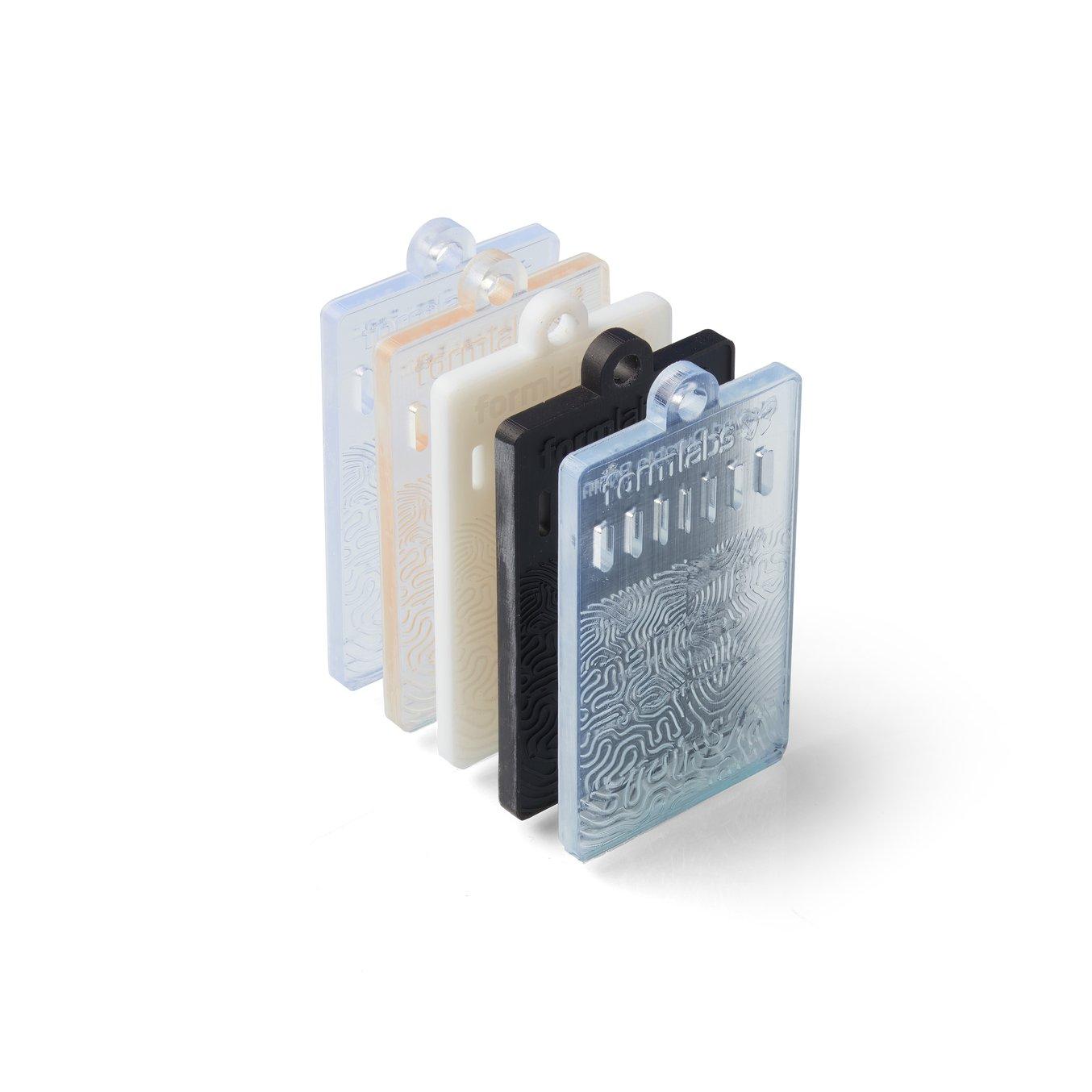
BioMed Resin Swatches
Each BioMed Resin swatch features embossed and debossed designs, 0.5-2.0 mm cutout thicknesses, as well as regulatory information unique to that resin.
