As more businesses turn to 3D printing for production as well as rapid iteration, 3D printing speed and throughput have become a greater consideration when choosing a technology. By reducing cost, manufacturing time, design cycle length, and process complexity, high-speed 3D printing is especially well-equipped to increase productivity and help companies get products to market faster. Speed is an important factor for professionals in industries as wide-ranging as manufacturing, engineering and product design, automotive, dental, medical, and education.
Fused deposition modeling (FDM), stereolithography (SLA), and selective laser sintering (SLS) are the three most popular types of 3D printers on the market. Each process has different strengths and weaknesses when comparing speed, the time it takes to print one part, and throughput, the total production capability of a given 3D printer in a given time period.
The fastest 3D printers today are masked stereolithography (MSLA) resin 3D printers. In almost all cases, they offer the shortest time to part, while their throughput can be comparable to SLS 3D printers. As a rule of thumb, FDM 3D printers are relatively fast for smaller parts and simple shapes that don’t require much post-processing, but their throughput is substantially lower than SLA and SLS. SLS 3D printer builds take longer, resulting in a longer time to part, but they can pack parts efficiently to achieve the highest throughput.
This 3D printer speed comparison will discuss the advantages and limitations of each of the most common 3D printing technologies in the specific context of 3D printing speed. Then we will walk through how these technologies can enable faster 3D printing based on various factors like material or design considerations.
While speed and throughput are important buying considerations, they’re not always the most important ones. Read our FDM vs. SLA vs. SLS: 3D Printing Technology Comparison for a comprehensive buyer's guide and learn how they compare in terms of print quality, materials, applications, workflow, speed, costs, and more, to help you decide which technique is ideal for your business.

How to Choose a 3D Printing Technology
Having trouble finding the best 3D printing technology for your needs? In this video guide, we compare FDM, SLA, and SLS technologies across popular buying considerations.
Fastest 3D Printer Comparison Table
Fused Deposition Modeling (FDM) | Stereolithography (SLA) | Selective Laser Sintering (SLS) | |
---|---|---|---|
Speed (Time to Part) | ★★★★☆ | ★★★★★ | ★★★☆☆ |
Throughput | ★★★☆☆ | ★★★★☆ | ★★★★★ |
Resolution | ★★☆☆☆ | ★★★★★ | ★★★★☆ |
Accuracy | ★★★★☆ | ★★★★★ | ★★★★★ |
Surface Finish | ★★☆☆☆ | ★★★★★ | ★★★★☆ |
Complex Designs | ★★★☆☆ | ★★★★☆ | ★★★★★ |
Ease of Use | ★★★★★ | ★★★★★ | ★★★★☆ |
Pros | Low-cost consumer machines and materials Fast and easy for simple, small parts | Great value High accuracy Smooth surface finish Fast printing speeds Range of functional applications | Strong functional parts Design freedom No need for support structures |
Cons | Low accuracy Low details Limited design freedom | Some materials are sensitive to long exposure to UV light | Slightly rough surface finish Limited material options |
Applications | Concept modeling Rapid prototyping Functional prototyping Manufacturing aids | Concept modeling Rapid prototyping Functional prototyping Rapid tooling Manufacturing aids Low volume, bridge, or custom manufacturing Dental models and appliances Medical models and medical devices Jewelry prototyping and casting Models and props | Rapid prototyping Functional prototyping Low volume, bridge, or custom manufacturing Long-lasting, durable manufacturing aids Medical devices, prosthetics, and orthotics |
Print Volume | Up to 300 x 300 x 600 mm (desktop and benchtop 3D printers) | Up to 353 x 196 x 350 mm (desktop and benchtop 3D printers) | Up to 165 x 165 x 300 mm (benchtop industrial 3D printers) |
Materials | Standard thermoplastics, such as ABS, PLA, and their various blends. | Varieties of resin (thermosetting plastics). Standard, engineering (ABS-like, PP-like, flexible, heat-resistant, rigid glass-filled), castable, and dental and medical (biocompatible). Pure silicone and ceramic. | Engineering thermoplastics. Nylon 12, nylon 11, glass or carbon-filled nylon composites, polypropylene, TPU (elastomer). |
Training | Minor training on build setup, machine operation, and finishing; moderate training on maintenance. | Plug and play. Minor training on build setup, maintenance, machine operation, and finishing. | Moderate training on build setup, maintenance, machine operation, and finishing. |
