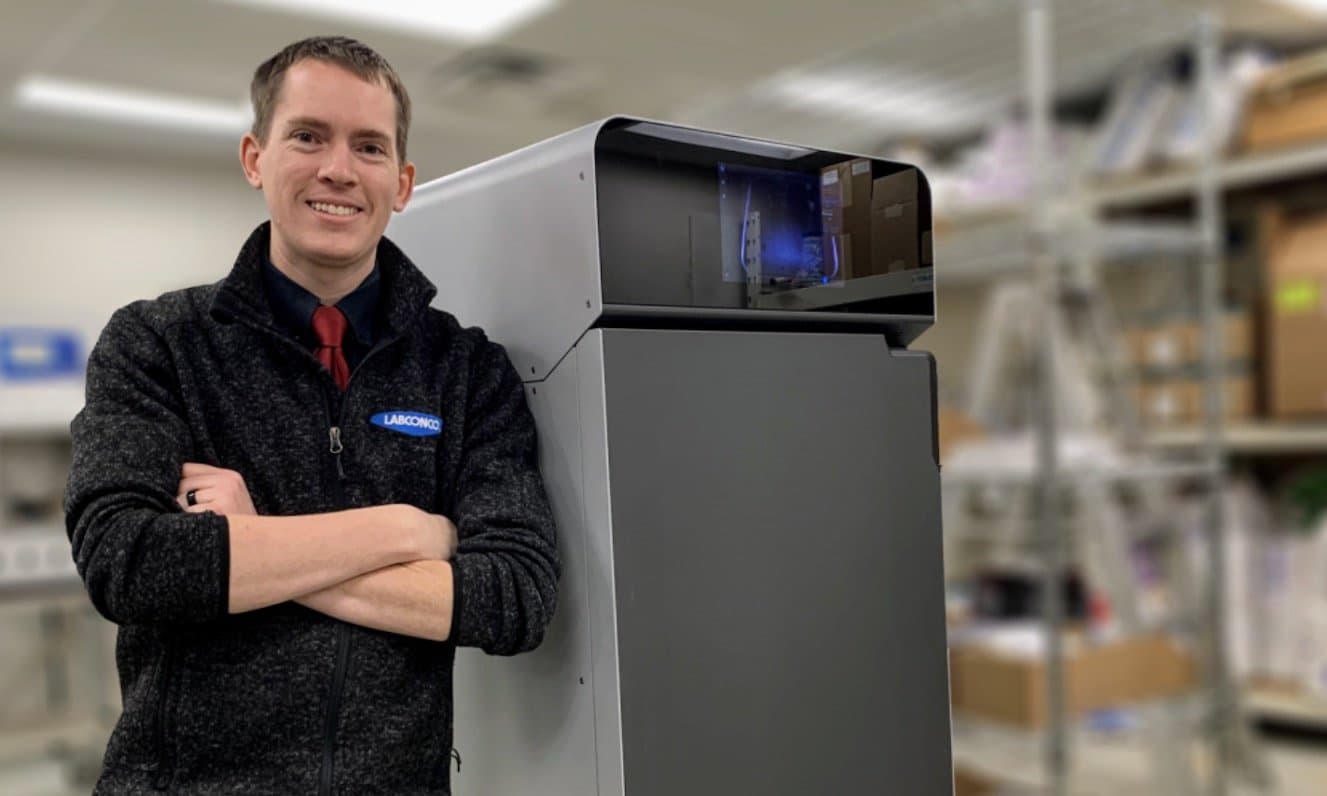
2020年初頭、Brent Griffith氏はLabconcoの一員として初めての会議で、3Dプリントのメリットを声高に力説して場を静まり返らせました。その会議の議題は、同社のLogic Vueシリーズの新製品で使用する射出成形製のパン・ステイクと呼ばれる小型の支柱でした。新製品であるため今後の生産量がまだ定まっておらず、$15,000以上もかけて金型を製作しても初年度の生産量は100点程度に留まる可能性もあります。当然、それでは部品製造単価が高くなり過ぎてしまうため、他の製造方法を検討していたところでした。「私はこう言ったんです。『3Dプリントなら、1年間で必要になりそうな部品を明日までに製作できますよ』と。そうしたら、部屋中が静まり返ってしまいました」とLabconcoのプロダクトエンジニア、Brent Griffith氏は言います。
当時、Labconcoはまだ3Dプリンタを導入していませんでした。翌日、Griffith氏は必要な部品を複数種類作って出社しました。個人で所有していた3Dプリンタを使って自宅で造形したものです。会社として、3Dプリントを活用するビジネスケースが自ずと見えてきた瞬間でした。
現在、Griffith氏は同社内で拡大を続ける3Dプリントラボを監督しています。現在、SLS(粉末焼結積層造形)方式の3DプリンタFuse 1+ 30Wが3台と、Fuse Sift、Fuse Blast、SLA光造形プリンタのForm 3Lがそれぞれ1台ずつ、その他複数のFDM(熱溶解積層)方式プリンタを所有する同社ラボでは、食品検査から製薬開発、腫瘍学診断、法医学に至るまで幅広い業界向けにラボ設備を生産しています。Griffith氏は現在、もともと加工や成形といった製造方法で量産された部品を改良し、生産に影響を及ぼすようなサプライチェーンの停滞が発生した場合には代替品となる部品や、Labconcoの数々の新製品の開発段階で役立つ部品を週に何百点も生産しています。
前例が無ければ作るのみ
パン・ステイクを3Dプリントで量産するというビジネスケースを実証して以来、Griffith氏は他の部品も3Dプリントで製作することで、エンジニアの開発業務を支援し始めました。その結果、「すぐに依頼が殺到するようになりました」とGriffith氏は言います。
他にも3Dプリントで実現できることを探るため、Griffith氏は同僚のエンジニアAustin Orme氏と共に、Labconco製品に使用する何千点もの部品や金型を次々と精査し始めました。「私たちに任された仕事は、造形量に優れ、試作品と実製品用部品の生産の両方に使用できるような非常に質の高い造形品を作れるプリンタを1台見つけ出すことでした。でもすぐに、1台だけでは不十分だということがわかったんです。1台だけでは、事業の成功に欠かせない広範な機能と柔軟性が不足するためです」とGriffith氏は言います。結局、ラボはSLS 3DプリンタのFuse 1+ 30Wを3台と、大容量SLA光造形3DプリンタのForm 3L 1台を含め、計6台の3Dプリンタを追加することになりました。