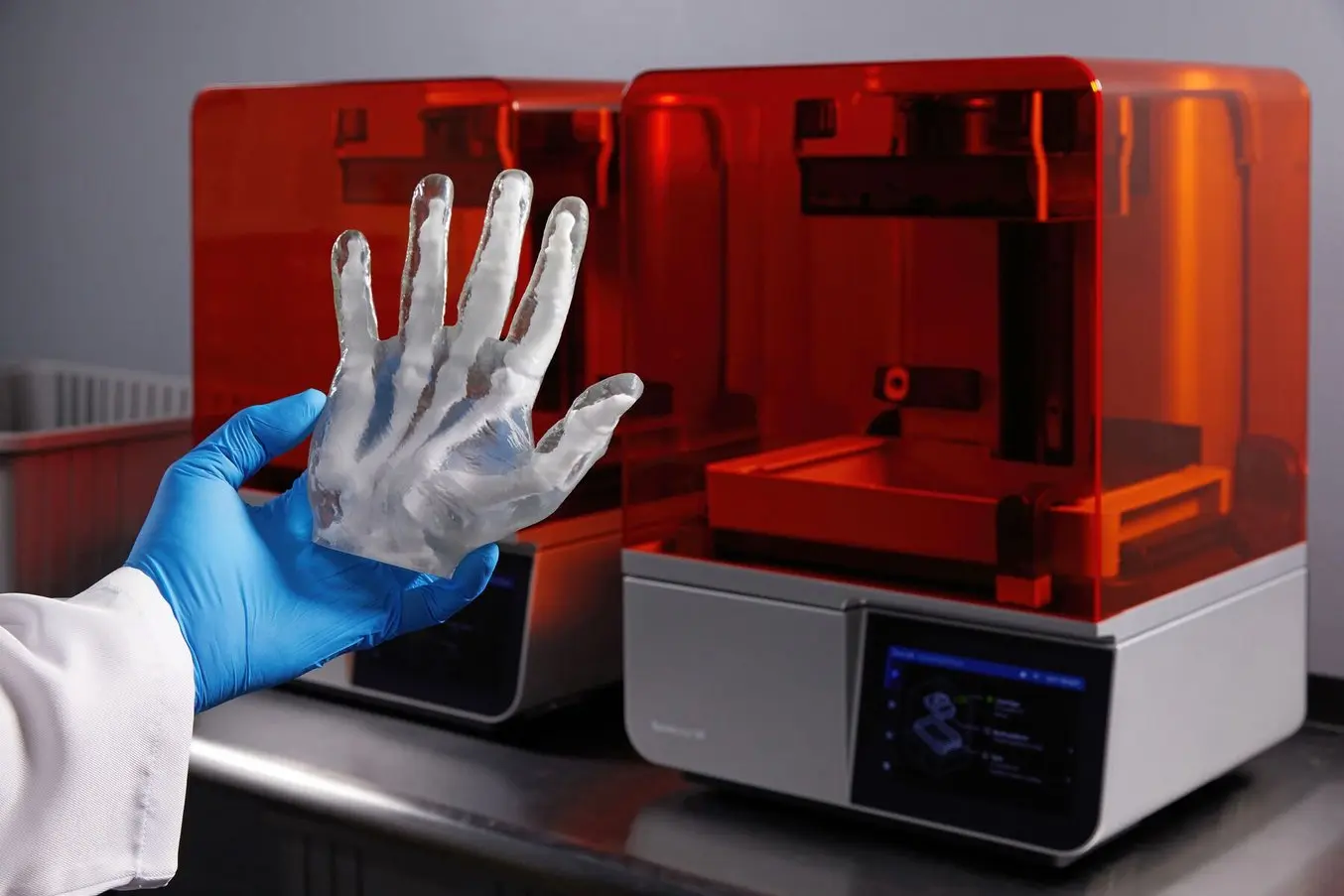
Formlabs Biocompatible Resins: A Comprehensive Guide To Choosing the Right Material
This paper aims to help users compare and contrast our biocompatible offerings, and determine the best fit for their medical applications.
