世界最大の鉄道会社の1つであるDB(ドイツ国鉄/Deutsche Bahn)は、毎日1000万人もの乗客の移動を支えています。何百万もの人々の移動を支える巨大インフラのメンテナンスは、それ自体が大かがりな作業です。同社はドイツ全土で50以上もの工場を運営し、旅客列車や貨物列車を提供しています。
DBの車両メンテナンスを専門で担当する子会社は、ドイツ最北端の車両センターをノイミュンスターという町に保有しており、約750人の従業員が都市間を結ぶ列車や通勤列車の車両メンテナンスや修理、そして時には徹底的な点検やモダナイズを行います。この拠点は現場に3Dプリンタの工房を持つ拠点の1つで、日々の業務の効率化を図っています。
「3Dプリントを導入した2015年以降、DBでは既に10万点以上もの部品をプリントしてきました。削減できたコストは何百ユーロにも上ります」
Susanne Tost氏、DB Group Project 3D Printing マーケティングスペシャリスト
以下の技術資料では、DB Vehicle Maintenanceの製造エンジニア兼アディティブマニュファクチャリング・スペシャリストのCarsten Wolfgramm氏と、DB Group Project 3D Printingのマーケティング責任者であるSusanne Tost氏によるFormlabs製3Dプリンタでの治具製作や作業手順簡素化、コスト削減、車両メンテナンスの高速化を実現した方法をご覧いただけます。
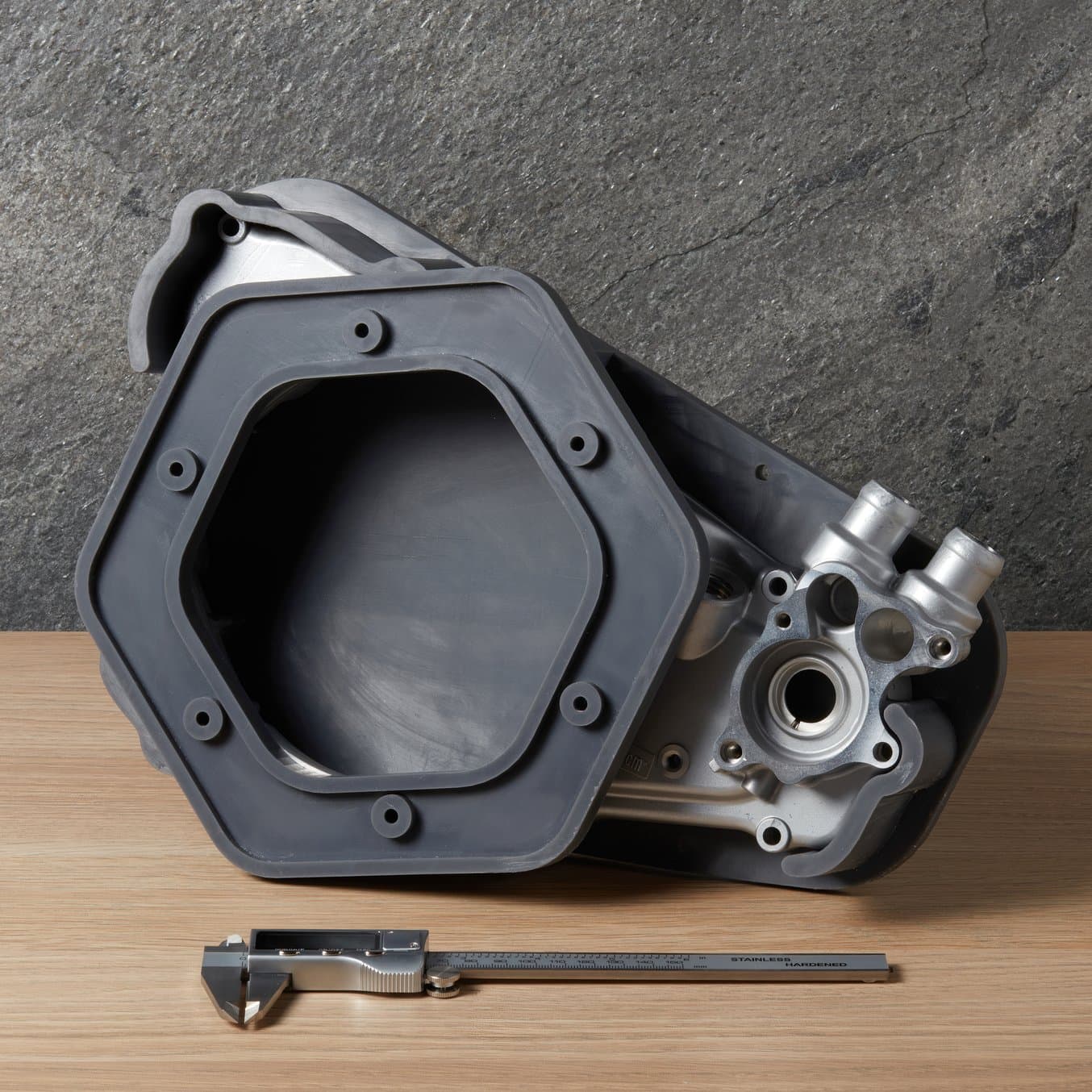
現場で必要な時に必要な治具をその場で製作
ビジネスでの出張利用者や長距離通勤者をターゲットに、時速320kmで移動するIntercity Express(ICE)は、Deutsche Bahnが提供する主要な旅客サービスです。
