Plastinaxは、1976年の創業以来、世界の名だたるブランドにアイウェアを提供してきました。世界中の顧客に製品を提供する同社では、サングラスやメガネフレーム、保護メガネのフレームを設計し、その後の量産で毎月8万点〜10万点ものフレームを射出成形で製造しています。グローバル市場で競争力を保つためには製作期間や迅速な対応が最も重要視される中、Plastinaxでは設計・製造工程を高速化することで、拠点とするモーリシャスから全大陸に散らばる顧客のもとにメガネフレームを届けてきました。
ENL Group傘下のPlastinaxでは、FormlabsのSLA光造形方式3DプリンタとSLS(粉末焼結積層造形)方式3Dプリンタを使って、金型製作に移る前にメガネフレームの機能確認用試作を少量製作し、顧客から評価・フィードバックをもらっています。また、アイウェア部品の小ロット量産や量産前のテスト生産向けに、Fuse 1 SLS 3DプリンタとNylon 12パウダーで3Dプリント製の成形型の製作も開始しました。
3Dプリントの導入により、対応速度が上がっただけでなく製作可能なデザインの幅も広がりました。今回私たちは、Plastinaxでデザインエンジニアを務めるSteeven Devasagayaum氏に、Form 2とFuse 1をどう既存の工程に組み込んだのか、そして、3Dプリントによって設計や製造に対する会社のアプローチがどう変わったのかを教えていただきました。
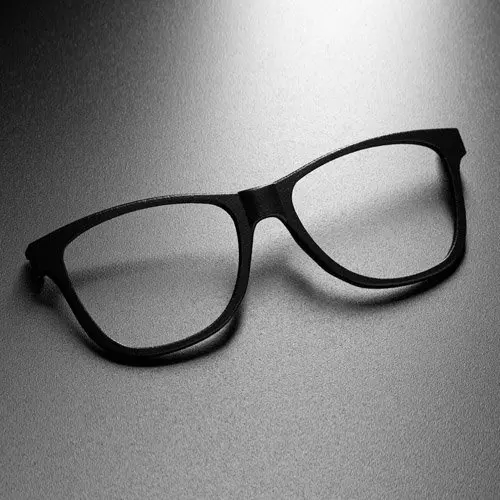