「Form 3Lを導入したのは、Formlabsの幅広い材料が使いたかったからです。これほど多彩な材料を簡単に切り替えて使用できれば、私たちの要件の多くを満たして今後の可能性を広げるような開発も可能になると確信していましたし、実際に使ってみて、やはり期待通りの製品だったと感じました」
Labconco プロダクトエンジニア、Brent Griffith氏
Griffith氏は、Form 3Lで利用可能な幅広い材料と、3台のFuseシリーズプリンタで可能になる中規模・大規模生産を組み合わせ、既存製品の改良、金型製作にかかるコストの数万ドル単位での節約、既存プロジェクトの開発工程の短縮化、オンデマンドでの部品交換を実現しています。
交換・改善・生産拡大:Labconcoの3Dプリント活用事例
SLS 3Dプリント製の充填検知センサで成形品を置き換え
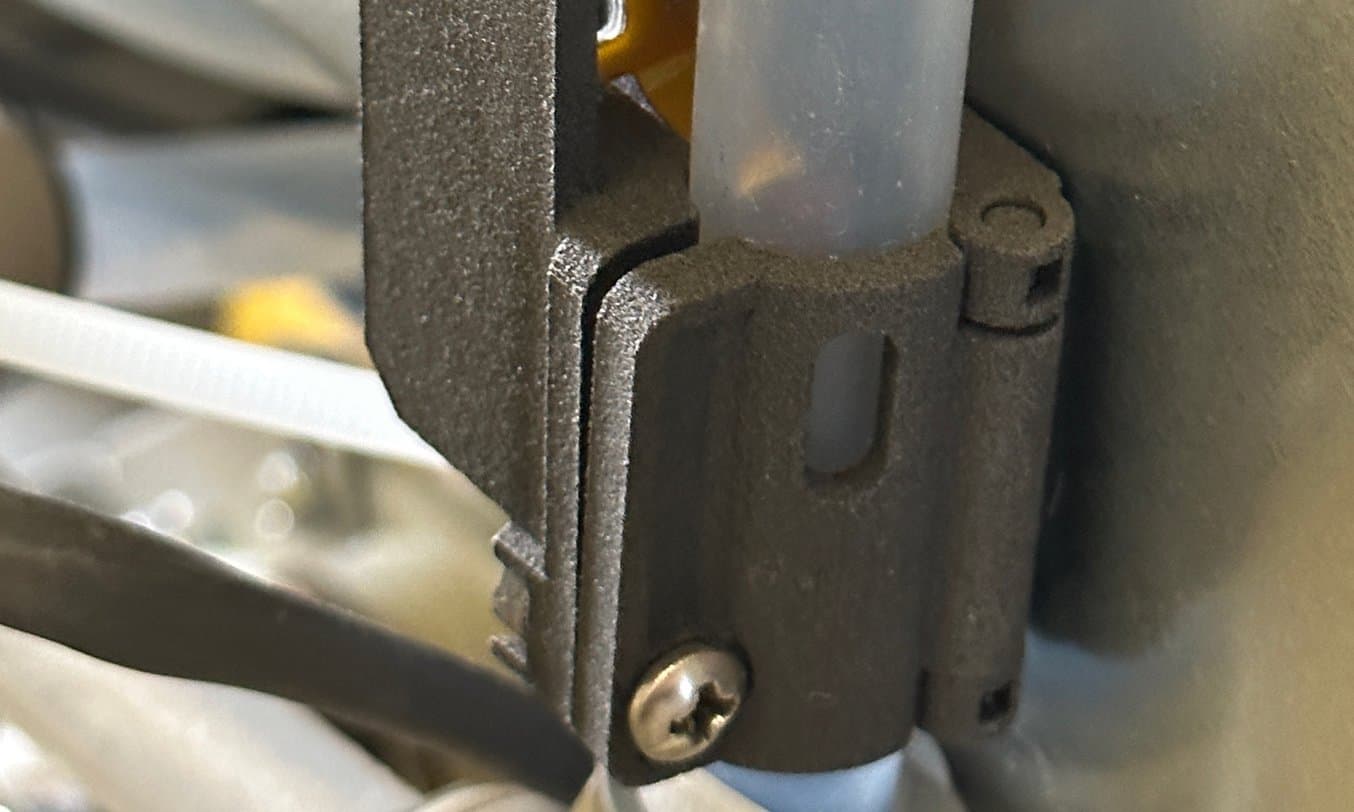
充填検知センサ用のこの部品には、LabconcoのプロダクトエンジニアであるTim Grove氏がNylon12パウダーの標準サンプルから着想を得て設計したヒンジ機能が実装されている。このヒンジ機能により、複数部品で構成されるアセンブリとしてではなく、単一部品としてプリントすることができ、作業時間と材料コストを削減できる。
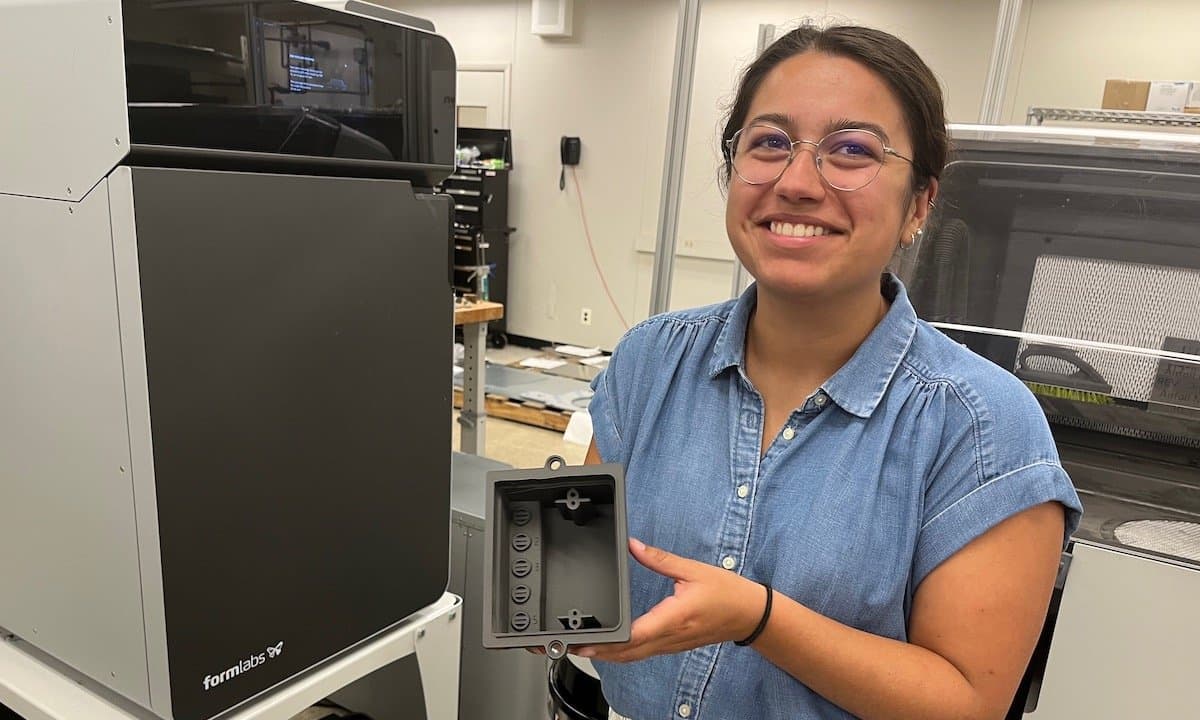
Labconcoのプロダクトエンジニアリングチームが3Dプリントの活用を効果的に拡大したことで、FuseシリーズのSLS 3Dプリンタなど、工業品質の技術を他の多くのチームメンバーが活用できるようになった。Griffith氏によると、同社の複数の部門が、コスト削減や柔軟性の向上、サプライチェーンを予期せぬ停滞から守ることを目的に、それぞれの作業工程に3Dプリントを組み込む方法を考え始めていると言う。
Labconcoのガラス食器洗浄機ラインには、アディティブマニュファクチャリング(AM)で製造した部品など、エンジニアリングの最先端技術を使って生産した部品が組み込まれています。そのような部品の1つである充填検知センサは、水が溢れ出すのを防ぐ機能のバックアップとして活用されています。従来の製造法では、まず2つの部品を別々に射出成形してから、後でその部品同士をピンで固定して組み立てる、という工程で生産されていました。
しかし、LabconcoのプロダクトエンジニアであるTim Grove氏は、SLS 3Dプリントで部品の生産にかかるコストと時間を削減できる可能性を見出しました。FormlabsのNylon12パウダーの標準サンプルであるクリップケースの可動部から着想を得たGrove氏は、充填検知センサの再設計に取り組み始めました。ここでの目標は、アセンブリを合理化し、複数の金型製作が必要なことによるコストを削減することです。
Griffith氏と何度も試作・検証を重ねて複数のバージョンを作成し、最終的に完璧な機能と最高のパフォーマンスを発揮する部品を設計することことに成功しました。