30年以上に渡り通勤者の足となってきた第一世代のICE 1車両を、完全改修することが決まりました。現行の車両を解体後、近代的な設備を搭載して一から作り直し、再塗装も行います。
この大規模なモダナイズプロジェクトでは複数の拠点や部署をまたいだ綿密な連携が必要となる他、塗装会社や鍵会社、電気技師など、様々な個別契約が発生します。国内全土にまたがる壮大なプロジェクトの中で、ノイミュンスターの車両センターはハブ拠点として機能します。
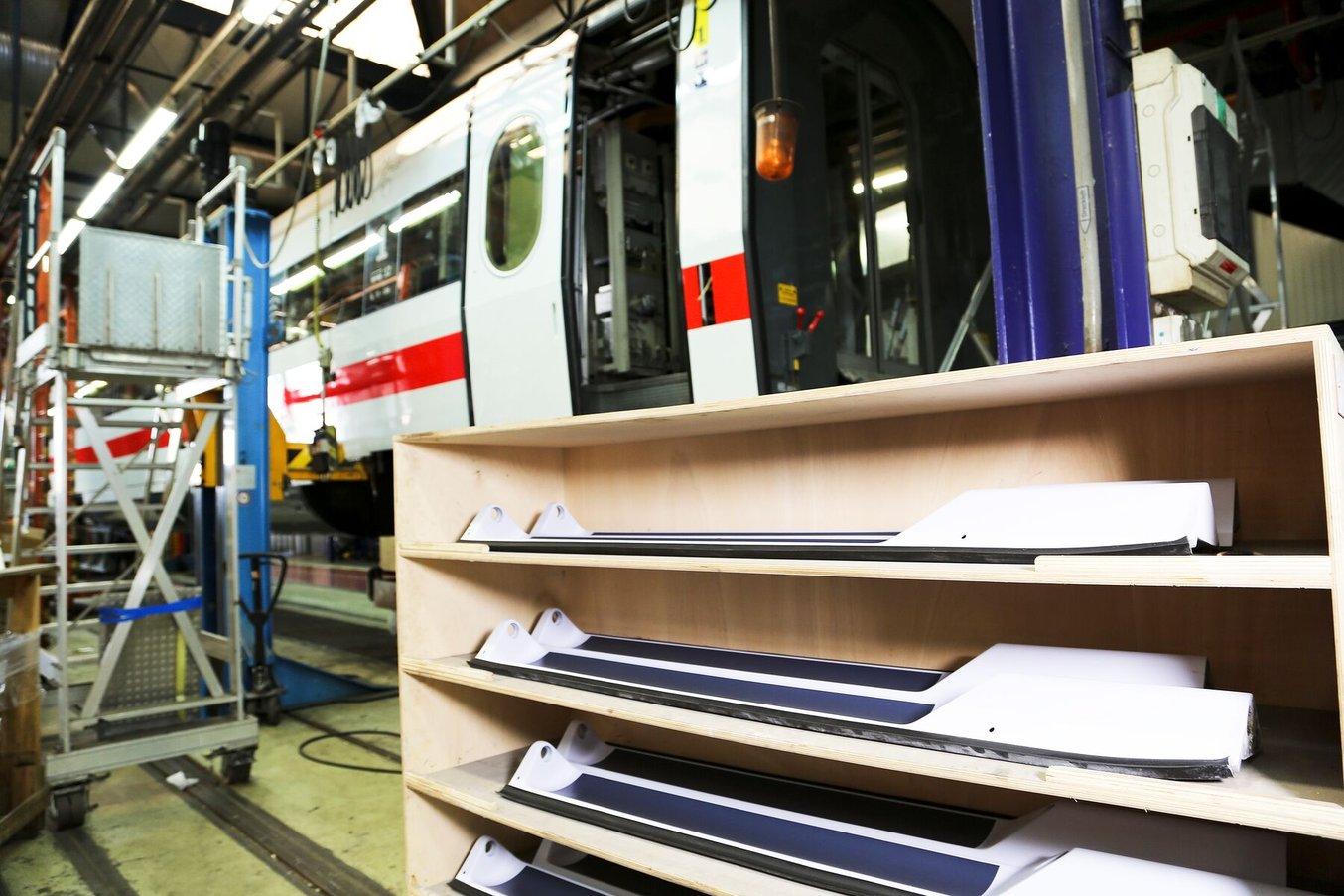
DB Vehicle Maintenanceノイミュンスターは、ICE 1車両の大規模モダナイズプロジェクトに関わる工場の1つ。
「市販の汎用品の治具ですべての作業が賄えるわけではないため、カスタムでの治具製作が必須になります」と、Wolfgramm氏は言います。
各部品の改修や車両の解体・再組立の際には、手順を簡素化することで品質とその均一性を落とさずに作業時間を短縮できる工程がたくさんあります。何十両もの車両をモダナイズする場合、カスタム治具を使うメリットも量に比例して大きくなります。
「この車両センターだけでなく他センターの従業員とも密な連携を取りながら、作業員が計測に長時間費やすことなくピクトグラムの接着や線引き、ドリルでの穴あけ箇所のマーキングなどができるような実用的な治具を大量に開発しています。3Dプリントのおかげで、テンプレートを作って作業を格段に簡素化できるんです」とWolfgramm氏は続けます。
従来、こういった治具を製作する場合、木製の場合は木工工場で木材の切り出し、やすりがけ、切削加工等が必要で、金属製の治具の場合は旋盤やフライスなど、従来型の金属加工機を使っていました。しかし、この方法では製作時間や作業量が大幅に増え、かつ高額になっていまします。
