Fuse Series Cooldown Recommendations: Optimize Your SLS Workflow for Throughput and Accuracy
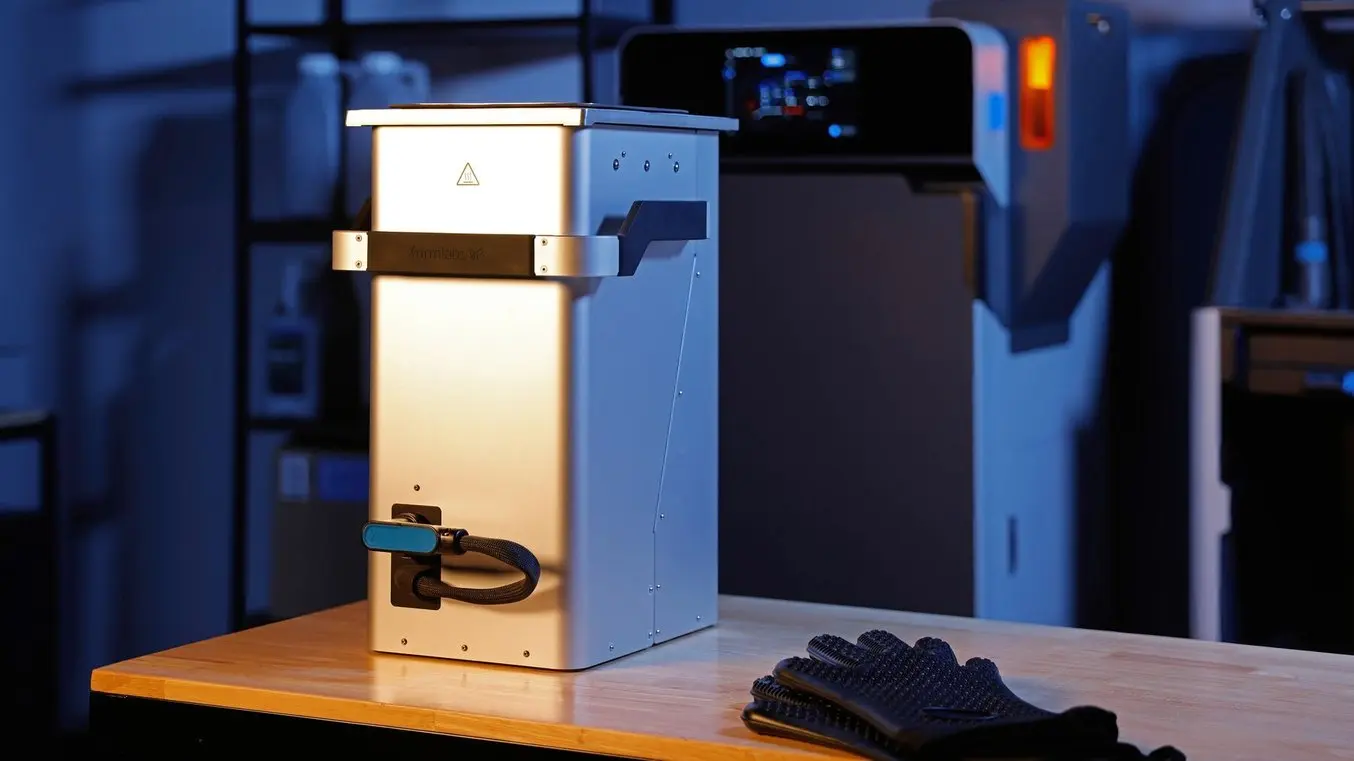
An integral but often overlooked step in the Fuse Series workflow is the cooldown. This period, when the print is finished but the build chamber and powder cake need to cool before being post-processed, has a direct impact on the accuracy of the parts. Removing the build chamber too quickly from the printer and removing the powder cake too quickly from the build chamber can cause severe warping on your parts.
Balancing a need for high throughput with 100% dimensional accuracy is key.Formlabs is changing our recommendations regarding cooldown times and build chamber removal, so that every Fuse Series user can get the most out of their workflow, without affecting the quality of their parts. By exhaustively testing our cooldown protocols, we want to empower users to make well-informed decisions about their own builds.
Cooldown Recommendations: Testing Parameters
The Formlabs team tested these parameters using Nylon 12 Powder on the Fuse 1+ 30W printer. The build chamber was fully packed with a variety of different parts, and pack density was 15%. Parts from all corners of the build chamber were tested. Multiple identical builds were printed, and build chambers were removed from the printers at varying temperatures, ranging from 100 °C to 25 °C. The parts were measured for warpage, and the variance from their intended shape was plotted against the temperature at which their build had been unpacked.