Designing and Printing Bone-Simulation Models Step-by-Step
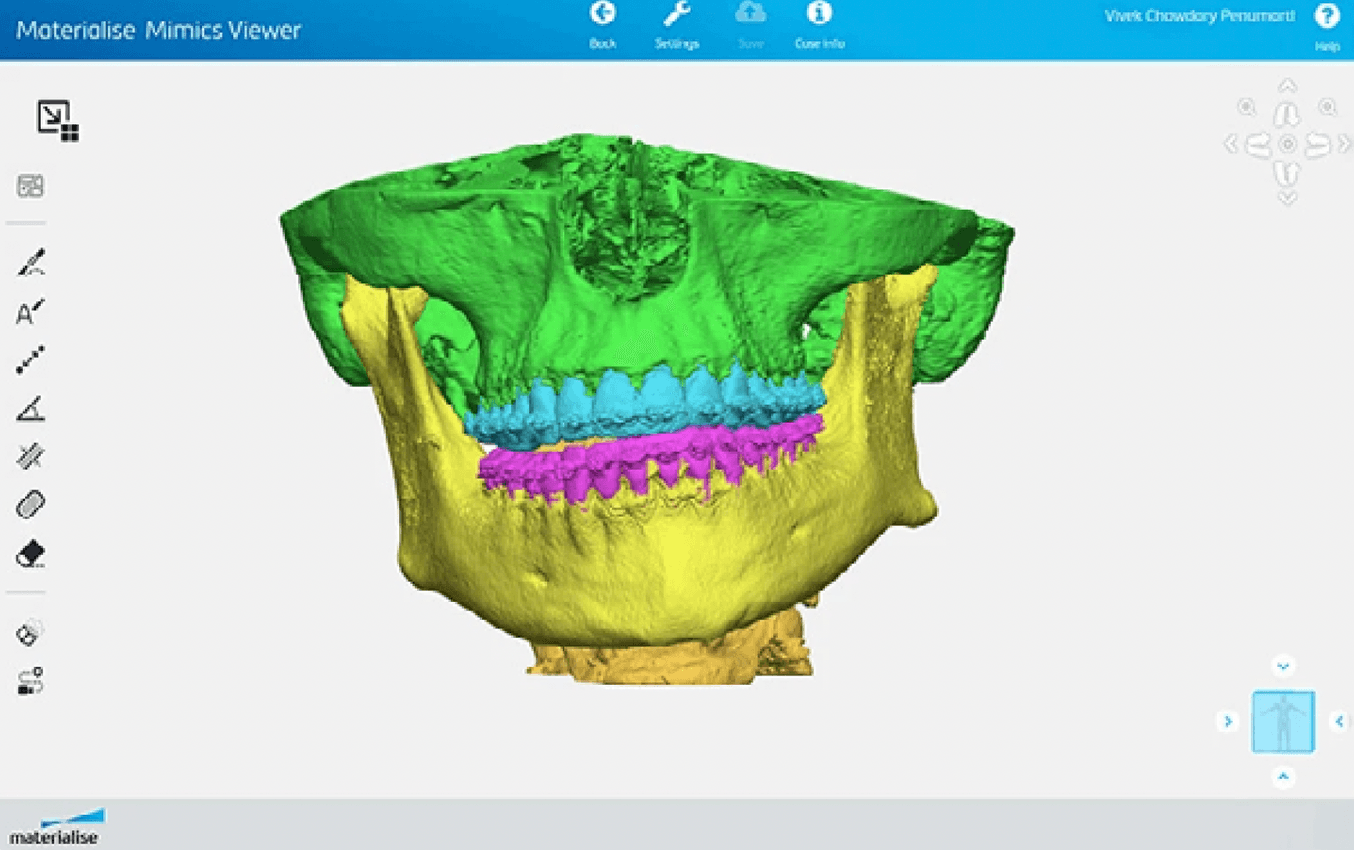
Segmentation of bony anatomy based on a patient scan using the Materialise Mimics Innovation Suite.