「アディティブマニュファクチャリングでは、とりあえず試作をしてみて、そこから微調整を重ねていくというこれまでにないアプローチが可能です。CADソフトウェアを使ってデジタルで設計するため、うまく合わなかったり変更が必要な場合にもすぐに調整ができます。設計に変更を加えたり、拡縮を行いたい場合には、3Dプリントの中でもパウダーを使った3Dプリントが特に秀逸です」
Deutsche Bahn 製造エンジニア兼アディティブマニュファクチャリング・エキスパート、Carsten Wolfgramm氏
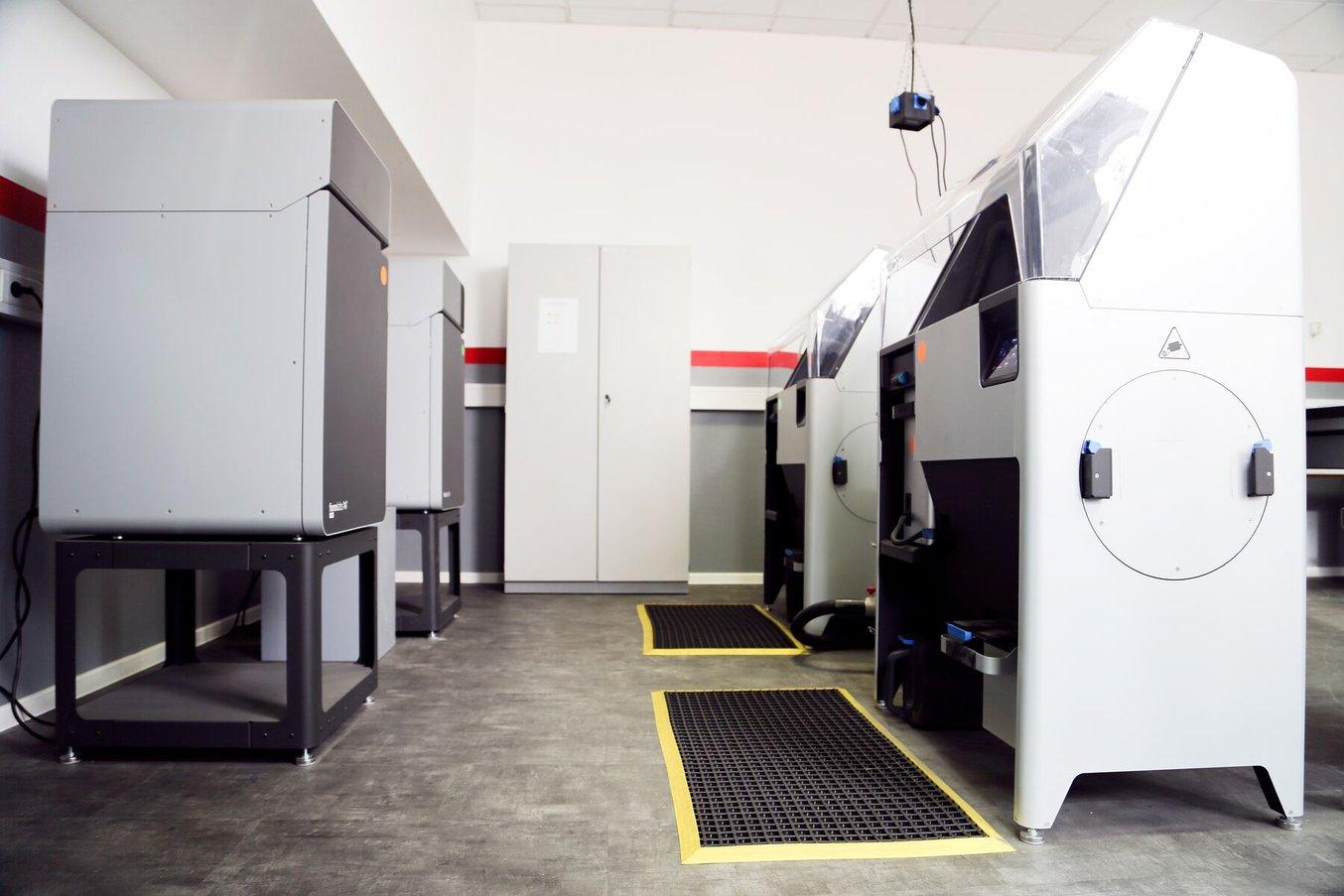
ノイミュンスターの3Dプリント工房には、FuseシリーズのSLSプリンタ2台を含め、10種類の3Dプリンタが設置されている。
Deutsche Bahnは、FormlabsのプレミアムパートナーであるIGO3Dと密に連携しながら、アディティブマニュファクチャリングを戦略的に発展させ、事業のニーズや様々な用途に適したソリューションを特定してきました。
ノイミュンスターの3Dプリント工房には、幅広い技術を搭載した10種類の3Dプリンタが設置されています。そのうち2台はFuseシリーズのSLSプリンタで、1台は高強度ながら一定の靭性を兼ね備えたNylon 12パウダー、もう1台は軟質部品に最適なTPU 90Aパウダー用として運用しています。工房には光造形方式の大容量プリンタForm 3LとForm 3も設置されています。
Wolfgramm氏率いるチームは、コンポーネントに関する問い合わせや要件に応じて最適なプリント方式と材料を選択します。
