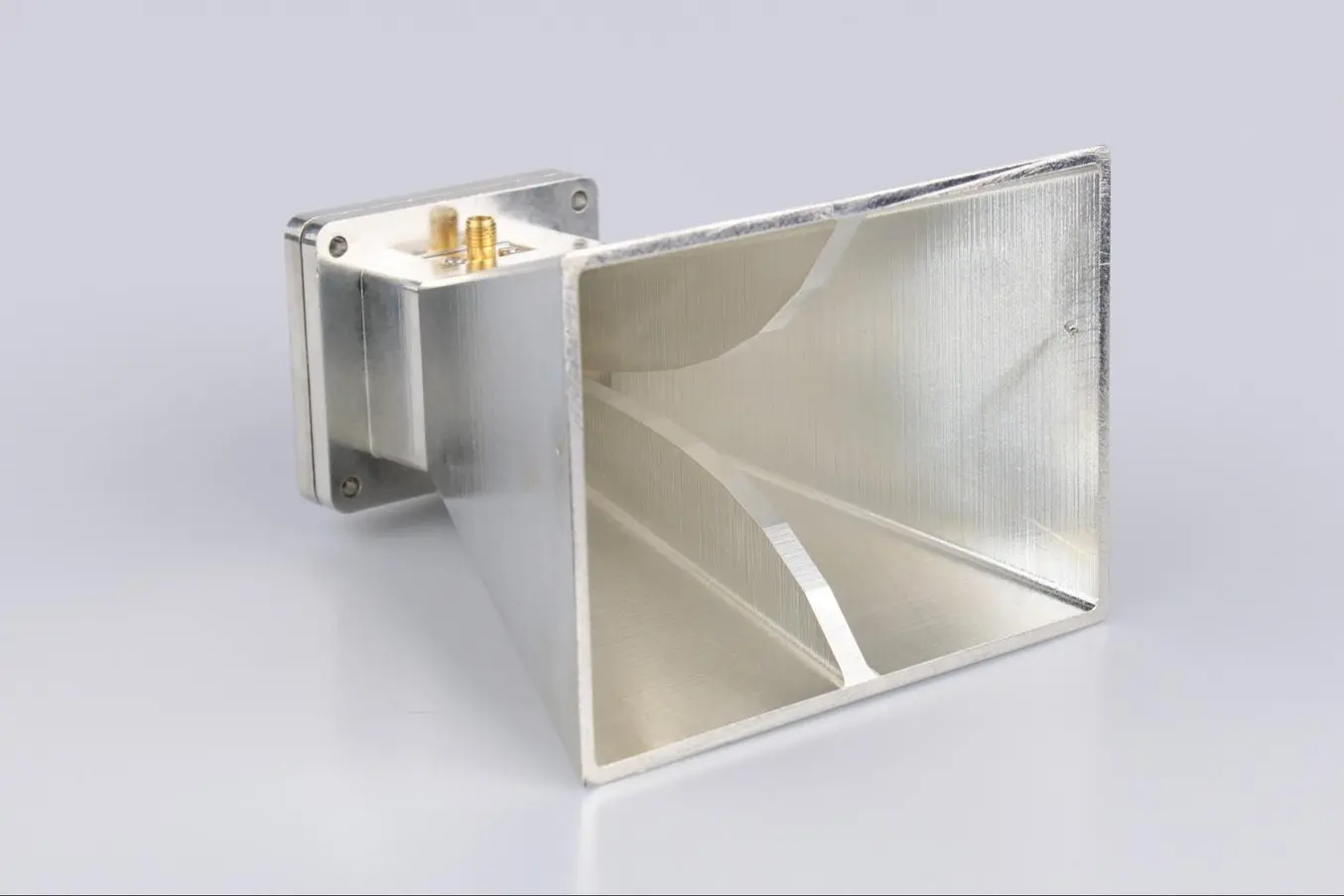
フランスのブレストに拠点を置くElliptikaは、高周波やマイクロ波の製品およびソリューションの設計・開発を専門とする企業です。同社は最先端のカスタムフィルターやアンテナを設計しており、これらの製品は自動車、防衛、医薬品、教育業界において、Thalesなどの企業で研究開発に利用されています。
アンテナに対してコンパクトさや極めて高いゲインなどの厳しい要件を満たしながら、コストを低く抑えて設計を素早く納品するために、同社は従来の製造技術の限界を超える必要に迫られました。
Elliptikaの高周波設計者であるGwendal Cochet氏とAlexandre Manchec氏が、3Dプリントと電解めっきを利用して高性能アンテナを製造し、コストとリードタイムを90%以上削減した方法についてご紹介します。
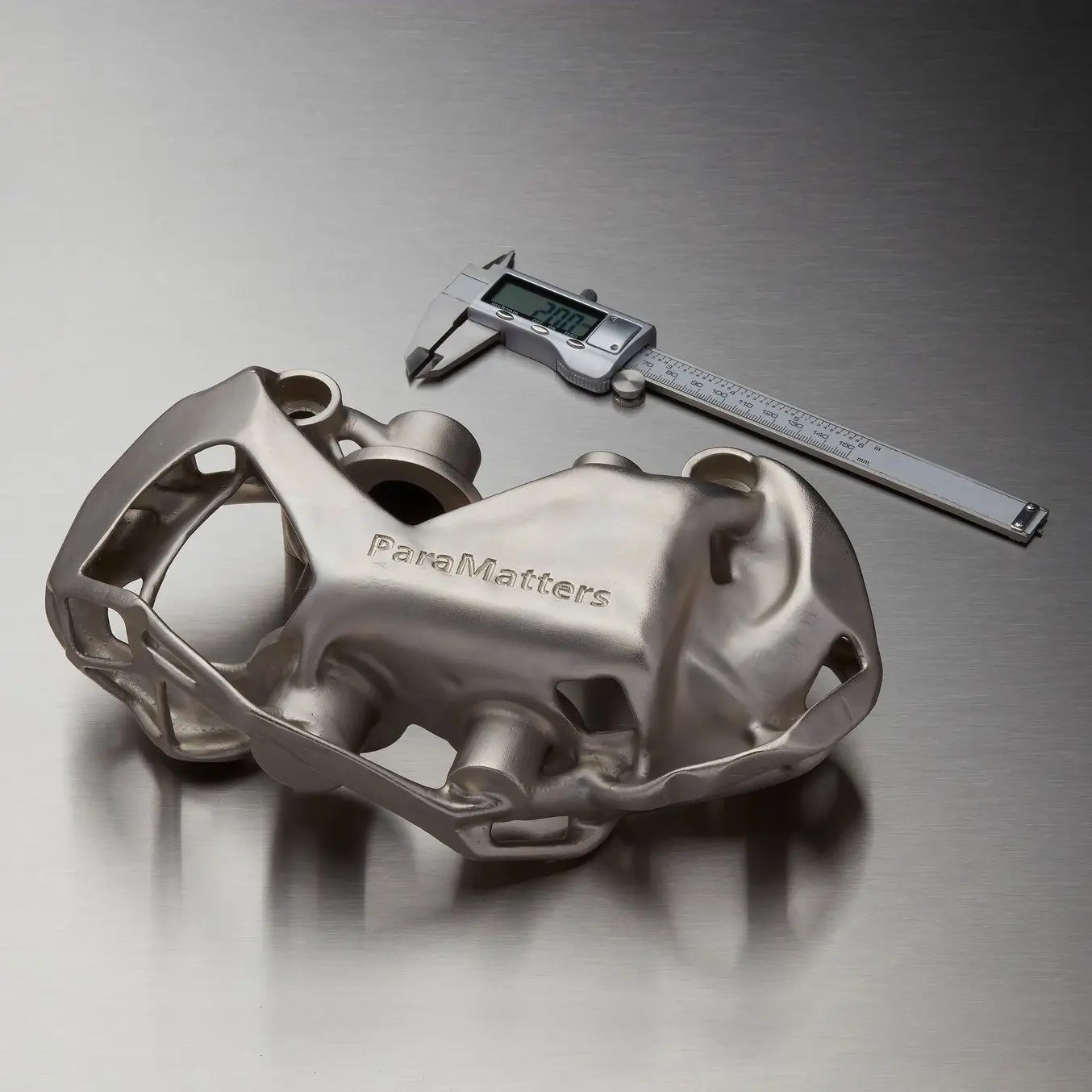
金属並みの強度: SLA方式でプリントしたパーツの電気めっきの方法と使用事例
