New Fuse Ecosystem Improvements Make Producing Consumer-Ready SLS Parts Easier Than Ever
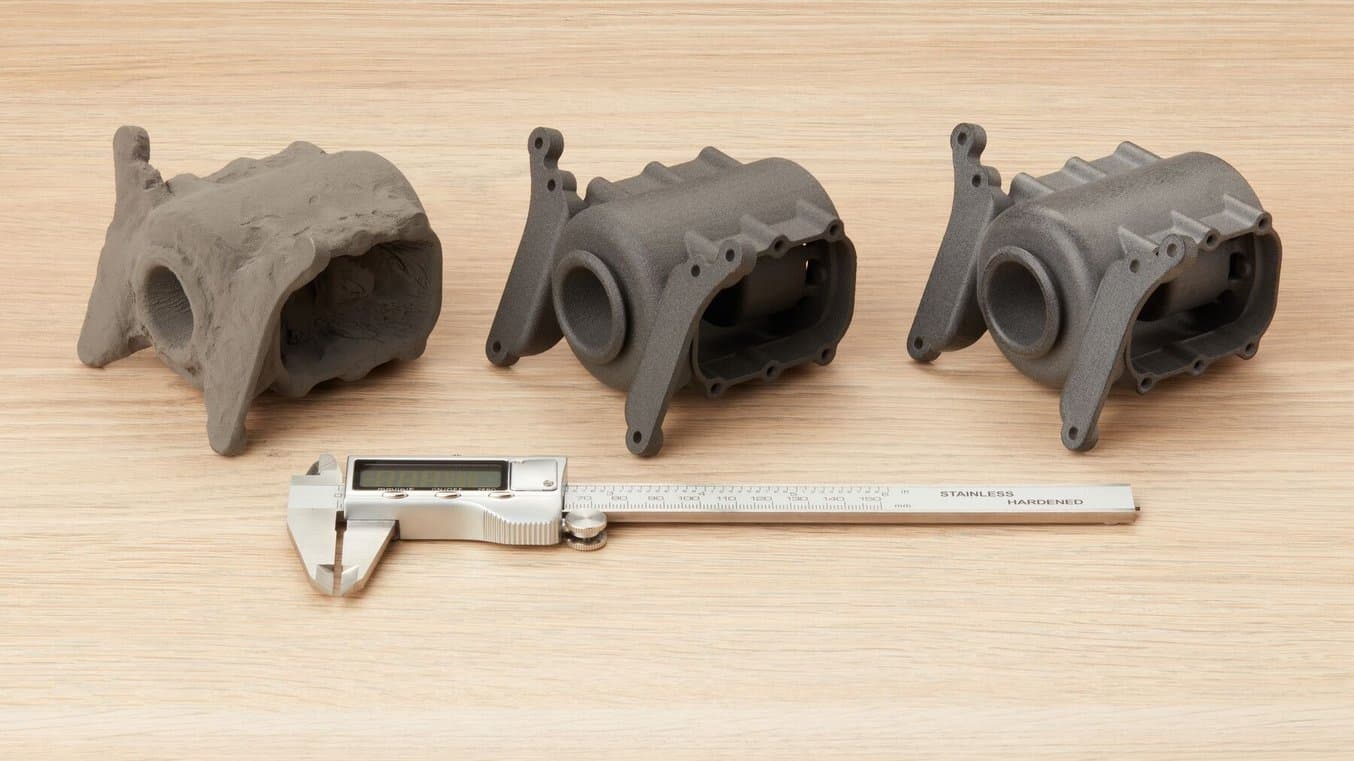
Formlabs is excited to announce the arrival of the Fuse Blast Polishing System and the Fuse Sift Glovebox Bundle — improvements to the selective laser sintering (SLS) workflow that enable users to produce consumer-ready parts in a simplified and more organized Fuse Ecosystem.
Adding the Fuse Blast Polishing System elevates your SLS workflow, enabling you to deliver professional, consumer-ready parts with high-quality surface finish for customer-facing applications in a simple, cost-effective package. The simple plug-in module eliminates the need for complex, third-party solutions for surface finishing, and can even replace coating or vapor smoothing in some situations. The Fuse Blast Polishing System delivers similar professional-quality finishes as a simple and affordable workflow improvement, saving you tens of thousands of dollars in expensive equipment while completing your SLS workflow. In one automated step for both cleaning and polishing, you can go from roughly cleaned part to a consumer-ready product that can stand up to any high visibility end-use application.
In addition to the improvements to part quality through Fuse Blast Polishing System, new Fuse Sift workflow improvements — Fuse Sift Glovebox and Fuse Sift Parts Carrier — help organize your workspace, making the post-print workflow cleaner and easier to manage.