「機能性も完璧で、プリンタしたそのままの状態でアセンブリも要らないため、多くのコストが削減でき、生産工程に柔軟性が得られます。Fuseシリーズのプリンタで使用できるNylon12パウダーが、バランスの良いポリマー材料だと感じます。様々な用途に活用できますし、私たちにとっては非常に使いやすい材料です」とGriffith氏は言います。
SLS 3Dプリント製の充填センサ | 部品数 | アセンブリにかかる時間(50点あたり) | 造形単価(人件費含む) | |
---|---|---|---|---|
成形品 | 3 | 1時間 | $4.45 + 金型製作費 | |
SLS 3Dプリント | 1 | 0 | $2.56 |
SLA光造形でブロワーホイールを製作し、絶版品の交換部品にも対応
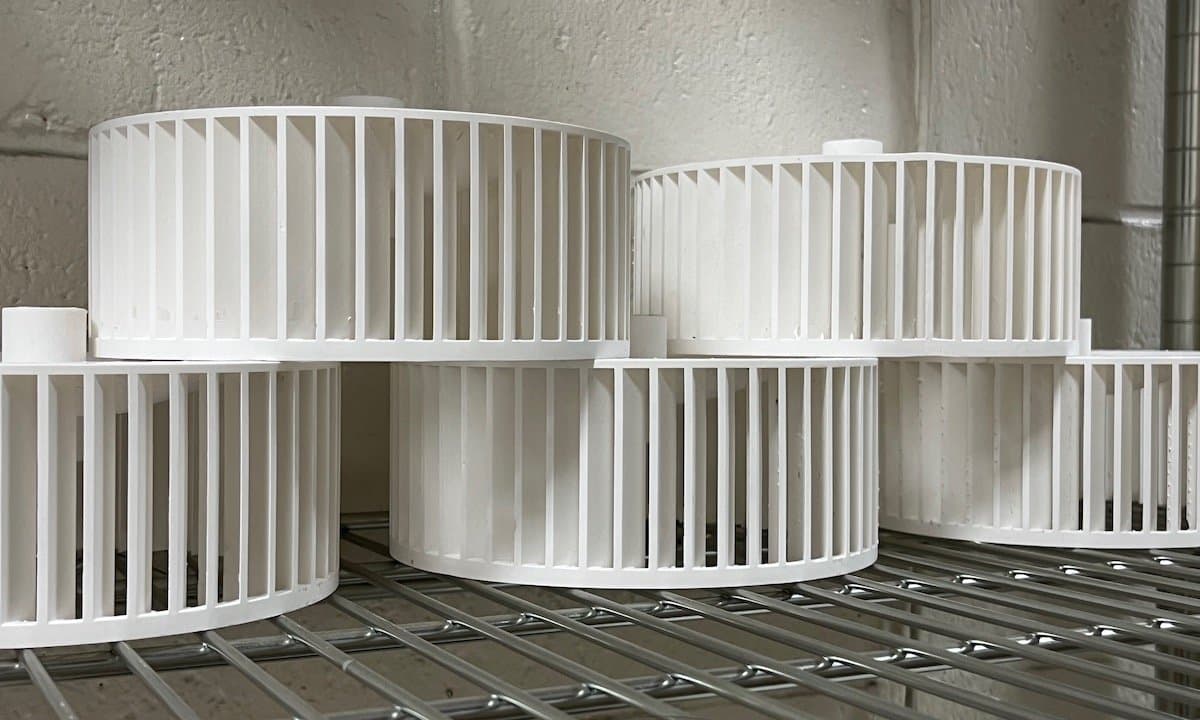
Labconco Kjeldahlの穀物分析製品に使用する写真の部品は、以前は外部のサプライヤーから購入していたが、生産終了が決定した。Griffith氏はこの部品をリバースエンジニアリングし、新しい設計をRigid 10KレジンにてForm 3Lで3Dプリント。1ヶ月以上毎日造形し、交換部品の在庫を豊富に確保し、今後発生することが確実なサプライチェーンの問題から生産ラインを守った。
穀物分析に使用するLabconco Kjeldahl製品に欠かせないブロワーホイールを製造するために、チームは以前まで外部サプライヤーに金型製作を依頼していました。ところが、生産数量が少ないために、そのサプライヤーでは金型のEOLに達した時点で生産を終了することが決定したのです。
そのためLabconcoは、新しいサプライヤーを探す必要性と、新しい金型の設計や製作の待ち時間、材料と人件費の高騰という様々な課題に直面することになりました。「十数種類の方法を検討しましたが、当社の仕様、特に化学的適合性を満たすものは見つかりませんでした。なので結局、製品を複製して部品をリバースエンジニアリングし、3Dプリント用に最適化してRigid 10Kレジンで造形することにしたんです。耐久性も検証した結果、これが最善策だとわかりました」とGriffith氏は言います。
ちょうど良いタイミングで新たな大容量SLA光造形3Dプリンタ、Form 3Lが届いたため、Griffith氏たちはリバースエンジニアリングしたブロワーホイールを40日間連続でプリントし、部品の在庫を増やすことに成功しました。
「複数の部品の生産に、Rigid 10Kレジンを使っています。このホイールの場合は酸、特に気化硫酸だったのですが、Rigid 10Kレジンの持つ化学的適合性で要件が満たせることがわかりました。アディティブマニュファクチャリングに切り替えたことで、サプライヤーや新しい材料を検証する時間を何百時間も節約することができました。そういう意味で、この一件はビジネスケースとしても3Dプリントの効果が実証された案件になりました」とGriffith氏。
SLA光造形3Dプリント製のブロワーホイール | コスト |