レジンの3D造形物へのメタルコーティングに取り組むエンジニアの事例と、金属でハイブリッドコーティング処理したエンドユースパーツの強度や耐久性の向上、そしてこれによって広がる(その他多数の)用途について説明しています。
3Dプリント品に対する電解めっき処理
アンテナには、電波を伝えるための導電性が必要です。3Dプリント製の樹脂部品は原則的に絶縁性ですが、デザインの自由度はほぼ無限で、材料には優れた機械的および熱的特性があります。このようなメリットを電解めっきと組み合わせることで必要な導電性を実現し、カスタム品のアンテナを製作する素晴らしいソリューションを実現できます。
Elliptikaは、さまざまな3Dプリントの造形方式を検討した結果、 SLA光造形方式が電解めっきに最適であるという結論に至りました。
「表面粗さによる電気信号のロスを避けるため、RF部品の表面は滑らかである必要があります。そのため、たとえば1層ごとの厚みが大きくなるFDM(熱溶解積層)方式を使うと、問題が発生します。ロスが増えるだけでなく、造形品の表面粗さが原因でめっき処理の工程中、金属の被覆が付かないという問題が発生します。SLA光造形でのプリント品では、そのような問題は発生しませんでした。」(Gwendal Cochet氏)
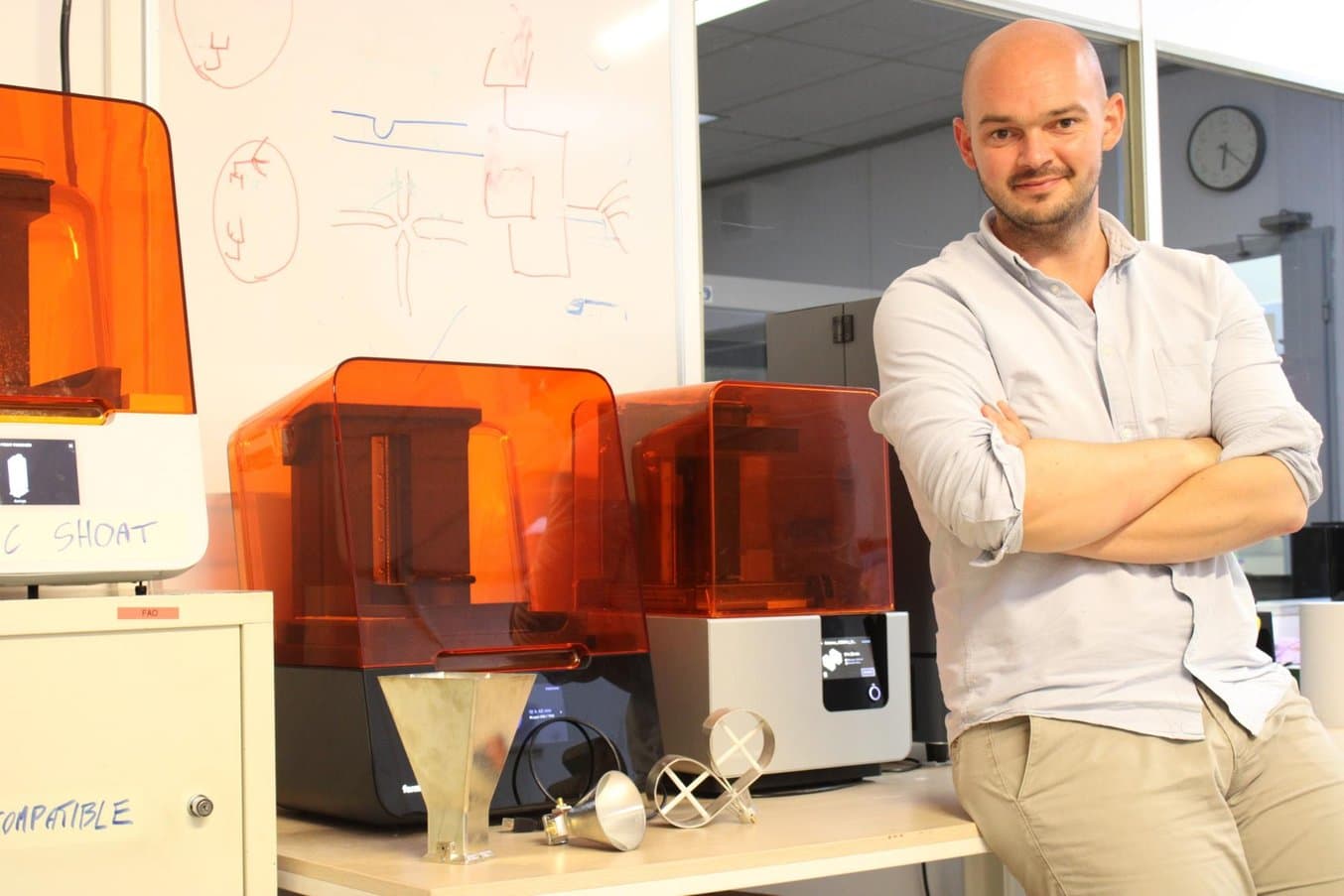
当初はFormlabsのSLA光造形プリンタ、Form 2でプロジェクトをスタートした同社ですが、後にその後継機であるForm 3を購入したほか、最近では新型コロナウイルスのパンデミック救済プロジェクトをサポートするため、7台のForm 3Bプリンタを追加導入しています。電解めっき用のプリントには主にスタンダードレジンの1つ、Whiteレジンを使用していますが、機械部品ではTough 2000レジンとHigh Tempレジンでの造形品への電解めっきも行っています。
めっき処理の工程は以下の通りです:
「造形品を3Dプリントした後、サポート材を取り除き、表面を洗浄して二次硬化を行います。次に、化学品を使用してプリント品に薄い銅の被膜(約3μm)をめっきします。最後に造形品の表面仕上げを行います。例えば、厚手のすずの被膜を加える等です。」(Cochet氏)
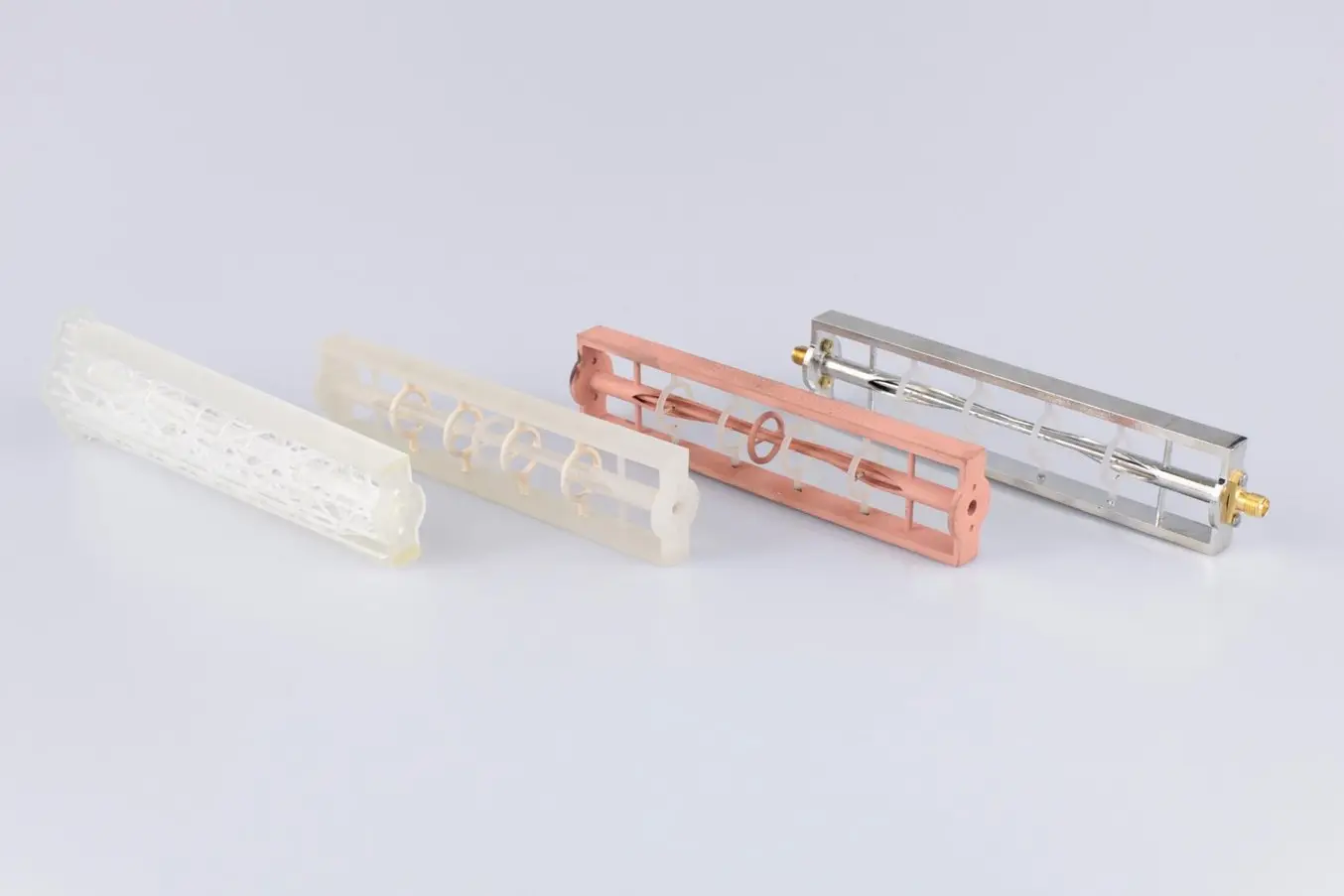
