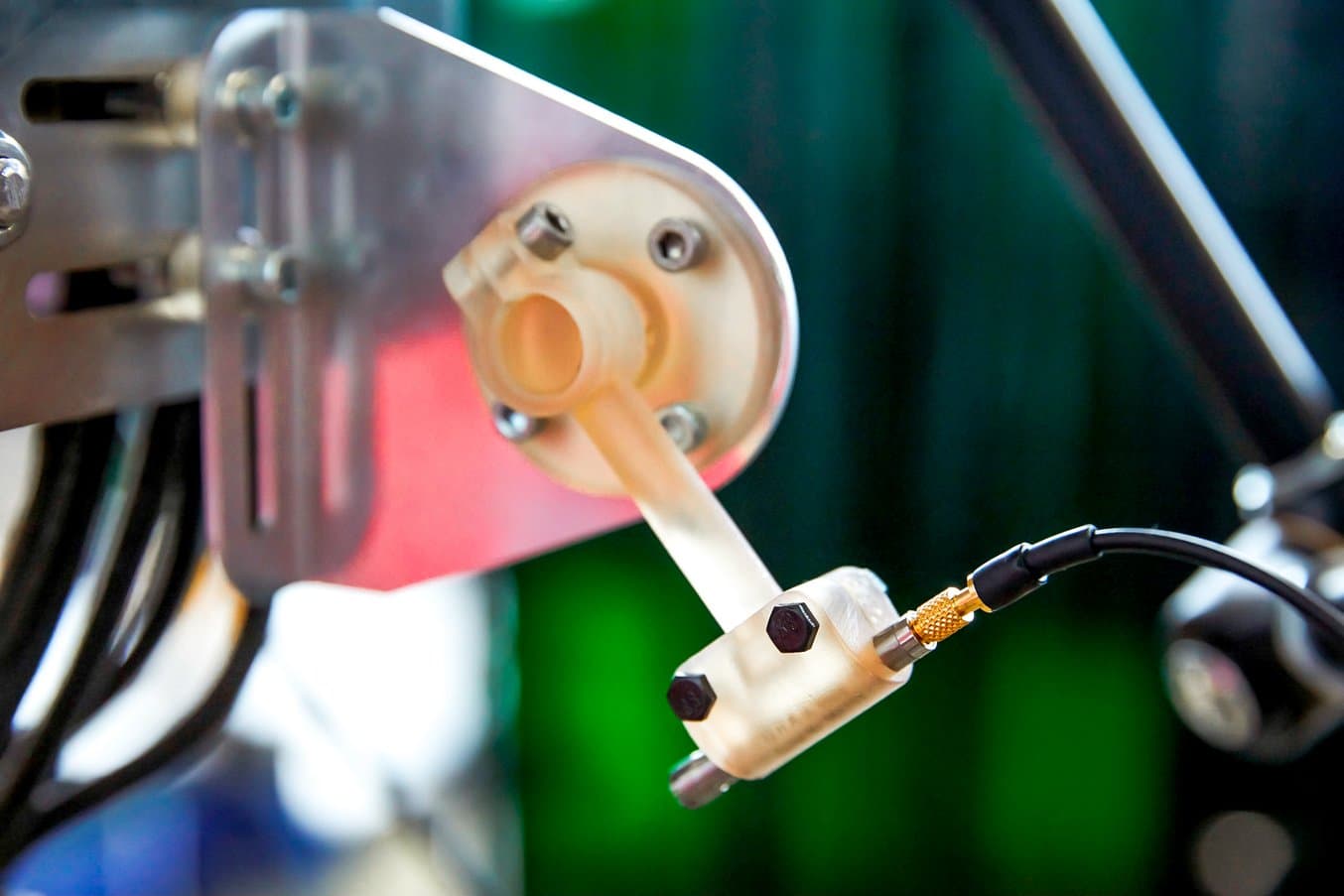
The Nuclear Advanced Manufacturing Research Centre (Nuclear AMRC) is a collaboration of academic and industrial partners from across the nuclear supply chain that conducts research in advanced manufacturing solutions for the civil nuclear industry to help UK manufacturers win work at home and worldwide.
A project the centre has recently worked on aims to develop an autonomous welding solution for the welding of pressure vessels for the nuclear industry. To achieve this, the team had to integrate multiple sensors into the equipment in a hazardous, high-temperature environment.