「Formlabsのプリンタを導入したのは、コストパフォーマンスが非常に優れていたからです。特にSLSプリンタは安定していますし、電源を入れればすぐに使えます。そのおかげで、部品に何度も改良を重ねる際の作業が格段に楽になりました。24時間365日連続稼働してくれます」
Deutsche Bahn 製造エンジニア兼アディティブマニュファクチャリング・エキスパート、Carsten Wolfgramm氏
ノイミュンスターの3Dプリント工房のおかげで、チームは常にアジャイルな姿勢を維持でき、リクエストにもオンデマンドで迅速に応えることができます。Wolfgramm氏は「サプライチェーンや製造期間が長い外注に頼る必要がなくなりました」と言います。
Tost氏もこう説明してくれました。「製造現場に3Dプリンタを常設しておくことで、工場で日々発生するニーズに迅速に応えることができています。事前に様々な用途向けにデザインを作っておき、その場で直接製作し、その後工場で実際の製造に移ります。このような工程が実現できるのは、3Dプリントだけです」
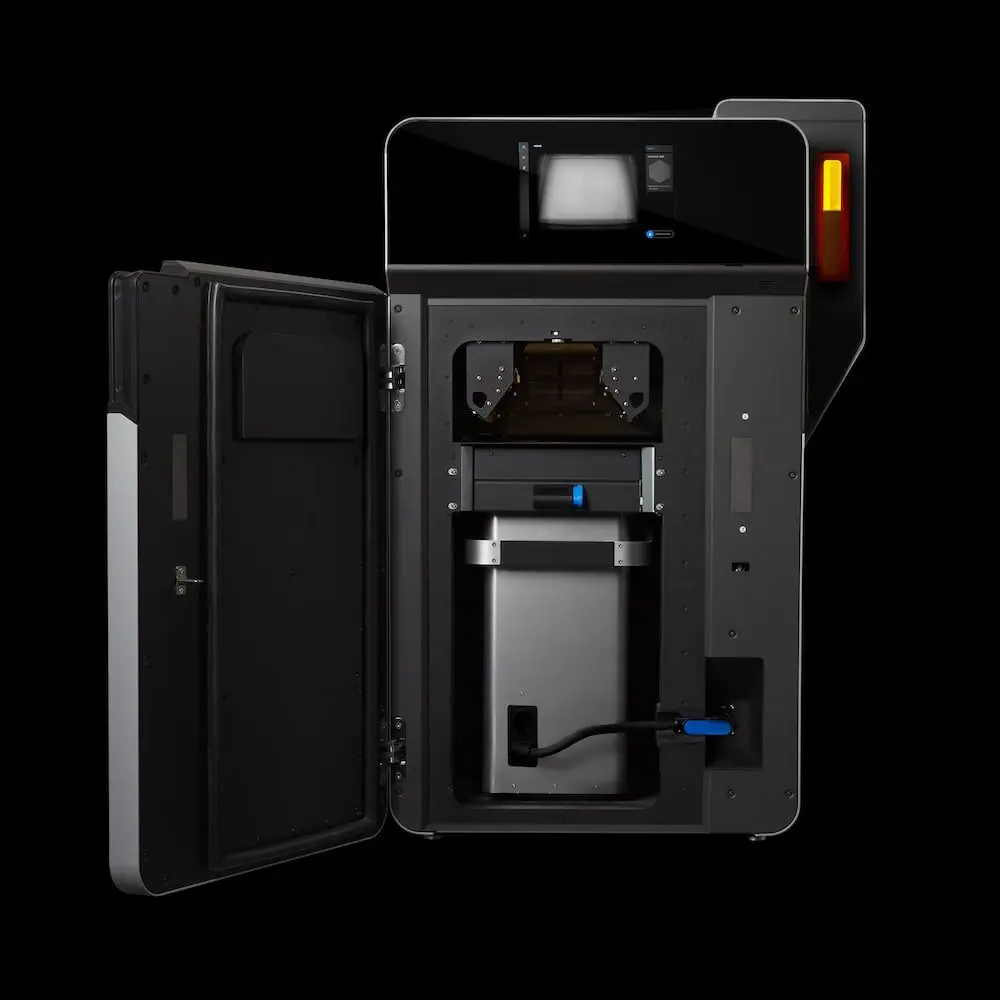
新しいSLS方式プリンタFuse 1+ 30Wで高性能部品を高速製作
本ウェビナーでは、Fuse 1+ 30Wの製品概要やSLS方式3Dプリントの概要をFormlabsのエキスパートがご説明します。
ノイミュンスターにおけるアディティブマニュファクチャリングの活用事例
塗装用のマスキング治具
ICE 1車両の改修作業では、プラスチック製の部品をすべて取り外し、やすりがけ、充填、再塗装を施しました。その部品の1つに、各車両のドアハンドルの後ろに取り付ける溝付きのプラスチックパネルがあります。すべてのパネルでデザインを刷新し、新しい車両では2色塗装を施すことになりますが、暗い色のセクションには泥や使用痕跡にも耐えられるような耐久性の高さが必要です。