FormlabsのFuseシリーズSLS方式3Dプリンタでアイウェアを製作
この製品仕様では、アイウェア業界で現在3Dプリントを活用しているメーカーが、3Dプリント用の設計や材料を決める際に考慮している点をご紹介します。
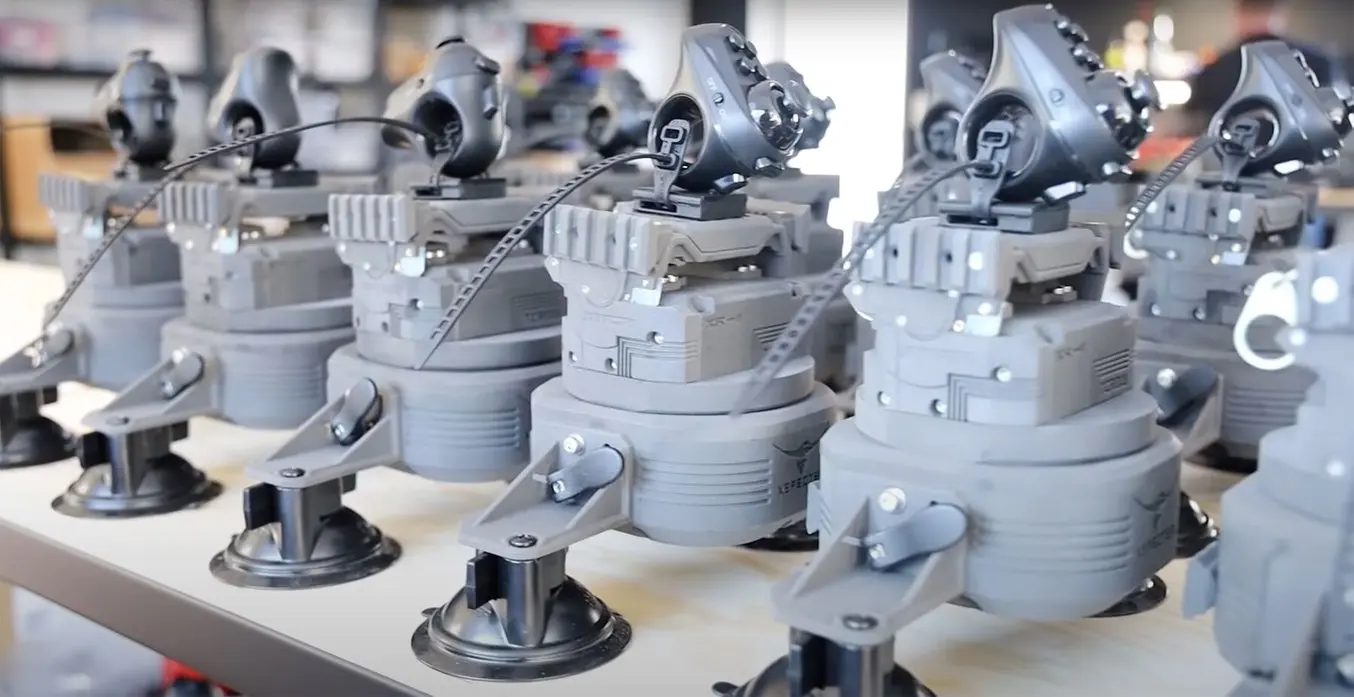
SLSを実製品の量産に活用
実製品の量産工程への3Dプリント導入は今や単に実現可能となっただけでなく、SLS Fuseシリーズを活用することでこれまでより安価かつ迅速に、そして規模の拡大にも柔軟に対応できます。量産工程におけるSLS活用事例ページにて、量産方法の比較、パウダー材料のボリュームディスカウントの詳細、現在Fuseシリーズを実際に量産工程に取り入れているメーカー15社の事例をご覧ください。
モーリシャスでの大規模製造
Plastinaxは、1970年代にアメリカやヨーロッパを始めとする世界中の有名ブランド向けにアイウェアフレームの製造を始めました。当時の他の業界と同様、設計工程は今と比べて遅く手作業の多いものでしたが、業界が始まって間もない頃でさえ、複雑なデザインやブランディングを通してクリエイティビティや差別化をアピールすることが重要視されていました。
Devasagayaum氏が同社に加わったのは2006年。それ以来、手作業での試作品製作から3Dプリント製モデルの外注に切り替えることに成功します。新しく導入されたこの工程により、最終的に射出成形で作る製品に近いモデルを早期に試作・検証できるようになり、設計工程が格段に高速化されました。デザインブリーフ、製図、手作業による試作品の製作を経て、3Dスキャンと3Dによるモデル作成を外注します。