Learn from Matthew Smart, the projects technical lead at the machining group at Nuclear AMRC, how the team used 3D printing to quickly iterate different designs and produced dozens of parts that withstood the elevated temperatures in close proximity to the welding.
Smart and the research team worked with the AMRC’s open access additive manufacturing station to manufacture the parts they needed. Read our case study to learn how open access to 3D printing can support hundreds of engineers across the site.
Why Welding Vessels Can Take Months in the Nuclear Industry
Current methods for welding pressure vessels require performing frequent hold points for manual inspection that requires cooling down and heating up components multiple times. This results in a lengthy process; welding a large vessel can take months. The Nuclear AMRC’s project aims to cut this lead time by developing an autonomous system that can detect flaws as they happen so the process is only halted if there is an actual flaw.
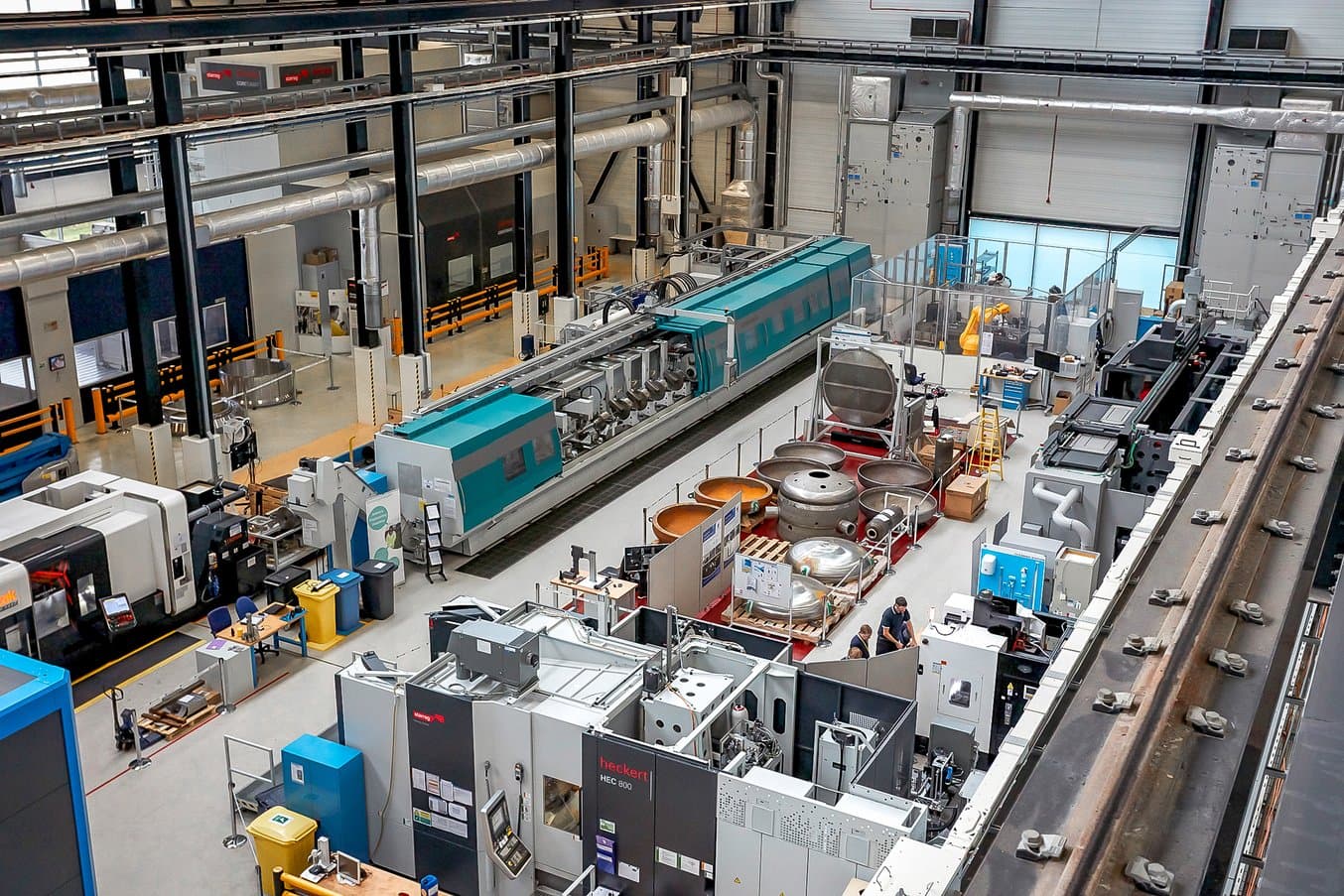
To analyze the welding process in real time, the researchers’ concept integrates a number of different sensors, such as laser scanners, acoustic monitoring, process monitoring for voltage and current, thermal imaging, and a camera system.