カーブのある形状や複雑なカラーデザインに沿って塗装をする場合、均一な仕上がりを実現するためには、作業者が適切にマーキングや表面のマスキングができるよう、折り畳み式の定規やキャリパなど非常に念入りな準備が必要です。
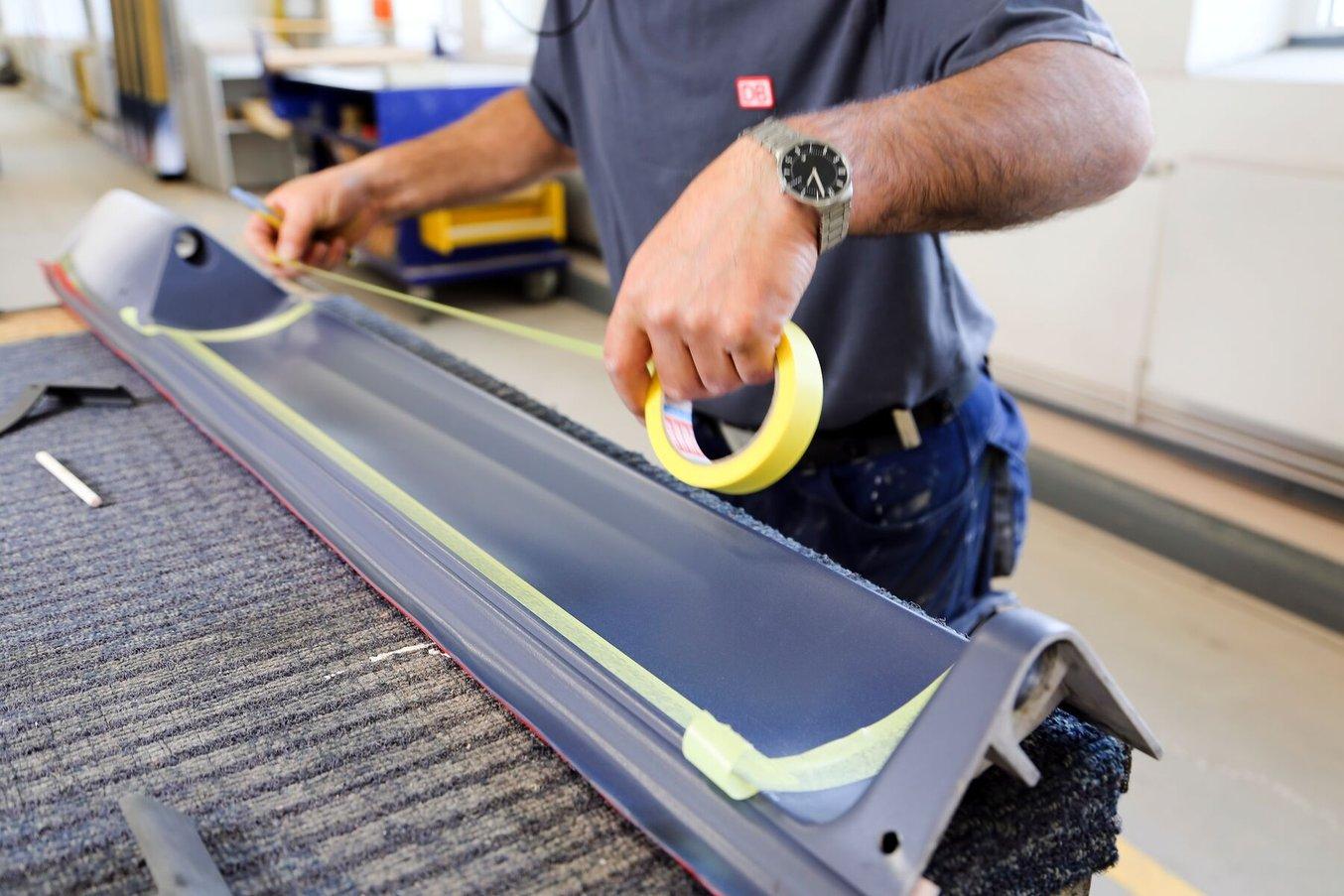
有機的な形状をマスキングする場合、従来は時間をかけて手作業で行っていた。
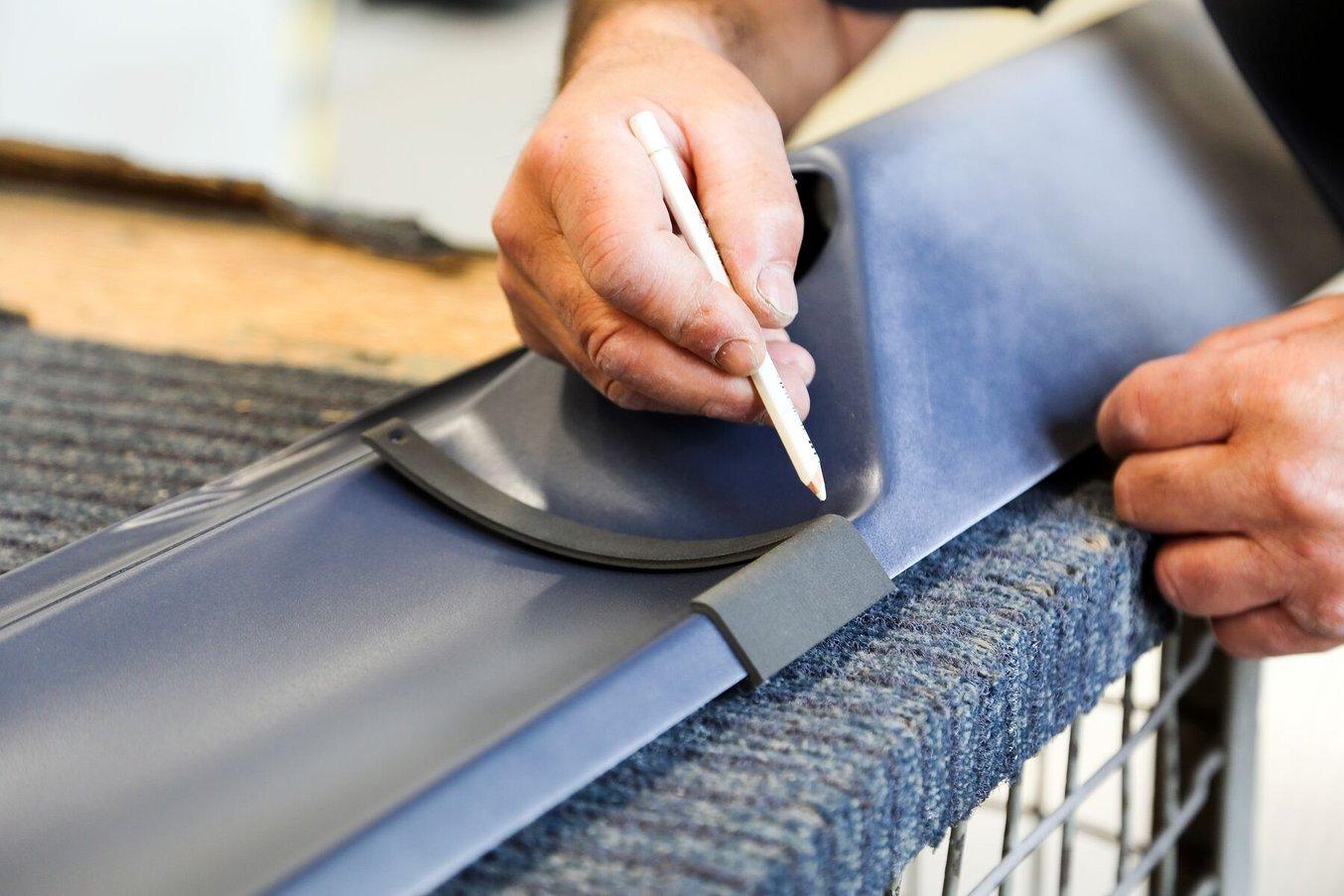
3Dプリント製のマスキング治具により、計測にかかる時間を大幅に削減できる。
「3Dプリントのおかげで、ステンシル製の部品を簡単に開発できるようになりました。一度作ってしまえば、他の工場や作業場所でも様々な方法で使用できます。これまでは30分掛かっていた塗装作業を、僅か2分にまで縮めることもできました」とTost氏は言います。
3Dプリントは従来の治具製作と比較して設計の自由度が高いため、特定の作業にフィットする複雑な形状の治具も製作が可能です。「アディティブマニュファクチャリング、特にSLS 3Dプリントでは、半径や突出部などの複雑な形状も実現できます」とWolfgramm氏は付け加えます。
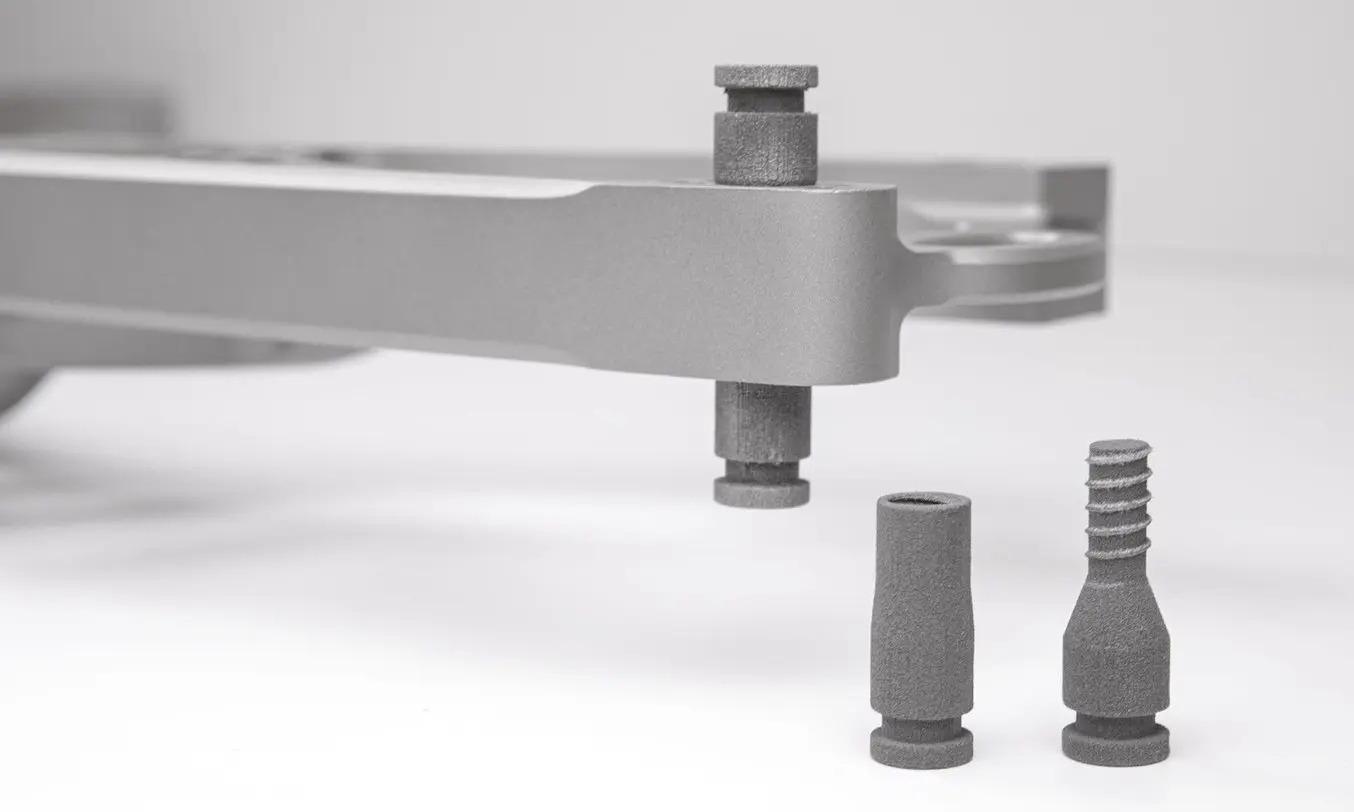
3Dプリント製マスキング治具の総合ガイド
本製品仕様では、3Dプリント製のマスキング治具で塗装、コーティング、めっきがけなどの表面処理にかかる作業時間やコストを削減しながら、新しい複雑な形状や表面品質を実現する方法をご紹介します。
手荷物棚の保護カバー