Design
Start with a CT, MRI, or 3D ultrasound image of the bony anatomy of interest and segment using your preferred segmentation software. Some bone models may require additional modification in order to print successfully. In some cases, you may need to add holes for drainage, or thicken weaker areas. Make sure that the finished model adheres to Formlabs’ design guidelines for Form 4 Series printers, Form 3/3B, or Form 3L/3BL.
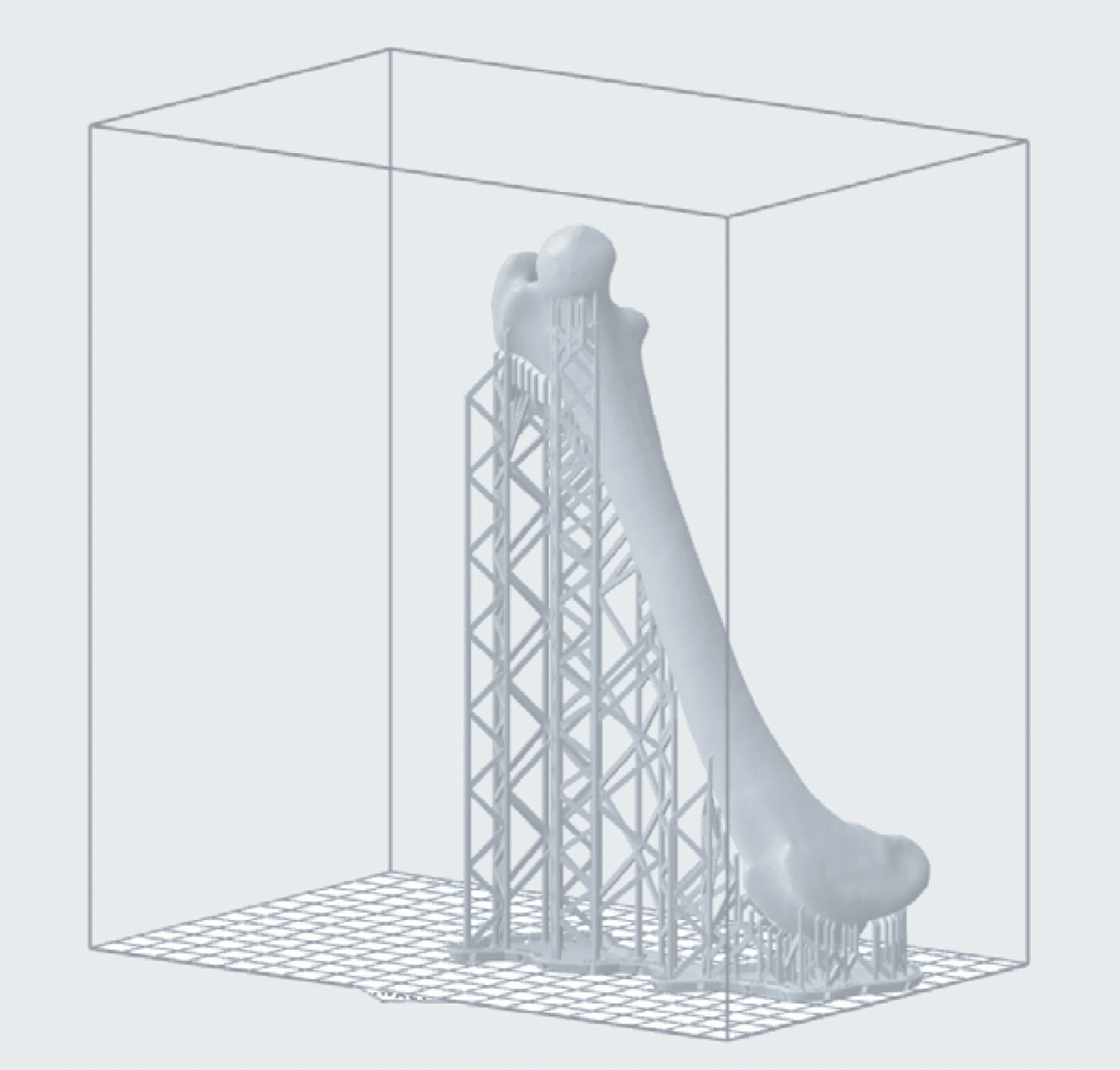
Example of a preferable orientation for a long part. The steep angle of the print allows for it to be largely self-supporting, resulting in a decreased support density and the ability to fit more parts on the build platform. Model is courtesy of Dr. Desmond Tan with Alfred Veterinary Orthopedics via Alogus Innovation.