“The mechanical integration of all these different sensors is a challenge in this hazardous environment. We need to test different setups and orientations to find out where all the sensors are going to be. But we need to be very flexible in how we test and use the equipment because it's very expensive to book time on this machine,” Smart said.
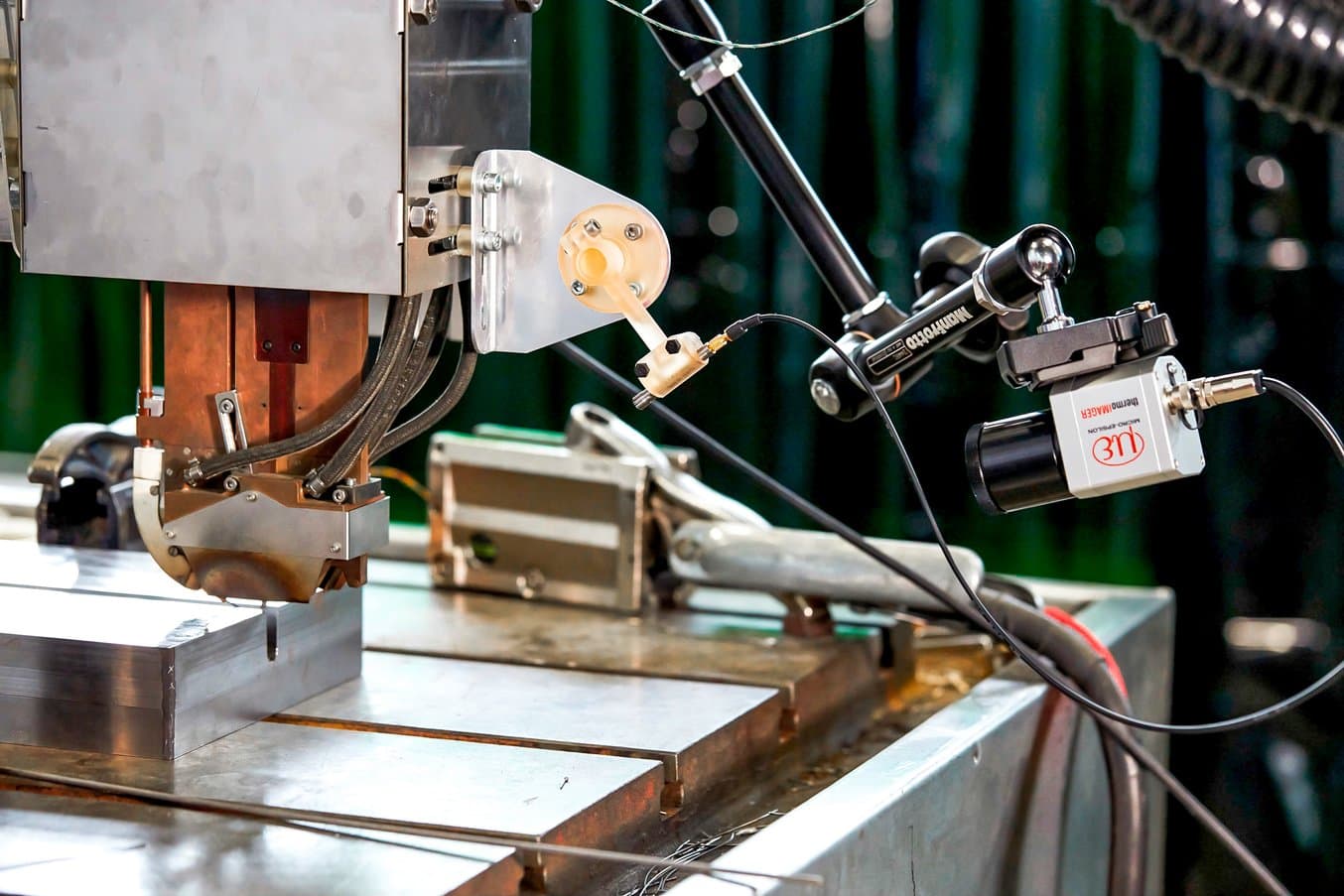
Rapidly Iterating Sensor Configurations and Mounting Strategy With 3D Printing
The current sensor setup contains about a dozen different 3D printed parts, mainly washers that hold brackets together and a mounting system for the acoustic microphones. All of these parts have to be able to withstand the elevated temperatures in close proximity to the welding.