Facility Requirements | Air-conditioned environment or preferably custom ventilation for desktop machines. | Desktop and benchtop machines are suitable for an office environment. | Workshop environment with moderate space requirements for benchtop systems. |
Ancillary Equipment | Support removal system for machines with soluble supports (optionally automated), finishing tools. | Washing station and post-curing station (both can be automated), finishing tools. | Post-processing stations for powder management and part cleaning. |
Equipment Costs | Budget FDM printers and 3D printer kits start at around $200. Professional desktop FDM printers range from $2,000 to $8,000, and industrial systems are available from $15,000. | Low-cost resin 3D printers are available for $200 to $1000, professional SLA 3D printers are in the $2,500 to $10,000 range, and large-format resin 3D printers are in the $5,000 to $25,000 range. | Benchtop industrial SLS 3D printers start just under $30,000 for the printer and $60,000 for the entire ecosystem, including powder management and cleaning stations. Traditional industrial SLS printers start at around $200,000. |
Material Costs | $50-$150/kg for most standard filaments, and $100-$200/kg for support materials or engineering filaments. | $100-$200/L for most standard and engineering resins, $200-$500/L for biocompatible materials. | $100/kg for nylon. SLS requires no support structures, and unfused powder can be reused, which lowers material costs. |
Labor Needs | Manual support removal (can be mostly automated for industrial systems with soluble supports). Lengthy post-processing is required for a high-quality finish. | Washing and post-curing (both can be mostly automated). Simple post-processing to remove support marks. | Simple and semi-automated workflow for cleaning parts and recovering powder. |
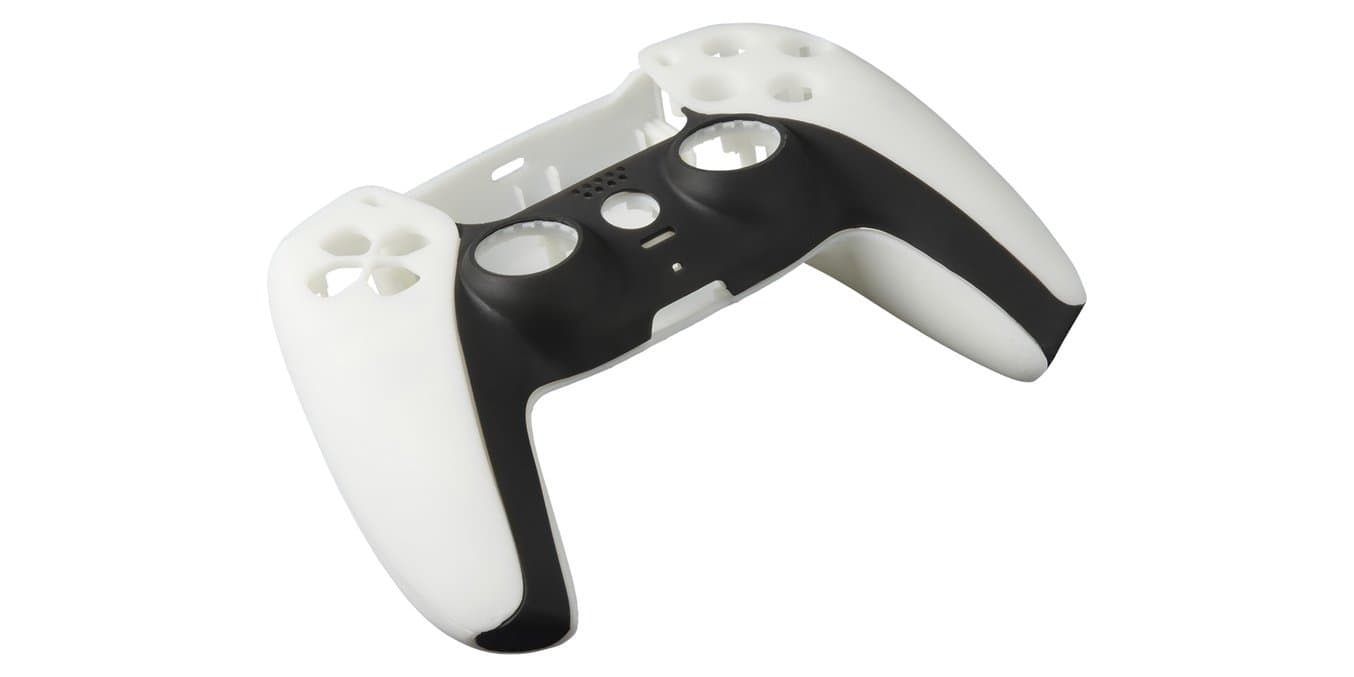
Print Speed Comparison: Gaming Controller
FDM 3D Printing | SLA 3D Printing | SLS 3D Printing | |
---|---|---|---|
1 assembly (3 parts) | 10 h 32 min | 2 h 36 m | 3 h 52 min printing (6 h 52 min cooling) |
5 assemblies (15 parts) | 52 h 40 min | 13 h | 9 h 38 min printing (13 h 47 min cooling) |
Compared printers and printing parameters:
- FDM 3D printer: Bambu Lab X1, PLA Basic, 120 microns layer height, 15% infill density
- SLA 3D printer: Form 4, Grey Resin, 100 microns layer height
- SLS 3D printer: Fuse 1+ 30W, Nylon 12 Powder, 110 microns layer height
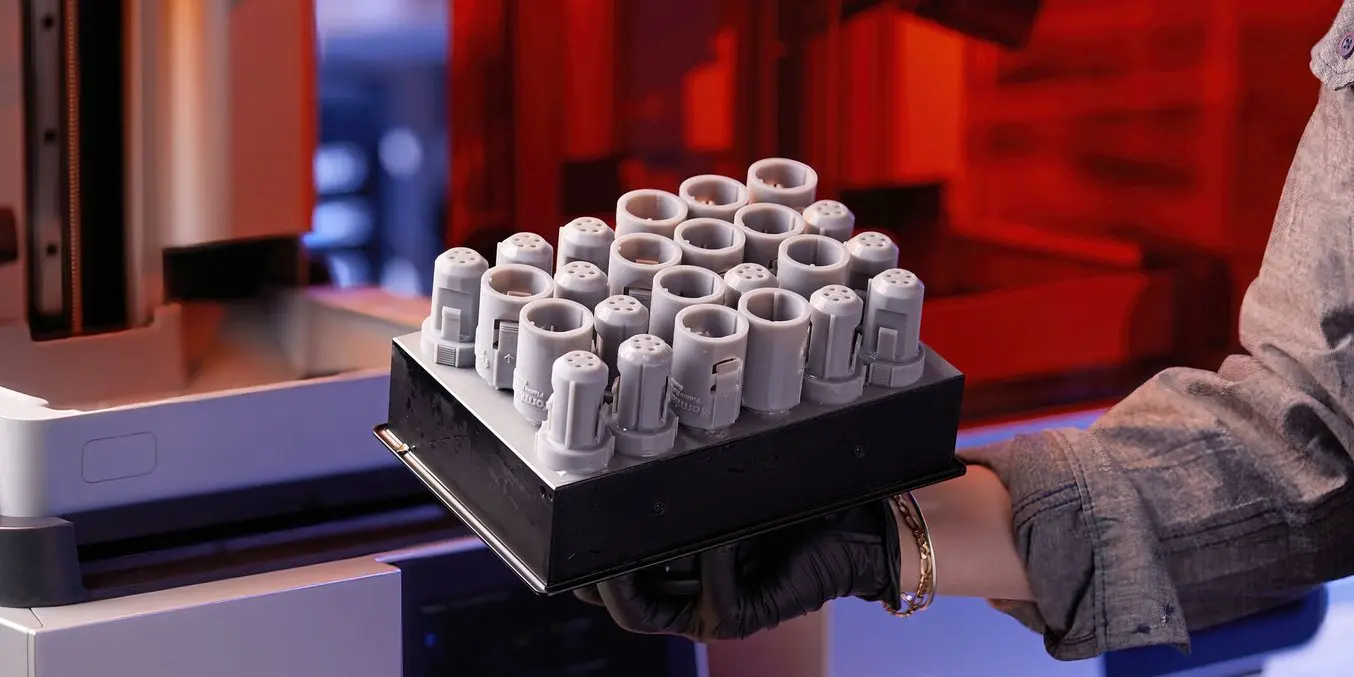
Print Speed Comparison: Electrical Connector
FDM 3D Printing | SLA 3D Printing | SLS 3D Printing | |
---|---|---|---|
1 assembly (2 parts) | 2 h 38 min | 1 h 3 min | 3 h 30 min printing (6 h 27 min cooling) |
50 assemblies (100 parts) | 84 h | 13 h 2 min | 12 h 59 min printing (13 h 49 min cooling) |
Compared printers and printing parameters:
- FDM 3D printer: Bambu Lab X1, PLA Basic, 120 microns layer height, 15% infill density
- SLA 3D printer: Form 4, Grey Resin, 100 microns layer height
- SLS 3D printer: Fuse 1+ 30W, Nylon 12 Powder, 110 microns layer height
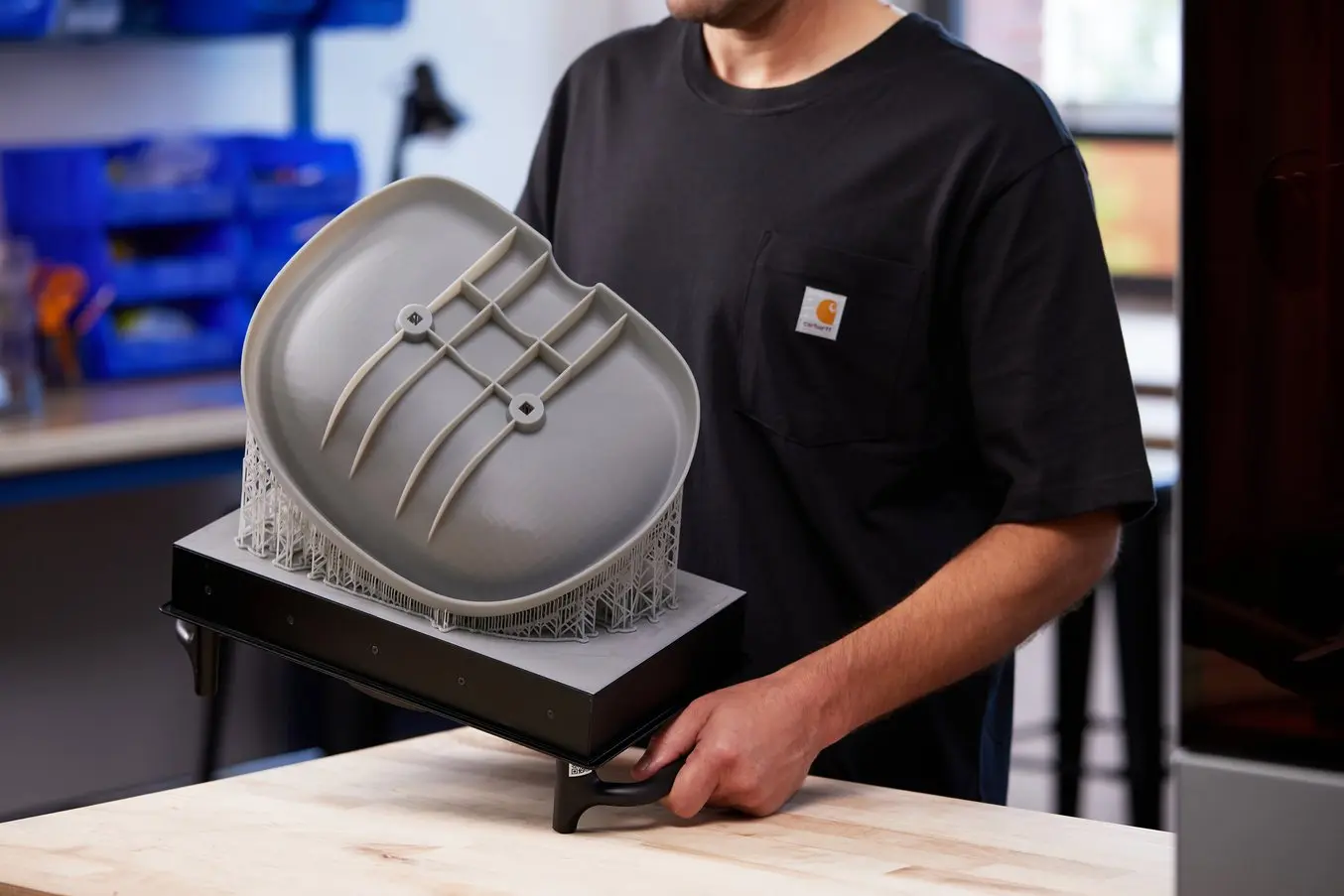
Print Speed Comparison: Radio Flyer Seat Prototype
FDM 3D Printing | SLA 3D Printing | |
---|---|---|
1 prototype | 42 hr 3 min | 2 hr 37 min |
Compared printers and printing parameters:
- FDM 3D printer: Ultimaker S7, PLA, 100 microns layer height, 20% infill density
- SLA 3D printer: Form 4, Fast Model Resin, 200 microns layer height
Curious to check the print speed for your own parts? Download PreForm, Formlabs’ free print preparation software to calculate print times when printing on Formlabs SLA and SLS 3D printers.
3D Printing Speed: Compare FDM, SLA, and SLS
How fast is a 3D printer? One of the most important factors that influence the answer to that question is the 3D printing process. Learn what’s behind 3D printer speed for FDM, SLA, and SLS 3D printers.
Fused Deposition Modeling (FDM)
Fused deposition modeling (FDM), also known as fused filament fabrication (FFF), is the most widely used type of 3D printing at the consumer level, and the most recognizable for the average layperson, who may associate the broader concept of 3D printing with this ‘hot-glue gun’ method of building parts. In an FDM 3D printer, plastic filament is heated until it becomes liquid. The liquid plastic is then extruded onto the print bed in layers, which are deposited on top of one another until the part has finished printing.