Impact of Varying Cooldown Times on Warpage
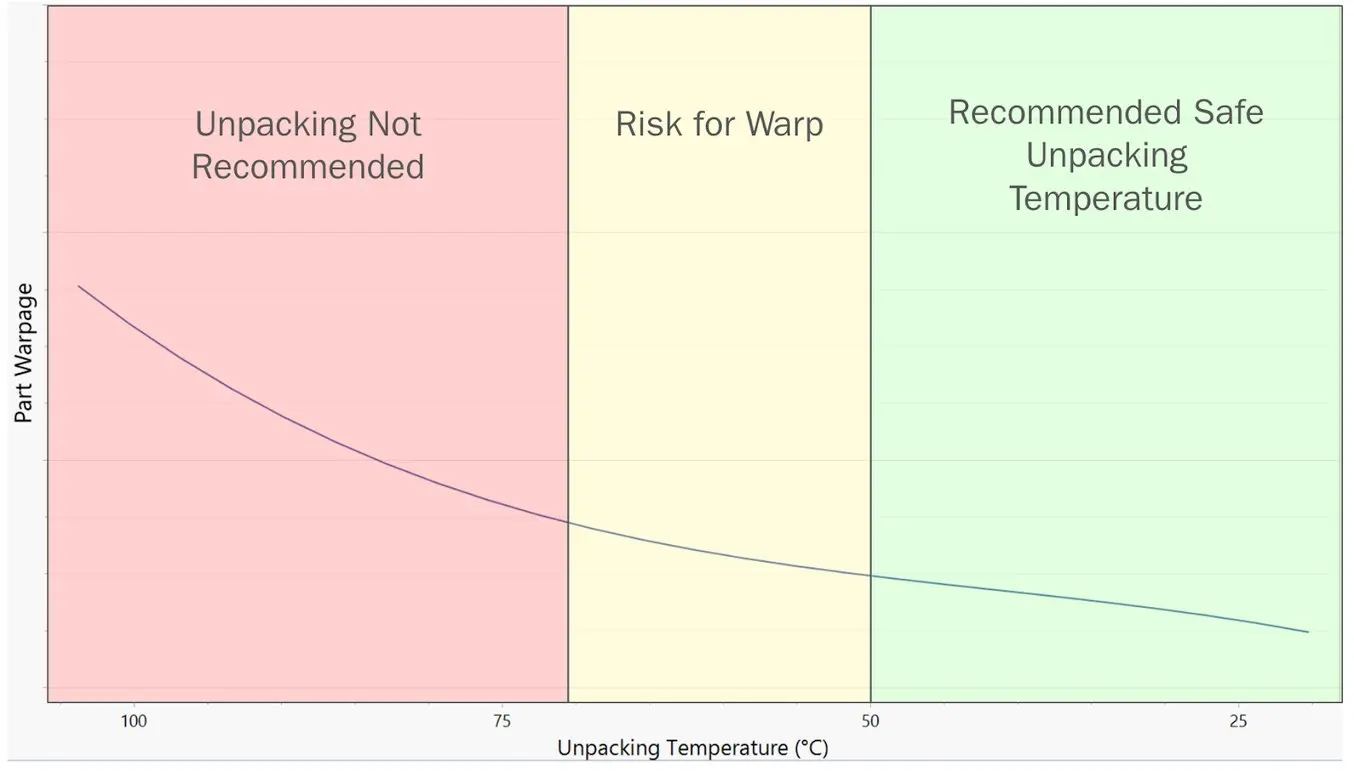
This chart is based on a build chamber that cooled outside a printer, once the print was complete.
The main conclusion of the test was that parts unpacked at higher temperatures demonstrated a higher degree of warp. In many of the builds that had been unpacked at 100 °C, the parts showed double the warp that those unpacked at room temperature did. Similarly, the most consistently dimensionally accurate parts were those unpacked at room temperature. However, those parts unpacked when the build chamber reached 50 °C were not significantly more warped than those unpacked at room temperature. Parts unpacked at temperatures higher than 70 °C showed consistent warping, and the Fuse Sift will continue to show warnings for users who attempt to insert a build chamber of parts at this temperature.
Fuse Sift Recommendations and Monitoring
Certain types of parts typically require longer cooldown times — such as long thin parts printed with their longest dimension oriented in the Z direction. Builds with these parts typically need to remain in the printer until they are 50 °C to prevent warping, but users who often print these types of parts repeatedly should conduct testing to find their own ideal threshold for build chamber removal, as this can vary based on pack density, material, and part geometry.
For users trying to optimize their workflows for throughput and high-volume production, shortening your cooldown process slightly can increase throughput, but users should expect to see some degree of warp on parts, especially on the outer corners of the build chamber. This effect can be seen most visibly on long and thin parts that are printed with their longest measure in the Z axis direction.