Formlabs High Temp Resin offers a heat deflection temperature (HDT) of 238 °C @ 0.45 MPa, making it ideal for parts that require high temperature resistance.
“If we had to make these parts through a traditional method, we would have had to be a lot more arduous in the design process in terms of capturing the requirements and fully locking down all of the exact tolerances before we fabricated the parts. Being able to 3D print the brackets means that we can go by a bit of trial and error, print multiple versions with different tolerances and test different orientations and sizes. It means that we can be a lot more innovative and test things much more quickly,” Smart said.
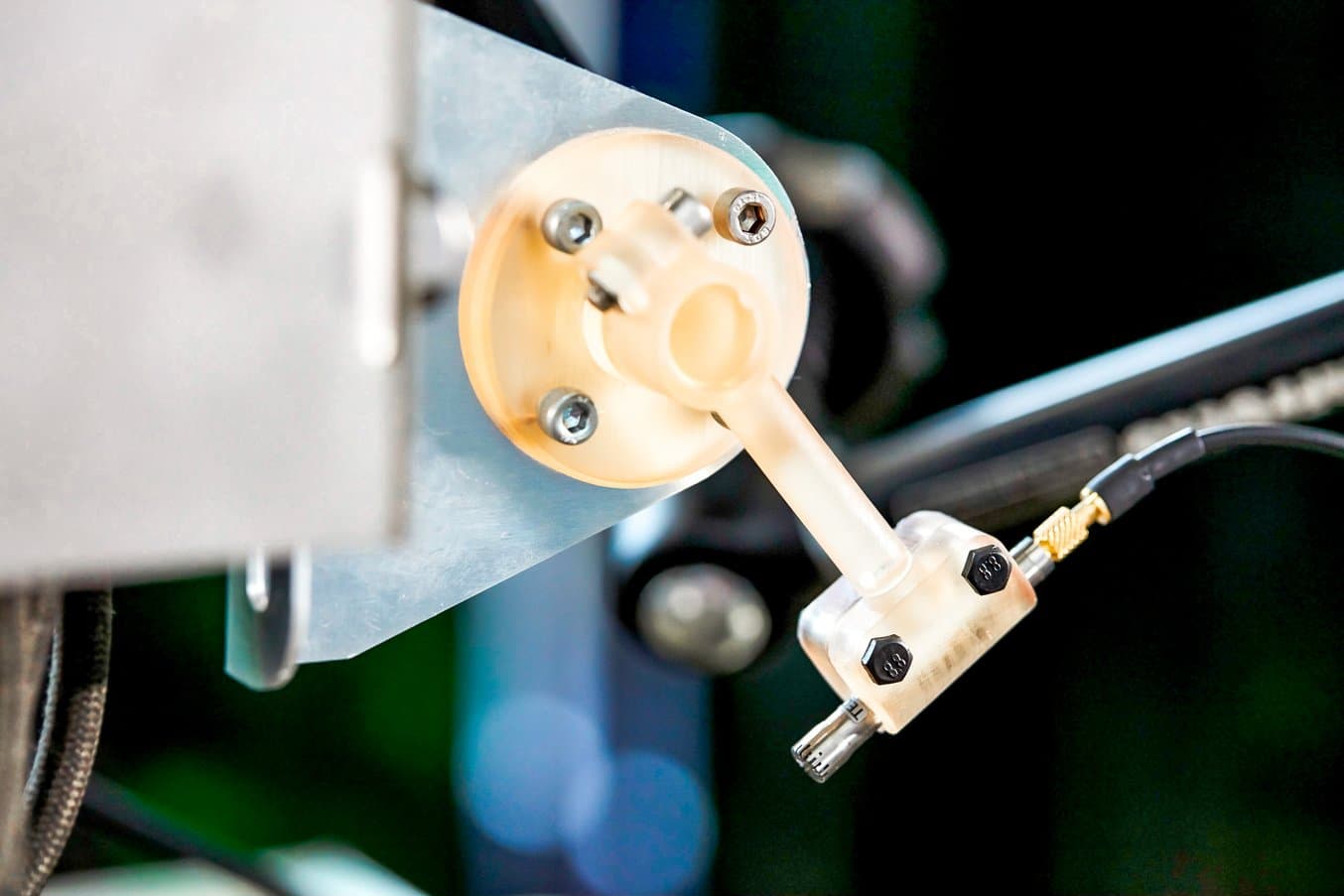
Being able to use 3D printing to rapidly test the different sensor configurations and mounting strategy let the team be very versatile and significantly reduced cost and time to get the parts fabricated.