3Dプリントでのモデル作成という新たなステップにより、最終的な製品により近づけながら、顧客から変更のリクエストがあった場合には問題の箇所がきちんと把握できるような試作品を作れるようになりました。手作業で別の試作品を作っていた場合は、完成までに1週間以上かかっていたでしょう。製作期間の長期化は、Plastinaxの競争力を損ないかねません。
3Dプリントによる内製化を実現
Plastinaxの研究開発チームは、内製で製作期間をさらに短縮できるよう、社内に導入可能なSLA光造形方式3Dプリンタを探し始めました。しかし、その当時市場に出ていた3Dプリンタはどれも高額で、3Dプリンタに投資するよりも試作品の製作を外注した方がコスト効率が良くなるほどでした。
2016年、Plastinaxは遂にForm 2を導入し3Dプリントによる内製化に踏み切ります。その1年後には、試作品製作の需要増加に対応するため、2台目が導入されました。「このプリンタで状況が一気に変わりました。設計からラピッドプロトタイピングまで、僅か数時間でこなせるようになったんです。海外顧客向けの変更も1週間以内に完了できましたし、対応の迅速さを示すことができました。性能面でコストパフォーマンスが非常に良く、何よりも安定感があります」とDevasagayaum氏は言います。
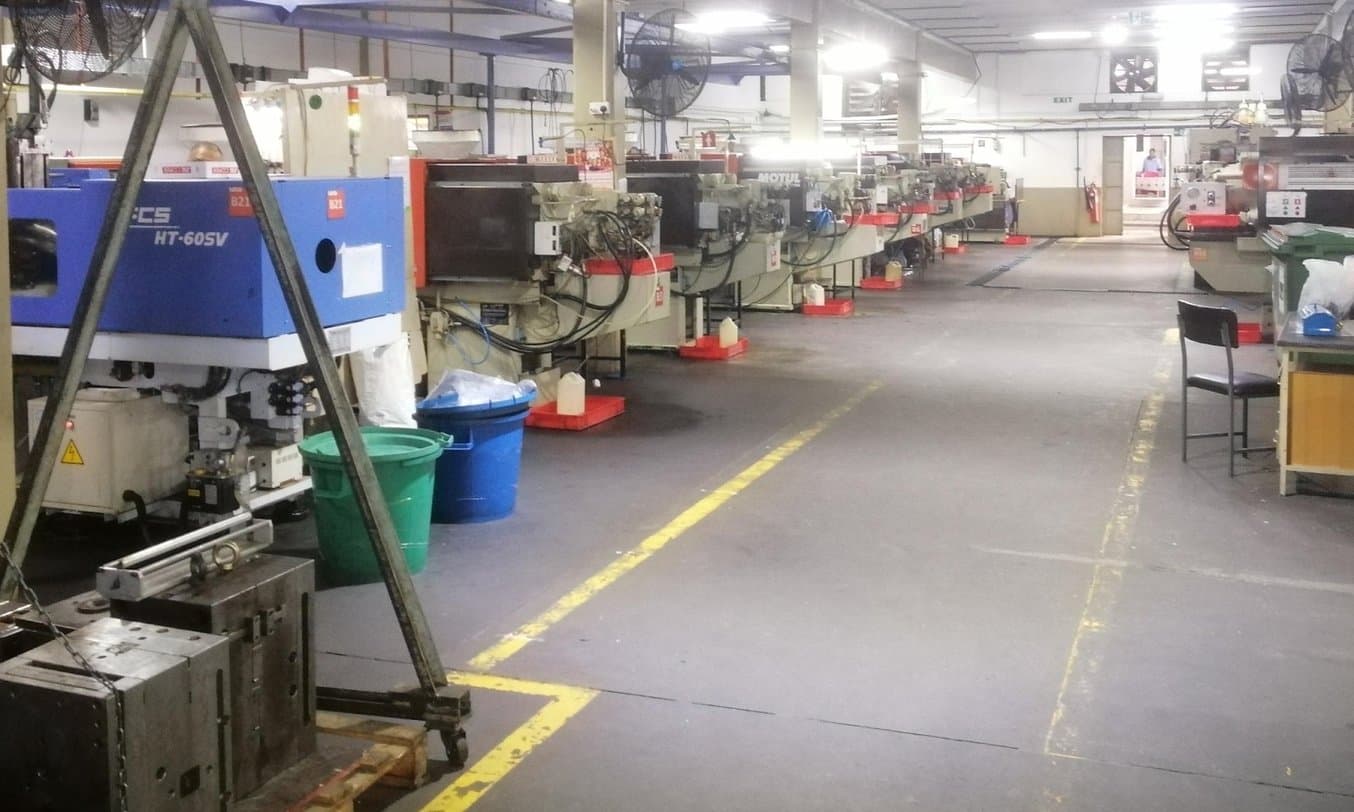
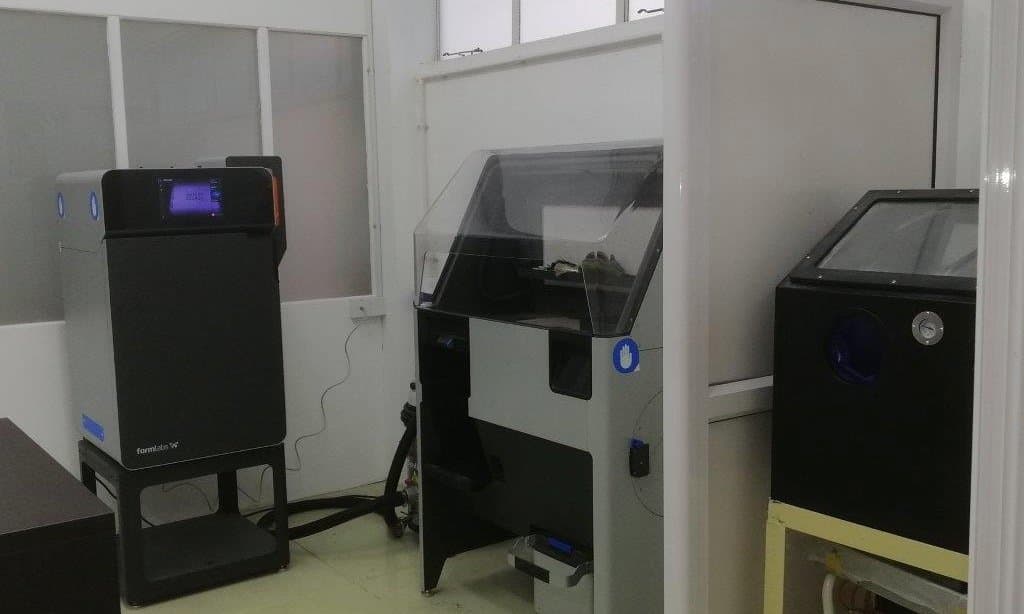