Import your file into PreForm. Set up the print by orientating it, adding supports, and setting the parts location on the build platform. If needed, patient identifiers can be added to the raft or part before sending the print to the printer.
Warning: For full compliance and biocompatibility, BioMed Durable Resin requires a dedicated resin tank and build platform. Full compliance and biocompatibility may not be necessary for all bone-simulation applications.
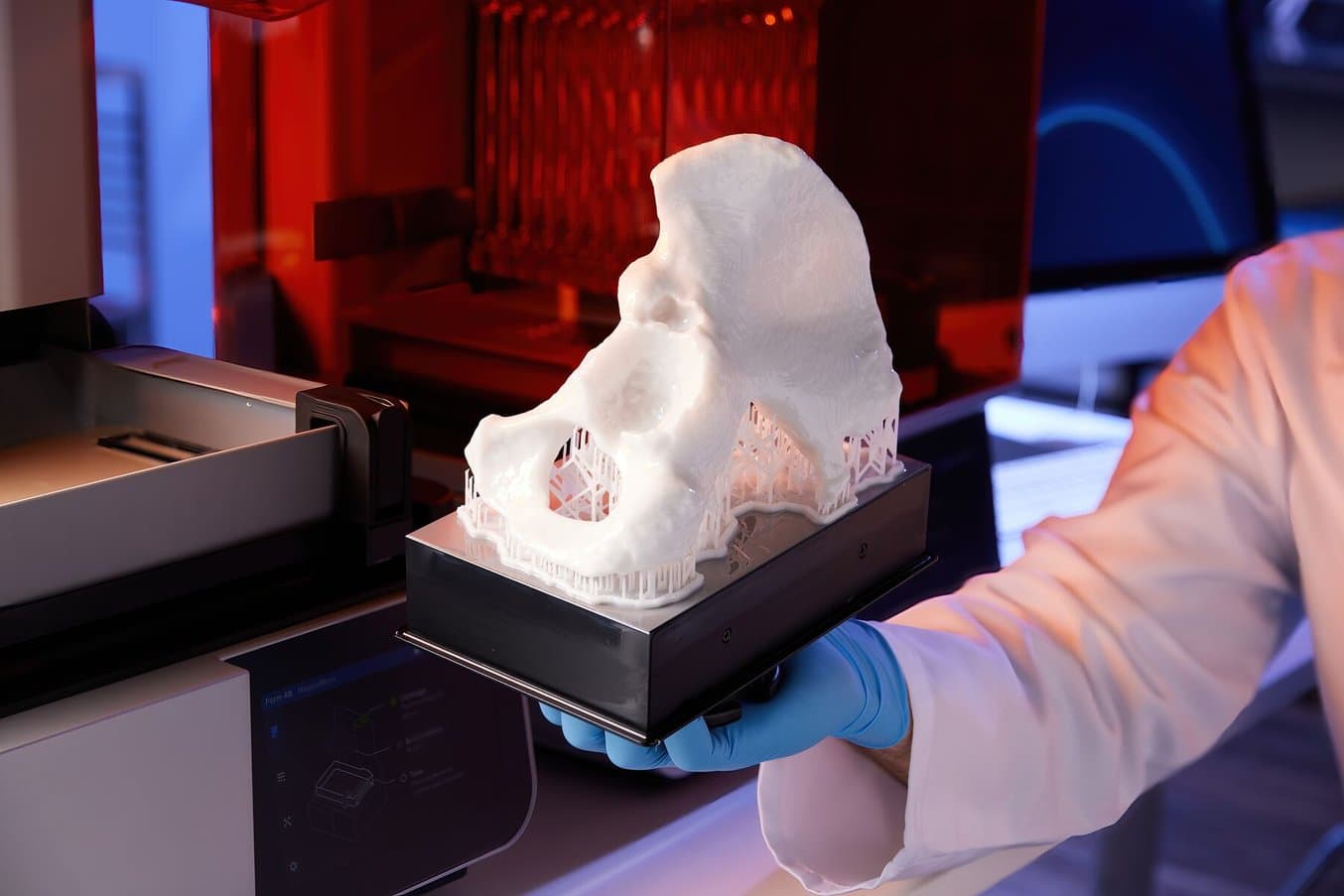
Ilium model printed in Rigid 4000 Resin straight out of Form 4B.
Post-Process
After printing, remove the part from the build platform and wash it in Form Wash or Form Wash L. Remove supports, wash again, and allow parts to dry before following cure directions. See the white paper for post-curing timing to achieve a more bone-like mechanical performance.
Warning: For full compliance and biocompatibility, BioMed Durable Resin requires a dedicated Form Wash or Form Wash L. Only use this Form Wash or Form Wash L with other Formlabs biocompatible resins.
Biocompatibility and Sterilization
BioMed Durable Resin is an ISO 10993 and USP Class VI certified material. It is made in an FDA-registered, ISO 13485 facility and can be used in applications for long-term skin and mucosal membrane contact (>30 days), and for externally communicating devices in short-term contact with tissue/bone/dentin (≤24 hours). BioMed Durable Resin can be sterilized by steam, gamma radiation, ethylene oxide, and E-Beam sterilization methods. Sterilization guidelines and results for BioMed Durable Resin are available upon request