SLS 3D printing is rapidly gaining popularity for every application, from consumer goods prototyping to the scalable production of end-use parts. Though the Fuse Ecosystem is already the most complete and accessible SLS workflow available, these new accessories take it to the next level. Current customers can make higher volumes of end-use quality products without increasing labor, and smaller businesses and startups can access industrial manufacturing power at an accessible price.
Fuse Blast Polishing System
SLS 3D printing, more so than any other type of polymer additive technology, is the tool of choice for businesses who need highly accurate, industrial, detailed parts for end-use or functional prototyping applications. However, surface finish — which on SLS parts can be slightly pebbled or rough — has held some businesses back from implementing the technology at scale for these applications.
Media blasters like Fuse Blast can remove loose powder, but for parts with high aesthetic requirements, polishing is required. The Fuse Blast Polishing system delivers an easy, drop-in solution to customers who are already saving time and money with Fuse Blast.
Fuse Blast Polishing System creates smooth parts by compacting the surface of parts, rather than melting or abrading the roughness away — this is a faster and more cost-effective way to achieve smooth surfaces. Compared to vapor smoothing systems or coating options, polishing in an existing blasting machine is low-cost, simplified, and contained — there is no need for additional costly hardware, extra training, or outsourcing to a specialist.
Fuse Blast Polishing System | Impact Smoothing (Blast Surfacing or Shot Peening) | Abrasive Smoothing Solution (Vibratory Tumbling) | Chemical Smoothing (Vapor Smoothing) | |
---|---|---|---|---|
Typical Cost | $2,699 | > $40,000 | ~ $3,000 | > $80,000 |
Processing Time | 20-60 min | Cleaning + 20-60 min | Cleaning + 4-8 hours | Cleaning + 1-2 hours |
Smoothness (Sdr)* | < 0.01 | < 0.01 | 0.005 - 0.01 | <0.005 |
Pros | Affordable Good feature preservation Part of a complete ecosystem | Fast Good feature preservation Works with most materials | Easy Fairly inexpensive | Smoothest parts Removes surface porosity |
Cons | Surface still porous | Requires separate machines | Leaves powdery cast Very slow Abrades parts Loud | Geometry-dependent Expensive Material-dependent |
*Fuse Blast Polishing System is a $2,699 add-on to Fuse Blast (available for $10,999). The cost of the latter is excluded from this comparison as other surfacing methods also require a cleaning and media blasting solution beforehand.
**Sdr (developed interfacial area ratio). This parameter is expressed as the percentage of the definition area's additional surface area contributed by the texture as compared to the planar definition area. The Sdr of a completely level surface is 0.
Fuse Blast Polishing System is an ecosystem improvement developed for existing Fuse Blast machines. The convenient drop-in module slots into the right-hand column of any Fuse Blast, so that operators can switch between cleaning parts with Glass Media and polishing parts with Polish Media, without purchasing a separate machine for polishing. Being able to switch between media allows operators to customize their workflow based on the desired finish or application, and is an affordable, simple way to level up any workflow.
Fuse Blast Polishing System is a part of Formlabs' commitment to continuous improvement of all of our products. It makes the Fuse Blast a more complete solution, which in turn improves the entire SLS workflow. The Fuse Series Ecosystem is the most popular SLS 3D printing solution in the world, accounting for over 50% of all powder bed fusion 3D printing solutions sold globally — and its popularity is due in large part to the streamlined, end-to-end workflow that the Fuse Blast Polishing System is now part of.