---|---|
元の設計で成形 | $178.77 |
再設計しRigid 10Kレジンで3Dプリント | $52.65 |
ベアリングケージのセパレーターをSLS 3Dプリントし、コストを$500から$20にまで削減
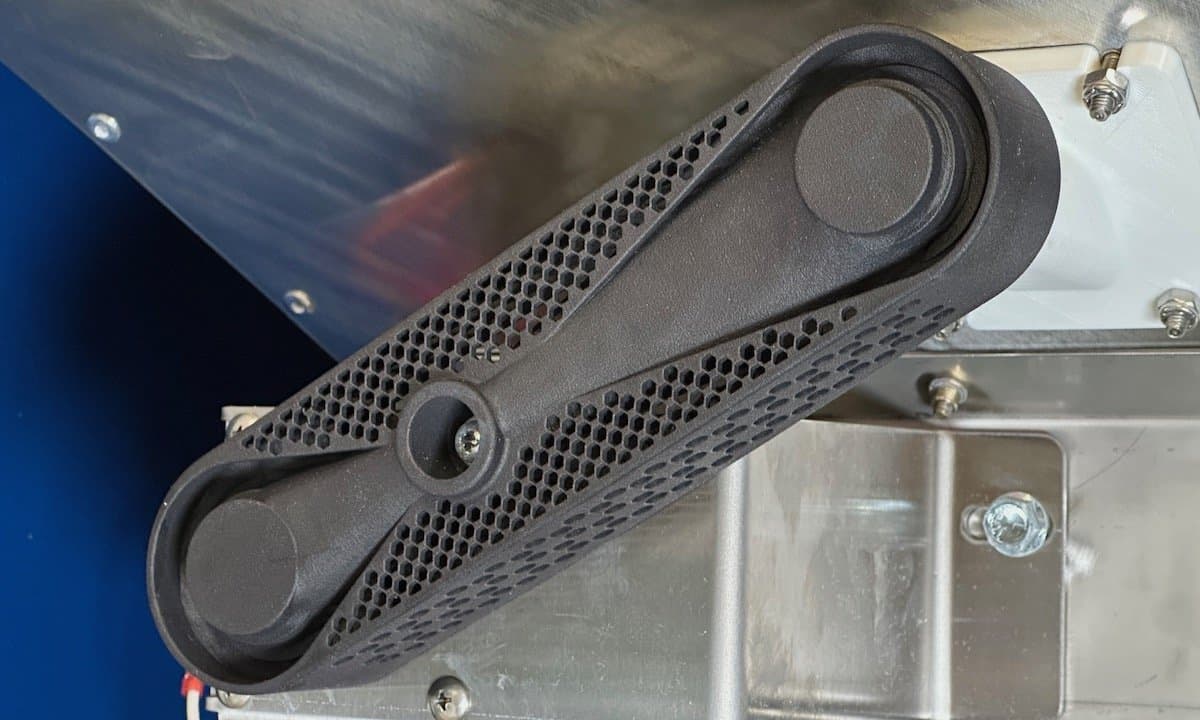
この部品は外部の加工業者の見積もりでは$500だったが、Griffith氏はそれと全く同じものを3Dプリントすることもできた。しかし、完全に同じものを作る代わりに、ペンシルベニア州立大学のAdditive Manufacturing and Design Programで学んだ原理を活かし、SLS方式で実現できる無数の可能性を生かして部品を再設計した。そうして出来上がった新しい部品のコストは僅か$21程度で、Labconcoは数百ドルを節約し、部品製作にかかる時間も2日未満に短縮することに成功した。
構造が比較的単純な部品でも、従来の製造法で作ろうとするとコストがかかります。2つのベアリングを分離し、互いに引っ張り合ってしまうのを防ぐ、セパレーターという部品の製作のため、加工業者に見積りを依頼したところ、1点につき約$500という金額が出てきました。この部品は新製品に使用するもので、Labconcoでは既に3Dプリントラボでユースケースを実証済みのものでした。Griffith氏はすぐにFuse 1+ 30Wでセパレーターのプリントを開始し、価格を$45程度にまで下げることに成功しました。これは、加工業者に外注した場合の10分の1の価格です。
改善はそれだけにとどまりません。Griffith氏は、ペンシルベニア州立大学のAdditive Manufacturing and Design Programで学んだ原理を活かし、単なる1対1の置き換えではなく、設計全体を最適化することに成功しました。
「まさに私が学んでいたことだったんです。アディティブマニュファクチャリングで可能になることと、逆に制約となること。それを理解した上で、どう活用するかということです。言わば『この部品をAMで作れないか?』という考え方ではなく、そもそも『これをAMで作るべきかどうか』という見方、考え方に変えるんです。今回のケースの場合、3Dプリントで1対1の置き換え品を作ることは可能でしたが、そうすることでせっかくAMで実現できることを活かせなくなるんです。私たちは、製作できる形状にほとんど制約のないFuseシリーズのプリンタを導入していたので、少し大胆な新設計も試すことができました」
Labconco プロダクトエンジニア、Brent Griffith氏
Griffith氏は、ジェネレーティブデザインを活用し、作業員の安全を守るセパレーターの安全装置は維持しながら、部品全体の材料を削減する設計を模索し始めました。そして僅か1日以内に設計を最適化し直すことに成功し、LabconcoはSLS 3Dプリントを活用したことで造形単価$20ドル程度で部品の内製を開始することができました。
