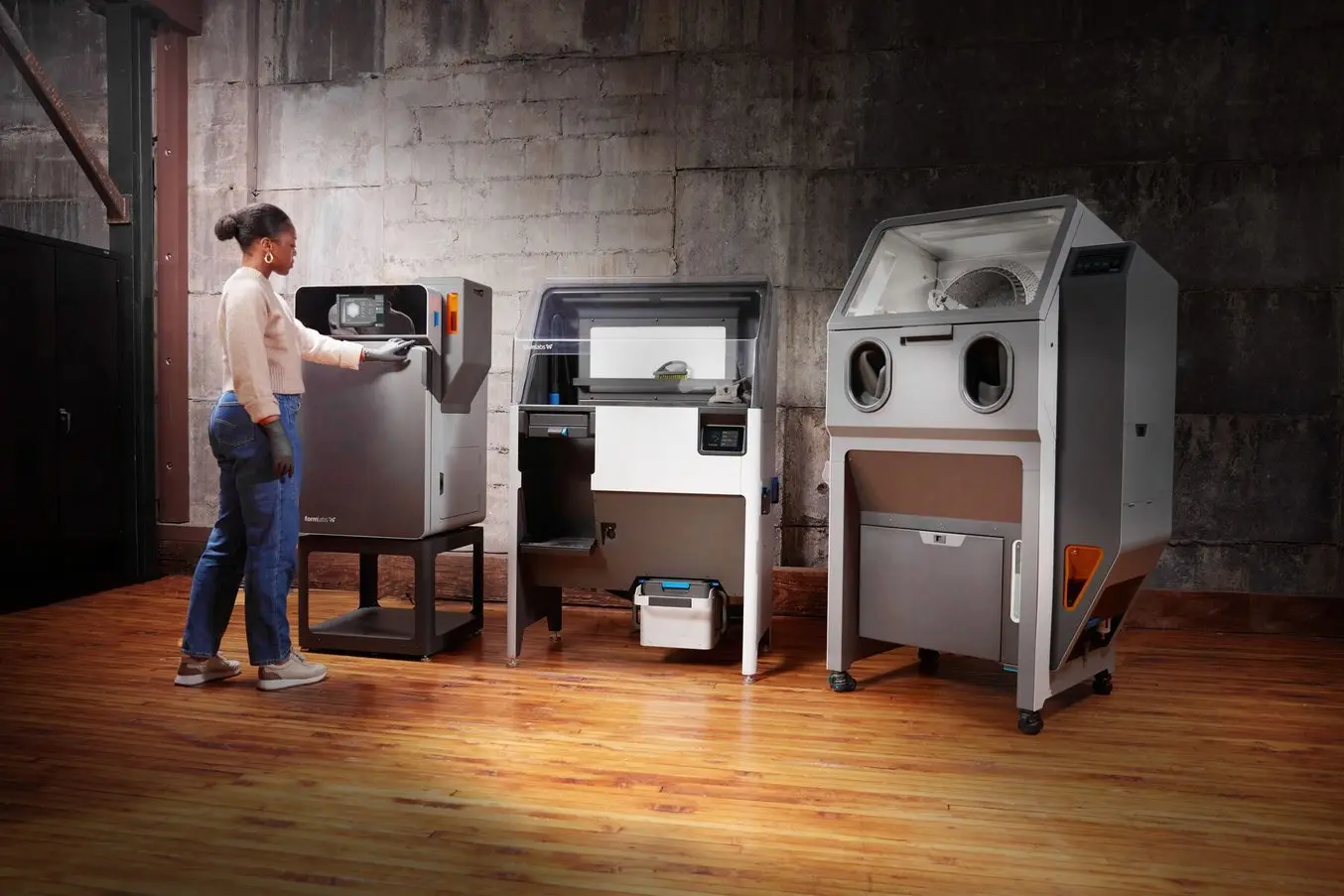
Formlabs’ most recent software update, PreForm 3.34.0, introduces several features that can unlock new printing capabilities for both stereolithography (SLA) and selective laser sintering (SLS) workflows.