Fuse Sift Glovebox Bundle
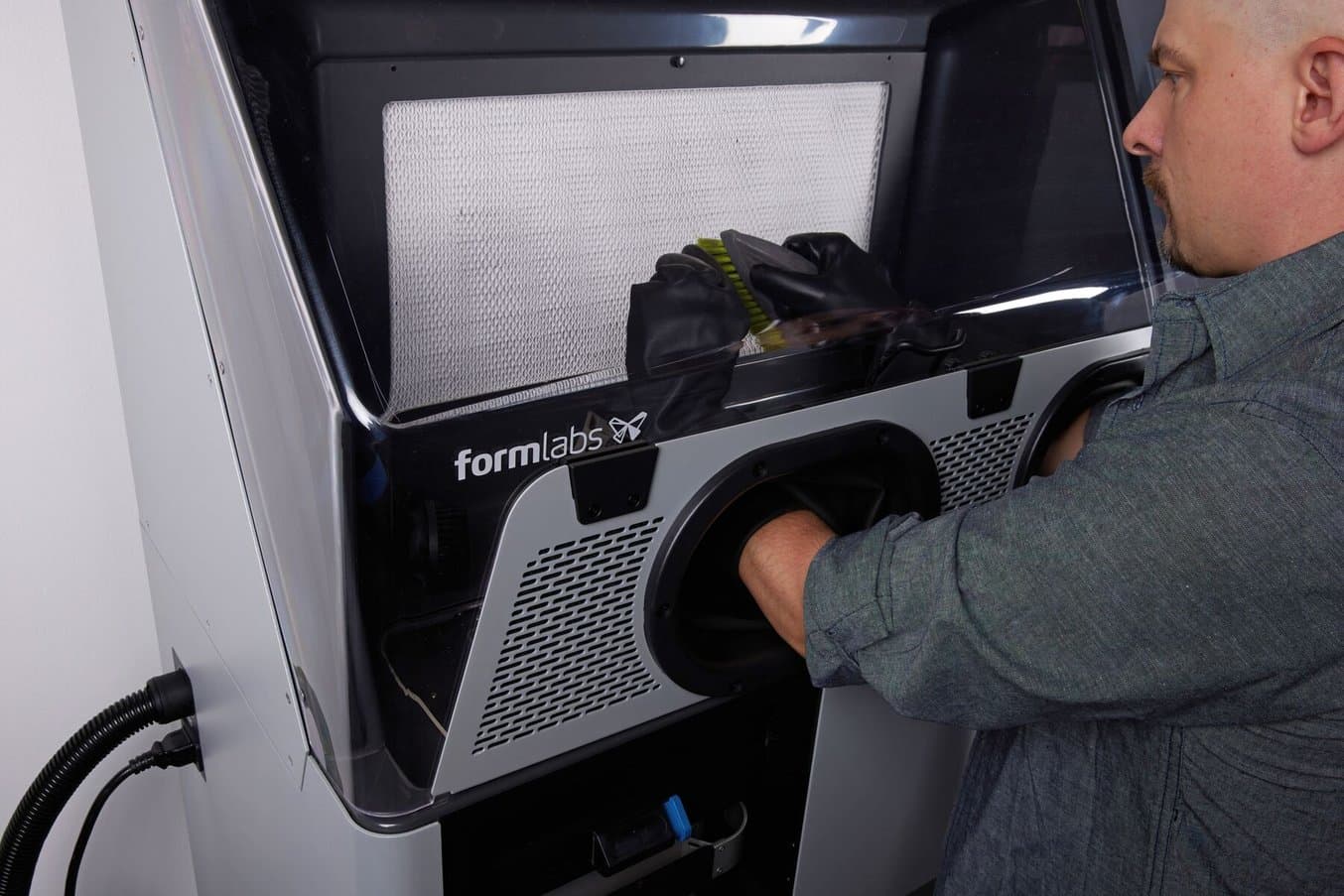
The Fuse Sift Glovebox Panel provides a contained environment that still gives users full control over the powder de-caking process and part extraction.
SLS 3D printing has come a long way in the past few years — powerful machines like the Fuse Series are no longer complicated, room-sized industrial behemoths, proving that the workflow doesn’t have to be complex and require special training. But one thing that hasn’t changed is that powder, like any 3D printing material, requires management.
One piece of feedback that we’ve heard consistently from Fuse Series customers is that the Fuse Sift should have a more comprehensive solution to keeping powder completely contained beneath the work area hood. The Fuse Sift Glovebox Bundle, consisting of a Fuse Sift Glovebox Panel and Fuse Sift Parts Carrier, provides a clean and contained workflow and streamlines the part extraction process.
The Fuse Sift Glovebox Panel closes off the front of the Fuse Sift while still allowing users to manipulate the powder cake within the work area through a pair of gloves, similar to Fuse Blast. The Fuse Sift Glovebox Panel provides a contained environment that still gives users full control over the powder de-caking process and part extraction.
Once the build chamber has emptied the powder cake into the Fuse Sift for initial extraction, users will remove the build chamber and slot in the Fuse Sift Parts Carrier — this will hold and store the parts so that they can be removed from the Fuse Sift and taken to the Fuse Blast or next step in your workflow.
Nylon 12 Powder Packaging And Bulk Pricing Changes
Formlabs is replacing the six kilogram plastic jug packaging for our Nylon 12 Powder with 10 kilogram bags. This change will reduce plastic waste coming from plastic jugs by 83% and offer customers the industry standard for SLS powder packaging.
Additionally, bulk powder pricing tiers are now open to customers looking to expand into serial production or higher volume printing of any application. Discounts start at 20% for customers purchasing 50+ kg of powder in bulk, with substantially lower prices possible after a verified cost per part analysis. To discuss which pricing tier makes the most sense for your workflow, storage capacity, and print volume, contact our sales team.