Creating a production schedule that allows for a complete cooldown to optimally 50 °C, but at the minimum between 50 °C and 70 °C, will improve chances of quality, consistently accurate parts. To help ensure the accuracy and fidelity of your parts, the Fuse Sift will display the temperature of the build chamber and recommendations for timing your unpacking and post-processing steps.
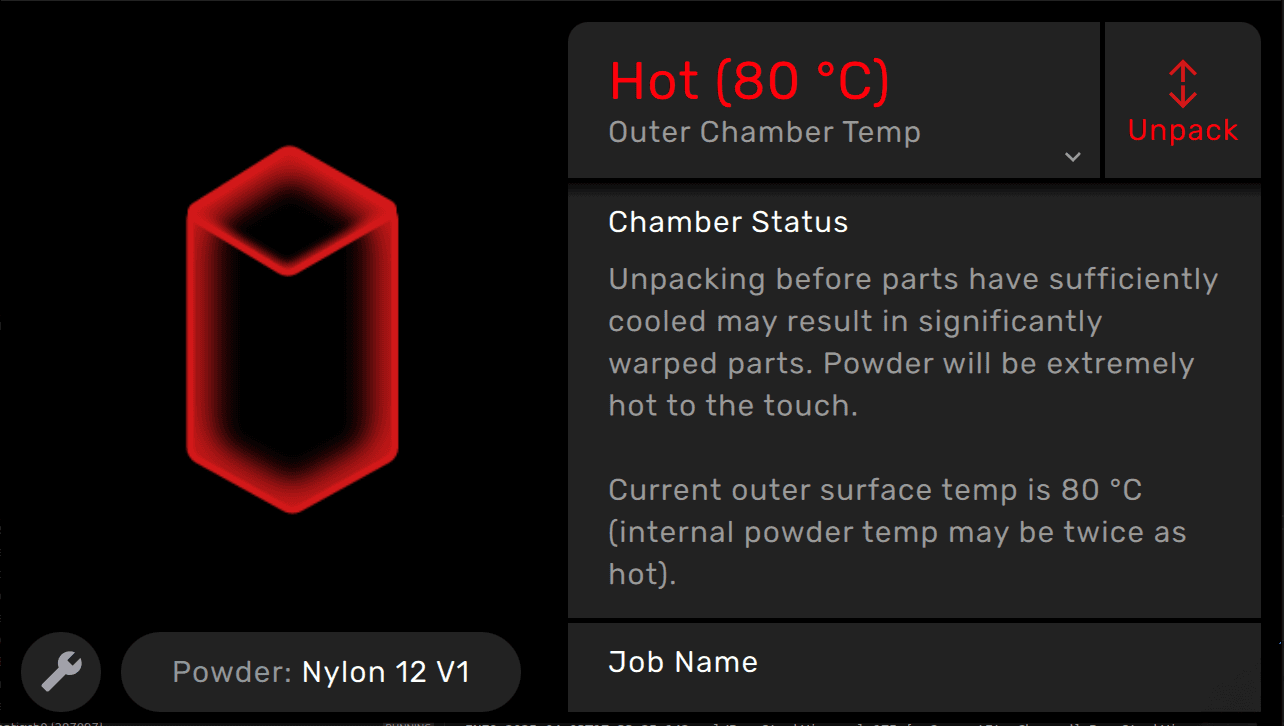
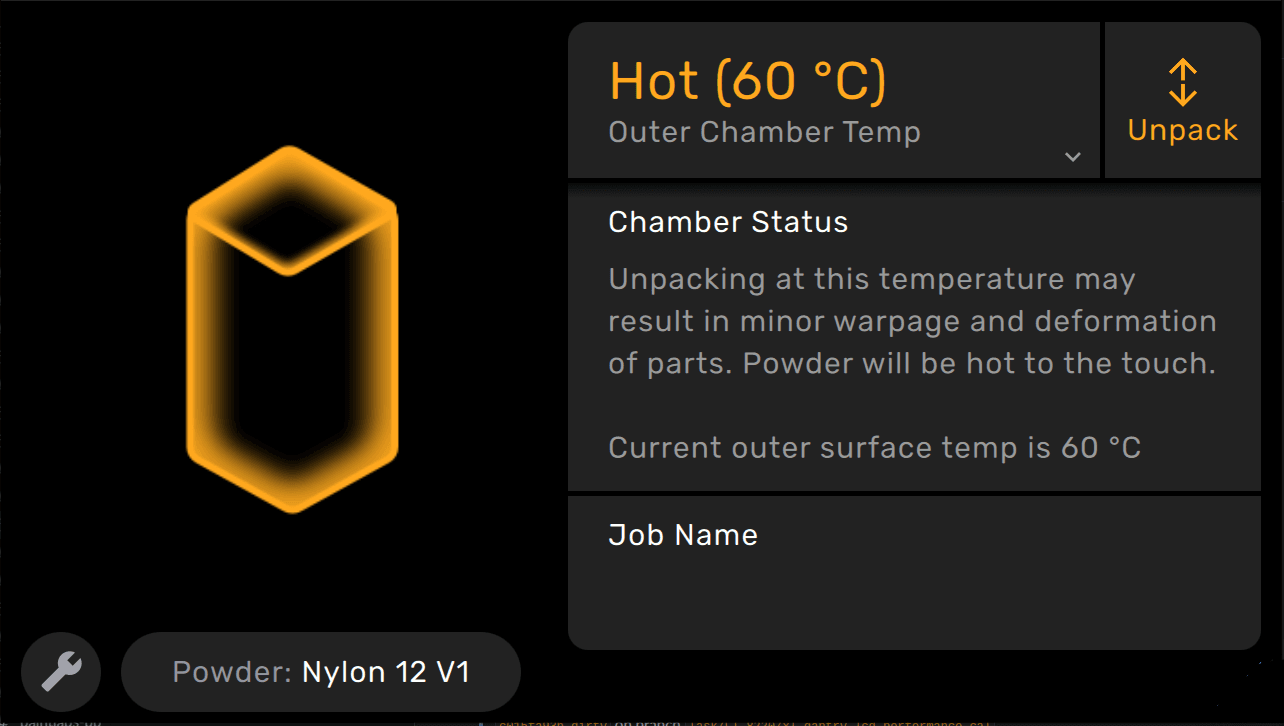