FDM 3D printing speed is limited by the extrusion process and the motor power. To create an accurate part, FDM 3D printers have to extrude filament at a specific rate, without deviation, and move the nozzle in the XY plane at an even, smooth pace. Speeding up that process can lead to variations in the mechanical properties of the filament and imprecise results.
Because there are many different types of FDM 3D printers — ranging from small hobbyist machines that cost a few hundred dollars to large industrial printers that can run into the tens of thousands of dollars — determining exact print speeds for an FDM 3D printer needs to be done on a case-by-case basis. However, all FDM printers are subject to certain factors:
- FDM 3D print speed is highly dependent on part size. Because the melted polymer is distributed by an extruder, parts that are larger along the X and Y axes take longer to print as the extruder has to travel longer distances.
- FDM print speed is affected by printer components. Many FDM 3D printers offer a wide variety of nozzles, printer beds, extruders, and other components that can impact print times.
- FDM print speed varies depending upon infill. FDM parts are not fully dense — infill density defines the “fullness” of the inside of a part. Higher infill requires more material to be deposited, making print time longer.
- FDM prints generally require little post-processing, but need to be heavily sanded in order to achieve a good surface finish. FDM prints typically have visible layer lines, which means that you may need to dedicate a lot of time (and labor) to achieve high-quality parts with smooth surfaces, especially when printing more complex parts that require heavy use of support structures.
Stereolithography is used to describe several different resin 3D printing processes that involve using light to cure liquid resin, most commonly through a tank with a transparent bottom, printing parts layer by layer upside down on a build platform that is lowered into the tank. These processes include: laser-powered stereolithography (SLA), digital light processing (DLP), or masked stereolithography (MSLA, also often used interchangeably with LCD 3D printing).
Typical print speeds vary by the type of resin 3D printing process, with the fastest type being MSLA and DLP technologies. The latest generation of MSLA 3D printers, like Formlabs’ Form 4 and Form 4L, rely on a combination of a powerful print engine and advanced optics system to cure each layer almost instantly.
- SLA print speed can be similar for one part and a fully packed build. While the laser in laser-based SLA printers has to travel a large area to cure the resin, MSLA and DLP cure each layer almost instantly. Because entire layers are cured at once, there is almost no difference in speed between prints with many parts and prints that contain just one part, enabling a higher possible throughput.
- SLA print speeds are affected by printer components. The quality and performance of the print engine and optics system influence how much light reaches the tank and have a direct impact on print times. Also, other factors, such as Form 4’s dual-layer flexible film resin tank, Release Texture, high-speed automated resin filling, and fast resin heating, decrease overall print time.
- SLA prints require post-processing, but most of it can be automated. After printing, SLA parts need to be washed with alcohol or ether to remove any excess resin and some parts also require a post-cure to help them reach optimal material properties. Both of these steps can be automated with advanced post-processing solutions.
Form 4 and Form 4L have been engineered to build parts as fast as 100 mm per hour using specifically designed materials like Fast Model Resin. Most Form 4 builds finish in under two hours using any material, enabling multiple design iterations per day. With Form 4L, most builds finish in under six hours. Even builds that are the full height of the printer, or higher-volume production runs with multiple pieces covering the entire build platform, can print in less than a day, making same-day iterations of large parts or production at higher volumes possible.
All 3D printing processes have become faster over time, but none can match the progress in resin printing. When that speed is compounded day by day and week by week, the throughput benefits are extraordinary. Form 4 and Form 4L can now match the speed of high-throughput technologies such as injection molding. Printing full build chambers over the course of a few hours, multiple times a day, can rival the output of a medium-volume injection molding machine, without the high up-front cost of tooling.
