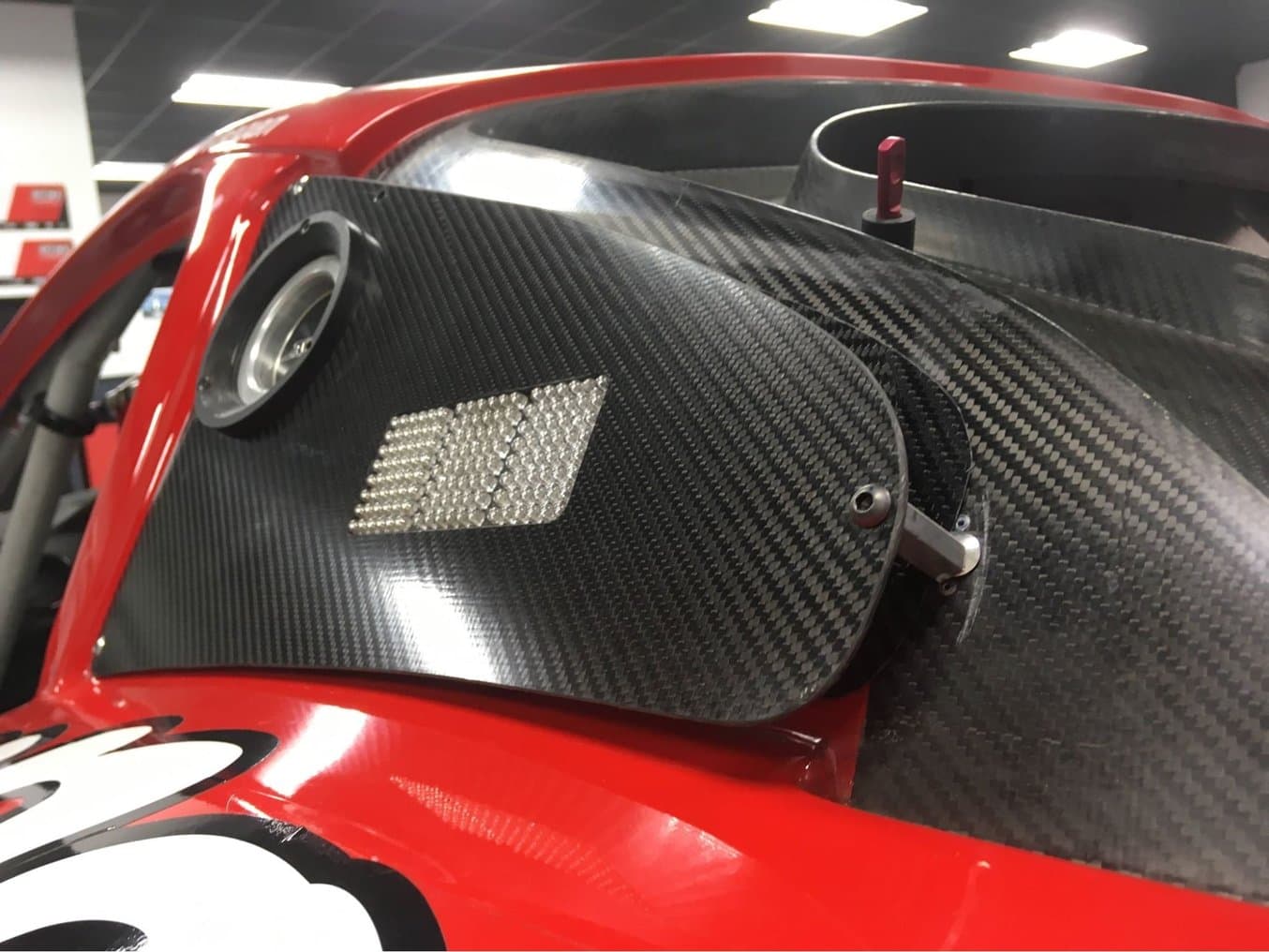
複合材料、特に炭素繊維強化プラスチックは、その高い汎用性と効率性から、航空宇宙から医療まで様々な市場でイノベーションを促進しています。この材料はスチール、アルミニウム、木材、樹脂などの従来の材料を上回る性能を持ち、高性能で軽量な製品の製造を可能にします。
このガイドでは、炭素繊維部品の製造の基本、様々な炭素繊維のレイアップ、ラミネート、成形方法、そして3Dプリントの活用でコストと時間を削減しながら炭素繊維の成形型を作成する方法について解説します。
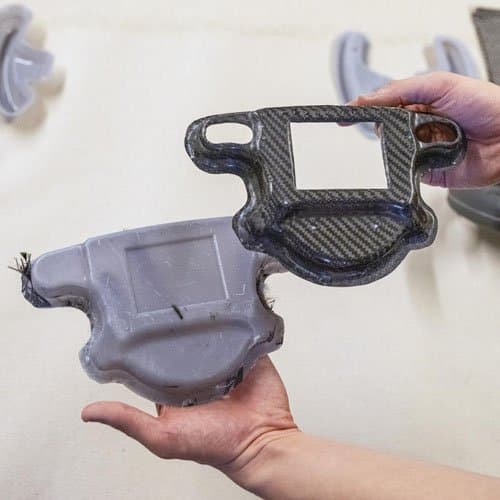
3Dプリント製の型で炭素繊維製パーツを製作
本技術資料では、複合材料を使用した成形型の設計ガイドラインや、炭素繊維部品の製造に必要なプリプレグや手作業によるラミネート成形について、手順ごとに詳しく解説しています。
複合材料の基礎知識
複合材料とは、2つ以上の成分を組み合わせ、それぞれの単独成分とは異なる特性を持つ材料のことです。通常、強度、効率性、耐久性などのエンジニアリング特性が向上します。複合材料は、強化材(繊維や粒子)と、それらを結合するマトリックス(ポリマー、金属、セラミック)で構成されます。
現在、繊維強化プラスチック(FRP)が市場を支配し、様々な業界で新たな活用法が次々と出てきています。その中でも、炭素繊維はアルミニウムの3倍以上の強度と剛性を持ちながら40%軽量であるため、航空機、レーシングカー、自転車などで広く使用されています。強化炭素繊維をエポキシ樹脂で結合することで構成されます。