電気めっきの過程。左から順に:3Dプリントされたプラスチックパーツ、サポート構造の取り外し後に二次硬化したパーツ、銅で電気めっきしたパーツ、スズのコーティングをまとい電気めっきを完了した最終パーツ。
コストとリードタイムを90%以上削減
殆どのアンテナは研究開発目的で使用されるため、Elliptikaは通常、1~20個程度の小ロットでの製造を行います。
「我々にとって3Dプリントは大変興味深い存在です。なぜなら、複雑なアンテナを極めて安価に製作できるからです。もう切削や射出成形などの従来工法に手を出そうとは思えません。」(Alexandre氏)
切削や成形での従来工法では、1本のアンテナを製作するのに3か月程度は要していました。これには金型製作のためだけの期間や、製品設計の詳細について外部委託先とやり取りする膨大な時間も含まれます。
「内製で3Dプリントができれば、2日で製品が出来上がります。プリントに1日、めっきに1日で、もう完成です。比較にならないほど早くできてしまうんです。価格面も大きな違いです。外注の場合、アンテナ1本を製造するのに約3,000ユーロもかかりますが、プリントすれば20ユーロ程度ですむからです。(3Dプリンタのコストを考慮すると)このアンテナを作るためのコストは、すべて1回の作業でまかなえます。」(Cochet氏)