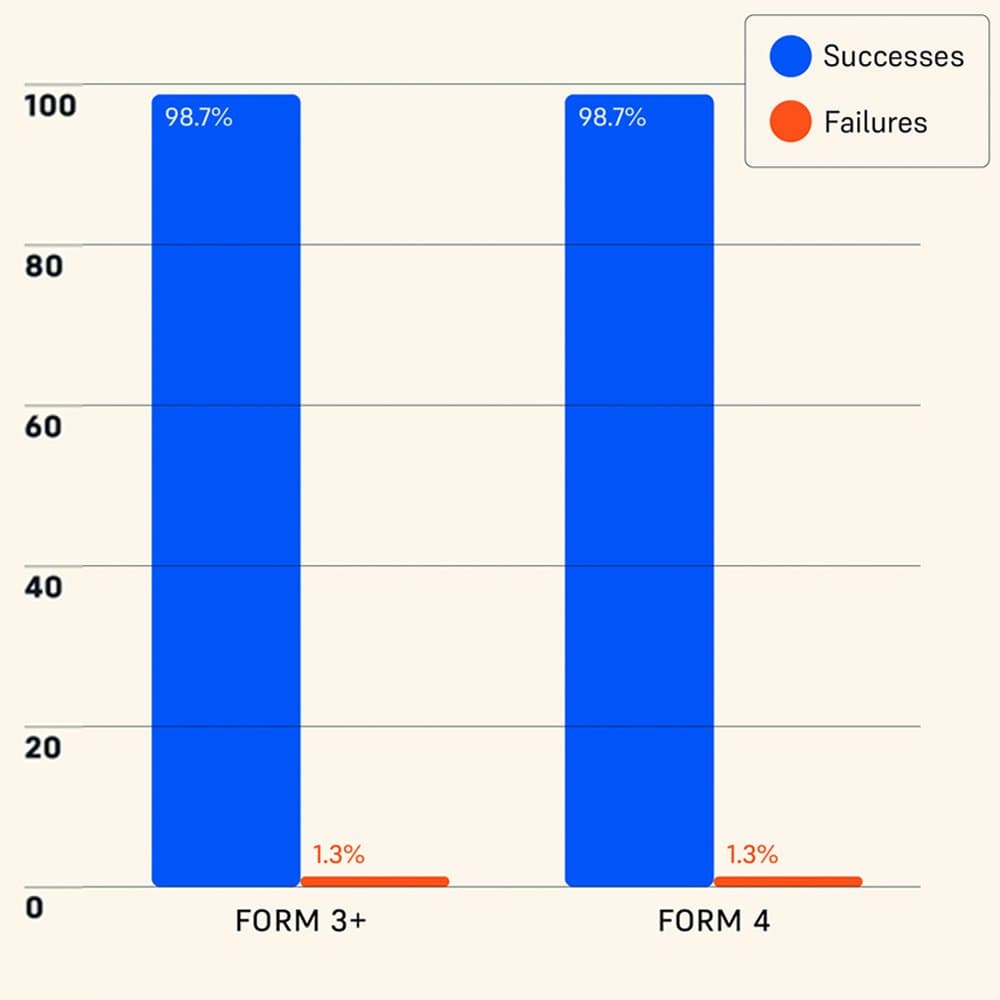
Independently Tested Reliability of Form 4 and Other Resin 3D Printers
Formlabs Form 4 was measured to have a 98.7% print success rate by an independent global leader in product testing. Read a complete description of the test methodology and see the results in our white paper.
Selective Laser Sintering (SLS)
Selective laser sintering (SLS) is the most common additive manufacturing technology for industrial applications, trusted by engineers and manufacturers across different industries for its ability to produce strong, functional parts in well-established materials like nylon, polypropylene, or TPU (elastomer).
SLS 3D printers use a high-powered laser to fuse small particles of polymer powder. The unfused powder supports the part during printing and eliminates the need for dedicated support structures.
SLS 3D printers are faster than FDM 3D printers because their high-powered lasers can be directed at each layer of powder and scanned across it faster than an extruder nozzle can move above an FDM print bed. However, the laser still moves slower than the light source flashing in MSLA or DLP resin 3D printing technologies.
Though not technically print speed, SLS 3D printing processes also have to account for the cooldown time of the build chamber — because the laser sinters the powder at such a high temperature, the build chamber has to cool down before being post-processed, which can add to increased overall lead time for parts.
This combined print and processing time for SLS parts, however, is generally not a concern for production. Though print speed for single parts may be longer than with other technologies, overall throughput is excellent for SLS 3D printers because of their larger build volumes and the self-supporting print bed that allows parts to ‘nest,’ so that customers can fully pack the build chamber and reach production volumes, even with only one printer.
For example, a fully packed print job on the Fuse 1+ 30W can be completed overnight during ‘dead time’ and the cooldown can finish outside the printer during the day, enabling same-day parts and 24/7 throughput.
- SLS 3D print speed depends upon part size. Parts that are larger along the X/Y axes take longer to print as the laser has to trace a larger area. By optimizing the path of the laser on the Fuse 1+ 30W for efficiency, Formlabs managed to decrease print times by up to 25%.
- SLS print speeds are affected by printer components. Print speed is highly dependent on the laser power. For example, the Fuse 1+ 30W uses a powerful 30W laser to achieve high throughout. A typical print job takes just seven hours and 95% of fully packed print jobs can be completed within 14 hours.
- SLS parts require post-processing, but it is very efficient. SLS post-processing can be quite short, since many steps can be automated with machines like Fuse Sift and Fuse Blast, and there are no supports to remove, empowering users to go from printed to professionally finished parts in as little as 15 minutes.
While SLS 3D printing is not the best choice for producing a single part as fast as possible, the combination of low cost per part, high productivity, efficient post-processing, and established materials make SLS a popular choice for manufacturers and a cost-effective alternative to injection molding for low-volume or bridge manufacturing.
What Factors Influence 3D Printing Speed
Part Size
As each 3D printing technology produces parts in layers, the larger the print is along the Z-axis, the longer it will take to print.
However, bigger part size or more parts in a build along the X and Y axes don’t necessarily increase print time. 3D printing processes that cure entire layers at once (MSLA, DLP) will print large parts and fully packed builds faster than technologies where the nozzle has to travel longer distances (FDM) or trace parts individually (laser-based SLA, SLS).