繊維を一方向に配置して特定の方向の強度を高めたり、クロス織りして複数方向の強度を持たせたりすることが可能なほか、クロス織りで複合部品の特徴的なキルティング模様を生み出すこともできます。両方を組み合わせて部品を製造することも一般的です。利用可能な繊維の種類は以下の通りです。
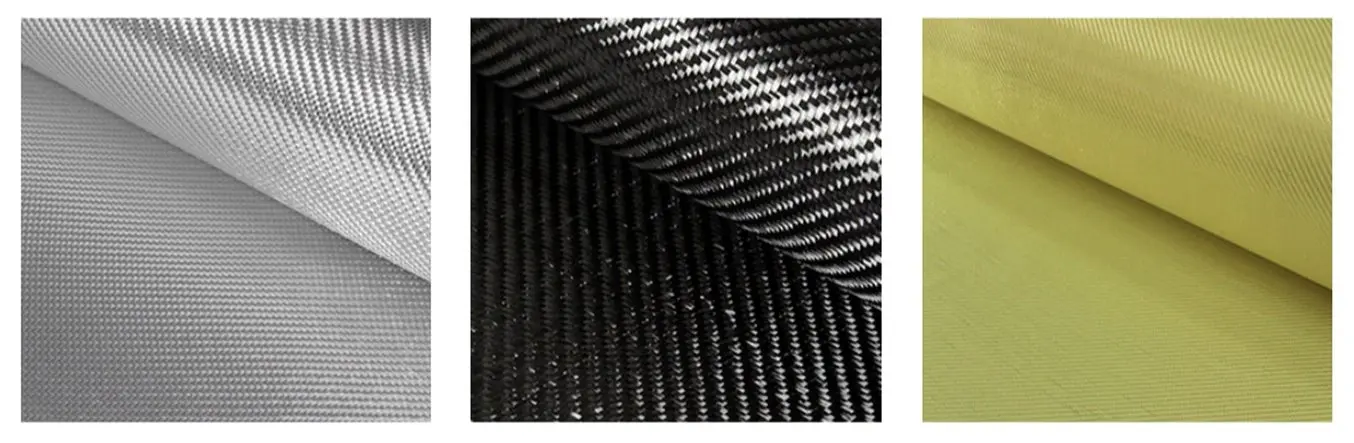
ガラス繊維 | 炭素繊維 | アラミド繊維(ケブラー) |
---|---|---|
最も一般的な繊維 軽量で、適度な引張・圧縮強度 低コストで加工が容易 | 業界最高の強度・剛性(比強度、比剛性) 他の繊維より高価 | 炭素繊維より高い耐衝撃性・耐摩耗性 低い圧縮強度 切断や加工が難しい |
繊維を結合して硬質の複合材料を作るためには、樹脂が使用されます。数百種類の樹脂が使用可能ですが、最も一般的なものは以下の通りです。
樹脂 | 長所 | 短所 | 二次硬化 |
---|---|---|---|
エポキシ | 最高の最終強度 最軽量 最長の保存期間 | 最も高価 混合比や温度変化に敏感 | 特定の硬化剤が必要(二成分系) エポキシの種類により加熱が必要な場合あり |
ポリエステル | 使いやすい(最も一般的) 紫外線への耐性あり 最も低コスト | 強度と耐腐食性が低い | 触媒(MEKP)で硬化 |
ビニールエステル | エポキシの性能とポリエステルのコストを併せ持つ 最高の耐腐食性、耐熱性、伸び率 | エポキシより強度が低く、ポリエステルよりコストが高い 保存期間が短い | 触媒(MEKP)で硬化 |