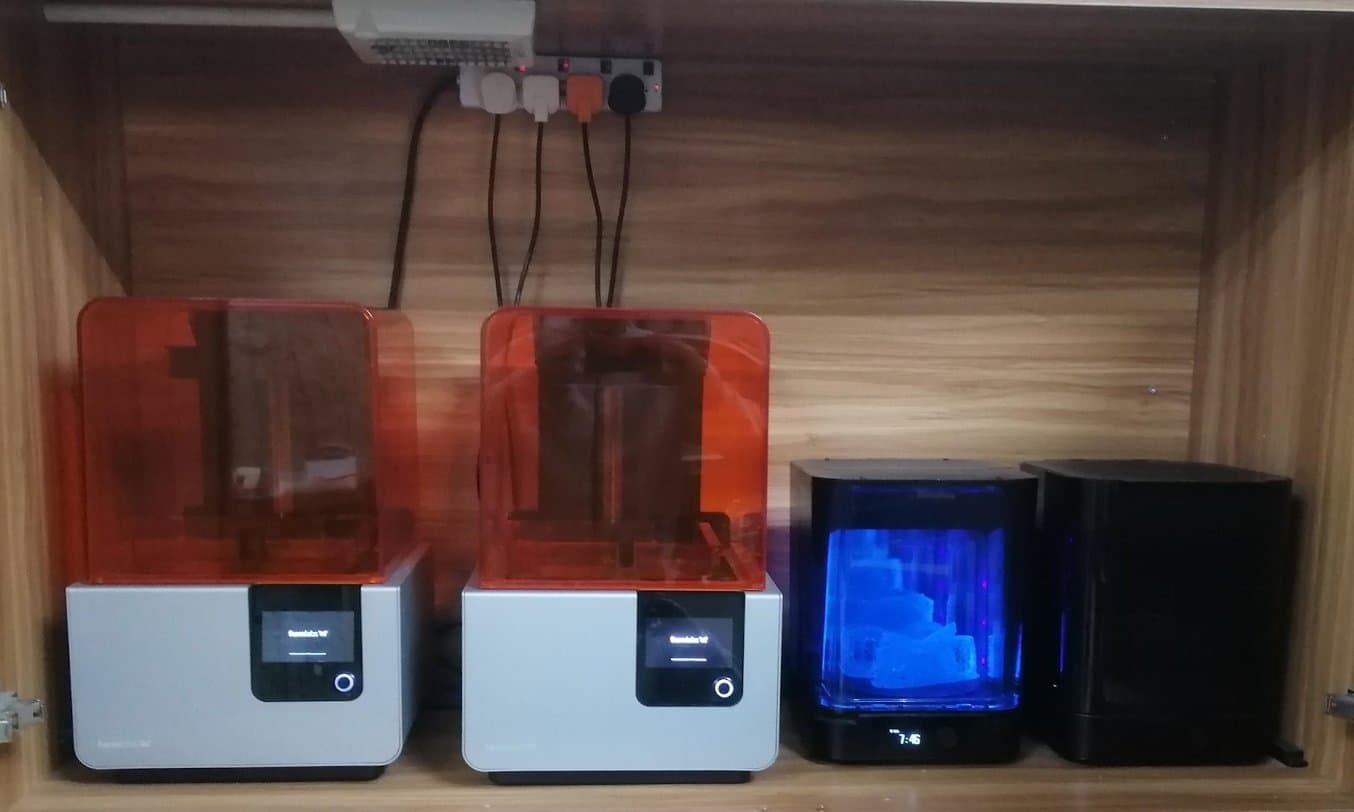
Plastinaxは、大規模製造が可能な工業力(左)を活かし、毎年100万組以上のメガネを製造している。Fuseシリーズ(中央)やForm 2(右)のような3Dプリンタを社内に導入したことで、徹底的な試作・検証が可能になり、ビジネスの継続的な成長につながっている。
SLSで製造規模を拡大
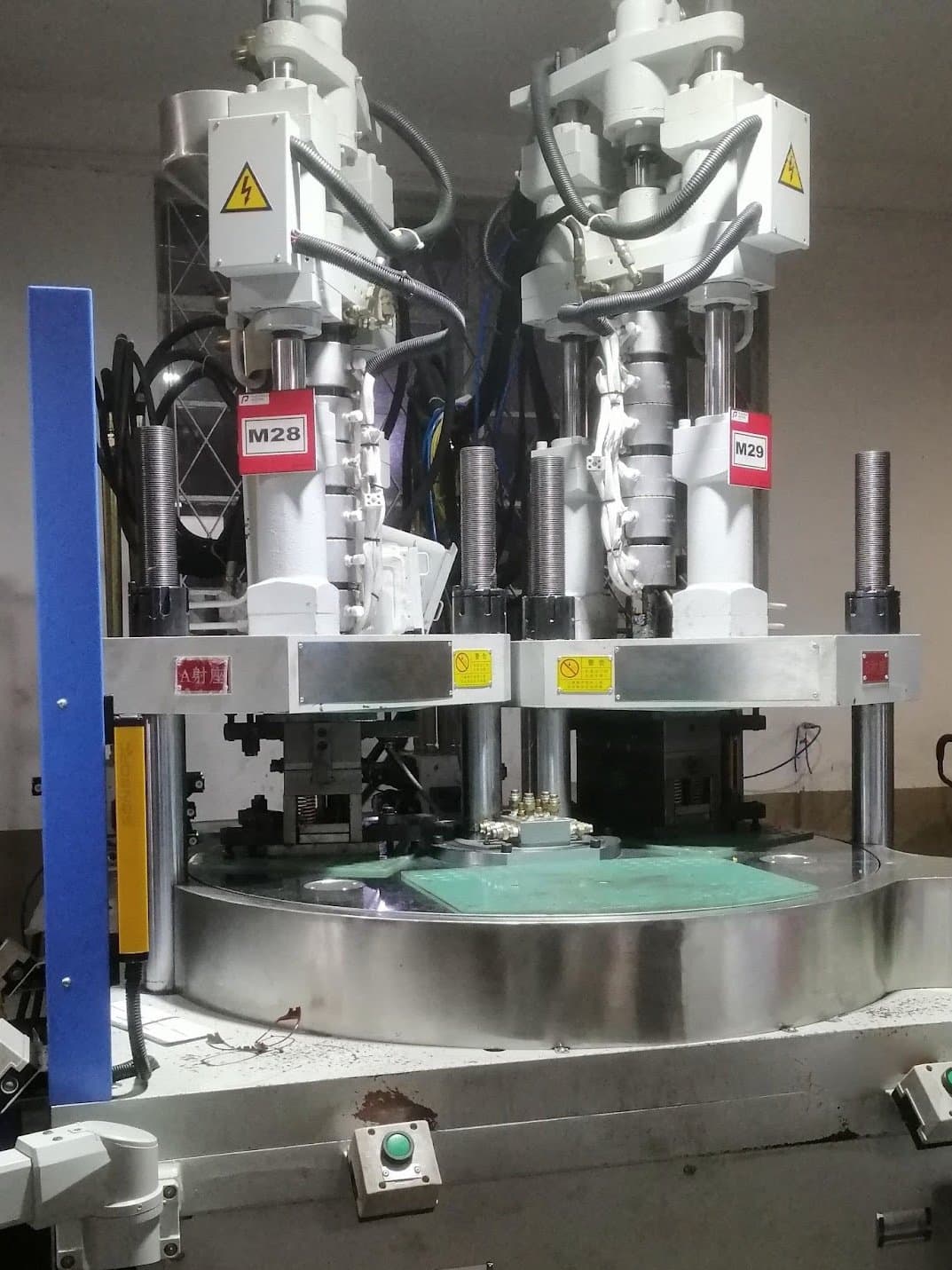
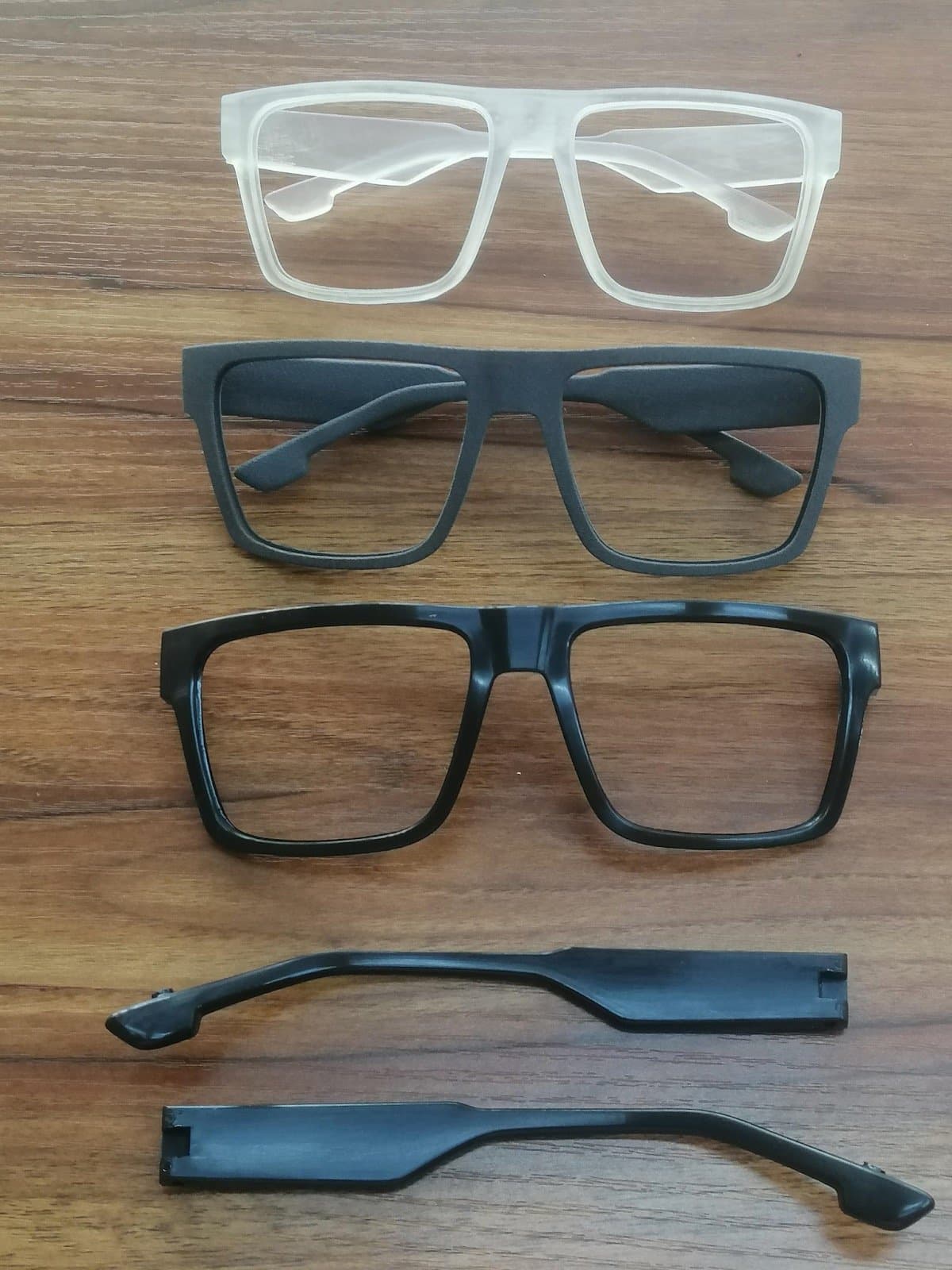
Plastinaxは現在、工業機で射出成形(左)を行いながら、SLA光造形・SLS 3Dプリント用の材料を使って実製品そっくりの外観と機能性を持つ3Dプリント製フレーム(右の写真の下段)を製作している。
Plastinaxは、半透明のデザイナーフレームにはClearレジン、機能試験用にはGrey Proレジンなど、使用するレジンの種類を拡大して製造をスケールアップしてきました。そして2021年、顧客が東アジアの競合会社がナイロン材料で3Dプリントした試作品を提示したことで、その耐久性を目の当たりにしました。「そこから、同じようなことができるプリンタを探し始めました。市場での競争力を可能な限り高めるためにも、安定感があって性能の高い3Dプリンタでイノベーションを起こす必要がありました。Formlabsとはもう6年来の付き合いになります。サポートとサービスが素晴らしかったので、Fuse 1の導入を決めました」とDevasagayaum氏が当時の様子を教えてくれます。