アンテナを製造する | コスト | リードタイム | ||
---|---|---|---|---|
SLA方式3Dプリン外部委託ト | 20ユーロ | 2日間 | ||
外部委託 | 3,000ユーロ | 最大3か月 |
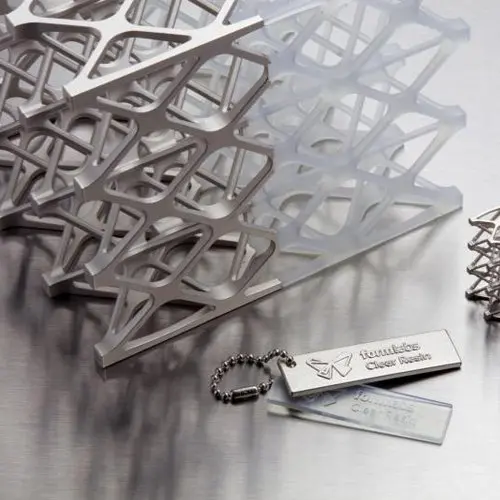
3,500ドルのプリンタで金属3Dプリントに限りなく近い造形品
このウェビナーでは、電気めっきによっていかにSLA方式3Dプリントの材料の幅が広がり、高剛性で耐摩耗性の最終製品用パーツの製造が可能になるかについてご説明します。
カスタマイズと製品開発の高速化でチャンスを掴む
3Dプリントのスピードにより、同社は新たなチャンスを獲得することにも成功しています。
「3Dプリントを導入する前は、PCBアンテナとフィルターしか取り扱っていませんでした。今では、比較的大型のパーツも作っています。以前から理論的には可能でしたが、我々のような小規模企業には不可能でした。