炭素繊維部品を製造する3つの方法
炭素繊維部品など、繊維強化プラスチックの製造はスキルと労力を要するプロセスで、一品ものからバッチ生産まで幅広く行われています。サイクルタイムは部品のサイズと複雑さに応じて1時間〜150時間です。通常、連続した繊維をマトリックスで結合して個々のプライを形成し、それらを層ごとに積層して最終的な部品を製作します。
複合材の特性はラミネート過程のみでなく使用する材料によっても変わり、繊維を取り込む方法が部品の性能に大きく影響します。熱硬化性樹脂は、補強材とともに成形型や金型で形作られ、硬化して頑丈な製品となります。様々な積層技術がありますが、主に以下の3つに分類できます。
1. ウェットレイアップ
ウェットレイアップでは、繊維をカットして金型に敷き、その上からブラシ、ローラー、スプレーガンで樹脂を密着させます。この方法は高品質な部品を作るためには最も技術力が必要になりますが、DIYで炭素繊維部品を作るのに最もコストが低く、始めやすい方法です。炭素繊維部品の製造に初めて取り組む場合や設備が整っていない場合は、手作業によるウェットレイアップから始めることをお勧めします。
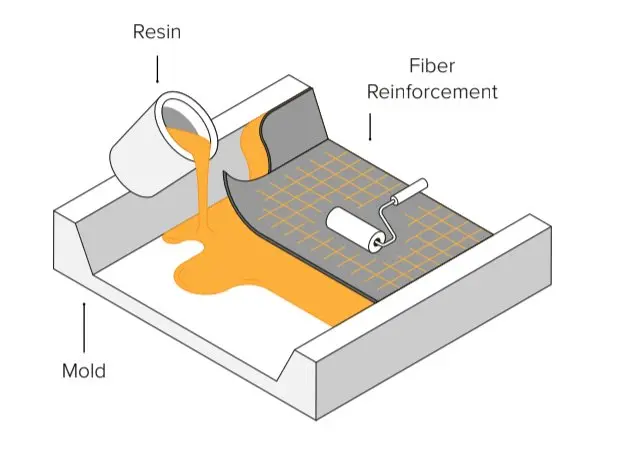
上の動画では、炭素繊維のウェットレイアップ成形の工程を紹介。
2.プリプレグ積層
プリプレグ積層では、樹脂があらかじめ繊維に含浸された状態でプリプレグシートとして硬化を防ぐために冷蔵保存されています。その後、オートクレーブ内で熱と圧力をかけてプライを金型内で硬化させます。樹脂の量が制御されているためより正確で再現性の高いプロセスですが、最も高価な技術であり、高性能な用途で使用されます。