「3Dプリントは、形状の自由度という点で非常に大きなメリットが得られます。部品を軽量化したり、様々な設計技術を実装したい場合には、これまでには実現されてこなかった方法で部品を組み合わせることもできるんです。製造を内製化することで、コストを大幅に削減することも可能です」とGriffith氏は言います。
SLS 3Dプリント製のベアリングケージのセパレーター | コスト(人件費含む) | 製作期間 |
---|---|---|
加工 | $485.82 | 2~3週間 |
SLS 3Dプリント品による1対1の置き換え | $43.50 | 29時間 |
SLS用に設計を最適化 | $21.08 | 28時間 |
SLS部品を使った部品検証:アセンブリに必要な部品数を減らして機能性を向上
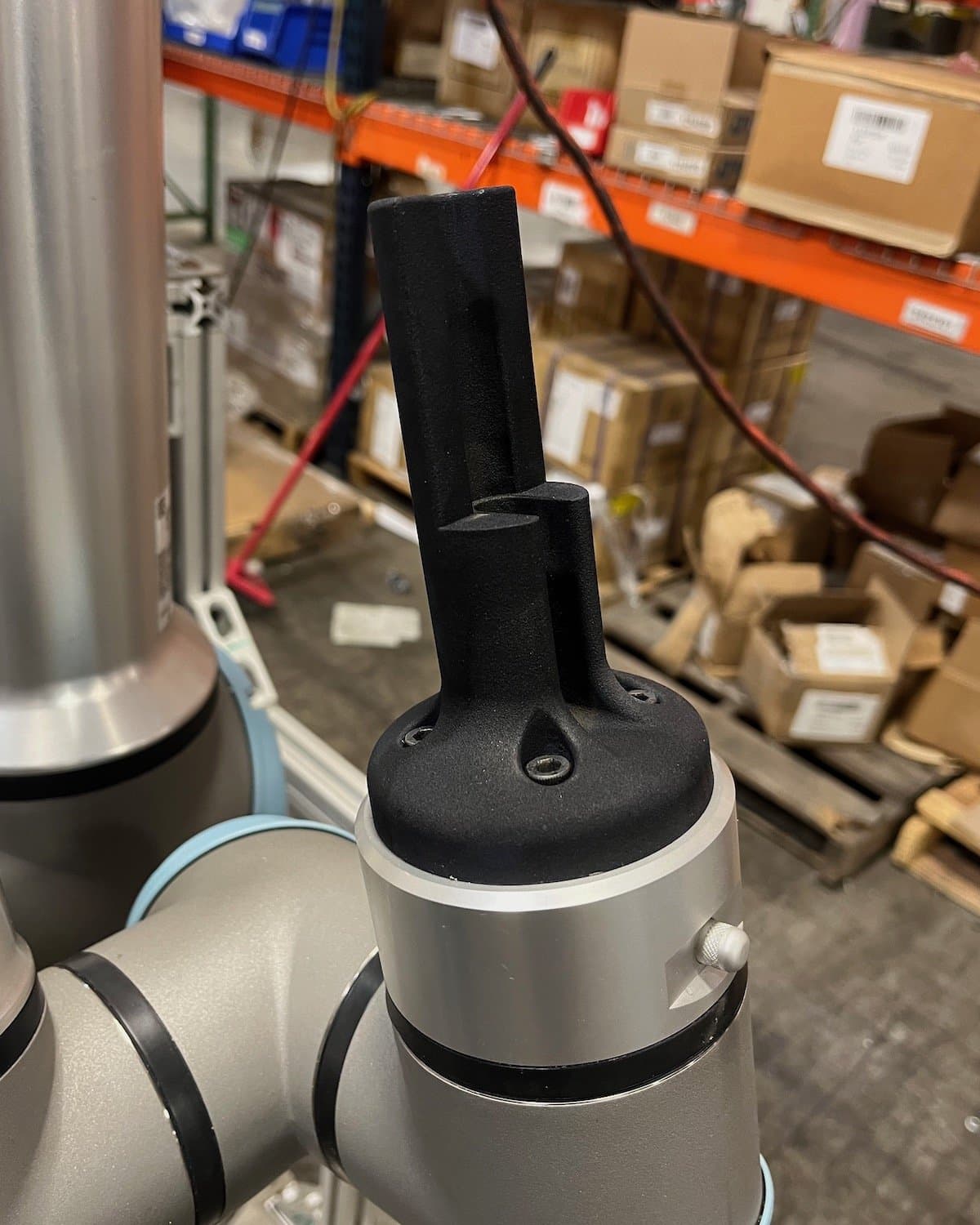
Labconcoが手作業とロボットアクチュエータを組み合わせたハイブリッド型の作業工程にスムーズに移行できるよう、Griffith氏率いるチームはFuseシリーズプリンタを使ってカスタム金型とエフェクタをNylon12パウダーでプリントした。
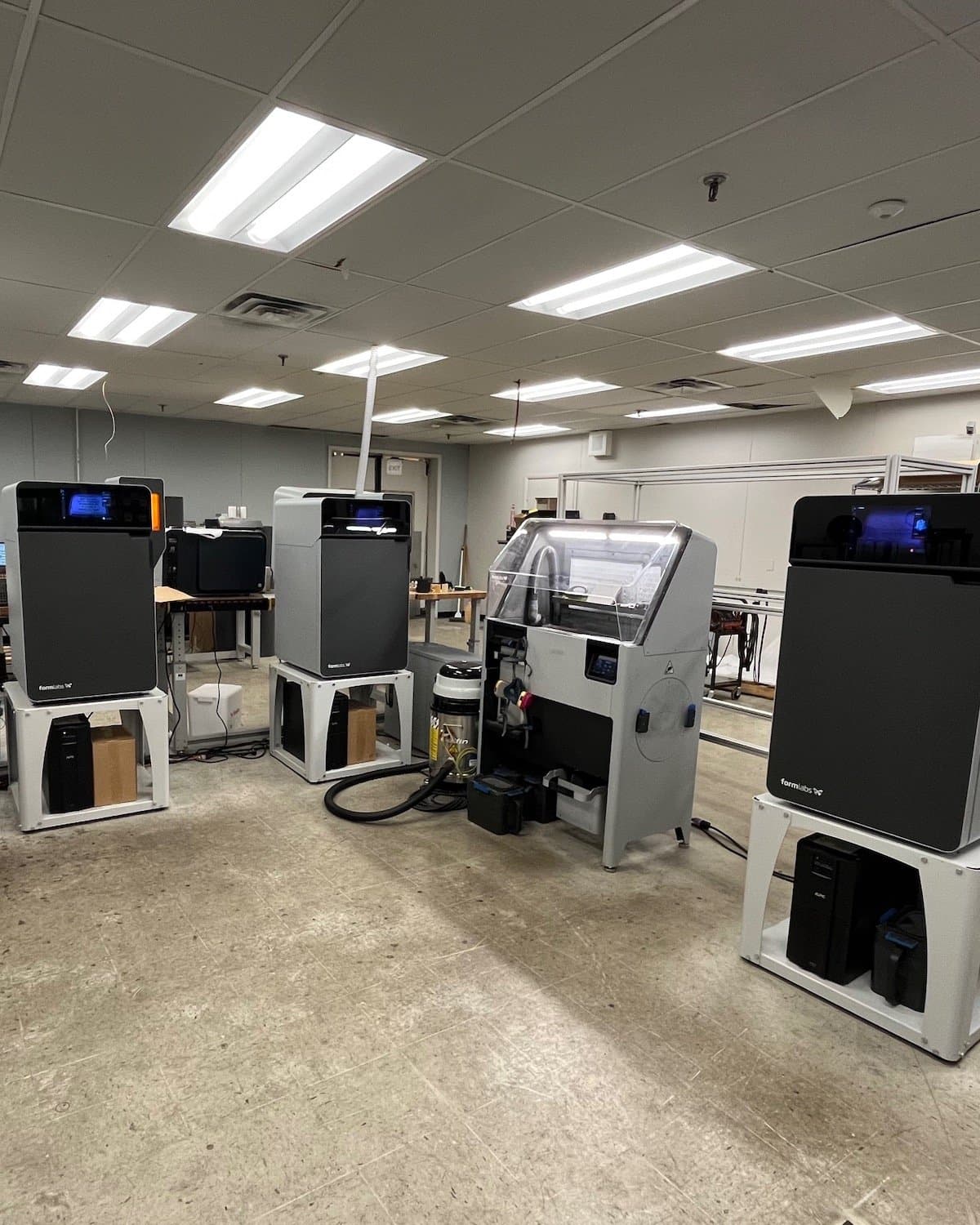
FuseシリーズのSLS 3Dプリンタはコンパクトで消費電力も少なく、台数を増やすことで頑丈で耐久性のあるSLS部品の生産拡大にも対応可能。
常に品質を追求し続けるLabconcoは、主力製品の1つに使用する生物学的安全キャビネットという重要部品の検証も行っています。このキャビネットは、内部で使用する製品と作業員の安全を確保するために必須のコンポーネントで、特定の気流パターンとHEPAフィルターが必要です。最高レベルの性能を保証するために、これらのフィルターには厳しい試験が行われ、認定を受けて初めて完成品になります。
以前は、この試験工程が人間の作業員に大きく依存していたため、潜在的なばらつきや限界がありました。しかし、Labconcoは革新的なアプローチを採用し、ロボットシステムの力を利用して各フィルターのスキャンを完璧な精度で自動化しました。自動化へシフトしたことで、試験を行うロボットアーム用にカスタム金型とエンドエフェクターの開発が必要になりました。従来の製造法では法外なコストがかかり、製作期間も数か月程度かかる可能性があります。必要な部品数が少ないため、Fuseシリーズのプリンタで3Dプリントできることが要でした。
Labconcoは、Fuse 1+ 30WでSLS部品を内製したことでコンポーネントの日々の利用率を大幅に向上させ、製品の安全性試験の精度と信頼性を高めることができました。アディティブマニュファクチャリングを追加したことが大きな転機となり、業務が合理化されただけでなく、製品の安全性と性能を妥協せずに確保できるようになりました。
エフェクター部品 | コスト |
---|---|
加工 | $508.32 |
SLS 3Dプリント | $73.44 |
ヒュームフード用部品をSLSで中規模生産し、アジリティを向上