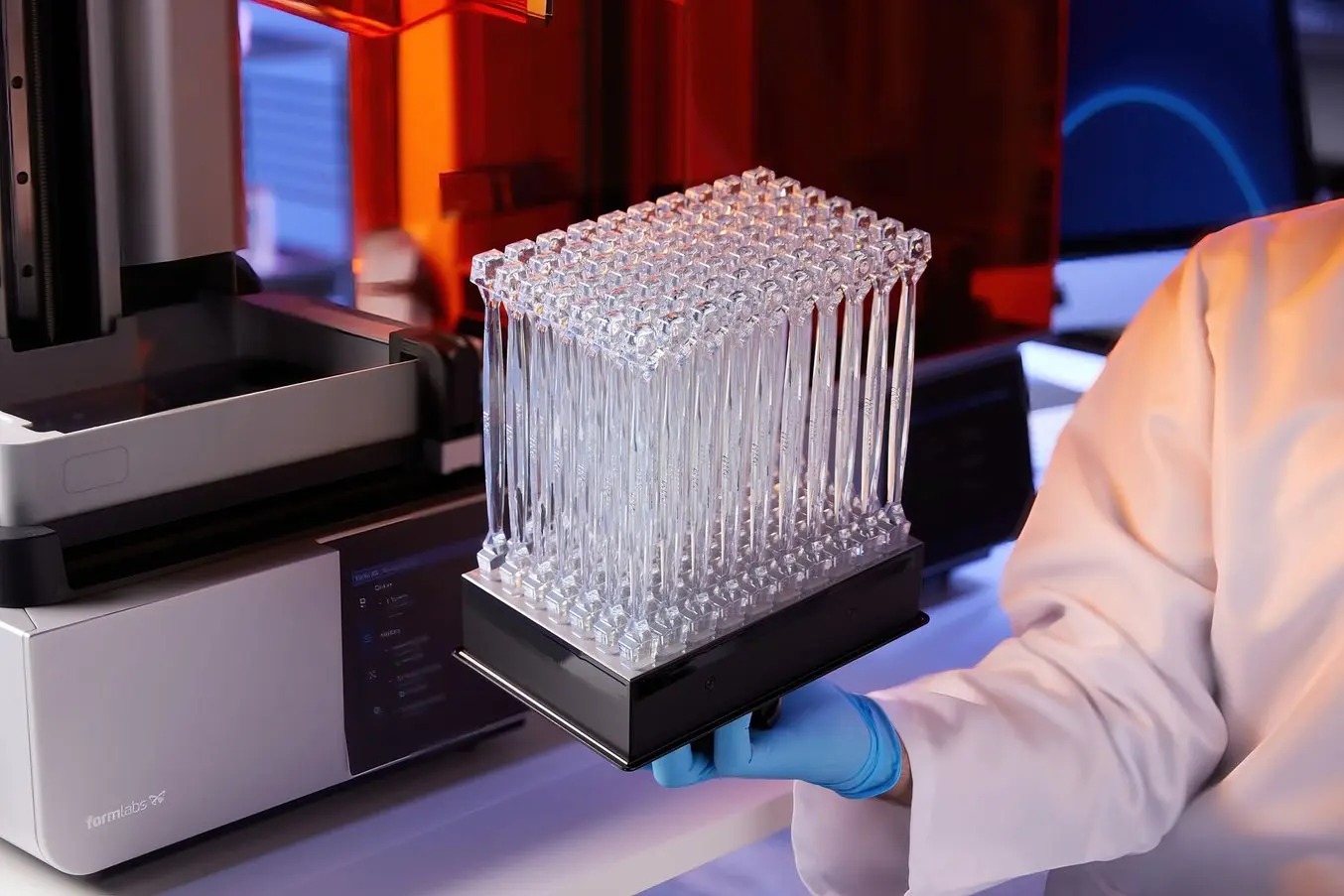
Form 4 can finish a fully packed build in 2-5 hours, depending on the material. The throughput possible with a fleet of affordable, fast, and easy-to-use 3D printers like Form 4 can match the output of traditional processes like injection molding.
Resolution
Understanding how to measure resolution in 3D printing, particularly across a wide range of technologies, involves analyzing a printed part on 3 axes: Z (vertical) and X/Y (horizontal). The Z-axis resolution is heavily influenced by layer height, while the X/Y resolution is influenced by a number of different factors depending on the 3D printing technology you use.
Layer height (Z-axis resolution) affects speed for all types of 3D printers. If your print has thicker layers, it will require fewer overall layers to be printed, decreasing overall print time.
With FDM 3D printers, there is a significant tradeoff between print time and resolution. Thicker layers will require fewer overall layers to be printed, decreasing overall print time, but they’ll also result in more visible layer lines and a less smooth surface finish.
Some FDM printers offer users the option to increase the speed at which the extruder deposits filament or moves over the build area. Additionally, users can also install larger nozzles that can deposit more material faster, but decrease X/Y/Z resolution. However, each of these options results in lower accuracy and resolution, worse surface finish, and other undesirable outcomes.