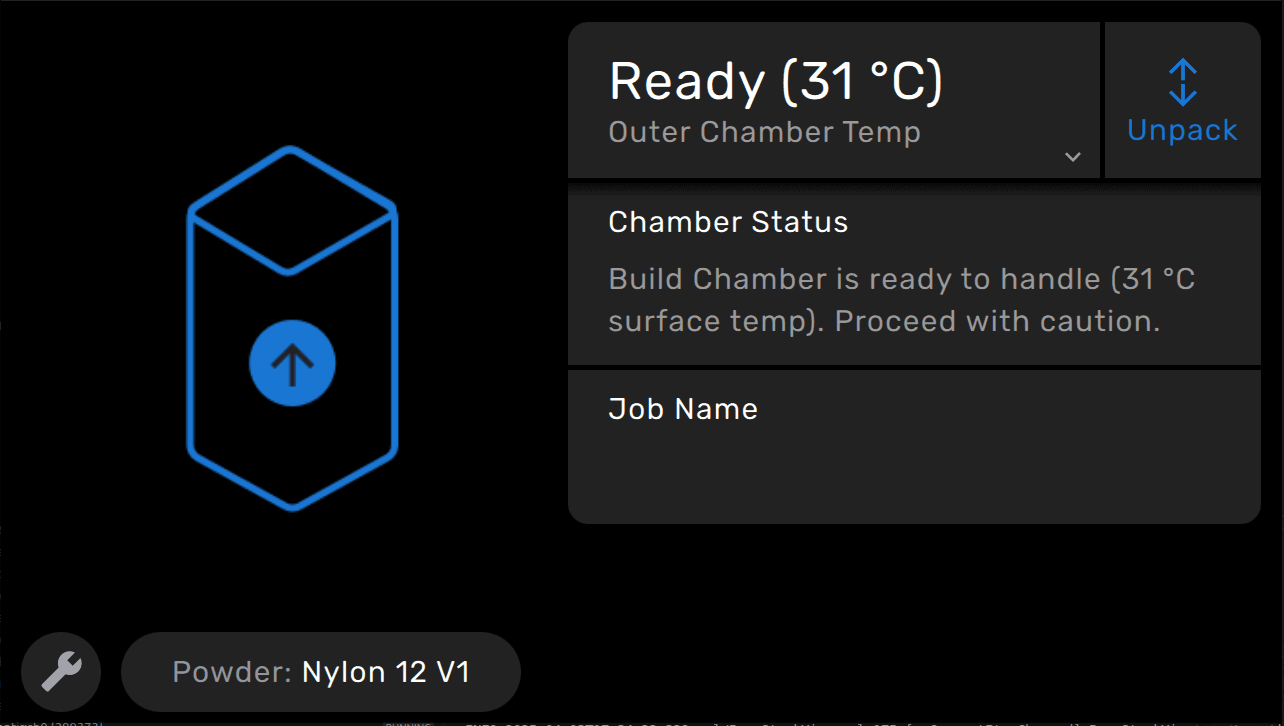
The Fuse Series SLS ecosystem and workflow are designed to deliver industrial-quality, durable parts with consistency and reliability. By providing extra guidance on cooldown times, we hope to make your workflow as efficient as possible, without losing any of your parts' fidelity or repeatability. For questions about your unique builds, cooldown times, or workflows, contact our sales team.