With these updates, the Fuse 1+ 30W makes fast, daily production of full builds possible — print speeds are 25% faster than with previous software, and over three times as fast as original Fuse 1 print times. Now, 95% of fully packed Nylon 12 Powder print jobs will be completed in less than 14 hours, and typical builds will finish in just seven hours.
In addition to the 25% speed improvement for the Fuse Series, new build volume parameters for the Form 3 Series increase available height by 4% for desktop and 7% for benchtop SLA, and new workflow updates demonstrate our commitment to continuous improvement for both our powder and resin printing ecosystems.
Constant iteration is not just something that 3D printing enables for our customers, but something that we know is necessary for any successful product, including our own. By listening to and incorporating feedback, Formlabs is working to ensure that our printers are powerful, reliable tools that reflect how real customers are using 3D printing to make their ideas reality.
Fuse 1+ 30W Leads the SLS Category With New Speed Improvements
PreForm 3.34.0 enables a faster, more efficient SLS print process, with print speeds 25% faster than the most recent software update, and twice as fast as all other benchtop SLS printers. SLS customers can spend less time waiting for parts and more time on design, testing, and other high-value tasks.
This software update increases print speed by improving the efficiency of the laser’s scan pattern as it moves across the top layer of powder, sintering particles together into a cross-section of the desired shape.
Previously, the laser approached each section linearly, moving from left to right, stopping, scrolling back, and then starting again in the same motion. Shapes separated by negative space were still sintered in this linear path, but the laser would have to pause as it traveled between segments during each left-to-right movement as well as at the end of each line.