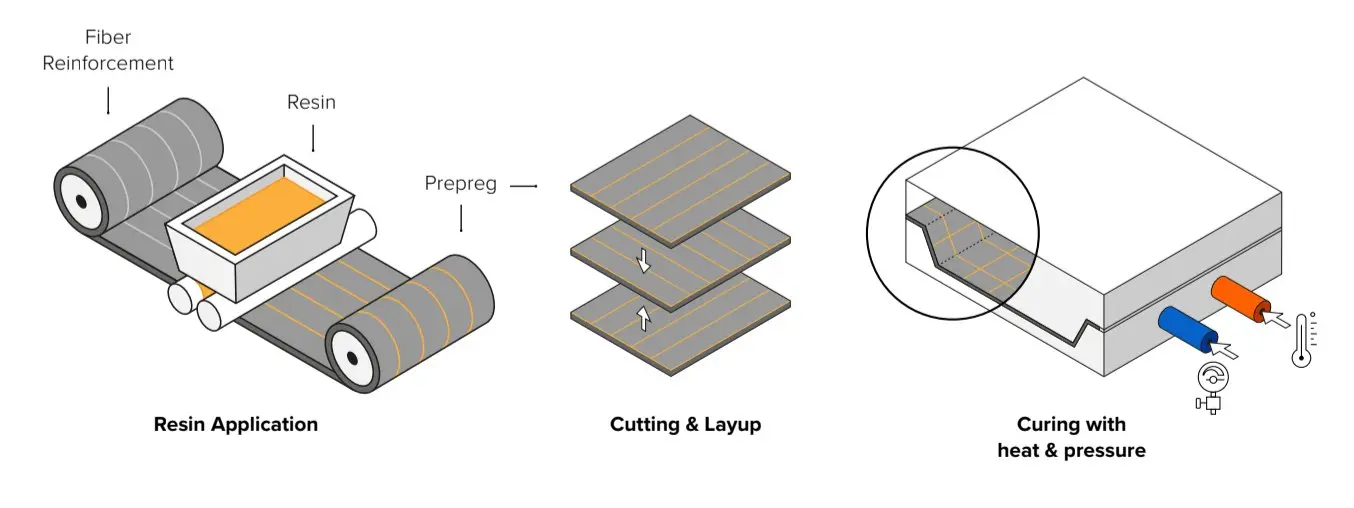
3. レジントランスファーモールディング(RTM)
RTMでは、乾燥した繊維を二つ割の金型の中に入れ、その後金型をクランプで閉じ、高圧をかけて樹脂をキャビティ内に押し当てます。工程が自動化されていることが一般的で、大量生産に使用されます。
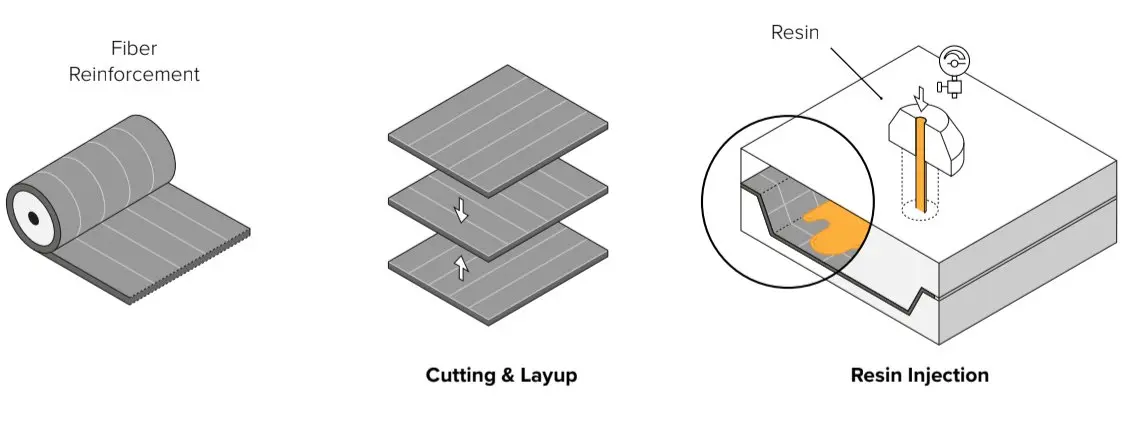
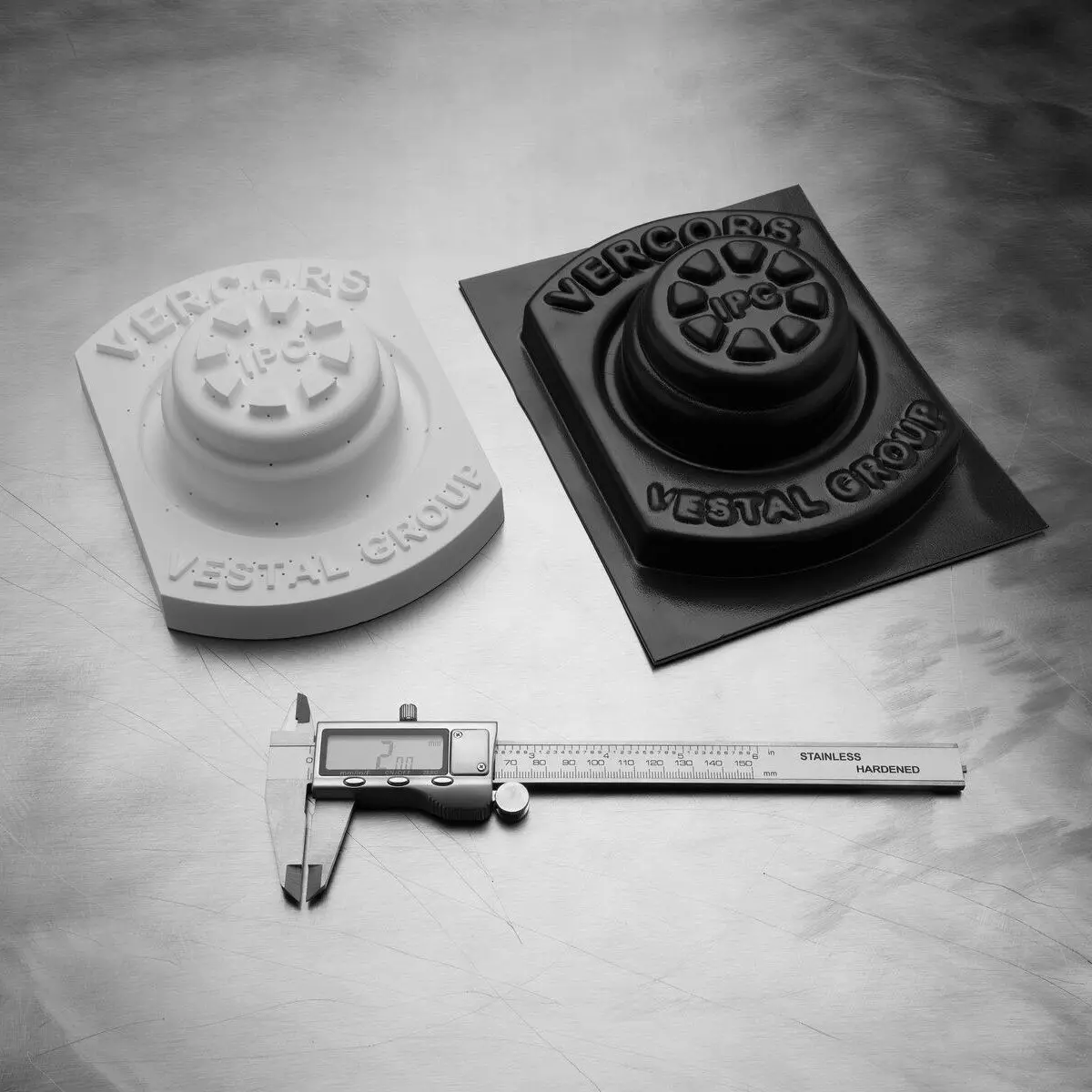
3Dプリント製の型を使用した少量高速熱成形
こちらの技術資料では、3Dプリントで複雑な成形型を短時間で製作する方法や、成形型を製作する際に参考になるヒントやガイドラインをご紹介しています。ダウンロードしてご覧ください。
3Dプリント製の型で炭素繊維部品を製造する
成形型の品質は最終的な製品の品質に直接影響するため、FRP製品の製造において成形型の製作プロセスが非常に重要なポイントになります。成形型の多くはワックス、フォーム、木材、プラスチック、金属を使用してCNC加工または手作業で製作されています。手作業で製作する場合は非常に労力がかかりますが、CNC加工も複雑で時間のかかる工程を必要とし、特に複雑な形状の場合はその傾向が強くなります。一方、外部委託は高コストで製作期間も長くなりがちです。どちらの方法も熟練の技術者を必要とし、デザインの試作・検証や成形型の細かな調整を柔軟に行うことができません。