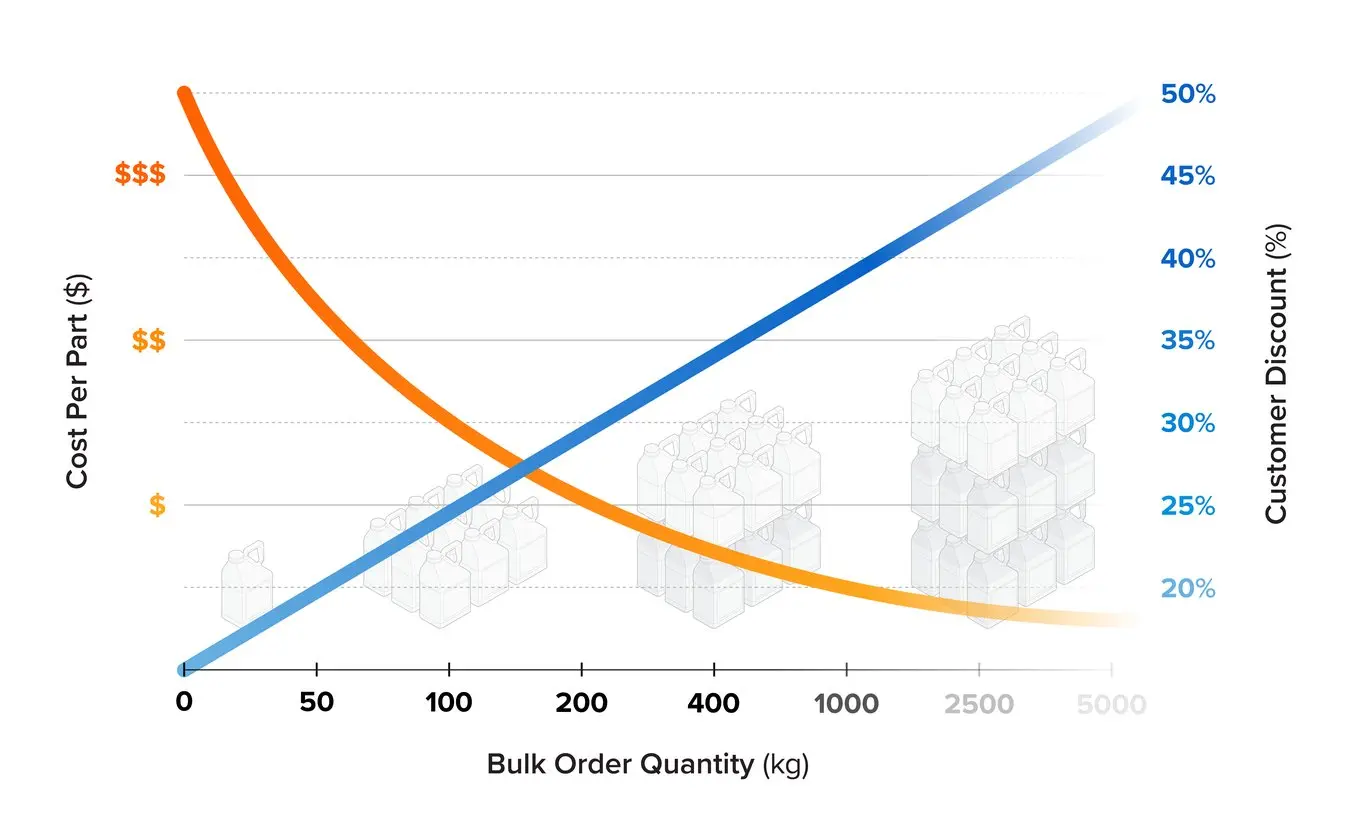
Low-Cost Powder-Safe Vacuum
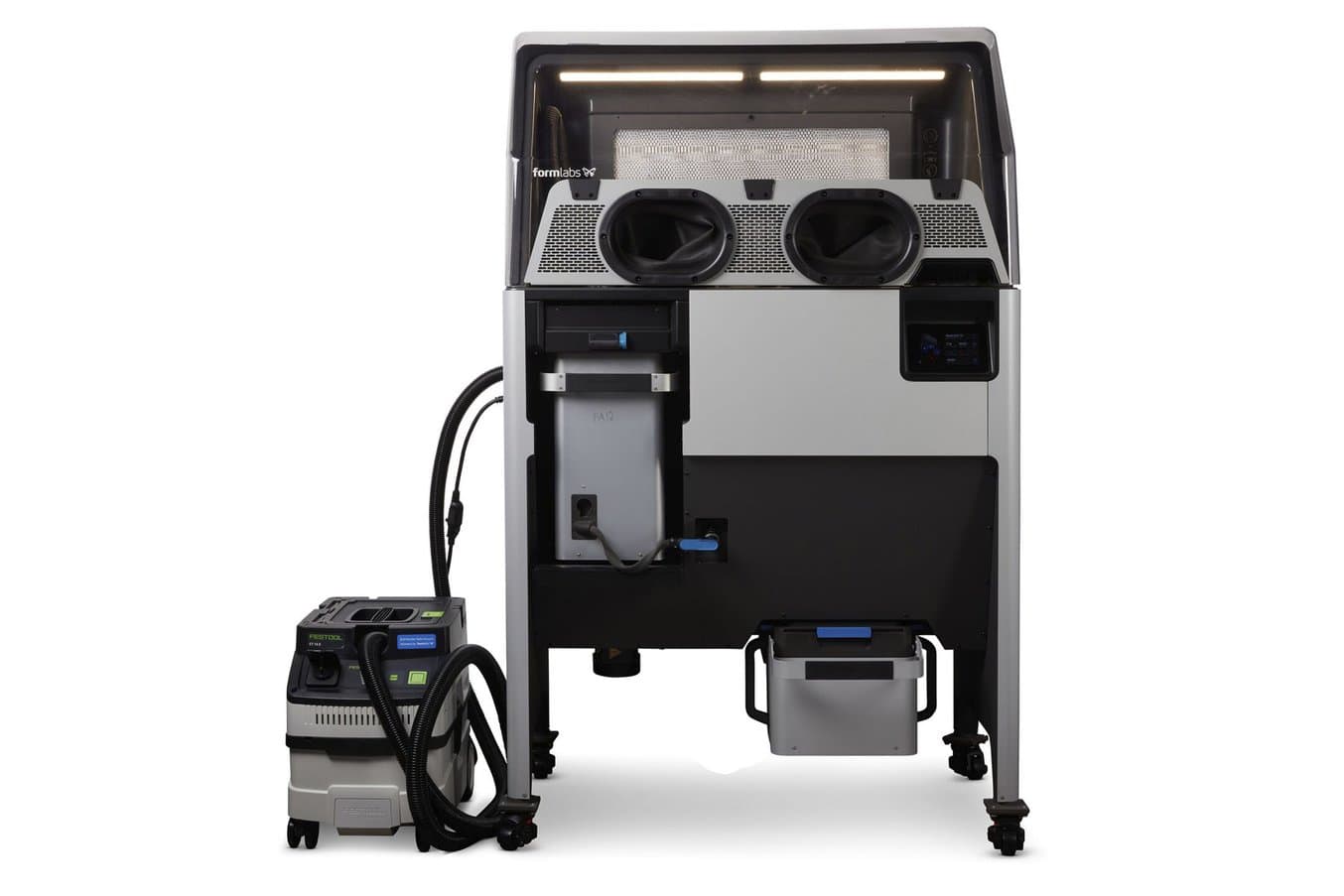
Compared to the current industrial option, the Powder-Safe SLS Vacuum is more affordable, at only $1199, and a more portable option, however, it must be operated manually instead of toggled through the Fuse Sift.
A new Powder-Safe Vacuum will now be available through our webstore and sales team. Industrial vacuums can be expensive, and though they are an important part of the Fuse Series workflow, we want to ensure that our SLS customers have access to and information about the lowest cost ways to achieve an industrial workflow at an affordable price.
The new powder-safe vacuum will be available in North America, and must be controlled manually instead of toggled through the Fuse Sift interface. Compared to the current industrial option, it is more affordable, at only $1199, and a more portable option. We recommend the heavier, more industrial option for customers who need a solution for any combustible material rather than just SLS Powders, or for those who want to prioritize workflow simplicity and would like the option to control the vacuum through the Fuse Sift interface.
From Prototype to Production, SLS Workflows Made Easier
Fuse Series customers are already pushing the boundaries of product innovation and production efficiency. Their partnership and our shared dedication to continuous improvement are what help Formlabs accelerate product development and focus on the additions that make the biggest difference in customers’ everyday lives.
The additions to the SLS workflow, Fuse Blast Polishing System and Fuse Sift Glovebox Bundle, address areas in the workflow that we saw were creating friction. Customers need an easy way to create end-use quality parts themselves, without relying on outsourcing, with a clean and simple workflow from printer to end-use part.
To order these accessories, visit our store. To learn more about bulk powder pricing and if its right for you, contact our sales team.