小さな変化で大きな成果を
Plastinaxのように海外からも注文が入る受託メーカーにとって、顧客のビジネスを堅実に支え、優れた実製品を提供できることが成功の鍵になります。そのため、単一のデザインを高品質材料で製作するだけでは十分でないこともあるのです。そういった時に、Steeven Devasagayaum氏はFuse 1の力を借りて顧客からの急な変更にも対応しています。
「アイウェアでは、わずかな違いがとても重要なんです。コンマ数ミリの違いかもしれません。ノーズブリッジの角度を1度だけ変えてほしい、という依頼を受けたことがありますが、このプリンタならそういった要望にも対応が可能で、複数のバージョンを送ることもできます」
Fuse 1 SLS 3Dプリンタは、造形中に未焼結のパウダーで造形品を支えるため、造形エリア内で造形品をネスト構造にしたり縦に積み重ねたりして効率的にパッキングすることで、パウダーの無駄を極力減らせます。今では10点以上のフレームを一度にプリントすることも可能になり、作業手順が簡素化されるだけでなく、Fuse Siftでの後処理も簡単になります。一度に複数のバリエーションを提示できたことで、Plastinaxはたった一度のやり取りで注文を獲得することができました。別の注文では、競合会社が顧客に納品したフレームのレンズサイズが間違っていたことがあり、Plastinaxが対応しました。「たった数時間で正しいサイズを見つけ出してフレームを3Dプリントし、翌日には顧客に送ることができました」とDevasagayaum氏は振り返ります。