Labconcoはヒュームフードの生産を商業化した最初の企業で、現在ではこの製品部門が同社の中で最も重要な部門の1つとなっています。ヒュームフードは、化学、製薬、農業関連の大型事業では欠かせない製品です。
その部品の1つである機能性サッシストッパーは、フードのサッシが定められた箇所以上に開かないようにする(つまりエネルギーコストを節約する)もので、以前は射出成形で製造されていました。1つの金型を使って大量の部品を製造するため、大口顧客のために設計を変更したりカスタマイズしたりすることが自由にできませんでした。使用を重ねると金型は劣化していきますが、交換の際はサプライヤーを安定して頼れない場合もあります。Griffith氏たちはこういったサプライチェーンの問題に対処すべく、Fuse 1+ 30Wでサッシストッパーをプリントし始め、現在ではNylon12パウダーを使って週に50~100点の部品を生産しています。
「成形の場合、一度部品を作ってしまうと簡単には修正できません。本来は起こるべきではなく、だからこそ頻度も少なく済んではいますが、それでも射出成形で作った部品がようやく届いて使用を開始した途端に壊れ始めたり、意図したとおりに動作しなかったりして、苦しめられたことが過去にありました。3Dプリントを活用するようになってから、部品によっては3Dプリント用に設計を変更しておけば再設計が必要な時も手間が省け、変更可能な領域も広がることを、今のエンジニアたちは認識しています。価値あるもの全てに値段がつけられるわけではありません。私は、アディティブマニュファクチャリングにはそういった『目に見えない』大きなメリットがあると考えています」とGriffith氏は語ります。
キャリアをスタートさせたばかりの若い従業員に自信を与えられることも、3Dプリントで内製をするもう1つのメリットです。新しい金型を注文する時に完璧な状態にしておく必要がないため、新しいことに挑戦したり、新しいアイデアを取り入れたりする意欲が高まります。「若いエンジニアには、部品を見ただけで『これはうまくいく』と言えるような20年来の実務経験はまだありません。3Dプリントができれば、何か1つ、あるいはたくさんのことを試すことができ、それが失敗しても取り返しのつかないことにはなりません。そういう意味で、挑戦する気持ちを後押ししてあげられるんです。どんな問題に対しても、一番クリエイティブな最善策を見つけ出すこと。彼らには、そういう頭の使い方ができるようになってほしいと思っています。そのためにも3Dプリントが重要な役割を担っています」とGriffith氏。
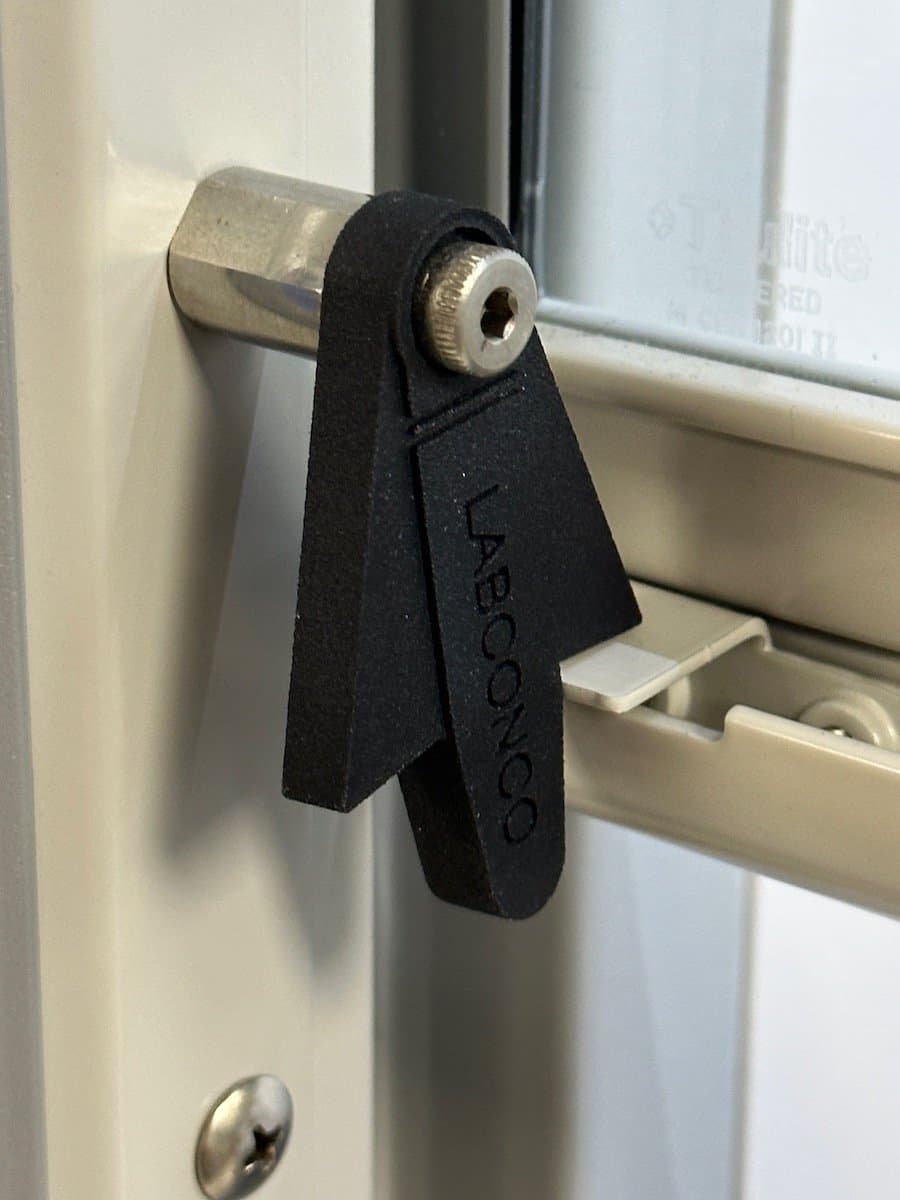
Griffith氏は、サッシストッパー用の部品をFuse 1+ 30WでNylon 12パウダーで週に50~100点生産し、1つの金型だけに頼って生産を行うリスクとコストの両方を回避している。
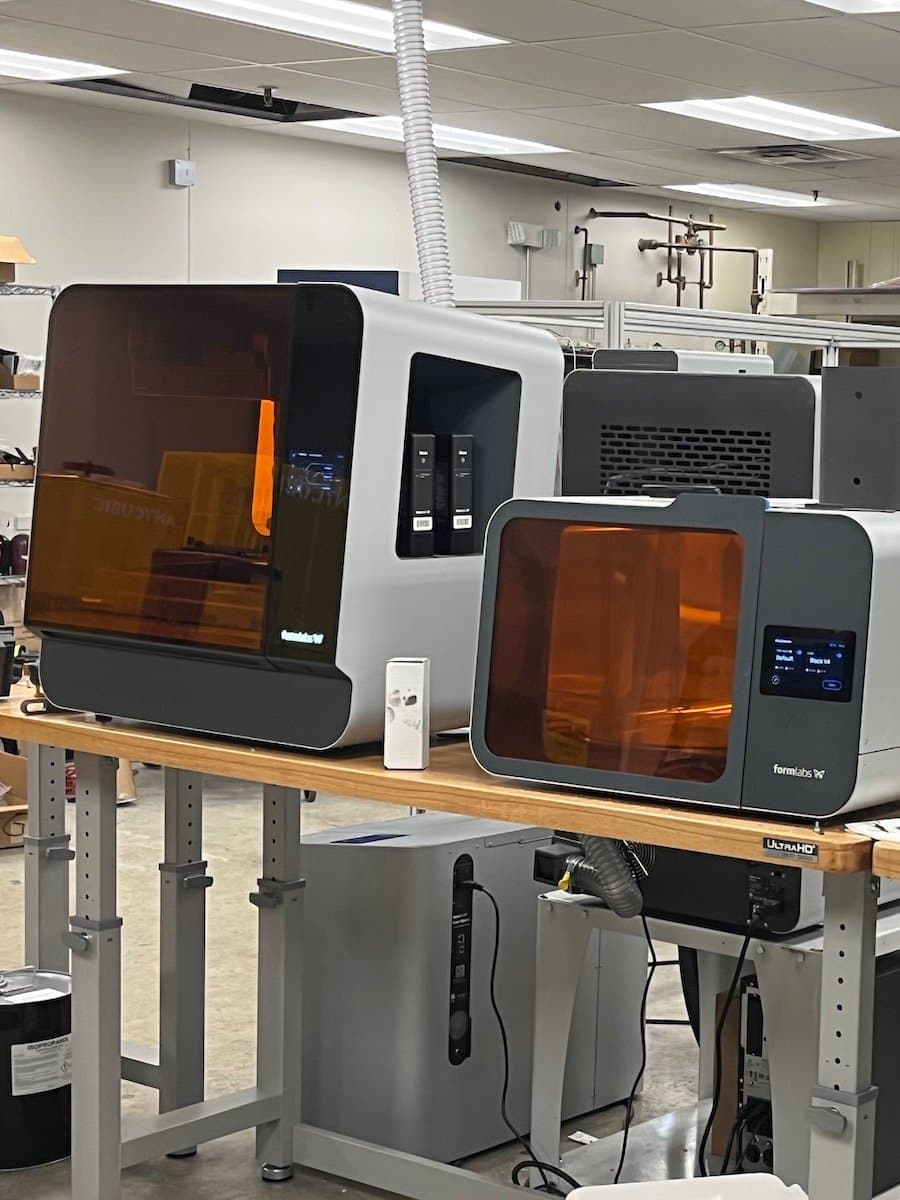
SLSやSLA光造形プリンタの使いやすさが、キャリアをスタートさせたばかりの若い従業員が新しい技術を使いこなす自信をつけ、新たなアイデアを次々と取り入れる意欲を促進している(この写真に写っているのはForm 3LとForm Cure L)。