アディティブマニュファクチャリングは、炭素繊維部品用の成形型や原型を迅速かつ低コストで製作するソリューションとなります。製造プロセスにおけるポリマー型の使用は増加し続けています。金型を内製のプラスチック型に置き換えることで成形型の製作期間を短縮し、設計の柔軟性も高まる強力でコスト効率の高い手段となります。エンジニアは、フィラメントワインディングや繊維の自動配置などをサポートする治具や固定具の製作に、ポリマーレジンを使用した3Dプリント品を活用しています。同様に、短時間でプリントした成形型やダイを使って、射出成形、熱成形、シートメタル成形などによる少量バッチの生産が行われています。
社内導入可能なデスクトップサイズの3Dプリントは必要な設備が少なく、ワークフローの複雑さが軽減されます。Form 3+のような工業品質のデスクトップサイズ光造形3Dプリンタは価格も手頃で導入が容易、かつ需要に応じて生産規模を迅速にスケールアップできます。Form 3Lのような大容量の3Dプリンタを使用すれば、大型の成形型や治具の製作も可能です。
SLA光造形方式3Dプリントは、炭素繊維のレイアップ成形型に不可欠な、非常に滑らかな表面仕上げや高精度で複雑な形状も実現できます。さらに、Formlabsのレジンライブラリには成形型や原型の製作に適した機械的・熱的特性を備えたエンジニアリング系材料が豊富に揃っています。
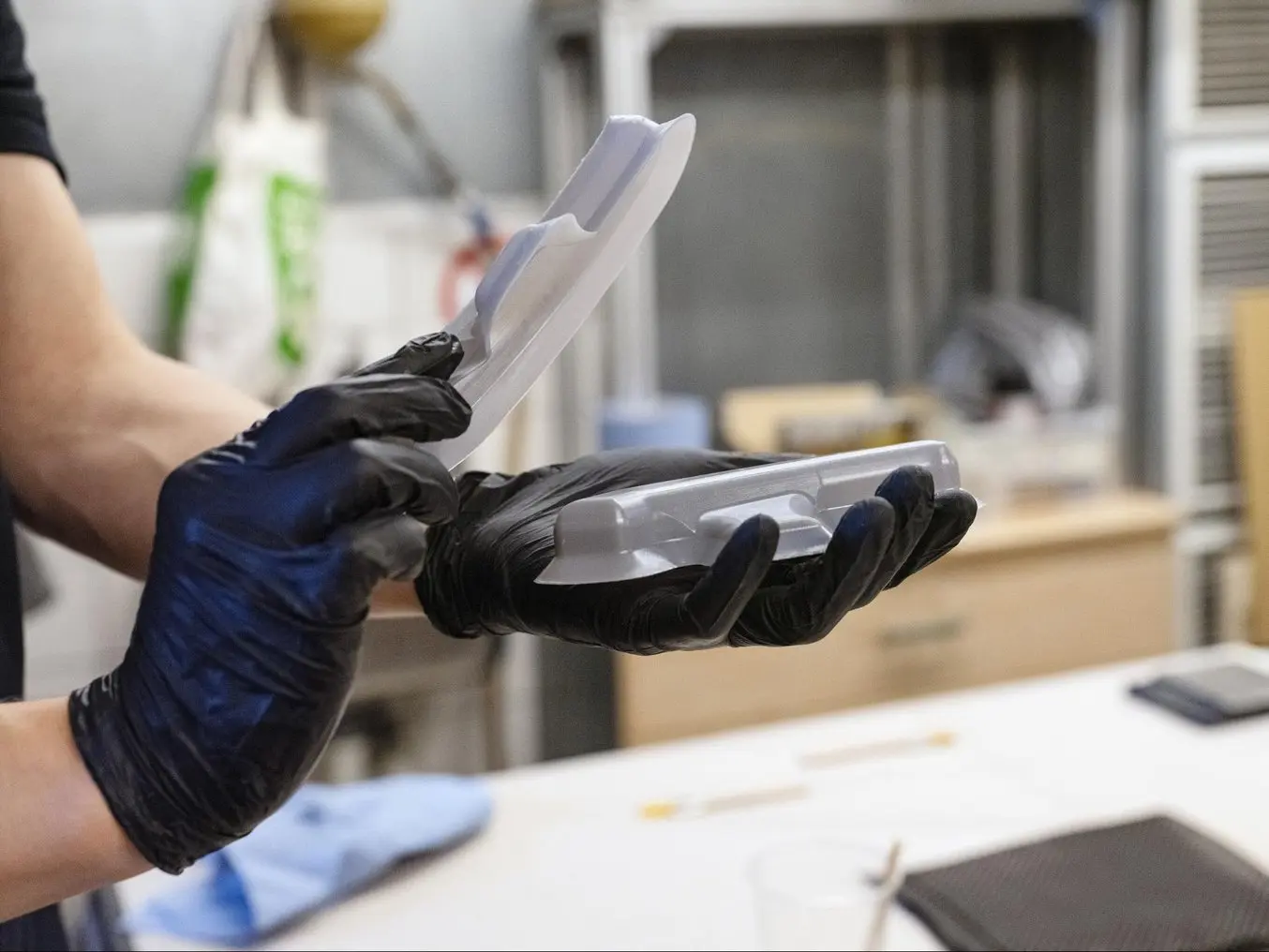
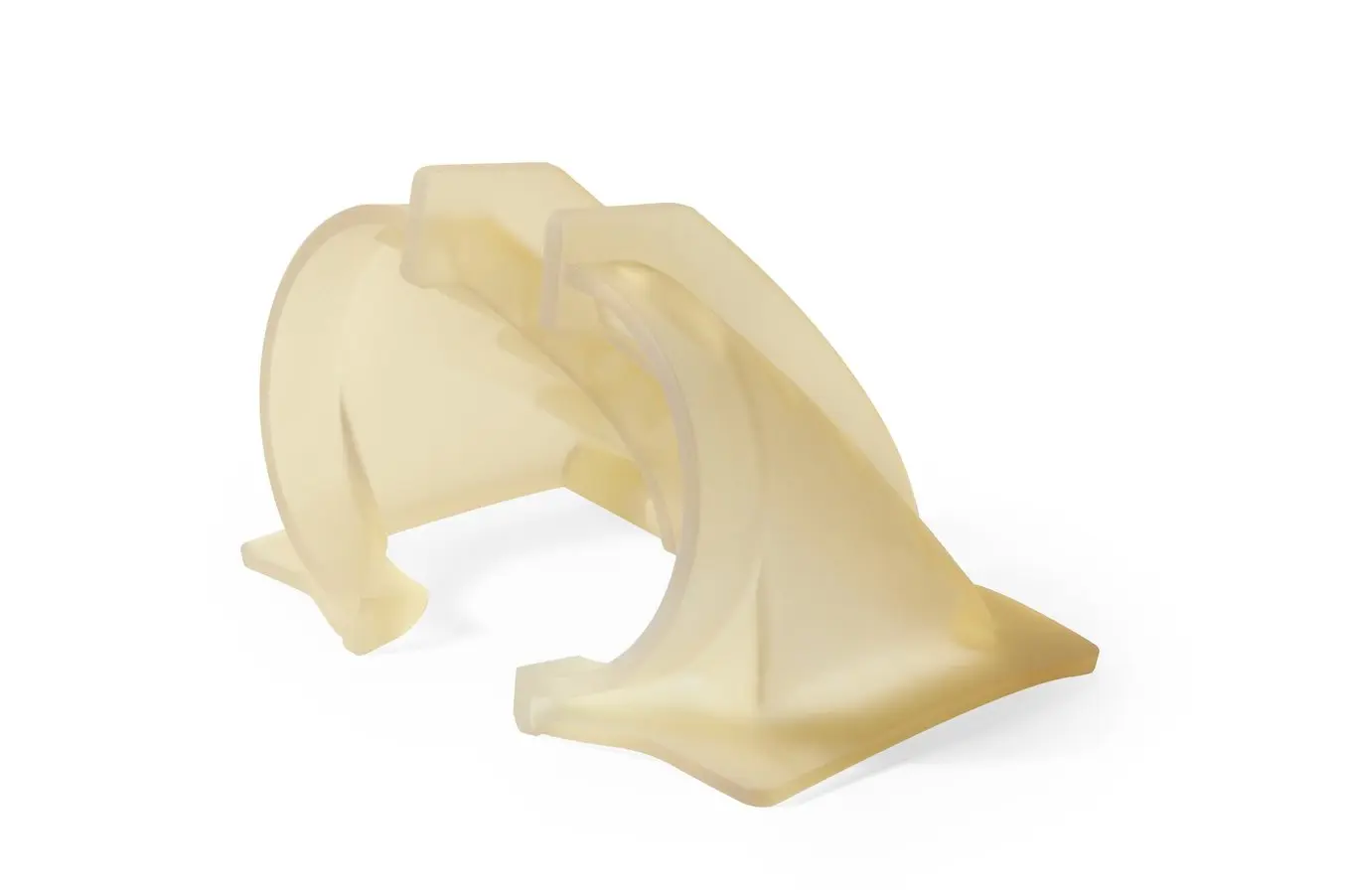
3Dプリント製の成形型を使用して炭素繊維部品を製造することで、コストを削減し、製作期間も短縮できます。