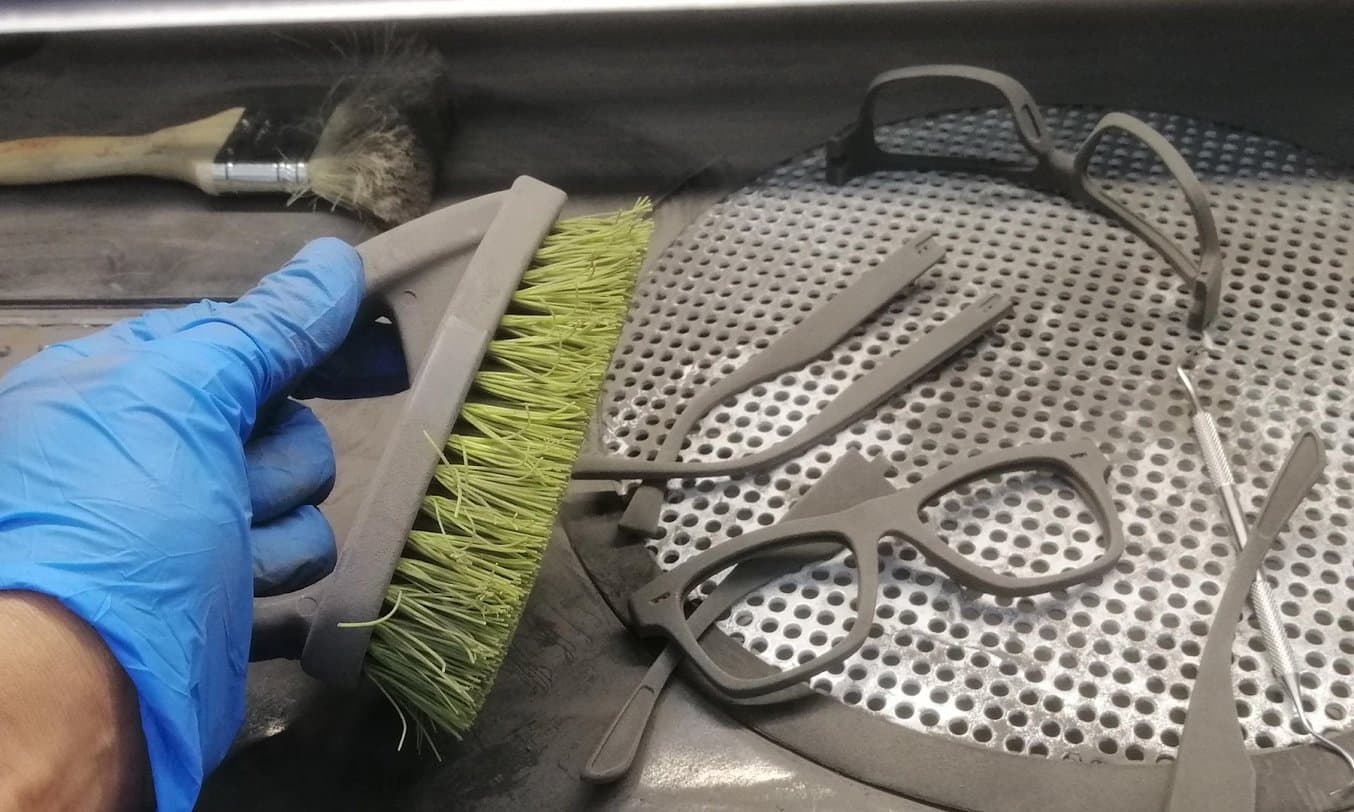
Fuse Siftにより、Plastinaxの作業手順が合理化され、フィット感や機能性、スタイルを検証する試作品の高速製作が可能に。
SLA光造形とSLSの簡素化された作業手順を活用
工業グレードのパワーを持つプリンタで内製できることで、作業手順の効率もアップします。Devasagayaum氏は設計工程でSLA光造形とSLSの両方を使用していますが、プリンタの設置面積が少ないことで、僅か1日もあれば1つの方式からもう1つの方式へと簡単に切り替えが可能です。Fuse 1では僅かな差も正確に表現する機能確認用試作を製作し、Form 2ではClearレジンを使って2種類のフレームをプリントし、塗装してそれぞれ異なる外観を提示します。
「どちらの技術も設計工程に役立っています。Nylon12パウダーは最終的に射出成形で作るフレームのポリアミド材料に似ていますし、Clearレジンで作った部品にはニスを塗ったり模様をつけたりして製品の外観を確認することができます。SLA光造形方式の優れた表面品質と、SLS用ナイロン材料の強度や耐久性の両方を活用しています。
Plastinax デザインエンジニア、Steeven Devasagayaum氏
ナイロンはポリアミド材料と特性が似ているため、最終的に射出成形で作るフレームの重量や強度をイメージしやすくなります。Devasagayaum氏は、顧客から保護ゴーグルのデザインブリーフをもとに依頼があった際、顧客のマーケティングチームに見せられるよう複数バージョンの試作品を高速製作しました。