Fuse BlastでLabconcoの大幅な工程効率化
SLS 3Dプリントで部品を週に100点以上生産しているLabconcoでは、造形品のブラスト処理やパウダー除去など、手作業による後処理工程に何時間も時間がかかっていました。この時間は、本来であればより付加価値の高い設計やエンジニアリング作業に割り当てたいところです「会社としては、従業員が造形品の後処理のために何時間も座って作業をするより、新たな機会の創出や既存部品の再設計、コストの削減などに時間を費やしてほしいというのが本音でした」と、Griffith氏は言います。
そこでLabconcoは、高額な自動ブラスタに加えて、Fuse Blastを追加して既存のFuseシリーズ製品を補完することにしました。10分ほどでセットアップが完了した後、Griffith氏はFuseシリーズプリンタ2台分の造形品のパウダー除去やブラスト処理を自動化することができました。「セットアップはとても簡単でした。大きさも既設のブラスタとほぼ同じです。SLS 3Dプリンタを導入済みの企業なら既にブラスタを設置しているでしょうが、そのスペースがあればFuse Blastも問題なく設置できます」とGriffith氏は言います。
造形品の品質と性能をさらに上へ
Labconcoの他チームが、すぐに造形品の表面の滑らかさや品質の違いに気づき始めました。
「Fuse Blastによる品質の違いは一目瞭然でした。プロトタイピングの時にFuse Blastで処理した造形品を手渡したエンジニアは一人残らず、品質の変化にすぐに気がつきました。後処理工程を自動化したことを伝えるまでもなく、全員がすぐに気付いたんです。造形品の表面の粉っぽさがなくなってさらに滑らかになったこと、手触りや見た目がぐっと良くなったこと、それら全てが造形品の品質向上に一役買っています」
Labconco プロダクトエンジニア、Brent Griffith氏
表面の粉っぽさが排除されて滑らかになったことで、機能面でも予想外の効果が得られました。Fuse Blastで処理した部品を使った機械が、これまでよりもスムーズに動くようになったのです。「造形品の滑らかさが増したことで、特に自社製品の試運転の時、部品の機能性が若干向上したんです」とGriffith氏は言います。
表面の仕上がりは、同社が所有する他の高額な自動ブラスタで処理したものとほぼ同じでした。「2つの製品を比べてみても、目立った違いは感じられません。[Fuse Blast]は重量の面で他社製品を遥かに凌いでいると言えます」とGriffith氏は付け加えます。
後処理の時間を短縮し、設計の最適化に注力