お客様のためを思うと、新しいアンテナを極めて迅速に開発しなければなりません。しかし3Dプリントを導入するまでは、新しいアンテナの開発と製作に、時間もコストもかかりすぎていたのです。」(Cochet氏)
「3Dプリントでは、要件に応じたカスタムが簡単に行えるので、極めて具体的な仕様の試作品を、高速かつコスト効率よくお客様にお届けできます。また、重量や体積が非常に重要な要件である場合もあります。機械加工のアンテナではできないような、非常に狭いスペースに設置するアンテナを作ることもできます。機械加工でアンテナを作る場合、通常はいくつかの部品を作り、それをアセンブリすることになりますが、往々にして3Dプリントでの1パーツよりも遥かに大きくなってしまいます。」(Cochet氏)
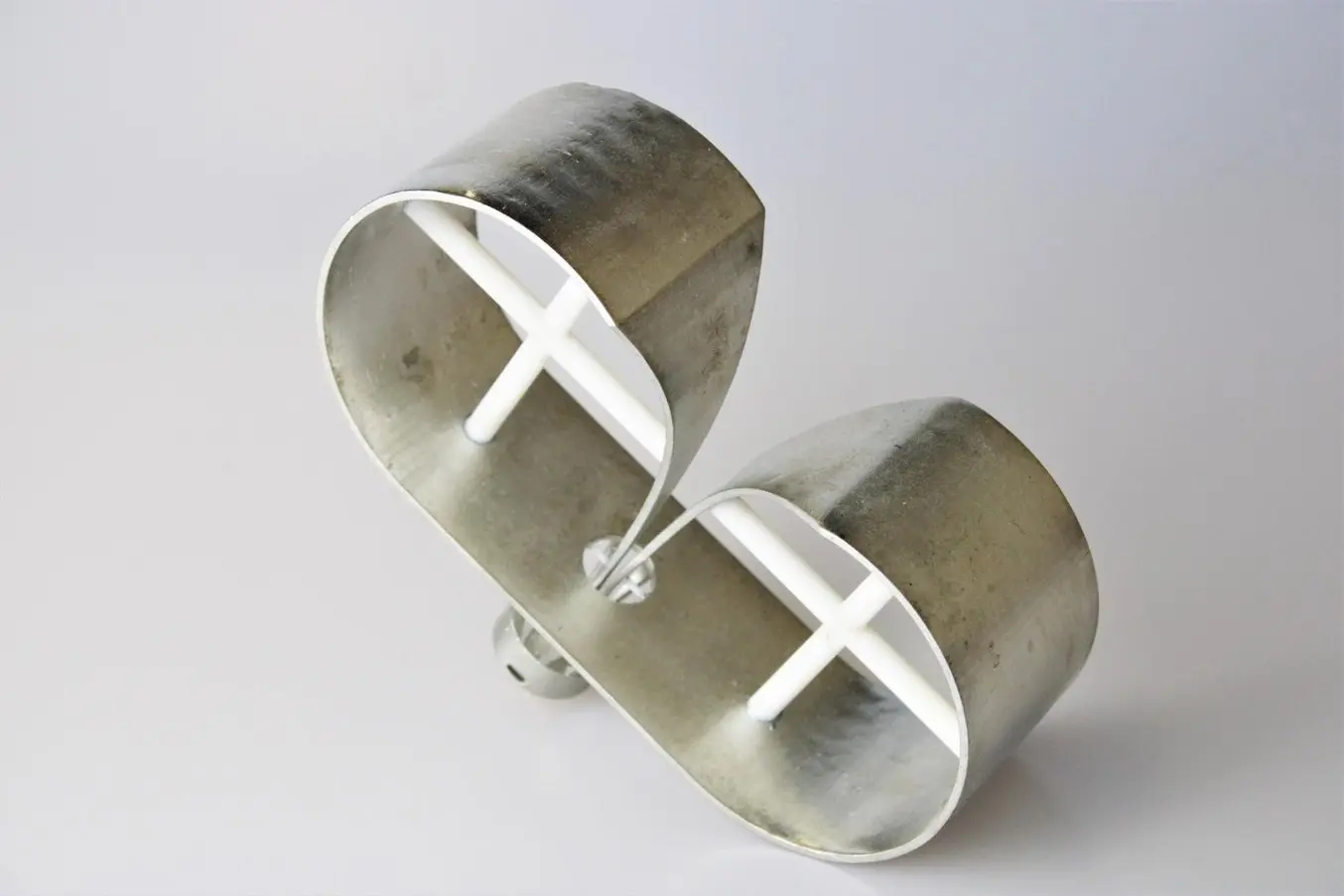
3Dプリント後に電解めっきが選択的に施されたTEMホーンアンテナ(Elliptika研究開発エンジニア、Julien Haumant氏による設計)。
「例えば、我々が作るアンテナには複雑なアール面で構成された非常に複雑な形状のものがあります。3Dプリントだからこそ、この装置がわずか75グラムの部品1点で製作できるんです。こうしたアンテナを切削で作ると、いくつもの部品に分割し、重量も重く、サイズも10倍から20倍になってしまうんです」(Cochet氏)。
電解めっきの活用法についてもっと知る
3Dプリントしたパーツへの電気めっきには多くの用途があり、フォルクスワーゲン社やオートデスク社は、これらの技術を使用して近未来的なコンセプトカーの美しいホイールキャップを製造しました。また、スイスの研究者はビームスプリッターなどの高度な実験装置を作成したほか、多くの企業がプラスチックの3Dプリントに電気めっきを施し、金属の強度を誇る複雑なパーツを安価に作成しています。
RePliForm社の社長兼創業者であるショーン・ワイズ氏をお招きした無料の教育用ウェビナーをご覧ください。RePliForm社で同氏とそのチームが電気めっきを活用し、3Dプリントを幅広い用途に応用している方法をご紹介します。また、電気めっきとSLA方式3Dプリントへの具体的な応用、および電気めっき3Dプリントの完成品を作るためのさまざまなプロセスについても説明します。