保護ゴーグルは、耐久性と耐衝撃性の他に僅かな柔軟性も必要となるため、SLS 3Dプリントでの製作が最適でした。「3Dプリントした試作品にニスを塗って、最終的なプラスチックの成形品にそっくりな見た目を再現することができました」とDevasagayaum氏は言います。
また、試作品にレンズを着脱する際はNylon 12パウダーの持つ柔軟性が役に立ちます。Plastinaxがさまざまなフレーム向けに厚みの異なるレンズで機能確認用試作を製作してくれるおかげで、顧客は射出成形で作る最終的なフレームの外観や機能を正確に確認できます。
同社は今では、産業見本市などで多数の製品が必要になる場合には28種類もの試作品を一度にFuse 1で3Dプリントしています。「外観も機能も完成品にそっくりな試作品を内製で高速製作できます。外注に頼っていた場合、製作期間として10日以上はかかっていたでしょうね」とDevasagayaum氏は言います。
Fuseシリーズは、試作品製作の他に、新しい成形型の製作でもPlastinaxの業務を支援しています。ナイロンの持つ僅かな柔軟性と高い寸法精度により、生産ラインを支援する丈夫な成形型を設計、検証、製作できます。例えば、Devasagayaum氏はレンズカット用のレンズフォーマー(型板)やベース、テンプル部分で使用する柔らかな金属製ヒンジを挿入するためのベース、金属製のカスタムロゴの埋め込む場所を掘る際にフレームを固定するためのベースを3Dプリントしています。
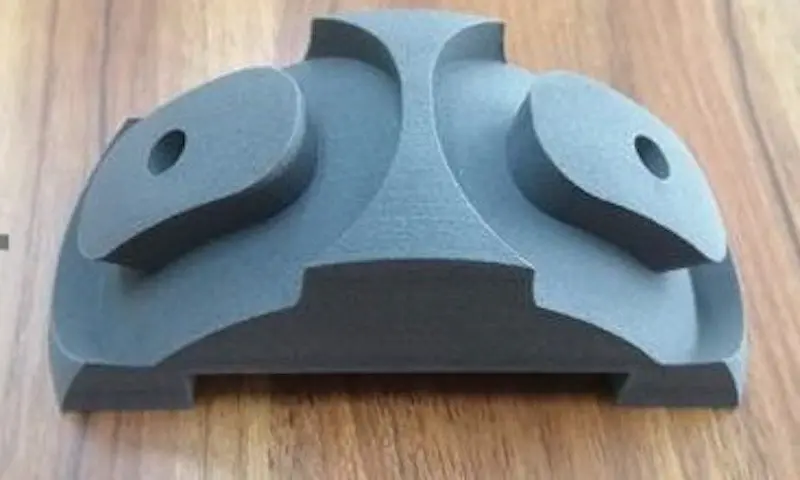