“We would be talking about days of engineering time to get all the paperwork, sort the material, do design work, and subcontract a company, versus a couple of hours on a CAD program and then the cost of the plastic. It's fractional compared to doing it traditionally,” Smart said.
“You can't really quantify the agility of it, because it just lets you test and iterate much more. Let’s say if you sent a design for fabrication and it wasn't fit for purpose, you'd have to go through that again, so we'd be talking about weeks to go from testing one prototype to another. With 3D printing, it's two days. The pace of innovation is unquantifiable.”
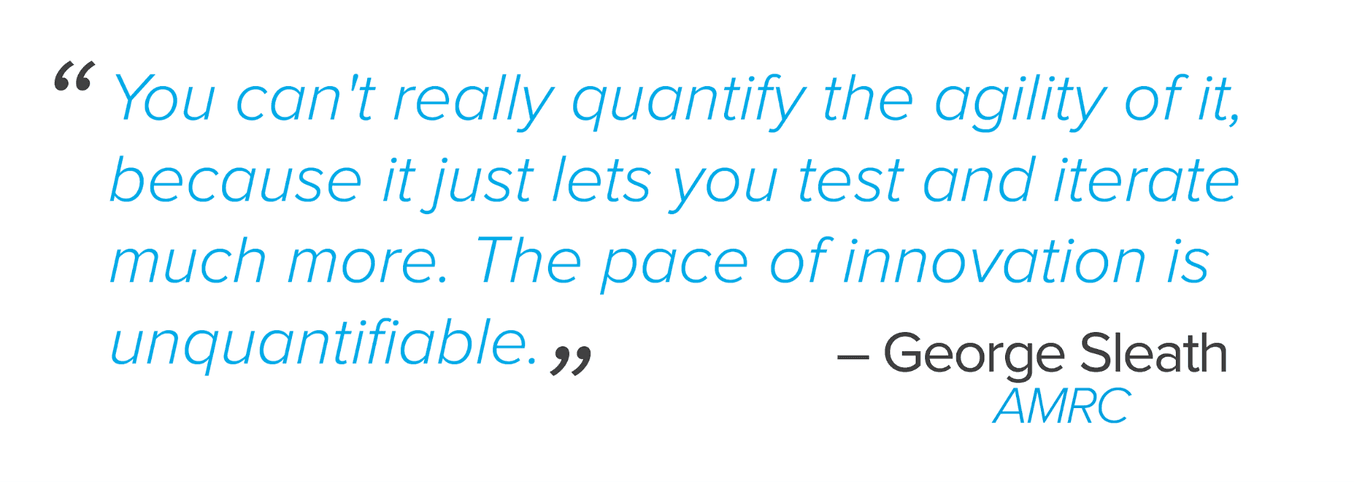
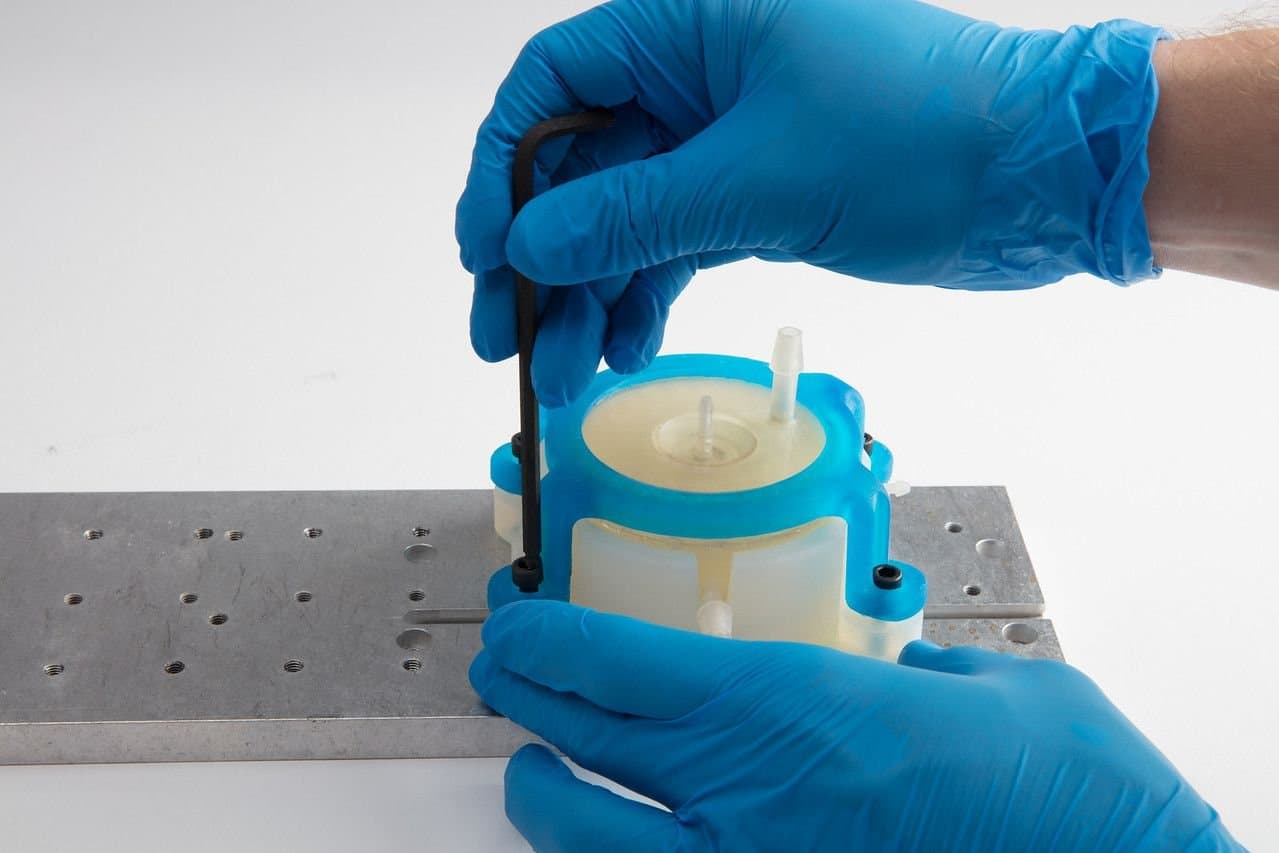
Designing Jigs & Fixtures with 3D Printing
Download our white paper to learn how to reduce costs, shorten development time, and create more optimized production workflows with 3D printed jigs and fixtures.
Download White Paper
Using an Internal 3D Printing Station to Cut Lead Time
Smart worked with the Design and Prototyping Group at the AMRC to produce the 3D printed parts. The group recently installed a new additive manufacturing station with a fleet of 12 Form 2 stereolithography (SLA) 3D printers that provides open access to 3D printing to all engineers across the site.
“We work quite closely with the design group. They've been very forward in getting us involved and showing us what's achievable and available in terms of the equipment and how you can optimize the design to make it a quick and easy build with the 3D printers. Having that accessibility and knowledge of the capability is vital to be able to use it within the research group,” Smart said.