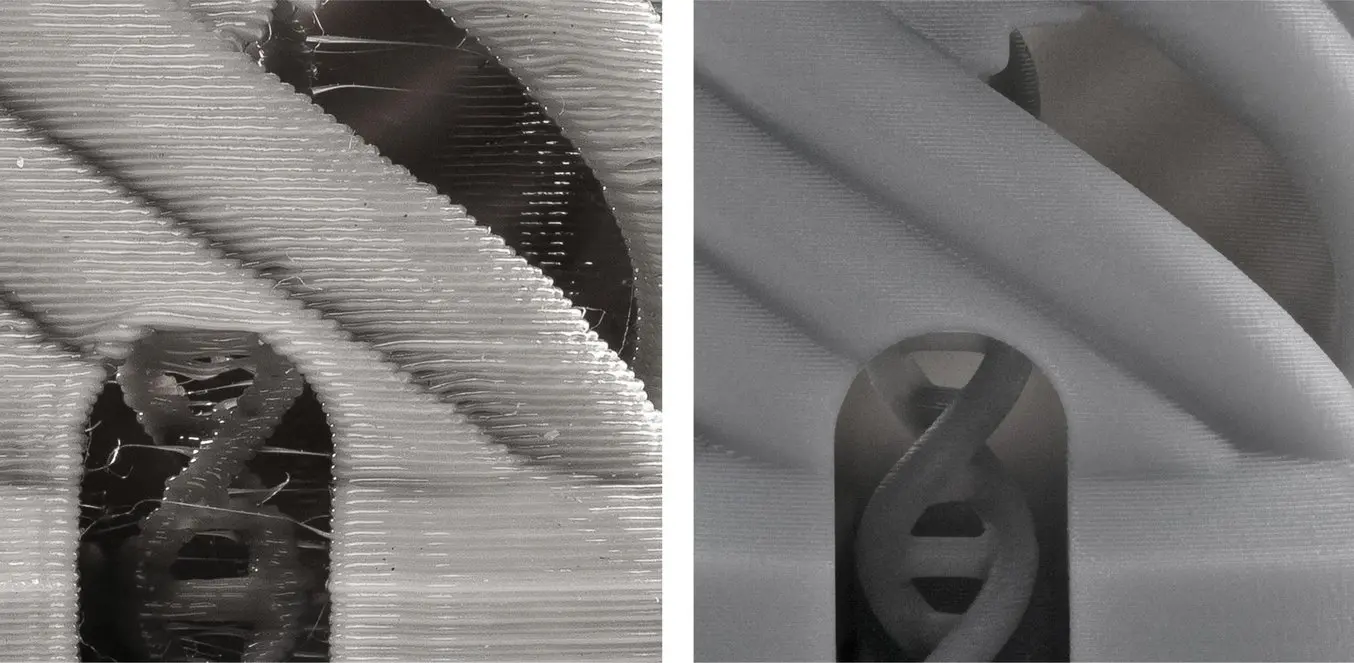
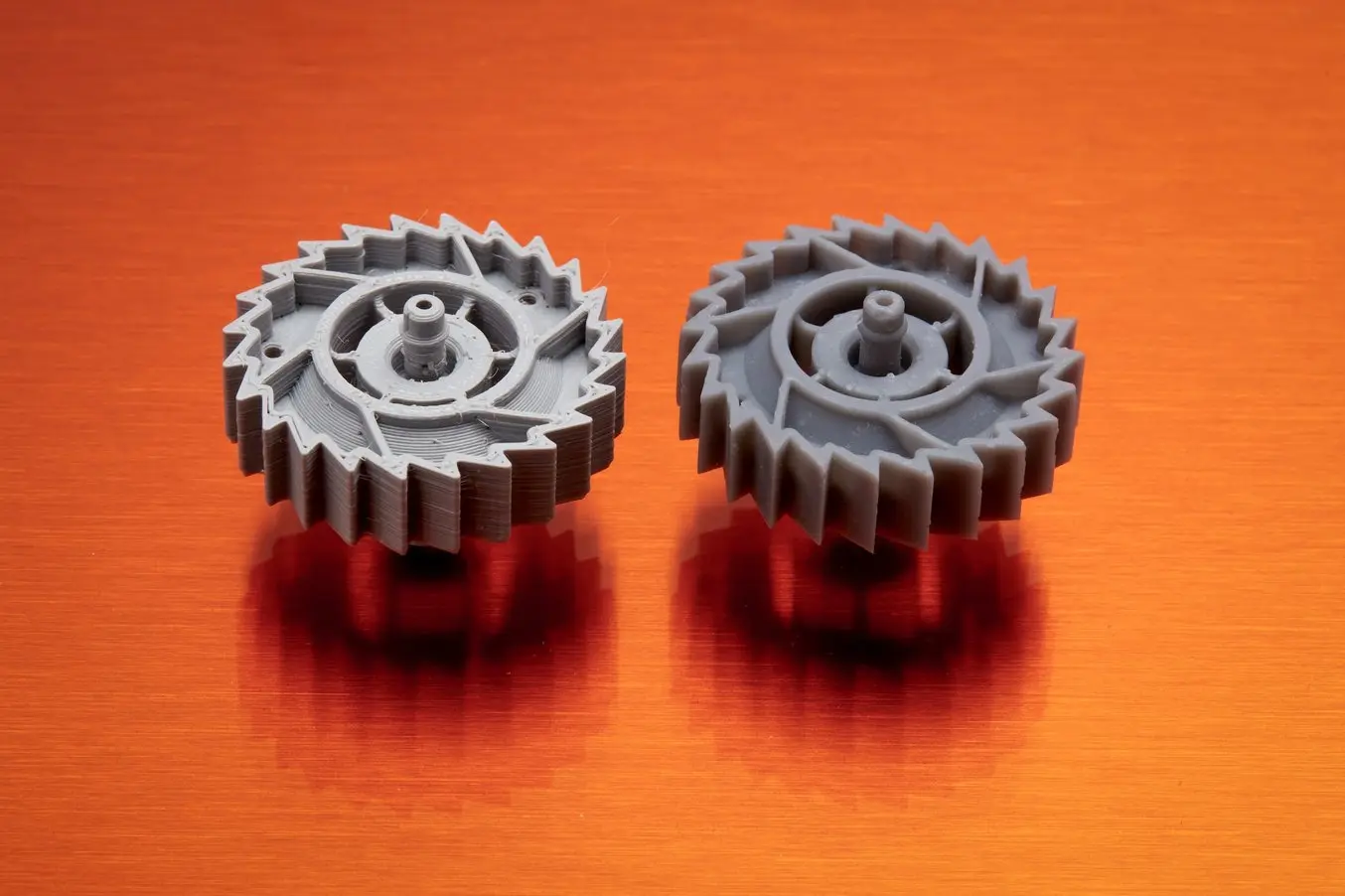
FDM printers struggle with complex designs or parts with intricate features (left), compared to SLA printers (right).
SLA 3D printers offer high resolution regardless of the layer height. Resin printers can direct the light extremely precisely at the liquid resin, resulting in parts with superior surface finish even when printing thicker layers. While layer lines might be slightly more visible on curved surfaces, for most parts, there’s barely any visible difference between a part printed at 50 microns or 100 microns that would justify the 2X print time. X/Y resolution depends on the resolution of the projector or LCD screen, or the laser spot size and how precisely it can be controlled — which are defined by the hardware specs and generally superior to all other processes (50 microns or below).
Similar to SLA, resolution is less of a concern for SLS 3D printers. The laser used in SLS 3D printers can precisely fuse particles and printed parts generally don’t have any visible layer lines. Most SLS printers don’t even allow users to change the resolution — Z resolution is not adjustable, while X/Y resolution is defined by the hardware specifications.
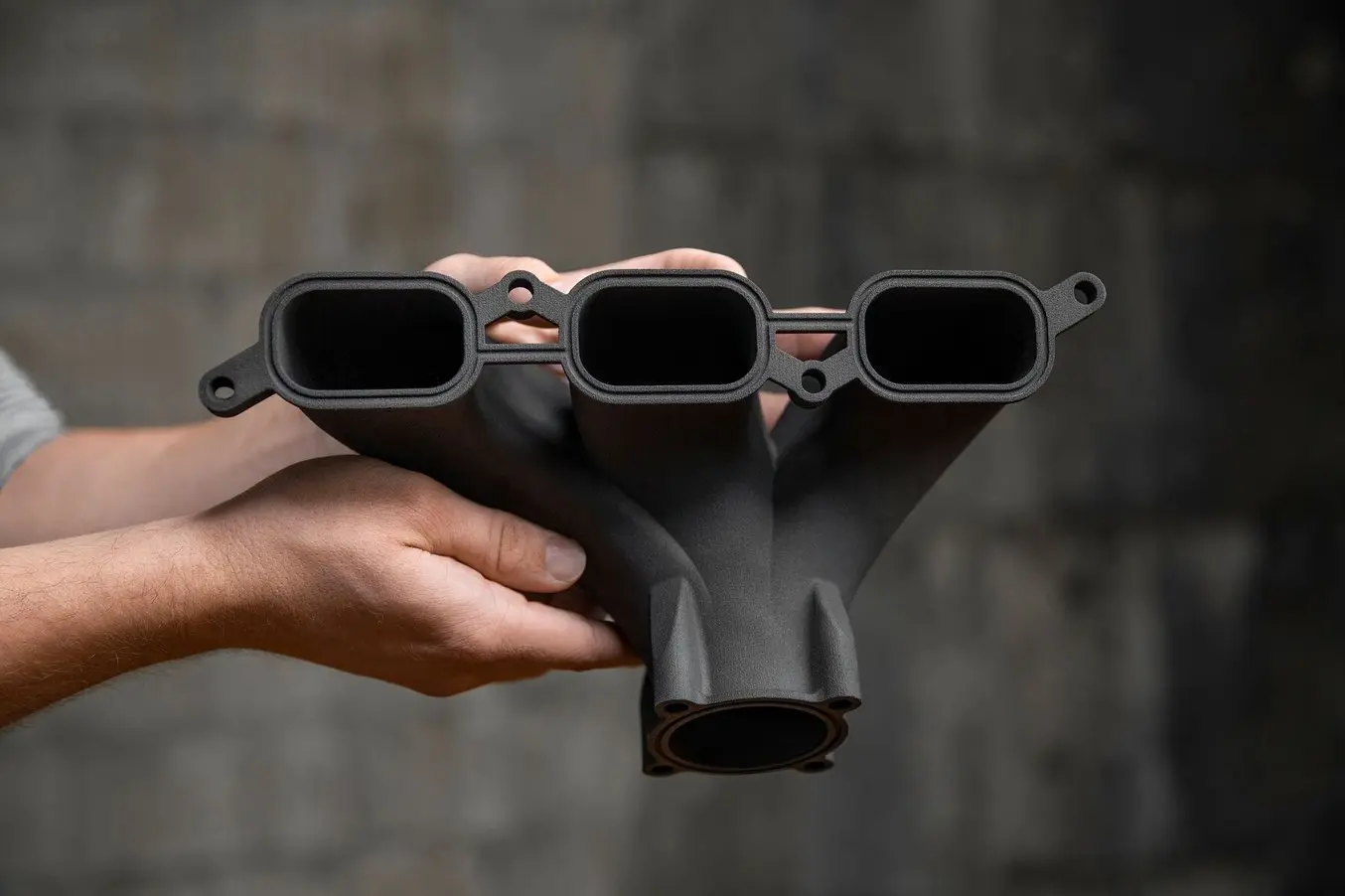
Industrial-quality SLS 3D printers, like the Fuse 1+ 30W, have excellent resolution and can create highly detailed parts that combine strength with organically curved features and precise negative or positive features.