While the laser was stopped, either over negative space or between lines, the print process was paused. Compounding hundreds of thousands of starts and stops for a full build could lead to hours of wasted ‘printing’ time.
With PreForm 3.34.0, laser pathing has been improved — the laser’s path is now optimized for efficiency rather than geometric simplicity. The laser avoids extended pauses and maintains a more continuous ‘up-time,’ making every second of printing more valuable and productive.
As a result of this path planning improvement, files sent to the Fuse are up to 90% smaller than those sent by previous versions of PreForm — making the entire SLS workflow simpler and easier to manage.
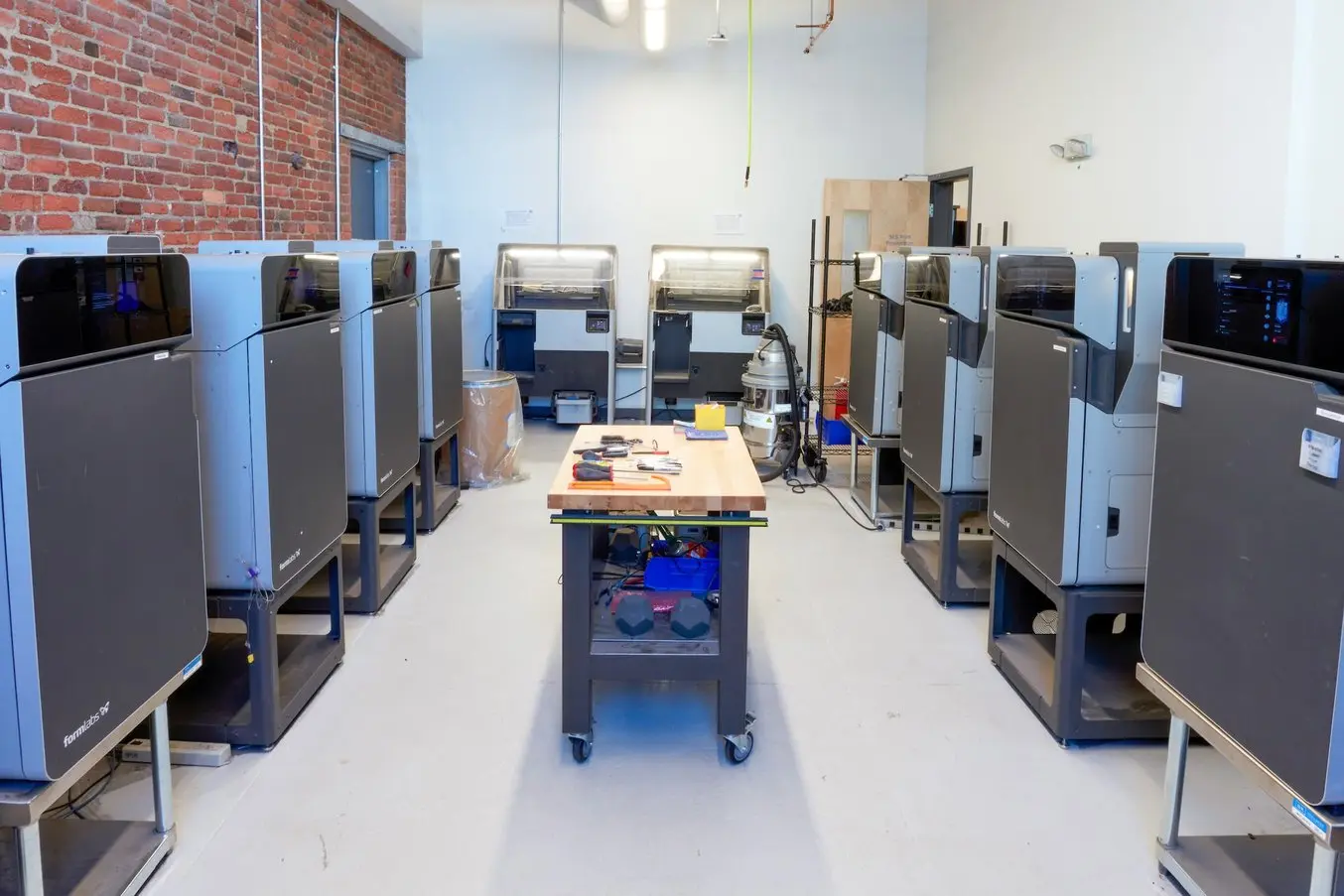
Faster print speeds can help production customers dramatically increase throughput without a commensurate increase in staffing — over 95% of builds with fully packed chambers can be completed in under 14 hours.
Contract manufacturers printing multiple jobs within one build chamber can improve their productivity, shorten lead times, and provide a better experience for their customers. Though industrial, large-format SLS printers may have been the most economical previously, these Fuse Series speed improvements mean that accessible, benchtop SLS printers can more frequently match overall output by printing multiple jobs in the time it takes an industrial machine to print one large batch.
Design teams can work through prototypes more quickly, accomplishing a tighter iterative cycle and delivering better results during the industrial design process. The new print speeds also make a more compelling case for low- to mid-volume production — if manufacturers can increase their weekly output without added labor or materials, 3D printing presents a more competitive case against traditional fabrication methods.