Fuse Blastで後処理が自動化できるようになったことで、手作業のブラスト処理にかける時間が不要になっただけでなく、Griffith氏や彼のチームメンバーがFuse Siftにかけていた作業時間も削減されました。これまでは、ブラスト処理にかける時間を短くしようとすると、Fuse Siftでの作業時間を長くして丁寧に処理をする必要がありました。しかしFuse Blastの導入後は、たとえ造形品に余分なパウダーが大量についていても、自動設定で粉っぽさのない表面に仕上がるようになりました。「[Fuse Siftで]どれだけパウダーを除去できるかをあまり気にしなくても良くなりました。Fuse Blastならどんなものでも処理できるとわかっているからです。Fuse Siftでの作業時間に関わらず、後処理全体の作業時間が短縮できるようになりました」Fuse Sift上でのパウダー除去は、細かな部位に関しては再利用できるパウダー量はごく僅かですが、その作業にかかる労力と時間がかなりのもので、それを人件費に換算してもコストに見合うものではなかったと思います」とGriffith氏は振り返ります。
例えば毎週50点程度を定期的に生産する部品の場合、Griffih氏のチームはこれまで、その部品についている3つの穴から一つ一つパイプ形状クリーナーを使って手作業でパウダーを除去しなければなりませんでした。Fuse Blastを導入後は、自動設定でお任せにしておけば、20分後にはパウダーが完全に除去された部品が手に入ります。「Fuse Blastは革新的です。穴部分のパウダー除去も文句なしにしてくれて、おそらくこの作業が無くなったことが一番の時間削減につながったと言えると思います」とGriffith氏は言います。
3Dプリントによる生産の拡大
Griffith氏率いるチームは、これまで3Dプリントを体系的に活用してきました。3Dプリントを導入してから初めての監査で、初期に導入した6台の3Dプリンタの有用性が証明されました。それ以降も常にコストや作業時間の削減、多種多様な部品の設計改良を重ねてきた彼らは今、3Dプリントの活用拡大を検討しています。
「部品が送られてくるたびに、自分に問いかけるんです。『この部品を、AMを使ってもっと良くできないか?』と。この問いを常に投げかけてきたことで、たくさんの部品で大幅な節約を実現し、コストを削減することができました」とGriffith氏。
3Dプリントによってもたらされるメリットは明らかです。特定の、あるいはニッチな用途で部品を求める顧客に対して、Labconcoのチームは、内製と小ロット量産によってコスト効率の高いソリューションを自信を持って提案することができます。「カスタム部品を5点、10点、もしくは50点だけ作ってほしいというお客様に対しても、コスト効率よくその需要に応えることができ、市場のニーズに素早く対応することができています」とGriffith氏。
3Dプリントの力を大々的に力説して会議室を静まり返らせたあの日以来、Griffith氏は様々な規模の生産でビジネスケースを確立し続けてきました。SLA光造形3DプリンタやSLS 3Dプリンタで部品を内製することで、新しい用途の創出、事業の成功、製品性能の最適化、サプライチェーンの混乱による生産停滞の回避、そしてコスト削減に成功しています。
SLS方式とSLA光造形方式を活用した生産の内製化については、Formlabsのスペシャリストまでお問合せください。