車両の解体後は、手荷物棚も取り外します。改修後、壁の塗装と箔の貼り直しが終わったら、元の場所に設置し直します。手荷物棚はサイズも重量も大きく、さらに棚と壁の間には僅かな隙間が空いています。そのため、傷や衝撃から保護できるような軟質材料が必要でした。作業者が誤って壁に傷をつけてしまった場合、高額かつ時間のかかる再作業が必要になります。DBはカスタムメイドの保護カバーを設計し、Fuse 1+ 30WプリンタでTPU 90Aパウダーを使って3Dプリントしました。
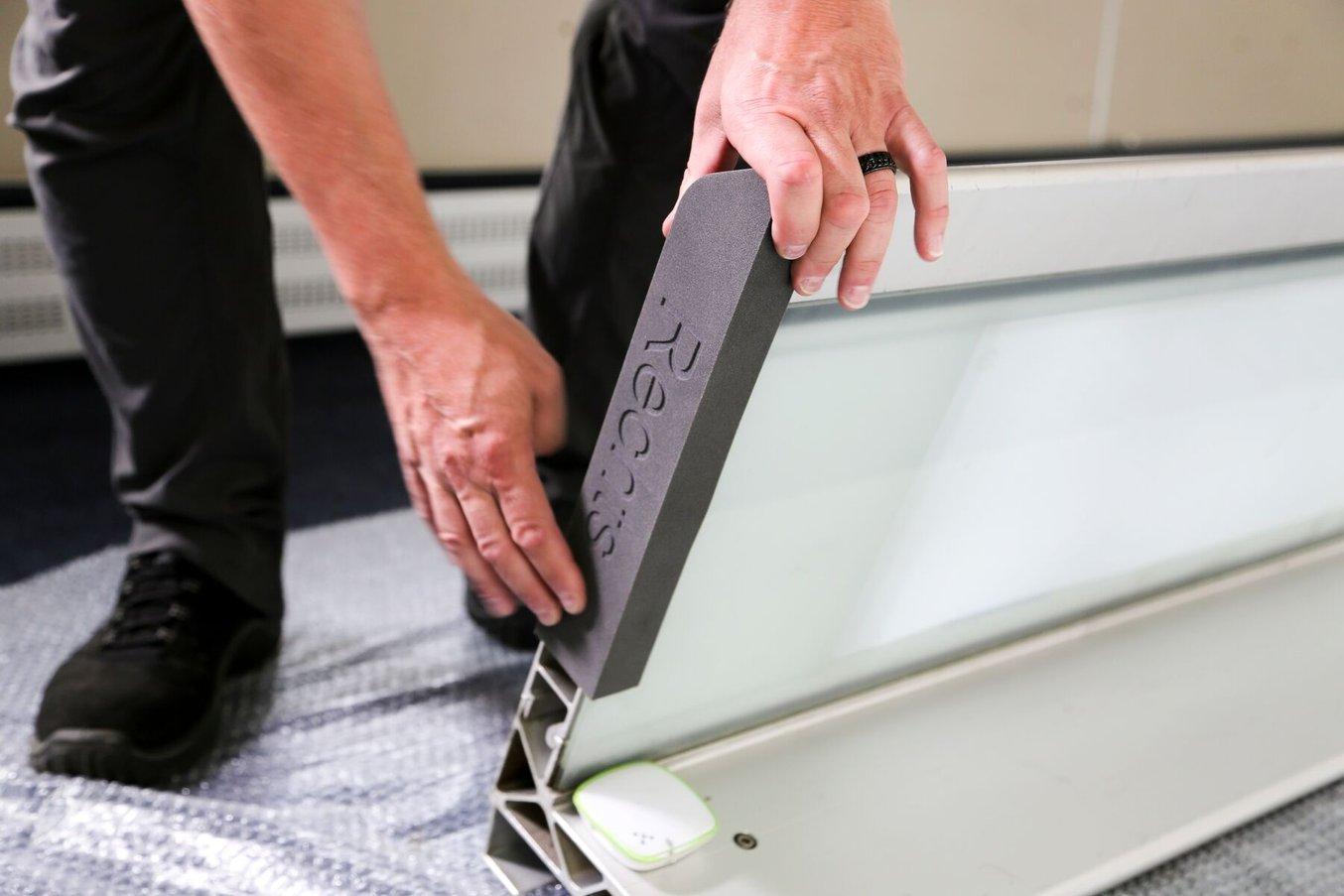
軟質材料のTPU 90Aパウダーを使って傷や衝撃から守る保護カバーを製作。
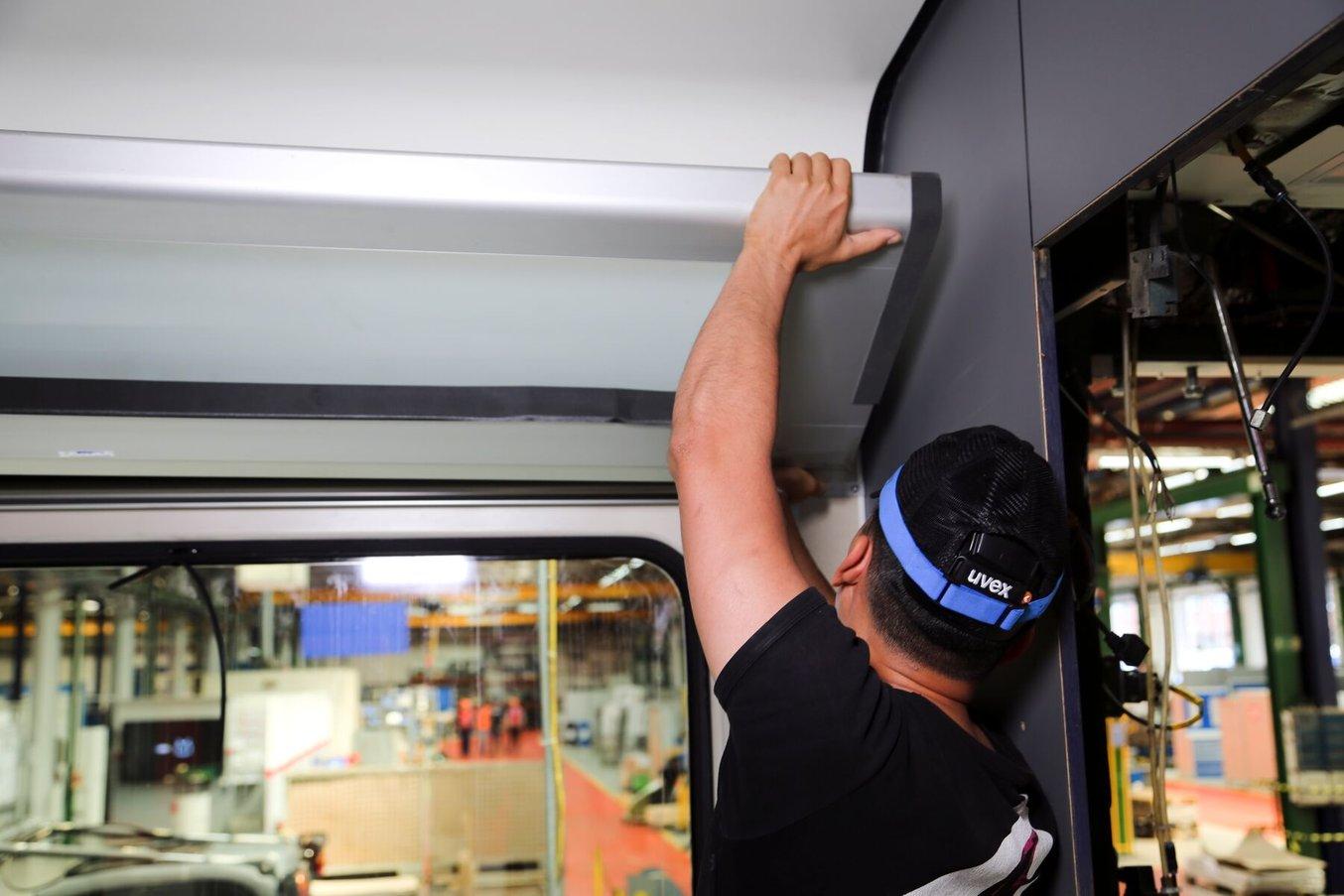
SLS 3Dプリントにより、手荷物棚と壁の隙間にフィットするスリムなデザインを実現。
「傷防止カバーを3Dプリントで製作するまでは、緩衝材や同様素材の治具を使って従来の方法でマスキングをし、傷をつけないようにしていました。でも、この方法が常にうまくいくとは限らないのです。新しく開発したTPU部品のおかげで、今回初めて傷をゼロにすることができました」とWolfgramm氏は言います。
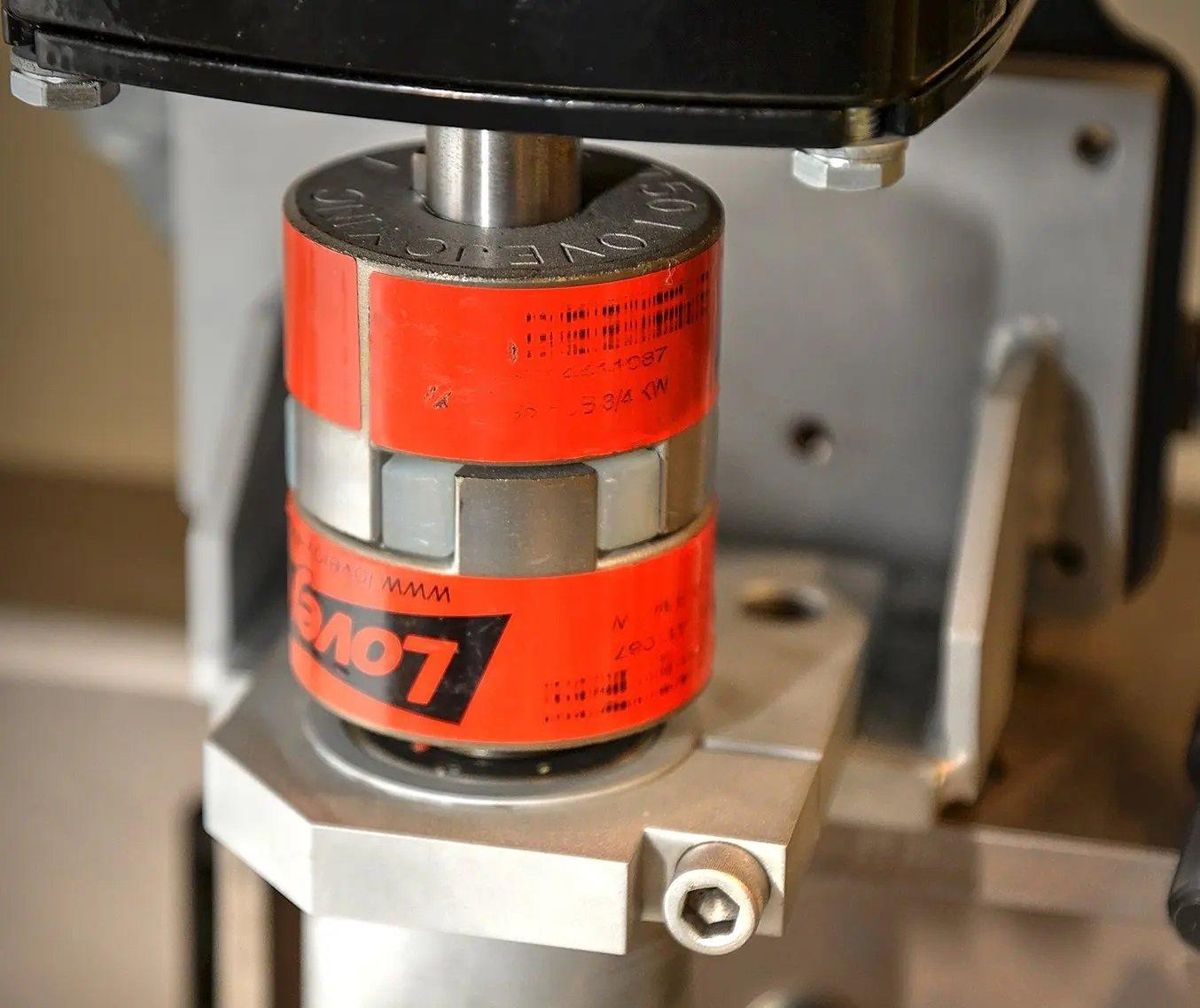
3Dプリント製の治具で生産効率をアップ
本ウェビナーでは、3Dプリントを活用してカスタムメイドの治具や固定具、金型を内製することで、生産工程を合理化し、生産コストを削減する方法をご紹介しています。
ケーブルガイド用カバーキャップの試作品
30年以上前に製造されたICE 1の車両の中には、今では製造終了となっている部品もあります。改修作業中、チームは座席の下に取り付けられている電源ソケットに向けてケーブルを保護・ガイドするカバーキャップの多くが清掃中に破損・紛失していることに気づきました。カバーキャップはカスタムメイドの部品のため、代替品を見つけることは容易ではありません。