小規模生産の場合は、エンジニアは成形型を低コストで数時間以内に直接3Dプリントできます。手作業で材料を掘り出したり、CNC加工機やCAMソフトウェアの取り扱い、機械のセットアップ、ワークの固定、切削、切りくずの除去などが必要ありません。成形型の製作にかかる作業量と製作期間が大幅に削減されることで、デザインの試作・検証を迅速に繰り返したり、部品のカスタマイズが可能になります。また、従来の方法では製造が困難だった繊細なディテールを持つ複雑な成形型も製作できます。
TU Berlinのフォーミュラ・スチューデントチーム(FaSTTUBe)は、レーシングカー用に多数の炭素繊維部品を製作しました。チームのエンジニアたちは、FormlabsのTough 1500レジンで直接プリントした成形型を使ってハンドラミネート成形を行いました。このレジンは引張弾性率1.5 GPa、破断伸び51%という特徴を備えており、レイアップ中に十分な強度とサポート力を持つだけでなく、硬化後に部品を成形型から分離するのに十分な柔軟性も備えています。
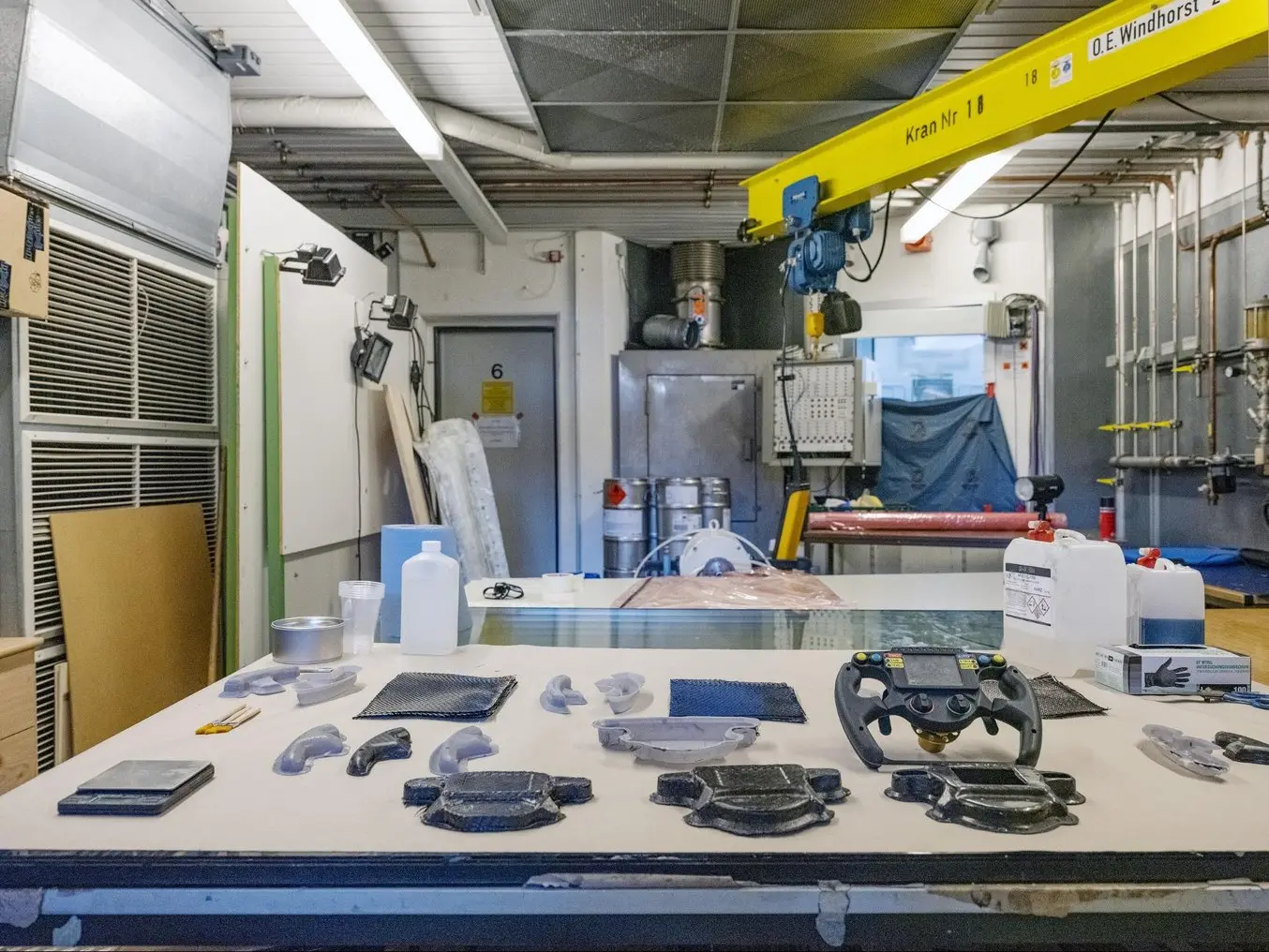
FaSTTUBeの炭素繊維部品の製作用セットアップ。
この技術には過酷な硬化条件が必要ないものの、他のラミネート成形プロセスでは高温・高圧が必要になる場合があります。DeltaWing Manufacturingは、High Tempレジンを使用してプリプレグ成形でエアフローコンポーネントを製造しています。