Rigid 4000 Resin is a standard engineering material and was not developed with medical applications specifically in mind. For this reason, Rigid 4000 Resin has not been tested for biocompatibility and does not currently have sterilization/disinfection guidelines.
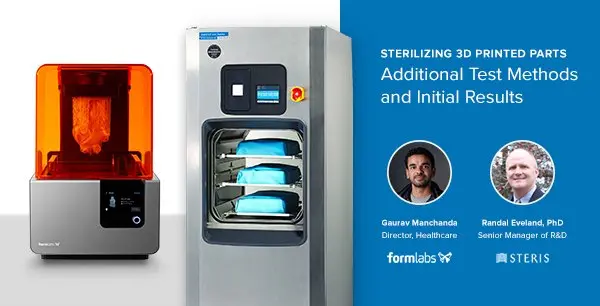
Sterilizing 3D Printed Models with STERIS and Formlabs
While sterilizing 3D printed parts is an important step to consider, relevant information can be difficult to source. Learn how 3D printed parts are used with STERIS, a leading provider of infection prevention and other procedural products.
Start 3D Printing In-House
Bone-simulation models offer benefits for medical training and education, surgical planning, research, and medical device development. 3D printing bone-simulation models in-house is less costly, faster, and more customizable than using cadaver bones or generic outsourced models. With an option for sterilizable models, bone-simulation models can even be brought into ORs for reference during surgery.
Download the complete application guide to learn more or explore Form 4B to start printing. Talk to a 3D printing expert to learn how 3D printing can help you reach your goals.