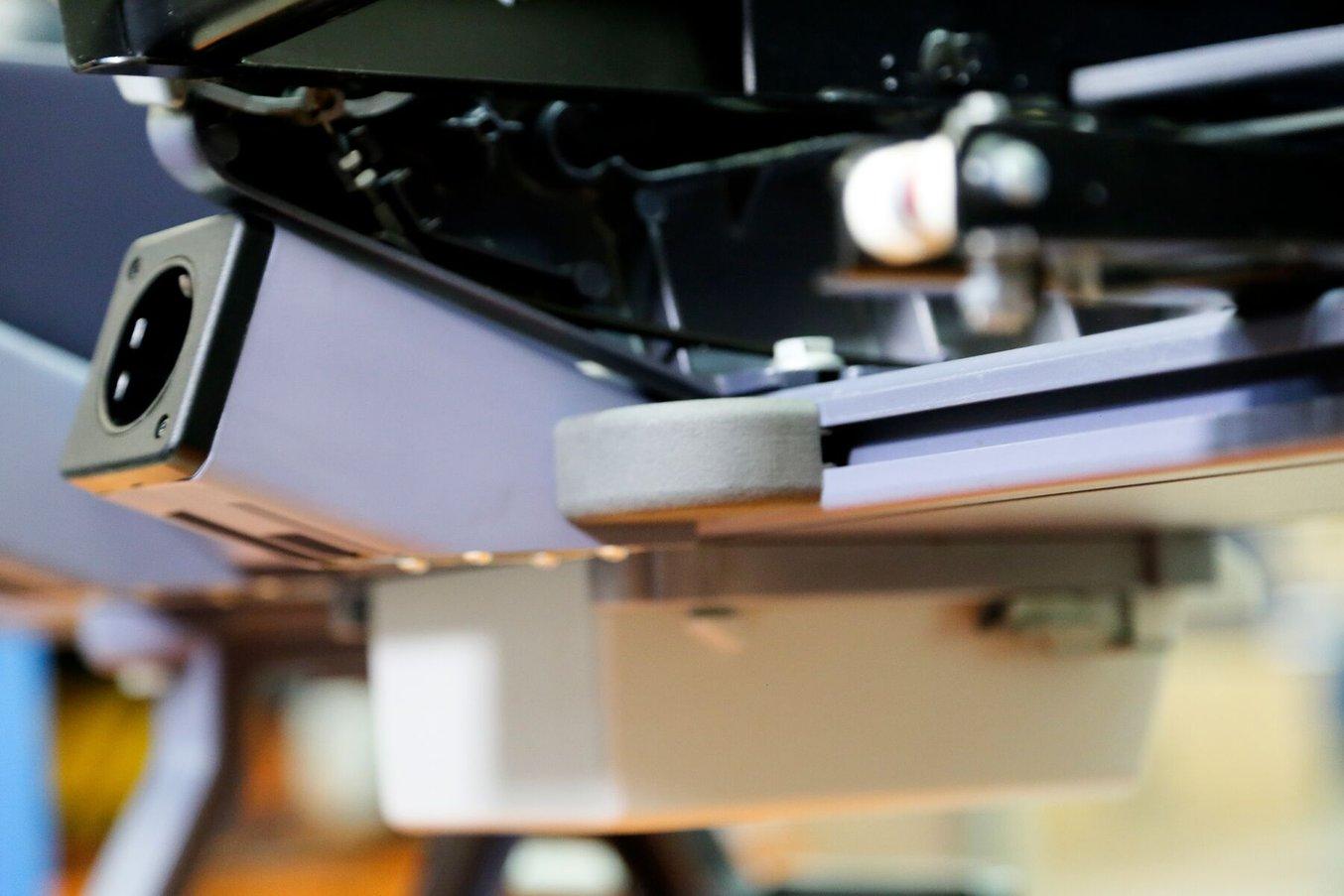
ICE 1車両では、電源ソケットに向けてケーブルを保護・ガイドするカバーキャップの多くが紛失していた。
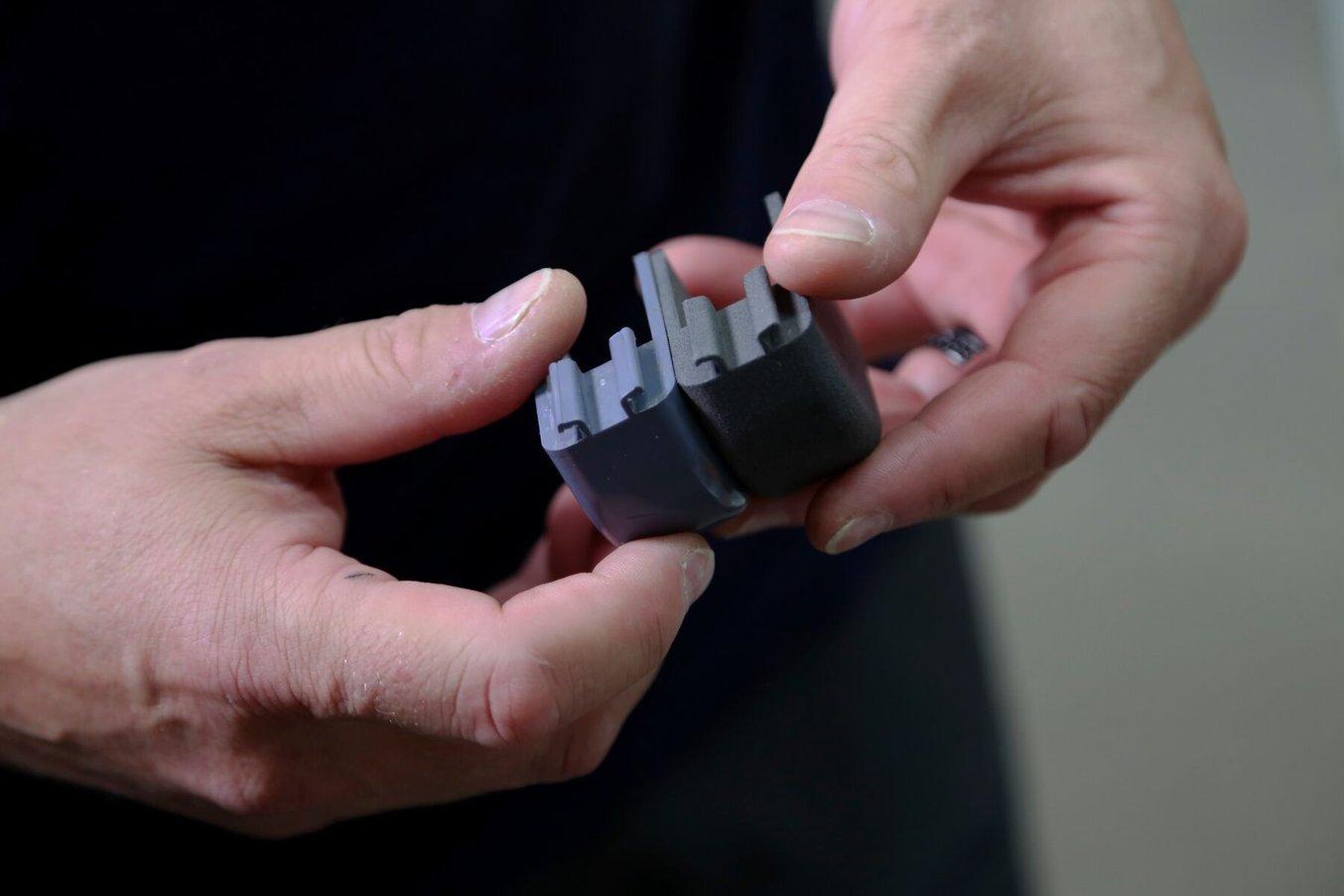
DBは、既存部品をリバースエンジニアリングし、試作品を3Dプリントして検証。実際の寸法とのフィット感を確認した。
「DB Groupが再設計したカバーキャップを、私たちがNylon 12パウダーでの3Dプリントで試作品を作り、フィット感を検証して実際の寸法を確認しました。2つ目のバージョンでは既に完璧にフィットするものが出来上がっていて、スライドさせて簡単に取り付けることができました。SLSプリントで広がる可能性は素晴らしいものばかりです。フィット感、スピード、材料の硬度も十分で、色々な試みができます」とWolfgramm氏は説明してくれます。
手持ちスキャナの携帯ホルダー
治具の活用で、様々な工場で働く従業員の日々の業務を簡素化できます。材料管理部門で働くDB Fernverkehrの従業員は、材料の特定・管理のために手持ちのスキャナを使っていました。常にスキャナを持ち運び、何かを拾いあげたり両手を使いたい場合にはスキャナをどこかに置かなければなりません。
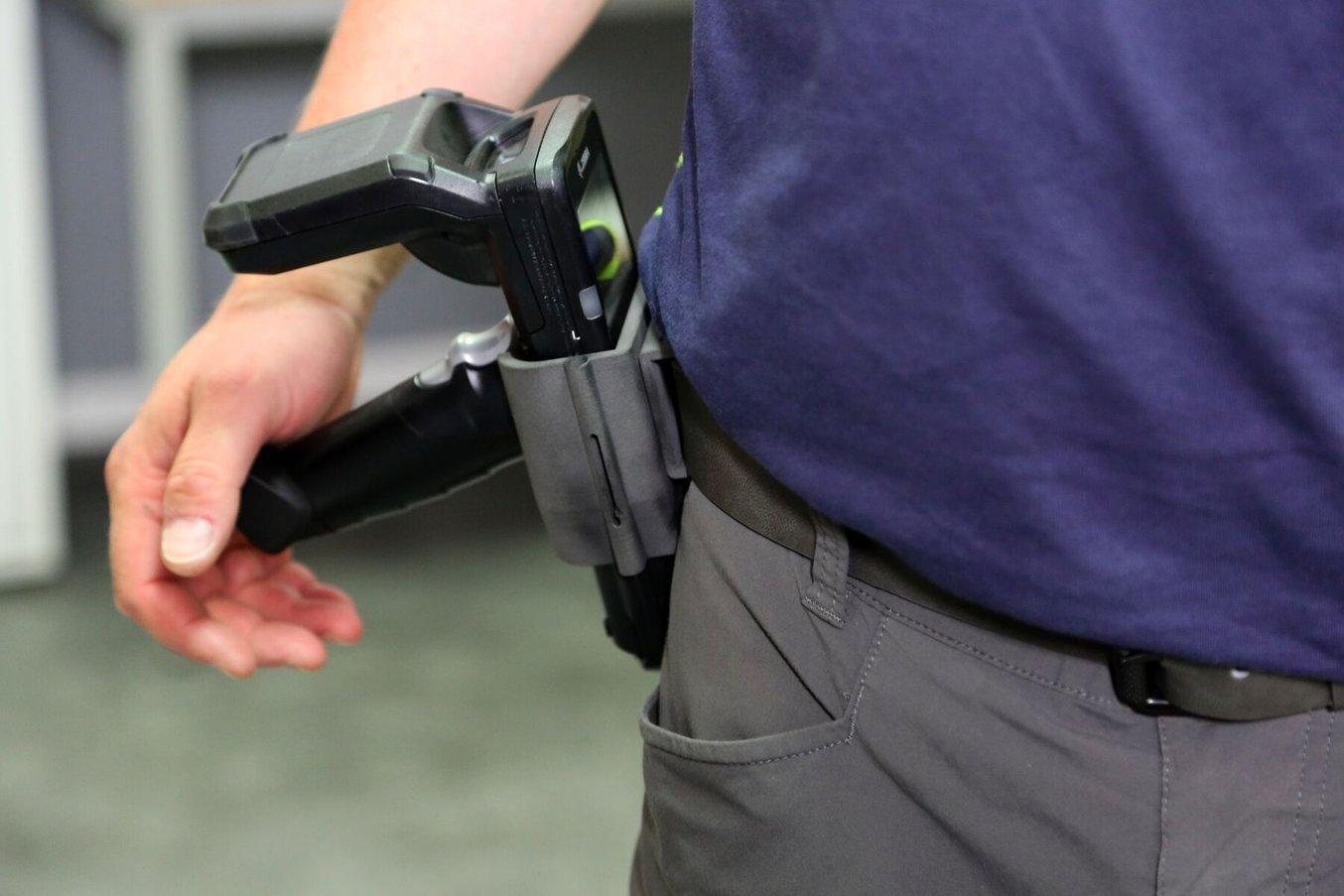
材料管理部門の従業員は、両手を自由に使える状態を保ちながらスキャナを持ち運べる方法が必要。
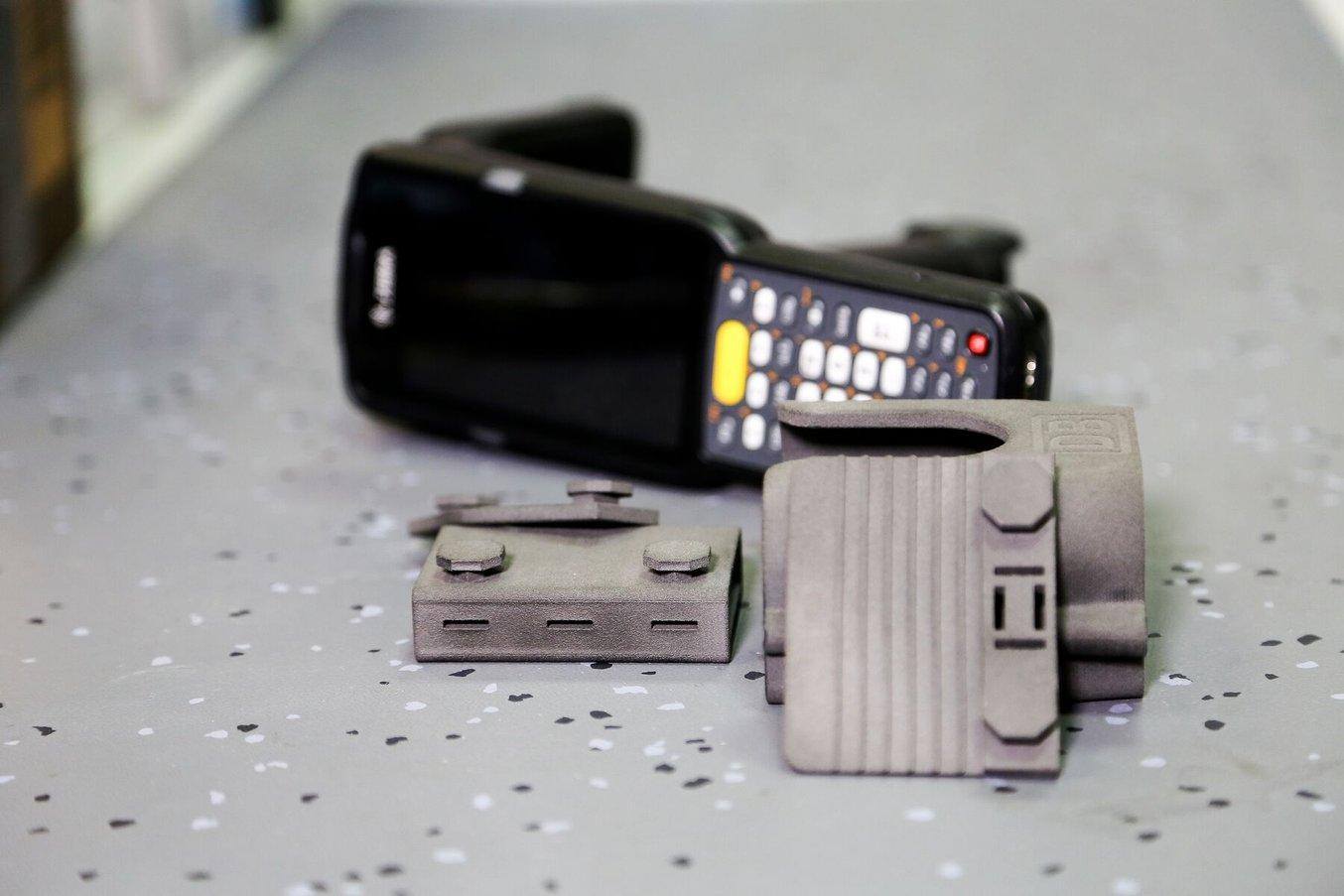
チームは、バッグ、ベルト、シャドウボードに取り付けられる3種類の装具を製作。