Materials
Material selection can have a measurable effect on the overall time to print. FDM, SLA, and SLS 3D printers all print polymers, but heating/extruding, curing, and sintering are very different processes.
With FDM 3D printers, the type of filament can make a big difference when it comes to 3D print speed. In general, materials that are easy to print with, like PLA and PETG are the fastest printing filaments. The print speed for engineering materials like ABS and nylon is slightly behind. However, flexible materials like TPU need to be printed substantially slower to ensure higher print success rates.
When printing with an FDM 3D printer, it is always a good idea to start on a slower setting to ensure the first few layers adhere properly to the print bed (and each other) before increasing speed. Faster print speed is also more likely to result in failed prints and overall lower print quality — learning how to optimize for quality on a fast FDM 3D printer is a matter of trial and error.
In SLA 3D printing, the opacity of resins as well as the concentration of photoinitiators and other curing agents added by the resin manufacturer can affect the printing speed.
For example, Fast Model Resin, Formlabs’ fastest resin, has a higher concentration of photoinitiators and is capable of printing at speeds of over 100 mm per hour on Form 4. This makes it possible to print smaller models in minutes and a fully packed build in less than two hours.
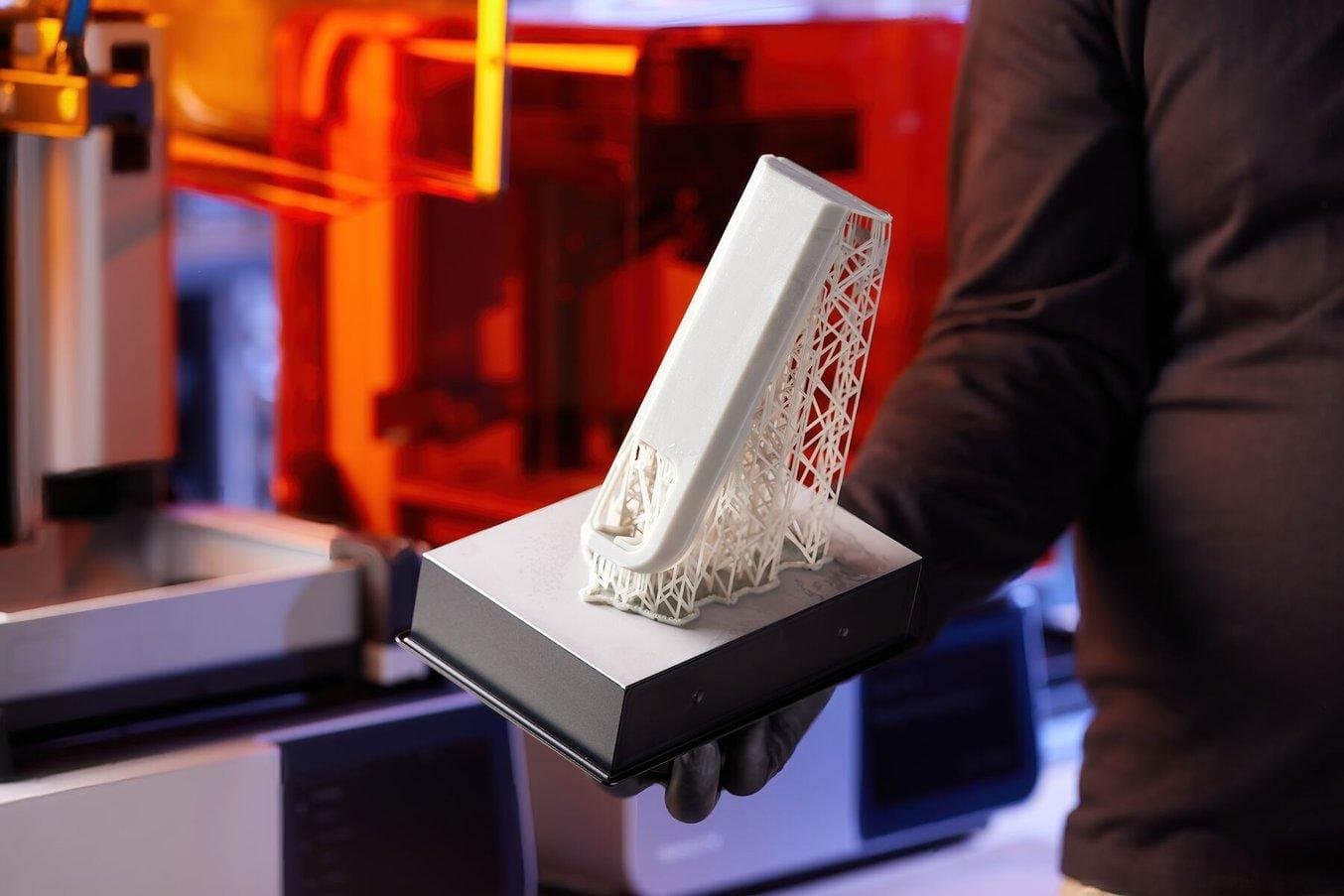
Fast Model Resin is capable of printing at speeds of over 100 mm per hour on Form 4.
In general, clear resins print slightly faster because they have a greater cure depth, which means the light source must spend less time curing each layer. Additionally, high-viscosity resins, such as glass-filled resins or those used in dentistry for dentures, will typically print more slowly than low-viscosity resins. Similarly to FDM, flexible materials also print slower than rigid materials.
With SLS 3D printers, nylon 12 is the most widely used material and is also generally the fastest, but all other materials offer comparable print speeds, including flexible materials.
Model Complexity
While the general perception is that complexity in 3D printing is free (compared to traditional processes like machining or injection molding), it’s not entirely the case when it comes to print speed.
Model complexity has a slight negative effect on print times for FDM, laser-based SLA, and SLS 3D printers. The reason is similar to why X/Y part size affects print speed more for some printers than others — these printers have to draw or trace the part geometry for every layer, which takes longer for more complex shapes. However, because MSLA and DLP printers cure an entire layer at one time, more complex parts do not equate to slower speeds.
The other, generally more important aspect is support structures. In both FDM and SLA printing, support structures are often needed to successfully print more complex parts, like those with many overhanging features. After a print job is completed, support structures need to be removed and any irregularities in the finished part sanded down.
Formlabs SLA 3D printers use light-touch supports that are easy to remove, reducing post-processing.
Not only do support structures add time to post-processing and use valuable material, but they can also add time to the printing process, particularly in FDM and single-laser SLA 3D printers.