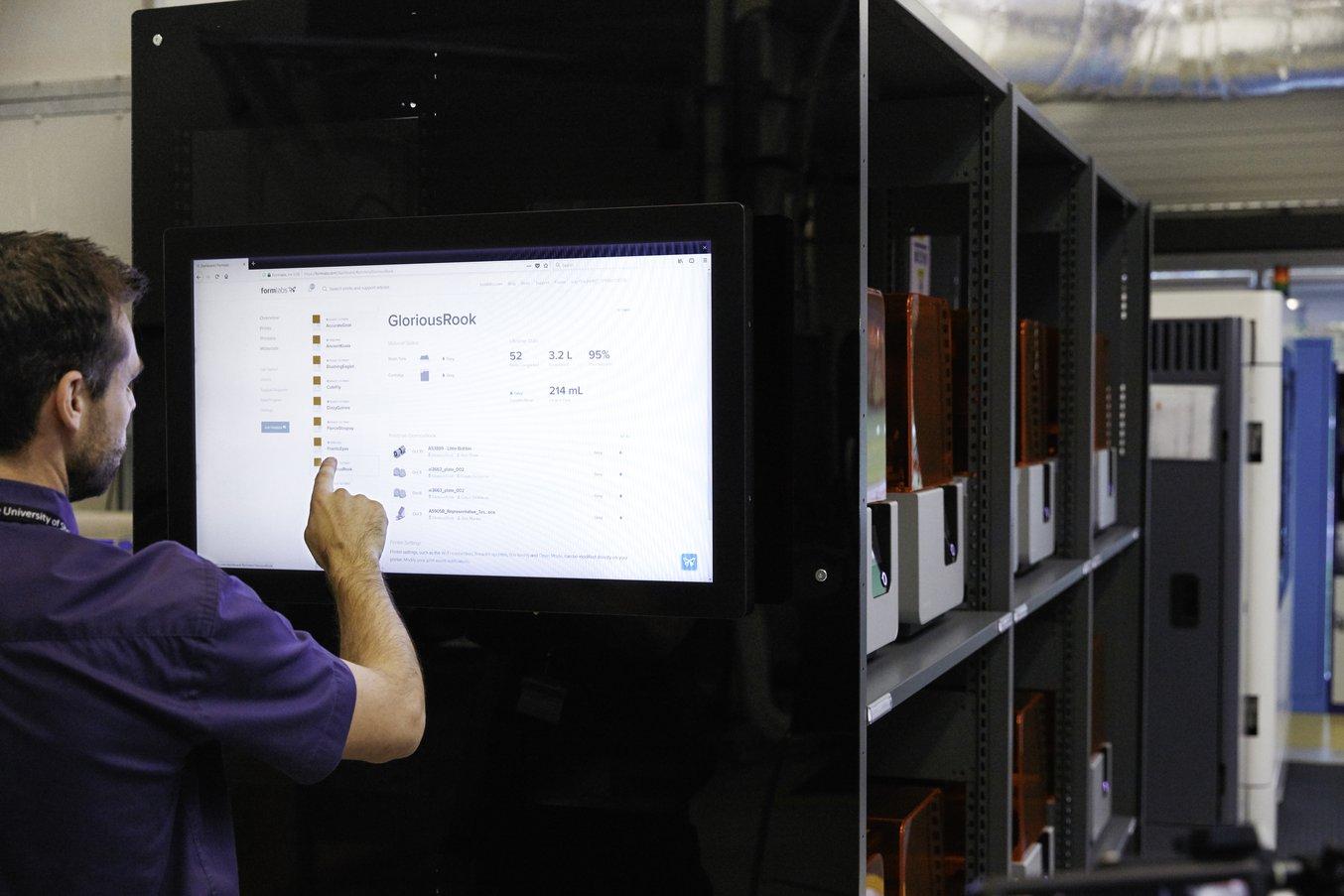
“If there wasn't [a 3D printing station], I would have been aware of the technology, but I wouldn't have known anything about the capabilities and how you go about designing something for us to manufacture. I've actually been trained on some of the machines, and being able to have free access to send components down there to be made is incredibly useful,” Smart said.
Explore How a 3D Printing Station Supports Hundreds of Engineers at AMRC
Learn about the 3D printing station at the AMRC and see other applications like batch 3D printing of 500 high-precision drilling caps for drilling trials for Airbus, highly intricate brackets for a robot gripper in composites manufacturing, and custom filament winding rollers for composites manufacturing.
Want to learn more about the printers and technology behind the AMRC’s 3D printing station? Explore Formlabs latest SLA 3D printers, the Form 3 and the large resin printer Form 3L, and Formlabs collection of engineering resins for your own project, or request a free sample 3D printed part to see materials firsthand.