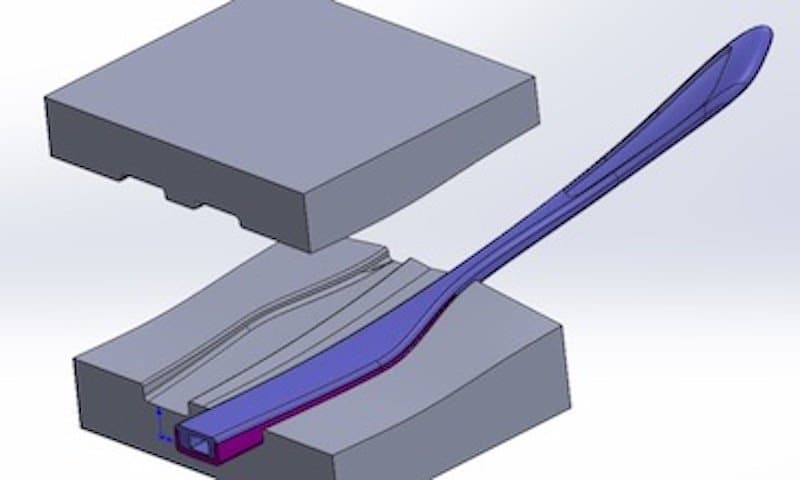
Plastinaxは、レンズ成形用の型(左)や、テンプル部分で使用する金属製フレックスヒンジを挿入するためのベース、金属製のカスタムロゴ用の空洞をCNC加工するためのフレームを3Dプリントで製作している。
この先に見据える可能性
アイウェア業界は、カスタマイゼーションの分野で第一線を走る業界になるかもしれません。メガネは、ファッションとしても何百万人もの視力を補う生活の一部としても使用できる数少ない製品の一つで、一人一人の顔の形に合わせたカスタマイズと、好みの外観に合わせたカスタマイズという両方の側面でアプローチが可能です。
Plastinaxは、そう遠くない未来でカスタマイゼーションの価値が高まることをすでに認識し、SLA光造形とSLSの両方に注目しています。Devasagayaum氏はすでに、SLA光造形でRigid 10Kレジンなどの材料を使い、射出成形用のラピッドツーリングで金型レスを目指しながら、SLSプリンタのFuse 1で実製品用のフレームを直接3Dプリントし、少量で連続生産する方法を視野に入れています。Devasagayaum氏は「可能性は無限大です。Form 2のおかげで2016年に状況が一変し、その後Fuse 1の導入でさらに変化がありました」と話します。
アイウェアフレームの3Dプリントの詳細については、アプリケーションガイドをご覧ください。また、FormlabsではSLSやSLA光造形3Dプリンタの導入に関するご相談も承っております。