「ある時、彼らに聞かれたんです。『このハンディスキャナの取り回しがもっと楽になるようなマウントを作れないかな?』と。最終的に、バッグ、ベルト、シャドウボードに取り付けられる3種類の装具を製作しました。SLS 3Dプリントならほぼ完璧にフィットするものがプリントできますし、サポート材が不要なのでパウダー除去やブラスト処理以外に長い時間をかけて後処理をする必要がありません」とWolfgramm氏は言います。
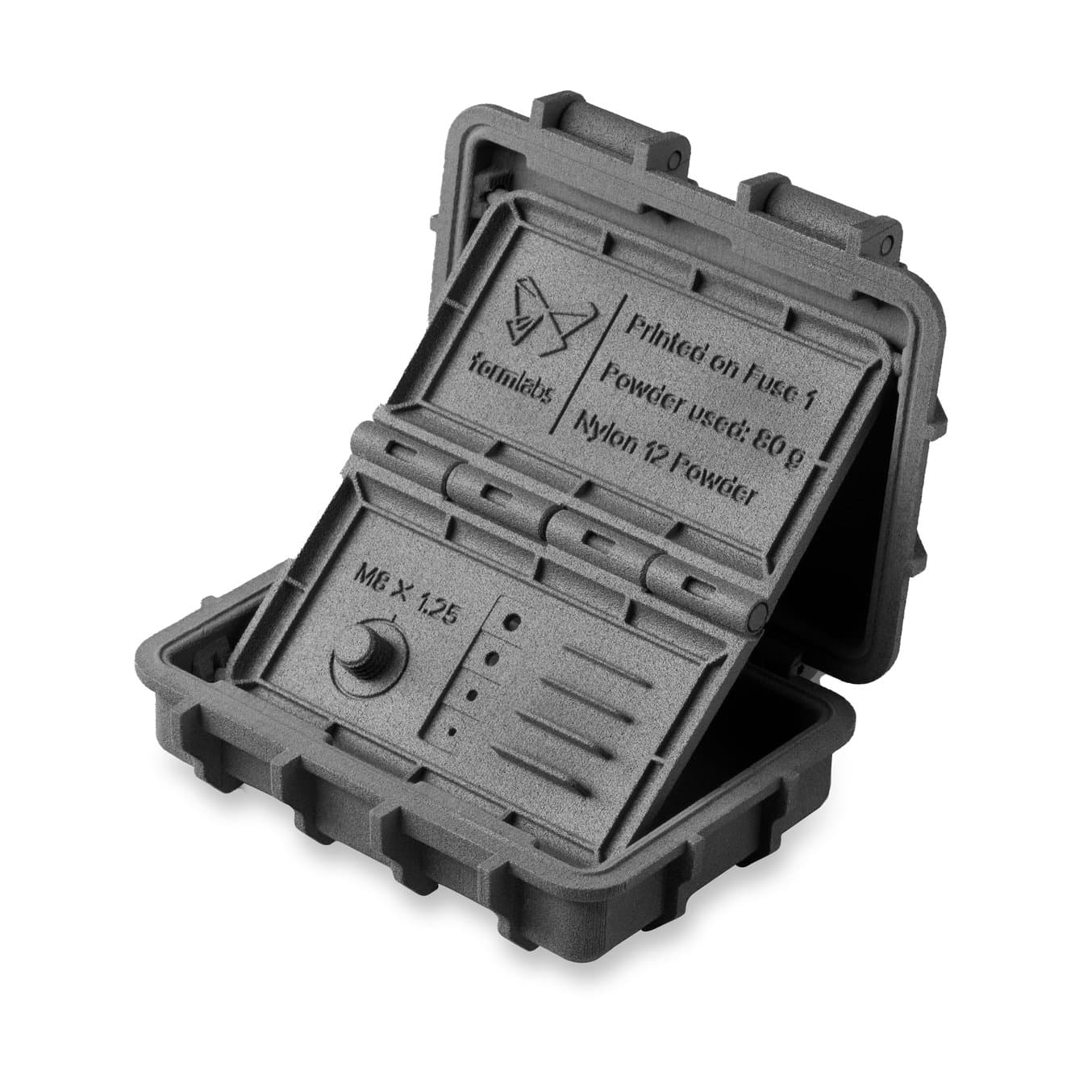
未来に向けて車両メンテナンスをデジタル化
「アディティブマニュファクチャリングはこれからも活用し続けます。従来型の加工では実現できなかった複雑な形状の部品も製作できますし、高額な追加コストを払うことなく治具の製造や再生産を行えます。治具や部品を一度デジタル化してしまえば、世界中どこでもプリント可能なことも魅力です」とWolfgamm氏。
もちろん、最終的な目標は3Dプリント製の部品をより実製品に近い用途で使用することです。しかし、列車の生産には飛行機と同じくらい、時にはそれ以上に厳しい安全規制が求められます。現時点で最も厳しい安全規制を満たせるのは、生産現場に設置する工業用FDMプリンタだけです。Deutsche BahnはFormlabsや他のパートナーと提携し、将来的にこれらの厳しい安全規制を満たせるような作業手順や工程、材料の開発を目指しています。
「我々の目標は、2030年までに車両メンテナンス用の予備部品の10%をデジタル化することです。それが実現できれば、ニーズに応じて僅かな時間で部品を再製造し、部品を短期納品できるよおうになります。また、グリーンな企業としてエコに配慮しながら材料や資源を管理できれば、その他の課題も解決できると考えています」