High Tempレジンは荷重たわみ温度(HDT)が238°[email protected]と、オートクレーブの熱と圧力に耐えることができます。DeltaWing Manufacturingは成形型を直接3Dプリントし、約10種類のカスタム部品を製造しています。
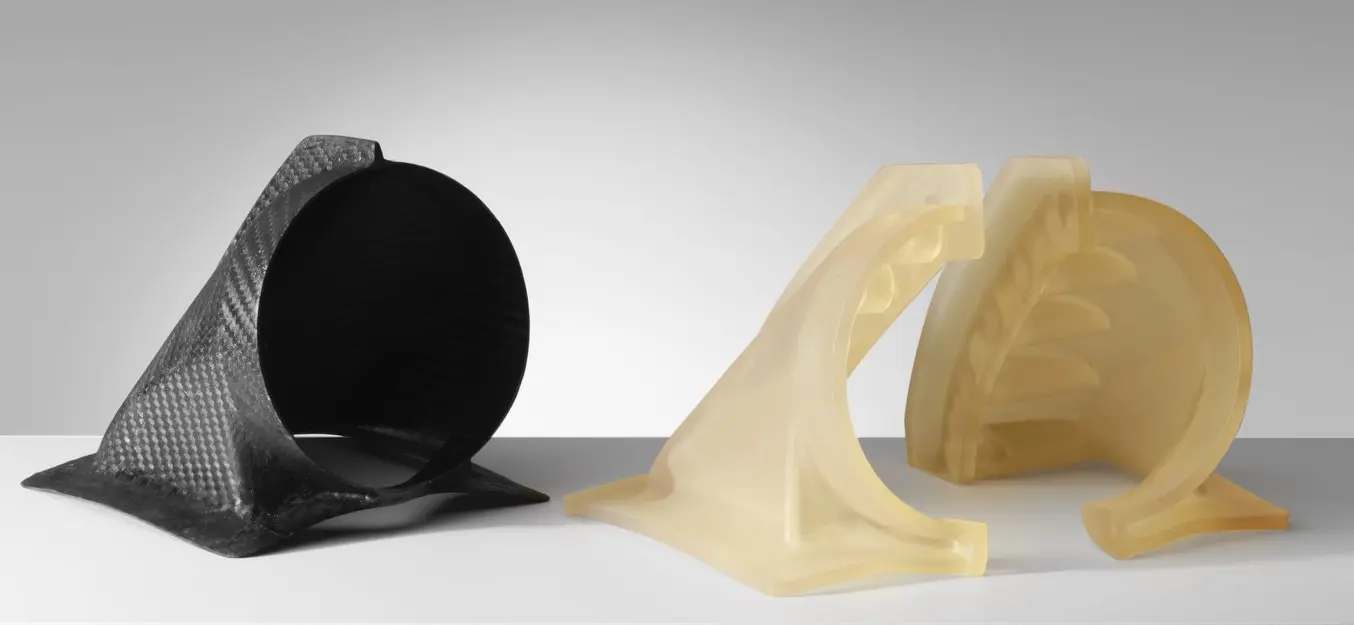
High Tempレジンでプリントした二つ割の成形型。その隣にあるのは炭素繊維で作ったフェンダーエアダクト(DeltaWing Manufacturing製)。
ポリマーを使って成形型を直接3Dプリントすることで、短期間の生産を最適化することができます。ただし、従来の成形型に比べると耐久性が低いため、大量生産には適していません。
生産量を増やすために、DeltaWing ManufacturingはHigh Tempレジンで原型を3Dプリントし、樹脂を使った鋳造を行っています。3Dプリント製の原型は、3Dプリント製の成形型には向いていない過酷な硬化条件を必要とするラミネート成形プロセスの強力な代替手段となります。メーカーはカスタム原型をオンデマンドで3Dプリントできることで、原型制作という成形型の製作工程の一部を省略できます。
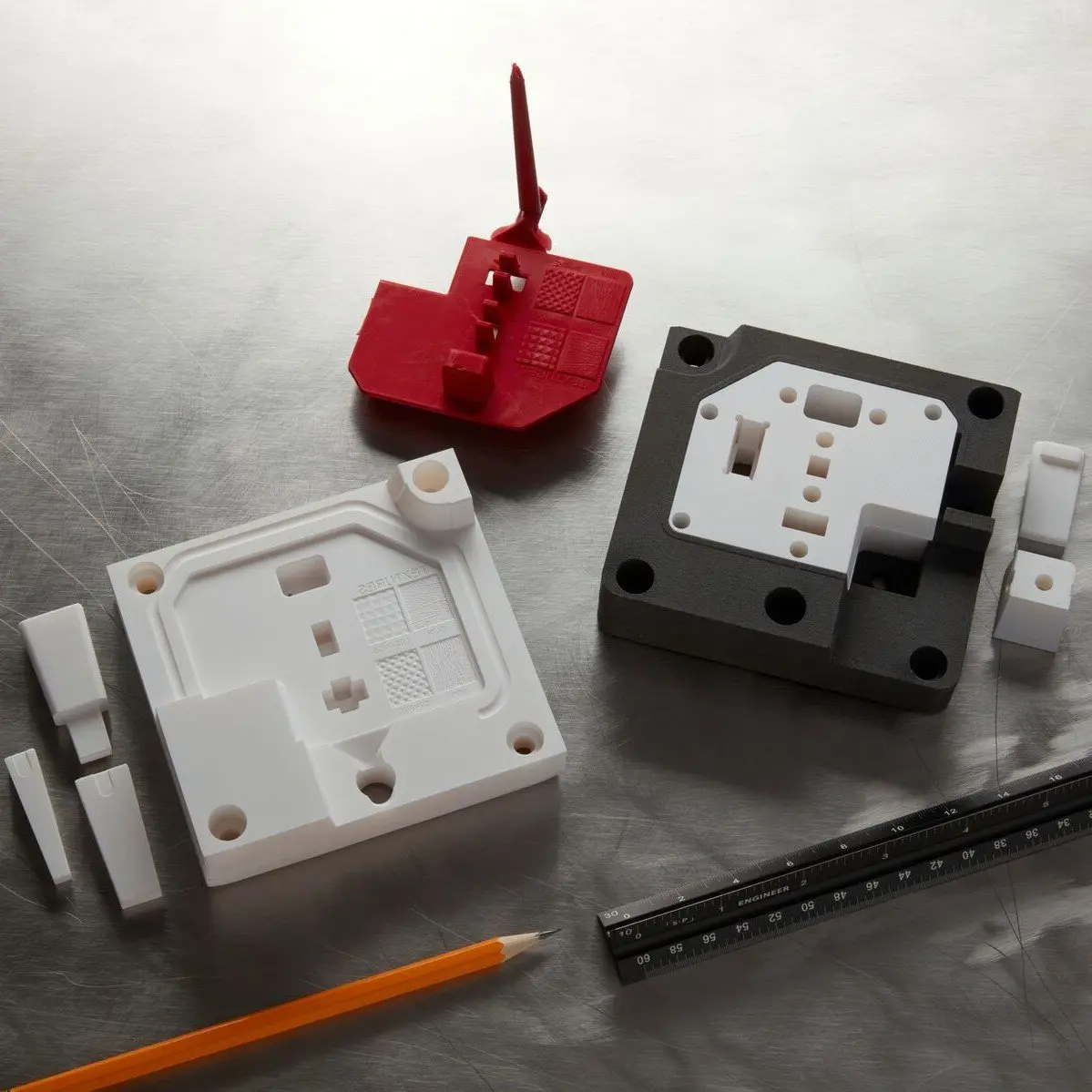
炭素繊維を使った3Dプリント
従来の炭素繊維部品の強度、耐久性、堅牢性と、3Dプリントの迅速性、形状自由度、再現性を組み合わせたワークフローには、大きな需要があります。そういった背景から、炭素繊維の3Dプリントを提供する多くの3Dプリント企業が存在するのも不思議ではありません。企業は短繊維または連続繊維を使用した炭素繊維3Dプリントを提供しています。