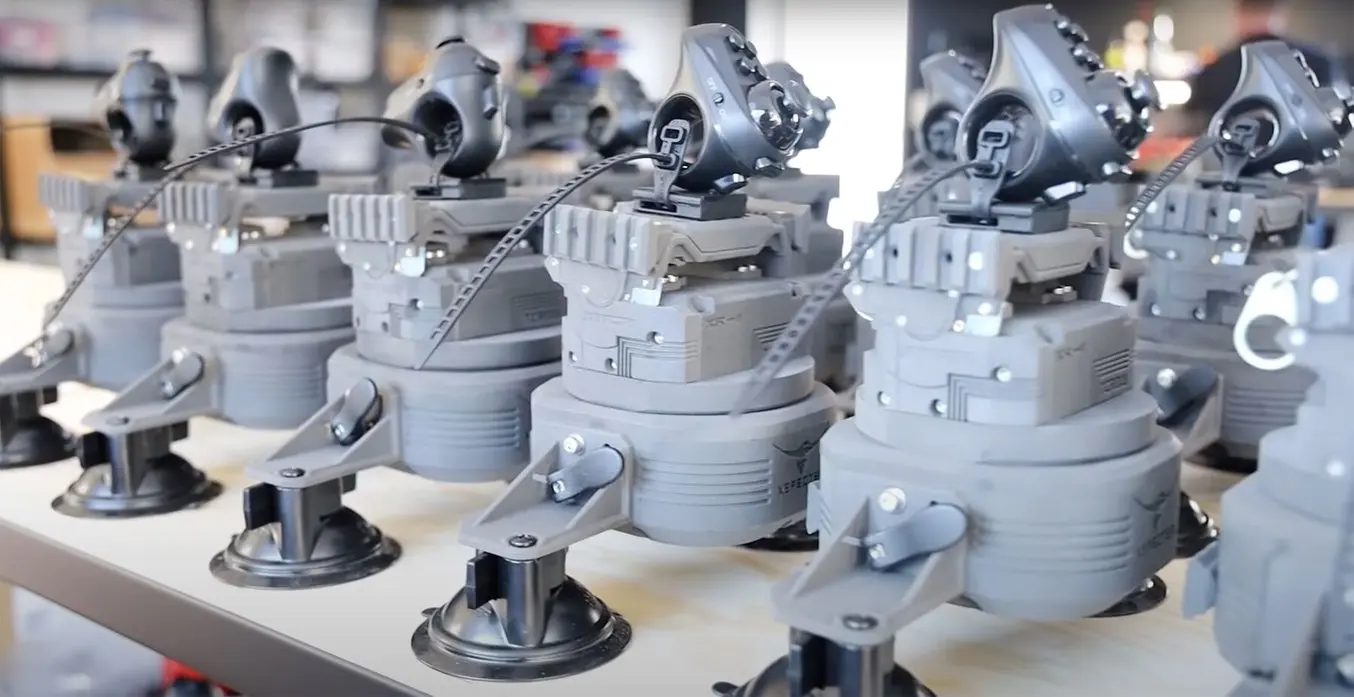
SLS for End-Use Production
3D printing for end-use production is not only possible, it's more affordable, agile, and scalable than ever with the Fuse SLS Ecosystem. Visit our SLS for Production page to compare production methods, learn about bulk powder pricing, and see production in action for 15 different manufacturers currently using the Fuse Series.
Extended SLA Build Volume for Larger Parts
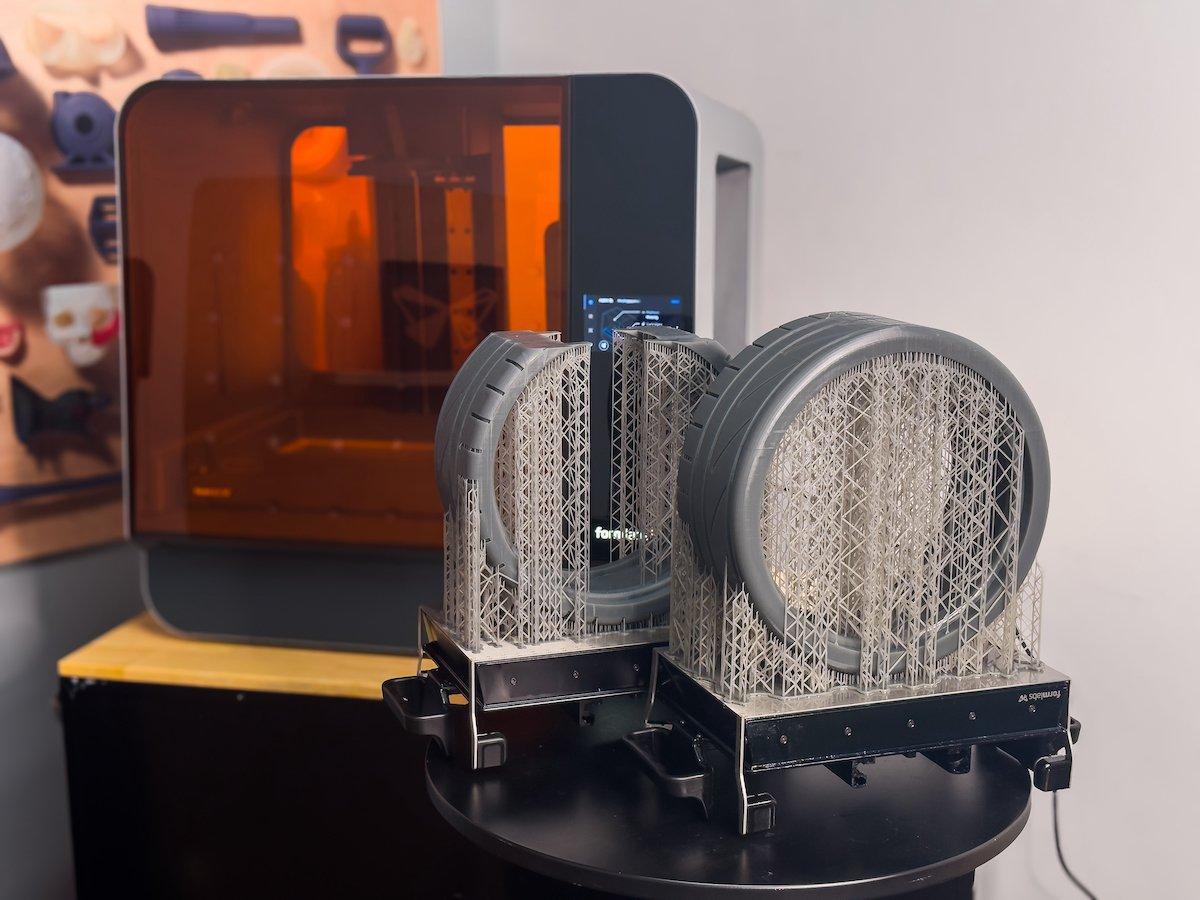
PreForm 3.34.0 enables taller Z-axis heights for both Form 3/B/+ prints and Form 3/B/L prints.
For Formlabs SLA customers, build volume has previously been restricted to ensure that every part could be easily removed from the printer without any chance of the part hitting the resin tank or clipping the edge of the printer. Though this restriction helps limit potential damage to parts, many customers have requested a way to override these protections and create larger parts that take advantage of as much of the build volume as possible.
With these new settings, you can now print up to 4% taller parts on the Form 3/B/+. The available height is now 193 mm compared to the earlier 185 mm. On Form 3L/BL, you can now print up to 7% taller parts. The available height is now 320 mm compared to 300 mm previously.
Previous Maximum Build Height | New Maximum Build Height | Percent Increase | |
---|---|---|---|
Form 3/B/+ | 185 mm | 193 mm | 4% |
Form 3L/3BL | 300 mm | 320 mm | 7% |
It’s important to exercise extra caution while removing tall prints from the printer. Make sure the print does not make contact with the wall of the tank; you may need to remove the tank and print simultaneously for a smooth extraction.
Based on material properties, some resins and print settings are better optimized for tall printing. While tall printing is available for the majority of Formlabs resins, it is not recommended for the following resins when printed in 100 microns:
- Silicone 40A Resin (Form 3/B/+)
- BioMed Amber Resin (Form 3/B/+)
- Surgical Guide Resin (Form 3/B/+)
- Rigid 10K Resin (Form 3L/BL)
Automatic Updates for Windows and Fuse Blast Support
In addition to speed and size improvements, PreForm 3.34.0 makes it easier for Windows users to stay up-to-date with the latest software settings. For Windows users, PreForm will automatically update if the software is open, and will update overnight if not in use. Of course, for customers with validated workflows, we recognize that your process has to stay perfectly consistent: this automatic update feature can be turned off in your PreForm settings.
PreForm 3.34.0 also makes it easier for Fuse Series users to oversee the full SLS ecosystem with Fuse Blast firmware updates and log downloads. Using the Fuse Blast for cleaning SLS prints reduces labor time and cost per part and improves surface quality. Updating to the latest version of PreForm improves oversight and monitoring of the Fuse Blast process.
Continuous Improvement Based on Your Feedback
Formlabs printers, materials, and software are tools that take our customers’ ideas from file to finished part, and tools should always be designed with the end user’s process in mind. By working with our users to understand their unique workflows, we can create products that keep the focus on the results.
The Fuse Series introduced affordable, industrial-quality SLS and, by increasing speed, Fuse Series users can match the output of pricier, traditional powder bed fusion 3D printing systems. By taking the large build volume of the Form 3L even larger, we can answer customers’ need for human-scale parts with an end-use finish.
To get in touch with our experts and discuss the technology and materials that are best suited to your unique workflow, contact our team.