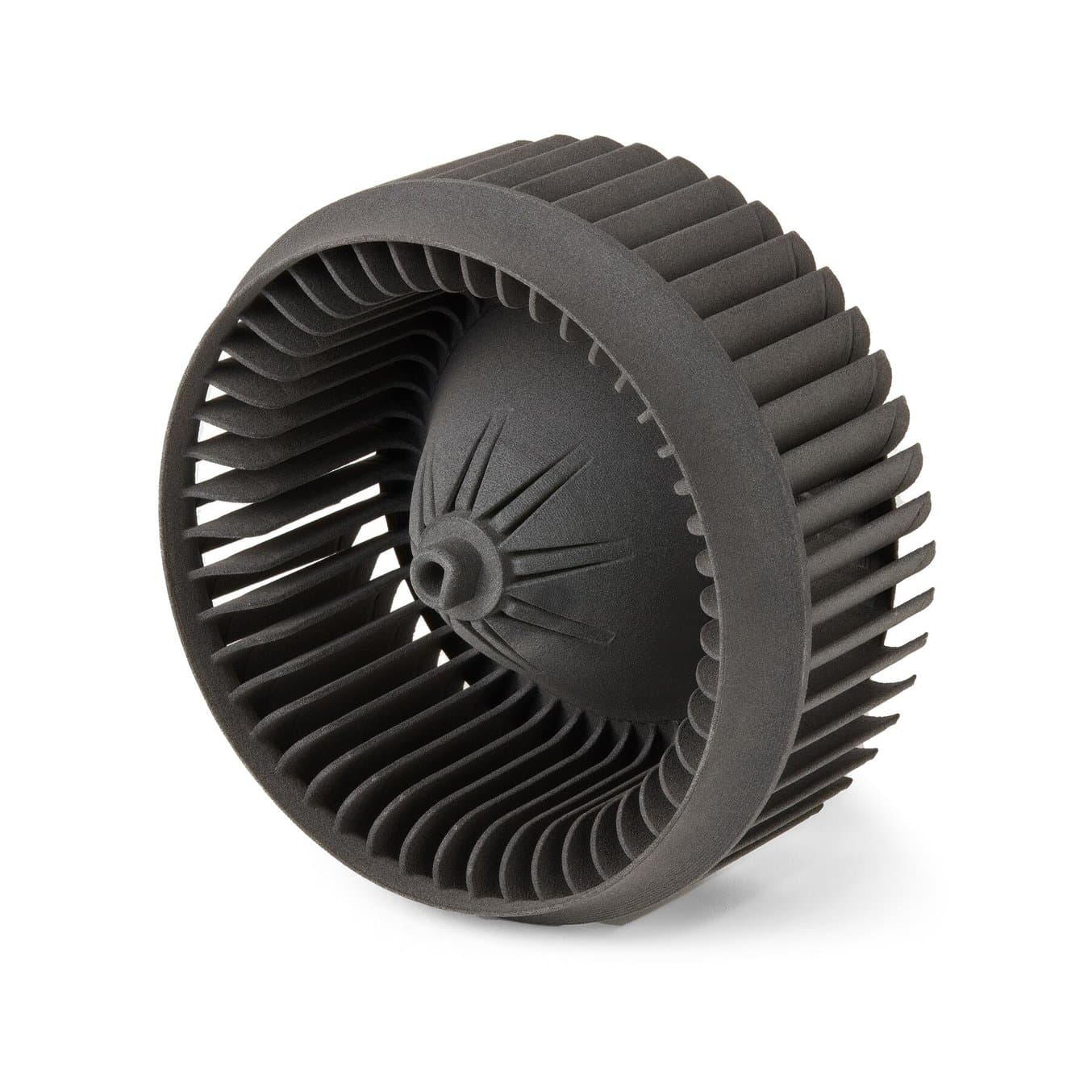
SLS 3D printing is ideal for printing complex shapes in both rigid and flexible materials.
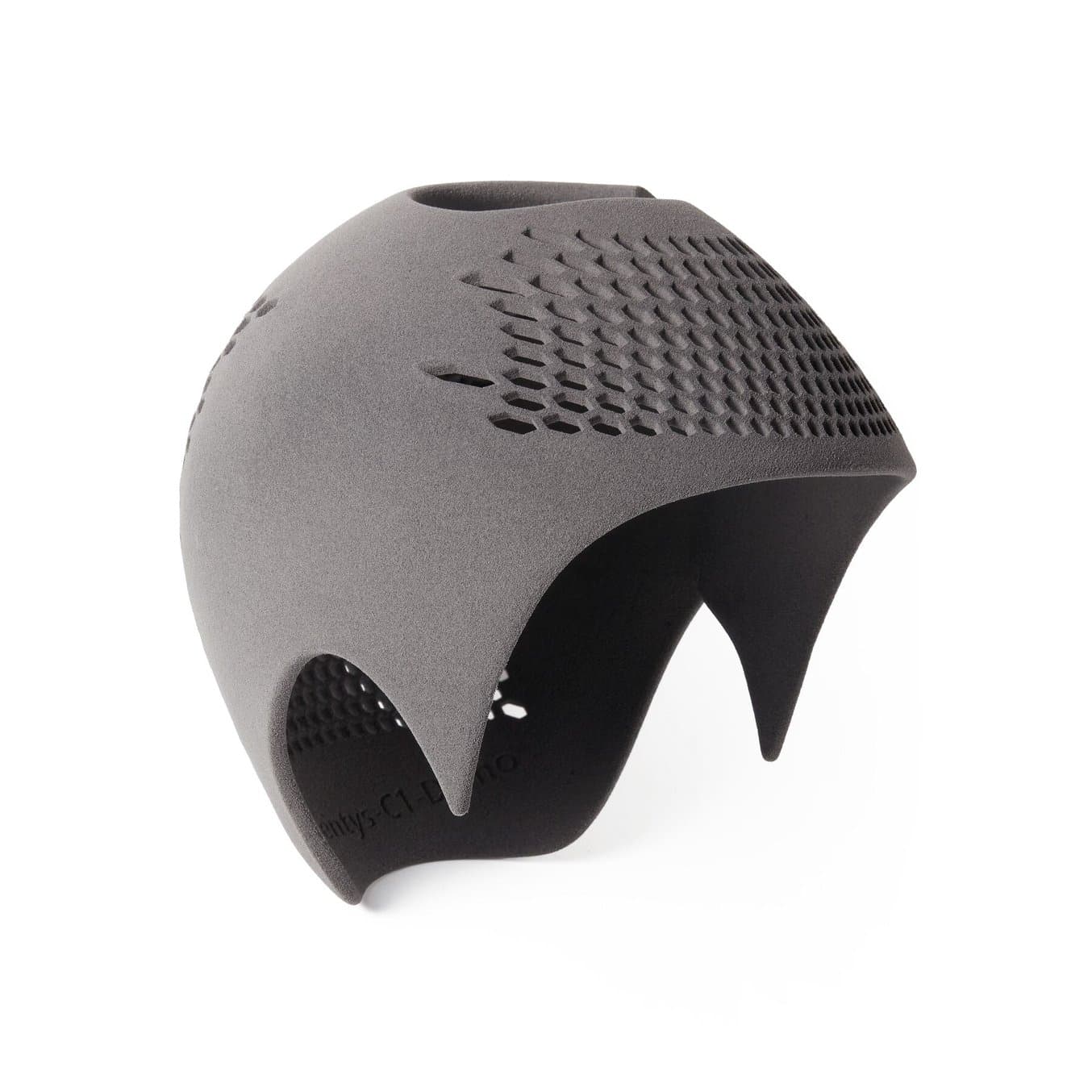
SLS 3D printing does not require the use of supports because unsintered powder keeps the printed structure in place. As a result, SLS print jobs don’t waste any powder, or time, on creating supports.
Conclusion
3D printing fulfills the needs of project teams across multiple industries to iterate on designs, improve processes, and even fabricate end-use parts more quickly than with traditional methods. High speed and high throughput 3D printing with technologies such as SLA and SLS enables you to shorten design and manufacturing cycles.
Curious to see SLA or SLS quality firsthand? Pick from our list of applications and request a free sample part to find a material that meets the requirements for your project.