短繊維を使用する場合、SLS(粉末焼結積層造形)方式の工業品質3DプリンタFuse 1+ 30W向けの材料、Nylon 11 CFパウダーを使用すると、メーカーは従来のオーバーレイや加工方法に頼ることなく、強力で軽量、かつ耐熱性のある部品を製作できます。
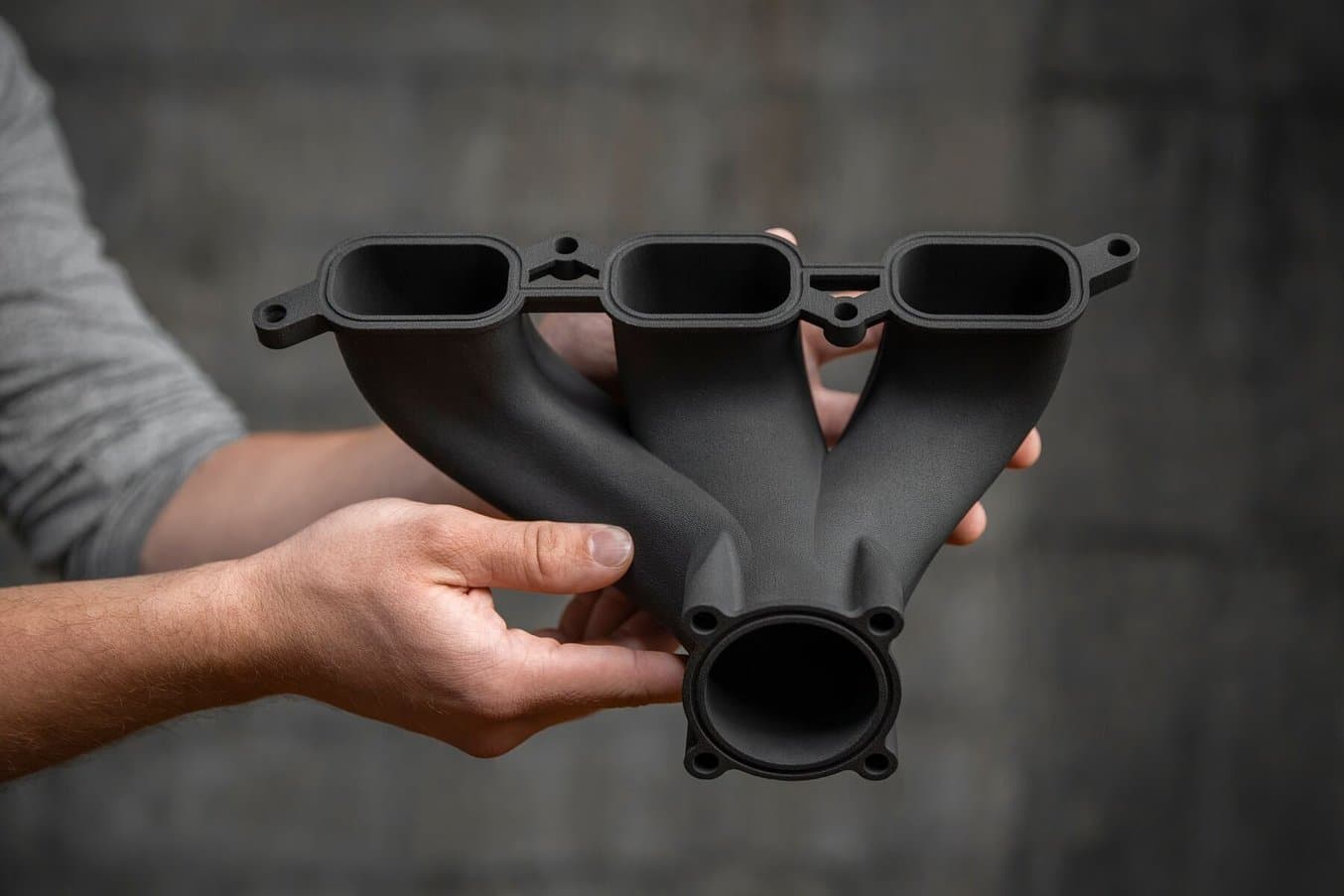
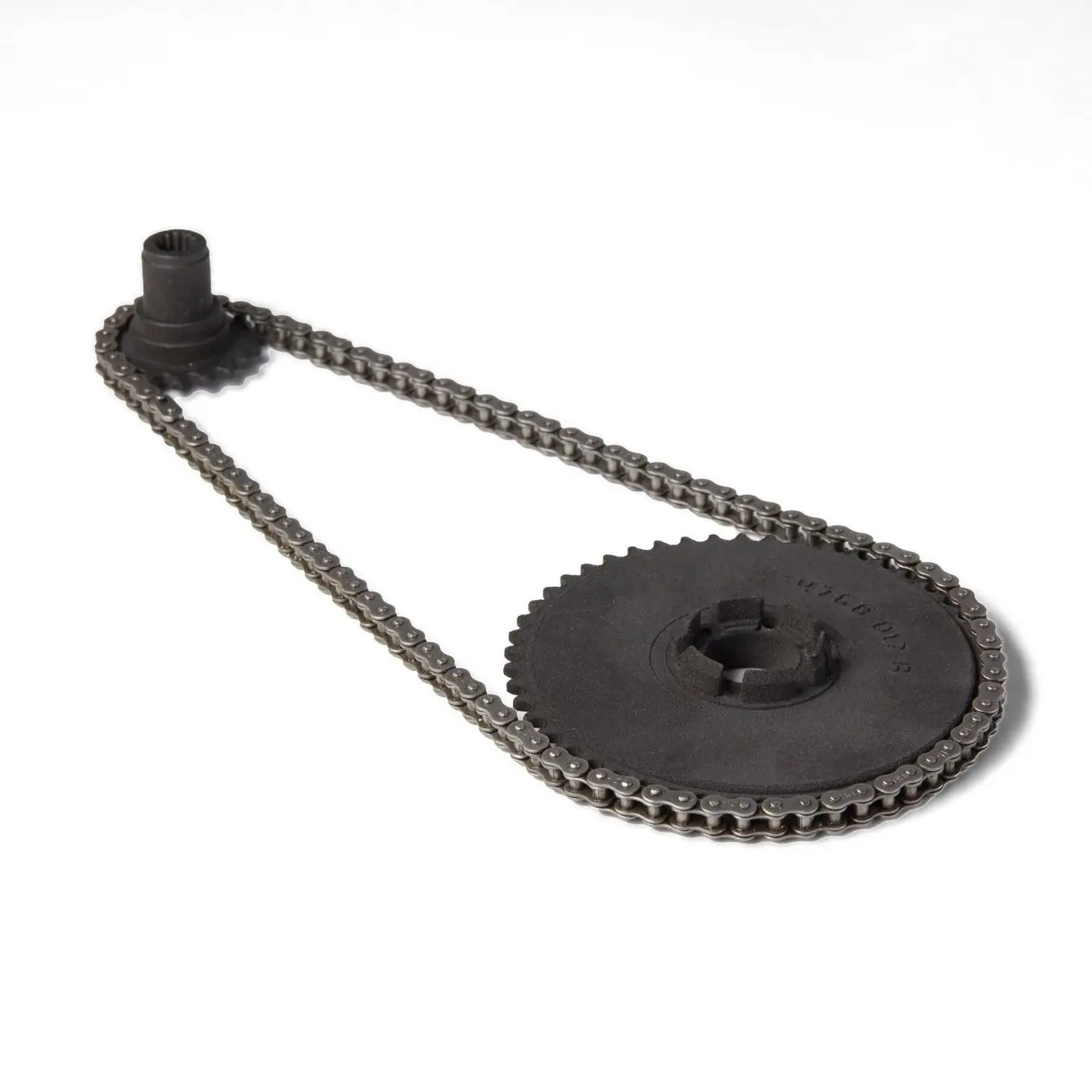
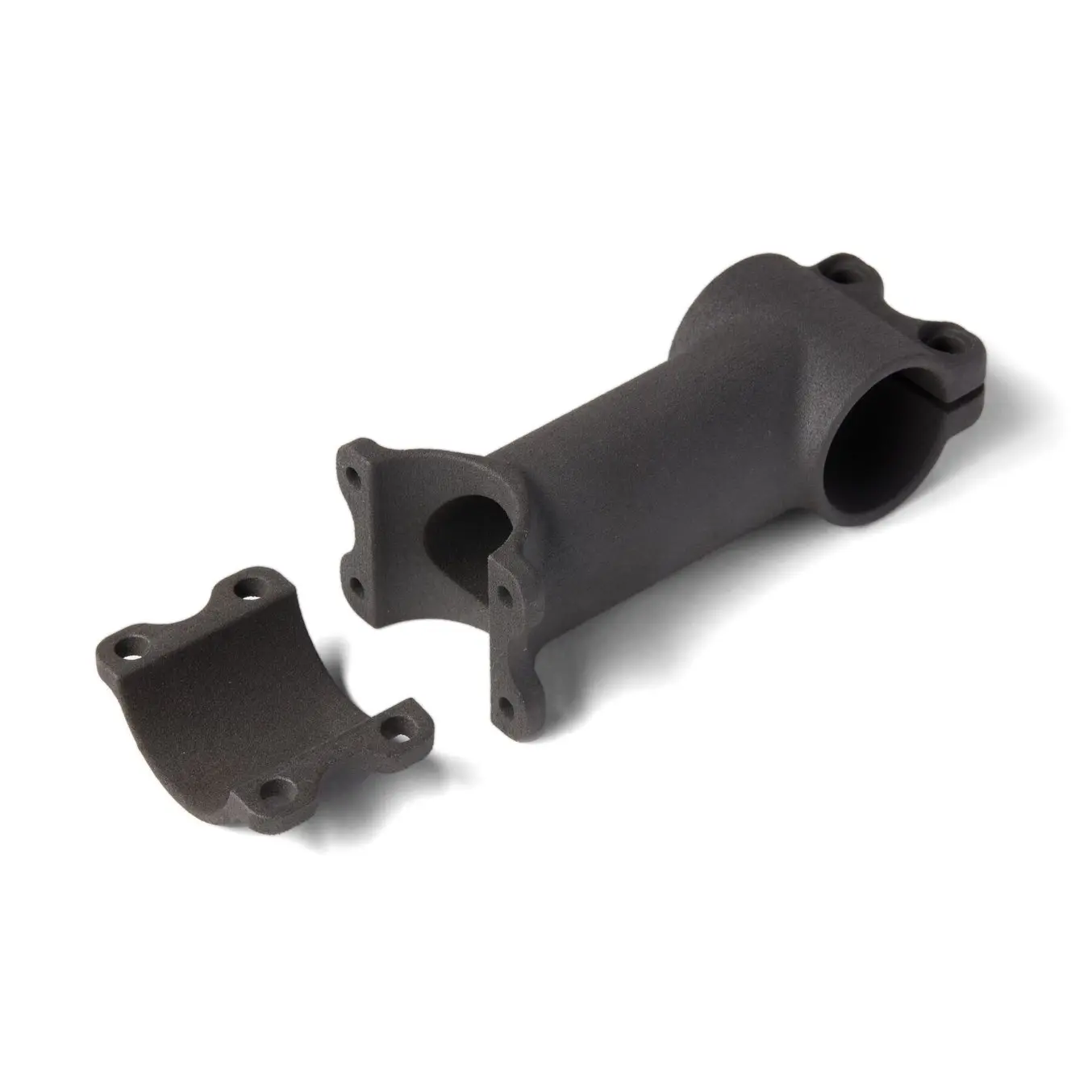
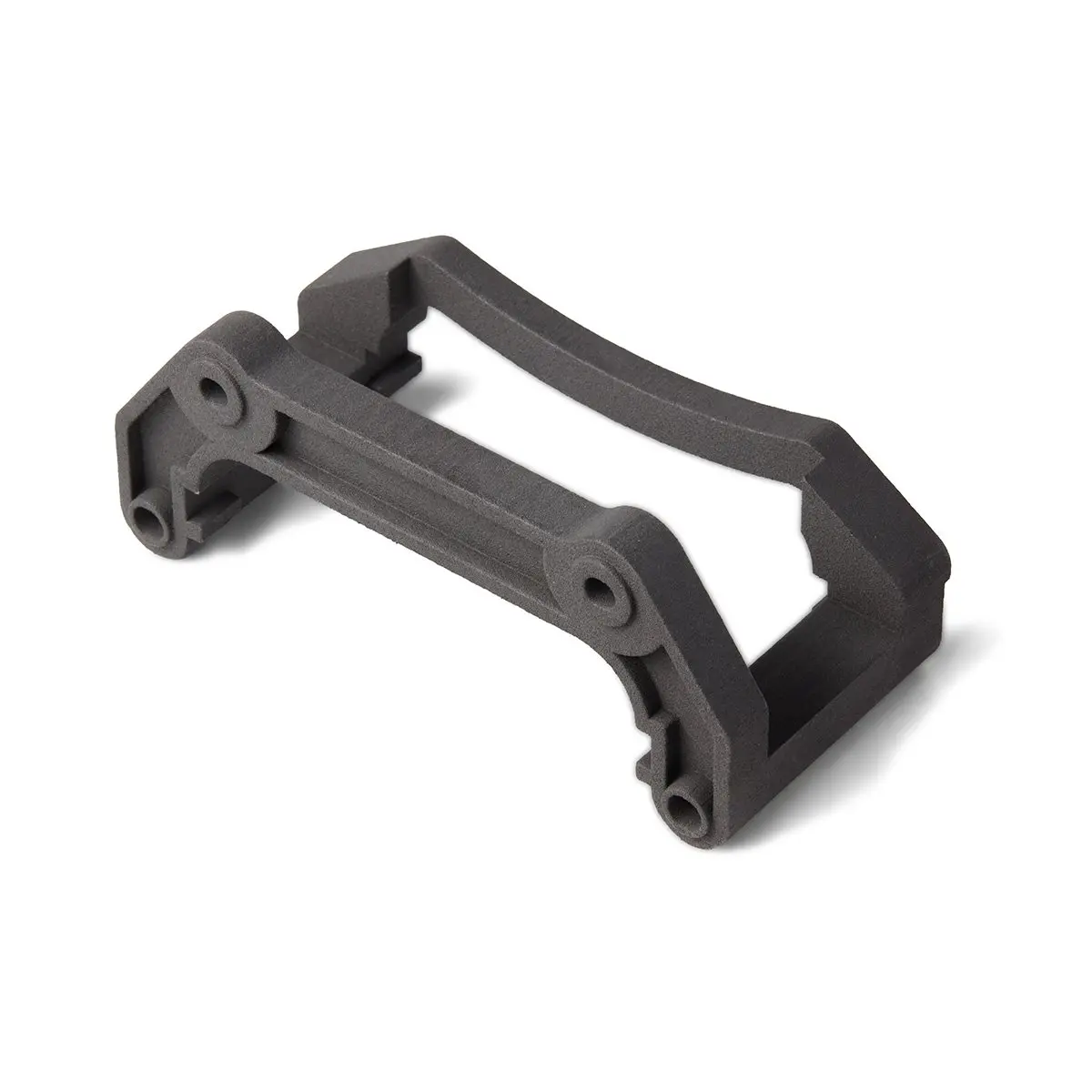
Formlabs Nylon 11 CFパウダーは強度が高く軽量で耐熱性があり、自動車、航空宇宙、製造業での用途に最適な材料。
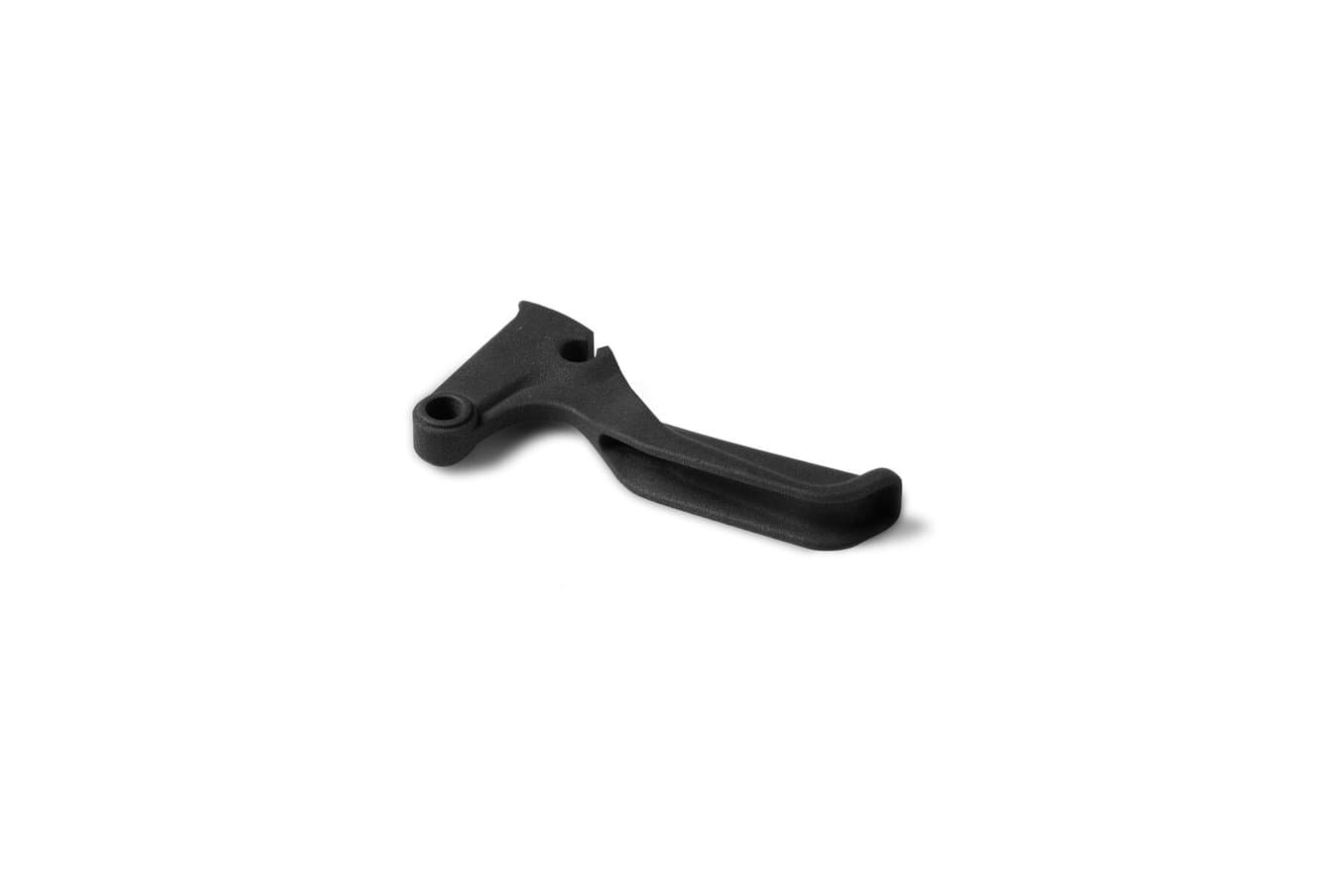
炭素繊維製造を始める
繊維強化プラスチックを使った製造は、エキサイティングである一方、複雑で多くの作業を必要とするプロセスです。3Dプリント製の成形型や原型を使用して炭素繊維部品を製造することで、ワークフローの複雑さを低減し、設計に対する柔軟性や新たな可能性を広げ、コストと製作期間を削減できます。
本技術資料では、TU BerlinとDeltaWing Manufacturingのケーススタディを通じて、成形型や原型を迅速に製作する3つのワークフローをご紹介するとともに、複合材料を使った製造における3Dプリントの活用方法をご提案します。